论基于并行工程的工业设计流程构建
基于并行工程的轿车新车型总装工艺过程的规划设计

2008年(第30卷)第2期汽 车 工 程A uto motiv e Eng ineering2008(Vo l .30)N o .22008039基于并行工程的轿车新车型总装工艺过程的规划设计**吉林大学985工程建设项目资助。
原稿收到日期为2007年4月3日,修改稿收到日期为2007年6月1日。
许小侠1,2,杨君武1,韩英淳1(1.吉林大学汽车工程学院,长春 130025; 2.长春工业大学机电工程学院,长春 130012)[摘要] 结合某企业新车型的开发工作,应用并行工程和CAP E 技术制订了新车型的总装工艺过程规划。
依照该规划,通过计算机三维动态虚拟仿真汽车总装过程,能将产品设计及工艺的潜在问题早期发现并予以解决。
实践证明,所做的研究工作确实收到了显著缩短新车型质量培育时间和提高总装技术水平的效果。
关键词:新车型开发;总装工艺流程;并行工程;CAPEProcess Planning fo r Final A ssembly o f N ew Car M odelBased on Concurrent EngineeringXu Xiaoxia 1,2,Yang Junwu 1&Han Yingchun 11.C o llege o f Automotive E ngineer ing ,J ilin Un iver sity ,Ch angch un 130025;2.College o f Mechanical and E lectr ical En gineer ing ,Chang chun University o f Technolo gy ,Changchun 130012[Abstract ] Based on the need of new car m odel developm ent in an ente rprise ,a pro cess planning fo r final assem bly o f new car m odel is w o rked out by applying co ncurrent engineering and CAPE techno logy .With the process planning ,a 3D dy namic virtual simulation on car final assembly process is perfo rmed ,en -abling the potential problem s in product design and pro cess technolo gy to be discove red and solved at an early stag e .The practice pro ves that the w o rk presented in this paper achieve s a go od effect in notably re -ducing the quality breeding time of new car m odel and im proving the technolo gical level o f final assembly .Keywords :new car model development ;final assembly process ;concurrent engineering ;C APE前言随着IT 技术和计算机虚拟仿真技术在制造业中的广泛应用,国外工业发达国家在汽车新车型开发中已普遍应用并行工程和CAPE 技术,以求使生产规划部门、产品研发部门和生产工程部门信息共享,实现部门间的并行的协同作业,同时还构建一个集成式的虚拟制造平台,采用计算机仿真技术模拟和预现产品的整个生产过程,从而能验证产品设计和制造过程方案的可行性,并将潜在的问题在产品的设计开发阶段解决。
并行工程案例
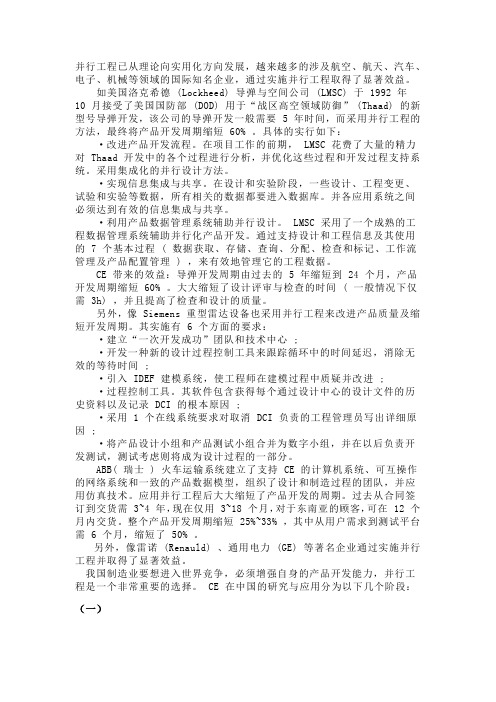
并行工程已从理论向实用化方向发展,越来越多的涉及航空、航天、汽车、电子、机械等领域的国际知名企业,通过实施并行工程取得了显著效益。
如美国洛克希德 (Lockheed) 导弹与空间公司 (LMSC) 于 1992 年10 月接受了美国国防部 (DOD) 用于“战区高空领域防御” (Thaad) 的新型号导弹开发,该公司的导弹开发一般需要 5 年时间,而采用并行工程的方法,最终将产品开发周期缩短 60% 。
具体的实行如下:·改进产品开发流程。
在项目工作的前期, LMSC 花费了大量的精力对 Thaad 开发中的各个过程进行分析,并优化这些过程和开发过程支持系统。
采用集成化的并行设计方法。
·实现信息集成与共享。
在设计和实验阶段,一些设计、工程变更、试验和实验等数据,所有相关的数据都要进入数据库。
并各应用系统之间必须达到有效的信息集成与共享。
·利用产品数据管理系统辅助并行设计。
LMSC 采用了一个成熟的工程数据管理系统辅助并行化产品开发。
通过支持设计和工程信息及其使用的 7 个基本过程 ( 数据获取、存储、查询、分配、检查和标记、工作流管理及产品配置管理 ) ,来有效地管理它的工程数据。
CE 带来的效益:导弹开发周期由过去的 5 年缩短到 24 个月,产品开发周期缩短 60% 。
大大缩短了设计评审与检查的时间 ( 一般情况下仅需 3h) ,并且提高了检查和设计的质量。
另外,像 Siemens 重型雷达设备也采用并行工程来改进产品质量及缩短开发周期。
其实施有 6 个方面的要求:·建立“一次开发成功”团队和技术中心 ;·开发一种新的设计过程控制工具来跟踪循环中的时间延迟,消除无效的等待时间 ;·引入 IDEF 建模系统,使工程师在建模过程中质疑并改进 ;·过程控制工具。
其软件包含获得每个通过设计中心的设计文件的历史资料以及记录 DCI 的根本原因 ;·采用 1 个在线系统要求对取消 DCI 负责的工程管理员写出详细原因 ;·将产品设计小组和产品测试小组合并为数字小组,并在以后负责开发测试,测试考虑则将成为设计过程的一部分。
基于并行工程思想的模具产品开发

基于并行工程思想的模具产品开发
□吕海秀
【摘 要】为解决传统模具开发的问题,提高市场竞争能力,以最快的速度开发出高质量的模具产品,技术领先的模具制造企业 在模具开发中开始采取并行工程思想,并行工程的目标在于强化企业竞争力,提高产品质量,降价制造成本,缩短产 品研发周期。
二、并行工程技术概述 1986 年美国国防部防御分析研究所( The Institute for Defense Analyses: IDA) 发表了著名的 R - 338 报告,提出了“并 行工程”CE 的概念,并行工程的定义为: “并行工程是集成 地、并行地设计产品及其相关的各种过程( 包括制造过程和 支持过程) 的系统方法。这种方法要求产品开发人员从设计 一开始就考虑产品整个生命周期从概念形成到产品报废处 理的所有因素,包括质量、成本、进度计划和用户的要求。” 并行工程的目 标 在 于 强 化 企 业 竞 争 力,提 高 产 品 质 量, 降价制造成本,缩短产品研发周期等。实现上述目标的主要 方法有: 设计质量改进———使早期生产中工程变更次数减少 50% 以上; 模具产品设计及其相关过程并行———使模具产品 开发周期缩短 40% ~ 60% ; 模具产品设计及其制造过程一体 化———使制造成本降低 30% ~ 40% 。并行工程要求在产品 设计阶段集中企业内有关产品研制部门的技术人员,共同设 计,并对产品的各 种 性 能 和 制 造 过 程 进 行 计 算 机 动 仿 真 ,生 成“软产品”,对它进行分析和评估,然后改进设计,以取得最 优结果。其技术内涵如图 2 所示:
Industrial & Science Tribune 2012.(11).1
·77·
产业与科技论坛 2012 年第 11 卷第 1 期
并行工程

Concurrent Engineering并行工程在本章中,提出了并行工程背后的理念以及当前方法用于实现并行工程。
并行工程设计鼓励在设计阶段同时考虑产品生命周期的所有方面。
它已被证明成功的缩短了产品开发时间和成本,避免了串行设计有关的典型问题。
公司在当今全球化和多变的市场竞争中不能承受长时间的开发周期及高成本。
并行工程的成功典例主要依赖设计团队的方法,来自不同部门的代表不同生产周期的观点的人协作。
然而,设计团队的做法和其他方法使他们无法管理(即存储,访问,更新等)进行并行工程所需的数据和巨大的信息量。
1、并行工程在当今竞争激烈的全球市场,制造企业必须通过高效的设计流程,确保产品的质量,有竞争力的价格,并给消费者提示可用性快速响应瞬息万变的市场需求和不断增长的产品复杂性。
成功案例[30]表明,这可以通过采用被称为并行工程(CE)制造的理念来实现。
这一理念鼓励在设计阶段同时考虑产品生命周期的各个方面。
它强调并行设计方法不同于传统方法的是在产品设计中隔离,然后才考虑在他们的可制造性、可测性、质量、适用性等方面 [19,20,32]。
传统的部门组织公司从事产品设计和制造时,使用串行或分阶段的方式来开发产品。
在这样的环境中工作的设计从一个部门到另一个预定的部门顺序推进。
每个部门负责产品的某些方面(即。
、可制造性、可测试性、质量、服务能力等)。
当检测出产品设计错误时产品必须送回责任部门重新设计,因此,串行设计的产品从概念到市场有着高开发的成本和较长的交货时间。
公司开始意识到这样的设计迭代在竞争日益激烈的市场中是不能被接受,正在改变他们的串行设计策略,平行进化成一个从概念开始强调产品的设计的新战略,即并行工程。
并行工程,也被称为同步或并行工程,是一个鼓励在设计阶段考虑产品的生命周期的所有方面的设计理念。
并行工程提倡对问题的预测和避免对潜在问题的时间延迟。
随后,减少了设计迭代,降低了开发成本,并缩短在将产品推向市场的交货期。
并行工程在冲模 CAD 系统设计中的应用研究的论文

并行工程在冲模 CAD 系统设计中的应用研究的论文本文从网络收集而来,上传到平台为了帮到更多的人,如果您需要使用本文档,请点击下载按钮下载本文档(有偿下载),另外祝您生活愉快,工作顺利,万事如意!1 前言模具技术是本世纪下半叶制造业中发展最快的技术之一,从理论上说,它是cad 技术最能发挥其优越性的领域。
由于模具的设计和制造是一个非常复杂的过程,并且是一个不断反复的过程,其中包括根据试模结果对实际模具的反复修改。
为了使产品质量高、成本低、周期短,正确的模具设计与制造方法应该是并行工程的方法[1] 。
目前,采用具有三维参数化特征造型功能的cad 支撑软件,在模具设计中应用并行工程原理,实现模具管理、工艺分析与设计及模具结构设计的一体化是一种较有代表性也很有应用前景的模具cad 系统开发方法。
2 并行工程的概念并行工程(concurrent engineering )或并行设计(concurrent design )实际是一种系统工程的方法,实行动态优化地处理问题[2] 。
传统的产品开发多采用串行方法,各个阶段都具有较强的独立性,这种工程方法由于在产品的设计阶段不能有效地评价产品的可制造性、可装配性、可维护性以及产品质量等诸多因素,造成在产品的制造阶段或实际组装阶段才有可能发现问题,形成产品开发过程制造到设计的大反馈,改动面广,改动量大,促使产品开发周期增长,成本提高,质量得不到保证。
并行工程以cims 信息集成技术为基础,通过组成多学科产品开发队伍,改进产品开发流程,利用各种dfx 工具等手段,把重点放在产品开发的早期——设计阶段,使产品开发的早期阶段就能及早考虑到其后阶段的各种因素,达到缩短产品开发周期、提高产品质量、降低产品成本的目标[3] 。
面向制造的设计方法(design for manufacturability )与面向装配的设计方法(design for assembly )是并行工程思想体现的重要方法。
从设计到制造集成解决方案-实现并行工程设计和制造

从设计到制造集成解决方案实现并行工程设计和制造并行工程设计和制造的重要性利用SOLIDWORKS 制造输出更快开始工作,同时争取时间进行创新并更快进入市场。
影响成本和质量的大部分决策都是在设计阶段作出的。
某些关键决策可能会在制造期间造成成本上升和质量下降,更快参与制造使它们能够对这些决策实施更大影响。
但是,在传统的串行流程中,设计工作基本上是“抛过墙”的,制造部门很难清晰了解并及时分享深入见解,因此无法作出什么改变。
SOLIDWORKS 解决方案支持完整的从设计到制造流程,使工程与制造之间的协作变得轻松很多。
这一集成平台意味着可以更加轻松地交换设计和制造数据,并且可降低出错风险。
任何设计变更都可以在整个平台内传播,从而确保每个人都在使用最新数据。
所有这些因素都能帮助制造团队及时了解会对其产生影响的工作情况,并帮助他们提供更多意见。
结果:并行完成更多工作,从而节省时间、提高质量并降低成本。
通过使用SOLIDWORKS PDM,可以妥善管理您的所有数据和相关工作流程。
这样,您就能更好地管理流程,并且绝对不会存在使用过时信息的风险。
更好地深入了解成本驱动因素以提高可盈利性利用SOLIDWORKS Costing 实现制造成本估算自动化、对照成本目标检查您的设计,并制定更准确的报价在设计和制造过程中,有很多机会可降低成本。
困难在于识别成本驱动因素,使您可以制定更好的决策以降低成本。
通过使用SOLIDWORKS 作为指导,您可以在设计当中准确发现会增加成本的区域,从而进行设计改进,以帮助实现成本目标。
可制造性问题是造成成本增加的最大来源之一。
我们讨论了几种SOLIDWORKS工具,它们可帮助您发现影响可制造性的问题。
SOLIDWORKS中的工具可用于检查正确的拔模、底切、干涉、公差叠加和可制造性设计(DFM),还有些工具可用于模拟并分析注射成型过程。
这些工具相结合,使您完全可以在进入制造阶段之前确保设计正确。
并行工程产品开发过程的建模方法学

并行工程产品开发过程的建模方法学[1]清华大学自动化系,北京100084彭毅吴祚宝张珂殊熊光楞摘要在并行工程中,为了实现产品开发过程的集成、并行和最优化,首先要建立能够充分反映产品开发过程各方面信息的产品开发过程模型。
通过对模型的仿真分析和优化,指导产品开发过程的实施。
本文首先提出了并行工程产品开发过程模型是集成多视图模型,随后提出了采用集成多视图建模理论的并行工程产品开发过程建模、分析和管理的方法学框架。
关键词并行工程产品开发过程建模管理集成多视图建模建模方法学引言并行工程[1]是集成地、协同地设计产品的系统化工作模式。
因为并行工程产品开发过程(Concurrent Engineering P roduct Development Process-CEPDP)是系统化工作模式的集中体现,其研究受到广泛重视。
目前文献中明确给出PDP定义的尚不多见,此处引用的定义[2]反映了对CEPDP一般的认识层次:/产品开发过程是对某产品从(形成)概念到生产开始这一特定工作流的一种既定方式(defined way),它要求生成考虑到直至产品废弃的整个产品生命周期中有关产品和生产的信息0。
由此定义可以看出,首先, CEPDP针对广义的设计阶段,制造阶段不在其中;其次,CEP DP以工作流为描述对象;对其他因素(如生成的产品信息)的考虑是隐含的。
此定义将并行工程的研究侧重点限制于广义的设计阶段是与并行工程的出发点相符的,以对CEPDP这一层次的理解为背景,对其研究基本采用工作流(wor kflow)的形式描述。
由此派生出多种描述任务顺序、串行并行和逻辑关系的工作流方法,如美国西弗吉尼亚大学的并行工程研究中心(CERC)提出的五类活动描述法[3][4]和美国空军阿姆斯特朗实验室(Armstro ng L ab.)提出的IDEF3方法[5]以及Kusiak的矩阵分析再造工程[6]等。
在这些方法中,建立CEPDP的过程是一次性的,只要事先用工作流描述,就可以按照执行,取得效果。
并行工程 论文 A4

并行工程及其实施摘要:为了在在市场上赢取最宝贵的时间,以最快的速度设计出高质量的产品,人们不得不想尽各种办法,而并行工程的思想只是其中一个,本文从并行工程的概念和目标出发,充分阐述了并行工程的特点,进一步论述了在机械产品开发过程中的并行,提出在产品并行开发过程中的冲突解决技术,最后谈到并行工程实施中的主要障碍。
关键词:并行工程团队过程并行冲突前言20世纪80年代中期以来,同类商品日益增多,企业之间的竞争愈来愈激烈,而且越来越具有全球性。
竞争焦点就是满足用户的T、Q、C、S(上市时间、产品质量、产品成本和售后服务)等指标。
竞争的核心问题就是时间。
为解决上述问题,提高市场竞争力,以最快的速度设计出高质量的产品,并尽快投放市场,在20世纪80年代末,制造业提出了并行工程(Concurrent Engineering,CE)的思想。
1.并行工程的定义与目标1988年12月,美国国防部防务分析研究所(IDA)提出了并行工程的概念,并给CE 下了定义:并行工程是一门以集成、并行方式开发产品及其相关过程(包括制造过程和支付过程) 的系统工程方法。
这种系统工程方法要求产品开发人员从设计一开始就考虑产品整个生命周期从概念形成到产品报废处理的所有因素,包括质量、成本、进度计划及用户要求。
并行工程其主要目标是:提高全过程(包括设计/工艺/制造/服务)中全面的质量;降低产品全生命周期中的成本(包括产品设计、制造、发送、支持、客户使用至产品报废等成本);缩短产品研制开发周期(包括减少设计反复,降低设计时间/生产准备时间/制造时间/发送时间等)。
并行工程与传统生产方式之间的本质区别在于并行工程把产品开发的各个活动看成是一个集成的过程,并从全局优点的角度出发,对集成过程进行管理与控制。
同时对已有的产品开发过程进行不断地改进与提高,以克服传统本行产品开发过程反馈造成的长周期与高成本等缺点,增强企业产品的竞争力。
从经营方面考虑,并行工程意味着产品开发过程重组(Reengineering),以便并行地组织作业。
- 1、下载文档前请自行甄别文档内容的完整性,平台不提供额外的编辑、内容补充、找答案等附加服务。
- 2、"仅部分预览"的文档,不可在线预览部分如存在完整性等问题,可反馈申请退款(可完整预览的文档不适用该条件!)。
- 3、如文档侵犯您的权益,请联系客服反馈,我们会尽快为您处理(人工客服工作时间:9:00-18:30)。
论基于并行工程的工业设计流程构建
作者:马德志谭卓然谭焱
来源:《中国科技博览》2016年第02期
[摘要]在企业产品创新管理集成化发展的推动下,工业设计的生产环境以及管理环境都有了较大的改变。
工业设计业务流程优化成为了研究适应并行工程要求的重中之重,在此条件下,优化和构建面向并行工程的工业设计新流程成为我们探讨的重要问题。
[关键词]并行工程;工业;设计
中图分类号:TB47 文献标识码:A 文章编号:1009-914X(2016)02-0080-01
一、并行工程中的工业设计
1. 并行工程对工业设计的影响
并行工程是对产品及其相关的制造过程和支持过程进行并行化设计的一种新产品开发模式。
它通过改进产品设计开发流程等手段,并行考虑产品生命周期各阶段因素,强调后续环节可能出现的问题要在设计的早期阶段就被析出并加以解决,最大限度地减少设计反复,缩短产品设计开发时间。
“并行”的核心内涵包括企业各部门的协助,生产各环节的协作,产品生命周期各阶段的协调,技术支持平台各系统的协同。
在产品并行设计条件下,产品开发过程的各环节、各要素在可能的情况下同时工作,协同运行。
工业设计的运行必须与并行工程的要求相一致,与其它并行要素协同运行。
2. 工业设计在产品并行设计中的地位
工业设计作为一个相对独立的部门,在市场导向的新产品开发流程中的地位越来越高,有主导新产品开发的趋势。
工业设计处在生产的上游环节,并贯穿于新产品开发的整个过程,其主导地位表现为:在产品开发团队中发挥主导作用,在产品形成中发挥创造作用,在质量成本效益中发挥控制作用。
具体包括:第一,产品的概念设计是由工业设计创意的;第二,产品的功能定位是由工业设计通过用户调研明确的;第三,产品的新造型、新结构、新包装等视觉形象是由工业设计孕育的;第四,产品结构设计的人性化趋势正在加强,工业设计对新产品开发的影响不断扩大;第五,产品的市场寿命周期是受工业设计制约和控制的,周期各阶段不同的设计策略对产品竞争构成重要影响。
二、工业设计与产品并行设计相关要素的链接
1.产品并行设计开发的相关要素
主要包括产品并行设计开发团队、虚拟设计网络平台和产品并行设计开发过程。
产品并行设计开发团队是由跨部门、跨职能的各专业人员组成,专业相近人员组成项目小组。
虚拟设计网络平台是由各类设计及管理软件、产品数据库、产品主模型等组成的信息管理系统。
产品主模型技术是产品并行虚拟设计的关键技术,它将整个产品开发活动视为一个整体,所有活动都围绕一个统一的产品主模型分布式并行协调推进。
而产品设计开发过程则覆盖产品从客户调研到报废回收整个生命周期的各个阶段,包括客户研究、概念设计、详细设计、技术设计、工艺装配、生产制造、市场营销和回收利用等业务,以及贯穿开发过程的成本控制和质量监控等流程。
2.工业设计与并行产品设计相关要素的链接
并行工程强调的是“并行”,这就把串行过程中按时间先后运行的环节,转变为同时并列运行的业务要素。
由于系统优化的需要以及生产过程诸要素的业务联系,工业设计与各个要素之间必然发生业务对接和交互影响。
从产品开发层面看,在时间上工业设计对产品开发进行的总体规划,尽量体现产品生命周期各阶段业务工作的协同并行,重点是工业设计与各阶段业务工作的对接以及从中得到有用的信息,值得强调的是“并行”不能理解为绝对的同时进行。
从并行工程管理系统层面看,工业设计在融入产品并行开发团队、并行工程过程重组、信息化管理等并行要素的同时,关键是处理与要素之间的关系,比如工业设计团队与产品并行开发团队的协同关系、工业设计与结构设计的协调一致、工业设计信息与数字化产品建模和产品数据信息库管理的交互关系,以及工业设计流程的协同运行和管理等。
三、面向并行工程的工业设计流程构建
为了适应并行工程的技术要求,工业设计的内部流程必须做出调整,由串行业务流程转变为并行业务流程。
1.工业设计的串行流程
传统的工业设计是串行流程,产品串行开发流程局限于研发工作的部门流程,不是面向市场的全流程,信息共享存在障碍,设计早期不能全面考虑产品生命周期中的各种因素;产品的结构设计与工业设计联系不紧,设计反复次数较多,每一反复都可能浪费掉大量的材料和时间,设计效率低下,一次设计成功率较低,而且设计周期长。
但是,随着市场竞争的加剧,客户订单要求交货周期越来越短,工业设计及产品开发必须缩短时间,这样,与市场竞争有关的因素诸如客户需求、成本质量控制等都成了工业设计关注的对象,进入工业设计业务流程,使工业设计的内涵和功能不断扩展,形成内容更加广泛的新流程。
2.面向并行工程的工业设计流程模型
面向并行工程的工业设计流程模型由产品并行设计开发团队、虚拟设计网络平台、工业设计主流程和产品并行设计其它环节四个模块组成。
下面以郑州宇通客车并行设计为例来深入分
析该模型。
为了缩短产品研发周期,提高设计效率,郑州宇通实施产品设计并行开发,市场竞争能力不断加强,成为国内客车行业首屈一指的标杆企业。
产品并行设计开发团队分工配合,协同工作。
设计理论 Design Theory宇通创造性地提倡“体系创新”模式,建立了由产品策划、技术研发、工艺装配、管理层级等构建起来的庞大创新体系。
对新产品开发实行项目管理,在新产品开发的各个阶段明确团队、职能、节点等概念,形成市场导向的新产品开发流程。
团队跨产品开发处、市场部、国家级客车技术中心、试验中心(博士后科研工作站、整车试验室等)、产品认证部等部门,包括工业设计师、工程师、销售人员等。
强化项目小组的功能,各小组之间各司其职,相互协调,共同完成产品并行设计任务。
宇通以及集成化管理模式,为产品开发项目的运作提供了人力资源保障。
虚拟网络平台保障设计活动并行实施。
结语
企业管理现代化的高速发展,让优化和构建工业设计流程有着举足轻重的作用,,加强对工业设计融入先进管理技术系统的深入研究势在必行。
通过以上案例的分析,深入阐述了并行工业设计流程模型的运行过程及其实施效果,也发现工业设计与并行工程、产品集成化开发等先进管理技术的对接还不够协调,有待深入研究,进一步整合流程,创新方法,推动工业设计全面融入产品创新体系之中。
注释
[1] 王斌:“基于顾客满意度评测的工业设计流程优化模式研究”.(2007-11-07)[2010-03-16]. http://202.196.13.209/
cddbn/cddbn.Articles/D028422/PDF/index.htm.
[2] 曾庆良等:“基于并行工程的产品成本评估系统研究”,《清华大学学报(自然科学版)》,2003.3。