HORSEMAN_L系列英日文说明书
摩里森兄弟公司 354系列上升式风口帽说明书

! !The 354 Series Updraft Vent is designed for use on underground and aboveground storage tanks. If properly sized, installed and maintained the vent allows the tank to “breathe” during fi lling and dispensing operations.Failure to follow any or all of the warnings and instructions in this document could result in a hazardous liquid spill, which could result in property damage, environmental contamination, fi re, explosion, serious injury or death.InstallationWarnings• Fire Hazard – Death or serious injury could result from spilled liquids.• Install only on shop fabricated atmospheric tanks built and tested in accordance to industry standards such as UL142, NFPA 30 & 30A, and API 650.• Install in accordance with all applicable local, state, and federal laws.• 354 Series vents must be properly sized and selected for each specifi c tank application.• For your safety, it is important to follow local, state, federal and/or OSHA rules that apply to working inside, above, or around the storage tank and piping area. Use all personal protective equipment required for working in the specifi c environment.• Tanks could be under pressure. Vapors could be expelled from tank vents, piping, valves or fi ttings while performing installation. Vapors could catch fi re or cause an explosion. Avoid sparks, open fl ame, or hot tools when working on vents.Steps1. Inspect unit for shipping damage. Do not use if damage is found.2. Check vent openings for foreign matter such as packaging material. Remove any that is found.3. Insure mounting pipe (riser) is in the vertical (plumb) position.4. Slip vent over riser pipe and tighten the two (2) set screws on the sides of the vent.5. Do not paint or cover the vent in any manner. This may inhibit proper vent operation.Note: There should be no reduction of pipe size between the storage tank and the Fig. 354 Series Updraft Vent.Important: Install the included warning tag where it will be visible to the operator fi lling or unloading the tank that is fi tted with this vent.Failure to follow any or all of the warnings and instructions in this document could result in a hazardous liquid spill, which could result in property damage, environmental contamination, fi re, explosion, serious injury or death.354 Series Updraft Vents Installation & Maintenance Instructions!MaintenanceMonthly inspection, and immediate inspection during freezing conditions, by someone familiar with the proper operation of the storage tank vents, is required to insure venting devices are functioning properly before fi lling or unloading a tank.WARNINGS• Fire Hazard – Death or serious injury could result from spilled liquids.• Clogged or restricted vents could cause damage to tanks and piping releasing liquids which could catch fi re.• Dust, debris, freezing rain, freezing condensation or other contaminants could clog or restrict the vents.• In freezing conditions, inspect the vents immediately before fi lling or unloading a tank.• Follow your employer’s instructions for making sure vents are not clogged or restricted.• You must be trained to inspect the vents. Stop now if you have not been trained.• Do notfi ll or unload from a tank unless you are certain that the tank vents will operate correctly.• For your safety, it is important to follow local, state, federal and/or OSHA rules that apply to working inside, above, or around the storage tank and piping area. Use all personal protective equipment required for working in the specifi c environment.• Tanks could be under pressure. Vapors could be expelled from tank vents, piping, valves or fi ttings while performing maintenance. Vapors could catch fi re or cause an explosion. Avoid sparks, open fl ame, or hot tools when working on vents.Steps1. Remove the vent by loosening the two (2) set screws and lifting the vent up off the riser pipe.2. Remove the three (3) screws holding the cover on the vent and remove the cover.3. Lift the screen carefully out of the body and clean. Compressed air can be used to clean screen.4. Replace screen if it cannot be cleaned. Replacement screens are available from Morrison Bros. Co.5. With the cover removed inspect the body and drain holes for dust, debris, snow or ice. Remove all such matter.6. Re-install the screen.7. Re-install the cover and screws.8. Re-install the vent onto the riser pipe and tighten the two (2) set screws.9. Inspect the vent warning tag located near the tank fi ll and offl oading area. If the tag is damaged or diffi cult to read, contact Morrison Bros. Co. at (800) 553-4840 for a free replacement tag.During maintenance procedure inspect all vent components and surfaces for damage, corrosion or excessive wear. If any is found, replace the vent.Failure to follow any or all of the warnings or instructions in this document could result in a hazardous product spill, which could result in property damage, environmental contamination, fi re explosion, serious injury or death.!。
奥克玛生产商品名称说明书

Live ToolingOKUMA CAPTAIN SERIES LATHES L370-M, L370-MW, L470-M, GENOS L-300M2Fax: (847) 367-4815Email:************************** Standard: 1) straight2) 90º (reducer/speeder)Offset Multi Output: 1) straight Adjustable Y straight Adjustable Angle Fixed Angle2) 90ºOf set: 1) straight2) 90ºSaw Blade Holder: 1) straight2) 90ºMulti Output: 1) straight2) 90ºSpecialsCustom-made live tools can be engineered for your specificO K U M A L I V E T O O L I N GSpecial Live Tool Inquiry Form2Table of Contents3Lyndex-Nikken is an official Okuma Live Tool supplier and a member of Partners in THINC.Lyndex-Nikken live tools aremanufactured by Alps Tool Co. Ltd.Parts inventory, maintenance and repair, and rebuild services are Okuma Face Mount TurretCommonly Referenced:Axial Live Tools Straight Live Tools Z-Axis Live ToolsCommonly Referenced:Radial Live Tools90 or Angle Live Tools X-Axis Live ToolsPart numbering structure for Lives Tools4Live Tooling for Face Mount Turretsmanufacturers who share your philosophy in producing live tools join you in doing what you do best- machining the highest quality parts.Enhanced with Alps/Lyndex-Nikken live tooling, your Okuma machine will allow you to reduce cycle times, eliminate extra operations and achieve maximum efficiency .5FEATURES AND TECHNOLOGYProtective Seals• Labyrinth Seals - provide a high-pressure multi-barrier construction that prevents contaminants and coolant from entering the main chamber.Gears for Stability• Gear Pairing - hand-matched for each pair to minimize backlash.• Gear Design - custom ground spiral bevel gear tooth design maximizes drive torque output and reduces tooth root stress allowing for more tool longevity.• Gear Equilibrium - placement of bearings balance torque stress evenly through input/output shafts.Eccentric Bearing Nut• Ground Eccentric Nut - allows for fine accuracy and strong tool shank gripping capacity by preventing collet twisting or rocking.• Runout - guarantee of under 5-micron repeatability at collet nose.Tool Design and Engineering• Tool Body - manufactured from the highest tensile and compression Nickel Chrome Molybdenum alloys.• Drive Shafts - all features are ground on both the input and output Chrome Molybdenum drive shafts to assure proper torque transmission and precision concentricity.• Bearing Quality - only the highest precision ABEC 7angular contact bearings are used for smooth and high speed rotation.• Quality Control - all live tools go through a vigorous 60-point final inspection to satisfy the highest expectations of live tool performance.As an authorized OEM supplier to Okuma, Lyndex-Nikken live tools are designed and manufactured in conjunction with Okuma engineers at the factory in Japan.Clockwise InputClockwise OutputExternal or Internal Coolant Radial/AxialMax.RPMGearRatioMax. TorqueOutputMax. PressureExternal Radial45001:117.3 ft-lbs(24N-m)1000 PSIOK105-00100OK116-20200OK116-70610FK-8Clockwise OutputExternal or Internal Coolant Radial/AxialMax.RPMGearRatioMax. TorqueOutputMax. PressureInternal Radial45001:117.3 ft-lbs(24N-m)1000 PSIOK105-00100OK116-20200OK116-00800PM2B-1FK-8Please refer to pages 14 - 17 for ER Series Collets and ER Tap Collets details.This tool requires a minimum 20 micron filter and cannot be run dry.Please refer to pages 14 - 17 for ER Series Collets and ER Tap Collets details.Clockwise InputClockwise InputClockwise OutputExternal or Internal Coolant Radial/AxialMax.RPMGearRatioMax. TorqueOutputMax. PressureInternal Axial45001:117.3 ft-lbs(24N-m)1000 PSIOK105-00100OK116-20200OK116-00700PM2B-1 & EXTGSF-1-24FK-8Clockwise OutputExternal or Internal Coolant Radial/AxialMax.RPMGearRatioMax. TorqueOutputMax. PressureExternal Axial45001:117.3 ft-lbs(24N-m)1000 PSIOK105-00100OK116-20200OK116-00700OK116-70060FK-8Please refer to pages 14 - 17 for ER Series Collets and ER Tap Collets details.This tool requires a minimum 20 micron filter and cannot be run dry.Please refer to pages 14 - 17 for ER Series Collets and ER Tap Collets details.Clockwise InputExternal or Internal Coolant Radial/AxialMax.RPMGearRatioMax. TorqueOutputMax.PressureExternal Adjustable40001:17.37 ft-lbs(10N-m)1000 PSIOK116-20200FK-7E20AXPlease refer to pages 14 - 17 for ER Series Collets and ER Tap Collets details.Clockwise Output Clockwise InputClockwise OutputExternal or Internal Coolant Radial/AxialMax.RPMGearRatioMax. TorqueOutputMax.PressureExternal Offset(M)45001:117.3 ft-lbs(24N-m)1000 PSIOK116-20200OK116-00500OK116-70060FK-8Please refer to pages 14 - 17 for ER Series Collets and ER Tap Collets details.Clockwise InputCounterclockwise OutputExternal or Internal Coolant Radial/AxialMax.RPMGearRatioMax. TorqueOutputExternal Axial45001:117.3 ft-lbs(24N-m)NA 32OK116-20200OK116-70060FK-8Please refer to pages 14 - 17 for ER Series Collets and ER Tap Collets details.Clockwise InputExternal or Internal Coolant Radial/AxialMax.RPMGearRatioMax. TorqueOutputMax.PressureExternal Offset(D)45001:117.3 ft-lbs(24N-m)1000 PSIOK116-20200OK116-00500FK-8On the main spindle, the clutch shaft and the collet shaft rotate in the same direction; on the sub spindle, they rotate in opposite directions.Please refer to pages 14 - 17 for ER Series Collets and ER Tap Collets details.Clockwise InputClockwise OutputExternal or Internal Coolant Radial/AxialMax.RPMGearRatioMax. TorqueOutputMax. PressureExternal Radial45001:117.3 ft-lbs(24N-m)1000 PSIOK116-20200OK116-00800OK116-70610FK-8Please refer to pages 14 - 17 for ER Series Collets and ER Tap Collets details.Clockwise OutputExternal or Internal CoolantRadial/Axial Max.RPM Gear Ratio Max. Torque Output Pressure ExternalRadial 30001:126.0 ft-lbs (35.3N-m)1000 PSIOK116-70980OK116-20300OK116-01000OK116-70930FK-9External or Internal CoolantRadial/Axial Max.RPM Gear Ratio Max. Torque Output Max.Pressure InternalRadial30001:126.0 ft-lbs (35.3N-m)1000 PSIOK116-20300OK116-01000OK116-70930FK-9Please refer to pages 14 - 17 for ER Series Collets and ER Tap Collets details.This tool requires a minimum 20 micron filter and cannot be run dry.Please refer to pages 14 - 17 for ER Series Collets and ER Tap Collets details.Clockwise InputClockwise OutputClockwise InputUnit:mm [inch]Clockwise OutputExternal or Internal CoolantRadial/Axial Max.RPM Gear Ratio Max. Torque Output ExternalAxial30001:126.0 ft-lbs (35.3N-m)OK116-20300OK116-00900OK116-70930FK-9External or Internal CoolantRadial/Axial Max.RPM Gear Ratio Max. Torque Output InternalAxial30001:126.0 ft-lbs (35.3N-m)OK116-20300OK116-00900OK116-70930FK-9Please refer to pages 14 - 17 for ER Series Collets and ER Tap Collets details.This tool requires a minimum 20 micron filter and cannot be run dry.Please refer to pages 14 - 17 for ER Series Collets and ER Tap Collets details.Clockwise InputClockwise OutputClockwise InputExternal or Internal Coolant Radial/AxialMax.RPMGearRatioMax. TorqueOutput PressureExternal Adjustable40001:17.37 ft-lbs(10N-m)1000 PSIOK116-20300FK-7E20AXPlease refer to pages 14 - 17 for ER Series Collets and ER Tap Collets details.Clockwise InputClockwise OutputSTANDARD (INCH)STANDARD (METRIC)ER Standardtype colletER Counter-Boredtype collet14COOLANT (INCH)COOLANT (METRIC)15ER Tap Collets feature a unique design that incorporates an internal square drive with our popular ER Series collets. The square drive matches the tap square, providing a tight fit for all rigid tapping applications.1617Lyndex-Nikken has now combinedthe versatility of our ER tapping collets with the popularity of our coolant collets to create our patented ER Coolant Tap Collets.Note:Seals up to maximum coolant pressure of 1000 PSI.18Wrench InstructionsAfter securing the setting fixture inposition, apply spanner wrenchonto collet nut.to tighten.Insert setting f ixture behindcollet nut.Service and SupportLyndex-Nikken is dedicated to providing not only the highestquality of equipment, but also the highest quality of serviceand customer care. With over 60 years of experience, ourservice engineers are looking forward to supporting yourneeds beyond your expectations.We fully stock all internal components to provide anexpedited and cost-effective maintenance program andrebuild package for your live tooling. Managing amaintenance schedule for all your machine tool accessorycomponents can be challenging, so we’ll be glad to remindyou when the time comes.Furthermore, to prevent an interruption in your productionschedule, for certain models we can offer a “loaner” live toolwhile your live tool is under repair.Warranty:1 year warranty for internal components2 year manufacturer warranty on external bodyFor any service request or inquiry, please contact our servicedepartment: (847) 367-480012319The TQW T orque Wrench is very accurate and easy-to-use, guaranteeing maximum accuracy and preventing tool overtightening or breakage.• Variable torque adjustable wrench • Robust and durable • Ergonomic grip• Easy to read inch and metric scale• Strong steel shaft is highly corrosion resistant • Easy to set up and operation:A. Set wrench to desired torque settingB. Insert attachmentC. Torque down on collet nut until it clicks in placeHandle is shaped to provide a firm and ergonomic grip.A wide selection of attachments are available: ER, SK, TG, Pull Stud, Milling Chuck, CaptoA ”Push-Button Locking Device”securely locks the preset torque and prevents inadvertentadjustment.Design and Construction (800) 543-6237 CAT2011-OK-CAP。
松下 骑马健身器 说明书

安全注意事项为确保本机的正确操作,使用前请仔细地阅读本安全注意事项。
列出这些安全注意事项的目的,就是为了告诉您正确和安全地使用本机,以免自己和他人受到伤害以及财产损失。
安全注意事项的详细说明如下。
一定要遵守下列重要的安全注意事项!警告:该信息表示有潜在危险的动作和状况,如果不加以避免,可能会导致死亡或严重伤害。
注意:该信息表示有潜在危险的动作和状况,如果不加以避免,可能会导致人员伤害和财产损失。
安全注意图标此符号表示禁止的行为。
此符号表示应遵守的强制性内容或指示的内容。
阅读这些安全注意事项后,请将手册置于使用者可看得见的地方,以备随时参考。
警告!强制!●正接受医生治疗时或下述患者请务必在与专门医生商谈后方可使用。
(1) 现在正腰疼者或过去腿、腰、颈曾经受过伤者,腿、腰、颈和手麻木者(有椎间盘突出、脊椎滑脱症、颈椎突出等宿疾者)(2) 有变形性关节炎、风湿症、痛风病者(3) 有骨疏松症等异常者(4) 有循环系统障碍(心脏病、血管障碍、高血压症等)者(5) 呼吸器官有障碍者(6) 正在使用人工心脏起搏器等植入体内型医疗电子产品者(7) 有恶性肿瘤者(8) 有血栓症或严重的动脉瘤、急性静脉瘤等血流障碍或各种皮肤炎及皮肤感染症等症状者(9) 有因糖尿病等引起的高度末梢循环障碍所引起的知觉障碍者(10)皮肤有创伤者(11)因生病等而发高烧者(38℃或以上)(12)背骨有异常者或背骨弯曲者(13)正在妊娠或可能妊娠者或正处于经期者(14)感到身体异常,需要静养者(15)明显身体状况不佳时(16)以康复为目的而利用者(17)除上述情况以外特别感到身体有异常时- 可能导致事故或身体状况不佳。
●在运动过程中感觉腰痛、腿脚麻木、头晕、心跳等身体与平时不同的疼痛或不协调的感觉或异常时,立即停止使用并向医生咨询。
●上下本机器时为了防止跌倒,要注意脚不要挂到脚镫。
- 如不遵守,将损害健康,有受伤的危险。
●不要让儿童使用本产品。
克罗尔自动洗车设备有限公司 商业跳跃启动器 充电器 产品说明书

Clore Automotive • Kansas City, MO 64161 • • 913.310.1050Owner’s Manual Model Nos. 2001/3001Commercial Jump Starter/ChargersOPERATING INSTRUCTIONSOPERATING THE UNIT AS A JUMP STARTERWarning: DO NOT JUMP START WHILE THE UNIT IS PLUGGED INTO 110 AC POWER SOURCE!NEVER JUMP START A FROZEN BATTERY!A SPARK NEAR BATTERY MAY CAUSE BATTERY EXPLOSION – FOLLOW INSTRUCTIONSBELOW TO REDUCE RISK OF A SPARK NEAR BATTERY.1. Position DC jumper cables to reduce risk of damage by hood, door, or moving engine part.2. Stay clear of fan belts, pulleys, and other parts that can cause injury to persons.3. Check polarity of battery posts. POSITIVE (POS, P, +) and NEGATIVE (NEG, N, –).4. Determine which post of battery is grounded (connected) to the chassis. If negative post is groundedto chassis (as in most vehicles) see step 5a. If positive post is grounded to the chassis, see step 5b.5. a) For negative-grounded vehicle, connect POSITIVE (RED) grip from unit to POSITIVE (POS, P, +)ungrounded post of battery. Connect NEGATIVE (BLACK) grip from unit to vehicle chassis or engine block away from battery.b) For positive-grounded vehicles only, connect NEGATIVE (BLACK) grip from unit to NEGATIVE(NEG, N, –) ungrounded post of battery. Connect POSITIVE (RED) grip from unit to vehicle chassis or engine block away from battery. (This arrangement is usually found in pre-1970 foreign vehicles orpre-1970 farm tractors. This is a rare occurrence.)Note: Do not connect grip to carburetor, fuel lines, or sheet-metal body parts.Connect to a heavy gauge metal part of the frame or engine block.6. After jump starting vehicle, disconnect the unit from the vehicle. When disconnecting unit, ALWAYS remove grip from vehicle chassis first, then remove grip from battery terminal second.OPERATING THE UNIT AS A BATTERY CHARGER (USE ON LEAD-ACID BATTERIES ONLY) Warning: DO NOT JUMP START WHILE THE UNIT IS PLUGGED INTO 110 AC POWER SOURCE!NEVER JUMP START A FROZEN BATTERY!A SPARK NEAR BATTERY MAY CAUSE BATTERY EXPLOSION – FOLLOW INSTRUCTIONSBELOW TO REDUCE RISK OF A SPARK NEAR BATTERY.1. Position DC jumper cables to reduce risk of damage by hood, door, or moving engine part.2. Stay clear of fan belts, pulleys, and other parts that can cause injury to persons.3. Check polarity of battery posts: POSITIVE (POS, P, +) and NEGATIVE (NEG, N, –).4. Determine which post of battery is grounded (connected) to the chassis. If negative post is groundedto chassis (as in most vehicles) see step 5a. If positive post is grounded to the chassis, see step 5b.5. a) For negative-grounded vehicle, connect POSITIVE (RED) grip from unit to POSITIVE (POS, P, +)ungrounded post of battery. Connect NEGATIVE (BLACK) grip from unit to vehicle chassis or engine block away from battery.b) For positive-grounded vehicles only, connect NEGATIVE (BLACK) grip from unit to NEGATIVE(NEG, N, –) ungrounded post of battery. Connect POSITIVE (RED) from unit to vehicle chassis orengine block away from battery.6. Do not connect grip to carburetor, fuel lines, or sheet-metal body parts. Connect to a heavy gauge metal part of the frame or engine block.7. Connect AC power cord to 110 AC outlet. When battery being charged is fully charged, the ampere gauge (on front panel) will flicker on “0”.8. Upon completion of charging, disconnect unit from vehicle. When disconnecting unit, ALWAYS remove grip from vehicle chassis first, then remove grip from battery terminal second.OPERATING THE UNIT AS AN AIR COMPRESSOR (Model No. 3001 Only)Warning: DO NOT INFLATE TIRES OR FLIP AIR COMPRESSOR “ON/OFF” SWITCH WHILE THE UNIT IS PLUGGED INTO 110 AC POWER SOURCE!1. Snap air chuck on tire valve stem (some wheel covers may require use of valve stem extension).2. Flip “ON/OFF” air switch on front panel to “ON” position.3. Tire will inflate to preset pressure and compressor will shut off.4. Disconnect air chuck from tire valve stem (compressor will come on again).5. Flip “On/Off” air switch on front panel to “Off” position.6. See Compressor section below to adjust shut off pressure.Adjusting the Compressor Shut Off Pressure1. Remove back panel by removing (2) 1/4” – 20 bolts securing panel.2. Locate the pressure switch and set screw (center of switch).3. When adjusting shut-off pressure, turn no more than 1/2 turn between settings.4. To increase pressure setting, turn clockwise (1/4 turn = approximately 4 lb.).5. To decrease pressure setting, turn counter- clockwise (1/4 turn = approximately 4 lb.).6. Check pressure setting by inflating a tire and checking tire pressure with an air gauge. If more adjustment is necessary, return to step 4 or 5.7. Secure back panel with (2) 1/4” – 20 bolts bolts.RECHARGING THE UNITThe charging circuitry in your unit utilizes a multi-phase, smart charging routine for more beneficial charging of the onboard battery for enhanced reserve capacity and longer battery life.The charging circuitry features the ability to properly charge both Standard Flooded and AGM batteries. This is an important enhancement, as AGM batteries are designed for better cycling (charge/discharge) longevity and are spill-proof, which is important in a mobile application such as this. • A ll units ship with the charging mode set to the Standard Flooded Battery charging setting. This setting should be changed if you choose to install an AGM battery in your unit. To change this setting, locate the control switch on the charging board inside the unit and change the setting to AGM mode.• T ake care to ensure that cables and clamps are properly stored and secure and that the AC power cord is not damaged in any way.• Connect the AC power cord to a properly grounded outlet.• T he charging routine is fully automatic and will bring the onboard battery to full charge and then turn off. The charger will turn back on if the battery discharges for any reason.• The charger can be left connected to the AC outlet with no harm to the onboard battery.Air Hose Connector Pressure Set ScrewCompressorTROUBLESHOOTINGPROBLEM: Unit does not jump start.POSSIBLE CAUSE SOLUTIONPoor grip connection Check grip connectionLow/defective battery Load test/charge/replace batteryLoose jumper cable connection to battery Tighten battery connections PROBLEM: Unit does not charge.POSSIBLE CAUSE SOLUTIONPoor grip connection Check grip connectionFaulty 110 AC outlet Check or change outletBad plug on unit Check continuity of plug pins/replace plug Loose/defective connections Check unit for loose connectionsDefective amp gauge Replace gaugeFaulty charger Replace charger PROBLEM: Unit does not inflate tires.POSSIBLE CAUSE SOLUTIONLow/defective battery indicated by Recharge/replace batteryclicking of circuit breakerLoose/defective connections Check unit for loose connectionsDefective air pressure switch Replace pressure switchDefective “On/Off” switch Replace “On/Off” switchDefective compressor Replace compressorFor Diagnostic and Repair Help, call the Clore Automotive Technical Service Hot Line at (800) 328-2921 or visit LIMITED WARRANTYClore Automotive, LLC warrants your SOLAR Commercial Jump Starter/Charger to be free from defectsin material and workmanship for a period of one year from the date of sale to the original user or consumer purchaser. If your SOLAR Commercial Jump Starter/ Charger malfunctions or fails within the first 30 daysof the warranty period because of a defect in material or workmanship, we will replace it. If your SOLAR Commercial Jump Starter/Charger malfunctions or fails within the 12 month warranty period because ofa defect in material or workmanship, we will repair it without charge.This warranty is in lieu of all other express warranties. The duration of any implied warranty, including but not limited to any implied warranty of merchantability or fitness for a particular purpose, made in respect to your SOLAR Commercial Jump Starter/Charger is limited to the period of the express warranty set forth above.This warranty excludes and does not cover defects, malfunctions, or failures of your SOLAR Commercial Jump Starter/Charger which were caused by repairs made by an unauthorized person, mishandling, modifications, normal wear, unreasonable use or damage to the SOLAR Commercial Jump Starter/Charger while in your possession. This warranty applies neither to battery, deterioration of the battery, nor damageto the unit caused by the use of a faulty battery.In no event shall Clore Automotive, LLC be liable for consequential or incidental damages. Some statesdo not allow limitations on the length of the implied warranty or the exclusion or limitation of incidental or consequential damages so the above limitations or exclusions may not apply to you. This warranty givesyou specific legal rights and you may also have other rights which vary from state to state. ArrayOwner’s ManualModel Nos. 2001/3001CommercialJump Starter/ChargersREAD CAREFULLYBEFORE OPERATING UNIT!WARNING: This product contains chemicals, including lead, knownto the State of California to cause cancer, birth defects and otherreproductive harm. Wash hands after handling.Clore Automotive • Kansas City, MO 64161 • • 913.310.1050© 2011 Clore Automotive 841-023-000 AWARRANTY AND TECHNICAL SUPPORT REGISTRATIONPlease complete the attached registration card to be eligible to receive FREE technical support, product updates and warranty service.TECHNICAL SUPPORTTechnical support is available to registered users only.Call (800) 328-2921 Monday through Friday, 8:00 AM to 4:30 PM CST.THREE EASY WAYS TO REGISTER1. Mail in the completed registration card below OR2. Fax the completed registration card to (800) 716-6531 OR3. Register your product online at .(Complete information below, detach at perforation and mail)WARRANTY AND TECHNICAL SUPPORTREGISTRATION CARDModel Number:____________________________________________________ Date of purchase:___/___/___ Purchased from:_______________________ Company Name:___________________________________________________ Shipping Address:__________________________________________________ City:______________________ State:_________ Postal Code:______________ Country:_______________ Contact Name:_______________________________ Telephone:( ) _________________ Fax: ( ) ___________________ E-mail Address:____________________________________________________ _。
霍金斯公司产品说明书

U F A C T U R I N G • Q U A L I T Y • S E R V I C E • M A N U F A C T U R I N G • Q U A L I T Y • S E R V I C E • M A N U F A C T U R I N G • Q U A L I T Y • S E R V I C E • M A N U F A C TDixon Sanitary Solutions for the Personal Care Market • Customer Service: 800.789.1718Dixon Sanitary • 800.789.1718Personal CareAseptic Seat ValvesFeatures:• PTFE bellows • B ody machined from solid bar • M anual or automated• Various control top options • 3A certified and CIPable Sizes:• 1" to 4"Applications:• Aseptic isolation • Aseptic diversion • Flow control Material:•316LBC/BP Series Centrifugal PumpsApplications:• Unloading • Transfer • CIP supplyMaterials:• 316L • B una, EPDM, silicone, or FKM elastomersFeatures:• I mpeller retainer or threaded impeller nut options • Stamped volute • W et ends, motor pump units, and carts• 3A certified and CIPable Sizes :• Inlet: 1½" to 6"•Outlet: 1½" to 4"JRZL SeriesPositive Displacement PumpsApplications:• Unloading • Fluid transfer • Metering • CIP supply Material:• 316L Features:• Front loading seals • Various rotor options • 1"- 4" models: stainless steel gear box standard •3A certified and EHEDG certified• 100% CIPable Sizes:• 1" to 10"SSV Series Seat ValvesFeatures:• B ody machined from solid bar• Field serviceable• Various control top options • 3A certified and CIPable Sizes:• 1" to 4"Applications:• Isolation • Diversion Material:• 316LDixon Sanitary 3 • 800.789.1718Personal CareBio-Pharmaceutical FittingsFinish:• PL finish- SF1• P M finish- SF4Sizes:• ½" to 6"Material:•316LExD Series "The Hawk"High Efficiency Centrifugal PumpApplications:• CIP• Fluid transfer • FillingMaterials:• 316L • B una, EPDM, silicone, or FKM elastomersFeatures:• N ut-less impeller and leak detection port•A djustable discharge port rotates 105° without disassembly of casing and front cover • 3A certified and CIPable Sizes:• I nlet: 1" to 4"• Outlet: 1" to 2½"Bio-Check Sampling Valve Application:• Aseptic sampling Material:• 316LFeatures:• Valve body from solid bar • M anual override on actuated valve • 3A and EHEDG certified • CIPable Size:•13mm x 1.5mmHSG Series Sight GlassFeatures:• H igher pressure ranges than other sight glasses •E asy assembly and disassembly • 3A certified and CIPable Sizes:• S ingle pin clamp: 1" - 6", EPDM or FKM gasket • B olted clamp: ½" - 6", PTFE gasketApplication:• View products and fluids Materials:• Body: 316L stainless steel • S ight glass: polycarbonate • G askets: PTFE, EPDM,or FKMDixon ®, founded in 1916, is a premier manufacturer and supplier of hose couplings, valves, dry-disconnects, swivels, and other fluid transfer and control products. The company’sglobal reach includes a wide range of products for numerous industries including petroleum exploration, refining,transportation, chemical processing, food & beverage, steel, fire protection, construction, mining and manufacturing.Dixon ®’s strategic objective is to create solutions that make products safer, leak-free, longer lasting, and always available.N25 W23040 Paul Road, Pewaukee, WI 53072Fax: 800.789.4046****************************For complete catalog and literature downloads go to .Dixon Sanitary© 2019 DVCC Printed in the USA DSPCB11192P500 • Customer Service: 800.789.1718。
马赫德锐1250巡洋艇说明书

page 35LOA to Transom 50´0˝ 15.24 m LOA53´4˝ 16.26 mLOA OB/Trailered 53´10˝/56´3˝ 16.41/17.15 m Maximum Beam 14´6˝ 4.42 m Approximate Weight 43,400 lbs 19,686 kg Cabin Headroom 6´7˝ 2.01 m Fuel Capacity650 gal 2,460 L Diesel Capacity - generator 50 gal 189 L Water Capacity100 gal 380 L Holding Tank Capacity60 gal 227 L Bridge Clearance (w/radar, mast down) 11´10˝ 3.61 m Bridge Clearance (w/mast & VHF antennas up) 19´5˝ 5.92 m Draft 51˝ 1.30 m Deadrise 19° 19°Available EnginesH.P. Liter Top Speed • Prop CodeMercury® Quad V12 Verado® 600 w/Joystick PilotingQ-600Q-7.664-67 MPHQ-V12 33 ∞• See prop index, page 53∞ Designates counter-rotating props (twin-prop drives)RangeMercury® Quad V12 Verado® 600 w/Joystick Piloting RPM MPH GAL/HR RANGE 1500 5 15 2072000 10 22 2742500 12 56 1253000 21 71 1773500 29 78 2204000 36 86 2474500 48 97 2905000 54 135 2355500 58 153 2226000 65 193 1956400 67 210187500 SS Cpage 36500 500 S uper S port C roSSover S tandard e quipment500 S uper S port C roSSover e xterior • NMMA Yacht Certification (pending)• Transferable 5-Year Formula Guard ® LimitedProtection Plan w/10-year Structural Warranty (USA only)• INEOS Maxguard™ LE gelcoat• Standard graphic in A, B or C w/Axalta™ Chroma Premier ® basecoat & Imron ® Elite clearcoat• FAS 3T eCh hull w/foam-filled continuous molded structural grid • Chemically bonded & thru-bolted deck-to-hull joint • Heavy-duty PVC gunwale w/stainless insert• Concealed electric windlass w/digital chain counter, 250´ chain, polished stainless anchor, yacht-design thru-hull stowage & freshwateranchor washdown system• Remote-control ACR LED searchlight• Polished stainless LED bow docking lights• Stainless hardware & 316L welded rails• Stainless pull-up cleats (12), fuel fills, polished port lights w/screens (2) & over-sized port lights (2)• Eight Formula logo fender clips• Coupe top w/tinted, tempered windshieldw/windshield wiper, washer & defogger system, sliding walk-thru door, full coupe windshieldside wings w/power side vents, large, motorized coupe-top Taylor Made ® glass sunroof w/Poseidon retractable sunshades and soft panels, multi-color LED accent lighting, motorized mast/dual flagstaff w/flush mount LED spreader light, American & Formula flags & white dual air horn• Rockford Fosgate ® waterproof transom-mounted stereo control & four 7.7” JL Audio ® M6 multi-color LED lighted chrome-finished speakers & 200W subwoofer• Integrated swim platform w/two telescopingstainless swim ladders & pull-up cleats• Concealed SureShade ATF™ electric powerretractable sun shade• 120V/240V shorepower w/fail-safe galvanicisolator & 50-amp cord w/Glendinning motorized extend/retract & storage system w/remote control • Starboard utility locker w/polished stainlessshorepower & cable TV inlets, transom shower w/hot/cold controls, chrome-finished city water inlet & fender (4 included) storage inside• Four full-spectrum color LED underwater lights w/wireless control & ‘Sound-to-Light’ stereo integration • Swim platform upholstered sport station w/six stainless drink holders & sliding safety rails 500 S uper S port C roSSover C oCkpit• Continuous molded deck & cockpit liner• Woodgrain vinyl decking throughout full cockpit & swim platform• Six dual USB charging ports – aft cockpit (3),bow (2) & sunpad (1)• 20 polished stainless drink holders• Cockpit/swim platform white LED courtesy lights w/remote control• Cockpit multi-color LED lighting system• Integral 316L safety rails• Weather-resistant cockpit seating featuringPre-Fixx ® coating, Tenara ® element-resistantthread, DriFast ® foam & StarLite ® XL synthetic marine panel construction 500 S uper S port C roSSover h elm S tation • Molded composite dash in Charcoal or Mocha w/Liquid Black panels, Ritchie ®compass, Dual Raymarine ®Axiom XL 24 GPS widescreen color chartplotters w/depth sounder & remote key- pad, illuminated waterproof accessory switches,E-T-A ® circuit breakers, auxiliary 12V outlet, two dual USB charging ports, captain and first mate wireless charging mounts, choice of tilt wheel inleather-wrapped stainless, dash storage compartment & padded mobile device station• Mercury Digital Throttle & Shift (DTS) controls w/9” SmartCraft ®VesselView ®• Mercury ®Joystick Piloting for Outboards (JPO) w/Active Trim • Mercury ®Theft Deterrent System• Digital switching w/helm-mounted dedicated Raymarine ® Axiom+ 12 display & wireless iPad control • Raymarine 48” Open-Array Magnum Radar • FLIR M332™ Thermal Camera • Raymarine forward and aft facing cameras w/augmented reality• VHF radio w/antenna • AIS receiver w/augmented reality overlay & antenna• Safety ignition tether & Bennett ® trim tab system w/switches & indicators• 30,000 BTU reverse cycle cockpit air conditioner & mooring windshield sun cover• Dash multi-port air boost ventilation system • Rockford Fosgate AM/FM stereo w/Bluetooth,USB port, dash-mounted stereo control w/full color display, chartplotter integrated stereo control, MP3 port, bow stereo remote, eight 7.7” hardtop & four 7.7” cockpit JL Audio M6 multi- color LED lighted chrome-finished speakers, 600W stereo amplification & three 200W subwoofers • Subscription-ready SiriusXM™ Satellite Radio • Triple helm & companion seating w/individual sit, stand or rest positions & power adjustable backrest ventilation system • Powered adjustable triple helm seat footrests w/woodgrain vinyl decking tops• Pullout Yeti ® Tundra ® 35 cooler • Portside gear lockers (3) w/dedicated storage for dock lines (6 included) & hydrostaticautomatic inflatable PFDs (6 included)500 S uper S port C roSSover B ow Z one • Modular wraparound bow seating/sunpad system w/triple-wide forward facing bow seating & two armrests • Two powered, adjustable-height bow tables w/woodgrain vinyl decking tops & filler cushions • Under-cushion bow storage w/dedicated storage for sun shade, seating covers & filler cushions• Recessed bow rails & two pop-up LED accent lights • Bow sun shade w/stainless supports • Dedicated glass wind door w/Corian frame • Bow cockpit seating covers• Pre-Fixx ® coating, Tenara ® element-resistant thread, DriFast ® foam & StarLite ® XL synthetic marine panel construction • All-weather bow cockpit cover in color- coordinated non-fading Sunbrella fabric w/Seamark™ vinyl undercoating 500 S uper S port C roSSover S alon• Salon tinted, tempered glass enclosure w/sliding glass door panels to port & bar-integrated power down window to starboard• 18,000 BTU reverse cycle air conditioner• Ultraleather L-shaped raised lounge w/fold-out Corian table & two tip-out barstools w/dedicated cushion storage below• 25-quart ice maker w/dedicated water reservoir • Pull-out Beverage Center w/assorted tempered stemware & glassware, adjustable bottle storage & blender or 26-bottle dual-zone wine cooler • Power lift 65” LED/LCD 4K Smart TV w/Bose soundbar, subwoofer & Blu-ray player• Salon galley w/Corian countertops, stainless sink w/Elka faucet & Corian cover, pullout 120V/12V Vitrifrigo All-In-One dual drawer refrigerator/freezer w/stainless front, concealed dual-burner induction cooktop w/glide-away self-cover lid & safety switch, Samsung PowerGrill Duo convection microwave oven, 6 hardwood dovetailed drawers, countertop & cabinet storage, tilt out trash container, paper towel holder, 120V GFCI outlets, water level gauge & fire extinguisher• Electronic drawer lock system• Entertainment bar w/elevated Corian countertop & two upholstered barstools• Demand water system w/100-gallon capacity& one-point water fill for freshwater tank and/or city water500 S uper S port C roSSover a ft C oCkpit • Starboard L-shaped aft lounge w/storage &54-gallon insulated cooler w/refrigerator/freezer coils & digitally controlled thermostat,120V• Portside U-shaped lounge w/storage below & stationary Corian table w/four drink holders & pop-up LED accent light, or powered, adjustable height cockpit table w/woodgrain vinyl decking top & filler cushion• Aft-facing sun lounge w/multi-position backrests & storage for available SEABOB• Disconnect switches for aux & start batteries • Battery parallel emergency switches• Fire Extinguisher• Sliding glass transom door w/Corian frame• 240V Gaggenau® electric grill w/pop-up LED accent light in aft cockpit• Aft cockpit enclosure w/easy-mount zippers in color-coordinated non-fading Sunbrella® fabricw/Seamark™ vinyl undercoating• Aft cockpit seating covers500 S uper S port C roSSover C aBin• Dash-integrated sliding cabin door• Color-coordinated Corian cabin entry steps• Woodgrain-finish flooring throughout cabin• Tinted cabin skylight & forward cabin windoww/electronic privacy smart glass• Sliding portside cabin window w/screen• Multi-color LED accent lighting throughout cabin • Electronic drawer lock system• Cedar-lined hanging locker• Portable Dyson V11 Vacuum w/dedicated pullout under-stair storage w/charging station& additional under-stair drawer storage500 S uper S port C roSSover C aBin S alon • Ultraleather™ lounge & powered adjustable- height Corian table w/flip-in cocktail conversion w/drink holders, filler cushions & fire extinguisher • Custom décor pillows• Motorized Poseidon pleated blind systems• 16,000 BTU reverse cycle air conditionerw/Breathe Easy™ photocatalytic Nano-Mesh UV air purifier & digital touch control • Illuminated 120V & 12V electrical panels• Four 61/2” JL Audio speakers• Two dual USB-A/USB-C charging ports• 7-bottle wine cooler w/digital thermostat• 32” LED/LCD Smart HDTV w/soundbar, Blu-ray player & multi-color LED accent lighting• Carbon monoxide detector• Electronic security safe500 S uper S port C roSSover C aBin g alley • Portside galley in open-grain or high-gloss finish w/storage & hardwood dovetailed drawers, multi-color LED lighted cabinet showcasew/tempered stemware & tumblers, multi-colored LED lighted backsplash panel, full Corian countertop, stainless sink w/Elka® swivel spout & Corian cover, pull-out Isotherm 120V/12V stainless refrigerator, microwave, Keurig® coffee maker & concealed trash container• Electronics station w/Rockford Fosgate stereo remote control, air conditioning control, table switches & LaunchPort inductive iPad charging system• 20-gallon 120V water heater500 S uper S port C roSSover C aBin h ead • Molded private head compartment w/vanity, open-grain or high-gloss finish doors, upper & lower cabinet storage, Corian countertop, custom-molded sink w/Elka faucet, Corian flooring & porcelain Flush and Forget® VacuFlush® head w/60-gallon holding tank & dockside pumpout • Separate shower room w/rain & wand dual shower heads, seat, tempered glass door, exhaust fan, night light, four swimsuit/towel hooks & plush woven towels500 S uper S port C roSSover C aBina ft S tateroom• Aft stateroom w/privacy curtain, queen-size memory foam bed w/quilted coverlet & pillow shams, plush throw & bed linens, side storagew/shelf & wireless phone charger, dual USB-A/ USB-C charging port, 32” LED/LCD Smart HDTV w/soundbar & Blu-ray player• Ultraleather settee & dual side consoles w/drawer storage, dual USB-A/USB-C charging port, two wireless phone chargers, pop-up 120V outlets, remote stereo volume control & LaunchPort inductive iPad charging system• Reading lights – 2 above bed & 2 above settee • Automatic cabin bilge pump w/high water alarm • Carbon monoxide detector500 S uper S port C roSSover e quipment r oom/e ngineS• Quad outboard engine installation w/thru-bolted engine mounts• Mercury Verado white outboard engines• Stainless props• Automatic outboard flushing system• Equipment room access hatches (1 salon/1 aftcockpit)• Four starting & three auxiliary marine batteriesw/battery retainers• Sea chest raw-water manifold system• Galvanic corrosion protection systems• Bennett XPT Premier dual-ram hydraulic trim tabs• 16 KW/120V diesel generator w/sound shield, battery & 50-gallon tank• Seakeeper® 9 gyro stabilization system, 240Vpage37page 38500 500 S uper S port C roSSover a vailaBle e quipment500 S uper S port C roSSover e xterior • Flagship graphic in A, B, C or D full hullside color w/Axalta™ Chroma Premier ® basecoat & Imron ® Elite clearcoat• Flagship Fusion in A, B, C or D full hullsidemulticolor fade effect w/Axalta™ Chroma Premier® basecoat & Imron ® Elite clearcoat• Polished stainless tow eye w/shackle guard• Removable dual Stand Up Paddleboard (SUP) rack system • Carbon fiber gangway w/rails & mounts • Painted coupe top electronics • SEABOB F5S premium underwater scooter w/quick charger – star white • SEABOB F5S premium underwater scooterw/quick charger & color coordinated graphic 500 S uper S port C roSSover C oCkpit• Raymarine 1,000W CHIRP™ transducer• Raymarine AIS650 AIS transceiver w/dedicated AIS antenna• FLIR M364™ thermal camera• FLIR M364C™ color HD/thermal camera • TracPhone ®LTE-1 WiFi hotspot (requires KVHservice)• SiriusXM Satellite Marine Weather Receiver (requires SiriusXM service)• Remote joystick (located in utility locker)• Mercury Premium Theft Deterrent System (requires Mercury service) 500 S uper S port C roSSover C aBin • Macerator discharge • Gray water holding system • TracVision TV3 high-definition satellite TV system (requires Dish service)500 S uper S port C roSSover e quipment r oom /e ngineS• Color-coordinated outboard cowl accents• Multi-color complete outboard cowl graphic。
马拉松MX系列发电机英文说明书
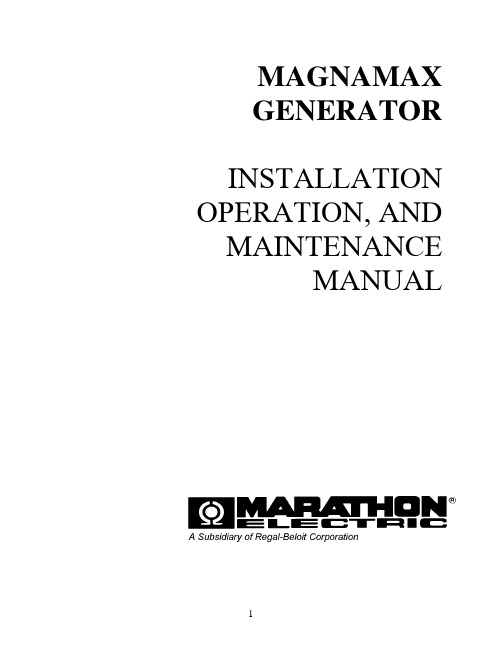
MAGNAMAXGENERATOR INSTALLATION OPERATION, AND MAINTENANCEMANUALTABLE OF CONTENTSTABLE OF CONTENTS (2)SAFETY (6)GENERAL INFORMATION (7)MECHANICAL DESIGN (7)General (7)Conduit Box (7)MagnaMAX Unirotor TM Construction (7)Adapters and Drive Discs (7)ELECTRICAL DESIGN (8)Temperature Rise (8)Standby Generator Ratings (8)Premium Insulation System (8)Power Factor (8)MagnaMAX Voltage Regulator (8)HOW TO READ A MODEL NUMBER (9)INSTALLATION (10)RECEIVING YOUR MAGNAMAX GENERATOR (10)UNPACKING AND HANDLING (10)STORAGE (10)PREPARATION FOR USE (10)GENERATOR MOUNTING - SINGLE BEARING (10)GENERATOR MOUNTING-TWO BEARING (11)BELT DRIVE (11)ENVIRONMENTAL CONCERNS (11)ELECTRICAL CONNECTIONS (12)GENERATOR LEAD CONNECTIONS (12)12 LEAD HIGH WYE CONNECTION (13)12 LEAD LOW WYE CONNECTION (13)12 LEAD HIGH DELTA CONNECTION (14)12 LEAD LOW DELTA CONNECTION (14)10 LEAD HIGH WYE CONNECTION (15)10 LEAD LOW WYE CONNECTION (15)6 LEAD WYE CONNECTION (16)6 LEAD DELTA CONNECTION (16)3 LEAD DELTA CONNECTION (17)4 LEAD WYE CONNECTION (17)DOUBLE DELTA -- SINGLE PHASE CONNECTION (18)LOW ZIG ZAG -- SINGLE PHASE CONNECTION (18)HIGH ZIG ZAG -- SINGLE PHASE CONNECTION (18)PARALLELING OPERATIONS (19)PRIME MOVER (19)VOLTAGE REGULATOR (19)SWITCHGEAR (19)PARALLELING BASICS (19)REACTIVE LOAD CONTROL (20)PARALLELING CIRCUITRY (20)THYRISTOR OR SCR LOADING (21)OPERATION (21)PRE-START INSPECTION (21)STARTING-UP THE GENERATOR (22)FIELD FLASHING (22)VOLTAGE ADJUSTMENTS (22)OTHER ADJUSTMENTS (23)MAINTENANCE (23)GENERAL INFORMATION (23)AIR INTAKE AND EXHAUST (23)ELECTRICAL CONNECTIONS, WINDINGS (24)LUBRICATION (24)DRYING ELECTRICAL INSULATION (26)Space Heaters (26)Oven (26)Forced Air (26)“Short Circuit” Method (26)CLEANING METHODS (27)Solvents (27)Cloth and Compressed Air (27)Brushing and Vacuum Cleaning (27)Shell Blasting (27)Steam Cleaning (27)DISASSEMBLY (28)REMOVAL FROM PRIME MOVER (28)CONDUIT BOX REMOVAL (29)EXCITER STATOR (FIELD) REMOVAL (30)EXCITER ARMATURE (ROTOR) REMOVAL (30)PMG STATOR REMOVAL (31)MAIN ROTOR REMOVAL (33)FRONT END BRACKET REMOVAL (35)EXCITER INSPECTION (35)EXCITER STATOR (35)EXCITER (ROTOR) ARMATURE (36)PMG INSPECTION (37)PMG STATOR (37)PMG ROTOR (37)MAIN ROTOR INSPECTION (37)BEARING (37)FAN (38)MAIN ROTOR CORE AND WINDINGS (40)DRIVE DISCS (SINGLE BEARING GENERATORS ONLY) (40)FRONT (EXCITER) END BRACKET INSPECTION (40)DRIVE END BRACKET OR SAE ADAPTER INSPECTION (41)MAIN STATOR INSPECTION (42)FRONT END BRACKET INSTALLATION (42)MAIN ROTOR INSTALLATION (42)PMG INSTALLATION (45)EXCITER INSTALLATION (46)CONDUIT BOX INSTALLATION (47)ASSEMBLY TO PRIME MOVER (48)TROUBLESHOOTING (50)INTRODUCTION (50)SYMPTOM: (51)NO VOLTAGE OR RESIDUAL VOLTAGE (51)LOW VOLTAGE - (52)NO LOAD (52)LOW VOLTAGE WHEN LOAD IS APPLIED (53)HIGH VOLTAGE (53)VOLTAGE IS FLUCTUATING (54)OPERATES SATISFACTORILY WHEN COLD, BUT SHUTS DOWN WHEN WARM (54)BUILDS VOLTAGE FROM STARTUP,THEN GOES TO LOW (RESIDUAL) VOLTAGE (54)EQUIPMENT RUNS NORMALLY ON UTILITY POWER, BUT WILL NOT RUN ON GENERATOR SET (54)GENERATOR TESTING (55)VISUAL INSPECTION (55)CONSTANT EXCITATION (12V BATTERY) TEST (55)MEASURING VOLTAGES (56)TYPICAL VOLTAGE MEASUREMENTS (57)Generator Output Voltage (57)Regulator Output (Exciter Stator Input) (57)Regulator Sensing (57)Regulator Input Volts (PMG Output Volts) (57)CURRENT (AMP) MEASUREMENTS (57)MEASURING RESISTANCE (58)Main Stator (58)Exciter Rotor (58)TESTING DIODES (RECTIFIERS) (58)INSULATION RESISTANCE - MAIN STATOR (59)GENERATOR TESTING (59)INSULATION RESISTANCE - MAIN ROTOR (59)INSULATION RESISTANCE - EXCITER STATOR (60)INSULATION RESISTANCE - EXCITER ROTOR (60)MAIN ROTOR FIELD AC IMPEDANCE TEST (60)MAGNAMAX EXPLODED VIEW (61)STANDARD TOOLS (64)SPECIAL TOOLS (65)MISCELLANEOUS (66)PREPARATION FOR SHIPMENT OR EXTENDED STORAGE (66)SHIPPING INSTRUCTIONS (66)STORAGE INSTRUCTIONS (66)TABLE 12-1: MAGNA MAX - FASTENER AND TORQUE SPECIFICATIONS (68)TABLE 12-2: CAPSCREW TORQUE VALUES (69)TABLE 12-3:EXCITATION DATA -60 HZ - 1800 RPM (70)TABLE 12-3:EXCITATION DATA -50 HZ - 1500 RPM (71)TABLE 12-5: RESISTANCE VALUES - MAIN WINDINGS (72)TABLE 12-6: RESISTANCE VALUES - EXCITER WINDINGS (73)SAFETYPLEASE REMEMBER SAFETY FIRST. If you are not sure of the instructions or procedures, seek qualified help before continuing.This service manual emphasizes the safety precautions necessary during the installation, opera-tion, and maintenance of your generator.Each section has caution and warning messages. These messages are for your safety and the safety of the equipment involved. If any of the cautions or warnings is not readily understood, seek clarification from qualified personnel before proceeding.Before any service work is done, disconnect all power sources and, where appropriate, lock out all controls, to prevent an unexpected start-up of the generator set. Proper grounding in compliance with local and national electrical codes must be provided. These safety precautions are necessary to prevent potential serious personal injury, or even death.The hazards associated with lifting or moving the generator are pointed out in the installation and service sections; incorrect lifting or moving can result in personal injury or property damage.Whenever the generator is running, always assume and proceed as if voltage is present. Residual voltage is present at the generator leads and at the regulator panel connections, even with the regulator fuse removed. Caution must be observed, or serious personal injury or death can result.Whenever solvents, cleaners, or flammable liquids are present, adequate ventilation must be available to avoid fire, explosion, and health hazards. Always avoid breathing vapors and use suitable personal protective equipment to prevent personal injuries. (Such as eyes, face, and hand protection.)This manual is not intended to be a substitute for properly trained personnel. Only qualified trained people should attempt repairs. The cautions and warnings point out known conditions that are potentially dangerous. Each installation will create its own set of circumstances. No manual can cover every possible situation.When in doubt, ask. Don’t be embarrassed to ask, “dumb questions”. Remember that dumb questions are much easier to handle than dumb mistakes.GENERAL INFORMATION MECHANICAL DESIGNGeneralAll single and two bearing units are manufactured with cast iron end brackets and adapters, and fabricated steel frames. Flexible drive discs and SAE adapters are machined to SAE standards. Pre-lubricated, regreasable, shielded ball bearings are used on MagnaMAX generators. Standard units are fully guarded. Drip proof shields are available as an option.Conduit BoxThe large end mounted conduit box is con-structed of formed sheet steel that will allow the addition of top mounted control packages. Refer to Marathon Electric for top mounted controls of more than 240 lbs. There is ample room inside the conduit box for a circuit breaker (through 800A Frame) and other options. The conduit box cover properly directs outside ventilating air through the generator.MagnaMAX Unirotor TM Construction An aluminum die cast rotor core affords high mechanical integrity and low vibration at operating speeds. Amortisseur winding and coil supports are die cast as an integral part of the rotor. Laminations are 4-pole, one piece laminations which are shrunk fit and keyed to the shaft. No dovetails, cross bolts or other pole to shaft connecting devices are used. The cast unidirectional aluminum alloy ventilation fan provides even air distribution to maximize cooling and generator efficiency.Adapters and Drive DiscsAll single bearing units are available with several adapters and drive disc arrangements. These can be shipped to order or can be changed in the field with standard shop tools. When changing flexible drive discs, spacers are used between the discs and the cast iron hub to maintain SAE standard dimensions.ELECTRICAL DESIGNAll standard products have 2/3 pitch main windings to eliminate the third harmonic. This serves to lower operating temperatures, give lower harmonic content and better waveform, and extend the overall life of the generator.Temperature RiseAll ratings and frame sizes are based on NEMA and CSA Class F and Class H temperature rises on both the rotor and stator windings. Ratings for British, German, French, IEC and all popular marine agencies are available.Standby Generator Ratings Synchronous generators used on emergency backup power can have temperature rises up to 25°C above those for continuous operation. (NEMA MG1 -22.40 and MG 1-22.84).Premium Insulation SystemAll MagnaMAX generators are built with Class H or better insulation materials. All standard generators are suitable for continuous duty at Class F temperature rise and will give equivalent or better winding life expectancy to generators supplied with Class A or B insulation systems operated within their temperature limits. The varnishes and epoxies used are synthetic, non-hygroscopic. Multiple dip and bake cycles of the main winding, plus a final coat of epoxy, make the standard winding moisture and fungus resistant. The MagnaMAX rotor is wet wound with thermo-setting epoxy applied between each layer, plus a final coating of epoxy for moisture and abrasion resistance. MagnaMAX generators can be ordered with an epoxy vacuum pressure impregnated insulation system as an option. (MagnaMAX generators with form wound coils include VPI as standard.)Power FactorAll standard generators are designed for operation at rated kVA at 0.8 lagging power factor but can be operated at rated kVA over the 0.8 to 1 .0 power factor range. MagnaMAX Voltage RegulatorThe standard voltage regulator is a fully encapsulated, static types with a solid state build up circuit. Standard features include 3-phase RMS sensing, paralleling, adjustable under frequency protection, and over excitation protection. The regulator meets EMI suppression to Mil Std-461B, part 9. An optional feature is adjustable armature current limiting. See the regulator manual for more information.HOW TO READ A MODEL NUMBERIt is extremely important to properly identify the machine when requesting parts or service. Always have the generator model number and serial number when requesting information from the factory. We cannot help you without this information.An Example For MagnaMAX Generators 431RSL 2000 AA - 000Character Category Description1st three characters Frame Number4th character Winding type R—Random WoundF—Form Wound5th character Bearing arrangement S—1 BearingD—2Bearings6th character Voltage range L—Up to 480 voltsM—1000-6600 voltsS—600 volts7th Character Product style4-Magna8th Character Type9th & 10th Character Wk2 Code11th Character Modification A-Z assigned sequentially 12th Character Mounting Arrangement A-Y see chart figurer 2-1 13th, 14th & 15th characters Modification numbers For internal use only Arrangement Adapter SAE Size Drive Disc SAE SizeA311-1/2B211-1/2C48D310E111-1/2F114G47-1/2H1DelcoJ1/214K210L1/2DelcoM014N2Small Delco0None NoneP018S0DelcoU0018V46-1/2W0021Y410Figure 2-1INSTALLATIONRECEIVING YOUR MAGNAMAX GENERATORUpon receipt of the generator, it is recommended that it be carefully examined for possible damage incurred in shipment. The generator was given to the Freight Company in good condition, and they are responsible for the product from our dock to yours. Any damage should be noted on the freight bill before accepting the shipment. Claims for damages must be promptly filed with the Freight Company. UNPACKING AND HANDLINGRead all instruction cards carefully. When lifting, attach an overhead crane to the lifting lugs on the generator frame. Apply lifting forces in a vertical direction.WARNINGTHE LIFTING LUGS ON THE GENERATOR ARE DESIGNED TO SUPPORT THE GENERATOR ONLY.DO NOT LIFT COMPLETE GENERATOR SET BY MEANS OF LIFTING DEVICES ON THE GENERATOR. PERSONAL INJURYOR QUIPMENT DAMAGE MAYOCCUR.STORAGEIn the event that the generator is not to be installed on the prime mover immediately, it is recommended that it be stored in a clean, dry area that is not subject to rapid changes in temperature and humidity. See "STORAGE INSTRUCTIONS" for more information.PREPARATION FOR USEAlthough the generator is carefully inspected and tested in operation before it leaves the factory, it is recommended the unit be thoroughly inspected. The insulation on the wire should be inspected and all bolts should be checked for tightness.Remove all shipping tapes, bags, blocks, and skids, which are used to prevent vibration and rotor movement during shipment. Dry, low-pressure compressed air of approximately 30 PSI (206 KPA) can be used to blow out the interior of the generator. In the case of two bearing machines, it is possible to turn the rotor by hand to make sure that it rotates smoothly without binding.If the machine has been in storage for a year or longer it is recommended that it be lubricated according to the lubrication instructions and chart supplied in the maintenance section.If the machine has been exposed to damp, humid conditions the insulation resistance should be checked. Refer to the instructions supplied in this manual.GENERATOR MOUNTING - SINGLE BEARINGSingle bearing generators are provided with an SAE flywheel adapter and flexible drive discs. Very close tolerances are maintained in the manufacture of the generator so that the alignment procedure is extremely simple. A coupling hub of nodular iron is shrunk on the shaft and special steel drivediscs are bolted to the hub. Holes are provided in the periphery of the coupling disc, which correspond to tapped holes inthe flywheel. The outside diameter of the discs fits in a rabbet in the flywheel so that concentricity is assured in all cases.WARNINGDO NOT APPLY ANY FORCE TO THE GENERATOR FAN FOR LIFITNG OR FOR ROTATING THE GENERATORROTOR. DISREGARDING THESEINSTRUCTIONS MAY CAUSE PERSONAL INJURY OR EQUIPMENTDAMAGECAUTION:GRADE 8 CAPSCREWSOR GRADE 8 PLACE-BOLTS AND HARDENED WASHERS ARE REC-OMMENDED TO MOUNT THE DRIVE DISCS TO THE FLYWHEEL.DO NOT USE HELICAL OR OTHER LOCKING DEVICES UNLESS APPROVED.The SAE adapter and the flywheel housing are designed to match each other with no further alignment necessary. Shims may be necessary under the feet of the generator to insure a solid mounting. See THE SERVICE SECTION for more information. GENERATOR MOUNTING-TWOBEARINGTwo bearing generators are provided with a shaft extension and key way. For direct-coupled sets the assembler furnishes a flexible coupling which is installed between the driver and the generator shaft.IMPORTANT: Aligning the two machinesas accurately as possible will reduce vibration, increase-bearing life, and insures minimum coupling wear. It may be necessary to shim the generator feet for proper support and alignment. Consult the coupling manufacturer’s instructions for alignment specifications and procedures. BELT DRIVEPlease refer to Marathon Electric for applications involving belt driven installations.ENVIRONMENTAL CONCERNSDirt, moisture, heat, and vibration are enemies of electrical equipment. The ambient temperature should not exceed the value shown on the generator nameplate. Generators for outdoor application should be protected from the elements by housings with proper openings for ventilation. This protection should be designed to prevent the direct contact of wind driven rain, snow, or dust with the generator. In moist or humid areas, such as the Tropics and marine serv-ice, additional protection is recommended. Although the standard windings are humidity and moisture resistant, special insulation and accessories such as space heaters can increase generator life. In extremely dirty and dusty environments a means of providing filtered cooling air to the generator is recommended. Please refer to Marathon Electric for filter kits that are available.ELECTRICAL CONNECTIONSThe generator conduit box construction allows conduit to enter the top, bottom, or either side of the box. A hole-saw or any suitable tool can be used to provide for the conduit entrance. Protect the interior of the generator from shavings when drilling or sawing. An approved connector must be used in conjunction with the conduit.To minimize the transmission of vibration, it is essential that flexible conduit be used for all electrical cable entrance to the generator. Refer to the connection diagram supplied with the generator and / or the proper diagrams shown in this section. Install all intercomponent and external wiring in accordance with the regulations of the national and local electrical codes. Clean all contact surfaces to assure good electrical bonding with the generator lugs or bus bars. Use heavy-duty terminal lugs or good quality clamps for making all connections. Insulate all connections in accordance with national and local regulations.Be sure the generator frame is grounded to all the other components of the system with a ground wire in accordance with national and local regulations.GENERATOR LEAD CONNECTIONS The electrical connections in the conduit box should be made in accordance with the appropriate “connection diagram.” Use the diagram appropriate for the number of leads and voltage range required. Refer to the drawings supplied with the generator and to drawings in this section.The final voltage setting is established within the selected range by an adjustment of the voltage regulator.CAUTION:SOME GENERATORS HAVE MULTIPLE, IDENTICALLY MARKED, CABLES FOR EACH LEAD. CONNECT ALL IDENTICALLY MARKED CABLES TOGETHER WHEN MAKING CONNECTIONS.PARALLELING OPERATIONSMagnaMAX generators come standard with amortisseur windings die cast as an integral part of the rotor. This exclusive, Unirotor TM, construction makes all MagnaMAX generators suitable for paralleling operations when the proper control equipment is added. Paralleling with other generator sets and / or with the utility power grid offers a number of advantages. Multiple unit installations increase power capacity; they can be added or removed from the line depending on the load requirements; they can be better maintained and repaired (since single source breakdown would mean total loss of power), and they often provide more reliable, efficient, and economical operation.Successful parallel operation means that the generators deliver power to the external system without delivering power to each other, or accepting power from the load bus or power grid. Additional equipment is necessary to insure safe and successful operation. PRIME MOVERThe prime mover provides the speed and torque which will be necessary to keep the machines in synchronized operation. A governor controls the prime mover's speed. The governor will directly control the watt or kW output and frequency of the unit. The governor must have special paralleling provisions to permit parallel operation with the other machines.VOLTAGE REGULATORThe voltage regulator controls the generator output voltage and the reactive power supplied by the generator. When two or more ac generators operate in parallel, the voltage regulator must have paralleling provisions (either internally or external to the regulator) to control the reactive or VAR load while it is in parallel operation. A separate paralleling current transformer is required to sense the reactive current and signal the voltage regulator. This additional paralleling circuitry is absolutely necessary to control the reactive current flowing between the generator sets. SWITCHGEARThere are additional relays and breaker controls that are necessary to insure safe, trouble free operation of paralleled units. Reverse power relays monitor the direction of power flow to insure that the generator is delivering power, not accepting it. These power relays control breakers, which are a means of connecting and disconnecting the gen-erator from the load. The total system can include over-voltage, over-current protection, under fre-quency protection, power factor correction provi-sion and a variety of associated control equipment from manual switchgear to microprocessors. The amount of control gear and level of sophistication will be determined by the needs and requirements of the particular application.PARALLELING BASICSThe following points are basic criteria which must be met before two units can be paralleled. THIS IS NOT MEANT TO BE SPECIFIC INSTRUCTIONS FOR PARALLELING OPERATION.1. Additional paralleling circuitryA. Voltage regulator-paralleling provisionsB.Paralleling current transformer(s)C. Paralleling provisions on governor controlsD. Switchgear2. The voltage and frequency must be the same for all sets with voltages in phase.3. The voltage regulation characteristics of the individual generators should be similar.4. The generators must have the same phase rotation.5.The driving engines should have the same speed regulation characteristics and the governors should be adjusted to give the same speed regulation.Before operating generator sets in parallel, each set should be checked by starting, operating, and adjusting the sets as individual units before attempting paralleling. REACTIVE LOAD CONTROLWhen two identical generators are operating together in parallel and an unbalance occurs in field excitation, circulating currents begin to flow between the generators. This current will appear as a lagging power factor or inductive load to the highly excited generator, and as a leading power factor or capacitive load to the generator with the lower field current. This is known as the reactive circulating current and there are two methods of controlling it in parallel operation:1. Reactive droop compensation. (Formerly known as parallel droop compensation.)The bus voltage droops, or decreases, as the reactive lagging power factor load is increased.2. Reactive differential compensation. (Formerly known as cross current compensation.) The reactive differential compensation circuit allows parallel generators to share reactive loads with no decrease or droop in generator voltage.The circuit must meet the following criteria:A.All paralleling current transformers for all the generators being paralleled must be included in the secondary interconnection loop.B. When different size generators are paralleled all paralleling current transformers must have the same proportional ratios that give approximately the same secondary current.C. Voltage regulator paralleling circuitry must be the same.D. Current transformer secondary and the generator lines must be isolated electrically.E. It is also desirable to have an auxiliary contact on the main generator breaker to short the parallel CT secondary when that breaker is open (not connected to the load bus).Because of the above criteria, reactive differential compensation cannot be used when paralleling with the utility power grid. There is no limit, however, in the number of generators that can be included in this type of circuit. PARALLELING CIRCUITRYBecause of the number of variables involved in paralleling generator sets, every installation will have its own circuitry and methods or procedure of bringing paralleled units on line. There are numerous ways of connecting paralleled units and an almost unlimited variety of applications and associated equipment.When parallel operation is desired, it is important that the control manufacturer, the generator manu-facturer, and the systems engineer work together to insure the proper selection of all components. Please refer to Marathon Electric for application assistance.THYRISTOR OR SCR LOADING Solid state electronic control devices which utilize thyristors or SCR firing circuits (such as variable frequency induction motor controls, precision motor speed controls, no-break powered battery chargers, etc.) can introduce high frequency harmonics which adversely affect or destroy the normal waveform of the generator. This creates additional heat in the generator stator and rotor, and can cause overheating. These devices can and do present problems to non-utility power generating equipment or any limited power bus system. The problems that can occur are not limited to the generator itself, but can effect the solid state control device, the equipment it controls, other associated loads, monitoring devices or a number of combinations over the entire system.MagnaMAX generators can supply power to thyristor or SCR loads when properly applied. The standard voltage regulator is PMG powered and senses 3 phase RMS voltages for maximum stability against severely distorted waveforms. SCR type applications such as cranes, shovels, etc., require special consideration of the generator insulation system due to greater dielectric stress and severe environmental conditions. It is impor-tant that the control manufacturer, the generator manufacturer, and the systems engineer work together to insure the proper selection of all components. Please refer to Marathon Electric for application assistance. OPERATIONPRE-START INSPECTIONBefore operating the generator for the first time, the following checks are recommended.1. A visual inspection should be made to check for any loose parts, connections, or foreign materials2. Check for clearance in the generator and exciter air gap. Be sure the generator set turns over freely. Bar the generator over by hand at least 2 revolutions to be sure there is no interference.WARNINGDO NOT APPLY ANY FORCE TO THEGENERATOR FAN FOR LIFITNG ORFOR ROTATING THE GENERATORROTOR. DISREGARDING THESEINSTRUCTIONS MAY CAUSE PERSONAL INJURY OR EQUIPMENTDAMAGE3. Check all wiring against the proper connection diagrams and make sure all connections are properly insulated. Support and tie leads to keep them from being damaged by rotating parts or by chafing on sharp corners.4. Be sure the equipment is properly grounded.5. Inspect for any remaining packing materials and remove any loose debris, building materials, rags, etc. that could be drawn into the generator.6. Check fasteners for tightness.7. Check to be sure no tools or other hardware have been left inside or near the machine.8. Install and check to be sure all covers and guards are in place and secure.WARNINGRESIDUAL VOLTAGE IS PRESENT AT THE GENERATOR LEADS AND AT THE REULATOR PANEL CONNECTIONS EVEN WITH THE REGULATOR FUSE REMOVED.CAUTION MUST BE OBSERVED OR SERIOUS PERSONAL INJURY OR DEATHCAN RESULT.STARTING-UP THE GENERATORThe following procedure should be followed for starting-up the generator for the first time:1.The generator output must be disconnected from the load. Be certain that the main circuit breaker is open.2.D isable the voltage regulator by removing the fuse.WARNINGDO NOT OVERSPEED THEGENERATOR. EXCESSIVE CENTRIFUGAL FORCES COULD DAMAGE THE ROTATING FIELDS. BE PREPARED FOR AN EMERGENCYSHUTDOWN.3.F ollow the manufacturer's instructions and start the prime mover. Check the speed and adjust to the RPM shown on the generator nameplate.4.Replace the regulator fuse and adjust the voltage to the required. Check all line to line and line to neutral voltages to be sure they are correct and balanced. If the voltages are not correct shut down immediately and recheck all connections.5. Close the main circuit breaker and apply the load.6. Monitor the generator output current to verify it is at or below nameplate amps.7. Adjust engine speed at full load to 1800 rpm for 60 hertz, 1500 rpm for 50 hertz. (Refer to prime mover/governor instruction manuals.)8. Before stopping the engine, remove the load by tripping the main circuit breaker.FIELD FLASHINGThe standard MagnaMAX generator is supplied with a PMG (permanent magnet generator). It will never require field flashing. In rare cases where a special generator may be furnished without a PMG, refer to the factory for more detailed information. Include the complete generator model and serial number.VOLTAGE ADJUSTMENTSThe voltage regulator controls the generator output voltage. There is a cover to access the controlpanel on the side of the generator conduit boxFigure 4-1Figure 4-2 Regulator Access Refer to the regulator manual for detailed information. In cases where special or remote mounted regulators are used, refer to instructions supplied by the generator set assembler and to the voltage regulator manual.。
Kentucky Mammoth Cave和Colossal Cavern产品说明书

to a n éx t e n t t h a t m an y p ro no u n ce d t h em roma n ces , a knowledge of t h e cave t h at was really q uite exact became
com m o n p ro p e rty a n d t h e i m m e n s e ca v e r n soo xf took i ts
Of al l t h e natu ra l wonders non e are more i nterestin g to t h e p rese n t ge n erat io n t h an t h e w ond e rfu l cav es a n d ca v e rn s t h at a re to b e fou n d i n va ri ou s l oca l i ti e s . T h e i nterest i n t h ese s ubte rran eo us wond ers i s attested by t h e large number of persons w h o are constantly visiting t h em, and t h e time and money spent by t h ose of a scientific turn of mind i n studying t h e rocks, air cu rrents