机械加工工艺汇总
机械制造工艺学知识点汇总 全 (复习资料)

粗基准概念:以未加工的表面为定位基准的基准。
精基准概念:以加工过的表面为定位基准的基准。
精基准的选择:1基准重合原则2统一基准原则3互为基准原则4自为基准原则5便于装夹原则6 精基准的面积与被加工表面相比,应有较大的长度和宽度,以提高其位置精度。
粗基准的选用原则:1保证相互位置要求2保证加工表面加工余量合理分配3便于工件装夹4粗基准一般不得重复使用原则(1、若必须保证工件上加工表面与非加工表面间的位置要求,则应以不加工表面作为粗基准;2、若各表面均需加工,且没有重点要求保证加工余量均匀的表面时,则应以加工余量最小的表面作为粗基准,以避免有些表面加工不起来。
3、粗基准的表面应平整,无浇、冒口及飞边等缺陷。
4、粗基准一般只能使用一次,以免产生较大的位置误差。
)生产纲领:计划期内,应当生产的产品产量和进度计划。
备品率和废品率在内的产量六点定位原理:用来限制工件自由度的固定点称为定位支承点。
用适当分布的六个支承点限制工件六个自由度的法则称为六点定位原理(六点定则)组合表面定位时存在的问题:当采用两个或两个以上的组合表面作为定位基准定位时,由于工件的各定位基准面之间以及夹具的各定位元件之间均存在误差,由此将破坏一批工件位置的一致性,并在夹紧力作用下产生变形,甚至不能夹紧定位误差:由于定位不准确而造成某一工序在工序尺寸或位置要求方面的加工误差。
产生原因:1工件的定位基准面本身及它们之间在尺寸和位置上均存在着公差范围内的差异;2夹具的定位元件本身及各定位元件之间也存在着一定的尺寸和位置误差;3定位元件与定位基准面之间还可能存在着间隙。
夹紧装置的设计要求:1夹紧力应有助于定位,不应破坏定位;2夹紧力的大小应能保证加工过程中不发生位置变动和振动,并能够调节;3夹紧后的变形和受力面的损伤不超出允许的范围;4应有足够的夹紧行程;5手动时要有自锁功能;6结构简单紧凑、动作灵活、工艺性好、易于操作,并有足够的强度和刚度。
机械加工工艺过程及工序卡片
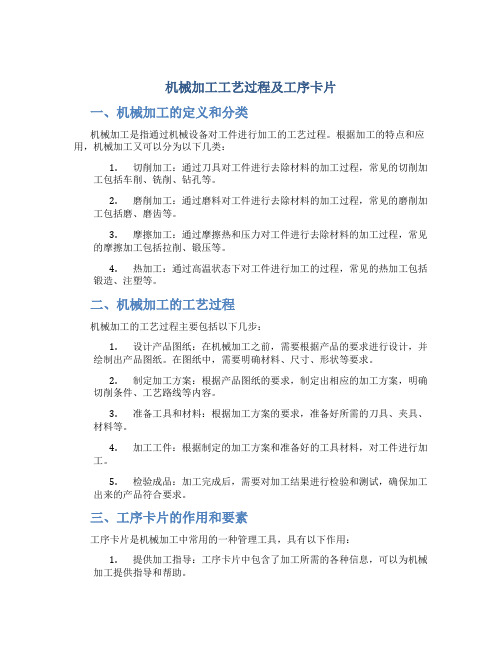
机械加工工艺过程及工序卡片一、机械加工的定义和分类机械加工是指通过机械设备对工件进行加工的工艺过程。
根据加工的特点和应用,机械加工又可以分为以下几类:1.切削加工:通过刀具对工件进行去除材料的加工过程,常见的切削加工包括车削、铣削、钻孔等。
2.磨削加工:通过磨料对工件进行去除材料的加工过程,常见的磨削加工包括磨、磨齿等。
3.摩擦加工:通过摩擦热和压力对工件进行去除材料的加工过程,常见的摩擦加工包括拉削、锻压等。
4.热加工:通过高温状态下对工件进行加工的过程,常见的热加工包括锻造、注塑等。
二、机械加工的工艺过程机械加工的工艺过程主要包括以下几步:1.设计产品图纸:在机械加工之前,需要根据产品的要求进行设计,并绘制出产品图纸。
在图纸中,需要明确材料、尺寸、形状等要求。
2.制定加工方案:根据产品图纸的要求,制定出相应的加工方案,明确切削条件、工艺路线等内容。
3.准备工具和材料:根据加工方案的要求,准备好所需的刀具、夹具、材料等。
4.加工工件:根据制定的加工方案和准备好的工具材料,对工件进行加工。
5.检验成品:加工完成后,需要对加工结果进行检验和测试,确保加工出来的产品符合要求。
三、工序卡片的作用和要素工序卡片是机械加工中常用的一种管理工具,具有以下作用:1.提供加工指导:工序卡片中包含了加工所需的各种信息,可以为机械加工提供指导和帮助。
2.提高工作效率:工序卡片可以明确加工的目标和要求,有助于机械加工工序的快速进行,提高工作效率。
3.保证加工质量:工序卡片中规定了加工的标准和要求,可以确保加工出来的产品符合质量要求。
工序卡片的要素包括以下几个方面:1.工序名称:明确工序名称,以便对加工过程进行管理。
2.工艺要求:明确加工工艺的要求,包括切削条件、加工速度、切削深度等。
3.程序流程:规定加工的流程和先后顺序,保证加工顺序的正确性和合理性。
4.成品要求:明确加工出来的产品的要求和标准,保证加工出来的产品符合客户的要求。
典型零件机械加工工艺过程(共29张PPT)精选

第十九页,共29页。
接盘(jiē pán)加工工艺规 程卡片
工序号 工种 工 序 内 容
加工简图
设备
1
锻
锻造毛坯
三爪自定心卡盘夹
小端,粗车大端面
2
车 见平,粗车大外圆
至Ø96。
车床
第二十页,共29页。
工序号 工种 工 序 内 容
加工简图
调头夹大端,粗车
小端面保证总长52,
3
第三页,共29页。
传动轴工艺规程
(guīchéng)卡片
工 序
工 种
工序内容
加工简 图
设 备
1
下 料
圆钢ø60×265
锯 床
车一端面见平;调 2 车 头,车另一端面保
证总长259。
车 床
3
车
钻一端中心孔;钻 另一端中心孔。
车 床
第四页,共29页。
工工 序种
工序内容
加工简 图
设 备
用尾架顶尖顶住,粗
10
铣
深度比图样规定尺 寸多铣0. 25mm,作
为磨削的余量。
加工简图
设 备
铣 床
11 钳 修研两端中心孔
车 床
第九页,共29页。
工工 序种
工序内容
加工简图
设 备
磨外圆Q,M,并用砂
轮端面靠磨台肩H,1,
12 磨 调头,磨外圆N,尸, 靠磨台肩G。
外 圆 磨 床
13 检
检验
第十页,共29页。
2.中间轴机械加工工艺规程 中间轴的材料(cáiliào)为45号钢,生 产批量为600件,中间轴如下图:
第十三页,共29页。
工序号 工序名称
机械加工工艺基础(完整版)
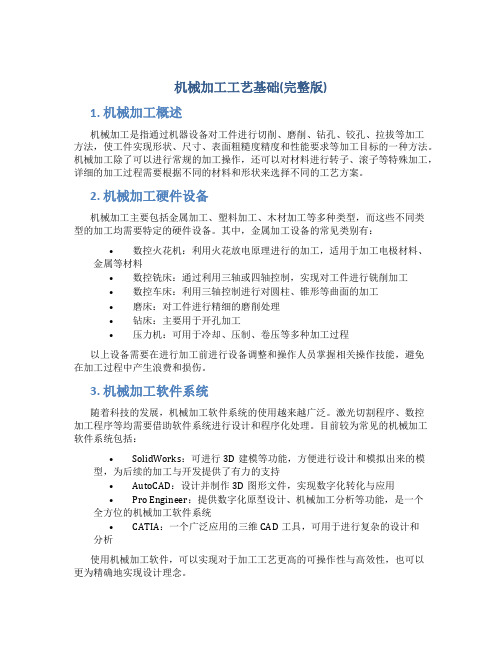
机械加工工艺基础(完整版)1. 机械加工概述机械加工是指通过机器设备对工件进行切削、磨削、钻孔、铰孔、拉拔等加工方法,使工件实现形状、尺寸、表面粗糙度精度和性能要求等加工目标的一种方法。
机械加工除了可以进行常规的加工操作,还可以对材料进行转子、滚子等特殊加工,详细的加工过程需要根据不同的材料和形状来选择不同的工艺方案。
2. 机械加工硬件设备机械加工主要包括金属加工、塑料加工、木材加工等多种类型,而这些不同类型的加工均需要特定的硬件设备。
其中,金属加工设备的常见类别有:•数控火花机:利用火花放电原理进行的加工,适用于加工电极材料、金属等材料•数控铣床:通过利用三轴或四轴控制,实现对工件进行铣削加工•数控车床:利用三轴控制进行对圆柱、锥形等曲面的加工•磨床:对工件进行精细的磨削处理•钻床:主要用于开孔加工•压力机:可用于冷却、压制、卷压等多种加工过程以上设备需要在进行加工前进行设备调整和操作人员掌握相关操作技能,避免在加工过程中产生浪费和损伤。
3. 机械加工软件系统随着科技的发展,机械加工软件系统的使用越来越广泛。
激光切割程序、数控加工程序等均需要借助软件系统进行设计和程序化处理。
目前较为常见的机械加工软件系统包括:•SolidWorks:可进行3D建模等功能,方便进行设计和模拟出来的模型,为后续的加工与开发提供了有力的支持•AutoCAD:设计并制作3D图形文件,实现数字化转化与应用•Pro Engineer:提供数字化原型设计、机械加工分析等功能,是一个全方位的机械加工软件系统•CATIA:一个广泛应用的三维CAD工具,可用于进行复杂的设计和分析使用机械加工软件,可以实现对于加工工艺更高的可操作性与高效性,也可以更为精确地实现设计理念。
4. 机械加工工艺流程机械加工工艺是一个复杂的加工领域,但总的流程可以分为如下几个环节:•原料准备:确定要使用的工件材料和复合类型•雕刻CAD设计:在软件中确定设计模型•预加工操作:根据实际工艺要求,组织添加与磨削•机械加工操作:进行火花加工、深孔加工和精细加工•检查与修整:针对加工效果进行检测和修整处理•表面处理:主要包括工件去刺、去毛刺、清洗和采用喷砂等高效处理方式•装配和测试:对加工完成的工件进行装配工作,验证其实际生产能力和工艺性能每一个加工环节都可能产生不同的实际运用效果。
机械加工工艺流程
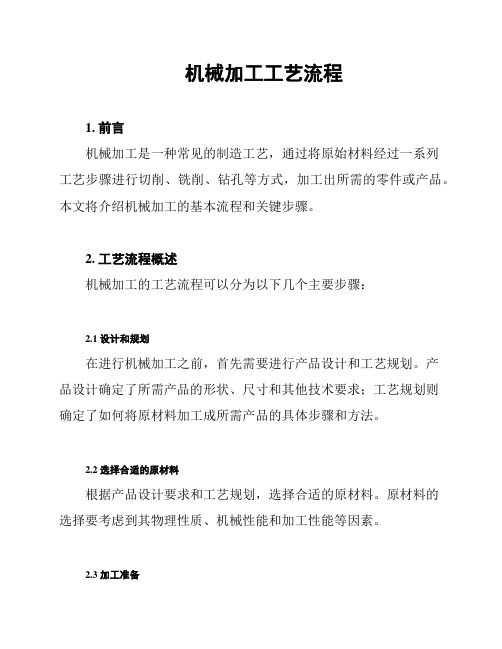
机械加工工艺流程1. 前言机械加工是一种常见的制造工艺,通过将原始材料经过一系列工艺步骤进行切削、铣削、钻孔等方式,加工出所需的零件或产品。
本文将介绍机械加工的基本流程和关键步骤。
2. 工艺流程概述机械加工的工艺流程可以分为以下几个主要步骤:2.1 设计和规划在进行机械加工之前,首先需要进行产品设计和工艺规划。
产品设计确定了所需产品的形状、尺寸和其他技术要求;工艺规划则确定了如何将原材料加工成所需产品的具体步骤和方法。
2.2 选择合适的原材料根据产品设计要求和工艺规划,选择合适的原材料。
原材料的选择要考虑到其物理性质、机械性能和加工性能等因素。
2.3 加工准备在进行机械加工之前,需要进行加工准备工作。
这包括准备加工设备和工具,调整设备参数以适应所需加工要求,检查刀具的磨损情况,确保加工过程的安全性。
2.4 切削加工切削加工是机械加工的常见方式之一,通过旋转或移动切削工具将原材料切削成所需形状。
切削加工常见的方法包括车削、铣削、钻孔等。
2.5 表面处理在机械加工完成后,可以进行表面处理。
表面处理可以改善零件的外观和性能,例如镀铬、喷涂等。
2.6 总结和检查在机械加工完成后,需要进行总结和检查工作。
这包括检查零件尺寸是否符合要求,检查表面质量,以及记录加工过程中的问题和经验教训,为今后的工艺改进提供参考。
3. 结论机械加工的工艺流程涉及多个步骤,包括设计规划、原材料选择、加工准备、切削加工、表面处理和总结检查等。
每个步骤都需要专业的技术和经验,以确保最终产品的质量和性能。
通过合理规划和执行工艺流程,可以提高机械零件和产品的加工效率和品质。
以上是机械加工工艺流程的简要介绍,希望对您有所帮助!。
典型零件机械加工工艺与实例

典型零件机械加工工艺与实例典型零件机械加工工艺与实例机械加工是制造业中一种重要的工艺技术,它可以将原材料加工成特定的形状和尺寸的零件。
在机械加工过程中,不同的零件需要采用不同的加工工艺,下面将介绍一些典型的零件机械加工工艺并给出实例。
1.车削加工车削是一种常见的切削加工工艺,它可以将圆柱形的工件加工成不同形状和尺寸的零件。
车削加工通常使用车床进行加工,将工件固定在车床上,然后通过旋转刀具的方式将工件加工成所需形状和尺寸。
例如,汽车发动机的曲轴就是通过车削加工加工而成的。
2.铣削加工铣削是一种将工件放置在铣床上进行加工的工艺技术。
铣削加工可以将工件从不同角度进行加工,可以加工出各种形状的凹凸面和倒角等。
例如,机床上的床身、工作台和立柱等零件,都是通过铣削加工加工而成的。
3.钻孔加工钻孔是一种加工孔洞的工艺技术,可以将工件上的孔洞加工成不同形状和尺寸的孔洞。
钻孔加工通常使用钻床进行加工,将工件固定在钻床上,然后通过旋转钻头的方式将工件加工成所需形状和尺寸。
例如,电器设备中的插座、开关和电线等,都是通过钻孔加工加工而成的。
4.冲压加工冲压是一种加工薄板材料的工艺技术,可以将材料加工成各种形状和尺寸的零件。
冲压加工通常使用冲床进行加工,将材料固定在冲床上,然后通过冲床上的模具将材料加工成所需形状和尺寸。
例如,汽车车身、电器外壳和日常生活中的金属制品等,都是通过冲压加工加工而成的。
以上是一些典型的零件机械加工工艺,虽然加工工艺不同,但都需要精确的加工工艺和技术,以达到所需的加工效果。
在实际加工中,应根据不同的工件选择合适的加工工艺,以提高生产效率和加工质量。
机械加工工艺介绍
5.3 车削的工艺特点1.粗加工:经济精度可达到IT10,表面粗糙度在25-12.5之间;精加工:经济精度可达IT7左右,表面粗糙度Ra6.3-1.6之间。
2. 易于保证相互位置精度要求。
一次装夹可加工几个不同的表面,避免安装误差。
3. 刀具简单,制造、刃磨和安装方便,容易选用合理的几何形状和角度,有利于提高生产率。
4. 应用范围广泛,几乎所有绕定轴心旋转的内外回转体表面及端面,均可以用车削方法达到要求。
5. 可以用精细车的办法实现有色金属零件的高精度的加工(有色金属的高精度零件不适合采用磨削)6.5 铣削的工艺特点1.铣削加工的精度可达IT10-IT7,表面粗糙度可达6.3-1.6左右2.生产效率高,铣刀是多刀齿刀具,铣削时有几个刀齿同时参加切削,主运动是刀具的旋转,所以铣削的生产效率比刨削高。
3.容易产生振动,铣刀的刀齿切入和切出时产生振动,加工过程中切削面积和切削力变化较大。
4.刀齿的散热条件较好,在刀具旋转过程的不切削时间内,刀具可以得到一定的冷却。
5.与刨床相比,铣床价格高,适用于批量生产。
7.4 刨削加工的工艺特点1.加工精度通常为:精刨:IT7-IT10,粗糙度Ra为6.3-1.6之间。
2.通用性好,刨床简单、价格低、调整和操作简便,刨刀形状简单,制造、刃磨方便。
3.生产率一般比较低,主运动为往复直线运动,返回行程不参加切削。
4.适用于单件小批生产。
8.4 镗孔加工的工艺特点1.镗床主要用于加工大型工件或形状复杂工件上的孔和孔系。
例变速箱、发动机缸体等。
2.镗孔尺寸公差等级可达IT8 IT7,表面粗糙度值一般为1.6~0.8 m。
3.镗孔可以校正孔原有的轴线偏差或位置偏差。
1.镗床主要用于加工大型工件或形状复杂工件上的孔和孔系。
例变速箱、发动机缸体等。
2.镗孔尺寸公差等级可达IT8 IT7,表面粗糙度值一般为1.6~0.8 m。
3.镗孔可以校正孔原有的轴线偏差或位置偏差。
8.5 钻削的工艺特点1.钻削属于低精度(IT11-IT13)和高表面粗糙度的(Ra50-12.5)加工方法2.容易产生“引偏”,是加工过程中由于钻头弯曲产生孔径扩大、孔不圆等缺陷。
机械加工工艺
机械加工工艺机械加工工艺的规范、规程与标准一、简介机械加工工艺是指通过机械设备和工具对工件进行加工、制造的一种生产过程。
它在工业生产过程中扮演着至关重要的角色。
本文将从机械加工的方法、工艺流程、常见加工技术以及质量控制等方面来讨论机械加工工艺的规范、规程与标准。
二、机械加工方法1. 机械加工方法的分类机械加工方法可以分为传统加工方法和非传统加工方法。
其中传统加工方法包括车削、铣削、钻削、磨削等常见的加工方式;非传统加工方法则包括激光加工、电火花加工、电子束加工等高精度、高效率的加工方式。
2. 机械加工方法的选择原则机械加工方法的选择应根据工件材料、形状、加工要求以及设备条件等方面进行综合考虑。
在选择时需根据工件材料的硬度、尺寸、形状复杂程度等因素来确定最适合的加工方法。
三、机械加工工艺流程1. 工艺流程的确定工艺流程是指加工过程中各个工序的排布和顺序。
在确定工艺流程时,需要考虑以下几个方面:工件准备、设备选择、工序安排、设备设置、刀具选择、工序间协调等。
2. 工序参数的确定工序参数主要包括切削速度、进给量、切削深度、刀具选择等内容。
在确定工序参数时,需考虑工件材料、硬度、切削稳定性等因素,以保证加工质量。
四、常见机械加工技术1. 数控机床技术数控机床技术是机械加工领域的重要发展方向,通过计算机控制完成各种复杂的加工操作。
其具有高精度、高效率和灵活性强等优点。
2. 刀具技术刀具是机械加工过程中的重要工具,对加工质量和效率有着重要影响。
刀具技术包括刀具材料的研发、刀具涂层技术、刀具加工精度等方面。
3. 自动化技术自动化技术通过使用传感器、执行器和控制系统等设备,实现机械加工过程的自动化控制,提高生产效率和加工质量。
五、质量控制1. 机械加工的质量检验常见的机械加工工件的质量检验方法包括工件尺寸测量、表面光洁度检测、硬度检测、均匀性检测等。
2. 质量控制的要求机械加工工艺要求对每个工序都进行严格的质量控制,确保每个工序加工的质量符合标准要求。
机加工流程及工艺
机加工流程及工艺一、引言机加工是一种常见的制造工艺,它通过使用机械设备对工件进行切削、钻孔、铣削等加工操作,以达到预定的形状和尺寸要求。
本文将介绍机加工的基本流程及常用的工艺。
二、机加工流程1.工件准备:首先需要准备待加工的工件,通常是由金属或其他材料制成的原始零件。
工件应经过清洗和检查,以确保表面没有污垢或损坏。
2.工艺规划:在进行机加工之前,需要进行工艺规划。
这包括确定所需的切削工具、加工顺序和切削参数等。
根据工件的形状和要求,选择合适的机床和夹具。
3.装夹工件:将工件安装在机床上的夹具中,以便进行加工操作。
夹具应牢固固定工件,以确保加工过程中的稳定性和精度。
4.切削加工:根据工艺规划,使用合适的切削工具进行切削操作。
切削工具通常是钻头、铣刀、刀具等。
通过旋转、移动或振动切削工具,将工件表面的材料逐渐切除,以达到所需的形状和尺寸。
5.加工检验:在切削加工完成后,需要对加工后的工件进行检验。
使用测量工具,如千分尺、卡尺等,对工件的尺寸、平面度、圆度等进行测量,以确保加工质量符合要求。
6.表面处理:根据需要,对工件进行表面处理。
这可能包括研磨、抛光、电镀等工艺,以改善工件的表面光洁度、耐腐蚀性或装饰效果。
7.清洁和包装:最后,对加工完成的工件进行清洁和包装。
清洁工作可以通过清洗、喷气或擦拭来完成。
包装工作可以采用纸箱、泡沫塑料等材料,以保护工件免受损坏。
三、常用机加工工艺1.车削:车削是一种常见的机加工工艺,它使用车床上的刀具对工件进行切削。
通过旋转工件,同时移动切削刀具,将工件上的材料逐渐切除,以得到所需的形状和尺寸。
2.铣削:铣削是另一种常见的机加工工艺,它使用铣床上的刀具对工件进行切削。
通过旋转刀具,同时移动工件,将工件表面的材料逐渐切除,以得到所需的形状和尺寸。
3.钻孔:钻孔是一种用于在工件上钻孔的机加工工艺。
使用钻床或钻头,将刀具旋转并施加压力,以将工件材料逐渐切除,形成孔洞。
4.切割:切割是一种用于将工件切成所需尺寸的机加工工艺。
机械制造加工工艺
机械制造加工工艺机械制造加工工艺是指通过各种工艺手段,将原材料加工成具有机械功能的制品的过程和方法。
它在现代工业生产中起着举足轻重的作用。
本文将介绍机械制造加工工艺的基本流程和常用方法,并探讨其在制造业中的重要性。
一、机械制造加工工艺的基本流程机械制造加工工艺的基本流程包括物料准备、加工工艺规划、设备选择、加工操作和质量检验五个环节。
1. 物料准备:在机械制造加工过程中,首先需要准备好所需的原材料。
这些原材料可以是金属、塑料、橡胶等,其选择应根据制品的具体要求和加工工艺来决定。
2. 加工工艺规划:在物料准备完成后,需要对加工工艺进行规划。
这包括确定加工工艺路线、加工顺序、切削参数等。
合理的加工工艺规划能够提高加工效率、降低成本,同时确保制品的质量。
3. 设备选择:根据加工工艺规划的要求,选择合适的加工设备。
这些设备可以是机床、切削工具、测量仪器等。
设备选择要考虑加工工艺的具体要求,同时兼顾设备性能和成本因素。
4. 加工操作:在设备选择完成后,进行具体的加工操作。
这包括切削、焊接、钻孔、磨削等一系列操作。
加工操作要严格按照加工工艺规程进行,确保制品的尺寸精度和表面质量。
5. 质量检验:在加工完成后,进行质量检验,以确保制品符合设计要求。
质量检验可以包括外观检查、尺寸测量、力学性能试验等。
合格的制品可以进入下一个环节,否则需要重新加工或修复。
二、常用的机械制造加工方法1. 切削加工:切削加工是最常见的机械制造加工方法之一。
它通过工具与工件之间的相对运动,将工件上的材料去除,以获得所需的形状和尺寸。
常见的切削加工方法有车削、钻削、铣削、镗削等。
2. 焊接加工:焊接是将两个或多个工件通过熔化填充材料的方法连接在一起的加工方法。
焊接广泛应用于金属制品的制造中,如船舶、桥梁、汽车等。
常见的焊接方法有电弧焊、气体保护焊、激光焊等。
3. 塑性加工:塑性加工是利用材料的可塑性,通过施加力或温度改变其形状的加工方法。
- 1、下载文档前请自行甄别文档内容的完整性,平台不提供额外的编辑、内容补充、找答案等附加服务。
- 2、"仅部分预览"的文档,不可在线预览部分如存在完整性等问题,可反馈申请退款(可完整预览的文档不适用该条件!)。
- 3、如文档侵犯您的权益,请联系客服反馈,我们会尽快为您处理(人工客服工作时间:9:00-18:30)。
典型习题和解答第一章机械加工工艺规程的制定〔例1.3〕试举例说明下列各组的概念、特点以及它们之间的区别:(1)零件尺寸链、工艺过程尺寸链,工艺系统尺寸链,装配尺寸链;(2)封闭环.组成环,增环.减环。
〔例 1.10〕设某一零件图上规定的外圆直径为Ф32005.0-mm ,渗碳深度为0.5~0.8 mm 。
现为使此零件可和另一种零件同炉进行渗碳,限定其工艺渗碳层深度为0.8~1.0 mm 。
试计算渗碳前车削工序的直径尺寸及其上、下偏差?[解] 渗碳深度是间接保证的尺寸,应为封闭环。
并作出尺寸链计算图。
车削外圆的半径及公差R δR为组成环之一。
求R δR: 0.8=1+16-R min ,R min =16.2mm0.5=0.8+15.975-R max , R max =16.275mm故车削工序的直径尺寸及公差应标注为Φ32.55015.0- mm 。
〔例 1.11〕設一零件,材料为2Cr13,其内孔的加工顺序如下: (1)车内孔Φ31.814.00+(2)氰化,要求工艺氧化层深度为磨内孔Φ320.0350.010++,要求保证氧化层深度为0.1~0.3mm, 试求氰化工序的工艺氧化层深度t T δ? [解] 按加工顺序画出形成氰化层深度0.1 ~0.3mm 的尺寸链计算图。
图中0.1~0.3 mm 是最后形成的尺寸应为封闭环。
计算 tTδ: 0.3=t max +15.97-16.0050.1=t min +15.9-16.0175得 t max =0.335mmt min =0.2175mm 故氰化工序的工艺氰化层深度tTδ=0.21751175.00+mm 。
〔例 1.12〕某小轴系成批生产,工艺过程为车、粗磨、精磨、镀铬。
所得尺寸应为Ф300045.0-㎜,镀层厚度为0.03~0.04㎜。
试求镀铬前精磨小轴的外径尺寸及公差。
[解] 列尺寸链如图示,镀铬后外径尺寸Φ300045.0-mm 为封闭环30=A 1max +0.08 得 A 1max =29.92mm30-0.045=A 1min +0.08-0.02 A 1min =28.895mm所以镀铬前精磨小轴的外径尺寸及公差大小为A 1=Φ29.920025.0- mm〔例 1.13〕某轴套的部分工艺过程为:粗磨内孔到Ф04.0076.154+Φ㎜,再渗氮,最后精磨内孔至04.00155+Φ㎜,单边渗氮层深度要求为0.3~0.5㎜,试计算渗氮工序的渗入深度。
[解] 列尺寸链如图,应保证的渗碳层深度为封闭环0.6—1.0mm (双边).解尺寸链 1.0=154.76+0.04+tmax-1550.6=154.76+tmin-(155+0.04)tmax=1.2mm得 tmin=0.88mm所以渗碳工序的渗入深度2t=0.44—0.6mm 。
〔例 1.14〕选择题1.在机械加工中直接改变工件的形状,尺寸和表面性能使之变成所需零件的过程称为(D )。
A 生产过程;B 工艺过程;C 工艺规程;D 机械加工工艺过程。
2.编制零件机械加工工艺规程,编制生产计划和进行成本核算最基本的单元是(C )。
A工步;B工位;C工序;D安装3.工艺规程对指导生产,组织生产的作用很大。
工艺文件的形式主要决定于生产类型,试指出下列各种生产类型大多采用哪种形式的工艺文件(l)单件小批生产(A); (2)成批生产(C);(3)大批大量生产(B)A工艺过程卡;B机械加工工序卡;C机械加工工艺卡。
4.确定毛坯种类及制造方法时,应综合考虑各种因素的影响,合理选用时主要应使(D)。
A毛坯的形状与尺寸尽可能接近成品的形状与尺寸,因而减少加工工时,减少材料损耗并节省加工成本;B毛坯制造方便,以节省毛坯成本;C加工后零件的物理机械性能好;D零件的总成本低,且物理机械性能好。
5.为改善机器和零件的结构工艺性,应在满足机器工作性能的前提下能采用优质、高产、低成本的方法制造,因此综合评定工艺性的要求是((C, D)A便于达到零件图上规定的加工要求;B有利于减少加工、装配的劳动量;C注意使机器和零件的结构与生产规模、生产条件相适应;D注意全面评价毛坯、加工、装配和维修的整个工艺过程。
6.零件在加工过程中使用的基准叫做(B,D)A设计基准;B工艺基准;C装配基准;D定位基准。
7.自为基准是以加工面本身为精基准,多用于精加工或光整加工工序,这是由于(C)A符合基准重合原则;B 符合基准统一原则;C 保证加工面的余量小而均匀;D 保证加工面的形状和位置精度。
8.轴类零件定位用的顶尖孔是属于(A,C):A精基准;B粗基准;C辅助基准;D自为基准。
第二章机械加工质量1.一批工件加工误差的性质分为哪几类?试举例说明它们的概念以及它们之间的区别?2.何谓误差敏感方向与误差不敏感方向7试举例说明不同方向的原始误差对加工误差影响程度有何不同?3.5.在车床上加工园盘件的端面时,有时会出现圆锥面(中凸或中凹)或端面凸轮似的形状(如螺旋面),试从机床几何误差的影响分析造成图3—2所示的端面几何形状误差的原因是什么?图3-2 6.何谓加工原理误差?由于近似加工方法都将产生加工原理误差,因而都不是完善的加工方法,这种说法对吗?7.为什么机床部件的加载和卸载过程的静刚度曲线既不重合,又不封闭.且机床部件的刚度值远比其按实体估计的要小得多?8.镗孔公差为o.1mm,该工序精度的均方差σ=o.025mm.已知不能修复的废品率为o.5%,试求产品的合格率为多少?图3—0—10 9.为什么机器上许多静止连接的接触表面〔如车床床头箱与床身接合面,过盈配合的轴10.为什么有色金属用磨削加工得不到小粗糙度?通常为获得小粗糙度的加工表面应采用哪些加工方法?若需要磨削有色金属,为减小表面粗糙度应采取什么措施?12.在车床上加工一批光轴的外圆,加工后经度量若整批工件发现在下列几何形状误差(图示)。
<a>鞍形,<b>喇叭形。
试分别说明可能产生上述误差的各种因素?解:对图(a):产生鞍形误差的原因:(1)机床纵导轨在水平面内不直;(2)导轨扭曲或机床两顶尖与纵导轨在垂直面内不平行;(3)加工粗而短工件时,由于机床刚度沿床身纵向不一致;(4)加工长轴时,开始因刀具热伸长,使加工直径减小,热平衡后,又因刀具磨损使加工直径增大。
对图(b):产生喇叭形误差的原因:(1)机床导轨在水平面不直;(2)悬臂加工,工件刚度随长度变化;(3)加工开始时,刀具因热伸长逐渐增大而使加工直径减小。
13.在车床上加工心轴时(图示),粗、精车外圆A及肩台面B,经检测发现A 有圆柱度误差,B对A有垂直度误差。
试从机床几何形状误差的影响,分析产生以上误差的主要原因有哪些?解: 产生A 面圆度误差的主要原因是车床主轴回转线的径向跳动。
产生A 面圆柱度误差的主要原因有:(1)车床导轨在水平面内的直线度误差;(2)主轴回转轴线的角向摆动;(3)床身导轨和主轴回转轴线在水平面内不平行 ;(4)床身导轨的扭曲。
产生B 面对A 面不垂直的主要原因有:(1)主轴回转轴线的轴向串动;(2)刀架横溜板导轨于主轴回转轴线不垂直。
14.在生产现场测量一批小轴的外圆(计1000件),其最大尺寸D max=25.030㎜,最小尺寸D min=25.000㎜,若整批工件尺寸为正态分布,图纸要求该轴的外径为Ф25025.0005.0+-m m ,求这批零件的废品有多少件?能否修复?(已知 Q (2)=0.4772) 解:整批工件的尺寸分散范围为6σ=Dmax-Dmin 所以均方差 σ=(Dmax-Dmin)/6=(25.030-25.000)/6=0.005mm 。
算术平均值 D=(Dmax+Dmin)/2=(25.030+25.000)/2=25.015mm按图纸要求确定公差带中心尺寸 25025.0005.0+-=25.010 ±0.015mm公差带中心与分布中心偏移值 ⊿0=25.015-25.010=0.005mm所以 Z=2005.0005.0203.020=-=∆-σδ 查表得Q (2)=0.4772废品率=0.5-0.4772=0.0228 废品的件数N=0.0228×1000=23件依题意分析废品尺寸都偏大,属于可修复废品15.选择题1)误差的敏感方向是指产生加工误差的工艺系统的原始误差处于加工表面的(A )。
A 法线方向(Y 向);B 切线方向(Z 向);C 轴线方向(Y 向)。
2)车床主轴的几何偏心(纯径向跳动)使加工阶梯轴时产生的误差是(C )。
A 圆度误差;B 端面平面度误差;C 加工面与装夹面的同轴度误差。
3)主轴具有纯角度摆动时,车削外圆得到的是(B )形状,产生(F )误差;镗出的孔得到的是(A )形状,产生(E )误差。
A椭圆;B圆锥;C棱圆;D腰鼓形;E圆度;F圆柱度;G直线度。
4)车床主轴的纯轴向窜动对(B, C)加工有影响:A车削内外圆;B车削端平面;C车削螺纹。
5)试指出下列刀具中,哪些刀具的制造误差会直接影响加工精度(A, D, E, F)。
A齿轮滚刀;B外圆车刀;C.端面铣刀;D铰刀;E成形铣刀;F键槽铣刀;G内圆磨头。
6)判别下列误差因素所引起的加工误差属于何种误差类型及误差性质:(1)夹具在机床上的安装误差(C, D); (2)工件的安装误差(C, F); (3)刀具尺寸调整不准确引起的多次调整误差(A, F); (4)车刀磨损发生在加工一批套筒的外圆(A, E); (5)工件残余应力引起的变形(B, C, F)。
A尺寸误差;B 几何形状误差;C 相互位置误差;D常值误差;E变值规律性误差;F随机误差。
7)加工齿轮、丝杠时,试指出下列各情况哪些属于加工原理误差(C,D, E)。
A传动齿轮的制造与安装误差;B母丝杠的螺距误差;C用阿基米德滚刀切削渐开线齿轮;D用模数铣刀加工渐开线齿轮;E用近似传动比切削螺纹。
8)测定机床部件静刚度的实验曲线说明(C):A机床部件的静刚度是不变的;B机床部件的静刚度是变化的,但与载荷无关;C 机床部件的静刚度是随载荷大小而变化的9)研究工艺系统受力变形时,若以车床两顶尖间加工光轴为例,试分别指出下列三种条件下,由于切削过程受力点位置的变化引起工件何种形状误差:(1)只考虑机床变(C);(2)只考虑车刀变形(D);(3)只考虑工件变形(B)。
A圆锥形;B腰鼓形;C马鞍形(双曲线);D圆柱形。
10)工艺系统的热变形只有在系统热平衡后才能稳定,可采取适当的工艺措施予以消减,其中系统热平衡的含义是(B)。
A机床热平衡后;B机床与刀具热平衡后;C机床刀具与工件都热平衡后。
11)在卧式镗床上,精镗车床尾架长孔时,为减小粗糙度一般应先考虑采用哪种工艺措施较有效(B)?A.对工件材料先进行正火,调质等热处理;B.增大刀尖圆弧半径和减少付偏角;C.使用润滑性能良好的切削液;D.采用很高的切削速度并配合较小的进给量12)磨削光轴时,若切削条件相同,哪种工件材料磨削后表面粗糙度小(B)?A. 20钢;B. 45钢;C.铸铁;D.铜13)在平面磨床上精磨连杆端面时(工件材料45钢),若磨削表面出现拉毛、划伤等缺陷,一般应先考虑采用哪种工艺措施较有效(A,E)?A.正确选用砂轮,检查砂轮的硬度是否合适;B.精细修正砂轮及增加光磨次数;C.降低磨削深度及工件纵向进给量,提高砂轮速度;D.磨削液是否有良好的冷却性和流动性,供应是否充分;E.磨削液是否清洁。