表面组装技术SMT
SMT简介

SMT是什么意思?SMT就是表面组装技术(Surface Mounted Technology的缩写),是目前电子组装行业里最流行的一种技术和工艺SMT有何特点:1、组装密度高、电子产品体积小、重量轻,贴片元件的体积和重量只有传统插装元件的1/10左右,一般采用SMT之后,电子产品体积缩小40%~60%,重量减轻60%~80%。
2、可靠性高、抗振能力强。
焊点缺陷率低。
3、高频特性好。
减少了电磁和射频干扰。
4、易于实现自动化,提高生产效率。
降低成本达30%~50%。
节省材料、能源、设备、人力、时间等。
SMT整套设备包括:印刷机:DEK,MPM,松下贴片机:松下,西门子,fuji,yamaha,三星,juki,环球,索尼回流焊炉:ERSA,ETA,BTU,埃塔SPI:VI,欧姆龙AOI:欧姆龙,德律泰以上这些都是好的品牌!国内知名品牌:印刷机:GKG,德森贴片机:没有回流焊:埃塔,劲拓,ETASMT生产工艺流程是什么?SMT基本工艺构成要素包括:丝印(或点胶),贴装(固化),回流焊接,清洗,检测,返修。
1、丝印:其作用是将焊膏或贴片胶漏印到PCB的焊盘上,为元器件的焊接做准备。
所用设备为丝印机(丝网印刷机),位于SMT生产线的最前端。
2、点胶:它是将胶水滴到PCB的的固定位置上,其主要作用是将元器件固定到PCB板上。
所用设备为点胶机,位于SMT生产线的最前端或检测设备的后面。
3、贴装:其作用是将表面组装元器件准确安装到PCB的固定位置上。
所用设备为贴片机,位于SMT生产线中丝印机的后面。
4、固化:其作用是将贴片胶融化,从而使表面组装元器件与PCB板牢固粘接在一起。
所用设备为固化炉,位于SMT生产线中贴片机的后面。
5、回流焊接:其作用是将焊膏融化,使表面组装元器件与PCB板牢固粘接在一起。
所用设备为回流焊炉,位于SMT生产线中贴片机的后面。
6、清洗:其作用是将组装好的PCB板上面的对人体有害的焊接残留物如助焊剂等除去。
SMT简介

SMT简介什么是SMT:SMT就是表面组装技术(Surface Mounted Technology的缩写),是目前电子组装行业里最流行的一种技术和工艺。
SMT有何特点:1、组装密度高、电子产品体积小、重量轻,贴片元件的体积和重量只有传统插装元件的1/10左右,一般采用SMT之后,电子产品体积缩小40%~60%,重量减轻60%~80%。
2、可靠性高、抗振能力强。
焊点缺陷率低。
3、高频特性好。
减少了电磁和射频干扰。
4、易于实现自动化,提高生产效率。
降低成本达30%~50%。
节省材料、能源、设备、人力、时间等。
为什么要用SMT:1、电子产品追求小型化,以前使用的穿孔插件元件已无法缩小2、电子产品功能更完整,所采用的集成电路(IC)已无穿孔元件,特别是大规模、高集成IC,不得不采用表面贴片元件。
3、产品批量化,生产自动化,厂方要以低成本高产量,出产优质产品以迎合顾客需求及加强市场竞争力4、电子元件的发展,集成电路(IC)的开发,半导体材料的多元应用5、电子科技革命势在必行,追逐国际潮流一、SMT工艺流程------单面组装工艺来料检测--> 丝印焊膏(点贴片胶)--> 贴片--> 烘干(固化)--> 回流焊接--> 清洗--> 检测--> 返修--------------------------------------------------------------------------------二、SMT工艺流程------单面混装工艺来料检测--> PCB的A面丝印焊膏(点贴片胶)--> 贴片--> 烘干(固化)--> 回流焊接--> 清洗--> 插件--> 波峰焊--> 清洗--> 检测--> 返修--------------------------------------------------------------------------------三、SMT工艺流程------双面组装工艺A:来料检测--> PCB的A面丝印焊膏(点贴片胶)--> 贴片--> 烘干(固化)--> A面回流焊接--> 清洗--> 翻板--> PCB的B面丝印焊膏(点贴片胶)--> 贴片--> 烘干-->回流焊接(最好仅对B面-->清洗--> 检测-->返修)此工艺适用于在PCB两面均贴装有PLCC等较大的SMD时采用。
SMT知识简述
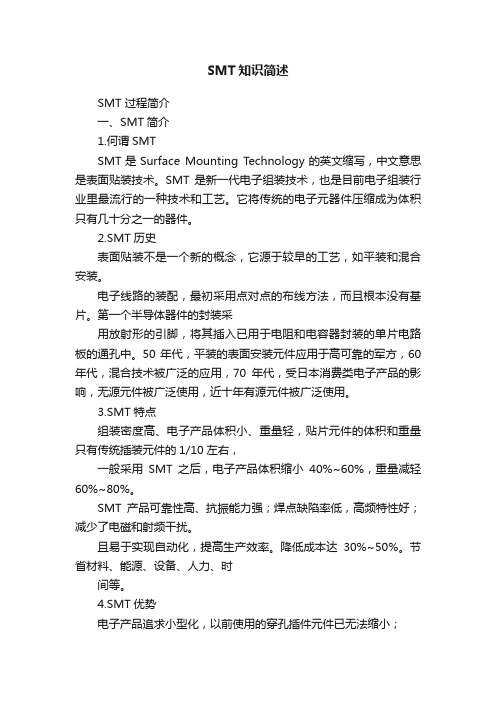
SMT知识简述SMT 过程简介一、SMT简介1.何谓SMTSMT是Surface Mounting Technology的英文缩写,中文意思是表面贴装技术。
SMT 是新一代电子组装技术,也是目前电子组装行业里最流行的一种技术和工艺。
它将传统的电子元器件压缩成为体积只有几十分之一的器件。
2.SMT历史表面贴装不是一个新的概念,它源于较早的工艺,如平装和混合安装。
电子线路的装配,最初采用点对点的布线方法,而且根本没有基片。
第一个半导体器件的封装采用放射形的引脚,将其插入已用于电阻和电容器封装的单片电路板的通孔中。
50年代,平装的表面安装元件应用于高可靠的军方,60年代,混合技术被广泛的应用,70年代,受日本消费类电子产品的影响,无源元件被广泛使用,近十年有源元件被广泛使用。
3.SMT特点组装密度高、电子产品体积小、重量轻,贴片元件的体积和重量只有传统插装元件的1/10左右,一般采用SMT之后,电子产品体积缩小40%~60%,重量减轻60%~80%。
SMT产品可靠性高、抗振能力强;焊点缺陷率低,高频特性好;减少了电磁和射频干扰。
且易于实现自动化,提高生产效率。
降低成本达30%~50%。
节省材料、能源、设备、人力、时间等。
4.SMT优势电子产品追求小型化,以前使用的穿孔插件元件已无法缩小;电子产品功能更完整,所采用的集成电路(IC)已无穿孔元件,特别是大规模、高集成IC,不得不采用表面贴片元件;产品批量化,生产自动化,厂方要以低成本高产量,出产优质产品以迎合顾客需求及加强市场竞争力;电子科技革命势在必行:电子元件的发展,集成电路(IC)的开发,半导体材料的多元应用等,都使追逐国际潮流的SMT工艺尽显优势。
5.SMT流程以某司A-Line为例:送板机=>Screen Printer(MPM:UP2000)=>Chip Mount(FUJI:CP-743E;Panasonic:MVⅡF )=>IC Mount(Panasonic:MPAVⅡB)=>Work Station=>Reflow (BTU:Paragon98)=>AOI(SONY:BFZ-Ⅲ)=>翻板机=>送板机=>Screen Printer(MPM:UP2000)=>Chip Mount(FUJI:CP-743E;Panasonic:MVⅡF )=>IC Mount(Panasonic:MPAVⅡB;PHLIPS:ACM Micro)=>WorkStation=>Reflow(BTU:Paragon98)=> AOI(SONY:BFZ-Ⅲ)=>目检=>ICT=>FCT二、零件简介1.表面贴装元件具备的条件表面贴装零件需具备以下条件:元件的形状适合于自动化表面贴装;尺寸,形状在标准化后具有互换性;有良好的尺寸精度;适应于流水或非流水作业;有一定的机械强度;可承受有机溶液的洗涤;可执行零散包装又适应编带包装;具有电性能以及机械性能的互换性;耐焊接热应符合相应的规定。
50条SMT工艺技术
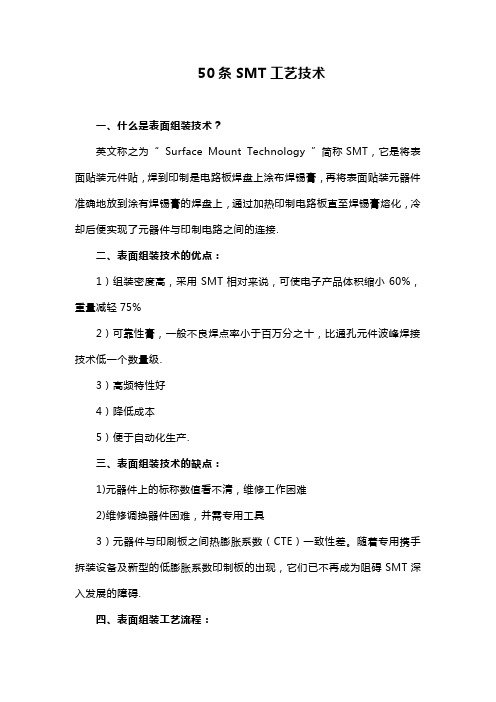
50条SMT工艺技术一、什么是表面组装技术?英文称之为“Surface Mount Technology ”简称SMT,它是将表面贴装元件贴,焊到印制是电路板焊盘上涂布焊锡膏,再将表面贴装元器件准确地放到涂有焊锡膏的焊盘上,通过加热印制电路板直至焊锡膏熔化,冷却后便实现了元器件与印制电路之间的连接.二、表面组装技术的优点:1)组装密度高,采用SMT相对来说,可使电子产品体积缩小60%,重量减轻75%2)可靠性膏,一般不良焊点率小于百万分之十,比通孔元件波峰焊接技术低一个数量级.3)高频特性好4)降低成本5)便于自动化生产.三、表面组装技术的缺点:1)元器件上的标称数值看不清,维修工作困难2)维修调换器件困难,并需专用工具3)元器件与印刷板之间热膨胀系数(CTE)一致性差。
随着专用携手拆装设备及新型的低膨胀系数印制板的出现,它们已不再成为阻碍SMT深入发展的障碍.四、表面组装工艺流程:SMT工艺有两类最基本的工艺流程,一类为锡膏回流焊工艺,另一类是贴片—波峰焊工艺.在实际生产中,应根据所用元器件和生产装备的类型以及产品的需求选择不同的工艺流程,现将基本的工艺流程图示如下:1)锡膏—回流焊工艺,该工艺流程的特点是简单,快捷,有利于产品体积的减小.2)贴片-波峰焊工艺,该工艺流程的特点是利用双面板空间,电子产品的体积可以进一步减小,且仍使用通孔元件,价格低廉,但设备要求增多,波峰焊过程中缺陷较多,难以实现高密度组装。
3)混合安装,该工艺流程特点是充分利用PCB板双面空间,是实现安装面积最小化的方法之一,并仍保留通孔元件价低的特点.4)双面均采用锡膏—回流焊工艺,该工艺流程的特点能充分利用PCB 空间,并实现安装面积最小化,工艺控制复杂,要求严格,常用于密集型或超小型电产品,移动电话是典型产品之一。
我们知道,在新型材料方面,焊膏和胶水都是触变性质流体,它们引起的缺陷占SMT总缺陷的60%,训练掌握这些材料知识才能保证SMT质量.SMT还涉及多种装联工艺,如印刷工艺,点胶工艺,贴放工艺,固化工艺,只要其中任一环节工艺参数漂移,就会导致不良品产生,SMT工艺人员必须具有丰富的工艺知识,随时监视工艺状况,预测发展动向。
精编【表面组装技术】SMT名词解释

【表面组装技术】SMT名词解释xxxx年xx月xx日xxxxxxxx集团企业有限公司Please enter your company's name and contentvSMT名词辞典索引:*A B C D E F G H I J K L M N O P Q R S T U V W X Y Z中*-----------------------------------------------------------------------------------------------------------------A-----------------------------------------------------------------------------------------------------------------Anti-Static Material抗静电材料【静电防制】在静电防制的领域中,所指的「抗静电材料」乃是指其材料具有下列的特性时即可称之:(1)能抑制摩擦生电的材料(ESDA ADV 1.0),或(2)能抑制摩擦生电至200V以下的材料(EIA 625);而抗静电材料的定义并不是由量测其表面电阻率或体积电阻率来决定其特性,而是直接利用摩擦后的结果来测定的。
《回索引》AOI自动视觉检查Automatic Optical Inspection【SMT】在自动化生产制程中,以光学机器设备对产品进行视觉检查的一种设备。
通常以CCD镜头将基板影像作分割照相后,再利用数字影像分析软件来对于零件之外型、标示、位置等及焊点之色泽来判定缺件、偏移、错件、空焊等问题;对于短路之色泽及形状判定目前技术上则显得有较差之倾向。
对于非视觉可检测之部份﹝如BGA焊点﹞则非其能力可及。
《回索引》---------------------------Bead电感器【SMT】Bead一字原本意思为「珠、串珠」的意思,但在SMT制程中不知何时开始却有了一约定俗成的说法来泛指片状大小﹝Chip-Size﹞之积层电感器组件。
SMT是什么意思?
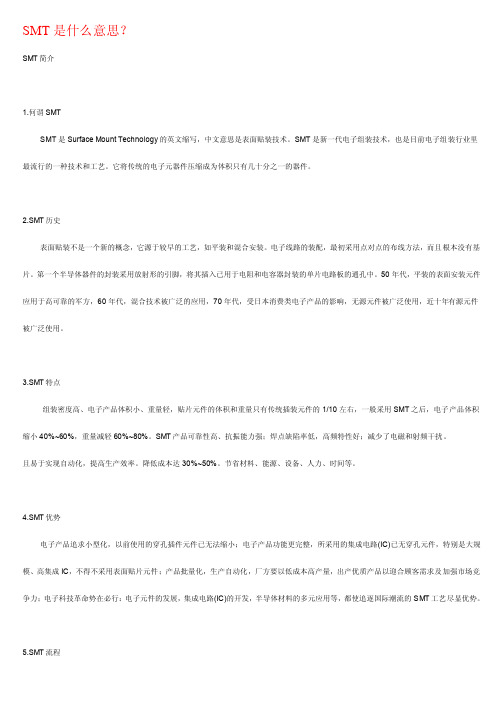
SMT是什么意思?SMT简介1.何谓SMTSMT是Surface Mount Technology的英文缩写,中文意思是表面贴装技术。
SMT是新一代电子组装技术,也是目前电子组装行业里最流行的一种技术和工艺。
它将传统的电子元器件压缩成为体积只有几十分之一的器件。
2.SMT历史表面贴装不是一个新的概念,它源于较早的工艺,如平装和混合安装。
电子线路的装配,最初采用点对点的布线方法,而且根本没有基片。
第一个半导体器件的封装采用放射形的引脚,将其插入已用于电阻和电容器封装的单片电路板的通孔中。
50年代,平装的表面安装元件应用于高可靠的军方,60年代,混合技术被广泛的应用,70年代,受日本消费类电子产品的影响,无源元件被广泛使用,近十年有源元件被广泛使用。
3.SMT特点组装密度高、电子产品体积小、重量轻,贴片元件的体积和重量只有传统插装元件的1/10左右,一般采用SMT之后,电子产品体积缩小40%~60%,重量减轻60%~80%。
SMT产品可靠性高、抗振能力强;焊点缺陷率低,高频特性好;减少了电磁和射频干扰。
且易于实现自动化,提高生产效率。
降低成本达30%~50%。
节省材料、能源、设备、人力、时间等。
4.SMT优势电子产品追求小型化,以前使用的穿孔插件元件已无法缩小;电子产品功能更完整,所采用的集成电路(IC)已无穿孔元件,特别是大规模、高集成IC,不得不采用表面贴片元件;产品批量化,生产自动化,厂方要以低成本高产量,出产优质产品以迎合顾客需求及加强市场竞争力;电子科技革命势在必行:电子元件的发展,集成电路(IC)的开发,半导体材料的多元应用等,都使追逐国际潮流的SMT工艺尽显优势。
以某司A-Line为例:送板机=>Screen Printer(MPM:UP2000)=>Chip Mount(FUJI:CP-743E;Panasonic:MVⅡF )=>IC Mount (Panasonic:MPAVⅡB)=>Work Station=>Reflow(BTU:Paragon98)=>AOI(SONY:BFZ-Ⅲ)=>翻板机=>送板机=>Screen Printer (MPM:UP2000)=>Chip Mount(FUJI:CP-743E;Panasonic:MVⅡF )=>IC Mount(Panasonic:MPAVⅡB;PHLIPS:ACM Micro)=>WorkStation=>Reflow(BTU:Paragon98)=> AOI自动光学检测仪(SONY:BFZ-Ⅲ)=>目检=>ICT=>FCT注:不良品经检出维修后继续按流程至后段SMT生产线经典配置方案SMT大概流程配置线:供给机+ 印刷机+ 高速贴片机+ 多功能贴片机+ 回流炉+ 收纳机SMT设备:贴片机的选择最为关键一般SMT生产工艺包括焊膏印刷、贴片和回流焊三个步骤,所以要组成一条完整的SMT生产线,必然包括实施上述工艺步骤的设备:印刷机、贴片机和回流焊炉。
SMT综述
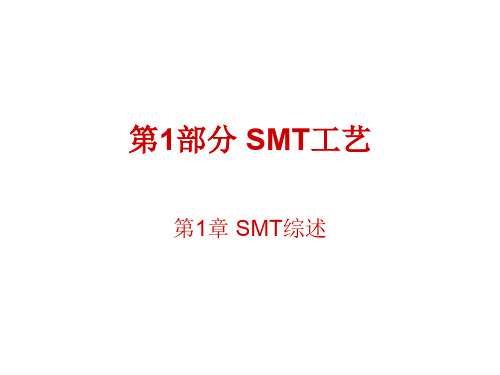
1.2.2 SMT工艺技术的基本内容
1.2.4 SMT生产系统的组线方式
•
1.印刷
•
将焊锡膏或贴片胶漏印到PCB的焊盘上,为元器件的焊接做准备。所用设备为焊
锡膏印刷机,位于SMT生产线的最前端。
,其主要作用是在采用波峰焊接时,将元器件
固定到PCB板上。所用设备为点胶机,位于SMT生产线的最前端或检测设备的后面。
• (2)多媒体化:从文字信息交流向声音、图像信息交流的转化发展,使电子设备 更加人性化、更加深入人们的生活与工作。
• (3)网络化:用网络技术把独立系统连接起来,高速、高频的信息传输使整个单 位、地区、国家以至全世界实现资源共享。
•
这种发展趋势和市场需求对电路组装技术的要求是:
•
高密度化:单位体积电子产品处理信息量的提高。
• (2)制造。各种元器件的制造技术。
• (3)包装。编带式、管式、托盘、散装等。
•
2.电路基板
•
单(多)层PCB、陶瓷、瓷釉金属板等。
•
3.组装设计
•
电设计、热设计、元器件布局、基板图形布线设计等。
•
4.组装工艺
• (1)组装材料。粘接剂、焊料、焊剂、清洗剂。
• (2)组装技术。涂敷技术、贴装技术、焊接技术、清洗技术、检测技术。
器件小得多,一般可减小60%~70%,甚至可减小90%;重量减轻60%~90%。 • (2)信号传输速度高。结构紧凑、组装密度高,在电路板上双面贴装时,组装密
度可以达到5.5~20个焊点/cm2,由于连线短、延迟小,可实现高速度的信号传输。 同时,更加耐振动、抗冲击。这对于电子设备超高速运行具有重大的意义。
展史与SMC/SMD的发展史基本是同步的。
表面贴装技术简介
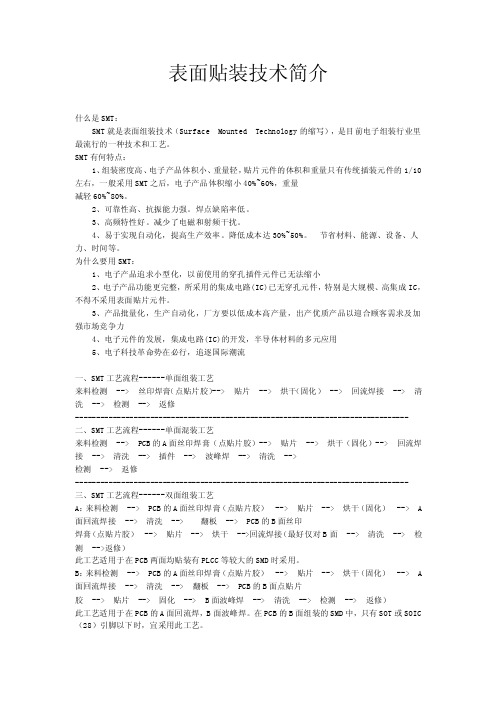
表面贴装技术简介什么是SMT:SMT就是表面组装技术(Surface Mounted Technology的缩写),是目前电子组装行业里最流行的一种技术和工艺。
SMT有何特点:1、组装密度高、电子产品体积小、重量轻,贴片元件的体积和重量只有传统插装元件的1/10左右,一般采用SMT之后,电子产品体积缩小40%~60%,重量减轻60%~80%。
2、可靠性高、抗振能力强。
焊点缺陷率低。
3、高频特性好。
减少了电磁和射频干扰。
4、易于实现自动化,提高生产效率。
降低成本达30%~50%。
节省材料、能源、设备、人力、时间等。
为什么要用SMT:1、电子产品追求小型化,以前使用的穿孔插件元件已无法缩小2、电子产品功能更完整,所采用的集成电路(IC)已无穿孔元件,特别是大规模、高集成IC,不得不采用表面贴片元件。
3、产品批量化,生产自动化,厂方要以低成本高产量,出产优质产品以迎合顾客需求及加强市场竞争力4、电子元件的发展,集成电路(IC)的开发,半导体材料的多元应用5、电子科技革命势在必行,追逐国际潮流一、SMT工艺流程------单面组装工艺来料检测 --> 丝印焊膏(点贴片胶)--> 贴片 --> 烘干(固化) --> 回流焊接 --> 清洗 --> 检测 --> 返修-------------------------------------------------------------------------------- 二、SMT工艺流程------单面混装工艺来料检测 --> PCB的A面丝印焊膏(点贴片胶)--> 贴片 --> 烘干(固化)--> 回流焊接 --> 清洗 --> 插件 --> 波峰焊 --> 清洗 -->检测 --> 返修-------------------------------------------------------------------------------- 三、SMT工艺流程------双面组装工艺A:来料检测 --> PCB的A面丝印焊膏(点贴片胶) --> 贴片 --> 烘干(固化) --> A 面回流焊接 --> 清洗 --> 翻板 --> PCB的B面丝印焊膏(点贴片胶) --> 贴片 --> 烘干 -->回流焊接(最好仅对B面 --> 清洗 --> 检测 -->返修)此工艺适用于在PCB两面均贴装有PLCC等较大的SMD时采用。
- 1、下载文档前请自行甄别文档内容的完整性,平台不提供额外的编辑、内容补充、找答案等附加服务。
- 2、"仅部分预览"的文档,不可在线预览部分如存在完整性等问题,可反馈申请退款(可完整预览的文档不适用该条件!)。
- 3、如文档侵犯您的权益,请联系客服反馈,我们会尽快为您处理(人工客服工作时间:9:00-18:30)。
表面组装技术概述及组装设备学习目标✧ 能了解表面组装技术;✧ 能了解表面组装设备;工作任务✧ 去相关企业(公司)参观或实习。
案例说明✧ 通过观看贴片机工作过程、SMT 工艺流程、MMIC 单片混合集成电路工艺视频,以及识读HT203-SMT 作业指导书,让学生能了解贴片机工作过程、能熟悉SMT 工艺流程、能了解最新微组装工艺流程和设备,从而进一步能了解表面组装技术及表面组装设备。
表面组装技术(Surface Mount Technology,简称SMT )是突破了传统的印制电路板(PCB )通孔基板插装元器件工艺(Through-hole Mounting Technology, THT )发展起来的第四代电子装联技术。
它是将表面贴装元器件(无引脚或短引脚的元器件)贴、焊到印制电路板表面规定位置上的电子装联技术,所用的印制电路板无需插孔。
概括地说,就是首先在印制电路板焊盘上涂覆焊锡膏,再将表面贴装元器件准确地放到涂有焊锡膏的焊盘上,再通过加热印制电路板直至焊膏熔化,冷却后便实现了元器件与印制电路板之间的互联。
图4-1为表面组装技术示意图。
4.1.1 表面组装技术的发展过程SMT 发展至今,已经经历了四个阶段:1)第一阶段(1970-1975年):以小型化为主要目标,此时的表面组装元器件主要用于混合集成电路,如石英表和计算器等。
图4-1 SMT 示意图2)第二阶段(1976-1980年):这一阶段的主要目标是减小电子产品的单位体积,提高电路功能,产品主要用于摄像机、录像机、电子照相机等。
3)第三阶段(1980-1995年):这一阶段的主要目标是降低成本,大力发展组装设备,表面组装元器件进一步微型化,提高电子产品的性价比。
4)第四阶段(1996-至今):SMT已经进入了微组装技术(Microelectronics Packaging Technology,简称MPT)、高密度组装和立体组装的新阶段,以及多芯片组件等新型表面组装元器件快速发展和大量应用阶段。
4.1.2 表面组装技术的特点SMT是今后电子产品能有效地实现“轻、薄、短、小”和多功能、高可靠、优质、低成本的主要手段之一,主要优点如下:1. 组装密度高片式元器件与传统穿孔元器件相比所占面积和质量大为减少。
一般地,采用SMT可使电子产品体积缩小60%,质量减轻75%。
通孔安装技术元器件,它们按2.54mm网格安装元器件,而SMT组装元器件网格从1.27mm发展到目前0.63mm网格,个别达0.5mm网格安装元器件,密度更高。
例如一个64引脚的DIP集成块,它的组装面积为25mm×75mm,而同样引线采用引线间距为0.63mm的QFP,它的组装面积为12mm×12mm,面积为通孔技术的1/12。
2. 可靠性高由于片式元器件的可靠性高,器件小而轻,故抗震能力强,采用自动化生产,贴装可靠性高,一般不良焊点率小于百万分之十,比通孔插元件波峰焊接技术低一个数量级,用SMT 组装的电子产品MTBF平均为25万小时,目前几乎有90%的电子产品采用SMT工艺。
3. 高频特性好由于片式元器件贴装牢固,器件通常为无引线或短引线,降低了寄生电感和寄生电容的影响,提高了电路的高频特性,采用SMC及SMD设计的电路最高频率达3GHz,而采用通孔元器件仅为500MHz。
采用SMT乜可缩短传输延迟时间,可用于时钟频率为16MHz以上的电路。
若使用MCM技术,计算机工作站的高端时钟频率可达100MHz,由寄生电抗引起的附加功耗可降低2~3倍。
4. 成本降低印制板使用面积减小,面积为通孔技术的1/12,若采用CSP安装则其面积还要大幅度下降;印制板上钻孔数量减少,节约返修费用;由于频率特性提高,减少了电路调试费用;由于片式元器件体积小、质量轻,减少了包装、运输和储存费用;SMC及SMD发展快,成本迅速下降。
5. 便于自动化生产表面组装技术与通孔插装技术相比更适合自动化生产。
通孔插装技术根据插装元器件的不同需要不同的插装设备,如跳线机、径向插装机、轴向插装机等,设备生产调整准备时间较长。
由于通孔的孔径较小,插装的精度也较差,返修的工作量也较大,而且换料时必须停机,缩短了工作时间。
而表面组装元器件在一台泛用机上就可以完成贴装任务,且具有不停机换料功能,节省了大量时间。
同时由于表面组装技术的相关设备具有视觉功能,所以贴装精度高,返修工作量低,自动化程度和生产效率就高得多。
当然,SMT生产中也存在一些问题,如元器件上的标称数值看不清,维修工作困难;维修调换器件困难,并需专用工具;元器件与印制板之间热膨胀系数一致性差。
但这些问题均是发展中的问题,随着寺用拆装设备的出现,以及新型低膨胀系数印制板的出现,均已不再成为阻碍SMT深入发展的障碍。
4.1.3 表面组装技术的基本组成表面组装技术通常包括:表面组装元器件、表面组装电路板及图形设计、表面组装专用料——焊锡膏及贴片胶、表面组装设备、表面组装焊接技术(包括双波峰焊、再流焊、汽相焊、激光焊)、表面组装测试技术、清洗技术以及表面组装生产管理等多方面。
表面组装技术(SMT)的基本组成如图4-2所示。
这些内容可以归纳为三个方面:一是设备,人们称它为SMT的硬件;二是装联工艺,人们称它为SMT的软件;三是电子元器件,它既是SMT的基础,又是SMT发展的动力,它推动着SMT专用设备和装联工艺不断更新和深化。
图4-2 SMT的基本组成4.1.4 表面组装技术的发展趋势表面组装技术自20世纪60年代中期问世以来,经过40多年的发展,已经成为了当今电子装联技术的主流,而且正在继续向纵深发展。
其发展趋势主要表现为以下几个方面:1. SMT设备正向高效、灵活、智能、环保等方向发展提高SMT设备的生产效率一直是人们的追求目标,SMT生产设备巳从过去的单台设备工作,向多台设备组合连线的方向发展;从多台分步控制方式向集中在线控制方向发展;从单路连线生产向双路组合连线生产方向发展。
此外,SMT设备主要是利用计算机来操作,提高自动化控制程度,把一些工艺参数储存固定,提高机器的自动化程度,稳定和提高产品质量。
随着欧盟《关于在电子电气设备中限制使用某些有害物质指令(RoHS)》在全球逐步执行,表面组装技术也迅速向无铅化方向发展,无铅焊料、各向异性导电胶、各向异性导电胶薄膜与焊料树脂导电材料都已经获得实际应用。
与此同时,为了实现真正无铅化,与之相适应的工艺材料、元器件、生产设备、检测方法及设备也在不断完善,并已进入实用阶段。
所以,SMT总的发展趋势是正向高效、灵活、智能、环保等方向发展。
2. 元器件的发展随着元器件的不断研发,元器件朝着体积更小、集成度更高的方向发展,元器件的封装形式也随着组装产品朝体积小、重量轻、工作频率更高、抗干扰更强、可靠性更高的要求在发展。
片式元件SMC的模块化等是其今后的发展方向。
由于元件尺寸已日益面临极限,自动生产设备的精度也趋于极限,片式元件复合化、模块化将得到迅速的发展和广泛的应用。
目前英制0603、0402和0201在PCB上的应用非常普遍,但01005已经接近设备和工艺的极限尺寸,因此,01005只适合模块的组装工艺和高性能的手机等场合。
集成电路封装技术的发展也非常迅速,从双列直插DIP向表面组装期间SMD发展,SMD 又迅速向小型、薄型和细间距发展;引脚间距从过去的1.27mm、1mm、0.86mm、0.65mm到目前的0.5mm、0.4mm、0.3mm发展;引脚排列从周边引脚向器件底部球栅阵列引脚发展;近年来又向二维、三维发展,出现了多芯片组件MCM(Multi Chip Module)、封装上堆叠POP(Package on Package),最后还要向单片系统SOC(System on a Chip)发展。
随着SMT技术的成熟,特别是低热膨胀系数的PCB以及专用焊料和填充材料的成功开发,裸芯片直接贴装到PCB上的技术发展十分迅速,目前裸芯片技术主要有板载芯片COB(Chip on Board)技术和倒装芯片FC(Flip Chip)技术,这将成为21世纪芯片应用的发展主流。
3. 生产设备及工艺的发展为了适应新型元器件的贴装,生产设备的贴装精度越来越高,可贴装超细间距元器件的技术越来越成熟,制造工艺技术不断提高,通孔回流焊工艺和选择性波峰焊工艺的应用越来越广泛。
总之,随着小型化高密度封装的发展,随着新型元器件的不断涌现,一些新技术、新工艺也随之产生,从而极大地促进了表面组装技术的创新和发展。
4.5 表面组装设备由表面涂敷设备、贴装机、焊接机、清洗机、测试设备等表面组装设备形成的SMT生产系统习惯上称为SMT生产线。
如图4-16所示。
图4-16 小规模全自动SMT生产线4.5.1 焊膏印刷机焊膏印刷机是将焊锡膏或贴片胶均匀正确地印刷或涂到PCB相应位置的一种SMT设备。
焊膏印刷现在被认为是,表面贴装技术中控制最终焊锡节点品质的关键的过程步骤。
目前焊膏印刷机可大致分三个档次:手动或半自动印刷机、配有视觉识别系统的半自动印刷机以及全自动印刷机。
印刷机大致上可分为三类:1)手动锡膏印刷机手工印刷机是最简单而且最便宜的印刷系统, PCB放置及取出均需人工完成,其刮刀可用手把或附在机台上,印刷动作亦需人手完成,PCB与钢板平行度对准或以板边缘保证位置度均需依靠作业者的技巧,如此将导致每印一块PCB,印刷的参数均需进行调整变化。
此种印刷方式速度慢且印刷质量低,根本不能满足现在生产的需求,基本已经淘汰。
图4-17(a)所示为一台手动印刷机的实物照片。
2)半自动锡膏印刷机半自动印刷机是当前使用最为广泛的印刷设备, 它们实际上很类似手工印刷机,其PCB 的放置及取出仍需依赖手工操作,与手工机的主要区别是印刷头的发展,它们能够较好地控制印刷速度,刮刀压力、刮刀角度,印刷距离以及非接触间距,工具孔或PCB边缘仍被用来定位,而钢板系统以助人员良好地完成PCB与钢板的平行度调整,此种印刷机比手动锡膏印刷机有了很大的完善,在产量和质量上有了很大的提高。
图4-17(b)所示为一台半自动印刷机的实物照片。
3)全自动锡膏印刷机全自动印刷机配有视觉识别、PCB自动装载等系统后,能实现全自动运行,印刷精度高,印刷速度快,适合大规模大批量自动化生产。
图 4-17(c)所示为一台全自动印刷机的实物照片。
(a)手动印刷机(b)半自动印刷机(c)全自动印刷机图 4-17 印刷机实物图焊锡膏的印刷是SMT整个工艺过程中最关键的一道工序,几乎70%左右的焊接问题与焊锡膏的印刷质量有关。
焊锡膏印刷除了对印刷机性能要求较高外,与模板、焊锡膏的好坏、印刷机的工艺参数设置、工艺过程、PCB的设计等多种因素密切相关,其中任何一个因素、一个环节出现问题都会直接影响整个印刷质量。