关于发酵罐的控制系统
发酵罐的操作及控制

发酵罐的操作及控制一、实验目的1、学习发酵过程中发酵控制、取样、流加等一般操作过程。
2、了解和学习自动发酵罐的操作过程和注意事项。
二、实验原理(一)发酵控制1、发酵温度的控制一般来说,接种后应适当提高培养温度,以利于孢子的萌发或加快微生物的生长、繁殖,而且此时发酵的温度大多数是上升的。
随着发酵液的温度逐渐上升,发酵液的温度应该控制在微生物的最适生长温度;到主发酵旺盛阶段温度的控制可比最适生长温度低些,即控制在微生物代谢产物合成的最适温度;到发酵的后期,温度出现下降的趋势,直至发酵成熟即可放罐。
工业发酵过程一般无须加热,因为释放的发酵热常常超过微生物的最适生长温度,所以需要冷却阶段较多。
通常是利用发酵罐的热交换装置进行降温(如采用夹套或蛇形管进行调温),冬季发酵时空气还需进行加热处理,以便维持发酵的正常温度。
2、发酵pH值控制首先应根据不同微生物的特性,不仅要控制原始培养基的pH值,而且在整个发酵过程中,必须随时检测pH值的变化情况,根据发酵过程中的pH值变化规律,选用适当的方法对pH值进行调节和控制。
3、提高溶解氧的措施控制溶解氧的工艺手段主要是从供氧和需氧两方面来考虑。
影响溶解氧效果的主要因素有:(1)通气流量(通风量);(2)搅拌速度;(3)气体组分中的氧分压;(4)罐压;(5)温度;(6)培养基的物理性质等。
而影响需氧的则是菌体的生理特性,诸如不同菌龄的呼吸强度差别,基质加入时菌丝耗氧的增加等。
4、二氧化碳浓度控制CO2在发酵液中的浓度变化受到许多因素的影响,如细胞的呼吸强度、发酵液的流变学特性、通气搅拌程度;罐压大小、设备规模等。
对CO2浓度的控制主要看其对发酵的影响,如果对发酵有促进作用,应该提高其浓度;反之应设法降低其浓度。
5、泡沫的控制泡沫产生的原因:通气和搅拌、培养基成分、培养基的灭菌方法、培养液的温度、酸碱度、浓度等对发酵过程的泡沫形成也有一定的影响泡沫的消除和防止:了解发酵过程中泡沫的消长规律,方可有效的控制泡沫。
发酵罐温度控制系统讲解

题目:发酵罐温度控制系统设计课程设计(论文)任务及评语院(系):教研室:Array注:成绩:平时40% 论文质量40% 答辩20% 以百分制计算摘要本题要设计的是温度控制系统,发酵是放热反应的过程。
随着反应的进行,罐内的温度会逐渐升高。
而温度对发酵过程具有多方面的影响。
因此,对发酵过程中的温度进行检测和控制就显得十分重要。
本课题设计了发酵罐温度控制系统,选择的传感器为Cu100,由于信号很小,所以就需要通过差动放大电路进行放大并且经过了滤波电路滤波,然后将处理后的电压信号经过V/I转换,输出4~20mA的电流信号,最后进行仿真分析以及参数的计算,以达到通过对冷水阀开度的控制对发酵罐温度控制的目的。
本系统应用温度控制系统,有助于提高发酵效率,有助于提高工厂产值,并且可以使资源得到更充分的作用。
关键词:温度控制;PID控制器;V/I转换;比较机构目录第1章绪论 (1)第2章课程设计的方案 (2)2.1 概述 (2)2.2 系统组成总体结构 (2)2.3 传感器选择 (2)第3章电路设计 (4)3.1 传感器电路 (4)3.2 比较机构电路 (7)3.3 PID调节器并联实现电路 (7)3.4 V/I转换电路 (8)3.5 直流稳压电源电路 (9)第4章仿真与分析 (10)4.1 传感器电路仿真 (10)4.2 PID控制器电路 (11)4.3 V/I转换电路 (12)第5章课程设计总结 (14)参考文献 (15)附录Ⅰ (16)附录Ⅱ (18)附录Ⅲ (20)第1章绪论在工业生产中,电流、电压、温度、压力、流量、流速和开关量都是常用的主要被控参数。
其中,温度控制也越来越重要。
在工业生产的很多领域中,人们都需要对各类加热炉、热处理炉、反应炉、发酵罐和锅炉中的温度进行检测和控制。
本次课设要求设计发酵罐的温度控制系统。
发酵是放热反应的过程。
随着反应的进行,罐内的温度会逐渐升高。
而温度对发酵过程具有多方面的影响:它会影响各种酶反应的速率,改变菌体代谢产物的合成方向,影响微生物的代谢调控机制,除这些直接影响外;温度还对发酵液的理化性质产生影响,如发酵液的粘度;基质和氧在发酵液中的溶解度和传递速率。
基于PLC的啤酒发酵自动控制系统设计

基于PLC的啤酒发酵自动控制系统设计
随着科技的不断发展,自动化控制系统在工业生产中扮演着越来越重要的角色。
本文将基于PLC(Programmable Logic Controller,可编程逻辑控制器)设计一个应用于啤酒发酵过程中的自动控制系统。
啤酒发酵是一个复杂的过程,需要严格控制温度、压力和气体浓度等参数。
传统的手动控制方式存在操作繁琐、易出错等不足之处,而自动控制系统则可以实现对发酵过程的精确控制,提高产品质量和生产效率。
本系统的硬件主要由传感器、PLC控制器和执行器组成。
使用温度传感器监测发酵罐内的温度,并将采集到的信号传输给PLC控制器。
PLC控制器根据设定的温度范围进行判断,若温度过高则控制执行器启动制冷设备,若温度过低则控制执行器启动加热设备,以此实现对温度的调控。
除了对发酵过程中关键参数进行监测和调控外,自动控制系统还应具备报警和记录功能。
当温度、氧气浓度或压力超过设定的安全范围时,系统应能够及时报警,并记录相关信息以供后期分析和改进。
基于PLC的啤酒发酵自动控制系统可以实现对温度、氧气浓度和压力等参数的精确控制,提高产品质量和生产效率。
该系统还能够报警和记录异常情况,为工程师提供便捷的故障排查和改进方向。
串级控制系统 发酵罐

•
在控制方面,该系统采用PID控制方式进 在控制方面,该系统采用PID控制方式进 行控制,具有控制稳定、控制精度高等特 点。同时系统还采用了串级控制(溶解氧 与转速、通气流量相关联)、比值控制、 计划曲线控制(温度、通气流量、pH值) 计划曲线控制(温度、通气流量、pH值) 等先进的控制技术。转速采用无级调速、 平稳可靠。
串级控制系统(发酵罐)
生物发酵DCS控制系统 生物发酵DCS控制系统
• 系统实现了发酵罐的空灭、实灭、冷却(一级、二
级)和发酵过程的温度、罐压、搅拌转速,通气流 量、pH、溶解氧、消泡、补料等自动控制。根据实 量、pH、溶解氧、消泡、补料等自动控制。根据实 际需要,还可随时切换到手动方式进行手动操作。 一台工控机可同时对多套发酵罐进行实时监测与控 制,可对各种数据进行存储、查询、打印报表、历 史曲线分析,批数据处理(按批号记录、比较,最 多16条用户可自由选择),超限报 警、历史报警查询,对各种操作事件、登陆事件进 行记录,通过权限登陆进行相应的操作等。此外, 还可以在Excel下查询历史数据。数据处理能力强, 还可以在Excel下查询历史数据。数据处理能力强, 用户操作方便。
发酵罐的基本结构及功能

发酵罐的基本结构及功能
发酵罐是一种用于进行微生物发酵的设备,它由罐体、进出料口、排气装置、搅拌器、温度控制系统和pH控制系统等部件组成。
罐体通常由不锈钢制成,具有优异的耐腐蚀性和耐高温性能。
进出料口用于加入和取出材料,排气装置能够排出二氧化碳等发酵产生的气体,以保证发酵过程中的氧气不会被过多地消耗。
搅拌器则可以让混合材料均匀加热和混合,使微生物得到更好的生长条件。
温度控制系统和pH控制系统是非常重要的组成部分,它们可以确保发酵罐内环境的稳定性和适宜生长条件。
温度控制系统可以通过加热或冷却来控制发酵罐内部的温度,使微生物在适宜的温度范围内进行发酵。
pH控制系统可以调节发酵罐内的酸碱度,确保微生物能够在适宜的pH值下进行发酵。
发酵罐的主要功能是促进微生物的生长和发酵,生产出需要的发酵产物。
在实际应用中,它被广泛应用于食品、药品、生物质能等领域。
例如,发酵罐可以用来生产酸奶、酵母、酒精、酢酸、抗生素等产品。
在使用发酵罐时,还需要注意保持罐体内的清洁卫生,以免杂菌或病菌的污染影响生产效果。
此外,及时检查和更换罐体内的配件和维护系统,也是确保发酵罐正常运转和延长寿命的关键措施。
综上所述,发酵罐是进行微生物发酵的重要设备,它的基本结构和功能对于生产出优质发酵产品至关重要。
同时,在使用发酵罐的过程中,需要合理运用控制系统和注意卫生维护问题,以保证生产过程的顺利进行和更好地保护人的健康和安全。
发酵罐工作原理
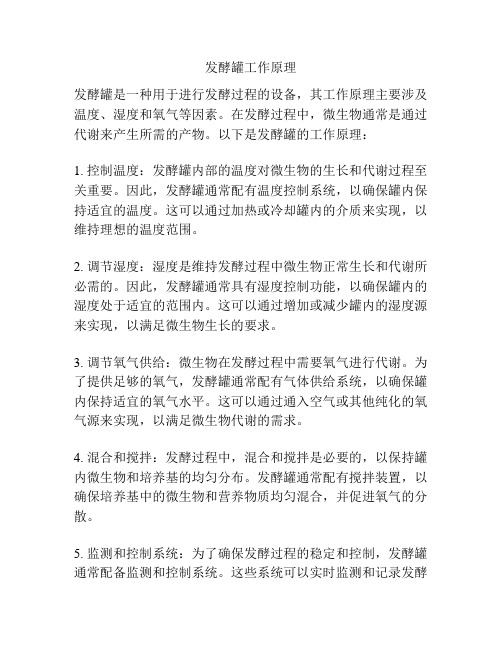
发酵罐工作原理
发酵罐是一种用于进行发酵过程的设备,其工作原理主要涉及温度、湿度和氧气等因素。
在发酵过程中,微生物通常是通过代谢来产生所需的产物。
以下是发酵罐的工作原理:
1. 控制温度:发酵罐内部的温度对微生物的生长和代谢过程至关重要。
因此,发酵罐通常配有温度控制系统,以确保罐内保持适宜的温度。
这可以通过加热或冷却罐内的介质来实现,以维持理想的温度范围。
2. 调节湿度:湿度是维持发酵过程中微生物正常生长和代谢所必需的。
因此,发酵罐通常具有湿度控制功能,以确保罐内的湿度处于适宜的范围内。
这可以通过增加或减少罐内的湿度源来实现,以满足微生物生长的要求。
3. 调节氧气供给:微生物在发酵过程中需要氧气进行代谢。
为了提供足够的氧气,发酵罐通常配有气体供给系统,以确保罐内保持适宜的氧气水平。
这可以通过通入空气或其他纯化的氧气源来实现,以满足微生物代谢的需求。
4. 混合和搅拌:发酵过程中,混合和搅拌是必要的,以保持罐内微生物和培养基的均匀分布。
发酵罐通常配有搅拌装置,以确保培养基中的微生物和营养物质均匀混合,并促进氧气的分散。
5. 监测和控制系统:为了确保发酵过程的稳定和控制,发酵罐通常配备监测和控制系统。
这些系统可以实时监测和记录发酵
过程中的温度、湿度、氧气和pH值等关键参数,并自动调节系统操作,以维持最佳条件。
总之,发酵罐通过控制温度、湿度和氧气等因素,为微生物的生长和代谢提供了合适的环境,并通过混合和搅拌来促进物料的均匀分布,以实现发酵过程的有效进行。
发酵罐的结构系统及使用

发酵罐的结构系统及使用发酵罐是用于微生物发酵生产的设备,广泛应用于食品、饲料、制药、化工等领域。
发酵罐的结构系统主要包括罐体结构、装置结构、传动系统和控制系统。
一、罐体结构发酵罐的罐体一般采用不锈钢材料制成,其外形一般为圆筒形或立方体。
不锈钢具有良好的耐腐蚀性能,能够耐受发酵过程中产生的酸碱性物质和高温高压等条件。
罐体内部通常是光滑的,以便于清洁和消毒。
为了方便观察和操作,罐体还会设置有透明或打开的观察口和进出料口。
二、装置结构发酵罐的装置结构主要包括搅拌装置、通气装置和温控装置等。
1.搅拌装置:搅拌装置可以通过改变液体中微生物、氧气和营养物质的接触程度,提高发酵效率。
搅拌装置通常由电动机、减速器和搅拌器组成,搅拌器的形式有桨叶式、锚式、螺旋式等。
选用合适的搅拌装置,可以保证物料的均匀性和发酵过程的稳定性。
2.通气装置:通气装置可以提供微生物生长所需的氧气,并帮助排出产生的二氧化碳等气体。
通气装置一般由气体过滤器、气体压力调节器和气体分配器等组成,可以实现对罐内气体浓度和压力的控制。
3.温控装置:温控装置可以控制发酵罐内的温度,确保环境适宜微生物的生长。
温控装置一般由加热装置、冷却装置和温度传感器组成。
通过控制加热和冷却设备的工作,可以保持发酵罐内温度的稳定和均匀。
三、传动系统发酵罐的传动系统主要用于驱动搅拌装置和通气装置的运转。
传动系统一般由电动机、传动装置和传动轴等组成。
根据发酵罐的规模和需求,可以选用不同功率和转速的电动机,并通过传动装置将电动机的转动传递给搅拌装置和通气装置。
四、控制系统发酵罐的控制系统用于实时监测和控制发酵过程中的各个参数。
主要包括温度控制器、压力控制器、液位控制器、pH控制器等。
通过这些控制器,可以对发酵罐的温度、压力、液位和pH值进行实时监测,并通过传感器的信号来调控加热、冷却、通气等设备的工作,以实现发酵过程的自动化控制。
发酵罐的使用过程中,需要严格控制和监测发酵过程中的各个参数。
啤酒发酵自动控制系统设计
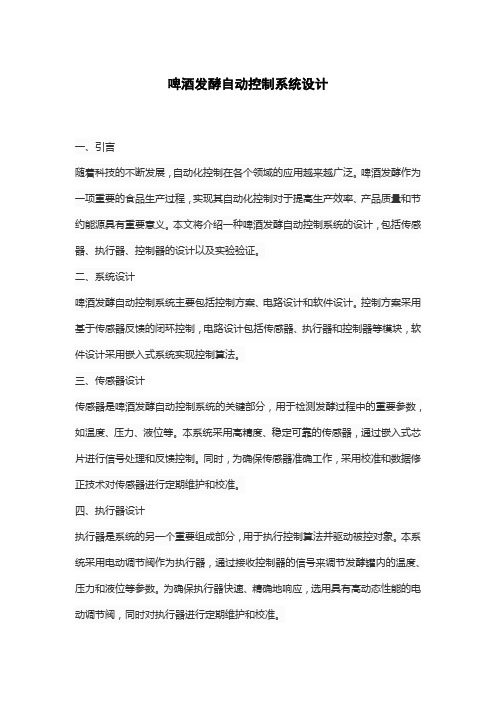
啤酒发酵自动控制系统设计一、引言随着科技的不断发展,自动化控制在各个领域的应用越来越广泛。
啤酒发酵作为一项重要的食品生产过程,实现其自动化控制对于提高生产效率、产品质量和节约能源具有重要意义。
本文将介绍一种啤酒发酵自动控制系统的设计,包括传感器、执行器、控制器的设计以及实验验证。
二、系统设计啤酒发酵自动控制系统主要包括控制方案、电路设计和软件设计。
控制方案采用基于传感器反馈的闭环控制,电路设计包括传感器、执行器和控制器等模块,软件设计采用嵌入式系统实现控制算法。
三、传感器设计传感器是啤酒发酵自动控制系统的关键部分,用于检测发酵过程中的重要参数,如温度、压力、液位等。
本系统采用高精度、稳定可靠的传感器,通过嵌入式芯片进行信号处理和反馈控制。
同时,为确保传感器准确工作,采用校准和数据修正技术对传感器进行定期维护和校准。
四、执行器设计执行器是系统的另一个重要组成部分,用于执行控制算法并驱动被控对象。
本系统采用电动调节阀作为执行器,通过接收控制器的信号来调节发酵罐内的温度、压力和液位等参数。
为确保执行器快速、精确地响应,选用具有高动态性能的电动调节阀,同时对执行器进行定期维护和校准。
五、控制器设计控制器是整个系统的核心部分,负责接收传感器的反馈信号,根据预设的控制算法对执行器进行控制,以实现啤酒发酵过程的自动化。
本系统采用嵌入式控制器,具有高可靠性、快速响应和鲁棒性等特点。
控制器通过算法优化,实现精确控制和自适应调节,以满足不同工况下的控制要求。
六、实验验证为验证啤酒发酵自动控制系统的有效性和可靠性,进行了一系列实验。
实验设置包括发酵罐、传感器、执行器和控制器等关键部件。
数据采集和处理采用专业的测试仪器进行实时监测与记录。
实验结果表明,该自动控制系统能够有效地控制啤酒发酵过程,确保产品质量和生产效率的提升。
同时,实验结果还显示,系统的稳定性和可靠性得到了充分验证,为实际生产提供了可靠保障。
七、结论本文介绍的啤酒发酵自动控制系统设计在实现生产过程的自动化和智能化方面具有显著优势。
- 1、下载文档前请自行甄别文档内容的完整性,平台不提供额外的编辑、内容补充、找答案等附加服务。
- 2、"仅部分预览"的文档,不可在线预览部分如存在完整性等问题,可反馈申请退款(可完整预览的文档不适用该条件!)。
- 3、如文档侵犯您的权益,请联系客服反馈,我们会尽快为您处理(人工客服工作时间:9:00-18:30)。
关于发酵罐的控制系统
一参数控制
1温度控制
a 信号输入为4-20mA电流,对应输出为0-150℃温度
b 输出温度需通过校对调整,可编在程序内,也可以做个人机界面,使用人调整(a+bx)
c 工作温度设定,通过人机界面由使用人输入
d 控制温度设定,分上限和下限,可采用工作温度加偏差温度(如0.5℃、1℃等)由使用人设定,也可以采用直接的温度值由使用人设定,也可以以0.5℃的偏差直接写入程序
e 控制方式:低于下限温度自动启动加热,高于上限温度自动启动冷却;加热和冷却过程需分别由使用人通过人机界面设定参数,参数为:加热时间(热水阀开启的时间,范围0-5分钟)和加热间隔时间(可设置为两次加热的间隔时间,也可以设置为热水阀关闭的时间,可以0-10分钟,由于加热过程中,热水进入发酵罐夹套后,发酵罐的温度上升要滞后一段时间,所以,关闭热水阀后要等一段时间,避免频繁启动而温度波动过大;同理,冷却过程也需要设置“冷却时间”和“冷却间隔时间”
2 酸碱度(pH)控制
a 信号输入为4-20mA电流,对应输出为0-14的pH值
b 输出pH需通过校对调整,需通过人机界面,使用人调整(a+bx)
c pH值设定,通过人机界面由使用人输入
d 控制pH值设定,分上限和下限,可采用工作pH值加偏差pH值(如0.1、0.2等)由使用人设定,也可以采用直接的pH值由使用人设定,
e 控制方式:低于下限pH值自动启动加碱,高于上限温度自动启动加酸;加碱和加酸过程需分别由使用人通过人机界面设定参数,参数为:加碱时间(加碱蠕动泵开启的时间,范围0-5分钟)和加碱间隔时间(可设置为两次加碱的间隔时间,也可以设置为加碱蠕动泵关闭的时间,可以0-10分钟,由于加碱过程中,氨水进入发酵罐后,发酵罐的pH值上升要滞后一段时间,所以,关闭加碱蠕动泵后要等一段时间,避免频繁启动而pH值波动过大;同理,加酸过程也需要设置“加酸时间”和“加酸间隔时间”
3 溶氧值(Do)控制
a 信号输入为4-20mA电流,对应输出为0-100的Do值
b 输出Do需通过校对调整,需通过人机界面,使用人调整(a+bx)
c Do值设定,通过人机界面由使用人输入
d 控制Do值设定,分上限和下限,可以采用直接的Do值由使用人设定,
e 搅拌电机的转速可设定为手动和自动,手动时由使用人通过人机界面直接输入,自动时则需要设定一个初始值和最低值,然后与溶氧(Do)相关联
f 控制方式:低于下限Do值自动启动搅拌电机加速,高于上限Do值自动启动搅拌电机减速;加速和减速过程需分别由使用人通过人机界面设定参数,参数
为:加速的速度值(范围可50转/分钟)和加速间隔时间(可设置为0-5分钟,由于加速过后,溶氧的提高要滞后一段时间,所以,关闭加速后要等一段时间,如Do值符合要求则维持在调整后的转速工作,如Do值仍偏低,则继续提高一档转速,直至达到最高转速,避免频繁启动而Do值波动过大);同理,减速过程也需要设置“减速的速度值”(也可以50转/分钟一档)和“减速间隔时间”,转速减到最低值就不再减速
4 消泡控制
a 信号为开关量
b 控制参数为自动状态下的消泡剂添加量(以毫升显示,实际对应为1毫升/秒种)和间隔时间(0-5分钟)
c 控制方式为手动/自动切换,手动时钮子开关人工确定添加量,自动时控制蠕动泵的添加时间(添加量)和间隔时间,考虑消泡剂作用的滞后时间
5 补料控制
补料控制全部为人工设定,设定参数两个:补料的时间(按绝对时间,即×月×日×时×分)和补料量(以毫升显示,按1毫升/秒种控制),每次可设定3个时间点(即每次进入补料的人机界面可预设定3次补料)
二报警
报警可以直接写入报警值,每个参数设一个报警上限值和一个报警下限值
三记录
采用表格和曲线两种方式,查询和输出的时间段由使用人选择,表格的输出还需要使用人确定时间间隔,默认时间间隔为10分钟,消泡和补料控制不需要曲线输出。