轧辊失效形式
热轧1750mm带钢轧机轧辊失效浅析

[摘要 ] 对轧辊失效方式进行 了研究 , 析了产生轧辊失效剥落 、 分 断裂、 裂纹等现象的原因。采取 了相应 的预 防措施 , 提高 轧辊剪切温度和塑性 , 降低残余应力 , 在使用前进行磁粉或渗透探 伤 , 使热轧轧辊的使用 寿命得 到提高 。
关键词 轧辊
1 前 言
剥落
断裂
疲劳
应 力 改进
tj jjtm ‘ o —一 可究与应用 j @t Cj c玎 ● 一 ' 哪 =|心 用 y y Ol = t i i
.
n
维普资讯
天沸 室 幺
型, 使得 辊 身两端 产生 了局 部 的接触 压力尖 峰 、 端 两
交变剪应 力的增大 , 快 了疲 劳破 坏 。辊 身 中部 的交 加 变剪应 力点 , 在轧 辊磨损 的推动作 用 下 , 渐 往辊 身 逐 内部移动 , 不易形成疲 劳裂纹 ; 而轧辊边部磨 损较少 , 最 大交变 剪应力 点基本 不 动 , 在其反 复作 用下 , 局部 材料弱化 , 出现裂纹。
层 的裂纹沿 径 向扩展 进入硬化层并 多方 向分支扩展 , 该 裂纹 在逆 向轧制条件下造成剥落 。 21 支撑辊辊 面剥 落 .1 . 支 撑辊 剥落 大多 位 于轧辊 两端 ,沿 圆周 方 向扩 展, 在宽度上呈块状片状剥落 , 剥落坑表 面较平整 。支
天铁集 团热轧板公 司 1 5mm热 轧带钢 工程主要 70 设 备有 E R 粗轧机 、 2 2 轧机 、 1 F 精 轧机 、 11 ER 粗 F 一v 7 三 台地下卷取机 ,其 中 E R 粗轧机和第 三台卷取机分 11 步实施 。作 为轧线 主要设 备 的轧机 , 将连铸坯 轧制成 厚度 1 ~ 6m . mm 1 m、宽度 7 0m 10 m 的成 品 2 3 m~ 60 m 带钢 。 为两辊可逆式粗轧机 , E 形成连轧 , 连 R1 与 1 将
第2章 轧辊综述
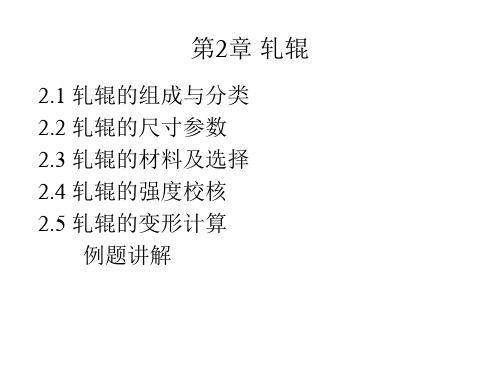
§2.2. 3轧辊的辊头尺寸
1、梅花轴头尺寸
通常梅花轴头的外径 d 1= 0.85 d (二辊薄板轧机), 其它轧机则取 d 1 = (0.90~0.95) d ; d 2 = 0.66 d 1 ; r1 = 0.207 d 1 ; l 1 = (0.7~0.75)d 1
3、辊头 (1)定义:是轧辊与连接轴相接的部分。 ( 2 )轧辊的辊头有梅花型、万向节型和带 双键型。 (3)参数:d1-辊头直径 l1-辊头长度 当轧辊不传动(工作辊驱动条件下的支 承辊)或只有单侧传动时,轧辊可以不做专 门的辊头,仅在辊颈外留有可供换辊的起吊 部分。
§2.1.2 轧辊的分类 1、按构造分类 ①光面轧辊:应用于轧制板带材。 ②有槽轧辊:应用于轧制型钢、线材和钢 坯。
3、辊身长度 L 是表征板带钢轧机特征的主要参数。板带 钢轧机以(四辊或多辊轧机则指工作辊)辊身 长度作为轧机标称的组成部分。这是因为辊身 长度能直观的反映出轧机所能生产的最大板宽, 而板宽也正反映出了板带材的使用范围和生产 板带材的难易程度。 型钢:L与孔型布置的数目和轧辊强度有关。 板带:L=bmax+Δ (Δ =50mm∽200mm)
2、轧辊的工作直径 Dg 是指轧辊与轧件接触进行变形而直接工作 的直径。在有槽轧辊上是指槽底处直径。 型钢:工作辊直径Dg一般小于公称直径D。 为了防止轧辊切槽过深而影响强度, D/ Dg的 比值一般不大于1.4。 板带:斯通根据轧机最小可轧厚度的临界条 件,推导出计算工作辊直径的公式: D1=(0.28 E hmin) / [f (K-σ p)] ((K为带材的条 件屈服限) D2 ≥K/0.3 (K为刚度系数)
§2.1. 5 轧钢生产对轧辊的要求 1、具有所要求的强韧性; 2、具有所要求的耐磨性; 3、具有一定的耐热性; 4、具有耐剥落性。
中厚板轧机工作辊失效分析及对策

S N Ha . Il li U o U J
JnnI n & Sel【 ou )c . J邮 2 0 0 .C i ia r o te Gr p 0. l r 5 1 1 hn a
Ab t a t: Th a e n r d  ̄ d t e man f i  ̄ t p o i h Ni 0 n ih Crwo k r l , wh c mp re r m b d a】 sr c e p p r i to u h i al u y 幅 fh g a d hg r o l s i h i o td fo a e 】 d
tme teifu n efc i , h n e c a mm _ r k g d a】 l m h ̄ a e 1
… epu 0r t f w .
Ke y wor : h , n e im a mi; w0 km l c ueo al ̄ ds  ̄ r a dm du y l l r h ¨ s 1fJu
性 好 、耐 腐蚀 、工作 层硬 度 落差 小等特 点 。与高
Ni r C 辊相 比,其 轧制 效 益 可 提 高 2 %以 上 ,尤 0
常 , 轧制力 和扭 矩校 验在 正常 范 围内, 用有 限元
法 对工 作 辊进 行 强 度 校 验, 也 在 许用 值 范 围 内. 因此排 除 了 由于 操 作 或 设 备 原 因 造 成断 辊 的 可 能 。但 金相 检验 表 明,芯 部的碳 化 物粗大 且 不均
其 在 进行 控 制 轧 制 时 , 由 于 终 轧 温 度 低, 磨 损
大 ,板 形和 同板 差 易 受 影响 ,高 c 上 作 辊 更 显 r
示 出优越 性 。但 高 辊 对水冷 条 件要求 较严 格 ,
轴承失效形式及原因分析

轴承基本知识
轴承基本知识
轴承基本知识
轴承基本知识
我们车间目前使用的主轴承就是轧机轴承:粗中轧 轧辊和红圈辊箱均使用四列圆柱滚子轴承,CCR辊箱 使用为调心滚子轴承。 圆柱滚子轴承内径与辊颈采用紧配合,承受径向力 ,具有负荷容量大、极限转速高、精度高、内外圈可 分离且可以互换、加工容易、生产成本低廉、安装拆 卸方便等优点。 调心滚子轴承具有双列滚子,外圈有1条共用球面 滚道,内圈有2条滚道 并相对轴承轴线倾斜成一个角 度。这种巧妙的构造使它具有自动调心性能, 因而 不易受轴与轴承箱座角度对误差或轴弯曲的影响,适 用于安装误差或轴 挠曲而引起角度误差之场合。该 轴承除能承受径向负荷外,还能承受双向作用的轴向 负荷。
三、轴承失效原因
三、轴承失效原因
1、氧化渣、水等异物侵入引起的失效: 轧辊轴承的精密度很高,它对异物十分敏感,氧化渣、水等异物侵入轴承内部是使其过早失 效的最主要原因。氧化渣、水等异物与润滑油脂综合后很容易产生油污泥,油污泥的形成和 堆积能造成许多不良后果,其一是油污泥占据了原来润滑油脂的很大一部分空间,因而迟缓 了热量的传递和散发;其二是硬而胶性的堆积物在滚动体和滚道上形成时,在工作负荷下滚 动体滚过这些沉积物时,工作应力将大为增加,结果是轴承的正常疲劳寿命减少:其三是保 持架发生疲劳,随之而来使整个轴承彻底损坏。 2、过载和过热引起的失效: 在安装正确,密封良好的情况下,过载是引起轴承失效的另一原因。众所周知,轧辊辊颈轴 承运行时承受着巨大而又频繁的冲击力,长时间超负荷过载运行,会引起轴承材料的过早疲 劳,最终将体现在滚道表面层材料的碎裂剥离(麻面),这种损坏开始时发生在某些小面积上 ,但扩展极快。通常由于过载而引起的损坏总是先从内圈开始。过热而引起的失效情况多发 生在高线转速相对较快的10架~14架。轧辊轴承上,产生过热的原因可大致归结为:(1)润 滑油脂变质以及不足或过量;(2)过载:(3)装配不良:(4)外部热源传导进来的热量。轴承 长期过热会引起表面变色(暗蓝、蓝黑等)。过热不仅能使保持架严重氧化,同时也能使滚动 体、滚道退火软化,甚至咬死。
轧辊的材料及热处理

轧辊的寿命主要取决于轧辊的内在性能和工作受力,内在性能包括强度和硬度等方面。
要使轧辊具有足够的强度,主要从轧辊材料方面来考虑;硬度通常是指轧辊工作表面的硬度,它决定轧辊的耐磨性,在一定程度上也决定轧辊的使用寿命,通过合理的材料选用和热处理方式可以满足轧辊的硬度要求。
轧辊按工作状态可分为热轧辊和冷轧辊,按所起的作用可分为工作辊、中间辊、支承辊,按材质可分为锻辊和铸辊(冷硬铸铁)。
通常轧辊的服役条件极其苛刻,工作过程中承受高的交变应力、弯曲应力、接触应力、剪切应力和摩擦力。
容易产生磨损和剥落等多种失效形式。
不同的用途、不同类型的轧辊处在各自特定的工况条件,其大致的性能要求如下:冷轧辊在工作过程中要承受很大的轧制压力,加上轧件的焊缝、夹杂、边裂等问题,容易导致瞬间高温,使工作辊受到强烈热冲击造成裂纹、粘辊甚至剥落而报废。
因此,冷轧辊要有抵抗因弯曲、扭转、剪切应力引起的开裂和剥落的能力,同时也要有高的耐磨性、接触疲劳强度、断裂韧性和热冲击强度等。
国内外冷轧工作辊一般使用的材质有GCr5、9Cr2、9Cr、9CrV、9Cr2W、9Cr2Mo、60CrMoV、80CrNi3W、8CrMoV、86CrMoV7、Mo3A等。
20世纪50~60年代,这一时期的轧件多为碳素结构钢,强度和硬度不高,所以轧辊一般采用 1.5%~2%Cr锻钢。
此类钢的最终热处理通常采用淬火加低温回火,常见的淬火方式有感应表面淬火和整体加热淬火。
其主要任务是考虑如何提高轧辊的耐磨性能、抗剥落性能,并提高淬硬层深度,尽量保证轧辊表面组织均匀,改善轧辊表层金属组织的稳定性。
从20世纪70年代开始,随着轧件合金化程度的提高,高强度低合金结构钢(HSLA)的广泛应用,轧件的强度和硬度也随之增加,对轧辊材料的强度和硬度也提出了更高的要求,国际上普遍开始采用铬含量约2%的Cr-Mo型或Cr-Mo-V 型钢工作辊,如我国一直使用的9Cr2Mo、9Cr2MoV和86CrMoV7、俄罗斯的9X2MΦ、西德的86CrMoV7、日本的MC2等。
浅析铸造热轧带钢工作辊的剥落与断裂失效

凰 2 挤压裂 纹和 带状疲劳 剥落
3 主 要 的 断裂 失 效 形 式
3 1 弯矩引起的轴承部位断裂 .
这种失效形式的断裂面从轴承部位外部开始延 为预防这类剥落失效 的产生 , 轧辊每次服役后
应对其缺陷进行检测。在发生严重轧机事故后 , 轧 辊应进行 10 0 %裂纹检测 , 除此之外 , 还应采取~ 系
于辊轴的方向形成, 然后逐渐沿径向传播 ; 随着轧制
过程的继续进行 , 疲劳会逐渐向圆周方向漫延 , 呈现
出平行于辊身表面的猫舌状断裂带 。断裂面的漫延 方 向同轧辊旋转方向相反。这种断裂首先是在工作 层 中产生 的 , 而逐渐 往 辊身 方 向变深 变宽 , 终导 进 最 致辊身大面积的剥落。见图 2 。 这种剥落形式产生的主要原因是过大的局部负
维普资讯
第2 8卷第 1 期
20 0 6年 3月
甘
肃
冶Hale Waihona Puke 金 V0 . No 1 128 .
GANS ME AL UR U T L GY
Ma..0 6 r 20
文章 编号 :6 2 4 1 2 0 } 1 0 40 17 - 6 ( 06 0 - 0 -3 4 0
2 工作辊 的剥落 失效形式
2 1 马鞍形 剥落 .
2 2 挤压裂纹和带状疲劳剥落 ( . 猫舌状剥落 )
轧制过程 中在局部挤压过大的区域 , 轧辊表面 会形成 I 条或几条裂纹 , 这样 的裂纹往往会在平行
这种马鞍形状的疲劳剥落是起源于结合层下部 芯部材质 , 从而引发 了大块 的掉 肉。从 断裂表面上
可 以看到许多疲劳截面的传播途径。这种剥落往往 发生在灰 口铁芯部 的离心工作辊 ( 4辊轧机 ) 而且 ,
轧机油膜轴承典型失效形式分析及预防

轧机 油膜 轴承典型失效形式分析及 预 防
王洪 印 ,赵 东亮 ,孙 凯 旋 , 吕树 民
( 郸 钢铁 集 团公 司 连 铸 连 轧 厂 ,河 北 邯 郸 邯 061) 5 0 5
摘 要 :对 轧 机 油 膜 轴 承 常 见 的 两 种 失 效 方 式 进 行 了总 结 , 从 理 论 上 分 析 了轴 承 失 效 的 原 因 . 并 结 合 生 产 实
超 出其 最 大值 , 轴承 的承 载能力 就会 低于其 额定 值 , 最
终 可 能会 导致轴 承事 故 的发生 。
润滑 油 内。总之所 有 可 能涉 及 污 染 油脂 的因 素 , 应 都 该 引起 特别 的关 注 。
磨 损 的直接 结果 就是 导致 轴承 间的 间隙增 大 。油
收 稿 日期 :2 1— 1 1 I修 回 日期 :2 1 1- 4 0 1 1- 4 0 卜 12
安装 油管接 头时应 保 证 接头 的 清 洁 , 免将 杂 质 带 入 避
形 成轴 承锥 衬套 之 间的 接 触 ; 由 于轴 承 润 滑油 被 污 或 染 后含 杂质 较多 、 水 量较 大 , 含 导致 其 黏 度 降低 , 膜 油 强度不 足 以抵消 轧制 力 的 时 候 , 也会 发 生 不 同程 度 的 磨损 。轴 承的磨 损失 效 是 一 个 量变 积 累 的过 程 , 不会 在短 时 间内发 生轴 承损 坏 烧 毁 事故 , 以其 是 可预 测 所 的 , 是 可以控 制 的 。但 量变会 产生 质变 , 也 当磨 损间 隙
所 以应 将轴 承间 隙控 制在 一 个 合 理 的范 围 内 , 以锡 基 巴氏合 金 耐磨材料 为 例 , 其相 对 间隙 可控 制在 轴 承 公
称直 径的 0 3 . ‰~ 1 o 间 。 %之
型钢线降辊耗措施探讨
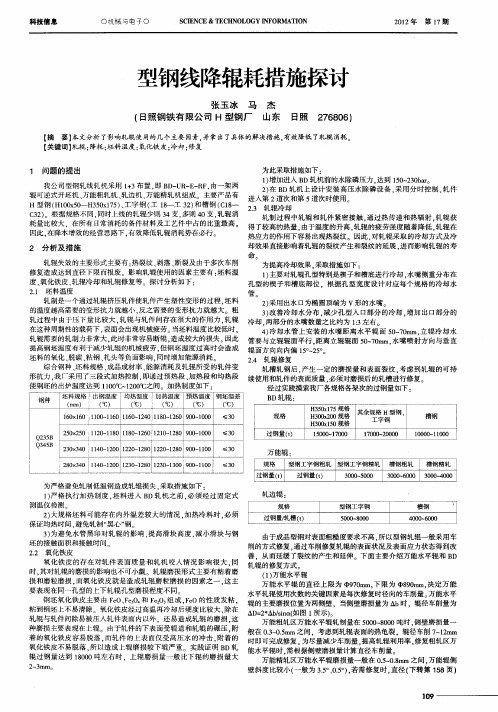
1 问题 的 提 出
我公 司型钢 轧线 轧机采用 1 3布置 . B — R E R 由一架两 + 即 D U — — F. 辊可逆式开坯机 、 万能粗轧机 、 轧边机 、 能精轧 机组 成。主要产品有 万 H 型 钢 ( O ) o _ 3 0 1 5 、 字 钢 ( l一 工 3 ) 槽 钢 ( 8 H1o【 _ H 5 x 7 ) 工 5 工 8 2和 C1一 C 2 。根据规格不同 , 3) 同时上线 的轧辊少则 3 4支 , 多则 4 0支 , 轧辊消 耗量 比较大 ,在所有 日常消耗 的备件材料及工艺件 中 占的 比重最高。 因此 . 在降本增效的经营思路下 , 有效 降低轧辊消耗势在必行。
2 分 析 及 措 施
轧辊失效的主要形式主要有 : 热裂纹 、 剥落 、 断裂及 由于多次车削 修复造成达到直径下限而报废。影 响轧辊使用 的因素主要有 : 坯料温 度、 氧化铁皮 、 轧辊冷却和轧辊修复等。探讨分析如下 : 2i 坯料温度 . 轧制是一个通过轧辊挤 压轧件使轧件产生 塑性 变形 的过程 . 坯料 的温度越高需要的变形抗力 就越小 , 反之需要 的变形 抗力就越大。粗 轧过程 中由于压下量 比较大 . 轧辊与轧件 间存 在很大的作用力 . 轧辊 在这种周期性的载荷下 , 表面会 出现机械疲劳 。 当坯料温度 比较低时 , 轧辊需要 的轧制力非常大 . 此时非 常容易断辊 , 造成较大的损失。 因此 提高钢坯温度有利于减少轧辊的机械疲劳 . 但钢 坯温度过高时会造成 坯料 的氧化 、 脱碳 、 粘钢 、 扎头等负面影 响, 同时增加能源消耗。 综合钢种 、 坯料规格 、 成品成材率 、 能源消耗及 轧辊所受的轧件变 形抗力 , 我厂采用了三段式加热控制 , 即通过 预热段 、 加热段 和均热段 使钢坯 的出炉温度达到 I0  ̄~ 20 之间。加热制度如下 10C 1 0 ' E
- 1、下载文档前请自行甄别文档内容的完整性,平台不提供额外的编辑、内容补充、找答案等附加服务。
- 2、"仅部分预览"的文档,不可在线预览部分如存在完整性等问题,可反馈申请退款(可完整预览的文档不适用该条件!)。
- 3、如文档侵犯您的权益,请联系客服反馈,我们会尽快为您处理(人工客服工作时间:9:00-18:30)。
铸轧辊失效的形式:①热龟裂;②裂纹扩展快;③表面局部塑形变形;④断裂。
在轧制中,裂纹扩展速度快,有时纵向裂纹长300mm,深2-4mm,是辊套过早的失效,原因是:辊套热处理工艺不合格,内部较大的残余应力为消除,在轧制过程中,受铝液热应力与辊芯内冷却水冷应力的交替作用,加速了裂纹的生成和扩展。
辊套的正常失效按下公式计算:有效厚度=(Dmax-Dmin)/2 Dmax为铸轧辊的最大的外径,Dmin为最小外径,每次车磨4mm左右,直至有效厚度接近于零,此辊套就认为失效为重新更换。
辊芯失效形式:①水槽阻塞;②水槽破裂,辊芯的材质:42CrMo 辊芯硬度HB在500左右。
调质硬度范围为2000MPa<HB<4000MPa
辊套:需具有良好的导热性,线性膨胀系数及弹性模数小,较高的抗拉强度、屈服强度及硬度,较好的耐热性、抗热疲劳及热变形等。
辊套粗糙度Ra为0.8-1.2μm。
辊套硬度HB为370-400左右,目前国内使用的辊套材质为PCrNi3Mou和32Cr3Mo1V钢。
冷却说的要求:水硬度:硬度总和不大于7. PH值:6-8 水压:0.4-0.6MPa
悬浮物:不大于50PPM 水温:一般控制在15-28℃辊芯辊套热装时温度的计算:t=I/αD内·C 式中:I=σ+Δmin
σ-过盈量;Δmin-热装的最小间隔;α材料线膨胀系数过盈量配合量的经验公式为:过盈量一般为铸轧辊辊径的0.09%-0.11%。
辊芯尺寸在φ500mm-φ700mm,过盈量(mm)=辊芯尺寸x1/650
辊芯尺寸在φ700mm-φ850mm, 过盈量(mm)=辊芯尺寸x1/700 当传递的轧制力矩一定时,辊套越薄,需要的过盈配合量越大。
辊套越薄所能产生的过盈压力越小,传递的轧制力矩越小。
对新辊(包括重新研磨的辊)进行热处理,首先用无水乙醇擦掉七表面的油污,后用自行配制的腐蚀溶液(只要成分是硝酸)均匀涂抹与辊面,待接近干燥,用清水洗净,此时辊面呈亮黑色,在轧辊完全干燥后,用800″砂纸沿轧制方向用力将其面的黑色物质打磨去掉。
下辊面比上辊面提前出现龟裂的原因是:下辊辊套温度梯度比上辊面大。
辊面车削深度为H+0.5mm,H为龟裂深度。
用液化石油气火焰润滑辊面。
冷石墨液喷涂润滑会对辊面产生一次冷冲击。
每生产600t-1000t铸轧板则需对铸轧辊进行车磨,磨削加工。
每次车磨的加工量为3mm-5mm。
现一般的辊套厚度为30mm-40mm,允许使用的最小厚度问为15mm,所以实际车磨只能进行6次到8次,每对辊套约生产铝板坯5000t-6000t。
Cr、Mn、Ni、W、V、Mo等元素可以提高钢的,淬透性,硬度,强度和耐磨性,并使刚才的韧性和抗热度疲劳性得以改善,目前国内铸轧辊套材料大多采用PCrNi3MoV和32Cr3Mo1V 钢。
过盈量过小,轧辊容易打滑,过盈量过大,轧辊容易炸裂。
精车、粗车、精磨、粗磨。
精车时预留0.60mm加工余量,精磨后预留0.15mm加工余量,精磨时只要辊套内孔表面园跳动小于0.04mm,直线度小于0.02mm表面粗糙度小于0.9μm,无明显烧伤、斑块,便可终止加工。
辊芯精车后预留0.1-0.15mm加工余量。
轧辊中部受力比边部大,塑形变形比较重,辊芯凸度定为1/10000左右为宜。
辊套在车削时尽可能采用一次车削法,以保证辊套两端同心度,磨削时必须采用一次磨削法,即一次从辊套的一端磨到另一端。
辊套的热装配:辊套从室温慢加热到300℃左右有时,用时8-10h,并在300℃左右保
辊套精加工面有较好的成色时,即可装配,辊套加热切记过烧。
辊套热装配应力:因为热装配冷却时,辊套不能回复到原来的尺寸(一般有7-8丝的塑性变形)因此在辊套内壁产生残余压力,以620x1450铸轧辊为例:轴向应力σ1=70-150MPa ,环向应力σ2=150-250MPa
热应力估算值:σ=E δΔQ/(1-δ)。
其中E=样式系数,δ=膨胀系数,ΔQ=外部温度-内部温度。
热应力水平取决于工作期间辊套表面的温度、接触的弧度、铸轧速度。
机械阴历来源于热装配(静压力)、运转(扭转和剪切)及轧制压力(弯曲)。
铸轧辊粗糙度应在0.7-0.9μm 之间,时间证明辊面磨得越粗糙,龟裂扩展的越快,轧辊寿命越短。
冷轧辊
在板材冷轧过程中,轧制金属的变形抗力远远高于热轧。
在咬入阶段,轧辊表面要承受超过10000MPa 的巨大压力,还要同时承受由于摩擦引起的剪应力。
为了满足使用要求,冷轧辊必须具有约2000MPa 的抗拉强度以及高纯净度(即内无夹杂),均匀的内部组织。
冷轧辊进行热处理的原因:①提高轧辊的硬度和耐磨性;②稳定轧辊尺寸,防止轧辊尺寸在存放和使用过程中发生变化;③防止轧辊开裂。
当应力与晶粒直径较大时,已发生脆性断裂,断面总体平齐。
应力与晶粒直径的增大,是轧辊断裂的内因。
轧制机械应力、热应力的叠加是造成辊断裂的外因。
辊套应与加工好的辊芯配做,保证配装过盈量为0.40mm-0.60mm ,过盈量Δ的确定也可以有下式求得:Δ=(1/100-1/2100)·D 内 式子中D 内为辊套内经(mm )。
辊套的加热温度:T= [(2-3)·Δmax ]/αd+T 0,T 为加热温度℃;Δmax 为最大过盈量mm ;T 0为室温℃。
α为辊套材料线膨胀系数,10-6/℃,d 为配合基本直径mm 。
轧制过程中,具有一定压力的冷却水,在辊芯水槽中循环。
当铸轧辊面与铝液接触后,吸收其热量并使其迅速凝固,然后再对已凝固的铝板进行一定的轧制。
当裂纹深度t 在2.5mm ≤t <4mm 时,则必须进行车磨修复。
高强度钢如Mo22、P913、C 级、32Cr3Mo1V 等钢种,一般连续使用1.5-2个月后,则必须进行修复,修复量(车+磨)≥裂纹深度+0.2-0.5mm 。
注:通常是以300kgf 的压力下,1kgf=9.8N ,kgf 即千克的力,D 为淬火钢球或硬质合金的直径(mm )D 为用读数显微镜测出的压痕平均值,一般来说,不是硬度越小,材料越软,其压痕直径越大;反之,布氏硬度值越小,材料越硬,其压痕直径越小。
辊芯水槽结构大部分仍采用矩形水槽,矩形圆底水槽,矩形尖角正好是应力集中源,最易破裂及堵塞。
建议采用正弦曲线平顶水槽,不宜破且水槽根部厚度增大使抗变形能力增强。
奥氏体是碳溶解在Y-Fe 中的间隙固溶体,常用符号A 表示。
奥氏体是在大于727℃高温下才能稳定存在的组织。
铝熔点为660度,如果在立板之前要用砂纸砂光,应沿圆周方向砂,砂纸粒度应<120。
水槽必须定期进行清洗,一般清洗周期为一个月左右,清洗介质用无腐蚀性的加压溶液,让铸轧辊在旋转状态下清洗,效果更佳。
当板材横截面呈“狗骨”形时,只能采取无损伤性拆卸,即用工频淬火机床快速加热,使辊套退出,然后对辊芯水道进行机械清理。
补焊损坏的水槽,若辊芯表形严重,可采用镀铬后精磨以恢复原辊芯尺寸及几何精度*,这样可以延长铸轧辊的使用
当轧辊辊芯直径大于φ700mm,辊套壁厚以70-80mm为宜,当轧辊辊芯直径小于φ700mm,辊套壁厚50-60为宜。
铸轧区长度偏小时,将减慢铸轧速度,同时铸轧板热加工率增大,是铸轧板组织致密。
正常铸轧时,金属液穴在铸嘴前沿与轧辊的间隙处存在一弯曲面。
其表面膜的表面张力产生的附加压力P1为P1=2σ/d 式中:σ-表面膜张力;d-嘴辊缝隙。
①在前箱页面高度下,熔体对铸嘴间隙最用的静压为P2为:P2=2ρgh,式中ρ表示金属的密度;g重力加速度;h液面高度。
正常铸轧时,静压力和表面张力处于平衡状态,即:P1=P2③由式①②③得h=2σ/ρgh 式中,前箱页面高度下,熔体对铸嘴前沿的间隙有关,铸嘴缝隙增大,液面高度降低,一般情况下,铸嘴辊间隙控制在0.5-1.5mm,上辊嘴辊间隙控制在1.0-2.0mm。
调整液面高度的时间一般要在切卷前后。
浇铸温度一般指前箱的熔体金属温度,在铸轧过程中,浇铸温度一般控制在680-710℃。
在保证正常生产的条件下,静置炉定温尽量定低。
一般情况下,静置炉定温控制在770-810℃。