复合材料的界面改性
复合材料的界面改性技术探讨
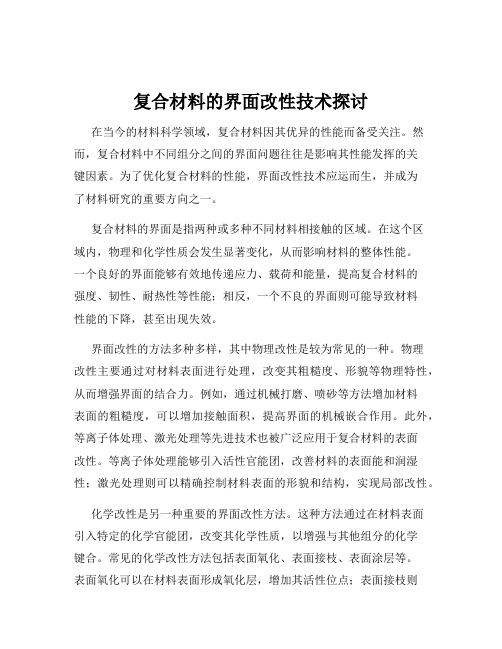
复合材料的界面改性技术探讨在当今的材料科学领域,复合材料因其优异的性能而备受关注。
然而,复合材料中不同组分之间的界面问题往往是影响其性能发挥的关键因素。
为了优化复合材料的性能,界面改性技术应运而生,并成为了材料研究的重要方向之一。
复合材料的界面是指两种或多种不同材料相接触的区域。
在这个区域内,物理和化学性质会发生显著变化,从而影响材料的整体性能。
一个良好的界面能够有效地传递应力、载荷和能量,提高复合材料的强度、韧性、耐热性等性能;相反,一个不良的界面则可能导致材料性能的下降,甚至出现失效。
界面改性的方法多种多样,其中物理改性是较为常见的一种。
物理改性主要通过对材料表面进行处理,改变其粗糙度、形貌等物理特性,从而增强界面的结合力。
例如,通过机械打磨、喷砂等方法增加材料表面的粗糙度,可以增加接触面积,提高界面的机械嵌合作用。
此外,等离子体处理、激光处理等先进技术也被广泛应用于复合材料的表面改性。
等离子体处理能够引入活性官能团,改善材料的表面能和润湿性;激光处理则可以精确控制材料表面的形貌和结构,实现局部改性。
化学改性是另一种重要的界面改性方法。
这种方法通过在材料表面引入特定的化学官能团,改变其化学性质,以增强与其他组分的化学键合。
常见的化学改性方法包括表面氧化、表面接枝、表面涂层等。
表面氧化可以在材料表面形成氧化层,增加其活性位点;表面接枝则是将特定的分子链或官能团接枝到材料表面,提高其相容性;表面涂层则是在材料表面涂覆一层具有特定性能的涂层,改善界面性能。
除了物理和化学改性方法,还有一些其他的改性技术也在不断发展和应用。
例如,纳米技术的引入为复合材料的界面改性带来了新的机遇。
纳米粒子由于其独特的尺寸效应和表面效应,可以有效地改善复合材料的界面性能。
将纳米粒子添加到界面区域,能够增强界面的结合强度,提高材料的力学性能和稳定性。
在实际应用中,选择合适的界面改性技术需要综合考虑多种因素,如复合材料的组成、性能要求、成本等。
复合材料的界面工程与性能优化
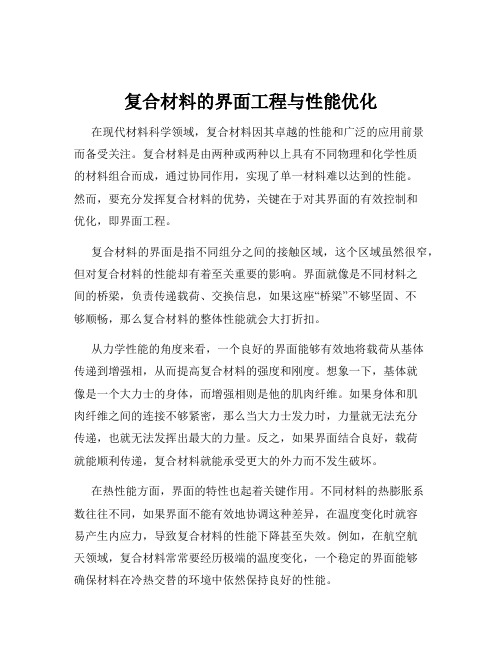
复合材料的界面工程与性能优化在现代材料科学领域,复合材料因其卓越的性能和广泛的应用前景而备受关注。
复合材料是由两种或两种以上具有不同物理和化学性质的材料组合而成,通过协同作用,实现了单一材料难以达到的性能。
然而,要充分发挥复合材料的优势,关键在于对其界面的有效控制和优化,即界面工程。
复合材料的界面是指不同组分之间的接触区域,这个区域虽然很窄,但对复合材料的性能却有着至关重要的影响。
界面就像是不同材料之间的桥梁,负责传递载荷、交换信息,如果这座“桥梁”不够坚固、不够顺畅,那么复合材料的整体性能就会大打折扣。
从力学性能的角度来看,一个良好的界面能够有效地将载荷从基体传递到增强相,从而提高复合材料的强度和刚度。
想象一下,基体就像是一个大力士的身体,而增强相则是他的肌肉纤维。
如果身体和肌肉纤维之间的连接不够紧密,那么当大力士发力时,力量就无法充分传递,也就无法发挥出最大的力量。
反之,如果界面结合良好,载荷就能顺利传递,复合材料就能承受更大的外力而不发生破坏。
在热性能方面,界面的特性也起着关键作用。
不同材料的热膨胀系数往往不同,如果界面不能有效地协调这种差异,在温度变化时就容易产生内应力,导致复合材料的性能下降甚至失效。
例如,在航空航天领域,复合材料常常要经历极端的温度变化,一个稳定的界面能够确保材料在冷热交替的环境中依然保持良好的性能。
除了力学和热性能,界面还对复合材料的电学、光学等性能产生影响。
比如在电子封装材料中,界面的电学特性直接关系到信号的传输速度和稳定性;在光学材料中,界面的平整度和折射率匹配程度决定了光线的透过率和反射率。
那么,如何进行复合材料的界面工程来优化其性能呢?这涉及到多个方面的策略和技术。
首先是对界面的物理和化学改性。
通过物理方法,如表面打磨、等离子体处理等,可以增加界面的粗糙度和活性,从而提高界面的结合强度。
化学改性则包括对基体和增强相表面进行化学处理,引入官能团,以增强它们之间的化学键合。
复合材料的界面

复合材料的界面复合材料是由两种或两种以上不同的材料组成的材料,通过各自的特性相互作用形成的一种新型材料。
界面是不同材料之间的接触面,是复合材料性能的决定因素之一。
下面将从界面的作用、界面的特性和界面的调控三个方面对复合材料的界面进行详细介绍。
界面在复合材料中起着连接、传递和分散应力的作用。
首先,界面连接了不同材料一起,使其形成整体性能优于单个材料的复合材料。
其次,界面能够传递应力,使复合材料整体受力均匀、分散应力集中,提高材料的强度和韧性。
最后,界面还能够分散应力,减少裂纹扩展和断裂的可能性,延长复合材料的使用寿命。
界面的特性主要包括接触角度、界面能、亲水性或疏水性等。
首先,接触角度反映了界面的亲水性或疏水性,即其与液体接触时的表面张力。
亲水性的界面会使液体在复合材料中能够更好地湿润、浸润,提高复合材料的粘合度和界面传递性。
其次,界面能是指界面上分子之间相互作用的能量。
界面能越小,表示复合材料中不同材料之间的相容性越好,界面强度越高。
最后,亲水性界面和疏水性界面对复合材料的性能也会产生不同的影响。
如亲水性界面可增加复合材料的应力强度、韧性和热稳定性,而疏水性界面可减少复合材料的吸湿性和电导性。
界面的调控主要通过界面改性和表面处理两个途径实现。
首先,通过界面改性可以改变界面的性质,提高其性能,例如通过添加界面活性剂进行处理,使界面能更好地吸附和传递应力;通过聚合物接枝物改性,增加界面粘合力等。
其次,通过表面处理可以对界面进行改善,例如通过物理或化学方法处理材料表面,使其表面特性更加适合复合材料的应用。
常用的表面处理方法有溶剂清洗、电子束辐照、化学氧化等。
综上所述,界面是影响复合材料性能的重要因素,通过界面的调控可以改善复合材料的性能。
理解和研究界面的特性和调控方法对于开发出更加优异的复合材料具有重要意义。
复合材料的复合原理及界面
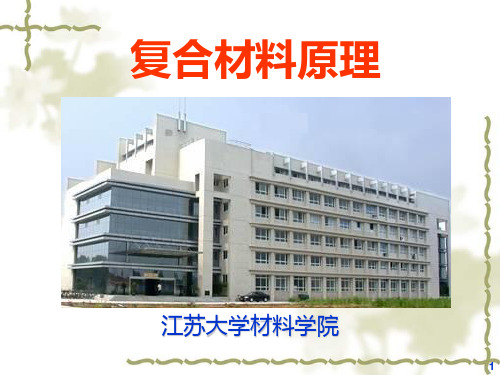
作用,而且在不同的生产过程中或复合材料的使
用期间,粘结机理还会发生变化,如由静电粘结 变成反应粘结。
33
体系不同,粘结的种类或机理不同,这主要取决于
基体与增强材料的种类以及表面活性剂(或称偶联剂) 的类型等。 界面粘结机理主要有机械作用理论、静电作用理论、 界面反应理论、浸润理论、可变形层理论、约束层 理论等。
28
为了提高复合材料组元间的浸润性,常常通过对增
强材料进行表面处理的方法来改善润湿条件,有时也可
通过改变基体成分来实现。
29
多数陶瓷基复合材料中增强材料与基体之间不发生化
学反应,或不发生激烈的化学反应。
有些陶瓷基复合材料的增强材料与其基体的化学成分 相同。
30
例如,如SiC晶须或SiC纤维增强SiC陶瓷,这种复合材 料也希望建立一个合适的界面,即合适的粘接强度、界面层 模量和厚度以提高其韧性。
外,还有基体中的合金元素和杂质、由环境带来的
杂质。 这些成分或以原始状态存在,或重新组合成新的化 合物。 界面上的化学成分和相结构非常复杂。
7
复合材料界面的作用可以归纳为以下几种效应: 1、传递效应 界面能传递力,即将外力传递给增强 体,起到基体和增强体之间的桥梁作用。 2、阻断效应 结合适当的界面有阻止裂纹扩展、中 断材料破坏、减缓应力集中的作用。 3、不连续效应 在界面上产生物理性能的不连续性 等现象,如抗电性、耐热性、尺寸稳定性等。
26
对于一个指定的体系,接触角随着温度、保持时 间、吸附气体等而变化。 浸润性仅仅表示了液体与固体发生接触时的情况, 而并不能表示界面的粘结性能。
27
一种体系的两个组元可能有极好的浸润性,但它们之 间的结合可能很弱,如范德华物理键合形式。
第十五章-复合材料的界面及界面优化设计
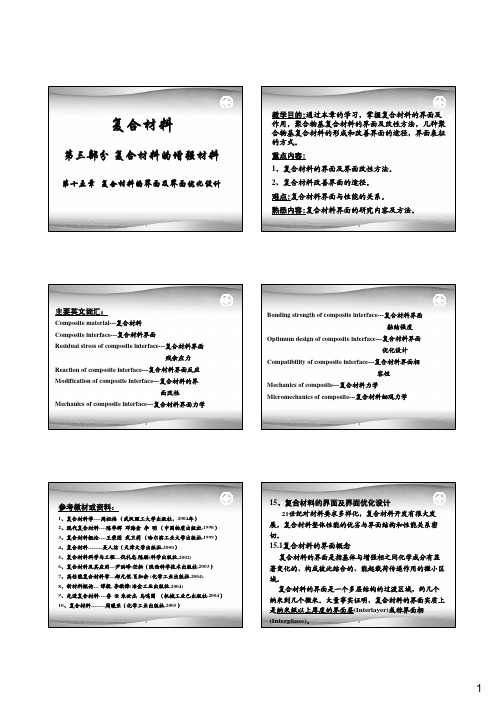
复合材料第三部分 复合材料的增强材料第十五章 复合材料的界面及界面优化设计教学目的:通过本章的学习,掌握复合材料的界面及 作用,聚合物基复合材料的界面及改性方法,几种聚 合物基复合材料的形成和改善界面的途径,界面表征 的方式。
重点内容: 1、复合材料的界面及界面改性方法。
2、复合材料改善界面的途径。
难点:复合材料界面与性能的关系。
熟悉内容:复合材料界面的研究内容及方法。
12主要英文词汇:Composite material---复合材料 Composite interface---复合材料界面 Residual stress of composite interface---复合材料界面 残余应力 Reaction of composite interface---复合材料界面反应 Modification of composite interface---复合材料的界 面改性 Mechanics of composite interface---复合材料界面力学3Bonding strength of composite interface---复合材料界面 黏结强度 Optimum design of composite interface---复合材料界面 优化设计 Compatibility of composite interface---复合材料界面相 容性 Mechanics of composite---复合材料力学 Micromechanics of composite---复合材料细观力学4参考教材或资料:1、复合材料学----周祖福 (武汉理工大学出版社,2004年) 2、现代复合材料----陈华辉 邓海金 李 明 (中国物质出版社,1998) 3、复合材料概论----王荣国 武卫莉 (哈尔滨工业大学出版社,1999) 4、复合材料--------吴人洁(天津大学出版社,2000) 5、复合材料科学与工程---倪礼忠,陈麒(科学出版社,2002) 6、复合材料及其应用—尹洪峰,任耘(陕西科学技术出版社,2003) 7、高性能复合材料学---郝元恺,肖加余 (化学工业出版社,2004) 8、新材料概论--- 谭毅, 李敬锋(冶金工业出版社,2004) 9、先进复合材料----鲁 云 朱世杰 马鸣图 (机械工业已出版社,2004) 10、复合材料--------周曦亚(化学工业出版社,2005)515、复合材料的界面及界面优化设计21世纪对材料要求多样化,复合材料开发有很大发 展,复合材料整体性能的优劣与界面结构和性能关系密 切。
PET纤维_环氧复合材料界面性能改性研究
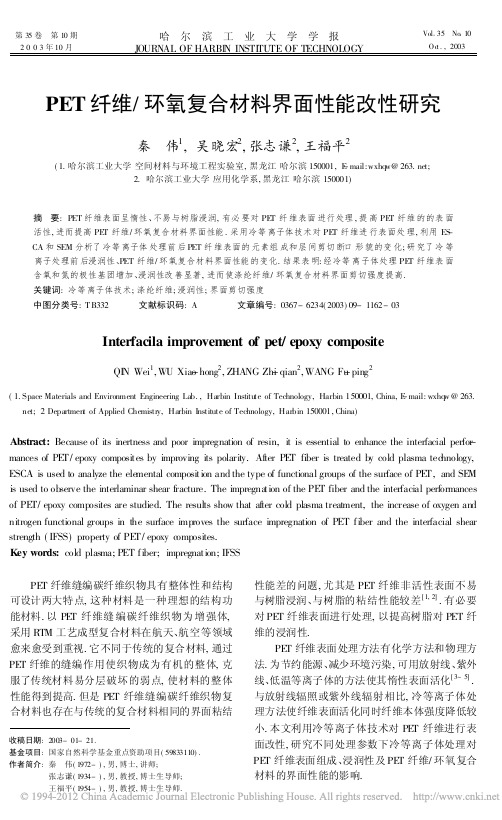
第35卷 第10期2003年10月哈 尔 滨 工 业 大 学 学 报JOURNAL OF HARBI N INSTI TUTE OF TECHNOLOGYVol 135No 110Oc t.,2003PET 纤维/环氧复合材料界面性能改性研究秦 伟1,吴晓宏2,张志谦2,王福平2(1.哈尔滨工业大学空间材料与环境工程实验室,黑龙江哈尔滨150001,E -mail:wxhq w@;2.哈尔滨工业大学应用化学系,黑龙江哈尔滨150001)摘 要:PET 纤维表面呈惰性、不易与树脂浸润,有必要对PE T 纤维表面进行处理,提高PE T 纤维的的表面活性,进而提高PE T 纤维/环氧复合材料界面性能.采用冷等离子体技术对PE T 纤维进行表面处理,利用ES -CA 和SEM 分析了冷等离子体处理前后PET 纤维表面的元素组成和层间剪切断口形貌的变化;研究了冷等离子处理前后浸润性、PET 纤维/环氧复合材料界面性能的变化.结果表明:经冷等离子体处理PE T 纤维表面含氧和氮的极性基团增加、浸润性改善显著,进而使涤纶纤维/环氧复合材料界面剪切强度提高.关键词:冷等离子体技术;涤纶纤维;浸润性;界面剪切强度中图分类号:T B332文献标识码:A文章编号:0367-6234(2003)09-1162-03Interfacila improvement of pet/epoxy compositeQI N Wei 1,W U Xiao -hong 2,ZHANG Zh-i qian 2,WANG Fu -ping 2(1.Space Materials and Environment Engineering Lab.,Harbin Institu te of Technology,Harbin 150001,China,E -mail:wxhq w @;2Departmen t of Applied Chemistry,Harbin Institute of Technology,Harbin 150001,China)Abstract:Because of its inertness and poor impregnation of resin,it is essential to enhance the interfacial perfor -mances of PE T/epoxy composites by improving its polarity.After PE T fiber is treated by cold plasma tec hnology,ESCA is used to analyze the ele mental composition and the type of functional groups of the surface of PE T,and SE M is used to observe the interlaminar shear fracture.The impregna tion of the PE T fiber and the interfacial performances of PE T/epoxy composites are studied.The results show that after cold plasma treatment,the increase of oxygen and nitrogen functional groups in the surface improves the surface impregnation of PET fiber and the interfacial shear strength (IFSS)property of PE T/epoxy c omposites.Key words:cold plasma;PET fiber;impregnation;IFSS 收稿日期:2003-01-21.基金项目:国家自然科学基金重点资助项目(59833110).作者简介:秦 伟(1972-),男,博士,讲师;张志谦(1934-),男,教授,博士生导师;王福平(1954-),男,教授,博士生导师.PE T 纤维缝编碳纤维织物具有整体性和结构可设计两大特点,这种材料是一种理想的结构功能材料.以PE T 纤维缝编碳纤维织物为增强体,采用RTM 工艺成型复合材料在航天、航空等领域愈来愈受到重视.它不同于传统的复合材料,通过PE T 纤维的缝编作用使织物成为有机的整体,克服了传统材料易分层破坏的弱点,使材料的整体性能得到提高.但是PE T 纤维缝编碳纤维织物复合材料也存在与传统的复合材料相同的界面粘结性能差的问题,尤其是PE T 纤维非活性表面不易与树脂浸润、与树脂的粘结性能较差[1,2].有必要对PE T 纤维表面进行处理,以提高树脂对PET 纤维的浸润性.PE T 纤维表面处理方法有化学方法和物理方法.为节约能源、减少环境污染,可用放射线、紫外线、低温等离子体的方法使其惰性表面活化[3~5].与放射线辐照或紫外线辐射相比,冷等离子体处理方法使纤维表面活化同时纤维本体强度降低较小.本文利用冷等离子体技术对PE T 纤维进行表面改性,研究不同处理参数下冷等离子体处理对PE T 纤维表面组成、浸润性及PE T 纤维/环氧复合材料的界面性能的影响.1实验111原料及试样制备用大连涤纶研究所提供的PE T纤维作为增强体.将PE T纤维均匀缠在8010mm@4010mm@110mm的铝合金框上,将整个框放在电容耦合式等离子系统的反应腔中处理.树脂为无锡树脂厂生产的E-51环氧树脂,固化剂为天津津东化工厂生产的2-乙基4-甲基咪唑,按m(环氧树脂)B m(咪唑)=100B7的比例配制胶液.将均匀缠绕PE T纤维的铝框放到密闭的模具中,采用RTM工艺成型制成复合材料.112试样测试用日本ESCA-750型电子能谱仪分析处理前后的PE T纤维表面组成的变化.以乙二醇(分析纯)为浸润剂,利用SB-312型浸润测定仪测定处理前后的PE T纤维浸润性的变化.用日本产的复合材料界面性能测试仪,测复合材料的界面剪切强度.采用美国Amray-1000B型扫描电子显微镜对层间剪切破坏的试样断口进行分析.2结果与讨论211冷等离子体处理对PET纤维表面性质的影响为了分析PET纤维经冷等离子体处理后与树脂基体间粘结强度提高的原因,采用XPS分析技术对冷等离子体处理前后PE T表面元素组成及表面官能团种类、含量进行定量分析,如表1所示.表1PET纤维表面元素组成的丰度比Tab.1Abundance radio o f surface of PET(%) PET C O N未处理78.8421.160经冷等离子体处理66.2132.23 1.56从表1中可见,PET纤维经冷等离子处理后表面的C元素含量减少,O元素含量增加,出现了少量的N元素.212冷等离子体处理对浸润性的影响用乙二醇作浸润剂考察冷等离子体处理对PE T纤维表面润湿程度,结果见图1.从图1可以看出,随着等离子体处理功率延长,乙二醇对PE T 纤维的接触角逐渐减小.等离子体在1min的处理条件下,0~300W,接触角急剧下降,300W后仍持续下降,但趋势平缓.这表明,冷等离子体可显著改善PET纤维的表面润湿性.这是由于冷等离子体处理使PET纤维的表面极性基团增加,从而使PET纤维表面张力增大,惰性表面自由能增大,因此表面润湿性变好.图1冷等离子体处理对PE T纤维浸润性的影响Fi g.1Effect of cold plasma on impregnation of PET fiber213冷等离子体处理对复合材料界面性能的影响界面的粘结性能好坏直接影响复合材料的界面性能.界面粘结强度的直接表征法主要有单丝拔出法、临界长度测量法等.复合材料界面性能测试仪是根据单丝拔出法的原理设计的可直接测试复合材料的界面粘结强度的仪器.其试样制作简单,并且能较准确给出复合材料的界面强度.冷等离子体处理对界面剪切强度(I FSS)的影响见图2.从图2可以看出,在300W之前,随功率增大,IF-SS不断增大,在300W时IFSS最大,提高26%,超过300W时逐渐下降.这是由于一方面PET纤维表面经冷等离子体刻蚀,纤维表面沟槽增多,比表面积增大,由此增加了纤维与基体间的机械互锁作用;另一方面PE T纤维表面的活性基团增多,增加了与树脂反应的活性点,从而可使复合材料界面剪切强度提高.图2冷等离子体处理对复合材料的界面剪切强度的影响Fi g.2Effect of cold plasma treatment on IFSS of composite#1163#第10期秦伟,等:PE T纤维/环氧复合材料界面性能改性研究214 复合材料的破坏断口的SEM 分析纤维复合材料的界面起传递载荷的作用,界面粘结强度的高低直接影响载荷传递的效率,进而影响复合材料的宏观力学性能.为了了解等离子体处理对PE T/环氧复合材料界面粘结强度的影响机理,对复合材料的层间剪切破坏的断口形貌进行了观察,结果如图3所示.图3中(a)、(b)分别为未经等离子体处理和冷等离子体处理的复合材料断口形貌.从图3可以看出,未处理试样的断口处纤维成细颈现象,与树脂脱粘,说明纤维与树脂间粘接强度差;而经冷等离子体处理的复合材料的断口呈脆性断裂,纤维与树脂结合良好,说明经冷等离子体处理复合材料的界面的粘结性能提高.这是由于:未处理的PE T 纤维大部分表面成惰性,与树脂的浸润性较差,进而与树脂结合较差;而冷等离子体处理增加了树脂浸润纤维的表面积,提高了浸润性,增加了纤维表面与环氧树脂基体之间强相互作用活性点,从而使界面粘结性能提高.图3 复合材料层间剪切断口SE M 图Fig.3 SE M photographs of composites after shear fracture3 结 论(1)经冷等离子体处理可使PE T 纤维表面N 和O 元素明显增多,因而可使PET 纤维的润湿性得到改善.(2)经冷等离子体处理使PE T 纤维/环氧复合材料的界面粘结强度大幅提高,在300W 、1min 处理条件下,界面剪切强度比未处理试样提高26%.(3)剪切破坏的样品的SE M 分析可以看出,经等离子体处理后的复合材料的界面粘结性能较好,进而证明冷等离子体处理可以使PE T 纤维/环氧复合材料的界面性能提高.参考文献:[1]秦 伟,张志谦.冷等离子体处理对碳纤维缝编织物/环氧复合材料界面性能的影响[J].航空材料学报,2001,21(4):38-41.[2]HSIEH Y L,WU M P.Residual reactivity for surface graftingof acrylic acid on argon glow -discharged ploy (ethylene terephthalate)(PE T )fil ms[J].J Appl Polym Sci,1991,43:2067-2082.[3]WU S R,SHEU G S,SHYU S S.Kevlar fiber-epoxy ad -hesion and its effect on composi te mechanical and fracture properties by plasma and chemical treatment[J].J Applied Polymer Science,1996,62:1347-1360.[4]PLAWKY U,LONDSC HIE N M ,MICHAELI W.Surfacemodification of an aramid fiber treated in low -temperature microwave plasma[J].J Material Science,1996,31:6043-6053.[5]张卫华,梁红军,後晓淮.等离子体引发聚合[J].化学通报,1999,8:26-31.(编辑 蔡公和)#1164#哈 尔 滨 工 业 大 学 学 报 第35卷。
什么是纤维增强复合材料的增韧其方法有哪些
什么是纤维增强复合材料的增韧其方法有哪些1.界面改性:界面是纤维与基体之间的接触区域,界面的性质对材料的力学性能起着重要的影响。
通过在界面处添加界面改性剂,可以提高纤维与基体的结合强度和界面的稳定性,增加材料的韧性。
2.纤维表面修饰:通过改变纤维表面的形貌和化学性质,可以增加纤维与基体的结合强度。
常见的纤维表面修饰方法包括表面粗化、表面氧化和表面涂覆。
3.高分子基质改性:通过在基质中添加改性剂,可以改善基质的韧性和能量吸收能力。
常用的基质改性方法包括添加增韧剂、添加弹性体和改变基质的组成。
4.交联:通过交联反应,可以增加材料的网络结构和结合强度。
常见的交联方法包括热交联、辐射交联和化学交联。
5.纤维增韧:在纤维增强复合材料中添加纤维增韧剂,可以提高材料的韧性。
常用的纤维增韧剂包括微纳纤维、碳纤维和纳米纤维。
6.层叠复合:通过层叠不同方向的纤维增强材料,可以提高材料的韧性和耐冲击性。
常见的层叠复合方法包括交替层叠和交叉层叠。
7.界面增强:通过在界面处添加增强层,可以增加纤维和基体之间的结合强度。
常见的界面增强方法包括纳米颗粒增强、表面修饰和涂覆增强。
8.组分设计:通过优化纤维和基体的比例和结构,可以提高材料的韧性和弯曲性能。
通常选择具有优良力学性能的纤维和基体组合,可以增强材料的整体性能。
9.加工工艺改进:改进材料的加工工艺,可以提高材料的致密度和结构均匀性,从而提高材料的韧性。
常见的加工工艺改进方法包括预浸法、层压法和注塑法。
综上所述,纤维增强复合材料的增韧方法包括界面改性、纤维表面修饰、高分子基质改性、交联、纤维增韧、层叠复合、界面增强、组分设计和加工工艺改进等。
这些方法可以综合应用,以满足不同应用场景对材料韧性的需求。
复合材料的界面性能与优化
复合材料的界面性能与优化在现代材料科学领域,复合材料因其出色的性能而备受关注。
复合材料是由两种或两种以上具有不同物理和化学性质的材料组合而成,其性能并非各个组分材料性能的简单加和,而是通过各组分之间的协同作用实现了性能的优化和提升。
而在这其中,复合材料的界面性能起着至关重要的作用。
复合材料的界面,简单来说,就是不同组分材料之间相互接触和作用的区域。
这个区域虽然在尺寸上相对较小,但却对复合材料的整体性能产生着深远的影响。
就好像一个团队中各个成员之间的沟通与协作环节,虽然看似细微,却决定着整个团队的运作效率和成果。
首先,我们来探讨一下复合材料界面性能的重要性。
良好的界面性能能够有效地传递载荷。
当复合材料受到外力作用时,如果界面能够将应力从一种材料传递到另一种材料,那么整个复合材料就能更好地承受外力,从而表现出更高的强度和韧性。
界面性能还对复合材料的热性能有着重要影响。
不同的材料具有不同的热膨胀系数,如果界面结合不好,在温度变化时就容易产生热应力,导致材料性能下降甚至失效。
此外,界面性能也会影响复合材料的耐腐蚀性能和电性能等。
那么,复合材料的界面性能具体包括哪些方面呢?界面的结合强度是一个关键因素。
如果结合强度过低,在使用过程中容易出现界面脱粘,从而降低材料的性能;而结合强度过高,又可能导致材料在受到冲击时无法通过界面的解离来吸收能量,造成脆性断裂。
界面的化学稳定性也是不容忽视的。
在一些恶劣的环境中,界面处容易发生化学反应,从而影响材料的长期使用性能。
界面的微观结构同样重要,它决定了界面的物理和化学性质,进而影响复合材料的整体性能。
接下来,我们看看影响复合材料界面性能的因素。
材料的表面处理方式是一个重要方面。
通过对增强材料表面进行化学处理、物理处理或者涂层处理,可以改变其表面的化学组成和物理形貌,从而提高与基体材料的相容性和结合力。
制备工艺条件也会对界面性能产生影响。
例如,在复合材料的制备过程中,温度、压力、时间等参数的控制都会影响界面的形成和性能。
复合材料的界面性能与性能优化
复合材料的界面性能与性能优化在现代材料科学领域,复合材料因其出色的性能而备受关注。
复合材料是由两种或两种以上不同性质的材料,通过物理或化学的方法组合在一起而形成的一种新型材料。
这些不同的材料在性能上相互补充、协同作用,从而使复合材料具有单一材料所无法比拟的优越性能。
然而,复合材料性能的优劣在很大程度上取决于其界面性能。
复合材料的界面是指两种或多种不同材料之间的接触面。
这个界面区域虽然很薄,但却对复合材料的整体性能产生着至关重要的影响。
就好像一座大楼的根基,如果根基不牢固,整座大楼就会摇摇欲坠;复合材料的界面性能不佳,其整体性能也会大打折扣。
那么,复合材料的界面性能究竟包括哪些方面呢?首先是界面的结合强度。
这就好比两个人手牵手,如果握得不够紧,一用力就会分开;界面结合强度不足,在受到外力作用时,不同材料之间就容易发生分离,导致复合材料失效。
其次是界面的相容性。
不同材料在界面处能否“和谐共处”,相互融合,直接关系到复合材料的性能稳定性。
如果相容性不好,就会在界面处产生应力集中、缺陷等问题,影响材料的使用寿命。
再者是界面的传质和传热性能。
良好的传质和传热性能有助于提高复合材料在各种工况下的性能表现。
界面性能对复合材料性能的影响是多方面的。
以纤维增强复合材料为例,如果界面结合强度高,纤维能够有效地将载荷传递给基体,从而提高复合材料的强度和刚度。
相反,如果界面结合强度低,纤维就无法充分发挥其增强作用,复合材料的性能也就难以达到预期。
在耐腐蚀性方面,界面的性能也起着关键作用。
如果界面处存在缺陷或相容性问题,腐蚀性介质就容易通过界面侵入复合材料内部,导致材料腐蚀失效。
此外,界面性能还会影响复合材料的热稳定性、电性能等。
既然界面性能如此重要,那么如何对其进行优化呢?这需要从多个方面入手。
首先是材料的选择。
在设计复合材料时,要精心挑选具有良好相容性和界面结合性能的基体和增强材料。
例如,在聚合物基复合材料中,可以选择与聚合物相容性好的纤维或填料,或者对纤维表面进行预处理,以改善其与聚合物基体的结合性能。
复合材料界面改性技术研究与应用
复合材料界面改性技术研究与应用复合材料是应用广泛的一种材料,其由两种或两种以上的材料组成。
复合材料的优点在于相较于单一材料,复合材料具有更好的性能,例如强度、刚度、耐磨性、耐腐蚀性等。
然而,复合材料仍然存在一些缺陷,例如低阻尼和劣化性能等。
因此,界面改性技术被广泛研究和应用于复合材料中。
一、界面改性技术概述界面改性技术的目的是改善复合材料的性能,其中界面指的是两种不同材料的相接触的位置。
一般来说,在材料接触界面处,由于材料间的不相容性,会导致一些问题,例如界面分离、弱的化学键缺陷、材料的互相传递等。
界面改性技术可以改善这些问题,提高复合材料的性能和可靠性。
界面改性技术主要包括两种方法:物理方法和化学方法。
物理方法主要包括选用适当的协同材料、控制复合材料内部的微观结构等;化学方法主要包括表面修饰、化学键的形成、共聚反应等。
物理方法主要包括增加金属、碳纤维等的应用,来加强复合材料的强度和刚度等性能。
此外,对于聚酰亚胺等高性能材料,常使用碳纤维增强增加材料性能。
其中,金属复合材料的优点在于具有较好的热膨胀系数,能够更好地匹配碳复合材料的热膨胀系数,使得复合材料更加稳定。
化学方法则主要包括表面化学改性、交联反应等。
例如,采用一些有机化合物,如二氧化钛、氧化锌等,在复合材料表面进行化学修饰,可以使得复合材料表面具有良好的亲水性,从而提高粘接强度。
此外,交联反应的目的是通过增加分子间相互联系的数量和强度来改善界面附着性质和强度。
二、复合材料界面改性技术的应用复合材料的界面改性技术已经被应用于很多领域。
例如航空航天、汽车、建筑等。
在航空航天领域,复合材料是一个非常重要的材料。
航空航天领域的材料要求具有高强度、低密度、高抗疲劳性等特点。
因此,复合材料的应用已经推广到航空航天的许多领域之中。
在汽车领域,作为车身结构的材料型态的沐浴也日益壮大,它可以提高汽车的强度和轻量化程度。
在竞速车领域,车辆要求具有轻量化、高强度、高弹性等特性。
- 1、下载文档前请自行甄别文档内容的完整性,平台不提供额外的编辑、内容补充、找答案等附加服务。
- 2、"仅部分预览"的文档,不可在线预览部分如存在完整性等问题,可反馈申请退款(可完整预览的文档不适用该条件!)。
- 3、如文档侵犯您的权益,请联系客服反馈,我们会尽快为您处理(人工客服工作时间:9:00-18:30)。
界面及界面改性方法
界面结合强度低,则增强纤维与基体很容易分离,在材料的断面可观察到脱粘、纤维拔出、纤维应力松弛等现象,起不到增强作用;但界面结合强度太高,则增强纤维与基体之间应力无法松弛,形成脆性断裂。
在研究和设计界面时,不应只追求界面粘结而应考虑到最优化和最佳综合性能。
1、聚合物基复合材料界面
界面结合有机械粘接与润湿吸附、化学键结合等。
大多数界面为物理粘结,结合强度较低,结合力主要来自如色散力、偶极力、氢键等物理粘结力。
偶联剂与纤维的结合(化学反应或氢键)也不稳定,可能被环境(水、化学介质等)破坏。
一般在较低温度下使用,其界面可保持相对稳定。
增强剂本身一般不与基体材料反应。
聚合物基复合材料界面改性原则:
1)在聚合物基复合材料的设计中,首先应考虑如何改善增强材料与基体间的浸润性。
一般可采取延长浸渍时间,增大体系压力、降低熔体粘度以及改变增强体织物结构等措施。
2)适度的界面结合强度
3)减少复合材料中产生的残余应力
4)调节界面内应力和减缓应力集中
聚合物基体复合材料改性方法
1、颗粒增强体在热塑性聚合物基体加入两性相溶剂(增容剂),则能使液晶微纤与基体间形成结合良好的界面
2、纤维增强体复合材料界面改善
a)纤维表面偶联剂
b)涂覆界面层
c)增强体表面改性
2、金属基复合材料界面
金属基体在高温下容易与增强体发生不同程度的界面反应,金属基体多为合金材料,在冷却凝固热处理过程中还会发生元素偏聚、扩散、固溶、相变等。
金属基复合材料界面结合方式有化学结合、物理结合、扩散结合、机械结合。
总的来讲,金属基体复合材料界面以化学结合为主,有时也会出现几种界面结合方式共存。
金属基体复合材料的界面有3种类型:第一类界面平整、组分纯净,无中间相。
第二类界面不平直,由原始组分构成的凸凹的溶解扩散型界面。
第三类界面中含有尺寸在亚微米级的界面反应物。
多数金属基复合材料在制备过程中发生不同程度的界面反应。
金属基复合材料的界面控制研究方法:
1)对增强材料进行表面涂层处理在增强材料组元上预先涂层以改善增强材料与基体的浸润性,同时涂层还应起到防止发生反应的阻挡层作用。
2)选择金属元素改变基体的合金成分,造成某一元素在界面上富集形成阻挡层来控制界面反应。
尽量避免选择易参与界面反应生成脆硬界面相、造成强界面结合的合金元素
3)优化制备工艺和参数金属基体复合材料界面反应程度主要取决于制备方法和工艺参数,因此优化制备工艺和严格控制工艺参数是优化界面结构和控制界面反应的有效途径。
3、陶瓷基复合材料的界面
陶瓷基体复合材料指基体为陶瓷材料的复合材料。
增强体包括金属和陶瓷材料。
界面结合方式与金属基体复合材料基本相同,有化学结合、物理结合、机械结合和扩散结合,其中以化学结合为主,有时几种结合方式同时存在。
陶瓷基体复合材料界面控制方法
1)改变基体元素例如:在SiCPCS纤维强化玻璃陶瓷(LAS,LiO,Al2O3,SiO2)中,添加百分之几的Nb(铌)时,热处理过程中会发生反应,在界面形成数微米的NbC相,获得最佳界面,从而达到高韧化的目的。
2)增强体表面涂层在玻璃、陶瓷作为基体时,使用的涂层材料有C、BN、Si、B等多种。
防止成型过程中纤维与基体的反应,调节界面剪切破坏能力以提高剪切强度。
纤维表面双层涂层处理是最常用的方法。
其中里面的涂层以达到键接及滑移的要求,而外部涂层在较高温度下防止纤维机械性能降低。
残余应力
●高聚物复合材料的残余应力是由于树脂和纤维热膨胀系数不同而产生和固化过程
中树脂体积收缩产生化学应力。
前者影响较大。
残余应力的存在,导致材料粘结强度下降。
残余应力对材料的影响程度依赖于纤维的含量、纤维与基体的模量比和纤维的直径
●金属复合材料残余应力来源于热和力学。
设计过程要注意基体模量不能太低,膨胀
系数要相差不大
●陶瓷复合材料热膨胀系数的不同导致残余应力。
纤维的膨胀系数往往大于基体材
料。
在一定程度下达到所追求的增韧机制。
但基体和增强纤维都是脆性的,残余应力过大容易导致裂纹。