淬火油槽问题探讨1
大型淬火水槽的流场分析及其优化研究

摘要目前我国重点发展高新装备制造业,大型铸锻件淬火工艺是突破大型工件制备技术的关键。
淬火是热加工过程的最后一道工序,起着举足轻重的作用。
淬火过程中,水槽内均匀、高速的液流是保证工件冷却速度、获得所需组织与性能的关键。
本文借助于计算流体力学技术对现有大型淬火水槽内的流场进行数值模拟,得到大型淬火水槽内部流场的分布情况及其特点,发现现有水槽结构设计不合理,出现短路现象及工件内壁附近流速过低;在此基础之上,重点考察了增加挡板和改变不同芯棒参数的淬火水槽内的流场,提出了改进方案,最终得到了优化结果。
关键词:大型淬火水槽,计算流体力学,数值模拟,流场ABSTRACTAt present we focus on developing high-tech equipment manufacturing industry, and Forging quenching process is a breakthrough technology the key to preparation of large workpieces. Quenching is a thermal process of the last process plays an important role. Quenching process, the tank uniform, high-speed flow is to ensure that the workpiece cooling rate, microstructure and properties of the necessary key. Existing large-scale flow within the quench tank has been simulated by means of computational fluid dynamics technology. Large-scale flow field quench tank and characteristics of the distribution is known, found that the existing tank structure design is unreasonable, short-circuit behavior and low velocity near the inner wall of the workpiece; On this basis, mainly inspected and changed different baffle mandrel to increase the quenching parameters of the flow tank, the improved scheme, the end result has been optimized.Key words:large quenching tank, computational fluid dynamics, numerical simulation, flow field目录1绪论 (1)1.1 课题的目的和意义 (1)1.2 国内外研究现状与发展趋势 (2)2淬火过程基础研究 (4)2.1 淬火原理 (4)2.2 淬火信息和工业生产情况 (5)3数值建模的基础研究 (9)3.1 流场的数学模型 (9)3.2 FLUENT软件介绍 (11)4淬火水槽流场CFD模拟计算 (15)4.1 水槽结构 (15)4.2 几何建模和网格划分 (15)4.3 数学模型和边界条件 (18)4.4 结果分析 (18)4.5 现有问题总结 (23)4.6 参数附录 (23)5 淬火水槽的优化改进 (28)5.1 挡板 (28)5.2 芯棒 (30)5.3 参数附录 (40)6 结论 (45)参考文献 (46)致谢 (48)1 绪论随着现代科学技术的发展,对金属零件的性能和可靠性的要求越来越高。
油槽安全技术操作规程

淬火油槽安全操作规程
1、工作前应仔细检查,冷却循环装置是否完好,能正常运行。
2、操作时应集中精力,注意油温,油槽最高温度必须控制在额定范围内。
3、操作人员不得擅自离开工作岗位,要经常观察油温,防止油温超高而引起火灾。
4、工件进入油槽要迅速、稳当。
严禁把带水工件放入槽内。
5、淬火工件侵入油槽后不允许露出油面,直至淬火完成,防止油面着火造成火灾。
6、往油槽加油时,油中不准带有水分,并注意不要加得太满,以免工件淬火时油液
溢出。
7、油槽如发生起火现象时,应用灭火器灭火,严禁用水灭火。
8、捆工件用的铁丝要扣牢,工件的工装要完好,以防掸入油槽或油液溅起伤人。
9、注意油液清洁,严格管理好油槽,防止油液外溢污染环境。
10、保持油槽周围的清洁,不准存放易燃易爆物品。
11、在油槽区,应注意脚下打滑,防止跌倒。
12、淬火工序完成后,应及时清理周边,防止污染环境。
2023年淬火槽的安全防护常识

2023年淬火槽的安全防护常识,包含以下几个方面内容:一、淬火槽的定义和作用1.1 定义淬火槽是一种用于将金属材料在高温下进行淬火处理的设备,它能使金属材料快速冷却,提高其硬度和强度。
1.2 作用淬火槽的主要作用是对金属材料进行淬火处理,使其获得理想的组织和性能,提高材料的硬度和强度,延长材料的使用寿命。
二、淬火槽的安全防护措施2.1 设备安全2.1.1 设备的材质选择淬火槽的材质应具备较高的抗热性能和抗腐蚀性能,能够耐受高温和淬火介质的腐蚀。
2.1.2 设备的结构设计淬火槽的结构设计应合理,保证其在使用过程中的稳定性和安全性,避免设备倾覆或发生其他意外情况。
2.1.3 设备的温度控制系统淬火槽应配备温度控制系统,能够精确控制淬火过程中的温度,防止温度过高导致设备失效或温度过低导致淬火效果不理想。
2.2 操作安全2.2.1 操作人员的培训和资质要求进行淬火槽操作的人员应经过专门的培训,掌握淬火槽的基本原理和操作技能,并且需具备相关的操作证书或资质。
2.2.2 操作规程和安全操作流程淬火槽的操作过程应严格按照操作规程和安全操作流程进行,确保操作的安全性和操作员的人身安全。
2.2.3 安全防护装置的使用淬火槽应配备必要的安全防护装置,如安全门、紧急停机装置等,以确保操作人员在紧急情况下能够及时脱离险境。
2.3 淬火介质的安全2.3.1 淬火介质的选择根据不同的金属材料和淬火要求,选择合适的淬火介质,确保其稳定性和安全性。
2.3.2 淬火介质的储存和使用淬火介质应存放在专门的容器中,防止泄漏和污染环境。
使用时要遵守安全操作规程,避免造成伤害。
2.3.3 淬火介质的排放和处理淬火槽在淬火过程中会产生大量的废液和废气,应采取相应的措施进行妥善处理,防止对环境造成污染。
三、常见问题及应对措施3.1 设备故障如果淬火槽发生故障,应立即停止使用,并及时进行维修和检修,确保设备的正常运行。
3.2 淬火效果不理想如果淬火效果不理想,可能是由于温度控制不准确、淬火介质的质量不合格等原因造成的,应及时调整参数或更换淬火介质。
淬火油污垢处理技术及应用
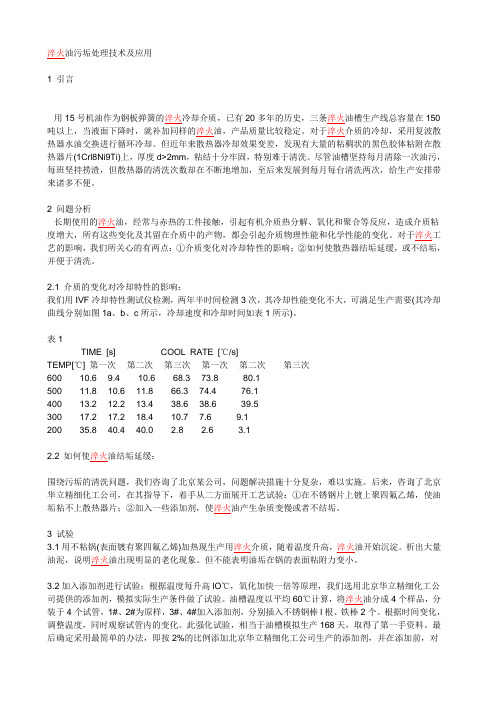
淬火油污垢处理技术及应用1 引言用15号机油作为钢板弹簧的淬火冷却介质,已有20多年的历史,三条淬火油槽生产线总容量在150吨以上,当液面下降时,就补加同样的淬火油,产品质量比较稳定。
对于淬火介质的冷却,采用复波散热器水油交换进行循环冷却。
但近年来散热器冷却效果变差,发现有大量的粘稠状的黑色胶体粘附在散热器片(1Crl8Ni9Ti)上,厚度d>2mm,粘结十分牢固,特别难于清洗。
尽管油槽坚持每月清除一次油污,每班坚持捞渣,但散热器的清洗次数却在不断地增加,至后来发展到每月每台清洗两次,给生产安排带来诸多不便。
2 问题分析长期使用的淬火油,经常与赤热的工件接触,引起有机介质热分解、氧化和聚合等反应,造成介质粘度增大,所有这些变化及其留在介质中的产物,都会引起介质物理性能和化学性能的变化。
对于淬火工艺的影响,我们所关心的有两点:①介质变化对冷却特性的影响;②如何使散热器结垢延缓,或不结垢,并便于清洗。
2.1 介质的变化对冷却特性的影响:我们用IVF冷却特性测试仪检测,两年半时间检测3次,其冷却性能变化不大,可满足生产需要(其冷却曲线分别如图1a、b、c所示,冷却速度和冷却时间如表1所示)。
表1TIME [s] COOL RATE [℃/s]TEMP[℃] 第一次第二次第三次第一次第二次第三次600 10.6 9.4 10.6 68.3 73.8 80.1500 11.8 10.6 11.8 66.3 74.4 76.1400 13.2 12.2 13.4 38.6 38.6 39.5300 17.2 17.2 18.4 10.7 7.6 9.1200 35.8 40.4 40.0 2.8 2.6 3.12.2 如何使淬火油结垢延缓:围绕污垢的清洗问题,我们咨询了北京某公司,问题解决措施十分复杂,难以实施。
后来,咨询了北京华立精细化工公司,在其指导下,着手从二方面展开工艺试验:①在不锈钢片上镀上聚四氟乙烯,使油垢粘不上散热器片;②加入一些添加剂,使淬火油产生杂质变慢或者不结垢。
淬火常见问题与解决方法与技巧

淬火常见问题与解决方法与技巧Ms点随C%的增加而降低淬火时,过冷奥氏体开始转变为马氏体的温度称之为Ms点,转变完成之温度称之为Mf点。
%C含量愈高,Ms点温度愈降低。
0.4%C碳钢的Ms温度约为350℃左右,而0.8%C碳钢就降低至约200℃左右。
淬火液可添加适当的添加剂(1)水中加入食盐可使冷却速率加倍:盐水淬火之冷却速率快,且不会有淬裂及淬火不均匀之现象,可称是最理想之淬硬用冷却剂。
食盐的添加比例以重量百分比10%为宜。
(2)水中有杂质比纯水更适合当淬火液:水中加入固体微粒,有助于工件表面之洗净作用,破坏蒸气膜作用,使得冷却速度增加,可防止淬火斑点的发生。
因此淬火处理,不用纯水而用混合水淬火。
(3)聚合物可与水调配成水溶性淬火液:聚合物淬火液可依加水程度调配出由水到油之冷却速率之淬火液,甚为方便,且又无火灾、污染及其他公害等,颇具前瞻性。
(4)干冰加乙醇可用于深冷处理容液:将干冰加入乙醇中可产生-76℃之均匀温度,是很实用的低温冷却液。
硬度与淬火速度之关联性只要改变钢材淬火冷却速率,就会获得不同的硬度值,主要原因是钢材内部生成的组织不同。
当冷却速度较慢时而经过钢材的Ps曲线,此时奥氏体转变温度较高,奥氏体会生成波来体,转变开始点为Ps 点,转变终结点为Pf点,波来体的硬度较小。
若冷却速度加快,冷却曲线不会切过Ps曲线时,则奥氏体会转变成硬度较高的马氏体。
马氏体的硬度与固溶的碳含量有关,因此马氏体的硬度会随着%C含量之增加而变大,但超过0.77%C后,马氏体内的碳固溶量已无明显增加,其硬度变化亦趋于缓和。
淬火与回火冷却方法之区别淬火常见的冷却方式有三种,分别是:(1)连续冷却;(2)恒温冷却及(3)阶段冷却。
为求淬火过程降低淬裂的发生,临界区域温度以上,可使用高于临界冷却速率的急速冷却为宜;进入危险区域时,使用缓慢冷却是极为重要的关键技术。
因此,此类冷却方式施行时,使用阶段冷却或恒温冷却是最适宜的。
淬火后有孔洞的原因

淬火后有孔洞的原因
淬火是一种常见的金属处理方法,通过加热金属至一定温度后迅速冷却,使金属获得更高的硬度和强度。
然而,在淬火过程中常常会出现孔洞,这是由一些原因导致的。
淬火后出现孔洞可能是由于金属内部存在气体或其他杂质。
在淬火过程中,高温会使金属内的气体膨胀,如果气体无法及时释放,就会形成孔洞。
此外,金属内的杂质也可能导致孔洞的形成,因为杂质会干扰金属晶格的排列,使金属在淬火过程中产生应力集中,从而形成孔洞。
淬火的冷却速度过快也会导致孔洞的形成。
淬火过程中,金属由于快速冷却而产生应力,如果冷却速度过快,金属内部的应力无法完全释放,就会形成孔洞。
尤其是当金属厚度较大或形状复杂时,冷却速度的不均匀性会导致孔洞的形成。
金属的化学成分以及淬火工艺参数的选择也会影响孔洞的形成。
金属中的某些元素可能会与其他元素发生反应,形成气体或产生气泡,导致孔洞的形成。
而淬火工艺参数的选择不当,如温度过高、冷却速度过快等,也会增加孔洞的出现。
为了避免淬火后出现孔洞,首先需要保证金属材料的质量。
金属材料应经过严格的筛选和检测,确保杂质含量低,并且内部无气孔。
其次,在淬火过程中,应控制好温度和冷却速度,避免过高的温度
和过快的冷却。
同时,淬火工艺参数的选择应根据金属的性质和形状进行合理调整。
在淬火过程中出现孔洞是由于金属内部的气体、杂质以及冷却速度等因素共同作用的结果。
通过合理的金属材料选择和淬火工艺参数控制,可以有效减少孔洞的形成,提高金属的质量和性能。
对传统淬火油槽增加搅拌装置的技术改造

大 部 分钢 材 的 淬火 通 常 使 用淬 火 油作 为淬 火 冷 却 介 质 ,相 对 应 盛 装 淬 火 油 的 淬 火 冷 却 设 备 即 为 淬 火 油 比重 增 加 下 降 ,油 槽 内 形 成 垂 直 温 差 层 ,
热 量 的传 递 。
经过对上述3 个方案的认真考虑 、比对、研究 和论证 ,根 据各 自的利弊 与性价 比 ,最终选 定方
案 三喷射式搅拌 。 2 . 喷射 式搅拌方案 实施
喷 射式 搅 拌 装 置是 由离 心 式 热 油泵 ,将 热 油从
( 2 )提 高淬 火 冷却 介 质温 度均 匀度 。搅 拌 可 使整个淬 火油槽 的介质形成一 个较为均 匀的温
致使工件冷却不均匀。 ( 2 )工 件在静 油 中淬 火 ,表 面极 易形 成 蒸 汽膜 ,影 响淬火质量 。工件刚刚进 入淬火油 的瞬
淬火油槽 。对于淬火 油槽 ,有两 个基本要求 :具
有 足 够 的 淬 火 冷 却 能 力 ;保 证 淬 火 油 温 度 均 匀 。
由于淬 火油槽淬火 冷却能 力的设计 ,应根 据实际 情况而 定 ,本文 不作论述 。本 文重 点阐述 如何对
( 4 )淬火时 间长 ,炉 内未淬火工件表面极 易 氧化 。由于操作者在 淬火过程 中炉 盖是敞开 的 ,
炉 内涌 入 大 量 空 气 ,原 有 密 封 情 况 下 的 保 护 气 氛
被破坏 ,使 尚未 出炉 的高温零件表 面氧化 ,特别 是最后 出炉的工件表面氧化尤为严重。
二、传统淬火油槽增加搅拌的必要性
响 。所 以 ,加 强 搅 拌 的 必 要 性 可 以 大 致 归结 为 如
淬火油及其使用过程中常见误区
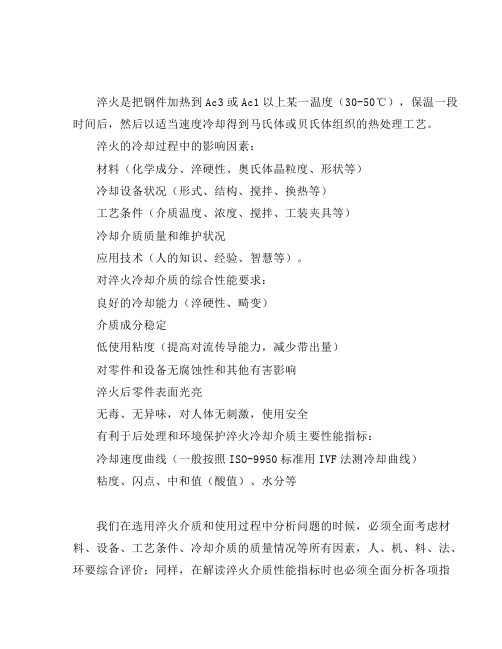
淬火是把钢件加热到Ac3或Ac1以上某一温度(30-50℃),保温一段时间后,然后以适当速度冷却得到马氏体或贝氏体组织的热处理工艺。
淬火的冷却过程中的影响因素:材料(化学成分、淬硬性、奥氏体晶粒度、形状等)冷却设备状况(形式、结构、搅拌、换热等)工艺条件(介质温度、浓度、搅拌、工装夹具等)冷却介质质量和维护状况应用技术(人的知识、经验、智慧等)。
对淬火冷却介质的综合性能要求:良好的冷却能力(淬硬性、畸变)介质成分稳定低使用粘度(提高对流传导能力,减少带出量)对零件和设备无腐蚀性和其他有害影响淬火后零件表面光亮无毒、无异味,对人体无刺激,使用安全有利于后处理和环境保护淬火冷却介质主要性能指标:冷却速度曲线(一般按照ISO-9950标准用IVF法测冷却曲线)粘度、闪点、中和值(酸值)、水分等我们在选用淬火介质和使用过程中分析问题的时候,必须全面考虑材料、设备、工艺条件、冷却介质的质量情况等所有因素,人、机、料、法、环要综合评价;同样,在解读淬火介质性能指标时也必须全面分析各项指标,并和历史数据对比,切忌以偏概全,犯盲人摸象的错误。
以下,我会列举淬火油使用方面可能存在的一些认识上的常见误区,供大家参考。
淬火油及其使用过程中常见误区问题一:如何评价淬火油冷却速度?经常有人拿淬火油冷却曲线的最高冷速大小来评价某种油的冷却性能,这种说法其实似是而非。
我们来看看快速油的冷却速度曲线,要准确评价油的冷却能力必须考虑淬火的对象—钢铁材料,考虑材料因素不得不考虑其C曲线。
对于大部分钢铁材料而言,C曲线拐点温度出现在500-600℃(钢渗碳后表面相当于过共析钢,拐点温度出现在550℃附近)。
因此如果油的最大冷速出现在这一区域的话,或者说淬火油在这一温度区域的冷速大,才是对产品淬火最有利的。
最大冷速必须与最大冷速出现温度结合起来看。
另外,由于IVF法是在特定条件下进行测量的,热电偶材料、尺寸与实际工件都有差异,考虑到工件截面大小,对于大截面工件,由于在实际淬火时其表面和心部冷却都要更慢,因此在这根曲线上还需要考虑400℃冷速,甚至是300℃冷速。
- 1、下载文档前请自行甄别文档内容的完整性,平台不提供额外的编辑、内容补充、找答案等附加服务。
- 2、"仅部分预览"的文档,不可在线预览部分如存在完整性等问题,可反馈申请退款(可完整预览的文档不适用该条件!)。
- 3、如文档侵犯您的权益,请联系客服反馈,我们会尽快为您处理(人工客服工作时间:9:00-18:30)。
方案对比
• (2)方案二为压缩空气搅拌:优点是改造 工程简单,方便,费用低,只要将压缩空 气接入油槽即可起到搅拌作用。缺点是: ①压缩空气在油中会产生气泡,使工件表 面产生软点。②压缩空气中含有水分,水 分进入淬火油槽,影响淬火油的冷却性能, 甚至导致淬火油报废。
方案对比
• (3)方案三为油液自身循环搅拌(即喷射 式搅拌)具体做法是用油泵从淬火油槽中 抽油、增压,通过管道将油打回淬火油槽, 从而使油液循环搅拌翻腾。高压油造成的 油液翻腾搅拌效果类似于压缩空气,但却 克服了压缩空气搅拌的两大缺点。
TRIZ的解题模式
TRIZ工具
标准问题 问题模型
解决方案 标准解法 模型
应用 验证
转化
归纳 定义
应用
具体 问题
具体问题解
问题描述与分析
• 淬火存在的问题 • (1)淬火油槽内上下油液温度相差较大, 给产品热处理质量带来隐患。 • (2)工件在静油中淬火,表面极易形成蒸 汽膜,影响淬火质量。 • (3)工人劳动强度大,生产效率低(特别 是大件)。
淬火油槽问题探讨
课题概要
• 淬火是将金属工件加热到某一适当温度并 保持一段时间,随即浸入淬冷介质中快速 冷却的金属热处理工艺。 • 对于淬火油槽,有两个基本要求:具有足 够的淬火冷却能力;保证淬火油温度均匀。
项目概要
• 本课题对淬火问题进行探讨,利用TRIZ理 论技术系统进化法则,建立物场模型,再 用专业技术理论进行方案设计,并对方案 进行验证。
问题描述与分析
问题描述与分析
构建系统模型
• 物场模型:是由两个物质和一个场这样三个元 素所构成的完全的、最小的技术系统。是一种 用图形表达问题的符合语言来揭示系统的功能, 描述任何技术系统中不同元素之间发生的不足 的、有害的、过度的和不需要的各种相互作用. 设计人员通过使用这些特定的符号来有序地进 行解决发明问题的方法。
构建系统模型
• 识别模型中的三个要素,构建物场模型
冷却
F
S1
S2
淬火油
工件
构建系统模型
• 对此物场模型进行分析,由于在问题描述 中静止的淬火油存在的问题,造成静止的 淬火油对工件的冷却作用不足,即作用力 有用但不充分。
寻找标准解
寻找标准解
• 根据物场模型中类型分析,作用不足主要 采用class2&3; • 从标准解中第二级增强物场模型中选取: 双物质——场模型。
方案对比
• 经过对上述3个方案的认真考虑、比对、研 究和论证,根据各自的利弊与性价比,最 终选定方案三喷射离心式热油泵,将热 油从油槽中抽出,经过板式换热器冷却, 再以较高的压力通过开有若干出油孔的喷 油管路垂直送回油槽,强制油液产生对流、 循环的原理制成(见附图)。该方案在实 现冷却的同时,也起到循环搅拌的效果。 且油液翻腾程度完全可控,操作者可根据 实际情况通过阀门进行流量大小的调整。
寻找标准解
冷却
F1
S1
S2
淬火油
工件
F2
机械场
寻找标准解
• 外加机械场主要通过搅拌完成,搅拌能够 造成淬火油在淬火工件之间的强烈运动, 以加快热交换过程,使高温阶段蒸汽膜形 成初期即被破坏,从而提高了工件在淬火 过程中的冷却速度,同时在低温对流期也 加速热量的传递,避免油温局部温度过高, 使槽中各部分油温趋于均匀,从而达到加 强冷却的效果。
具体方案
• 提出三种搅拌方案:叶轮搅拌、压缩空气 搅拌和油液自身循环搅拌(即喷射式搅 拌)。
方案对比
• (1)方案一为叶轮搅拌:是目前使用较多 的一种方法,因其可获得较好的紊流效果, 叶轮无需管道,容易安装、取出和维修。 缺点是:①制造工作量大,且需安装导流 板,费用高。②叶轮占据油槽的有效空间。 ③油液横向流动势必会加大细长件的变形 量。
方案实施
结论
• 改造完成后,经过生产实践,效果非常理 想并顺利通过验收。