立式加工中心主轴部件设计说明
立式加工中心说明书

目录1 概述 (3)1.1 零件技术要求 (3)1.2 总体方案设计 (3)2 设计计算 (3)2.1主切削力及其切削分力计算 (3)2.2 导轨摩擦力计算 (4)2.3 计算滚珠丝杠螺母副的轴向负载力 (4)2.4 滚珠丝杠的动载荷计算与直径估算 (4)3 工作台部件的装配图设计 (9)4 滚珠丝杠螺母副的承载能力校验 (9)4.1 滚珠丝杠螺母副临界转速压缩载荷的校验 (9)4.2 滚珠丝杠螺母副临界转速n的校验 (10)c4.3滚珠丝杠螺母副额定寿命的校验 (10)5 计算机械传动系统的刚度 (10)5.1 机械传动系统的刚度计算 (10)5.2 滚珠丝杠螺母副的扭转刚度计算 (12)6 驱动电动机的选型与计算 (12)6.1 计算折算到电动机轴上的负载惯量 (12)6.2 计算折算到电动机上的负载力矩 (13)6.3 计算坐标轴折算到电动机轴上的各种所需的力矩 (13)6.4选择驱动电动机的型号 (14)7 机械传动系统的动态分析 (15)7.1 计算丝杠-工作台纵向振动系统的最低固有频率 (15)7.2 计算扭转振动系统的最低固有频率 (15)8 机械传动系统的误差计算与分析 (16)8.1 计算机械传动系统的反向死区 (16)8.2 计算机械传动系统由综合拉压刚度变化引起的定位误差 (16)8.3 计算滚珠丝杠因扭转变形产生的误差 (16)9 确定滚珠丝杠螺母副的精度等级和规格型号 (16)9.1 确定滚珠丝杠螺母副的精度等级 (17)9.2 确定滚珠丝杠螺母副的规格型号 (17)课程设计总结 (18)参考文献 (19)1. 概述1.1 零件技术要求工作台、工件和夹具的总质量m=833kg,其中,工作台的最大行程Lp=650mm;工作台快速移动速度15000mm/min;工作台采用贴塑导轨,导轨的动、静摩擦系数为0.15 ,0.2,工作台的定位精度为0.04mm,重复定位精度为0.02mm;机床的工作寿命为20000h(即工作时间为10年)。
立式加工中心主轴设计论证报告

机电工程学院毕业设计方案论证报告设计题目: VMC4032加工中心立柱主轴设计学生姓名:王毅可学号: 200848050315专业班级:机制F0802指导教师:朱红瑜2012 年03月14日目次1、任务书分析 (1)2、课题关键问题及难点 (2)2.1 主传动系统组成 (2)2.2 主轴部件的要求 (3)2.3 支撑件设计 (4)2.4 导轨设计 (5)2.5 进给传动系设计 (5)3、方案论证 (6)3.1 主轴电动机 (6)3.2 传动方案 (6)3.3 自动夹紧 (9)3.4 主轴准停装置 (10)3.5 切屑清除 (11)3.6 加工中心的支撑系统设计 (12)3.7、进给传动系设计 (14)4、本设计方案选择 (16)5、进度安排 (17)参考文献 (18)VMC4032加工中心立柱主轴设计论证报告1、任务书分析本设计任务书主要要求是完成V400性柔性制造单元主轴主轴箱部分方案选择,结构设计及零件设计,同时对于主轴支撑系统如立柱,Z方向进给系统如导给定的条件和要求,主要参数要求如下:主轴伺服电机功率7.5/11KW,主轴转速0~6000r/min,自动无级变速,主轴内锥孔采用BT40#,具有定向停止功能,立柱、主轴箱具有较好的刚度,与床身联接尺寸协调。
通过这次毕业设计对于机械的设计方案有一定的了解对于已经学习的课程做一个总结,学会整合所学习的知识,能够灵活运用。
同时使自己检索文献的能力也有所提高,培养自己的自学能力独立解决问题的能力。
对于三维软件的练习也是本次设计中所应当注意到的方面。
2、课题关键问题及难点主轴组件是加工中心的关键部件,包括主轴,主轴轴承及安装在主轴上的传动件,密封件等。
对于加工中心,为了实现刀具在主轴上的自动装卸与夹持,还必须具有刀具自动加紧装置,主轴定向装置和主轴锥孔清理装置等结构。
对于加工中心的进给系统及加工中心的丝杠导轨系统的精度设计,立式主轴的准停机构。
立柱的刚度等都要做详细的论证。
主轴组件

加工中心主轴组件分析报告一、主轴组件概述1.主轴组件定义加工中心主传动系统是由主轴电动机、主轴传动系统以及主轴组件组成,而主轴组件是加工中心的主传动部分的主要组成部分,在机床上,主轴主要作用是夹持工件或刀具旋转,提供足够的驱动功率或输出转矩,能在整个速度范围内提供切削所需功率和转矩,以满足机床强力切削时的要求,直接参加表面成形运动。
(应附图)主轴被比喻为“机床的心脏”,这是再恰当不过了,人们期望它输出更高的转速、更大的扭矩、更强劲的功率、更小的主轴跳动、更低的磨损率、更少的故障及更低的价格。
目前国内机床主轴的水平还未满足用户的要求。
2.国内外主轴现状比较在国外,主轴单元的设计大多是可以公开的,一些大轴承公司甚至公开出版书籍,教人们如何设计适合的主轴单元具体到使用什么轴承、轴承的精度等级、相应的配合公差、形位公差、主轴单元可以达到的精度、润滑方式、润滑油、密封方法、动平衡精度等,有的公司还会介绍如何装配,应在什么环境下装配等。
设计可以公开,但加工工艺就很少见诸文献。
大多数公司对工艺都严守秘密,好多出国考察的人士就反映主轴单元零件的精加工场所,甚至装配场所几乎都不允许参观。
因此很难叙述目前国外的工艺水平,只能从一些间接的现象来评估。
例如有时我们采用相同的设计、相同的材料、用同一轴承公司的型号、精度等级相同的轴承,而做不出相同精度或相同速度的主轴单元来。
对铣削加工中心,主轴跳动在1um已经是国内用户购买高精度机床的一个标淮,这对于国外的机床来说,也已经是一个非常普通的参数,甚至于价位很低的机床,反观我们国内的情况,还没有哪个厂家明确地在产品样本上标明主轴跳动为lum,而实际的情况更糟糕,机床的主轴指标往往是5um。
情况为什么会是这样呢?原因主要的还是主轴的结构设计、加工工艺、热处理工艺、装配工艺的问题。
这个也是以后开发主轴的技术难点。
此处至少应就主轴类技术指标、材料及热处理的差距列表,差距比较是表现技术水平高低的重要形式,必须有数据,国外在主轴方面的发展方向是什么,必须在文中有回答(并提供一些参考资料作为支持)二主轴组件的分类、功能、性能要求以下以铣加工中心作为例子介绍(1)主轴组件的分类:皮带式主轴、直结式主轴、内藏式主轴(电主轴)(应附图)三类主轴使用环境:皮带式主轴广泛用于小型机床上,并能满足机床对转矩特性的要求;直结式主轴虽然简化了主轴结构,有效地提高了主轴刚度,但主轴输出转矩小,电动机发热对主轴精度影响大;内藏式主轴是集皮带式主轴和直结式主轴优点,具有高速度,高精度,以及良好的稳定性能等多项优点,广泛用于数控钻铣设备,精密雕刻、雕铣、木工机械、精密磨床及其他数控高速机械。
JCS-018立式加工中心主轴箱及进给系统设计

摘要:本次设计通过对现有加工中心的分析研究,提出一种新的设计方案,其自动化程度更高,结构也相对比较简单.这一点在论文会得以体现.本方案中,主轴箱采用交流调速电机实现无级变速,在X、Y、Z三个方向上的进给运动均采用滚珠丝杠,而动力则由步进电动机通过调隙齿轮来传递,并且采用单片机进行数字控制.控制系统采用MCS-51系列单片机,通过扩展程序存储器、数据存储器和I/O 接口实现硬件电路的设计.论文中也对软件系统的设计做出了相关说明.关键词:交流调速电机滚珠丝杠步进电机单片机系统扩展Abstract: This design tries a new method after the analyze and research of the exited machining center with the higher automatization degrees and the simpler configuration,which will be explained in the paper. In the method, AC adjustable-speed motor is used for the realization of the level shift in variable speed,and in the motion of, we all adopt ball bearing thread haulm for the X、Y、Z direction,The power of which is step by step electromotor transferred by gear that used for adjusting gaps.And more,we used singlechip for numerical control.The control system introduces MCS-51 series singlechip,and the realization of hardware circuit was accomplished by enlarging program memorizer、data memorizer and I/O meet meatus.Also,the paper explained the design for software system. Keywords: AC adjustable-speed motor、ball bearing thread haulm、the step by step electromotor、the enlarge for SCM system目录前言 (1)1、机床总体方案设计 (1)1.1 机床总体尺寸参数的选定 (1)1.2 机床主要部件及运动方式的选定 (2)1.3 机床总体布局的确定 (3)2、主传动的设计计算 (8)2.1 电机的选择 (8)2.2 齿轮传动的设计计算 (9)2.3 轴的设计计算 (13)2.4 离合器的选用 (21)3、进给系统的设计计算 (22)3.1 概述 (22)3.2 设计计算 (22)3.3 工作台部件的装配图设计 (29)3.4 滚珠丝杠螺母副的承载能力的校验 (30)3.5 计算机械传动系统的刚度 (31)3.6 驱动电动机的选型与计算 (33)3.7 机械传动系统的动态分析 (36)3.8 机械传动系统的误差计算与分析 (37)3.9 确定滚珠丝杠螺母副的精度等级和规格型号 (38)3.10 滚珠丝杆副的预紧方式 (38)3.11 齿轮传动消隙 (39)4、控制系统的设计 (39)4.1 控制系统总体方案的拟订 (39)4.2 总控制系统硬件电路设计 (39)参考文献 (56)谢辞 (57)科技译文 (58)前言加工中心集计算机技术、电子技术、自动化控制、传感测量、机械制造、网络通信技术于一体,是典型的机电一体化产品,它的发展和运用,开创了制造业的新时代,改变了制造业的生产方式、产业结构、管理方式,使世界制造业的格局发生了巨大变化。
立式加工中心主轴部件设计说明

引言装备工业的技术水平和现代化程度决定着整个国民经济的水平和现代化程度,数控技术及装备是发展高新技术产业和尖端工业(如:信息技术及其产业,生物技术及其产业,航空、航天等国防工业产业)的使能技术和最基本的装备。
制造技术和装备是人类生产活动的最基本的生产资料,而数控技术则是当今先进制造技术和装备最核心的技术。
当今世界各国制造业广泛采用数控技术,以提高制造能力和水平,提高对动态多变市场的适应能力和竞争能力。
此外世界上各工业发达国家还将数控技术及数控装备列为国家的战略物资,不仅采取重大措施来发展自己的数控技术及其产业,而且在“高精尖”数控关键技术和装备方面对我国实行封锁和限制政策。
数控机床技术的发展自1953年美国研制出第一台三坐标方式升降台数控铣床算起,至今已有很多年历史了。
20世纪90年开始,计算机技术及相关的微电子基础工业的高速发展,给数控机床的发展提供了一个良好的平台,使数控机床产业得到了高速的发展。
我国数控技术研究从1958年起步,国产的第一台数控机床是北京第一机床厂生产的三坐标数控铣床。
虽然从时间上看只比国外晚了几年,但由于种种原因,数控机床技术在我国的发展却一直落后于国际水平,到1980年我国的数控机床产量还不到700台。
到90年代,我国的数控机床技术发展才得到了一个较大的提速。
目前,与国外先进水平相比仍存在着较大的差距。
总之,大力发展以数控技术为核心的先进制造技术已成为世界各发达国家加速经济发展、提高综合国力和国家地位的重要途径。
1 绪论1.1 加工中心的发展状况1.1.1 加工中心的国外发展对于高速加工中心,国外机床在进给驱动上,滚珠丝杠驱动的加工中心快速进给大多在40m/min以上,最高已达到90m/min。
采用直线电机驱动的加工中心已实用化,进给速度可提高到80~100m/min,其应用围不断扩大。
国外高速加工中心主轴转速一般都在12000~25000r/min,由于某些机床采用磁浮轴承和空气静压轴承,预计转速上限可提高到100000r/min。
SK40立式数控铣床设计-主轴部件设计
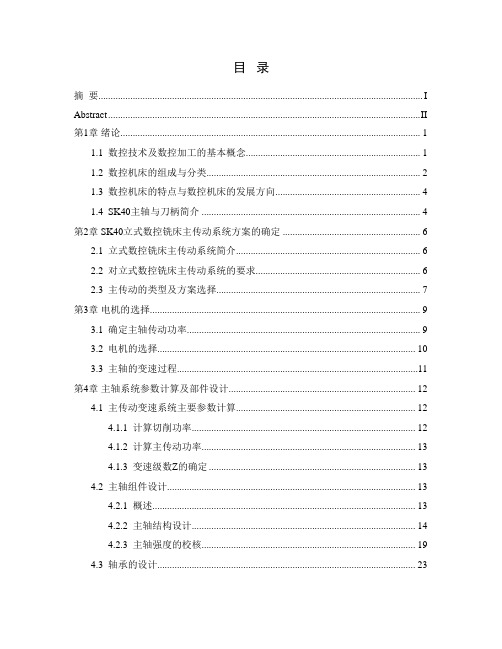
目录摘要 (I)Abstract ............................................................................................................................... I I 第1章绪论 (1)1.1 数控技术及数控加工的基本概念 (1)1.2 数控机床的组成与分类 (2)1.3 数控机床的特点与数控机床的发展方向 (4)1.4 SK40主轴与刀柄简介 (4)第2章 SK40立式数控铣床主传动系统方案的确定 (6)2.1 立式数控铣床主传动系统简介 (6)2.2 对立式数控铣床主传动系统的要求 (6)2.3 主传动的类型及方案选择 (7)第3章电机的选择 (9)3.1 确定主轴传动功率 (9)3.2 电机的选择 (10)3.3 主轴的变速过程 (11)第4章主轴系统参数计算及部件设计 (12)4.1 主传动变速系统主要参数计算 (12)4.1.1 计算切削功率 (12)4.1.2 计算主传动功率 (13)4.1.3 变速级数Z的确定 (13)4.2 主轴组件设计 (13)4.2.1 概述 (13)4.2.2 主轴结构设计 (14)4.2.3 主轴强度的校核 (19)4.3 轴承的设计 (23)4.3.1 概述 (23)4.3.2 轴承的类型选择 (23)4.3.3 轴承游隙等级的选择 (24)4.3.4 轴承的寿命计算 (24)4.3.5 轴承布局 (24)4.3.6 轴承装置的设计 (25)第5章主轴的加工工艺设计 (29)5.1 主轴加工工艺的主要内容 (29)5.2 对电主轴进行工艺分析 (29)5.3 电主轴的工艺路线设计 (30)5.3.1 工序的划分 (30)5.3.2 工步划分 (30)5.4 电主轴加工工序设计 (30)5.5 制定加工工艺卡 (31)参考文献 (Ⅲ)摘要本文介绍了立式数控铣床的一些基本概况,简述了机床主传动系统方面的原理和类型,分析了各种传动方案的机理。
立式加工中心机床结构
立式加工中心机床结构简介立式加工中心机床5大件各个部分展示:底座部件有地脚调整螺钉,丝杆组件和底座。
底座与滑台采用双侧导轨导向定位。
底座导轨下方有费油回收槽和孔,废油由底座后中部位的回收接头回收到废油收集盒。
加工中心主轴结构主轴部件包括主轴、主轴箱、主转动机构和打刀机构等。
主轴箱体设有油冷通道,机油通过外部油冷机,能降低加工过程中主轴单元的升温。
因此,机床更具有热稳定性。
如下图所示:主轴的传动方式分为皮带传动和直联传动皮带最高转速可达8000转,直连可达15000转工作台工作台与滑台采用双侧导轨导向定位工作台两侧的伸缩护罩要和工作台保持密封链接,如下图立式加工中心立柱结构立柱与主轴箱采用双侧导轨导向定位立柱结构组成如下图:立式加工中心X、Y、Z三轴进给如下图:数控加工中心作为一种全自动的数控加工机床和普通的机床相比具有比较大的优势,主要有以下几点:1、全封闭防护结构在机床的结构上,数控加工中心采用了全封闭的制造方式,能有效防止加工过程中出现的人身意外等情况。
2、加工的连续性数控加工中心具有多个进给轴:三轴或以上,能自动完成多个平面或多个角度的加工。
3、自动换刀结构数控加工中心具有自动换刀装置,能够通过程序控制进行自动换刀。
4、高自动化、高精度、高效率通过合理的切削参数选择和数控加工中心的加工连续性,减少了停机时间,提升了机床的加工效率。
5、改善劳动条件操机人员和编程人员只需要将设定好的程序输入系统,装卸零件和刀具准备等工作,降低了劳动强度。
6、加工精度高,产品质量稳定数控机床的精度比普通机床的高,采用计算机自动编程和减少装夹次数,有效降低误差。
XH716立式加工中心总体设计及主轴系统设计
XH716立式加工中心总体设计及主轴系统设计机械设计制造及其自动化摘要加工中心是典型的集高技术于一体的机械加工设备,它大大提高了劳动生产率,降低了劳动成本,改善了工人的工作环境,降低了工人的劳动强度。
本文经过对不同运动方案和各部件的设计方案的定性分析比较确定该立式加工中心的进给传动方案为:采用固定倒T型床身,电动机轴通过安装座安装在立柱导轨的滑座上,立柱导轨采用滚动直线导轨,可以实现Z方向的进给运动。
由X、Y向精密数控装置分别控制工作台和立柱完成X, Y两个方向的进给运动;X, Y, Z三个方向的进给运动均滚珠丝杠,并由交流伺服电机驱动。
导轨、滚珠丝杠采用多种润滑方式。
关键词:立式加工中心;伺服电机;精度;主轴箱;进给运动。
AbstractMachining center is a typical set of high-tech machining equipment in one, its greatly increased the labor productivity, reduce labor costs, improved working environment and reduce the labor of workers strength. This movement through the different programs and the design of various components of qualitative analysis and comparison of vertical machining centers to determine the progress of education to drive the program are: fixed inverted T-type bed, spindle seat installed by installing the sliding seat rail bed , use linear rolling guide rail bed can be achieved to the movement into the Z direction. By X, Y, precision CNC device to control the feed motion of the table and column X, Y two directions; X, Y, Z three directions of movement are ball screw feed, driven by AC servo motor. Guides, ball screws using a variety of lubrication.Key words: Vertical machining center; Servo motor; Accuracy;spindle box;Feed motion。
立式加工中心主轴部件综述
立式加工中心主轴部件综述立式加工中心的主轴部件,嘿,听起来是不是有点高大上?其实它就像是整台机器的“心脏”,没了它,啥都别想动。
你看啊,主轴的作用可大了,它负责把刀具转起来,就像我们开车得有发动机一样,主轴就是驱动整台机器的动力源泉。
想象一下,没有主轴,刀具也没办法精准地去切削那些金属、塑料、木材啥的,整个加工过程就像是乱了套,什么都做不成。
所以说,主轴对加工中心来说,就跟食堂的厨师对一锅菜的重要性是一样的。
可以没有花里胡哨的调料,但一定不能少了主厨。
先说说主轴的工作原理,哎呦喂,听着可能有点复杂,其实也不难。
你看主轴呢,像是个大电动机,或者说是电机的“兄弟”,它是通过电力来驱动刀具转动的。
别看它外形不怎么起眼,实际上它得承受巨大的转矩和振动。
比如说你想把一块坚硬的金属切割成一片片,那个过程可不是开玩笑的,刀具跟主轴之间的配合那叫一个默契,才能顺利完成这些“暴力”动作。
所以,主轴的强度和稳定性,直接决定了加工质量和效率。
主轴要是太弱了,转速上不去,刀具也没法快速有效地工作。
再比如,假如主轴的精度有问题,那可就糟糕了。
想象一下,你用一把刀子做菜,切出来的东西歪歪扭扭的,不对称,那能做出好吃的饭菜吗?说到这里,可能大家会有点疑问,为什么要专门聊主轴呢?其实不光是因为它重要,更因为它容易出问题。
主轴就像是咱们的手机电池,一旦坏了,你就啥都做不了了。
主轴的故障会导致设备运转不正常,甚至让整个生产线停摆。
就好比你的电脑一旦蓝屏了,基本上全世界都停止运转。
常见的主轴问题包括振动过大、噪音大,甚至会发生过热,导致机器无法继续工作。
比如说,主轴的轴承如果没保养好,就可能发生卡顿,最后就只能停下来修了。
所以啊,定期检查主轴部件是每个技术员的“必修课”,这种活儿不能马虎,得细心。
你说,主轴也有“寿命”啊。
它不像咱们人类,可以吃点保健品来延长“使用年限”,它的寿命主要取决于材料、制造工艺和使用环境。
好比一辆车子,开得太猛,没给它做保养,最后早晚得出问题。
加工中心主轴系统设计
加工中心主轴系统设计主轴系统是加工中心的核心部件之一,其设计和运行状态直接影响到加工中心的性能和加工效果。
在设计加工中心主轴系统时,需要考虑诸多因素,包括主轴转速、动力源、轴承类型和润滑方式等。
下面将介绍一些重要的设计要点。
首先,主轴转速是主轴系统设计的重要指标之一、主轴转速一般根据加工件材料的种类和加工要求来确定。
较高的主轴转速可以实现高速切削,提高加工效率,但也会增加主轴系统的负荷,影响主轴寿命。
因此,在设计主轴转速时,需要根据实际需求进行权衡。
动力源是主轴系统设计的另一个重要考虑因素。
加工中心主轴系统通常采用电机作为动力源。
在选择电机时,需要考虑其功率和扭矩输出等参数。
较大的功率和扭矩输出可实现更大的加工能力,但也增加了电机的体积和重量,对加工中心整体结构的设计带来一定的挑战。
轴承类型是主轴系统设计中的关键环节。
轴承的选择会影响主轴系统的准确性、刚性和稳定性等。
常见的轴承类型包括角接触球轴承、圆柱滚子轴承和角接触滚子轴承等。
不同的轴承类型适用于不同的工况和要求。
例如,角接触球轴承适用于高速回转和轻负荷的情况,而圆柱滚子轴承适用于较大的径向载荷。
此外,润滑方式也是主轴系统设计的重要考虑因素之一、润滑方式可以影响主轴系统的摩擦和磨损情况,进而影响主轴系统的寿命和稳定性。
常见的润滑方式包括油脂润滑和油气润滑等。
油脂润滑通常适用于低速和中速加工中心,而油气润滑适用于高速加工中心。
综上所述,设计加工中心主轴系统时,需要考虑主轴转速、动力源、轴承类型和润滑方式等因素。
合理的设计可以提高加工中心的性能和加工效果,满足加工需求。
同时,也需要对不同的加工条件和加工材料做出相应调整,以达到最佳加工效果。
最后,对主轴系统的定期维护和保养也是确保其正常运行和延长寿命的重要环节。
- 1、下载文档前请自行甄别文档内容的完整性,平台不提供额外的编辑、内容补充、找答案等附加服务。
- 2、"仅部分预览"的文档,不可在线预览部分如存在完整性等问题,可反馈申请退款(可完整预览的文档不适用该条件!)。
- 3、如文档侵犯您的权益,请联系客服反馈,我们会尽快为您处理(人工客服工作时间:9:00-18:30)。
引言装备工业的技术水平和现代化程度决定着整个国民经济的水平和现代化程度,数控技术及装备是发展高新技术产业和尖端工业(如:信息技术及其产业,生物技术及其产业,航空、航天等国防工业产业)的使能技术和最基本的装备。
制造技术和装备是人类生产活动的最基本的生产资料,而数控技术则是当今先进制造技术和装备最核心的技术。
当今世界各国制造业广泛采用数控技术,以提高制造能力和水平,提高对动态多变市场的适应能力和竞争能力。
此外世界上各工业发达国家还将数控技术及数控装备列为国家的战略物资,不仅采取重大措施来发展自己的数控技术及其产业,而且在“高精尖”数控关键技术和装备方面对我国实行封锁和限制政策。
数控机床技术的发展自1953年美国研制出第一台三坐标方式升降台数控铣床算起,至今已有很多年历史了。
20世纪90年开始,计算机技术及相关的微电子基础工业的高速发展,给数控机床的发展提供了一个良好的平台,使数控机床产业得到了高速的发展。
我国数控技术研究从1958年起步,国产的第一台数控机床是第一机床厂生产的三坐标数控铣床。
虽然从时间上看只比国外晚了几年,但由于种种原因,数控机床技术在我国的发展却一直落后于国际水平,到1980年我国的数控机床产量还不到700台。
到90年代,我国的数控机床技术发展才得到了一个较大的提速。
目前,与国外先进水平相比仍存在着较大的差距。
总之,大力发展以数控技术为核心的先进制造技术已成为世界各发达国家加速经济发展、提高综合国力和国家地位的重要途径。
1 绪论1.1 加工中心的发展状况1.1.1 加工中心的国外发展对于高速加工中心,国外机床在进给驱动上,滚珠丝杠驱动的加工中心快速进给大多在40m/min以上,最高已达到90m/min。
采用直线电机驱动的加工中心已实用化,进给速度可提高到80~100m/min,其应用围不断扩大。
国外高速加工中心主轴转速一般都在12000~25000r/min,由于某些机床采用磁浮轴承和空气静压轴承,预计转速上限可提高到100000r/min。
国外先进的加工中心的刀具交换时间,目前普遍已在1s左右,高的已达0.5s,甚至更快。
在结构上,国外的加工中心都采用了适应于高速加工要求的独特箱中箱结构或龙门式结构。
在加工精度上,国外卧式加工中心都装有机床精度温度补偿系统,加工精度比较稳定。
国外加工中心定位精度基本上按德国标准验收,行程1000mm以下,定位精度可控制在0.006~0.01mm之。
此外,为适应未来加工精度提高的要求,国外不少公司还都开发了坐标镗精度级的加工中心。
相对而言,国生产的高速加工中心快速进给大多在30m/min左右,个别达到60m/min。
而直线电机驱动的加工中心仅试制出样品,还未进入产量化,应用围不广。
国高速加工中心主轴转速一般在6000~18000r/min,定位精度控制在0.008~0.015mm之,重复定位精度控制在0.005~0.01mm之。
在换刀速度方面,国机床多在4~5s,无法与国际水平相比。
虽然国产数控机床在近几年中取得了可喜的进步,但与国外同类产品相比,仍存在着不少差距,造成国产数控机床的市场占有率逐年下降。
国产数控机床与国外产品相比,差距主要在机床的高速、高效和精密上。
除此之外,在机床可靠性上也存在着明显差距,国外机床的平均无故障时间(MTBF)都在5000小时以上,而国产机床大大低于这个数字,国产机床故障率较高是用户反映最强烈的问题之一。
1.1.2 立式加工中心的研究进展图1-1 立式加工中心结构图1-切削箱 2-X轴伺服电机 3-Z轴伺服电机 4-主轴电机5-主轴箱 6-刀库 7-数控柜 8-操纵面板9-驱动电柜 10-工作台 11-滑座 12-立柱13-床身 14-冷却水箱 15-间歇润滑油箱 16-机械手典型加工中心的机械结构主要有基础支承件、加工中心主轴系统、进给传动系统、工作台交换系统、回转工作台、刀库及自动换刀装置以及其他机械功能部件组成。
图1-1所示为立式加工中心结构图。
1.2 课题的目的及容加工中心是典型的集高新技术于一体的机械加工设备,它的发展代表了一个国家设计、制造的水平,因此在国外企业界都受到高度重视。
毕业设计的基本数据:1、工作台尺寸:600mm×400mm;最大承载:600kg2、主轴功率: 3.5 – 5KW;主轴转速: 20 - 3000rpm3、进给速度:X、Y向 1 - 10000mm/min;Z向 1 - 5000mm/min4、行程:X、Y向、Z向:600mm×400mm×400mm5、定位精度:±0.025mm;重复精度:±0.01mm6、圆盘式刀库:10个刀位,换刀时间为6秒1.3 课题拟解决的关键问题各类机床对其主轴组件和进给组件的要求,主要是精度问题,就是要保证机床在一定的载荷与转速下,组件能带动工件或刀具精确地、稳定地绕其轴心旋转,并长期地保持这一性能。
主轴组件和进给组件的设计和制造,都是围绕着解决这个基本问题出发的。
为了达到相应的精度要求,通常,主轴组件和进给组件应符合以下几点设计要求:1、旋转精度高,保证加工零件的几何精度和表面粗糙度。
2、在允许的条件下,尽量提高刚度值。
使主轴组件和进给组件在外力的作用下,仍能保持一定工作精度的能力。
3、提高抗振性,保证切削过程中的平稳运转。
4、控制温升,避免热变形,防止温度过高会改变轴承等元件的间隙、破坏润滑条件,加速磨损,影响加工精度。
5、保证耐磨性,以保持其原始精度的能力。
2 加工中心机械系统方案拟定2.1 加工中心主轴组件的组成主轴组件是由主轴、主轴支承、装在主轴上的传动件和密封件等组成的。
主轴的启动、停止和变速等均由数控系统控制,并通过装在主轴上的刀具参与切削运动,是切削加工的功率输出部件。
主轴是加工中心的关键部件,其结构的好坏对加工中心的性能有很大的影响,它决定着加工中心的切削性能、动态刚度、加工精度等。
主轴部刀具自动夹紧机构是自动刀具交换装置的组成部分。
2.2 机械系统方案的确定2.2.1 主轴传动机构对于现在的机床主轴传动机构来说,主要分为齿轮传动和同步带传动。
齿轮传动是机械传动中最重要的传动之一,应用普遍,类型较多,适应性广。
其传递的功率可达近十万千瓦,圆周速度可达200m/s,效率可达0.99。
齿轮传动大多数为传动比固定的传动,少数为有级变速传动。
但是齿轮传动的制造及安装精度要求高,价格较贵,且不宜用于传动距离过大的场合。
同步带是啮合传动中唯一一种不需要润滑的传动方式。
在啮合传动中,它的结构最简单,制造最容易,最经济,弹性缓冲的能力最强,重量轻,两轴可以任意布置,噪声低。
它的带由专业厂商生产,带轮自行设计制造,它在远距离、多轴传动时比较经济。
同步带传动时的线速度可达50m/s(有时允许达100m/s),传动功率可达300kw,传动比可达10(有时允许达20),传动效率可达0.98。
同步带传动的优点是:无滑动,能保证固定的传动比;预紧力较小,轴和轴承上所受的载荷小;带的厚度小,单位长度的质量小,故允许的线速度较高;带的柔性好,故所用带轮的直径可以较小。
其主要缺点是安装时中心距的要求严格。
由于齿轮传动需要具备较多的润滑条件,而且为了使主轴能够达到一定的旋转精度,必须选择较好的工作环境,以防止外界杂物侵入。
而同步带传动则避免了这些状况,并且传动效率和传动比等都能符合课题的要求,故在本课题的主轴传动方式中选择同步带传动。
2.3加工中心主轴组件总体设计方案的确定综合2.1,2.2节中的方案,本课题的总体设计方案现确定如下:由于同步带无滑动,能保证固定的传动比,且传动效率高,允许的线速度较高,无需安置在很良好的工作环境中,所以在主轴传动方式中选择同步带传动。
但是需要注意的是同步带的安装具有严格的要求。
在主轴的进给运动中,采用滚珠丝杠。
其耐磨性好、磨损小,低速运行时无爬行、无振动,能够很好地确保Z轴的进给精度。
由于加工中心具备自动换刀功能,所以在主轴组件中还应有主轴准停装置、刀具自动夹紧机构以及切屑清除机构。
在本课题中,主轴准停机构采用磁力传感器检测定向,其不仅能够使主轴停止在调整好的位置上,而且能够检测到主轴的转速,并在加工中心的操控面板上显示出来,方便机床操作者调整转速。
在换刀过程中,刀具自动夹紧机构也是不可获缺的一部分。
它控制着刀杆的松紧,使刀具在加工时能紧紧地固定在主轴上,在换刀时能轻松地卸载。
本课题采用了液压缸运行的方式,通过活塞、拉杆、拉钉等一系列元件的运动来达到刀杆的松紧目的。
同时,为了减少液压推力对主轴支承的磨损,在主轴的部设置了一段碟形弹簧,使活塞对拉杆的作用起到一个缓冲的作用。
同时,在换刀过程中,活塞及拉杆的部将被加工成中空状。
其间将通入一定的压缩空气来清除切屑。
使刀杆和主轴始终具有很好的配合精度。
在伺服系统中,本课题在进给系统中选用直流伺服电动机,而在主运动系统中则选用交流伺服电动机。
由于直流伺服电动机具有电刷和换向器,需要常常维修,故不适合于主运动系统中。
3 主轴主运动部件的设计3.1 主轴电动机的选用3.1.1 主电机功率估算由毕业设计任务书知主轴功率5kw主电机功率 kw kw P P m m E 36.598.099.00.55≈⨯==η 式中:ηm ——机床主传动系统传动效率。
滚珠轴承传动效率0.99,同步带传动效率0.983.1.2 主电机选型利用交流伺服系统可进行精密定位控制,可作为CNC 机床、工业机器人等的执行元件。
FANUC 交流主轴电机S 系列从0.65kW ~37kW 共分13种。
它的特点是转速高、输出功率大、性能可靠、精度好、振动小、噪音低,既适合于高速切削又适合于低速重切削[5]。
该系列可应用在各种类型的数控机床上。
根据主电机功率PE=5.36kW ,故本课题选用FANUC 交流主轴电机6S 型号。
其主要技术参数如下:额定输出功率:5.5km/h ;最高速度:3000r/min ;额定输出转矩:35.0N ·M ;转子惯量:2022.0s m N ⋅⋅。
3.2 主轴3.2.1 主轴的结构设计主轴的主要参数是指:主轴前轴颈直径D 1;主轴孔径d ;主轴悬伸量a 和主轴支承跨距L ,见图3-1。
图3-1 主轴主要参数示意图(1)主轴轴径的确定主轴轴径通常指主轴前轴颈的直径,其对于主轴部件刚度影响较大。
加大直径D ,可减少主轴本身弯曲变形引起的主轴轴端位移和轴承弹性变形引起的轴端位移,从而提高主轴部件刚度。
但加大直径受到轴承d n 值的限制,同时造成相配零件尺寸加大、制造困难、结构庞大和重量增加等,因此在满足刚度要求下应取较小值。
设计时主要用类比分析的方法来确定主轴前轴颈直径D 1。
加工中心主轴前轴颈直径D 1按主电动机功率来确定,由《现代数控机床结构设计》查得D 1=85mm 。