LTNF常温Ni-Fe合金镀层的耐蚀原因分析
影响金属材料耐蚀性因素的研究和探讨

影响金属材料耐蚀性因素的研究和探讨摘要:金属材料对金属的发展有很重要的作用,被运用在很多的范畴。
金属材料的腐蚀是当今需要面临的一大重要难题。
无效的金属再加上装置被腐蚀而造成损耗,相当于全球大约合百分之二十的生产量。
金属材料的耐腐蚀机能,有着保护环境并且节能的作用。
本文主要对影响金属材料耐蚀性因素进行了分析研究。
关键词:金属材料;腐蚀危害;影响因素;防腐路径引言金属材料因其便利性与易得性等多种特点,被广泛应用于各个领域中,但是金属材料的易腐蚀性也同样影响到了其具体的使用效果,使得金属材料应用存在明显的局限性。
对此,可通过减少金属材料的应用,或者在应用金属材料时尽可能的避免与易产生化学反应的介质产生直接接触。
除此之外,还可以利用阴阳两极的极化作用来进行电化学腐蚀保护,提高对金属材料的保护。
这对于延长金属材料应用寿命、降低应用成本,提高应用效果都具有非常重要的现实意义。
1金属材料的腐蚀及其危害1.1金属材料的腐蚀金属材料的腐蚀是指金属材料与其周围介质接触时发生化学或电化学反应而引起的一种破坏金属材料自身的现象。
自然界中,大部分金属以其各种化合物形式存在,而金属元素的化学活性通常高于其化合物,因此这些金属会自发地演变成它们在自然界中的本身存在状态,所以金属腐蚀是自发的、普遍存在的一种现象,是不可避免的。
根据金属材料腐蚀发生的机理,通常可将腐蚀分为化学腐蚀和电化学腐蚀。
化学腐蚀是指金属材料与周围介质中存在的非电解质发生接触后,发生了氧化还原化学反应,是金属表面的原子与腐蚀介质产生直接作用而形成的腐蚀现象,如金属材料在有机溶液(芳香烃、原油等)中所发生的腐蚀。
电化学腐蚀主要是指金属材料与电解质进行接触后,金属表面与电解质溶液发生化学反应,进而形成吸氢腐蚀或析氢腐蚀的腐蚀现象,如碳钢与空气中的氧气、二氧化碳以及水等发生作用,最后变成铁锈。
1.2腐蚀的危害腐蚀会弱化金属材料的强度和机械性能,缩短其使用寿命,甚至造成金属材料无效化,造成经济损失。
金属结构材料的耐蚀性
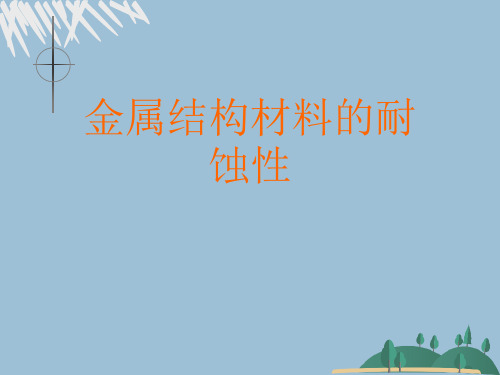
– 如果基体是阴极而第二相或合金中其它微小区域(例 如晶界)是阳极的情况下,进一步减小微阳极的面积 ,则可加大阳极极化电流密度,增加阳极极化程度
– 但是,实际合金中第二相是阳极的情况很少,绝大多 数合金中的第二相都起阴极作用(阴极相),所以, 应用这种耐蚀合金化途径的局限性很大
金属耐蚀合金化原理
金属耐蚀合金化原理
➢ 纯金属的耐蚀特性
– 金属的热力学稳定性
➢ 金属热力学稳定性的分界依据
– 当氢分压等于1atm(101325Pa)时,在中性(pH=7)水溶 液中,氢的平衡电极电位 EH2/H 0.41V4;在酸性(pH=0 )极的电水位溶分液 别中 小EH于2/H和 00时,;可在能相发应生条析件氢下腐,蚀当金属的标准电
➢ 易钝化的金属,往往作为合金元素加入钢中,使合金钝化 而获得耐蚀性
➢ 热力学不稳定的金属中,除了因钝化耐蚀外,还有因在腐 蚀过程初期或一定阶段生成致密的保护性能良好的腐蚀产 物膜耐蚀。这种化学转化膜通常为机械钝态膜
金属耐蚀合金化原理
➢ 金属耐蚀合金化的途径
– 理论依据
➢ 研究金属及其合金的耐蚀性,可从反映腐蚀速度大小的腐 蚀电流的计算式着手,寻求途径 I Ek0 EA0 PK PA R 分子是腐蚀反应的推动力,如果减少推动力,可达到防腐 蚀的目的,即设法使电极极化;分母是腐蚀反应的阻力, 如果增大阻力,也可达到防腐蚀的目的,提高耐蚀性
– 固溶处理可使阴极性杂质转入固溶体内,消除作为活 性阴极的第二相,减小阴极面积
金属耐蚀合金化原理
➢ 金属耐蚀合金化的途径
– 减弱合金的阴极活性
➢ 加入析氢超电压高的合金元素
– 往合金中加入析氢超电压高的合金元素,增大合金阴 极析氢反应的阻力,可显著降低合金在酸性介质中的 腐蚀速率。这种办法只适用于基体金属在某些介质中 不会钝化,由析氢超电压控制的析氢腐蚀过程
涂层金属的腐蚀及涂层的防护机制

涂层金属的腐蚀及涂层的防护机制发表时间:2018-03-22T16:20:24.550Z 来源:《基层建设》2017年第36期作者:许乐乐[导读] 摘要:金属材料容易被腐蚀,而涂层是有效而经济的防腐蚀方法。
中铁建电气化局集团轨道交通器材有限公司 213011摘要:金属材料容易被腐蚀,而涂层是有效而经济的防腐蚀方法。
引起金属腐蚀的因素较多,像涂层性能失效、气体污染物的侵蚀、金属沾染了可溶盐污染物质或者金属表面处理不当引起的。
涂层金属之所以老化是因为自由基原理,而金属腐蚀则是电化学反映机理。
本文主要阐述了大气环境中涂层金属的腐蚀及涂层的防护机制。
关键词:涂层金属;金属腐蚀;防护机制一.引言金属材料在大气环境中很容易被腐蚀这是一个很常识的现象。
在化学热力学原理中金属腐蚀是一种自发过程,因此要想保护金属不被腐蚀,在金属表层进行涂层是常用的方法之一。
金属涂层是一种经济有效的保护金属的材料,金属在涂层之下其电化腐蚀的几率减少,涂层阻断了金属和大气中腐蚀物质的结合来源,使得金属在涂层下保持原有的性质。
但是金属涂层的保护作用也不是万能的,军涂层金属依然有可能遭遇腐蚀,那么如何能加强有机涂层在大气环境中的防腐蚀效果,本文就金属腐蚀的规律和涂层失效的原理进行了分析和论述。
二.涂层金属腐蚀及涂层失效的机制分析(一)涂层金属腐蚀原理(二)涂层老化和失效原理金属暴露在大气中会产生腐蚀,而涂层失效的原理则是老化和失效,像一些化学成分、物理机械等外部因素的侵入都能导致金属涂层失效。
金属涂层失效会呈现出以下状态:表面色泽暗淡,颜色失真,表层碎化导致的开裂或细纹等。
导致涂层老化的原因很多,像昼夜变化引起的张力及紫外线照射等都是引起涂层老化的外界因素。
紫外线暴烈照射下的涂层其吸水率增加,暴晒后一些亲水基团会大量增加,像羟基、烷基过氧化氢、羰基等,这些都导致了涂层的吸水性增加,进而使得涂层失效引起金属腐蚀。
另外,自由基浓度也是引起金属涂层老化的一个因素。
亚磷酸体系镍磷合金电镀工艺及影响镀层耐蚀性的主因素

亚磷酸体系镍磷合金电镀工艺及影响镀层耐蚀性的主因素[摘要]为了弄清影响亚磷酸体系电镀镍磷合金层耐蚀性能的主因素,用极差法分析了各工艺参数的影响,采用SEM/EDAX考察了镍磷镀层的形貌、成分,采用电化学测试考察了镀层的耐蚀性,测定了镀层与基体的结合强度,并确定了最佳工艺条件。
结果表明:亚磷酸含量是影响镀层耐蚀性的主要因素,在240 g/L硫酸镍,45 g/L 氯化镍,30 g/L硼酸,30 g/L亚磷酸,电流密度5 A/dm2,温度40℃条件下所得镀层均匀,耐蚀性和结合力好。
[关键词]电沉积;镍磷合金;亚磷酸体系;耐蚀性能;影响因素[中图分类号]TQ153.2[文献标识码]A[文章编号]1001-1560(2011)07-0064-030·前言镍磷合金镀层耐腐蚀、耐高温、耐磨,导电性和导磁性高,原料成本低,环保性能好,在汽车、航空航天、电子、通讯等行业得到了广泛应用。
获得镍磷合金镀层的主要途径包括化学镀和电镀。
其中在沉积速率、镀液稳定性、成本、最大厚度等诸多方面,电镀法具有化学镀法不具备的优点[1~7]。
目前,电镀镍磷合金工艺和性能的报道较化学镀少,进一步了解电镀工艺参数对镀层耐蚀性的影响对于扩大电镀镍磷的应用范围很有意义。
次磷酸盐体系镍磷合金电镀层质量不稳定,温度及电流稍有变化就容易引起镀层发黑[8,9]。
本工作采用电镀方法,在亚磷酸镍盐体系中获取了镍磷合金镀层;通过正交试验优选了可获得耐蚀性好的镀层的工艺参数,并探讨了各参数对镀层耐蚀性的影响。
1·试验1.1基材前处理以纯铜片为基材,尺寸10 mm×10 mm×1 mm,用环氧树脂封装,留出施镀的面积为1 cm2。
镀前处理流程:基材磨光→水洗→除油→水洗→酸洗→水洗。
用800号水砂纸打磨基材试样至平整光滑后除油。
除油60~100 g/L Na2CO3,5~10 g/L Na3PO4·12H2O,5~15 g/L Na2SiO3,1~3 g/L OP-10乳化剂,温度80~90℃,至将油除净为止。
热处理对Ni-P化学镀层阻垢和耐蚀性能的影响 (1)
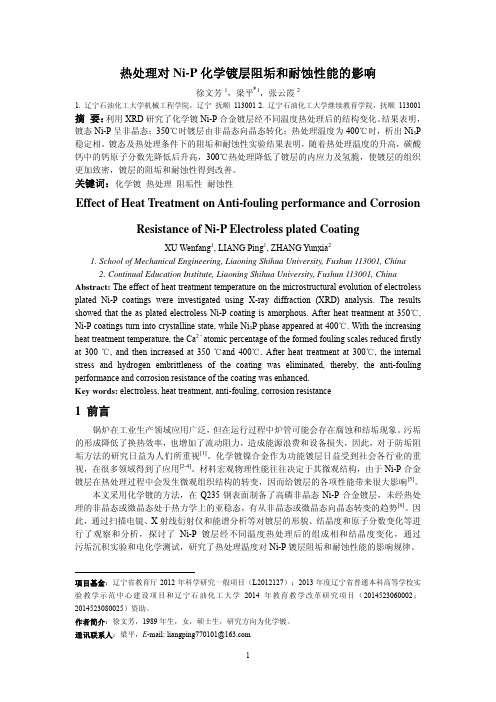
Intensity /a.u
300℃
400
200
镀态
0 10 20 30 40 50 60 70 80 90
2/ degree
图 4 污垢的 X 射线衍射图 Fig. 4 XRD patterns of fouling
4
3.4
热处理后 Ni-P 镀层的耐蚀性能变化
图 6 为镀态和经不同温度热处理后的 Ni-P 镀层试样在通入 CO2 气体的氢氧化钙溶液中 的阻抗图谱。可以看出,在交流阻抗图上只有一个容抗弧[10],随着热处理温度的升高,合 金镀层的容抗弧半径变化明显,说明热处理对合金镀层的耐腐蚀性能影响较大。 采用等效电路图对阻抗图谱进行数值拟合,镀态下 Ni-P 镀层电荷转移电阻 Rct 为 7400 Ω • cm2。300℃热处理后镀层 Rct 为 26290 Ω • cm2,是镀态下的 3.5 倍,表明其耐蚀性得到 很大改善,XRD 分析表明,此时的镀层仍为非晶结构,由于应力的释放和 H 的去除,镀层 的组织更加致密,使镀层的耐蚀性得到较大的提高[11]。350℃热处理后出现了晶界和位错等 缺陷,而且由于形成了 Ni2P 过渡相,使合金镍相中 P 含量降低,使原来的非晶态单相均匀 组织变化为 Ni 和镍磷化合物的混合组织,减少了富磷钝化膜的形成[12]。400℃热处理后镀 层中析出稳定相 Ni3P,Ni3P 在腐蚀原电池中是阴极,Ni 固溶体是阳极,因此,Ni3P 的析出 及其面积增大加速了镀层腐蚀,导致其耐蚀性低于镀态。 耐蚀性随热处理温度先提高后降低,耐蚀性与阻垢性能一致,由文献[13]可知,被腐蚀 的表面易于形成连接污垢与基体的“过渡界面”,有利于污垢离子的附着和沉淀,导致阻垢性 能降低。
1 前言
锅炉在工业生产领域应用广泛, 但在运行过程中炉管可能会存在腐蚀和结垢现象。 污垢 的形成降低了换热效率,也增加了流动阻力,造成能源浪费和设备损失,因此,对于防垢阻 垢方法的研究日益为人们所重视[1]。化学镀镍合金作为功能镀层日益受到社会各行业的重 视,在很多领域得到了应用[2-4]。材料宏观物理性能往往决定于其微观结构,由于 Ni-P 合金 镀层在热处理过程中会发生微观组织结构的转变,因而给镀层的各项性能带来很大影响[5]。 本文采用化学镀的方法,在 Q235 钢表面制备了高磷非晶态 Ni-P 合金镀层,未经热处 理的非晶态或微晶态处于热力学上的亚稳态,有从非晶态或微晶态向晶态转变的趋势[6]。因 此,通过扫描电镜、X 射线衍射仪和能谱分析等对镀层的形貌、结晶度和原子分数变化等进 行了观察和分析,探讨了 Ni-P 镀层经不同温度热处理后的组成相和结晶度变化,通过 污垢沉积实验和电化学测试,研究了热处理温度对 Ni-P 镀层阻垢和耐蚀性能的影响规律。
如何改善化学镀镍的耐腐蚀性能
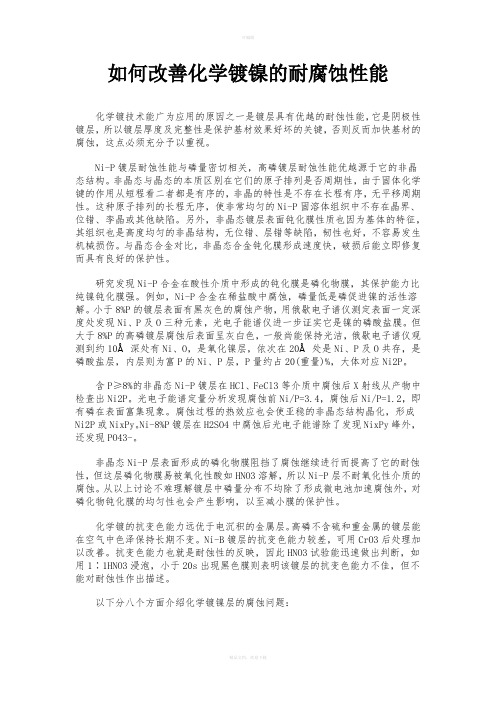
如何改善化学镀镍的耐腐蚀性能化学镀技术能广为应用的原因之一是镀层具有优越的耐蚀性能,它是阴极性镀层,所以镀层厚度及完整性是保护基材效果好坏的关键,否则反而加快基材的腐蚀,这点必须充分予以重视。
Ni-P镀层耐蚀性能与磷量密切相关,高磷镀层耐蚀性能优越源于它的非晶态结构。
非晶态与晶态的本质区别在它们的原子排列是否周期性,由于固体化学键的作用从短程看二者都是有序的,非晶的特性是不存在长程有序,无平移周期性。
这种原子排列的长程无序,使非常均匀的Ni-P固溶体组织中不存在晶界、位错、孪晶或其他缺陷。
另外,非晶态镀层表面钝化膜性质也因为基体的特征,其组织也是高度均匀的非晶结构,无位错、层错等缺陷,韧性也好,不容易发生机械损伤。
与晶态合金对比,非晶态合金钝化膜形成速度快,破损后能立即修复而具有良好的保护性。
研究发现Ni-P合金在酸性介质中形成的钝化膜是磷化物膜,其保护能力比纯镍钝化膜强。
例如,Ni-P合金在稀盐酸中腐蚀,磷量低是磷促进镍的活性溶解。
小于8%P的镀层表面有黑灰色的腐蚀产物,用俄歇电子谱仪测定表面一定深度处发现Ni、P及O三种元素,光电子能谱仪进一步证实它是镍的磷酸盐膜。
但大于8%P的高磷镀层腐蚀后表面呈灰白色,一般尚能保持光洁,俄歇电子谱仪观测到约10Å深处有Ni、O,是氧化镍层,依次在20Å处是Ni、P及O共存,是磷酸盐层,内层则为富P的Ni、P层,P量约占20(重量)%,大体对应Ni2P。
含P≥8%的非晶态Ni-P镀层在HCl、FeCl3等介质中腐蚀后X射线从产物中检查出Ni2P。
光电子能谱定量分析发现腐蚀前Ni/P=3.4,腐蚀后Ni/P=1.2,即有磷在表面富集现象。
腐蚀过程的热效应也会使亚稳的非晶态结构晶化,形成Ni2P或NixPy。
Ni-8%P镀层在H2SO4中腐蚀后光电子能谱除了发现NixPy峰外,还发现PO43-。
非晶态Ni-P层表面形成的磷化物膜阻挡了腐蚀继续进行而提高了它的耐蚀性,但这层磷化物膜易被氧化性酸如HNO3溶解,所以Ni-P层不耐氧化性介质的腐蚀。
铝上化学镀镍层耐蚀性研究

摘要 :采用中性盐雾腐蚀试验方法对铝上化学镀镍层的耐蚀性进行了研究 ,重点比较和讨论了 镀层厚度和镀层含磷量以及镀覆工艺对化学镀 Ni - P 合金层耐蚀性的影响 。
关键词 :铝 ;化学镀镍 ;耐蚀性 中图分类号 : TG42 文献标识码 :A 文章编号 :1001 - 3474 (2003) 06 - 0254 - 03
层腐蚀后的电镀试样的评级 。
解质 ,将沿着表面孔隙渗进内层 ,发生纵向微电池腐
2 结果与讨论
蚀 ,内层为阳极 ,形成针状孔蚀点 。另外 ,有作者对
2. 1 在相同厚度 (22μm~25μm) 条件下 ,高磷化学 Ni - P 镀层表面的不均匀胞状凸起物采用电子探针
镀镍层 (1 组 、2 组) 的耐盐雾腐蚀的能力明显优于中 研究后发现 ,凸起物中心磷含量略高于边缘部位 ,由
表 1 试验结果 ,说明厚度为 25 μm 的铝上高磷 化学镀镍层 (1 、2 组) 和 25μm 铝上中磷化学镀镍层 + 化学钝化 (5 、6 组) 能满足 MIL - C - 26074E 要求 。 而厚度为 25μm 的钢上中磷化学镀镍层 (9 组) 能满 足 AMS2404D 要求 。 2. 3 铝上中磷化学镀镍层经化学钝化处理后 (5 、6 组) ,其耐盐雾腐蚀的能力明显高于相同厚度的普通 中磷化学镀镍层 (3 、4 组) ,并可以和相同厚度的高 磷化学镀镍层 (1 、2 组) 相媲美 。同样 , (8) 组耐盐雾 腐蚀能力也优于 (7) 组 。由于铝上化学镀镍层属于
电沉积Ni-Fe合金工艺及镀层耐蚀性的研究

性 ; 张郁 彬 等 研 究 表 明 , 3 5 氯 化 钠 溶 液 在 .% 中 , 着 镍一 合 金 中 铁 含 量 的 升 高 , 粒 细 化 , 随 铁 晶 ( e 为 3 % 的镍 . 合 金 耐 蚀 性 最 佳 , 以在 防 F) 6 铁 可
hg e tc ro in r ssa c . ih s o r so e itn e
Ke wor y ds:NiFe a ly c ai g;ee to e o i o — lo o tn l cr d p st n;c ro in r ssa c i o so e it n e
引 言
N .e合金 具 有 不 同 于单 质 铁 、 金 属 粉 末 的 i F 镍 特殊 性能 和 软 磁 性 , 吸 波 材 料 、 性 材 料 及 硬 质 在 磁 合金 等领 域 具 有 广 泛 的 应 用 前 景 , 合 金 镀 层 其 不但 具有 优 良的焊 接 性 , 可 作 为 纯 镍 镀 层 的替 代 还
中 图分类 号 : Q 5 . T 132
文献标 识 码 : A
Elc r d p st0 c n l g n r o i n Re it n e o e t 0 e 0 ii n Te h o o y a d Co r so ssa c f
NiFe Al y Co tn — l a ig o C E G H a U o gxa WA u ,WA G C e A G Y nh i H N u ,G O H n —i , NG Q n N h ,T N u —u
采 用 L 2 0 A电化学 工作 站 ( 津兰力 科 化 学 K 05 天 电子 高技术公 司 ) 测定 所 制 备 的 N—e 金 镀 层 在 i 合 F