回参考点
数控机床回参考点的故障分析和排除
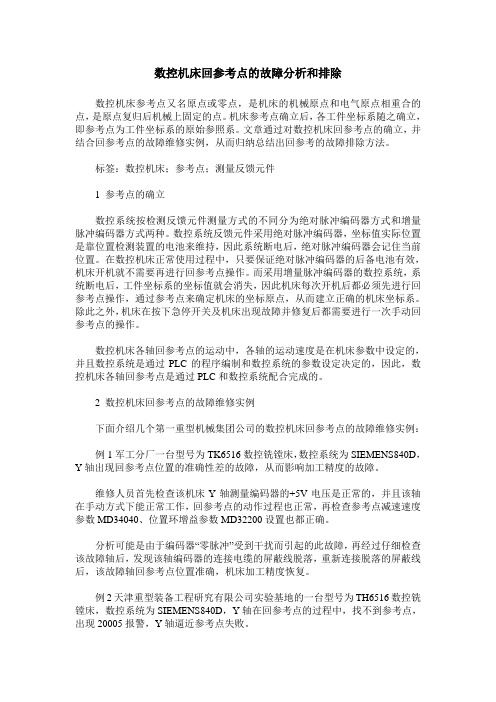
数控机床回参考点的故障分析和排除数控机床参考点又名原点或零点,是机床的机械原点和电气原点相重合的点,是原点复归后机械上固定的点。
机床参考点确立后,各工件坐标系随之确立,即参考点为工件坐标系的原始参照系。
文章通过对数控机床回参考点的确立,并结合回参考点的故障维修实例,从而归纳总结出回参考的故障排除方法。
标签:数控机床;参考点;测量反馈元件1 参考点的确立数控系统按检测反馈元件测量方式的不同分为绝对脉冲编码器方式和增量脉冲编码器方式两种。
数控系统反馈元件采用绝对脉冲编码器,坐标值实际位置是靠位置检测装置的电池来维持,因此系统断电后,绝对脉冲编码器会记住当前位置。
在数控机床正常使用过程中,只要保证绝对脉冲编码器的后备电池有效,机床开机就不需要再进行回参考点操作。
而采用增量脉冲编码器的数控系统,系统断电后,工件坐标系的坐标值就会消失,因此机床每次开机后都必须先进行回参考点操作,通过参考点来确定机床的坐标原点,从而建立正确的机床坐标系。
除此之外,机床在按下急停开关及机床出现故障并修复后都需要进行一次手动回参考点的操作。
数控机床各轴回参考点的运动中,各轴的运动速度是在机床参数中设定的,并且数控系统是通过PLC的程序编制和数控系统的参数设定决定的,因此,数控机床各轴回参考点是通过PLC和数控系统配合完成的。
2 数控机床回参考点的故障维修实例下面介绍几个第一重型机械集团公司的数控机床回参考点的故障维修实例:例1军工分厂一台型号为TK6516数控铣镗床,数控系统为SIEMENS840D,Y轴出现回参考点位置的准确性差的故障,从而影响加工精度的故障。
维修人员首先检查该机床Y轴测量编码器的+5V电压是正常的,并且该轴在手动方式下能正常工作,回参考点的动作过程也正常,再检查参考点减速速度参数MD34040、位置环增益参数MD32200设置也都正确。
分析可能是由于编码器“零脉冲”受到干扰而引起的此故障,再经过仔细检查该故障轴后,发现该轴编码器的连接电缆的屏蔽线脱落,重新连接脱落的屏蔽线后,该故障轴回参考点位置准确,机床加工精度恢复。
什么是无挡块回参考点?300号报警怎么消除?

什么是⽆挡块回参考点?300号报警怎么消除?FANUC系统关于参考点设置,所谓的⽆挡块(without dog)回参考点,是针对增量式回参考点中需采⽤减速挡块⽽⾔的。
⽽之所以不需要挡块(减速信号)确定参考点位置,是因为FANUC编码器可当作绝对式编码器使⽤。
所以,FANUC系统中,⽆挡块回参考点就是指绝对式回参考点(或称绝对式回零)。
⽆挡块回参考点的技术⽅法是:⾸先将轴在⼿动⽅式下移动⾄参考点位置,通过参数实现机械位置与参考点位置的同步,通过电池实现零点位置记忆。
此后开机即能读取零点位置,不需每次都作回零操作。
绝对式回零相关参数如果设备把FANUC编码器当绝对式使⽤,则可按表1设定相关参数。
其中对于APZ的操作决定了参考点设置的有效性。
表1 绝对式回零参数⼀览表序号参数号含义使⽤情境举例11005#1(DLZ)0:⽤减速挡块回参考点1:⽆挡块回参考点121815#5(APC)位置检测器为0: 增量式编码器1: 绝对式编码器131815#4(APZ)使⽤绝对式编码器时,机械位置与参考点位置之间的对应关系0: 尚未建⽴1: 已经建⽴进⾏第 1 次调节或更换绝对位置编码器时,务须将其设定为 “0”。
然后将设定轴⼿动移⾄参考点位置,再将APZ设为1DLZ:without dog zeroAPC:absolute pulse coderAPZ:absolute pulse zero绝对式回零设置步骤1. 确认电池连接和超程保护⽤于编码器位置记忆的电池安装在伺服放⼤器上。
超程保护开关必须有效。
2. 设定参数DLZ和APC将DLZ和APC设为1,此时屏幕出现000号报警。
关机重启,则屏幕出现300号报警,如图1所⽰。
图1 300号报警画⾯3. ⼿动⽅式下将设定轴移⾄参考点位置确定参考点所在机械位置(戳蓝字看参考点在哪个位置),位于机床坐标系极限处。
在JOG或⼿轮⽅式下,将设定轴移动⾄参考点位置,⼀般位于正向超程开关内侧。
机床操作步骤

机床操作步骤一、开机、关机、复位、回参考点1、开机、复位操作步骤按下操作台右上角的“急停”按钮,合上机床后面的空气开关,手柄的指示标志到“ON”的位置。
松开总电源开关,打开计算机电源,进入数控系统的界面,右旋松开“急停”按钮,系统复位,对应于目前的加工方式为“手动”,显示“手动”。
2、关机操作步骤首先按下“急停”按钮,然后按下总电源开关,最后关闭空气开关,手柄的指示标志到“OFF”的位置。
开、关机操作之前都要求先按下“急停”按钮,目的是减少电冲击。
3、手动回参考点操作步骤按下“回参考点”按键,键内指示灯亮之后,按“+X”键及“+Z”键,刀架移动回到机床参考点。
4、超程解除步骤当出现超程,显示“出错”,“超程解除”指示灯亮。
解除超程的步骤:应先按住“超程解除”键不放,再将工作方式置为“手动”或者“手摇”,哪个方向超程,假设目前是+X方向超程,则选择相反的方向按“-X”键移动刀架,直到“超程解除”指示灯灭,显示“运行正常”。
二、手动操作步骤1、点动操作按“手动”,先设定进给修调倍率,再按“+Z”或者“-Z”、“+X”、“-X”,坐标轴连续移动;在点动进给时,同时按压“快进”按键,则产生相应轴的正向或负向快速运动。
2、增量进给将坐标轴选择波段开关置于“OFF”档,按一下控制面板上的“增量”按键(指示灯亮),按一下“+Z”或者“-Z”、“+X”、“-X”,则沿选定的方向移动一个增量值。
请注意与“点动”的区别,此时按住“+Z”或者“-Z”、“+X”、“-X”不放开,也只能移动一个增量值,不能连续移动。
增量进给的增量值由“×1”、“×10”、“×100”、“×1000”四个增量倍率按键控制。
增量倍率按键和增量值的对应关系如表所示。
3、手摇进给以X轴为例,说明手摇进给操作方法。
将坐标轴选择开关置于“X”档,顺时针/逆时针旋转手摇脉冲发生器一格,可控制X轴向正向或负向移动一个增量值。
数控机床回参考点设置方法

摘要:发那科、三菱,西门子几种常用数控系统参考点的工作原理、调整和设定方法,并举例说明参考点的故障现象,解决方法。
关键词:参考点相对位置检测系统绝对位置检测系统1 概述当数控机床更换、拆卸电机或编码器后,机床会有报警信息:编码器内的机械绝对位置数据丢失了,或者机床回参考点后发现参考点和更换前发生了偏移,这就要求我们重新设定参考点,所以我们对了解参考点的工作原理十分必要。
参考点是指当执行手动参考点回归或加工程序的G28指令时机械所定位的那一点,又名原点或零点。
每台机床有一个参考点,根据需要也可以设置多个参考点,用于自动刀具交换(ATC)、自动拖盘交换(APC)等。
通过G28指令执行快速复归的点称为第一参考点(原点),通过G30指令复归的点称为第二、第三或第四参考点,也称为返回浮动参考点。
由编码器发出的栅点信号或零标志信号所确定的点称为电气原点。
机械原点是基本机械坐标系的基准点,机械零件一旦装配好,机械参考点也就建立了。
为了使电气原点和机械原点重合,将使用一个参数进行设置,这个重合的点就是机床原点。
机床配备的位置检测系统一般有相对位置检测系统和绝对位置检测系统。
相对位置检测系统由于在关机后位置数据丢失,所以在机床每次开机后都要求先回零点才可投入加工运行,一般使用挡块式零点回归。
绝对位置检测系统即使在电源切断时也能检测机械的移动量,所以机床每次开机后不需要进行原点回归。
由于在关机后位置数据不会丢失,并且绝对位置检测功能执行各种数据的核对,如检测器的回馈量相互核对、机械固有点上的绝对位置核对,因此具有很高的可信性。
当更换绝对位置检测器或绝对位置丢失时,应设定参考点,绝对位置检测系统一般使用无挡块式零点回归。
2 使用相对位置检测系统的参考点回归方式:(1)发那科系统:1)工作原理:当手动或自动回机床参考点时,首先,回归轴以正方向快速移动,当挡块碰上参考点接近开关时,开始减速运行。
当挡块离开参考点接近开关时,继续以FL速度移动。
第一章回参考点的必要性
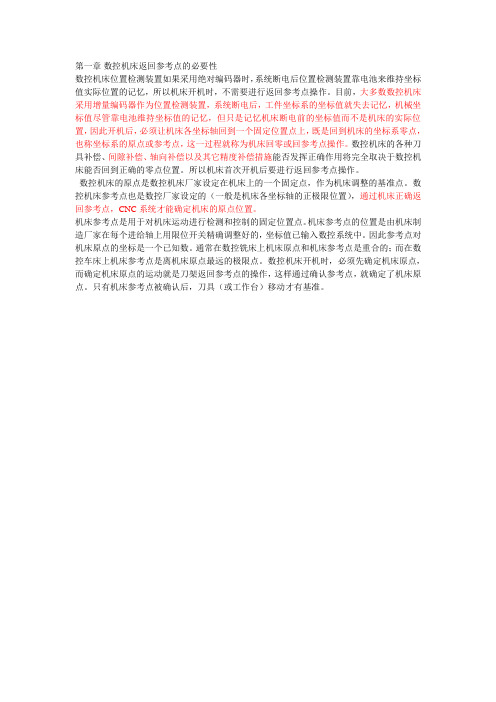
第一章数控机床返回参考点的必要性
数控机床位置检测装置如果采用绝对编码器时,系统断电后位置检测装置靠电池来维持坐标值实际位置的记忆,所以机床开机时,不需要进行返回参考点操作。
目前,大多数数控机床采用增量编码器作为位置检测装置,系统断电后,工件坐标系的坐标值就失去记忆,机械坐标值尽管靠电池维持坐标值的记忆,但只是记忆机床断电前的坐标值而不是机床的实际位置,因此开机后,必须让机床各坐标轴回到一个固定位置点上,既是回到机床的坐标系零点,也称坐标系的原点或参考点,这一过程就称为机床回零或回参考点操作。
数控机床的各种刀具补偿、间隙补偿、轴向补偿以及其它精度补偿措施能否发挥正确作用将完全取决于数控机床能否回到正确的零点位置。
所以机床首次开机后要进行返回参考点操作。
数控机床的原点是数控机床厂家设定在机床上的一个固定点,作为机床调整的基准点。
数控机床参考点也是数控厂家设定的(一般是机床各坐标轴的正极限位置),通过机床正确返回参考点,CNC系统才能确定机床的原点位置。
机床参考点是用于对机床运动进行检测和控制的固定位置点。
机床参考点的位置是由机床制造厂家在每个进给轴上用限位开关精确调整好的,坐标值已输入数控系统中。
因此参考点对机床原点的坐标是一个已知数。
通常在数控铣床上机床原点和机床参考点是重合的;而在数控车床上机床参考点是离机床原点最远的极限点。
数控机床开机时,必须先确定机床原点,而确定机床原点的运动就是刀架返回参考点的操作,这样通过确认参考点,就确定了机床原点。
只有机床参考点被确认后,刀具(或工作台)移动才有基准。
数控铣床机床回参考点

数控铣床机床回参考点
一、返回参考,点操作
控制机床运动的前提是建立机床坐标系,为此系统接通电源、复位后首先应进行机床各轴回参考点操作,方法如下:
(1)按机床控制面板回零键,系统显示当前工作方式是回零。
(2)依次按下“+Z,-X,-Y”按钮(根据X,Y,Z轴机床今数中的“回参考点方向”参数
来确定,如:X轴回参点方向为“一”,则按-X),待按钮内的指示灯亮后,机床返回参考点
结束,机床坐标系建立。
二、注意事项
(1)返回参考点时,为防止机床运行时发生碰掩,一般应选择Z轴先回参考点,即先将刀具抬起。
(2)在每次电源接通后,必须先完成各轴的返回参考点操作.然后再进人其他运行方
式.以确保各轴坐标的正确性,同时使用多个相容(十X与-X不相容,其余类同)的轴向选
择按键,每次能使多个坐标轴返回今考点。
(3)在回参考点前应确保回零轴位于今考点方向相反侧.如X轴的回参考点方向为
负,则回参考点前应保证X轴当前位里在参考点的正方向,否则应手动移动该轴直到满足此条件。
(4)在回参考点过程中若出现超程故障,按住控制面板上的超程解除按键.待系统运行
状态显示正常后,向相反方向手动移动该轴,使其退出超程状态,然后返回参考点。
(5)系统各轴回参考点后,在运行过程中只要伺服驭动装置不出现报普,其他报警出现都不需要重新回零,包括按下急停按键。
数控铣床专业研发,制造厂家,提供报价、维修等多方位服务,买各型号数控铣床更放心,网络直销中.
大天数控是数控铣床、加工中心、龙门铣床的专业生产厂家,拥有几十年研发、制造经验,与世界500强有成功合作。
为您提供完美的解决方案,免费电话:400-800-9706。
机床回参考点命令G27、G28、G29

机床参考点是可以任意设定的,设定的位置主要根据机床加工或换刀的需要。
设定的方法有两种:其一即根据刀杆上某一点或刀具刀尖等坐标位置存入参数中,来设定机床参考点:其二用调整机床上各相应的挡铁位置,也可以设定机床参考点。
一般参考点选作机床坐标的原点,在使用手动返回参考点功能时,刀具即可在机床X、Y、Z坐标参考点定位,这时返回参考点指示灯亮,表明刀具在机床的参考点位置。
返回参考点校验功能(G27)指令程序中的这项功能,用于检查机床是否能准确返回参考点。
格式:G27 X____ Y____ :当执行G27指令后,返回各轴参考点指示灯分别点亮。
当使用刀具补偿功能时,指示灯是不亮的,所以在取消刀具补偿功能后,才能使用G27指令。
当返回参考点校验功能程序段完成,需要使机械系统停止时,必须在下一个程序段后增加M00或M01等辅助功能或在单程序段情况下运行。
自动返回参考点(G28)指令利用这项指令,可以使受控轴自动返回参考点。
格式:G28 X____ Y____ :或G28 Z____ X____ ;或G28 Y____ Z____ ;其中X、Y、Z为中间点位置坐标,指令执行后,所有的受控轴都将快速定位到中间点,然后再从中间点到参考点。
G28指令一般用于自动换刀,所以使用G28指令时,应取消刀具的补偿功能。
从参考点自动返回(G29)指令从参考点自动返回指令G29的形式为:G29 X____ Y____;或G29 Z____ X____ ;或G29 Y____ Z____;这条指令一般紧跟在G28指令后使用,指令中的X、Y、Z坐标值是执行完G29后,刀具应到达的坐标点。
它的动作顺序是从参考点快速到达G28指令的中间点,再从中间点移动到G29指令的点定位,其动作与G00动作相同。
第二参考点返回(G30)指令G30 X____ Y____;或G30 Z____ X____ ;或G30 Y____ Z____;G30为第二参考点返回,该功能与G28指令相似。
回参考点
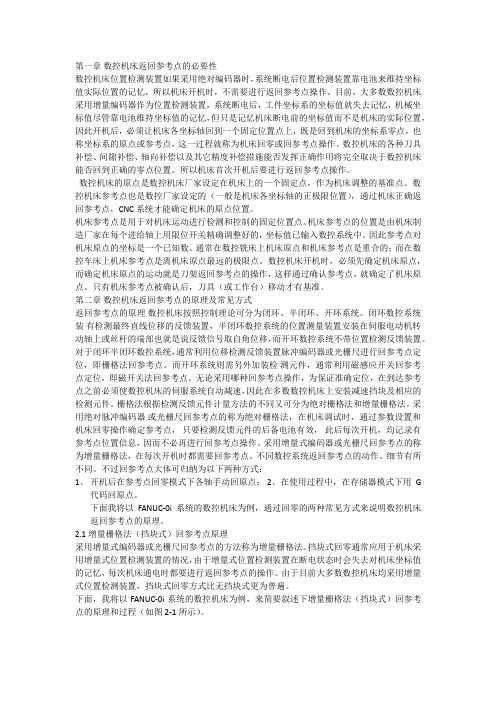
第一章数控机床返回参考点的必要性数控机床位置检测装置如果采用绝对编码器时,系统断电后位置检测装置靠电池来维持坐标值实际位置的记忆,所以机床开机时,不需要进行返回参考点操作。
目前,大多数数控机床采用增量编码器作为位置检测装置,系统断电后,工件坐标系的坐标值就失去记忆,机械坐标值尽管靠电池维持坐标值的记忆,但只是记忆机床断电前的坐标值而不是机床的实际位置,因此开机后,必须让机床各坐标轴回到一个固定位置点上,既是回到机床的坐标系零点,也称坐标系的原点或参考点,这一过程就称为机床回零或回参考点操作。
数控机床的各种刀具补偿、间隙补偿、轴向补偿以及其它精度补偿措施能否发挥正确作用将完全取决于数控机床能否回到正确的零点位置。
所以机床首次开机后要进行返回参考点操作。
数控机床的原点是数控机床厂家设定在机床上的一个固定点,作为机床调整的基准点。
数控机床参考点也是数控厂家设定的(一般是机床各坐标轴的正极限位置),通过机床正确返回参考点,CNC系统才能确定机床的原点位置。
机床参考点是用于对机床运动进行检测和控制的固定位置点。
机床参考点的位置是由机床制造厂家在每个进给轴上用限位开关精确调整好的,坐标值已输入数控系统中。
因此参考点对机床原点的坐标是一个已知数。
通常在数控铣床上机床原点和机床参考点是重合的;而在数控车床上机床参考点是离机床原点最远的极限点。
数控机床开机时,必须先确定机床原点,而确定机床原点的运动就是刀架返回参考点的操作,这样通过确认参考点,就确定了机床原点。
只有机床参考点被确认后,刀具(或工作台)移动才有基准。
第二章数控机床返回参考点的原理及常见方式返回参考点的原理数控机床按照控制理论可分为闭环、半闭环、开环系统。
闭环数控系统装有检测最终直线位移的反馈装置,半闭环数控系统的位置测量装置安装在伺服电动机转动轴上或丝杆的端部也就是说反馈信号取自角位移,而开环数控系统不带位置检测反馈装置。
对于闭环半闭环数控系统,通常利用位移检测反馈装置脉冲编码器或光栅尺进行回参考点定位,即栅格法回参考点。
- 1、下载文档前请自行甄别文档内容的完整性,平台不提供额外的编辑、内容补充、找答案等附加服务。
- 2、"仅部分预览"的文档,不可在线预览部分如存在完整性等问题,可反馈申请退款(可完整预览的文档不适用该条件!)。
- 3、如文档侵犯您的权益,请联系客服反馈,我们会尽快为您处理(人工客服工作时间:9:00-18:30)。
第一章数控机床返回参考点的必要性数控机床位置检测装置如果采用绝对编码器时,系统断电后位置检测装置靠电池来维持坐标值实际位置的记忆,所以机床开机时,不需要进行返回参考点操作。
目前,大多数数控机床采用增量编码器作为位置检测装置,系统断电后,工件坐标系的坐标值就失去记忆,机械坐标值尽管靠电池维持坐标值的记忆,但只是记忆机床断电前的坐标值而不是机床的实际位置,因此开机后,必须让机床各坐标轴回到一个固定位置点上,既是回到机床的坐标系零点,也称坐标系的原点或参考点,这一过程就称为机床回零或回参考点操作。
数控机床的各种刀具补偿、间隙补偿、轴向补偿以及其它精度补偿措施能否发挥正确作用将完全取决于数控机床能否回到正确的零点位置。
所以机床首次开机后要进行返回参考点操作。
数控机床的原点是数控机床厂家设定在机床上的一个固定点,作为机床调整的基准点。
数控机床参考点也是数控厂家设定的(一般是机床各坐标轴的正极限位置),通过机床正确返回参考点,CNC系统才能确定机床的原点位置。
机床参考点是用于对机床运动进行检测和控制的固定位置点。
机床参考点的位置是由机床制造厂家在每个进给轴上用限位开关精确调整好的,坐标值已输入数控系统中。
因此参考点对机床原点的坐标是一个已知数。
通常在数控铣床上机床原点和机床参考点是重合的;而在数控车床上机床参考点是离机床原点最远的极限点。
数控机床开机时,必须先确定机床原点,而确定机床原点的运动就是刀架返回参考点的操作,这样通过确认参考点,就确定了机床原点。
只有机床参考点被确认后,刀具(或工作台)移动才有基准。
第二章数控机床返回参考点的原理及常见方式返回参考点的原理数控机床按照控制理论可分为闭环、半闭环、开环系统。
闭环数控系统装有检测最终直线位移的反馈装置,半闭环数控系统的位置测量装置安装在伺服电动机转动轴上或丝杆的端部也就是说反馈信号取自角位移,而开环数控系统不带位置检测反馈装置。
对于闭环半闭环数控系统,通常利用位移检测反馈装置脉冲编码器或光栅尺进行回参考点定位,即栅格法回参考点。
而开环系统则需另外加装检测元件,通常利用磁感应开关回参考点定位,即磁开关法回参考点。
无论采用哪种回参考点操作,为保证准确定位,在到达参考点之前必须使数控机床的伺服系统自动减速,因此在多数数控机床上安装减速挡块及相应的检测元件。
栅格法根据检测反馈元件计量方法的不同又可分为绝对栅格法和增量栅格法。
采用绝对脉冲编码器或光栅尺回参考点的称为绝对栅格法,在机床调试时,通过参数设置和机床回零操作确定参考点,只要检测反馈元件的后备电池有效,此后每次开机,均记录有参考点位置信息,因而不必再进行回参考点操作。
采用增量式编码器或光栅尺回参考点的称为增量栅格法,在每次开机时都需要回参考点。
不同数控系统返回参考点的动作、细节有所不同。
不过回参考点大体可归纳为以下两种方式:1、开机后在参考点回零模式下各轴手动回原点;2、在使用过程中,在存储器模式下用G代码回原点。
下面我将以FANUC-0i系统的数控机床为例,通过回零的两种常见方式来说明数控机床返回参考点的原理。
2.1 增量栅格法(挡块式)回参考点原理采用增量式编码器或光栅尺回参考点的方法称为增量栅格法。
挡块式回零通常应用于机床采用增量式位置检测装置的情况,由于增量式位置检测装置在断电状态时会失去对机床坐标值的记忆,每次机床通电时都要进行返回参考点的操作。
由于目前大多数数控机床均采用增量式位置检测装置,挡块式回零方式比无挡块式更为普遍。
下面,我将以FANUC-0i系统的数控机床为例,来简要叙述下增量栅格法(挡块式)回参考点的原理和过程(如图2-1所示)。
9快速进给速度参数、慢速进给速度参数、加减速时间常数、栅格偏移量等参数分别由数控系统的相应参数设定。
机床返回参考点的操作步骤为:A.将方式开关拨到“回零工作方式”档,选择返回参考点的轴,按下该轴正向点动按钮(+J),该轴以快速移动速度(V1)移向参考点;(图2-1中①→②的过程)B.当与工作台一起运动的减速挡块压下减速开关触点时(图2-1中②→③的过程,减速信号(*DEC)由通(1) 转为断(0) 状态,工作台进给会减速,按参数设定的慢速进给速度(V2)继续移动(减速可削弱运动部件的移动惯量,使零点停留位置准确);C.栅格法是采用脉冲编码器上每转出现一次的栅格信号(又称一转信号PCZ) 来确定参考点,当减速挡块释放减速开关(图2-1中③→④的过程),减速信号由断(0)转为通(1)后,数控系统将等待编码器上的第一个栅格信号的出现。
该信号一出现,工作台运动就立即停止,以此位置作为机床零点,同时数控系统发出参考点返回完成信号,参考点灯亮,表明机床该轴回参考点成功。
一转信号是编码器产生的信号,编码器除产生反馈位移和速度的脉冲信号外,还每转产生一个基准信号即一转信号。
需要注意的是,栅格信号(GRID)并不是编码器直接发出的信号,而是数控系统在一转信号和软件共同作用下产生的信号。
FANUC公司使用栅格信号的目的,就是可以通过调整栅格偏移量(FANUC 0i中由1850号系统参数设定),在一定范围内灵活调整机床零点位置。
机床使用中,只要不改变脉冲编码器与丝杠间的相对位置或不移动参考点撞块调定的位置,栅格信号就会以很高的重复精度出现。
2.2 绝对栅格法(无挡块式)回参考点原理无挡块式回零不需要挡块和减速开关,位置检测装置通常采用绝对位置编码器或距离编码光栅尺,无须每次开机都回零操作(使用绝对位置编码器时)或者回零距离短,方便快捷(使用距离编码光栅尺时),因此目前采用无挡块回零方式的数控机床越来越普遍。
采用无挡块式回零的机床,如果位置检测装置为绝对编码器,则通常在绝对编码器电池电压不足、伺服电机或伺服放大器拆下修复、系统参数初始化操作等情况下,零点位置会丢失,需要重新设定和调整;如果位置检测装置为距离编码的光栅尺,机床零点的位置也需要根据实际情况进行调整,以便更好满足加工需要。
下面以FANUC 0i系统为例,结合机床采用绝对编码器和采用距离编码的光栅尺这两种典型情况说明无挡块式回零的调整原理和过程。
一、采用绝对编码器时无挡块式回零的设定和调整当机床采用绝对编码器时,在后备存储器电池支持下,只需在机床第一次开机调试时进行回零点操作调整,此后每次开机均记录有零点位置信息,因而不必再进行回零操作。
但是更换伺服电机或伺服放大器后,由于反馈线与电机航空插头脱开或电机反馈线与伺服放大器脱开,必将导致编码器电路与电池脱开,储存在S-RAM中的位置信息即刻丢失。
再开机后机床会出现300#报警,需要重新建立零点。
回零相关参数设定及建立过程如下所示。
1.回零方式和编码器类型参数设定机床是挡块式回零还是无挡块式回零由系统参数1002.1(DLZ)、1005.1(DLZX)设定。
1002.1(DLZ)设定所有轴,1005.1(DLZX)设定各轴。
如果机床所有进给轴回零都为无挡块式,则将1002.1设定为 1即可。
如果机床并不是所有轴回零都为无挡块式,则应将1002.1设定为0,同时在1005.1(DLZX)中将无挡块回零的轴设为1,将挡块式回零的轴设为0。
如果机床所有轴回零都为挡块方式,则将1002.1(DLZ)、1005.1(DLZX)全部设为0即可。
2.绝对位置编码器建立零点过程绝对位置编码器建立零点过程如图2-2.1所示。
1、首先将系统参数1815#5(APCX)设为1(绝对位置编码器),然后再将系统参数1815#4(APZX)置为0。
当1815#4(APZX)为0时,表示机床零点需要重新建立;而当1815#4(APZX)为1,表示机床零点已经建立。
完成此操作后,系统断电重启。
2、将方式开关打到手动(JOG)方式状态下,手动使轴移动电动机转1转以上的距离,移动速度不得低于300mm/min。
只有这样,才能在脉冲编码器内检测到一个以上的一转信号。
3、在手动方式下将轴移动到靠近机床零点(约数毫米)的位置。
4、然后选择回零(ZRN)方式。
当ZRN信号由0变成1时,系统开始寻找栅格信号。
5、按进给轴方向选择信号“+”或“-”按钮后,机床移动到下一个栅格位置后停止,该点即为机床零点。
机床零点建立后1815#4(APZX)自动置为1。
若机床零点位置并不要求与原来位置一致,则可通过设置系统参数1815#4(APZX)和1815#5(APCX)在行程内任意位置设置新的机床零点。
具体操作如下:1、首先将系统参数1815#4(APZX)和1815#5(APCX)均设置为0,即系统零点需要设置,且编码器为增量式。
2、系统断电重启后,手动移动各轴到新的机床零点位置。
3、然后再将系统参数1815.4(APZX)、1815.5(APCX)均设定为1。
4、系统再次断电重启后设置成功。
二、采用距离编码式光栅尺的零点设定和调整传统的光栅尺有A相、B相以及标志信号,A相、B相作为基本脉冲根据光栅尺分辨精度产生步距脉冲,而标志信号是相隔一固定距离产生一个脉冲,所谓固定距离是根据光栅尺规格或订货要求而确定的,如10mm、15 mm、20 mm、25 mm、30 mm、50 mm等。
标志信号的作用相当于编码器的一转信号,用于返回零点的基准信号。
距离编码的光栅尺,其标志距离不像传统光栅尺是固定的,它是按照一定比例系数变化的,如图2-2.2所示。
当机床沿着某个轴返回零点时,数控系统读到几个不等距离的标志信号后,会自动计算出当前的位置,不必像传统的光栅尺那样每次断电后都要返回到固定机床零点(参考点),它仅需在机床的任意位置移动一个相对小的距离就能够找到零点。
距离编码光栅尺的零点设定和调整步骤如下1.将系统参数1815.1(OPTX)、1815.2(DCLX)均设为1,即告诉数控系统当前轴使用了距离编码的直线光栅尺。
2.设置系统参数1802.1(DC4)。
当1802.1(DC4)=0,系统检测3个标志后确定零点位置;当1802.1(DC4)=1,系统检测4个标志后确定零点位置。
3.设置系统参数1821、1882。
参数1821设置各轴参考计数器容量,对于使用距离编码光栅尺的轴,该参数则设定标志1的间隔。
参数1882设置标志2的间隔。
数据设置需要根据光栅尺规格确定,单位均为检测单位(通常为微米)。
例如一机床某轴采用距离编码的海德汉LB302C光栅尺,该尺相邻两个标志1的距离为80mm,相邻两个标志2的距离为80.04mm。
则将参数1821值设定为80000,参数1882值设定为80040。
4.设置系统参数1883,即设置光栅尺起始点与机床零点(参考点)的距离。
如图2所示,光栅尺起始点是指标志1和标志2的重合点,通常此点仅是一个假象点,在光栅尺上并不存在。
光栅尺起始点与机床零点的距离可按以下步骤得出。