气烧辊道窑余热发电技术方案
燃气辊道窑

50M燃气辊道窑方案第一部分技术设计说明气烧辊道窑,是我公司在消化吸收国内外窑炉技术的基础上,自行开发设计的新一代组装式窑炉,具有烧成周期短、能耗低、燃料成本少、自动化程度高等一系列优点。
在本项目技术方案设计中,我们结合近年来所接触到的国内外窑炉的先进技术及实用成功经验,将从烧成车间的工艺布置、窑炉的设计、种类设备选型及关键材料的选用等方面进行详细描述。
一、辊道窑主要技术参数序号项目单位指标备注1 产品50M辊道窑含入窑平台2M、出窑平台3M2 质量国家现行产品标准3 产品规格mm4 年产量件万件5 产品合格率% ≥986 产品优等率% ≥907 烧成周期小时4-5小时可调8 烧成温度℃≤1250℃设计温度1400℃9 单位制品热耗900kal/kg10 燃料发生炉煤气11 燃料热值≥1250kal/m312 总热耗≥1760 m3/小时13 窑有效长度M 4514 窑外有效尺寸M/M 45000L*3000W*2500H 不包含平台尺寸15 主控制柜尺寸M/M 3600L*800W*2200H14 窑体单元节1515 单元长度M 316 窑内宽M 1.4 产品宽1.217 窑内高M/M 420 产品高330mm18 进料台M 219 出料台M 320 辊棒间距mm 10021 辊棒规格mm ф6022 棍棒数量根45023 烧咀数量支4824 温度监测点点16第二部分分部功能描述一、烧成辊道窑及附属设备功能描述1、全窑共设15节单元箱体2、其中:预热带4节长12M烧成带6节长18M急冷带1节长3M冷却带3节长9M最后冷却带1节长3M采用较长的烧成区域,更适合满足烧制不同的产品以达到快速烧成的目的。
2、采用不同型号的方钢管制成窑体骨架,箱式吊顶结构,外墙装饰烤漆板。
(烤漆颜色可根据客户要求选择)。
窑体其它结构示意图1—事故处理孔2—陶瓷辊棒3—烧咀4—观察孔5—热电偶 6 —挡火墙7—挡火板8—热电偶3、窑炉传动装置包括调速电机、传动轴、斜齿轮、辊棒等装置,主传动采用45°斜齿轮分节传动,轴承固定方式为单联体。
余热发电工程施工方案

余热发电工程施工方案一、项目背景余热发电是一种利用工业生产中产生的废热来发电的技术,通过有效利用工业生产中的余热,可以减少能源浪费,降低生产成本,同时也对环境起到一定的净化作用,因此备受行业关注。
本次余热发电工程项目位于某家大型钢铁厂,该厂生产废热丰富,且经过初步分析与评估,满足余热发电的基本条件。
该项目计划利用工厂产生的高温废气进行余热发电,项目规模较大,设计总装机容量为10000KW,属于较为复杂的余热发电工程。
为了确保工程施工能够顺利进行,特制定本施工方案。
二、总体设计思路1. 技术选型根据该钢铁厂的实际情况,本项目拟采用直接循环余热发电技术,通过余热锅炉与汽轮发电机组的结合,实现废热的有效利用。
此外,还将采用先进的数控系统进行监控与管理,以确保工程运行安全稳定。
2. 工程施工方案本项目总体施工方案分为以下几个步骤:(1)前期准备首先,需要对工程现场进行勘察和测量,了解施工环境以及场地情况;其次,进行工程设计评审和技术方案论证,确定最合适的施工方案;然后,编制施工组织设计方案和施工方案,确定施工队伍和施工计划等;最后,准备必要的施工材料和设备,确保施工可以有序进行。
(2)土建施工在完成前期准备之后,需要进行土建施工。
主要包括场地平整、基础施工、设备基础浇筑等工序。
在这个过程中,需要根据当地的气候和地质条件,科学合理地设计土建方案,并保证施工质量。
(3)设备安装土建施工完成后,需要进行设备安装工作。
这是整个工程中最为重要的一个环节,需要严格按照设备安装图纸和要求进行安装,确保设备的安全和正常运行。
(4)电气接线设备安装完成后,需要进行电气接线。
这是工程的最后一个环节,需要确保电气接线的质量和安全。
三、工程施工计划1. 工程施工周期该项目总投资较大,施工任务复杂,预计施工周期为12个月。
具体的施工周期安排如下:前期准备:1个月土建施工:3个月设备安装:4个月电气接线:2个月试运行与调试:2个月2. 施工队伍组织本项目施工队伍由总包施工队伍和分包施工队伍组成,总包施工队伍负责整体施工任务的协调和管理,分包施工队伍负责具体的施工任务的执行。
辊道窑尾冷段余热利用浅析

1 1 计 算依据 .
要计 算窑尾 余 热 的大 体 贮 量 , 须 确 定 一些 原 始 必 数 据 , 有这些 数据 , 没 根本 无法 计算 。
设定 : 某建 陶企 业 陶瓷砖 日产 量为 1 n , 万 f 单位 产
品质 量 为 2 g ; 0k / 测定 : 品 出 窑 在 缓 冷 段 、 尾 冷 段 时 的 温 度 为 产 进 2 0℃ ; 5 最终 出窑时 的温 度 为 10℃ ; 冷段 排 出 的空 5 尾
次性增加设备投 资 7 0 , 0元 年创效益 1.1 8 88 万元 。
关键 词 辊 道 窑 尾 冷 段 余 热 助 燃 风 经 济效 益
利用 价值 不大 , 这也许 是一 种误解 , 或者 是没有 找到合
前 言
在 陶瓷墙地 砖 生产 成 本 中 , 料成 本 所 占比重 是 燃 最大 的 , 电力 成 本所 占比重 仅 次于 原 料 排第 3位 。从 河南 省 的陶瓷 企业情 况来看 , 这两 项 ( 以生产 耐磨砖 为 例) 成本要 占到 生产成 本 的 5 %以上 。随 着能 源 价 格 0
带 走 的热量 为 :
l 窑尾 余 热 的应 用价值
窑尾快 速 冷却部 分的余 热利用 一直 没有 引起人 们 的重视 , 主要 原 因是 多数 人认 为这部 分余热 温度 较 低 ,
l 0 00 0×2 0×1 1×( 5 . 2 0—1 0 5 )=2 2×1 。k 0 J
单 位时 间带 走的热 量 为 :
的余热 利用 问题进 行粗 浅分析 , 旨在 明确利 用潜 力 , 找
出利用 方 向和 利 用 价 值 , 以期 达 到节 约能 源 、 轻 { 减 亏 染、 降低 生产成 本 以及提 高效 益之 目的。
余热发电技技术方案
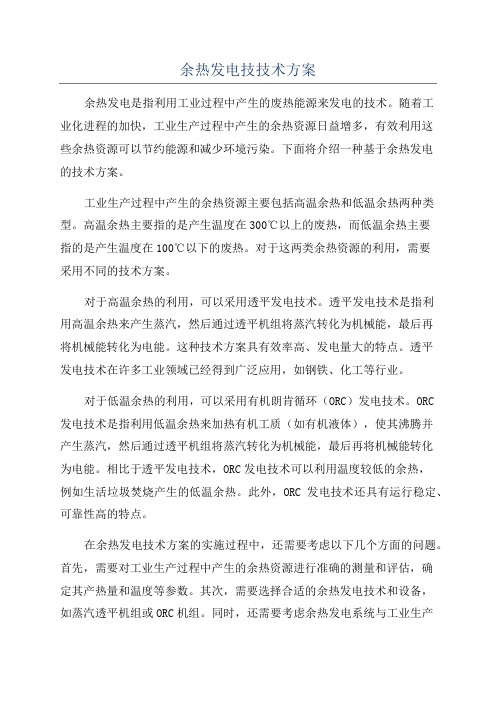
余热发电技技术方案余热发电是指利用工业过程中产生的废热能源来发电的技术。
随着工业化进程的加快,工业生产过程中产生的余热资源日益增多,有效利用这些余热资源可以节约能源和减少环境污染。
下面将介绍一种基于余热发电的技术方案。
工业生产过程中产生的余热资源主要包括高温余热和低温余热两种类型。
高温余热主要指的是产生温度在300℃以上的废热,而低温余热主要指的是产生温度在100℃以下的废热。
对于这两类余热资源的利用,需要采用不同的技术方案。
对于高温余热的利用,可以采用透平发电技术。
透平发电技术是指利用高温余热来产生蒸汽,然后通过透平机组将蒸汽转化为机械能,最后再将机械能转化为电能。
这种技术方案具有效率高、发电量大的特点。
透平发电技术在许多工业领域已经得到广泛应用,如钢铁、化工等行业。
对于低温余热的利用,可以采用有机朗肯循环(ORC)发电技术。
ORC发电技术是指利用低温余热来加热有机工质(如有机液体),使其沸腾并产生蒸汽,然后通过透平机组将蒸汽转化为机械能,最后再将机械能转化为电能。
相比于透平发电技术,ORC发电技术可以利用温度较低的余热,例如生活垃圾焚烧产生的低温余热。
此外,ORC发电技术还具有运行稳定、可靠性高的特点。
在余热发电技术方案的实施过程中,还需要考虑以下几个方面的问题。
首先,需要对工业生产过程中产生的余热资源进行准确的测量和评估,确定其产热量和温度等参数。
其次,需要选择合适的余热发电技术和设备,如蒸汽透平机组或ORC机组。
同时,还需要考虑余热发电系统与工业生产过程的协调,确保余热资源的稳定供应和发电系统的可靠运行。
最后,还需要进行经济性分析和环境影响评估,评估余热发电技术方案的可行性和效益。
总之,利用工业生产过程中产生的余热资源进行发电是一种重要的节能减排技术。
通过采用透平发电技术和ORC发电技术等余热发电技术方案,可以有效利用余热资源,提高能源利用效率,减少环境污染。
未来应继续加大对余热发电技术的研发和推广力度,进一步提高其应用水平,推动可持续发展。
辊道窑尾冷段余热利用浅析
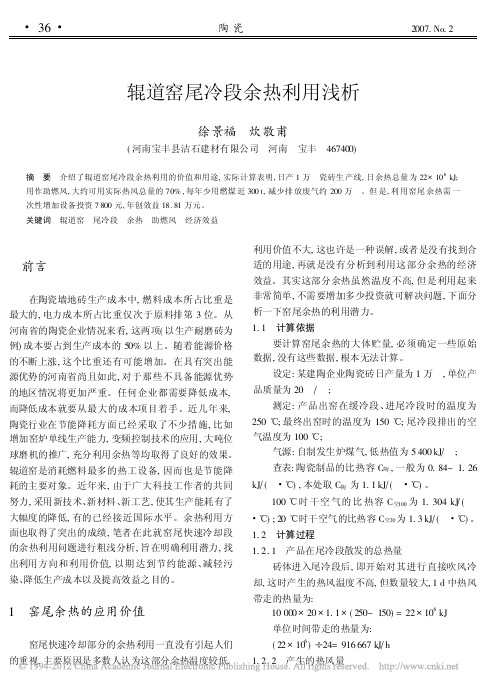
辊道窑尾冷段余热利用浅析徐景福炊敬甫(河南宝丰县洁石建材有限公司河南宝丰467400)摘要介绍了辊道窑尾冷段余热利用的价值和用途,实际计算表明,日产1万 瓷砖生产线,日余热总量为22@106kJ;用作助燃风,大约可用实际热风总量的70%,每年少用燃煤近300t,减少排放废气约200万 。
但是,利用窑尾余热需一次性增加设备投资7800元,年创效益18.81万元。
关键词辊道窑尾冷段余热助燃风经济效益前言在陶瓷墙地砖生产成本中,燃料成本所占比重是最大的,电力成本所占比重仅次于原料排第3位。
从河南省的陶瓷企业情况来看,这两项(以生产耐磨砖为例)成本要占到生产成本的50%以上。
随着能源价格的不断上涨,这个比重还有可能增加。
在具有突出能源优势的河南省尚且如此,对于那些不具备能源优势的地区情况将更加严重。
任何企业都需要降低成本,而降低成本就要从最大的成本项目着手。
近几年来,陶瓷行业在节能降耗方面已经采取了不少措施,比如增加窑炉单线生产能力,变频控制技术的应用,大吨位球磨机的推广,充分利用余热等均取得了良好的效果。
辊道窑是消耗燃料最多的热工设备,因而也是节能降耗的主要对象。
近年来,由于广大科技工作者的共同努力,采用新技术、新材料、新工艺,使其生产能耗有了大幅度的降低,有的已经接近国际水平。
余热利用方面也取得了突出的成绩,笔者在此就窑尾快速冷却段的余热利用问题进行粗浅分析,旨在明确利用潜力,找出利用方向和利用价值,以期达到节约能源、减轻污染、降低生产成本以及提高效益之目的。
1窑尾余热的应用价值窑尾快速冷却部分的余热利用一直没有引起人们的重视,主要原因是多数人认为这部分余热温度较低,利用价值不大,这也许是一种误解,或者是没有找到合适的用途,再就是没有分析到利用这部分余热的经济效益。
其实这部分余热虽然温度不高,但是利用起来非常简单,不需要增加多少投资就可解决问题,下面分析一下窑尾余热的利用潜力。
1.1计算依据要计算窑尾余热的大体贮量,必须确定一些原始数据,没有这些数据,根本无法计算。
辊道窑窑炉设计说明书
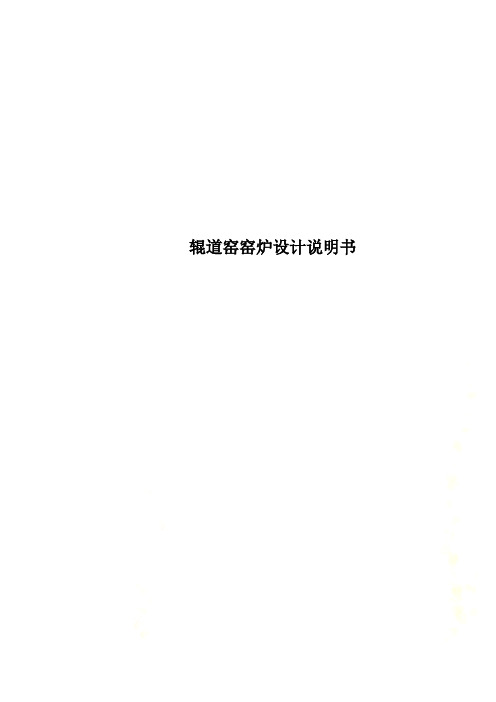
辊道窑窑炉设计说明书目录摘要 (6)前言 (8)1 设计任务书及原始资料 (9)2 烧成制度的确定 (10)2.1 温度制度的确定 (10)2.2 气氛制度 (11)2.3 压力制度 (11)3 窑体主要尺寸确定 (12)3.1窑内宽的确定 (12)3.2 窑体长度的确定 (13)3.3 各带长度的确定 (13)3.4 辊上高、辊下高的确定 (14)4 工作系统确定 (15)4.1 排烟系统 (15)4.2 烧成系统 (16)4.3冷却系统 (16)4.4窑体附属结构的布置 (17)5 窑体材料及厚度的确定 (19)6 燃料及燃烧计算 (21)6.1理论空气需要量 (21)6.2实际空气需要量 (21)6.3 用经验公式计算实际烟气生成量 (22)6.4 燃烧温度 (22)7 物料平衡 (22)7.1每小时出窑制品的质量G出 (22)7.2每小时入窑干制品的质量G干 (22)7.3每小时入窑湿制品的质量G湿 (22)7.4每小时蒸发自由水的质量G w (23)8 预热带烧成带热平衡计算 (23)8.1热平衡计算基准及范围 (23)8.2热平衡示意框图 (24)8.3热收入项目 (24)8.4热支出项目 (25)8.5热平衡方程 (30)8.6热平衡表 (31)9 冷却带平衡计算 (31)9.1热平衡计算准则: (31)9.2热平衡示意图: (32)9.3热收入 (33)9.4热支出 (33)9.5热平衡方程 (41)9.6冷却带平衡列表 (41)10 传动计算 (42)10.1 传动系统的选择 (42)10.2 传动过程 (43)10.3 辊子材质的选择 (43)10.4 辊距的确定 (43)10.5 辊子传动过程中的联接方式 (44)10.6 辊子转速的选择 (44)11管道计算、阻力计算和风机选型 (44)11.1管道计算 (44)11.2阻力计算 (45)11.3排烟风机选型 (46)11.4其他管路阻力计算: (46)12 烧嘴选型 (50)12.1每个烧嘴所需燃烧能力 (50)12.2 选用烧嘴应注意的原则 (50)12.3 烧嘴选用 (50)13 工程材料概算 (52)13.1 钢架结构所用钢材用量概算: (52)13.2 钢板用量概算: (53)13.3 耐火材料概算: (54)致谢 (57)参考文献 (58)外文翻译 (59)摘要本设计的题目是日产1.4万㎡抛光砖气烧辊道窑。
电烧辊道窑技术与装备开发及应用方案(二)
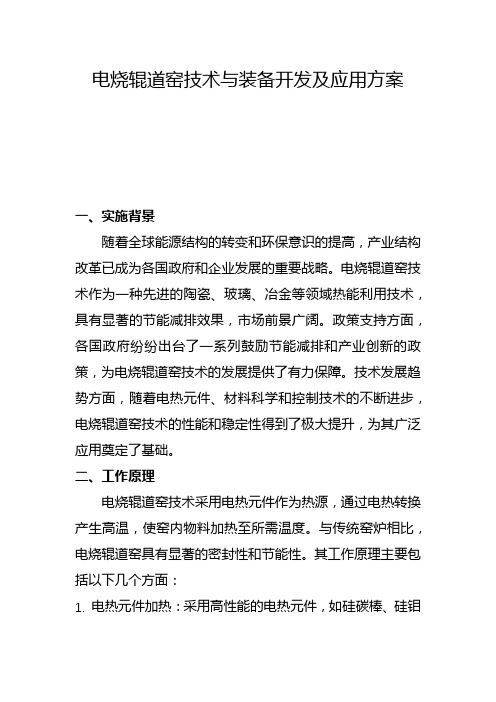
电烧辊道窑技术与装备开发及应用方案一、实施背景随着全球能源结构的转变和环保意识的提高,产业结构改革已成为各国政府和企业发展的重要战略。
电烧辊道窑技术作为一种先进的陶瓷、玻璃、冶金等领域热能利用技术,具有显著的节能减排效果,市场前景广阔。
政策支持方面,各国政府纷纷出台了一系列鼓励节能减排和产业创新的政策,为电烧辊道窑技术的发展提供了有力保障。
技术发展趋势方面,随着电热元件、材料科学和控制技术的不断进步,电烧辊道窑技术的性能和稳定性得到了极大提升,为其广泛应用奠定了基础。
二、工作原理电烧辊道窑技术采用电热元件作为热源,通过电热转换产生高温,使窑内物料加热至所需温度。
与传统窑炉相比,电烧辊道窑具有显著的密封性和节能性。
其工作原理主要包括以下几个方面:1. 电热元件加热:采用高性能的电热元件,如硅碳棒、硅钼棒等,将电能转化为热能,产生高温。
2. 密封性能:电烧辊道窑采用先进的密封技术,如耐火纤维、陶瓷纤维等,确保窑内热量不流失,提高热效率。
3. 控制系统:采用先进的温度控制系统和自动化仪表,对窑内温度、气氛等参数进行实时监测和调节,确保产品质量稳定。
4. 辊道输送:物料在窑内通过辊道输送,实现连续化生产,提高生产效率。
三、实施计划步骤电烧辊道窑技术与装备开发及应用方案的实施计划步骤如下:1. 设计阶段:进行电烧辊道窑的整体设计和电热元件、密封材料、控制系统的选型。
根据实际需求,确定窑炉尺寸、产量、能耗等参数。
2. 实施阶段:按照设计方案进行设备制造和安装。
确保设备质量符合要求,安装过程符合安全规范。
3. 调试阶段:完成设备安装后进行调试,对温度控制系统、输送系统等关键部件进行测试和优化。
确保设备运行稳定,满足生产工艺要求。
4. 验收阶段:组织专家对电烧辊道窑进行验收,评估其性能、能耗等指标是否达到设计要求。
根据验收结果进行调整和优化。
四、适用范围电烧辊道窑技术及装备适用于陶瓷、玻璃、冶金等领域。
在陶瓷行业,电烧辊道窑可用于烧制瓷砖、卫生洁具、日用陶瓷等产品;在玻璃行业,可用于熔制平板玻璃、容器玻璃等;在冶金行业,可用于冶炼钢铁、有色金属等。
带尾气处理装置的燃气辊道窑炉的制作技术

本技术新型属于烧结设备技术领域,涉及一种带尾气处理装置的燃气辊道窑炉,预热段的顶部设有与尾气处理装置的进气管连接的排烟支管,烧成段内设有与燃气管相连的烧嘴,烧嘴的一侧设有助燃风管,冷却段内设有冷风管,冷却段的顶部设有抽热风管,抽热风管通过抽热风机与换热器的内进气口连接;进气管与窑炉顶部的排烟支管连接,进气管上设有风机,进气管与燃烧室的进气口相连,燃烧室的出气口与换热器的内进气口相连,换热器的内出气口与排气管相连,换热器的外出气管上设有引风机二;燃烧室内的烧嘴与燃气管连接;排气管上设有排烟蝶阀;对窑炉预热段和降温段尾气中的热量实现回收利用,节约能源;尾气处理设备简单,操作方便,安全可靠。
技术要求1.一种带尾气处理装置的燃气辊道窑炉,包括窑体包括依次相连的预热段(1)、烧成段(2)和冷却段(3),所述预热段(1)的顶部设有排烟支管(12),排烟支管(12)与尾气处理装置的进气管(41)连接,排烟支管(12)上设有调节阀(11);所述烧成段(2)内设有烧嘴(21),烧嘴(21)与燃气管一(22)相连,每个烧嘴(21)的一侧设有助燃风管,助燃风管与助燃风机(23)相连;所述冷却段(3)内设有冷风管(31),冷风管(31)与冷风机相连,冷却段(3)的顶部设有抽热风支管(38),抽热风支管(38)汇集于抽热风管(37),其特征在于:抽热风管(37)通过抽热风机(34)与换热器的内进气口连接;所述尾气处理装置,包括进气管(41)、燃烧室(47)、换热器(412)和排气管(45),所述进气管(41)与窑炉预热段的排烟支管(12)连接,进气管(41)上设有风机(410),进气管(41)与燃烧室(47)的进气口相连,进气管(41)与燃烧室(47)进气口之间设有主调节阀(42);所述燃烧室(47)的出气口与换热器(412)的内进气口相连,换热器(412)的底部设有排水口(415),换热器(412)的内出气口通过引风机(413)与排气管(45)相连,换热器(412)的外出气管(414)上设有引风机二(411);燃烧室(47)内设有烧嘴(43),烧嘴(43)与燃气管(48)连接;燃气管(48)的一侧设有助燃管;排气管(45)上设有排烟蝶阀。
- 1、下载文档前请自行甄别文档内容的完整性,平台不提供额外的编辑、内容补充、找答案等附加服务。
- 2、"仅部分预览"的文档,不可在线预览部分如存在完整性等问题,可反馈申请退款(可完整预览的文档不适用该条件!)。
- 3、如文档侵犯您的权益,请联系客服反馈,我们会尽快为您处理(人工客服工作时间:9:00-18:30)。
气烧辊道窑余热发电技术方案
一、辊道窑余热发电概述
余热发电技术是利用企业的高品位热量进行回收,并集中转化为电力供企业自用的技术。
我国从上世纪“八五”期开始,对余热发电技术和装置进行系统的研制开发,经过十多年的开发、研究和若干实际工程投产运行,余热发电技术和国产化设备都已成熟可靠,总体上的技术水平已经赶上国际先进工业国家。
国家也把利用余热发电,作为节能降耗,实现循环发展的重要措施之一,给予大力支持和发展,使我国的余热发电技术应用领域不断扩大。
但在建筑陶瓷、卫生陶瓷行业生产领域,辊道窑余热发电方面是个空白。
根据国家发展改革委节能中长期专项规划[发改环资[2004]2505号]精神,在“十一五”期间,辊道窑是陶瓷行业推广的技术。
由于国内对辊道窑余热利用技术的研究起步较晚,余热利用率较低,除部份企业把余热用于原料烘干外,大部份企业是把高品位的辊道窑排烟热量(温度400~800℃)和产品冷却热量(温度950~1200℃)直接废弃,从而造成大量的能源浪费和热源污染。
陶瓷企业的余热利用,国内外先进企业主要是将辊道窑烟气和产品冷却产生的热风,通过风机送到原料干燥塔,对陶瓷原料进行干燥,以减少干燥塔一次能源消耗量,使陶瓷企业获得一定的经济效益。
由于陶瓷原料的干燥主要是蒸发原料中的水份,利用辊道窑100~400℃的余热足够干燥所需热量;若直接利用辊道窑高品位余热(排烟温度400~800℃和产品冷却温度650~1200℃)用于干燥,则会导致干燥塔热量过剩,同时大大地降低余热的利用价值,使辊道窑的能源浪费转移到干燥塔,干燥塔能源损失量大,而能量品位又低,散失了余热再利用的价值。
陶瓷企业的余热利用除原料干燥以外,其它方式的余热利用量很小,利用价值很低(如加热浴室用热水等),相当多的企业根本就不利用而直接废弃。
根据陶瓷企业余热利用的现状,如何有效地提高余热的利用效率和利用价值,是本项目研究的目的。
电力作为二次能源,价值高且使用方便。
如果将陶瓷企业辊道窑高品位余热(400~800℃的排烟余热和650~1200℃的产品冷却余热)收集转化为价值更高的电力能源,而品位较低、余热锅炉难以利用的余热(100~400℃)再用于原料干燥,既可满足陶瓷生产的需求,并充分利用好现有干燥设备,提高陶瓷企业辊道窑余热利用的价值和效率,解决陶瓷企业余热过剩的问题,将大大地降低企业的生产成本,并节约资源,从而推动陶瓷企业的循环经济发展。
辊道窑消耗的一次能源(煤、油或天然气),除炉窑散热、产品水份蒸发、烧结等必须消耗的能量外,约70%的能量是随排烟热损失和产品冷却热损失而浪费。
在这些浪费的热量(简称余热)中,采用余热干燥原料的方式,可利用余热的20%,20%因品位低无法利用,另有60%左右的余热还没有得到充分利用。
以一条每小时耗标准煤1400Kg的气烧辊道窑为例,进入炉窑总的热量为41×106KJ/h,有12.3×106KJ/h热量直接用于陶瓷生产,有28.7×106KJ/h余热;其中5.74×106KJ/h热量可用于原料干燥,有17.22×106KJ/h热量没有得到充分利用,5.74×106KJ/h热量不能利用。
若将17.22×106KJ/h热量通过余热锅炉转化为蒸汽的热量,余热锅炉效率为85%,则可产生2.5MPa、400℃的蒸汽(蒸汽焓为3214KJ/Kg)2380Kg/h,利用凝汽式汽轮发电机发电,其汽耗率为5.6Kg/KWh,则这条炉窑的余热可发电370KW。
按平均电价0.55元/度计算,这条炉窑每小时可额外回收203.5元的电,经济效益显著。
若
选用排汽压力0.3MPa的小型背压式汽轮发电机发电,汽耗率为26Kg/KWh,则这条炉窑的余热可发电91.5KW,发电的经济效益比凝汽式机组更低,但可利用汽轮机排汽用于陶瓷原料低温干燥或其它工业、生活用汽,提高余热利用的经济效益。
利用辊道窑余热发电的关键,在于开发出适合陶瓷生产的余热锅炉技术和分散热源热工监控技术。
设计的余热锅炉不能影响陶瓷的正常生产(即不影响产品的产量和质量),也不增加一次能源消耗量,余热锅炉产汽压力、温度稳定、可控。
本项目以公司“辊道窑余热发电装置”专利技术为核心,集合我国余热发电的先进技术,自主研制开发出煤烧辊道窑余热发电技术和装置。
项目经过近一年的反复研制开发,以及陶瓷生产企业的使用,在技术上有较大的突破。
创新的“满足辊道窑生产工艺需要的分段换热技术”、“辊道窑余热锅炉过热蒸汽恒温技术”、“辊道窑消烟除尘技术”、“分散热源能量回收热力系统热工监控技术”,较好地解决了煤烧辊道窑余热吸收、收集、能量转换、汽轮机排汽利用、安全运行等技术问题。
同时集合现有成熟的“分散热源能量回收汇集技术”、“钠离子交换水处理技术”、“余热锅炉技术”、“蒸汽发电技术”和“热工仪表监控保护技术”,使整套余热利用装置达到余热利用率高、发电量大(平均每条炉窑可发电266万度/年)、节能降耗效果显著、无烟尘和热源污染、企业经济效益提高(平均每条炉窑可为企业节约近120万元/年的电费开支)的目标。
与余热用于原料干燥技术相比,节能效果更好,技术更先进,有利于陶瓷企业循环经济的发展。
二、气烧辊道窑余热发电能量平衡概算
二条气烧辊道窑,日耗煤85吨(低位发热量5500Kcal/kg),日产瓷砖17000m2(10 kg/m2),产品烧成温度1100℃,窑头排烟温度400~500℃,其中可利用余热量:
1、急冷带(1100℃冷却至600℃和400℃冷却至200℃)余热:
0.26 Kcal/(kg.℃)×17000m2/d×10 kg/m2÷24 h/d×[(1100-600)+(400-200)] ℃=128.92万Kcal/h
2、排烟余热(烟气温度400℃冷却至200℃):
(3970-1930)Kj/kg×85×103 kg/d÷24 h/d÷4.18Kj/Kcal=172.8万Kcal/h
3、合计:128.92万Kcal/h +172.85万Kcal/h=301.77万Kcal/h,折合标准煤431.1 kg/h,余热锅炉效率85%。
可产生2.5 MPa、390℃的蒸汽(焓值为769 Kcal/ kg)
431.1×104Kcal/h×0.85÷769Kcal/ kg=4765 kg/h
采用进汽参数2.35 MPa、390℃的次中压凝汽式机组,汽耗率为5.6 kg/KWh,可发电
4765kg/h÷5.6kg/KWh =851KW
4、由于实际生产过程中,炉窑保温性能差异和炉管积灰等因素,致使余热利用率会下降10~15%,实际发电量为:
次中压(2.35MPa、390℃)参数:851KW×0.85=723KW
因此,根据该厂炉窑保温情况和维护上的关系,采用次中压参数运行时发电量为700~850KW,装置自用电量40~50KW,供电量为650~800KW。