自动化设备机械加工件来料检验标准
来料检验规范
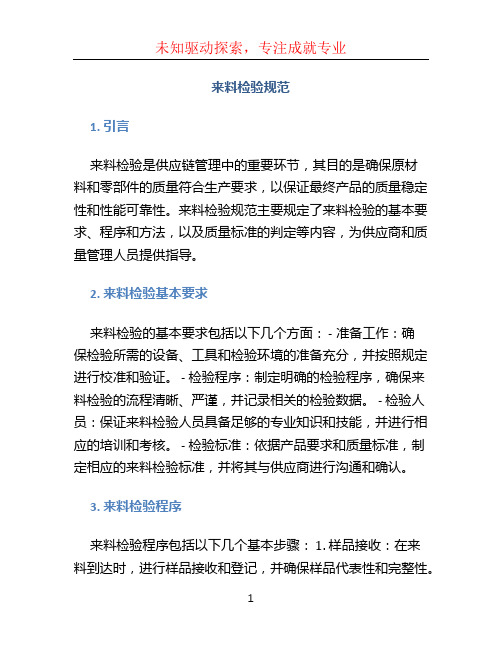
来料检验规范1. 引言来料检验是供应链管理中的重要环节,其目的是确保原材料和零部件的质量符合生产要求,以保证最终产品的质量稳定性和性能可靠性。
来料检验规范主要规定了来料检验的基本要求、程序和方法,以及质量标准的判定等内容,为供应商和质量管理人员提供指导。
2. 来料检验基本要求来料检验的基本要求包括以下几个方面: - 准备工作:确保检验所需的设备、工具和检验环境的准备充分,并按照规定进行校准和验证。
- 检验程序:制定明确的检验程序,确保来料检验的流程清晰、严谨,并记录相关的检验数据。
- 检验人员:保证来料检验人员具备足够的专业知识和技能,并进行相应的培训和考核。
- 检验标准:依据产品要求和质量标准,制定相应的来料检验标准,并将其与供应商进行沟通和确认。
3. 来料检验程序来料检验程序包括以下几个基本步骤: 1. 样品接收:在来料到达时,进行样品接收和登记,并确保样品代表性和完整性。
2. 外观检验:对来料进行外观检查,包括尺寸、颜色、表面质量等方面的检验。
3. 物理性能检验:对来料进行物理性能测试,包括强度、硬度、密度等方面的检验。
4. 化学成分检验:对来料进行化学成分测试,如含量分析、元素分析等。
5. 材料鉴别:使用相应的测试方法和工具进行来料的材料鉴别,确认材料的真实性和原材料的符合性。
6. 尺寸检验:通过测量和检验来料的尺寸准确性,确保其符合图纸和设计要求。
7.功能性能检验:根据产品的功能要求,进行来料的功能性能测试,以确保其满足产品的使用要求。
8. 检验记录:对每个来料样品的检验过程和结果进行详细记录和存档。
4. 质量标准的判定质量标准的判定是来料检验的重要环节,主要包括以下几个方面: - 合格标准:根据产品要求和质量标准,制定合格的定义和界限,对来料进行判定。
- 不合格处理:对不符合质量标准的来料,按照相应的不合格处理程序进行处理,包括退货、返修等。
- 问题解决:对于出现的质量问题,及时与供应商沟通,共同解决问题,并采取预防措施避免类似问题的再次发生。
机械加工件来料通用检验标准

测量范围为 0-500mm,卡尺的测量位置与图纸要求相对应,卡爪左右轻轻摆动,
数显卡尺 最小值为产品的尺寸,工件的全长取前、中、后几点测量,所得最大值与最小值
4
长度尺寸
之差的一半为工件的平行度误差。
工件过长,精度要求不高,可用卷尺测量,测量时需拉直卷尺与规则工件的侧 卷尺
面平行,取两端面间的最小值。
千分尺 小值为外径尺寸,适用于公差范围:<0.02mm。
深度 测量时将深度尺横端面与被测工件的标准面靠紧、摆正、保持垂直,轻轻用力
百分尺 旋转尺尾端旋钮,所得值为实际尺寸。
3
深度尺寸 游标 测量时将深度尺横端面与被测工件的标准面靠紧、摆正、保持垂直,轻轻用力
深度尺 推入,所得值为实际尺寸。
深度量规 通规靠紧工件标准面,无透光现象,止规靠紧加工面有透光现象,为合格产品。
7
内螺纹
完整牙型的通规正好拧进,截短牙型的止规拧不进,工件螺纹精度合格
8
孔距
测量两孔间最小距离,通过运算测量出两孔间中心线距离,对于有角度要求的 分布在工件端面的孔应用角度尺进行测量。
2.3 外观检验条件:在 40W 日光灯下距离 30~40cm(照度约 500Lux~550Lux),旋转角度进行检查,每一面目视时
点比较其测量值,最大值与最小值之差的一半即为孔的圆柱度误差,在孔径圆
周上变换方向,比较其测量值可测孔的圆度。
内径 千分尺
用来测量 50mm 以上的孔径,按孔径选择合适长杆,并用外径千分尺校正零位。 使用时,在孔内摆动,在直径方向找出最大值,轴上找出最小值,这两个重合 值,就是孔的实际尺寸
6
外螺纹
用螺纹环规测量,完整牙型的通规正好拧进,截短牙型的止规拧不进,工件螺 纹精度合格,
机加工零部件质量检验标准
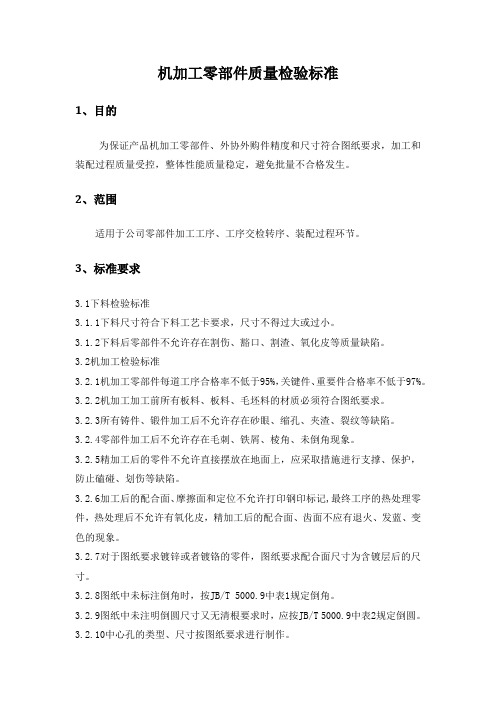
机加工零部件质量检验标准1、目的为保证产品机加工零部件、外协外购件精度和尺寸符合图纸要求,加工和装配过程质量受控,整体性能质量稳定,避免批量不合格发生。
2、范围适用于公司零部件加工工序、工序交检转序、装配过程环节。
3、标准要求3.1下料检验标准3.1.1下料尺寸符合下料工艺卡要求,尺寸不得过大或过小。
3.1.2下料后零部件不允许存在割伤、豁口、割渣、氧化皮等质量缺陷。
3.2机加工检验标准3.2.1机加工零部件每道工序合格率不低于95%,关键件、重要件合格率不低于97%。
3.2.2机加工加工前所有板料、板料、毛坯料的材质必须符合图纸要求。
3.2.3所有铸件、锻件加工后不允许存在砂眼、缩孔、夹渣、裂纹等缺陷。
3.2.4零部件加工后不允许存在毛刺、铁屑、棱角、未倒角现象。
3.2.5精加工后的零件不允许直接摆放在地面上,应采取措施进行支撑、保护,防止磕碰、划伤等缺陷。
3.2.6加工后的配合面、摩擦面和定位不允许打印钢印标记,最终工序的热处理零件,热处理后不允许有氧化皮,精加工后的配合面、齿面不应有退火、发蓝、变色的现象。
3.2.7对于图纸要求镀锌或者镀铬的零件,图纸要求配合面尺寸为含镀层后的尺寸。
3.2.8图纸中未标注倒角时,按JB/T 5000.9中表1规定倒角。
3.2.9图纸中未注明倒圆尺寸又无清根要求时,应按JB/T 5000.9中表2规定倒圆。
3.2.10中心孔的类型、尺寸按图纸要求进行制作。
3.2.11所有内径、外径、轴类加工表面粗糙度必须严格按照图纸制作。
4、职责和要求4.1技术部负责按照产品设计确认产品关键件、重要件并提供清单;负责产品在生产制作过程中图纸尺寸的修改和提供技术支持。
4.2工艺部负责确认关键工序和重要工序并制定工艺文件;负责产品制作过程中加工工艺的指导和工艺文件的制定并监督工作执行情况。
4.3 生产部负责按照最新版设计图纸和工艺文件进行派工,并将图纸和工艺卡一并交给操作者。
操作者在加工前必须熟悉图纸尺寸要求和工艺制作流程要求,熟练掌握本工序所用的工装、夹具和量具的使用,并复检上道工序(如:下料)零部件是否存在尺寸不合格或外观缺陷等质量问题。
来料检验标准

隔离并标识来料检验报告特采选用退货 供应商NGOK 跟进签批1. 目的:确保来料质量符合本公司规定要求。
2. 范围:适合公司原辅材料及外加工半成品的检验。
3. 职责:质控部:负责材料的检验。
4.作业流程:5.公司来料按类别分类为:纸张类、辅料类、外协类。
5.1 纸张类 5.1.1 术语及定义:A 、尺寸偏差(横向坚向):对规矩型样品进行平行或垂直方向测量得到数据与标准数据比。
B 、歪斜底:对规矩型样品,进行对角线测量,对比其两者的数据差异。
C 、克重:指在一般条件下,所测量数据(不考虑环境及材料本身的含水量)。
D 、厚薄均匀度:包含同一样张的不同部位或不同样张的同一部位两组数据。
5.1.2 指标要求:来料与《来料通知单》一致,有效的标签(生产厂家、日期、批号及等级等),整批1.仓管员通知IQC 检验。
2.IQC 开始准备检验。
检验合格流程:1、IQC 依据《物料RoHS 对应清单》确认所来物料其有害物质含量是否符合要求后进行后续检验,如不符合作则直接作退货处理;2、检验物料与《收货通知单》一致性及外观有无异常。
3、据物料的抽样标准及检验标准进行验收检查,填写《来料检验报告单》。
3、检验合格后书面通知仓库办理入库手续,并挂“合格品”标识牌,注明检验状态、检验时间及检验人。
检验不合格流程:1、检验不合格的,由IQC 挂“不合格品”标识牌,通知仓库隔离并提交《来料检验报告单上报品质经理处理。
2、根据《来料检验报告单》的签批情况,进行相关处理。
3、特采与选用合格的按合格品流程入仓,选用不合格的与报告签批退货的通知仓库退供应商。
流程 操作规范OKNGIQC 验收物料通知IQC 检验仓库品质部异常处理入库纸张平整,没有卷曲,外观包装一致,包装完好。
5.1.3 抽样标准:5.1.3.1 来料为散装纸(分切纸等)的,按国标GB2828.1-2003的AQL 2.5标准进行抽检。
5.1.3.2来料为板装铜版纸、灰卡纸、单铜纸、哑粉纸的查看外观及生产日期即可。
来料检验标准
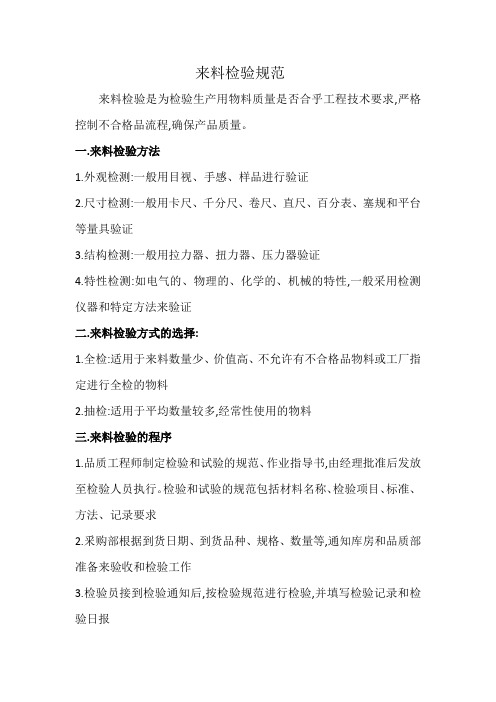
来料检验规范来料检验是为检验生产用物料质量是否合乎工程技术要求,严格控制不合格品流程,确保产品质量。
一.来料检验方法1.外观检测:一般用目视、手感、样品进行验证2.尺寸检测:一般用卡尺、千分尺、卷尺、直尺、百分表、塞规和平台等量具验证3.结构检测:一般用拉力器、扭力器、压力器验证4.特性检测:如电气的、物理的、化学的、机械的特性,一般采用检测仪器和特定方法来验证二.来料检验方式的选择:1.全检:适用于来料数量少、价值高、不允许有不合格品物料或工厂指定进行全检的物料2.抽检:适用于平均数量较多,经常性使用的物料三.来料检验的程序1.品质工程师制定检验和试验的规范、作业指导书,由经理批准后发放至检验人员执行。
检验和试验的规范包括材料名称、检验项目、标准、方法、记录要求2.釆购部根据到货日期、到货品种、规格、数量等,通知库房和品质部准备来验收和检验工作3.检验员接到检验通知后,按检验规范进行检验,并填写检验记录和检验日报4.检验完毕后,对合格的来料贴上合格标识,通知采购与库房人员办理入库手续5.如果是生产急需的来料,在来不及检验和试验时,须按紧急放行规定的程序执行6.检测中不合格的来料应及时填写《产品检验不合格品单》,由品质工程师确认并给出参考意见,提交经理作出处理:重大问题必须提交品质部经理与工程部、生产部审核后再作出处理;不合格的来料不允许入库,并进行相应标识,将移入不合格品库区.隔离,采购部按处理意见办理相关事宜;保证不合格的零件、成品不装配、不合格的产品不出7.来料检验和试验的记录由品质部文员每日收取,做好数据统计汇总后,整理成册存档备查,按规定期限妥善保存8.检验时,如来料检验员无法判定是否合格,应立即请品质工程师或经理会同验收来判定是否合格,会同验收的参与人员必须在检验记录表内签字9.回馈来料检验情况,并将来料供应商的交货质量情况及检验处理情况记录,每月汇于供应商的交货质量月报内10.来料检验员根据来料的实际检验情况,对检验规范提出改善意见11.来料检验员定期校正检验仪器、量规,保养试验设备,以保证来料检验结构的正确四、来料检验的结果1.检验合格:经来料检验员按照检验规范要求操作,来料检验员应在《检验合格证》上签名,通知采购与库房收货2.检验不合格:来料检验员按照检验规范要求操作,检岀不合格品应及时填写《产品检验不合格品单》,会同品质工程师、经理作出处理;不合格品处理有报废、让步接收特釆.、返工返修三种处理方式:重大问题必须提交品质部经理与工程部、生产部审核后再作出处理;并进行相应标识,将移入不合格品库区.隔离,通知采购部根据处理意见办理相关事宜3.让步接收特采.:即来料经检验员的检验发现其质量低于标准要求,但由于生产急需或其他原因,会同品质工程师、经理、工程部、生产部作出降级次品.的让步接收处理,会同验收的参与人员必须在检验记录表内签字方可签收过程检验规范装配过程的质量对一个产品的质量起着决定性的作用,零件的质量是合格的,但由于装配质量不合格,制造出来的产品的质量肯定不合格。
机械加工检验标准及方法(1)

机械加工检验标准及方法(1)机械加工是现代工业生产中不可或缺的一环,机械加工检验是确保机械加工产品质量的重要环节。
为了确保机械加工产品的合格率,合理地制定适合生产的检验标准及方法是必要的。
本文将详细介绍机械加工检验标准及方法。
机械加工检验标准机械加工产生的产品有尺寸精度、表面质量、几何精度、材料硬度等多个方面的品质要求。
机械加工检验标准是指根据机械加工产品的不同品质要求,制定出一系列检验标准,用于对机械加工产品进行检验。
常见的机械加工检验标准有GB、ISO、JIS等标准。
在实际操作中,应根据机械加工产品的实际需求和使用要求,选择合适的检验标准进行检验。
同时,对于特定的机械加工产品,也可以根据实际需求制定符合实际情况的检验标准。
机械加工材料的检验方法机械加工材料的检验是确保机械加工产品质量的关键环节。
在机械加工成品的检验过程中,不仅要对成品进行检验,还要对原材料进行检验。
下面我们将详细介绍机械加工材料的检验方法。
金属材料的检验方法金属表面缺陷的检验钢材表面缺陷常见有裂纹、划痕、气泡、硅酸盐夹杂物等。
缺陷类型众多,方法不同。
一般来说,通过目视检查、手摸检查、探伤、磁粉探伤等方法可检测出钢材表面缺陷。
但有些缺陷需要通过仔细打磨能够去除,在制作机械零件时才可使用。
金属含量的检验从金属材料中提取样品,经过化学分析,就可以得到其组成。
从而判断其是什么金属及含量是否符合标准。
非金属材料的检验方法干燥状态的检验如混凝土等,在干燥状态下检测其强度。
取样检验如塑料等,可在规定的机器、水平面等条件下,按规定的方法将试样切割成均匀大小的试样,然后采用拉伸、弯曲等方法进行检验。
机械加工验收方法验收是机械加工产品交付使用前的最后一道程序。
通过验收可以确定机械加工产品是否符合质量标准,以及确认产品的使用性能是否符合用户要求。
机械加工产品的验收方法主要包括自检、互检和专家检查。
自检自检主要是由机械加工产品生产者自己进行,通过严格的自我检查,查找产品的问题,使其能够符合相应的质量标准。
机械加工件检测标准
机械加工件检测标准1、目的:通过严格执行三检,“首件检验”、“巡回检验”、“完工检验”将检验工件与工序控制紧密结合,对每一工序的质量问题或可能出现的质量问题不放过,不合格品不能转入下工序,从而提高产品质量。
2、适用范围:所有加工件3.检验原则3.1.检验人员必须具有一定的专业知识和实际工作经验,且能满足现行产品对检验工作的各项要求。
3.2.检验人员所用的计量器具必须是经计量部门校验合格并在规定周期内。
3.3.检验人员验收产品前应熟读相关图样和技术文件,了解零件的关键尺寸及装配关系要点。
3.4 检验人员必须严格按照图样和技术文件所规定的要求对零件进行判定。
4.检验依据检测依据按图纸及工艺卡检测5.检测种类:“工序自检”“首件检验”、“巡回检验”、“完工检验”5.1.工序自检:工件完成工序后进行自检,自检合格后在工艺卡进行签字;5.2.首件检验:批量工件必须首件检验后,才能开始加工5.2.1.对首件,根据加工工艺要求,核实首件产品或工件(毛坯)产品的质量特性是否符合要求。
对首批检查的工件,操作者必须做好自检,在操作者缺乏检测手段时,也应对工件外观质量自检,合格后送质量专员检查。
无论在任何情况下,首件检验未经检验合格,不得进行批量生产或继续加工作业。
5.2.2.工作班开始加工的第一个工件;5.2.3.调换操作者后加工的第一个工件;5.2.4. 更换(调整)工艺装备或更换模具后加工的第一个工件;5.2.5.更换材料批(炉)号后加工的第一个工件;5.2.6. 代用材料后加工的第一个工件;5.2.7.检验内容:根据检验标准的要求,核对首件产品的质量特性值是否真正符合要求;对首件检验合格,批准生产加工,首件检验不合格,进行不合格品的处理,同时分析不合格原因,采取改进措施后加工,产品继续首件检验,直至合格为止。
5.3.巡回检验:5.3.1.由检验人员在生产现场,进行日常巡回监督检查,重点监控工序质量和典型零件质量;5.3.2根据检验标准、图纸和工艺的要求、检验、核对巡检产品的质量特性值是否真正符合要求;5.3.3.若巡检某质量特性值不合格,应按《不合格品报告单》处理,同时。
机加工件检验标准
机加工件检验标准机加工件的质量直接关系到产品的使用性能和安全性,因此对机加工件的检验标准尤为重要。
机加工件的检验标准主要包括尺寸、形位公差、表面质量和材料成分等方面,下面将分别对这几个方面进行详细介绍。
首先,尺寸是机加工件检验的重要内容之一。
尺寸的检验主要包括外观尺寸和内部尺寸两个方面。
外观尺寸主要是通过测量工具对机加工件的外形尺寸进行检验,包括直径、长度、宽度等。
内部尺寸则需要通过专用的测量工具或检测设备进行检验,确保机加工件的内部尺寸符合设计要求。
其次,形位公差也是机加工件检验的重要内容之一。
形位公差是指机加工件在装配或使用过程中,各个特征之间的相对位置关系所允许的偏差范围。
形位公差的检验需要使用三坐标测量仪或其他高精度测量设备,对机加工件的形位公差进行全面检测,确保其符合相关标准要求。
另外,表面质量也是机加工件检验的重要内容之一。
表面质量的检验主要包括表面粗糙度、表面平整度、表面清洁度等方面。
表面质量的检验需要使用表面粗糙度仪、平整度测量仪等专用设备,对机加工件的表面质量进行全面检测,确保其符合产品要求。
最后,材料成分也是机加工件检验的重要内容之一。
材料成分的检验需要使用化学分析仪器对机加工件的材料成分进行检测,确保其符合设计要求,以保证产品的使用性能和安全性。
总之,机加工件的检验标准涉及到尺寸、形位公差、表面质量和材料成分等多个方面,需要使用不同的测量工具和检测设备进行全面检验。
只有严格按照相关标准要求进行检验,才能确保机加工件的质量符合产品要求,提高产品的使用性能和安全性。
来料检验规范【范本模板】
来料检验规范来料检验是为检验生产用物料质量是否合乎工程技术要求,严格控制不合格品流程,确保产品质量。
一、来料检验方法:1)外观检测:一般用目视、手感、样品进行验证;2)尺寸检测:一般用卡尺、千分尺、卷尺、直尺、百分表、塞规和平台等量具验证;3)结构检测:一般用拉力器、扭力器、压力器验证;4)特性检测:如电气的、物理的、化学的、机械的特性,一般采用检测仪器和特定方法来验证。
二、来料检验方式的选择:1)全检:适用于来料数量少、价值高、不允许有不合格品物料或工厂指定进行全检的物料.2)抽检:适用于平均数量较多,经常性使用的物料.三、来料检验的程序:1)品质工程师制定检验和试验的规范、作业指导书,由经理批准后发放至检验人员执行.检验和试验的规范包括材料名称、检验项目、标准、方法、记录要求。
2)采购部根据到货日期、到货品种、规格、数量等,通知库房和品质部准备来验收和检验工作。
3)检验员接到检验通知后,按检验规范进行检验,并填写检验记录和检验日报。
4)检验完毕后,对合格的来料贴上合格标识,通知采购与库房人员办理入库手续。
5)如果是生产急需的来料,在来不及检验和试验时,须按紧急放行规定的程序执行。
6)检测中不合格的来料应及时填写《产品检验不合格品单》,由品质工程师确认并给出参考意见,提交经理作出处理;重大问题必须提交品质部经理与工程部、生产部审核后再作出处理;不合格的来料不允许入库,并进行相应标识,将移入不合格品库(区)隔离,采购部按处理意见办理相关事宜;保证不合格的零件、成品不装配,不合格的产品不出厂。
7)来料检验和试验的记录由品质部文员每日收取,做好数据统计汇总后,整理成册存档备查,按规定期限妥善保存。
8)检验时,如来料检验员无法判定是否合格,应立即请品质工程师或经理会同验收来判定是否合格,会同验收的参与人员必须在检验记录表内签字。
9)回馈来料检验情况,并将来料供应商的交货质量情况及检验处理情况记录,每月汇总于供应商的交货质量月报内.10)来料检验员根据来料的实际检验情况,对检验规范提出改善意见.11)来料检验员定期校正检验仪器、量规,保养试验设备,以保证来料检验结构的正确性。
机加工类产品检验要求及方法
WI指导文件机加工类产品检验要求及方法DOC NO文件编号WI-PZ-013 REV 版本A PAGE页码 3 of 9e. 金属精铸件按IT12检验,未经加工的普通铸造件按IT17检验。
f. 机加工采购原材料及外协件按IT17检验。
6.2 表面质量6.2.1 文字符号文字符号清晰、完整且与研发部下发的丝印图保持一致。
文字的涂覆层均匀、光滑、干净、牢固。
用3M 胶带反复对标识的同一部位进行3次粘接,如涂覆层无脱落,则视为合格。
6.2.2 整体结构a.结构完整,没有裂痕,无开焊现象。
b. 材料平整,无加工毛刺。
c. 门锁与机箱导通良好(在机箱的螺丝柱上拧上一个螺钉,把万用表调到二极管档,红黑表笔分别接触门锁和螺钉,万用表发出蜂鸣声则视为导通良好)。
6.2.3 涂覆层a. 涂料涂覆不允许有开裂、自然脱落现象,表面不允许有漏涂及露原底的现象。
b. 防涂覆对于起接地作用的預埋螺柱及焊板等要求防涂覆的部件,起根部涂覆层的长度不多于该件长度的20%;对于起安装作用的預埋螺柱和預埋螺母等要求防涂覆的件上,不允许有涂覆层。
C 电镀涂覆要求镀层清洁、光亮、无缺损,同一平面上的镀层颜色均匀一致,主要表面上不应有明显的镀层缺陷,如起泡、孔隙、粗糙、裂纹、脱色、局部无镀层等。
6.2.4 表面平整度使直尺下边轻轻接触试样两端翘起的边缘,从主尺上读出跨距L(mm),并测量板与主尺上表面的最大距离h,用h减去主尺厚度,即板的弓曲值D。
按下式换算成1000 mm跨距时的弓曲值d,d=D*1000*1000/(L*L)测量出原材料平整面的d值应小于0.56.2.5 表面A级:要求边、角、窗口、孔边涂覆层均匀、光滑,不允许有飞边、毛刺和积塑现象。
在。
- 1、下载文档前请自行甄别文档内容的完整性,平台不提供额外的编辑、内容补充、找答案等附加服务。
- 2、"仅部分预览"的文档,不可在线预览部分如存在完整性等问题,可反馈申请退款(可完整预览的文档不适用该条件!)。
- 3、如文档侵犯您的权益,请联系客服反馈,我们会尽快为您处理(人工客服工作时间:9:00-18:30)。
自动化设备机械加工件来料检验标准自动化设备机械加工件来料检验标准
一、引言
本文档旨在制定自动化设备机械加工件来料的检验标准,确保加工件的质量符合要求,提高产品的可靠性和稳定性。
本标准适用于所有自动化设备机械加工件的来料检验过程。
二、术语定义
2.1 自动化设备:使用机电一体化、信息化等技术,能够实现产业生产过程中的自动化操作的设备。
2.2 机械加工件:通过机械加工方式加工而成的各类零部件。
2.3 来料:指供应商送达生产企业的原材料、零部件或半成品等。
2.4 检验标准:对来料进行检验的规范和要求。
三、检验项目及要求
3.1 尺寸检验
3.1.1 外径测量:要求加工件的外径在允许误差范围内。
3.1.2 内径测量:要求加工件的内径在允许误差范围内。
3.1.3 高度测量:要求加工件的高度在允许误差范围内。
3.2 表面质量检验
3.2.1 表面粗糙度检测:要求加工件的表面粗糙度符合要求的等级。
3.2.2 表面缺陷检测:要求加工件的表面没有明显的裂纹、磨损或划痕等缺陷。
3.3 材料成分分析
3.3.1 化学成分检测:要求加工件的化学成分符合设计要求。
3.3.2 金相组织检测:要求加工件的金相组织均匀、无明显气孔和夹杂物。
3.4 力学性能检验
3.4.1 抗拉强度检测:要求加工件的抗拉强度在允许误差范围内。
3.4.2 延伸率检测:要求加工件的延伸率在允许误差范围内。
四、检验方法
4.1 尺寸检验方法
4.1.1 使用测量仪器对加工件进行尺寸测量。
4.1.2 根据设计图纸要求,对测量结果进行判断。
4.2 表面质量检验方法
4.2.1 使用表面粗糙度仪对加工件表面进行粗糙度检测。
4.2.2 使用目视和触摸等方法对加工件表面进行缺陷检测。
4.3 材料成分分析方法
4.3.1 采用化学分析方法对加工件的成分进行检测。
4.3.2 采用金相显微镜等设备对加工件的金相组织进行检测。
4.4 力学性能检验方法
4.4.1 使用拉伸试验机对加工件进行抗拉强度检测。
4.4.2 使用延伸试验机对加工件进行延伸率检测。
五、检验记录与报告
5.1 对每批来料进行详细记录,包括检验项目、检验结果等内容。
5.2 对符合要求的来料进行入库,并检验报告。
5.3 对不符合要求的来料进行处理,并记录处理结果。
附件:
1.设备测量仪器清单
法律名词及注释:
1.适用于本标准的法律名词及注释。
2.相关法律法规的引用和解释。