第三章弯曲模
第三章 弯曲工艺及弯曲模

回弹性的表现形式: (1) 卸载前板料的内半径与凸模的半径吻合,在卸载后增加。 (2)
卸载前弯曲中心角与凸模顶角相吻合,卸载后变化。
第三章 弯曲工艺及弯曲模
二、影响回弹的因素 1.材料的力学性能
材料的屈服点 越高,弹性模量E越小,弯曲变形的回弹也越大。 2.相对弯曲半径
第三章 弯曲工艺及弯曲模
3. 从工艺上采取措施 (1)采用热处理工艺 (2)增加校正工序
第三章 弯曲工艺及弯曲模
4. 从模具结构采取措施 (1) 补偿法
(2)校正法
第三章 弯曲工艺及弯曲模
(3) 纵向加压法
第三章 弯曲工艺及弯曲模
第四节 弯曲件的结构工艺性
定义:弯曲件的工艺性是指弯曲件的形状、尺寸、材料的选用及技术 要求等是否满足弯曲加工的工艺要求。具有良好冲压工艺性的 弯曲件,不仅能提高工件质量,减少废品率,而且能简化工艺 和模具结构,降低材料消耗。
第七节 弯曲模工作部分设计
一、凸、凹模的圆角半径及凹模的深度
第三章 弯曲工艺及弯曲模
1、凸模的圆角半径
2、凹模的圆角半径
第三章 弯曲工艺及弯曲模
二、凸凹模间隙 弯曲有色金属时 Z=tmin+ct 弯曲黑色金属时 Z=tmax+ct
第八节 凸凹模工作部分的尺寸与公差
(1)弯曲件外形尺寸的表注 当弯曲件为双向对称偏差时,凹模尺寸为
1 d Ld (L 2 Δ)0
第三章 弯曲工艺及弯曲模
当弯曲件为单向偏差时,凹模尺寸为
凸模ห้องสมุดไป่ตู้寸为
3 d Ld (L 4 Δ)0
第三章 弯曲工艺及弯曲模

3.1 弯曲变形3.2 最小相对弯曲半径3.3 弯曲件的回弹3.4 弯曲件的工艺性3.5 弯曲件的展开尺寸计算353.6弯曲力的计算3.7 弯曲模工作部分设计373.8 凸、凹模工作部分的尺寸与公差3.9 弯曲模的典型结构及弯曲模具中主要零部件制造工艺过程示例弯曲:在冲压力的作用下,把平板坯料弯折成一定角度和形状的种塑性成型工艺。
定角度和形状的一种分类:压弯、折弯、扭弯、滚弯和拉弯。
弯曲模:弯曲工艺使用的冲模。
压弯的典型形状典型的压弯工件第一节弯曲变形一、板料的弯曲过程、板料的弯曲过程在弯曲过程中,板料的弯曲半径123......n r r r r ,,,,和支点距离随凸模的下行逐渐减小,12......n l l l ,,,随凸模的下行逐渐减小而弯曲终了时,板料与凸模完全贴合凸、凹模完全贴合。
第一节弯曲变形通过网格试验观察弯曲变形特点。
二、弯曲变形的特点①弯曲件的圆角部分是弯曲变形的主要变形区弯曲变形有以下几个特点:变形区的材料外侧伸长,内侧缩短,中性层长度不变。
②弯曲变形区的应变中性层应变中性层是指在变形前后金属纤维的长度没有发生改变的那一层金属纤维。
③变形区材料厚度变薄的现象变形程度愈大,变薄现象愈严重,变薄后的厚度为。
④变形区横截面的变化变形区横断面形状尺寸发生改变称为畸变主要影响因素为板料的相1t t η=(宽板) :横断面几乎不变;变形区横断面形状尺寸发生改变称为畸变。
主要影响因素为板料的相对宽度。
3B t>(窄板) :断面变成了内宽外窄的扇形。
3B t <第一节弯曲变形应变状态应力状态三、变形区和应力应变状态εσ长度内区压应变,外区拉应变,内区压应力,外区拉应力,绝对值最大绝对值最大厚度内区拉应变,外区压应变,变形区引起压应力,由表及里递t σ变变与符号相反表面,由表及里递增窄板内区拉伸窄板θε0t σ=宽度窄板:内区拉伸,外区压缩窄板:宽板:内区压应力,0ε≈0ϕσ=宽板:外区拉应力ϕ第一节弯曲变形三、变形区和应力应变状态第二节最小相对弯曲半径设中性层半径为,弯曲中心角为,则最外层金属(半径为的ρα为R)的伸长率为δ外()()aa oo R R ραρ−−−===oo δραρ外另设中性层位置在半径为处,且弯曲后厚度保持不变,则,故有2r t ρ=+R r t =+将两式联立则有()(2)21=r t r t t rδ+−+==外将两式联立,则有2221r t t r t +++第二节最小相对弯曲半径影响最小相对弯曲半径的因素主要有以下几方面:材料的塑性及热处理状态板料的表面和侧面质量弯曲方向弯曲中心角各种材料在不同状态下的最小相对弯曲半径的数值可参见表33。
第三章 弯曲-08

式中: ——最大自由弯曲力,即自由弯曲在冲压行程结束时的弯曲力,N;
σb——材料抗拉强度,MPa; k——安全系数,一般取k=1.3; b——弯曲件宽度,mm; r——弯曲件的内弯曲半径,mm; t——板料厚度,mm。
冲压工艺与学——弯曲
2.应力状态
切向ζθ:内区受压,外区受拉。 径向ζρ :塑性弯曲时,由于变形区曲度增大,以及金属各层之间的相互 挤压的作用,从而引起变形区内的径向压应力ζρ,在板料表面ζρ= 0,由表及 里逐渐递增,至应力中性层处达到了最大值。 宽度方向ζb :对于窄板,由于宽度方向可以自由变形,因而无论是内区 还是外区ζb =0;对于宽板,因为宽度方向受到材料的制约作用,σb ≠0。内 区由于宽度方向的伸长受阻,所以σb为压应力。外区由于宽度方向的收缩受 阻,所以σb为拉应力。 结论:窄板弯曲时的应力状态是平面的,宽板则是立体的。
内移结果:外层拉伸变薄区范围逐步扩大,内层压缩增厚区范 围不断减小,外层的减薄量会大于内层增厚量,从而使弯曲区板料 厚度变薄。 规律:r/t愈小,变形程度愈大,系数ξ就愈小,弯曲区的变薄 现象也愈严重(见表3-1) 。 影响:弯曲时的厚度变薄会影响零件的质量。
四、板料长度的增加
一般弯曲件,其宽度方向尺寸b比厚度方向尺寸大得多,所以弯曲前 后的板料宽度b可近似地认为是不变的。 由于板料弯曲时中性层位置向内移动,出现了板厚的减薄,根据体积 不变条件,减薄的结果使板料长度必然增加——相对弯曲半径r/t愈小,减 薄量愈大,板料长度的增加量也愈大。 对于r/t值较小的弯曲件:在计算弯曲件的毛坯长度时,必须考虑弯曲 后的板料增长,并通过多次试验,才能得出合理的毛坯展开尺寸。有关毛
冲压工艺与学——弯曲
在r/t≤4的情况下弯曲,由试验测定系数ξ<1(见表3-1),因此,由 r 。 1 / 2 t 式(3-3)可知,当ξ<1时,应变中性层位置ρ0将小于 而 r 1 / 2 t 为塑性弯曲时的中心位置, 0 r 1 / 2 t 则表示了塑性弯曲 时应变中性层位置向内移动。 由表3-1看出:系数ξ值随r/t大小变化,r/t愈小,ξ值也愈小,应 变中性层的内移量就愈大。——凸模下行,变形程度不断增加,应 变中性层位置逐步向内移动,变形量愈大,中性层的内移量也愈大。 结论:由应变中性层内移可知,应变中性层处的纤维在弯曲前 期的变形是切向压缩,而弯曲后期必然是伸长变形,才能补偿弯曲 前期的纤维缩短,使其切向应变为零。而弯曲后期的纤维伸长变形, 一般来说,仅发生在应力中性层的外层纤维上。由此可见,应力中 性层在塑性弯曲时也是从板料中间向内层移动的,且内移量比应变 中性层还大。
弯曲PPT课件

缩之间存在一个既不伸长、也不压缩的纤维层,称应变中性
层。而毛坯截面上的应力,在外层的拉应力过渡到内层压应
力时,发生突然变化的或应力不连续的纤维层,称应力中性
层。应变中性层用于计算弯曲件毛坯长度计算;应力中性层
用于计算弯曲应力和应力分析。弹性弯曲时,应变中性层与
应力中性层相重合,其应变和应力为零,中性层位置一定通
弯曲:将板料、型材、管材或棒料等按设计要求弯 成一定的角度和一定的曲率,形成所需形状零件的 冲压工序。 弯曲毛坯的种类:板料、棒料、型材、管材
本章与第2章相比:
准确工艺计算难,模具动作复杂、结构设计规律性不强。
.
2
弯 曲 成 形 典 型 零 件
.
3
生活中的弯曲件
.
4
压弯的典型形状: 典型压弯工件:
二、中性层位置的内移(续)
金属体积不变条件,得
tlbR 2r22 b 31
塑性变形后,弯曲中性层长度不变,得
l 0 3 2
联解, Rr因 t
0 r t 2 t
二、中性层位置的内移(续)
0rt2tr1 2t
可以看出,塑性弯曲时应变中性层位置与r/t、系数ξ的数 值有关,而弯曲时,随着凸模下行,相对弯曲半径r/t和系数ξ 是不断变化的,所以板料塑性弯曲时的应变中性层位置,也 在逐渐改变、逐步移动。
变形程度愈大,变薄现象愈严重。 弯曲时的厚度变薄会影响零件的质量。因此,在拟定弯 曲工艺和模具设计时,必须采取有效措施,才能弯制出合乎 要求的零件。
.
22
§3.1 板料的弯曲现象及其原因
四、板料长度的增加
根据体积不变条件,弯曲区板料厚度的减薄的结果使板 料长度l必然增加。相对弯曲半径r/t愈小,减薄量愈大,板 料长度的增加量也愈大。因此,对于r/t值较小的弯曲件, 在计算弯曲件的毛坯长度时,必须考虑弯曲后板料增长, 并通过多次弯曲试验,才能得出合理的毛坯展开尺寸。
弯曲工艺和弯曲模具设计复习题答案

第三章弯曲工艺及弯曲模具设计复习题答案一、填空题1 、将板料、型材、管材或棒料等弯成一定角度、一定曲率 . 形成一定形状的零件的冲压方法称为弯曲。
2 、弯曲变形区内应变等于零的金属层称为应变中性层。
3 、窄板弯曲后起横截面呈扇形状。
窄板弯曲时的应变状态是立体的.而应力状态是平面。
4 、弯曲终了时. 变形区内圆弧部分所对的圆心角称为弯曲中心角。
5 、弯曲时.板料的最外层纤维濒于拉裂时的弯曲半径称为最小弯曲半径。
6 、弯曲时.用相对弯曲半径表示板料弯曲变形程度.不致使材料破坏的弯曲极限半径称最小弯曲半径。
7、最小弯曲半径的影响因素有材料的力学性能、弯曲线方向、材料的热处理状况、弯曲中心角。
8 、材料的塑性越好.塑性变形的稳定性越强.许可的最小弯曲半径就越小。
9 、板料表面和侧面的质量差时.容易造成应力集中并降低塑性变形的稳定性 .使材料过早破坏。
对于冲裁或剪切坯料.若未经退火.由于切断面存在冷变形硬化层.就会使材料塑性降低 .在上述情况下均应选用较大的弯曲半径。
轧制钢板具有纤维组织. 顺纤维方向的塑性指标高于垂直于纤维方向的塑性指标。
10 、为了提高弯曲极限变形程度.对于经冷变形硬化的材料.可采用热处理以恢复塑性。
11 、为了提高弯曲极限变形程度.对于侧面毛刺大的工件.应先去毛刺;当毛刺较小时.也可以使有毛刺的一面处于弯曲受压的内缘(或朝向弯曲凸模) .以免产生应力集中而开裂。
12 、为了提高弯曲极限变形程度.对于厚料.如果结构允许.可以采用先在弯角内侧开槽后.再弯曲的工艺.如果结构不允许.则采用加热弯曲或拉弯的工艺。
13 、在弯曲变形区内.内层纤维切向受压而缩短应变.外层纤维切向受受拉而伸长应变.而中性层则保持不变。
14 、板料塑性弯曲的变形特点是:( 1 )中性层内移( 2 )变形区板料的厚度变薄( 3 )变形区板料长度增加( 4 )对于细长的板料.纵向产生翘曲.对于窄板.剖面产生畸变。
15 、弯曲时.当外载荷去除后.塑性变形保留下来 .而弹性变形会完全消失 .使弯曲件的形状和尺寸发生变化而与模具尺才不一致 .这种现象叫回弹。
第三章:弯曲工艺与弯曲模具设计

校正弯曲时,回弹角修正量: K90
不是90°的角按下式修正: x ( / 90)90
➢ 当r/t < 8~10时,要分别计算弯曲半径和弯曲角的回弹值,再修正。
弯曲板料时
凸模的圆角半径: rp 1/(1/ r) (3 s / Et)
凸模圆弧所对中心角: p
(r
/ rp )
弯曲件的滑移
6. 最小弯曲半径 rmin
❖ r/t 小 —— 变形程度大 —— 弯曲破坏。 影响最小弯曲半径的因素:
❖ 材料的机械性能:好塑性(塑稳)、退火处理、热弯、开槽减薄 ❖ 方向性:折弯线垂直纤维方向:伸长变形能力强
❖ 板宽:B/t 小(< 3) ❖ 弯曲角:小, 直边有切向形变。 ❖ 板料表面质量和断面质量:差处易应力集中发生破坏。 ❖ 板料厚度:t小 —— 切向应变小 —— 开裂小。
弯曲件的工序安排
1. 工序安排的一般原则 ➢ 先弯外角后弯内角,后次弯曲不能影响前一次弯曲变形,前次弯曲应考 虑后次弯曲有合适的定位基准。 ➢ 当有多种方案时,要进行比较,进行优化。
2. 工序安排的一般方法 ➢ 形状简单的弯曲件可一次弯曲成形。如V形、U形、Z形。 ➢ 形状复杂的弯曲件可用两次或多次压弯成形。
➢ r/t值
小r/t: 加厚筋边或 减小 r; 其值大时拉弯
(在同条件下,r/t越小,则总变形量就越大,回弹就越小。) 工艺处理
➢ 弯曲中心角
(α越大,变形区长度越长,参与变形的区域越大,回弹越多。)
小
➢ 弯曲方式与校正力大小
(自由弯曲回弹大,校正弯曲回弹小,校正力越大回弹越小。)
➢ 工件形状
(工件形状越复杂,回弹就越少。)
弹-塑性变形: 塑性变形:
L1-L2 ,r1-r2 超过屈服极限,
第3章 弯曲工艺与弯曲模具
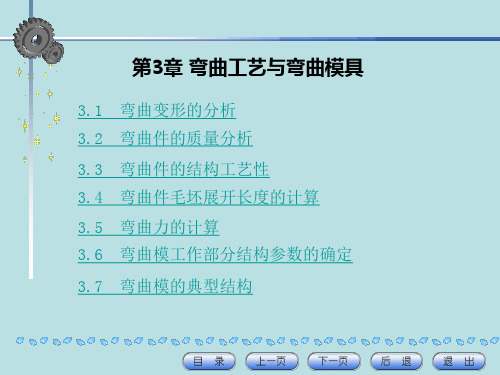
总之影响最小弯曲半径的主要因素如下:
⒈ 材料的机械性能;
⒉ 板材纤维的方向性;
⒊ 弯曲件的宽度; ⒋ 板材的表面质量和剪切断面质量;
⒌ 弯曲角;
⒍ 板材的厚度。 最小弯曲半径可按表3-1选取
表3-1 最小弯曲半径rmi
3.2.2、弯曲时的回弹及控制回弹的措施 1、弯曲回弹现象 弯曲回弹现象产生于弯曲变形结束后的卸载过程,是由其内部产生 的弹性回复力矩造成的。弯曲件卸载后的回弹,表现为弯曲件的弯曲 半径和弯曲角的变化,如图3-6所示。
(a )
(b ) (c) 图3-25 防止尖角处撕裂的措施
0 绪论 一、冲压概念
图3-26所示的零件,根据需要设置了工艺孔、槽及定位孔。图(a) 所示工件弯曲后很难达到理想的直角,甚至在弯曲过程中变宽、开 裂。如果在弯曲前加工出工艺缺口(M×N),则可以得到理想的弯 曲件。图(b)所示的工件,在弯曲处预先冲制了工艺孔,效果与 图(a)相同。图(c)所示的工件,要经过多次弯曲,图中的D是 定位工艺孔,目的是作为多次弯曲的定位基准,虽然经多次弯曲, 该零件仍保持了对称性和尺寸精度,
0 绪论 一、冲压概念
凸模下行,减小到r/t>200时,板料处于线形弹塑性状态,
即板料中心几附近区域为弹性变形,其他部分为塑性变形, 弯曲进行至r/t值大约在(200>r/t>5)时,板料进入线形全塑
性弯曲状态。
当其进一步减小到r/t3~5时,则为立体塑性弯曲,此即模 具弯曲最终状态。
• 窄板(b/t3)弯曲时,宽度 方向可以自由变形,故其应 力b0,内外层的应变状态 是立体的,应力状态是平面 的。 • 宽板(b/t>3)弯曲时,由于 宽度方向材料不能自由变形 (宽度基本不变),即
第三章 弯曲

第三章 弯 曲
弯曲:将板料、型材、管材或棒料等按设计要求弯 成一定的角度和一定的曲率,形成所需形状零件的 冲压工序。 弯曲毛坯的种类:板料、棒料、型材、管材
本章与第2章相比:
准确工艺计算难,模具动作复杂、结构设计规律性不强。
弯 曲 成 形 典 型 零 件
生活中的弯曲件
压弯的典型形状: 典型压弯工件:
内层切向应力
内 2 3 n 1 B n 1 1 - ln 0 n 1 - - ln R 0 n 1 - - ln 0 n 3 - 1 9
§3.3 宽板弯曲时的应力和弯矩的计算
二、按宽板弯曲的平面应变状态计算变形区的应力数值 外层宽度方向上的主应力
曲
8、9-螺钉
模
10-定位板
用模具成形的弯曲件之一
用模具成形的弯曲件之二
连续弯曲模拟 闹钟双铃提环弯曲模模拟 阶梯件弯曲模 双摆块弯曲模 摆块式形件弯曲模 圆筒形件一次弯曲 自动卸料机构的摆块弯曲模
§3.1 板料的弯曲现象及其原因
(a)
(b)
(c)
(d)
在弯曲过程中,板料的弯曲半径r1、r2…rn与支点距离l1、 l2…ln随凸模下行逐渐减小,而在弯曲终了时,板料与凸、凹
第三章 弯 曲
§3.1 板料的弯曲现象及其原因 §3.2 窄板弯曲和宽板弯曲时的
应力应变状态分析 §3.3 宽板弯曲时的应力和弯矩的计算 §3.4 弯曲力计算和设备选择 §3.5 弯曲件毛坯长度计算 §3.6 最小相对弯曲半径rmin/ t的确定 §3.7 弯曲回弹 §3.8 弯曲模工作部分的尺寸计算
§3.1 板料的弯曲现象及其原因
五、板料横截面的畸变、翘曲和拉裂(畸变)
窄板(B/t≤3) 宽板(B/t>3) 弯曲变形区的横截面变化情况
- 1、下载文档前请自行甄别文档内容的完整性,平台不提供额外的编辑、内容补充、找答案等附加服务。
- 2、"仅部分预览"的文档,不可在线预览部分如存在完整性等问题,可反馈申请退款(可完整预览的文档不适用该条件!)。
- 3、如文档侵犯您的权益,请联系客服反馈,我们会尽快为您处理(人工客服工作时间:9:00-18:30)。
1、影响回弹量的因素
⑴材料的力学性能:回弹角的大小与材料的屈服点σ s成正比,与 弹性模量E成反比。 ⑵材料的相对弯曲半径R/t:当其他条件相同时,R/t 值越小,则 Δ θ /θ 与Δ ρ /ρ 也越小。 ⑶弯曲工件的形状:一般U形工件比V形工件回弹要小。回弹量与 工件弯曲半径也有关,当比值是R/t<0.2~0.3时,则回弹角可能 为零,甚至达到负值。 ⑷模具间隙:U形弯曲模的凸、凹模单边间隙Z/2越大,则回弹越 大; Z/2<t时,可能产生回弹。 ⑸校正力:增加校正力可减小回弹量。板料弯曲时,弯曲部位受 到拉伸或压缩应力与板厚方向的压应力的合成,可使材料内的实 际应力达到屈服点,可将板料弯曲的弹性变形变为塑性变形而减 少回弹。
用于冷冲压的材料大都属于轧制板材, 轧制的板材在弯曲时各方向的性能是有差 别的,纤维纹的方向就是轧制的方向。对 于卷料或长的板料,纤维线与长边方向平 行。作为弯曲用的板料,材料沿纤维线方 向塑性较好,所以弯曲线最好与纤维线垂 直。这样,弯曲时不容易开裂。如下图:
如果在同一零件上具有不同方向的 弯曲,在考虑弯曲件排样经济性的同时, 应尽可能使弯曲线与纤维方向夹角α不 小于30°。如上图。
二、弯曲零件的工艺性
1、弯曲件的圆角半径 材料产生塑 性变形才能形成所需的形状,为了 实现弯曲件的形状,弯曲圆角半径 最大值是没有限制的。例如:可以 将0.3mm厚的铁板卷成ф 300mm的 圆桶,只需要计算或试验出其回弹 量,就可制出所需的形状。 板料弯曲的最小半径是有限制的, 如果弯曲半径过小,弯曲时外层材 料拉伸变形量过大,而使拉应力达 到或超过抗拉强度σ b,则板料外层 将出现断裂,至使工件报废。因此, 板料弯曲存在一个最小圆角半径允 许值,最小圆角半径值查表3—1选 用。
5、孔与弯曲处的最小距离
工件在弯曲线附近有预先冲出的孔,在弯曲后由于弯曲时材料的流动, 会使原有的孔变形。为了避免此情况,必须使这些孔分布在变形区以 外的部位。如图3-9,设孔的边缘至弯曲半径R中心的距离为l,则应 满足以下关系: 当t<2mm时,L≥t。当t>2mm时,L≥2t。 如工件不能满足上述要求时,可采用图3-10所示的方法,以保证孔 形的正确性。
为了防止材料在弯曲处因受力不均匀而产 生裂纹、角部畸变等缺陷,应预先在工件 上设置弯曲工艺所要求的孔(工艺孔)、 槽(工艺槽)或缺口(工艺缺口)。如图a, 压弯后难以形成理想的直角,甚至将产生 裂纹或使支架在H处变宽,若如图所示在该 处弯曲前加工出M×N的缺口,则能得到较 好的弯曲成形。图b所示为在弯曲处K预冲 工艺孔可以防止偏移,得到正确的形状和 尺寸。 对于需经过多次弯曲才能成形的工件, 如图c所示,就应增加定位工艺孔
3、弯曲时压力机的压力
弯曲时压力机的压力是自由弯曲力和校正弯曲力之和。 F―压力机的压力。 即F≥ F1+F2 校正弯曲时,由于校正弯曲力比自由弯曲力大得多, 故F1可以忽略,而F2的大小取决于压力机的调整。
五、弯曲件的回弹
回弹:压弯过程除材料的塑性变形外,还存在弯曲部 位的弹性变形,所以压弯后零件形状与模具的形状并 不完全一致。 回弹的大小通常用角度回弹量Δ θ 和曲率回弹量Δ ρ 来表示。角度回弹是指模具在闭合状态时工件弯曲角 θ 与从模具中取出后工件的实际角度θ 0之差,即 Δ θ =θ 0-θ ;曲率回弹量是指模具处于闭合状态时压 在模具中工件的曲率半径ρ 与从模具中取出后工件的 实际曲率半径ρ 0之差,即Δ ρ =ρ 0-ρ 。
弯曲有色金属时,间隙值: Z/2=tmin+nt 弯曲黑色金属时,间隙值: Z/2=t(1+n) 式中:Z/2-凸、凹模间的单面间隙; tmin -材料的最小厚度; t-材料的公称厚度; n-因数,其与弯曲件高度H和弯曲线 长度B有关,见表3-6。
2、凸、凹模工件部位尺寸
由于弯曲件尺寸的标注和尺寸的允许偏 差不同,故凸、凹模工作部位尺寸的计 算方法也不同。 对于要求外形有正确尺寸的工件,其模 具的尺寸如右上图所示。计算公式如下: 1 凹 零件尺寸标注双向偏差 B 凹 B 2 时,凹模尺寸为: 0 凹 零件尺寸标注单向偏差 3 时,凹模尺寸为: B 凹 B
第三章
第一节
弯曲模
弯曲模设计基础
第二节
弯曲模设计示范
第一节 弯曲模设计基础
一、弯曲变形分析 弯曲是使材料产生塑性变形、形成有一定 角度形状零件的冲压工序。弯曲工序可以 用模具在普通压力机上进行, 也可以在专用的弯曲 机或弯曲设备上进行。
1、弯曲过程分析
弯曲变形有很多种形式,如图所示的 为V形弯曲,被弯曲的材料是平面板料。 当模具上受到压力作用时,首先达到图3 -1a所示的位置,板料与凸模有三点接触。 此后凸模下行,弯曲区缩小,未成形件的 两边逐步贴向凹模工作表面,直到弯曲件 与凸模和凹模全部贴紧,如图3-1b所示。 凸模和凹模分开后,工件就弯成具有φ 角 的弯曲工件了。成形件的角度往往稍大于 φ 角,这种现象称为回弹,回弹的角度可 以估算,并可采取措施消除回弹。 弯曲分自由弯曲和校正弯曲。所谓自 由弯曲是指当弯曲终了时,凸模、毛坯和 凹模三者吻合后凸模不再下压。而校正弯 曲是指在上述基础上凸模再往下压,对弯 曲件起校正作用,从而使工件产生进一步 的塑性变形。
⑵校正法
校正法是在模具结构上采取措施,让校正压力集 中在弯角处,使其产生一定塑性变形,克服回弹。 图3-14a、b所示为弯曲校正力集中作用于弯曲 圆角处。
六、弯曲模工作部分尺寸计算
1、弯曲时凸模与凹模之间 的间隙
弯曲V形工件时,凸、凹 模间隙是靠调整压力机闭合高 度来控制的,不需要在模具结 构上确定间隙。U形工件弯曲, 则必须选择适当的间隙。间隙 的大小对于工件质量和弯曲力 有很大影响。间隙越小,弯曲 力越大。间隙过小,会使工件 壁变薄,并降低凹模寿命。间 隙过大,则回弹较大,还会降 低工件精度。 U形工件弯曲的凸、凹模 间隙,根据材料的种类、厚度 以及弯曲件的高度和宽度(即 弯曲线的长度)而定。
3、最小弯曲高度
在进行直角弯曲时,如果弯曲的直立部分过小,将产 生不规则变形,或称为稳定性不好,如右图b所示。为了 避免这种情况,应当如图a, 使直立部分的高度H>2.5t。当H<2.5t时, 则应在弯曲部位加工出槽, 使之便于弯曲,或加大此 处的弯边高度H,在弯曲后 再截去加高的部分。
4、工艺孔、槽及缺口
第二节 弯曲模设计示范
双向弯曲模
零件名称:铰支板 生产批量:中批量 材料:10钢,厚1.2mm 零件简图:如图3-26所示
1、弯曲工艺与模具结构
工件的冲压由落料和弯曲两道工序组成。(在此只介绍弯曲模的设计) 本工件的弯曲工艺可分为左、右两部分;左边是U形弯曲,右边是Z形弯曲。 若用两套弯曲模分别完成左、右两部分的弯曲,将增加模具费用。 左边的U形弯曲模具结构简单。右边的Z形弯曲模具上、下方向的运动 不能实现,需利用斜楔产生水平方向的运动来完成右边Z形弯曲。模具结构 如图3-27所示。
(冲压行程结束,尚未进行校正弯曲时的压力)(N);
B―弯曲件宽度(mm ); t―弯曲件材料厚度(mm); R―弯曲内半径(mm); σ b―材料抗拉强度(MPa); K―安全因数,一般取K=1.3。
2、校正弯曲的弯曲力计算
F2=qA 式中F2 ―校正力; q―单位校正力(MPa)见表3-3; A―工件被校正部分的投影面积(mm2)。
2、回弹量的确定
由于影响回弹数值的因素很多,而且各因素往往又相 互影响,故难以进行精确的计算或分析。一般情况下, 设计模具时对回弹量的确定大多按照经验数值,或计 算后在实际试模中再进行修正。 只有当弯曲工件的圆角半径R≥(5~8)t时,计算才 近似正确。当要求工件的弯曲圆角半径为R时,则可根 据材料的有关参数,用以下公式计算回弹补偿时弯曲 凸模的圆角半径R凸。 R R R 板材弯曲用: 凸 s R 棒材弯曲用 R凸 R
⑵凹模圆角半径 工件在压弯过
Hale Waihona Puke 程中,凸模将工件压入凹模而成形, 凹模口部的圆角半径R凹对于弯曲 力和零件质量都有明显的影响。凹 模圆角半径R凹的大小与材料进入凹 模的深度、弯边高度和材料厚度有 关(见左下图)。在一般情况下: R凹=(2~6)t 在实际应用中也可根据制件的 弯边高度H和弯曲深度L以及材料厚 度t等因素,按表3-7选取R凹。 对于校正弯曲,如图3-18c所示, 图中凹模M值可根据材料厚度在表3 -8中选取。
6、冲裁毛刺与弯曲方向
弯曲件的毛坯往往是经冲裁落料而成的。其冲裁 的断面一面是光亮的,另一面是有刺的。弯曲件 尽量使有毛刺的一面作为弯曲件的内侧,如图3 -11a。当弯曲方向必须将毛刺面至于外侧时, 应尽量加大弯曲半径,如图3-11b所示。
三、弯曲件展开长度的确定
当板料弯曲变形时,在弹性 阶段中性层位于板厚的中间。冲 压工件的弯曲变形主要是塑性变 形,其中性层的位置往往向弯曲 的内侧偏移。如右图所示,此时 中性层半径的大小可按式:
当中性层半径确定后,即 可按照几何方法计算中性 层展开长度,进而计算出 板料的展开长度。由于材 料的性能、弯曲方法不同, 中性层的位置将受到影响。
ρ =R+Kt计算。
式中ρ ―中性层半径(mm) R ―弯曲内半径(mm) K―中性层位置因数表3-2 t―材料厚度(mm)。
四、弯曲力计算
弯曲力:工件完成预定弯曲时需要压力机所施加的压力。 弯曲力不仅与材料品种、材料厚度、弯曲几何参数有关, 还同设计弯曲模所确定的凸、凹模间隙大小等因数有关。 1、自由弯曲的弯曲力计算 V形弯曲件的计算F1=(0.6KBt² σ b)÷(R+t) U形弯曲件的计算F1=(0.7KBt² σ b)÷(R+t) 式中F1―自由弯曲力