加工中心对刀与刀具补偿操作教程
加工中心如何对刀步骤详解,会这六步妈妈再也不担心不会对刀了

加⼯中⼼如何对⼑步骤详解,会这六步妈妈再也不担⼼不会对⼑了⾸次使⽤数控加⼯中⼼对⼑存在疑问,随后⼩编就将如何对⼑告诉⼤家吧。
1,回零(返回机床原点)对⼑之前,⼀定要进⾏回零(返回机床原点)的操作,刹车于清除掉上次操作的坐标数据。
注意:X,Y,Z三轴都需要回零。
2,主轴正转⽤“ MDI”模式,通过输⼊指令代码使主轴正转,并保持中等旋转速度。
然后换成“⼿轮”模式,通过转换调节进⾏进⾏机床移动的操作。
3,X向对⼑⽤⼑具在⼯件的右边轻轻的碰下,将机床的相对坐标清零;将⼑具沿Z向提起,再将⼑具移动到⼯件的左边,沿Z向下到之前的同⼀⾼度,移动⼑具与⼯件轻轻接触,将⼑具提起,记下机床相对坐标的X值,将⼑具移动到相对坐标X的⼀半上,记下机床的绝对坐标的X值,并按(INPUT)输⼊的坐标系中即可(发那科系统输⼊“ X0。
”并按“测量”也可以)。
想学ug编程请加Q群699197696群⽂件下载ug学习100G学习资料。
4,Y向对⼑⽤⼑具在⼯件的前⾯轻轻地碰下,将机床的相对坐标清零;将⼑具沿Z向提起,再将⼑具移动到⼯件的后⾯,沿Z向下到之前的⾼度,移动⼑具与⼯件轻轻接触,将⼑具提起,记下机床相对坐标的Y值,将⼑具移动到相对坐标Y的⼀半上,记下机床的绝对坐标的Y值,并按(INPUT)输⼊的坐标系中即可(发那科系统输⼊“ Y0。
”按“测量”也可以)。
5,Z向对⼑将⼑具移动到⼯件上要对Z向零点的表⾯,慢慢移动⼑具⾄与⼯件上表⾯轻轻接触,记下此时的机床的坐标系中的Z向值,并按(INPUT)输⼊的坐标系中即可(发那科系统输⼊“ Z0。
”按“测量”也可以)。
6,主轴停转先将主轴停⽌转动,并把主轴移动到合适的位置,调取加⼯程序,准备正式加⼯。
模具加工中心对刀操作方法

模具加工中心对刀操作方法
模具加工中心对刀操作方法如下:
1. 准备工作:清洁加工中心的工作台面和刀具,确保工作区域干净整洁。
2. 安装刀具:选择合适的刀具并安装到加工中心的刀柄上,确保刀具安装牢固。
3. 定位工件:将待加工的工件放在加工中心的工作台面上,并使用夹具将工件固定好,确保工件位置准确。
4. 手动移动工件:通过手动操作,移动工件使其靠近刀具。
5. 切换到手动操作模式:切换加工中心为手动操作模式,使操作者可以自由移动和调整工件位置。
6. 对刀:在手动操作模式下,使用对刀仪或其他精密测量工具测量刀具和工件的相对位置,并调整刀具的位置,使其与工件上的尺寸和位置要求相符合。
7. 固定刀具位置:当刀具位置调整到合适的位置后,将刀具固定好,确保刀具不会松动或移动。
8. 检查刀具和工件位置:再次使用测量工具检查刀具和工件的相对位置,确保
调整准确。
9. 切换到自动操作模式:切换加工中心为自动操作模式,开始进行正式加工工作。
以上就是模具加工中心对刀的操作方法,希望对您有帮助。
如何用好加工中心刀具长度补偿功能

如何用好加工中心刀具长度补偿功能第一篇:如何用好加工中心刀具长度补偿功能如何用加工中心刀具长度补偿功能刀具补偿功能,是数控机床的一项重要功能,在准备功能中用G43、G44、G49表示,但是若使用得不好恨容易造成撞车和废品事故。
下面以加工中心为例,介绍生产实践中常用的机种刀具长度补偿方法。
1、刀具长度补偿功能的执行过程典型的指令格式为G43 Z_H_;或G44 Z_H_。
其中G43指令加补偿值,也叫正向补偿,即把编程的Z值加上H代码的偏值寄存器中预设的数值后作为CNC实际执行的Z坐标移动值。
相应的G44指令减去预设的补偿值,也叫负向补偿。
当指令G43时,实际执行的Z坐标值Z’=Z_+(H_);当指令G44时,实际执行的Z坐标值为Z’=Z_-(H_);这个运算不受G90绝对值指令或G91增量值指令状态的影响。
偏值寄存器中可预设正值或负值,因此有如下等同情况。
1)指令G43、H设正值等同于指令G44、H设负值的效果; 2)指令G43、H设负值等同于指令G44、H设正值的效果因此一般情况下,为避免指令输入或使用错误时失误,可根据操作者习惯采用两种方式: 1)只用指令G43,H设正值或负值; 2)H 只设正值,用指令G43或G44。
以下介绍使用较多的第一中情况:指令格式中Z值可以为0,但H0或H00将取消刀具长度补偿,与G49效果等同,因为0号偏值寄存器被NC永远置0.一般情况下,为避免失误,通过设定参数使用刀具长度补偿只对Z轴有效。
例如当前指令为G43X_H_;时,X轴的移动并没有被补偿。
被补偿的偏置值由H后面的代码指定。
例如H1设20.、H2-30.,当指令“G43 Z100.H1;”时,Z轴将移动至120处:而当指令“G43 Z100.H2;”时,Z轴将移动至70.处。
G43(G44)与G00、G01出现在一个程序段时,NC将首先执行G43(G44)。
可以在固定循环的程序段中指令G43(G44),这时只能指令一个H代码,刀具长度补偿同时对Z值和R值有效。
加工中心对刀方法
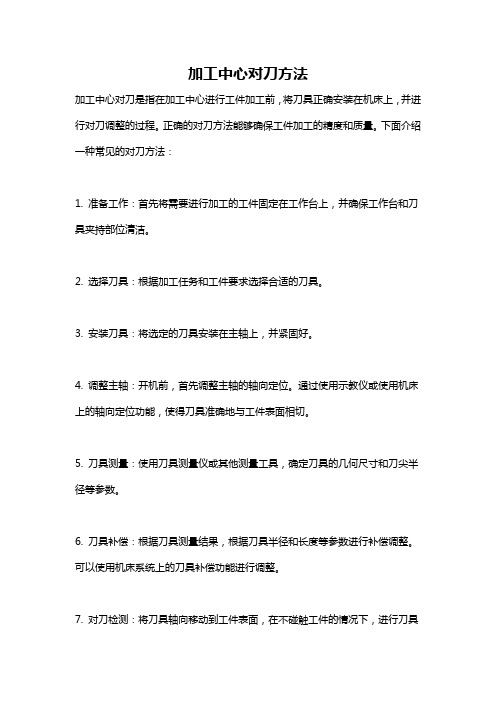
加工中心对刀方法
加工中心对刀是指在加工中心进行工件加工前,将刀具正确安装在机床上,并进行对刀调整的过程。
正确的对刀方法能够确保工件加工的精度和质量。
下面介绍一种常见的对刀方法:
1. 准备工作:首先将需要进行加工的工件固定在工作台上,并确保工作台和刀具夹持部位清洁。
2. 选择刀具:根据加工任务和工件要求选择合适的刀具。
3. 安装刀具:将选定的刀具安装在主轴上,并紧固好。
4. 调整主轴:开机前,首先调整主轴的轴向定位。
通过使用示教仪或使用机床上的轴向定位功能,使得刀具准确地与工件表面相切。
5. 刀具测量:使用刀具测量仪或其他测量工具,确定刀具的几何尺寸和刀尖半径等参数。
6. 刀具补偿:根据刀具测量结果,根据刀具半径和长度等参数进行补偿调整。
可以使用机床系统上的刀具补偿功能进行调整。
7. 对刀检测:将刀具轴向移动到工件表面,在不碰触工件的情况下,进行刀具
与工件的相对位置和距离检测。
可以使用示教仪或机床上的检测功能进行检测。
8. 调整刀具:根据对刀检测结果,通过调整刀具的位置和角度,使其与工件表面的相对位置和距离满足要求。
9. 完成对刀:完成上述步骤后,再次进行对刀检测和调整,直至满足加工要求为止。
10. 加工确认:对整个刀具和工件的安装和调试进行确认,确保工件加工的准确性和稳定性。
以上是常见的加工中心对刀方法,操作时需要根据具体机床的设备和操作手册进行操作,并注意安全措施。
铣削加工中心对刀方案及刀具长度补偿措施

() 2将刀具初始参 考点位置设置在非机床参考 点合 度补 偿值 的方 法 ( 2 。 种方 法 图 )这
合适 位 置上 ( 1 , 然 是为 了降低 调 整 刀具 和工件 相 对 图 )显 位置 的难度 ,它 使 得程 序员 可 以将刀 具位 置 设在 机 床运 动范围内, 在保 证 安 全 的前 提 下 的任 何合 适 位置 , 并且将 该位置作为换刀位置 。 至于 G 2 9 指令 中 x Y z的坐标 值 的 、、 获取 与前 方法 基本相 同 , 常先 移 动测量 刀具 参 考点移至 通 专用夹具 固定 点( 工件 坐标 原点 )然后在 MD 运行 方式下 , , I
实际操作时 z向工件偏置和刀具长度补偿值有 以下
( ) 于机外 对 刀 的 Z向设置 1基
这种对刀方法选择 了机床参考点作为刀具参考点的 设 置方法 : 起始点 , 当执行 回参考点操作 , 刀具就 找到程序的起点 ,
同时 选 择 机 床 参 考 点 作 为 换 刀位 置 就 显 得 比较 合 适 方 便 , 批量 生产 中很 有效 的对刀 方法 。 是 问题 在 于 G 2 令 9指 中 x、 z的坐 标值 不 能 由程序 员 在 编程 时 直接 给 出 , Y、 而 是 由操 作 者在 对 刀操 作后 给 出 ,这要 求 加工 前程 序 员 和 操作 者进 行 良好 沟通 。
这 是 一 种 靠 手 动 的操 作 机床 , 刀 具参 考 基 准 位 于 机 从
从 以上可 以看 出 , 利用 位置 寄存 器指 令 ( 9 或 G 0 G2 5) 际对 刀 调整 过程 中显得 繁 琐 复杂 , 率 不高 , 效 是一 种 传统
的对 刀方 法 。
加工中心对刀

指令格式:
G43 Z__ H__ G44 G49 指令功能 : 对刀具的长度进行补偿 指令说明: (1) G43指令为刀具长度正补偿; (2) G44指令为刀具长度负补偿; (3) G49指令为取消刀具长度补偿; (4) 刀具长度补偿指刀具在Z方向的实际位移比程 序给定值增加或减少一个偏置值;
(5) 格式中的 值是指程序中的指令值,即目 格式中的Z值是指程序中的指令值 值是指程序中的指令值, 标点坐标; 标点坐标; (6) H为刀具长度补偿代码,后面两位数字是 刀具长度补偿寄存器的地址符。 H01指01号寄存器,在该寄存器中存放对应 刀具长度的补偿值。 • 使用G43、G44时,不管用绝对尺寸还是用 增量尺寸指令编程,程序中指定的Z轴移动 指令的终点坐标值,都要与H代码指令的存 储器中的偏移量进行运算。
1. 刀具长度补偿 刀具长度补偿G43、G44、G49指令 、 、 指令 刀具长度补偿指令一般用于刀具轴向(Z 方向)的补偿,它使刀具在Z方向上的实际 位移量比程序给定值增加或减少一个偏置量, 这样当刀具在长度方向的尺寸发生变化时 (如钻头刃磨后),可以在不改变程序的情 况下,通过改变偏置量,加工出所要求的零 件尺寸。
执行G43时 H__中的偏置值 执行G43时:Z实际值=Z指令值+H__中的偏置_中的偏置值 H__中的偏置值
加工中心的刀具和刀具补偿说课讲解
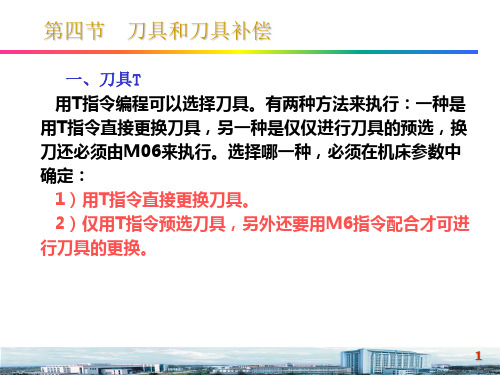
M05
25
M30
26
铣销凸台轮廓程序的实例;工件如图所示,凸台高为5mm。
27
12
第三节 加工中心的刀具补偿
N10 T1 M6; N20 G54 G90 G17 M03 S800 ; N30 G00 X0 Y0; N40 G41 G00 X20.0 Y10.0 D1 ; N50 G01 Y50.0 F200; N60 X50.0; N70 Y20.0; N80 X10.0; N90 G00 G40 X0 Y0 M05 ; N100 M02;
20
铣刀举例说明所要、刀具补偿 使用刀具补偿功能对工件的加工进行编程时,无需考虑 刀具长度或刀具半径。可以直接根据图纸尺寸对工件进行 编程。 刀具长度补偿
22
四、刀具长度补偿 刀具长度补偿基格式:T1 D1 说明:刀具更换后,程序中调用的刀具长度补偿立即生
N20 X40 Y80
N30 G02 X65Y55 I0 J-25
N40 G01 X95
N50 G02 X65 Y70 I15 J0
N60 G01 X105 Y45
N70 X110 Y35
N80 X90
N90 X65 Y15
N100 X40 Y40
N110 X30 Y60
N120 G40 X5 Y60 ;取消补偿方式
使用刀具半径补偿需要特别注意的问题
1)刀具半径补偿功能只能在轮廓的插补平面(G17~G19 指定)内生效,而在除插补平面外的其它坐标轴上不起作 用。 2)刀具半径补偿通过G41/G42生效。刀具必须有相应的D 补偿号才能有效。 3)只有在线性插补时(G00,G01)才可以进行 G41/G42 的补偿和G40取消补偿运行。即必须在运动中建立和取消刀 补,G41/G42没有使刀具运动的功能。
加工中心对刀步骤

加工中心对刀步骤
加工中心对刀:
一、对刀步骤:
注意事项:对刀完成后,机床坐标系与工件坐标系除了Z轴以外的正向是相反的。
1、机床主轴返回机床原点。
图1 图2
图3
首先将机床模式旋钮(图3)旋转至REF档位。
然后,按下+Z键,然后按下homestart键,机床返回到Z轴坐标原点;XY轴返回坐标原点时,情况相同,以X轴为例,如果工作台处于主轴的正侧,则按下+x 键,如果处于负侧则按下-X键,然后按homestart键,则主轴返回了X轴原点。
2.对刀:对刀时根据刀具行走路线不与工件碰撞的原则,选择XYZ三方向的对刀顺序。
(下面以XYZ顺序为例)
(1)、对刀开始,首先将机床调整至handle模式,通过手轮将刀尖移动至与预想作为工件坐标系原点的相近的位置。
(2)、Z轴按下offset按钮,将操作界面切换至参数输入界面。
通过手轮将主轴向下移动,待刀尖将要与工件接触时,更换手轮倍率,进行微量调整,直至听到开始切削的声音,或者接触,此时在输入面板上输入“Z0.0”,然后按测量键,此时Z轴零点确定了。
X轴按下offset按钮,切换至参数输入界面。
用手轮移动主轴至预想设为X轴坐标原点的位置,待刀尖与工件表面接触时,在输入面板上输入X31.5(或-31.5)。
正负的确定方法:如果机床的主轴轴线相对于工件上的对刀点处于机床坐标系的X轴的较小值的一侧,则输入X-31.5,否则输入X31.5 。
- 1、下载文档前请自行甄别文档内容的完整性,平台不提供额外的编辑、内容补充、找答案等附加服务。
- 2、"仅部分预览"的文档,不可在线预览部分如存在完整性等问题,可反馈申请退款(可完整预览的文档不适用该条件!)。
- 3、如文档侵犯您的权益,请联系客服反馈,我们会尽快为您处理(人工客服工作时间:9:00-18:30)。
加工中心对刀与刀具补偿操作教程
时间:2012-05-30 作者:模具联盟网点击: 1479 评论:0 字体:T|T
一、对刀
对刀方法与具体操作同数控铣床。
二、刀具长度补偿设置
加工中心上使用的刀具很多,每把刀具的长度和到 Z 坐标零点的距离都不相同,这些距离的差值就是刀具的长度补偿值,在加工时要分别进行设置,并记录在刀具明细表中,以供机床操作人员使用。
一般有两种方法:
1、机内设置
这种方法不用事先测量每把刀具的长度,而是将所有刀具放入刀库中后,采用 Z 向设定器依次确定每把刀具在机床坐标系中的位置,具体设定方法又分两种。
( 1 )第一种方法将其中的一把刀具作为标准刀具,找出其它刀具与标准刀具的差值,作为长度补偿值。
具体操作步骤如下:
①将所有刀具放入刀库,利用 Z 向设定器确定每把刀具到工件坐标系 Z 向零点的距离,如图 5-2 所示的 A 、 B 、 C ,并记录下来;
②选择其中一把最长(或最短)、与工件距离最小(或最大)的刀具作为基准刀,如图 5-2 中的 T03 (或 T01 ),将其对刀值 C (或 A )作为工件坐标系的 Z 值,此时 H03=0 ;
③确定其它刀具相对基准刀的长度补偿值,即 H01= ±│ C-A │, H02= ±│ C-B │,正负号由程序中的 G43 或 G44 来确定。
④将获得的刀具长度补偿值对应刀具和刀具号输入到机床中。
( 2 )第二种方法将工件坐标系的 Z 值输为 0 ,调出刀库中的每把刀具,通过 Z 向设定器确定每把刀具到工件坐标系 Z 向零点的距离,直接将每把刀具到工件零点的距离值输到对应的长度补偿值代码中。
正负号由程序中的 G43 或 G44 来确定。
2、机外刀具预调结合机上对刀
这种方法是先在机床外利用刀具预调仪精确测量每把在刀柄上装夹好的刀具的轴向和径向尺寸,确定每把刀具的长度补偿值,然后在机床上用其中最长或最短的一把刀具进行 Z 向对刀,确定工件坐标系。
这种方法对刀精度和效率高,便于工艺文件的编写及生产组织。
三、刀具半径补偿设置
进入刀具补偿值的设定页面,移动光标至输入值的位置,根据编程指定的刀具,键入刀具半径补偿值,按 INPUT 键完成刀具半径补偿值的设定。
一、对刀
对刀方法与具体操作同数控铣床。
二、刀具长度补偿设置
加工中心上使用的刀具很多,每把刀具的长度和到 Z 坐标零点的距离都不相同,这些距离的差值就是刀具的长度补偿值,在加工时要分别进行设置,并记录在刀具明细表中,以供机床
操作人员使用。
一般有两种方法:
1、机内设置
这种方法不用事先测量每把刀具的长度,而是将所有刀具放入刀库中后,采用 Z 向设定器依次确定每把刀具在机床坐标系中的位置,具体设定方法又分两种。
( 1 )第一种方法将其中的一把刀具作为标准刀具,找出其它刀具与标准刀具的差值,作为长度补偿值。
具体操作步骤如下:
①将所有刀具放入刀库,利用 Z 向设定器确定每把刀具到工件坐标系 Z 向零点的距离,如图 5-2 所示的 A 、 B 、 C ,并记录下来;
②选择其中一把最长(或最短)、与工件距离最小(或最大)的刀具作为基准刀,如图 5-2 中的 T03 (或 T01 ),将其对刀值 C (或 A )作为工件坐标系的 Z 值,此时 H03=0 ;
③确定其它刀具相对基准刀的长度补偿值,即 H01= ±│ C-A │, H02= ±│ C-B │,正负号由程序中的 G43 或 G44 来确定。
④将获得的刀具长度补偿值对应刀具和刀具号输入到机床中。
( 2 )第二种方法将工件坐标系的 Z 值输为 0 ,调出刀库中的每把刀具,通过 Z 向设定器确定每把刀具到工件坐标系 Z 向零点的距离,直接将每把刀具到工件零点的距离值输到对应的长度补偿值代码中。
正负号由程序中的 G43 或 G44 来确定。
2、机外刀具预调结合机上对刀
这种方法是先在机床外利用刀具预调仪精确测量每把在刀柄上装夹好的刀具的轴向和径向尺寸,确定每把刀具的长度补偿值,然后在机床上用其中最长或最短的一把刀具进行 Z 向对刀,确定工件坐标系。
这种方法对刀精度和效率高,便于工艺文件的编写及生产组织。
三、刀具半径补偿设置
进入刀具补偿值的设定页面,移动光标至输入值的位置,根据编程指定的刀具,键入刀具半径补偿值,按 INPUT 键完成刀具半径补偿值的设定。
一、对刀
对刀方法与具体操作同数控铣床。
二、刀具长度补偿设置
加工中心上使用的刀具很多,每把刀具的长度和到 Z 坐标零点的距离都不相同,这些距离的差值就是刀具的长度补偿值,在加工时要分别进行设置,并记录在刀具明细表中,以供机床操作人员使用。
一般有两种方法:
1、机内设置
这种方法不用事先测量每把刀具的长度,而是将所有刀具放入刀库中后,采用 Z 向设定器依次确定每把刀具在机床坐标系中的位置,具体设定方法又分两种。
( 1 )第一种方法将其中的一把刀具作为标准刀具,找出其它刀具与标准刀具的差值,作为长度补偿值。
具体操作步骤如下:
①将所有刀具放入刀库,利用 Z 向设定器确定每把刀具到工件坐标系 Z 向零点的距离,如图 5-2 所示的 A 、 B 、 C ,并记录下来;
②选择其中一把最长(或最短)、与工件距离最小(或最大)的刀具作为基准刀,如图 5-2 中的 T03 (或 T01 ),将其对刀值 C (或 A )作为工件坐标系的 Z 值,此时 H03=0 ;
③确定其它刀具相对基准刀的长度补偿值,即 H01= ±│ C-A │, H02= ±│ C-B │,正负号由程序中的 G43 或 G44 来确定。
④将获得的刀具长度补偿值对应刀具和刀具号输入到机床中。
( 2 )第二种方法将工件坐标系的 Z 值输为 0 ,调出刀库中的每把刀具,通过 Z 向设定器确定每把刀具到工件坐标系 Z 向零点的距离,直接将每把刀具到工件零点的距离值输到对应的长度补偿值代码中。
正负号由程序中的 G43 或 G44 来确定。
2、机外刀具预调结合机上对刀
这种方法是先在机床外利用刀具预调仪精确测量每把在刀柄上装夹好的刀具的轴向和径向尺寸,确定每把刀具的长度补偿值,然后在机床上用其中最长或最短的一把刀具进行 Z 向对刀,确定工件坐标系。
这种方法对刀精度和效率高,便于工艺文件的编写及生产组织。
三、刀具半径补偿设置
进入刀具补偿值的设定页面,移动光标至输入值的位置,根据编程指定的刀具,键入刀具半径补偿值,按 INPUT 键完成刀具半径补偿值的设定。