IMID2007-3M精度障壁制作工艺
3M防火封堵方案
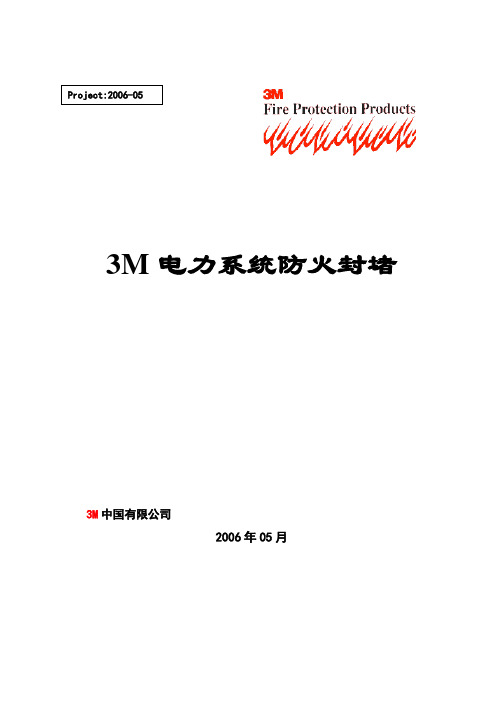
Project:2006-053M电力系统防火封堵3M中国有限公司2006年05月一. 3M公司简介3M公司全称为明尼苏达矿业制造股份有限公司(由英文全名M innesota M ining & M anufacturing Corporation中前三个英文单词的首字母组成),多年来一直是全球500强企业之一,并名列全球“最受崇敬企业”前十位,也是美国华尔街道琼斯30种工业股票成分指数的公司。
公司创建于1902年,总部设立在美国明尼苏达州圣保罗市。
3M生产制造的产品在世界二百多个国家及地区进行销售。
一百年来,3M针对客户的需求发明了多不胜数的创新产品。
“3M创意全为您”的企业精神已成为3M公司服务客户的真实写照。
3M中国有限公司在中国由外商投资的独资企业,并在国内建有自己的工厂和技术中心,可更好地为中国的客户提供全面的技术服务。
3M防火封堵材料产品是基于其核心技术---精密陶瓷材料开发出来的创新产品,产品完全符合市场需求。
得到全球范围内广大客户的充分信赖。
3M卓越的产品质量,严格的质量控制,让全世界的客户感到放心。
今天,3M防火延烧产品已广泛应用在核电站、高层建筑、化工厂、电信大楼、变电站、发电厂、医院、半导体芯片厂、钢铁厂、军工厂、船舶工业、银行、大型公众场所等等。
全系列的防火封堵材料组成了3M的具有创新意义的完善的建筑物被动防火保护系统,这些系统有助于阻止火焰、烟雾及有毒气体的蔓延和传播。
产品被许多权威机构如UL、FM、Warnock-Hersey、Omega Point及中国国家防火材料检测中心NCFM检测认证为合格的被动防火保护系统。
事实上3M公司是世界上目前为止唯一的能够制造出如此众多的被认证的被动防火材料的公司。
本资料介绍使用的3M公司防火封堵材料已通过国家防火建筑材料质量监督检验中心检测合格。
所使用的3M公司防火封堵材料通过了美国UL:Underwriters,Inc.保险商实验所(又称美国安全检测实验室)和美国FM:Factory Mutual Researcdh 美国FM保险公司研究中心检测合格。
彩色等离子体显示器的障壁制造工艺

彩色等离子体显示器的障壁制造工艺随着科技的进步和人们对高质量显示的需求不断增加,彩色等离子体显示器作为一种高分辨率、高对比度的显示技术逐渐得到了广泛应用。
而彩色等离子体显示器中的障壁制造工艺是实现其高质量显示的重要关键。
彩色等离子体显示器的障壁是指屏幕上的红、绿、蓝三种荧光物质之间的隔离结构,它的制造工艺直接影响着显示器的分辨率、对比度和色彩饱和度等性能指标。
彩色等离子体显示器的障壁制造工艺需要使用到光刻技术。
光刻技术是一种利用光敏胶涂层和光刻胶板的显影、曝光和刻蚀等工艺步骤,将光刻胶板上的图案转移到基板或薄膜上的高精度制造工艺。
通过光刻技术,可以在彩色等离子体显示器的基板上制造出微小的颜色隔离墙。
彩色等离子体显示器的障壁制造工艺需要使用到薄膜沉积技术。
薄膜沉积技术是一种通过物理或化学方法将薄膜材料沉积在基板上的工艺。
在彩色等离子体显示器的障壁制造中,常用的薄膜沉积技术有物理气相沉积(PVD)和化学气相沉积(CVD)等。
这些技术可以在基板上沉积出具有高透明度和高平整度的薄膜,用于构成彩色等离子体显示器的颜色隔离墙。
彩色等离子体显示器的障壁制造工艺还需要使用到微影技术。
微影技术是一种通过光刻和刻蚀等工艺步骤,在基板上制造出微小图案的工艺。
在彩色等离子体显示器的障壁制造中,微影技术可以用来制造出红、绿、蓝三种荧光物质的小孔阵列,以实现颜色的隔离和显示。
彩色等离子体显示器的障壁制造工艺还需要考虑材料选择和工艺参数的优化。
障壁材料需要具有高透明度、低漏光性和良好的耐久性等特性,以确保显示器的性能和寿命。
而工艺参数的优化则需要考虑到障壁的厚度、孔径和间距等因素,以实现最佳的显示效果。
彩色等离子体显示器的障壁制造工艺是一项复杂而关键的技术。
通过光刻、薄膜沉积、微影和材料选择等工艺步骤的组合应用,可以制造出高质量的彩色等离子体显示器障壁,实现优异的分辨率、对比度和色彩饱和度等显示效果。
随着科技的不断进步,相信彩色等离子体显示器的障壁制造工艺将会不断优化和创新,为人们带来更加出色的视觉体验。
3m布制作工艺

3M布制作工艺简介3M布是一种由3M公司开发的高性能复合材料,具有优异的耐磨、耐腐蚀和抗撕裂性能。
它由纤维素材料和聚合物树脂组成,经过特殊工艺制作而成。
3M布广泛应用于汽车、航空航天、电子、建筑等领域,是一种重要的工业材料。
制作工艺1. 材料准备制作3M布所需的材料包括纤维素材料、聚合物树脂、添加剂等。
纤维素材料可以选择天然纤维如棉、麻,也可以选择合成纤维如涤纶、尼龙等。
聚合物树脂可以选择丙烯酸酯、聚氨酯等。
添加剂可以根据需要选择防火剂、增强剂等。
2. 纤维素材料处理将选定的纤维素材料进行预处理,包括洗涤、漂白、干燥等。
这些步骤可以去除杂质、改善纤维质量。
3. 聚合物树脂制备将选定的聚合物树脂与添加剂按照一定比例混合,并进行加热、搅拌等处理,使其充分融合。
4. 复合制备将处理好的纤维素材料与聚合物树脂混合物进行复合制备。
可以采用浸渍法、涂布法、熔融法等不同的工艺。
其中,浸渍法是最常用的制备方法,具体步骤包括: - 将纤维素材料浸入聚合物树脂混合物中,使其充分浸润; - 将浸润好的纤维素材料取出,经过一定的脱水、固化等处理; - 将固化后的材料进行烘干,使其达到一定的硬度和稳定性。
5. 后处理制备好的3M布需要进行后处理,包括修整、打磨、涂覆等。
这些步骤可以改善材料的表面质量和外观。
应用领域1. 汽车行业3M布在汽车行业中有广泛的应用,可以用于汽车内饰、座椅、车身覆盖件等部件的制作。
它具有耐磨、耐腐蚀、防火等特性,可以提高汽车的安全性和舒适性。
2. 航空航天领域由于3M布具有轻质、高强度的特性,因此在航空航天领域中也有广泛的应用。
它可以用于飞机内饰、座椅、舱壁等部件的制作,可以降低飞机的重量,提高飞行效率。
3. 电子行业3M布在电子行业中被广泛应用于电子产品的外壳、保护膜等部件的制作。
它具有良好的绝缘性能和抗静电性能,可以保护电子产品免受外界环境的影响。
4. 建筑领域3M布在建筑领域中可以用于墙面装饰、天花板、地板等部位的制作。
一种大面积高耐用性超疏水表面结构的制备方法及其产品[发明专利]
![一种大面积高耐用性超疏水表面结构的制备方法及其产品[发明专利]](https://img.taocdn.com/s3/m/92f9c9dea32d7375a51780c5.png)
专利名称:一种大面积高耐用性超疏水表面结构的制备方法及其产品
专利类型:发明专利
发明人:史铁林,林建斌,廖广兰,李小平,孔令贤,罗京,段暕
申请号:CN202010899353.5
申请日:20200831
公开号:CN112028010A
公开日:
20201204
专利内容由知识产权出版社提供
摘要:本发明属于微纳结构相关技术领域,并具体公开了一种大面积高耐用性超疏水表面结构的制备方法及其产品。
该方法包括:在基底表面制备刻蚀掩膜层,并通过刻蚀在基底上制得倒锥形阵列;对倒锤形阵列进行纳米压印,以此制得锥形掩膜,然后进行一次倒模,获得倒锥形阵列结构;构建耐磨层,获得倒锥形模板,利用疏水聚合物对倒锥形模板进行二次倒模,制得锥形阵列结构;对锥形阵列结构的表面进行研磨,以得到锥台阵列结构。
本发明采用一次倒模、构建耐磨层的方式制备大面积倒锥形模板,后续利用疏水聚合物进行二次倒模得到大面积的超疏水表面,无需任何低表面能物质修饰,最后通过研磨进行微纳结构的加工,能够进一步提高表面的粗糙度和结构稳定性。
申请人:华中科技大学
地址:430074 湖北省武汉市洪山区珞喻路1037号
国籍:CN
代理机构:华中科技大学专利中心
更多信息请下载全文后查看。
3M灯箱制作工艺 ppt课件
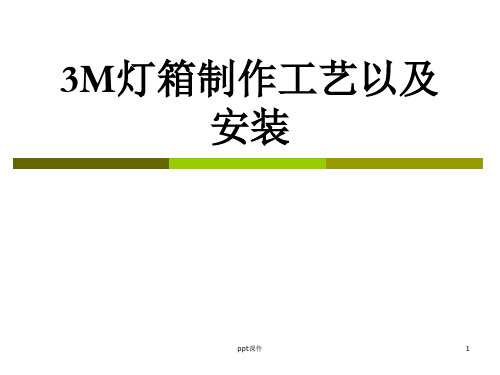
ppt课件
39
卷尺测量
3
ppt课件
8
二、灯箱的结构及安装
灯箱结构的制作
1)灯箱主体结构:为灯箱的主要框架,决定 灯箱的外观形状、牢固程度、重量及结构耐久 性等方面。
ppt课件
9
二、灯箱的结构及安装
灯箱结构的制作
灯箱主体结构 前檐口使用角钢反焊, 前檐口扣板折弯1cm,打灯后正
面无阴影。
ppt课件
10
二、灯箱的结构及安装
电器的安装
ppt课件
16
二、灯箱的结构及安装
5)灯箱的灯具排布:
a.灯管的排列间距为200~250mm(40~50cm LEF), b.灯管距灯箱布距离应大于150mm。 c.电线必须为阻燃型。灯管以灯管夹固定于灯箱内框
架上。灯管应尽量横排。 d.相临两排灯管头部必须搭接7-10cm。 e.电线连接采用压线帽连接,总线与分线路连接采用
制 电工
操作符合国家《低压电气规范》要求; 电线连接处用压线帽连接; 分线路与电源总线连接处使用接线端子; 电源线出灯箱处用橡胶护圈保护; 保证灯箱箱体良好接地; 电源线规格必须根据灯箱内灯具功率计算数据选用; 电源线在灯箱外部分必须外套PVC管或镀锌管保护。
钢结构部分完工后全部手工打磨去除表面氧化层;
ppt课件
13
二、灯箱的结构及安装
灯箱主体结构、灯箱辅助结构、功能构件等框架结构在焊 接完毕后,应去除焊渣并人工打磨除锈,至少涂刷两遍防 锈漆后,喷涂白色硝基漆。
焊接:
选用J422焊条,满 焊,焊缝堆高不小于 3mm,焊接后打磨 焊缝,手工除锈,涂 刷两遍 以上防锈漆后 喷涂一遍白色硝基漆。
利用等离子体表面预处理改善光掩模IP胶显影工艺特性

利用等离子体表面预处理改善光掩模IP胶显影工艺特性李勇;程秀兰
【期刊名称】《微细加工技术》
【年(卷),期】2007(002)002
【摘要】IP胶亲水性较差,在显影时易造成显影不完全.介绍了一种在显影前适当增加等离子体表面预处理,以提高IP胶表面微粗糙度,进而改善IP胶显影特性的方法.研究表明,这种方法可有效地提高IP胶的亲水性和显影均匀性,其中静态接触角可从原来的77°降至45°,而IP胶的厚度损失仅为3 nm~5 nm;同时,还可有效降低由于胶表面的颗粒污染所造成的铬金属点缺陷数量,即从原来的4颗/块降至0.53颗/块.除此之外,这种方法还非常有助于提高具有密集图形和带孔掩模版的图形分辨率和成品率,其中成品损失率可从原来的14%降至处理后的2%.
【总页数】4页(P16-19)
【作者】李勇;程秀兰
【作者单位】上海交通大学,微电子学院,上海,200030;上海凸版光掩模有限公司,上海,200233;上海交通大学,微电子学院,上海,200030
【正文语种】中文
【中图分类】TN305.7
【相关文献】
1.小顶角平台硅中阶梯光栅光刻胶掩模制备工艺研究 [J], 焦庆斌
2.全息光栅制作中光栅掩模槽形形状随光刻胶特性曲线的演化规律 [J], 韩建;巴音
贺希格;李文昊;孔鹏
3.孤立接触孔掩模显影工艺优化 [J], 张海平;尤春;周家万;陈卓
4.施胶工艺对常压冷等离子体处理改善杨木单板胶合特性的影响 [J], 章蓉;周晓燕;汤丽娟;杨雪慧;陈钊
5.全息光栅掩模制备中的光刻胶薄膜特性控制研究 [J], 陈南曙;黄元申;张大伟因版权原因,仅展示原文概要,查看原文内容请购买。
美国IDEA07展会上的纺粘、熔喷法非织造布新技术介绍

非 织造 布
N o wov ns n e
Vo . 5. 1 1 No. 5 OC . 20 t . 07
≥ ≯ 薹
毒≥ ≥≯ ≯ 0 ≥ i_薯 i- 参 ≥ ≮ ≯ 叠 0_ ≯ - =
麓 麓 燎 篓 ≤0囊麓 ≥ ≯蔓0移曩≯ 羔 0: :薯 尊■:毒 ≯ 0 参 : ; 誓 ≯警≯誓 纛 : -≯嚣 0 — 蓦 : :黟 薯0: 豸 I 等 第 j
剪彩 了此 次展 览 会的开幕 仪式 。 I DA会 长介绍 , 自全球 6 个 国家 和地 区 N 来 0多
的 4 0多 家 公 司参 展 。 中 1 1家 企 业 首 次 参 展, 0 其 2
接 到美 国希 尔斯 ( l ) 司 的邀 请 , 织 相 关 企 业 His 公 l 组 参观 了位于 墨 尔本 市 的 His 厂 和纺 粘 法 及 熔 喷 l工 l
维普资讯
20 年 ( 0 7 总第 6 3期 )
熔 喷双组分 技术 的生 产 线 投产 ; 目前 日本 可 乐 丽公 司正在 与其接 洽有关 “ 纺粘 +水刺 ” 非织 造布 生产线
的项 目。之后 , 们参观 了其 工厂 内的试 验线 , 线 我 该
时 1 中旬将 会在 印度 首 次 召开 有 关 非织 造布 的 0月 会议 。2 4日当天 印度 I R C A首 席 经 济 学 家 和 印度
市 场作 了预测 ; 并介 绍 了该 公 司在 纺粘法 、 喷法 非 熔
此次展 览 会 的 主 题 关 键 词 为 : 印度 、 源 和 创 能 新 。印度 拥 有 众 多 的 人 口, 过 8 的 G P增 长 超 % D
率, 未来 的 消费 市场 将 会 非 常 可观 。近 两 年来 印度
障壁基本概念、制作方法和工艺

P-18
3. 感光性浆料法
P-19
感光性浆料法
• 工艺步骤:涂敷感光性浆料(第一层)→曝光→涂 敷感光性浆料(第二层)→曝光→……→显影→高 温烧结形成障壁。
• 缺点:工艺复杂,对位要求精度高,材料成本高。
P-20
日本TORAY公 司有一种感光性 障壁浆料,不需 要多次涂敷、曝 光,可以一次性 完全曝光,因此 工艺非常简单, 且不存在对位的 要求,是制作障 壁的一种非常理 想的材料。
• 优点:障壁尺寸均一性好,效率高,且能形成精细 的图形,能够满足XGA及其以上精度产品的要求。
• 缺点:材料使用率低。
P-23
P-24
5. 填充法
Thick Layer Resist
Exposure/Develop
Squeezing Glass Paste into grooves
Strip
填充法
• 主要技术要求:对障壁的要求是高度一致(偏差在5m以 内),形状均匀,还要求具有可以支撑前基板的强度特性。 在保证障壁强度的前提下,障壁宽度应尽可能窄,以增大 单元的开口率,提高器件亮度。
• 障壁是构成PDP放电单元的基本要素,其高度和宽度直接 影响放电空间的大小和控制驱动电路的动态范围,它们在 全屏范围内的一致性更是决定显示器性能的重要指标。
• 对材料的要求:需要浆料能同时具有保形性和流 动性两个相反的特性,并且梳挤极为高精度。
• 工艺步骤:涂敷感光材料→曝光→显影形成与障 壁相反的图形→填充障壁材料→除去感光胶→高 温烧结形成障壁。
• 优点:材料损耗少,不存在环境问题,制作出的 障壁高宽比大,形状呈典型的窄梯形。且使用的 感光材料与障壁的剥离性好,障壁的侧面光滑无 损伤。
- 1、下载文档前请自行甄别文档内容的完整性,平台不提供额外的编辑、内容补充、找答案等附加服务。
- 2、"仅部分预览"的文档,不可在线预览部分如存在完整性等问题,可反馈申请退款(可完整预览的文档不适用该条件!)。
- 3、如文档侵犯您的权益,请联系客服反馈,我们会尽快为您处理(人工客服工作时间:9:00-18:30)。
Abstract3M has developed a Precision Replication Process for the produ ction of PDP Barrier Ribs and other display devices. This process, is fast, clean and capable of produ cing very high resolu tion (FHD and beyond), high apertu re ratio and fine cell stru ctu res. Recent advances in materials and process features will be discussed.1. IntroductionPresently, PDP manufacturers face multiple challenges to maintain a strong position in the field of Large Area TV Displays. W hile PDP TVs feature many superb visual properties and offer great value to the consumer, ever increasing customer expectations for quality and feature improvements are coupled with demands for lower costs and greater value.In particular, the competitive pressure from the wide scale availability of 1080p capable LCD TV’s is a serious threat to the PDP Industry. It is a significant problem that no PDP manufacturer has yet introduced a 40” class PDP TV offering full high definition(FHD - 1920 x 1080) resolution. Recent market analysis shows 40” class PDP’s loosing market share to the widely available 1080p capable LCD’s.The PDP industry has consistently underestimated the importance of high resolution over the past 5 years. Even now, future display requirements are in fact forming for even higher (QFHD – 3840 x 2160) and 8Kx4K resolution displays.Amongst the technical challenges to be resolved are the economic production of a fine feature rib structure, increased aperture ratio and luminous efficiency [1] [2] [3] [4] and compatibility with environmental requirements such as RoHS.2. Process DescriptionAll presently practiced processes used to fabricate barrier rib plate discharge cell microstructures are subtractive processes. Subtractive means that material is machined away by various means (chemical or mechanical etching or photo-lithographically) until the desired microstructure is formed. This is a slow and often low yield process leading to the production of much waste materials (frit, blast media, photoresist…) and energy inputs.Alternately, 3M has developed a new “Additive” fabrication methodology for the production of fine structures such as PDP Barrier Rib’s. An additive process provides inherent design flexibility, simplicity and economies of operation beyond those achieved with conventional processes [4] [5] [6]. Material consumption energy, labor and capital are reduced by more than 50%.The 3M process (Fig 1) is a lamination molding process. It is based upon the development of a unique set of materials (3M Barrier Rib paste and Precision Sheet Mold) and the 3M rib replication process. Major process steps would include the following:Steps 1-2 Required once at initial setup of process1.) Initial registration & alignment of sheet mold2.) Initial registration of glass plate fiducialsSteps 3-6 Comprise Process Cycle3.) Coating of glass frit paste onto glass substrate 30 sec4.) Lamination of sheet mold onto substrate 30 sec5.) Paste light cured (through mold or glass) 30 sec6.) Mold stripping (mold is reusable for next cycle) 30 sec Total Cycle Time ~2 min7.) Conventional debinding and sintering processing.Recent Advances with the 3M PDP High Resolution Rib ReplicationProcessP. McGuire*, J.C. Cha#, H. Kikuchi#, A. Yoda#*3M Company: 3M Center, Building 235-1WS-46, Saint Paul, MN 55144-1000 USATEL: 1-651-736-1770, e-mail: pmcguire@#Sumitomo 3M Ltd: 8-8, Minami-Hashimoto 3-chome, Sagamihara-shi, Kanagawa 229-1185 JapanTEL:82-2-320-1616, e-mail: yskim@wow.tech.ac.kr.2Dept. of Electric Engineering, Your College, Town/City, MA 02139, U.S.A.Keywords: Barrier Rib, Transfer, Multi-panel20-1 / P. McGuireIMID '07 DIGEST313.Fig. 1. 3M Precision Replication Process MapThis simple 4 step process yields a green cured ceramicmicrostructure which incorporates a dielectric layer over theaddress electrodes. Process cycle time is minimally invariant with respect to panel size or resolution. Typicalcycle time is ~2 minutes. Equivalent sandblasting andchemical etching process times can exceed 200 minutes and comprise 10-15 yield-robbing process steps. 3. Process Materials PerformanceSheet mold and paste materials compatibility,precision and quality are key elements of the 3MBarrier Rib process. Novel and proprietarymanufacturing processes enable the accurateproduction (Fig 2) of large format sheet molds.Fig. 2. Sheet Mold Precision Forming MetrologyEconomic use of the process is assured through the reusability of the precision replicated sheet molds. Careful selection of materials ensures long term compatibility and the preservation of sheet molddimensional precision.4. Multi-panel Production CompatibilityThe economic production of PDP modules requires the ability to process multiple Barrier Rib plate panels simultaneously. Panel production configurations can consist of simple 1 dimensional arrays comprising 2 and 3-up strips and more recently 2 dimensional arrays of 4, 6 and 8-up production, Some PDP OEM’s are planning new production processes that anticipate 10-up production of 42” panels. 8-up and 10-up production would utilize huge mother glass substrates with typical dimensions of 2x3 meters. Despite these huge dimensions, the 3M process can be used effectively with multi-panel production. Whileit is almost impossible to envision a thin, flexible plastic sheet mold which could be dimensionallyaccurate over size scales of 3 meters, the process can be economically and accurately broken down into smaller elements.3M has developed the ability to produce 2-up sheet molds with precision. Shown below (Fig.3.) is ametrology map of a typical 42” 2-up FHD sheet mold.We describe this layout as a series configuration. Twosuch molds can be utilized to meet a 4-up productionrequirement; four such molds can complete an 8-upconfiguration.Fig. 3. 42” 2-up Sheet Mold - Typical MetrologyAlternately, multi-up production can be completed by the use of multiple 1-up sheet molds and a multiple-headed precision lamination machine. Such a20-1 / P. McGuireIMID '07 DIGEST314.machine configuration provides the lowest cost production configuration and highest reliability and flexibility.5. Multi-panel Production Laminator Designs Our basic machine design concepts for a 1-D (strip type) multi-headed laminator is shown (Fig. 4.) below.Fig. 4. 1-D (strip type) Multi-panel LminatorOur more advanced machine design concept for a 2-D (X x 2 panel array type)is shown (Fig. 5.) below.Curing Lamps CameraLaminating RollMold SheetBack PanelFig. 5. 2-D Mul ti-up Mul ti-headed sheet mol d laminatorKey elements of this design include the ability to use either 1-up or 2-up sheet molds, the feeding of individual sheet molds from a sheet mold magazine and the individual sheet mold alignment & clamping mechanisms. Production using this process concept would follow the following process steps:Step 1 Required once at initial setup1.) Load sheet molds and align to machine datumStep 2 Completed previously on other equipment 2.) Pattern coat glass frit paste onto mother glassSteps 3-7 Process Cycle3.) Register mother glass to machine datum4.) Laminate individual sheet molds to mother glass5.) Cure paste6.) Delaminate sheet molds7.) Inspect finished panel patternsAutomatically adjust sheet mold positions as neededReplaceindividualsheet molds as needed6. SummaryThe 3M R ib R eplication process provides many features and benefits to the PDP Industry and the consumers which we serve. Improved display quality, aperture ratio, resolution, and manufacturing productivity and cost are shown to be possible with this process. Methods of scaling the process to the multi-panel production needs of the industry have been shown.7. References[1] J inno, Satoshi, “Development of 50-in Diagonal Full HD (1920x1080) PDP’s, Proc. SID ’06, pp147-150[2] Yim, Sang-Hoon, “A Study on Full High-Definition PDP’s of under 50in”, Proc. SID ’06, pp 155-158[3] Tolner, Harm, “Color Plasma Display Manufacturing”, SID ’01 Seminar F-4, ppF-4/1-21[4] Kim, Young-Seog, “Characteristics of Counter Electrode Discharge Cells of PDP”, Proc SID ’06, pp 579-581[5] Choi, Hak-Nyun, “Formation of Barrier Ribs for PDP by Micro-Injection Molding Route”, Proc SID ’03,pp 463-465, [6] Toyoda, Osamu, “Low Cost Barrier Rib Formation Technologies for High Efficiency PDP’s”, Proc SID ’03, pp 1002-100520-1 / P. McGuireIMID '07 DIGEST315.。