渐开线齿轮设计计算书04784
渐开线齿轮齿廓范成实验- 机械设计基础

渐开线齿轮齿廓范成实验- 机械设计基础渐开线是一种齿廓曲线,具有相对滚动过程中齿面接触良好、传动精度高等优点,广泛应用于各种机械传动中。
齿轮是渐开线的常见应用,而齿轮的齿廓设计对保证传动的性能至关重要。
本文将介绍渐开线齿轮齿廓的范成实验流程及方法。
渐开线齿轮齿廓的范成实验主要依据以下原理:1.渐开线齿轮齿廓曲线的方程若一个圆在另一个圆内滚动,且同时保持两圆心之间距离不变,则圆上某点的轨迹为渐开线。
圆的轨迹称为基圆,而另一圆称为从动圆。
若基圆为圆柱,从动圆为齿轮,则圆心所在直线即为两齿轮轴线。
令Z1和Z2分别为主动轮和从动轮的齿数,d1和d2分别为主动轮和从动轮的分度圆直径,则渐开线方程为:x=a(θ-sinθ)其中a=d1/2,θ为参数,s=Z2/Z1,实际计算时一般采用插齿法进行计算。
2.插齿法插齿法也称为逐齿法,主要用于推导渐开线齿轮齿廓。
其基本思想是从基圆上一点出发,逐步向定轴方向平移,并将平移轨迹图转换为从动轮上的齿廓。
1.确定齿轮参数在进行齿轮齿廓范成实验前,需要先确定齿轮的参数,包括齿数、分度圆直径、法向压力角等。
一般情况下,齿轮的参数由机械设备工程师根据实际需求进行设计。
2.绘制齿轮的CAD图根据齿轮的参数绘制齿轮的CAD图,使用CAD图软件或其他计算机辅助设计软件完成齿轮的绘制工作。
3.使用CNC机床制作齿轮母模在完成齿轮的CAD图设计后,将其通过CAM软件编程,使其转化为CNC机床所能识别的指令,然后通过CNC机床进行齿轮母模的加工。
4.制作齿轮精度测量仪制作齿轮精度测量仪,测量仪主要包括准确的齿轮中心定位装置,精确的齿廓扫描仪和数据处理器等。
5.进行齿轮齿廓范成实验利用齿轮的母模和精密齿轮测量仪,将齿轮母模和齿轮之间进行相互配合和精密测量,即可获得高精度的齿轮齿廓。
1.加工齿轮母模时需要采用高精度的CNC机床,以保证母模加工的精度和表面光洁度。
2.制作齿轮精度测量仪时需要选择精度高、鲁棒性强的元器件,并利用合理的设计方法,避免测量误差的产生。
齿轮的设计与计算
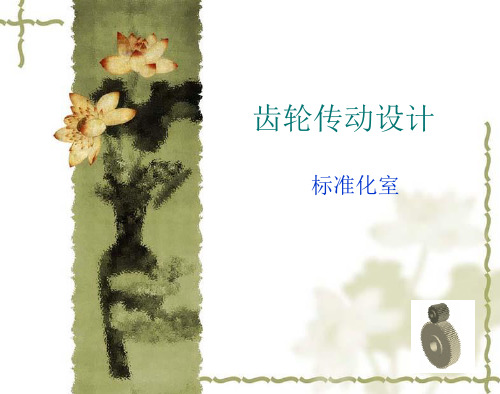
标准化室
目录
❖ §1.齿轮传动的特点及分类 ❖ §2.渐开线直齿圆柱齿轮各部分名称、基本参数和
几何尺寸 ❖ §3.变位齿轮传动和变位系数的选择 ❖ §4.渐开线直齿圆柱齿轮传动的几何计算 ❖ §5.齿轮材料及热处理
§6.渐开线直齿圆柱齿轮的强度计算 §7.圆柱齿轮精度 §8.渐开线圆柱齿轮图样上应注明的尺寸数据 §9.直齿圆锥齿轮传动 §10.齿轮结构设计 小结
m越大,p越大,轮齿的尺寸也越大,齿轮承受载荷的 能力也越高。
(8)齿顶高 齿顶圆和分度圆间的径向距离,用ha表示。 ha=ha*m ( ha*—齿顶高系数)
(9)齿根高 分度圆和齿根圆间的径向距离,用hf表示。
h f=(ha*+c*)m (c* —顶隙系数) 我国标准规定:正常齿制ha*=1 ,c*=0.25
二、齿轮的常用材料及热处理
1.锻钢 锻钢因具有强度高、韧性好、便于制造、便于热处理
等优点,大多数齿轮都用锻钢制造。
(1)软齿面齿轮:齿面硬度<350HBS,常用中碳钢和中 碳合金钢,如45钢、40Cr、35SiMn等材料,进行调质或 正火处理。这种齿轮适用于强度、精度要求不高的场合, 轮坯经过热处理后进行插齿或滚齿,生产便利、成本较低。
三、齿根弯曲疲劳强度计算 (摘自GB/T 3480-1997 渐开线圆柱齿轮承载能力计算方法)
轮齿的弯曲强度校核公式为
F
2KT1 bd1m
YFYs
2KT1 bm2 z1
YF
YS
[ F ](MPa)
将齿宽系数
d
b d
代入上式,得弯曲强度的设计公式
m
1.263
d
KT1
z12
齿轮渐开线方程图解
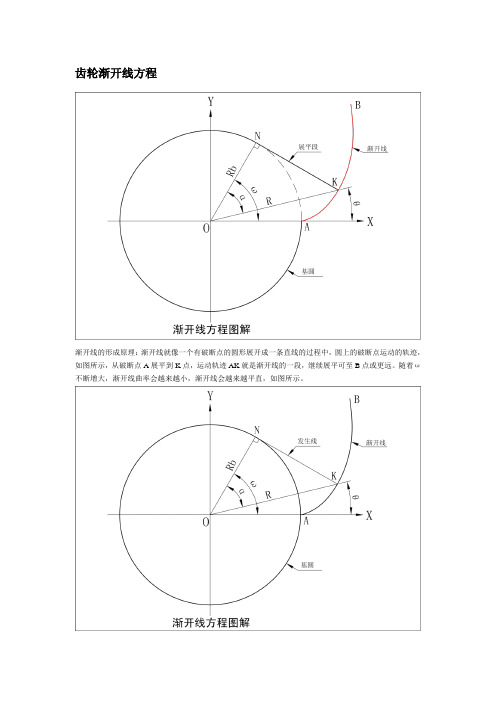
建立方法同大端,但球面半径rx变为rx-bc
大端齿根圆:
以默认的笛卡尔坐标为基准,用从方程功能建立基准曲线,方程关系式如下:
x=bb1*cos(t*360)
y=bb1*sin(t*360)
z=ob1
小端齿根圆:
建立方法同大端,但半径bb1变为b2b3,x方向尺寸ob1变为ob3。
齿根过度曲线:
3.齿顶圆压力角为参数控制的“极坐标”表示的渐开线方程B:
FAI=T*TAN(ACOS(DB/DW))*180/PI
Rb=DB/2
R=Rb/COS(ATAN(FAI*PI/180))
THETA=FAI-ATAN(FAI*PI/180)
Z=0
B.设ω为滚角参数,设定一个参数值,如45°,将ω用个人习惯的字母符号代替,如FAI。根据“勾股定理”,极轴R的长度R=( Rb^2+NK^2)^0.5。因式中NK=Rb*FAI*PI/180,将其代入。即可写成:
Z=0
滚角为参数“笛卡尔”坐标表示的渐开线:
A=T*45
X=DB/2*COS(A)+DB/2*SIN(A)*A*PI/180
Y=DB/2*SIN(A)-DB/2*COS(A)*A*PI/180
Z=0
所以创建齿轮模型时,如果对渐开线方程不熟悉,尽可能采用“极坐标”方程表达式:式1。
控制渐开线长度的方法:
C.在所有的“极坐标”渐开线方程表达式中,式1是最直接最简单的表达方法,公式简单,容易理解或记忆。而直角渐开线方程式表达式比较繁琐,不容易理解或记忆,如以下两种方程式的比较:
压力角为参数“极坐标”表示的渐开线方程1:
FAI=T*45
Rb=DB/2
R=Rb/COS(FAI)
渐开线花键设计计算公式

渐开线花键设计计算公式
一、基本齿形
一、尺寸计算
D F e mx=2√(0.5Db)²+(0.5DsinαD-)²-(hs/sinα) ²
三、公差和公差值
1、配合公差指齿槽宽和齿厚的公差
基本偏差对内花键的齿槽宽取基孔制H 它是作用齿槽宽的下偏差对外花键的齿厚取K=0js=(T+λ)/2 h、f、e和d它们是作用齿厚的上偏差
配合尺寸的公差
注:1、*以分度圆直径D为基础的公差,其公差单位I为:
当D≤500mm时,I=0.45 ³√D+0.001D.
当D>500mm时,I=0.004D+2.1.
**一基本齿槽宽E或基本齿厚S为基础的公差,其公差单位I为:I=0.45 ³√E+0.001E或
I=0.45 ³√S+0.001S.
式中D、E和S为mm。
2、L为分度圆周长之半,即L=πmZ/2 mm.
3、公差因素φ=m+0.0125D mm.
4、G为花键长度mm.
非配合尺寸的公差
齿向公差Fβ
内花键M值和W值计算
一、内花键量棒测量尺寸的计算公式
D’R i=D b[tanαci-tan(αci-Emax/D+invαci-inva D)]
式中:
D’R i---量棒的计算直径;
a ci---内花键与量棒接触点上的压力角,以弧度表示,αci=cos-¹。
渐开线计算

30°平齿根花键计算书第 1 页模数 m = 3齿数 z = 15标准压力角αD = 30°配合代号:H7/h7分度圆直径 D = m×z = 45基圆直径Db = m×z×cos(αD) = 38.9711周节 p = π×m = 9.42477796076937内花键大径Dei = m×(z 1.5) = 49.5外花键作用齿厚上偏差 esv = 0(根据<<机械传动设计手册>>1463页表9-1-49或由公差代号计算)外花键渐开线起始圆直径最大值:DFemax = 2×((0.5Db)^2 (0.5Dsin(αD)-(hs-0.5esv/tan(αD))/sin(αD))^2)^0.5 = 41.8669(其中hs = 0.6m = 1.8)内花键小径 Dii = DFemax 2CF) = 42.47(其中CF = 0.1m = .3)内花键基本齿槽宽 E = 0.5πm = 4.71238898外花键基本齿厚 S = 0.5πm = 4.71238898内花键:内花键总公差 T λ = 40i* 160i** = 179其中i* = 0.45(D)^(1/3) 0.001D (D = (30×50)^0.5 = 38.7298334620742)i** = 0.45(E)^(1/3) 0.001E (E = (3×6)^0.5 = 4.24264068711928)周节累积公差 Fp = 7.1(L)^0.5 18 = .078其中分度圆周长之半 L = πmz/2 = 70.6858347057703齿形公差 ff = 6.3ψf 40 = .062其中公差因数ψf = m 0.0125D = 3.48412291827593齿向公差 Fβ = 2.0×(g)^0.5 10 = .023其中花键长度 g = 40综合公差λ= 0.6((Fp)^2 (ff)^2 (Fβ)^2)^0.5 = .061作用齿槽宽最小值 Evmin = 0.5πm = 4.712实际齿槽宽最大值 Emax = Evmin (T λ) = 4.891实际齿槽宽最小值 Emin = Evmin λ =4.773作用齿槽宽最大值 Evmax = Emax - λ = 4.83外花键:外花键大径Dee = m×(z 1) = 48外花键小径Die = m×(z - 1.5) = 40.5外花键总公差 T λ = 40i* 160i** = 179其中i* = 0.45(D)^(1/3) 0.001D (D = (30×50)^0.5 = 38.7298334620742)i** = 0.45(E)^(1/3) 0.001E (E = (3×6)^0.5 = 4.24264068711928)周节累积公差 Fp = 7.1(L)^0.5 18 = .078其中分度圆周长之半 L = πmz/2 = 70.6858347057703齿形公差 ff = 6.3ψf 40 = .062其中公差因数ψf = m 0.0125D = 3.48412291827593齿向公差 Fβ = 2.0×(g)^0.5 10 = .023其中花键长度 g = 40综合公差λ= 0.6((Fp)^2 (ff)^2 (Fβ)^2)^0.5 = .061作用齿厚最小值 Svmin = Smin λ = 4.594实际齿厚最大值 Smax = Svmax - λ = 4.651实际齿厚最小值 Smin = Svmax - (T λ) =4.533作用齿厚最大值 Svmax = S esv = 4.71230°平齿根花键计算书第 2 页量棒直径 DRi = DRe = 5.04内花键量棒中心圆上的压力角 invαi = Emax/D invαD - DRi/Db= 4.891/45 inv(αD) - 5.04/38.9711= .108688888888889 5.37514935913267E-02-.129326603560074= 3.31224454025424E-02αi = 25.7996333°内花键棒间距最大值MRimax = Db × cos(90/z)/cosαi - DRi = 37.3内花键棒间距最小值 MRimin = MRimax - Ki×T = 37.07其中 Ki = cosαD × cos(90/z)/sinαi T = (T λ)-λ外花键量棒中心圆上的压力角 invαe = DRe/Db invαD Smin/D - π/z= 5.04/38.9711 inv(αD) 4.533/45 - π/15= .129326603560074 5.37514935913267E-02 .100733333333333-.209439510239319 = 7.43805866859188E-02αe = 33.1259646°外花键跨棒距最大值MRemin = Db × cos(90/z)/cosαe DRe = 50.74外花键跨棒距最小值MRemax = MRemin Ke×T = 50.557其中 Ke = cosαD × cos(90/z)/sinαe T = (T λ)-λ挤压强度计算计算挤压应力σc = 1000T/(ψ×z×h×l×r) = 27.1 MPa其中传递转矩T = 30000×P/π/n = 658.5722 N×m系数ψ取 0.75齿数 z = 15花键工作高度h = 0.8×m = 2.4花键工作长度 l = 40花键平均半径 r = D/2 = 22.5根据联接情况:静联接使用、制造条件:中等热处理工艺:齿面未经热处理许用挤压应力 [σc] = 60--100 MPa挤压强度满足要求σc < [σc]许用应力[σ]一般按下式原则来确定:[σ]=材料极限应力σ°/安全系数n. 式中,材料极限应力σ°的选用原则为:对于塑性材料,以材料的屈服极限σs作为其设计的材料极限应力σ°;对于脆性材料,以材料的强度极限σb作为其设计的材料极限应力σ°。
渐开线花键设计计算公式

渐开线花键设计计算公式渐开线花键是一种常用于传动装置的机械零件,通过渐开线花键的组合与配合,实现两个轴之间的旋转传动。
渐开线花键设计计算公式一般包括渐开线花键的尺寸、齿数和齿厚的计算公式,以及渐开线花键的切向力和径向力的计算公式等。
首先,我们来看渐开线花键的尺寸计算公式。
渐开线花键的尺寸一般包括齿顶直径(D),齿底直径(d)、齿顶高度(h1)和齿根高度(h2)等。
这些尺寸的计算公式如下:齿顶直径(D)=2r+b齿底直径(d)=2r-b齿顶高度(h1)=0.5h+0.5b齿根高度(h2)=0.5h-0.5b其中,r表示渐开线花键的基圆半径,h表示花键厚度,b表示花键齿廓的宽度。
接下来,我们来看渐开线花键的齿数的计算公式。
渐开线花键的齿数取决于花键齿廓与被齿合轮齿廓的分割数,齿数的计算公式如下:Z=πD/(0.7P)其中,Z表示齿数,D表示齿顶直径,P表示被齿合轮的分度圆周长。
除了尺寸和齿数的计算公式,渐开线花键的切向力和径向力也是设计时需要考虑的重要参数。
我们来看这两个力的计算公式。
Ft=T/(0.5P)其中,Ft表示切向力,T表示传递的扭矩,P表示花键齿廓的分度圆周长。
Fr = Ft * tan(α)其中,Fr表示径向力,α表示花键齿廓的压力角。
需要注意的是,在实际设计中,还需要根据实际工作条件和使用要求对以上公式进行修正和适应。
总结起来,渐开线花键设计计算公式主要包括渐开线花键的尺寸计算公式、齿数计算公式以及切向力和径向力的计算公式。
通过这些公式,我们可以在设计过程中快速准确地计算出渐开线花键的尺寸、齿数和受力情况,从而满足设备的传动需求。
当然,在实际设计中还需要考虑其他因素,如材料、加工工艺和装配要求等,以确保渐开线花键的可靠性和安全性。
(完整word)渐开线圆柱齿轮设计

第一章渐开线齿轮传动的基本理论齿轮传动的特点和类型:齿轮优点:传动比不变,功率大,高,速度范围大,结构紧凑,维护简单,寿命长,缺点:高精度的齿轮制造要求高,精度要求高,成本高,低精度的噪音大,不适合远距离传动工作条件:闭式:需要良好的润滑和密封开式:磨损比较严重,用于简单机械和低速场合齿面硬度:软齿面:硬度小于等于350HBS硬齿面;硬度大于350HBS齿轮轴线的相对位置:平面齿轮传动;直齿圆柱齿轮传动斜齿圆柱齿轮传动人字齿轮传动齿轮和齿条空间齿轮传动;圆锥齿轮传动蜗杆传动交错轴斜齿轮传动齿轮啮合的基本规律:基节相同渐开线方程inva形成是由基圆形成的基圆以内无渐开线第二章渐开线支持圆柱齿轮传动渐开线齿轮的尺寸参数分度圆的基节等于齿厚加齿槽宽内齿轮的齿顶圆必须大于基圆直径径节制DP等于Z/D和模数互为倒数DP等于25.4/m我国的标准齿轮齿形:齿形角20度工作齿高2m 齿距p等于πm 齿顶系数c等于0。
25 齿根圆角半径pf 0.38m(11页底部有详解)其他国家的圆柱齿轮常用的基本轮廓参数美国英国DP 苏联,德国,瑞士,日本,国标,iso都是m公制,单位毫米渐开线齿轮的标准参数齿数圆周齿轮的总齿数,模数齿轮的分度圆是计算齿轮各部分尺寸的基准,如果已知齿数z和分度圆齿距p 那么d就等于p/π乘以z,但是π是个无理数,所以我们人为的把这个比值规定为标准值,也就是我们说的模数,单位是mm模数系列分为第一和第二,优先选用第一系列,第二系列带括号的尽量不用,压力角离基圆越近的压力角小,对传动有利,但是曲率半径也小,对接触强度不利,齿根无强度,远离基圆的压力角大,曲率半径也大,所以规定标准为20度,角度加大,综合强度会增大,推荐25度顶隙系数齿c❀为了传动不被卡死,能够储存润滑油,两个齿轮在径向方向应留有间隙,这一间隙就是顶隙,c等于c❀*m正常齿制,当m≥1,ha❀等于1 c❀等于0。
25, m<1时ha❀不变,c❀等于0.35短齿制 ha❀0。
渐开线圆柱齿轮传动计算初稿

渐开线圆柱齿轮传动计算设计参数:传递功率 P=8.38 Kw传递转矩 T=5001.29 N.m (m N n P T ⋅=⨯==81.50011638.895509550) 齿轮1转速 n1=16 rpm齿轮2转速 n2=2 rpm 传动比 i=8原动机载荷特性 中等振动 工作机载荷特性 中等振动 预定寿命 H=1000 小时布置与结构:闭式 对称布置材料及热处理:齿面啮合类型 软硬齿面齿轮1材料及热处理 42CrMo <表面淬火>齿轮1硬度取值范围 48~56(此处应该是HRC 吧?) 齿轮1硬度 HBS1=52齿轮2材料及热处理 42CrMo<调质> 齿轮2硬度取值范围 255~286 齿轮2硬度 HBS2=260齿轮精度齿轮1 8FH-GB10095 齿轮2 8FH-GB10095工作条件润滑油粘度 V50=120 不允许点馈 载荷类型 静强度齿轮基本参数模数(法面模数) Mn=9 齿轮1齿数 Z1=15 齿轮1变位系数 X1=0 齿轮1齿宽 B1=75齿轮1齿宽系数 Φd1=0.556 齿轮2齿数 Z2=120齿轮2变位系数 X2=0 齿轮2齿宽 B2=75齿轮2齿宽系数 Φd2=0.069齿顶高系数 ha*=0.8 顶隙系数 c*=0.25 压力角 α*=20中心距 A0=607.5 (5.472212=-=d d a )齿数比 U=8端面重合度 εα=1.6760 纵向重合度 εβ=0总重合度 ε=1.67640 端面重合度:385.1)]'tan (tan )'tan (tan [2175.17)/cos arccos(88.31)/cos arccos(8.5322/7.742/22112221112211=-±-=︒==︒======ααααπεαααααa a a a a a a a a a z z r r r r d r d r齿轮1分度圆直径 d1=135 齿轮1齿顶圆直径 da1=149.4 齿轮1齿根圆直径 df1=116.1 齿轮1齿顶高 ha1=7.2 齿轮1齿根高 hf1=9.45 齿轮1全齿高 h1= 16.65齿轮2分度圆直径 d2=1080齿轮2齿顶圆直径 da2=1094.4 da2=1065.6 齿轮2齿根圆直径 df2=1061.1 df2=1098.9 齿轮2齿顶高 ha2=7.2 齿轮2齿根高 hf2=9.45 齿轮2全齿高 h2= 16.65强度校核:接触疲劳强度校核:齿轮1接触疲劳强度许用值 [ζH]1=1507.6 齿轮2接触疲劳强度许用值 [ζH]2=905.4 接触强度用安全系数 SHmin=1 接触强度计算应力 ζH=1659.6接触疲劳强度校核 ζH ≤[ζH]=不满足(注明:大齿轮即使是表面淬火,硬度达到55HRC , 齿轮2接触疲劳强度许用值 [ζH]2=1124.6,接触强度计算应力 ζH=1659.6,ζH ≤[ζH]=不满足) 弯曲疲劳强度计算:齿轮1弯曲疲劳强度许用值 [ζF]1=1171.2 齿轮2弯曲疲劳强度许用值 [ζF]2=1019.6 弯曲强度用安全系数 SFmin=1.40齿轮1弯曲疲劳强度计算应力 ζF1=689.4 齿轮2弯曲疲劳强度计算应力 ζF2=579.2 齿轮1弯曲疲劳强度校核 ζF1≤[ζF]1=满足齿轮2弯曲疲劳强度校核 ζF2≤[ζF]2=满足强度校核:小齿轮 大齿轮 齿面粗糙度(μm )Ra 3.2 3.2 接触强度极限(MPa )ζHlim 1170 710 弯曲强度极限(MPa )ζFlim 360 290 应力循环次数N L 5106.9⨯ 5102.1⨯ N L1=60n 1t ,N L2= N L1/U 接触强度系数使用系数KA 1.5 (原动机是电动机,从动机中等振动)动载系数Kv 0.2 齿向载荷分布系数 KH β 1.195 1.331b C d bd b C C C K H 34212132110)]()(1[-⋅+++=β其中:C 1=1.23,C 2=0.18,C 3=0,C 4=0.61;齿间载荷分布系数 KH α 1.2 1.1 节点区域系数 ZH 2.5'sin cos 'cos cos 22t t t b H Z αααβ=弹性系数 ZE 189.8 重合度系数 Z ε 0.93334αεε-=Z 螺旋角系数 Z β 1.000 寿命系数 ZNT 1.36 1.60 单对齿啮合系数 ZBD 1.000 1.000润滑剂系数 ZL 1.02 1.02 速度系数 ZV 0.94 0.90 粗糙度系数 ZR 1.045 1.075 齿面工作硬化系数 ZW 1.000 1.000 尺寸系数 ZX 0.97 1.000 弯曲强度系数齿向载荷分布系数KF β 1.15 1.252NH F K K )(ββ= 其中 787.0)/()/(1)/(22=++=h b h b h b N 齿间载荷分布系数 KF α 1.2 1.1 重合度系数 Y ε 0.79 0.79nY αεε75.025.0+=螺旋角系数 Y β 1.000 1.000 尺寸系数 YX 0.95 0.97 齿形系数 YFa 3.11 2.16 应力修正系数 YSa 1.5 1.81 寿命系数 YNT 1.12 1.71 试验齿轮的应力修正系数YST 2.0 2.0 相对齿根圆角敏感系数 Y δrelT 0.98 1.009 相对齿根表面状况系数 YRrelT 1.063 1.063 轮缘系数YB 1.000 1.000 A 、接触强度计算结果计算接触应力(MPa )ζH 833.347 742.595αββεσH H V A t E H BD H K K K K u u b d F Z Z Z Z Z 11±= 其中:112d TF t =许用应力(MPa )ζHP 1546.47 1121.06X W R V L NT H HP Z Z Z Z Z Z lim σσ=接触安全系数 SH 1.856 1.510HHPH S σσ=小齿轮接触强度足够! 大齿轮接触强度足够! B 、弯曲触强度计算结果计算弯曲应力(MPa )ζF 161.828 140.031αββεσF F V A B Sa Fa ntF K K K K Y Y Y Y Y bm F =许用应力(MPa )ζFP 798.056 1031.859x RreIT reIT NT ST F FP Y Y Y Y Y δσσlim =弯曲安全系数SF 4.932 7.369FFPF S σσ=小齿轮弯曲强度足够! 大齿轮弯曲强度足够!。
- 1、下载文档前请自行甄别文档内容的完整性,平台不提供额外的编辑、内容补充、找答案等附加服务。
- 2、"仅部分预览"的文档,不可在线预览部分如存在完整性等问题,可反馈申请退款(可完整预览的文档不适用该条件!)。
- 3、如文档侵犯您的权益,请联系客服反馈,我们会尽快为您处理(人工客服工作时间:9:00-18:30)。
渐开线齿轮设计已知条件:增速齿轮; 齿轮传递功率 P=3300 kW ;高速轴转速1n =11600 r/min ;传动比 i=1.6; 工作时间:50000小时一、确定齿轮类型标准斜齿轮,齿轮配合为外啮合传动。
二、选择材料小齿轮:50SiMn ,调质,HB=207~255大齿轮:42SiMn ,调质,HB=196~255根据图2.5-14(a)和图2.5-43(a),取σHlim1=1350 MPa ,σHlim2=1350 MPa ,σFlim1=360 MPa ,σFlim2=360 MPa 。
齿面粗糙度Rz1=3.2 m μ,Rz2=3.2 m μ,齿根表面粗糙度Rz1=10 m μ,Rz2=10 m μ。
大、小齿轮设计修缘量Ca1=30 μm ,Ca2=30 μm 。
油浴润滑,ν50=20 s mm/2,胶合承载能力为FZG7级。
三、初步确定主要参数1.按接触强度初步确定中心距a (根据表2.5-1)系数Aa :螺旋角β=8~12°,根据表2.5-2,对于钢对钢的齿轮副Aa=476载荷系数k :取k=2齿宽系数a φ:根据表2.5-4,φa=0.5小齿轮的名义转矩:T1=9549*P/n1=2717 N·m许用接触应力:σHlim=min{σHlim1,σHlim2}=1350 MPaσHP=0.9*σHlim=1215.00 MPa计算:a=Aa*(u+1)*[(K*T1)/(Φa*u*бHP^2)]^(1/3)≥205.83 mm圆整为a=250 mm 。
2.初步确定模数、齿数、螺旋角根据表2.1-1,取模数m=3.5 mm由表2.2-1的公式可导出初选β=12°Ζ1=2acosβ/[m*(u+1)]=53.74 (74.53)]1(/[cos 21=+*=u m a Z β)取Ζ1=54,Ζ2=u*Ζ1=86.40,取Ζ2=87。
Ζ2经圆整后,齿数比发生了变化,实际齿数比为u=Ζ2/Ζ1=1.611。
精算β=arccos[m*(Ζ2+Ζ1)/2a]=9°14′55″四、其他几何参数的计算(根据表2.2-1)1.分度圆压力角αn=20°00′00″2.齿顶高系数hanˇ=13.顶隙系数cnˇ=0.254.齿宽b1=140 mm ,b2=140 mm5.齿数比u=Ζ2/Ζ1=1.6116.分度圆直径d1=mn*Ζ1/cosβ=191.489 mmd2=mn*Ζ2/cosβ=308.511 mm7.基圆直径αt=arctan(tanαn/cosβ)=20°14′32″db1=d1*cosαt=179.662 mmdb2=d2*cosαt=289.457 mm8.齿顶高ha1=ha2=hanˇ*mn=3.500 mm9.齿根高hf1=hf2=(hanˇ+cnˇ)*mn=4.375 mm10.全齿高h1=h2=ha1+hf1=ha2+hf2=7.875 mm11.齿顶圆直径da1=d1+2*ha1=198.489 mmda2=d2+2*ha2=315.511 mm12.齿根圆直径df1=d1-2*hf1=182.739 mmdf2=d2-2*hf2=299.761 mm13.齿顶压力角αat1=arccos(db1/da1)=25°9′24″αat2=arccos(db2/da2)=23°26′52″14.端面重合度α′t=αtεα=[Ζ1(tanαat1-tanα′t)+Ζ2(tanαat2-tanα′t)]/2π=1.76715.轴向重合度εβ=b*sinβ/(π*mn)=2.046(b=min{b1,b2})16.总重合度εγ=εα+εβ=3.81317.当量齿数Ζv1=Ζ1/(cosβb^2*cosβ)=55.988Ζv2=Ζ2/(cosβb^2*cosβ)=90.203五、齿厚测量尺寸的计算1.公法线长度跨齿数:Ζ1′=Ζ1*invαt/invαn=56.06Ζ2′=Ζ2*invαt/invαn=90.31k1=αn*Ζ1′/180°+0.5=6.73k2=αn*Ζ2′/180°+0.5=10.53取k1=7,k2=11Wk1=Wk1ˇ*mn=cosαn*[π(k1-0.5)+Ζ1′*invαn]*mn=69.9088 mmWk2=Wk2ˇ*mn=cosαn*[π(k2-0.5)+Ζ2′*invαn]*mn=112.9178 mm2.分度圆弦齿厚、弦齿高弦齿厚:s1¨=mn*Ζv1*sin(π/2Ζv1)=5.4971 mms2¨=mn*Ζv2*sin(π/2Ζv2)=5.4975 mm弦齿高:h1¨=ha1+0.5*mn*Ζv1*[1-cos(π/2Ζv1)]=3.5386 mmh2¨=ha2+0.5*mn*Ζv2*[1-cos(π/2Ζv2)]=3.5239 mm3.固定弦齿厚、弦齿高弦齿厚:sc1¨=0.5*π*mn*cosαn^2=4.8547 mmsc2¨=0.5*π*mn*cosαn^2=4.8547 mm弦齿高:hc1¨=ha1-π*mn*sin(2αn)/8=2.6165 mmhc2¨=ha2-π*mn*sin(2αn)/8=2.6165 mm4.量柱(球)直径、量柱(球)跨距量柱(球)直径:dp1=1.68*mn=5.8800 mmdp2=1.68*mn=5.8800 mm量柱(球)中心的渐开线端面压力角:invαMt1=invαt+dp1/(mn*Ζ1*cosαn)-π/2Ζ1,αMt1=21°48′1″invαMt2=invαt+dp2/(mn*Ζ2*cosαn)-π/2Ζ2,αMt2=21°14′19″量柱(球)跨距:M1=d1*cosαt/cosαMt1+dp1=155.2486 mmM2=d2*cosαt*cos(π/2Ζ2)/cosαMt2+dp2=245.5618 mm六、接触疲劳强度的校核1.名义切向力Ft=2000T1/d1=28373 N2.使用系数(根据表2.5-7)ΚA=1.25,因为增速传动乘以1.1,得ΚA=1.3753.动载系数(根据表2.5-11)计算单对齿刚度和啮合刚度(根据表2.5-32)理论修正值:Cm=0.8轮坯结构系数:实心齿轮CR=1基本齿廓系数:CB1=[1+0.5*(1.2-hfp1/mn)]*[1-0.02*(20°-αn)]=0.97CB2=[1+0.5*(1.2-hfp2/mn)]*[1-0.02*(20°-αn)]=0.97CB=(CB1+CB2)/2=0.97齿轮柔度的最小值:q′=0.04723+0.15551/Ζv1+0.25791/Ζv2=0.05287 (mm·μm)/N 单对齿刚度理论值:Cth′=1/q′=18.92 N/(mm·μm)ξ=2*E1*E2/(E1+E2)=1.00单对齿刚度:c′=ξ*Cth′*Cm*CR*CB*cosβ=14.5623 N/(mm·μm)啮合刚度:cr=(0.75*εα+0.25)*c′=22.9392 N/(mm·μm)计算临界转速比(根据表2.5-12)平均直径:dm1=(da1+df1)/2=190.614 mmdm2=(da2+df2)/2=307.636 mm轮缘内腔直径比:q1=Di1/dm1=0.000q2=Di2/dm2=0.000转动惯量:I1=πρ1*b1*(1-q1^4)*dm1^4/32=1415277.860 kg·mm^2I2=πρ2*b2*(1-q2^4)*dm2^4/32=9602209.037 kg·mm^2当量质量:m1=I1/(b1*rb1^2)=1.253 kg/mmm2=I2/(b2*rb2^2)=3.274 kg/mm诱导质量:mred=m1*m2/(m1+m2)=0.9061 kg/mm临界转速:nE1=30000/(π*Ζ1)*(cr/mred)^0.5=889.778 r/min(778.889)/()/(3000011=**=red r E m c Z n π)临界转速比:N=n1/nE1=13.037计算齿廓跑合量(根据表2.5-30)ya1=160/σHlim1*fpb1=0.759 μmya2=160/σHlim2*fpb2=0.853 μmya=(ya1+ya2)/2=0.806 μm计算系数Bp ,Bf ,Bk (根据表2.5-16)有效基节偏差:fpbeff=fpb2-yp=fpb2-ya=6.394 μm有效齿形公差:ffeff=ff2-yf=ff2-ya=7.094 μm设计修缘量:Ca=(Ca1+Ca2)/2=30.000 μmBp=c ′*fpbeff/(Ft*ΚA/b)=0.334Bf=c ′*ffeff/(Ft*ΚA/b)=0.371Bk=|1-c ′*Ca/(Ft*ΚA/b)|=0.568计算系数Cv (根据表2.5-15)εγ>2,取Cv1=0.32Cv2=0.57/(εγ-0.3)=0.162Cv3=0.096/(εγ-1.56)=0.043Cv4=(0.57-0.05*εγ)/(εγ-1.44)=0.160Cv5=0.47Cv6=0.12/(εγ-1.74)=0.058εγ>2.5,取Cv7=1.0N ≥1.5,属于超临界区Κv=Cv5*Bp+Cv6*Bf+Cv7=1.17854.齿向载荷分布系数(根据表2.5-18)计算加工、安装误差产生的啮合齿向误差分量装配时进行检验调整,fma=0.5*F β1=6.000 μm取小齿轮结构系数(根据表2.5-21)刚性,Κ′=0.48计算小齿轮结构尺寸系数(根据表2.5-22)通过该对齿轮的功率Κ=100%B ′=1+2*(100-Κ)/Κ=1.000γ=[|B ′+Κ′*l*s/d1^2*(d1/dsh)^4-0.3|+0.3]*(b/d1)^2=0.550 (μm·mm)/N计算单位载荷作用下的啮合齿向误差(根据表2.5-20)一般齿轮fsh0=0.023*γ=0.013 (μm·mm)/N综合变形产生的啮合齿向误差分量fsh=(Ft*ΚA*ΚV/b)*fsh0=4.157 μm初始啮合齿向误差:受载时接触不良F βx=1.33*fsh+fma=11.529 μm计算齿向跑合系数(根据表2.5-23)xβ1=1-320/σHlim1=0.763 μmxβ2=1-320/σHlim2=0.763 μmxβ=(xβ1+xβ2)/2=0.763 μm跑合后啮合齿向误差F βy=F βx*x β=8.796 μmΚHβ=1+0.5*Fβy*cr/(Ft*ΚA*ΚV/b)=1.30725.齿间载荷分配系数(根据表2.5-29)ΚtH/b=Ft*ΚA*ΚV*ΚHβ/b=429.291 NΚHα=0.9+0.4*[2*(εγ-1)/εγ]^0.5*cr*(fpb-ya)/(ΚtH/b)=1.06606.节点区域系数基圆螺旋角βb=arccos{[1-(sinβ*cosαn)^2]^0.5}=8°41′11″ΖH=[2*cosβb*cosα′t/(cosαt^2*sinα′t)]^0.5=2.46417.弹性系数ΖE={1/π[(1-ν1^2)/E1+(1-ν^2)/E2]}^0.5=189.81 MPa^0.58.重合度系数(根据表2.5-35)Ζε=(1/εα)^0.5=0.7523经验算:ΚHα≤εγ/(εα*Ζε^2)9.螺旋角系数Ζβ=(cosβ)^0.5=0.993510.单对齿啮合系数(根据表2.5-33)ΖB=tanα′t/{[(da1^2/db1^2-1)^0.5-2π/Ζ1]*[(da2^2/db2^2-1)^0.5-(εα-1)*2π/Ζ2]}^0.5=1.0087 ΖD=111.寿命系数(根据表2.5-40)NL1=n1*L=34800000000NL2=NL1/u=21600000000ΖNT1=(5*10^7/NL1)^0.0306=0.8185ΖNT2=(5*10^7/NL2)^0.0306=0.830512.润滑剂系数(根据表2.5-36)σHlim1>1200 MPa,取σHlim1=1200 MPa,CZL1=σHlim1/4375+0.6357=0.910ΖL1=CZL1+4*(1.0-CZL1)/(1.2+80/ν50)^2=0.9233σHlim2>1200 MPa,取σHlim2=1200 MPa,CZL2=σHlim2/4375+0.6357=0.910ΖL2=CZL2+4*(1.0-CZL2)/(1.2+80/ν50)^2=0.923313.速度系数(根据表2.5-36)σHlim1>1200 MPa,取σHlim1=1200 MPa,CZV1=0.85+(σHlim1-850)/350*0.08=0.930ΖV1=CZV1+2*(1.0-CZV1)/(0.8+32/ν)^0.5=1.0650σHlim2>1200 MPa,取σHlim2=1200 MPa,CZV2=0.85+(σHlim2-850)/350*0.08=0.930ΖV2=CZV2+2*(1.0-CZV2)/(0.8+32/ν)^0.5=1.065014.粗糙度系数(根据表2.5-37)节点处曲率半径:ρ1=0.5*db1*tanα′t=33.126 mmρ2=0.5*db2*tanα′t=53.371 mm节点处诱导曲率半径:ρred=ρ1*ρ2/(ρ1+ρ2)=20.440 mm相对平均表面粗糙度:Rz10=(Rz1+Rz2)/2*(10/ρred)^(1/3)=2.521σHlim1>1200 MPa,取σHlim1=1200 MPa,CZR1=0.32-0.0002*σHlim1=0.080ΖR1=(3/Rz10)^CZR1=1.0140σHlim2>1200 MPa,取σHlim2=1200 MPa,CZR2=0.32-0.0002*σHlim2=0.080ΖR2=(3/Rz10)^CZR2=1.014015.齿面工作硬化系数HB>470HBW,取HB=470ΖW1=ΖW2=1.2-(HB-130)/1700=116.尺寸系数(根据表2.5-41)ΖX1=1.0000ΖX2=1.000017.最小安全系数根据表2.5-42,取SHmin=1.60,SFmin=2.0018.计算接触应力(表2.5-6)бH0=ΖHΖEΖεΖβ[Ft/(d1*b)·(u+1)/u]^0.5=457.83 MPaбH1=ΖB*бH0*(ΚAΚvΚHβΚHα)^0.5=693.96 MPaбH2=ΖD*бH0*(ΚAΚvΚHβΚHα)^0.5=687.98 MPa19.许用接触应力(表2.5-6)бHP1=бHG1/SHmin=бHlim1*ΖNT1ΖL1ΖV1ΖR1ΖW1ΖX1/SHmin=688.59 MPaбHP2=бHG2/SHmin=бHlim2*ΖNT2ΖL2ΖV2ΖR2ΖW2ΖX2/SHmin=698.69 MPa由以上计算可知:бH1>бHP1,小齿轮的接触强度不满足要求бH2≤бHP2,大齿轮的接触强度满足要求。