单兵多功能应急供电系统中风机叶片的设计
风力发电系统中风机叶片优化设计
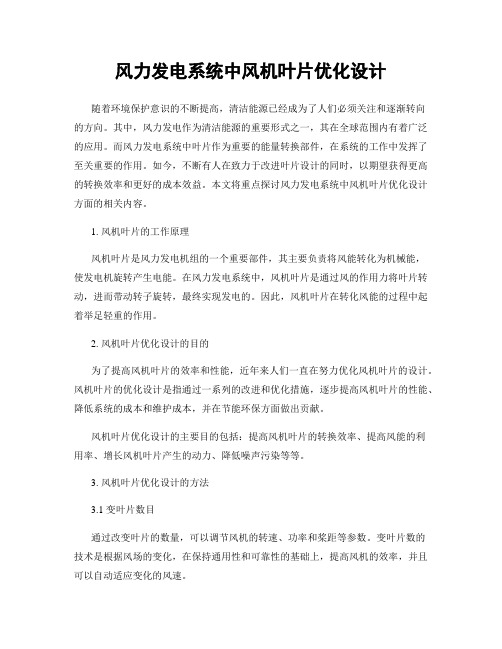
风力发电系统中风机叶片优化设计随着环境保护意识的不断提高,清洁能源已经成为了人们必须关注和逐渐转向的方向。
其中,风力发电作为清洁能源的重要形式之一,其在全球范围内有着广泛的应用。
而风力发电系统中叶片作为重要的能量转换部件,在系统的工作中发挥了至关重要的作用。
如今,不断有人在致力于改进叶片设计的同时,以期望获得更高的转换效率和更好的成本效益。
本文将重点探讨风力发电系统中风机叶片优化设计方面的相关内容。
1. 风机叶片的工作原理风机叶片是风力发电机组的一个重要部件,其主要负责将风能转化为机械能,使发电机旋转产生电能。
在风力发电系统中,风机叶片是通过风的作用力将叶片转动,进而带动转子旋转,最终实现发电的。
因此,风机叶片在转化风能的过程中起着举足轻重的作用。
2. 风机叶片优化设计的目的为了提高风机叶片的效率和性能,近年来人们一直在努力优化风机叶片的设计。
风机叶片的优化设计是指通过一系列的改进和优化措施,逐步提高风机叶片的性能、降低系统的成本和维护成本,并在节能环保方面做出贡献。
风机叶片优化设计的主要目的包括:提高风机叶片的转换效率、提高风能的利用率、增长风机叶片产生的动力、降低噪声污染等等。
3. 风机叶片优化设计的方法3.1 变叶片数目通过改变叶片的数量,可以调节风机的转速、功率和桨距等参数。
变叶片数的技术是根据风场的变化,在保持通用性和可靠性的基础上,提高风机的效率,并且可以自动适应变化的风速。
3.2 叶片弯度设计叶片弯度设计是指在保证强度和刚度的前提下,通过调整叶片剖面,轮廓和断面曲线等参数,实现风机叶片优化设计的目标。
在叶片弯度设计中,需要考虑的是叶片的剖面,以及长度、厚度、弯曲等参数的调整。
在叶片的设计中,叶片的RPM、长度,材料的选择,厚度,弯曲等因素都对性能有着深刻的影响。
3.3 叶尖形状设计叶尖形状是叶片的重要结构之一,其形状对叶片的振动、噪音和气动性能有着非常重要的影响。
因此,针对不同转速区间,需要设计最佳的叶尖形状,以达到最佳的性能和效益。
风机叶片结构设计与优化

风机叶片结构设计与优化随着现代工业的快速发展,风力发电作为一种可再生的可持续能源形式也逐渐成为了人们关注的焦点。
而在风力发电的核心部件,风能转换系统中,风机叶片的设计和优化也十分关键。
风机叶片的结构设计风机叶片是风力发电机组的重要部分,主要作用是将风能转化为机械能,进而驱动发电机发电。
对于风机叶片的结构设计,需要考虑到以下几个方面。
首先,要充分考虑风速和风向的变化,以及风场的特性,从而设计出符合实际工作环境的叶片结构。
在设计叶片的根部、中部和尖部等位置时,还需要根据不同的受力情况进行合理的加强设计。
其次,叶片的长度和宽度也需要充分考虑。
如果叶片长度过短,那么就不能充分利用风能进行转换,从而影响到风力发电机组的发电效率。
而如果叶片长度过长,对于材质和生产成本的要求将会更高,也会带来更大的制造难度。
此外,叶片的形状也是设计的重要方面。
对于一般的三叶片风机叶片来说,需要考虑到叶片弯曲度、扭曲度、翼型等因素。
这些因素将直接影响到叶片的起飞速度、最大风速以及噪音等问题。
风机叶片的优化针对风机叶片的结构设计,优化也是设计的一个重要方面。
对于现有的风机叶片,需要进行深入的研究和优化,以提高风力发电机组的整体效率。
首先,要优化叶片的气动性能。
通过研究叶片的气动流场等问题,可以进一步改善叶片的气动性能,提高叶片的起飞速度和最大功率输出。
此外,还可以利用附面效应和扭曲设计等技术手段,改善叶片的空气动力学特性。
其次,要针对叶片的材质和结构进行优化。
目前常用的叶片材料主要为玻璃钢、碳纤维复合材料等。
但是,在复杂环境中,这些材料容易受到外界环境和受力情况的影响,导致叶片的损坏和破坏。
因此,需要对叶片的材料进行深入研究,开发出更加适合风力发电场景下的叶片材料。
最后,还需要对叶片的生产和装配进行优化。
对于现有的生产和装配工艺来说,需要考虑到生产成本、制造难度和效率等因素,进一步提高叶片的生产效率和质量水平。
结语风机叶片的结构设计和优化是风力发电系统中重要的研究内容。
风力发电机组叶片设计与性能分析

风力发电机组叶片设计与性能分析叶片作为风力发电机组的核心部件之一,其设计和性能分析对于提高风力发电机的发电效率和性能至关重要。
本文将围绕风力发电机组叶片的设计和性能进行详细讨论,包括叶片的设计原理、材料选择、结构设计以及性能分析与优化等方面。
1. 叶片设计原理风力发电机组叶片的设计原理主要包括气动力学原理和结构力学原理。
气动力学原理研究风力对叶片的作用力,包括气动力的大小、方向和分布等;结构力学原理研究叶片的强度、刚度和振动等特性。
在进行叶片设计时,需要将这两个原理进行综合考虑,以满足风力发电机组的性能要求。
2. 材料选择叶片的材料选择直接影响到叶片的强度、刚度和重量等性能指标。
常用的叶片材料有纤维复合材料(如碳纤维、玻璃纤维)、铝合金和钢材等。
纤维复合材料具有优良的强度和刚度,同时具备较低的重量和惰性,因此在风力发电机组叶片设计中被广泛应用。
3. 结构设计风力发电机组叶片的结构设计主要包括叶片的长度、形状和剖面等几何参数的确定。
通常情况下,叶片的长度应根据风力发电机组的机组容量和环境条件进行确定,以实现最佳的发电效率。
叶片的形状和剖面则直接影响到叶片的气动特性,如风阻、升力和推力等。
为了充分利用风能,叶片的气动特性应该尽可能优化,逐步增大风阻和升力,减小风阻系数和剪力等。
4. 性能分析与优化风力发电机组叶片的性能分析与优化通常采用计算流体动力学(CFD)模拟和试验验证相结合的方法。
通过CFD模拟,可以对叶片在不同工况下的流动场进行数值计算,获得叶片的气动特性,如风阻、升力系数、剪力等。
同时还可以对叶片进行结构力学分析,评估其强度和刚度等。
通过与试验数据的对比,可以验证CFD模拟的准确性,并对叶片的设计进行优化。
在进行风力发电机组叶片设计与性能分析时,还需要考虑以下几个关键因素:A. 多工况性能分析:叶片在不同风速下的气动特性会发生变化,因此需要对叶片在多个工况下进行性能分析,并针对不同风速进行优化设计。
风力发电升力型叶片设计

风力发电升力型叶片设计风力发电是一种利用风能转化为电能的可再生能源,其clean、renewable、environmentally friendly、和inexhaustible等优点使其受到越来越广泛的关注。
在整个风力发电系统中,叶片作为风能转化的核心部分扮演着至关重要的角色。
而叶片的设计是影响风力发电效率的重要因素之一。
本文将从风能转化原理出发,简要介绍了目前常用的风力发电叶片类型及其特点,着重阐述了升力型叶片设计的相关技术和发展趋势。
一、风能转化原理风能转化原理是利用风的动能转化为叶片的机械能,再经过发电机转化为电能。
风能转化的基本原理是利用叶片的旋转来捕捉风的动能,然后通过机械传动和发电机转化为电能。
因此,叶片的设计直接影响了风能转化效率。
一般来说,风能转化效率的高低取决于叶片的设计是否合理、结构是否坚固、重量是否轻、空气动力学性能是否优越等因素。
二、常用的风力发电叶片类型及其特点目前常用的风力发电叶片类型主要有两种,一种是升力型叶片,另一种是桨距型叶片。
升力型叶片一般为弯曲形状,其设计灵感来自于飞机的机翼。
升力型叶片的特点是在一定风速范围内具有较高的风能转化效率,尤其是在低风速下效果更加显著。
此外,升力型叶片在结构上相对轻盈,比较适合用于小型风力发电机组。
桨距型叶片的特点是叶片长度较长,为平直或微弯曲形状。
这种叶片的特点是结构简单、制造成本较低。
桨距型叶片在高风速下,其风能转化效率一般比升力型叶片要高。
因此,桨距型叶片适合用于大型风力发电机组。
三、升力型叶片设计的相关技术升力型叶片的设计是一项复杂的工程,需要结合空气动力学、结构力学、材料科学等多个学科的知识。
其基本设计原则包括叶片的气动外形、空气动力学特性、材料选择等。
在具体的设计过程中,需要考虑叶片的长度、宽度、弯曲度、厚度等参数,以及叶片的材料强度、质量、成本等因素。
与传统的桨距型叶片相比,升力型叶片的设计更加复杂。
其气动外形需考虑到横向和纵向的气动力学特性,以确保叶片在复杂的气流条件下能够稳定转动并捕捉风能。
风力发电系统的新型叶片设计

风力发电系统的新型叶片设计一、引言风力发电作为新能源的一种形式,已经成为了现代社会中不可或缺的一部分。
发电的过程中,风力叶片是非常重要的。
如今,随着技术的发展,人们对风力发电设备的性能和效率也提出了更高的要求,尤其是针对于风力叶片的设计。
本文将讨论风力发电系统中一种新型叶片设计方案。
二、传统风力叶片的设计传统风力叶片通常是由玻璃纤维和环氧树脂等材料制成的。
在设计中,主要考虑的因素包括减少噪音和提高叶片的力学强度。
叶片的形状和尺寸也是设计中需要考虑的一个重要因素,因为它们直接决定了叶片的效能。
三、新型叶片的设计近年来,研究人员在传统叶片基础上提出了一些新型叶片设计方案,以实现更高的效率和性能。
1. Vortex Bladeless西班牙的Vortex Bladeless公司开发出了一种不同于传统叶片的设计,他们称之为“无叶片叶轮”。
它不像传统的叶片那样具有固定的形状,而是由两个柱状物组成,通过压力波来达到捕捉风能的目的。
这种设计具有减少噪音、减少能源损失和较低的生产成本等优点。
2. Smart Blade德国的Smart Blade公司研究出了一种可以自适应改变形态的叶片,这种叶片搭载了传感器和电机,可以通过电子控制实现根据风力变化而自适应改变形态,以达到最佳效能。
这种智能叶片设计可以提高叶片的效率,并提高使用寿命。
3. Aerodyn德国的Aerodyn公司研究出了一种类似降落伞的风力叶片,其形状能更好地应对风力的变化,以及减少振荡和噪音。
这种“降落伞”形状叶片与传统的叶片相比效率提高了3%至5%,这是一个相当大的提高。
四、新型叶片设计的优点和挑战1. 优点新型叶片设计具有很多的优点,其中最显著的就是提高了效率、减少了噪音、缩短了制造周期,降低了生产成本。
此外,新型叶片的设计也使得输电线路的构建更加方便,这对于新型能源的推广具有非常重要的作用。
2.挑战新型叶片设计也面临一些挑战,例如实现该设计需要高精度的加工技术,这增加了生产成本和制造周期。
风机叶片应急预案

一、预案编制目的为提高风机叶片安全运行水平,保障人员生命财产安全,确保风机稳定运行,特制定本预案。
二、预案适用范围本预案适用于风机叶片在运行过程中出现的各类故障和突发事件。
三、组织机构及职责1. 预案领导小组负责组织、协调、指挥风机叶片应急预案的实施,下设以下小组:(1)应急指挥部:负责制定应急预案、组织协调、指挥应急处置工作。
(2)现场处置小组:负责现场应急处理、人员疏散、设备抢修等工作。
(3)技术支持小组:负责技术指导、故障分析、应急物资保障等工作。
2. 应急指挥部职责(1)制定、修订风机叶片应急预案。
(2)组织应急演练,提高应急处置能力。
(3)指挥、协调各小组开展应急工作。
(4)及时向上级报告事故情况。
3. 现场处置小组职责(1)现场应急处理:立即切断故障风机叶片电源,确保人员安全。
(2)人员疏散:迅速组织人员撤离危险区域,确保人员生命安全。
(3)设备抢修:组织抢修人员对故障风机叶片进行修复。
4. 技术支持小组职责(1)故障分析:对故障原因进行分析,提出修复方案。
(2)技术指导:为现场处置小组提供技术支持。
(3)应急物资保障:负责应急物资的采购、储备和分发。
四、应急响应流程1. 风机叶片故障报警(1)现场操作人员发现风机叶片故障时,立即向现场处置小组报告。
(2)现场处置小组接到报告后,立即向应急指挥部报告。
2. 应急指挥部启动预案(1)应急指挥部接到报告后,立即启动应急预案。
(2)组织现场处置小组、技术支持小组等相关部门开展应急工作。
3. 现场处置(1)现场处置小组迅速切断故障风机叶片电源,确保人员安全。
(2)组织人员疏散,确保人员生命安全。
(3)技术支持小组对故障原因进行分析,提出修复方案。
4. 设备抢修(1)现场处置小组根据技术支持小组提出的修复方案,组织抢修人员对故障风机叶片进行修复。
(2)抢修完成后,经现场处置小组确认故障排除后,恢复风机叶片运行。
5. 应急结束(1)故障排除后,应急指挥部宣布应急结束。
风力发电系统中叶片设计技巧研究

风力发电系统中叶片设计技巧研究随着可再生能源的重要性日益凸显,风力发电逐渐成为一种可持续发展的清洁能源选择。
风力发电系统中的叶片是其中最关键的组成部分之一,其设计对于提高发电效率和降低成本至关重要。
本文将探讨风力发电系统中叶片设计的技巧和研究进展。
叶片是风力发电机转换风能为机械能的关键部件。
在设计叶片时,需要考虑到诸多因素,包括气动特性、结构稳定性、材料选择以及制造成本等。
首先,叶片的气动特性决定了其转换风能的效率。
通过改变叶片的形状、曲率和厚度等参数,可以使叶片在不同的风速下实现最大的能量捕获。
同时,叶片的结构稳定性也是另一个需要考虑的重要因素。
由于风力发电系统需要长时间稳定运行,叶片的结构设计必须能够承受不同的风速和气候条件下的负荷。
此外,在叶片的材料选择和制造过程中,需要平衡材料的重量、强度和成本等因素,以确保叶片的质量和可持续性。
近年来,在风力发电叶片设计技巧的研究中取得了一些突破性进展。
首先是通过先进的气动设计方法来提高叶片的效率。
以往的叶片设计主要依赖于经验公式和试验数据,难以得到最优的设计方案。
而如今,计算流体力学(CFD)等先进模拟技术的应用使得设计师能够更好地理解和优化叶片的气动特性。
通过在计算机上模拟气流对叶片的影响,设计师可以预测叶片在不同风速下的性能,并根据模拟结果进行形状和结构的优化。
其次,材料科学的进步也为叶片设计带来了更多的选择。
传统的叶片制造材料主要是玻璃纤维增强塑料(GFRP),具有良好的强度和耐候性。
然而,随着碳纤维复合材料的发展与成本的下降,它们正在成为新一代风力发电叶片的备选材料。
碳纤维具有更高的强度和刚度,并且重量更轻,可以提高叶片的性能和耐久性。
此外,还有一些新型材料的研究正在进行中,如生物基复合材料等,这些材料具有较低的环境影响和更好的可持续性。
除了上述技术进展,叶片设计中的制造过程也在不断改进。
利用先进的制造技术,如3D打印和自动化制造,可以更高效地生产叶片,并减少制造成本。
风力发电机组风机叶片设计与优化

风力发电机组风机叶片设计与优化风力发电是一种清洁能源,得到了越来越广泛的应用。
而风机叶片作为风力发电机组的关键部件,其设计与优化对于风力发电机组的性能至关重要。
本文将着重探讨风机叶片设计与优化的相关内容,分析其在风力发电领域的重要性。
一、风机叶片的基本结构与功能风机叶片是风力发电机组的核心部件之一,通常由复合材料制成。
其主要功能是利用风力驱动风力发电机组的转子旋转,通过转子转动驱动发电机发电。
风机叶片的设计直接影响着整个风力发电机组的性能,因此合理的设计与优化显得尤为重要。
二、风机叶片设计的关键参数在进行风机叶片设计时,需要考虑的关键参数包括叶片的长度、形状、倾角、材料等。
叶片长度直接影响着叶片的受力情况和风力的受损情况,叶片形状和倾角则会影响风力的捕捉效率和叶片的受力分布。
选择合适的材料也是风机叶片设计中需要重点考虑的因素,通常采用的复合材料具有重量轻、强度高等优点,能够有效提高叶片的性能。
三、风机叶片设计的优化方法为了提高风机叶片的性能,需要进行设计的优化。
常用的优化方法包括气动外形优化、叶片结构优化和材料选择优化等。
气动外形优化可以通过数值模拟和实验测试来确定最佳的叶片外形,以提高叶片的气动效率;叶片结构优化可以通过有限元分析等手段来确定最佳的叶片结构,以提高叶片的受力性能;材料选择优化可以通过比较不同材料的性能和成本等因素,选择最适合的材料。
四、风机叶片设计与优化的发展趋势随着风力发电技术的不断发展,风机叶片设计与优化也在不断创新。
未来的风机叶片设计将更加注重性能与经济的平衡,通过不断提升叶片的气动效率、受力性能和材料性能,实现风力发电机组的更高效率和更长寿命。
综上所述,风机叶片设计与优化是风力发电技术中的关键环节,对于提高风力发电机组的性能至关重要。
随着技术的不断进步和发展,相信未来风机叶片的设计与优化会有更大的突破,为风力发电行业的发展贡献力量。
- 1、下载文档前请自行甄别文档内容的完整性,平台不提供额外的编辑、内容补充、找答案等附加服务。
- 2、"仅部分预览"的文档,不可在线预览部分如存在完整性等问题,可反馈申请退款(可完整预览的文档不适用该条件!)。
- 3、如文档侵犯您的权益,请联系客服反馈,我们会尽快为您处理(人工客服工作时间:9:00-18:30)。
收稿日期:2012-07-02第30卷第2期计算机仿真2013年2月文章编号:1006-9348(2013)02-0247-05单兵多功能应急供电系统中风机叶片的设计蒋亮亮,赵雁(武警工程大学,陕西西安710086)摘要:关于单兵多功能供电系统中风机叶片的可靠性问题,为了保证设计质量,选择单兵多功能应急供电系统中风机叶片的翼型(NACA4409和NACA4412)进行分析,并选取了合适的翼型,采用基于贝茨理论,利用几何变换及计算机仿真的方法,运用profili 软件获得叶型各截面的初始参数,经坐标变换后得到了三维坐标,并进行分析,得到了扭曲叶片的三维实体模型。
仿真结果表明,单兵多功能应急供电系统中风机叶片的整体设计具有低风速启动和整体重量轻的特性,是一种可行的设计方案。
关键词:军事装备;风机叶片设计与建模;几何变换;计算机仿真中图分类号:N945.12文献标识码:ADesign of Fan Blade for Individual Functionof Emergency Power Supply SystemJIANG Liang -liang ,ZHAO Yan(Armed Police Engineering University ,Xi'an Shanxi 710086,China )ABSTRACT :In this paper ,individual function of emergency power supply system of fan blade airfoil (NA-CA4409and NACA4412)was analyzed in order to ensure the design quality about the multi function power supply system on individual fan blade reliability problems.We selected the right wing based on Bates theory ,used the geo-metric transformation and the method of computer simulation ,and the profili software to obtain the initial parameters of each section of the leaf ,and finally obtained the three -dimensional coordinates.The analysis was carried on to obtained the twisted blade 3-D solid model.The simulation results show that individual function of emergency power supply system for fan blade design has the characteristics of starting at low wind speed and light weight ,which is a feasible design scheme.KEYWORDS :Military equipment ;Wind turbine blade design and modeling ;Geometric transformation ;Computer simulation1引言随着武警部队遂行多样化任务的增多,临时勤务的复杂性,突发性越来越考验部队的应急反应能力和综合保障能力。
如何在突发状况下,保障应急分队中的突击小队具有可靠的能源供应,满足在复杂或紧急情况下通信、警示、降温、照明、求救等设备的能源供应,保障任务的圆满完成和官兵的生命安全是一个值得研究的问题。
基于部队在野外艰苦环境下的条件限制和任务要求,设计出一款专用于野外特殊环境的风光手摇蓄联合发电系统是一个创新的想法。
风力机叶片是风力机中最基础和最关键的部件,其良好的设计、可靠的质量和优越的性能是保证风力发电机组正常稳定运行的决定因素。
因此,风轮叶片的设计在风力发电机组设计中占有不可估量的地位[1 3]。
本文采用CFD 软件对NACA4409和NACA4412两种翼型进行气动性分析,选取合适的翼型,并基于贝茨理论,采用较为简化的设计方法对特定的微型风力机叶片进行了外形设计,在此之后,运用点的坐标变换理论[4]将翼型的二维剖面坐标转换成对应安装角处的三维空间实际坐标,通过一定方式导入Pro /E 软件中,最终得到扭曲叶片的三维实体模型。
2风力机叶片的外形设计2.1风力发电机的设计要求整套发电系统满足部队在野外任何艰苦环境下能随时—742—随地发电,确保任务的圆满完成,这要求设备质量轻、便于携带,因此风机设计是重点,经过查阅相关的技术资料,根据当前部队的实际,风机初始设计条件如表1。
表1风力发电机设计初始条件额定功率(W)额定风速(m/s)启动风速(m/s)停机风速(m/s)2.2112252.2风轮直径D的确定风力机直径通常根据所设计风力发电机的功率,确定风轮叶片扫掠面积,从而可计算出风轮直径[5]:D=2S/槡π(M)式中S=NeKCaCtv3η(Ne———风力机有效功率,取2.2W;K———单位换算系数,按选取0.6127;C a、C t———分别为空气高度换算系数和空气湿度密度换算系数,根据有关资料查得C a= 0.912、Ct=0.963;v———按风力发电机使用地方的风速给定11m/s;η———风力机全效率,取0.1)。
经计算可得D= 0.198m,则取D=20cm。
2.3确定叶片数B及叶尖速比λ一般小型风力发电机为高速风轮,叶尖速比系数较高,一般选择尖速比系数的范围为6 7[6]。
风轮叶片数和叶尖速比系数及风轮转速有着密切的联系,风轮的阻力越大,风轮的转速越慢,此外叶片数还与叶尖速比有一定的匹配关系,见表2。
根据实际需要,本文选定B=4,λ=6。
表2叶尖速比与叶片数匹配[7]尖速比叶片数尖速比叶片数1 2 38 246 123 845 88 153 52 42 12.4翼型的选择在所有叶片影响参数中,翼型是最重要的一个。
翼型的选择对风力机效率十分重要,为提高风力机的效率,翼型的选取应尽量使升阻比趋于最大值。
本文利用CFD软件Flu-ent对常用的NACA翼型中具有代表性的NACA4409和NA-CA4412两种翼型进行气动性分析,研究其翼型在二维流场中的压力和速度分布情况,通过对比分析选取合适的翼型。
2.4.1翼型的网络划分在ANSYS ICEM-CFD中建立两种翼型的几何模型和计算域,对计算域进行C型网格划分如图1和图2所示。
2.4.2翼型的压力云图将生成的网格导入FLUENT求解器,选择SST k-ω湍流模型,该模型使用混合函数将标准k-e模型与k-ω模型结合起来,包含了转捩和剪切选项。
SST k-ω模型和标准k -ω模型相似,但有以下改进:①SST k-ω模型和k-e模型的变形增长于混合功能和双模型加在一起。
混合功能是为近壁区域设计的,这个区域对标准k-ω模型有效;对于自由表面,则对k-e模型有效。
②SST k-ω模型合并了来源于ω方程中的交叉扩散。
③湍流粘度考虑到了湍流剪应力的传波。
④模型常量不同。
这些改进使得SST k-ω模型比标准k-ω模型在在广泛的流动领域中有更高的精度和可信度。
将流体设定为ideal-gas,并将其物理属性设定为suth-erland三系数定律来求黏性。
设定边界条件时,将远场边界设定为压力远场,攻角为5.26度,来流速度0.7马赫;将物面条件设定为无滑移的固壁边界。
离散格式为二阶迎风格式,算法采用SIMPLE算法。
通过计算得到的NACA4409翼型和NACA4412翼型周围的压力分布云图,分别如图3和图4所示。
图3NACA4409翼型周围的压力分布—842—图4NACA4412翼型周围的压力分布2.4.3翼型静压力曲线为了直观地比较两种翼型的上下表面的压力差,运用TECPLOT360得到两种NACA4409和NACA4412两种翼型上下表面的静压力分布曲线,如图5、6所示。
2.4.4仿真结果分析图3和4中表明:由浅到深压强逐渐增大,其中浅色区域代表的压强为负值。
由于翼型上方和下方的气流速度不同,因此,翼型上方、下方所受的压力也不同,总的合力即为翼型在流动空气中受到的空气动力,此力可分解为升力和阻力,压强差越大产生的升力就越大[8]。
NACA4409的负压区域主要集中在翼型上表面中部,而NACA4412比较靠近翼型的前缘,NACA4409翼型下表面的浅灰色区域明显大于NA-CA4412,因此产生的压力也比较大。
由图5和6可知,NACA4412下表面的静压大多在0.2ˑ10-4Pa 左右,NACA4409的大多在0Pa 左右,因此NA-CA4409的下表面静压要大于NACA4412,而NACA4409与NACA4412的上表面静压的最小值都为-1.6ˑ10-4Pa ;NAC -A4412的上表面静压最小值在离整个翼型约处就急速增大而NACA4412则是在约处时才开始增大,因此,NACA4409翼型上表面的平均静压。
由图可看出,在整个翼型上表面的平均静压。
综上所述,NAC -A4409翼型的上下表面压力差要大于NACA4412翼型的上下表面的压力差,即NACA4409升力要大于NACA4412。
2.5翼型升阻比的比较采用Prifili 分析两种翼型的升阻比如图7所示,得到两种翼型在雷诺数Re 为392000时的升阻比的对比情况,雷诺数是在风速为6m /s ,弦长为1m 时计算得到的。
图7为NA-CA4409和NACA4412的升阻比曲线,从图可知在攻角为-4ʎ 6ʎ时NACA4409具有较高的升阻比,两种翼型在最大升阻比,两种翼型在最大升阻比时的相关参数对比如表7所示,因此,NACA4409翼型更能满足低风速启动的要求。
图7NACA4409与NACA4412的升阻比2.6翼型弦长计算考虑轮直径为4cm ,叶根至叶尖的距离为8cm ,由于风轮直径小,所以整个叶片为工作区域。
将叶片沿展向分为9个断面[9],叶片从转动中心至叶尖不同半径r i 处的叶片弦长(叶片翼型弦长)L i 计算式为:L i =(r i C i )/(C L B )式中:r i —叶片从转动中心至叶尖的不同位置的半径;C i —不同半径r i 处对应的形状参数,C i =16π9R /r iλ0λ2r i()R 2+槡49;C L —最佳升阻比时对应的升力系数0.9;B —风轮的叶片数。