第6章压铸模浇注系统及排溢系统设计
《金属压铸工艺与模具设计》浇注系统及排溢系统设计

浇注系统和排溢系统的案例分 析
通过多个实际案例的分析,我们将深入了解浇注系统和排溢系统的设计过程 和关键技术,以及对最终产品质量的影响。
总结与展望
浇注系统和排溢系统的设计对金属压铸工艺至关重要。通过综合考虑各种因 素和采用合理的设计方法,可以提高产品质量、减少不良品率、降低制造成 本。
金属压铸工艺与模具设计
欢迎来到《金属压铸工艺与模具设计》浇注系统及排溢系统设计的演示。本 演示将探讨浇注系统和排溢系统的设计重要性、关键组成部分、设计原则与 考虑因素、设计步骤和方法、以及案例分析。让我们开始吧!
浇注系统设计的重要性
浇注系统设计是金属压铸工艺中至关重要的一步。它直接影响到产品的质量 和性能,包括去除气体和杂质、冷却均匀和填充性良好等。
浇注系统的三个关键组成部分
浇注系统通常由浇注系统入口、浇注系统道架、以及浇注系统出口组成。每 个组成部分的设计都需要考虑材料流动和热量传递等因素。
浇注系统的设计原则与考虑因素
浇注系统的设计应遵循原则,如缩短流动路径、减少涡流和飞溅等。同时需要考虑材料的流动性、冷却效果、 压力损失、和模具制造技术等。
浇注系统设计的步骤和方法1Fra bibliotek几何设计
2
绘制浇注系统几何图形,包括道架布置、
入口设计等。
3
制造和安装
4
根据设计图纸制造浇注系统零件,并在 模具上进行安装和调试。
需求分析
理解产品要求和压铸过程,确定浇注系 统的要求。
计算仿真
使用压铸仿真软件进行模拟,评估浇注 系统的性能和优化设计。
排溢系统的作用和设计原则
第6章A浇注系统设计[new](2)素材
素材](https://img.taocdn.com/s3/m/0f4276cb28ea81c758f578e0.png)
• 凡在型腔中带有螺纹的部位不易直接布置内浇口,以 防螺纹被冲击而受浸蚀。
(3)除特大型铸件、箱体及框架类铸件和结构比较特殊 的铸件外,内浇口的数量以单道为主,多道浇口要在 形状上采取措施以防多道金属液流入型腔互相冲击, 产生涡流、裹气和夹渣等缺陷,如下图。
(4)薄壁复杂压铸件,宜采用较薄的内浇口,以保持必 要的充填速度。一般结构的压铸件以取较厚的内浇口 为主,使金属液充填平稳,有利于排气和有效地传递 静压力。 (5)根据铸件的设计要求,凡精度要求高、表面粗糙度 数值小且不加工的部位,不宜布置内浇口,以防在除 浇口后留下痕迹。 (6)布置内浇口时要考虑到内浇口的切除和清理。
一、按位置分
1)侧浇口 • 一般开设在分型面上,按铸件结构特点,可布置在压 铸件外侧或内侧。 • 适用于板类、盘类或型腔不太深的壳体类。不仅适用 于单型腔模,也适用于多型腔模。此种浇口去除方便, 适应性强,所以应用最为普遍。
• 由于金属液从型腔端面的中心部位流向分型面,因此有利于克服 深腔处气体不易排出的缺点,排气通畅。同时,从浇口到型腔各 部位的流程最短,流动距离基本接近,金属液分配均匀,也有利 于模具的热平衡。这种浇口形式使压铸件和浇注系统在分型面上 的投影面积最小,模具结构紧凑,金属液消耗量小,压铸机受力 均匀。其缺点是切除浇口比较困难,在大批量生产中,一般需采 用机械加工方法将浇口切除。
•
(2)内浇口的宽度和长度 • 内浇口的厚度确定后,根据内浇口的截面积即可计 算出内浇口的宽度。根据经验:矩形压铸件一般取 边长的0.6~0.8倍;圆形压铸件一般取直径 的0.4~0.6倍。 • 在整个浇注系统中,内浇口的截面积最小(除直接 浇口外),因此金属液充填型腔时,内浇口处的阻 力最大。为了减少压力损失,应尽量减少内浇口的 长度,内浇口的长度一般取2~3mm。也有资料 介绍越短越好。表6-5、6为内浇口宽度和长度的经 验数据。
压铸模浇注系统设计PPT
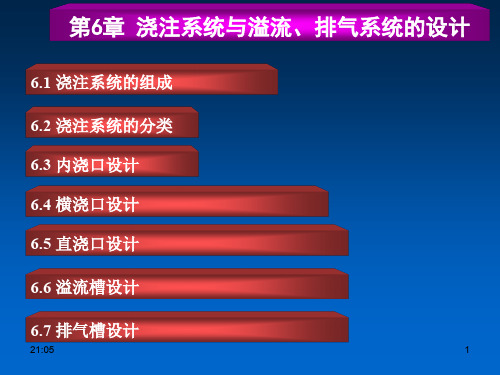
21:05
16
6.3 内浇口设计
具设计者的一个任务。其次,浇口的切除比较困难,
一般采用机械加工方法切除。由于金属液从直浇道
大端进入型腔后直冲型芯,容易造成粘模,影响模
具的寿命。
11
直接浇口的浇注系统,一般仅适用于单型腔模具,多用于热压 室压铸机或立式冷压室压铸机上生产。
21:05
12
6.2.3 中心浇口
中心浇口是直接浇口的一种特殊形式,当有底的筒或盘壳类压铸件的底部中心或 接近中心部位有不大的通孔时,内浇口就开设在通孔处,中间设置分流锥,金属 液在压铸件底部以环状进入型腔。图a为深筒型压铸件的中心浇口,图b为壳类压 铸件的中心浇口。
由于侧浇口设计与制造简单,浇口去除容易,适应性很强,因 此应用最为普遍。
21:05
10
6.2.2 直接浇口
21:05
直接浇口亦称顶浇口,是直浇道直接开设在筒形 或者壳形压铸件底部外侧中心部位的一种浇注系统
形式。直浇道与压铸件的连接处即为内浇口它是浇 注系统中截面积最大的地方,便于压铸终了保压时
的补缩。
21:05
7
6.2 浇注系统的分类
6.2.1 侧浇口 6.2.2 直接浇口 6.2.3 中心浇口 6.2.4 环形浇口 6.2.5 缝隙浇口 6.2.6 点浇口
21:05
8
6.2 浇注系统的分类
6.2.1 侧浇口
侧浇口开设在模 具的分型面上, 它可以开设在压 铸件最大轮廓处 的外侧(图a)或 内侧(图c),也 可以在压铸件的 侧面进料如图b所 示,侧浇口还可 以从压铸件的端 面搭接进料如图c 所示。
压铸模具排溢系统的设计
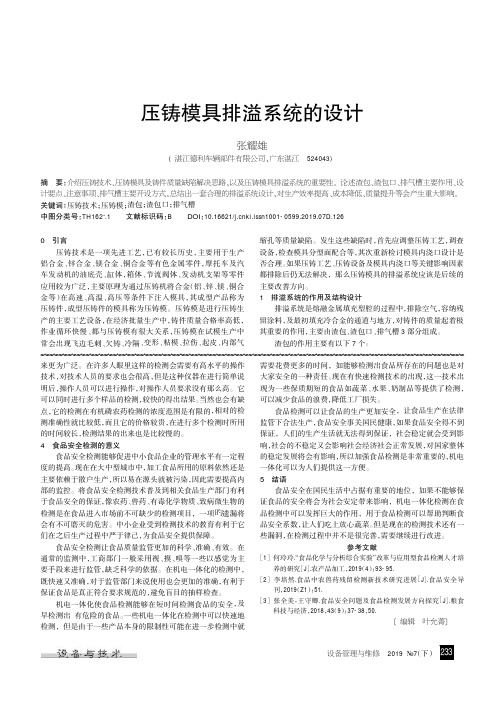
来更为广泛。
在许多人眼里这样的检测会需要有高水平的操作技术,对技术人员的要求也会很高,但是这种仪器在进行简单说明后,操作人员可以进行操作,对操作人员要求没有那么高。
它可以同时进行多个样品的检测,较快的得出结果。
当然也会有缺点,它的检测在有机磷农药检测的浓度范围是有限的,相对的检测准确性就比较低,而且它的价格较贵,在进行多个检测时所用的时间较长,检测结果的出来也是比较慢的。
4食品安全检测的意义食品安全检测能够促进中小食品企业的管理水平有一定程度的提高。
现在在大中型城市中,加工食品所用的原料依然还是主要依赖于散户生产,所以易在源头就被污染,因此需要提高内部的监控。
将食品安全检测技术普及到相关食品生产部门有利于食品安全的保证,像农药、兽药、有毒化学物质、致病微生物的旳检测是在食品进入市场前不可缺少的检测项目,一项遗漏将会有不可磨灭的危害。
中小企业受到检测技术的教育有利于它们在之后生产过程中严于律己,为食品安全提供保障。
食品安全检测让食品质量监管更加的科学、准确、有效。
在通常的监测中,工商部门一般采用视、摸、嗅等一些以感觉为主要手段来进行监管,缺乏科学的依据。
在机电一体化的检测中,既快速又准确,对于监管部门来说使用也会更加的准确,有利于保证食品是真正符合要求规范的,避免盲目的抽样检查。
机电一体化使食品检测能够在短时间检测食品的安全,及早检测出有危险的食品。
一些机电一体化在检测中可以快速地检测,但是由于一些产品本身的限制性可能在进一步检测中就需要花费更多的时间,如能够检测出食品所存在的问题也是对大家安全的一种责任。
现在有快速检测技术的出现,这一技术出现为一些保质期短的食品如蔬菜、水果、奶制品等提供了检测,可以减少食品的浪费,降低工厂损失。
食品检测可以让食品的生产更加安全,让食品生产在法律监管下合法生产,食品安全事关国民健康,如果食品安全得不到保证,人们的生产生活就无法得到保证,社会稳定就会受到影响,社会的不稳定又会影响社会经济社会正常发展,对国家整体的稳定发展将会有影响,所以加强食品检测是非常重要的,机电一体化可以为人们提供这一方便。
压铸分型面、浇注系统和排溢系统设计
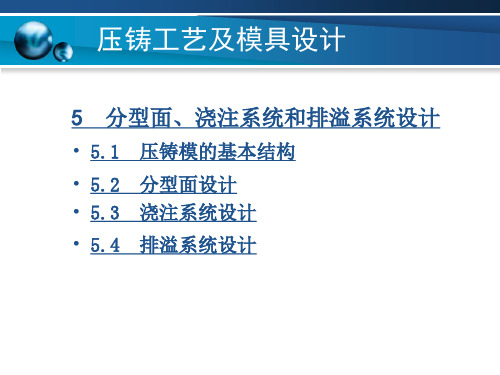
5 分型面、浇注系统和排溢系统设计
• 5.1 压铸模的基本结构 • 5.2 分型面设计 • 5.3 浇注系统设计 • 5.4 排溢系统设计
压铸工艺及模具设计
5 分型面、浇注系统和排溢系统设计
5.1 压铸模的基本结构
压铸模、压铸设备和压铸工艺是压铸生产的三个要 素。在这三个要素中,压铸模最为关键。
血糖生成指数测定方法
数指成生糖血
食 物
肠道
食欲
肠降糖素
Wha消t is the glycaemic index?
化
A ran酶k ing of foods bas e d on the ir pos tprandial
肠-胰岛轴
血糖
blood
glu胰c岛o素s e
response
组织
胰高血糖素
The re fe re nce food (glucos e or bre ad) has a GI of 100
—
(不可消化)多糖
纤维素和纤维素衍生物
羟丙基纤维素 甲基纤维素 阿拉伯木聚糖 半乳聚糖 果胶 β-葡聚糖 抗性淀粉,包括变性淀粉如乙酰化淀粉 抗性麦芽糊精 树胶(瓜尔胶,阿拉伯树胶,胶凝糖,角叉菜聚糖)
聚葡萄糖
糖 醇
常见糖醇可利用碳水化合物转化量
组分 赤藓糖醇
甘露醇 乳糖醇 异麦芽酮糖醇 山梨醇 麦芽糖醇 麦芽糖醇糖浆b 氢化葡萄糖浆 木糖醇 麦芽糖醇糖浆a a普通、中级、高麦芽糖醇糖浆 b高聚合体麦芽糖醇糖浆
一段时间内(2 h)血糖应答曲线下面积相比空腹时 的增幅除以进食含等量可利用碳水化合物的参考食物 (葡萄糖)后相应的增幅,以百分数表示。
念概个几清分
• 参考食物 reference food 用于测定食物GI值的基准物质,通常为食 品级或药品级葡萄糖或葡萄糖溶液。 参考食物的GI值定为100。
压铸模具的制作流程与浇排系统设计

压铸模具的制作流程与浇排系统设计压铸模具的制作流程与浇排系统设计压铸是有色金属成型的一个重要方法之一。
压铸件的质量好坏80%取决于压铸模具。
制作好压铸模具是产品开发的关键所在。
在压铸过程中,由于型腔内的金属液流动状态不同,可能产生冷隔、花纹、气孔、偏析等不良现象。
所以控制型腔内的金属液流动状态是相当必要的,而控制型腔内的金属液流动状态,关键在于压铸模具浇排系统的设计。
1 压铸模具的制作流程上述流程是压铸模具制作的大致流程,但并非一成不变。
应在整个制作过程中前后协调,不断反馈与调整各阶段的信息,根据分析结果,修改设计方案,以期取得实效。
笔者从事压铸模具开发多年,就模具制作流程中的相关注意事项总结如下,供同行参考。
(1)要对客户来图应进行检证根据压铸工艺的特性结合有色金属的牌号,先进行毛坯方案设计,然后开始模具设计。
对有些不符合压铸工艺的结构,应及时与客户沟通,在征求客户同意的基础上再行修改。
日本三大著名摩托车品牌的研发部门都是在开发之初就重点把握图面检证这一关,这样可避免开发损失、减少开发时间。
压铸模具的设计与有色金属的牌号有关。
特别是ADC6(JIS标准)铝合金,其浇排系统结构及其拔模斜度与普通铝合金有所不同,应根据其流动性差、压铸温度较高等特点适当应对。
日本在高强度的零件上已大量应用ADC6铝合金,而国内应用的较少。
ADC6铝合金压铸模具常见的问题有:模具寿命短;脱模阻力大,易变形、拉模,工件顶出易产生裂纹;流动性差,易产生花纹、冷隔;模具突出部位易产生裂纹等,在设计过程中应提前应对。
(2)做好模具的检测在模具检测阶段,不应单纯检测模具尺寸,更重要的是应检测压铸产品质量。
压铸产品质量检测可分外观检测、内部品质检测及机械性能检测。
检测的数据应符合压铸产品的合格率要求、内部品质标准及机械性能指标。
(3)做好试模试模阶段是验证模具的.关键阶段,通常初次试模后还要进行修模,修模时针对不良项目逐二进行改善,直至符合客户要求。
浇注系统及排溢系统设计
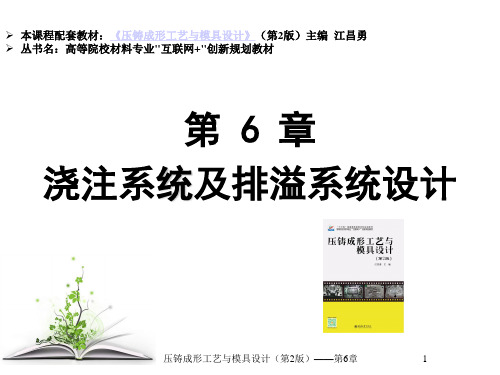
浇注系统 的设计
溢流、排 气系统
掌握 掌握
把握老师所介绍的重点内容,掌握适用 于不同压铸机的三种直浇道的结构及基本 技术要求;结合不同结构压铸件浇注系统 的设计实例,理解消化浇注系统设计要点, 初步领会一些相关的设计技巧。
将溢流、排气系统与浇注系统作为一个 整体来考虑。通过对实例的分析理解,掌 握溢流槽的位置选择要求和排气槽的结构 形式。
压铸成形工艺与模具设计(第2版)——第6章
39
(4)金属液进入型腔后不宜正面冲击型芯或型壁,
尤其应避免冲击细小型芯或螺纹型芯,以减少动能损 失,防止冲蚀及产生粘模。
(5)尽量减少金属液在型腔中的分流。
(6)压铸件上精度、表面粗糙度要求较高且不加工 的部位,不宜设置内浇口。
(7)内浇口的设置应考虑模具温度场的分布,以便
压铸成形工艺与模具设计(第2版)——第6章
28
2)浇口套
浇口套一般镶在定模座板上, 采用浇口套可以节省模具钢 和便于加工。
浇口套一个端面A与喷嘴端面 相吻合,控制好配合间隙不 允许金属液窜入接合面;浇 口套的另一端面B与定模镶块 相接,接触面上的镶块孔比 浇口套孔大1-2mm。
应固定牢固,拆装方便。
压铸成形工艺与模具设计(第2版)——第6章
36
1.内浇口的形式
压铸成形工艺与模具设计(第2版)——第6章
37
2.内浇口的位置
内浇口位置的选择是设计浇注系统 时首先要考虑的问题。在确定内浇口位 置时要综合考虑压铸件的结构特征、壁 厚大小、收缩变形情况、合金种类、压 铸机特性、模具分型面以及压铸件使用 性能等方面的因素,分析金属液充填时 的流动状态、充填速度的变化,预计充 填过程中可能出现的死角、裹气和产生 冷隔的部位,以便布置合适的溢流和排 气系统。
10-11浇注系统与排溢系统-48
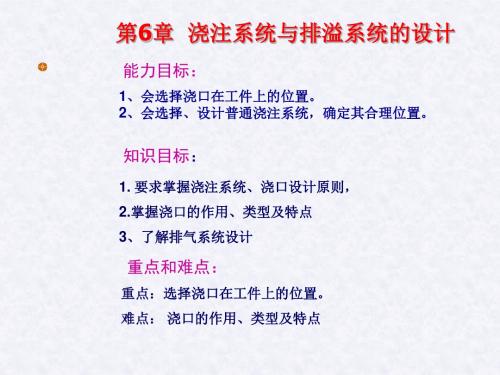
6 压铸模具浇注系统与排溢系统的设计
在设计压铸模的浇注系统时,为保证金属液连续保持充
满浇道,最大限度地减少涡流卷起的现象。在一般情况
下,应从直浇道 开始使各截面呈逐渐递减的变化趋势, 如图6-26所示。这是压铸模浇注系统设计的一条重要原 则。
图6-26 浇注系统各截面的变化趋势
上一页 下一页 返回
(5)直浇道与横浇道连接处圆角半径R=6~20mm。
2).卧式冷压室压铸机用直浇道
(1)根据压室比压选定压室直径D;
(2)直浇道厚度H一般取压室直径的1/2~1/3,直浇道脱模斜度1°30′~2°; (3)压室内径和浇口套内径应保持同轴度。
图6-11 卧式冷压室压铸机用直浇道 a)直浇道结构 b)直浇道起模斜度 1—压室 2—浇道套 3—分流器 4—余料
图6-19 横浇道不合理形状
图6-20 盲浇道的设置
④横浇道应具有一定的厚度和长度,若横浇道过薄,则热量损失大; 若过厚,则冷却速度缓慢,影响生产率,增大金属消耗。 保持一 定长度的目的,主要是对金属液起到稳流和导向的作用。 ⑤横浇道截面积在任何情况下都不应小于内浇口截面积。多腔压铸 模主横浇道截面积应大于各分支横浇道截面积之和。 ⑥对于卧式压铸机,一般情况下横浇道在模具中应处于直浇道(余 料)的正上方或侧上方,多型腔模也应如此,以保证金属液 在压 射前不过早地流人横浇道,这是根据压铸机的结构特点而定的,
举例
一、任务描述 本项目以前面项目所选案例一阀盖(二维图如图4-1 所示,三维图如图4-2所示)为载体,要求设计一套 成型该铸件的模具。
图4-2 阀盖三维图形
图4-1 阀盖铸件图
二、阀盖模具浇注系统和排溢系统设计的相关内容如下。
①分析图4-1所示阀盖铸件的结构特点,根据现场设备初选 压铸机型号,确定压室直径等。该项内容已在项目三任 务3.2任务实 施中完成。该阀盖铸件选用DCC280卧式冷 压室压铸机,锁模力为2800kN,压室直径50mm。 ②确定金属液进入型腔的位置方向和流动状态。 该模具分型面选在铸件底面,即整个型芯布置在动模,模
- 1、下载文档前请自行甄别文档内容的完整性,平台不提供额外的编辑、内容补充、找答案等附加服务。
- 2、"仅部分预览"的文档,不可在线预览部分如存在完整性等问题,可反馈申请退款(可完整预览的文档不适用该条件!)。
- 3、如文档侵犯您的权益,请联系客服反馈,我们会尽快为您处理(人工客服工作时间:9:00-18:30)。
第6章压铸模浇注系统及排溢系统 设计
上一页 下一页 返回
6.1 浇注系统设计
• 内浇口宽度也应适当选取,宽度太大或太小会使金属液直冲浇口对面
• 内浇口的长短直接影响铸件质量,内浇口太长,影响压力传递,降温 大,铸件表面易形成冷隔花纹等。内浇口太短,进口处温度容易升高,
• 内浇口宽度和长度的经验数据如表6-4所示。
第6章压铸模浇注系统及排溢系统 设计
上一页 下一页 返回
6.1 浇注系统设计
• 分流锥起分流金属液和带出直浇道的作用。分流锥单独加工后装在镶 块内,不允许在模具镶块上直接做出,如图6-5所示。圆锥形分流锥 的导向效果好、结构简单、使用寿命长,因此应用较为广泛。对直径 较大的分流锥,可在中心设置推杆,如图6-6所示。
上一页 下一页 返回
6.1 浇注系统设计
• ② 位于浇口套部分的直浇道的直径应比喷嘴部分直浇道的直径每边放 大 0.5~1 mm
• ③ 喷嘴部分的脱膜斜度取1°30′,浇口套的脱模斜度取1°30′~3°。 • ④ 分流锥处环形通道的截面积一般为喷嘴导入口的1.2倍左右,直浇
道底部分流锥的直径一般情况下可按下式计算
第6章压铸模浇注系统及排溢系统 设计
上一页 下一页 返回
6.1 浇注系统设计
• 2. • 直浇道是传递压力的首要部位。在立式压铸机和热室压铸机上,直浇
道是指从浇口套起到横浇道为止的一段浇道。 • (1)立式冷压室压铸机直浇道。立式压铸机直浇道主要由压铸机上
的喷嘴和模具上的浇口套组成,图6-3所示为立式压铸机用直浇道的
• 式中 d3——直浇道底部分流锥直径,mm • d2——直浇道底部环形截面处的外径,mm • d1——直浇道小端(喷嘴导入口处)直径,mm。
第6章压铸模浇注系统及排溢系统 设计
上一页 下一页 返回
6.1 浇注系统设计
•
•⑤
R
5~20 mm
• 采用浇口套可以节省模具钢且便于加工。直浇道部分浇口套的结构形 式如图6-4所示。
第6章 压铸模浇注系统及排溢系统设计
• 6.1 浇注系统设计 • 6.2 排溢系统设计
第6章压铸模浇注系统及排溢系统 设计
6.1 浇注系统设计
• 6.1.1
• (1)浇注系统的结构。浇注系统主要由直浇道、横浇道、内浇口和 余料组成。压铸机的类型不同,浇注系统就有所不同。各种类型压铸 机所采用的浇注系统的结构如图6-1
第6章压铸模浇注系统及排溢系统 设计
上一页 下一页 返回
6.1 浇注系统设计
• 内浇口的厚度对金属液的充型影响较大。一般情况下,当铸件较薄并 要求外观轮廓清晰时,内浇口厚度要求较薄。当铸件表面质量要求高、 组织要求致密时可采用较厚的内浇口,但内浇口太厚,充填速度过低 而降温大,可能导致铸件轮廓不清,切除内浇口也麻烦。内浇口厚度 的经验数据如表6-3所示。
• ④ 分流器上形成余料的凹腔的深度等于横浇道的深度,直径与浇口套
相等,沿圆周的脱模斜度约为5
第6章压铸模浇注系统及排溢系统 设计
上一页 下一页 返回
6.1 浇注系统设计
• ⑤ 有时将压室和浇口套制成一体,形成整体式压室。整体式压室内孔
• ⑥ 采用深导入式直浇道(见图6-8)可以提高压室的充满度,减小深 型腔压铸模的体积,当使用整体式压室时,有利于采用标准压室或现
后充填其他部位,并应注意不要过早地封闭分型面和排气槽,以便型
• ② 金属液进入型腔后,不正面冲击型壁和型态,力求减少动能损耗,
• ③ 应尽可能采用单个内浇口而少用分支浇口(大型铸件、箱体和框架 类以及结构形状特殊的铸件除外),以避免多路金属液汇流互相撞击, 形成涡流,产生裹气和氧化物夹杂等缺陷。
第6章压铸模浇注系统及排溢系统 设计
上一页 下一页 返回
6.1 浇注系统设计
• ④ 形状复杂的薄壁铸件应采用较薄的内浇口,以保证有足够的充填速 度。对一般结构形状的铸件,为保证最终静压力的传递作用,应采用
• ⑤ 内浇口设置位置应使金属液充填压铸模型腔各部分时流程最短,流
• (2)内浇口的分类。内浇口的分类如表6-2所示。
第6章压铸模浇注系统及排溢系统 设计
ห้องสมุดไป่ตู้
• ⑦ 压室和浇口套的内孔应在热处理和精磨后,再沿轴线方向进行研磨, Ra 0.2μm
上一页 下一页 返回
6.1 浇注系统设计
• (3)内浇口的尺寸确定。内浇口最合理的截面积计算涉及多方面的 因素,目前尚无切实可行的精确计算方法。在生产实践中,主要结合
• 式中 Ag——内浇口截面积,m2 • G ——通过内浇口的金属液质量,kg
• ρ ——液态金属的密度,kg·m-3
• vg——充填速度,m/s • t ——型腔的充填时间,s。
• (1)内浇口的设计要点。设计内浇口时,主要是确定内浇口的位置 和方向,并预计合金充填过程的流态、可能出现的死角区和裹气部位, 以便设置适当的溢流和排气系统。
第6章压铸模浇注系统及排溢系统 设计
上一页 下一页 返回
6.1 浇注系统设计
• • ① 从内浇口进入型腔的金属液应首先充填深腔处难以排气的部位,然
• (2)浇注系统的分类。各种类型的浇注系统适应不同结构铸件的需 要。浇注系统的分类如表6-1和图6-2
第6章压铸模浇注系统及排溢系统 设计
下一页 返回
6.1 浇注系统设计
• 6.1.2
• 1. • 内浇口是指横浇道到型腔的一段浇道,其作用是使横浇道输送出来的
低速金属液加速并形成理想的流态而顺序地充填型腔,它直接影响金
• (2)卧式冷压室压铸机直浇道。其结构如图6-7所示,它由压铸机上 的压室和压铸模上的浇口套组成,在直浇道上的这一段称为余料,其
第6章压铸模浇注系统及排溢系统 设计
上一页 下一页 返回
6.1 浇注系统设计
•①
D
• ② 浇口套的长度一般应小于压铸机压射冲头的跟踪距离,以便余料从
• ③ 横浇道入口应开设在压室上部内径2/3以上部位,避免金属液在重
第6章压铸模浇注系统及排溢系统 设计
上一页 下一页 返回
6.1 浇注系统设计
• • ① 根据浇注系统内浇口截面积,选择喷嘴导入口直径。喷嘴导入口小
端截面积一般为内浇口截面积的1.2~1.4倍。可按下式计算喷嘴导入
• 式中 d1——喷嘴导入口小端直径,mm • Ag——内浇口截面积,mm2。
第6章压铸模浇注系统及排溢系统 设计