回焊炉温度曲线量测规范
炉温曲线测量管理规程

XXX有限公司受控标识:f丄竖TJ 分发号:02D炉温曲线测量管理规程1.LI的:指导回流焊锡工艺以及胶水固化的回流炉之温度的设定。
2.适用范围适用于电子分厂SMT生产车间,采用熔点为200-220°C的无铅焊膏、以及使用环氧树脂类型胶水(红胶)进行固化的生产3.定义:无4.职责工程:工程师判断温度profile的正确性。
品质:质量部IPQC按照规定要求监督和检查温度profile的执行情况,并如实记录温度。
生产:生产部技术员按照规定要求设定和测量温度并负责制作测温板5.工作内容5. 1 炉温测量时间5. 1. 1 生产线转换机种,过炉前必须测量温度profileo5. 1. 2 回流炉维修保养后,开机生产前必须测量温度profileo5. 1. 3 回流炉停机4小时以上,开机生产前必须测量温度profileo5. 1.4 同一机种除了开始的时候测量温度profile,回流焊没有中途出现5. 1. 2、5.1. 3、修改炉温和软件、硬件故障等条件下每12H测一次温度profileo5. 1. □工艺工程师的要求测量温度profile条件下需测量profileo5. 2 测量所需工具5. 2. 1 高温锡线:成分大致Pb90Snl0,熔点温度约304度5.2.2 PCB:和生产产品类似的PCB。
5. 2.3 热电偶:K型,温度测量范围-200〜1250°C,精度±1.5°C。
5.2.4烙铁:烙铁温度可以达到450°C。
5.2.5手钻:直径约1mm的钻头5. 2. 6 测温仪:温度profile专用测量仪器。
5.3测温板的制作:5. 3. 1 本司规定在温度profile测量中测量3点温度,分别为PCB表面温度、BGA底部温度(如果无其它测量点,BGA测量两点),如果产品中有CPU插座等温度敬感元件也必须测量一点。
如果PCB有其它特殊的地方也需要在该点测量温度。
回流焊温度曲线测试操作指示
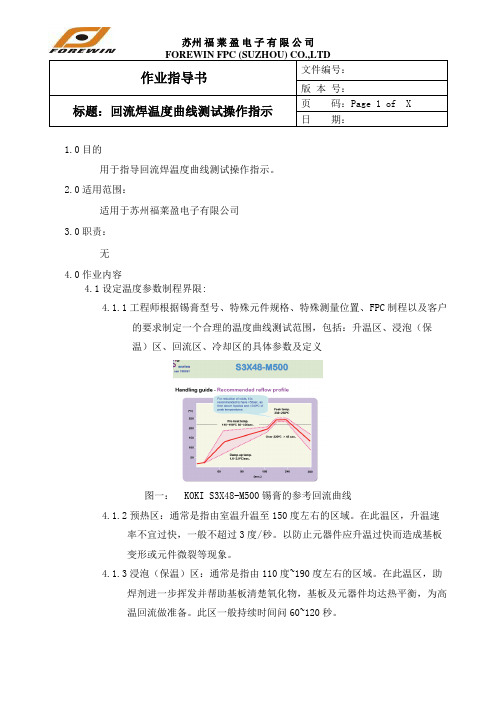
1.0目的用于指导回流焊温度曲线测试操作指示。
2.0适用范围:适用于苏州福莱盈电子有限公司3.0职责:无4.0作业内容4.1设定温度参数制程界限:4.1.1工程师根据锡膏型号、特殊元件规格、特殊测量位置、FPC制程以及客户的要求制定一个合理的温度曲线测试范围,包括:升温区、浸泡(保温)区、回流区、冷却区的具体参数及定义图一: KOKI S3X48-M500锡膏的参考回流曲线4.1.2预热区:通常是指由室温升温至150度左右的区域。
在此温区,升温速率不宜过快,一般不超过3度/秒。
以防止元器件应升温过快而造成基板变形或元件微裂等现象。
4.1.3浸泡(保温)区:通常是指由110度~190度左右的区域。
在此温区,助焊剂进一步挥发并帮助基板清楚氧化物,基板及元器件均达热平衡,为高温回流做准备。
此区一般持续时间问60~120秒。
4.1.4回流区:通常是指超过217度以上温度区域。
在此温区,焊膏很快熔化,迅速浸润焊接面,并与基板PAD形成新的合金焊接层,达到元件与PAD之间的良好焊接。
此区持续时间一般设定为:45~90秒。
最高温度一般不超过250度(除有特定要求外)。
4.1.5冷却区:该区为焊点迅速降温,将焊料凝固,使焊料晶格细化,提高焊接强度。
本区降温速率一般设置为-3~-1度/秒左右。
4.2测温板的制作4.2.1采用与生产料号一致的样品板作为测温板,制作测温板时,原则上应保留必要的具有代表性的测温元器件,以保证测试测量温度与实际生产温度保持一致。
4.2.2测温板与生产料号在无法保持一致情况下,经工程师验证认可,可使用与之同类型的测温板进行测量。
4.2.3测温点应该选择最具有代表性的区域及元件,比如最大及最小吸热量的元件,零件选取优先级(如Socket->Motor->大型BGA ->小型BGA->QFP或SOP->标准Chip)除此之外,还应选择介于两者之间的一个测温区。
如图:4.2.4一般测温点在每板上不得少于3个,有BGA或大型IC至少选取4个,基于特殊代表型元件为首选原则选取元件。
回流炉炉温曲线讲解

回流炉炉温曲线讲解
本课件PPT仅供大家学习使用 学习完请自行删除,谢谢! 本课件PPT仅供大家学习使用 学习完请自行删除,谢谢! 本课件PPT仅供大家学习使用 学习完请自行删除,谢谢! 本课件PPT仅供大家学习使用 学习完请自行删除,谢谢!
ECD炉温测试仪进炉前
ECD炉温测试仪出炉后
ECD炉温测试仪测得曲线结果
ECD炉温测试仪
ECD炉温测试仪详细介绍
ECD炉温测试仪优点及操作手册 请参考ECБайду номын сангаас炉温测试仪介绍附件
深圳市意希帝科技 谢谢
回流炉温曲线回流区作用
回流阶段,温度继续升高越过回流线,锡膏融化并发生 润湿反响,开场生成金属间化合物层。到达最高温度〕, 然后开场降温,落到回流线以下,焊锡凝固。
回流区同样应考虑温度的上升和下降斜率不能使元件受 到热冲击。回流区的最高温度是由PCB板上的温度敏感 元件的耐温能力决定的。在回流区的时间应该在保证元 件完成良好焊接的前提下越短越好,一般为30-60秒最 好,过长的回流时间和较高温度,如回流时间大于90秒, 最高温度过大,会造成金属间化合物层增厚,影响焊点 的长期可靠性。
焊点的位置一般为选取元件的焊脚和焊盘接触的地方。焊点不能太 大,以焊牢为准。焊点大,温度反响迟后,不能准确反映温度变化, 尤其是对QFP等细间距焊脚。对特殊的器件如BGA还需要在PCB板 下钻孔,把热偶线穿到BGA下面。
热偶线的安装位置一般根据PCB板的工艺特点来选取,如双面板应 在板上下都安装热偶线,大的IC芯片脚要安装,BGA件要安装,某 些易造成冷焊的元件〔如金属屏蔽罩周围,散热器周围元件〕一定 要放置。 还有就是你认为要研究的焊接出了问题的元件。
回流焊温度与温度曲线设置规范

回流焊温度与温度曲线设置规范
1目的
1.1指导技术人员正确设置温度
2 范围
2.1本司SMT技术人员适用
2.2本司回流焊适用
3 内容
3.1设定原则:根据锡膏、胶水供应商所提供有关锡膏、胶水的温度曲线图与性
能数据等资料作为参考,以实际生产产品不同适当设定各温区温度;
3.2设定温度依据测试温度为准,若不合格需做相应修改后再测试,直到合格为
止;
3.3无特殊要求下,本司回流焊温度曲线应符合如下条件:
3.3.1 无铅锡膏(一般以Sn96 /Ag3.5/Cu0.5、Sn96.5/ Ag3/ Cu0.5、、Sn96.5/
Ag3.5为准);
150℃-190℃之时间段为: 60ses-120ses
高于220℃之时间段为: 30 ses-90 ses;
峰值温度为:235℃~255℃
3.32胶水:130℃~155℃之间保持时间为:120 ses-180 ses
3.4我公司回流焊显示器实际温度与设置温度相差5℃以上(不含5℃)时为异常,
此时不可使用回流焊.
4 温度测试
4.1 每个班次需对运行中的回流炉进行一次温度测量确认,如有转线之机型重新设置温度曲线后需要再次测量温度达到合格。
关于SMT回流焊炉温测试的规定

关于SMT回流焊炉温测试的规定
一目的和适应范围
为规范SMT回流焊炉温测试要求,明确测试频率、测试步骤和判定标准,特制定本规定。
本规定适用于SMT回流焊炉温的测试。
二术语和定义
2.1 SMT炉温测试仪
SMT炉温测试仪是指检测SMT(表面贴装)行业回流炉炉温曲线的精密仪器。
2.2 测温板
测温板是指为配合测试SMT回流焊炉温而专门制作的PCB样板。
三权责
3.1 SMT车间线(组)长负责开展SMT回流焊炉温测试,并对测试结果负责。
3.2 SMT车间经理(副经理)负责监督SMT回流焊炉温测试符合要求。
四规定细则
4.1 SMT车间经理(副经理)应制定SMT回流焊炉温测试要求,包括测试频率、测试步骤和判定标准,设计并制作相配套使用的测温板。
4.2 测温板制作所需工具:测温仪、测温线、烙铁、耐高温胶布、高温焊锡丝(Sn10Pb88Ag2)。
4.3 测温板制作要求:
a)一般PCB测温板测试点位置选取要求六个点,测温线镍铬端应接在测温头正极;
b)测温板应结合元器件的温度特性;
c)测温板上最大元器件脚必须测量;
d)测温点直接用高温焊锡丝焊接到测温板上;
e)防止测温线松动应使用高温胶布固定。
4.4 SMT车间线(组)长应依据如下测试频率开展SMT回流焊炉温测试:
a)早上开机必须测试炉温;
b)更换机种必须测试炉温;
c)炉后异常必须测试炉温;
d)炉温异常必须测试炉温。
4.5 SMT车间线(组)长应依据如下测试步骤开展SMT回流焊炉温测试:。
回流焊接温度曲线
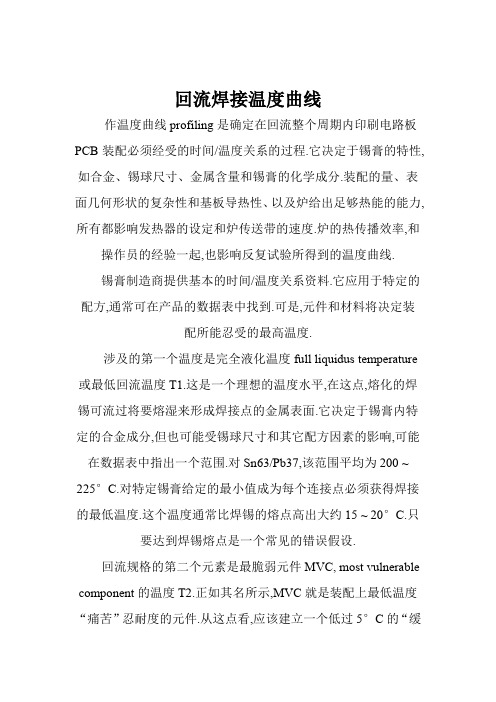
回流焊接温度曲线作温度曲线profiling是确定在回流整个周期内印刷电路板PCB装配必须经受的时间/温度关系的过程.它决定于锡膏的特性,如合金、锡球尺寸、金属含量和锡膏的化学成分.装配的量、表面几何形状的复杂性和基板导热性、以及炉给出足够热能的能力,所有都影响发热器的设定和炉传送带的速度.炉的热传播效率,和操作员的经验一起,也影响反复试验所得到的温度曲线.锡膏制造商提供基本的时间/温度关系资料.它应用于特定的配方,通常可在产品的数据表中找到.可是,元件和材料将决定装配所能忍受的最高温度.涉及的第一个温度是完全液化温度full liquidus temperature 或最低回流温度T1.这是一个理想的温度水平,在这点,熔化的焊锡可流过将要熔湿来形成焊接点的金属表面.它决定于锡膏内特定的合金成分,但也可能受锡球尺寸和其它配方因素的影响,可能在数据表中指出一个范围.对Sn63/Pb37,该范围平均为200 ~ 225°C.对特定锡膏给定的最小值成为每个连接点必须获得焊接的最低温度.这个温度通常比焊锡的熔点高出大约15 ~ 20°C.只要达到焊锡熔点是一个常见的错误假设.回流规格的第二个元素是最脆弱元件MVC, most vulnerable component的温度T2.正如其名所示,MVC就是装配上最低温度“痛苦”忍耐度的元件.从这点看,应该建立一个低过5°C的“缓冲器”,让其变成MVC.它可能是连接器、双排包装DIP, dual in-line package的开关、发光二极管LED, light emitting diode、或甚至是基板材料或锡膏.MVC是随应用不同而不同,可能要求元件工程人员在研究中的帮助.在建立回流周期峰值温度范围后,也要决定贯穿装配的最大允许温度变化率T2-T1.是否能够保持在范围内,取决于诸如表面几何形状的量与复杂性、装配基板的化学成分、和炉的热传导效率等因素.理想地,峰值温度尽可能靠近但不低于T1可望得到最小的温度变化率.这帮助减少液态居留时间以及整个对高温漂移的暴露量.传统地,作回流曲线就是使液态居留时间最小和把时间/温度范围与锡膏制造商所制订的相符合.持续时间太长可造成连接处过多的金属间的增长,影响其长期可靠性以及破坏基板和元件.就加热速率而言,多数实践者运行在每秒4°C或更低,测量如何20秒的时间间隔.一个良好的做法是,保持相同或比加热更低的冷却速率来避免元件温度冲击.图一是最熟悉的回流温度曲线.最初的100°C是预热区,跟着是保温区soak or preflow zone,在这里温度持续在150 ~ 170°C 之间对Sn63/Pb37.然后,装配被加热超过焊锡熔点,进入回流区,再到峰值温度,最后离开炉的加热部分.一旦通过峰值温度,装配冷却下来.温度热电偶的安装适当地将热电偶安装于装配上是关键的.热电偶或者是用高温焊锡合金或者是用导电性胶来安装,提供定期检测板的温度曲线精度和可重复性的工具.对很低数量的和高混合技术的板,也可使用非破坏性和可再使用的接触探头.应该使用装配了元件的装配板来通过炉膛.除非是回流光板bare board,否则应该避免使用没有安装元件的板来作温度曲线.热电偶应该安装在那些代表板上最热与最冷的连接点上引脚到焊盘的连接点上.最热的元件通常是位于板角或板边附近的低质量的元件,如电阻.最冷的点可能在板中心附近的高质量的元件,如QFPquad flat pack、PLCCplastic leaded chip carrier或BGAball grid array.其它的热电偶应该放在热敏感元件即MVC 和其它高质量元件上,以保证其被足够地加热.如果用前面已经焊接的装配板,则必须从那些热电偶将要安装的连接点上去掉焊锡.因为板可能是用Sn63/Pb37焊接的,而现在将要用Sn10/Pb90,用后者来简单焊接热电偶将会产生一种“神秘”合金,或者一种不能维持测试板所要求的多个温度变化的合金.在去掉老的焊锡后,用少量助焊剂,跟着用少量而足够的高温焊锡.如果用导电性胶来安装热电偶,同样的步骤去掉下面的Sn63/Pb37或其它合金.这是为了避免破坏热电偶的胶合附着,从而可能导致回流期间的托焊.推荐使用K型、30 AWG 的热电偶线,最好预先焊接.在安装之后,热电偶引线引到PCB装配的后面相对行进方向.有人宁愿用一个接头接在热电偶引线的尾沿.这样测量设备可很快连接和分开.开普敦Kapton胶带一种耐高温胶带用来在适当位置固定热电偶的引线.多数回流机器装备有机上作温度曲线的软件,允许热电偶引线插在炉子上,实时地从系统显示屏幕上跟踪.有人宁愿使用数据记录设备,和测试装配板一起从炉中通过,以可编程的时间间隔从多个热电偶记录温度.这些系统是作为“运行与读数run-and-read”或数据发送单元来使用的,允许实时地观察温度曲线.对后者,系统必须不受射频干扰RFI, radio frequency interference、电磁干扰EMI, electromagnetic interference 和串扰crosstalk的影响,因此当来自发射机的数据还没有来时,不会去“猜测”温度.不管用哪一种数据记录器,定期的校准是必要的.渐升式温度曲线Ramp profile保温区soak zone有热机械的thermomechanical重要性,它允许装配的较冷部分“赶上”较热部分,达到温度的平衡或在整个板上很低的温度差别.在红外IR, infrared回流焊接开始使用以来,这个曲线是常用的.在加热PCB装配中,SMT早期的红外与对流红外炉实际上缺乏热传导能力,特别是与今天的对流为主的convection-dominant炉相比较.这样,锡膏制造商们配制它们的几乎松香温和活性RMA, rosin mildly active材料,来满足回流前居留时间的要求,尝试减少温度差别图二.另一方面,以对流为主要热机制的对流为主的convection-dominant炉通常比其前期的炉具有高得多的热传导效率.因此,除非装配的元件实在太多,需要保温来获得所希望的温度差别,否则回流前的保温区是多余的,甚至可能是是有害的,如果温度高于基板玻璃态转化温度substrate glass-transitionTg的时间过长.在大多数应用中,渐升式温度曲线ramp profile是非常好的图三.尽管有人认为锡膏助焊剂配方要求回流前保温preflow soak,事实上,这只是为了能够接纳那些老的、现在几乎绝种的、对流/IR炉技术.一项最近的有关锡膏配方的调查显示,大多数RMA、免洗和水溶性材料都将在渐升式温度曲线上达到规定要求1.事实上,许多有机酸OA, organic acid水溶性配方地使用的保温时间也要尽可能小—由于有大量的异丙醇含量作为溶剂,它们容易很快挥发.在使用渐升式温度曲线ramp profile之前,应该咨询锡膏制造商,以确保兼容性.虽然一些非常量大或复杂的PCB装配还将要求回流前的保温,但大多数装配即,那些主要在线的将受益于渐升式温度曲线ramp profile.事实上,后者应该是如何锡膏评估程序中的部分,不管是免洗,还是水溶性.氮气环境一个焊接的现有问题是有关在回流焊接炉中使用氮气环境的好处.这不是一个新问题—至少一半十年前安装的回流炉被指定要有氮气容器.而且,最近与制造商的交谈也显示还有同样的比例存在,尽管使用氮气的关键理由可能现在还未被证实.首先,重要的是理解使回流环境惰性化是怎样影响焊接过程的.焊接中助焊剂的目的是从要焊接的表面,即元件引脚和PCB 焊盘,去掉氧化物.当然,热是氧化的催化剂.因为,根据定义,热是不可能从基本的温度回流焊接过程中去掉的,那么氧—氧化的另一元素—通过惰性的氮气的取代而减少.除了大大地减少,如果没有消除,可焊接表面的进一步氧化,这个工艺也改善熔锡的表面张力.在八十年代中期,免洗焊锡膏成为可行的替代品.理想的配方是外观可接受的光亮的、稀薄的和无粘性的、腐蚀与电迁移良性的、和足够薄以致于不影响ICTin-circuit test针床的测试探针.残留很低的锡膏助焊剂固体含量大约为 ~ %满足前两个标准,但通常影响ICT.只有固体含量低于%的超低残留材料才可看作与测试探针兼容.可是,低残留的好处伴随着低侵蚀性助焊剂处理的成本代价,需要它所能得到的全部帮助,包括回流期间防止进一步氧化的形成.这个要用氮气加入到回流过程来完成.如果使用超低残留焊锡膏,那么需要氮气环境.可是,近年来,也可买到超低残留的焊锡膏,在室内环境非氮气也表现得非常的好.原来的有机可焊性保护层OSP, organic solderability preservative在热环境中有效地消失,对双面装配,要求氮气回流环境来维持第二面的可焊性.现在的OSP也会在有助焊剂和热的时候消失,但第二面的保护剂保持完整,直到印有锡膏,因此回流时不要求惰性气体环境.氮气回流焊接的最古老动机就是前面所提到的改善表面张力的优点,通过减少缺陷而改善焊接合格率即是归功于它.其它的好处包括:较少的锡球形成、更好的熔湿、和更少的开路与锡桥.早期的SMT手册提倡密间距的连接使用氮气,这是基于科学试验得出的结论.可是,这测试是实验室的试验,即,“烧杯试验”与实际生产的关系,没有把使用氮气的成本计算在内.应该记住,在过去十五年,炉的制造商已经花了许多钱在开发R&D之中,来完善不漏气的气体容器.虽然当使用诸如对流为主的convection-dominant这类紊流空气时,不容易将气体消耗减到最小,但是有些制造商使用高炉内气体流动和低氮气总消耗,已经达到非常低的氧气水平.这样做,他们已经大大地减低了使用氮气的成本.随着连接的密度增加,过程窗口变小.在这个交接口,在有CSPchip scale package和倒装芯片flip chip的应用中使用氮气是很好的保证.双面回流焊接人们早就认识到的SMT的一个优点是,元件可以贴装在基板的两面.可是,问题马上出现了:怎样将前面回流焊接的元件保持在反过来的一面上完好无损,如果第二面也要回流焊接人们已经采取了无数的方法来解决这个困难:一个方法是有胶将元件粘在板上,这个方法只用于波峰焊接无源元件passive component、小型引脚的晶体管SOT和小型引脚集成电路SOIC.可是,这个方法涉及增加步骤和设备来滴胶和固化胶.另一个方法是为装配的顶面和底面使用两种不同的焊锡合金,第二面的锡膏的熔点较低.第三个方法是企图在炉内装配板的顶面和底面之间产生一个温度差.可是,由于温度差,基板Z轴方向产生的应力可能对PCB结构,包括通路孔和内层,有损耗作用.在有些应用中,虽然这种应力可能是有名无实的,但还是需要小心处理.事实上,有更实际的解决办法.人们不要低估熔化金属的粘性能力—它远比锡膏的粘性强. 记住这一点,元件绑解的表面积越大,保持它掉落的力就越大.为了决定哪些元件可用作底面贴附与随后的“回流”,导出了一个比率,评估元件质量与引脚/元件焊盘接触面积之间的关系2:元件重量克焊盘配合的总面积平方英寸这里,第二面的每平方英寸克必须小于或等于30.侵入式焊接Intrusive Soldering波峰焊接是一个昂贵的工艺,因为伴随着越来越多的对其废气排放的研究—这也是工业为什么要减少波峰焊接需求的一个理由.另一个理由是随着表面贴装元件SMD的使用,放用回流焊接传统通孔元件特别是连接器的兴趣越来越多.取消波峰焊接不仅经济上和制造上有好处,而且消除了一个处理中心,通过减少周期时间和占地面积使得装配线更流畅.从工艺观点来看,PCB 减少一次加热过程,这一点对潜在的温度损害和金属间增长是很重要的.侵入式焊接即通孔回流through-hole reflow、单中心回流焊接single-center reflow soldering、引脚插入锡膏pin-in-paste,等是一个表面贴装和通孔元件都在回流焊接系统中焊接的工艺.采用该工艺可减少波峰和手工焊接.这不是一个“插入式drop-in”的工艺 151; 因为沉积的焊锡用来连接SMD 和传统两种元件,控制锡量是必须的.有人用模板stencil来将锡膏印刷到孔内.这里,小心是很重要的,以保证插入的通孔元件引脚不会带走太多的锡膏.其它的使用者将焊锡预成型结合到工业中,来提供足够的锡量给插入的元件.可是,这是一个昂贵的选择,并且不太适合于自动过程.一个更先进的方法是调节围绕电镀通孔周围的焊盘直径与几何形状.最主要的问题是多少锡量才达到“足够的”通孔连接以及“最佳的”锡膏沉积方法,该工艺还处在试验阶段.侵入式焊接Intrusive soldering也要求回流系统比平常多的加热能力.工艺中增加的通孔元件数量对回流系统的热传送效率的要求更高.许多混合技术装配的复杂表面几何形状要求一个很高的热传送系数,以可接受的温度差来充分地回流装配.虽然大多数对流为主的炉可胜任这个任务,在某些装配上的某些元件的热敏感性可能阻碍其通过回流焊系统.这个情况可能在使用较高熔点的无铅焊锡时,变得更富挑战性.可是,对大多数应用,侵入式焊接具有很大的吸引力,理所当然应该得到考虑.结论虽然本文重点在量的回流焊接上面,但相同的原则与惯例对其它的选择性的回流工艺,包括激光,都是可应用的.虽然回流焊接是一个高要求的工艺,但它不是“火箭科技”—必须控制但非常可受的.适当的设备与材料选择,以及理解主要的热、化学和冶金的工艺,将向高合格率的焊接工艺迈出一大步.溅锡的影响减到最小罗丝.伯恩逊、大卫.斯比罗里和杰弗里.安卫勒美在回流之后,内存模块的连接器“金手指”可能出现溅锡的污染,这意味着产品的品质和可靠性问题和制造流程问题.溅锡只是表面污染的一种,其它类型包括水渍污染和助焊剂飞溅.这些影响较小,但由于焊锡飞溅,焊锡已实际上熔湿了“金手指”的表面.“小爆炸”溅锡有许多原因,不一定是回流焊接时热的或熔化的焊锡爆发性的排气结果.例如,通过观察过程,以保证锡膏丝印时的最佳清洁度,溅锡问题可以减少或消除.任何方法,如果使锡膏粉球可能沉积在金手指上,并在回流过程时仍存在,都可以产生溅锡.包括:在丝印期间没有擦拭模板底面模板脏误印后不适当的清洁方法丝印期间不小心的处理机板材料和污染物中过多的潮汽极快的温升斜率超过每秒4° C在后面的原因中,助焊剂的激烈排气可能引起熔化焊接点中的小爆炸,促使焊锡颗粒变成在回流腔内空中乱飞,飞溅在PCB 上,污染连接器的“金手指”.PCB材料内夹住潮气的情况是一样的,和助焊剂排气有相同的效果.类似地,板表面上的外来污染也引起溅锡.溅锡的影响虽然人们对溅锡可能对连接器接口有有害的影响的关注,还没有得到证实,但它仍然是个问题,因为轻微的飞溅“锡块”产生对连接器金手指平面的破坏.这些锡块是不柔顺的,锡本身比金导电性差,特别是遭受氧化之后.第一个最容易的消除溅锡的方法是在锡膏的模板丝印过程.如果这个过程是产生溅锡的原因的话,那么通过良好的设备的管理及保养来得到控制,包括适当的丝印机设定和操作员培训.如果原因不在这里,那么必须检查其它方面.水印污染:其根本原因还未完全理解,虽然可能涉及许多根源.因为已经显示清洁的、未加工的、无锡膏的和没有加元件的板,在回流后也会产生水印污染,所以其中包括了许多的原因:PCB制造残留、炉中的凝结物、干助焊剂的飞溅、清洗板的残留和导热金的变色等.水印污染经常难于发现,但其对连接器接口似乎并无影响.事实上内存模块的使用者并不关心这类表面污染,常常看作为金的变色.助焊剂飞溅:一般理解为,助焊剂水滴在回流炉中变成空中乱飞,分散和附着在整个板上,包括金手指.有两种理论试图说明助焊剂飞溅:溶剂排放理论和合并理论丝印期间的清洁再次认为有影响,但可控制.溶剂排放理论:认为锡膏助焊剂中使用的溶剂必须在回流时蒸发.如果使用过高温度,溶剂会“闪沸”成气体类似于在热锅上滴水,把固体带到空中,随机散落到板上,成为助焊剂飞溅.为了证实或反驳这个理论,使用热板对样板进行导热性试验,并作测试.使用的温度设定点分别为190° C,200° C和220°C.膏状的助焊剂不含焊锡粉末在任何情况下都不出现飞溅.可是,锡膏含有粉末的助焊剂在焊锡熔化和焊接期间始终都有飞溅.表一和表二是结果.表一、溶剂排气模拟试验表二、从金属焊接中的助焊剂飞溅模拟试验可以推断,如果助焊剂沸腾引起飞溅,那么当助焊剂单独加热时应该看到.可是,由于飞溅是在焊锡结合时观察到的,这里应该可找到其作用原理.测试说明溶剂排气理论不能解释助焊剂飞溅.结合理论:当焊锡熔化和结合时熔化材料的表面张力―一个很大的力量―在被夹住的助焊剂上施加压力,当足够大时,猛烈地排出.这一理论得到了对BGA 装配内焊锡空洞的研究的支持,其中描述了表面张力和助焊剂排气之间的联系助焊剂排气率模型.因此,有力的喷出是助焊剂飞溅最可能的原因.接下来的实验室助焊剂飞溅模拟说明了结合的影响,甚至当锡膏在回流前已烘干.尽管如此,完全的烘干大大地减少了飞溅表三.表三、来自金属结合的助焊剂飞溅模拟―烘干研究150oC 观察到飞溅1-2飞溅无飞溅无飞溅160oC 1-2飞溅无飞溅无飞溅无飞溅170oC 无飞溅无飞溅无飞溅无飞溅用锡膏B 90% Sn63/Pb37 合金作试验熔湿速度因为结合模型看来会成功,所以调查了各种材料的熔湿速度.熔湿速度受合金类型、温度、助焊剂载体和回流环境的影响.如图一所说明,温度对熔湿速度有戏剧性的影响,温度越高,速度越快.图一、一种焊锡配方在不同温度测试的熔湿速度,影响因素包括合金类型、温度、助焊剂载体和回流环境.李宁成博士在其论文,“通过缺陷机制分析优化回流曲线”中说,惰性气体氮也会增加熔湿速度.SMT专栏作家珍尼.黄博士和其它人的报告说,共晶合金的熔湿速度倾向于比非共晶材料快.因此,Sn63/Pb37一般比Sn62/Pb36/Ag2熔湿速度更快.影响熔湿、从而影响结合和潜在飞溅的因素如表四所示. 表四、可能引起溅锡的因素溅锡的解决方案预防:防止溅锡沉积的一个方法就是在金手指上涂敷一层可驳除的阻焊层,在丝印锡膏后涂敷,回流后拿掉.这个方法还没有印证,可能成本高,因为牵涉手工作业,涂敷板上选择性区域会造成困难,中断生产流水作业.另外可选择在金手指上贴临时胶带.这个方法也有同样的缺点.最小化:优化助焊剂载体的化学成份,和回流温度曲线,将溅锡减到最低.为了证明这一点,得到内存模块制造商的支持,通过评估对材料和回流温度曲线优化的影响,来评价表准锡膏系统.清楚地表明活性剂、溶剂、合金和回流温度曲线对溅锡程度有重要影响.因此,有信心着手解决问题,这些参数的适当调整可以将溅锡减到最小.非标准材料,如聚合助焊剂系统由于成本高、货架寿命丝印寿命短、工艺变化范围小、并返工困难,不包括在本研究范围.但是,聚合助焊剂有希望最终提供一个可能最小化的溅锡解决方案,因为潜在的飞溅材料在温度激化的聚合过程中被包围.因此,没有液体助焊剂留下来产生飞溅.测试样板是一块六个小板的内存模块,没有贴装元件.已发现元件回减小溅锡的影响,因为元件会阻隔助焊剂从金手指上排出.现有生产材料和温度曲线作基本的试验条件表五.生产电路板的飞溅水平大约每100块组合板有一个飞溅锡球.两个工程师通过20倍的显微镜观察所有的板,以评估溅锡程度.表五、测试材料残留慢高推荐惰性中助焊剂E 低残留,高溶剂含量,空气或氮气回流慢高惰性中助焊剂F 极低残留,惰性回流助焊剂A: Kester244, B: 92, C: 92J, D:51SC, E: 73D, F:75 在线研究中使用不同特性的表准锡膏.根据其不同的湿润速度和溶剂性能来选择这些材料.为减少研究中的变量参数,所有锡膏使用同一种合金:Sn63/Pb37,粒度-325/+500目.最小化试验结果回流温度曲线的选择:试验期间得到明确,回流曲线和材料类型两者都必须调整以使飞溅最小.测试使用的两条主要的回流曲线不同在于其保温区的特性.没有平坦保温区的线性上升温度曲线图二结果是所有材料都存在一些溅锡,在原来的生产材料上增加了溅锡.因此,这个曲线形状没有作继续研究.基于飞溅机制的假设,这个线性的曲线没有充分烘干助焊剂.一个更有前途的基本曲线形状包括一个160oC的高温保温烘干,以蒸发所有溶剂图三.这种溶剂失散增加助焊剂剩余的粘性,减少挥发成份,因此减少飞溅.可是,这样烘干的潜在问题包括熔湿变差和产生空洞.使用惰性气体氮气可以帮助改善熔湿和减少空洞,但对飞溅却无效果.这个曲线也是一个“长”曲线,消除了过快温升率的需要最高每秒175oC.图二、线性温升曲线,没有保温平台区,对任何焊锡和助焊剂材料都造成一些溅锡图三、有一个高温保温区的温度曲线,溶剂的消失提高余下的助焊剂粘性,因此减少溅锡所有温度曲线研究的结果在图四和表六中总结.光板上测得的飞溅程度,在已贴装元件的生产板上大大减少.估计表明,光板上少于10-20个飞溅锡球,将在贴装元件板上不产生飞溅.因此,助焊剂类型D,E和F表五都提供了可行的溅锡解决方案.D型助焊剂载体有其它有点,工艺范围大和可以空气回流.三种材料的特点都是熔湿速度慢,但溶剂种类不同,这显示所有溶剂都可以有效烘干,熔湿速度才是助焊剂飞溅的关键因素.。
回流焊曲线图

使用范围设备名称版本/版次:A/01页码5.3.1测出炉温曲线后,确认各温区的关键参数是否符合按本文件6.0相关标准。
如有必要再进行调整。
排小批量(10PCS板左右)试过炉。
2.2 恒温区:使产品在进入较高温度区域前达到热平衡,同时对锡膏中没有用的化学成 5.5 炉温曲线的再调整份进行进一步地挥发处理。
该工序如设置不当可能造成 ‘热坍塌’、‘连锡’ 在产品试过炉过程中,如发现过炉结果存在质量问题,需马上对炉温曲线进行调整,直到 ‘高残留物’、‘焊球’、‘润湿不良’、‘气孔’、‘立碑’等等不良现象。
满意为止。
最后需对炉温曲线进行再一次测试.5.6 批量过炉技术员全程跟进以上各过程,全部OK后,即可通知生产车间安排批量过炉.5.7 炉温曲线管控一般情况下,以电子挡的形式按客户要求保存在机器电脑中。
5.8 炉温曲线测试频率5.8.1刚转线的所有产品均需对炉温进行实测。
5.8.2正在生产的产品,每天至少安排测试一次炉温,这种情况统一 由白班进行测试. 5.8.3每次调整炉温设置参数时,均需对炉温进行重新测试;每次批量生产使用的炉温曲线如和以前不同均需在电脑中对炉温曲线进行存档。
6.0炉温曲线格式为使炉温曲线更好地发挥作用,炉温曲线的制作需使用统一的格式(见附件一)。
7.0 标准设置温度5.1.1根据PCB厚度、大小及元器件热容量大小、数量等调取已经生产过的相似产品炉温设置参数,并结合生产产品的实际情况进行适当调整。
5.2.1 制作测温板:选择结构有代表性的几个产品制作测温板,一般性的产品均可用此测温板进行测试炉温。
测温板上主要的A级物料及屏蔽盖必须有。
的温度参数和实测温度之间相差应在在±2℃以内.否则,需进行调查处理。
制定: 日期: 审核: 日期: 批准: 日期:4.0 职责:SMT技术员负责确定和调整炉温曲线并作记录。
5.0 作业内容5.1 设置炉温曲线5.2 测量炉温5.2.2 测试炉温:待炉温达到预定的设置值后即可安排对炉温进行测试。
回焊炉温度调整规范

<1.5℃/S
28~150℃
90~120 S
2均温区
<=1℃/S
120~170℃
60~120 S
3回焊区-1
<=1℃/S
183℃>=
60~120 S
4回焊区-2
<=1℃/S
200℃>=
20~60 S
5冷却区
<=4℃/S
<=183℃
6最高温度:BGA TOP219~223℃
基材220~225℃
6注意事项:
6-1避免在预烤区的升温速度过激,容易使锡膏的流动性恶化。
6-2避免均温不足,容易引起较大锡球发生的可能;反之,则有引发微细锡球与较大锡球密集发生的可能。
6-3避免均温过低,在回焊炉后有焊锡未熔化的情形发生。
6-4避免熔锡区温度上升过激,容易使锡膏的流动性恶化。
6-5最高温度不应过高,避免锡膏老化。
b.人员:生产工程师、技术员均可.
4-3回焊炉Profile正确与否由当日量测Profile工程师确认。
4-4档案命名方式:
a.存档名称:以年月日+线别+机种名称+正背板(TOP/BOT)+ GP(nGP、有铅
不用标示)命名.
b.过程檔:以线别+机种名称+正背板+GP(nGP、有铅不用标示)命名.
c.烘炉檔:以线别命名.
2均温区
<=1℃/S
120~170℃
60~120 S
3回焊区-1
<=1℃/S
183℃>=
90~120 S
4回焊区-2
<=1℃/S
217℃>=
40~60 S
5冷却区
<=4℃/S
<=183℃
- 1、下载文档前请自行甄别文档内容的完整性,平台不提供额外的编辑、内容补充、找答案等附加服务。
- 2、"仅部分预览"的文档,不可在线预览部分如存在完整性等问题,可反馈申请退款(可完整预览的文档不适用该条件!)。
- 3、如文档侵犯您的权益,请联系客服反馈,我们会尽快为您处理(人工客服工作时间:9:00-18:30)。
4.1测温点之选择:
4.1.1BGAType测温点选择如下:
4.1.1.1当BGABody≧27mm时,需点选3点作为测试点,且此3点测试点皆需为
温度同时到达点之处。
4.1.1.2当BGABody≦27mm时,点选中心点作为测试点
4.1.2QFPType
4.1.3ChipssetType
4.1.4connectorType
E.降温斜率: <3℃/sec
F.最高温度时间:最高温度230℃~250℃以内时间: 30~70Sec
4 .3.5厂商特别要求之Profile制程参数规格,超出正常管制界线,需做可靠度验证方可
特别更改Profile制程参数.
4.4标准曲线图
无铅炉温标准曲线:
温度(℃)
250Peak 230~250℃
4.5.3当超出检验规范应立即通知ME工程师处理.
4.5.4制程参数如需修改,必须由技术员或工程师确认.
4.6注意事项:
4.6.1测温线不要用力拉扯.
4.6.2确认测温器仍在校验有效期内.
4.6.3KIC测温器电压低于7V时,应该更换电池.
4.6.4打印Profile前不可将测温器Power off
4.2.1.3检查测温器电量是否充足。
4.2.1.4检查测温板上测试点接线是否良好。
4.2.1.5 Reflow温度达到MPI设定时才可进行量测。
4.2.1.6将测温器上启动按钮拉出Stop﹐再Power on
4.2.1.7将测试板上的测温线插头和测温器上插孔相对应好.
4.2.1.8将测试板和测温器平放在轨道上,按下测温器按钮至Start位置.
A.升温斜率(25℃~130℃):<2.5℃/sec. (183℃~235℃):<2.5℃/sec
B.浸泡时间(150℃~183℃):80sec~145sec.
C.回流时间(over183℃):60sec~100sec. (over200℃):30~60sec
D.最高温度
焊点最高温度:>210℃
BGA零件温度:<220℃
4.6.5测温器出炉膛时温度高,需要配戴手套作业,以免烫伤
4.6.6测温器需冷却至室温才可再次测温.
五.应用表单:
5.1.Profile
D.最高温度
焊点最高温度:>210℃
BGA零件温度:<220℃
其它零件温度:<235℃
E.冷却斜率:BGA上表面球要大于1.0℃/sec
4.3.3无铅Sn3.0Ag0.5Cu制程检验标准
检查项目
A.升温斜率(25-150℃):<3.0℃/Sec (200-250℃): <1.5℃/Sec
B.浸泡时间: (155℃-190℃): 60-120Sec
125℃-150℃
Peak-130℃
<4℃/S
60-160 sec
<4℃/S
4.5量测时间及管制
4.5.1每班开线前和换线时须量测Profile并于每班10:00前将测好之炉温挂于产线相应位置,回流炉故障须重新测试炉温,未测炉温,不准开线。
4.5.2SMT人员检查各项参数是否符合检验规范,并填写回流炉温度记录表IPQC人员每日检查并在回流炉温度记录表上签名(参考标准曲线图)
230
217升温速度3℃/S以下冷却速度<3℃/S
217℃以上60-120sec
190
155
升温速度
<3℃/S
155~190℃: 60 ~ 120sec
Rising slope
Time between
Reflow time
Reflow time
Peak temperature
Falling slope
C.回流时间: (over217℃):60-120Sec
D.最高温度:焊点温度>230℃
(Peak Temperature参照下图,BGA类最高温度Target:240℃)
E.降温斜率: <3℃/sec
F.最高温度时间:最高温度5℃以内时间: 20~40Sec
4.3.4无铅Sn0.3Ag0.7Cu制程检验标准
4.2.2.8将测温板和测温器平放在轨道上,打开测温器开关至ON位置。
4.2.2.9将测温板和测温器通过炉膛后,将测温器内之数据通过数据线导出,确认合格,然后将曲线图打印出来。
4.2.2.10将测温器的开关至OFF位置,把测温器与数据线分开。
4.3检验标准:
4.3.1锡铅63/37制程检验标准
检查项目:
b. NEC无铅SnZnBi参照<<Regulation of reliability evaluation for lead free soldering process>>规范
c. HP EL-MF866-00<< Baseline Requirements for PCA Suppliers Pb-free Assembly and Rework Processes>>
修订履历记录
版本
文件编号
制/修内容简述
生效日期
制/修订部门
制/修订人
一.目的:
规范正确的量测方法,确保Reflow的各项工作温度正常,防止不良品产生.
二.范围:
广西三诺数字PCBA部
三.应用文件:
a.参考IPC/JEDEC J-STD-020C
<<Moisture/Reflow Sensitivity Classification for Non-hermetic Solid State Surface Mount Devices>>
其它零件温度:<235℃
E.降温斜率: <3℃/sec
4.3.2无铅(SnZnBi)制程检验标准
检查项目:
A.升温斜率(170℃~peak):<2.5℃/sec.
B.浸泡时间(150℃~170℃):60sec~100sec.
C.回流时间(over200℃):30sec~60sec. (over210℃):0sec~30sec
25℃-150℃
155℃-190℃
Above217℃
Above 230℃
230℃-250℃
Peak-217℃
<3℃/S
60-120sec
60-120sec
30-70 sec
<3℃/S
红胶炉温标准曲线
FUJI NE8800K,NE300S红胶炉温曲线
设定一:
Rising slope
Reflow time
4.2测试步骤:
4.2.1MALCOM测温系统:
4.2.1.1测温板与测温线之焊接材料为:测温线型号使用OMEGA-TT-K-30和MEGA-TT-K-36。BGA Type可使点胶方式固定,其余零件(如:QFP,CHIPS,CONNECTOR)之焊接点皆限定使用熔点为270℃的高温锡丝。
4.2.1.2确认程序与MPI相符后Run程序。
检查项目
A.升温斜率(Leabharlann 5-150℃):<4.0℃/Sec (200-250℃): <2.0℃/Sec
B.浸泡时间: (155℃-190℃): 60-120Sec
C.回流时间: (over217℃):60-120Sec
D.最高温度:焊点温度>230℃
(Peak Temperature参照下图,BGA类最高温度Target:240℃)
4.2.2.2确认程序与MPI相符后Run程序。
4.2.2.3检查KIC2000测温系统所选程序与MPI相符
4.2.2.4将测试板上的测温线插头和测温器上插孔相对应好。确认连接良好。
4.2.2.5打开测温器开关,确认电池容量>7V,测温器内部温度<50℃。
4.2.2.6至测温画面后,关闭测温器。
4.2.2.7Reflow温度达到MPI设定时才可进行量测
4.2.1.9将测试板和测温器通过炉膛后,将测温器的按钮拔至Stop位置,冷却测温器。
4.2.1.10将测温器取下,到Reflow checker中打印profile,并填写纪录.
4.2.2KIC2000测温系统:
4.2.2.1测温板与测温线之焊接材料为:测温线型号使用OMEGA-TT-K-30和EGA-TT-K-36。BGA Type可使点胶方式固定,其余零件(如:QFP,CHIPS,CONNECTOR)之焊接点皆限定使用熔点为270℃的高温锡丝。
Peak temperature
Falling slope
25℃-125℃
Above 150℃
140℃-160℃
Peak-130℃
<4℃/S
60-120 sec
<4℃/S
设定二:
Rising slope
Reflow time
Peak temperature
Falling slope
25℃-125℃
Above125℃