SiC_Cu材料磨损界面研究(2)
材料表面与界面(2-4).

在具有面心立方晶 体结构的SiC晶须 内部观察到了大量 在{111}面上的孪 晶和层错
面心立方SiC晶须中层错(a)和孪晶(b)的高分辨透射电镜照片
第2章 材料表面与界面的基础知识
2.4 固体和固体之间的界面
在具有面心 立方晶体结 构的Cu中也 很容易地观 察到{111} 孪晶的存在
材料的表面与界面 Surfaces and Interfaces in Materials
第2章 材料表面与界面的基础知识
第2章 材料表面与界面的基础知识
2.4 固体和固体之间的界面
固体和固体之间的界面可以分为同相界面和异相界面。 同相界面是指具有不同晶体取向或者有过渡层分开的两个相同相晶体组成的界面, 如晶界、孪晶界和层错。
2.4.1 同相界面(晶界)
(1)小角晶界
界面处主要有{111} 晶面和少量的{001} 晶面构成,并且是由 大部分的原子匹配区 域和周期出现的少量 位错组成。因此,对 称倾斜晶界的界面能 高于完全匹配的孪晶 界,但高于由非密排 晶面组成的小角晶界 界面能。
面心立方Au中的对称倾斜晶界的高分辨透射电镜照片
第2章 材料表面与界面的基础知识
2.4 固体和固体之间的界面
2.4.1 同相界面(晶界)
(3)大角晶界能量 晶界的能量为单位面积自由能,包含表面张力和成分 偏聚的影响。EFra biblioteka t
dF dA ii dA
式中:i——i元素化学,Γi——i元素界面与内部浓度 差 从图2-17可以看出,在小角晶界范围内,晶界能(E) 随晶界位向角(θ)的增加而迅速增大。大角晶界界面 能与位向角基本无关,但在共格孪晶(t)和重合位置
点阵(a和b)出现时,晶界能有一个明显的下降。
MoS_2与金属表面摩擦后生成转移膜的研究――Ⅰ

MoS_2与金属表面摩擦后生成转移膜的研究――Ⅰ.用AES和SEM的初步考察MoS_2是一种重要的二维材料,其在催化、电池、传感器等领域具有广泛的应用。
然而,MoS_2与金属表面之间的摩擦行为及其形成的转移膜却一直是一个热门研究领域。
本文通过应用Auger电子能谱(AES)和扫描电子显微镜(SEM)技术,对MoS_2与金属表面摩擦后生成转移膜的研究进行初步考察。
首先,实验中使用的金属表面为铜(Cu)。
在MoS_2与Cu表面摩擦的过程中,AES测试结果显示,MoS_2表面的S原子会逐渐与Cu表面的Cu形成化学键,并形成一层薄膜,这层薄膜被称为转移膜。
该转移膜的组成主要为MoS_2、Cu_2S 和CuS。
值得注意的是,转移膜的形成是一个相对慢的过程,需要较长时间才能形成。
其次,SEM测试结果显示,MoS_2与Cu表面摩擦后形成的转移膜有明显的层状结构。
通过SEM观察,可以看到膜的表面上有许多微小颗粒,这些颗粒可能是MoS_2与Cu表面在摩擦过程中剥落的颗粒。
此外,薄膜的厚度也呈现出一定的变化,可能是由于摩擦次数不同导致表面剥落的颗粒数量和大小不同。
综上所述,本文通过AES和SEM技术的初步考察,研究了MoS_2与金属表面摩擦后形成的转移膜。
结果表明,转移膜的形成是一个相对慢的过程,转移膜的组成主要为MoS_2、Cu_2S和CuS,且膜的表面有明显的层状结构和微小颗粒存在。
这些发现有助于深入理解MoS_2与金属表面之间的摩擦行为及其应用于催化、电池、传感器等领域的机制。
此外,由于MoS_2是一种常见且重要的固体润滑材料,在工程领域中应用广泛。
因此,研究MoS_2在金属表面上的摩擦行为及其生成的转移膜对于摩擦学领域的发展和应用具有重要的意义。
研究表明,MoS_2与金属表面之间的摩擦行为是一个复杂的过程,受到多种因素的影响。
例如,表面化学性质、压力、速度、温度和湿度等因素都会对摩擦行为产生不同的影响。
在实际工程应用中,需要结合实际情况进行优化设计,以达到最佳的润滑效果、摩擦性能和耐磨性能。
3C-SiC界面的研究的开题报告

光电子能谱线站的建设及Cu/3C-SiC界面的研究的
开题报告
一、研究背景
光电子能谱(PE)可以很好地研究物质的电子结构和表面化学反应。
随着现代科技的发展,越来越多的实验室和研究机构开始关注光电子能谱技术的应用。
本文拟建设一条光电子能谱线站,主要用于研究Cu/3C-SiC界面的性质和特征。
二、研究内容
本文主要研究以下内容:
1、建设光电子能谱线站,选用适合的仪器设备,优化实验流程和条件,建立光电子能谱研究平台。
2、针对Cu/3C-SiC界面的问题,采用光电子能谱技术研究该界面结构、成分、电子态密度等性质,探讨Cu/3C-SiC界面特征和机理,为今后开展材料处理和系统工程研究提供理论基础。
三、研究方法
1、建设光电子能谱线站,选用高分辨率的光电子能谱仪,引进在PE 实验分析和数据处理方面有着深厚实践经验的专家组成研究团队。
2、采用光电子能谱技术研究Cu/3C-SiC界面结构和性质,包括表面和体内的电子结构和化学反应。
通过对光电子光谱和角分辨数据的测量和分析,揭示界面上的化学反应机理和物理特性。
四、研究意义
1、建设光电子能谱线站将为材料科学、光子学和化学等多学科研究提供充分的测试手段和研究工具,加速学科交叉和协同发展。
2、探究Cu/3C-SiC界面特征和机理,对于了解此类材料的性质和应用前景具有重要意义。
3、为今后科学家和工程师提供研究依据,为新型电子材料设计和制备提供一系列指导,有望为相关领域的技术进步和工程应用做出积极贡献。
钛合金摩擦磨损及改善技术的研究进展
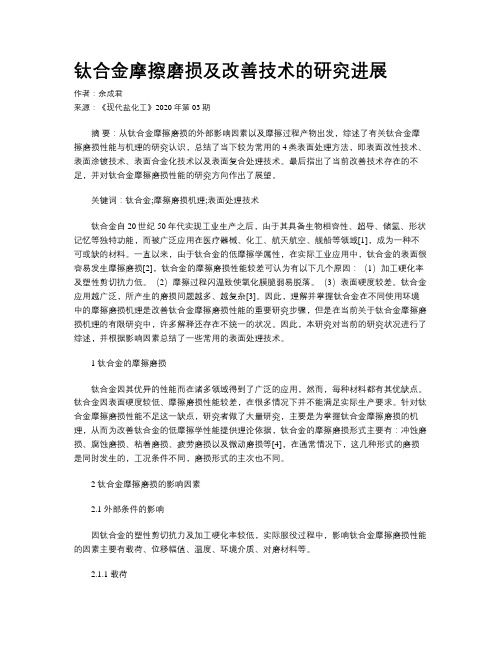
钛合金摩擦磨损及改善技术的研究进展作者:余成君来源:《现代盐化工》2020年第03期摘要:从钛合金摩擦磨损的外部影响因素以及摩擦过程产物出发,综述了有关钛合金摩擦磨损性能与机理的研究认识,总结了当下较为常用的4类表面处理方法,即表面改性技术、表面涂镀技术、表面合金化技术以及表面复合处理技术。
最后指出了当前改善技术存在的不足,并对钛合金摩擦磨损性能的研究方向作出了展望。
关键词:钛合金;摩擦磨损机理;表面处理技术钛合金自20世纪50年代实现工业生产之后,由于其具备生物相容性、超导、储氢、形状记忆等独特功能,而被广泛应用在医疗器械、化工、航天航空、舰船等领域[1],成为一种不可或缺的材料。
一直以来,由于钛合金的低摩擦学属性,在实际工业应用中,钛合金的表面很容易发生摩擦磨损[2],钛合金的摩擦磨损性能较差可认为有以下几个原因:(1)加工硬化率及塑性剪切抗力低。
(2)摩擦过程闪温致使氧化膜脆弱易脱落。
(3)表面硬度较差。
钛合金应用越广泛,所产生的磨损问题越多、越复杂[3]。
因此,理解并掌握钛合金在不同使用环境中的摩擦磨损机理是改善钛合金摩擦磨损性能的重要研究步骤,但是在当前关于钛合金摩擦磨损机理的有限研究中,许多解释还存在不统一的状况。
因此,本研究对当前的研究状况进行了综述,并根据影响因素总结了一些常用的表面处理技术。
1 钛合金的摩擦磨损钛合金因其优异的性能而在诸多领域得到了广泛的应用,然而,每种材料都有其优缺点。
钛合金因表面硬度较低、摩擦磨损性能较差,在很多情况下并不能满足实际生产要求。
针对钛合金摩擦磨损性能不足这一缺点,研究者做了大量研究,主要是为掌握钛合金摩擦磨损的机理,从而为改善钛合金的低摩擦学性能提供理论依据,钛合金的摩擦磨损形式主要有:冲蚀磨损、腐蚀磨损、粘着磨损、疲劳磨损以及微动磨损等[4],在通常情况下,这几种形式的磨损是同时发生的,工况条件不同,磨损形式的主次也不同。
2 钛合金摩擦磨损的影响因素2.1 外部条件的影响因钛合金的塑性剪切抗力及加工硬化率较低,实际服役过程中,影响钛合金摩擦磨损性能的因素主要有载荷、位移幅值、温度、环境介质、对磨材料等。
碳碳化硅复合材料摩擦磨损性能分析
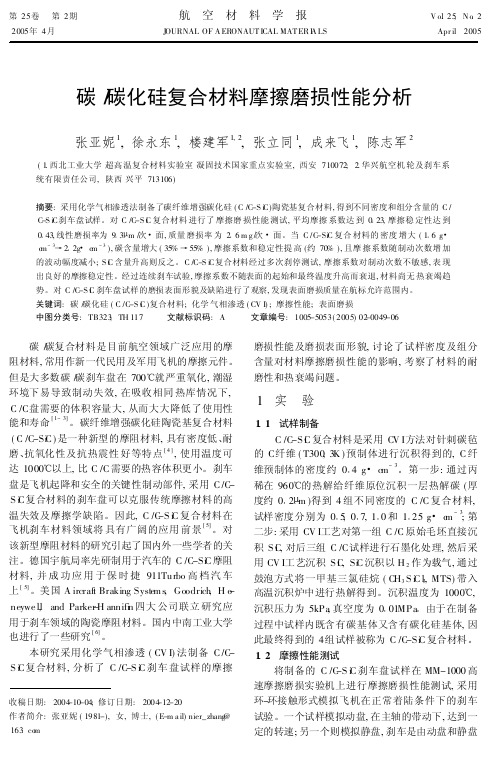
表 1 C /C-S iC 复合材料刹车盘的磨损率 T ab le 1 T he w ear rate of C /C-S iC d isks
T ype
Th ickness loss /Lm# cycle- 1
W e ight lo ss /m g# cyc le- 1
Rotating disk Stationary disk Ro tating disk Stationary disk
现 / 前峰 0, 中间过程平稳且有增大趋势, 接近刹停 时急剧上升, 静止时达到最大, 曲线存在 / 后翘 0现 象。刹车力矩曲线 4类似于摩擦系数曲线 3, 制动 初期出现 / 前峰 0, 中间过程平稳, 接近刹停时急剧 增大, 静止时最大。曲线 5表示摩擦面的压强曲线, 在本实验中施加给摩擦面的是恒定载荷, 压强曲线 本应是水平线, 但所有试样的压强曲线都是在一、两 秒钟后才趋于一个固定值 0182M Pa, 这是由于在仪 器设计上有响应滞后的特点。
本研究采用化学气相渗透 ( CV I) 法制备 C /CS iC复合材料, 分析了 C /C-S iC 刹车 盘试样的摩擦
收稿日期: 2作者简介: 张亚妮 ( 1981-), 女, 博士, ( E-m a il) nier_zhang@ 163. com
制动时间 t / s, 摩擦稳定性系数 S, 其计算公式为:
S = Lcp / Lm ax
( 1)
式中: Lcp代 表平均摩擦系 数, Lmax 代表最 大摩擦系
数。
1. 3 密度及表面形貌测试 测试了 4组 C /C-SiC 复合材料的密度, 在模拟
刹车试验完成后, 采用光学显微镜对 C /C-SiC 试样
观 察 C / C-SiC复合材料在每一次刹车实验中的
SiC_体积分数对铜基复合材料性能的影响

SiC体积分数对铜基复合材料性能的影响蔡佳宁1,2,樊子民1,乐 晨2,李 鑫1,2,唐明强2,赵 放2(1. 西安科技大学材料科学与工程学院, 西安 710000)(2. 泉州天智合金材料科技有限公司, 福建泉州 362000)摘要 采用热压粉末冶金法引入Al和Mg元素制备SiC/Cu复合材料,研究SiC体积分数对SiC/Cu复合材料性能的影响。
采用X射线衍射、阿基米德排水法、三点弯曲法和扫描电镜分析复合材料样品的物相组成、相对密度、力学性能及微观形貌,并测定其导热系数和热膨胀系数,用ROM混合定律和Turner模型预测复合材料的热膨胀系数。
结果表明:试样基体中生成了AlCuMg相,强度大幅增加,且以混合型断裂为主;当SiC 体积分数较低时,SiC颗粒在基体中分散较均匀。
当SiC体积分数为35%时,SiC/Cu复合材料的致密度、抗弯强度、导热系数和热膨胀系数分别为98.81%、478 MPa、254.76 W/(m·K)和11.84 × 10−6 /K。
随着SiC体积分数的增加,SiC颗粒团聚较严重,复合材料的致密度、抗弯强度、导热系数和热膨胀系数随之降低,其硬度呈先增加后降低的趋势,在SiC体积分数为45%时达到最大值110 HRB。
Turner模型的预测值与复合材料实测值最为接近。
关键词 SiC/Cu复合材料;AlCuMg;力学性能;热学性能中图分类号 TB333 文献标志码 A 文章编号 1006-852X(2023)06-0743-07 DOI码 10.13394/ki.jgszz.2022.0183收稿日期 2022-11-03 修回日期 2023-03-18SiC具有低密度、高强度、高硬度、良好的导热性、导电性能及热稳定性,而Cu具有优异的导热和导电性能[1]。
SiC和Cu制成的高导热系数和高强度的复合材料,被广泛应用于电子封装、电器、换热设备、航空航天领域(如飞行器构架)、汽车领域(如刹车片、内燃机活塞和发动机叶轮)、焊接工业中的电极材料[2-4]。
CC复合材料表面SiC涂层摩擦磨损性能研究

164管理及其他M anagement and otherC/C 复合材料表面SiC 涂层摩擦磨损性能研究王锦阳(湖南工学院机械工程学院,湖南 衡阳 421000)摘 要:C/C 复合材料具有诸如重量轻,使用寿命长,产生噪音小,运行平稳等优良性能,在用作制动器时具有特别的优势,目前被认为是高性能制动系统的优良候选材料。
本文对C/C 复合材料表面SiC 涂层的研究进程及现状、制备方法、SiC 涂层的选择及性能等进行了详细的整理研究。
关键词:C/C 复合材料;制动器;氧化磨损;SiC 涂层中图分类号:TG174.4 文献标识码: A 文章编号:11-5004(2020)09-0164-2收稿日期:2020-05作者简介:王锦阳,男,生于1997年,汉族,陕西西安人,本科,研究方向:金属材料。
1 研究背景安全,稳定和舒适的制动系统是人们一直以来的追求,尤其是近年来发展迅速。
铜基金属复合材料,再加上铸钢盘,可被用作时速超过250 km/h 的火车的刹车片。
它显示出许多优异的性能,例如稳定的摩擦系数(COF),高韧性和良好的导热性,这使其有希望成为摩擦材料。
但是,其具有相对较低的耐磨性,高的密度,并且基体在高温下会软化,尤其是较短的寿命周期,限制了其长期用作为摩擦材料来使用。
本文将主要针对C/C 复合材料表面SiC 涂层摩擦磨损性能进行深入研究,为拓宽C/C 复合材料的应用范围提供行之有效的方法。
2 C/C复合材料的研究进展及应用C/C 复合材料,是基于碳或石墨纤维和织物增强的材料,是以碳(或石墨)为基质,通过加工和处理所有由碳化物以制成的碳复合材料。
C/C 复合材料具有质量轻,良好的抗侵蚀和热冲击性能,高的耐损伤性以及高的强度和刚度,使其成为一种特殊的新兴结构材料,可用于航空,航天等应用。
其独特的特点和先进的制造技术,最终导致产生了更便宜的生产工艺,使得这种材料越来越多地用于工业应用。
其在机械、冶金化工和生物医学等多个领域也具有巨大的应用潜力。
碳化硅晶圆的表面
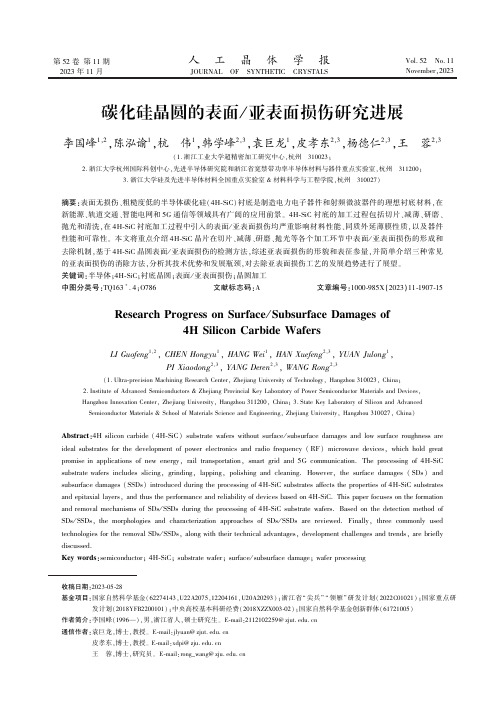
第52卷第11期2023年11月人㊀工㊀晶㊀体㊀学㊀报JOURNAL OF SYNTHETIC CRYSTALSVol.52㊀No.11November,2023碳化硅晶圆的表面/亚表面损伤研究进展李国峰1,2,陈泓谕1,杭㊀伟1,韩学峰2,3,袁巨龙1,皮孝东2,3,杨德仁2,3,王㊀蓉2,3(1.浙江工业大学超精密加工研究中心,杭州㊀310023;2.浙江大学杭州国际科创中心,先进半导体研究院和浙江省宽禁带功率半导体材料与器件重点实验室,杭州㊀311200;3.浙江大学硅及先进半导体材料全国重点实验室&材料科学与工程学院,杭州㊀310027)摘要:表面无损伤㊁粗糙度低的半导体碳化硅(4H-SiC)衬底是制造电力电子器件和射频微波器件的理想衬底材料,在新能源㊁轨道交通㊁智能电网和5G通信等领域具有广阔的应用前景㊂4H-SiC衬底的加工过程包括切片㊁减薄㊁研磨㊁抛光和清洗,在4H-SiC衬底加工过程中引入的表面/亚表面损伤均严重影响材料性能㊁同质外延薄膜性质,以及器件性能和可靠性㊂本文将重点介绍4H-SiC晶片在切片㊁减薄㊁研磨㊁抛光等各个加工环节中表面/亚表面损伤的形成和去除机制,基于4H-SiC晶圆表面/亚表面损伤的检测方法,综述亚表面损伤的形貌和表征参量,并简单介绍三种常见的亚表面损伤的消除方法,分析其技术优势和发展瓶颈,对去除亚表面损伤工艺的发展趋势进行了展望㊂关键词:半导体;4H-SiC;衬底晶圆;表面/亚表面损伤;晶圆加工中图分类号:TQ163+.4;O786㊀㊀文献标志码:A㊀㊀文章编号:1000-985X(2023)11-1907-15 Research Progress on Surface/Subsurface Damages of4H Silicon Carbide WafersLI Guofeng1,2,CHEN Hongyu1,HANG Wei1,HAN Xuefeng2,3,YUAN Julong1,PI Xiaodong2,3,YANG Deren2,3,WANG Rong2,3(1.Ultra-precision Machining Research Center,Zhejiang University of Technology,Hangzhou310023,China;2.Institute of Advanced Semiconductors&Zhejiang Provincial Key Laboratory of Power Semiconductor Materials and Devices,Hangzhou Innovation Center,Zhejiang University,Hangzhou311200,China;3.State Key Laboratory of Silicon and AdvancedSemiconductor Materials&School of Materials Science and Engineering,Zhejiang University,Hangzhou310027,China) Abstract:4H silicon carbide(4H-SiC)substrate wafers without surface/subsurface damages and low surface roughness are ideal substrates for the development of power electronics and radio frequency(RF)microwave devices,which hold great promise in applications of new energy,rail transportation,smart grid and5G communication.The processing of4H-SiC substrate wafers includes slicing,grinding,lapping,polishing and cleaning.However,the surface damages(SDs)and subsurface damages(SSDs)introduced during the processing of4H-SiC substrates affects the properties of4H-SiC substrates and epitaxial layers,and thus the performance and reliability of devices based on4H-SiC.This paper focuses on the formation and removal mechanisms of SDs/SSDs during the processing of4H-SiC substrate wafers.Based on the detection method of SDs/SSDs,the morphologies and characterization approaches of SDs/SSDs are reviewed.Finally,three commonly used technologies for the removal SDs/SSDs,along with their technical advantages,development challenges and trends,are briefly discussed.Key words:semiconductor;4H-SiC;substrate wafer;surface/subsurface damage;wafer processing㊀㊀收稿日期:2023-05-28㊀㊀基金项目:国家自然科学基金(62274143,U22A2075,12204161,U20A20293);浙江省 尖兵 领雁 研发计划(2022C01021);国家重点研发计划(2018YFB2200101);中央高校基本科研经费(2018XZZX003-02);国家自然科学基金创新群体(61721005)㊀㊀作者简介:李国峰(1996 ),男,浙江省人,硕士研究生㊂E-mail:2112102259@㊀㊀通信作者:袁巨龙,博士,教授㊂E-mail:jlyuan@皮孝东,博士,教授㊂E-mail:xdpi@王㊀蓉,博士,研究员㊂E-mail:rong_wang@1908㊀综合评述人工晶体学报㊀㊀㊀㊀㊀㊀第52卷0㊀引㊀㊀言4H碳化硅(4H-SiC)材料具有禁带宽度大㊁饱和电子漂移速率高㊁击穿电场高㊁导热系数高㊁抗辐照等优点,能够满足现代电力电子技术对高频㊁高功率㊁高温应用的要求[1]㊂而表面无损伤㊁低粗糙度的4H-SiC衬底晶圆是制造4H-SiC基电力电子器件的基础㊂由于材料的高硬度㊁强化学惰性等特点,4H-SiC的晶圆加工存在加工损耗大㊁损伤多㊁效率低等难题[2]㊂目前,4H-SiC晶圆的主要加工流程包括切片㊁减薄㊁研磨㊁抛光和清洗[3]㊂在晶圆加工过程中,减薄㊁研磨和抛光会依次去除切片引入的损伤层,实现晶圆的全局平坦化加工,得到无损伤㊁低表面粗糙度的4H-SiC晶圆㊂然而,4H-SiC晶圆的加工过程存在加工损伤去除不彻底或不可避免地引入新损伤的问题㊂根据损伤在光学显微镜检测下是否可见,4H-SiC晶圆表面的损伤分为表面损伤(surface damages,SDs)和亚表面损伤(subsurface damages,SSDs)㊂其中,SDs包括划痕㊁凸起㊁凹坑等,可通过光学显微镜直接观测;而SSDs主要分布于表面以下,无法通过光学显微镜直接观测㊂目前已发现的4H-SiC晶圆的SSDs包括:亚表面微裂纹㊁位错聚集㊁非晶相和残余应力等[4]㊂SDs/SSDs会在后续外延过程中作为缺陷的形核中心,严重影响外延层质量,进而影响4H-SiC基器件的性能与可靠性[5]㊂因此,准确识别SDs/SSDs,并阐明4H-SiC晶圆加工过程中SDs/SSDs的产生与去除机制,对于高质量4H-SiC晶圆的加工及应用至关重要㊂本文针对4H-SiC晶圆加工过程中产生的SDs/SSDs的形貌和来源进行分析,论述了在晶圆加工各个环节产生的SDs/SSDs的形成和去除机理,随后介绍了SSDs对后续外延和晶体生长的影响;最后简要介绍了SDs/SSDs的去除方法,比较去除效果,分析了其技术优势和发展瓶颈,并对其发展趋势进行展望㊂1㊀4H-SiC加工过程中的SDs/SSDs4H-SiC晶圆的主要加工流程分为切片㊁减薄㊁研磨㊁抛光和清洗㊂除了晶体本身的质量问题(如碳包裹㊁多型体㊁微管㊁位错等缺陷)[6],对衬底外延和后续器件制造影响最大的缺陷就是SDs/SSDs㊂由于二者均源于晶圆加工环节,因此明确SDs/SSDs的产生和去除机制,优化晶圆加工工艺,对严格控制4H-SiC晶圆的SDs/SSDs,并提升后续4H-SiC单晶生长或同质外延的质量具有重要意义㊂在4H-SiC的切片等加工工艺中,材料主要通过脆性断裂模式去除,这不可避免地会在表面下方引入微裂纹[7],造成材料的SDs和SSDs㊂亚表面的微裂纹不仅降低4H-SiC晶片的机械强度,还影响后续工艺和生产成本,是评价晶圆加工质量的一个重要指标㊂如图1(a)所示,切片工艺是影响切片过程中微裂纹损伤层厚度的关键因素㊂在后续减薄㊁研磨和抛光的加工过程中,损伤层的厚度逐渐减小,并在抛光后得到有效去除,获得全局平坦化的近无损4H-SiC晶圆㊂纳米压痕试验结果表明,4H-SiC在机械应力下产生的损伤层在宏观上呈现 Y 字形的裂纹,包括中位裂纹和侧位裂纹(见图1(b))[8]㊂其中,中位裂纹发生于磨料加载过程,随着磨料压入深度的增加,中位裂纹从变形区底端开始萌生,并向下扩展;当卸载时,中位裂纹逐渐闭合,侧位裂纹从变形区的底端开始萌生并向两侧和表面扩展,当侧位裂纹扩展到表面,形成表面破碎[2]㊂图1㊀4H-SiC衬底晶圆加工过程中SDs/SSDs的厚度变化(a)及裂纹产生的模型示意图(b)[8] Fig.1㊀Evolution of SDs/SSDs and change of the thickness(a),and diagram showing the generation mechanism ofcracks(b)in a4H-SiC substrate wafer[8]1.1㊀切片过程引入的损伤层作为4H-SiC晶圆加工过程的第一道工序,切片工艺质量决定了后续减薄㊁研磨㊁抛光的加工水平㊂切片㊀第11期李国峰等:碳化硅晶圆的表面/亚表面损伤研究进展1909㊀是影响晶圆损伤层厚度和面型参数的关键工艺㊂面型参数包括总厚度偏差(total thickness variation,TTV)㊁局域厚度变化(local thickness variation,LTV)㊁弯曲度(BOW)和翘曲度(WARP)㊂切片极易在4H-SiC晶片表面和亚表面产生大量裂纹和微裂纹,增加晶片的破片率和制造成本,因此控制晶片表层裂纹损伤对降低4H-SiC晶圆成本㊁推动4H-SiC基器件的发展具有重要意义㊂4H-SiC晶圆的切片方法有金刚线锯切片㊁游离砂浆线锯切片㊁激光切割和电火花切片等㊂其中,金刚线锯切片和游离砂浆线锯切片是目前4H-SiC晶圆加工最常用的切片方法,其原理是依靠金刚线或金属线带动砂浆使磨粒到达加工区域,并对磨粒施加压力,在磨料与晶锭表面接触瞬间,磨粒尖端会因冲击形成局域的微破碎,进而形成裂纹和材料脱落,以达到切片的目的[9]㊂该切割现象在单颗粒的游离砂浆线锯切实验中得到验证,但是划痕表面的材料剥落会使划痕的宽度超过磨料的直径[10],这与材料的去除方式有关㊂在晶圆加工过程中,材料的去除方式可分为脆性去除和延性去除[11]㊂由于4H-SiC具有高硬度㊁高脆性的特点,刀具刻划4H-SiC表面产生划痕的过程分为塑性阶段㊁塑脆性共存阶段和完全脆性阶段3个阶段,可以用摩擦力信号来表征[12]㊂图2所示为4H-SiC单晶的动载荷划痕实验,在塑性阶段主要以延性去除为主,摩擦力曲线光滑,划痕也以平滑凹槽为主;在塑脆性共存阶段,材料的去除既有延性去除又有脆性去除,划痕中显露出鱼鳞状凹坑;而在完全脆性阶段,脆性去除占主导,材料表面鱼鳞状凹坑进一步恶化并伴有裂纹萌生[13]㊂研究者们期望4H-SiC的材料去除机制更多表现为延性去除,以尽可能减小加工损伤和材料的损耗㊂然而,过分追求延性去除将会导致极低的材料去除率㊂因此,在脆性去除和延性去除两者间寻求一个平衡点是4H-SiC衬底加工的一个关键点㊂图2㊀4H-SiC晶圆动载荷划痕实验中划痕的摩擦力信号与载荷变化的关系(a)及划痕形貌变化图(b)[13] Fig.2㊀The dependence of the frictional force on the position(a),and the change of the scratch shape(b)during the dynamicload scratch experiment of a4H-SiC wafer[13]在4H-SiC线锯切片过程中,材料的脆性去除占据主导,导致4H-SiC在材料破碎去除的同时,产生大量的裂纹等损伤㊂随着钢线(或金刚线)深入材料内部,磨削力有所降低,4H-SiC材料的脆性去除进一步加剧㊂表1列出了金刚线锯切片和游离砂浆线锯切片两种切片方法的主要切削方式及其在4H-SiC中产生的损伤层的缺陷类型㊂在游离砂浆线锯切片时,4H-SiC亚表面会出现弥散的三角形损伤区,并带有半环束和堆垛层错;而金刚线锯切片会在4H-SiC晶片表面引入损伤区㊁半环束位错和堆积层错[14]㊂虽然由切片产生的SDs/SSDs是整个4H-SiC衬底加工中最严重的损伤,但通过优化切片工艺参数可以明显改善损伤层的厚度㊂如图3所示,通过优化线锯切工艺可显著控制4H-SiC的SDs/SSDs的厚度,其中减小晶体进给速度㊁增大线速度均有利于减小SDs/SSDs的厚度[15]㊂1910㊀综合评述人工晶体学报㊀㊀㊀㊀㊀㊀第52卷表1㊀不同切片方法对4H-SiC加工造成的损伤[14]Table1㊀Damages caused by different sawing technologies of4H-SiC wafers[14]切片方法切削方式主要缺陷金刚线锯固定磨料平移损伤层半环束位错(U型30ʎ倾斜和V型)堆垛层错游离砂浆线锯游离磨料旋转三角形损伤区半环束位错(不倾斜U型)堆垛层错图3㊀金刚线锯切片4H-SiC晶圆过程中进给速度(a)和线速度(b)对微裂纹损伤的厚度影响[15] Fig.3㊀Effect of feed rate(a)and wire speed(b)on the thickness of microcrack damages during the diamond wiresawing of4H-SiC wafers[15]1.2㊀磨削过程引入的损伤层磨削的目的是去除4H-SiC切片过程引入的SDs/SSDs,同时降低晶圆的TTV㊁LTV和表面粗糙度[16]㊂由于4H-SiC的高硬度特性,磨削过程中必须使用高硬度的磨料(如金刚石[17])㊂磨削工艺一般包括减薄和研磨,分别对应于以固结磨料(砂轮)和游离磨料(研磨液)体系的磨削机制㊂固结磨料磨削具有材料去除速率高的优点,但是,砂轮磨削后,晶圆表面粗糙度较高,且SDs/SSDs层的厚度较大㊂为解决砂轮磨削后表面质量差的问题,学者们采用辅助增效[18],选用更合适的磨料比例和固结方式[19]等方法改善磨削4H-SiC晶片时的表面质量㊂研磨分粗磨和精磨,粗磨使用粒径较大的磨粒和铜盘,精磨使用粒径较小的磨料和锡盘[20]㊂虽然使用金刚石研磨液可以保证较好的晶体表面质量,但研磨效率低,研磨时间较长㊂4H-SiC磨削过程中SDs/SSDs主要包括凹坑㊁划痕㊁侧位裂纹和中位裂纹[21]等㊂在磨削过程中,与磨料接触的4H-SiC表面的晶相会向非晶结构转变[22],由于磨粒挤压在工件材料上,原有的晶格受到破坏,非晶相形成,在外力作用下,材料表面出现很多微断裂,进而实现材料去除[23-24]㊂非晶结构更容易被去除,这是因为此结构可以通过产生更小的法向应力和非晶态相变以及更薄的塑性变形诱导SiC软化并产生SSDs㊂这一发现与后续的单晶4H-SiC进行单颗粒磨削的模拟实验结果类似,即塑性变形初期的SSDs由非晶化和位错引发产生㊂随着磨削过程的进行,形成了滑移带,塑性变形后期滑移带的延伸是裂纹萌生的原因[25]㊂此外,分子动力学研究表明,非晶化是导致SDs产生的主要原因,而位错滑移则造成了SSDs的出现[26]㊂另一方面,当磨削过程中温度升高时,非晶层的润滑作用和表面的再结晶过程可以有效抑制高切削温度下的SSDs[27]㊂因此,通过工艺调试,探索总结出合适的磨削参数,确保较小的非晶层和高效的磨削效率是很有必要的㊂如图4所示,使用砂轮磨削4H-SiC晶圆时,单位切削进给深度的实际材料去除量和SSDs层的厚度不随磨削速度的增加而单调变化㊂其中存在材料去除量最大㊁SSDs层的厚度最小的最佳磨削速度㊂损伤层的厚度随磨削速度的增加而增大[28],这是因为在一定的磨削范围内,材料的去除主要以延性磨削为主,在晶圆表面,靠近晶圆中心位置磨削更加均匀,从而产生更高的表面质量[29];而当单位去除量超过一定范围,脆性去除模式会渐渐显露,这时横向裂纹开始萌生[21,30]㊂以此为基础,可以通过提高磨削速度和减小切削深度以提高材料的应变速率,从而以增强材料的动态脆性的方式降低SDs/SSDs[31]㊂除了磨削时的进给速率㊁砂轮转速等因素外,磨料的尺寸也是影响SSDs的关键因素之一㊂在砂轮磨削过程中,表面粗糙度和亚表面裂纹㊀第11期李国峰等:碳化硅晶圆的表面/亚表面损伤研究进展1911㊀深度随磨料颗粒粒径的减小而减小[32]㊂从砂轮磨削的单颗粒实验模拟中可以看到,裂纹从磨粒的前部和底部开始㊂随着磨粒不断向划痕方向移动,晶粒前部的裂纹通过研磨作用被去除,但晶粒下方的裂纹不能被去除,形成SDs /SSDs [33]㊂将微裂纹刻蚀暴露并与磨削参数对比发现,后者的变化趋势对微裂纹的影响和对表面粗糙度的影响是一致的㊂磨料的平均尺寸和磨削力对SSDs 和表面粗糙度的危害甚至大于砂轮速度和磨削的进给深度;而微裂纹的角度和密度几乎不受磨削参数的影响[34]㊂砂轮磨削工艺属于二体磨损加工㊂具体而言,磨削过程中固结在砂轮上的磨粒随着砂轮规则地往复运图4㊀砂轮磨削4H-SiC 过程中,切削速度对切削深度和SSDs 层的厚度的影响[28]Fig.4㊀Effect of cutting speed on the cutting depth and SSDs layer thickness during grinding of 4H-SiC [28]动,进而通过特定的轨迹摩擦晶圆表面,最终实现材料的去除㊂而使用研磨液的游离磨料研磨属于三体磨损加工,材料的去除伴随着磨料的随机滚动㊁挤压和刮擦三种状态㊂与二体磨损加工不同的是,三体磨损下磨料尺寸的不均匀可能会影响晶圆的表面加工质量[35]㊂在使用游离磨料研磨液研磨过程中,SDs /SSDs 层的厚度与磨粒的粒度㊁研磨盘的硬度成正比,而与研磨浆料的浓度成反比,并且与研磨压力和速度无关㊂同时,磨料尺寸对SDs /SSDs 层的厚度的影响比研磨盘硬度的影响更显著,而研磨浆料浓度的影响最小[36]㊂因此,相较于砂轮磨削,游离磨粒研磨的损伤更依赖于磨料尺寸㊂如图5所示,游离磨料加工后,晶圆的层错密度降低,且晶相显现非晶㊂同时,加工表面出现明显的晶格畸变现象,这是延性去除发挥优势的结果[37]㊂图5㊀砂轮磨削(a)~(c)和游离磨料研磨(d)~(f)4H-SiC 的Si 面的横截面TEM 照片[37]Fig.5㊀Cross-sectional TEM images of the Si surface of 4H-SiC by grinding (a)~(c)and lapping (d)~(f)[37]经砂轮磨削加工后,晶圆表面会产生螺旋式花纹状的表面划痕,而使用游离磨料研磨后,晶圆的表面划痕则是无序的㊂这种无序的表面划痕是由研磨液中磨料尺寸的不均匀性导致[38]㊂由于4H-SiC 材料具有各1912㊀综合评述人工晶体学报㊀㊀㊀㊀㊀㊀第52卷向异性,C面的硬度大于Si面,在C面的脆性去除更明显㊂正是由于C面硬脆性较大,C面材料更容易产生微裂纹使材料剥落,因而C面的材料去除速率高于Si面[20],研磨后C面形成的SSDs的厚度大于Si面[35]㊂1.3㊀抛光过程引入的损伤层抛光工艺旨在进一步提高晶片的表面质量,改善表面粗糙度及平整度,使其表面质量特征参数符合后序加工中的精度要求㊂适合4H-SiC单晶片的精密抛光加工方法主要有机械抛光[39]㊁离子束抛光[40]㊁等离子体辅助抛光[41]和化学机械抛光(chemical mechanical polishing,CMP)[42]等㊂机械抛光以机械研磨为主,采用更小粒径的硬磨料对晶片表面进行延性去除,以去除研磨过程的残留应力层和机械损伤层,提高表面平面度及表面质量㊂离子束抛光技术是一种通过离子源发射离子束轰击光学零件表面产生物理溅射效应去除面形误差的新型抛光技术,近年来已逐渐应用于大口径光学元件的加工[43]㊂而CMP是目前实现4H-SiC晶片全局平坦化最有效的方法㊂4H-SiC衬底晶圆的CMP主要是在以氧化铝(Al2O3)㊁二氧化硅(SiO2)和二氧化铈(CeO2)等磨料,和以高锰酸钾(KMnO4)㊁双氧水(H2O2)等氧化剂共同组成的抛光液中,伴随氧化反应和机械去除同步进行,实现材料的去除和表面修整[44]㊂在CMP过程中,抛光浆料中的氧化剂首先氧化4H-SiC,在材料表面形成Si-C-O的过渡氧化态㊂氧化物的硬度低于4H-SiC,这确保了氧化物可以通过低硬度磨料的机械作用被去除,基于氧化和机械去除的循环实现了4H-SiC晶圆的CMP[45]㊂一般来说,CMP工艺可以在不造成SSDs的情况下加工全局平坦化的4H-SiC 衬底晶圆,且CMP处理后的SiC晶圆表面可以出现原子级台阶结构[46]㊂然而在实际生产加工中,由于操作不当或抛光耗材不合格等问题,经CMP后依旧发现衬底有局部损伤㊂在此条件下,重复CMP步骤时,可以看出残留划痕的位置发生了变化,这表明CMP本身是可能会产生细微划痕的[47]㊂CMP处理后残留的损伤有以下两种产生机制:1)在CMP之前引入的损伤,在CMP期间持续存在;2)在CMP期间引入的损伤[48]㊂在原子力显微镜(AFM)下,这些表面可以是无特征的或显示一些极小的抛光损伤㊂然而,在外延生长之前或期间经过高温热加工后,可以显示出密集的划痕和缺陷网络,该网络对应于机械磨损过程中冲击到4H-SiC 表面的SSDs或位错网络[49]㊂这些损伤有的来自于前道工序残留CMP没有完全去除的,而有的损伤则是由于CMP进行过程中,环境中的颗粒物等意外掉落于晶圆表面并参与抛光过程引起的划伤㊂因为这些纳米级划痕并不是均匀地引入到晶圆表面,而是非常局部地存在[42,50]㊂这些掉落物可能是大颗粒的二氧化硅,也有可能是4H-SiC晶圆的纳米级或亚微米级切屑㊂为了更好地解释CMP工序中意外引入损伤的产生机制,对比损伤形貌和在不同条件下获得的4H-SiC晶圆的位错结构,可以发现晶圆上的局部损伤是由CMP过程中施加的高局部应力造成的[51]㊂Tsukimoto等[52]通过高角度分辨电子背散射衍射(HR-EBSD)技术测量了4H-SiC晶片磨削损伤层的弹性应变分布来验证以上猜想㊂如图6所示,在晶圆加工位置的下方由于非常大的塑性应变会产生缺陷区域,通过研磨相互作用与相关的塑性变形和断裂不均匀地引入了晶格缺陷㊂基于这一机理,可以解释为在整个4H-SiC衬底的加工环节中,晶圆表面被施加高局部作用力而发生弹塑性变形是SSDs产生的最根本原因㊂图6㊀4H-SiC晶圆损伤层的高分辨TEM照片,显示微裂纹沿箭头所示路径从表面上的一点(X)向晶圆内部点(Y)扩展[52] Fig.6㊀The high-resolution TEM image of the damage layer showing the microcrack propagating from a point(X)on thesurface to an internal point(Y)along the path indicated by the arrow[52]㊀第11期李国峰等:碳化硅晶圆的表面/亚表面损伤研究进展1913㊀2㊀SDs /SSDs 的形貌和表征2.1㊀SDs /SSDs 形貌从线切到磨削㊁抛光,材料的SSDs 层的厚度会严重影响加工效率和下一步工序的移除量㊂因此,要想实现材料的高效低损伤加工,延长材料的使用寿命,降低后续工序的移除量,对材料的SSDs 层的厚度进行检测分析和预测十分必要[53]㊂如图7所示,SSDs 在晶圆表面仅呈现为划痕,但其纵向裂纹深度㊁具体结构等需要借助特殊手段来观测㊂脆性材料晶圆的SSDs 检测方法可分为有损检测和无损检测两类㊂其中,有损检测包括截面显微法[54]㊁角度抛光法[55]㊁化学刻蚀法[56]等㊂然而,它们在检测上都有一些瑕疵:前两者虽然可以直观看到SSDs 的形貌,但样本制作流程过于繁琐;化学刻蚀法操作方便,但刻蚀深度无法精准控制㊂无损检测方法包括声学显微镜[57]㊁拉曼光谱分析[55]㊁X 射线衍射[58]㊁共聚焦激光扫描法[59]㊁光致发光(PL)[60]等㊂这些方法同样适用于4H-SiC 晶圆的SSDs 的检测㊂图7㊀4H-SiC 晶圆在CMP 后残留划痕的光学显微镜(a)和SEM(b)照片[50]Fig.7㊀Optical microscopy (a)and SEM (b)images of the residual scratch of a 4H-SiC wafer after CMP [50]如图8所示,4H-SiC 的SDs /SSDs 主要成分是在切片㊁磨削和抛光过程中产生的断裂和划痕,而这些断裂和划痕会被抛光再沉积层部分或全部隐藏起来[61]㊂参考Si 的SSDs 模型可以发现,SSDs 主要可分为严重损伤部分和高应力弹性变形部分,其中严重损伤部分由微裂纹㊁非晶层㊁多晶层㊁位错等组成㊂而这两部分的比例由加工的参数和磨料的性质决定,且这两部分没有确切的边界,如图9所示[62]㊂随着加工的深入和磨料的尺寸降低,损伤逐渐降低至外延可接受范围,获得近无损的晶圆表面㊂图8㊀4H-SiC 晶圆抛光后的SSDs 分布的示意图[61]Fig.8㊀Schematic of SSDs after the polishing of 4H-SiC wafers [61]图9㊀Si 研磨后SSDs 的形貌和成分示意图[62]Fig.9㊀Schematic diagram of the morphology and composition of SSDs after the grinding of Si [62]图10所示为TEM 观察到的4H-SiC 衬底晶圆的SDs /SSDs 中位错层的微观形貌㊂可以看到局部损伤在垂直方向表现为划痕,两侧伴随有环形位错㊂经过衍射矢量和伯格斯矢量对比,确定该位错环为基平面位错(BPD)[50,63]㊂从这些位错环的形状推断,这些位错环主要是硅核心不全位错的滑移造成的[51,64]㊂同时,1914㊀综合评述人工晶体学报㊀㊀㊀㊀㊀㊀第52卷BPD位错环的方向和局部损伤方向有关㊂4H-SiC衬底中的局部损伤会直接在外延层中反映出来,因此可以通过直接使用紫外灯照射外延晶圆使4H-SiC衬底中残留的BPD位错环在衬底中继承,并演化和延伸成肖克利型层错(Shockley-type stacking faults,SSF),如图11所示,外延层经UV处理后在PL中检测出半菱形结构[65]㊂对比发现,SSF的形貌又恰好可以和衬底中的BPD位错环对应㊂通过对半菱形SSF的方向统计后发现,虽然菱形大致分布于损伤的两侧,但不同晶向的损伤会使菱形的尖角方向分布出现偏差,这也可以说明衬底中不同晶向上的损伤,其BPD位错环的伯格斯矢量方向会有差异㊂图10㊀4H-SiC衬底中SSDs的表面TEM照片[50]Fig.10㊀Plane-view TEM image of SSDs of a4H-SiC substrate[50]图11㊀紫外光照射下4H-SiC外延薄膜中的Shockley型堆垛层错[65]Fig.11㊀Shockley-type stacking faults in4H-SiC epitaxial layer under UV irradiation[65]要观察SSDs的完整形貌,截面显微法是最直观的方法[66]㊂对4H-SiC损伤部分切片制样,在TEM中可看到损伤的完整纵向形貌,如图12所示[14]㊂损伤部分从上到下可分为覆盖层㊁亮层(损伤层)㊁半环形BPD 位错并伴随有SF㊂损伤层的形貌随划痕的晶向略有差异,但大致呈Y型,底部连接有层错,半环束从亮层向内扩散,形状为U型[61]㊂而在位错下方还有一层由于弹塑性变形而未被完全释放的应力层[62]㊂图12㊀4H-SiC衬底中的SSDs沿划痕方向(a)和垂直划痕方向(b)的缺陷分布示意图[14] Fig.12㊀Distribution diagram of SSDs parallel(a)and perpendicular(b)to the scratch of4H-SiC substrates[14]。
- 1、下载文档前请自行甄别文档内容的完整性,平台不提供额外的编辑、内容补充、找答案等附加服务。
- 2、"仅部分预览"的文档,不可在线预览部分如存在完整性等问题,可反馈申请退款(可完整预览的文档不适用该条件!)。
- 3、如文档侵犯您的权益,请联系客服反馈,我们会尽快为您处理(人工客服工作时间:9:00-18:30)。
2008年 3月郑州大学学报(工学版)Mar 1 2008第29卷 第1期Journal of Zhengzhou University (Engineering Science )Vol 129 No 11 收稿日期:2007-09-31;修订日期:2007-12-24 基金项目:教育部新世纪人才计划项目;河南省杰出青年基金资助项目(512002200) 作者简介:范冰冰(1982-),女,河南淮阳人,郑州大学博士研究生,主要从事Si C /Cu 复合材料研究,E 2mail:bing 2bingfan@yahoo .cn;通讯作者:张 锐(1967-),男,郑州大学教授,博士. 文章编号:1671-6833(2008)01-0028-03SiC /Cu 复合材料磨损界面研究范冰冰,侯铁翠,刘瑞瑜,李 凯,吴曰送,张 锐(郑州大学材料科学与工程学院,河南郑州,450001)摘 要:采用非均相沉淀法制备了Si C /Cu 包裹复合粉体,热压烧结制备Si C /Cu 复合材料.以Si 3N 4球为摩擦副,在400℃条件下进行磨损实验.采用XRD 、SE M 分别对磨损前后材料的界面物相、磨损界面的形貌以及裂纹的扩展变化情况进行分析.结果表明:在该实验条件下,Si C /Cu 复合材料界面的物相随着磨损的进行发生变化,Cu 2O 含量大大增加,同时出现Cu O.随着循环荷载的增加,复合材料的内部产生了裂纹,裂纹的扩展是沿着Si C /Cu 界面进行;而Si C 颗粒的存在,使复合材料内部裂纹发生偏转,有利于提高材料的耐磨性.关键词:Si C /Cu;复合材料;磨损界面;裂纹扩展中图分类号:T B 333 文献标识码:A0 引言Si C /Cu 金属陶瓷复合材料作为理想的结构-功能一体化材料,具有良好耐磨和抗氧化等性能,在航空航天、电子和国防等领域具有十分广阔的应用前景,成为近年来材料科学领域的研究热点之一[1-2].Kennedy [3]等研究了Si C 颗粒增强Cu 金属陶瓷复合材料的摩擦学性能及探索该材料在汽车刹车片的应用可能性,湛永钟[4]等人着重研究了Si C 颗粒含量对磨损性能的影响,然而对于Si C /Cu 陶瓷金属材料的磨损界面研究报道还较少,对磨损状态下Si C /Cu 复合材料的破坏行为没有统一的理论.笔者通过对Si C /Cu 复合材料磨损界面的分析,研究了复合材料的裂纹扩展情况,为设计高可靠性的金属基复合材料提供依据.1 实验部分采用非均相沉淀法将纳米Cu 包裹到Si C 颗粒(β2Si C 粉体,平均粒径:100n m )上,制备出25Si C /75Cu (体积百分数)包裹复合粉体[5],从而实现了两相之间的均匀分散.经包裹工艺处理获得的Si C /Cu 复合粉体经过筛分(75μm ),采用热压烧结,压力为36MPa,烧成温度分别为600℃、650℃、700℃、750℃,保温时间为10m in .制备得到的Si C /Cu 复合材料表面经过磨平、抛光加工,表面粗糙度小于100nm;将处理过的样品置于高温摩擦磨损试验机(THT07-135,CSE M I n 2strument L td .,S wiss )旋转样品台上固定.磨损方式为干法“点-面”磨损.样品在空气中被加热至400℃,恒温后进行加压磨损试验.选用的摩擦副为Si 3N 4球,直径为3mm ,表面粗糙度小于100nm ,安装在位置固定的上压头上,并与Si C /Cu 样品表面接触,点接触位置距离旋转轴心为4mm.通过Si 3N 4球施加在样品表面的试验载荷为10N.样品的旋转速度为43±2c m /s,磨损时间为20m in .采用XRD (D /MAX -2250V,R igaku T okyo,Japan )对磨损界面物相进行分析,SE M (JS M -6700F,JE OL T okyo,Japan )观察磨损界面的形貌以及裂纹的扩展情况.2 结果与讨论图1是25Si C /75Cu (体积百分数)样品在磨损前后的XRD 图谱,可以看出复合材料界面物质相在磨损前后发生了变化.磨损前(图1(a ))复合粉体由Cu 、Si C 和极少量的Cu 2O 组成,其中Cu 的峰强很高,而且Si C 相的峰强相对较弱;而磨损后(图1(b )),样品表面Cu 2O 峰值大大升高,甚至超过Cu 峰值,并出现CuO 相,这是由于在摩擦过程中,样品的表面发生氧化所造成的,其氧化方 第1期范冰冰等 Si C/Cu 复合材料磨损界面研究29 程式如下:4Cu +O 2→2Cu 2O (1)2Cu 2O +O 2→4Cu O(2)图中箭头所指的衍射峰是Si C (111)与Cu O 的重叠峰.图1 25S i C /75Cu(vol%)样品磨损前后XRD 谱线F i g .1 XRD pa ttern s of 25S i C /75Cu(vol%)co m posites after wear tests and before wear tests图2是Si C /Cu 复合材料的磨损表面SE M 照片.磨损表面除了犁沟状的磨痕外,还有大量的磨屑和块状黏着磨损痕迹.这是由于在磨损过程中产生的高温,使不断裸露的新鲜金属表面很快被氧化形成Cu O 和Cu 2O (图1(b )),氧化物从基体表面剥落形成磨屑,磨屑对磨损面的划伤,形成划痕.在磨损过程中,由于局部出现瞬间的高温,导致Si C /Cu 界面处形成Cu -Cu 2O 、Cu 2O -Si O 2低共熔相[5].同时,由于这些氧化物低共熔相的存在,在复合材料表面出现釉质层[6],形成以Cu 为基体,氧化物颗粒弥散分布的结构,该结构具有良好的润滑性能,有利于降低材料的摩擦系数,提高耐磨性.图3是裂纹通过Si C /Cu 界面时的SE M 照片.从图中可以看出,裂纹的扩展沿着Si C /Cu 界面进行,在遇到大颗粒Si C 时,裂纹发生偏转.磨损过程中,在法向载荷(法向力)和滑动摩擦力(剪切力)作用下,由于Si C 颗粒与周围Cu 颗粒硬度上相差悬殊,两相之间承受载荷的剪切作用力不同,由于Cu 颗粒自身的延展性和塑性变形而承受较小的作用力.作用力尤其是剪切力主要集中于Si C 颗粒,循环载荷通过Si C 颗粒的瞬间在Si C /Cu 界面产生应力集中,使Si C /Cu 界面处的晶界玻璃相区域疲劳,加上高温环境及摩擦过程中产生的热量使晶界相软化,强度降低,产生微裂纹.随着磨损时间的增加,微裂纹超过临界尺寸以后,开始向周围的Cu 基体扩展,形成大的裂纹,导致样品的韧性破坏[7].而当裂纹尖端遇到另一个大的Si C (Cu )晶粒时而停止扩展,如图4(a )所示.这表明,Si C 颗粒或者较大的Cu 晶粒能够通过引起裂纹偏转,较大的Si C 颗粒在复合材料中起到“钉扎”的作用,从而阻止裂纹的进一步扩展,即成为裂纹的终止点,因此提高了Si C /Cu 复合材料的机械性能.图4(b )所示,E DS 能谱分析发现同样有氧元素的存在,表明在磨损过程中30 郑州大学学报(工学版)2008年出现了氧化现象,这与XRD 检测结果一致.图4 25S i C /75Cu(vol%)样品内部裂纹尖端SE M 照片及E D S 谱F i g .4 SE M i m age and spectru m of crack ti ps i n the 25S i C /75Cu(vol%)co m posite 图5中为破坏磨损界面的SE M 照片,如图所示,样品的磨损过程中没有Si C 颗粒的拔出现象,相反Si C 颗粒以及Cu 颗粒不断被磨平.这由于Si C /Cu 界面结合具有一定强度[8].当外加载荷小于Si C /Cu 界面结合强度时,Si C 颗粒被不断地磨平;当外加载荷超过临界载荷时,颗粒拔出,形成粗糙表面.大颗粒Si C 存在时,容易产生磨平磨损,从而起到增强耐磨作用.图5 S i C 2Cu 界面的破坏后的SE M 照片F i g .5 SE M i m age of the damaged S i C 2Cu i n terface3 结论(1)在磨损过程中,Si C /Cu 复合材料的磨损表面,由于Cu 的氧化而出现Cu 2O 与Cu O,并且Cu 2O 含量随磨损的进行大大升高.(2)在法向载荷作用下,裂纹的扩展主要是沿着Si C /Cu 的结合界面处进行,材料破坏主要发生在Cu 晶粒内部.当裂纹到达Si C 颗粒时,沿Si C /Cu 界面向Cu 晶粒内部偏转,使Cu 晶粒穿晶断裂,由于Si C 颗粒的“钉扎”作用,裂纹在扩展方向上不断偏转.因此,Si C 颗粒的存在,可以阻止裂纹的进一步扩展,有利于提高复合材料的耐磨性,提高材料使用的可靠性.参考文献:[1] K OCK T,BRE NDE L A,BOLT H.I nterface reacti onsbet w een silicon carbide and interlayers in silicon car 2bide 2copper metal 2matrix composites [J ].Journal of NuclearMaterials,2007,362(2-3):197-201.[2] ZHU J H,L I U L,SHE N B.Mechanical p r operties ofCu /Si Cp composites fabricated by composite electr ofor 2m ing [J ].Materials Letters,2007,61(13):2804-2809.[3] KE NNE D Y F E,BALBAHADUR A C,LASH MORED S .The fricti on and wear of Cu -based silicon car 2bide particulate metal matrix composites f or brake ap 2p licati ons[J ].W ear,1997,203-204:715-721.[4] 湛永钟,张国定.Si Cp /Cu 复合材料摩擦磨损行为研究[J ].摩擦学学报,2003,23(6):495-499.[5] 张 锐,王海龙,付元中,等.Si C /Cu 纳米包裹粉体及其复合材料的制备[J ].郑州大学学报:工学版,2004,25(3):74-76.[6] 湛永钟,张国定.Si Cp /Cu 复合材料的高温磨损行为[J ].兵器材料科学与工程,2005,29(6):22-25.[7] PERSS ON B N J,ALBOHR O,MANCOS U F .On thenature of the static fricti on,kinetic fricti on and creep [J ].W ear,2003,254(9):835-851.[8] KI O URTSI D I S G E,SK OL I A NOS S M.W ear behav 2i our of artificially aged AA2024/40μm Si Cp co mposites in co mparis on with conventi onally wear resistant ferr ous materials[J ].W ear,2002,253(9-10):946-956.(下转第55页) 第1期敖天勇等 新型迈克尔逊干涉仪条纹计数器的设计55表1 实验数据Tab.1 Exper i m en t a l da t aD1/c m D2/c m△d/mm条纹数N/个λ实验值/n mλ理论值/n m相对误差/‰35.5242535.555930.0316*******.6632.81.3034.4774034.540720.06332200633.2632.80.6036.6849536.590010.09494300632.9632.80.16参考文献:[1] 刘芳元.关于迈克尔逊干涉条纹的理论分析[J].中南工学院科技通讯,1995,11(1):33-35.[2] 王守权,张绍良,张 薇.干涉条纹计数器的研制[J].长春邮电学院学报,2000,18(2):55-58. [3] 谢自美.电子线路设计・实验・测试[M].武汉:华中科技大学出版社,2006:32-33.[4] 陈本永,吴晓维,李达成.一种新型的干涉条纹软件计数方法及其实现研究[J].传感技术学报,2004,(9):371-374.[5] 陈光东.单片微型计算机原理及其C语言程序设计[M].武汉:华中科技大学出版社,2004:109-158.[6] BARONE F,C ALLON I E.Fringe-counting tech2nique used t o l ock a sus pended interfer ometer[J].App lied Op tics,1994,(3):1194-1197.[7] I ntersil Americas I nc.D igitally Contr olled Potenti ome2ter[E B/OL]/data/fn/fn8176.pdf,2005-03-15.The D esi gn of a Novel Fr i n ge Coun ter for M i chelson I n terferom eterAO Tian-yong,X I A NG B ing(School of Physics and Electr onics,Henan University,Kaifeng475001,China)Abstract:A counter for fringes of M ichels on interfer ometer is designed,which can adap t aut omatically t o different degress of illu m inati on intensity of backgr ound.A phot osensitive di ode transf or m s the changes of fringes int o electric signal.The signal and the out put of the digital potenti ometer are differential a mp lified by a differential a mp lifier.A Schm itt trigger transf or m s the out put of the a mp lifier int o pulseswhich are counted and shown by a single chi p m icr ocomputer.It has been p r oved that the counter can be used in circum stances of different illu m inati on intensity of backgr ound and la mp-house.The counter has many advantages,such as high accuracy,easy operati on and wide adap tability.Key words:interference fringe;counter;digital potenti ometer;single chi p m icr ocomputer(上接第30页)Research on the A ttr iti on I n terface of S i C/Cu Com positeF AN B ing-bing,HOU Tie-cui,L IU Rui-yu,L I Kai,WU Yue-s ong,ZHANG Rui(School of Material Science and Engineering,Zhengzhou University,Zhengzhou450001,China)Abstract:Nanoscale Si C/Cu composite particles were p repared with the heter ogeneous p reci p itati on method. Si C/Cu composite material was obtained by hot2p ressing.The wear experi m ent was carried out at400℃.XRD was used t o characterize the phase of hot2p ressed composite before and after the wear test.SE M techniques were used t o observe the mor phol ogy of the wear track and the p r opagati on of cracks in the wear traces.The results indicated that,under the experi m ental conditi on,the phase of fricti on interface changed.The content of Cu2O increased and Cu O appeared.W ith the circulati on l oad increase,the crack was observed,and it car2 ried on al ong the Si C/Cu interface.W hile the existence of Si C particles,which will p revent the crack expan2 si on,is advantage ous t o enhance the wear resistance of the co mpound material greatly.Key words:Si C/Cu;composite;attriti on interface;crack expansi on。