常减压塔顶系统腐蚀控制
常减压装置塔顶腐蚀原因分析及防护策略研究

常减压装置塔顶腐蚀原因分析及防护策略研究常减压装置是炼油加工的重要工序,常称之为龙头装置。
随着炼油装置的大型化发展,我国的原油储量已经无法满足生产需求,多数采用国外原油混炼。
由于国内油井的枯竭,因此采用国外原油,而国外原油含硫,盐量较高,加快了塔器的腐蚀速度。
本文针对常减压装置塔顶腐蚀的原因进行分析,同时提出了有效地防护措施。
标签:常减压装置;塔顶腐蚀;原因分析目前,石化行业的工艺变得越来越复杂,需要在高温和高压的环境下作业,在这种情况下,各种工艺设备发生腐蚀越来越常见。
在实际的生产过程中,常减压是炼厂的第一道加工工序,由于原油的性质劣化,导致常减压装置腐蚀情况越来越严重。
1常减压装置塔顶腐蚀的原因分析1.1电化学腐蚀电化学腐蚀是导致减压装置塔顶腐蚀的一个重要原因,原油中含有很大含量的盐,在加工过程中,这些盐会溶解在水中,发生水解产生大量的氢离子,另外,原油中含有的H2S溶解在水中也会电离出大量的氢离子,发生电极反应。
阳极反应会使金属电离成金属离子,而在阴极,则会发生一系列的析氢反应,电离出大量的氢离子。
在酸溶液中,还会发生氧化还原反应,生成氢氧根离子,同时出现金属沉积。
如果有氧化物存在,发生电化学腐蚀的速度会加快。
阳极:M=M2+ne,阴极:①析氢:2H+2e=H2,②氧还原(酸溶液):O2+4H++4e=4OH-,③氧还原(中性或碱性溶液):O2+2H2O+4e=4OH-,④金属离子还原:M3++e=M2+,⑤金属沉积:M++e=M。
1.2化学腐蚀减压装置塔顶腐蚀的一个重要因素就是化学腐蚀。
在炼油过程中,原油中含有大量的无机盐,包括NaCl、MgCl2和CaCl3等,并且这些无机盐会跟随者水被带入到蒸馏塔中,当达到一定的温度,就会发生水解,最终生成氯化氢、硫化氢等。
原油中也含有一定的硫化氢,这些硫化氢会和生成的硫化物发生分解。
经过一定的化学反应,生产工艺中会生成大量的硫化物和氯化氢,在加热的条件下,会发生反应,生成硫化氢气体,这些气体会跟随者挥发的原油进入到分馏塔顶部和冷凝冷却系统中。
减压塔顶空冷腐蚀原因分析及对策

一套常减压装置减压塔顶空冷腐蚀原因分析及对策(扬子石化炼油厂常减压车间 张崇林)一套常减压装置建成于1987年,为燃料-化工型装置,减压塔为全填料干式蒸馏塔,目前加工能力350万吨/年,以加工鲁宁管输原油为主,掺炼部分进口原油。
一套常减压装置减压塔塔顶采用三级蒸汽抽真空系统,其后冷器全部采用表面喷淋的湿式空冷。
2011年3月因气体脱硫装置压缩机频繁出现析硫堵塞现象,分析常减压装置瓦斯成分时发现减压塔塔顶瓦斯氧含量偏高,随之对常减压的瓦斯成分进行分析,其中一套常减压减顶瓦斯氧含量为10%左右。
在随后进行的水压查漏过程中发现减压塔顶一级冷凝空冷片存在大面积腐蚀穿孔现象。
1 原因分析 1.1 腐蚀特点减压塔塔顶共有三级空冷,其中第一级空冷入口采用注氨水、缓蚀剂和洗水的工艺防腐措施,由于从减压塔中蒸发出的HCl 主要溶解在第一级空冷的冷凝水中,形成腐蚀,因此第二、三没有采取“三注”的工艺防腐措施。
减压塔顶第一级冷凝器有8片空冷,全部为2008年投用。
减顶空冷腐蚀主要有以下几个特点:一是腐蚀速度快。
2010年9月装置进行大修后开车,蒸汽试压过程中,没有发现空冷腐蚀穿孔现象。
至2011年3月装置运行仅半年,出现了大面积空冷腐蚀穿孔现象,腐蚀速度较检修前大幅度上升。
二是腐蚀部位主要集中在离空冷入口0.5-1.0m 处,且外喷淋侧腐蚀减薄更严重(如图1.1.1和图1.1.2)属于典型的露点腐蚀。
三是腐蚀表面不均匀,以槽蚀、坑蚀为主。
1.2 减顶切水铁离子含量的异常攀升图1.2.1统计了2010年9月装置检修后开工至2011年3月31日的减压塔顶冷凝水(以下称减顶切水)铁离子含量,趋势显示自检修后开车,减顶切水铁离子长期高于5mg/l ,尤其是2011年初开始塔顶切水铁离子波动幅度增加,且最高可达25 mg/l 左右,减顶切水的分析数据显示塔顶冷凝系统的腐蚀明显加剧。
喷淋侧减薄更严重图1.1.2 基管腐蚀减薄示意图图 1.1.1 对剖的空冷基管图1.2.1 减压塔塔顶排水铁离子变化趋势1.3 氯化物、硫化物对减顶腐蚀的影响常减压装置蒸馏塔顶的腐蚀以HCl-H2S-H2O腐蚀为主,其中HCl来源于原油中CaCl2、MgCl2等无机盐的水解,以及原油中有机氯的分解,H2S主要是原油中的硫化物分解而来。
常减压塔腐蚀状况及防腐蚀对策

常减压塔腐蚀状况及防腐蚀对策摘要:大部分进口原油均是含硫、高硫原油和高酸原油。
由于长期加工该种原油,严重影响常减压蒸馏装置设备的正常运行,许多装置因腐蚀减薄而引起泄露、火灾或非计划停工,特别是高温部位尤其严重,直接威胁着常减压蒸馏装置的安全生产,对长周期运行造成极大的隐患。
因此需要加强对常减压塔腐蚀状况及防腐蚀对策分析。
关键词:减压塔;腐蚀因素;防腐对策前言常减压蒸馏装置是对原油进行蒸馏加工的装置,利用原油混合物中汽油、煤油、柴油、蜡油、渣油等物质沸点的不同,将其分离,并提供给二次加工装置。
因此,常减压蒸馏装置的处理量往往也代表着炼油厂的处理量,在炼油厂中处于至关重要的位置。
近年来,原油的劣质化让国内炼油厂加工高硫高酸原油的比例越来越大,使得常减压蒸馏装置的腐蚀问题日益突出,严重影响了常减压蒸馏装置乃至整个炼油厂的长周期安全稳定运行。
对设备进行腐蚀调查,并将调查结果汇总后进行分析,以便于设备的日常维护与定期检修,并给本领域技术人员提供参考。
1常减压塔概述1.1常减压塔的原理常减压塔的工作原理基于物理学中的节流原理和相分离原理。
当高压气体或流体通过减压阀进入减压塔内部时,流体经过节流装置,使其速度增加,而压力则降低。
随着流体的流速增加,其动能增大,从而减小了静压能,实现了压力的降低。
在减压塔内部,由于压力的降低,液相和气相发生相分离作用,液相被留在塔底,气相则从塔顶排出。
1.2常减压塔的结构组成(1)塔体:常减压塔通常采用立式圆筒形结构,具有足够的强度和密封性。
塔体内部设有塔板,用于引导流体进行分离。
(2)塔板:位于常减压塔内的水平平台,通过塔板上的孔洞来引导和分离流体。
常见的塔板类型有穿孔板、筛板等。
(3)减压阀:常减压塔中的减压阀用于限制流体进入塔体的流速,并实现压力的降低。
减压阀可以采用多种类型,如活塞式、膜片式等。
(4)进料装置:用于将高压气体或流体引入常减压塔内,通常由进料管道、阀门和控制系统组成。
常减压装置的腐蚀与防护分析!

原油之所以对装置具有一定的腐蚀性,主要是因为其中含有一定的盐、硫物质。
我国油田油品含有较高的硫,进口原油往往高酸高硫,所以原油生产中,常减压装置时刻处于腐蚀环境中。
另外石化工艺流程复杂,在高温高压环境中,腐蚀性介质可能会发生一系列化学反应,给设备带来更加严重的腐蚀环境。
实际化工生产中,常减压装置通常被作为第一加工装置,原油劣质化问题会首先反映到这类设备中,同时常减压设备会对原油进行脱盐脱硫处理,其工作效率也决定了原油是否会对后续设备带来腐蚀性影响。
可以说,加强对常减压装置腐蚀问题的分析,对于保持整套设备平稳运行具有积极的意义。
1、常减压装置中常见的腐蚀介质(1)化工腐蚀介质中,氯化物是非常常见的一种,原油经过初步的脱水处理后,依然会有少量的水残留下来,残留水分一般含有由氯化物构成的盐类成分,比如,氯化钠、氯化镁、氯化钙等,这些盐类成分受热后,会发生化学反应—水解反应,产生氯化氢,氯化氢具有强腐蚀性。
(2)硫化物也是一种常见的腐蚀性介质,一般来说,硫化物的腐蚀性的发挥往往受环境温度因素的影响。
原油中所含有的硫化物一般具有不稳定性,如果环境温度升高,这类硫化物就会分解生成分子量相对较小的硫化物。
原油生产中,元素硫与硫化氢之间可以相互转化,在转换过程中,硫化物分布在装置的不同部位,比如具有强腐蚀性的硫化氢一般聚集在装置低温部位,而硫元素则聚集在装置的高温部位。
(3)除了上述两种腐蚀性物质,有机酸、游离状态的氧、二氧化碳、水也会对常减压装置造成腐蚀性影响。
2、常减压装置腐蚀类型2.1 低温露点腐蚀引起这类腐蚀的主要原因是原油中含有盐类成分,主要发生在常减压蒸馏塔顶管部位以及初馏塔。
原油生产加工中,原油中的盐类物质发生水解反应,生成氯化氢,比如:在系统中,如果HCl以气体形式存在,其具有的腐蚀性几乎可以忽略,但是当氯化性进入到冷凝区后,遇到水,迅速溶于水形成稀盐酸,经测定,冷凝区域的稀盐酸浓度处于1%-2%,对于设备来说,系统内部就形成了强酸性腐蚀环境,继而给系统带来严重的腐蚀性影响。
5.5Mt/a常减压蒸馏装置常压塔塔顶冷凝系统防腐技措

向浮 阀塔板 。其 中顶 部 4层 塔 盘 材 料 为 0 r3 Cl ,
塔 内件 材料 为 0 Cl N l Mo , 顶 封 头 以及 壳 0 r7 i 4 2塔 体材料 均为 1 M R+ C l A 6 n 0 r3 L复合 钢板 。
的混合 比为 20 2 0 5 。混 合 原 油 、 疆 原 油 、 7 :3:0 北 南 疆 原 油 和 吐 哈 原 油 的 性 质 见 表 1 。 表 1数 据 表 明 , 合 原 油 的 酸 值 为 1 2 混 .6 m K H g 硫 的 质 量 分 数 为 0 4 % , 疆 原 油 的 gO / , .3 北
原 油 最 高 酸 值 和 最 大 硫 含 量 情 况 下 , 设 备 以 及 对
工 艺 管 线 所 造 成 的腐 蚀 。
温度
压力
12 3 ℃
6k a 0 P
{ 高 尚 , ,9 1年 1 男 18 O月 生 , 理 工 程 师 。 甘 肃 省 兰 州 市 ,3 0 0 助 70 6 。
ቤተ መጻሕፍቲ ባይዱ
48 9 H, S含 量 00 % ( 量分数 ) .5 质
化
工
机
械
21 0 1年
冷器管 束采用 2 0 2 5双 相钢 。
硫含 量
酸值
0 0 42 % ( 量 分 数 ) .0 6 质
0 06 K . 1 mg OH/ g
表 2 塔顶设 备选型 选材参数
2 1 设备 防腐 .
注 : 中所 有 含 量 均 为 庾 量 分 数 。 表
2 防 腐 技 措
常 压 塔 塔 顶 冷 凝 系 统 存 在 较 为 严 重 的 低 温
炼油常减压装置常顶系统腐蚀分析及防护
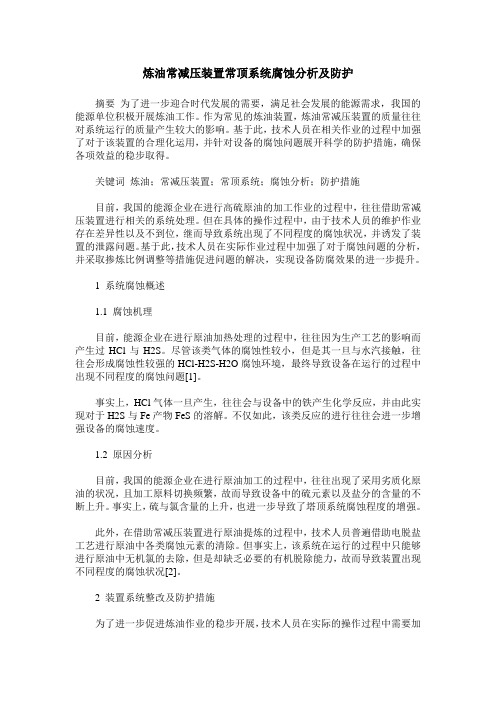
炼油常减压装置常顶系统腐蚀分析及防护摘要为了进一步迎合时代发展的需要,满足社会发展的能源需求,我国的能源单位积极开展炼油工作。
作为常见的炼油装置,炼油常减压装置的质量往往对系统运行的质量产生较大的影响。
基于此,技术人员在相关作业的过程中加强了对于该装置的合理化运用,并针对设备的腐蚀问题展开科学的防护措施,确保各项效益的稳步取得。
关键词炼油;常减压装置;常顶系统;腐蚀分析;防护措施目前,我国的能源企业在进行高硫原油的加工作业的过程中,往往借助常减压装置进行相关的系统处理。
但在具体的操作过程中,由于技术人员的维护作业存在差异性以及不到位,继而导致系统出现了不同程度的腐蚀状况,并诱发了装置的泄露问题。
基于此,技术人员在实际作业过程中加强了对于腐蚀问题的分析,并采取掺炼比例调整等措施促进问题的解决,实现设备防腐效果的进一步提升。
1 系统腐蚀概述1.1 腐蚀机理目前,能源企业在进行原油加热处理的过程中,往往因为生产工艺的影响而产生过HCl与H2S。
尽管该类气体的腐蚀性较小,但是其一旦与水汽接触,往往会形成腐蚀性较强的HCl-H2S-H2O腐蚀环境,最终导致设备在运行的过程中出现不同程度的腐蚀问题[1]。
事实上,HCl气体一旦产生,往往会与设备中的铁产生化学反应,并由此实现对于H2S与Fe产物FeS的溶解。
不仅如此,该类反应的进行往往会进一步增强设备的腐蚀速度。
1.2 原因分析目前,我国的能源企业在进行原油加工的过程中,往往出现了采用劣质化原油的状况,且加工原料切换频繁,故而导致设备中的硫元素以及盐分的含量的不断上升。
事实上,硫与氯含量的上升,也进一步导致了塔顶系统腐蚀程度的增强。
此外,在借助常减压装置进行原油提炼的过程中,技术人员普遍借助电脱盐工艺进行原油中各类腐蚀元素的清除。
但事实上,该系统在运行的过程中只能够进行原油中无机氯的去除,但是却缺乏必要的有机脱除能力,故而导致装置出现不同程度的腐蚀状况[2]。
常压塔顶低温轻油部位腐蚀原因分析及对策

随着 加 工原 油 的硫含 量 及 酸值 的升 高 , 炼厂 设
属含硫含酸原油。在 2 1 年大修腐蚀检查工作中 , 00 发现常压塔顶系统低温轻油部位的腐蚀问题较为突 出, 如常压塔顶西侧塔壁塔盘条形浮阀断裂 、 脱落严 重, 塔顶 回流分布管主管处法兰垫片已腐蚀殆尽 , 两 侧弯头存在细小裂纹 ; 塔顶油气挥发线直管与第二 弯头东侧焊缝连接处存在 O 0 半 圆形 区域腐蚀减 30 薄 。图 1 图 6 一 所示分别 为塔顶塔盘、 回流分布 顶 管南侧弯头 、 管束 、 塔顶挥发线、 常顶冷凝器 E 1 2 C0、 E 11 C 2 的腐蚀形貌 。常顶冷凝器 E 2 / ~4 11 1 管束 外锈蚀 严 重, 体 布满 蚀 坑, 部 坑深 较 重, 基 局 E 2/ C112管束 测厚 检 查 减 薄 较 重 , 薄 量 约 为 0 2 减 . O 3mm; . 常顶 空气 冷 却 器 E 0 / C121第 1排 左 数 第 1 根和 E 1 24 1 4 C 0 / 第 排左数第 1 4根翅 片管腐 蚀穿孑, L造成 大 量 的常顶油 气泄 漏 , 重影 响了装 置 严
常减压装置常压塔塔顶系统腐蚀失效分析与防腐
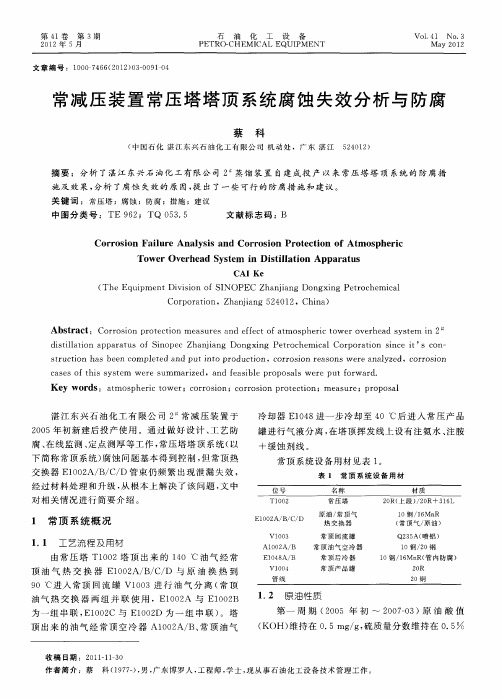
c s soft i y t m r u a e h s s s e we e s mm a ie rz d,a e sbl r os l r or r . nd f a i e p op a s we e putf wa d
K e r s a m o p e i o r o r so y wo d : t s h rc t we ;c r o i n;c r o i n p o e to o r so r t c i n;me s r ;p o o a au e rp sl
经 过材料 处理 和升 级 , 根本 上解决 了该 问题 , 中 从 文 对 相关情 况进 行简 要介 绍 。
常顶 系统设 备用 材见 表 1 。
表 1 常 顶 系统 设 备 用 材
l 常顶 系统 概 况
1 1 工艺 流程 及用材 . 由常压 塔 T1 0 0 2塔 顶 出来 的 1 0℃ 油 气 经 常 4
顶 油 气 热 交 换 器 E 0 2 B C D 与 原 油 换 热 到 1 0 A/ / /
9 0℃进 入常 顶 回流 罐 V1 0 0 3进 行 油 气 分 离 ( 顶 常 油气 热 交 换 器 两 组 并 联 使 用 ,E 0 2 与 E1 0 B 10A 02 为一 组 串联 , 0 2 E1 0 C与 E 0 2 为一 组 串联 ) 10 D 。塔 12 . 原油性 质 第 一 周 期 ( 0 5年 初 ~ 2 0 —3 原 油 酸 值 20 0 70 )
s r c i a e o p e e nd puti o p o c i n,c r o i e s ns we e a l z d,c r o i n t u ton h s be n c m l t d a nt r du to o r son r a o r na y e o r so
- 1、下载文档前请自行甄别文档内容的完整性,平台不提供额外的编辑、内容补充、找答案等附加服务。
- 2、"仅部分预览"的文档,不可在线预览部分如存在完整性等问题,可反馈申请退款(可完整预览的文档不适用该条件!)。
- 3、如文档侵犯您的权益,请联系客服反馈,我们会尽快为您处理(人工客服工作时间:9:00-18:30)。
收稿日期:2003-09-09;修稿日期:2004-03-08。
作者简介:邵建雄(1958-),男,浙江宁波人。
1982年毕业于浙江工业大学化机专业,现任镇海炼化公司副总经理。
常减压塔顶系统腐蚀控制邵建雄(镇海炼油化工股份有限公司,浙江宁波315207)摘要:在原油加工品种杂(既有高硫又有高酸)且切换频繁的情况下,常减压塔顶系统的腐蚀问题仅靠传统方法已很难从根本上解决。
镇海炼油化工股份有限公司一方面采取原油混炼措施,另一方面,采用最新的腐蚀在线监测方法和建立塔顶系统的离子平衡模型及时调节缓蚀剂、中和剂的投加量与注水量,最终使该系统的腐蚀得到有效控制。
关键词:混炼 腐蚀在线监测 离子平衡模型 缓蚀剂 中和剂中图分类号:TE985.9 文献标识码:A 文章编号:1007-015X (2004)03-0016-03 镇海炼油化工股份有限公司自1994年首次尝试加工伊朗轻质原油获得成功后,以中东原油为主的含硫或高硫原油的加工量保持逐年增加的势头:2000年共加工原油10.72Mt ,其中中东原油4.03Mt ;2001年加工原油10.72Mt ,其中硫含量大于1.5%的原油超过4.98Mt (平均硫含量1.123%),平均酸值为0.529mgK OH/g ,酸值大于 1.0mgK OH/g 的原油超过2.30Mt (酸值最大的是罗凯利亚原油,达3.4mgK OH/g );2002年加工原油11.89Mt ,其中硫含量大于1.5%的原油超过6.06Mt (平均硫含量1.11%,平均酸值0.429mgK OH/g ),酸值大于1.0mgK OH/g 的原油超过1.90Mt 。
中东原油的加工在拓展该公司原油采购渠道、提升原油加工量、降低原油成本和提高经济效益等方面均起到了重要作用。
但是,大量加工高硫及高酸原油,加上原料切换频繁,使设备、管道的腐蚀日趋严重,设备防腐蚀管理工作难度加大。
常减压蒸馏装置作为炼油的龙头装置,首当其冲经受着严峻的考验。
这些年来,公司从原油的加工工艺、腐蚀在线监测到在线腐蚀控制等方面做了大量有效的工作,取得了可喜的成效。
1 优化含硫原油加工工艺路线镇海炼油化工股份有限公司加工的含硫或高硫原油主要有伊朗轻质、伊朗重质原油以及沙特轻质、沙特中质和沙特重质等原油。
几年来,通过多次技改和不断完善,目前已初步形成具有自身特点的加工流程。
加工流程的主要特点为灵活加氢裂化-催化裂化组合、焦化-CF B 锅炉一体化和产品全加氢精制工艺等。
在一次加工中,含硫或高硫原油的加工采取混炼方案,这样可降低原油硫含量。
须注意的是要避免与酸值较高的原油混炼,以防止高硫和高酸值产生共同效应加剧对设备的腐蚀。
沙特中质原油因其减压渣油是生产1号高等级道路沥青的好原料,则采用单炼方案。
由于加工流程中没有渣油加氢脱硫装置,同时脱碳工艺的能力占了相当大的比例,因此高硫渣油主要是通过焦化装置消化,部分作为生产道路沥青原料或作燃料油出厂。
焦化装置在处理高硫渣油时,所生产的蜡油进加氢裂化、精制装置处理后供催化裂化装置作原料,高硫焦则作为CF B 锅炉燃料。
另外,在催化裂化加工时,为均衡原料的硫含量、满足产品质量要求,适当掺炼一些低硫蜡油。
2 含硫原油加工过程的工艺防腐蚀低温部位的工艺防腐蚀措施重点在一次加工装置,并应继续坚持做好传统的“一脱三注”工艺防腐蚀。
近年来在电脱盐方面引进了BAKER PETRO LITE 公司的电脱盐专利技术,先后在Ⅲ套和Ⅰ套常减压蒸馏装置上应用,其技术关键是在原油分配器的结构设计及原油进入电场的位置确定上,专 论 石油化工腐蚀与防护C orrosion &Protection in Petrochemical Industry2004,21(3)・16・其特点是高速分配和低停留时间,适合密度、粘度范围较宽的原油脱盐。
目前该设施运行稳定,是值得推广的电脱盐技术。
在破乳剂的筛选方面,先是筛选出适合含硫或高硫原油加工的NS-21及NS -31破乳剂,在Ⅰ套和Ⅱ套装置上使用,后来又选用BAKER PETRO LITE公司的E-2714破乳剂在Ⅲ套装置试用,对轻质和重质原油均有较好的脱盐效果。
另外,选用油溶性缓蚀剂以替代20余年一直不变的水溶性缓蚀剂,在注氨的同时注入一定量的有机胺中和剂以调节pH值。
Ⅰ套装置从2000年12月底起使用了国产SF-121B缓蚀中和剂,Ⅲ套装置使用了BAKER PETRO LITE公司的E-8237有机胺中和剂。
2001年还对Ⅲ套装置进行了包括在塔顶每一组换热器分支都增加注入系统并增加分配器保证油溶性缓蚀剂均匀注入的改造,使工艺防腐蚀设施进一步完善。
3 腐蚀在线监测技术的应用从国外管理先进的炼油厂所采取的腐蚀监测措施以及国内的经验来看,对装置的设备与管道进行大规模定点测厚,是一项行之有效的措施。
定点测厚可以避免其它几种腐蚀监测手段的局限性。
例如:电阻探针,使用温度受到较大限制;极化电阻法腐蚀速率测定仪,只适用于电解质溶液;旁路釜,监测面较窄;挂片试验,只能在大修期间放入和取出。
而超声波测厚具有简单、可靠、直接、全面的优点,可以监测设备与管道的均匀腐蚀和冲刷腐蚀。
公司从1996年开始进行装置定点测厚的研究与试验工作,目前定点测厚工作已经覆盖主要炼油生产装置。
电感探针是通过测量敏感元件的阻抗变化来测定腐蚀速率的。
与具有类似形状的电阻传感器的电阻值2~60mΩ相比,电感阻抗的数值可达到1~5Ω。
因此,若采用与电阻探针法相类似的测量准确度(±2/3μΩ)来衡量,则电感探针的响应时间可由几天缩短至几十甚至十几分钟,分辨率可提高100~2500倍。
所以说,电感抗法是把线性极化方法的快速响应和电阻探针方法的广泛适用的优点结合起来,克服了它们各自的不足之处,使得快速准确地测量腐蚀速率成为可能。
III套常减压塔顶系统的腐蚀主要集中于常顶热交换器E102与常顶空冷器AC-102,因此监测和控制这两个部位的设备腐蚀显得尤为重要。
在2001年大修期间,在常顶挥发线,E102/GH,E102/ AB及空冷器AC-102入口、出口等五个位置安装了电感探针监测系统,用于快速评价这些部位的腐蚀状况,使用效果较为满意。
目前Ⅲ套常减压常顶工艺防腐蚀采用注栗田公司的油溶性缓蚀剂E1572和有机胺中和剂E8237,缓蚀剂注入量为30kg/d,有机胺中和剂注入量为100kg/d。
从安装在常顶挥发线的电感探针监测到的腐蚀速率数据分析,2001年10月份常顶挥发线位置的碳钢腐蚀速率在逐渐变大,取10月20日8点至22日8点二天的数据分析,第一天的平均腐蚀速率在0.89mm/a波动,第二天腐蚀速率有上升趋势,最大腐蚀速率为1.17mm/a。
针对腐蚀速率上升情况调整了中和剂量,从2001年11月13日12点至18日8点,中和剂注入量调整为150kg/d;18日8点至20日10点,中和剂注入量调整为200kg/d;20日10点至28日10点,中和剂注入量调整为150kg/d;28日10点以后,中和剂注入量调整为100kg/d。
通过对中和剂量进行调整后,电感探针监测到的腐蚀率也大大降低(最低0.19mm/a)。
经过一段时间的摸索和对各助剂注入量的优化,现常压塔顶的腐蚀已处于受控状态。
除塔顶挥发线的腐蚀速率有个别稍微偏高外,其它各点的腐蚀均得到了有效控制,腐蚀速率在0.0254mm/a左右(控制指标0.254mm/a),说明改进的塔顶工艺防腐蚀方案是成功的。
塔顶注氨存在以下三方面的问题:(1)在常顶一段冷凝中,氨不会与初期冷凝水一同冷凝,NH3与HCl的沸程不同。
有报道认为,常压塔塔顶系统全部的HCl集中在初期冷凝水中,在水的露点温度下,NH3对HCl的中和作用不大,所以仍然有HCl的腐蚀作用。
V-02切水的pH值一般在5~7,所以注氨解决不了常顶至V-02段初期冷凝的露点腐蚀问题。
(2)稳定的pH值控制对于塔顶系统的腐蚀控制相当重要。
当pH<6时,HCl的腐蚀会很严重;而当pH>8时,H2S的腐蚀作用最强。
因此,塔顶回流罐的pH值应控制在7~7.5的范围内较合适,而使用无机氨作中和剂时,很难将pH值控制在这一范围。
(3)NH3与HCl反应易形成NH4Cl垢堵塞管道。
氯化铵的升华点在350℃,而常顶系统温度远低于这一温度,沉积在塔内和空冷器传热表面上的・71・ 第3期 邵建雄.常减压塔顶系统腐蚀控制 氯化铵,会造成垢下腐蚀。
在不同pH 值的情况下,注氨会与H 2S 形成硫氢化铵和硫化铵,其水解后同样会造成腐蚀。
针对注氨、注缓蚀剂存在的问题,并借鉴法国T OT A L 经验,从1998年8月开始改注有机胺中和缓蚀剂,取得了较好的效果。
有机胺为长链烃类胺基化合物,呈弱碱性,热稳定性好。
有机胺注入到物料中即吸附到金属表面形成隔离膜,同时其胺基(-NH 2)能中和物料中的H +形成有机胺盐,其水溶性好,不会产生垢下腐蚀。
4 建立腐蚀离子模型塔顶系统通过添加中和剂以提高凝结液相的pH 值,从而减缓酸腐蚀。
然而,不足量的中和剂可能导致高腐蚀速率使设备失效。
中和剂还会与HCl 反应,在露点前形成盐。
盐垢下的加速腐蚀也会导致设备的失效。
离子平衡模型(I onic Equilibria M odeling )可以正确地指导添加中和剂,使得塔顶系统既不发生酸腐蚀,也不产生垢下腐蚀。
离子平衡模型包括了两个主要方面:第一,利用工艺仿真模型来确定液相中特殊离子(例如:HCl ,NH 3,RNH 2,S O x ,C O 2)的作用;第二,根据相平衡数据确定系统中氨和有机胺的铵盐形成趋势。
应用该模型可以计算出塔顶系统介质露点时的pH 值以及形成铵盐的温度。
根据III 套常减压塔顶系统离子平衡模型及2002年4月24日III 套常减压塔实际操作的数据(见表1)计算表明:塔顶热交换器会出现盐沉积现象;设备损伤的主要原因是盐的垢下腐蚀;为有效地防止腐蚀的发生,需注34t/h 的洗涤水。
表1 常压塔顶工艺数据(2002-04-24) 项 目工艺参数原油处理量/t ・h -1749塔蒸汽量/kt ・h -13221.4回流量/t ・h -1137.5V103/t ・h -164.77V104/t ・h -122.32V104排气/kt ・h -12300塔顶温度/℃138.8TPA 排凝温度/℃225.7TPA 返回温度/℃149.6V103温度/℃89.6V104温度/℃49.6塔顶压力/kPa 101.9V104压力/kPa71.25 结束语腐蚀与防护是石化行业的永恒课题,随着时间的推移以及加工工艺的改进和原油劣质化,腐蚀问题将“日新月异”,因此必须加强腐蚀调查和防腐蚀基础研究,同时采取适宜的腐蚀在线监测和腐蚀控制方法,以减少因腐蚀造成的经济损失。