复合材料的界面问题研究
复合材料的界面特性与粘结机制研究
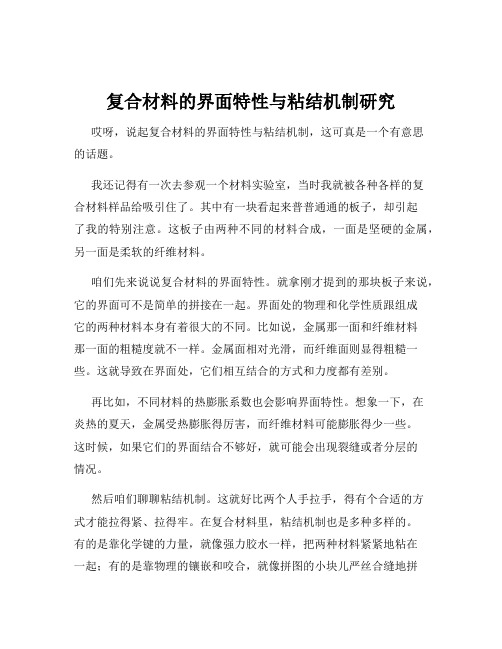
复合材料的界面特性与粘结机制研究哎呀,说起复合材料的界面特性与粘结机制,这可真是一个有意思的话题。
我还记得有一次去参观一个材料实验室,当时我就被各种各样的复合材料样品给吸引住了。
其中有一块看起来普普通通的板子,却引起了我的特别注意。
这板子由两种不同的材料合成,一面是坚硬的金属,另一面是柔软的纤维材料。
咱们先来说说复合材料的界面特性。
就拿刚才提到的那块板子来说,它的界面可不是简单的拼接在一起。
界面处的物理和化学性质跟组成它的两种材料本身有着很大的不同。
比如说,金属那一面和纤维材料那一面的粗糙度就不一样。
金属面相对光滑,而纤维面则显得粗糙一些。
这就导致在界面处,它们相互结合的方式和力度都有差别。
再比如,不同材料的热膨胀系数也会影响界面特性。
想象一下,在炎热的夏天,金属受热膨胀得厉害,而纤维材料可能膨胀得少一些。
这时候,如果它们的界面结合不够好,就可能会出现裂缝或者分层的情况。
然后咱们聊聊粘结机制。
这就好比两个人手拉手,得有个合适的方式才能拉得紧、拉得牢。
在复合材料里,粘结机制也是多种多样的。
有的是靠化学键的力量,就像强力胶水一样,把两种材料紧紧地粘在一起;有的是靠物理的镶嵌和咬合,就像拼图的小块儿严丝合缝地拼在一起;还有的是靠分子间的相互作用力,虽然这种力量相对较弱,但在一定条件下也能发挥不小的作用。
比如说,有一种复合材料是用树脂把玻璃纤维粘结起来的。
在这个过程中,树脂会渗透到玻璃纤维的缝隙里,然后经过固化,形成一个牢固的整体。
这里面树脂的选择就很关键,如果树脂的性能不好,或者在粘结过程中没有处理好温度、压力等条件,那粘结效果就会大打折扣。
还有一种情况,是在金属和陶瓷的复合材料中。
由于金属和陶瓷的性质差异很大,要实现良好的粘结就更不容易了。
这时候,往往需要对金属表面进行特殊处理,比如增加粗糙度,或者在表面镀上一层薄薄的过渡层,来提高粘结的效果。
在实际应用中,了解复合材料的界面特性和粘结机制那是太重要了。
先进复合材料的界面性能研究
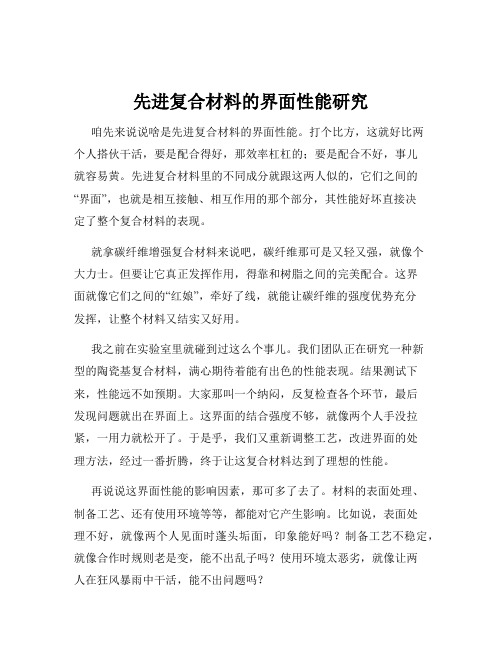
先进复合材料的界面性能研究咱先来说说啥是先进复合材料的界面性能。
打个比方,这就好比两个人搭伙干活,要是配合得好,那效率杠杠的;要是配合不好,事儿就容易黄。
先进复合材料里的不同成分就跟这两人似的,它们之间的“界面”,也就是相互接触、相互作用的那个部分,其性能好坏直接决定了整个复合材料的表现。
就拿碳纤维增强复合材料来说吧,碳纤维那可是又轻又强,就像个大力士。
但要让它真正发挥作用,得靠和树脂之间的完美配合。
这界面就像它们之间的“红娘”,牵好了线,就能让碳纤维的强度优势充分发挥,让整个材料又结实又好用。
我之前在实验室里就碰到过这么个事儿。
我们团队正在研究一种新型的陶瓷基复合材料,满心期待着能有出色的性能表现。
结果测试下来,性能远不如预期。
大家那叫一个纳闷,反复检查各个环节,最后发现问题就出在界面上。
这界面的结合强度不够,就像两个人手没拉紧,一用力就松开了。
于是乎,我们又重新调整工艺,改进界面的处理方法,经过一番折腾,终于让这复合材料达到了理想的性能。
再说说这界面性能的影响因素,那可多了去了。
材料的表面处理、制备工艺、还有使用环境等等,都能对它产生影响。
比如说,表面处理不好,就像两个人见面时蓬头垢面,印象能好吗?制备工艺不稳定,就像合作时规则老是变,能不出乱子吗?使用环境太恶劣,就像让两人在狂风暴雨中干活,能不出问题吗?研究这界面性能,可不是一件轻松的事儿。
得用上各种各样的先进技术和设备。
像扫描电子显微镜,能让我们看清界面的微观结构,就像拿着放大镜看细节;还有各种力学性能测试设备,能测出界面的强度和韧性,看看这“红娘”牵线到底牢不牢固。
而且,这研究可不光是在实验室里捣鼓,还得考虑实际应用。
比如说,在航空航天领域,对复合材料的性能要求那是极高的。
一点点界面性能的不足,都可能导致严重的后果。
所以,我们得不断地探索、创新,找到更好的方法来优化界面性能。
总之,先进复合材料的界面性能研究,就像是一场精细的“牵线搭桥”游戏。
复合材料的界面缺陷与性能分析

复合材料的界面缺陷与性能分析在现代材料科学领域,复合材料因其优异的性能而备受关注。
然而,复合材料的性能并非仅仅取决于其组成成分,界面特性在很大程度上也决定了其整体性能的优劣。
复合材料的界面就如同是连接各个部分的桥梁,一旦这座“桥梁”存在缺陷,就会对整个复合材料的性能产生显著的影响。
首先,我们需要明确什么是复合材料的界面。
简单来说,复合材料的界面是指两种或两种以上不同材料之间的过渡区域。
这个区域虽然很薄,但却具有独特的化学和物理性质。
在这个界面区域内,材料之间的相互作用、化学键合、物理结合等因素共同决定了界面的性能。
那么,复合材料的界面缺陷都有哪些类型呢?常见的界面缺陷包括界面脱粘、孔洞、裂纹、残余应力等。
界面脱粘是指两种材料在界面处失去了有效的结合,这就好像是原本紧紧相连的手松开了。
孔洞则是在界面处形成的空穴,它们会削弱材料的连续性和承载能力。
裂纹的出现往往是由于应力集中或者材料本身的缺陷导致的,一旦裂纹在界面处扩展,就会严重影响复合材料的强度和韧性。
残余应力则是在复合材料制备过程中产生的内应力,当这种应力超过一定限度时,也会导致界面的破坏。
这些界面缺陷是如何产生的呢?一方面,复合材料在制备过程中的工艺参数不当可能会导致界面缺陷。
例如,在复合材料的成型过程中,如果温度、压力、时间等参数控制不好,就可能会出现界面结合不良的情况。
另一方面,原材料的表面处理不当也会引发界面缺陷。
如果原材料表面存在杂质、油污或者氧化层等,就会影响界面的结合强度。
此外,复合材料在使用过程中受到外界环境的影响,如温度变化、湿度变化、化学腐蚀等,也可能会导致界面缺陷的产生和扩展。
界面缺陷对复合材料的性能有着多方面的影响。
从力学性能来看,界面缺陷会显著降低复合材料的强度、刚度和韧性。
例如,界面脱粘会导致载荷无法有效地从一种材料传递到另一种材料,从而使复合材料在承受外力时容易发生过早失效。
孔洞和裂纹的存在会成为应力集中的源头,加速材料的破坏。
新型复合材料的界面调控与性能研究

新型复合材料的界面调控与性能研究一、引言随着科学技术的不断发展,新材料的开发与应用逐渐成为人们关注的焦点。
而新型复合材料作为材料领域中的一大热点,在其制备和应用方面也得到了广泛的研究与应用。
其中,复合材料的界面调控与性能研究是构建优质复合材料的重要方面。
二、复合材料的界面调控1、界面调控的概念复合材料的性能不仅与单个组分的性能有关,同时也受到各组分间界面的影响。
界面调控是指通过改变各组分间的相互作用,调节其界面的结构和性能以优化复合材料性能的方法。
界面调控方法包括物理、化学和力学三种方式。
在实际应用中,制备过程和材料结构的控制是实现界面调控的关键。
2、常见的界面调控方法(1)表面修饰表面修饰是指在固体颗粒表面上引入一层同类型或不同类型的物质,形成新的界面结构。
通过表面修饰,可以提高复合材料的界面结合强度和界面层的生物相容性,从而提高复合材料的综合性能。
(2)界面结构设计界面结构设计是根据各组分在偏析和相互作用方面的情况,设计需要的界面结构。
通过对界面结构的设计,可以实现各组分之间的最佳结合,达到优化复合材料性能的目的。
(3)界面改性界面改性通常是指将改性剂引入到复合材料的界面层中,从而改变其化学性质。
以增强材料为例,通过界面改性可以提高其强度和硬度,并提高复合材料的抗拉、抗弯强度和疲劳性能。
(4)界面聚合界面聚合是在复合材料的界面上引入交联剂,或者通过化学反应使得各组分之间发生交联反应,从而改变复合材料的界面结构和性质。
界面聚合可以使得复合材料的界面层更加紧密,从而提高其强度和韧性。
三、复合材料性能研究1、复合材料的物理性能复合材料的物理性能包括密度、热膨胀系数、热导率、导热系数、电导率等。
在制备复合材料时,需要根据具体应用要求选择合适的填充材料和基体材料,以实现预期的物理性能。
2、复合材料的化学性能复合材料的化学性能主要表现在两个方面。
一是复合材料材料自身的耐腐蚀性能,二是复合材料在特定环境下的耐腐蚀性能。
复合材料的界面相互作用研究
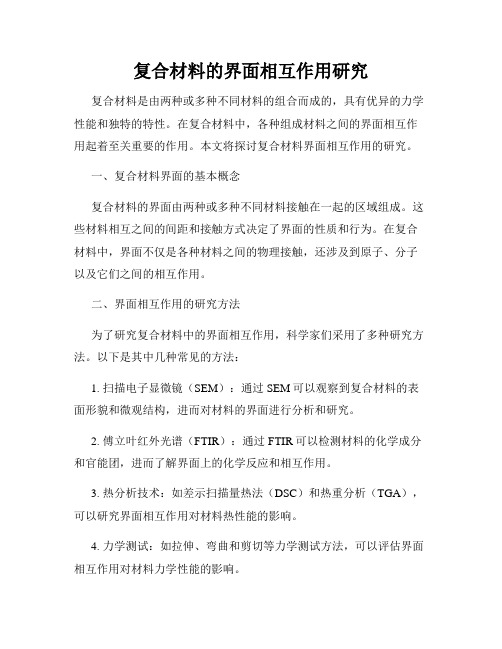
复合材料的界面相互作用研究复合材料是由两种或多种不同材料的组合而成的,具有优异的力学性能和独特的特性。
在复合材料中,各种组成材料之间的界面相互作用起着至关重要的作用。
本文将探讨复合材料界面相互作用的研究。
一、复合材料界面的基本概念复合材料的界面由两种或多种不同材料接触在一起的区域组成。
这些材料相互之间的间距和接触方式决定了界面的性质和行为。
在复合材料中,界面不仅是各种材料之间的物理接触,还涉及到原子、分子以及它们之间的相互作用。
二、界面相互作用的研究方法为了研究复合材料中的界面相互作用,科学家们采用了多种研究方法。
以下是其中几种常见的方法:1. 扫描电子显微镜(SEM):通过SEM可以观察到复合材料的表面形貌和微观结构,进而对材料的界面进行分析和研究。
2. 傅立叶红外光谱(FTIR):通过FTIR可以检测材料的化学成分和官能团,进而了解界面上的化学反应和相互作用。
3. 热分析技术:如差示扫描量热法(DSC)和热重分析(TGA),可以研究界面相互作用对材料热性能的影响。
4. 力学测试:如拉伸、弯曲和剪切等力学测试方法,可以评估界面相互作用对材料力学性能的影响。
三、界面相互作用的影响因素复合材料中界面相互作用的性质和行为受多种因素的影响。
以下是几个重要的影响因素:1. 材料选择:界面相互作用的性质受到组成材料的选择和特性的影响。
不同类型的材料在界面上的相互作用方式各不相同。
2. 温度和湿度:界面相互作用对温度和湿度的敏感性较强。
温湿度的变化会导致界面的物理和化学行为发生改变,进而影响材料的性能。
3. 表面处理:采用不同的表面处理方法可以改变界面的性质。
例如,化学处理、表面涂覆和增加粗糙度等方法可以改善界面的结合强度和相互作用性能。
四、界面相互作用的作用机制复合材料中的界面相互作用涉及到多种机制,其中最常见的包括物理吸附、化学键合和电荷转移等。
这些作用机制直接影响着界面的结构、力学性能和化学性质。
1. 物理吸附:界面上的物理吸附是材料间的非化学吸附,通过分子间的范德华力和静电作用产生。
复合材料的界面粘结性能研究
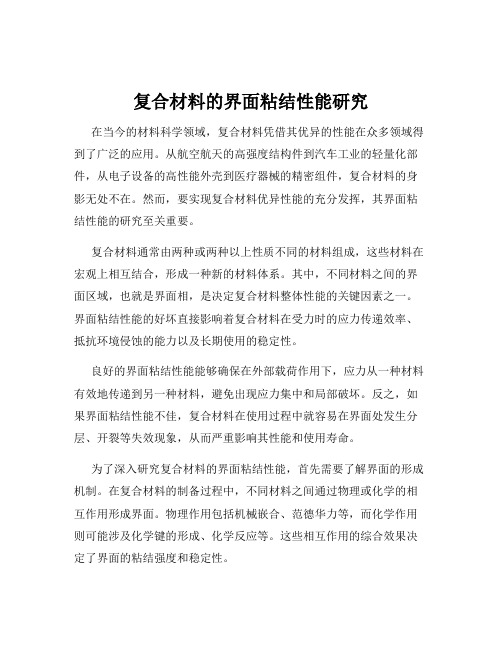
复合材料的界面粘结性能研究在当今的材料科学领域,复合材料凭借其优异的性能在众多领域得到了广泛的应用。
从航空航天的高强度结构件到汽车工业的轻量化部件,从电子设备的高性能外壳到医疗器械的精密组件,复合材料的身影无处不在。
然而,要实现复合材料优异性能的充分发挥,其界面粘结性能的研究至关重要。
复合材料通常由两种或两种以上性质不同的材料组成,这些材料在宏观上相互结合,形成一种新的材料体系。
其中,不同材料之间的界面区域,也就是界面相,是决定复合材料整体性能的关键因素之一。
界面粘结性能的好坏直接影响着复合材料在受力时的应力传递效率、抵抗环境侵蚀的能力以及长期使用的稳定性。
良好的界面粘结性能能够确保在外部载荷作用下,应力从一种材料有效地传递到另一种材料,避免出现应力集中和局部破坏。
反之,如果界面粘结性能不佳,复合材料在使用过程中就容易在界面处发生分层、开裂等失效现象,从而严重影响其性能和使用寿命。
为了深入研究复合材料的界面粘结性能,首先需要了解界面的形成机制。
在复合材料的制备过程中,不同材料之间通过物理或化学的相互作用形成界面。
物理作用包括机械嵌合、范德华力等,而化学作用则可能涉及化学键的形成、化学反应等。
这些相互作用的综合效果决定了界面的粘结强度和稳定性。
目前,研究复合材料界面粘结性能的方法多种多样。
其中,微观分析技术如扫描电子显微镜(SEM)、透射电子显微镜(TEM)等可以帮助我们直观地观察界面的微观结构,包括界面的形貌、粗糙度、相分布等。
通过这些观察,我们能够了解界面的物理结合情况,并推测其对粘结性能的影响。
此外,力学性能测试也是评估界面粘结性能的重要手段。
常见的测试方法有拉伸试验、剪切试验、弯曲试验等。
通过这些试验,可以获得复合材料的强度、模量、断裂伸长率等力学性能参数,从而间接反映界面的粘结强度。
同时,化学分析方法如 X 射线光电子能谱(XPS)、傅里叶变换红外光谱(FTIR)等可以用于检测界面处的化学组成和化学键的变化,进而揭示界面的化学结合机制。
1.11复合材料界面的研究方法
通过红外光谱分析来研究表面和界面的方法。可以了解物质在增强材料 表面是发生了物理吸附还是化学吸附。
拉曼光谱法是利用氩激光激发的拉曼光谱来研究表面和界面,它可用于 研究偶联剂与玻璃纤维间的粘接。
• 4.能谱仪法 用于纤维表面偶联剂处理前后的研究、用于界面的研究。可了解到界面
间有否化学键存在,偶联剂的作用机理也进一步得到证实。 确切判断粘接破坏发生的部位,因而可以很好地研究界面的破坏机理,
以及改进界面状况以提高复合材料的性能。
• 5.X射线衍射法 利用公式λ=2dsinθ(λ为X射线波长,d为晶体间距,θ为布拉格角)测定
由于纤维变形而引起布拉格角的变化。可研究增强材料与基体之间的粘接 强度。
• 3)表面反应性的测定 通常可以采用溶液吸附法来研究碳纤维的处理前后反应性的变化。如用
亚甲基兰作为吸附质,用分光光度法分析吸附前后溶液浓度的变化,在某— 温度下进行等温吸附试验,得到吸附等温值,并按Langmin直线方程处理, 求得最大吸附量作为纤维表面反应性的表征。吸附量的公式如下:
X (C C')V W
复合材料界面的研究方法
1.浸润性的测定
若基体能完全润湿被粘附的固体表面,则基体与 被粘附固体间的粘附强度将超过基体的内聚强度。
1)静态法测定接触角
静态法测定接触角,通常多用于测定玻璃纤维与液态树脂间的接触角。 测量仪器主要是各种角度测定仪,也可以用其它物理方法进行测定。
2)动态浸润速率的测定
基本原理:是纤维束(试样)底面上所受的压力,等于纤维束浸润树脂部分所 受的浮力,此压力作用下致使树脂渗进单向排列的纤维束间隙中去,树脂 的渗进速度取决于纤维与树脂间的浸润性和浸润速率。
复合材料的界面性能与优化分析
复合材料的界面性能与优化分析在当今的材料科学领域,复合材料因其优异的性能而备受关注。
复合材料是由两种或两种以上不同性质的材料通过物理或化学的方法组合在一起而形成的一种新型材料。
其性能不仅取决于各组成材料的性能,还在很大程度上取决于它们之间的界面性能。
复合材料的界面是指两种或多种材料相接触的区域。
这个区域虽然很薄,但对复合材料的整体性能有着至关重要的影响。
界面性能的优劣直接关系到复合材料在使用过程中的力学性能、物理性能、化学性能以及耐久性等。
首先,从力学性能方面来看,良好的界面结合能够有效地传递载荷。
当复合材料受到外力作用时,如果界面结合强度不足,就容易在界面处产生脱粘、开裂等现象,从而导致复合材料的强度和刚度下降。
相反,强界面结合可以使各组分材料协同工作,充分发挥各自的优势,提高复合材料的力学性能。
例如,在纤维增强复合材料中,纤维与基体之间的界面结合强度对复合材料的拉伸强度、弯曲强度和冲击强度等都有着显著的影响。
其次,在物理性能方面,界面性能也起着关键作用。
复合材料的热传导、电传导、热膨胀等物理性能都与界面的结构和性质密切相关。
例如,在金属基复合材料中,如果界面处存在大量的缺陷和杂质,会严重阻碍热和电的传导,降低复合材料的导热和导电性能。
此外,界面的存在还会影响复合材料的热膨胀系数,如果界面结合不良,在温度变化时容易产生热应力,导致复合材料的变形和破坏。
化学性能方面,界面是复合材料与外界环境相互作用的前沿阵地。
界面的化学稳定性决定了复合材料的耐腐蚀性、抗氧化性等化学性能。
如果界面处容易发生化学反应,如氧化、腐蚀等,就会削弱复合材料的性能,缩短其使用寿命。
例如,在聚合物基复合材料中,界面的亲水性或疏水性会影响其对水分的吸收和扩散,进而影响复合材料的耐湿性和耐老化性能。
那么,如何优化复合材料的界面性能呢?这需要从多个方面入手。
一方面,可以通过对原材料的表面处理来改善界面性能。
例如,对于纤维增强复合材料,可以对纤维表面进行氧化、涂层等处理,增加纤维与基体之间的化学键合和物理结合,提高界面结合强度。
复合材料的界面结构与性能研究
复合材料的界面结构与性能研究复合材料是由两种或两种以上的材料组成的,具有优异的性能和广泛的应用领域。
然而,复合材料中不同材料之间的界面结构对其性能有着至关重要的影响。
因此,对复合材料的界面结构与性能进行研究具有重要意义。
复合材料中不同材料之间的界面结构主要包括化学键、物理键和弱键。
其中,化学键是最强的一种键,能够在不同材料之间形成牢固的连接。
物理键则是通过分子间的吸引力和排斥力形成的键,其强度较弱。
弱键则是指表面吸附力和静电力等弱相互作用力,其强度最弱。
界面结构对复合材料的性能影响主要体现在以下几个方面:1. 强度:复合材料中不同材料之间的界面结构强度越高,其整体强度也就越高。
因此,通过优化界面结构可以提高复合材料的强度。
2. 耐久性:界面结构对复合材料的耐久性也有着重要影响。
如果界面结构不牢固,容易发生剥离和断裂等现象,从而降低了复合材料的耐久性。
3. 界面反应:不同材料之间的化学反应会导致界面结构发生变化,从而影响复合材料的性能。
因此,在设计复合材料时需要考虑不同材料之间的化学反应。
4. 热膨胀系数:复合材料中不同材料之间的热膨胀系数不同,会导致界面结构发生变形和应力集中等现象。
因此,在设计复合材料时需要考虑不同材料之间的热膨胀系数。
为了优化复合材料的界面结构,可以采用以下几种方法:1. 表面处理:通过表面处理可以改变材料表面的化学性质和物理性质,从而提高界面结构的牢固程度。
2. 添加剂:添加剂可以改变复合材料中不同材料之间的相互作用力,从而改善界面结构。
3. 界面增强剂:界面增强剂可以填充不同材料之间的空隙,从而提高界面结构的牢固程度。
4. 界面调节剂:界面调节剂可以调节不同材料之间的相互作用力,从而优化界面结构。
在实际应用中,需要根据具体情况选择适当的方法来优化复合材料的界面结构。
同时,还需要进行系统的研究和实验验证,以确保优化后的复合材料具有优异的性能和稳定性。
综上所述,复合材料中不同材料之间的界面结构对其性能有着至关重要的影响。
复合材料力学中的界面特性研究
复合材料力学中的界面特性研究复合材料作为一种重要的材料在现代工程领域中得到了广泛的应用。
而复合材料的性能受到许多因素的影响,其中界面特性是非常关键的一个方面。
本文将介绍复合材料力学中的界面特性的研究进展。
一、复合材料界面的概念复合材料由两种或两种以上的材料组成,其中界面是各个组分之间的交界面。
界面在复合材料的力学性能中起着重要的作用。
界面可以影响复合材料的强度、刚度、断裂韧性等性能指标。
二、复合材料界面特性的研究方法研究复合材料界面特性一般采用实验方法和数值模拟方法相结合的研究方法。
1. 实验方法实验方法是研究复合材料界面特性的重要手段之一。
常见的实验方法包括扫描电镜观察界面形貌、拉伸试验、剪切试验等。
通过实验可以得到界面的形貌信息、界面粘结强度等参数。
2. 数值模拟方法数值模拟方法可以帮助研究人员更全面地了解复合材料界面特性。
常用的数值模拟方法包括有限元法、分子动力学模拟、分子力场法等。
通过数值模拟可以模拟复合材料界面的力学行为,预测力学性能。
三、界面特性对复合材料性能的影响复合材料界面的性能对整体复合材料的性能起着至关重要的作用。
1. 粘结强度界面的粘结强度直接影响复合材料的强度和断裂韧性。
界面粘结强度越高,复合材料的性能越好。
2. 界面剪切界面剪切也是一个重要的界面特性。
界面剪切可以导致复合材料的剪切变形,影响其刚度。
3. 界面应力分布界面应力分布对复合材料的局部失效产生重要影响。
应力集中可能导致界面失效,从而影响复合材料的寿命。
四、改善复合材料界面特性的方法为了提高复合材料的性能,研究人员提出了一些改善界面特性的方法。
1. 表面处理通过表面处理可以增加界面的粘结强度,常见的表面处理方法有化学处理、物理处理等。
2. 添加界面增强剂添加界面增强剂可以改善界面的性能,如添加纳米颗粒、纳米纤维等。
3. 设计合理的复合材料结构合理的复合材料结构设计可以减少界面应力集中,提高界面的性能。
五、结论复合材料力学中的界面特性研究对于提高复合材料的性能具有重要意义。
- 1、下载文档前请自行甄别文档内容的完整性,平台不提供额外的编辑、内容补充、找答案等附加服务。
- 2、"仅部分预览"的文档,不可在线预览部分如存在完整性等问题,可反馈申请退款(可完整预览的文档不适用该条件!)。
- 3、如文档侵犯您的权益,请联系客服反馈,我们会尽快为您处理(人工客服工作时间:9:00-18:30)。
论文题目:复合材料的界面问题研究学院:材料科学与工程学院专业:材料学任课老师:霍冀川姓名:夏松钦学号:2011000148复合材料的界面问题研究摘要:界面问题,在复合材料制备中起很大的作用,界面结合的好坏,直接影响复合材料的整体性能,现针对国内外增强树脂用玻璃纤维、碳纤维及芳纶纤维的表面处理方法,强调界面问题的重要性关键词:界面问题;玻璃纤维;碳纤维;芳纶纤维1 前言界面是复合材料极为重要的微观结构,它作为增强体与基体连接的“桥梁”,对复合材料的物理机械性能有重要的影响。
随着对复合材料界面结构及优化设计研究的不断深入。
研究材料的界面力学行为与破坏机理是当代材料科学、力学、物理学的前沿课题之一。
复合材料一般是由增强相、基体相和它们的中间相(界面相)组成,各自都有其独特的结构、性能与作用,增强相主要起承载作用;基体相主要起连接增强相和传载作用,界面是增强相和基体相连接的桥梁,同时是应力的传递。
对增强相和基体相的研究已取得了许多成果,而对作为复合材料3大微观结构之一的界面问题的研究却不够深入,其原因是测试界面的精细方法运用起来较困难,其理论尚不完整,尤其从力学的角度研究界面的性质、作用及其对复合材料力学性能的影响和破坏机理等方面的工作正在开展。
界面的性质直接影响着复合材料的各项力学性能,尤其是层间剪切、断裂、抗冲击等性能,因此随着复合材料科学和应用的发展,复合材料界面及其力学行为越来越受到重视。
热塑性复合材料不仅有优越的力学性能、耐腐蚀、无毒性和低价格指数,还由于具有热固性复合材料所不具备的可重复加工和使用的特点,避免产生三废,有利于环保,因而倍受人们的重视,发展很迅速。
对于增强热塑性复合材料来说,由于基体本身缺乏可反应的活性官能团,很难与纤维产生良好化学键结合,因而界面结合的问题就显得更为重要。
2玻璃纤维的表面处理方法玻璃纤维在复合材料中主要起承载作用。
为了充分发挥玻璃纤维的承载作用,减少玻璃纤维和树脂基体差异对复合材料界面的影响,提高与树脂基体的粘合能力,因此有必要对玻璃纤维的表面进行处理[1],使之能够很好地与树脂粘合,形成性能优异的界面层,从而提高复合材料的综合性能。
2.1玻璃纤维表面的偶联剂处理Zisman[2]于1963年发表关于粘结的表面化学与表面能,他认为要获得完全的表面润湿,粘结剂起初必须是低粘度且其表面张力须低于无机物的临界表面张力,其结果引发了对采用偶联剂处理玻璃纤维表面的研究。
偶联剂主要用于增强玻璃纤维表面处理,其种类很多,包括硅烷偶联剂、铝酸酯偶联剂、钛酸酯偶联剂等,通过偶联剂能使两种不同性质的材料很好地“偶联”起来,从而使复合材料获得较好的粘结强度。
2.1.1硅烷偶联剂处理在用偶联剂对玻璃纤维表面处理中研究较多的是硅烷偶联剂。
硅烷偶联剂的水解产物通过氢键与玻纤表面作用,在玻纤表面形成具有一定结构的膜。
偶联剂膜含有物理吸附、化学吸附和化学键作用的3个级分,部分偶联剂会形成硅烷聚合物。
在加热的情况下,吸附于玻纤表面的偶联剂将与玻纤表面的羟基发生缩合,在两者之间形成牢固的化学键结合。
氨基硅烷偶联剂是偶联剂的一种,研究结果表明:含有氨基的偶联剂比不含氨基的偶联剂对玻璃纤维的表面处理效果好,因为偶联剂的氨基与基体中的氨基有亲和性,使界面较好粘结;氨基还能与接枝的酸酐官能团反应,提高复合材料的性能。
Pluedde—mann[3]采用含羧基的化合物改性聚丙烯。
并用含氨基的硅烷偶联剂来处理玻璃纤维,使玻璃纤维增强聚丙烯复合材料的力学性能得到极大提高。
Crespy[4]采用含有双键的乙烯基—乙氧基硅氧烷和正丙稀—三甲氧基硅氧烷以及相容助剂混合物处理玻璃纤维的表面,使玻璃纤维增强聚丙烯复合材料的冲击强度、拉伸强度和弯曲强度得到大幅度的提高。
2.1.2铝酸酯偶联剂处理铝酸酯偶联剂具有处理方法多样化、偶联反应快、使用范围广、处理效果好、分解温度高、价格性能比好等优点而被广泛地应用。
陈育如[5]用铝锆偶联剂对玻璃钢中玻璃纤维的表面处理比用沃兰(甲基丙稀酰氯化铬络合物)、硅烷偶联剂处理的效果要好,其弯曲强度、拉伸强度、弯曲模量都高于后者处理的结果。
2.1.3偶联剂和其它助剂协同处理由于偶联剂的独特性质,利用偶联剂和其它物质的协同效应对玻璃纤维的表面进行处理,如运用氯化物和硅烷偶联剂混合处理玻璃纤维的表面,可显著改善PP/GF复合材料强度,特别是采用具有热稳定性的氯化二甲苯,其性能最优异[6]。
3碳纤维的表面处理方法碳纤维增强树脂基复合材料(CFRP)由于具有密度小、比强度高、比模量高、热膨胀系数小等一系列优异特性,在航天器结构上已得到广泛的应用。
碳纤维表面惰性大、表面能低,缺乏有化学活性的官能团反应活性低,与基体的粘结性差,界面中存在较多的缺陷,直接影响了复合材料的力学性能,限制了碳纤维高性能的发挥。
为了改善界面性能,充分利用界面效应的有利因素,可以通过对碳纤维进行表面改性的办法来提高其对基体的浸润性和粘结性。
国内外对碳纤维表面改性的研究[7-8]进行得十分活跃,主要有氧化处理、涂覆处理、等离子体处理法等,经表面改性后的砂纤维,其复合材料层间剪切强度有显著提高。
3.1氧化处理3.1.1 气相氧化法气相氧化[9]是用氧化性气体来氧化纤维表面而引入极性基团(如—OH等),并给予适宜的粗糙度来提高复合材料层间剪切强度。
如把碳纤维在450℃下空气中氧化10min,可提高复合材料的剪切强度和拉伸强度;采用浓度为0.5—15mg/l 的臭氧连续导入碳纤维表面处理炉对碳纤维进行表面处理,处理后碳纤维复合材料的层间剪切强度为78.4~105、8MPa;除这种对纤维直接进行表面气相氧化外,还可以对经涂覆处理的纤维进行氧化改性。
气相氧化虽易于实现工业化,但它对纤维拉伸强度的损伤比液相氧化大。
此外随纤维种类的不同(高模量碳纤维、高强度碳纤维)、处理温度的不同,气相氧化处理效果也不尽相同。
纤维产生过度的刻蚀和裂解,而且在一定条件下含氧基团数量较气相氧化多,因此是实践中常用的处理方法之一。
3. 1.2液相氧化法液相氧化处理对改善碳纤维/树脂复合材料[10]的层间剪切强度很有效。
硝酸、酸性重铬酸钾、次氯酸钠、过氧化氢和过硫酸钾等都可以用于对碳纤维进行表面处理[11]。
硝酸是液相氧化中研究较多的一种氧化剂,用硝酸氧化碳纤维,可使其表面产生羧基、羟基和酸性基团,这些基团的量随氧化时间的延长和温度的升高而增多,氧化后的碳纤维表面所含的各种含氧极性基团和沟壑明显增多,有利于提高纤维与基体材料之间的结合力。
由于液相氧化的方法较气相氧化法温和,不易使纤维产生过度的刻蚀和裂解,而且在一定条件下含氧基团数量较气相氧化多,因此是实践中常用的处理方法之一。
3.1.3电化学氧化法电化学氧化法[12] 处理利用了碳纤维的导电性,一般是将碳纤维作为阳极置于电解质溶液中,通过电解所产生的活性氧来氧化碳纤维表面而引入极性基团,从而提高复合材料性能。
与其它氧化处理相同,电化学氧化使纤维表面引入各种功能基团从而改善纤维的浸润、粘敷特性及与基体的键合状况,增强碳纤维复合材料的力学性能。
国内房宽峻等通过正交试验的方法对碳纤维在酸、碱、盐3类电解质中的电化学氧化进行研究,认为在氧化过程中,电解质种类是影响处理后碳纤维表面酸性官能团的最主要因素,其次是处理时间和电流密度,电解质浓度的影响不显著。
4芳纶纤维的表面处理方法芳纶纤维以其高比模量、高比强度、耐疲劳等优异性能在航空航天领域得到了广泛的应用。
但是从其结构可知,它是刚性分子,分子对称性高,横向分子间作用力弱,且分子间氢键弱,在压缩及剪切力作用下容易产生断裂。
因此,为了充分发挥芳纶优异的力学性能.对芳纶表面进行改性处理,改善芳纶增强复合材料的界面结合状况成为材料科学界研究的一个热点。
目前,针对芳纶进行的表面改性技术,主要集中在利用化学反应改善纤维表面组成及结构,或借助物理作用提高芳纶与基体树脂之间的浸润性。
4.1表面涂层法表面涂层法是在纤维表面涂上柔性树脂,而后与基体复合。
涂层可以钝化裂纹的扩展,增大纤维的拔出长度,从而增加材料的破坏能。
这类处理剂主要是改善材料的韧性,同时又使材料的耐湿热老化性能提高。
目前用于芳纶的涂层主要是饱和、不饱和脂肪族酯类,包括SVF一200硅烷涂层、Estapol一7008聚氨酯涂层[13]等。
4.2.1表面刻蚀技术表面刻蚀技术是通过化学试剂处理芳纶,引起纤维表面的酰氨键水解,从而破坏纤维表面的结晶状态,使纤维表面粗化。
一般表面刻蚀技术采用的化学试剂为酰氨。
Tarantili、Andreopoulos 等人采用甲基丙烯酸酰氨的CCl4溶液对芳纶进行了处理,并研究了表面刻蚀芳纶后,芳纶/环养复合材料的力学性能。
经过丙烯酰氯处理后的纤维,一方面,表面粗糙度增加,增大了纤维与基体的啮合,同时消除了弱界面层,增加了纤维/基体间的接触面积;另一方面提高了纤维的表面能,使树脂更有效地润湿纤维,因而使改性后的芳纶/环氧复合材料韧性提高8%。
4.2.2表面接枝技术表面接枝技术改性芳纶是化学改性方法中研究最多的技术。
根据接枝官能团位置的不同,可将表面接枝技术分为两大类:一是发生在苯环上的接枝反应;另一种则是取代芳纶表面层分子中酰氨键上的氢的接枝反应。
5结束语影响纤维/树脂基复合材料性能的因素很多,如纤维与树脂基体的匹配性、成型工艺中的质量控制参数优化等,以上介绍了玻纤、碳纤维及芳纶纤维表面处理方法,主要是针对如何提高纤维与树脂基体的粘接性能,还有其它一些处理方法,实际应用中,应根据纤维类型、基体材料的种类及实际需要和条件来选择表面处理方法。
总之,作为先进复合材料的增强材料,对纤维的表面结构与性质、表面改性的研究将会受到越来越多的关注,碳纤维、芳纶纤维也将在航天领域中发挥越来越重要的作用。
参考文献[1] 杨俊.蔡力锋,林志勇.增强树脂用玻璃纤维的表面处理方法及其对界面的影响[J].塑料,2004,33(1).[2]Wazisman.Surface chemistry of plastic reinforced by strong fibers[J].IEC Product Research and Development,1963,8(2):98~111.[3]P G Pape.E P Plueddemann.Improvements in saline coupling agents for more durable bonding at the polymer reinforcement interface fJ J.ANTEC.1991:1870~1875.[4]A Crespy,J P Franon.S Turenne,et al.Effect of silanes on the glass fiber/polypropylene.[5] 陈育如铝锆偶联剂的应用[J].塑料工业.2001.29(6):44-46.[6]姜勇.徐声钧,王燕舞玻璃纤维增强聚丙烯的研制与应用[J].塑料科技.2000,(1):7~9.[7] 吴士庆碳纤维的表面处理[J].化工新型材料.2000.28(3):11~14[8] 贺福.等用气相氧化法对碳纤维进行表面处理[J]复合材料学报.1998.(1):569.[9]贺福.王润娥.等.碳纤维表面处理方法及其设备[P] CN 1032042,1989—03—29.[10] Yang Yonggang.He Fu.Li Zhijing.et a1.Method for treating carbon fiber surface[P].CN 1157354,1997—08—20.[11]康永.等.沥青基碳纤维表面复合处理的研究[J].功能高分子学报.1999.12(4):450~452.[12]Yue Z R.Jiang W Wang L,et a1.Surface characterization of electrochemically oxidized carbon fibers carbon[J],1999,37(11):1785~1796.[13]Y M Ma.F Castino Fracture toughness of kevlar—epoxy composites with controlled interfacial bonding[J]Journal of Material Science.1984.(19):1638~1655.。