如何提高变压吸附装置产品回收率的经验总结
提高变压吸附单元氢气收率的措施
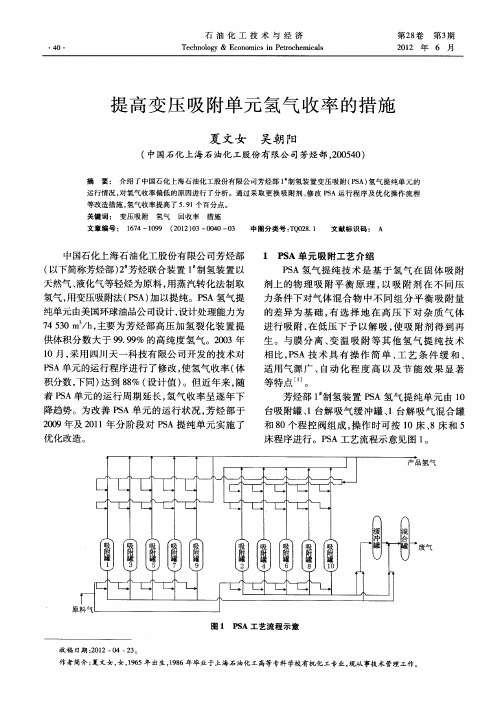
4 1 1 更 换 吸 附剂 ..
20 0 9年 1 2月 , 装 置 原 料 适 应 性 改 造 期 间 在
( 原料 由轻石脑 油改 为 天然 气 )对 原 先 使用 的吸 ,
附剂 进行 了更 换 。 P A单 元各 吸 附罐 的吸附剂 重新 装填 情况 见 S
到 20 09年该 吸 附剂 已超 过 预期使 用寿命 , 能逐 性 步下 降 ; 同时 由于原装 填 的吸 附剂种类 单一 , 能 不
适 应处 理含 有微 量 水 、 甲烷 和 二 氧化 碳 含 量 较 高
的原料 , 由于 吸附剂 的密 度较低 , 装填 数量较 且 其
少, 造成 P A单罐 吸 附时 问逐 渐 缩 短 , 洗 、 S 冲 逆放
再 生时 间相对 减少 , 导致 产 品收率 下 降 。
3 3 P A 工艺 的影 响 . S
自 20 03年修 改 运 行程 序 以来 ,S PA单 元 负 荷 基本 维持 在 3% ~ 0 , 0 9 % 运行 初 期 氢 气 收 率 达 到
8 % 。近 年来 由于各 种原 因 ,S 8 P A氢气 提纯 单元 产
表 3 运 行 程 序 优 化 前 后 工 艺 参 数 对 比
运行 程 序 工 艺 参数
1 —3 —4 P 0 . . / 1 — — /P 0— 2—4
艺 原设 计 中没有 设 置顺 放气 缓 冲罐 , 对 而 言 吸 相 附剂 再生效 果较 差 , 响了产 品 的收 率 。 影
项 目
, 、
扫可能带来 的杂质析 出进 而污染被 吹扫床 的问题 ;
20 08年 20 0 8年 20 0 9年 2 0 0 9年 设 计值 ” 4月 1 0月 8月 1 0月
变压吸附提氢装置氢收率低的原因分析及改进措施
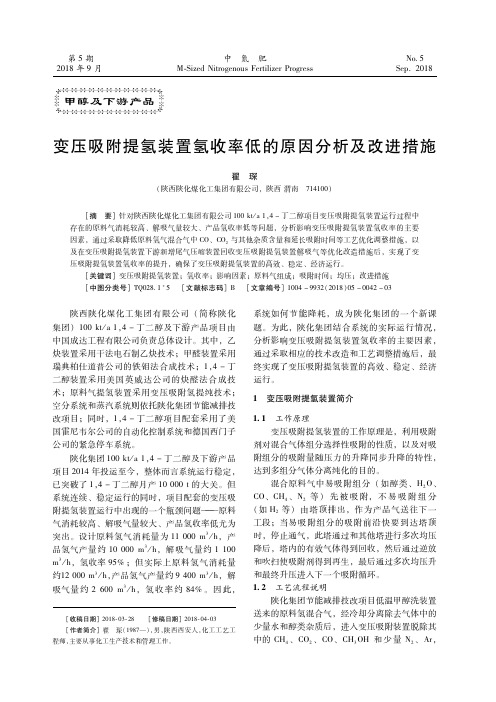
中 氮 肥 MSizedNitrogenousFertilizerProgress
櫋櫋櫋櫋櫋櫋櫋櫋櫋櫋櫋殹
甲醇及下游产品
No5 Sep.2018
櫋櫋殹
櫋櫋殹
櫋櫋櫋櫋櫋櫋櫋櫋櫋櫋櫋殹
变压吸附提氢装置氢收率低的原因分析及改进措施
翟 琛
(陕西陕化煤化工集团有限公司,陕西 渭南 714100)
变压吸附提氢装置于 2014年投运,原设计 程序为 14—1—11双冲洗流程,即变压吸附提氢 装置的 14台吸附塔中有 1台吸附塔始终处于进 料吸附的状态,其吸附和再生工艺过程由吸附、 连续 11次均压降、逆放、冲洗、连续 11次均压 升和最终升压等步骤组成。
但随着变压吸附提氢装置运行时间的延长, 其氢收率呈逐年下降趋势。经过对原设计程序的 多次修改后,实际运行程序为 14—1—9流程, 即 14台吸附塔中有 1台吸附塔始终处于进料吸 附的状态,其吸附和再生工艺过程由吸附、连续 9次均压降、逆放、冲洗、连续 9次均压升和最 终升压等步骤组成。装置原料氢气消耗约 12000 m3/h,产品氢气产量约 9400m3/h,氢收率约 84%,远低于设计值。
[摘 要]针对陕西陕化煤化工集团有限公司 100kt/a1,4-丁二醇项目变压吸附提氢装置运行过程中 存在的原料气消耗较高、解吸气量较大、产品氢收率低等问题,分析影响变压吸附提氢装置氢收率的主要 因素,通过采取降低原料氢气混合气中 CO、CO2与其他杂质含量和延长吸附时间等工艺优化调整措施,以 及在变压吸附提氢装置下游新增尾气压缩装置回收变压吸附提氢装置解吸气等优化改造措施后,实现了变 压吸附提氢装置氢收率的提升,确保了变压吸附提氢装置的高效、稳定、经济运行。
提高变压吸附装置的产品回收率

装置的产品回收率成为 目前需要研究解决的课题 。 提高 回收率的工作 ,无论在变压吸附的设计还
是实际的生产操作 中均成为人们攻关 的主要方向。
因为提高了装置的回收率 ,等同于减少了原料气的
1 产 品回收率的计 算
M e s r so m p o i g Th c v r fPS a u e fI r vn e Re o e y o A
F N h — o A Z ia t
(H b i  ̄ghuD h aT I o ,Ld ,C nzo 6 0 0 hn ee l o au D . t. aghu0 10 ,C ia) C z C
附容量和吸附剂 的分离系数 ,来提高产品回收率。
收稿 日期 :20 -92 0 50 -6
维普资讯
3 4
低 温 与 特 气
第 2 卷 4
吸附容量是指单位质量吸附剂所能吸附气体的
改造前顺 向放压夹在了 2 次均压降中间 ,通过
体积或质量。吸附剂的分离系数是指强、弱组分分 对均压方式进行改造 ,顺向放压设置在连续 3次均 别在死空间中的含量 占床内存 留量的 比值之比。只 压降后 ,降低了气体放空的压力 ,增加 了气体 回收 有吸附容量大、分离系数高的吸附剂 ,才能把气体 率 。例如 ,顺放 前压 力为 09 P ,顺放结束 后 .8 M a 最大程度的分离 ,使产品回收率最大化 。 为 06 P ,有 0 3M a .8M a . P 的气体和压力不能 回收。
Ke O d :P A ;r c v r yW r s S e o ey
0 前
言
效组分绝对数量和原料气中有效组分绝对数量的百 分 比值进行计算。
提升轻烃回收装置运行效率的措施
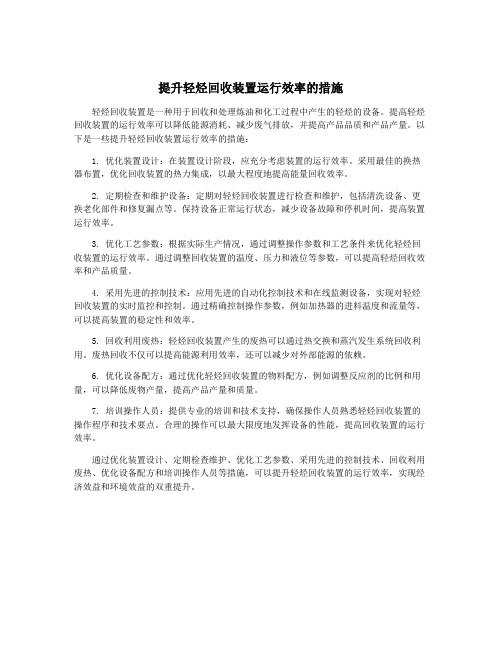
提升轻烃回收装置运行效率的措施轻烃回收装置是一种用于回收和处理炼油和化工过程中产生的轻烃的设备。
提高轻烃回收装置的运行效率可以降低能源消耗、减少废气排放,并提高产品品质和产品产量。
以下是一些提升轻烃回收装置运行效率的措施:1. 优化装置设计:在装置设计阶段,应充分考虑装置的运行效率。
采用最佳的换热器布置,优化回收装置的热力集成,以最大程度地提高能量回收效率。
2. 定期检查和维护设备:定期对轻烃回收装置进行检查和维护,包括清洗设备、更换老化部件和修复漏点等。
保持设备正常运行状态,减少设备故障和停机时间,提高装置运行效率。
3. 优化工艺参数:根据实际生产情况,通过调整操作参数和工艺条件来优化轻烃回收装置的运行效率。
通过调整回收装置的温度、压力和液位等参数,可以提高轻烃回收效率和产品质量。
4. 采用先进的控制技术:应用先进的自动化控制技术和在线监测设备,实现对轻烃回收装置的实时监控和控制。
通过精确控制操作参数,例如加热器的进料温度和流量等,可以提高装置的稳定性和效率。
5. 回收利用废热:轻烃回收装置产生的废热可以通过热交换和蒸汽发生系统回收利用。
废热回收不仅可以提高能源利用效率,还可以减少对外部能源的依赖。
6. 优化设备配方:通过优化轻烃回收装置的物料配方,例如调整反应剂的比例和用量,可以降低废物产量,提高产品产量和质量。
7. 培训操作人员:提供专业的培训和技术支持,确保操作人员熟悉轻烃回收装置的操作程序和技术要点。
合理的操作可以最大限度地发挥设备的性能,提高回收装置的运行效率。
通过优化装置设计、定期检查维护、优化工艺参数、采用先进的控制技术、回收利用废热、优化设备配方和培训操作人员等措施,可以提升轻烃回收装置的运行效率,实现经济效益和环境效益的双重提升。
变压吸附法制氧提高纯度和收率的分析研究
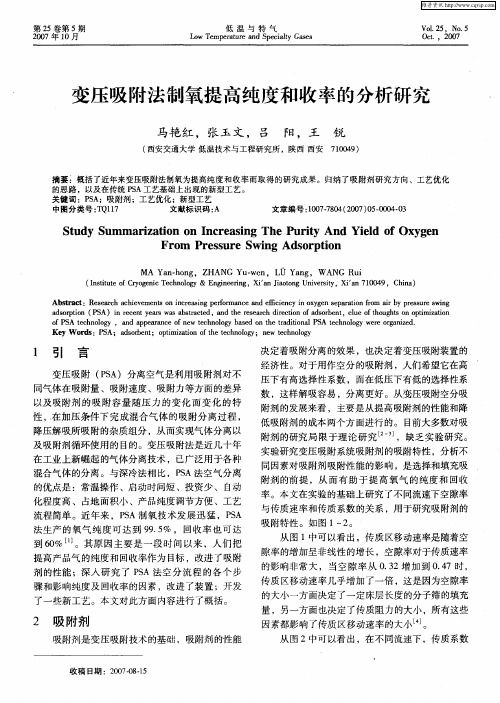
1 引 言
变压 吸 附 (S 分离空 气是利 用 吸附剂 对不 PA) 同气体在 吸 附量 、吸附速度 、吸 附力 等方面 的差异
以及吸 附剂 的 吸 附容 量 随 压力 的变 化 而变 化 的特
决 定着 吸附分离 的效果 ,也决 定着变 压吸附装置 的 经 济性 。对于用作 空分 的吸附剂 ,人们 希望它在高
asrt n( S dopi P A)i rcn ya a bt c d adter erhdrco f dobn, l fhuhs not i t n o n eet er W as at , e a i t no sret c eo ogt o p mz i s s r e n h s c ei a u t i ao
Ab t a t e e rh a h e e n so n r a ig p r r n e a d e iin y i x g n s p a in f m i b r su es n sr c :R s ac c iv me t n i ce n e f ma c f ce c n o y e e a t o ar y p e s r wig s o n r o r
Fr m e s e S ng Ad o pto o Pr s ur wi s r i n
MA n h n Ya — o g, ZHANG Yu— n, LU n we Ya g, W ANG Rui
(ntueo roei T cnl y& E g er g X i t gU i rt, i n7 0 9 h a Ist f ygnc eho g it C o ni ei , i J o n nv sy X 压条件 下 完 成混 合气 体 的吸 附分 离过 程 , 降压解 吸所 吸附的 杂质组分 ,从而实 现气体 分离 以 及 吸 附剂 循环使 用 的 目的。变压 吸附法是近 几十年 在 工业上 新 崛起 的气 体分离 技术 ,已广泛用 于各种 混 合气 体的分 离 。与深冷法 相 比 ,PA法空 气分 离 S 的优点是 :常温 操作 、启动 时间短 、投资少 、 自动 化 程度高 、 占地面 积小 、产 品纯度 调节方便 、工艺 流程简单 。近年来 ,PA制 氧技 术发 展 迅猛 ,P A S S
提高变压吸附分离法H2收率的工艺改进
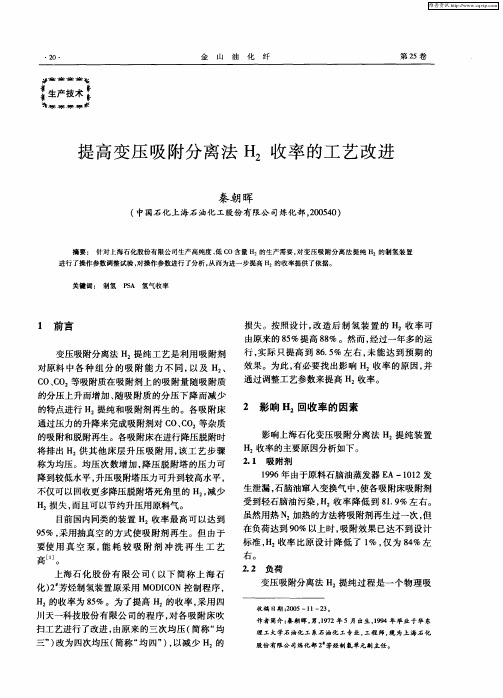
率 为 8 .% 。 61 实验 分三个 步骤 进行 。 第 一步 : 加 分周 期 时 间 以增 加 吸 附容 量 。 增
分周期时间先增加 1s为 7 , , 3s单塔吸附容
量上 升至 140m , 品 H 4 产 中 C O含 量逐 步 上 升
的分压上升而增加 、 随吸附质的分压下降而减少
: 的特点进行 H 提纯和吸附剂再生的。各 吸附床 2 影响 H 回收率的 因素 :
通过压力的升降来完成吸附剂对 C 、 O 等杂质 OC: 的吸附和脱附再生。各吸附床在进行降压脱附时 将排出 H 供其他床层升压吸附用 , : 该工艺 步骤 称为均压 。均压次数增加 , 降压脱 附塔 的压力 可 降到较低水平 , 升压吸附塔压力可升到较高水平 , 不仅可以回收更多降压脱附塔死角里的 H , :减少
2 3 低 杂质 含量 要求 .
维普资讯
金
山
油
化
纤
第2 5卷
业
业
业
;产 术 生技 : }
萧 萧 萧 萧
提 高 变 压 吸 附分 离 法 H 2收 率 的工 艺 改进
秦 朝 晖
( 国石化 上 海石 油化 工股 份有 限公 司炼化 部 ,050 中 20 4 )
摘要 : 针对上海石化股份有限公司生产高纯度 、 c 低 0含量 H 的生产需要 , 变压吸附分离法提纯 H 的制氢装 置 z 对 :
高 了吸 附剂再 生质量 , 但在 高负荷 情况 下 , 短 的 过 再 生时间 已直接 影 响到 吸附床再 生过 程 中最 为关 键 的排 放 和吹扫 两个 步骤 。排放 和吹扫 时 间太短 会降 低床层 再次 吸附 的能力 , 因此 , 负荷影 响 了 高
提高变压吸附脱碳装置运行效率总结
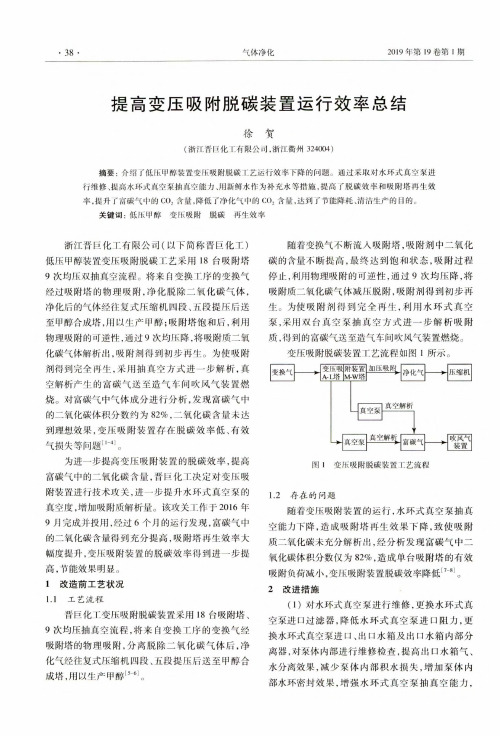
•38•气体净化2019年第19卷第1期提高变压吸附脱碳装置运行效率总结徐贺(浙江晋巨化工有限公司,浙江衢州324004)摘要:介绍了低压甲醇装置变压吸附脱碳工艺运行效率下降的问题。
通过采取对水环式真空泵进行维修、提高水环式真空泵抽真空能力、用新鲜水作为补充水等措施,提高了脱碳效率和吸附塔再生效率,提升了富碳气中的CO?含量,降低了净化气中的CO?含量,达到了节能降耗、清洁生产的目的。
关键词:低压甲醇变压吸附脱碳再生效率浙江晋巨化工有限公司(以下简称晋巨化工)低压甲醇装置变压吸附脱碳工艺采用18台吸附塔9次均压双抽真空流程。
将来自变换工序的变换气经过吸附塔的物理吸附,净化脱除二氧化碳气体,净化后的气体经往复式压缩机四段、五段提压后送至甲醇合成塔,用以生产甲醇;吸附塔饱和后,利用物理吸附的可逆性,通过9次均压降,将吸附质二氧化碳气体解析出,吸附剂得到初步再生。
为使吸附剂得到完全再生,采用抽真空方式进一步解析,真空解析产生的富碳气送至造气车间吹风气装置燃烧。
对富碳气中气体成分进行分析,发现富碳气中的二氧化碳体积分数约为82%,二氧化碳含量未达到理想效果,变压吸附装置存在脱碳效率低、有效气损失等问题【7。
为进一步提高变压吸附装置的脱碳效率,提高富碳气中的二氧化碳含量,晋巨化工决定对变压吸附装置进行技术攻关,进一步提升水环式真空泵的真空度,增加吸附质解析量。
该攻关工作于2016年9月完成并投用,经过6个月的运行发现,富碳气中的二氧化碳含量得到充分提高,吸附塔再生效率大幅度提升,变压吸附装置的脱碳效率得到进一步提高,节能效果明显。
1改造前工艺状况1.1工艺流程晋巨化工变压吸附脱碳装置采用18台吸附塔、9次均压抽真空流程,将来自变换工序的变换气经吸附塔的物理吸附,分离脱除二氧化碳气体后,净化气经往复式压缩机四段、五段提压后送至甲醇合成塔,用以生产甲醇[5_6]o随着变换气不断流入吸附塔,吸附剂中二氧化碳的含量不断提高,最终达到饱和状态,吸附过程停止,利用物理吸附的可逆性,通过9次均压降,将吸附质二氧化碳气体减压脱附,吸附剂得到初步再生。
提高CO回收率工艺改造总结

甘 肃聚银 化 工有 限公 司气 体 制 造厂 ( 以下 简
称聚银 公 司 ) 新 建 了 1套 水 煤 气 处 理 能 力 为
式, 即 6台吸 附器 中的 2台同 时进 料 、 两步 置换 和
抽空解 析 工 艺 。因 5 A 分 子 筛 对 原 料 气 中 的 C H , N 和 H : 分 离效 果 差 , 造 成 前 端工 艺 调 整 弹
连续 生产 的瓶 颈 。为 此 , 对制 C O工 序 进 行 了研 究分析, 利 用最 短 的 时 间和 最 低 的投 入 进 行 优化
设 计企业 进行 详细考 察 、 调研 , 通过 对改 造工艺 的 先进性 、 投 资 回报 期 、 生 产 成本 等 因 素 的 反 复 论 证、 对 比, 并 结合 企 业 自身 特 点 , 决定采 用 C O专
d o w n r a t i o o f p r e s s u r e s w i n g a d s o pt r i o n( P A S )u n i t i s h i g h , t h e q u a l i i f e d r a t i o o f p r o d u c t g a s r e a c h e s
8 5 0 0 m / h ( 标态 ) 的 变压 吸 附 ( P S A) 生产装置 , 用于分 离提 纯 生产 C O和 H ( 产 量 分 别 为
1 5 0 0 m / h和 4 0 0 0 m / h , 标 态) 。该 P S A装 置
性受限 、 损失增加 , 导 致后 段 产 品 的 质 量合 格 率 低、 收率 低 , 生产成 本大 大增加 。
Zh a n g Gu o y i ,L i Xi a o x i a,Di n g Li a n h e,S h i Yu ho n g,Ta n g Ho n g b i n
- 1、下载文档前请自行甄别文档内容的完整性,平台不提供额外的编辑、内容补充、找答案等附加服务。
- 2、"仅部分预览"的文档,不可在线预览部分如存在完整性等问题,可反馈申请退款(可完整预览的文档不适用该条件!)。
- 3、如文档侵犯您的权益,请联系客服反馈,我们会尽快为您处理(人工客服工作时间:9:00-18:30)。
如何提高变压吸附装置产品回收率的经验总结
摘要本文介绍了提高产品回收率的几种办法,通过这些办法和措施,使装置的回收率大幅提高,减少了原料气的消耗,降低了产品成本提高了变压吸附装置运行效率。
关键词回收率变压吸附吸附剂程控阀
一、前言
变压吸附(Pressure Swing Adsorption.简称PSA)是吸附分离技术中的一项用于分离气体混合物新型技术,其基本原理是利用气体组分在固体材料上吸附特性的差异以及吸附量随压力变化而变化的特性,通过周期性的压力变换过程实现气体的分离或提纯。
它有以下特点:⑴产品纯度高。
⑵操作简便、能耗低:一般可在室温和不高的压力下工作,床层再生不需外加热源,操作弹性大。
⑶工艺简单、维护简便:不需预先处理,即可一步除去杂质。
⑷吸附剂寿命长:吸附剂使用期限为半永久性。
由此可见变压吸附分离法,有着不可比拟的优点,但是存在产品回收率低的缺憾,对于如何提高产品回收率,无论是在变压吸附的设计还是在实际的生产操作中均成为人们攻关的主要方向。
二、在提高装置产品回收率上的几点经验总结
装置回收率的提高,等于减少了原料气的消耗,降低了产品成本。
我们在实际生产中根据运行经验总结了以下几种措施,用于提高装置的产品回收率。
2.1、程控阀问题
程控阀是变压吸附装置专用阀门,它的完好性是提高回收率的重要保障。
阀门的内漏和外泄漏会影响再生效果,导致产品回收率降低。
阀门在用材、安装和日常维护中要注意以下几点。
由于变压吸附工艺的特殊性,普通阀门难以保障装置长期稳定、可靠运行,对程控阀有以下要求:1、所用介质一般为高纯度的气体,所以密封性能要好,要达到零泄漏2、要求寿命长,做到经受长期频繁动作而保持不泄漏,能运用于易燃、易爆、有毒等特殊气体环境。
3、根据工艺要求,做到易实现调节功能和阀位状态现场指示及远传等功能。
4、具备有双向耐压性和抗高速气流冲刷性能,阀门的开关速度要快,随阀门的通经不同其启闭时间应控制在3秒以内。
变压吸附装置中,程控阀组是主要的运动部件,如果出现泄漏,会对产品的回收率造成重大影响。
在安装维护中做到以下几点:1、阀门方向不要装错,物料流向要按照“高进低出”的原则,或按阀体上的箭头方向安装。
2、气动截止阀一般只允许安装在水平管道上,即气动执行机构在阀体和管道的上方。
3、要注意介质温度变化,阀门应在允许的温度和压差下使用,温度过高或过低,会使密封元件在高温时老化或在低温时硬化变脆;压差过高,则会损坏密封材料或无法关闭阀门,导致阀门泄漏或动作失灵。
4、程控阀填料函、阀杆外露部分及阀门的外表面要保持清洁干净,要注意防锈及润滑,以延长阀门使用寿命。
2.2、对吸附剂进行改进改良
良好的吸附性能是吸附分离过程的基本条件,选择吸附剂时要考虑两点:第一,要解决吸
附和解吸之间的矛盾,吸附剂对杂质不仅要有较大的吸附量,同时被吸附的杂质要易于解吸,以便在短周期内达到吸附解吸平衡,使分离提纯过程能够维持。
第二,组分间的分离系数尽可能大。
气体组分的分离系数越大,分离越容易,得到的产品气纯度就高,回收率也就越高。
吸附容量越大、分离系数越高的吸附剂,越容易把气体分离,也易使产品回收率达到最大化。
通过对吸附剂改进改良,增加吸附剂的吸附量和分离系数,来提高产品回收率。
如,目前变压吸附提取CO装置中,吸附剂总体分为两类。
一类是采用传统的5A 分子筛,另一类是采用负载Cu吸附剂的工艺。
采用负载Cu吸附剂代替传统的5A分子筛,可使装置回收率大幅提升,它是基于盐类和氧化物在载体表面自发单层分散的原理,将CuCl单层分散在分子筛内外表面上,利用CO可和Cu+生成δ-π配键络合物,使CO在室温附近可以和氮气、甲烷、氢气和二氧化碳等有效地分离。
如新乡中新化工变压吸附装置所使用的吸附剂就是的PU-1B,CO专用吸附剂产品纯度可达98%以上,可一步提纯CO。
2.3、改进工艺流程
变压吸附的吸附特性是,在同一温度下,加压吸附、减压解吸。
通过均压、逆放、等步骤回收气体的机械能、减少产品组分损失,是提高装置回收率的主要措施。
变压吸附装置工艺改进的重点,在于采用合适数量的吸附床流程、合理的工艺步骤设计;比如均压、逆放、冲洗等步骤的设计。
如安阳九天化工变压吸附提取CO装置的改造,目的在于提高一氧化碳的回收率。
改造前由于是两塔吸附,周期短处理量小,均压、逆放不到位,两次均压后机械能回收率低,由于均压、逆放不到位,导致吸附剂再生不完全,造成产品回收率低。
通过工艺改进,吸附塔由原来的5塔运行2塔吸附、2次均压,改进为9塔运行4塔吸附、4次均压,增加了均压次数,通过对均压方式进行改造,降低了吸附塔压力,增加了气体回收率。
改造前均压逆放结束后压力由0.5MPa降至0.08MPa,改造后通过增加均压次数,降低逆放时的压力,减少吸附塔内死空间和床层内残留气体的损失,压力由0.5MPa降至0.02MPa,提高了机械能回收率。
改造前吸附剂均压及逆放再生为塔对塔,造成吸附剂长时间的均压和逆放占用了自身的再生时间,降低了再生效果。
冲洗再生过程需要较长的传质再生时间才能保证再生的效果,造成再生效果差吸附量小。
通过对工艺的改进,产品回收率较以前有了大幅提升。
2.4、调整装置运行参数
变压吸附装置的运行参数调整办法主要通过以下方法来实现:
第一,要及时分析判断物料各组分变化,使生产参数随机化,及时进行调整,使装置回收率保持在较高状态。
根据取得产品不同,变压吸附分离法一般分为两类:即从吸附废气中取得产品和从吸附相中取得产品。
如安阳九天化工变压吸附装置,就是利用两步法从PSA-I 吸附废气中取得半产品,从PSA-II吸附相中取得产品的。
在PSA-I为了提高产品回收率,在保证产品质量的前提下,必须尽可能的延长吸附时间,最大程度的回收有效气体成分。
如安阳九天化工变压吸附装置,PSA—I在吸附周期为800s和920s时CO气回收率分别在68%和73%。
PSA-II为了提高产品回收率。
在保证产品产量和质量的前提下,必须尽可能的减少吸附时间,避免有效组分过多穿透。
九天化工两段法制CO,PSA-II在吸附周期为260s和230s 时CO回收率分别为70%和74%。
第二,当吸附达到饱和后,只有提高吸附剂的再生效果才能提高平均吸附量。
如九天化工变压吸附提取CO装置,通过提高解吸能力来提高产品回收率。
装置原有4台W-300型、改造后又增加1台W-600型真空泵,利用真空泵从吸附相取得产品,使吸附剂脱附再生,通过增加抽空再生时间和增加真空泵数量措施,使真空度由原来的-0.0625MPa提高到-0.075MPa,CO的回收率也相应提高了很多。
第三,装置负荷发生变化时,操作参数要随工况及时加以调整,避免产品回收率的降低。
如,当装置负荷降低时,各步骤的均压压力会产生波动,终充压力会升不到位,调整不及时会使充压用气过多,减少产品回收率,相应增加吸附时间、调整冲洗气用量等措施。
三、结束语
经过不断的追求创新,艰苦的实验,变压吸附技术有了革命性的提高,特别是在提高气体回收率方面取得了长足的进步。
但也存在不少问题,如目前国内还不能大规模生产高效吸附剂,对吸附剂的改良性研究成本投入大。
提高产品回收率的途径,集中在寻找新的吸附材料,提高吸附剂性能和降低成本;对工艺流程和装置本身的不断改进;不断保持装置及其参数的最优化,来保障回收率的提高。