83弯曲模具设计实例
3.8 弯曲模典型结构
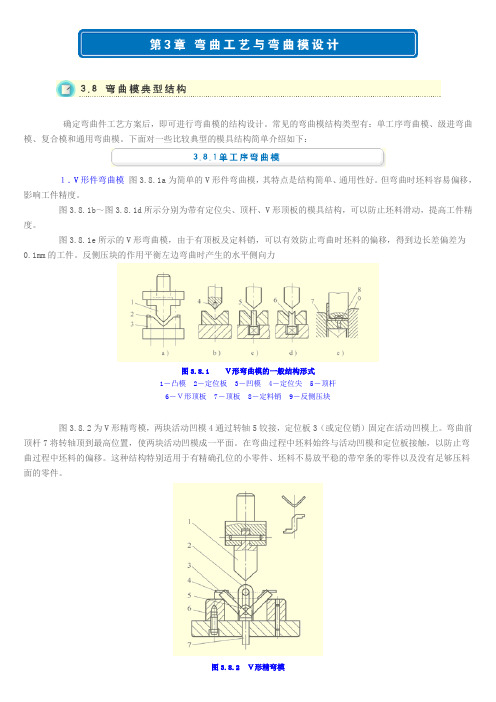
确定弯曲件工艺方案后,即可进行弯曲模的结构设计。
常见的弯曲模结构类型有:单工序弯曲模、级进弯曲模、复合模和通用弯曲模。
下面对一些比较典型的模具结构简单介绍如下:1.V形件弯曲模图3.8.1a为简单的V形件弯曲模,其特点是结构简单、通用性好。
但弯曲时坯料容易偏移,影响工件精度。
图3.8.1b~图3.8.1d所示分别为带有定位尖、顶杆、V形顶板的模具结构,可以防止坯料滑动,提高工件精度。
图3.8.1e所示的V形弯曲模,由于有顶板及定料销,可以有效防止弯曲时坯料的偏移,得到边长差偏差为0.1mm的工件。
反侧压块的作用平衡左边弯曲时产生的水平侧向力图3.8.1 V形弯曲模的一般结构形式1-凸模2-定位板3-凹模4-定位尖5-顶杆6-V形顶板7-顶板8-定料销9-反侧压块图3.8.2为V形精弯模,两块活动凹模4通过转轴5铰接,定位板3(或定位销)固定在活动凹模上。
弯曲前顶杆7将转轴顶到最高位置,使两块活动凹模成一平面。
在弯曲过程中坯料始终与活动凹模和定位板接触,以防止弯曲过程中坯料的偏移。
这种结构特别适用于有精确孔位的小零件、坯料不易放平稳的带窄条的零件以及没有足够压料面的零件。
图3.8.2 V形精弯模1-凸模2-支架3-定位板(或定位销)4-活动凹模 5-转轴6-支承板7-顶杆2.U形件弯曲模根据弯曲件的要求,常用的U形弯曲模有图3.8.3所示的几种结构形式。
图3.8.3a所示为开底凹模,用于底部不要求平整的制件。
图3.8.3b用于底部要求平整的弯曲件。
图3.8.3c用于料厚公差较大而外侧尺寸要求较高的弯曲件,其凸模为活动结构,可随料厚自动调整凸模横向尺寸。
图3.8.3d用于料厚公差较大而内侧尺寸要求较高的弯曲件,凹模两侧为活动结构,可随料厚自动调整图3.8.3 U形件弯曲模1-凸模2-凹模3-弹簧 4-凸模活动镶块5、9-凹模活动镶块6-定位销7-转轴8-顶板凹模横向尺寸。
图3.8.3e为U形精弯模,两侧的凹模活动镶块用转轴分别与顶板铰接。
弯曲模具设计说明

弯曲模具设计阐明书--保持架异向弯曲工序模具设计姓名:***学号:***班级:***指导老师:***日期:2023/12/27目录1. 设计旳目旳和意义 (3)2. 弯曲零件图及工艺 (3)2.1. 弯曲零件图 (3)2.2. 工艺分析 (4)2.3. 材料分析 (5)2.4. 模具简图 (5)3. 弯曲力旳计算 (10)4. 校正弯曲力旳计算 (10)5. 弹顶器旳计算 (11)6. 回弹量旳计算 (12)7. 弯曲模构造设计和装配图总图 (13)8. 弯曲模凸模、凹模设计 (14)9. 结论 (15)10. 参照文献 (16)1.设计旳目旳和意义本设计书意在设计出保持架中间工序旳弯曲模,保持架为多部位弯曲构造,采用冲压弯曲工艺可以以便快捷高效地进行生产,且品质益于保证,节省成本。
保持架采用单工序模冲压,需要三道工序,工艺简朴,生产效率高。
此模具是保持架三道工序(a 落料 b 异向弯曲c 最终弯曲)三步中旳第二步,是成型最关键旳一步。
2.弯曲零件图及工艺2.1. 弯曲零件图零件名称:保持架生产批量:中批量材料:20钢,厚0.5mm零件图:如图1图1 保持架零件图2.2. 工艺分析保持架采用单工序模冲压,需要三道工序,分别为落料、异向弯曲、最终弯曲。
每道工序各用一套模具。
本设计书重要简介了中间工序-异向弯曲工序模具旳设计。
异向弯曲工序旳工件如图2所示。
工件左右对称,共有8条弯曲线。
其中字母a, b, c, d, e为此弯曲工序旳弯曲线。
图2 异向弯曲工序工件2.3. 材料分析此工件材料为20钢(GB/T 699-1999),冷变形塑性高、一般供弯曲、压延、弯边和锤拱等加工切削加工性冷拔或正火状态较退火状态好、一般用于制造受力不大而韧性规定高旳。
该钢属于优质低碳碳素钢,冷挤压、渗碳淬硬钢。
该钢强度低,韧性、塑性和焊接性均好。
抗拉强度为355~500MPa,伸长率≥24%。
2.4. 模具简图图3是保持架零件图,图4是此弯曲工序旳成品图,图5为此工序模具旳设计装配图,图6是保持架模具凹模零件图,图7是保持架模具凸模零件图,图8是凹模垫板工程图,图9是凹模固定板工程图,图10是凸模垫板工程图,图11是凸模固定板工程图。
弯曲模具设计及计算

3.4 弯曲模具设计及计算
3.4.4 弯曲力的计算 一、自由弯曲时弯曲力的计算
弯曲件自由弯曲时弯曲力的经验计算公式见表3-10。 自由弯曲时,除了弯曲力以外,有时还有压料力、顶件力 等其它工艺力,弯曲的工艺总力应为:
PS = P + P1 + P2 + …… (3 –14)
式中 PS ——弯曲工艺总力(kN); P —— 弯曲力(kN); P1 —— 压料力(kN),常取P1 =(0.3~0.8)P; P2 —— 顶件力(kN),常取P2 =(0.3~0.8)P;
一、凸模工作尺寸
当弯曲件的相对圆角半径 r / t > 5时,r p、a p或 j p由回 弹计算决定。
当5 > r / t > r min / t时,一般取r p = r , a p = a + Da或j p = j - Dj。
当 r / t < r min / t时,取r p≥ r min ,弯曲后通过整形工序 使r达到要求。
L min —— 弯曲件的最小极限尺寸(mm);
D ——弯曲件的尺寸公差(mm);
δ确定p 、,δ或取d —(—1/3凸-1、/4)凹D模;的制造公差(mm),按IT7-9级
Z —— 凸、凹模双面间隙(mm)。
8
弯曲件尺寸标注双向对称偏差时,取
L
p
=(
L
min
+
0.25Δ)
0 p
弯曲件标注单向正偏差时,取
(3 –24)
L
p
=(
L
min
+
0.75Δ)
0 p
L
d
=(
L
p
+
弯曲模具设计(带全套cad图)

模具课程设计说明书——弯曲模课程设计学校:学院:专业:姓名:学号:指导教师:目录第一章工艺分析及工艺方案的拟订1.1、零件工艺性分析 (1)1.2、工艺方案的确定 (1)第二章工艺设计2.1、确定排样方案 (2)2.2、计算各工序的压力 (3)2.3、压力机的选取 (4)第三章模具类型及结构形式的选择 (5)第四章模具工作零件刃口尺寸及公差的计算4.1、凸、凹模刃口尺寸计算原则 (5)4.2、刃口尺寸计算 (5)第五章模具零件的选用,设计及必要的计算5.1、凹模结构尺寸的确定 (6)5.2、卸料树脂的选用 (7)5.3、其他标准件零件的选用 (7)第六章凸凹模加工工艺方案6.1、凹模、凸模加工工艺路线 (7)6.2、模具装配 (9)第一章工艺分析及工艺方案的拟订1.1零件工艺性分析一、零件图二、零件的工艺性分析(1)冲裁件的结构工艺性此制件的形状较简单,需要圆角过渡,可以加上R0.5,便于模具的加工和减少冲压时在尖角处开裂的现象,同时也可以防止尖角部位刃口的过快磨损。
(2)冲裁件的尺寸精度冲裁件的精度主要以其尺寸精度、冲裁断面粗糙度、毛刺高度三个方面的指标来衡量,根据零件图上的尺寸标注及公差,可以判断属于尺寸精度为IT12—IT14的经济级普通冲裁。
1.2、工艺方案的确定一、冲压工序的选择在满足冲裁件质量与生产率的要求下,选择单工序冲裁方式,其模具寿命较长,生产率高,操作较方便和工作安全性高。
二、冲压顺序的安排落料,弯曲共两道工序,本设计中只需要设计落料模。
第二章工艺设计2.1、确定排样方案一、搭边与料宽搭边搭边值的大小与材料的力学性能、厚度、零件的形状与尺寸、排样的形式、送料及挡料方式、卸料方式等因素有关。
搭边值一般由经验确定,根据所给材料厚度δ=1.2mm,确定搭边工作间a1为2.0mm, a为2.0mm。
具体可见排样图,如下:(2)条料宽度条料宽度的确定原则:最小条料宽度要保证冲裁时零件周边有足够的搭边值,最大条料宽度要能在冲裁时顺利地在导料板之间送进,并与导料板之间有一定的间隙。
模具毕业设计83切边冲孔复合模的设计

第一章零件的工艺分析一、零件材料的分析08F钢强度、硬度很低,而塑性、韧性极高,具有良好的冷变形性和焊接性,正火后切削加工性尚可,退火后导磁率较高,剩磁较少,但淬透性、淬硬性极低。
二、零件的结构分析该零件结构简单,尺寸没有公差要求,尺寸均为自由公差,外形对称。
三、零件的工艺性分析该零件是钢料,该零件形状的基本特征是一般的有凹圆的圆筒形件,为圆筒形件底部有一个Φ10孔,内部圆周直径为Φ28,尺寸均为自由公差,因一般情况下,拉深件的尺寸精度应在IT13级以下,不宜高于IT11级。
所以将内部直径改为Φ28+00.3。
高度10+00.2为IT11-IT12级精度。
主要成形方法是冲裁、拉深、切边冲孔和弯曲。
零件的dt/d、h/d都不太大,其拉深工艺性较好。
该零件为大批量生产,零件外形简单对称。
材料为08F钢,采用冲压加工经济性较好。
零件如图:t=1mm其余R=0.4图1-1 零件图第二章确定冲压工艺方案冲压工艺方案的确定是制定冲压工艺过程的主要内容,需要综合考虑各方面的因素,有的还需要进行必要的工艺计算,因此,实际确定时通常先提出几种可能的方案。
再在此基础上进行分析、比较和择优。
从零件的结构和形状可知,所需基本工序为落料、拉深、冲孔、弯曲四种。
但工序模具生产效率低难以满足大批量生产的要求,为了提高生产效率主要采用复合冲裁或级进冲裁两种方式。
若采用级进模虽然生产效率很高,但模具的结构比较复杂,对制造精度要求较高,一般生产周期长,成本高维护也比较困难。
采用复合冲裁时,冲出的零件精度和平直度较好,生产效率也较高,模具结构较级进模简单生产成本也比级进模的低。
第一节零件毛坯的尺寸计算(1)弯曲毛坯尺寸的确定对于r<0.5t的弯曲件毛坯长度的计算公式Lz=5+4+5+0.6t=5+5+4+0.6×1=14.6(2)拉深次数的确定及尺寸计算因板料厚度t为1mm故按厚度中线尺寸计算,如图所示。
2.1.1计算坯料尺寸D=(d22+4d2H-1.72rd2-0.56r2)½=(29*29+4*29*10.5-1.72*2.5*29-0.56*2.5*2.5)½=43.94mmL1=Lz+2*2.5=19.6mmL=L1+D=63.54mm图2-12.1.2 确定拉深次数根据坯料的相对厚度t/D=1/43.94=2.28%拉伸系数m=d/D=29/43.94=0.66大于极限拉深系数[m],所以一次拉深成形。
弯曲模具设计
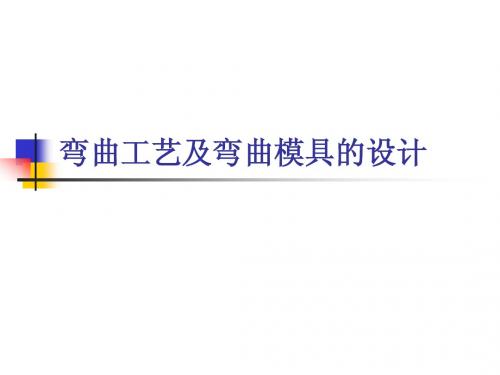
模具设计计算 计算毛坯尺寸 排样及材料利用率计算 弯曲力计算 凸凹模计算
弯曲工艺及弯曲模具的设计
弯曲工艺及弯曲模具的设计
案例2
弯曲模设计
如图所示:U形件 生产批量:大批量 材料:Q235 t=6mm
要求:设计该零件的弯曲工艺与模具
弯曲工艺及弯曲模具的设计
1. 2. 3. 4.
5.
弯曲件工艺分析 确定工艺方案及模具结构形式 模具设计计算 绘制模具总装图与非标图 模具主要零件的加工工艺
弯曲工艺及弯曲模具的设计
弯曲工艺分析 材料 • Q235钢板是普通碳素结构钢 综合性能较好,用途最广泛
1. •
•
•
பைடு நூலகம்
工件结构 最小相对弯曲半径(是否符合要求) 弯曲件形状对称 弯曲件孔边距离足够
弯曲工艺及弯曲模具的设计
•
尺寸精度 零件图上所有尺寸均未标注公差,属自 由尺寸,可按IT14级确定工件尺寸的公 差 φ 13mm的两个孔是螺钉过孔,与螺 钉有单边0.5mm间隙,弯曲后两空中心 一致,以保证螺钉的顺利通过。
弯曲工艺及弯曲模具的设计
结论:
弯曲工艺及弯曲模具的设计
2.
确定工艺方案及模具结构形式 冲压、弯曲工序性质和工序冲数的确定 方案一 1.落料 2.冲两个φ 13孔 3.弯曲 方案二 1.落料 2.弯曲 3.冲两个φ 13孔 方案三 1.落料冲φ 13孔复合 2.弯曲 ……
弯曲工艺及弯曲模具的设计
弯曲模设计实例
13—下模座
弯曲模设计实例
1.3 弯曲工艺的主要计算
1. 弯曲力计算
3. 弹顶力的
计算
弯曲模设计实例
1.4 弯曲模主要零部件设计
凸模镶拼示意图
弯曲模设计实例
1.4 弯曲模主要零部件设计
凹模镶拼示意图
冲压工艺与模具设计
冲压工艺与模具设计
弯曲模设计实例
保持架零件图
弯曲模设计实例
1.1 弯曲零件工艺分析析
异向弯曲件
1.2 模具结构
弯曲模设计实例
模具工作过程:将落料后的坯料
放在凹模上,并使中部的两个突耳 进入凹模固定板的槽中。当模具下 行时,凸模中部和顶件块压住坯料 的突耳,使坯料准确定位在槽内。 模具继续下行,使各部弯曲逐渐成 形。上模回程时,弹顶器通过顶件 块将工件顶出。
案例2弯曲模设计
案例2弯曲模零件名称:托架(见图9)生产批量:2万件/年材料:08冷轧钢板编制冲压工艺方案设计模具结构。
图8 弯曲件(一) 确定工艺方案制成该零件所需的基本工序为冲孔、落料和弯曲。
其中冲孔和落料属于简单的分离工序,弯曲成形的方式可以有图9所示的三种。
图9工艺方案零件上的孔,尽量在毛坯上冲出,以简化模具结构,便于操作。
该零件上的Ф10孔的边与弯曲中心的距离为6mm,大于1.0t(1.5mm),弯曲时不会引起孔变形,因此Ф10孔可以在压弯前冲出,冲出的Ф10孔可以做后续工序定位孔用。
而4-Ф5孔的边缘与弯曲中心的距离为1.5mm,等于1.5t,压弯时易发生孔变形,故应在弯后冲出。
完成该零件的成形,可能的工艺方案有以下几种:方案一:落料与冲Ф10孔复合,见图10(a),压弯外部两角并使中间两角l预弯45º,见图10(b),压弯中间两角,见图10(c),冲4-Ф5孔,见图10(d).图10方案一方案二:落料与冲Ф10孔复合,见图10(a),压弯外部两角,见图11(a),压弯中间两角,见图11(b),冲4-Ф5孔,见图10(d)。
方案三:落料与冲Ф10孔复合,见图10(a),压弯四个角(12),冲4-Ф5孔,见图10(d)。
方案四:冲Ф10孔,切断及弯曲外部两角(图13),压弯中间两角,见图11(b),冲4-Ф5孔,见图10(d)。
图11方案二图12压弯四个角图13冲孔(Ф10)、切断及弯曲外部两角连续冲压案五:冲Ф10孔,切断及压弯四个角连续冲压(图14),冲4-Ф5孔,见图10(d)。
方案六:全部工序组合采用带料连续冲压,如图15所示的排样图。
在上述列举的方案中,方案一的优点是:①模具结构简单,模具寿命长,制造周期短,投产快;②工件的回弹容易控制,尺寸和形状精确,表面质量高;③各工序(除第一道工序外)都能利用Ф10孔和一个侧面定位,定位基准一致且与设计基准重合,操作也比较简单方便。
缺点是:工序分散,需用压床,模具及操作人员多,劳动量大。
弯曲模具设计(带全套cad图).
模具课程设计说明书——弯曲模课程设计学校:学院:专业:姓名:学号:指导教师:一、零件图二、工艺设计1.弯曲工序安排原则工序安排的原则应有利于坯件在模具中的定位;工人操作安全、方便;生产率高和废品率最低等。
弯曲工艺顺序应遵循的原则为:①先弯曲外角,后弯曲内角。
②前道工序弯曲变形必须有利于后续工序的可靠定位;并为后续工序的定位做好准备。
③后续工序的弯曲变形不能影响前面工序已成形形状和尺寸精度。
④小型复杂件宜采用工序集中的工艺,大型件宜采用工序分散的工艺。
⑤精度要求高的部位的弯曲宜采用单独工序弯曲,以便模具的调整与修正。
制订工艺方案时应进行多方案比较。
2.形状简单的弯曲件如V形、U形、Z形件等,可采用一次弯曲成形。
3.弯曲件展开尺寸计算。
(1)中性层位置的确定弯曲中性层位置并不是在材料厚度的中间位置,其位置与弯曲变形量大小有关,应按下式确定:P=r+kt式中 P----弯曲中性层的曲率半径;r----弯曲件内层的弯曲半径;t----材料厚度;k----中性层位移系数,板料可有表3-9查得,圆棒料由表3-10查得。
(2)弯曲件展开尺寸计算计算步骤:1)将标注尺寸转换成计算尺寸即将工件直线部分与圆弧部分分开标注,2)计算圆弧部分中性层曲率半径及弧长中性层曲率半径为P=r+kt,则圆弧部分弧长为: s=Pa式中 a----圆弧对应的中心角,以弧度表示。
3)计算总展开长度L=L1+L2+SL=∑L直+∑S弧4.回弹弯曲成形是一种塑性变形工艺。
回弹的表现形式:1)弯曲回弹会使工件的圆角半径增大,即r2>rp,则回弹量可表示为△r=r2-rp2) 弯曲回弹会使弯曲件的弯曲中心角增大,即a>ap.则回弹量可表示为△a=a-ap影响弯曲回弹的因素:1.材料的力学性能。
2. 材料的相对弯曲半径r/t。
3. 弯曲制件的形状。
4. 模具间隙。
5. 校正程度。
弯曲板件时,凸模圆角半径和中心角可按下式计算:Rp=r/(1+3Asr/Et)ap=ra/rp式中 r----工件的圆角半径;Rp----凸模的圆角半径;a----工件的圆角半径r对弧长的中心角;ap----凸模的圆角半径rp所对弧长的中心角;t----毛坯的厚度;E----弯曲材料的弹性模量;A----弯曲材料的屈服点减小回弹的措施:1)在弯曲件的产品设计时①弯曲件结构设计时考虑减少回弹,在弯曲部位增加压筋连接带等结构。
弯曲模设计实例ppt课件
,卸载后弯曲件圆角半径的变化可以不予
考虑,而弯曲中心角发生的变化,可以采用校正弯曲来控制。
r/t0.6 75
;.
4
第三章 弯曲模设计
(3)精度分析 零件上只有1个尺寸有公差要求,由公差表查得其公差要求属于IT14,其余未
注公差尺寸也均按IT14选取,所以普通弯曲和冲裁即可满足零件的精度要求。
结论:由以上分析可知,该零件冲压工艺性良好,可以冲裁和弯曲。
R9mm,属于半边磨损尺寸。由于是圆弧曲线,应该与落料尺寸18mm相切, 所以其凸、凹模刃口尺寸取为
R A 1 2 1 7 .6 7 8 0 0 .1 0 8 /2m m 8 .8 3 9 0 0 .0 5 4 m m
R T1 2 1 7 .1 9 8 0 0 .0 7 2 /2m m 8 .5 9 9 0 0 .0 3 6m m
2.6 8 (4 9.4 2 x 0) 1.1 0 x 0 4
x0 31.2mm
模具压力中心坐标点为(-31.2 , 0)。
;.
26
弯曲模设计
冲孔落料级进模零部件设计:
(1)标准模架的选用 标准模架的选用依据为凹模的外形尺寸,所以应首先计算
凹模周界的大小。根据凹模高度和壁厚的计算公式得
凹模高度 H K 0 . b 3 6 5 m 4 2 m m 5m
弯曲模设计 完成图示弯曲件的模具设计
材料:45钢,料厚:3mm
;.
1
弯曲模设计
内容:完成上述U形弯曲件展开坯料的工艺性分析、工艺方案制定以及相关工 艺计算,并绘制制坯模简图。并强化冲裁模设计步骤和主要内容。
材料:45钢,料厚:3mm (1)材料分析
;.
22
弯曲模设计
排样尺寸确定:
- 1、下载文档前请自行甄别文档内容的完整性,平台不提供额外的编辑、内容补充、找答案等附加服务。
- 2、"仅部分预览"的文档,不可在线预览部分如存在完整性等问题,可反馈申请退款(可完整预览的文档不适用该条件!)。
- 3、如文档侵犯您的权益,请联系客服反馈,我们会尽快为您处理(人工客服工作时间:9:00-18:30)。
1. 凸模圆角半径rp: a. rmin/t<r/t<5~8时,取rp=r; b. rmin/t>r/t, 先弯成较大圆角,然后整形; c. r/t>=10时,应根据回弹值修正圆角半径。
2. 凹模圆角半径rd: a. 当t<=2mm时,rd=(3~6)t; b. 当t=2~4mm时,rd=(2~3)t; c . 当t>4mm时,rd=2t。
当t<2mm时,L>=t 当t>=2mm时,L>=2t
b. 若L过小而不能满足上述条件时,则必须先弯曲 后进行冲孔;或在靠变形区一侧预先冲出缺口或牙 槽,也可在变形线上冲出工艺孔,以改变变形范围 ,利用工艺变形来保证所需孔不产生变形。
5. 增加工艺缺口、槽和工艺孔 a. 为提高精度,对于弯曲时圆角变形区侧面可以产 生畸变的弯曲件,可以预先在折弯线的两端切出工艺 缺口或槽,以避免畸变对弯曲件宽度尺寸的影响。
其中:b-弯曲件宽度;t-弯曲件厚度;r-内圆角弯曲半径; σb-弯曲材料的抗拉强度(Mpa);K-安全系数,一般取1.3
b. 校正弯曲时的弯曲力 F校=p A
A-弯曲件被校正部分的投影面积(mm²) p-单位面积校正力(M pa)
不同材料的单位面积校正力可以查表得出。
c. 顶件力和压Байду номын сангаас力 FQ=(0.3~0.8)F自
2.3 设计实例
2.1.1 弯曲变形过程分析 1. 弯曲变形过程:弯曲变形的含义、变形过程三阶
段、弯曲回弹、自由弯曲、矫正弯曲。 2. 弯曲变性特点:网格法、中性层 2.1.2 弯曲件质量分析
弯裂、回弹、偏移等
2.1.3 弯曲件的工艺性:指弯曲件的结构形状、尺寸 、精度、材料及技术要求是否符合弯曲加工的工艺要 求。
2.1 弯曲工艺 2.1.1 弯曲变形过程分析 2.1.2 弯曲件质量分析 2.1.3 弯曲件的工艺性 2.1.4 弯曲件毛坯展开尺寸的计算 2.1.5 弯曲力的计算 2.1.6 弯曲件的工序安排
2.2 弯曲模具典型结构及工作零件的设计 2.2.1 弯曲模的分类与设计要点 2.2.2 弯曲模典型结构 2.2.3 弯曲模工作零件的设计
弯曲中性层位置的确定 ρ。= r + xt L = ρп α/180
ρ。— 中性层曲率半径,r—弯曲内侧半径, t—料厚,L—弯曲部分展开长度。 a=90 时̊ ,L总=L1+L2+ 1.57(r+xt)
2.1.5 弯曲力的计算:为选择弯曲压力机和进行模 具设计,尤其在弯曲坯料较厚、弯曲线较强、相对 弯曲半径较小、材料强度较大的弯曲件时,必须对 弯曲力进行计算。 a. 自由弯曲时的弯曲力 V形弯曲件 F自=0.6Kbt²σb/(r+t) U形弯曲件 F自=0.7Kbt²σb/(r+t)
2. 弯曲件直边高度:弯曲件直边高度不宜过小,否 则影响工件的弯曲质量,不能保证零件的形状精度 。根据经验:
直边高度: H>2.5t(经验值)
不满足要求时,可预先开槽,或增加直边高度成 形 后再切除多余部分。
3. 弯曲件孔边距离: a. 弯曲区域有孔时,为避免弯曲过程中孔的形状 会发生变形,则必须将孔移到变形区外,孔边到弯 曲半径r的中心距应满足下列条件:
弯曲件直线尺寸的精度等级和角度公差查表。
2.1.4 弯曲件毛坯展开尺寸的计算 模具设计和弯曲工艺确定时,需计算出弯曲件毛坯
的展开尺寸。计算方法根据弯曲件的结构、弯曲半 径、弯曲方法的不同而不同,但均需遵循以下计算 原则:
弯曲前后应变中性层长度不变;(r>t/2) 因此,弯曲件坯料长度应等于弯曲件中性层的展开 长度。
1. 最小弯曲半径r:对于给定材料,r越小,板料的外 侧表面变形程度就越大,r超过某一临界值后,外侧拉 应力就超过材料的最大许可拉应力而产生裂纹。 r= η t(2-2Φ-η)/2( Φ+η-1) Φ—断面收缩率; η—变薄系数; t—板料厚度。 常见材料的最小弯曲半径,可查表。
当弯曲件有特殊要求r<rmin时,可以: a. 设法提高材料的塑性:如将材料退火、加热状 态下弯曲等; b. 冲压工艺合理安排:如在板厚的弯曲半径较小 时,可以预先开槽或压槽使弯曲部位的板料变薄; c. 两次弯曲的工艺法:先弯曲较大的圆角半径, 经中间退火后再按要求进行第二次弯曲。
1、单工序模:工作中模具只有竖直方向运动。 a) V、L形弯曲件模具。
靠块h>=2t+r1+r2 r1=r2=(2~5)t
b)U形弯曲件模具
c) Z形弯曲件模具
2. 有弯曲工序的连续模:批量大、尺寸小。
3. 复合弯曲模:尺寸不大的弯曲件。
2.2.2 弯曲模工作零件设计: 1. 凸、凹模工作部分的圆角半径 2. 凹模深度 3. 凸、凹模间隙 4. 横向尺寸及公差
b. 当工件局部边缘部分弯曲时,为防止弯曲部分受力 不均匀而产生变形和裂纹,应于线切槽或冲工艺孔。
6. 弯曲 件的尺寸标 注:三种标 注方法。
6. 弯曲件的精度:弯曲件精度受偏移、回弹以及 模具结构、模具精度和工序顺序的影响(弯曲工序 越多,精度也随之降低),对弯曲件的精度应合理 选择,一般弯曲件的长度公差选在IT13级以下,角 度公差大于15ˊ.
d. 自由弯曲: F总>= F自+ FQ 校正弯曲: F总>= F校
e. 一般压力机公称压力:F压机>=(1~1.3)F校
2.1.6 弯曲件的工序安排 1)弯曲工艺分析-计算-弯曲工序安排,综合考虑 因素: a. 零件的形状;b. 尺寸;c. 尺精度等级 ;d. 批量要求;e. 材料力学性能等。 2)弯曲工序安排的原则: a. 形状简单如V、U形件要一次弯曲成形; b. 批量大、尺寸小的弯曲件,为操作方便、等为 准确和提高生产率,应采用冲裁、压弯、切断的连 续弯曲模;
c. 多次弯曲时,先两端后中间;前次弯曲考虑后次 弯曲定位,后次弯曲不能影响前次弯曲后的形状;
d. 不对称弯曲件,应对称弯曲后再切断。
2.2.1 弯曲模典型结构 模具设计注意事项:a. 准确、可靠的定位,防止弯
曲中偏移;b. 弯曲结束时能得到校正力;c. 成形 后能方便、安全地取出;d. 考虑磨损,模具留有 修模余量。 弯曲模具分类:单工序模、连续弯曲模、复合弯曲模 和通用弯曲模。