硝基氯苯生产工艺规范文件
硝基氯苯生产工艺规程

硝基氯苯生产工艺规程引言硝基氯苯是一种重要的有机化工产品,广泛用于医药、农药、染料和化学合成等领域。
本文档旨在规范硝基氯苯的生产工艺,确保生产过程的安全性、稳定性和高效性。
原料准备1.氯苯:以优质氯苯作为原料,应满足生产的质量要求。
2.硝化混酸:使用浓硝酸和浓盐酸混合制备硝化混酸,要保证成分稳定、纯度高。
反应装置1.反应釜:采用耐腐蚀材料制造的密闭式反应釜,容量根据生产规模确定。
2.加热设备:采用电加热方式,温度可调控,保证反应温度的稳定性。
生产工艺步骤1.反应物的预处理–将氯苯加入反应釜中,并加入适量的硝化混酸。
–搅拌均匀至反应液体。
2.反应过程–控制反应釜内的温度,将反应温度维持在80℃ - 90℃。
–随着反应的进行,观察反应液体的颜色变化。
–当反应液体呈现暗黄色时,表示反应完成。
3.分离与提纯–反应结束后,将反应液体倒入分离漏斗中。
–分离出的有机相为硝基氯苯,水相则可作为废水处理。
–对硝基氯苯进行蒸馏提纯,除去残留的反应物和杂质。
4.产品质量检验–采用物理化学方法对产品进行质量检验,包括外观、纯度、挥发性等。
–保留样品进行备案。
5.废物处理–将废水进行中和处理,达到环保要求。
–将废弃物进行安全集中处理,遵守相关法律法规。
安全操作规程1.操作人员必须穿戴个人防护装备,包括防护服、手套、安全眼镜和防毒面具等。
2.操作人员应熟悉应急处理程序,并定期进行事故应急演练。
3.严禁在无风险评估和防护措施下进行操作。
4.确保操作区域通风良好,避免有毒气体积聚。
5.确保加热设备正常工作,避免温度过高导致事故。
6.严禁饮食、吸烟和使用明火等行为。
结论本文档详细介绍了硝基氯苯的生产工艺规程,包括原料准备、反应装置、生产工艺步骤、产品质量检验和安全操作规程等方面的内容。
通过严格按照规程进行操作,可确保硝基氯苯的生产过程安全、稳定和高效。
同时,也需要重视废物处理和环境保护工作,保护生态环境,遵守相关法律法规。
2,4-二硝基氯苯生产工艺

2,4-二硝基氯苯生产工艺1. 引言2,4-二硝基氯苯是一种重要的有机化工原料,广泛应用于染料、药物和农药等领域。
本文将介绍2,4-二硝基氯苯的生产工艺及其相关情况。
2. 原料准备2,4-二硝基氯苯的生产原料主要包括苯、硝酸、氯化亚铁和硫酸等。
首先,苯经过精制处理,去除杂质,提高反应的纯度。
硝酸和氯化亚铁也需要经过精制处理,以确保原料的质量。
硫酸作为催化剂,起到促进反应的作用。
3. 反应步骤2,4-二硝基氯苯的生产主要通过硝化反应完成。
具体的反应步骤如下:3.1 苯硝化在反应釜中加入苯和硝酸,经过搅拌混合均匀。
然后,加入硫酸作为催化剂,控制反应温度和反应时间。
反应温度一般在50-60摄氏度之间,反应时间一般为2-4小时。
在反应过程中,要保持反应釜内的温度稳定,并进行有效的搅拌以提高反应效率。
3.2 氯化反应苯硝化反应完成后,将反应液加入到氯化釜中。
在氯化釜中,加入氯化亚铁并进行搅拌混合。
反应温度一般控制在60-70摄氏度之间,反应时间为2-3小时。
在反应过程中,要保持反应釜内的温度和搅拌速度稳定,以确保反应的有效进行。
4. 分离与纯化氯化反应完成后,得到的反应产物为混合物。
为了获得纯度较高的2,4-二硝基氯苯,需要进行分离与纯化。
常用的分离方法包括蒸馏、结晶和萃取等。
根据具体情况,选择合适的分离方法进行操作。
5. 产品质量控制在2,4-二硝基氯苯的生产过程中,需要进行产品质量控制。
常用的检测方法包括气相色谱法、红外光谱法和质谱法等。
通过这些方法,可以对产品进行成分分析和纯度检测,确保产品质量符合要求。
6. 安全注意事项在2,4-二硝基氯苯的生产过程中,需要注意安全事项。
硝化反应和氯化反应都是放热反应,因此要控制好反应温度,避免发生危险事故。
同时,要加强通风设备的使用,防止有毒气体的积聚。
在操作中要佩戴好个人防护装备,严格按照操作规程进行操作,确保人身安全。
7. 结论2,4-二硝基氯苯是一种重要的有机化工原料,在染料、药物和农药等领域有广泛应用。
硝基氯苯生产工艺规程副本
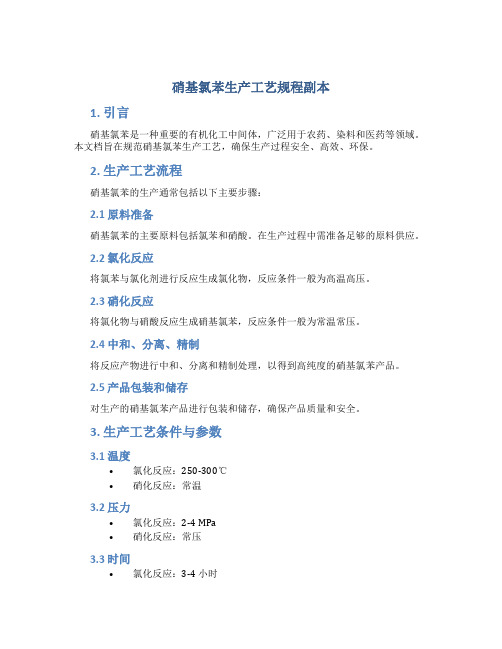
硝基氯苯生产工艺规程副本1. 引言硝基氯苯是一种重要的有机化工中间体,广泛用于农药、染料和医药等领域。
本文档旨在规范硝基氯苯生产工艺,确保生产过程安全、高效、环保。
2. 生产工艺流程硝基氯苯的生产通常包括以下主要步骤:2.1 原料准备硝基氯苯的主要原料包括氯苯和硝酸。
在生产过程中需准备足够的原料供应。
2.2 氯化反应将氯苯与氯化剂进行反应生成氯化物,反应条件一般为高温高压。
2.3 硝化反应将氯化物与硝酸反应生成硝基氯苯,反应条件一般为常温常压。
2.4 中和、分离、精制将反应产物进行中和、分离和精制处理,以得到高纯度的硝基氯苯产品。
2.5 产品包装和储存对生产的硝基氯苯产品进行包装和储存,确保产品质量和安全。
3. 生产工艺条件与参数3.1 温度•氯化反应:250-300℃•硝化反应:常温3.2 压力•氯化反应:2-4 MPa•硝化反应:常压3.3 时间•氯化反应:3-4 小时•硝化反应:30-60 分钟3.4 搅拌速度•氯化反应:100-200 rpm•硝化反应:适度搅拌3.5 配料比例•氯化反应:氯苯与氯化剂摩尔比为1:1•硝化反应:氯化物与硝酸摩尔比为1:13.6 废气处理生产过程中产生的废气需要进行处理,以防止对环境造成污染。
常见的废气处理方法包括吸收/吸附、气体燃烧等。
4. 安全措施4.1 通风设施生产车间应配备良好的通风设施,以确保有害气体的排除和新鲜空气的流通。
4.2 防护设备操作人员应佩戴符合安全要求的防护设备,如防护眼镜、手套、防护服等,以降低事故风险。
4.3 储存安全生产过程中的原料和产物需储存在防火、防爆的仓库,并按照规定分类和标识。
4.4 废物处理废弃物需分类储存,并通过合法的处理方式进行环保处理,以减少对环境的影响。
5. 质量控制5.1 原料检验对进厂的原料进行严格的检验,确保其质量符合规定标准。
5.2 过程监控对生产过程中的关键环节进行实时监控,如温度、压力等,及时调整参数以保证产品质量。
硝基苯工艺规程

3、酸性硝基苯的中和、水洗
液碱的配制:液碱由液碱泵打碱到配碱罐循环,同时 打开软水稀释,其加软水量和液碱加料量为2:1,使碱 浓度在10%左右,当配碱罐(V517)液位达80%停止配 碱,再用液碱泵将稀碱送到稀碱高位槽备用。
自硝化分离器分离后的酸性硝基苯溢流至中和锅, 10%液碱从稀碱高位槽底部经流量计流入混合器中,同 时回收软水从软水高位槽(V519)经流量计流入混合器 中与稀碱混合,经混合稀释至3-5%浓度的稀碱流入中和 锅(F506),控制其出口PH在9-10,使酸性硝基苯得以 中和,中和后的硝基苯与废水由溢流管流出,沿切线方 向进入中和分离器(V521)中部,分离后上层废水去废 水捕集器(V534),下层硝基苯去一水洗锅(F507), 一水洗锅(F507)所用洗水系从二水洗锅(F508)水洗 后回收水,从一水洗锅(F507)中溢流出的硝基苯沿切 线方向进入一水洗分中部,分离后下层粗硝基苯流入二 水洗锅(F508),上层废水去废水捕集器(V534)。
4、产品用途:
硝基苯是重要的有机化工原料之一,用 于生产多种医药和染料中间体,例如用硝 基苯经磺化可生产硝基苯磺酸。也可直接 还原重排生产对氨基酚还可以进一步硝化 制得一系列中间体等。
硝基苯最大用途是用作生产苯胺。
二、原料规格
三、生产原理及主要化学反应
1、苯的硝化 主反应:
反应机理:HONO2++H2SO4→NO2++H2O+HSO4-
冀衡集团蓝天化工有限公司
硝基苯 工艺流程
主讲:冯世华
2011-04-09
主要内容:
产品说明 原料规格 生产原理及主要化学反应 工艺过程的叙述(附流程示意图) 不正常现象及其原因和处理办法 生产操作
氯苯硝化反应生产硝基氯苯间歇式反应釜的设计

氯苯硝化反应生产硝基氯苯间歇式反应釜的设计流程图:1.基本设计条件的选定1.1反应温度的确定设定: 物料的进料温度为25℃, 反应温度为45℃,出口温度为80℃【氯苯硝化工艺条件的研究】,夹套中水的进口温度为25℃,出口温度为40℃1.2 反应器的选择氯苯的硝化是一个强放热反应,而且在以混酸作硝化剂时,混酸中的硫酸被反应生成水稀释而放出大量热量。
这样大的热量如不及时移出,势必会使反应温度迅速上升,不仅会引起多硝化、氧化等副反应,使产品质量变坏,同时还会发生硝酸分解,产生大量红棕色二氧化氮气体,污染周围环境,严重时甚至会发生爆炸事故。
因此采取有效的冷却方式及时移出反应热是维持一定硝化温度、保持反应正常进行的重要条件。
此外,本实验产量小.因此,选用夹套式间歇反应釜1.3搅拌装置的选择搅拌器的作用是使釜内物料混合均匀。
搅拌器的类型很多,分为∶推进式、桨式、涡轮式、锚式、框式、螺杆式、螺带式等,搅拌器选型时主要考虑∶(1)保证从反应器壁或浸入式热交换装置到反应混合物能有高的给热系数。
(2)具有显著的搅拌效果,特别是对多相反应。
(3)搅拌所消耗的能量应尽可能小。
搅拌器结构的确定按标准构型搅拌装置考虑。
由于本设计中的混合液为不互溶的硝化反应液,常采用径向涡轮式搅拌器;当搅拌器置于容器中心时搅拌粘度不高的液体时,液体易形成旋窝,为了改善搅拌效果,消除打旋,则在器内设挡板.涡轮式搅拌器直径小,转速高,产生循环量大反应釜的传动装置的选择1、电动机的基本特性及选用通常电动机与减速机配套供应,设计时可根据反应器应配电机功率、转速、安装形式及防爆要求,选择电动机及配套的减速机。
减速装置的选择目前我国已颁布的标准釜用立式减速机,有摆线针齿行星减速机、两级齿轮减速机、三角皮带减速机和谐波减速机四种。
釜用立式搅拌机减速机外形及尺寸可查标准HG5-745-747-78根据上表选择两级齿轮减速机型号为A-LC100-12-Ⅱ型1.4换热装置的选择氯苯的硝化是一个强放热反应,而且在以混酸作硝化剂时,混酸中的硫酸被反应生成水稀释而放出大量热量,氯苯在这样大的热量如不及时移出,势必会使反应温度迅速上升,不仅会引起多硝化、氧化等副反应,使产品质量变坏,同时还会发生硝酸分解,产生大量红棕色二氧化氮气体,污染周围环境,严重时甚至会发生爆炸事故。
一硝基氯苯生产车间硝化工段工艺初步设计

一硝基氯苯生产车间硝化工段工艺初步设计学院:化工专业:应用化学(工)目录第一章设计任务书 (1)1.1 工艺流程示意图 (1)1.2 反应方程式 (2)1.3 已知条件 (3)第二章绪论 (5)2.1 产品的意义和用途 (5)2.2 产品的发展史 (5)2.3 年工作日的确定 (5)2.4 水、电、气及原料的供应 (6)2.5 厂址的水文、地质和气象资料 (6)2.6 设计依据及技术资料 (6)第三章工艺设计部分 (7)3.1 产品技术说明 (7)3.2 生产方法选择 (7)3.3 生产的基本原理 (7)3.4 原料规格与主要物化数据 (8)3.5 原料配比的确定 (9)3.6 工艺流程示意图 (9)3.7 流程叙述及控制条件 (11)3.8 物料衡算 (13)3.8.1 氯苯用量 (13)3.8.2 萃取锅计算 (13)3.8.3 1#硝化锅 (13)3.8.4 2#硝化锅 (14)3.8.5 3#硝化锅 (15)3.8.6 硝化分离 (15)3.8.7 萃取分离 (15)3.8.8 复算 (16)3.8.9 混酸配制 (17)3.8.10 一次水洗分离 (17)3.8.11 碱洗及碱洗分离 (18)3.8.12 二次水洗分离 (18)3.8.13 物料衡算表 (19)3.9 热量衡算 (23)3.9.1 配酸过程热量衡算 (23)3.9.2 1#硝化锅热量衡算 (25)3.10 设备计算和选型 (26)3.10.1 配酸锅 (26)3.10.2 1#硝化锅 (26)3.10.3 2#硝化锅 (27)3.10.4 3#硝化锅 (28)3.10.5 硝化分离器 (28)3.10.6 萃取锅 (29)3.10.7 萃取分离器 (30)3.10.8 一次水洗锅 (30)3.10.9 一次水洗分离器 (31)3.10.10 碱洗锅 (32)3.10.11 碱洗分离器 (32)3.10.12 二次水洗锅 (33)3.10.13 二次水洗分离器 (33)3.10.14 补集器 (34)3.10.15 贮罐 (35)3.11 设备一览表 (37)3.12 原料消耗定额表 (38)第四章三废治理 (39)4.1 三废的产生和数量 (39)4.2 三废的治理措施 (39)第五章安全技术与防火 (40)5.1 物料的危险特性 (40)5.2 防火、防爆、防腐蚀的要求和措施 (41)5.3 安全防火规则 (41)第六章建筑部分 (43)6.1 建筑特点 (43)6.2 防火、防毒、防腐蚀的考虑 (43)6.3 设备布置说明 (44)第七章参考文献 (45)附录 (46)附录1 工艺流程图(PFD) (46)附录2 设备平面布置图 (46)第一章设计任务书1.1 工艺流程示意图图1 工艺流程示意图1.2 反应方程式1、主反应(一硝基氯苯:邻、间、对位三种异构体混合)2、副反应二硝化:(二硝基物)硝酸分解: 2HNO 3 −−→ N 2O 5 + H 2O氧化反应:(硝基酚)Cl +HNO 3H SO NO 2H 2O +Cl Cl+HNO 3H 2SO 4NO 2H 2O+ClNO 2Cl +HNO 3H 2SO 4NO 2H 2O +Cl OH1.3 已知条件生产规模:年产1.2万吨一硝基氯苯产品质量:一硝基氯化苯纯度99%(包括邻、间、对位异构体混合物)车间总收率:95%年生产时间:330天建厂地点:甘肃兰州原料:工业氯苯纯度99.2%,含有机杂质0.8%浓硫酸纯度98%浓硝酸(发烟硝酸)纯度98%液碱纯度40%(NaOH水溶液)氯苯转化率:萃取锅1%1#硝化锅79%2#硝化锅16%3#硝化锅3.4%副反应:硝酸分解量为3%,假定只有硝酸分解,在1#硝化锅中进行。
氯苯硝化反应生产硝基氯苯间歇式反应釜的设计

氯苯硝化反响生产硝基氯苯间歇式反响釜的设计流程图:1.基本设计条件的选定反响温度确实定设定 : 物料的进料温度为 25℃ , 反响温度为 45℃ , 出口温度为 80℃【氯苯硝化工艺条件的研究】,夹套中水的入口温度为 25℃, 出口温度为 40℃反响器的选择氯苯的硝化是一个强放热反响,并且在以混酸作硝化剂时,混酸中的硫酸被反响生成水稀释而放出大批热量。
这样大的热量如不实时移出,必然会使反响温度快速上涨,不单会惹起多硝化、氧化等副反响,使产质量量变坏,同时还会发生硝酸分解,产生大批红棕色二氧化氮气体,污染四周环境,严重时甚至会发生爆炸事故。
所以采纳有效的冷却方式实时移出反响热是保持必定硝化温度、保持反响正常进行的重要条件。
别的 , 本实验产量小 . 所以 , 采纳夹套式间歇反响釜搅拌装置的选择搅拌器的作用是使釜内物料混淆平均。
搅拌器的种类好多,分为∶推动式、桨式、涡轮式、锚式、框式、螺杆式、螺带式等,搅拌器选型时主要考虑∶(1)保证从反响器壁或浸入式热互换装置到反响混淆物能有高的给热系数。
(2)拥有明显的搅拌成效,特别是对多相反响。
(3)搅拌所耗费的能量应尽可能小。
搅拌器构造确实定按标准构型搅拌装置考虑。
因为本设计中的混淆液为不互溶的硝化反响液, 常采纳径向涡轮式搅拌器;当搅拌器置于容器中心时搅拌粘度不高的液体时, 液体易形成旋窝 , 为了改良搅拌成效 , 除去打旋 , 则在器内设挡板 .涡轮式搅拌器直径小 , 转速高 , 产生循环量大反响釜的传动装置的选择1、电动机的基本特征及采纳往常电动机与减速机配套供给,设计时可依据反响器应配电机功率、转速、安装形式及防爆要求,选择电动机及配套的减速机。
减速装置的选择当前我国已公布的标准釜用立式减速机,有摆线针齿行星减速机、两级齿轮减速机、三角皮带减速机和睦波减速机四种。
釜用立式搅拌机减速机外形及尺寸可查标准HG5-745-747-78 依据上表选择两级齿轮减速机型号为 A-LC100-12- Ⅱ型换热装置的选择氯苯的硝化是一个强放热反响,并且在以混酸作硝化剂时,混酸中的硫酸被反响生成水稀释而放出大批热量,氯苯在这样大的热量如不实时移出,必然会使反响温度快速上涨,不单会惹起多硝化、氧化等副反响,使产质量量变坏,同时还会发生硝酸分解,产生大批红棕色二氧化氮气体,污染四周环境,严重时甚至会发生爆炸事故。
一硝基氯苯生产车间硝化工段工艺初步设计

一硝基氯苯生产车间硝化工段工艺初步设计1. 引言一硝基氯苯是一种重要的有机化工原料,广泛应用于化学合成、医药和染料工业。
本文档旨在就一硝基氯苯生产车间硝化工段的工艺进行初步设计,确保生产过程的安全和高效。
2. 工艺流程以下是一硝基氯苯生产车间硝化工段的初步工艺流程:1.原料准备:将氯苯和硝酸按照一定的摩尔比例准备好。
2.配料及混合:将准备好的氯苯和硝酸加入反应釜中。
3.反应过程:在反应釜中控制温度和压力,使氯苯和硝酸发生硝化反应,生成一硝基氯苯。
4.分离和提纯:经过硝化反应的混合物需要进行分离和提纯,以得到纯度较高的一硝基氯苯。
5.废水处理:在硝化过程中产生的废水需要经过处理,以达到环保要求。
3. 设备选择与布局3.1 设备选择1.反应釜:需要选择能够承受高温和高压的反应釜,确保反应过程的安全进行。
2.分离设备:可选用常见的分离设备,如蒸馏塔、萃取塔、结晶器等,根据生产需求进行选择。
3.废水处理设备:根据废水处理的性质选择合适的设备,如沉淀池、过滤器、膜分离设备等。
3.2 布局根据工艺流程和设备选择,进行车间布局设计。
要求在车间内保持合理的设备间距离,方便操作、维护和通风。
4. 工艺参数控制4.1 温度控制在硝化反应过程中,温度的控制对反应速度和产物质量有重要影响。
需要根据具体的反应动力学参数和工艺要求,选择合适的温度范围,并在实际生产中进行精确控制。
4.2 压力控制硝化反应过程中,压力的控制同样影响反应速度和产物质量。
根据反应动力学参数和工艺要求,选择合适的压力范围,并在实际生产中进行精确控制。
4.3 反应时间反应时间是反应过程中需要控制的重要参数。
通过实验和经验总结,确定适宜的反应时间范围,并在生产过程中严格控制。
5. 安全措施在一硝基氯苯生产车间硝化工段的工艺设计中,需采取一系列安全措施以确保工人和设备的安全。
1.设立紧急停车装置,一旦发生异常情况能够迅速停止设备运行。
2.设置通风系统,保证室内空气质量,减少有害气体的积聚。
- 1、下载文档前请自行甄别文档内容的完整性,平台不提供额外的编辑、内容补充、找答案等附加服务。
- 2、"仅部分预览"的文档,不可在线预览部分如存在完整性等问题,可反馈申请退款(可完整预览的文档不适用该条件!)。
- 3、如文档侵犯您的权益,请联系客服反馈,我们会尽快为您处理(人工客服工作时间:9:00-18:30)。
硝基氯苯生产工艺规程
1. 装置概况
1.1装置的目的
本装置的目的是利用氯苯与混酸在环形硝化器中在废酸存在的条件下,生成硝基氯苯,酸性硝基氯苯经中和、水洗、干燥、分离,得到对硝、邻硝和间硝成品。
1.2 设计能力
本装置设计能力为生产硝基氯苯100000吨/年。
2.产品讲明
2.1、产品名称
2.1.1、对硝基氯化苯
2.1.2、邻硝基氯化苯
2.2、分子式、结构式和分子量
2.2.1、对硝基氯化苯(以下简称对硝)
分子式:C6H4·NO2·Cl
分子量:157.5
2.2.2、邻硝基氯化苯(以下简称邻硝)
分子式:C6H4·NO2·Cl
分子量:157.5
2.3、物化性质
2.3.1、物理性质
2.3.1.1、对硝的物理性质
本产品为淡黄色的单斜形晶体,有甜味。
密度:68℃为1.520g/cm3 , 90℃为1.2979g/cm3 110℃为1.2722g/cm3 , 134℃为1.2457g/cm3凝固点:83.5℃
沸点:239.1℃(在101.33kPa<1atm>)
饱和蒸汽压与温度的关系:
lgP=3.66321 — 2184.9 t+230
P-MPa , t-℃
闪点:127℃(工业品为120℃)
熔化热:107.16 kJ/kg
汽化热:287.16 kJ/kg
热容量:固——1.088 kJ/kg·℃
液——1.633 kJ/kg·℃
溶解性:对硝难溶于水(见表一),易溶于醇、醚、丙酮等有机溶剂。
毒性:人体受该物质作用后, 能引起血压降低、肝脏病、肾脏病、刺痛皮肤和头痛 ,对血液有剧毒。
能够引起血色素变性,从而引起急性或慢性心脏病。
其他:此产品还有腐蚀性;易燃 ,能无氧燃烧;在密闭容器中能够发生爆炸。
在操作厂房里最大同意浓度为1mg/m3。
2.3.1.2、邻硝的物理性质
本产品为黄色斜形晶体 ,有苦杏仁味。
密度:71.5℃为1.320 g/cm3 , 90.5℃为1.2945g/cm3
92.5℃为1.297g/cm3 ,110℃为1.276g/cm3
凝固点:32.5℃
沸点:246℃(在101.33kPa<1atm)
饱和蒸汽压与温度的关系:
lgP=3.68122 – 2225.6 t+230
闪点:127℃-133℃
熔化热:108.42 kJ/kg
汽化热:389.30 kJ/kg
热容量:固——1.088 kJ/kg·℃
液——1.633 kJ/kg·℃
溶解性:邻硝难溶于水, 50℃时在水中的溶解度为0.0125g, 但它易溶于乙醇、乙醚和苯等有机溶剂。
毒性:本品有剧毒,对人体造血系统、神经系统有损害, 能够通过呼吸道及皮肤引起人体中毒,能够造成皮肤炎、肝功能减退等症状。
其他:在操作厂房内最大同意浓度为1mg/m3。
2.3.2、化学性质
2.3.2.1、对硝的化学性质
a.苯环上的氯原子在一定温度和压力下能够水解。
b.苯环上的氢原子能够被亲电质子取代,如:-NO2、-SO3H
c.硝基在酸性介质中易被还原
d.在高温下脱氯形成树脂化合物
e.在加热加压下与甲醇或乙醇作用生成醚类化合物
f.氨化脱氯生成胺
2.3.2.2、邻硝的化学性质
发生在氯原子上的取代反应和热聚合作用
邻硝上的氯原子比对硝上的氯原子爽朗。
a.水解反应
b.在加热加压下与甲醇或乙醇作用生成醚类化合物
c.在4.0-5.0Mpa下,氨化脱氯生成胺
d.在高温下能够热敏脱氯,在铜或铁的作用下能够加速反应
发生在碳原子上的取代反应
发生在硝基上的还原反应
2.4、产品用途
2.4.1、对硝能够衍生为对硝基苯胺、对硝基苯酚、对氨基苯酚、对氨基苯乙醚、对氨基苯甲醚、4,4’—二氨基联苯醚等有机化工产品,它广泛用于染料中间体、农药、医药、橡胶助剂等化工行业。
2.4.2、邻硝为制造农药的中间体之一,它经氨化还原为邻苯
二胺,再经环化等过程而制成多菌灵;它也是制取染料的中间体之一,经还原、甲基氧化、缩合、偶合等过程,可制多种染料;经甲基化、还原、水解、醛化等过程可制成香料;经还原、硫化、闭环等过程,可制得橡胶促进剂。
5、生产工序
5.1、生产工艺概述
氯苯在硫酸的存在下与硝酸起反应生成硝基氯苯混合物,硝基氯苯混合物与硝化废硫酸(俗称废酸)用沉降法分离, 酸性硝基氯苯混合物去中和、水洗,使之达到中性。
中性硝基氯苯混合物经干燥除去其中的氯苯和水分等,得粗品硝基氯苯混合物,再用精馏和结晶相结合的分离方法分离出对硝和邻硝两种产品以及富含间硝基氯苯的间位油和高沸点有机物废液(简称邻硝焦油)。
硝化废酸通过真空浓缩脱水硫酸浓度超过88﹪后, 和硝酸配成混酸循环使用。
5.2化学反应方程式
氯苯与混酸中的硝酸进行硝化反应, 要紧生成对、邻硝基氯苯和少量的间位异构体。
5.3副反应方程式
5.3.1、硝基氯苯与硝酸在硫酸的存在下生成二硝基氯苯。
5.3.2、氯苯中含有少量的苯和二氯苯的硝化反应
5.3.3、发生在苯环上的亲核反应
6、工艺流程叙述
6.1、原料接收
氯苯由氯化苯装置经泵输送沿架空管至本装置氯苯储罐,32﹪液碱由离子膜烧碱装置经泵输送沿架空管至本装置液碱罐,硝酸、硫酸经泵输送沿架空管进入硝酸大罐和硫酸大罐中。
硝酸、硫酸、氯苯、30﹪液碱供硝化岗位使用。
6.2、混酸配制
将符合原料规格的硫酸、废酸、硝酸按各自的用量,分不加入混酸釜内,进行搅拌,在混酸过程中放出的热量由混酸釜内的蛇管冷却器带走。
取样分析合格的混酸由混酸循环泵输送至混酸中间罐C,供硝化工序使用。
6.2.1、混酸配制的原料条件
原料名称原料浓度﹪
硫酸 H2SO4≥88 或≥98
硝酸 HNO3≥97.2 或≥98.2
抽取后废酸 H2SO4≥70
6.2.2、混酸组成
H2SO4 53.5±0.5﹪
HNO3 39±0.5﹪
H2O 7.5±0.5﹪
D.V.S 2.75~3.00
6.3、氯苯硝化
6.3.1、连续硝化加料表
硝化按最小生产量和最大生产量计算每小时所加的酸性氯苯(简称洗后油)。
酸性氯苯:混酸为(0.95~1.1):1(体积比)。
混酸:循环废酸为 1:(1.5~2.5)(体积比)计算。
6.3.2、生产工序叙述
6.3.2.1、硝化器A有效容积为4.34m3,材质为316L/Q235-B (管程/壳程),内有换热列管,装有混流泵,硝化器上设有温度计。
混流泵停止运转时,安全连锁装置开始运转,操作室内报警器自动报警,混酸进料切断阀、酸性氯苯进料切断阀同时关闭,洗后油泵和混酸输送泵的电源同时被切断。
6.3.2.2、硝化器B有效容积为2.17m3,材质为316L/Q235-B (管程/壳程),内有换热列管,装有混流泵,硝化器上设有温度计,混流泵停止运转时,安全连锁装置开始运转,操作室内报警器自动报警,硝化器A的混酸进料切断阀、酸性氯苯进料切断阀同时关闭,洗后油泵和混酸输送泵的电源同时被切断。
6.3.2.3、硝化锅A,有效容积为6.35m3,材质为304/Q235-B (内盘管/夹套),内有换热蛇管,外有夹套,装有推进式搅拌器,
锅上设有温度计。
6.3.2.4、硝化锅B,有效容积为6.35m3,材质为304/Q235-B (内盘管/夹套),内有换热蛇管,外有夹套,装有推进式搅拌器,锅上设有温度计。
6.3.2.5、硝化锅C,有效容积为6.35m3,材质为304/Q235-B (内盘管/夹套),内有换热蛇管,外有夹套,装有推进式搅拌器,锅上设有温度计。
6.3.2.6、硝化锅D,有效容积为6.35m3,材质为304/Q235-B (内盘管/夹套),内有换热蛇管,外有夹套,装有推进式搅拌器,锅上设有温度计。
6.2.3.7、酸性氯苯(又称洗后油)从酸性氯苯贮罐用卧式泵经流量计连续加入硝化器A;废酸从废酸高位罐底部,经流量计连续进入酸混合器内;混酸从混酸输送罐用混酸泵经流量计连续进入酸混合器内,混酸与废酸在酸混合器内混合后,进入硝化器A。
酸性氯苯与混酸在硝化器A中反应,反应物料由溢流管连续溢流到硝化器B, 然后进入硝化锅A,硝化锅B,硝化锅C,硝化锅D, 并连续反应, 硝化反应热由冷却水及废酸带走。
硝化温度较低达不到工艺指标时, 应调节冷却水量或用蒸汽保温。
6.3.2.8、硝化器和硝化锅内产生的氮氧化物废气,集中用废
酸汲取,含有氮氧化物的废酸进入废酸高位罐。
6.3.2.9废酸高位罐中的废气用碱性水汲取,进入汽液分离器。
6.3.2.10汽液分离器中的废气去尾气汲取塔,再次经碱性水汲取后,去废水储罐。
6.3.3、各硝化器、硝化锅反应温度操纵
注:加料应连续均匀, 温度操纵应准确, 否则会造成副反应增加或反应转化率过低。
硝化器A、B高位报警温度为45℃。
6.3.4、其他工艺操纵指标
工艺操纵指标见10.2,硝化工序生产操纵一览表见10.1。
6.3.5、硝化锅D的反应物料,由溢流管流出,分不沿切线方向进入硝化分离器A中部。
酸性硝基氯苯和废酸在分离器中进行连续分层, 上层为酸性硝基氯苯, 流向硝化分离器B,沿切线方向从硝化分离器B中部进入, 酸性硝基氯苯和废酸在分离器B中再次进行分层, 上层为酸性硝基氯苯流入中和锅A。
硝化分离器。