型腔加工工艺规程
6、型腔铣削加工

O0002; G90 G94 G21 G17 G54; G00 X-10. Y0.; Z20.; M03 S600; G01 Z-4. F60; G41 G01 Y7. D02; G03 X-17. Y0. R7.; G01 Y-10.; G03 X-10. Y-17. R7.; G01 X10.; G03 X17. Y-10. R7.; G01 Y10.; G03 X10. Y17. R7.; G01 X-10.; G03 X-17. Y10. R7.; G01 Y0.; G03 X-10. Y-7. R7.; G40 G01 Y0.; G28 Z20.; M30;
Y83.5; X74.5; Y95.5; X25.5; Y107.5; X74.5; X70.Y114.5; X25.5; G00Z20.; M30;
8 7
9
10
1
0 11
2
3 6
R4
5
4
O0002; G90 G94 G21 G17 G54; G00 X70. Y70.; 1、(70,85) Z20.; 2、(85,70) M03 S600; G01 Z-5. F100; 3、(85,35) G42 G01 Y85. D02; 4、(65,15) G02 X85. Y70. R15.; 5、(19,15) G01 Y35.; 6、(15,19) G02 X65. Y15. R20.; 7、(15,121) G01 X19.; 8、(19,125) G02 X15. Y19. R4.; G01 Y121.; 9、(65,125) G02 X19. Y125. R4.; 10、(85,105) G01 X65.; 11、(70,55) G02 X85. Y105. R20.; G01 Y70.; G02 X70. Y55. R15.; G40 G01 Y70.; G00 Z20.; M30;
型腔加工工艺

江门职业技术学院学生毕业论文(设计)论文题目:型腔的加工工艺作者:指导教师:所学专业:数控加工与维护班别:学号:年级:完成日期:目录(一)绪论----------------------- 11.1数控加工在机械制造业中的地位和作用--11.2数控加工的工作原理----------------1 1.3数控实际加工中需要注意的问题-------- 1.4 数控加工工艺内容-------------21.5数控加工零件工艺设计1.6典型铣削零件数控加工工艺设计---------------(二)工艺分析与选择-------2.1零件图工艺分析---------------- --2.2确定装夹方案--------------------2.3确定加工顺序-----------------------------2.4刀具选择--------------------------------2.5切削用量选择-----------------------------(三) 主要操作步骤及加工程序3.1确定编程原点3.2按工序编制各部分加工程序(四)小结 ------(一)绪论1.1 数控加工在机械制造业中的地位和作用随着科学技术的发展,机械产品结构越来越合理,其性能、精度和效率日趋提高,更新换代频繁,生产类型由大批量生产向多品种小批量生产转化。
因此,对机械产品的加工相应地提出了高精度、高柔性与高自动化的要求。
随着计算机技术的高速发展,传统的制造业开始了根本性变革,各工业发达国家投入巨资,对现代制造技术进行研究开发,提出了全新的制造模式。
在机械产品中,单件与小批量产品占到70%~80%,这类产品一般都采用通用机床加工,当产品改变时机床与工艺装备均需作相应的变换与调整,而且通用机床的自动化程度不高,基本上由人工操作,难以保证生产效率与产品质量。
特别是一些曲线、曲面轮廓组成的复杂零件,只能借助靠模和仿形机床,或者借助划线或样板用手工操作的方法来加工,加工精度和生产效率受到很大的限制。
注塑模具型腔的电火花加工工艺基本规程操作有哪些?
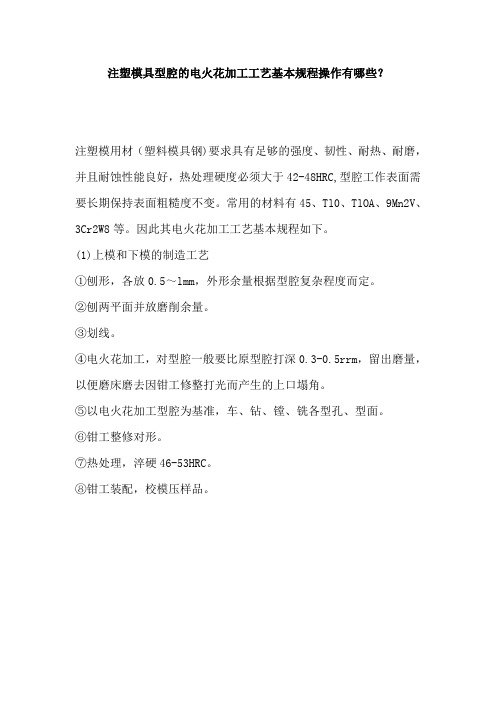
注塑模具型腔的电火花加工工艺基本规程操作有哪些?注塑模用材(塑料模具钢)要求具有足够的强度、韧性、耐热、耐磨,并且耐蚀性能良好,热处理硬度必须大于42-48HRC,型腔工作表面需要长期保持表面粗糙度不变。
常用的材料有45、Tl0、TlOA、9Mn2V、3Cr2W8等。
因此其电火花加工工艺基本规程如下。
(1)上模和下模的制造工艺①刨形,各放0.5~lmm,外形余量根据型腔复杂程度而定。
②刨两平面并放磨削余量。
③划线。
④电火花加工,对型腔一般要比原型腔打深0.3-0.5rrm,留出磨量,以便磨床磨去因钳工修整打光而产生的上口塌角。
⑤以电火花加工型腔为基准,车、钻、镗、铣各型孔、型面。
⑥钳工整修对形。
⑦热处理,淬硬46-53HRC。
⑧钳工装配,校模压样品。
电极材料可选用高纯细石墨、紫铜和钨铜等。
(2)电极制造工艺石墨在加工前应预处理,在油里浸透好,这样,在机械加工时,石墨屑不易飞扬,清角线和棱角线不易剥落。
石墨和紫铜电极采用一般的机械加工(车、铣、刨、磨等,必要时采用数控机床加工),最后钳工修整成形。
紫铜屯极还可采用线切割加工。
对于形状比较简单的型腔,多数采用单电极成形工艺,即采用一个电极,借助平动扩大间隙,达到修光型腔的目的。
单电极可以是独块电极,也可以是镶拼电极,这由电极加工工艺而定。
对于大中型及型腔复杂的模具,可以采用多电极加工,各个砲极可以是独块的,也可以是镶拼的,视具体情况而定。
(3)电火花加工型腔模(上模或下模)一般先加工外形,再以电火花加工后的型腔为基准加工其他型孔,这样对于电火花加工操作者来说,找准定位还是比较方便的。
但也不是一概如此,有些模具涉及许多因素,最后一道工序是电火花加工,这就对电火花加工的定位、装夹、加工等有更高的要求。
在模具加工中要用到电火花加工的地方是非常多的,因为电火花加工的速度较慢,所以在模具加工可以用切削加工的地方尽量用切削加工来加工,切削加工不到的地方才用电火花机来加工。
带型腔的凸台零件的数控加工工艺

带型腔的凸台零件的数控加工工艺如图所示,材料为45钢,单件生产,毛坯尺寸为84mm×84mm×22mm),试对该零件的顶面和内外轮廓进行数控铣削加工工艺分析。
零件图一、零件图工艺分析1)加工内容该零件主要由平面、孔系、型腔轮廓及外圆弧轮廓组成,几何元素之间关系描述清楚完整,尺寸标注完整。
毛坯是长方体块件,尺寸为84mm×84mm×22mm,加工内容包括ø22H8的内孔,外圆弧轮廓,型腔轮廓,四个平面(上表面、凸台面、型腔表面和下底面)和工件四周面。
2)加工要求零件主要加工要求为ø20H8的内孔的尺寸公差为H8,表面粗糙度要求较高,其值为Ra=1.6μm。
其他的加工要求只标注了公称尺寸,所以按自由尺寸公差等级为IT11~IT12级来加工,表面粗造度为Ra=3.2μm,表面质量要求一般。
3)各结构的加工方法①由于ø22H8的内孔加工要求较高,拟定钻中心孔-----钻孔-----粗镗-----半精镗-----精镗的加工方案。
②外圆弧轮廓以及平面和型腔轮廓以及平面可用键槽铣刀铣削,因为表面粗造度为Ra=3.2μm,故采用粗铣-----精铣的方法加工。
③底面、上表面和四周面可用面铣刀,因为表面粗造度为Ra=3.2μm,故也采用粗铣-----精铣的方法加工。
零件毛坯为45钢,切削性能好,无热处理和硬度要求。
二、选择设备根据被加工零件的外形和材料等特点,选用XK713A型数控铣床。
技术参数XK713A床身型数控铣床工作台工作台面积800x350 mm T形槽3x18H8 mm 工作台最大承重550 kg行程X向、Y向、Z向行程600x410x510 mm 主轴端面至工作台面距离126-635 mm 主轴中心至立柱导轨面距离215-625 mm主轴主轴转速60-4000(8000可选) rpm 主轴电机功率(连续/30分) 5.5/7.5 kw 主轴孔锥度BT-40 -三向进给切削进给速度1-5000 mm/min 快速移动速度15000 mm/min 进给电机扭矩12 Nm精度定位精度±0.013 mm 重复定位精度±0.005 mm电机进给电机容量主轴电机 5.5/7.5 kw X、Y向0.9 kw Z向 1.8 kw一般规格机床外形尺寸(长x宽x高)2500x2630x2550 mm 机床重量4500 kg 总电源供应量15 kw 典型配用数控系统FANUC Oi -XK713A型数控铣床技术参数三、确定零件的定位基准和装夹方式1)定位基准根据基准重合的原理选取零件的底面做为定位基准,保证设计基准与定位基准重合。
17.型腔的机械加工
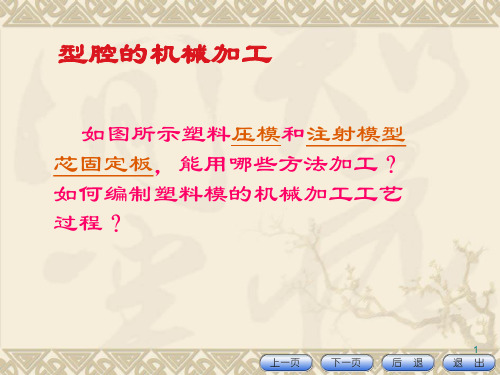
如图所示塑料压模和注射模型 芯固定板,能用哪些方法加工? 如何编制塑料模的机械加工工艺 过程?
1
型腔的机械加工
1.圆形型腔
1)当型腔形状不大时,可将型腔装夹在车床四爪单动卡盘或花 盘上进行车削加工。 2)采用立式铣床配合回转式夹具进行铣削加工。 3)采用数控铣削或加工中心进行铣削加工。 4)淬火后可在内圆磨床上或电火花机床上完成精加工。 2.矩形型腔
图3.65对拼式塑压模型腔
分 型面
8
15
A
A' 15
20
B
20
B'
23
型腔的机械加工
表1 型腔的机械(用普通机床)加工工艺过程(图2.15 、 图2.66 、 图2.67 表2.15 -1 表2.15 -2) 工序号 工序名称
备料 热处理
工序内容
按尺寸125 × 130 ×210 mm锻造毛坯 预硬30~32HRC
型 腔 的 铣 削 加 工
③ R14 mm 到R26mm中心的距离60.78mm;
④ 两R40mm圆心的距离36mm;
① 加工出一个R14mm的圆弧槽; ② 取走61mm的块规,铣削出另一个圆弧 槽。
铣削过程
③ 垫入30.5mm和60.78mm的块规,移动 工作台使铣刀和型腔圆弧槽对正。 ④ 垫入尺寸为96.78mm的块规。 ⑤ 铣削直线圆弧槽。
Ra 0.4
R4 0 +00.0 25
R a 0. 8
25
16
12
8
+ 0.0 18 0
4× M 8
4 ×φ 1 2
Ra 0.8
Ra 0.8
Ra 0.4 +0 .02 1 0 0 a0. R .4 4
单元七-型腔铣削的加工工艺与程序编程共17页文档

❖ 斜线下刀时刀具使用X/Y和Z方向的线性坡走切削,以达到全
部轴向深度的切削。
螺旋下刀
斜线下刀
❖ 2.走刀路线 ❖ (1)圆腔挖腔程序的编制
❖ 圆腔挖腔,一般从圆心开始,根据所用刀具,也可先预钻一孔, 以便进刀。挖腔加工多用立铣刀或键槽铣刀。
❖ (2)方腔挖腔程序的编制
❖ 方腔挖腔与圆腔挖腔相似,但走刀路径可有以下几种
任务实施
(一)工艺分析
❖ 根据零件的特点,选择φ10的键槽铣刀,Z方向采用垂直下刀的 进刀方式,在XY平面走刀路线为OH(建立刀补)→HI(切向 切入)→IJ→JK→KL→LM→MI→IN(切向切出)→NO(取 消刀补),由于表面精度要求不高Ra6.3,采用粗加工一次完成, 切削用量选择为:主轴转速1200r/min,进给速度为 50mm/min
❖ 2.型腔加工的工艺编制 ❖ 3.刀具的选用
任务导入
❖ 如图所示的零件, 已知材料为45#钢, 毛坯为100 mm×80 mm×22 mm,上表面和轮 廓四周都已加工完 毕(在前一个学习 情景),完成轮廓 铣削的工艺设计及 加工程序的编制)。
相关知识点
❖ (一)型腔铣削工艺设计 ❖ 1.挖槽和型腔加工中的进刀方式 ❖ 对于封闭型腔零件的加工,下刀方式主要有垂直下刀、螺旋下
学习情景七 型腔铣削的加工工艺与程序编程
学习目标及能力要求:
❖ 1. 能根据零件结构特点和技术要求,制订工艺方案并 编制符合技术规范的工艺文件
❖ 2.能正确编制平面型腔零件的数控加工程序 ❖ 3.能使用仿真系统进行程序效验 ❖ 4. 小组完成零件的加工、检测,并分析和思考考
主要学习内容
❖ 1.型腔加工的进刀方式,粗精 加工的走刀路线
型腔类零件设计及加工工艺分析-毕业设计-5
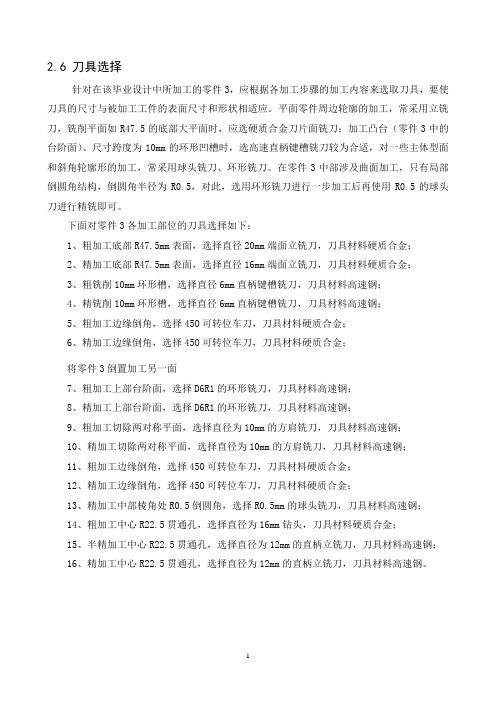
2.6 刀具选择针对在该毕业设计中所加工的零件3,应根据各加工步骤的加工内容来选取刀具,要使刀具的尺寸与被加工工件的表面尺寸和形状相适应。
平面零件周边轮廓的加工,常采用立铣刀,铣削平面如R47.5的底部大平面时,应选硬质合金刀片面铣刀;加工凸台(零件3中的台阶面)、尺寸跨度为10mm的环形凹槽时,选高速直柄键槽铣刀较为合适,对一些主体型面和斜角轮廓形的加工,常采用球头铣刀、环形铣刀。
在零件3中部涉及曲面加工,只有局部倒圆角结构,倒圆角半径为R0.5,对此,选用环形铣刀进行一步加工后再使用R0.5的球头刀进行精铣即可。
下面对零件3各加工部位的刀具选择如下:1、粗加工底部R47.5mm表面,选择直径20mm端面立铣刀,刀具材料硬质合金;2、精加工底部R47.5mm表面,选择直径16mm端面立铣刀,刀具材料硬质合金;3、粗铣削10mm环形槽,选择直径6mm直柄键槽铣刀,刀具材料高速钢;4、精铣削10mm环形槽,选择直径6mm直柄键槽铣刀,刀具材料高速钢;5、粗加工边缘倒角,选择45O可转位车刀,刀具材料硬质合金;6、精加工边缘倒角,选择45O可转位车刀,刀具材料硬质合金;将零件3倒置加工另一面7、粗加工上部台阶面,选择D6R1的环形铣刀,刀具材料高速钢;8、精加工上部台阶面,选择D6R1的环形铣刀,刀具材料高速钢;9、粗加工切除两对称平面,选择直径为10mm的方肩铣刀,刀具材料高速钢;10、精加工切除两对称平面,选择直径为10mm的方肩铣刀,刀具材料高速钢;11、粗加工边缘倒角,选择45O可转位车刀,刀具材料硬质合金;12、精加工边缘倒角,选择45O可转位车刀,刀具材料硬质合金;13、精加工中部棱角处R0.5倒圆角,选择R0.5mm的球头铣刀,刀具材料高速钢;14、粗加工中心R22.5贯通孔,选择直径为16mm钻头,刀具材料硬质合金;15、半精加工中心R22.5贯通孔,选择直径为12mm的直柄立铣刀,刀具材料高速钢;16、精加工中心R22.5贯通孔,选择直径为12mm的直柄立铣刀,刀具材料高速钢。
型腔加工工艺规程
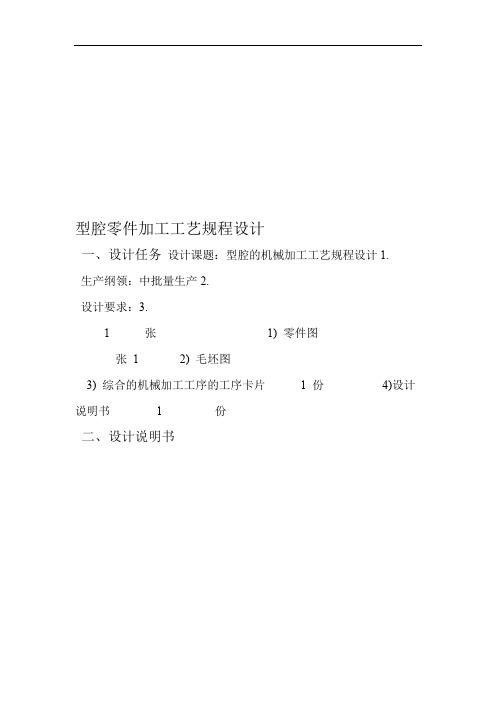
型腔零件加工工艺规程设计一、设计任务设计课题:型腔的机械加工工艺规程设计1.生产纲领:中批量生产2.设计要求:3.1 张1)零件图张1 2)毛坯图3)综合的机械加工工序的工序卡片 1 份4)设计说明书 1 份二、设计说明书言序机械制造工艺学课程设计是我们学完了大学的大部分基础课和这是我们在进行毕业设计之专业课之后进行的一门综合的课程设计。
前对所学课程的一次深入的综合性的复习。
了解并认识一般机器零件的生产工我希望能通过这次课程设计,理论联系巩固和加深已学过的技术基础课和专业课的知识,艺过程,实际,从中锻炼自己分析问题、解决问题的能力,为后续课程的学习打下良好的基础。
一、零件的分析(一)零件的作用型腔。
毛坯由石蜡铸造而成(二)零件的工艺分析35mm、10mm、5mm三个尺寸是以B面为设计基准,100mm、90mm、80mm、60mm则是以原点O为设计基准。
型腔有两组加工表面,他们之间有一定的位置要求。
现分述如下:1、以100*100面为基准的加工表面这一组加工表面包括:四个尺寸100*30mm的与基面相垂直的平面,的凸台40*35mm的凹槽以及80*80mm的平面,90*90mm2、4*10深的孔?这两组加工表面之间有着一定的位置要求,主要是:0.02560±10的两孔之间的位置要求是?可以先加工其中一组表面,对于两组加工表面而言,由以上分析可知,然后借助于专用夹具加工另一组表面,并且保证他们的位置精度要求。
工艺规程设计二、(一)确定生产类型已知此零件的生产类型为中批量生产,所以初步确定工艺安排为:在加工过程划分阶段,工序应适当集中,机床设备可采用专用设备,但以使用通用设备为主。
确定毛坯的制造形式(二)石蜡不能承受,材料为石蜡,由于零件毛坯尺寸不大,形状简单力矩,所以要选铸件做为毛胚,铸件可以一次性成型,适合石蜡这种且零件属于中批量生产,故可采用铸造成型,精加材质材料的加工,工采用铣削。
这从提高生产、保证加工精度上考虑,也是应该的(三)基面的选择对于保证零件的尺寸和位置精度有着决定合理地选择定位基准,基面选择的基面选择是工艺规程设计中的重要工作之一。
- 1、下载文档前请自行甄别文档内容的完整性,平台不提供额外的编辑、内容补充、找答案等附加服务。
- 2、"仅部分预览"的文档,不可在线预览部分如存在完整性等问题,可反馈申请退款(可完整预览的文档不适用该条件!)。
- 3、如文档侵犯您的权益,请联系客服反馈,我们会尽快为您处理(人工客服工作时间:9:00-18:30)。
型腔零件加工工艺规程设计一、设计任务1.设计课题:型腔的机械加工工艺规程设计2.生产纲领:中批量生产3.设计要求:1)零件图1张2)毛坯图1张3)综合的机械加工工序的工序卡片1份4)设计说明书1份二、设计说明书序言机械制造工艺学课程设计是我们学完了大学的大部分基础课和专业课之后进行的一门综合的课程设计。
这是我们在进行毕业设计之前对所学课程的一次深入的综合性的复习。
我希望能通过这次课程设计,了解并认识一般机器零件的生产工艺过程,巩固和加深已学过的技术基础课和专业课的知识,理论联系实际,从中锻炼自己分析问题、解决问题的能力,为后续课程的学习打下良好的基础。
一、零件的分析(一)零件的作用型腔。
毛坯由石蜡铸造而成(二)零件的工艺分析35mm、10mm、5mm三个尺寸是以B面为设计基准,100mm、90mm、80mm、60mm则是以原点O为设计基准。
型腔有两组加工表面,他们之间有一定的位置要求。
现分述如下:1、以100*100面为基准的加工表面这一组加工表面包括:四个尺寸100*30mm的与基面相垂直的平面,90*90mm的平面,80*80mm的凹槽以及40*35mm的凸台2、4*φ10深的孔这两组加工表面之间有着一定的位置要求,主要是:φ10的两孔之间的位置要求是60±0.025由以上分析可知,对于两组加工表面而言,可以先加工其中一组表面,然后借助于专用夹具加工另一组表面,并且保证他们的位置精度要求。
二、工艺规程设计(一)确定生产类型已知此零件的生产类型为中批量生产,所以初步确定工艺安排为:在加工过程划分阶段,工序应适当集中,机床设备可采用专用设备,但以使用通用设备为主。
(二)确定毛坯的制造形式材料为石蜡,由于零件毛坯尺寸不大,形状简单,石蜡不能承受力矩,所以要选铸件做为毛胚,铸件可以一次性成型,适合石蜡这种材质材料的加工,且零件属于中批量生产,故可采用铸造成型,精加工采用铣削。
这从提高生产、保证加工精度上考虑,也是应该的(三)基面的选择合理地选择定位基准,对于保证零件的尺寸和位置精度有着决定性的作用。
基面选择是工艺规程设计中的重要工作之一。
基面选择的正确与合理,可以使加工质量得到保证,生产率得以提高。
否则,加工工艺过程会问题百出,更有甚者,还会造成零件大批报废,使生产无法正常进行。
粗基准的选择:在选择粗基准时,考虑的重点是如何保证各加工表面有足够多的余量,及保证不加工表面与加工表面间的尺寸,位置符合零件图样设计要求。
粗基准的选择原则:1、保证不加工表面与加工表面相互位置要求原则。
当有些不加工表面与加工表面之间有相互位置要求时,一般不选择加工表面作为粗基准。
2、保证各加工表面的加工余量合理分配的原则。
应选择重要加工表面为粗基准。
3、粗基准不重复使用的原则。
粗基准的精度低,粗糙度数值大,重复使用会造成较大的定位误差,因此,同一尺寸方向的粗基准,通常只允许使用一次。
现选取顶平面作为粗基准,利用顶平面作主要定位面,以消除三个自由度,再用虎台钳装夹工件,用以消除另外三个自由度,达到完全定位。
精基准的选择:精基准的选择原则主要考虑如何减少误差,保证加工精度和安装方便以及以及设计基准和工序基准重合问题。
当二者不重合时,应该进行换算。
1、基准重合原则:应尽可能选择零件的设计基准作为定位基准,以避免产生基准不重合原则。
2、基准统一原则:应尽可能选用精基准定位加工各表面,以保证各表面之间的位置精度。
3、自为基准原则:有些精加工或光整加工工序要求加工余量小而均匀,应选择加工表面为精基准。
4、互为基准反复加工原则:有些相互位置精度要求较高的表面,可以采用互为基准反复加工的原则来保证5、定位可靠性原则:精基准应凭整光洁,具有相应的精度,确保定位简单准确,便于安装,夹紧可靠。
考虑保证零件的加工精度和装夹准确方便,依据“基准统一和基准重合”原则,以粗加工后的底平面为精基准。
第一道工序一般只能以为加工的毛坯面作为定位基准,这种基准称为粗基准。
此零件以一个A面作为定位基准,铣削出定位粗基准。
然后翻转装夹,再以这个粗基准作为定位基准加工上端面即B面。
然后加工侧面,将一个加工过的侧面作为精基准,加工零件的最大外轮廓。
在第一道工序之后,根据基准统一原则,纵向铣削应使尽量多的表面加工时都用已加工的上端面作为定位基准,加工型腔、梯台面、ø10孔。
横向的铣削都以加工过的侧面作为定位基准。
以保证各加工面的位置精度。
(一)制定工艺路线制定工艺路线的出发点,应当是使零件的几何形状、尺寸精度及位置精度等技术要求能得到合理的保证,在生产纲领已确定的情况下,可以考虑采用万能性机床配以专用工夹具,并尽量使工序集中来提高生产率。
除此之外,还应当考虑经济效果,以便使生产成本尽量下降。
1、工艺路线方案一工序1 铣基准面。
粗、精铣削A面作为定位粗基准面,见平即可。
工序2 第二次装夹,粗、精铣削上端面即B面,将上端面作为纵向加工的定位基准,保证厚度尺寸35mm。
工序3 加工两个未被装夹的侧面,以其中一个侧面作为横向加工的定位基准,加工零件的外轮廓。
工序4 铣台阶面型腔轮廓,沿型腔轮轨迹铣削出型腔的轨迹,保证尺寸和精度要求。
工序5 以底平面定位并夹紧工件,采用划线找正,钻4×φ10mm×15mm的孔,保证两孔中心的距离为60±0.025mm。
工序6 检验。
2、工艺路线方案二工序1铣基准面。
粗、精铣削A面作为定位粗基准面,见平即可。
工序2第二次装夹,粗、精铣削上端面即B面。
粗、精型腔轮廓,沿型腔轨迹铣削出型腔的轨迹,保证尺寸和精度要求。
工序3粗精铣、台阶面、周铣四个侧面,保证尺寸和精度要求。
工序4以底平面定位并夹紧工件,采用划线找正,钻4×φ10mm×15mm的孔,保证两孔中心的距离为60±0.025mm。
工序5检验。
(二)工艺方案的比较与分析两个工艺路线的分析:相比工艺路线方案一,工艺路线方案二只采用数控铣床和钻床就可实现凹件的完全加工,而且工艺路线方案二的工序更少,因而能提高生产效率,节约成本。
因此选用工艺路线方案二。
(三)机械加工余量、工序尺寸及毛坯尺寸的确定零件材料为石蜡,毛坯重量约为318克,生产类型为中批量生产,采用铸造成型的毛坯。
根据上述原始资料及加工工艺,分别确定各加工表面的机械加工余量、工序尺寸及毛坯尺寸如下:1、表1 型腔厚度的加工余量、工序尺寸及毛坯尺寸表表2 型腔长度、宽度的加工余量、工序尺寸及毛坯尺寸表(四)确定切削用量及基本工时加工条件:XK713A数控铣床,一把YT15面铣刀,刀盘直径125mm,宽20mm,齿数20,通用夹具,0~200、0.2mm 游标卡尺,柴油冷却。
a.确定背吃刀量端面的总加工余量为4mm,由毛坯图已知铣削宽度为a e=106mm,两次走刀加工,a p=2mm.b. 确定进给量及基本工时根据《工艺手册》中表4.2-38,XK713A数控铣床,刀杆直径为22mm,再查《切削手册》表3.15和《工艺手册》表4.2-38可得,我们可以取进给量f=0.10mm/z。
c.计算切削速度根据《切削手册》表3.27可得,C v=186mm, q v=0.2, y v=0.4, u v=0.2, m=0.2, x v=0.1,P v=0,修正系数k v=1.1,选择刀具使用寿命T=60min.v c= C v d qv k v /(T m a p xv f yv a e uv z Pv) =186×1250.2×1.1/(600.2×20.1×0.10.4×600.2×200) ≈4.87m/min.d.确定铣床主轴转速n w=1000v c/(π×d w)=1000×4.87/(3.14×22)≈70.51r/min 根据《工艺手册》表4.2-39,与70.51r/min相近的转速为75r/min。
现选择n w=75r/min.所以实际切削速度为v=5 m/min.e.计算基本时间按《工艺手册》表6.2-7,l=106mm,l10.5(d=+(1~3) =32mm.l 2=2mm.时间t=12Mzl l l f ++=140/150=0.93min ,取时间t=56s 。
因为分两次加工,所以切削时间T=2×56s=112s工序2用数控铣床以底平面为精基准半精铣顶平面,保证其厚度尺寸为35mm 。
然后加工四周、凹槽,保证其尺寸要求和精度要求。
在工序2的半精加工中,端面的总加工余量为2mm ,由毛坯图已知铣削宽度为a e =106mm ,两次走刀加工,a p =1mm 。
基本加工时间的算法同上。
工序4 以底平面定位并夹紧工件,钻4×φ10mm ×15mm 的孔,保证两孔中心的距离为60±0.025mm 。
加工条件:Z515钻床,Φ10mm 标准锥柄麻花钻,通用夹具,0~200、0.2mm 游标卡尺,柴油冷却。
a.确定进给量根据《切削手册》表2.7,f=1.0~1.2,查《工艺手册》4.2-16,根据机床实际进给量取f=0.12mm/rb.选择钻头磨钝标准及耐用度根据《切削手册》表2.12可得,钻头后刀面的最大磨损限度为0.8~1.2mm,使用寿命为70min.c.计算切削速度根据《切削手册》表2.30,C v =4.8, z v =0.4, x v =0, y v =0.7,m=0.2, 表2,31得,修正系数k v =1.0.v c =C v d 0zv k v /(T m a p xv f yv )=4.8×39× 1.0/(700.2×19.50×0.120.7)≈18m/minn v =1000v c /(πd w )=1000×18/(3.14×39)≈147r/min根据《工艺手册》表4.2-15,按机床实际钻速选取n w =125r/min,则实际切削速度为v=15m/min.e.计算基本时间按《工艺手册》表6.2-7,l =15mm,1cot (1~2)2r D l κ=+=1~2mm ,r κ=90。
,取l 1=2mm. l 2=3mm.时间t=12w l l l n f++=20/15=1.33min ,取时间t=80s 。
因为要加工4个孔,所以切削时间T=4×80s=320s最后,将以上各工序的切削用量、工时定额的计算结果,连同其他加工数据,一并填入机械加工工艺过程综合卡片。
参考文献1、赵家奇主编,机械制造工艺学课程设计指导书,机械工业出版社,2006年.2、王先逵主编,机械制工艺学,机械工业出版社,2011年.3、卢秉恒主编,机械制造技术基础,机械工业出版社,2011年.4、肖诗纲主编,切削用量手册,机械工业出版社,1993年.5、邹青主编,机械制造技术基础课程设计指导教程,机械工业出版社,2009年-6、陈宏钧万向明主编,典型零件机械加工生产实例,机械工业出版社,2010年7、马宏伟主编,数控技术,电子工业出版社,2011年8、王伯平主编,互换性与测量技术基础。