化工设计大作业(课程设计)剖析
化工设计课程设计

化工设计课程设计一、设计背景及要求化工设计是化学工程专业中重要的核心课程之一,其课程涉及了化工工业生产中各个环节,是化学工程专业学生必学的课程之一。
本次化工设计课程设计主要是针对学生在该课程学习期间所学知识进行的实践性设计任务,旨在锻炼学生的实践操作能力,提高实际问题解决能力。
本次化工设计课程设计的主要要求如下:1.确定化工系统的结构和流程,建立物料及能量平衡计算单元。
2.进行系统的热力学计算,确定物料的流量和温度等参数。
3.确定新工艺流程和设备选型,进行方案的具体设计。
4.对设计结果进行评价,分析设计方案的合理性和优劣势。
二、设计流程1.确定化工系统结构和流程在进行化工系统设计之前,首先需要根据分析目标确定化工系统的结构和流程,以此为基础建立物料及能量平衡计算单元。
化工系统结构主要包括组件之间的相互关系及其所在的位置。
在确定结构时,应注意系统的连通性和稳定性。
化工流程则是指从原料投入到产品产出的整个过程。
对于化工流程的设计,应注意流程的简洁性、合理性及处理流程的稳定性。
2.进行系统的热力学计算在确定好化工系统的结构和流程后,需要进行系统的热力学计算,以确定物料的流量和温度等参数。
热力学计算是指通过分析化工系统的热量变化来确定质量流量、热量流量和热交换情况等因素,并且控制流体的运动状况。
热力学计算不仅可以帮助设计师对化工系统进行优化设计,还可以对热连续系统进行优化,从而实现系统的最优化。
3.确定新工艺流程和设备选型在进行热力学计算后,需要确定新工艺流程和设备选型,进行方案的具体设计。
根据化工系统的各项参数及物料及能量平衡计算单元得到的计算结果数据,确定新工艺流程和设备选型,从而进一步具体化设计方案。
设计师应根据化工系统的实际情况选定相应的设备,并基于设备特点设计相应的工艺流程。
4.对设计结果进行评价最后,对设计结果进行评价,分析设计方案的合理性和优劣势。
评价主要分为两个方面:结果的可行性和成本的可控性。
化工设计的课程设计

化工设计的课程设计一、课程目标知识目标:1. 让学生理解化工设计的基本概念、原理和方法,掌握化工流程的绘制和优化。
2. 使学生掌握化工设备的设计与选型,了解材料选择、工艺参数确定等关键环节。
3. 帮助学生了解化工安全、环保等方面的知识,提高其在化工设计中的责任意识和风险防控能力。
技能目标:1. 培养学生运用CAD等软件绘制化工图纸的能力,提高其空间想象和实际操作能力。
2. 培养学生运用化工原理和计算方法解决实际问题的能力,提高其分析、解决问题的能力。
3. 培养学生团队协作、沟通表达的能力,提高其在项目实践中的组织和协调能力。
情感态度价值观目标:1. 激发学生对化工设计的兴趣,培养其探究精神和创新意识。
2. 培养学生关注化工行业的发展,使其认识到化工技术在国民经济中的重要性。
3. 引导学生树立安全、环保意识,培养其良好的职业素养和社会责任感。
本课程针对高年级学生,结合化工学科特点,注重理论知识与实践操作的相结合。
通过本课程的学习,使学生能够具备化工设计的基本知识和技能,为未来从事相关工作打下坚实基础。
同时,注重培养学生的团队协作、沟通表达等综合素质,提升其在化工行业中的竞争力和发展潜力。
二、教学内容本章节教学内容主要包括以下几部分:1. 化工设计基本概念:介绍化工设计的目的、意义、基本原理和方法,使学生了解化工设计在工程实践中的应用。
2. 化工流程绘制与优化:讲解化工流程图的绘制方法,运用CAD等软件进行流程图绘制,分析并优化化工流程。
3. 化工设备设计与选型:学习化工设备的设计原理,掌握设备选型的依据和方法,了解材料选择、工艺参数确定等关键环节。
4. 化工安全与环保:介绍化工设计中安全、环保方面的知识,分析典型事故案例,提高学生在设计过程中的风险防控能力。
5. 化工设计实例分析:结合实际案例,分析化工设计过程中的关键问题,使学生学会运用所学知识解决实际问题。
教学内容安排如下:第一周:化工设计基本概念及方法;第二周:化工流程绘制与优化;第三周:化工设备设计与选型;第四周:化工安全与环保;第五周:化工设计实例分析及总结。
化工课程设计总结
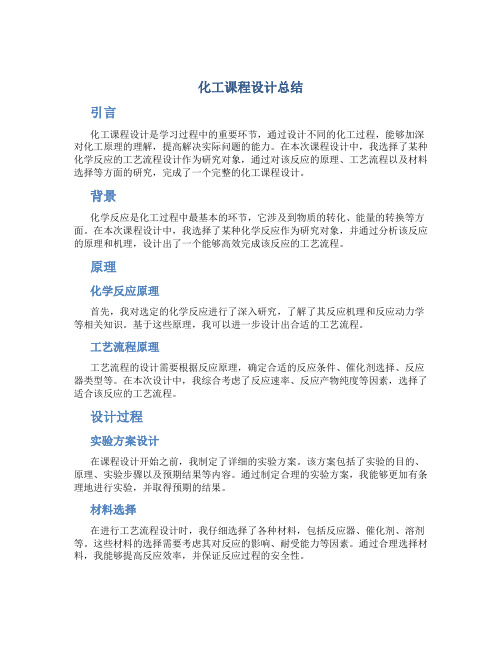
化工课程设计总结引言化工课程设计是学习过程中的重要环节,通过设计不同的化工过程,能够加深对化工原理的理解,提高解决实际问题的能力。
在本次课程设计中,我选择了某种化学反应的工艺流程设计作为研究对象,通过对该反应的原理、工艺流程以及材料选择等方面的研究,完成了一个完整的化工课程设计。
背景化学反应是化工过程中最基本的环节,它涉及到物质的转化、能量的转换等方面。
在本次课程设计中,我选择了某种化学反应作为研究对象,并通过分析该反应的原理和机理,设计出了一个能够高效完成该反应的工艺流程。
原理化学反应原理首先,我对选定的化学反应进行了深入研究,了解了其反应机理和反应动力学等相关知识。
基于这些原理,我可以进一步设计出合适的工艺流程。
工艺流程原理工艺流程的设计需要根据反应原理,确定合适的反应条件、催化剂选择、反应器类型等。
在本次设计中,我综合考虑了反应速率、反应产物纯度等因素,选择了适合该反应的工艺流程。
设计过程实验方案设计在课程设计开始之前,我制定了详细的实验方案。
该方案包括了实验的目的、原理、实验步骤以及预期结果等内容。
通过制定合理的实验方案,我能够更加有条理地进行实验,并取得预期的结果。
材料选择在进行工艺流程设计时,我仔细选择了各种材料,包括反应器、催化剂、溶剂等。
这些材料的选择需要考虑其对反应的影响、耐受能力等因素。
通过合理选择材料,我能够提高反应效率,并保证反应过程的安全性。
工艺流程设计综合考虑了反应原理和材料选择等因素后,我开始进行工艺流程的设计。
通过分析反应步骤、反应条件等因素,我确定了一个能够高效完成反应的工艺流程,并对该流程进行了优化和调整。
实验操作与结果分析在进行实验操作时,我严格按照设计方案进行操作,并及时记录实验数据。
通过对实验结果的分析,我能够了解反应的效果,并根据分析结果进行进一步的优化。
结论通过本次化工课程设计,我深入了解了化学反应的原理和工艺流程的设计方法。
通过实践操作,我更加熟悉了实际化工过程中各种材料的选择和操作技术。
化工课程设计心得体会

化工课程设计心得体会
在化工课程设计中,我学到了很多知识和技能,并且有一些心得体会。
首先,化工课程设计是将之前学到的理论知识应用到实际情况中的一个过程。
通过设
计一个化工过程,我深入了解了各种反应器的性能和操作条件,以及不同反应物之间
的相互作用。
这让我对化工原理有了更深刻的理解。
其次,化工课程设计需要综合运用多门学科的知识。
在设计过程中,我需要考虑到化
学反应、热力学、流体力学等多个方面的因素。
这让我意识到化工工程的复杂性,需
要不同学科的知识相互配合,才能得到最佳的设计方案。
此外,化工课程设计还加强了我解决问题的能力。
在设计过程中,我遇到了很多困难
和挑战,需要分析问题、查找信息、做出决策。
这让我学会了如何面对问题和挑战,
并找到解决问题的方法和思路。
最后,化工课程设计还培养了我的团队合作能力。
因为设计一个化工过程往往需要多
个人共同努力,我需要和队友一起分工合作、互相支持和协调。
这培养了我与他人合
作的能力,并加深了我对团队合作重要性的认识。
总的来说,化工课程设计是一个非常有意义和有挑战的过程。
通过设计一个化工过程,我不仅学到了知识和技能,还培养了解决问题和团队合作的能力。
这对我今后从事化
工工作和研究都有着重要的指导意义。
化工设计大作业(新)

化工设计大作业设计目的和要求化工设计是把一项化工过程从设想变成现实的一个建设环节,涉及政治、经济、技术;资源、产品、市场、用户、环境;国策、标准、法规;化学、化工、机械、电气、土建、自控、安全卫生、给排水等专业和方方面面,是一门综合性很强的技术科学。
要求综合应用本门课程和有关先修课程所学知识,完成以化工生产装置设计为主的一次设计实践。
使学生掌握化工设计的基本程序和方法,并在查阅技术资料、选用公式和数据、用简洁文字和图表表达设计结果、制图以及计算机辅助计算等能力方面得到一次基本训练,在设计过程中还应培养学生树立正确的设计思想和实事求是、严肃负责的工作作风.帮助学生学会综合运用各种已学过的知识系统地分析问题和解决问题,帮助学生从高等学校走向社会时能适应新的工作岗位的需要,迅速实现从大学生向工程师的转化.2.设计的内容围绕某一典型生产单元的设计为中心,其基本内容为:设计方案简介:对给定或选定的工艺流程、主要设备的型式进行简要的论述.(2)主要设备的工艺设计计算(含计算机辅助计算):物料衡算,能量衡量,工艺参数的选定,设备的结构设计和工艺尺寸的设计计算。
(3)工艺流程图:以单线图的形式绘制,标出主体设备与辅助设备的物料方向,物流量、能流量,主要测量点。
(4).主要设备图:图面应包括设备的主要工艺尺寸,技术特性表和接管表。
(5)。
设计说明书的编写。
设计说明书的内容应包括:设计任务书,目录,设计方案简介,工艺计算及主要设备设计,工艺流程图,主要设备图,设计结果汇总,设计评述,参考文献。
整个设计由论述,计算和图表三个部分组成,论述应该条理清晰,观点明确;计算要求方法正确,计算公式和所有数据必需注明出处;图表应能简要表达计算的结果。
3.设计的进度安排日期内容第三周布置设计题目,安排学生查阅相关文献,了解设计项目的背景、意义及主要生产方法等。
第四、五周对文献中查阅的产品不同生产方法进行分析,确定产品生产方案及绘制工艺框图。
课程设计报告化工
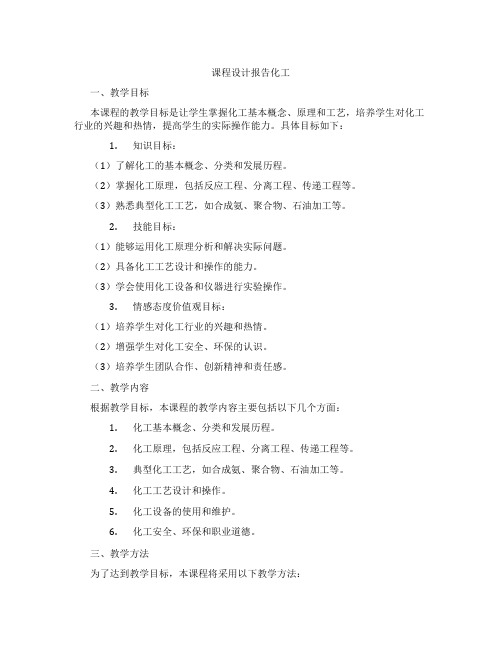
药店培训总结和计划表一、培训总结经过为期一个月的药店员工培训,我们取得了一定的成果,也发现了一些问题。
在此做一下总结和评估。
1. 培训内容在这一个月的培训中,我们主要覆盖了以下内容:- 药品知识:各类药品的功效、用法用量、不良反应等知识。
- 销售技巧:如何与顾客进行有效沟通、提升销售技巧等。
- 服务理念:提供更加贴心的服务,满足顾客需求。
- 应对突发状况:如何应对突发情况,保障工作安全。
2. 培训效果在培训结束后,我们进行了一次测试,结果显示,大部分员工的药品知识、销售技巧、服务理念等方面均有一定提升。
同时,员工们在实际工作中的表现也有所改善,顾客满意度提高了。
3. 存在问题然而,我们也发现了一些问题:- 培训缺失:在培训内容上,针对一些员工的具体需求还不够全面,需进一步完善。
- 应用不足:部分员工在实际工作中还未能很好地将培训内容应用到实践中,需要更多的指导和辅导。
4. 下一步计划为了进一步提升员工的综合素质和工作能力,我们制定了以下的培训计划。
二、培训计划1. 培训目标通过培训,提升员工的专业水平和服务态度,增强他们的职业素养。
2. 培训内容我们将进一步加强以下方面的培训内容:- 药品知识:不仅要求员工熟悉各类药品的基本知识,还要求他们能解答客户的常见问题。
- 销售技巧:从销售技巧的理论知识到实际操作的技能培训,全面提升员工的销售能力。
- 服务理念:加强员工的服务意识,提高服务质量,满足客户需求,提升客户满意度。
- 应对突发状况:安全问题的培训,教导员工如何应对突发情况,保障自身和顾客的安全。
3. 培训时间我们计划安排一个月的时间,每周进行一次集中培训,每次培训4小时,加上每天的自学时间,确保员工充分领会培训内容。
4. 培训方式我们将采用讲座、互动交流、实践操作等多种方式开展培训,以期更好地激发员工学习的积极性和主动性。
5. 培训师资我们计划邀请专业的医药行业人士、销售专家等进行培训和辅导,提供更加专业和全面的指导。
化工课程设计
化工课程设计化工课程设计是指以化学工程为基础,通过课程学习和实践操作,培养化工专业学生的综合素质和实践操作能力。
化工课程设计是现代化工教育的重要组成部分,是培养优秀化工人才的必要手段之一。
一、化工课程设计的意义化工课程设计是化工专业学生进行实践操作和创新研究的重要环节,可以充分发挥学生的想象力和创造力,培养学生实践操作技能和解决问题的能力,促进学生对所学理论知识的理解和掌握,使学生能够更好地适应职业发展需要。
1. 培养学生实践操作能力化工课程设计是一种综合性的实践操作,通过实验操作、数据统计与分析等方式,培养学生的实践操作能力,提高学生实践操作的技能和基本素质,为学生今后从事相关职业奠定了基础。
2. 培养学生解决问题的能力在实践操作过程中,学生不仅需要掌握基本的实验技能和实验方法,还需要独立思考、发现问题、解决问题的能力。
因此,化工课程设计可以培养学生发现问题、独立思考、团队协作和解决问题的能力,使学生具备了较高的创新能力和实践能力。
3. 促进学生对所学理论知识的掌握和理解化工课程设计是将理论知识与实践紧密结合的具体体现,通过实验操作、数据分析等方式,使学生更加深入地理解所学专业知识,加速学生理论知识向实践的转化。
二、化工课程设计的设计思路在进行化工课程设计时,首先需要明确实验的目的,了解实验的基本流程和操作技能,确定实验所需的器材和药品,以及对实验结果进行统计与分析。
具体的化工课程设计思路如下:1.明确实验的目的在进行化工课程设计前,需要明确实验的目的。
实验目的应与学生掌握的知识和能力需求相适应,同时应具有实践性和操作性。
明确实验目的可以帮助学生更好地进行实验设计,并更好地完成实验任务。
2.确定实验的基本流程和操作技能确定实验的基本流程和操作技能非常重要。
在确定实验基本流程和操作技能前,需考虑一系列因素,例如实验时间、器材数量和药品种类等,以保证实验的正常进行和实验结果的准确性。
3.确定实验所需的器材和药品确定实验所需的器材和药品是化工课程设计的基础,为实验的正常进行提供了基础设施。
化工课程设计自我总结800字6篇
化工课程设计自我总结800字6篇篇1通过这次化工课程设计,我深刻体验到了理论与实践相结合的重要性,并在实际操作中收获颇丰。
在此,我对这一阶段的成果进行一个系统的自我总结。
一、设计背景与目标本次化工课程设计旨在通过实际操作,加深我们对化工原理、工艺流程及实际操作的理解。
在设计之初,我明确了几个主要目标:一是掌握化工设计的基本流程和方法;二是培养解决实际问题的能力;三是培养团队协作和沟通能力。
二、设计与实施过程在设计过程中,我首先深入研究了相关化工原理和工艺流程,确保理论知识的扎实。
随后,我结合实验室的实际情况,进行了详细的设计规划。
过程中涉及到了多个关键环节,如工艺流程的选择与优化、设备的选型与布局等。
我注重细节,多次与团队成员讨论交流,确保设计的合理性和可行性。
在实验阶段,我严格按照操作规程进行,时刻关注实验数据的变化,确保实验结果的准确性。
遇到问题时,我积极查阅资料、请教老师,努力寻找解决方案。
同时,我也注重实验安全,确保整个过程的顺利进行。
三、收获与成长通过这次设计,我深刻感受到了理论与实践的结合之美。
在实际操作中,我不仅巩固了所学的理论知识,还学会了很多实际操作技能。
此外,我还提高了解决实际问题的能力,对化工行业的认识也更加深刻。
在团队协作方面,我学会了如何与队友有效沟通,如何在团队中发挥个人优势。
这次设计也让我明白了责任与担当的重要性,我时刻提醒自己要对团队负责、对项目负责。
四、存在问题与反思尽管本次设计取得了一定的成果,但仍存在一些不足。
首先,在设计中我还存在一些知识盲区,需要进一步加强学习。
其次,在实验操作中,我的操作技能还有待提高。
此外,我还需要提高自己在高压、高温等极端环境下的操作能力。
五、未来展望未来,我将继续深入学习化工知识,不断提高自己的专业技能。
同时,我还会加强实践操作能力,努力成为一名优秀的化工工程师。
此外,我还会注重团队协作和沟通能力的培养,为将来的工作打下坚实的基础。
化工课程设计
化工课程设计化工课程设计是化工专业中非常重要且不可避免的一部分。
它涉及到化工专业学生的实践技能、学术知识和实践经验等方面。
化工课程设计的主要目的是为化工学生提供一个实践平台,让他们能够在实践中掌握学习到的知识和技能,并通过课程设计获得实践经验,进一步培养化学实践的能力。
化工课程设计的重要性非常显著。
它是一种将理论知识和实践技能结合起来的做法,可以帮助学生深入了解化工原理、提高实践技能,并将理论应用于实际操作。
通过化工课程设计,学生能够独立思考问题并创新,深化对化工知识的认识,提高实践能力和实验技能,为将来从事化工领域的工作做好充分准备。
化工课程设计包括实验、综合设计和创新设计三个部分。
实验是化学专业中最基础的实践课程之一。
通过实验,化学学生可以更好地理解课堂上学到的知识,同时在实践中掌握实验操作和实验技能。
综合设计是将多方面的知识和技能融为一体,综合运用所掌握的化学知识和实验技能,独立设计一套系统方案的课程。
综合设计将涉及到多个学科,需要学生在实践过程中进行合理的分析和综合,为将来应对更复杂的问题做好预备。
创新设计是在综合设计的基础上,通过创新思维和创业精神来提出更好的解决方案。
创新设计的重点是提高创新能力,大学生不仅要掌握传统化学学科知识和实验技能,还要有创新思维和创业意识,为未来的创业做好准备。
在化工课程设计中,学生们的实践经验非常重要。
学生需要通过实验操作,实际控制流程参数,了解和理解化学反应的特点和机制。
掌握实验技能,熟悉仪器的原理和使用方法等,能够在今后的实践中运用。
通过课程设计的实践环节,学生们可以获得大量非书本知识和实践经验,并在以后的工作中受益匪浅。
除了实践经验之外,化工课程设计还要求学生具备批判性思维和创新思维。
当涉及到实验设备的设计时,学生需要了解常规设备构造和制造过程,并思考如何进行改进以达到更高的精度和效率。
此外,学生还需要熟练运用各种软件,模拟和优化实验过程,提高实验设计的效率和精度。
化工专业课程设计全解
流程简图
D
RADFRAC FEED
W16:23:5816:23:5816:23:58
16:23:58
16:23:58
16:23:58
16:23:58
1、塔径的计算 采用Smith法分别计算精馏段和提馏段的D 2、塔板上流体流型的选择 根据塔径和液体流量 3、降液管和溢流堰尺寸的确定 4、浮阀及其排列
16:23:58
5、塔板布置 确定边缘区和安定区尺寸 根据阀孔动能因数F0=9~12,计算阀孔气速ω0 浮阀个数N=V/(0.785d02 ω0 ) 确定排列高度 确定横向上排列的浮阀排数 开孔率
16:23:58
6、塔板水力学计算 塔板压降 降液管中清液高Hd 液体在降液管中停留时间 雾沫夹带量e 泄露 负荷性能图
16:23:58
塔顶冷凝器
16:23:58
塔顶空间高度、板间距、塔底空间高度、进 料空间高度 人孔设计:位置及其板间距 塔体总高度 封头设计 裙座设计 接管设计
16:23:58
16:23:58
16:23:58
工艺计算 6、回流比和理论板数计算
根据恩德伍德公式试差计算θ和Rmin 根据芬斯克方程计算Nmin 取不同的R/Rmin=(1.0~3.0),计算不同的R、 X=(R-Rmin)/(R+1) 根据吉利兰图或公式计算出不同的Y,根据 Y=(N-Nmin)/(N+1)计算出不同的N
16:23:58
工艺计算
以R/Rmin为横坐标、N为纵坐标作回流比与理 论板数关系曲线图 根据曲线拐点确定回流比和理论板数
16:23:58
工艺计算 7、求实际塔板数
计算塔顶塔底算术平均温度
计算相对挥发度和进料粘度 根据奥康奈尔关联式计算全塔效率ET
- 1、下载文档前请自行甄别文档内容的完整性,平台不提供额外的编辑、内容补充、找答案等附加服务。
- 2、"仅部分预览"的文档,不可在线预览部分如存在完整性等问题,可反馈申请退款(可完整预览的文档不适用该条件!)。
- 3、如文档侵犯您的权益,请联系客服反馈,我们会尽快为您处理(人工客服工作时间:9:00-18:30)。
化工工艺课程设计任务书设计题目:常压甲醇-水筛板精馏塔的设计设计条件:常压P=1atm(绝压)处理量:20kmol/h进料组成0.2 馏出液组成0.995釜液组成0.005 (以上均为摩尔分率)加料热状况q=1.0塔顶全凝器泡点回流回流比R=(1.1—2.0)R min单板压降≤0.7kPa设计要求:1.撰写一份设计说明书,包括:(1)概述(2)物料衡算(3)热量衡算(4)工艺设计要求(5)工艺条件表2.绘制图纸(1)设备尺寸图(2)管道方位图(3)部分零件结构图一概述1.精馏操作对塔设备的要求和类型㈠对塔设备的要求精馏所进行的是气(汽)、液两相之间的传质,而作为气(汽)、液两相传质所用的塔设备,首先必须要能使气(汽)、液两相得到充分的接触,以达到较高的传质效率。
但是,为了满足工业生产和需要,塔设备还得具备下列各种基本要求:⑴气(汽)、液处理量大,即生产能力大时,仍不致发生大量的雾沫夹带、拦液或液泛等破坏操作的现象。
⑵操作稳定,弹性大,即当塔设备的气(汽)、液负荷有较大范围的变动时,仍能在较高的传质效率下进行稳定的操作并应保证长期连续操作所必须具有的可靠性。
⑶流体流动的阻力小,即流体流经塔设备的压力降小,这将大大节省动力消耗,从而降低操作费用。
对于减压精馏操作,过大的压力降还将使整个系统无法维持必要的真空度,最终破坏物系的操作。
⑷结构简单,材料耗用量小,制造和安装容易。
⑸耐腐蚀和不易堵塞,方便操作、调节和检修。
⑹塔内的滞留量要小。
实际上,任何塔设备都难以满足上述所有要求,且上述要求中有些也是互相矛盾的。
不同的塔型各有某些独特的优点,设计时应根据物系性质和具体要求,抓住主要矛盾,进行选型。
㈡板式塔类型气-液传质设备主要分为板式塔和填料塔两大类。
精馏操作既可采用板式塔,也可采用填料塔,板式塔为逐级接触型气-液传质设备,其种类繁多,根据塔板上气-液接触元件的不同,可分为泡罩塔、浮阀塔、筛板塔、穿流多孔板塔、舌形塔、浮动舌形塔和浮动喷射塔等多种。
板式塔在工业上最早使用的是泡罩塔(1813年)、筛板塔(1832年),其后,特别是在本世纪五十年代以后,随着石油、化学工业生产的迅速发展,相继出现了大批新型塔板,如S型板、浮阀塔板、多降液管筛板、舌形塔板、穿流式波纹塔板、浮动喷射塔板及角钢塔板等。
目前从国内外实际使用情况看,主要的塔板类型为浮阀塔、筛板塔及泡罩塔,而前两者使用尤为广泛。
筛板塔也是传质过程常用的塔设备,它的主要优点有:⑴结构比浮阀塔更简单,易于加工,造价约为泡罩塔的60%,为浮阀塔的80%左右。
⑵处理能力大,比同塔径的泡罩塔可增加10~15%。
⑶塔板效率高,比泡罩塔高15%左右。
⑷压降较低,每板压力比泡罩塔约低30%左右。
筛板塔的缺点是:⑴塔板安装的水平度要求较高,否则气液接触不匀。
⑵操作弹性较小(约2~3)。
⑶小孔筛板容易堵塞。
2.精馏塔的设计步骤本设计按以下几个阶段进行:⑴设计方案确定和说明。
根据给定任务,对精馏装置的流程、操作条件、主要设备型式及其材质的选取等进行论述。
⑵蒸馏塔的工艺计算,确定塔高和塔径。
⑶塔板设计:计算塔板各主要工艺尺寸,进行流体力学校核计算。
接管尺寸、泵等,并画出塔的操作性能图。
⑷管路及附属设备的计算与选型,如再沸器、冷凝器。
⑸抄写说明书。
⑹绘制精馏装置工艺流程图和精馏塔的设备图。
本设计任务为分离醇和水的混合物,对于二元混合物的分离,应采用连续常压精馏流程。
设计中采用泡点进料,将原料液通过预热器加热至泡点后送入精馏塔内。
塔顶上升蒸气采用全凝器冷凝,冷凝液在泡点下一部分回流至塔内,其余部分经产品冷凝器冷却后送至贮罐。
该物系属于易分离物系,最小回流比比较小,故操作回流比取最小回流比的1.8倍。
塔底采用间接蒸气加热,塔底产品经冷却后送至贮罐。
二物料衡算1 ⑴原料液及其塔顶、塔底产品的摩尔分率甲醇的摩尔质量为:32kg/kmol水的摩尔质量为:18kg/kmolx f=0.2x d=0.995⑵原料液及其塔顶与塔底产品的平均摩尔质量M f=32×0.2+18×(1-0.2)=20.8kg/molM d=32×0.995+18×(1-0.995)=31.93kg/mol则可知:原料的处理量:F=10*1000/24/20.8=20kmol/h根据x d =0.995 x w=0.005由总物料衡算:F= D+W以及: x f×F= x d×D+W×x w容易得出:D=3.94kmol/hW=16.06kmol/h附:气液平衡图体系介绍2塔板数的确定⑴理论板层数N T的求取因为甲醇与水属于理想物系,可采用图解法求解(见相平衡图1---1)最小回流比及其操作回流比的求解:yδ=0.647,xδ=0.2Rmin=(x D-yδ)/(yδ-xδ)=(0.995-0.647)/(0.647-0.2)=0.16取操作回流比为:R=1.8Rmin=1.8×0.16=0.3a.精馏塔的气、液相负荷L=R×D=0.3×3.94=1.182kmol/hV=(R+1)×D=1.3×3.94=5.122kmol/hL’=L+F=1.182+20=21.182kmol/hV’=V=5.122kmol/hb.精馏段、提馏段操作线方程精馏段操作线:y=L/V×x+D/V×x d=0.231x+0.001提馏段操作线:y’=L’/V’×x’-W/V’×x w=4.135x’-0.016c.图解法求理论塔板层数根据图一所示,可求得结果为总理论塔板数N T为8块(包括再沸器)进料板位置N F为自塔顶数起第4块⑵理论板层数N T的求取精馏段实际塔板数N精=3/60%=5块提馏段实际塔板数N提=5/60%=9块三热量衡算1 原料预热器原料加热:采用压强为270.25kPa的水蒸汽加热,温度为130℃,冷凝温度至130℃流体形式采用逆流加热则Qm,h=50000×1000/(330×24)=6313.13 kj/(kg·K)同时有Cp,h,甲醇=2.48 kj/(kg·K) C p,h,水=4.183 kj/(kg·K)质量分数x F=0.40根据上式可知:C p c=2.48×0.4+4.138×0.6=3.502kj/(kg·K)设加热原料温度由10℃到85℃则有:φ= Qm,h×c p,c×ΔT=6313.13×3.502×75=1.658×106 kj/h选择传热系数K=800 w/(m2·K)则传热面积由下列公式计算:A=φ/(K×ΔTm)其中ΔTm=(ΔT1-ΔT2)/ln(ΔT1/ΔT2)=76.49 K 故有:A=φ/(K×ΔTm)= 27.20 m2取安全系数为0.8 则A实际=27.20/0.8=33.87 m2选择固定管板式换热器系列,规格为:2 塔顶全凝器甲醇的气化热r⑹Qc=(R+1)D×r=(1.130+1)×(89.02×30.38/3600)×1101= 1758.85kg/h冷凝塔顶产品由温度67.0℃冷却到温度40℃采用冷凝水由20℃到40℃知道ΔTm=(ΔT1-ΔT2)/ln(ΔT1/ΔT2)=23.33 K选择K=800w/( m2·K) 则有:A= Qc /(K×ΔTm)= 94.24m2取安全系数为0.8实际面积A=94.24/0.8=117.80 m2选择冷凝器的系列:3.塔底再沸器Qc=V’w r=(189.61×2258×18.02)=2143.8kg/h塔釜产品由温度103.2℃加热到温度130℃ΔTm=130.0-103.2=26.8K选择K=1000w/( m2·K) 则有:A= Qc /(K×ΔTm)=78.00 m2取安全系数为0.8 则有24产品冷却器假设产品从67.0℃冷却到40℃时冷却水从进口温度15℃到40℃时CH3OH :Cp,c=2.48 Kj/kg KH2O :Cp,c=4.183 Kj/kg Kφ=Qm,c Cp,c △T=89.02×30.38×2.48×(67-40)=1.811×105kj/h取K=600 w/( m2·K)A=φ/K△Tm=(1.811×105×1000)/(600×26.0×3600)=3.22 m2取安全系数为0.8 则2四工艺设计计算1 塔体工艺尺寸计算⑴由上面可知精馏段L=1.182kmol/hV=5.122kmol/ha . 塔径的计算 精馏段的气、液相体积流率为V S =VM Vm /3600ρVm =(1.182×28.405)/(3600×1.01)=0.092m 3/sL S =LM Lm /3600ρLm =(5.122×24.655)/(3600×819.1)=0.000428m 3/smax L V Vu Cρρρ-=式中,负荷因子2.020)02.0(σC C =由史密斯关联图⑶查得C 20再求图的横坐标为 F lv =L/V×(ρl /ρv )0.5=0.0162取板间距,H T =0.40m,板上清液层高度取h L =0.05m ,则H T -h L =0.35 m史密斯关联图如下由上面史密斯关联图,得知 C 20=0.075 气体负荷因子 C= C 20×(σ/20)0.2=0.08526 U max =2.43取安全系数为0.8,则空塔气速为 U=0.8U max =0.8×2.43=1.94m/suVD 785.0/==0.986m按标准塔径圆整后为D=1.0m 塔截面积为At=3.14×1×1=0.785 m 2实际空塔气速为U 实际=1.481/0.785=1.887 m/sU 实际/ U max =1.887/2.43=0.78(安全系数在充许的范围内,符全设计要求)⑵ 由上面可知提馏段 L=21.182kmol/hV=5.122kmol/ha .提馏段塔径的计算 提馏段的气、液相体积流率为V ’S =V ’M Vm /3600ρ’Vm =(5.122×22.26)/(3600×0.80)=0.04m 3/sL ’S =L ’M Lm /3600ρ’Lm =(21.182×19.56)/(3600×915.6)=0.00013m 3/smax u =2.020)02.0(σC C =由史密斯关联图⑶查得C 20再求图的横坐标为 F lv =L/V×(ρl /ρv )0.5=0.051取板间距,H T =0.40m ,板上清液层高度取h L =0.06m ,则H T -h L =0.34 m 由史密斯关联图,得知 C 20=0.076 气体负荷因子 C= C 20×(σ/20)0.2=0.093 U max =3.14m/s取安全系数为0.7,则空塔气速为 U=0.7U max =0.7×3.14=2.20m/suVD 785.0/==0.921m按标准塔径圆整后为D=1.0m 塔截面积为At=3.14×1×1=0.785 m 2实际空塔气速为U 实际=1.466/0.785=1.868 m/sU 实际/ U max =1.868/3.14=0.59(安全系数在充许的范围内,符全设计要求) ⑶ 精馏塔有效高度的计算精馏段有效高度为 Z 精=(N 精-1)H T =(5-1)×0.40=1.6 m 提馏段有效高度为 Z 提=(N 提-1)H T =(9-1)×0.40=3.2 m 在进料板上方开一个人孔,其高度为0.8 m故精馏塔有效高度为Z=Z 精+Z 提+0.5=1.6+3.2+0.8=5.6m2 塔板主要工艺尺寸的计算⑴ 精馏段 a .溢流装置计算 因塔径 D=1.0m ,所以可选取单溢流弓形降液管,采用凹形受液盘。