轧辊失效方式及其原因分析
轧辊爆裂原因

轧辊爆裂是轧制生产中常见的一种失效形式,可能会导致严重的生产事故和经济损失。
以下是几种可能导致轧辊爆裂的原因:
1. 轧辊材质不适:轧辊材质应该具有高的强度、韧性和耐磨性。
如果材料不符合轧辊的使用要求,则会引起轧辊疲劳失效和裂纹扩展,导致轧辊爆裂。
2. 轧辊表面缺陷:轧辊表面缺陷、裂纹、凹坑等缺陷也可能导致爆裂。
这些缺陷将在轧制过程中扩展并使轧辊破裂。
3. 轧辊使用过程中温度过高:过高的轧辊表面温度会使轧辊产生变形和热疲劳裂纹,最终导致轧辊爆裂。
4. 轧辊使用寿命过长:轧辊在使用过程中会不可避免地出现疲劳损伤和磨损,长期使用可能导致轧辊的强度减小,出现裂纹和爆裂。
5. 非正常操作:轧辊在使用过程中需要严格遵循规定的操作程序和参数范围。
如果操作不当,例如过多受力或者运转速度过快,就有可能导致轧辊疲劳损伤和爆裂。
综上所述,预防轧辊爆裂需要严格控制轧辊的材质、缺陷、温度、使用寿命和操作规范,定期检测和维修轧辊以及合理调整轧制过程参数等措施。
1420轧机弯辊缸失效分析与对策

1420轧机弯辊缸失效分析与对策
一、问题描述
二、失效原因分析
1.润滑不良:润滑不良会导致摩擦增大,加速零部件的磨损,从而导
致弯辊缸失效。
2.密封不严:密封不严会导致液压系统内部液压漏油,降低了液压系
统的工作效率,同时也会影响到了弯辊缸的正常运行。
3.缸体磨损:长时间使用或者操作不当会导致弯辊缸的缸体磨损,进
而导致其失效。
三、对策建议
1.加强润滑管理:定期检查加油润滑情况,确保润滑油的充足和质量。
严格按照润滑标准操作,确保润滑效果。
2.定期检查维护:定期检查弯辊缸的密封情况,及时更换密封件。
并
定期检查缸体磨损情况,根据情况进行修复或更换部件。
3.加强操作规范:员工在操作弯辊缸时,应按照操作规程进行操作,
避免操作不当导致的缸体磨损。
4.提高维护意识:定期对弯辊缸进行维护保养,确保设备长期稳定运行。
同时,员工应加强维护意识,发现问题及时报修,避免小问题演变成
大问题。
四、总结
1420轧机弯辊缸的失效会给生产带来不小的影响,因此对其进行定期维护和保养是非常重要的。
除了以上提到的对策建议外,还应加强员工培训,提高其维护技能和意识,确保设备的长期稳定运行。
只有全面加强对设备的维护管理,才能最大程度地减少设备失效带来的影响,提高生产效率和产品质量。
轧辊破坏常见原因分析及对策
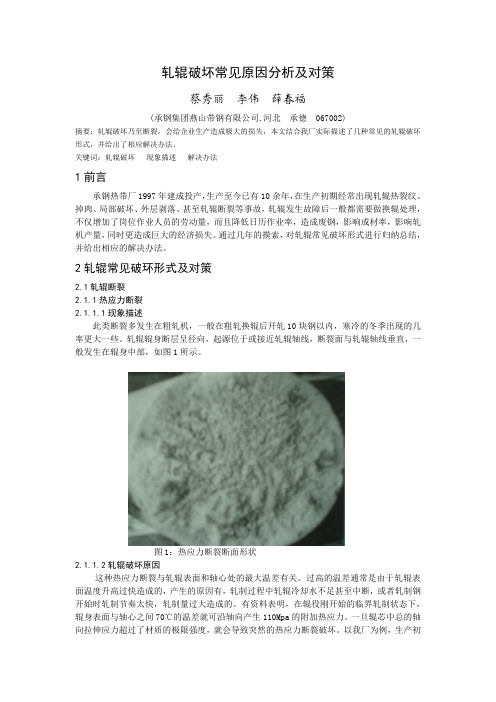
轧辊破坏常见原因分析及对策蔡秀丽李伟薛春福(承钢集团燕山带钢有限公司,河北承德 067002)摘要:轧辊破坏乃至断裂,会给企业生产造成极大的损失,本文结合我厂实际描述了几种常见的轧辊破坏形式,并给出了相应解决办法。
关键词:轧辊破坏现象描述解决办法1前言承钢热带厂1997年建成投产,生产至今已有10余年,在生产初期经常出现轧辊热裂纹、掉肉、局部破坏、外层剥落、甚至轧辊断裂等事故,轧辊发生故障后一般都需要做换辊处理,不仅增加了岗位作业人员的劳动量,而且降低日历作业率,造成废钢,影响成材率,影响轧机产量,同时更造成巨大的经济损失。
通过几年的摸索,对轧辊常见破坏形式进行归纳总结,并给出相应的解决办法。
2轧辊常见破环形式及对策2.1轧辊断裂2.1.1热应力断裂2.1.1.1现象描述此类断裂多发生在粗轧机,一般在粗轧换辊后开轧10块钢以内,寒冷的冬季出现的几率更大一些。
轧辊辊身断层呈径向,起源位于或接近轧辊轴线,断裂面与轧辊轴线垂直,一般发生在辊身中部,如图1所示。
图1:热应力断裂断面形状2.1.1.2轧辊破坏原因这种热应力断裂与轧辊表面和轴心处的最大温差有关。
过高的温差通常是由于轧辊表面温度升高过快造成的,产生的原因有,轧制过程中轧辊冷却水不足甚至中断,或者轧制钢开始时轧制节奏太快,轧制量过大造成的。
有资料表明,在辊役刚开始的临界轧制状态下,辊身表面与轴心之间70℃的温差就可沿轴向产生110Mpa的附加热应力。
一旦辊芯中总的轴向拉伸应力超过了材质的极限强度,就会导致突然的热应力断裂破坏。
以我厂为例,生产初期,有一次正值寒冬腊月,室外温度-20℃,厂房内温度较低,备辊正处在风口上,轧辊上线前没有预热,仅烫辊4块,在烫辊效果不好的前提下,温度较低的冷却水很快浇凉辊面,在轧制中与红钢接触,轧辊处于冷热交替中,内外表面温差大。
断辊后约10分钟,用手摸断辊边缘,触觉为凉辊,带钢轧制部位的轧辊表面微温,轧辊断口内触觉发凉。
轧辊失效形式
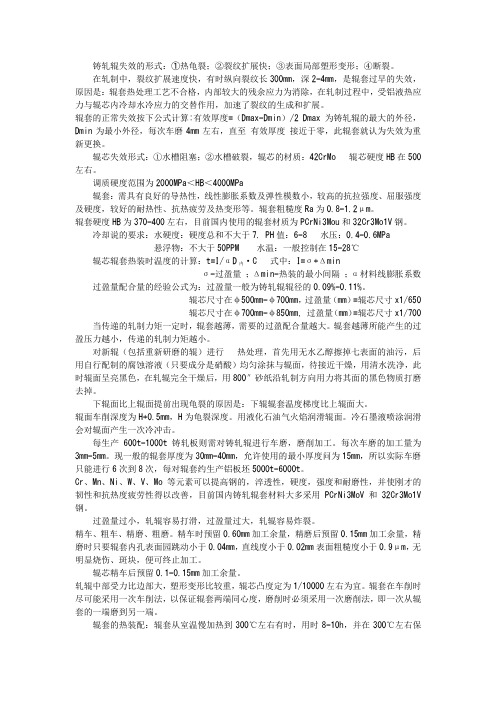
铸轧辊失效的形式:①热龟裂;②裂纹扩展快;③表面局部塑形变形;④断裂。
在轧制中,裂纹扩展速度快,有时纵向裂纹长300mm,深2-4mm,是辊套过早的失效,原因是:辊套热处理工艺不合格,内部较大的残余应力为消除,在轧制过程中,受铝液热应力与辊芯内冷却水冷应力的交替作用,加速了裂纹的生成和扩展。
辊套的正常失效按下公式计算:有效厚度=(Dmax-Dmin)/2 Dmax为铸轧辊的最大的外径,Dmin为最小外径,每次车磨4mm左右,直至有效厚度接近于零,此辊套就认为失效为重新更换。
辊芯失效形式:①水槽阻塞;②水槽破裂,辊芯的材质:42CrMo 辊芯硬度HB在500左右。
调质硬度范围为2000MPa<HB<4000MPa辊套:需具有良好的导热性,线性膨胀系数及弹性模数小,较高的抗拉强度、屈服强度及硬度,较好的耐热性、抗热疲劳及热变形等。
辊套粗糙度Ra为0.8-1.2μm。
辊套硬度HB为370-400左右,目前国内使用的辊套材质为PCrNi3Mou和32Cr3Mo1V钢。
冷却说的要求:水硬度:硬度总和不大于7. PH值:6-8 水压:0.4-0.6MPa悬浮物:不大于50PPM 水温:一般控制在15-28℃辊芯辊套热装时温度的计算:t=I/αD内·C 式中:I=σ+Δminσ-过盈量;Δmin-热装的最小间隔;α材料线膨胀系数过盈量配合量的经验公式为:过盈量一般为铸轧辊辊径的0.09%-0.11%。
辊芯尺寸在φ500mm-φ700mm,过盈量(mm)=辊芯尺寸x1/650辊芯尺寸在φ700mm-φ850mm, 过盈量(mm)=辊芯尺寸x1/700 当传递的轧制力矩一定时,辊套越薄,需要的过盈配合量越大。
辊套越薄所能产生的过盈压力越小,传递的轧制力矩越小。
对新辊(包括重新研磨的辊)进行热处理,首先用无水乙醇擦掉七表面的油污,后用自行配制的腐蚀溶液(只要成分是硝酸)均匀涂抹与辊面,待接近干燥,用清水洗净,此时辊面呈亮黑色,在轧辊完全干燥后,用800″砂纸沿轧制方向用力将其面的黑色物质打磨去掉。
轧辊轴承失效的原因
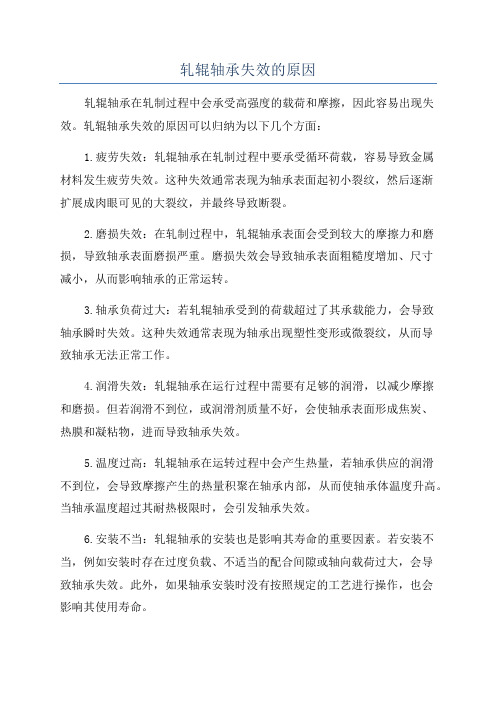
轧辊轴承失效的原因轧辊轴承在轧制过程中会承受高强度的载荷和摩擦,因此容易出现失效。
轧辊轴承失效的原因可以归纳为以下几个方面:1.疲劳失效:轧辊轴承在轧制过程中要承受循环荷载,容易导致金属材料发生疲劳失效。
这种失效通常表现为轴承表面起初小裂纹,然后逐渐扩展成肉眼可见的大裂纹,并最终导致断裂。
2.磨损失效:在轧制过程中,轧辊轴承表面会受到较大的摩擦力和磨损,导致轴承表面磨损严重。
磨损失效会导致轴承表面粗糙度增加、尺寸减小,从而影响轴承的正常运转。
3.轴承负荷过大:若轧辊轴承受到的荷载超过了其承载能力,会导致轴承瞬时失效。
这种失效通常表现为轴承出现塑性变形或微裂纹,从而导致轴承无法正常工作。
4.润滑失效:轧辊轴承在运行过程中需要有足够的润滑,以减少摩擦和磨损。
但若润滑不到位,或润滑剂质量不好,会使轴承表面形成焦炭、热膜和凝粘物,进而导致轴承失效。
5.温度过高:轧辊轴承在运转过程中会产生热量,若轴承供应的润滑不到位,会导致摩擦产生的热量积聚在轴承内部,从而使轴承体温度升高。
当轴承温度超过其耐热极限时,会引发轴承失效。
6.安装不当:轧辊轴承的安装也是影响其寿命的重要因素。
若安装不当,例如安装时存在过度负载、不适当的配合间隙或轴向载荷过大,会导致轴承失效。
此外,如果轴承安装时没有按照规定的工艺进行操作,也会影响其使用寿命。
针对以上原因,可以采取以下措施来延长轧辊轴承的寿命:1.选择合适的轴承:根据轧辊轴承的工作条件和载荷大小,选择合适的轴承类型、规格和材料,使其能够承受工作环境中的载荷。
2.加强润滑管理:采用合适的润滑方式和润滑剂,确保轧辊轴承在工作过程中有足够的润滑。
同时,定期检查和更换润滑剂,清洗轴承表面,以避免润滑失效引发的问题。
3.控制负荷:通过改变轧辊间距、调整轧机参数等方式,减少轧辊轴承受到的负荷。
同时,注意控制轧机的工作温度,避免轴承过热。
4.正确安装轴承:遵循正确的安装工艺,确保轧辊轴承按照规定的预压力安装,并检查轴承的配合间隙和轴向负荷是否符合要求。
轧制过程中断辊原因
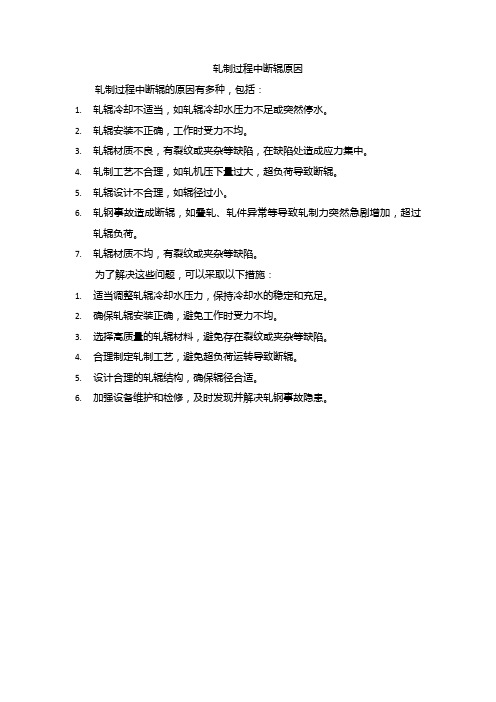
轧制过程中断辊原因
轧制过程中断辊的原因有多种,包括:
1.轧辊冷却不适当,如轧辊冷却水压力不足或突然停水。
2.轧辊安装不正确,工作时受力不均。
3.轧辊材质不良,有裂纹或夹杂等缺陷,在缺陷处造成应力集中。
4.轧制工艺不合理,如轧机压下量过大,超负荷导致断辊。
5.轧辊设计不合理,如辊径过小。
6.轧钢事故造成断辊,如叠轧、轧件异常等导致轧制力突然急剧增加,超过
轧辊负荷。
7.轧辊材质不均,有裂纹或夹杂等缺陷。
为了解决这些问题,可以采取以下措施:
1.适当调整轧辊冷却水压力,保持冷却水的稳定和充足。
2.确保轧辊安装正确,避免工作时受力不均。
3.选择高质量的轧辊材料,避免存在裂纹或夹杂等缺陷。
4.合理制定轧制工艺,避免超负荷运转导致断辊。
5.设计合理的轧辊结构,确保辊径合适。
6.加强设备维护和检修,及时发现并解决轧钢事故隐患。
热轧轧辊失效分析及预防措施
联 系人 : 占福, 3 岁 , 马 男, 7 博士生 , 轧钢工程师, 乌鲁木齐( 3 o 2 新疆八一钢铁股份有限公司 802 )
E-mai maf y t O 11 l z@b g. B.1 : C 3
~
36 按 制 造工 艺 分 为 铸 造 、 造 、 末 冶 金 、 .%; 锻 粉 喷
射成型 、 堆焊热喷涂等 ; 按结构分为整体辊 、 复合辊 、
镶 装辊 等 ;按 功 能分 为 连铸 辊 、热 轧辊 、冷轧 辊 、
S nm r 、 艺辊 、 道 等 e z i辊 工 辊 。
3 轧 辊 的 失 效 形 式
1 前 言
轧辊是使金属产生塑性变形的一种生产工具, 其在 实 际生产使 用 中 , 于一种 复杂 的应力 状态 , 处 如
轧 辊与 轧件 接 触加 热 、 辊水 冷 却 引起 的周期 性 热 轧 应力 、 轧制 负荷 引起 的接触 应力 、 剪切 应力 以及残 余 应力 等川 。如果轧 辊 的材质 、 加工 、 生产 、 操作 等工 艺
3 1 断 裂 .
不合理 , 就会使轧辊失效 , 出现剥落、 断裂、 辊面损伤 等情况, 任何一种失效形式都会直接导致轧辊寿命
缩短 , 至造 成轧 辊报废 , 甚 因此分 析轧辊 的失 效形 式
轧辊在 生产 中往 往会 发生 突然 断辊事 故 ,其 断
裂部位 主要 为工 作辊 的辊 身 、 颈及 轴头部 位 。 辊 断辊 因轧 制 不 同钢种 、 同品种 、 同 的生 产 工艺 条件 , 不 不 其断裂 部位 有所 不 同。 断裂形 式来 看 , 可能是 一 从 有 次性 的脆断 ,也 可能是 由于疲劳 裂纹 而导致 断辊 l 3 _ ,
可从 内因 、 因两 方面来 分 析 ( 图 1 。 外 如 )
冷轧辊的失效分析
冷轧辊的失效分析材料工程1306封骥2013153冷轧辊的失效分析冷轧辊是冷轧机的大宗消耗备品,其能否安全运行将直接影响着轧机的生产率、成材率以及成本控制。
由于冷轧辊从材质、制造工艺、使用、维护及失效等诸方面与热轧辊有着较大的差异,故对初次进行冷轧生产的单位、轧辊管理者及使用者来说,需要掌握冷轧辊的失效机理及预防措施,通过对冷轧辊失效机理的论述及案例的相关分析,提出降低轧辊消耗的预防措施。
失效:金属装备及其构件在使用过程中,由于压力、时间、温度和环境介质和操作失误等因素的作用,丧失其规定功能的现象。
失效分析:对装备及其构件在使用过程中发生各种形式失效现象的特征及规律进行分析研究,从中找出产生失效的主要原因及防止失效的措施,称为失效分析。
失效分析的一般过程①深入装备失效现场、广泛收集、调查失效信息,寻找失效构件及相关实物证据。
②对失效构件进行全面深入的宏观分析,通过种类认定推理,初步确定失效件的失效类型。
③对失效件及其相关证物展开必要的微观分析、理化检验,进一步查找失效的原因。
④通过归纳、演绎、类比、假设、选择性推理,建立整个失效过程及其失效原因之间的联系,进行综合性分析。
⑤在可能的情况下,对重大的失效事件进行模拟试验,验证因果分析的正确性。
一、冷轧辊失效机理冷轧辊特性:目前冷轧厂常用的冷轧辊材质有高碳铬铝系及高碳铬铝钒系,一般生产工艺过程为电渣重熔或钢包精炼——铸锭——锻造——球化退火——粗加-——探伤——调质——精加工——探伤——工频感应淬火——低温回火——精加工成品。
为确保优良的使用性能,其表层组织要求为细针马氏体、隐针马氏体+少量残余奥氏体+粒状碳化物。
冷轧工作辊工作时要承受高的轧制压力、冲击载荷、疲劳及磨损,需要有足够的强度抵抗大的弯深而均匀的表面硬化层及耐磨层,以获得良好的耐磨性;三是要有优良的表层抗裂性及抗剥落性能。
冷轧辊的失效形式:冷轧工作辊工作时处于复杂的应力状态。
受残余应力、接触应力、弯曲应力、扭转应力以及因温度分布不均引起的热应力等的影响,失效形式有早期磨损、粗糙化、略坑、勒痕、裂纹、剥落以及断裂,但工作层剥落是冷轧辊的主要失效形式,占到工作辊正常失效的50%以上,轧辊剥落往往造成轧辊彻底报废。
轧机上断辊的原因分析
断裂原因一、脆性断裂,此类轧辊断口形状较为平整,断口周围辊身表面较为齐整;二、韧性断裂,此类轧辊断口形状多呈"蘑菇头"状,断口附近的辊身均成粉碎状破碎。
将二者比对发现,此次断辊事故的断辊形式为韧性断裂。
脆性断裂和韧性断裂都是因为轧辊应力超过芯部强度造成的。
其产生原因与轧辊本身残余应力,轧制时机械应力以及轧辊热应力有关,特别是当辊身的表面和芯部的温差大时更容易产生。
这种温差可能由不良的辊冷却,冷却中断或在新的轧制周期开始时轧辊表面过热引起。
轧辊的这种表面和芯部间的巨大温差引起较大的热应力,当较大的热应力,机械应力以及轧辊的残余应力超过轧辊的芯部强度时引起断辊。
例如,轧辊表面和芯部间的温差在70℃时轧辊会增加100MPa的纵向热应力,温差越大,增加的热应力越大。
与产生脆性断口的轧辊相比较,产生韧性断口的轧辊的芯部材料韧性更好,更不容易出现断裂。
导致轧辊失效的应力共有四种:一、制造过程中的残余应力;二、轧制过程中的机械应力;三、轧制过程中轧辊的组织应力;四、轧辊内外温差造成的热应力。
如果是因为制造残余应力过大产生断裂,断辊通常发生在轧辊初始上机使用的前几次,且为开轧的前几块轧材。
此次断裂的轧辊已经上机轧制了四次,工作层消耗了14mm,因此不应是因制造残余应力形成的断裂。
如果是因为机械应力产生的断裂,需要很大的机械应力。
经粗略计算,如此大截面的高铬铸钢轧辊若被机械应力拉断,则需要100MN 以上的拉力,对于该轧辊工作的轧机来说这是不可能的。
轧辊受力最大的部位是传动端辊颈,如果材料的力学性能指标不足,正常轧制情况下首先损坏的是传动端辊颈。
从实际轧制和断辊情况来看,不是由于机械应力造成辊身断裂。
对组织应力影响最大的就是外层组织中残余奥氏体含量。
残余奥氏体在轧制温度,轧制压力和水冷的交变作用下,发生奥氏体向马氏体或贝氏体的转变,由于奥氏体的比容小,而马氏体的比容大,因而在组织转变的过程中伴随着体积的膨胀,会致使轧辊的工作层产生更大的压应力,芯部产生更大的拉应力,芯部应力一旦超过材料的强度,必然造成轧辊断裂。
热轧轧辊的失效原因及科学预防
热轧轧辊的失效原因及科学预防摘要轧辊的失效形式主要包括剥落、断裂、裂纹等,无论哪种失效都会影响轧辊的使用寿命。
因此,为延长轧辊使用寿命、降低轧辊消耗,必须要针对不同的失效原因,采取科学性、针对性的预防措施。
基于此,本文对轧辊失效的原因进行了阐述,并分析了科学的预防措施,旨在为提高轧辊的使用寿命,提升轧辊质量,提供参考借鉴。
关键词轧辊失效;应力;剥落;裂纹;预防1 轧辊常见失效形式及原因1.1 剥落剥落的发生不是瞬间的,而是需要一个疲劳的过程,轧辊的非正常失效形式中剥落占比达60%~70%,属于较为严重的生产事故,严重时会导致轧辊报废。
其主要形式及原因为:首先,马鞍形剥落。
在对薄而硬的带钢进行轧制时,由于压下比大,使得在承受较大负荷的作用下而产生交变应力、残留应力及热应力,会使拉应力变大,一旦超过轧辊芯部材质的疲劳极限,就会导致出现微裂纹。
裂纹的进一步蔓延,就会表现在辊身表面,致使产生马鞍形剥落。
其次,带状疲劳剥落。
轧辊局部过大超负荷运转时,当大于轧辊外层的抗剪切强度极限时,就会出现裂纹,在进行轧制过程中,持续的疲劳状态会引发裂纹的增多,致使辊身局部出现大面积剥落。
另外,对于服役期较长的工作辊和支承辊,中间磨损量大于两端磨损量,致使辊身两端交变剪应力不断增大,加速了疲劳破坏,从而产生带状疲劳剥落。
另外,表层/芯部结合层处脱落。
在发生轧制事故时,局部出现过大负荷,导致外部与芯部材质出现脱落,随着这一分割面的逐渐延伸,一旦达到临界尺寸,就会出现二次脱落。
这种形式的剥落出现通常有以下几种情况,表层和芯部间有氧化层残留,结合层留有杂质、碳化物或是气孔等。
1.2 断裂轧制过程中的断辊事故时有发生,断裂通常发生在辊身、辊颈及轴头部位。
当钢种以及生产工艺存在差异時,断裂的部位也会出现差异。
通常,断辊是由于疲劳裂纹所致,也可能会出现一次性脆断,具体分析如下:(1)内因在轧辊的材质内部存在缺陷时,引发轧辊断裂的可能性也会增大,例如,钢材球化率低、渗碳体数量过高、局部晶粒不均匀以及结构疏松等缺陷,非正常情况下的芯部组织致使机械性能降低,在承受的热应力大于材料抗拉强度时,轧辊内部的材质出现局部裂纹,裂纹逐步蔓延最终导致轧辊断裂。
- 1、下载文档前请自行甄别文档内容的完整性,平台不提供额外的编辑、内容补充、找答案等附加服务。
- 2、"仅部分预览"的文档,不可在线预览部分如存在完整性等问题,可反馈申请退款(可完整预览的文档不适用该条件!)。
- 3、如文档侵犯您的权益,请联系客服反馈,我们会尽快为您处理(人工客服工作时间:9:00-18:30)。
轧辊失效方式及其原因分析
轧机在轧制生产过程中,轧辊处于复杂的应力状态。
热轧机轧辊的工作环境更为恶劣:轧辊与轧件接触加热、轧辊水冷引起的周期性热应力,轧制负荷引起的接触应力、剪切应力以及残余应力等。
如轧辊的选材、设计、制作工艺等不合理,或轧制时卡钢等造成局部发热引起热冲击等,都易使轧辊失效。
轧辊失效主要有剥落、断裂、裂纹等形式。
任何一种失效形式都会直接导致轧辊使用寿命缩短。
因此有必要结合轧辊的失效形式,探究其产生的原因,找出延长轧辊使用寿命的有效途径。
1 、轧辊剥落(掉肉)
轧辊剥落为首要的损坏形式,现场调查亦表明,剥落是轧辊损坏,甚至早期报废的主要原因。
轧制中局部过载和升温,使带钢焊合在轧辊表面,产生于次表层的裂纹沿径向扩展进入硬化层并多方向分枝扩展,该裂纹在逆向轧制条件下即造成剥落。
1.1 支撑辊辊面剥落
支撑辊剥落大多位于轧辊两端,沿圆周方向扩展,在宽度上呈块状或大块片状剥落,剥落坑表面较平整。
支撑辊和工作辊接触可看作两平行圆柱体的接触,在纯滚动情况下,接触处的接触应力为三向压应力。
在离接触表面深度为 0.786b 处 ( b 为接触面宽度之半 ) 剪切应力最大,随着表层摩擦力的增大而移向表层。
疲劳裂纹并不是发生在剪应力最大处,而是更接近于表面,即在 Z 为 0.5b 的交变剪应力层处。
该处剪应力平行于轧辊表面,据剪应力互等定理,与表面垂直的方向同样存在大小相等的剪应力。
此力随轧辊的转动而发生大小和方向的改变,是造成接触疲劳的根源。
周期交变的剪切应力是轧辊损坏最常见的致因。
在交变剪切应力作用下,反复变形使材料局部弱化,达到疲劳极限时,出现裂纹。
另外,轧辊制造工艺造成的材质不均匀和微型缺陷的存在,亦有助于裂纹的产生。
若表面冷硬层厚度不均,芯部强度过低,过渡区组织性能变化太大,在接触应力的作用下,疲劳裂纹就可能在硬化过渡层起源并沿表面向平行方向扩展,而形成表层压碎剥落。
支撑辊剥落只是位于辊身边部两端,而非沿辊身全长,这是由支撑辊的磨损型式决定的。
由于服役周期较长,支撑辊中间磨损量大、两端磨损量小而呈 U 型,使得辊身两端产生了局部的接触压力尖峰、两端交变剪应力的增大,加快了疲劳破坏。
辊身中部的交变剪应力点,在轧辊磨损的推动作用下,逐渐往辊身内部移动至少 0.5mm ,不易形成疲劳裂纹;而轧辊边部磨损较少,最大交变剪应力点基本不动。
在其反复作用下,局部材料弱化,出现裂纹。
轧制过程中,辊面下由接触疲劳引起的裂纹源,由于尖端存在应力集中现象,从而自尖端以与辊面垂直方向向辊面扩展,或与辊面成小角度以致呈平行的方向扩展。
两者相互作用,随着裂纹扩展,最终造成剥落。
支撑辊剥落主要出现在上游机架,为小块剥落,在轧辊表面产生麻坑或椭球状凹坑,分布于与轧件接触的辊身范围内。
有时,在卡钢等情况下,则出现沿辊身中部轴向长达数百毫米的大块剥落。
1.2 工作辊辊面剥落
工作辊剥落同样存在裂纹产生和发展的过程,生产中出现的工作辊剥落,
多数为辊面裂纹所致。
工作辊与支撑辊接触,同样产生接触压应力及相应的交变剪应力。
由于工作辊只服役几个小时即下机进行磨削,故不易产生交变剪应力疲劳裂纹。
轧制中,支撑辊与工作辊接触宽度不到 20mm ,工作辊表面周期性的加热和冷却导致了变化的温度场,从而产生显著的周期应力。
辊面表层受热疲劳应力的作用,当热应力超过材料的疲劳极限时,轧辊表面便产生细小的网状热裂纹,即通称的龟裂。
轧制中发生卡钢等事故,造成轧辊局部温度升高而产生热应力和组织应力。
轧件的冷头、冷尾及冷边引起的显著温差,同样产生热应力。
当轧辊应力值超过材料强度极限时产生热冲击裂纹。
在轧制过程中,带钢出现甩尾、叠轧时,轧件划伤轧辊,亦可形成新的裂纹源。
另外,更换下来的轧辊,尤其上游机架轧辊,多数辊面上存在裂纹,应在轧辊磨削时全部消除。
如轧辊磨削量不够,裂纹残留下来,在下一次使用时这些裂纹将成为疲劳核心。
轧辊表面的龟裂等表层裂纹,在工作应力、残余应力和冷却引起的氧化等作用下,裂纹尖端的应力急剧增加并超过材料的允许应力而朝轧辊内部扩展。
当裂纹发展成与辊面成一定的角度甚至向与辊面平行的方向扩展,则最终造成剥落。
轧辊剥落问题 , 大多数剥落与六类轧机操作和轧辊使用不当有关:如轧制量过高、换辊周期过长、轧辊修磨量不足、冲击载荷、轧辊工作面压力分布不均、轧制时停机造成轧辊内部温度分布不均、热冲击等。
前四种情况常与轧辊亚表层赫兹应力有关,应力作用产生的裂纹向内或向外扩展产生剪切破坏,导致剥落。
后两种情况 , 易造成内部裂纹按螺旋方式扩展成表面裂纹,导致大块剥落。
改善轧辊抗剥落性的措施有:提高轧辊的显微组织及硬度均匀性;保证适当的淬透性;提高轧辊的剪切强度和塑性,降低轧辊残余应力。
对中厚板轧机,在辊身边部时常会遇有掉肩(烂肩)剥落现象发生,避免轧辊边部剥落措施是支撑辊带倒角。
带倒角支撑辊是将支撑辊辊身两端 250mm 宽倒一棱角约 -1mm 。
倒角 ( 曲线 ) 量采用仿真计算,其依据是轧制最大板宽时不至发生过大的反凸度,从而避免轧辊边部产生应力集中和剥落。
2 、轧辊断裂
轧辊在工作过程中还常常发生突然断辊事故,其断裂部位主要为工作辊的辊身、辊颈处、辊脖与辊颈交界处。
因轧制钢种、品种与生产工艺条件差异,各断裂部位所占比例不同。
断辊可以是一次性的瞬断,也可以是由于疲劳裂纹发展而致。
根据柯垂尔脆断条件: ( τD/2 + K) K≥4 Gγ时,才发生脆断。
其中τ——应力;
D——晶粒直径;
K——系数;
G——材料的弹性模量;
γ——有效表面能。
也就是说,当τ和D较大时,易发生脆性断裂,脆性断裂的断面总体平齐。
对高铬复合铸铁轧辊,如果轧辊热处理回火不充分 , 外层组织中会含有大量马氏体、残余奥氏体 , 导致轧辊铸态应力较高,亦即τ值增大;τ与D
的增大 , 是轧辊断裂的内因。
轧制机械应力、热应力的叠加是造成辊断裂的外因。
锻造工艺不当也会导致轧辊脆性断裂。
如终锻温度过低,易形成位于轧辊心部附近其形貌具有“ 人” 字形特征的裂纹。
若加上在终锻时控制不当,很容易造成穿晶型裂纹。
在锻造变形时,热加工压力过小,变形不合理造成心部未锻透,仅钢材表面产生塑性变形而内部产生拉应力,当此拉应力超过该区的金属强度时,即可引起内部横裂。
脆性断裂总是以轧辊内部存在的裂纹作为裂纹源。
如果轧辊内部存在大量裂纹,在服役过程中,裂纹尖端产生应力集中而快速扩展连接,形成一个较大的裂纹,这种裂纹在交变应力作用下,由内向外逐渐扩大,当裂纹大到一定程度时就发生疲劳断裂。
轧辊组织缺陷也会导致轧辊断裂,轧辊芯部组织不正常(球化率低,渗碳体数量过高等)导致机械性能显著下降。
这种轧辊使用时,由于芯部组织不正常,在热应力的作用下,较薄弱处先被拉裂,然后裂纹迅速扩展,也会导致轧辊断裂。
轧辊铸造缺陷是轧辊辊颈断裂的另一个原因。
如果辊颈截面存在铸造缺陷组织:较多大面积粗条状、网状渗碳体,心部疏松孔洞区等,都会使材料内应力增大,力学性能下降。
因此在辊身发生碰撞时,在外加震动应力与内应力的交互作用下,以脆性相和一些缺陷为核心,萌生出裂纹。
由于材料较脆,裂纹便立即扩展产生瞬间断裂。
除上述原因外,造成轧辊断裂的因素还有很多:简单的机械性过载;设计和加工不当,对于截面尺寸发生变化的部位,未设计足够的圆角或精密加工,致使应力集中;辊面和辊颈硬度相差过大;辊颈的直径过小,强度不够等都有可能导致轧辊断裂。
3 、轧辊裂纹
轧辊裂纹是由于多次温度循环产生的热应力所造成的逐渐破裂,是发生于轧辊表面薄层的一种微表面层现象。
轧制时,轧辊受冷热交替变化剧烈,从而在轧辊表面产生严重应变,逐渐导致热疲劳裂纹的产生。
此种裂纹是热循环应力、拉应力及塑性应变等多种因素形成的,塑性应变使裂纹出现,拉应力使其扩展。
4 、缠辊
热轧生产中,由于钢料加热温度不均,阴阳面温差大,卫板安装不稳,造成缠辊。
经常出现在轧制矿用支撑钢、矿用工字钢及轻轨的过程中。
有些缠辊经轧辊车削车间处理后可以使用,但修复量大,会严重减少轧辊的轧出量。
缠辊严重时报废,还可能影响到另外一 ( 两 ) 支轧辊,造成整套轧辊的报废。
因此,在孔型设计时,应着重考虑压力的配置,使钢料从孔型中平直出口;牢固安装卫板;保证钢料加热温度均匀,以防止缠辊现象发生。
5 、粘辊
在冷轧过程中,如果出现钢带漂移、堆钢、波浪折叠,且由于高压出现瞬间高温时,极易形成钢带与轧辊粘接,致使轧辊出现小面积损伤。
通过修磨,轧辊表面裂纹消除后可以继续使用,但其使用寿命明显降低,并在以后的使用中易出现剥落事故。
6 、烧轴承
轧辊在使用时,往往因轧辊轴承与辊轴配合间隙过小,润滑不好、辊轴与轴承热膨胀变形不同步、轴承制造质量差等原因,均可导致轴承与轧辊轴发生干磨擦,严重时导致轧辊轴断裂。
有效控制烧轴承事件发生,严格控制轴承质量与润滑效果,有效监控轧辊轴承箱温度,遇有异常问题发生即刻停止轧辊使用,更换轴承箱、强制轴承润滑,可解决此问题。
轧辊的损坏由多种因素相互影响和相互作用引起,其损坏形式也多样。
但只要了解轧辊损坏原因,针对具体的轧机系统、损坏形式采取相应措施,轧辊失效可以得到有效控制,可以最大限度降低辊耗,从而提高轧辊的使用寿命,提高轧钢生产效率。