如何解决线切割加工表面粗糙度差的方法文库
机械线切割加工合理化建议

机械线切割加工合理化建议
中走丝线切割机的切割效果已经是比较好的了,如果用中走丝机割件光洁度不好,朋友们可以看下以下几条建议。
总的来说,提高线切割光洁度的方法不外乎以下几条:
【1】适当降低脉宽和峰值电流,即减小蚀坑的大小。
【2】导轮和轴承保持好的精度和运转的平稳性,减少丝抖、丝跳,使丝运动轨迹保持一线变位量减到小。
【3】钼丝维持适当的张力,且调好导轮和进电块,使丝上行下行时,工作区的张力保持不变。
【4】线切割液不宜过新,新水对切割效率肯定有益,但切割光洁度不是新水好。
【5】过薄的工件上下两面各添加一块夹板,使换向条纹在夹板范围内被缓冲。
XY运动稳定、准确、随动保真性好、无阻滞爬行也极为重要。
【6】中走丝切割机保持稳定偏松的变频跟踪。
适当留量的再次切割或多次切割,在切削量很小的情况下把切割面扫一遍,对尺寸精度和光洁度都会产生有益的作用,连扫三次,会把换向条纹基本去掉,只要机床重复定位精度高,适当留量的递进多次加工,会使切割面的光洁度提高一到两个量级,效果与慢走丝相似,且费时并不太多,这是中走丝切割机床的长项之一。
较厚的工件可适当使用短丝,一次换向进给量小于半个丝径,也掩盖了换向条纹。
提高模具线切割加工质量的探索与实践
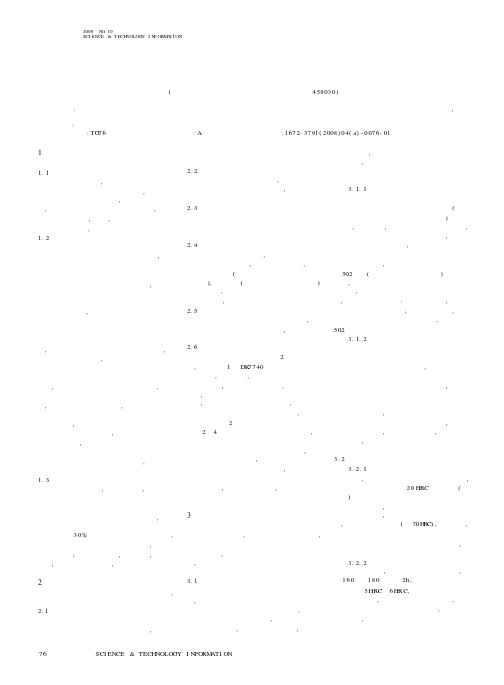
6科技资讯科技资讯S I N &T NOLOGY I NFORM TI ON2008N O .10SCI ENC E &TECH NOLOG Y I N FOR M A TI ON工程技术1应选择合适的工具、附件及确定加工对象1.1选择合适的设备从社会环境来看,一些小型的线切割机床生产厂还处在原始资本的积累阶段,这些厂家往往不具备整机制造能力,只能是组装式生产,生产全过程的质量控制根本谈不上,研发、创新就更不可能,因此,应根据模具的材料、形状及尺寸要求,慎重选择线切割机床。
1.2确定加工对象线切割加工为新产品试制、精密零件加工及模具制造开辟了一条新的工艺途径,主要适用于以下几个方面。
加工冲压及塑料模具。
适用于加工各种形状的冲模。
调整不同的间隙补偿量,只需一次编程就可以切割凸模、凸模固定板、凹模及卸料板等。
模具配合间隙、加工精度通常都能达到要求。
此外,还可加工挤压模、粉末冶金模、弯曲模、塑压模等通常带锥度的模具。
加工电火花成形加工用的电极。
一般穿孔加工用的电极以及带锥度型腔加工用的电极,以及铜钨、银钨合金之类的电极材料,用线切割加工特别经济,同时也适用于加工微细复杂形状的电极。
加工复杂型腔的模具。
在试制新产品模具时,用线切割在坯料上直接割出型腔,例如试制切割特殊微电机硅钢片定、转子铁心模具,由于不需另行制造母模,可大大缩短制造周期、降低成本。
另外修改设计、变更加工程序比较方便,加工薄件时还可多片叠在一起加工。
在模具零件制造方面,可用于加工品种多、数量少的零件,特殊难加工材料的零件、材料试验样件、各种型孔、特殊齿轮凸轮、样板、成型刀具。
同时还可进行微细加工,异形槽和人工标准缺陷的窄缝加工等。
1.3购买高强度钼丝选用优质钼原料,经专用设备,特殊工艺制造的超高强度线切割专用钼丝。
对每一盘线切割专用钼丝分别进行抗拉强度、延伸率、色泽、曲环、精度、排线共六项质量检测,严格控制钼丝制品的质量。
浅析线切割加工中存在的问题及对策

污垢堵塞, 妨碍电极丝顺利送进, 引起断丝, 因此要 定期清洗导丝模块。污垢去除后, 导丝模块通畅, 保 证了合理的送丝速度, 电极丝就不容易断。 电极丝通过上、 下导电块的传导而通电+ 长时间
图 ( 电极丝送进装置 ( %贮丝筒 # %圆柱滚轮 ; %导 向 孔 模 块 、 、 张紧轮 ) 压紧轮 , 0 ( $ ( (滚轮 4 % % % 毛毡 1 断丝检测器 5 毛刷 ( % % # %导丝 管 ( 下臂 ( ; % 0 %接丝装置 ( 4 %电极丝 输送轮 ( 废丝孔模块 ( 废丝箱 ) % , %
1 % 1 加工面平直度差 加工面平直度差的原因可能是电极丝线速低, 加工时损耗大, 形成上、 下切割尺寸不同3 见图 4 , 5 也可能是喷淋不当, 上、 下压力及流量不同, 此外导 丝模块及导丝板松动也会影响加工面的平直度。电 极丝张力过低可导致加工面平直度差,对此应采取 的措施是增加送丝速度3 拨至第 6档 , 增加电极丝 5 张力, 调整上、 下喷淋的压力和流量, 检查导丝模块 及导丝板的工作状况。 1 % + 鼓 形
( 引 言 在线切割加工中,对加工机床中的表 面质量问题影响到了其高精度,本文仅对线切割加 工中影响工件表面质量的主要原因作了分析,并提 出了相应的对策。 # 电极丝断丝 断丝是线切割加工中常碰到的问题。它既降低 了加工速度,又对加工精度及表面粗糙度有影响。 造成断丝的原因是多方面的,大体可分为送丝机构 故障、 加工条件和电参量选择不当、 操作不合理、 工 件及电极丝不合要求等。 # % ( 送丝机构的故障及排除 送丝机构的结构如图 ( 、图 #所示,长期使用 后,上导丝模块、剖分式导丝板及下导丝模块会被
图 # 电极上下导向通电装置 、( ( %上 法 兰 # %导 向 孔 模 块 , , %导 电 体 、 止动螺钉 2 、 、 、 3 % ) ( 2 # $ % 4 形密封圈 、 5 # # %导 电 块 6 %电 极 丝 导 向 体 ( $ %滚 轮 ( ( %下法兰 ( # %导向孔模块 ( 3 %电极丝导 向套 ( 下浮动喷嘴 ( 下喷嘴压套 ( ) % 5 % % 上喷嘴压套 ( 上喷嘴 # 电极丝导向套 6 % ( % 图 , 开始加工时电极丝易断示意图 电极丝 # 污物或铁锈 ( % %
降低机械加工表面粗糙度的途径
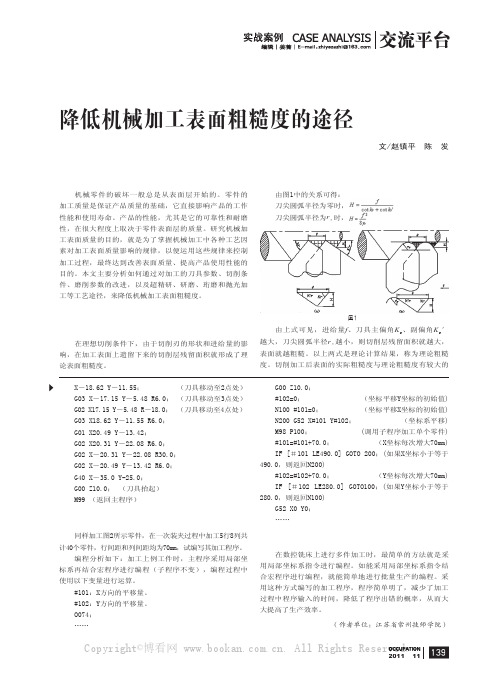
OCCUPATION 1392011 11由图1中的关系可得:刀尖圆弧半径为零时,刀尖圆弧半径为r ε时,由上式可见,进给量f 、刀具主偏角K r 、副偏角K r ′越大,刀尖圆弧半径r ε越小,则切削层残留面积就越大,表面就越粗糙。
以上两式是理论计算结果,称为理论粗糙度。
切削加工后表面的实际粗糙度与理论粗糙度有较大的降低机械加工表面粗糙度的途径文/赵镇平 陈 发机械零件的破坏一般总是从表面层开始的。
零件的加工质量是保证产品质量的基础,它直接影响产品的工作性能和使用寿命。
产品的性能,尤其是它的可靠性和耐磨性,在很大程度上取决于零件表面层的质量。
研究机械加工表面质量的目的,就是为了掌握机械加工中各种工艺因素对加工表面质量影响的规律,以便运用这些规律来控制加工过程,最终达到改善表面质量、提高产品使用性能的目的。
本文主要分析如何通过对加工的刀具参数、切削条件、磨削参数的改进,以及超精研、研磨、珩磨和抛光加工等工艺途径,来降低机械加工表面粗糙度。
一、降低切削加工表面粗糙度的途径1.选择合理的刀具几何参数在理想切削条件下,由于切削刃的形状和进给量的影响,在加工表面上遗留下来的切削层残留面积就形成了理论表面粗糙度。
图1X-18.62 Y-11.55; (刀具移动至2点处)G03 X-17.15 Y-5.48 R6.0; (刀具移动至3点处)G02 X17.15 Y-5.48 R-18.0; (刀具移动至4点处)G03 X18.62 Y-11.55 R6.0; G01 X20.49 Y-13.42; G02 X20.31 Y-22.08 R6.0; G02 X-20.31 Y-22.08 R30.0; G02 X-20.49 Y-13.42 R6.0; G40 X-35.0 Y-25.0; G00 Z10.0; (刀具抬起)M99 (返回主程序)三、批量加工实例同样加工图2所示零件,在一次装夹过程中加工5行8列共计40个零件,行间距和列间距均为70mm,试编写其加工程序。
浅析影响线切割加工质量的原因及解决办法
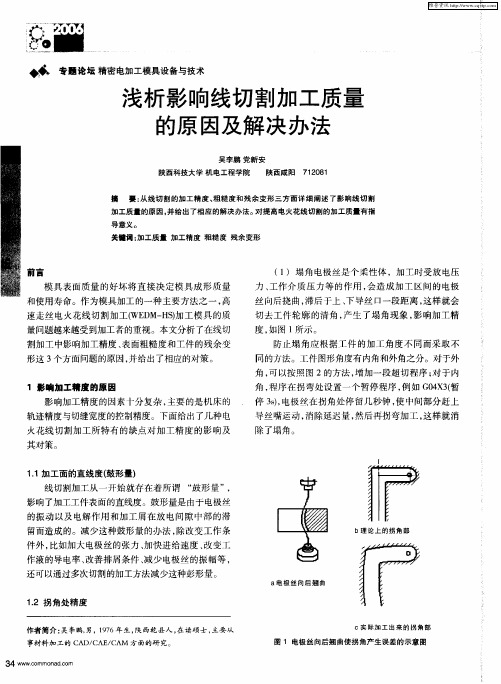
作液 的导电率 、 改善排屑条件 、 减少电极丝 的振幅等 ,
还可以通过多次切割的加工方法减少这种彭形量。
a电 极 丝 向 后 翘 曲
1 . 2拐角处精度
作者简 介 : 吴李鹏, 1 7 男, 9 6年生 , 陕西乾县人 , 在读硕士 , 主要从
c实际加工 出 来的 拐角部
事材料加工的 c D/ E c A cA / AM 方面的研 究。
_
整的部位 。若是切割 凹模 , 可以设法将 内部的废料取
这是线切割加工过程中必然要产生的现象, 无法消除。
13 接痕 .
冲能量 的因素有脉冲宽度 、 功放管个数 、 功放管峰值
电流 。所 以, 减小脉冲宽度 、 减小峰值 电流 , 可改善加 工表面粗糙度。然而 , 减小脉 冲宽度 , 生产效率大幅度 利用线切割加工 , 在工件 的进刀处总会留有如 图 3 所示接痕( 凸垅) , 产生的原凶是由子放电间隙及电极 丝半径 的存 在 , 当切割完毕以前 , 电极丝 的中心轨迹 还没有达到 P点时 , 因为 自重的缘故工件就 已经掉下 来了。若是切割凸模 , 这种接痕最好留在容易进行修
下降, 不可用 ; 减小功放管峰值电流 , 生产效 率也会下
降, 但影响程度 比减小脉冲宽度小 。因此 , 笔者认为减
小功放管峰值 电流 , 适当增大脉 冲宽度 , 调节合适的
加工表 面粗 糙度 。 22 电极 丝对 线切 割加 工表 面粗 糙 度 的影 响 _
脉冲间隔 , 这样既可提高生产效 率 , 又可获得较低 的
因是 多方 面 的。
另外 , 根据塌角形成的原因 , 采取弱的电规准 , 降
低喷淋压力 , 有助于提高拐角精度。 () 2 角部附加 R 角部形状精度) ( 正如立铣加工一 样 ,被加工工件 的角部都存在着铣刀半径 R的圆角。 线切割加工也有附加 R ,这在加工工件的凹角部分才
切削过程中减小表面粗糙度值的方法

切削过程中减小表面粗糙度值的方法
减小表面粗糙度值的方法有刀具几何参数,工件材料和加工因素等方面。
(1)刀具方面
减小主偏角、副偏角,增大刀尖圆弧半径,都可以减小表面粗糙度值。
但主偏角太小、刀尖圆弧半径太大,易引起振动。
减小副偏角是减小表面粗糙度值的有效措施。
采用修光刃也是减小残留面积高度的有效措施,但修光刃太宽,易引起振动。
适当增大前角、后角,有利于减小表面粗糙度值。
但后角过大,易引起振动。
正值刃倾角使切屑流向工件待加工表面,并采取卷屑、断屑措施,可防止切屑划伤已加工表面。
车刀刃磨后,进行研磨,减小刀具的表面粗糙度值,有利于减小工件表面粗糙度值。
及时刃磨或更换车刀,使车刀保持锐利状态。
(2)工件材料
塑性材料的塑性越大,表面粗糙度值增大。
工件金相组织的晶粒越细,加工后,表面粗糙度值越小。
(3)加工因素
进给量增大,表面粗糙度值增大。
但进给量太小,切削刃不锋利时,切削刃不能切削而形成挤压,表面粗糙度值增大。
选择较低或较高的切削速度,不出现积屑瘤,有利于减小表面粗糙度值。
背吃刀量a
<0.02~0.03㎜时,经常与工件发生挤压和摩擦,表面粗糙度值增
p
大。
切削液的极压添加剂,增加润滑性能,减小刀具与工件的摩擦,有利于减小表面粗糙度值。
降低零件粗糙度的方法

降低零件粗糙度的方法
一、简介
零件表面粗糙度是量度表面形貌精密度以及表面质量的重要指标。
零件粗糙度的改善能够提高机械零部件的精密度和性能,减少零件生产中的误差,提高零件的使用寿命,减少损坏率,从而提高产品质量。
二、降低零件粗糙度的方法
1、加工工艺的优化:加工工艺的优化是改善零件粗糙度的重要手段,优化加工工艺可以提高加工精度,减少零件表面粗糙度,可以通过合理的调整检测、切削参数,改善切削噪声,减少切削温度,从而改善零件表面粗糙度。
2、机械表面处理:对于已经加工好的零件,可以采用机械表面处理方法进行粗糙度降低,典型的机械表面处理方法有抛光、研磨和石英砂磨等。
3、光学抛光:对于表面质量要求较高的零件,可以采用光学抛光的方法,通过使用特殊的抛光膏,采用自动化或人工抛光的方法,抛光表面,从而达到表面粗糙度的降低目的。
4、电子表面处理:可以通过电子表面处理,借助于电磁力,从而降低零件表面粗糙度,比如电离辐照,电火花处理等。
三、结论
降低零件粗糙度是提高产品质量的重要手段之一,可以通过优化加工工艺、采用机械表面处理、光学抛光以及电子表面处理等方法来
达到这一目的。
线切割加工直齿轮

线切割加工直齿轮一研究背景目前工程训练教学中的直齿轮加工多以插齿和铣齿为主要加工手段,期中铣齿属于成形法,插齿属于展成法。
这俩种加工相比较展成法加工精度高,生产效率低,而且需要插齿机和相关配件,生产成本高。
这俩种加工齿轮的方法都有一定的局限性,对于直齿轮内径和模数都有要求和需要相关配件,且加工键槽还需额外加工。
因现在工程训练教学中的用的直齿轮数量少,模数多,种类多,如果仅用这俩种加工方式不能解决所有的问题,于是本人就想到了用线切割加工直齿轮的办法来解决这个问题。
二研究的目标和方法工程训练的目的是让学生在实际操作的过程中理论联系实际,让学生在学中做,做中学,用理论来推动实践,用实践来修正或补充理论。
(注1出自作家廖沫沙)因线切割加工直齿轮灵活,多变可加工任意模数标准直齿轮,对于工件的外形要求不高;还可以加工非圆的直齿轮。
所以本文选择线切割加工直齿轮。
三研究的详细过程及阶段结果问题一,直齿轮表面粗糙度。
齿轮分度圆上表面粗糙度代表齿面的粗糙程度,滚齿和刨齿的齿面粗糙程度一般在3.2um到1.6um之间,磨齿的齿面粗糙程度在1.6um以下。
线切割加工直齿轮的时候可采用多次切割加工的方式,提高表面光洁度,完全满足直齿轮的表面粗糙度需求。
解决办法:线切割多次切割加工,首先采用较大的电流进行粗加工,然后逐步用小电流一步一步精修,从而得到较好的加工精度和光滑的加工表面。
具体切割的次数根据工件、加工要求等来确定,一般进行三次切割即可。
多次切割基本工艺选择原则:①根据工件粗糙度要求来决定切割次数与电参数。
②根据切割次数及工件厚度来选择走丝速度大小。
③根据钼丝直径来决定工件补偿量。
④根据放电电流及产生的放电间隙来确定偏移量的大小。
1、一次切割任务是高速稳定切割(1)脉冲参数:选用高峰值电流,较长脉宽的规准进行大电流切割,以获得较高的切割速度。
(2)第一次切割的偏离量应在0.05~0.06mm之间,选大了会影响第二次切割的速度,选小了又难于消除第一次切割的痕迹。
- 1、下载文档前请自行甄别文档内容的完整性,平台不提供额外的编辑、内容补充、找答案等附加服务。
- 2、"仅部分预览"的文档,不可在线预览部分如存在完整性等问题,可反馈申请退款(可完整预览的文档不适用该条件!)。
- 3、如文档侵犯您的权益,请联系客服反馈,我们会尽快为您处理(人工客服工作时间:9:00-18:30)。
如何解决线切割加工表面粗糙度差的方法?
在线切割机床加工过程中,常会出现加工表面粗糙、有沟痕、精度下降等问题。
造成这种状况的原因,通常有以下几种:
(1)钢丝过松、抖丝。
(2)工作液过脏。
(3)脉冲参数选择不当。
(4)导轮的钼丝槽过大。
(5)卷丝筒不同心等。
解决的方法:不外乎是紧丝、更换工作液选择最佳脉冲参数、更换导轮或轴承等。
除以上原因外,在修理中我们还发现卷丝简直流电机轴与摩擦联轴节间的键槽因长期反复运行,导致键槽变形变大,换向时因大间隙丝筒振动加大造成加工表面沟痕。
【好的光洁度是怎么获得的?】
线切割光洁度是由两个要素构成的,一是单次放电蚀除凹坑的大小,它的RZ 通常是0.05μ~1。
5μ之间,这对切割光洁度说是次要的。
二是因换向造成的凸凹条纹,它的RZ通常是1μ~50μ之间,大到0。
1MM以上也有可能,这是构成线切割光洁度的最重要因素。
同时它伴随着换向的黑白条纹,给人视觉影响是很强烈的。
因单次放电造成凹坑大小的控制是较容易的,只需降低单个脉冲的能量。
只是单个脉冲能量小到一定程度造成较厚的工件切不动,甚至是只短路不放电的无火花状态,这类似于电火花加工中的精细规准,造成效率极低,排屑能力极差的不稳定加工。
何况因放电凹坑造成的RZ与换向条纹造成的RZ不在同一个量级范围内,所以控制伴随换向条纹的RZ 是最重要的。
导轮、轴承的精度,上下行时张力的恒定性等原因,造成丝上下行的运动轨迹不一致,这种机械因素是造成换向凸凹的主要原因。
采取如下措施,会在一定程度上改善光洁度:
1、适当降低脉宽和峰值电流,即减小蚀坑的大小。
2、导轮和轴承保持好的精度和运转的平稳性,减少丝抖、丝跳,使丝运动轨迹保持一线变位量减到最小。
3、丝维持适当的张力,且调好导轮和进电块,使丝上行下行时,工作区的张力保持不变。
4、丝不宜过紧,水不宜过新,新水对切割效率肯定有益,但切割光洁度不是新水最好。
5、过薄的工件上下两面各添加一块夹板,使换向条纹在夹板范围内被缓冲。
1、XY运动稳定、准确、随动保真性好、无阻滞爬行也极为重要。
2、保持稳定偏松的变频跟踪。
3、适当留量的再次切割或多次切割,在切削量很小的情况下把切割面扫一遍,对尺寸精度和光洁度都会产生有益的作用,连扫三次,会把换向条纹基本去掉,只要机床重复定位精度高,适当留量的递进多次加工,会使切割面的光洁度提高一到两个量级,效果与
慢走丝相似,且费时并不太多,这是快走丝切割机的长项之一。
4、较厚的工件可适当使用短丝,一次换向进给量小于半个丝径,也掩盖了换向条纹。
当然只是掩盖而已。