弯曲模设计
模具设计与制造第6章弯曲工艺与模具设计

06
总结与展望
弯曲工艺与模具设计的现状与挑战
现状
随着制造业的快速发展,弯曲工艺与模具设计在产品制造中占据重要地位。目前,弯曲工艺与模具设 计已经取得了长足进步,能够满足多种复杂形状的加工需求。
挑战
然而,在弯曲工艺与模具设计过程中,仍存在一些挑战,如高精度控制、复杂曲面加工、高效自动化 等方面的问题。
未来发展方向与技术前沿
柔性制造技术
随着个性化需求的增加,柔性制造技术将成为未 来发展的重点。通过柔性制造技术,可以实现快 速、高效、个性化的产品制造,提高生产效率和 降低成本。
增材制造技术
增材制造技术是一种基于数字模型的快速成型技 术,能够实现复杂形状的高精度加工。未来,增 材制造技术有望在弯曲工艺与模具设计中发挥更 大的作用。
模具材料的选择蚀性等。
常用材料
碳素工具钢、合金工具钢、硬质合金、铸铁等。
材料处理
热处理、表面处理等。
模具设计的流程与方法
设计流程
明确设计任务→收集设计资料→设计 出图→审查→修改。
设计方法
经验设计法、解析设计法、计算机辅 助设计法等。
04
弯曲工艺与模具设计的关系
THANK YOU
模具设计对弯曲工艺的影响
模具结构
模具的结构对弯曲工艺的实施具 有重要影响,合理的模具结构可 以提高弯曲效率并降低不良品率。
模具材料
模具材料的选取直接影响弯曲工艺 的效果,选用高强度、耐磨和耐热 的材料可以提高模具的使用寿命和 弯曲质量。
冷却系统
模具中的冷却系统对于控制弯曲过 程中的温度至关重要,合理的冷却 系统设计可以减少热应力,提高产 品质量。
02
弯曲工艺的基本原理
弯曲变形的过程与特点
弯曲模设计

弯曲模设计一.凸模圆角半径当弯曲件的相对弯曲半径r / t 较小时,取凸模圆角半径等于或略小于工件内侧的圆角半径r ,但不能小于材料所允许的最小弯曲半径r min 。
若弯曲件的r / t 小于最小相对弯曲半径,则应取凸模圆角半径r t > r min ,然后增加一道整形工序,使整形模的凸模圆角半径r t = r 。
当弯曲件的相对弯曲半径r / t 较大(r / t > 10 ),精度要求较高时,必须考虑回弹的影响,根据回弹值的大小对凸模圆角半径进行修正。
二.凹模圆角半径凹模入口处圆角半径r a 的大小对弯曲力以及弯曲件的质量均有影响,过小的凹模圆角半径会使弯矩的弯曲力臂减小,毛坯沿凹模圆角滑入时的阻力增大,弯曲力增加,并易使工件表面擦伤甚至出现压痕。
在生产中,通常根据材料的厚度选取凹模圆角半径:当t ≤ 2 mm ,r a = (3 ~ 6) tt =2 ~ 4 mm ,r a = (2 ~ 3) tt >4 mm ,r a = 2 t对于V 形弯曲件凹模,其底部圆角半径可依据弯曲变形区坯料变薄的特点取r ' a = (0.6 ~ 0.8)( r t + t) 或者开退刀槽。
三. 弯曲凹模深度凹模深度要适当,若过小则弯曲件两端自由部分太长,工件回弹大,不平直;若深度过大则凹模增高,多耗模具材料并需要较大的压力机工作行程。
图20 弯曲模工作部分尺寸对于V 形弯曲件,凹模深度及底部最小厚度如图20a 所示,数值查表2 。
表2 弯曲V 形件的凹模深度及底部最小厚度值(mm)对于 U 形弯曲件,若直边高度不大或要求两边平直,则凹模深度应大于工件的深度,如图 20b 所示,图中 h 0 查表 3 。
如果弯曲件直边较长,而且对平直度要求不高,凹模深度可以小于工件的高度,见图 20c ,凹模深度 l 0 值查表 4。
表 3 弯曲 U 形件凹模 的 h 0 值 (mm) 板料厚度 t≤ 1 1~2 2~3 3~4 4~5 5~6 6~7 7~8 8~10 h 03456810 15 20 25表 4 弯曲 U 形件的 凹模深度 l 0 (mm)四. 弯曲 凸 、凹模的间隙V 形件弯曲 时, 凸 、凹模的间隙是*调整压力机的闭合高度来控制的。
弯曲模具设计(带全套cad图)

模具课程设计说明书——弯曲模课程设计学校:学院:专业:姓名:学号:指导教师:一、零件图二、工艺设计1.弯曲工序安排原则工序安排的原则应有利于坯件在模具中的定位;工人操作安全、方便;生产率高和废品率最低等。
弯曲工艺顺序应遵循的原则为:①先弯曲外角,后弯曲内角。
②前道工序弯曲变形必须有利于后续工序的可靠定位;并为后续工序的定位做好准备。
③后续工序的弯曲变形不能影响前面工序已成形形状和尺寸精度。
④小型复杂件宜采用工序集中的工艺,大型件宜采用工序分散的工艺。
⑤精度要求高的部位的弯曲宜采用单独工序弯曲,以便模具的调整与修正。
制订工艺方案时应进行多方案比较。
2.形状简单的弯曲件如V形、U形、Z形件等,可采用一次弯曲成形。
3.弯曲件展开尺寸计算。
(1)中性层位置的确定弯曲中性层位置并不是在材料厚度的中间位置,其位置与弯曲变形量大小有关,应按下式确定:P=r+kt式中 P----弯曲中性层的曲率半径;r----弯曲件内层的弯曲半径;t----材料厚度;k----中性层位移系数,板料可有表3-9查得,圆棒料由表3-10查得。
(2)弯曲件展开尺寸计算计算步骤:1)将标注尺寸转换成计算尺寸即将工件直线部分与圆弧部分分开标注,2)计算圆弧部分中性层曲率半径及弧长中性层曲率半径为P=r+kt,则圆弧部分弧长为: s=Pa式中 a----圆弧对应的中心角,以弧度表示。
3)计算总展开长度L=L1+L2+SL=∑L直+∑S弧4.回弹弯曲成形是一种塑性变形工艺。
回弹的表现形式:1)弯曲回弹会使工件的圆角半径增大,即r2>rp,则回弹量可表示为△r=r2-rp2) 弯曲回弹会使弯曲件的弯曲中心角增大,即a>ap.则回弹量可表示为△a=a-ap影响弯曲回弹的因素:1.材料的力学性能。
2. 材料的相对弯曲半径r/t。
3. 弯曲制件的形状。
4. 模具间隙。
5. 校正程度。
弯曲板件时,凸模圆角半径和中心角可按下式计算:Rp=r/(1+3Asr/Et)ap=ra/rp式中 r----工件的圆角半径;Rp----凸模的圆角半径;a----工件的圆角半径r对弧长的中心角;ap----凸模的圆角半径rp所对弧长的中心角;t----毛坯的厚度;E----弯曲材料的弹性模量;A----弯曲材料的屈服点减小回弹的措施:1)在弯曲件的产品设计时①弯曲件结构设计时考虑减少回弹,在弯曲部位增加压筋连接带等结构。
弯曲模具设计及计算

l2
B
l1 L (a) L (b)
图3-31 弯曲件毛坯长度计算
图3-31(a)所示弯曲件,毛坯长度为: L= L1+L2 + A = L1+L2+pa(r+kt)/180° (3 –2) 式中 L——弯曲件毛坯长度(mm); L1、L2——弯曲件直边部分长度(mm); A——弯曲变形区中性层弧长(mm); a——弯曲中心角; r——弯曲件内圆角半径(mm); k——中性层偏移量系数; t——弯曲件材料厚度(mm)。
3.4 弯曲模具设计及计算
3).铰链式弯曲件毛坯长度计算 铰链式弯曲件通常采用凸模对毛坯一端施加压力进行卷 圆弯曲成形,其变形区外表面与模具工作面接触,变形后 材料厚度不是变薄而是增厚,即中性层位置由板料中心向 外侧偏移。
R
r
R
r
1
1 2
(a)
(b)
铰链式弯曲件的常见形式如图3-32所示,毛坯展开长度的计 算方法为:
(1) 对于(a)图 (2) 对于(b)图 L = L1 +π(r + k t) a /180° L = L1 + L2 +π( r + k t ) a / 10° (3 –5) (3 –6)
图3-32 铰链式弯曲件的形式
式中 k —— 中性层偏移量系数。 4).圆杆弯曲件毛坯长度计算 公式与r≥0.5t毛坯长度计算公式相同,中性层偏移系数见表3-
3.4 弯曲模具设计及计算
3.4.3 弯曲件的回弹
r
p
3.4 弯曲模具设计及计算
1毛坯长度计算公式 1).圆角半径r≥0.5t的弯曲件毛坯长度计算 弯曲件圆角半径r≥ 0.5t时, 由于圆角半径较大, 弯曲变形区料厚变薄不严重,断面畸变较少,可 以按毛坯长度等于中性层展开长度的原则计算毛 坯长度。
3弯曲模具设计实例(PPT)
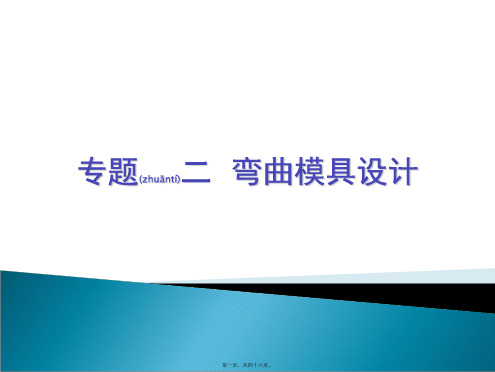
第二页,共四十六页。
2.1.1 弯曲变形过程分析 1. 弯曲变形过程:弯曲变形的含义、变形过程三阶段
、弯曲回弹、自由弯曲、矫正(jiǎozhèng)弯曲。 2. 弯曲变性特点:网格法、中性层 2.1.2 弯曲件质量分析
弯裂、回弹、偏移等
第三页,共四十六页。
2.1.3 弯曲件的工艺性:指弯曲件的结构形状、尺寸 、精度、材料及技术要求(yāoqiú)是否符合弯曲加工的工 艺要求(yāoqiú)。
第十九页,共四十六页。
2.2.1 弯曲模典型结构 模具设计本卷须知:a. 准确、可靠的定位,防止弯
曲中偏移;b. 弯曲结束(jiéshù)时能得到校正力;c. 成形后能方便、平安地取出;d. 考虑磨损,模具 留有修模余量。 弯曲模具分类:单工序模、连续弯曲模、复合弯曲模 和通用弯曲模。
第二十页,共四十六页。
第十页,共四十六页。
5. 增加工艺缺口、槽和工艺孔 a. 为提高精度,对于弯曲时圆角变形区侧面可以
产生畸变(jībiàn)的弯曲件,可以预先在折弯线的两端切 出工艺缺口或槽,以防止畸变(jībiàn)对弯曲件宽度尺寸 的影响。
第十一页,共四十六页。
b. 当工件局部边缘局部弯曲时,为防止弯曲局部受力 不均匀而产生变形和裂纹(liè wén),应于线切槽或冲工艺孔 。
弯曲半径较小、材料强度较大的弯曲件时,必须对
弯曲力进行计算。
a. 自由弯曲时的弯曲力
V形弯曲件 F自=0.6Kbt²σb/(r+t)
U形弯曲件 F自=0.7Kbt²σb/(r+t)
其中:b-弯曲件宽度;t-弯曲件厚度;r-内圆
角弯曲半径;
σb-弯曲材第十七料页,共四的十六页抗。 拉强度〔Mpa〕;K-
精选弯曲工艺与弯曲模设计
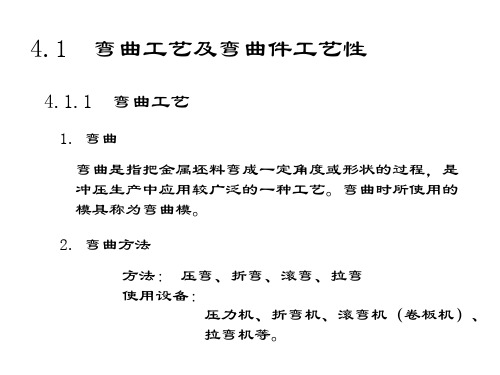
3.弯曲件的直边高度
直边高度H过小,那么直边在弯曲模上支承的长度也过小,不易形成足够的弯矩,弯曲件的形状难以控制。
如果
可加大直边高度,待弯曲成形后,再将直边的高出部分切除。
当弯曲边带有斜度时,应保证
图 4-9 直边高度要求
4.弯曲件孔边距
图 4-10 弯曲件孔边距
图 4-11 防止孔变形的措施
(5)弯曲校正力。 弯曲校正力愈大,塑性变形程度愈大,回弹愈小。
3.减小回弹的措施
1)补偿法
预先估算或试验出工件弯曲后的回弹量,在设计模具时,使弯曲件的变形量超过原设计量,工件回弹后就得到所需要的正确形状。
图 4-30 补偿法示意图
2)校正法
图 4-31 校正法示意图
校正压力集中施加在弯曲变形区,使其塑性变形成分增加,弹性变形成分减小,从而使回弹量减小。
2.弹-塑性弯曲阶段
促使材料塑性变形的弯曲力矩是逐渐增大的。由于弯曲力臂l逐渐减小,因此弯曲力处于不断上升的趋势。凸模继续下行,板料与凸模V形斜面接触后被后向弯曲。
后向弯曲
3. 塑性弯曲阶段
当凸模到达下止点时,毛坯被紧紧地压在凸模与凹模之间,使毛坯内侧弯曲半径与凸模的弯曲半径吻合,完成弯曲过程,变形由弹—塑性弯曲过渡到塑性弯曲。
2.工序安排方法
(1)简单形状一次弯曲成形
图 4-36 一道工序弯曲成形
(2)复杂形状,一般采用两次或多次弯曲成形
图 4-37 二道工序弯曲成形
图 4-38 三道工序弯曲成形
(3)对于某些结构不对称的零件,采用弯曲后再切开的方法
图 4-39 成对弯曲成形
(4)弯曲件有高精度孔时,采用先弯曲后冲孔的方法
4.4.2 弯曲力的计算
第三章:弯曲工艺与弯曲模具设计
校正弯曲时,回弹角修正量: K90
不是90°的角按下式修正: x ( / 90)90
➢ 当r/t < 8~10时,要分别计算弯曲半径和弯曲角的回弹值,再修正。
弯曲板料时
凸模的圆角半径: rp 1/(1/ r) (3 s / Et)
凸模圆弧所对中心角: p
(r
/ rp )
弯曲件的滑移
6. 最小弯曲半径 rmin
❖ r/t 小 —— 变形程度大 —— 弯曲破坏。 影响最小弯曲半径的因素:
❖ 材料的机械性能:好塑性(塑稳)、退火处理、热弯、开槽减薄 ❖ 方向性:折弯线垂直纤维方向:伸长变形能力强
❖ 板宽:B/t 小(< 3) ❖ 弯曲角:小, 直边有切向形变。 ❖ 板料表面质量和断面质量:差处易应力集中发生破坏。 ❖ 板料厚度:t小 —— 切向应变小 —— 开裂小。
弯曲件的工序安排
1. 工序安排的一般原则 ➢ 先弯外角后弯内角,后次弯曲不能影响前一次弯曲变形,前次弯曲应考 虑后次弯曲有合适的定位基准。 ➢ 当有多种方案时,要进行比较,进行优化。
2. 工序安排的一般方法 ➢ 形状简单的弯曲件可一次弯曲成形。如V形、U形、Z形。 ➢ 形状复杂的弯曲件可用两次或多次压弯成形。
➢ r/t值
小r/t: 加厚筋边或 减小 r; 其值大时拉弯
(在同条件下,r/t越小,则总变形量就越大,回弹就越小。) 工艺处理
➢ 弯曲中心角
(α越大,变形区长度越长,参与变形的区域越大,回弹越多。)
小
➢ 弯曲方式与校正力大小
(自由弯曲回弹大,校正弯曲回弹小,校正力越大回弹越小。)
➢ 工件形状
(工件形状越复杂,回弹就越少。)
弹-塑性变形: 塑性变形:
L1-L2 ,r1-r2 超过屈服极限,
弯曲模工作部分尺寸的设计
弯曲模工作部分尺寸的设计
1.凸模圆角半径相对弯曲半径r/t较小时,凸模圆角半径:
r p = r (弯曲件内侧的圆角半径),
但r p 不得小于最小弯曲半径值r min 。
当r/t>10时,应考虑回弹,将凸模圆角半径适量修正。
→V
形弯曲
2. 凹模圆角半径
)
)((8.0~6.0t r r d +=t ≤ 2 mm时,r d =(3~6)t;t=2~4 mm时,r d =(2~3)t;V 形弯曲凹模的底部可开退刀槽或取圆角半径:
U 形弯曲中,凹模两边的圆角半径应一致。
否则,坯料会在弯曲时发生偏移。
即:
t>4mm时,r d =2t。
3. 凸、凹模间隙
V 形弯曲模的凸、凹模间隙靠调整压机的闭合高度来控制,设计时可以不予考虑。
U 形件弯曲模的凸、凹模单边间隙一般可按下式计算,即:
Z = kt
max
式中k—间隙系数。
钢板,取k =1.05~1.15。
当工件精度要求较高时,其间隙应适当缩小,取
Z =tmax。
4. U 形件弯曲凸、凹模宽度及公差
以凹模为基准件,间
隙取在凸模上。
1)尺寸标注在外侧时
()d b b δ075.0+∆−=d 凹模宽度
)(p
d p Z b b δ−−=凸模宽
度
2)尺寸标注在内侧时
0)75.0(p p b b δ−∆+=凸模宽度
d Z b b d δ0
)(++=凹模宽度
式中δp 、δd ——凸、凹模的制造公差,可采用IT6~IT8 级精度。
一般凸模精度比凹模精度高一级。
以凸模为基准件,间隙取在凹模上。
弯曲模具设计
6 弯曲模具设计本章内容: V形弯曲模、U形弯曲模,多角弯曲件、圆形弯曲件等复杂件弯曲成形的多工序复合弯曲模,U形弯曲模设计实例。
本章难点:复杂弯曲模的结构组成与动作过程。
6.1 简单弯曲模简单弯曲模——工作时模具通常只有一个垂直运动的单工序弯曲模。
完成的制件有单角的V形件、双角的U形件和小于90°的U形件等简单件。
6.1.1 V形件弯曲模图6.1 V 形件弯曲模 图6.2 V 形件弯曲模三维模型图6.3 V 形件压板式弯曲模图6.4 V形件折板式弯曲模(a) 开模状态 (b) 合模状态图6.5 V形件折板式弯曲模三维模型V形件折板式弯曲模6.1.2 U形件弯曲模图6.6 U形件的弯曲模图6.7 弯制夹角小于90°的U形件弯曲模弯制夹角小于90°的U形件弯曲模异形U形件弯曲模Z形件弯曲模6.1.3 通用弯曲模图6.8 通用弯曲模6.2 复杂弯曲模复杂弯曲模——在工作时通常具有两个或两个以上的运动,可将多个弯曲变形一次完成。
6.2.1 C形弯曲模图6.9 C形弯曲模图6.10 C形弯曲模立体模型(a) 弯曲初始状态 (b) U形中间弯曲状态 (c) C形最终弯曲状态图6.11 C形件弯曲动作过程四角弯曲模1四角弯曲模2异形件弯曲模6.2.2 O形件弯曲模O形件弯曲模图6.12 滑板式弯曲模图6.13 滑板式弯曲模模型(a) 初始弯曲状态 (b) 中间弯曲状态 (c) 最终弯曲状态图6.14 弯制带有耳翅的环类工件的滑板式弯曲模图6.16 圆形件自动卸料弯曲模图6.17 圆形件自动卸料弯曲模动作过程其他弯曲1其他弯曲26.3 U形弯曲件冲压实例6.3.1工艺分析及工艺方案图6.18 弯曲件材料为35钢板(退火),板厚3mm,大批量生产该零件形状简单,批量生产,精度无特殊要求,结构不对称,应注意弯曲中的偏移问题。
该零件弯曲半径R=5mm,查表5-2可知min ,有R>minr,故此不会弯裂。
弯曲与弯曲模具设计
二、弯曲件的工艺计算
2.弯曲力的计算
(1)自由弯曲力对于V形件,有
F自
0.6kbt 2 b
rt
对于U形件,有
F自
0.7kbt 2 b
rt
(2)校正弯曲力如果弯曲件在冲压行程结束时受到模具的校正
(见图3-27)
上一页 下一页
第四节 弯曲件的工艺特性及工艺计 算
二、弯曲件的工艺计算
(3)顶件力或压料力
上一页 下一页
第四节 弯曲件的工艺特性及工艺计 算
一、弯曲件的工艺性
(6)增添连接带和定位工艺孔 如图3-22所示。 (7尺寸标注 尺寸标注对弯曲件的工艺性有很大的影响。 如图3-23所示。
上一页 下一页
第四节 弯曲件的工艺特性及工艺计 算
二、弯曲件的工艺计算
1.弯曲件展开长度的确定
第三章 弯曲与弯曲模具设计
第一节 弯曲技术概述 第二节 弯曲变形过程分析 第三节 弯曲件坯料尺寸的计算 第四节 弯曲件的工艺特性及工艺计算 第五节 弯曲件的工序安排 第六节 弯曲模典型结构及结构设计
第一节 弯曲技术概述
弯曲是利用压力使金属板料、管料、棒料或型材在模具中弯 成一定曲率、一定角度和形状的变形工序。弯曲工艺在冲压 生产中占有很大的比例,应用相当广泛,如汽车纵梁、电器 仪表壳体、支架、铰链等,都是用弯曲方法成型的。
所示为V形件弯曲的变形过程。 2.弯曲变形特点 为了分析板料弯曲变形的规律,将试验用的长方形板料的 侧面画成正方形网格,如图3-4(a)所示,然后弯曲,观察其
变形特点,弯曲后情况如图3-4(b)所示。
下一页
第二节 弯曲变形过程分析
一、弯曲的变形特点
(1)变形区主要在弯曲件的圆角部分,圆角区内的正方形网 格变成厂扇形。
- 1、下载文档前请自行甄别文档内容的完整性,平台不提供额外的编辑、内容补充、找答案等附加服务。
- 2、"仅部分预览"的文档,不可在线预览部分如存在完整性等问题,可反馈申请退款(可完整预览的文档不适用该条件!)。
- 3、如文档侵犯您的权益,请联系客服反馈,我们会尽快为您处理(人工客服工作时间:9:00-18:30)。
值时,为了提高极限弯曲变形程度,防止弯裂,常采用的措施有退
火、加热弯曲、消除冲裁毛刺、两次弯曲(先加大弯曲半径,退火
后再按工件要求小弯曲半径弯曲)、校正弯曲以及对较厚的材料开
槽后弯曲。
大连理工大学出版社
三 弯曲件质量分析
(三) 弯曲卸载后的回弹 1
回弹现象
塑性弯曲时伴随有弹性变形,当外载荷去除后,塑性变形保留 下来,而弹性变形会完全消失,使弯曲件的形状和尺寸发生变化而 与模具尺寸不一致,这种现象叫回弹。
(3)弯曲中心角
越大,变形区的长度越
长,回弹积累值也越大,故
回弹角 越大。
变形程度对弹性恢复值的影响
大连理工大学出版社
三
弯曲件质量分析
(三) 弯曲卸载后的回弹 3
影响回弹的因素
(4)弯曲方式及弯曲模 ①在无底凹模内作自由弯曲时回弹最大。 ②在有底凹模内作校正弯曲时,回弹较小。 校正弯曲圆角部分的回弹比自由弯曲时大为减小。 校正弯曲时圆角部分的较小正回弹与直边部分负回弹的抵销 , 回弹可能出现正、零或是负三种情况。 (5)在弯曲U形件时,凸、凹模之间的间隙对回弹有较大的影响。 间隙越大,回弹角也就越大。 (6)工件的形状 一般而言,弯曲件越复杂,一次弯曲成形角的数量越多,回弹 量就越小。
V形件弯曲模
大连理工大学出版社
一
概
述
弯曲及弯曲模具
大连理工大学出版社
二
弯曲变形过程及变形特点
(一) 弯曲变形过 程
弯曲分类:自由弯曲和校正弯曲。
弯曲过程
大连理工大学出版社
二
弯曲变形过程及变形特点
(二) 弯曲变形特点
弯曲变形主要发生在弯曲带中 心角α 范围内,中心角以外基本不 变形。 坯料在长、宽、厚三个方向都
宽度方向σ3:内外侧压力均为零
长度方向σ1:内区受压,外区受拉 厚度方向σ2:内外均受压应力 宽度方向σ3:内区受压,外区受拉
两 向 应 力 三 向 应 力
大连理工大学出版社
二
弯曲变形过程及变形特点
(二) 弯曲变形时的应力与应变状态
长度方向ε1:内区压应变,外区拉应变 窄板 (B/t<3) 应变状态 宽板 (B/t>3) 厚度方向ε2:内区拉应变,外区压应变 宽度方向ε3:内区拉应变,外区压应变
大连理工大学出版社
三
弯曲件质量分析
(三) 弯曲卸载后的回弹 5
减小回弹的措施
克服回弹措施1
大连理工大学出版社
三
弯曲件质量分析
(三) 弯曲卸载后的回弹 5
减小回弹的措施
克服回弹措施2
大连理工大学出版社
三
弯曲件质量分析
(四) 弯曲时的偏移 1
偏移现象
弯曲时的偏移现象
大连理工大学出版社
三
弯曲件质量分析
模块三
一 概 述
弯
六
曲
弯曲力的计算
二
弯曲变形过程及变形特点
七
弯曲件的工序安排
三
弯曲件质量分析
八
弯曲件的典型结构
四 弯曲件的结构工艺性
九 弯曲模工作零件设计
五
弯曲件展开尺寸计算
十
U形件弯曲模设计
大连理工大学出版社
模块三
本 模 块
弯
内
曲
容
弯曲是冷冲压基本工序之一。本模块以U形件弯曲工艺和弯
曲模结构设计为学习任务,包含的弯曲工序基本知识有:弯曲变 形过程及弯曲件质量影响因素,弯曲工艺计算、工艺方案制定和
大连理工大学出版社
四
弯曲件的结构工艺性
(四) 弯曲件的精度
大连理工大学出版社
四
弯曲件的结构工艺性
(二) 弯曲件的材料
具有足够的塑性,屈强比( s / b )小, 屈服点与弹性模量的比值( s / E )小, 则有利于弯曲成形和工件质量的提高。 脆较大的材料,则最小相对弯曲半径 rmin / t 大,回弹大,不利于成形。
大连理工大学出版社
模块三
难点
弯
曲
1.弯曲变形规律及弯曲件质量影响因素; 2.影响回弹的因素与减少回弹的措施 ; 3.弯曲工艺计算; 4.弯曲模典型结构与弯曲模工作零件设计。
大连理工大学出版社
一
弯曲
概
述
将板料、型材、管材或棒料等按设计要求弯成一定的角度和一定的 曲率,形成所需形状零件的冲压工序。 弯曲方法
弯曲中心角为90°时部分材料的平均回弹角见表。
当弯曲件弯曲中心角不为90°时,其回弹角可用下式计算:
大连理工大学出版社
90
90
三
弯曲件质量分析
(三)弯曲卸载后的回弹 4
回弹值的确定
(2)校正弯曲时的回弹值 校正弯曲的回弹可用试验所得的公式(见表3-3)计算,符号如 图所示。
大连理工大学出版社
减小回弹的措施
(1)改进弯曲件的结构设计
①尽量避免选用过大的r/t 。如有可能,在弯曲区压制加强筋,以提高
零件的刚度,抑制回弹。
在零件结构上考虑减小误差
②尽量选用 s / E 小、力学性能稳定和板料厚度波动小的材料。
大连理工大学出版社
三
弯曲件质量分析
(三) 弯曲卸载后的回弹 5
减小回弹的措施
(2)从工艺上采取措施
形状对称及形状不对称的弯曲件
大连理工大学出版社
四
弯曲件的结构工艺性
(三) 弯曲件的结构 3
弯曲件高度
弯曲件的直边高度不宜
过小,其值应为
h>r+2t
弯曲件的弯边高度
大连理工大学出版社
四
弯曲件的结构工艺性
(三) 弯曲件的结构 4
防止弯曲根部裂纹的工件结构
在局部弯曲某一段边缘时,为避免弯曲根部撕裂,应减小不弯曲 部分的长度B,使其退出弯曲线之外,即b≥r(如上页图(a)),或在弯
弯曲模设计。涉及弯曲变形过程分析、弯曲半径及最小弯曲半径
影响因素、弯曲卸载后的回弹及影响因素、减少回弹的措施、坯 料尺寸计算、工艺性分析与工艺方案确定、弯曲模典型结构、弯
曲模工作零件设计等。
大连理工大学出版社
模块三 弯
重点
曲
1. 弯曲变形规律及弯曲件质量影响因素; 2. 弯曲工艺计算方法; 3. 弯曲工艺性分析与工艺方案制定; 4. 弯曲模典型结构与结构设计; 5. 弯曲工艺与弯曲模设计的方法和步骤。
①采用校正弯曲代替自由弯曲。对冷作硬化的材料先退火,降低其屈
服极限σs,以减小回弹,弯曲后再淬硬。 ②采用拉弯代替一般弯曲方法。拉
弯的工艺特点是弯曲之前使坯料承受一
定的拉伸应力,其数值使坯料截面内的 应力稍大于材料的屈服强度,随后在拉
力作用下同时进行弯曲。
拉弯用模
大连理工大学出版社
三
弯曲件质量分析
曲部分与不弯曲部分之间切槽,或在弯曲前冲出工艺孔。
大连理工大学出版社
增加工艺槽和工艺孔
四
弯曲件的结构工艺性
(三) 弯曲件的结构 5
弯曲件孔边距离
当t<2mm时, l t 当t≥2mm时, l 2t
弯曲件孔边距离
大连理工大学出版社
四
弯曲件的结构工艺性
(三) 弯曲件的结构 6
增添连接带和定位工艺孔
尽量将圆角半径取大一些。只有当产品结构上有要求时,才采用最小
弯曲半径。
大连理工大学出版社
三 弯曲件质量分析
(二)弯裂与最小相对弯曲半径的控制 1
最小相对弯曲半径
压弯时的变形情况
大连理工大学出版社
三
2
弯曲件质量分析
(二) 弯裂与最小相对弯曲半径的控制
最小弯曲半径影响因素
(1)材料的力学性能 (2)弯曲方向 (3)弯曲件角度φ (4)板料的热处理状态 (5)板料的边缘以及表面状态
(三) 弯曲卸载后的回弹 3
影响回弹的因素
(1)材料的力学性能
S / E 越大,回弹越大。
材料的力学性能对回弹值的影响 1、3-退火软钢;2-软锰黄铜;4-经冷变形硬化的软钢
大连理工大学出版社
三
弯曲件质量分析
(三) 弯曲卸载后的回弹 3
影响回弹的因素
(2)相对弯曲半径 r / t
r / t 越大,回弹越大。
大连理工大学出版社
四
弯曲件的结构工艺性
(三) 弯曲件的结构 1
弯曲半径
弯曲件的弯曲半径不宜小于最小弯曲半径,否则,要多次弯曲, 增加工序数; 也不宜过大,因为过大时,受到回弹的影响,弯曲角度与弯曲 半径的精度都不易保证。
大连理工大学出版社
四
弯曲件的结构工艺性
(三) 弯曲件的结构 2
弯曲件的形状
一般要求弯曲件形状对称,弯曲半径左右一致,则弯曲时坯料受力 平衡而无滑动。
层由于受过大的拉应力作用而出现开裂。因此常用板料的相对弯曲半
径r/t来表示板料弯曲变形程度的大小。
大连理工大学出版社
三
弯曲件质量分析
(一) 弯曲变形程度与最小弯曲半径 2
最小弯曲半径
通常将不致使材料弯曲时发生开裂的最小弯曲半径的极限值称 为该材料的最小弯曲半径。各种不同材料的弯曲件都有各自的最小弯 曲半径。一般情况下,不宜使制件的圆角半径等于最小弯曲半径,应
(四) 弯曲时的偏移 2
消除偏移的措施
克服偏移措施1
克服偏移措施2
大连理工大学出版社
三
弯曲件质量分析
(五) 弯曲后的翘曲与剖面畸变
弯曲后的翘曲
型材、管材弯曲后的剖面畸变
大连理工大学出版社
四
弯曲件的结构工艺性
(一) 弯曲件的精度
弯曲件的结构工艺性:指弯曲件的形状、尺寸、精度、材料以及技术要 求等是否符合弯曲加工的工艺要求。 尺寸公差按GB/T 13914-92,角度公差按GB/T 13915-92,形状和位置 未注公差 按GB/T 13916-92,未注公差尺寸的极限偏差按GB/T 5055-94。 对于弯曲件的精度要求要合理。