弯曲模具设计计算说明书
弯曲模设计

弯曲模设计一.凸模圆角半径当弯曲件的相对弯曲半径r / t 较小时,取凸模圆角半径等于或略小于工件内侧的圆角半径r ,但不能小于材料所允许的最小弯曲半径r min 。
若弯曲件的r / t 小于最小相对弯曲半径,则应取凸模圆角半径r t > r min ,然后增加一道整形工序,使整形模的凸模圆角半径r t = r 。
当弯曲件的相对弯曲半径r / t 较大(r / t > 10 ),精度要求较高时,必须考虑回弹的影响,根据回弹值的大小对凸模圆角半径进行修正。
二.凹模圆角半径凹模入口处圆角半径r a 的大小对弯曲力以及弯曲件的质量均有影响,过小的凹模圆角半径会使弯矩的弯曲力臂减小,毛坯沿凹模圆角滑入时的阻力增大,弯曲力增加,并易使工件表面擦伤甚至出现压痕。
在生产中,通常根据材料的厚度选取凹模圆角半径:当t ≤ 2 mm ,r a = (3 ~ 6) tt =2 ~ 4 mm ,r a = (2 ~ 3) tt >4 mm ,r a = 2 t对于V 形弯曲件凹模,其底部圆角半径可依据弯曲变形区坯料变薄的特点取r ' a = (0.6 ~ 0.8)( r t + t) 或者开退刀槽。
三. 弯曲凹模深度凹模深度要适当,若过小则弯曲件两端自由部分太长,工件回弹大,不平直;若深度过大则凹模增高,多耗模具材料并需要较大的压力机工作行程。
图20 弯曲模工作部分尺寸对于V 形弯曲件,凹模深度及底部最小厚度如图20a 所示,数值查表2 。
表2 弯曲V 形件的凹模深度及底部最小厚度值(mm)对于 U 形弯曲件,若直边高度不大或要求两边平直,则凹模深度应大于工件的深度,如图 20b 所示,图中 h 0 查表 3 。
如果弯曲件直边较长,而且对平直度要求不高,凹模深度可以小于工件的高度,见图 20c ,凹模深度 l 0 值查表 4。
表 3 弯曲 U 形件凹模 的 h 0 值 (mm) 板料厚度 t≤ 1 1~2 2~3 3~4 4~5 5~6 6~7 7~8 8~10 h 03456810 15 20 25表 4 弯曲 U 形件的 凹模深度 l 0 (mm)四. 弯曲 凸 、凹模的间隙V 形件弯曲 时, 凸 、凹模的间隙是*调整压力机的闭合高度来控制的。
弯曲模具设计(带全套cad图)

模具课程设计说明书——弯曲模课程设计学校:学院:专业:姓名:学号:指导教师:一、零件图二、工艺设计1.弯曲工序安排原则工序安排的原则应有利于坯件在模具中的定位;工人操作安全、方便;生产率高和废品率最低等。
弯曲工艺顺序应遵循的原则为:①先弯曲外角,后弯曲内角。
②前道工序弯曲变形必须有利于后续工序的可靠定位;并为后续工序的定位做好准备。
③后续工序的弯曲变形不能影响前面工序已成形形状和尺寸精度。
④小型复杂件宜采用工序集中的工艺,大型件宜采用工序分散的工艺。
⑤精度要求高的部位的弯曲宜采用单独工序弯曲,以便模具的调整与修正。
制订工艺方案时应进行多方案比较。
2.形状简单的弯曲件如V形、U形、Z形件等,可采用一次弯曲成形。
3.弯曲件展开尺寸计算。
(1)中性层位置的确定弯曲中性层位置并不是在材料厚度的中间位置,其位置与弯曲变形量大小有关,应按下式确定:P=r+kt式中 P----弯曲中性层的曲率半径;r----弯曲件内层的弯曲半径;t----材料厚度;k----中性层位移系数,板料可有表3-9查得,圆棒料由表3-10查得。
(2)弯曲件展开尺寸计算计算步骤:1)将标注尺寸转换成计算尺寸即将工件直线部分与圆弧部分分开标注,2)计算圆弧部分中性层曲率半径及弧长中性层曲率半径为P=r+kt,则圆弧部分弧长为: s=Pa式中 a----圆弧对应的中心角,以弧度表示。
3)计算总展开长度L=L1+L2+SL=∑L直+∑S弧4.回弹弯曲成形是一种塑性变形工艺。
回弹的表现形式:1)弯曲回弹会使工件的圆角半径增大,即r2>rp,则回弹量可表示为△r=r2-rp2) 弯曲回弹会使弯曲件的弯曲中心角增大,即a>ap.则回弹量可表示为△a=a-ap影响弯曲回弹的因素:1.材料的力学性能。
2. 材料的相对弯曲半径r/t。
3. 弯曲制件的形状。
4. 模具间隙。
5. 校正程度。
弯曲板件时,凸模圆角半径和中心角可按下式计算:Rp=r/(1+3Asr/Et)ap=ra/rp式中 r----工件的圆角半径;Rp----凸模的圆角半径;a----工件的圆角半径r对弧长的中心角;ap----凸模的圆角半径rp所对弧长的中心角;t----毛坯的厚度;E----弯曲材料的弹性模量;A----弯曲材料的屈服点减小回弹的措施:1)在弯曲件的产品设计时①弯曲件结构设计时考虑减少回弹,在弯曲部位增加压筋连接带等结构。
导向板冲压成形工艺及冲裁模、弯曲模模具设计说明书

1.1国内模具的现状和发展趋势目前,我国冲压技术与工业发达国家相比还相当的落后,主要原因是我国在冲压基础理论及成形工艺、模具标准化、模具设计、模具制造工艺及设备等方面与工业发达的国家尚有相当大的差距,导致我国模具在寿命、效率、加工精度、生产周期等方面与工业发达国家的模具相比差距相当大。
1.1.1国内模具的现状我国模具近年来发展很快,据不完全统计,2003年我国模具生产厂点约有2万多家,从业人员约50多万人,2004年模具行业的发展保持良好势头,模具企业总体上订单充足,任务饱满,2004年模具产值530亿元。
进口模具18.13 亿美元,出口模具4.91亿美元,分别比2003年增长18%、32. 4%和45. 9%。
进出口之比2004年为3.69:1,进出口相抵后的进净口达13.2亿美元,为净进口量较大的国家。
在2万多家生产厂点中,有一半以上是自产自用的。
在模具企业中,产值过亿元的模具企业只有20多家,中型企业儿十家,其余都是小型企业。
近年来,模具行业结构调整和体制改革步伐加快,主要表现为:大型、精密、复杂、长寿命中高档模具及模具标准件发展速度快于一般模具产品;专业模具厂数量增加,能力提高较快;“改革开放以来,随着国民经济的高速发展,市场对模具的需求量不断增长。
近年来,模具工业一直以15%左右的增长速度快速发展,模具工业企业的所有制成分也发生了巨大变化,除了国有专业模具厂外,集体、合资、独资和私营也得到了快速发展。
浙江宇波和黄岩地区的“模具之乡”;广东一些大集团公司和迅速崛起的乡镇企业,科龙、美的、康佳等集团纷纷建立了自己的模具制造中心;中外合资和外商独资的模具企业现已有儿千家。
随着与国际接轨的脚步不断加快,市场竞争的日益加剧,人们已经越来越认识到产品质量、成本和新产品的开发能力的重要性。
而模具制造是整个链条中最基础的要素之一,模具制造技术现已成为衡量一个国家工业发展工业现状的重要度量工具。
近年许多模具企业加大了用于技术进步的投资力度,将技术进步视为企业发展的重要动力。
弹性夹弯曲模具设计
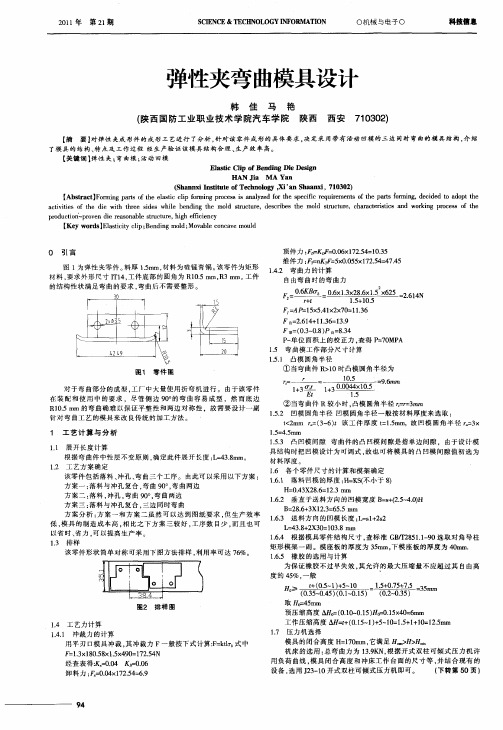
21 年 01
第 2 期 1
S IN E&T C N L G F R A I N CE C E H O O Y N O M TO I
o机械 与电子 0
科技信息
弹性夹弯 曲模具设计
韩 佳 马 艳
( 陕西国防-q ̄,技术学院汽车学院 rl n , ,
【 摘
了模 具 的 结 构 、 点及 工作 过 程 经 生 产 验 证 该 模 具 结 构 合 理 、 产 效 率 高。 特 生
5 I 1
2 0
FⅧ ( .- . ) = . = 03 08 P自 8 4 3 P 单 位 面 积 上 的 校 正 力 . 得 P 7 MP 一 查 =0 A
15 弯 曲模 工 作 部 分 尺 寸 计 算 . 151 凸 模 圆 角 半 径 ..
图1 零件 图
① 当弯 曲件 R 1 >0时凸模 圆角半径 为
HAN i M A Ya Ja n
(h n x n tueo eh oo y, ’IS a n i 7 0 0 ) S a n i s tt fT c n lg XiaI h a x , 13 2 I i
弯曲冲压模课程设计

2设计工艺计算2.1弯曲件展开尺寸的计算根据文献(2)125页, 按圆角半径r=3mm>0.5t=1.5mm的弯曲件计算方法进行计算。
将弯曲件制件分为如图3段图 1-1(1)直边段为L1, L3L1=30-3-3=24mmL3=80-3-3=74mm(2)圆角边段为L2由于R/t=3/3=1>0.5,则该圆角属于有圆角弯曲, 根据中性层长度不变原理计算。
查文献(2)表4-6查得, x=0.32L2=πρ/2=π(r+xt)/2=3.14*(3+0.32*3)/2=6.22mm(3)弯曲毛坯展开总长度:L=L1+L2+L3=24+74+6.22=104.22mm查文献(1)表9-13, 该尺寸采用IT14级, 公差为0.87m2.2冲压力的计算及冲压设备的选择2.1.1冲压力的计算由于弯曲力受到材料的力学性能, 零件形状与尺寸, 板料厚度, 弯曲方式, 模具结构形状与尺寸, 模具间隙和模具工件表面质量等多种因素的影响, 很难用理论分析方法进行准确计算。
因此, 在生产中均采用经验公式估算弯曲力。
查文献(2)130页, L 形弯曲件是在自由弯曲阶段相当于弯曲U 形件的一半, 而且应设置压料装置, 所以可近似地取弯曲力为F L =(F UZ+F Q )/2 (1-1) 其中: FUZ 为弯曲力F Q 为压料力查文献(2)129页, U 形件弯曲时的自由弯曲力tr t 7.0F b 2UZ += σKB (1-2) K 为安全系数, 取1.3b σ=420Mpa,为弯曲材料的抗拉强度t 为弯曲件的厚度, t=3mmB 为弯曲件的宽度, B=30mmr 为内圆弯曲半径(等于凸模圆角半径), r=3mm将数据代入式1-2, 计算, 可得:F UZ =17199N对设置压料装置的弯曲模, 其压料力也要由压力机滑块承担, FQ 可近似取自由弯曲力的30%~60%,即FQ=(0.3~0.6)FUZ 。
, 这里取FQ=0.5FUZ 。
3弯曲模具设计实例(PPT)
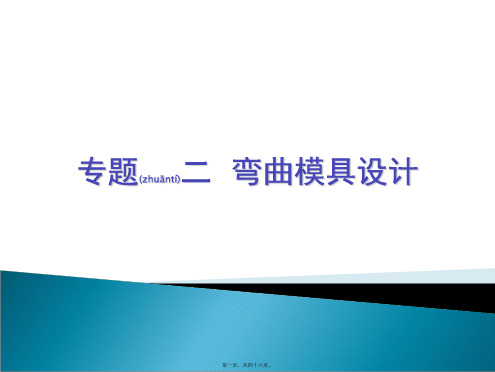
第二页,共四十六页。
2.1.1 弯曲变形过程分析 1. 弯曲变形过程:弯曲变形的含义、变形过程三阶段
、弯曲回弹、自由弯曲、矫正(jiǎozhèng)弯曲。 2. 弯曲变性特点:网格法、中性层 2.1.2 弯曲件质量分析
弯裂、回弹、偏移等
第三页,共四十六页。
2.1.3 弯曲件的工艺性:指弯曲件的结构形状、尺寸 、精度、材料及技术要求(yāoqiú)是否符合弯曲加工的工 艺要求(yāoqiú)。
第十九页,共四十六页。
2.2.1 弯曲模典型结构 模具设计本卷须知:a. 准确、可靠的定位,防止弯
曲中偏移;b. 弯曲结束(jiéshù)时能得到校正力;c. 成形后能方便、平安地取出;d. 考虑磨损,模具 留有修模余量。 弯曲模具分类:单工序模、连续弯曲模、复合弯曲模 和通用弯曲模。
第二十页,共四十六页。
第十页,共四十六页。
5. 增加工艺缺口、槽和工艺孔 a. 为提高精度,对于弯曲时圆角变形区侧面可以
产生畸变(jībiàn)的弯曲件,可以预先在折弯线的两端切 出工艺缺口或槽,以防止畸变(jībiàn)对弯曲件宽度尺寸 的影响。
第十一页,共四十六页。
b. 当工件局部边缘局部弯曲时,为防止弯曲局部受力 不均匀而产生变形和裂纹(liè wén),应于线切槽或冲工艺孔 。
弯曲半径较小、材料强度较大的弯曲件时,必须对
弯曲力进行计算。
a. 自由弯曲时的弯曲力
V形弯曲件 F自=0.6Kbt²σb/(r+t)
U形弯曲件 F自=0.7Kbt²σb/(r+t)
其中:b-弯曲件宽度;t-弯曲件厚度;r-内圆
角弯曲半径;
σb-弯曲材第十七料页,共四的十六页抗。 拉强度〔Mpa〕;K-
V形弯曲件模具设计

V形弯曲件模具设计(一)零件工艺分析工件图为图1所示V形件,材料为Q235,料厚1.5mm。
大批量生产其工艺分析如下:图1弯曲工件图1.材料分析Q235为普通钢,属于软钢,具有良好的弯曲成形性能。
2.结构分析零件结构简单,弯曲成90度,对弯曲成形较为有利,可查得此材料允许的最小弯曲半径rmin =0.5t=0.75mm,而零件弯曲半径r=1mm>0.75mm,故不会弯裂。
另外零件上的孔位于弯曲变形之外,所以弯曲时孔不会变形,可以先冲孔后弯曲。
计算零件相对弯曲半径r/t=0.67<5,卸载后弯曲件圆角半径的变化可以不予考虑,而弯曲中心角发生了变化,采用校正弯曲来控制角度回弹。
3.精度分析零件上尺寸无公差要求,从公差表选取IT14,可满足普通弯曲和冲裁。
4.结论:由以上分析可知,该零件冲压工艺良好,可以冲裁和弯曲。
(二)工艺方案的确定零件为V形弯曲件,该零件的生产包括落料、冲孔和弯曲。
三个基本工序,可有以下四种工艺方案:方案一:先落料,后冲孔,再弯曲。
采用三套工序模生产。
方案二:落料—冲孔复合冲压,再弯曲。
采用复合模和单工序弯曲模生产。
方案三:冲孔—落料连续冲压,再弯曲。
采用连续模和单工序弯曲模生产。
方案四:冲孔落料弯曲,采用多工位级进模方案一模具结构简单,但需三道工序三副模具,生产效率较低。
方案二需两副模具,且用复合模生产的冲压件行位精度和尺寸精度保证,生产效率较高。
方案三也需两副模具,生产效率也很高,但零件的冲压精度稍差。
方案四需一副模具,可以冲裁和弯曲,同时采用了自动送料、自动检测、自动出件等自动化装置,操作安全,具有较高的劳动生产率。
通过对上述四种方案的综合分析比较,该件的冲压生产采用方案四为佳。
图2坯料展开图1.弯曲工艺计算(1)毛坯尺寸计算,对于r>0.5t有圆角半径的弯曲件,由于变薄不严重,按中性层展开的原理,坯料总长度应等于弯曲件直线部分和圆弧部分长度之和,可查得中性层位移系数x=0.28,所以坯料展开长度为Lz=48×2+270π(1+0.28)÷180=102.288≈102mm 由于零件宽度尺寸为40mm,故毛坯尺寸应为102mm×40mm。
弯曲模具设计
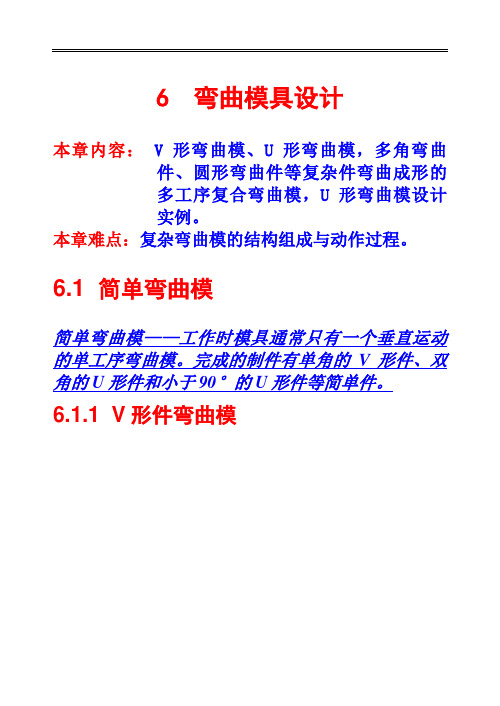
6 弯曲模具设计本章内容: V形弯曲模、U形弯曲模,多角弯曲件、圆形弯曲件等复杂件弯曲成形的多工序复合弯曲模,U形弯曲模设计实例。
本章难点:复杂弯曲模的结构组成与动作过程。
6.1 简单弯曲模简单弯曲模——工作时模具通常只有一个垂直运动的单工序弯曲模。
完成的制件有单角的V形件、双角的U形件和小于90°的U形件等简单件。
6.1.1 V形件弯曲模图6.1 V 形件弯曲模 图6.2 V 形件弯曲模三维模型图6.3 V 形件压板式弯曲模图6.4 V形件折板式弯曲模(a) 开模状态 (b) 合模状态图6.5 V形件折板式弯曲模三维模型V形件折板式弯曲模6.1.2 U形件弯曲模图6.6 U形件的弯曲模图6.7 弯制夹角小于90°的U形件弯曲模弯制夹角小于90°的U形件弯曲模异形U形件弯曲模Z形件弯曲模6.1.3 通用弯曲模图6.8 通用弯曲模6.2 复杂弯曲模复杂弯曲模——在工作时通常具有两个或两个以上的运动,可将多个弯曲变形一次完成。
6.2.1 C形弯曲模图6.9 C形弯曲模图6.10 C形弯曲模立体模型(a) 弯曲初始状态 (b) U形中间弯曲状态 (c) C形最终弯曲状态图6.11 C形件弯曲动作过程四角弯曲模1四角弯曲模2异形件弯曲模6.2.2 O形件弯曲模O形件弯曲模图6.12 滑板式弯曲模图6.13 滑板式弯曲模模型(a) 初始弯曲状态 (b) 中间弯曲状态 (c) 最终弯曲状态图6.14 弯制带有耳翅的环类工件的滑板式弯曲模图6.16 圆形件自动卸料弯曲模图6.17 圆形件自动卸料弯曲模动作过程其他弯曲1其他弯曲26.3 U形弯曲件冲压实例6.3.1工艺分析及工艺方案图6.18 弯曲件材料为35钢板(退火),板厚3mm,大批量生产该零件形状简单,批量生产,精度无特殊要求,结构不对称,应注意弯曲中的偏移问题。
该零件弯曲半径R=5mm,查表5-2可知min ,有R>minr,故此不会弯裂。
- 1、下载文档前请自行甄别文档内容的完整性,平台不提供额外的编辑、内容补充、找答案等附加服务。
- 2、"仅部分预览"的文档,不可在线预览部分如存在完整性等问题,可反馈申请退款(可完整预览的文档不适用该条件!)。
- 3、如文档侵犯您的权益,请联系客服反馈,我们会尽快为您处理(人工客服工作时间:9:00-18:30)。
弯曲模具设计计算说明书设计内容设计说明书 1份模具装配图 1张凸模零件图 1张凹模零件图 1张班级:学号:姓名:指导:2009年12月目录一、模具设计的内容 (3)二、设计要求 (3)三、模具设计的意义 (3)四、弯曲工艺的相关简介 (3)(一)、弯曲工艺的概念 (3)(二)、弯曲的基本原理 (4)(三)、弯曲件的质量分析 (4)(四)、弯曲件的工艺性 (7)(五)、最小相对弯曲半径 (7)五、设计方案的确定 (7)(一)、弯曲件工艺分析 (8)(二)、弯曲件坯料展开尺寸的计算 (8)(三)、弯曲力的计算与压力机的选用 (9)(四)、弯曲模工作部分尺寸设计 (10)六、模具整体结构 (16)七、模具的工作原理及生产注意事项 (18)八、总结 (19)九、参考资料 (20)一、模具设计的内容设计一副如下图所示弯曲件的成形模具:(补充图纸)二、设计要求详尽的设计计算说明书1份、主要零件图、模具装配图1份。
三、模具设计的意义冲压成形/塑料成型工艺与模具设计是机制专业的专业基础课程。
通过模具的课程设计使学生加强对课程知识的理解,在掌握材料特性的基础上掌握金属成形工艺和塑件成型工艺,掌握一般模具的基本构成和设计方法,为学生的进一步发展打下坚实的理论、实践基础。
四、弯曲工艺的相关简介(一)、弯曲工艺的概念弯曲是将金属板料毛坯、型材、棒材或管材等按照设计要求的曲率或角度成形为所需形状零件的冲压工序。
弯曲工序在生产中应用相当普遍。
零件的种类很多,如汽车上很多履盖件,小汽车的柜架构件,摩托车上把柄,脚支架,单车上的支架构件,把柄,门扣,铁夹等。
(二)、弯曲的基本原理以V形板料弯曲件的弯曲变形为例进行说明。
其过程为:1、凸模运动接触板料(毛坯)由于凸,凹模不同的接触点力作用而产生弯短矩,在弯矩作用下发生弹性变形,产生弯曲。
2、随着凸模继续下行,毛坯与凹模表面逐渐靠近接触,使弯曲半径及弯曲力臂均随之减少,毛坯与凹模接触点由凹模两肩移到凹模两斜面上。
(塑变开始阶段)。
3、随着凸模的继续下行,毛坯两端接触凸模斜面开始弯曲。
(回弯曲阶段)。
4、压平阶段,随着凸凹模间的间隙不断变小,板料在凸凹模间被压平。
5、校正阶段,当行程终了,对板料进行校正,使其圆角直边与凸模全部贴合而成所需形状。
(三)、弯曲件的质量分析在实际生产中,弯曲件的质量主要受回弹、滑移、弯裂等因素的影响,重点介绍回弹因素,具体如下。
1、弯曲件的回弹回弹——常温下的塑性弯曲和其它塑性变形一样,在外力作用下产生的总变形由塑性变形和弹性变形两部分组成。
当弯曲结束,外力去除后,塑性变形留存下来,而弹性变形则完全消失。
弯曲变形区外侧因弹性恢复而缩短,内侧因弹性恢复而伸长,产生了弯曲件的弯曲角度和弯曲半径与模具相应尺寸不一致的现象。
这种现象称为弯曲件的弹性回跳(简称回弹)。
弯曲件的回弹现象通常表现为两种形式:一是弯曲半径的改变,由回弹前弯曲半径r0变为回弹后的 r1。
二是弯曲中心角变变,由回弹前弯曲中心角度α0(凸模的中心角度)变为回弹后的工件实际中心角度α1。
2、影响回弹的主要因素1)材料的力学性能金属材料的变形特点与材料的屈服强度成正比,与弹性模数E成反比,即材料的屈服强度σs越高,弹性模量E越小,弯曲弹性回跳越大。
2)相对弯曲半径r/t相对弯曲半径r/t越大,板料的弯曲变形程度越小,在板料中性层两侧的纯弹性变形区增加越多,塑性变形区中的弹性变形所占的比例同时也增大。
故相对弯曲半径r/t越小,则回弹也越小。
3)弯曲中心角α4)弯曲方式及弯曲模板料弯曲方式有自由弯曲和校正弯曲。
在无底的凹模中自由弯曲时,回弹大;在有底的凹模内作校正弯曲时,回弹值小。
原因是:校正弯曲力较大,可改变弯曲件变形区的应力状态,增加圆角处的塑性变形程度。
5)弯曲件形状工件的形状越复杂,一次弯曲所成形的角度数量越多,各部分的回弹值相互牵制以及弯曲件表面与模具表面之间的摩擦影响,改变了弯曲件各部分的应力状态(一般可以增大弯曲变形区的拉应力),使回弹困难,因而回弹角减小。
如Π形件的回弹值比U形件小,U形件又比V形件小。
6)模具间隙在压弯U形件时,间隙大,材料处于松动状态,回弹就大;间隙小,材料被挤压,回弹就小。
3、减少回弹的措施1)选用合适的弯曲材料在满足弯曲件使用要求的条件下,尽可能选用弹性模量E大、屈服极限σs小、加工硬化指数n小、机械性能较稳定的材料,以减少回弹。
2)改进弯曲工艺(1)采用热处理工艺对一些硬材料和已经冷作硬化的材料,弯曲前先进行退火处理,降低其硬度以减少弯曲时的回弹,待弯曲后再淬硬。
在条件允许的情况下,甚至可使用加热弯曲。
(2)增加校正工序运用校正弯曲工序,对弯曲件施加较大的校正压力,可以改变其变形区的应力应变状态,以减少回弹量。
通常,当弯曲变形区材料的校正压缩量为板厚的2%~5% 时,就可以得到较好的效果。
(3)采用拉弯工艺3)改进零件的结构设计在变形区压加强肋或压成形边翼,增加弯曲件的刚性,使弯曲件回弹困难。
4)改进模具结构(1)补偿法利用弯曲件不同部位回弹方向相反的特点,按预先估算或试验所得的回弹量,修正凸模和凹模工作部分的尺寸和几何形状,以相反方向的回弹来补偿工件的回弹量。
(2)校正法当材料厚度在 0.8mm 以上,塑性比较好,而且弯曲圆角半径不大时,可以改变凸模结构,使校正力集中在弯曲变形区,加大变形区应力应变状态的改变程度(迫使材料内外侧同为切向压应力、切向拉应变),从而使内外侧回弹趋势相互抵消。
(3)采用聚氨酯弯曲模利用聚氨酯凹模代替刚性金属凹模进行弯曲,弯曲时金属板料随着凸模逐渐进入聚氨酯凹模,激增的弯曲力将会改变圆角变形区材料的应力应变状态,达到类似校正弯曲的效果,从而减少回弹。
4、回弹值的确定1)小变形(r/t ≥10)自由弯曲时的凸模弯曲角 和凸模圆角半径13T s r r rEtσ=+;0(180)(/1)T T r r ϕϕϕ=---式中:T r ——凸模圆角半径; r ——弯曲件圆角半径;ϕ——弯曲件弯曲角;T ϕ ——凸模弯曲角;s σ——材料屈服点; E ——材料弹性模量; t ——板料厚度; 2)大变形(r/t<5)时弯曲件圆角半径变化很小,而只修正弯曲角。
对于弯曲件弯曲角不为90°时回弹角:'00(180)/90ϕϕϕ∆=-⨯∆式中:'ϕ∆——弯曲角为ϕ时的回弹角;ϕ——弯曲件弯曲角;ϕ∆——弯曲角为90°的回弹角;模具设计时,当弯曲件弯曲角090ϕ=时,取凸模角度T ϕϕϕ=-∆;当090ϕ≠时,取凸模角度'T ϕϕϕ=-∆,通过试模来进行修正。
该弯曲件弯曲角都为90°,其回弹角查表-1得01.5ϕ∆=,则00090 1.588.5T ϕϕϕ=-∆=-=其他影响因素 1、弯曲件的弯裂弯曲件变形区外边是拉伸区,当此区的拉应力超出材料的应力极限时(强度极限)就产生裂纹。
弯曲件的相对弯曲半径r/t 越小,则变形越大,越易拉裂。
2、弯曲件的滑移由于毛坯与模具之间磨擦的存在,当磨擦力不平衡时造成毛坯的移位,称作滑移,使弯曲件的尺寸达不到要求:1) 产生滑移的原因:由于两边磨擦力不等。
工作不对称,毛坯两边与凹模接触面不相等;凹模两边的边缘圆角半径不相等,半径小,磨擦力更大;两边折弯的个数不一样;V 形弯曲中凹模不是中心对称,角度小的一边正压力大,磨擦大; 凹模两边的间隙和润滑情况不一样。
2)防止滑移的措施尽可能采用对称凹模,边缘圆角相等,间隙均匀;采用弹性顶件装置的模具结构;采用定位销的模具结构。
(四)、弯曲件的工艺性1、最小弯曲半径:在保证外层纤维不发生破坏的条件下,所能弯曲零件内表面的最小圆角半径,称作弯曲件的最小弯曲半径,表示弯曲时的成形极限。
最小弯曲半径的影响因素:材料的力学性能;弯曲线的方向:由于板料的扎制造成板料性能和各项异性,扎制方向塑性较好,使弯曲的切向变形方向与扎制方向一致;板料宽度:宽度加大,最小弯曲半径增大;板料的表面质量;弯曲角;板料的厚度。
2、弯曲件直边高度弯曲件的弯曲边高度不宜太小,h>R+2t,如弯曲边高度太小,则难以形成足够的弯矩。
(五)、最小相对弯曲半径max11123 12122rtθε===++⨯;minmax111(1)(31)122rtθε=-=⨯-=;而弯曲件的相对弯曲半径为:212rt==,所以minrrt t=在弯曲工艺时不必采取特殊工艺措施。
五、设计方案的确定(一)、弯曲件工艺分析该弯曲件名为压块,形状对称,尺寸无精度要求,材料是Q235A,普通碳素钢。
采用复合模冲压成形,其需要经过三道工序完成:落料、冲中间孔、复合弯曲、冲两侧孔。
落料工序已经在上道工序中冲制完成。
本模具是完成1个U形和2个V形弯曲的冲压工艺,弯曲角都是90°。
(二)、弯曲件坯料展开尺寸的计算(补充图纸)1、中性层的确定由于中性层的长度在弯曲变形前后不变,其长度就是弯曲件坯料展开尺寸的长度。
而欲求中性层长度就必须找到其位置,用曲率半径ρ表示。
中性层位置与板料厚度t、弯曲半径r、变薄系数ξ等因素有关,在实际生产中为了使用方便,通常采用下面的经验公式来确定中性层的位置:0r xt ρ=+式中:0ρ——中性层半径;r ——弯曲件内弯半径;x 为中性层位移系数,其值件下表:表-2从弯曲件图可以看到:圆角半径都为r=2mm ,板料厚度t=2mm ,查表-2得x=0.32,则中性层半径为:020.322 2.64r xt mm ρ=+=+⨯=2、毛坯展开尺寸的计算由于圆角半径r>0.5t ,所以毛坯展开长度等于弯曲件直线部分长度与弯曲部分中性层展开长度的总和,即0()180ii i i L l r x t πα=∑+∑+。
弯曲件有5段直线部分和4段弯曲部分,因此220.5212424 2.64123.582L mm π=⨯+⨯++⨯⨯=(三)、弯曲力的计算与压力机的选用1、弯曲力的计算弯曲力是指弯曲件在完成预定弯曲时所需要的压力机施加的压力,是设计冲压工艺过程和选择设备的重要依据之一。
弯曲力的大小与毛坯尺寸、零件形状、材料的机械性能、弯曲方法和模具结构等多种因素有关,理论分析方法很难精确计算,在实际生产中常按经验公式进行计算。
1)自由弯曲时的弯曲力公式V 形弯曲件:20.6b Vz KBt F r t σ=+ ; U 形弯曲件:20.7b Uz KBt F r tσ=+;式中:Vz F 、Uz F ——自由弯曲力;B ——弯曲件的宽度;t ——弯曲件厚度;r ——内圆弯曲半径;b σ——弯曲材料的抗拉强度;K ——安全系数,一般取1.3。
2)、校正弯曲力公式J q F F A =式中:J F ——校正力;q F ——单位面积上的校正力,Mpa ,见表-3;A ——弯曲件被校正部分的投影面积,mm 2。