制程检验控制流程图
HSF制程管制与检验管理程序
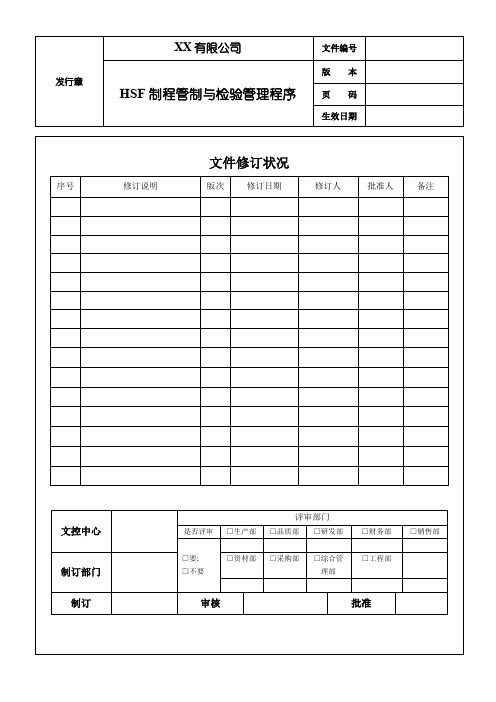
a、新产品每次导入时,由供应商提供有害物质测试报告。
b、每次检测之数据1年内保持有效。
c、供货商提供之有害物质测试报告,由品质部专人维护,在报告到期前一个月MAIL通知采购,由采购通知供应商提供更新有害物质测试报告。如在上一期报告到期日,但新报告还未提供者,则由我司直接送测,送测费用由供货商负担。
6.2.《HSF异常控制程序》
6.3.《HSF产品标识与追溯管理程序》
6.4《风险辨识和评价控制程序》
6.5.《HSF采购管理程序》
7.0.相关记录
7.1《产品批次流转卡》
7.2《质量状态标签》
7.3《生产日报表》
7.4.《首检记录》
7.5.《首件确认单》
7.6.《出货检验报告》
7.7《质量检验记录》
4.流程图:
无
5.程序内容:
5.1进料检验:
5.1.1.品质部进料检验员接到仓库开出的《采购收货报检单》后需核对以下信息:
1)确认供应商是否在《合格供应商名录》中,若不在合格供应商名录中的供应商送货,则及时将现况上报主管,并依照其指示做批退处理。
2)来料HSF标识及外箱标识(来料厂商名称、材料品名及规格、料号)是否清晰及符合我司要求;
文件修订状况
序号
修订说明
版次
修订日期
修订人
批准人
备注
文控中心
评审部门
是否评审
□生产部
□品质部
□研发部
□财务部
□销售部
□要;
□不要
制订部门
□资材部
□采购部
□综合管理部
□工程部
制订
审核
批准
1.目的:
为保证进入我司之所有原材料、辅助材料及出货成品均符合HSF(有害物质限制或消除)管理相关要求,以预防非环保品流入客户端,特制定本程序。
成品检验流程图

成品检验流程图在生产过程中,成品检验是一个至关重要的环节。
它确保了产品的质量,并防止不合格的产品流入市场。
下面是一个成品检验流程图的示例,它概述了成品检验的主要步骤。
1、准备检验设备在开始成品检验之前,需要准备必要的检验设备,包括测量仪器、检测工具、实验室设备等。
这些设备应按照相关规定进行校准和维护,以确保其准确性和可靠性。
2、接收产品从生产线上接收待检验的产品,并将其放在指定的检验区域。
同时,应记录产品的信息,如型号、规格、批次等。
3、检查外观对产品的外观进行检查,包括是否有划痕、瑕疵、变形等问题。
同时,检查产品的完整性,确保没有明显的缺陷或损坏。
4、检查尺寸和形状使用测量仪器对产品的尺寸和形状进行检测,确保其符合设计要求和规格。
对于关键尺寸和形状,应进行详细的测量和记录。
5、检查材料质量对产品的材料质量进行检查,包括材料的硬度、韧性、耐久性等指标。
对于关键材料,应进行实验室测试和分析。
6、检查功能性能对产品的功能性能进行检查,包括开关、按钮、指示灯等部件的功能测试。
确保产品能够在正常条件下运行,并满足设计要求。
7、审核质量文件查阅产品质量文件,包括生产记录、检测报告、合格证明等。
确保产品质量符合相关标准和客户要求。
8、填写检验报告根据检验结果填写检验报告,记录产品的信息、检测数据和评价结果。
检验报告应准确、完整地反映检验过程和结果。
9、审核检验报告对检验报告进行审核,确认检验结果是否符合要求。
如有不合格的产品,应进行返工或报废处理。
10、交付合格产品将合格的产品交付给下一道工序或客户,确保产品质量符合要求并满足市场需求。
成品检验流程是产品质量控制的关键环节之一。
通过实施严格的成品检验流程,可以确保产品的质量符合标准要求,提高产品的可靠性和安全性。
及时发现并处理潜在问题,有助于降低生产成本和减少质量损失。
成品检验流程图的推广和应用有助于提高企业生产效率和产品质量水平,提升企业的市场竞争力。
在任何生产或制造过程中,原材料的检验都是至关重要的环节。
检验与试验管理程序(含流程图)
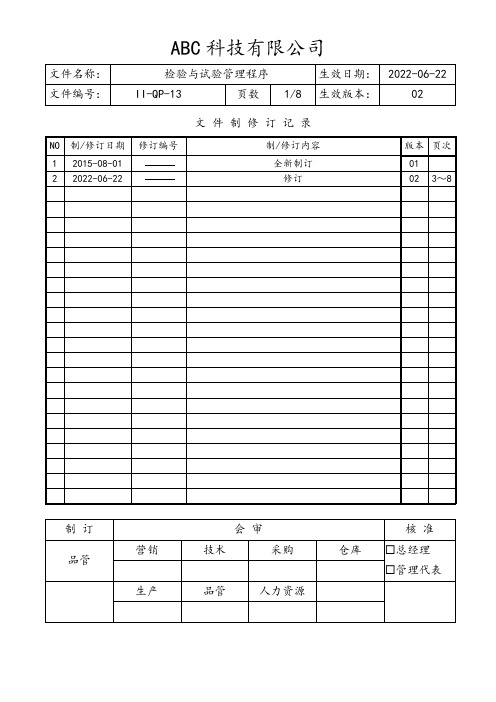
ABC科技有限公司
文件制修订记录
文件编号II-QP-13 页数2/8 生效版本02
1.目的:
规范检验流程及标准,使公司的生产、服务提供过程品质得到有效的控制,从而不流入不良品、不制造不良品,不流出不良品。
2.范围:
适用于本公司进料(包括客供料)、制程、成品检验工作和可靠性试验作业。
3.参考文件:
3.1产品防护与出货管理程序
3.2不合格品控制程序
3.3采购与供应商管理程序
4.定义:
4.1可靠性试验:对实现产品功能的保障能力的测试。
4.2首件:每个新订单生产前或生产过程中生产条件发生变化后(5M1E等)所生产的第一或前几件产品。
4.3首检:对首件产品进行检查及确认的过程。
5.责任:
5.1品管:负责来料、制程及成品的检验及标识、试验仪器操作及可靠性实验执行。
5.2生产:负责生产成品的送检,制程不合格情况的改善,将生产成品入库。
5.3仓库&采购:负责来料的送检,不合格品的处理,出货成品的送检;检测单位选定及管理。
5.4工程部:负责检验标准技术文档的提供。
6抽样方案:
文件编号II-QP-13 页数3/8 生效版本02
6.1特殊部件进行全检(例如摄像头等),电子料和线材按0.4抽样,壳料和包材按1.5抽样(若质量问题多则加严抽样)
7.相关记录:
7.1进料检验报告
7.2进料品质异常单
7.3制程巡检报表
7.4首件检验记录
7.5成品检验报告
7.6可靠性实验报告。
IQC--IPQC--FQC--OQC检验控制流程图
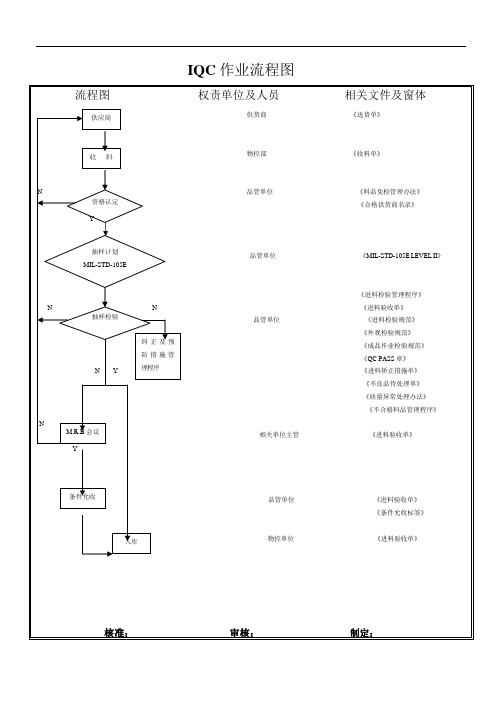
纠 正 及 预防 措 施 管
理程序
IQC 作业流程图
流程图
权责单位及人员
相关文件及窗体
供货商
《送货单》
物控部
《收料单》
N
品管单位
《料品免检管理办法》 资格认定
Y
《合格供货商名录》
抽样计划 MIL-STD-105E
品管单位 《MIL-STD-105E LEVEL II 》
《进料检验管理程序》
N
N
《进料验收单》 抽样检验
品管单位
《进料检验规范》 《外观检验规范》 《成品作业检验规范》 《QC PASS 章》 N
Y
《进料矫正措施单》 《不良品待处理单》 《质量异常处理办法》 《不合格料品管理程序》
N
相关单位主管
《进料验收单》
Y
品管单位
《进料验收单》 《条件允收标签》
物控单位 《进料验收单》
核准: 审核: 制定:
供应商
收
料
入库
M.R.B 会议 条件允收
核准:审核:制定:。
制程检验不合格品处理流程图
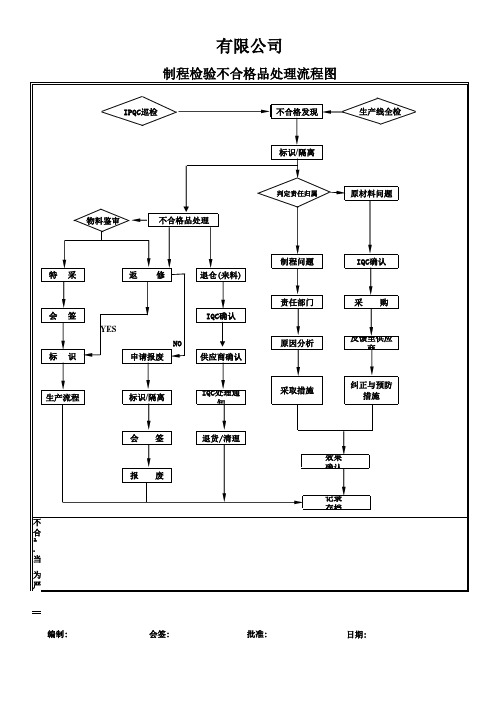
制程检验不合格品处理流程图
IPQC巡检 不合格发现 生产线全检
标识/隔离
判定责任归属
原材料问题
物料鉴审
不合格品处理
制程问题 特 采 返 修 退仓(来料) 责任部门 会 签 YES NO 标 识 申请报废 供应商确认 原因分析 IQC确认
IQC确认
采
购
反馈至供应商
生产流程
标识/隔离
IQC处理通知
采取措施
纠正与预防 措施
会
签
ቤተ መጻሕፍቲ ባይዱ
退货/清理 效果确认
报
废 记录存档
不合格品处理说明: 1.当某项不合格品数量超过“停机整改要求”的条件时,则必须要求生产进行停机调试,当异常较 为严重或必要时须以<品质异常通知单>形通知生产单位停机整改。
编制:
会签:
批准:
日期:
IPQC制程检验流程(流程版)

生产部
品检组
业务
首五件产品量测记录表
异常联络单
IPQC巡回检验记录
作业流程
流程说明
权责
单位
产出
表单
6.5主管不定时地巡回检查,发现问题,要让检验人员清楚问题所在,查找原因,提出改善对策,同时要求IPQC记录于《IPQC巡回检验记录》,并指定跟催确认人回馈最终改善结果,必要时再到现场亲自查实。
5.5 确认成品首件时必须对打好钉的成品进行轮子检验:
5.5.1检验轮子三只脚/外八字:把装好轮子的成品放在一玻璃平面上,转动箱体(需正方向和反方向),观察四个轮子是否完全接触玻璃板,如有轮子未完全接触玻璃板(轮子与玻璃板有空隙或四脚未落地),则视为三只脚. 用手分别转动每个轮子,观察轮子转动是否顺畅,不卡顿,再把箱子放在玻璃板上,观察前后轮子是否在一直线上,观察方法:前左轮对后左轮,前右轮对后右轮,前左轮对前右轮,后左轮对后右轮,如有任意一个轮子不在一直线上,则视为八字脚。
3. 检验标准:
3.1顾客订单资料
3.2业务员(含)以上干部签名确认的样包或顾客提供的样包、原物料确认卡、订单通知与反馈单、顾客原始订单、工艺单,资料单。
3.3《QC工程表》。
4.标准核对步骤:
4.1IPQC根据业务所提供的工艺单逐步核对两者的物料名称、规格、颜色、配色是否正确,如两者无误时,以工艺单做为标准核对大货及样包。
一 范围:
产品试做、过程品质控制,成品首件检验、关注新产品上线成品品质,跟催确认品质改善。
二 参考文件:
2.1 QC工程总表PB-G-001
三术语和定义:
3.1检验标准:业务员(含)以上干部签名确认的样包或顾客提供的样包、原物料确认卡、订单通知与反馈单、顾客原始订单、工艺单,资料单。
制程检验流程
1.《制程抽检记录表》
2.《制程巡检记录表》
3.检验结果分析与判定
3.1质检专员对检验数据进行分析
1.《制程抽检记录表》
2.《制程巡检记录表》
3.2质检专员在分析检验数据的基础上,同企业的制程质量要求进行比较,判断是否存在问题,包括工艺问题、流程问题及人员问题等
《制程复检记录表》
7.编制质量报表与存档
7.1 质检专员根据检验和复检情况编制《质量报表》报质量管理部经理审核,报表内容包括检验的数据、存在的问题、整改措施及整改后发生的改变等
《质量报表》
7.2 质检专员将常规检验和复检过程中所形成的各种文件进行归档保存,包括《质量报表》及《数据记录单》等,以便查找和调用
制程检验流程
工作目标
知识准备
关键点控制
细化执行
流程图
1.监督生产的各环节,防止存在质量隐患发生
2.保证产成品质量,减少不合格品出现,降低生产成本
3.按照规定的程序进行,保持良好的生产环境
1.企业质量管理的相关规定
2.产品质量标准及检验规范
3.工序质量控制的各类图示法
1.制程检验准备
每一型号的新产品投产时,质量工程师规定制程品质检验点、检查项目及检查方法等,作为制程质量检验的操作依据。各岗位质检员要熟悉各资料文件,保证制程检验的准确性
质量检验的各项文件资料
1.产品质量检验操作规程
2.《质量检验日程表》
3.各阶段产品质量标准
2.实施常规检验
2.1质检员根据生产计划和生产进度在既定时间和地点对制程质量实施常规检验,主要内容包括工艺流程查核、计量仪器检验、作业人员作业标准指导等,常用的检验方法包括首件检验、抽样检验和巡回检验等
制程控制程序
(六)检验判定不良品按照「不合格品管理程序」办理。
(七)检验各阶段特采判定申请、核准,按照「检验与测试管理程序」办理,并进行生产过程跟踪。
6.原料批量号纳入生产表单,增设原(辅)材料追溯记录表管理运行,记录由品管存档以备追溯查看。
八、附件:
(一)各工艺记录表;
(二)换线清场点检表;
(三)原(辅)材料批号追溯记录表;
(四)模具保养表;
(五)生产责任追踪单;
(六)试样工艺记录表;
(七)样品制程记录表;
(八)样品检验报告单;
(十一)其它相关制程控制:
1.生产现场工作区域,各类产品(原料、产出品、待加工品、模具、工具等)按区域堆放与生产现场无关的产品必须及时清理出生产现场并在换线时填写《换线清场点检表》;
2.生产现场通道应保持畅通;
3.生产各主管负责生产现场工作环境的管理;
4.不良品应与合格品隔离或标示,避免误用;
5.进入厂房应更换工作鞋,工作服及戴工作帽(或一次性鞋帽),四楼装配车间需加配戴口罩,进入车间应经过风淋室,维持车间洁净的作业环境。
(八)机修应对/模具管理程序执行。
(九)成品的鉴别、储存、包装、防护、流转下工序或出货都能够完好无异常。
(十)生管文员应定期收集车间各项生产日报数据,进行每日、每月统计,并完成统计报表提交生管/生产部门主管审查,作为生产管理的信息依据。
(五)相关检验规范;
(六)相关工艺作业标准书
(七)检验与测试管理程序;
QC process chart
成品检验
Finish product
inspect
OK 入库、入帐 Input、chalk it up
NG
OK
发出出货通知 Inform ship
OQC
NG
FQC 组长
确认
FQC
leader
confirm
定期巡仓 Random
Inspection
regularly
NG
NG
复检
recheck
OK
OK
备货
Prepare goods
必要时 If necessary
安排交付 Plan delivery
抽检
NG
Sample
inspect
OK
标识盖合格章,附 出货检验报告
Sealing chapter, Attached OQC
report
不合格品 reject
结束 End
不合格品 reject
按《不合格品 控制流程》
调机/调油/调色/调拉 Debug machine/
paint/mix colors /line
取样 rm first sample
必要时
If ecessary
尺寸检测 Dimension measurem
ent
标识、防护、保管 Mark\ fence\save
制程品质控制流程图ipqcprocesschartproduceleader生产组长operater作业员technician技术员ipqcleadersurveyor测量员首件确认confirmfirstsample签名贴合格首板标签signandstickthelableofpassfirstsampleng调机调油调色调拉debugmachinepaintmixcolorsline标识防护保管markfencesave培训作业员trainingoprator取样sampling接收首板receivedfirstsample安排生产planproduce巡检randominspectionok开始startokng照计划排机拉arrangemachinelineaccordingtoplan尺寸检测dimensionmeasurementokng自检selfinspection尺寸检测可靠性测试dimensionreliabilitytestng成品待检finishproductwaitingforinspect结束end必要时ifnecessary必要时ifecessaryok按成品品质控制储存和交付流程implementingoqccontrolprocedure按不合格品控制流程implementingrejectproductcontrolprocedure不合格品reject3
制程检验作业流程图
制程检验作业流程流程图1.0目的为保证产品在生产制程中得到有效检验作业,控制制程品质,降低制程返工、报废,提升产品合格率,提高不良出来的时效性,特制定本作业流程。
2.0 范围适用于(备料车间、白身车间、油漆车间、包装车间)生产过程中的检验与控制及不良品处理。
3.0 职责3.1 PMC部:计划课负责生产指令的下达,参与生产异常处理;仓务课负责完成不良品的回仓分类保管、标识确认及不良品退料的督促工作。
3.2 各生产车间:负责制程产品材料确认,首件产品品质确认及生产过程中的自检、互检工作。
反馈、参与生产异常处理;3.3品管部:首件产品确认及生产过程中的巡检、完工后检验,反馈、主导或参与品质异常处理工作,并对数据记录保存、统计、分析、改善,持续改善;3.4 相关部门:主导或参与品质异常处理及异常分析工作。
4.0 作业程序4.1 PMC部下发《生产日计划》给各生产车间主管,各生产车间主管根据《生产日计划》,组织安排操作工做好生产前的准备工作;4.2 各车间组长、技术员准备工装夹具、测量量具、签样等,按样品或产品工程作业标准书等准备物料进行生产。
备料、白身、总装车间:工装夹具、测量量具、签样、作业指导书、图纸、模具等。
油漆车间:色板、签样、作业指导书、图纸等。
包装车间: 签样、作业指导书、图纸、产品包装示意图、模具等。
4.3组长、技术员对首件先自检,合格报制程检验员对首件进行检验,详细参考《首件检验控制卡》。
4.4制程检验员全检或按规定频次(正常情况下每天不少于6次)及工艺图纸等要求巡检各工序制程品质状况,巡检要有相关侧重点,填写巡检记录,若不符图纸和工艺要求,则知会操作员异常状况;当生产操作工自检发现不良现象时及时隔离和标识;当产生不良品超标时,发现人即时通知本组组长到现场确认,组长到现场确认后,按《生产异常提报控制卡》进行操作,必要时组长填写《品质异常报告和处理单》交责任单位处理(来料引起的不良交品管部处理;制程引起的不良交本部车间主管处理)。
- 1、下载文档前请自行甄别文档内容的完整性,平台不提供额外的编辑、内容补充、找答案等附加服务。
- 2、"仅部分预览"的文档,不可在线预览部分如存在完整性等问题,可反馈申请退款(可完整预览的文档不适用该条件!)。
- 3、如文档侵犯您的权益,请联系客服反馈,我们会尽快为您处理(人工客服工作时间:9:00-18:30)。
《首件确认书》
IPQC 巡回检查
颜色、外观、尺 寸、功能、强度、 包装、组装
《纠正与预防措施 报告》 《QC 巡检记录表》
不合格品依据 《不合格品控 制程序》处理
合格品 / 检验入 库
版 本 A/1
首件检验 在每批产品生产或 因某种原因再生产 时,首件自检合格 后填单 进行尺寸、外观、 材质、结构,组装 等检验后填单 品质部另外复制 样板悬挂于品检 员工位,生产结 束后品质部要将 首件板妥善保存
深圳瑞捷金富科技有限公司
制程检验控制流程图
《首件确认书》 各生产单位
不合格 IPQC 合格 生产按照Байду номын сангаас品生产