微细宏观结合的金属断裂理论方块图
第1章 金属断裂

解理断的过程(三各阶段):
a) 塑性变形形成微裂纹; b) 裂纹在同一个晶粒内初期长大; c) 裂纹越过晶界向相邻晶粒扩展。
a)
b)
c)
2. 柯垂耳位错反应理论 (解理裂纹)
在α-Fe (bcc)中:
滑移面(110),滑移方向[111]。 右图中两个正交滑移面(101)与 (101)相交于解理面(001)中的 [010]轴线。 若沿(101)和(101)各有柏 氏矢量为a/2[111]和a/2[111]的平行 位错列在交叉线上相遇,即可形成 新位错a[001],其反应式如下:
1)弹性体裂纹失稳扩展判据 无限大板拉紧再固定拉应力σ,单位厚度 主要研究有2c长裂纹后强度情况
① 开长2c裂纹能量情况 a. 弹性能减少量(能量释放率)
c 2 2 We E 2 2 (1 2 ) c E 平面应力 平面应变
b. 表面能增加 Ws=(2c· 1· γ)×2=4cγ ② 裂纹扩展 2c→2c+2dc a. 扩展单位面积释放能量(弹性能变化)
舌状花样形成方式: 解理裂纹沿孪晶界扩展留下舌头状凹台或凸台。
另外:还有准解理(是解 理而非解理)。特点:断 裂路径不再与晶粒位相有 关,不再沿一定的晶体学 平面,主要与细小碳化物 质量有关。(撕裂棱较多,往
往有一定的塑性)
解理:一定 晶体内平面 准解理:不一定 与解理的区别 裂纹源 解理:晶界 准解理:第二相
x E 。 E E a0 → th 2 a0
→
th 2 πa0 E
2)能量平衡法求σth与E关系
① σth与拉断外力做功W外关系
W外 =
断裂图谱-1

断口分析fractography研究金属断裂面的学科,是断裂学科的组成部分。
金属破断后获得的一对相互匹配的断裂表面及其外观形貌,称断口。
断口总是发生在金属组织中最薄弱的地方,记录着有关断裂全过程的许多珍贵资料,所以在研究断裂时,对断口的观察和研究一直受到重视。
通过断口的形态分析去研究一些断裂的基本问题:如断裂起因、断裂性质、断裂方式、断裂机制、断裂韧性、断裂过程的应力状态以及裂纹扩展速率等。
如果要求深入地研究材料的冶金因素和环境因素对断裂过程的影响,通常还要进行断口表面的微区成分分析、主体分析、结晶学分析和断口的应力与应变分析等。
随着断裂学科的发展,断口分析同断裂力学等所研究的问题更加密切相关,互相渗透,互相配合;断口分析的实验技术和分析问题的深度将会取得新的发展。
断口分析现已成为对金属构件进行失效分析的重要手段。
断口的宏观和微观观察断口分析的实验基础是对断口表面的宏观形貌和微观结构特征进行直接观察和分析。
通常把低于40倍的观察称为宏观观察,高于40倍的观察称为微观观察。
对断口进行宏观观察的仪器主要是放大镜(约10倍)和体视显微镜(从5~50倍)等。
在很多情况下,利用宏观观察就可以判定断裂的性质、起始位置和裂纹扩展路径。
但如果要对断裂起点附近进行细致研究,分析断裂原因和断裂机制,还必须进行微观观察。
断口的微观观察经历了光学显微镜(观察断口的实用倍数是在 50~500倍间)、透射电子显微镜(观察断口的实用倍数是在 1000~40000倍间)和扫描电子显微镜(观察断口的实用倍数是在 20~10000倍间)三个阶段。
因为断口是一个凹凸不平的粗糙表面,观察断口所用的显微镜要具有最大限度的焦深,尽可能宽的放大倍数范围和高的分辨率。
扫描电子显微镜最能满足上述的综合要求,故近年来对断口观察大多用扫描电子显微镜进行(见金属和合金的微观分析)。
脆性断口和延性断口根据断裂的性质,断口大致可以分为几乎不伴随塑性变形而断裂的脆性断口,和伴随着明显塑性变形的延性断口。
断口的宏观形貌、微观形态及断裂机理
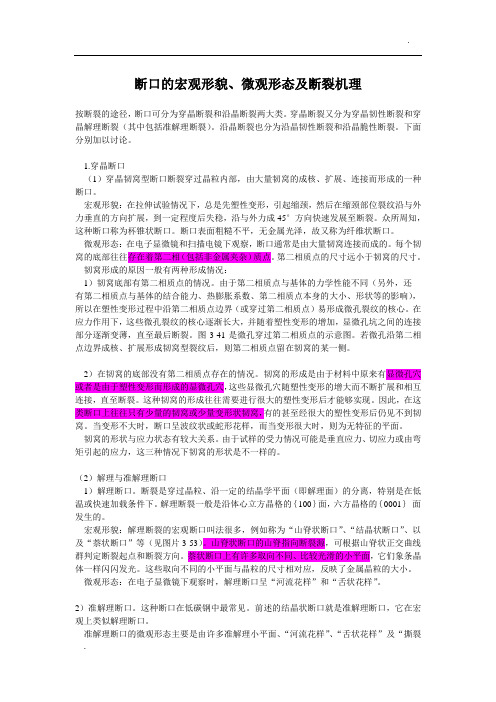
断口的宏观形貌、微观形态及断裂机理按断裂的途径,断口可分为穿晶断裂和沿晶断裂两大类。
穿晶断裂又分为穿晶韧性断裂和穿晶解理断裂(其中包括准解理断裂)。
沿晶断裂也分为沿晶韧性断裂和沿晶脆性断裂。
下面分别加以讨论。
1.穿晶断口(1)穿晶韧窝型断口断裂穿过晶粒内部,由大量韧窝的成核、扩展、连接而形成的一种断口。
宏观形貌:在拉伸试验情况下,总是先塑性变形,引起缩颈,然后在缩颈部位裂纹沿与外力垂直的方向扩展,到一定程度后失稳,沿与外力成45°方向快速发展至断裂。
众所周知,这种断口称为杯锥状断口。
断口表面粗糙不平,无金属光泽,故又称为纤维状断口。
微观形态:在电子显微镜和扫描电镜下观察,断口通常是由大量韧窝连接而成的。
每个韧窝的底部往往存在着第二相(包括非金属夹杂)质点。
第二相质点的尺寸远小于韧窝的尺寸。
韧窝形成的原因一般有两种形成情况:1)韧窝底部有第二相质点的情况。
由于第二相质点与基体的力学性能不同(另外,还有第二相质点与基体的结合能力、热膨胀系数、第二相质点本身的大小、形状等的影响),所以在塑性变形过程中沿第二相质点边界(或穿过第二相质点)易形成微孔裂纹的核心。
在应力作用下,这些微孔裂纹的核心逐渐长大,并随着塑性变形的增加,显微孔坑之间的连接部分逐渐变薄,直至最后断裂。
图3-41是微孔穿过第二相质点的示意图。
若微孔沿第二相点边界成核、扩展形成韧窝型裂纹后,则第二相质点留在韧窝的某一侧。
2)在韧窝的底部没有第二相质点存在的情况。
韧窝的形成是由于材料中原来有显微孔穴或者是由于塑性变形而形成的显微孔穴,这些显微孔穴随塑性变形的增大而不断扩展和相互连接,直至断裂。
这种韧窝的形成往往需要进行很大的塑性变形后才能够实现。
因此,在这类断口上往往只有少量的韧窝或少量变形状韧窝,有的甚至经很大的塑性变形后仍见不到韧窝。
当变形不大时,断口呈波纹状或蛇形花样,而当变形很大时,则为无特征的平面。
韧窝的形状与应力状态有较大关系。
金属材料断口机理及分析
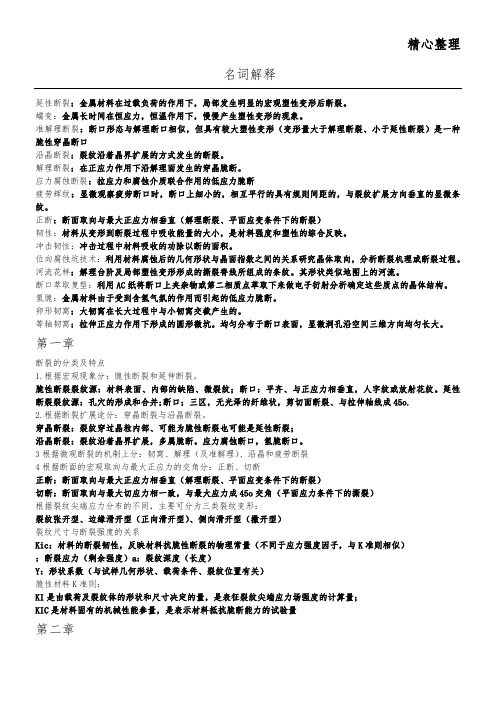
精心整理名词解释延性断裂:金属材料在过载负荷的作用下,局部发生明显的宏观塑性变形后断裂。
蠕变:金属长时间在恒应力,恒温作用下,慢慢产生塑性变形的现象。
准解理断裂:断口形态与解理断口相似,但具有较大塑性变形(变形量大于解理断裂、小于延性断裂)是一种脆性穿晶断口沿晶断裂:裂纹沿着晶界扩展的方式发生的断裂。
解理断裂:在正应力作用下沿解理面发生的穿晶脆断。
应力腐蚀断裂:拉应力和腐蚀介质联合作用的低应力脆断疲劳辉纹纹。
正断韧性: 河流花样 氢脆:卵形韧窝等轴韧窝1.2.34裂纹张开型、边缘滑开型(正向滑开型)、侧向滑开型(撒开型) 裂纹尺寸与断裂强度的关系Kic :材料的断裂韧性,反映材料抗脆性断裂的物理常量(不同于应力强度因子,与K 准则相似) :断裂应力(剩余强度)a :裂纹深度(长度)Y :形状系数(与试样几何形状、载荷条件、裂纹位置有关) 脆性材料K 准则:KI 是由载荷及裂纹体的形状和尺寸决定的量,是表征裂纹尖端应力场强度的计算量; KIC 是材料固有的机械性能参量,是表示材料抵抗脆断能力的试验量第二章裂纹源位置的判别方法:T型法(脆断判别主裂纹),分差法(脆断判别主裂纹),变形法(韧断判别主裂纹),氧化法(环境断裂判别主裂纹),贝纹线法(适用于疲劳断裂判别主裂纹)。
断口的试样制备:截取,清洗,保存。
断口分析技术设备:1.宏观断口分析技术(用肉眼,放大镜,低倍率光学显微镜观察分析)2.光学显微断口分析(扫描电子显微镜光学显微镜,透射电子显微镜),3.电镜断口分析。
第三章延性断裂:12.3.1(1约成45(2(321.2.(1)内颈缩扩展:质点大小、分布均匀,韧窝在多处形核(裂纹萌生),随变形增加,微孔壁变薄,以撕裂方式连接(2)剪切扩展:材料中具有较多夹杂物,同时具有细小析出相时,微孔之间可能以剪切方式相连接。
注意:内颈缩扩展与剪切扩展在同一韧窝断口上可能同时发生。
影响韧窝的形貌因素:夹杂物或第二相粒子,基体材料的韧性,试验温度,应力状态。
金属断裂机理完整版
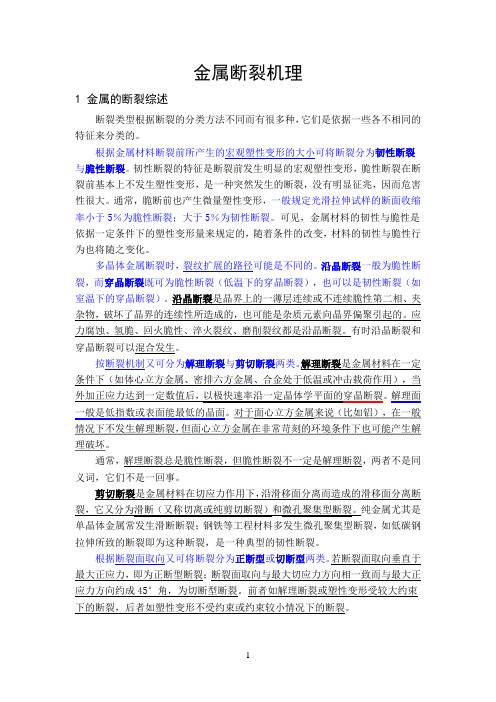
金属断裂机理1 金属的断裂综述断裂类型根据断裂的分类方法不同而有很多种,它们是依据一些各不相同的特征来分类的。
根据金属材料断裂前所产生的宏观塑性变形的大小可将断裂分为韧性断裂与脆性断裂。
韧性断裂的特征是断裂前发生明显的宏观塑性变形,脆性断裂在断裂前基本上不发生塑性变形,是一种突然发生的断裂,没有明显征兆,因而危害性很大。
通常,脆断前也产生微量塑性变形,一般规定光滑拉伸试样的断面收缩率小于5%为脆性断裂;大于5%为韧性断裂。
可见,金属材料的韧性与脆性是依据一定条件下的塑性变形量来规定的,随着条件的改变,材料的韧性与脆性行为也将随之变化。
多晶体金属断裂时,裂纹扩展的路径可能是不同的。
沿晶断裂一般为脆性断裂,而穿晶断裂既可为脆性断裂(低温下的穿晶断裂),也可以是韧性断裂(如室温下的穿晶断裂)。
沿晶断裂是晶界上的一薄层连续或不连续脆性第二相、夹杂物,破坏了晶界的连续性所造成的,也可能是杂质元素向晶界偏聚引起的。
应力腐蚀、氢脆、回火脆性、淬火裂纹、磨削裂纹都是沿晶断裂。
有时沿晶断裂和穿晶断裂可以混合发生。
按断裂机制又可分为解理断裂与剪切断裂两类。
解理断裂是金属材料在一定条件下(如体心立方金属、密排六方金属、合金处于低温或冲击载荷作用),当外加正应力达到一定数值后,以极快速率沿一定晶体学平面的穿晶断裂。
解理面一般是低指数或表面能最低的晶面。
对于面心立方金属来说(比如铝),在一般情况下不发生解理断裂,但面心立方金属在非常苛刻的环境条件下也可能产生解理破坏。
通常,解理断裂总是脆性断裂,但脆性断裂不一定是解理断裂,两者不是同义词,它们不是一回事。
剪切断裂是金属材料在切应力作用下,沿滑移面分离而造成的滑移面分离断裂,它又分为滑断(又称切离或纯剪切断裂)和微孔聚集型断裂。
纯金属尤其是单晶体金属常发生滑断断裂;钢铁等工程材料多发生微孔聚集型断裂,如低碳钢拉伸所致的断裂即为这种断裂,是一种典型的韧性断裂。
根据断裂面取向又可将断裂分为正断型或切断型两类。
断口的宏观形貌、微观形态及断裂机理

断心的宏瞅形貌、微瞅形态及断裂机理之阳早格格创做按断裂的道路,断心可分为脱晶断裂战沿晶断裂二大类.脱晶断裂又分为脱晶韧性断裂战脱晶解理断裂(其中包罗准解理断裂).沿晶断裂也分为沿晶韧性断裂战沿晶坚性断裂.底下分别加以计划.(1)脱晶韧窝型断心断裂脱过晶粒里里,由洪量韧窝的成核、扩展、对接而产死的一种断心.宏瞅形貌:正在推伸考查情况下,经常先塑性变形,引起缩颈,而后正在缩颈部位裂纹沿与中力笔直的目标扩展,到一定程度后得稳,沿与中力成45°目标赶快死少至断裂.寡所周知,那种断心称为杯锥状断心.断心表面细糙不仄,无金属光芒,故又称为纤维状断心.微瞅形态:正在电子隐微镜战扫描电镜下瞅察,断心常常是由洪量韧窝对接而成的.每个韧窝的底部往往存留着第二相(包罗非金属夹纯)量面.第二相量面的尺寸近小于韧窝的尺寸.韧窝产死的本果普遍有二种产死情况:1)韧窝底部有第二相量面的情况.由于第二相量面与基体的力教本能分歧(其余,还有第二相量面与基体的分散本领、热伸展系数、第二相量面自己的大小、形状等的效率),所以正在塑性变形历程中沿第二相量面鸿沟(大概脱过第二相量面)易产死微孔裂纹的核心.正在应力效率下,那些微孔裂纹的核心渐渐少大,并随着塑性变形的减少,隐微孔坑之间的对接部分渐渐变薄,直至末尾断裂.图3-41是微孔脱过第二相量面的示企图.若微孔沿第二相面鸿沟成核、扩展产死韧窝型裂纹后,则第二相量面留正在韧窝的某一侧.2)正在韧窝的底部不第二相量面存留的情况.韧窝的产死是由于资料中本去有隐微孔穴大概者是由于塑性变形而产死的隐微孔穴,那些隐微孔穴随塑性变形的删大而不竭扩展战相互对接,直至断裂.那种韧窝的产死往往需要举止很大的塑性变形后才搞够真止.果此,正在那类断心上往往惟有少量的韧窝大概少量变形状韧窝,有的以至经很大的塑性变形后仍睹不到韧窝.当变形不大时,断心呈波纹状大概蛇形格式,而当变形很大时,则为无特性的仄里.韧窝的形状与应力状态有较大闭系.由于试样的受力情况大概是笔直应力、切应力大概由直矩引起的应力,那三种情况下韧窝的形状是纷歧样的.(2)解理与准解理断心1)解理断心.断裂是脱过晶粒、沿一定的结晶教仄里(即解理里)的分散,特天是正在矮温大概赶快加载条件下.解理断裂普遍是沿体心坐圆晶格的{100}里,六圆晶格的{0001}里爆收的.宏瞅形貌:解理断裂的宏瞅断心喊法很多,比圆称为“山脊状断心”、“结晶状断心”、以及“萘状断心”等(睹图片3-53).山脊状断心的山脊指背断裂源,可根据山脊状正接直线群判决断裂起面战断裂目标.萘状断心上有许多与背分歧、比较光润的小仄里,它们象条晶体一般闪闪收光.那些与背分歧的小仄里与晶粒的尺寸相对于应,反映了金属晶粒的大小.微瞅形态:正在电子隐微镜下瞅察时,解理断心呈“河流格式”战“舌状格式”.2)准解理断心.那种断心正在矮碳钢中最罕睹.前述的结晶状断心便是准解理断心,它正在宏瞅上类似解理断心.准解理断心的微瞅形态主假如由许多准解理小仄里、“河流格式”、“舌状格式”及“撕裂岭”组成.沿晶断心是沿分歧与背的晶粒鸿沟爆收断裂.其爆收的主要本果是由于晶界强化,使晶界强度明隐矮于晶内强度而引起的.制成晶界强化的本果很多,比圆,锻制历程中加热战塑性变形工艺不当引起的宽沉细晶;下温加热时气氛中的C、H等元素浓度过下以及炉中残存有铜,渗人晶界;过烧时的晶界熔化大概氧化;加热及热却不当制成沿晶界析出第二相量面大概坚性薄膜;合金元素战夹纯偏偏析制成沿晶界的富集;其余沿晶界的化教腐蚀战应力腐蚀等等,皆不妨制成晶界强化,爆收沿晶断心.(1)沿晶韧窝型断心若第二相量面沿晶界析出的稀度很下,大概果有一定稀度的第二相量面再加上晶粒细大,皆市爆收沿晶韧窝型断裂.沿晶韧窝产死的本果与脱晶韧窝相共.那种断裂的隐微裂纹是沿着大概脱过第二相量面成核的.隐微裂纹的扩展战对接,伴伴随一定量的微瞅塑性变形.正在断心表面可瞅到许多位背分歧、无金属光芒的“小棱里”大概“小仄里”.那些“小棱里”大概“小仄里”的尺寸与晶粒尺寸相对于应(如果晶粒细小,则断心表面上的“小棱里”大概“小仄里”用肉眼便不克不迭瞅到大概不明隐).正在电子隐微镜下瞅察“小校里”大概“小仄里”,它是由洪量韧窝组成的,韧窝底部往往存留有第二相量面(大概薄膜).石状断心战棱里断心皆是沿晶韧窝型断心.其余,偏偏析线也是一种沿晶韧窝型断心.(2)沿晶坚性断心正在沿晶坚性断心上,险些不塑性变形的痕迹大概仅瞅到极少的韧窝.比圆,过烧后的断心,便是沿晶界氧化物薄膜爆收的一种沿晶坚性断裂.其余,18-8奥氏体不锈钢沿晶界洪量析出碳化物后,也易爆收沿晶坚断;沿晶界化教腐蚀战应力腐蚀(包罗氢坚)后爆收的断心,也皆是沿晶坚性断心.属于那类断心的另有层状断心战撕痕状断心等.上头介绍的断心微瞅形态,是依照断裂的道路去分类的.而本量死产中睹到的断心偶尔往往是由几种典型并存的混同断心.比圆,石状断心中,如果“小棱里”大概“小仄里”不是贯脱所有断里,断心时常是沿晶战脱晶混同断心.正在本量死产中根据缺陷断心的宏瞅形貌战微瞅形态便不妨推断出缺陷的典型、缺陷爆收的本果战应采与的对于策.比圆某厂死产的迫打炮炮尾,正在试炮时时常爆收合断的情况,经断心考查创制是石状断心,经选区电子衍射分解确认韧窝底部的析出相颗粒是MnS再分散现场考察认为该缺陷爆收的本果是末锻前的加热温度过下,末锻时的变形程度过小制成的.由于加热温度下,使奥氏体晶粒细大,并使MnS洪量溶进基体,锻后热却时,MhS沿细大的奥氏体晶界析出,制成晶界宽沉强化所致,厥后改变预制坯的尺寸以删大末锻的变形量,并落矮末锻前的加热温度,问题便圆谦天办理了.又比圆某厂死产的Cr—Ni—Mo—V钢某种庞大轴类锻件,正在运止中爆收的坚性断裂,经断心考验创制:此类锻件存留有棱里断心.该锻件用的钢是正在5t碱性电弧炉中用氧化法冶炼的,锭沉2.2t,锻制加热温度为1180~1200℃,保温3h以上,锻后坐时收热处理炉举止退火、扩氢处理,而后举止细加工战调量处理.调量后正在二端切与试片,做纵背断心考验,创制有棱里断心,棱里断心大多出当前庞大锻件的心部,而锻件边部仍为仄常的纤维状断心,金相构制中有沿本细大奥氏体晶界的析出相的链状搜集.棱里断心的微瞅形态,韧窝内的析出相为不准则的四边形,呈薄片状,经选区电子衍射决定为AlN.由AlN的等温析出直线可睹,正在约900℃缓缓热却时,将有洪量的AlN析出.根据上述考验截止分解认为:1)该Cr—Ni—Mo—V钢庞大轴类锻件,其棱里断心主假如正在锻制加热时温度较下,保温时间过少,正在锻后缓热历程中,固溶进基体的洪量AlN呈薄片状沿细大的奥氏体晶界呈链状搜集析出,制成微孔散合型沿晶断裂而产死的.奥氏体晶粒越细大,析出相稀度愈下,晶界强化愈宽沉. 2)锻制下温加热的时间越少,固溶人基体的AlN越多,随后缓热历程中产死校里断心的倾背越大,果此适合统制锻制加热典型是很要害的.3)由于AlN正在奥氏体区析出峰值的温度约为900℃,其析出相随保温时间的延少而减少.果此,采与落矮待料温度,减少一次过热工艺,则能加快锻后热却速度,缩小锻件正在奥氏体区AlN析出峰值温度的停顿时间,果而便能压制AlN沿细大奥氏体晶界的析出.死产考查说明,那是预防Cr—Ni—Mo—V钢锻件爆收棱里断心的灵验步伐.。
课件:第5讲 金属的断裂(断裂力学中格雷菲斯模型简介、断裂理论的应用)
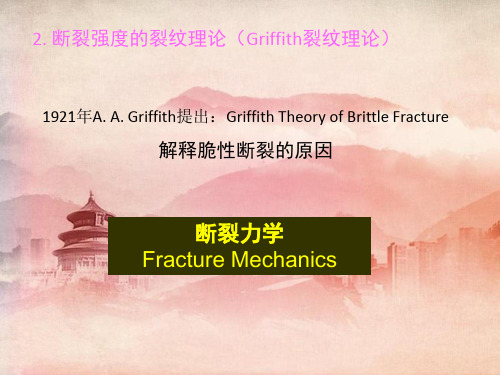
理论应力集中系数
(Theoretical Stress-concentration factor)
理论应力集中系数
K t max nominal
无限大平板圆孔周围的应力分布情况:
格雷菲斯理论
当此值达到(1-44)时,裂纹开始扩展,
一般裂纹: 裂纹很尖:来自1cE s
4aa 0
2
1
c
E s
Eq.(1-50)
平面应变状态(厚板缺口拉伸)
平面应变状态: z (0 厚板 z) 0,弹性变形
• 裂纹扩展的临界应力:
1
c
2E s (1 2 )a
2
Eq.(1-51)
• 临界裂纹长度:
ac
2E s (1 2 )
Eq.(1-52)
2
应力集中(Stress Concentration)
• 含有裂纹的平板在弹性变形范围内应力分布如下图所示
常数
常数
系统失稳的临界条件
(Ue
W)/a
( 2a2
E
4a s )
/
a
0
Eq.(1-48)
(Ue W)
被微分的函数 是一条下凹函数曲线
极大值条件 教材中图 1-35
裂纹扩展的临界应力(Griffith公式)
1
c
2E s a
2
Eq.(1-49)
临界裂纹长度(Griffith公式)
ac
2E s 2
《断裂力学》中著名的Griffith模型
平面应力状态: z 0 (薄板),弹性变形
产生2c(2a)裂纹所释放的弹性能:
Ue
2a2
E
Eq.(1-46)
产生2c(2a)裂纹所需要的表面能:
(2)金属塑性变形宏观规律与微观机制课件

图3-4 拔长坯料的变形模式
图3-5 不同宽度坯料轧制时 宽展情况
图3-6 轨辊直径不同时 轧件变形区 纵横方向阻力图 (D′>D,B′2>B2)
§3. 2 影响金属塑性流动和变形的因素
3. 2. 1 摩擦的影响 3. 2. 2 变形区的几何因素的影响 3. 2. 3 工具的形状和坯料形状的影响 3. 2. 4 外端的影响 3. 2. 5 变形温度的影响 3. 2. 6 金属性质不均的影响
2.工艺条件对残余应力的影响
变形条件: 主要是变形温度、变形速度、变形程度、接触摩擦、工具和变形物体形状等等。 热处理条件:
淬火温度、淬火介质条件、淬火方式、工件形状尺寸等。
3.残余应力所引起的后果
(1)引起物体尺寸和形状的变化。 (2)使零件的使用寿命缩短。 (3)降低了金属的塑性加工性能。 (4)降低金属的耐蚀性以及冲击韧性和疲劳强度等。
3. 2. 2 变形区的几何因素的影响
变形区的几何因子(如H/D、H/L、H/B等)是影响变形和应力分布很重要的因素。
图3-10 钢球压缩时的流线
图3-11 受塑压时物体内部质点 滑移变形的近似模型
图3-12 h2 为各种数值时的情况
3. 2. 4 外端的影响
外端(未变形的金属)ห้องสมุดไป่ตู้变形区金属的影响主要是阻碍变形区金属流动,进而产生或加剧附加的应力和应变。
图3-15 拔长时外端的影响
(a)
(b)
图3-16 开式冲孔时的“拉缩” 图3-17 弯曲变形对外端的影响
3. 2. 1 摩擦的影响
摩擦影响的实质:由于摩擦力的作用,在一定程度上改变了金属的流动特性并使应力分布受到影响。