精馏塔回流比控制
回流比

回流比回流比实质上就是增加气液分离的次数,增强分离效果而以,是提纯工序中增加产品纯度最有效的方法回流比越大,分离效果越好,产品质量越高,生产能力就越小,能耗越高。
回流比:精馏段内液体回流量与采出量之比,通常用R来表示。
R=L/DR:回流比L:单位时间内从精馏段内某一塔板下降的液体,单位:Kmol/h。
D:单位时间内从精馏塔顶采出的馏出液(产品),单位:Kmol/h。
回流比越大,分离效果越好,产品质量越高,生产能力就越小,能耗越高对某一种需要分离的介质,根据其物料和选用塔型特性,有一个回流比下限,即叫做最小回流比。
在规定的要求下,最小回流比时所需要的理论塔板数将无限大。
对固定分离要求过程,最适宜的回流比确定依据为:回流比减少,生产操作费用减少,但所需的塔板数增加,投资费用增加,反之,增加回流比,减少塔板数,却增加运行费用。
最适宜的回流比是以投资费用和经常运行费用之和在特定的经济条件下为最小。
通常实际生产操作中回流比取最小回流比的1.3—2倍回流:通过整个精馏过程,最终由塔顶得到高纯度,易挥发的组分,由塔顶馏出,塔釜得到基本是难挥发的组分。
精馏六区别于一次蒸馏在于回流,包括塔顶的液相回流及塔底的部分气化造成的液相回流。
回流是构成气液相接触传质传热的必要条件。
没有气液两相的接触也就无从进行质的交换。
当然组分挥发度的差异仍然是精馏过程的基础。
精馏过程中混和液加热所产生的蒸汽由塔顶馏出,进入塔顶分离器,冷凝成液体将其一部分冷凝液返回塔顶,沿塔板下流,这部分液体称为回流液。
将一部分冷凝从塔顶采出作为产品,回流比就是精馏段内液体回流与采出液量之比。
回流比大,分离效果好,产品质量高,回流比过大,生产能力下降,能耗增加,回流比对精馏操作影响很大,直接关系到塔内各层塔板上的物料浓度的改变和温度的分布,最终反映在它的分离效率上。
回流比的调节:主精馏塔的回流比为:2.0-2.5调节的依据是:根据塔的负荷和精甲醇质量,当塔的负荷较轻时,这时塔板比较富余,可以取较低的回流比,比较经济,为了保证精甲醇的质量,精馏段灵敏板的温度可控制略低,反之,则增大回流比,在照顾精甲醇的质量的同时,为保持塔釜温度、灵敏板的温度可控制略高。
精馏塔的控制要求

精馏塔的控制要求2.1 质量指标混合物分离的纯度是精馏塔控制的主要指标。
在精馏塔的正常操作中,产品质量指标就必须符合预定的要求,即保证在塔底或塔顶产品中至少有一种组分的纯度达到规定的要求,其他组分也应保持在规定的范围内,因此,应当取塔底或塔顶产品的纯度作为被控变量。
但是,在线实时监测产品纯度有一定的困难,因此,大多数情况下是用精馏塔内的“温度和压力”来间接反应产品纯度。
对于二元精馏塔,当塔压恒定时,温度与成分之间有一一对应的关系,因此,常用温度作为被控变量。
对于多元精馏塔,由于石油化工过程中精馏产品大多数是碳氢化合物的同系物,在一定的塔压下,温度与成分之间仍有较好的对应关系,误差较小。
因此,绝大多数精馏塔当塔压恒定时采用温度作为间接质量指标。
2.2 平稳操作为了保证精馏塔的平稳操作,首先必须尽可能克服进塔之前的主要可控扰动,同时缓和一些不可控的主要扰动,例如,对塔进料温度进行控制、进料量的均匀控制、加热剂和冷却剂的压力控制等。
此外,塔的进出物料必须维持平衡,即塔顶馏出物与塔底采出物之和应等于进料量,并且两个采出量的变化要缓慢,以保证塔的平稳操作。
另外,控制塔内的压力稳定,也是塔平衡操作的必要条件之一。
2.3 约束条件为了保证塔的正常、平稳操作,必须规定某些变量的约束条件。
例如,对塔内气体流速的限制,塔内气体流速过高易产生液泛,流速过低会降低塔板效率;再沸器的加热温差不能超过临界值的限制等。
3精馏塔的温度控制精馏塔控制最直接的质量指标是产品的组分,但产品组分分析周期长,滞后严重,因而温度参数成了最常用的控制指标,即通过灵敏板进行控制[3]。
3.1 精馏段温度控制精馏段温控灵敏板取在精馏段的某层塔板处,称为精馏段温控。
适用于对塔顶产品质量要求高或是气相进料的场合。
调节手段是根据灵敏板温度,适当调节回流比。
例如,灵敏板温度升高时,则反映塔顶产品组成XD下降,故此时发出信号适当增大回流比,使XD上升至合格值时,灵敏板温度降至规定值。
回流比

[习题] 在连续精馏塔中分离二甲苯混合液。原料液中 乙苯的摩尔分数为0.40,要求馏出液中含乙苯99.0%, 釜残液乙苯含量不超过1%。料液在饱和液体下加入塔 中,操作回流比R = 75,乙苯与对二甲苯的平均相对挥 发度α = 1.06。 (1)试估算所需的理论塔板数。 (2)若为了降低能耗,将回流比降至50,所需理论塔 板数为多少。
在1940年吉利兰关联提出后,不少研究者提 出了各种关联,希望提高估算精度,但效果不明 显,吉利兰关联至今仍到得广泛应用。 用吉利兰关联估算理论板数,包括如下三步: ①首先用芬斯克方程计算最少理论板数; ②计算给定条件下的最小回流比; ③应用吉利兰经验关联式估算所需理论板数。
[例] 在连续精馏塔中分离苯、甲苯混合液。原料液的流 量为5000kg/h,其中苯的摩尔分数为0.45,要求馏出液中 含苯98.0%,釜残液中含甲苯 95%。料液在饱和液体下加 入塔中,操作回流比R=2.5,苯与甲苯的平均相对挥发度 α = 2.41。试估算所需的理论塔板数。 解:(1) 计算Nmin
相对挥发度
AB
PA PB
相对挥发度的估算:
lg AB Tb A Tb B 9.177 (Tb ) A (Tb ) B
(3)理论塔板的简捷计算法
将许多不同精馏塔的回流比、最小回流比、 理论板数及最小理论板数即R、Rmin、N、Nmin四 个参数进行定量的关联。常见的这种关联如图所 示,称为吉利兰图(Gillilad)图。 吉利兰关联是根据61个双组分和多组分精馏 塔的逐板计算结果理得到。可近似表示为下式:
另外,加料量的变化直接影响蒸汽速度的改变。后 者的增大,会产生夹带、甚至液泛。 当然,在允许负荷
的范围内,提高加料量,对提高产量是有益的。如果超 出了允许负荷,只有提高操作压力,才可维持生产。但 也有一定的局限性。 加料量过低,塔的平衡操作不好维持,特别是浮阀 塔、筛板塔、斜孔塔等,由于负荷减低,蒸汽速度减小, 塔板容易漏液,精馏效率降低。在低负荷操作时,可适 当的增大回流比,使塔在负荷下限之上操作,以维持塔 的操作正常稳定。
甲醇水精馏塔设计回流比确定
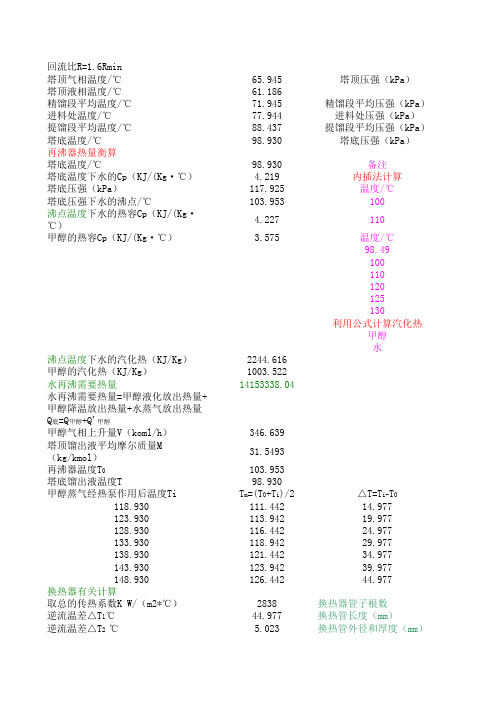
温差对数平均值 ℃
换热面积A m2 换热器2利用热蒸汽提供水再沸需要剩 余热量
取总的传热系数K W/(m2*℃)
逆流温差△T1℃ 逆流温差△T2 ℃
温差对数平均值 ℃
换热面积A m2 减压阀 热量衡算 塔顶液相温度/℃ 塔顶温度下甲醇Cp KJ/(Kg·℃) 塔顶温度下甲醇汽化热(KJ/Kg) 水的汽化热(KJ/Kg) 甲醇流出再沸器温度/℃ 甲醇降温放出热量Q(KJ/h)=部分甲 醇气化吸收热量Q'(KJ/h) 气化部分甲醇的质量流量(Kg/h) 在管程中使这部分气体液化,冷却水 进出冷凝器的温度分别是20℃、50℃ 冷却水进入冷凝器温度℃
沸点温度下水的汽化热(KJ/Kg) 甲醇的汽化热(KJ/Kg) 水再沸需要热量 水再沸需要热量=甲醇液化放出热量+ 甲醇降温放出热量+水蒸气放出热量 Q底=Q甲醇+Q'甲醇 甲醇气相上升量V(koml/h) 塔顶馏出液平均摩尔质量M (kg/kmol) 再沸器温度T0 塔底馏出液温度T 甲醇蒸气经热泵作用后温度Ti
换热器有关计算
取总的传热系数K W/(m2*℃) 逆流温差△T1℃ 逆流温差△T2 ℃ 温差对数平均值 ℃
换热面积A m2
塔顶换热器热量衡算 水蒸气放出热量Q=塔顶料液吸收热量 Q'
热蒸气进入换热器的温度T1 ℃
流出换热器的温度T2℃ 温差△T℃ 平均温度Tm℃ 水蒸气在Tm下的热容Cp KJ/(Kg·℃)
0.50 0.0622
68
泡点温度下甲醇密度ρ (kg/m3)
735.8499806
厚度∮(mm) 平衡方程 PV=nRT
其中R为 8.314
精馏塔操作中常见的几大问题与控制办法
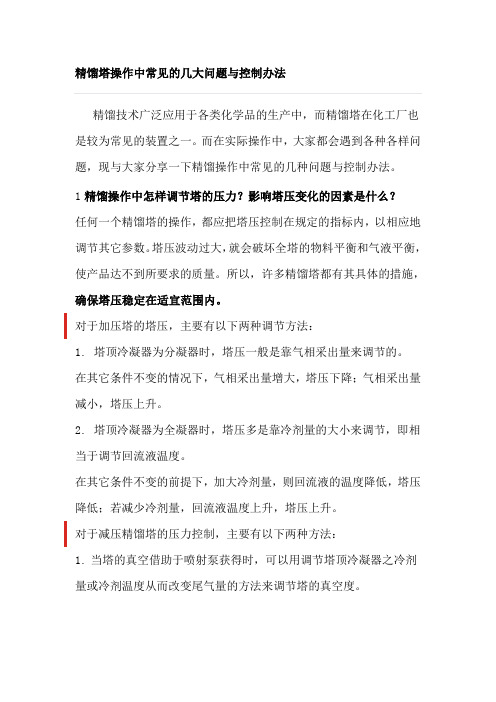
精馏塔操作中常见的几大问题与控制办法精馏技术广泛应用于各类化学品的生产中,而精馏塔在化工厂也是较为常见的装置之一。
而在实际操作中,大家都会遇到各种各样问题,现与大家分享一下精馏操作中常见的几种问题与控制办法。
1精馏操作中怎样调节塔的压力?影响塔压变化的因素是什么?任何一个精馏塔的操作,都应把塔压控制在规定的指标内,以相应地调节其它参数。
塔压波动过大,就会破坏全塔的物料平衡和气液平衡,使产品达不到所要求的质量。
所以,许多精馏塔都有其具体的措施,确保塔压稳定在适宜范围内。
对于加压塔的塔压,主要有以下两种调节方法:1. 塔顶冷凝器为分凝器时,塔压一般是靠气相采出量来调节的。
在其它条件不变的情况下,气相采出量增大,塔压下降;气相采出量减小,塔压上升。
2. 塔顶冷凝器为全凝器时,塔压多是靠冷剂量的大小来调节,即相当于调节回流液温度。
在其它条件不变的前提下,加大冷剂量,则回流液的温度降低,塔压降低;若减少冷剂量,回流液温度上升,塔压上升。
对于减压精馏塔的压力控制,主要有以下两种方法:1. 当塔的真空借助于喷射泵获得时,可以用调节塔顶冷凝器之冷剂量或冷剂温度从而改变尾气量的方法来调节塔的真空度。
当被分离的物料允许与空气接触时,在此控制方案中,蒸汽喷射泵在最大的能力下工作,调节阀装在通大气的管线上,用调节阀开度的大小,调节系统的尾气抽气量,从而达到调节塔的真空度的目的。
2. 当采用电动真空泵抽真空时,调节阀装在真空泵的回流管线上,用调节阀开度的大小来调节系统的尾气抽出量,从而调节塔的真空度。
对于常压塔的压力控制,主要有以下三种方法:1. 对塔顶压力在稳定性要求不高的情况下,无需安装压力控制系统,应当在精馏设备(冷凝器或回流罐)上设置一个通大气的管道,以保证塔内压力接近于大气压。
2. 对塔顶压力的稳定性要求较高或被分离的物料不能和空气接触时,塔顶压力的控制可采用加压塔塔压的控制方法。
3. 用调节塔釜加热蒸汽量的方法来调节塔釜的气相压力。
实验十二、精馏塔部分回流操作及塔效率的测定实验

yn1
x R xn D R 1 R 1
式中, yn 1 -精馏段第 n+1 块塔板上升的蒸汽组成,摩尔分数;
xn -精馏段第 n 块塔板下流的液体组成,摩尔分数; xD -塔顶溜出液的液体组成,摩尔分数;
R -泡点回流下的回流比。
提馏段的操作线方程为:
ym1
Wx L' xm ' W ' L W L W
c pF (tS tF ) rF
其中, 式中, q -进料热状况参数;
q 1
rF -进料液组成下的汽化潜热,kJ/kmol; t S -进料液的泡点温度,℃; t F -进料液温度,℃;
c pF -进料液在平均温度 (tS tF ) /2 下的比热容,kJ/(kmol℃) ;
xF -进料液组成,摩尔分数。
图 2 塔顶回流示意图 对第一块板作物料、热量衡算:
V1 L1 V2 L V1IV 1 L1I L1 V2 IV 2 LI L
对上面两式整理、化简后,近似可得:
L1 L[1
即实际回流比:
c p (t1L t R ) r
]
R1
L1 D
L[1
c p (t1L t R ) r D
rm 1.9867 103 x2 13.8799 x 2.2525 103
式中: rm ——汽化潜热[kJ/kg]
x ——乙醇的质量百分数
乙醇---水溶液的比热计算公式
c pm 4.229 1.3377t log( x) 2.307 x 1.2773t 102
五.数据记录及处理
1. 数据记录 实际塔板数: 进料温度: 塔釜温度:
不同回流比对精馏分离效果的影响

17
参考文献
1.1 理论塔板
若气、液两相在塔板上接触时间足够长,使得离开该塔板的气、液两相互呈 平衡,即������������ 与������������ 平衡, ,则称该塔板为理论板。实际上由于塔板上气液接触时间 有限,������������ 与������������ 难以达到平衡,即理论板是不存在的。理论板作为衡量塔板分离效 率的依据和标准[2]。
1、流量计 2、进料阀 3、进料泵 4、热交换器 5、塔板 6、原料罐 7、残液罐 8、产品罐 9、反应釜 3
2.1 全回流
配制浓度为 18.1%的乙醇水溶液原料液加入贮缺罐中, ,打开进料阀,由进 料泵将原料打入塔釜中,观察塔釜的液位高度,进料至容积的 2/3 处停止进料。 打开塔顶冷凝器的冷却水,调节为 140L/h,关闭进料阀,启动电加热管电源, 调节加热功率为 90%,并关闭塔顶出料管路,使整塔处于全回流状态。经过 2 小时后,塔顶回流量、温度、塔釜温度稳定后,开始进入部分回流状态。
引言
精馏是化工分离工程中最基本、最重要的单元操作之一。在精馏的操作中, 回流比(R)是关系着精馏产品质量的重要参数。每当塔顶馏出液浓度下降或需 要进一步提高塔顶馏出液浓度时, 通常都以增加回流比的操作方式使产品得以 提高。 间歇操作回流比得出产品浓度一般都是变化的。本文通过实验讨论连续操 作过程中不同回流比对精馏分离效果的影响。
14
反应条件:回流温度 27.1℃,进料温度 40.3℃,������������ =0.897,������������ =0.178。 塔板层数 1 2 3 4 5 6 7 8 9 R=1 74.8 75.3 75.3 75.8 76.1 76.5 76.5 79.3 84.3 全回流温度 部分回流温度 78.8 80.4 81.1 84.3 85.0 85.2 85.2 87.7 88.3
回流比的影响及其选择

对角线
yn 1 xn
xW
xD
GLL
最小回流比
对于一定的进料和分离要求: R,精馏段操作线截距增大,操作线向平衡线移动; 进料不变则 q 线不变。操作线交点 d 将向平衡线靠近。 R,提馏段操作线也向平衡线移动。 结论: R,达到指定分离程度所需理论板数将增多。
a g
yq
d
f
饱和液体进料:xq=xF
Rmin 1 x D (1 x D ) 1 xF 1 xF
其它进料热状态下,可由相平衡方程和 q 线方程联立 求解得到交点坐标: xq,yq
GLL
非理想物系的Rmin
一般情况下,xq与 yq 互成平衡(交点 g 在平衡线上)。 平衡线有凹凸时,随R,交点 d 未落到平衡线上之前,操 作线已与平衡线相切(g点)。此时恒浓区出现在 g 点附 近,对应的回流比为最小回流比。
GLL
全回流与最小理论板数
全回流时:R 精馏段操作线: yn1 D=0 W=0 F=0
yn 1 xn
R xD xn R1 R1 V V
提馏段操作线:yn1 L xn WxW 全回流操作只适用于精馏塔的开工、 调试及实验研究。 全回流时操作线和平衡线的距离最远, 达到相同的分离程度所需的理论板数 最少,以 Nmin 表示。计算方法见7.5.3
1.0 1.0 q d g a a
yq yd
q
yd
d
yq
g
0
xW
xd
xF
xq
xD
1.0
0 xW x q
xd
xF
xD 1.0
计算Rmin 时,式中xq 与 yq分别为 xd 与 yd 。 Rmin
- 1、下载文档前请自行甄别文档内容的完整性,平台不提供额外的编辑、内容补充、找答案等附加服务。
- 2、"仅部分预览"的文档,不可在线预览部分如存在完整性等问题,可反馈申请退款(可完整预览的文档不适用该条件!)。
- 3、如文档侵犯您的权益,请联系客服反馈,我们会尽快为您处理(人工客服工作时间:9:00-18:30)。
精馏塔回流比控制
精馏塔回流比控制是精馏塔操作中的关键参数之一。
精馏塔回流比是指在精馏塔中返回到塔顶的液相流量与原料进料流量的比值。
精馏塔回流比的控制对于分离效果的优化和产品纯度的提高至关重要。
精馏塔回流比的控制可以通过调节精馏塔中的回流量来实现。
通常,精馏塔的回流量是通过调节顶塔下液位的高度来控制的。
如果回流量比较大,那么回流液将占据较大的塔容积,使得分馏效果较好,但同时也会增加能耗和成本。
精馏塔回流比的控制可以根据需要进行调整。
一般来说,增加回流比可以提高产品的纯度,但也会增加能耗和成本。
相反,减少回流比可以降低能耗和成本,但可能会影响产品的纯度。
精馏塔回流比的控制可以通过反馈控制系统来实现。
控制系统可以根据塔顶压力、温度、液位和组分浓度等参数进行调整,以实现回流比的控制。
此外,还可以根据产品规格要求和经济因素进行优化调整。
总而言之,精馏塔回流比的控制对于精馏塔的操作和产品纯度的提高具有重要作用。
通过合理的回流比控制,可以实现分离效果的优化和产品成本的降低。