一模多腔真空压铸浇注系统改善对产品的影响
压铸机实时压射控制系统对铸件质量的影响

压铸机实时压射控制系统对铸件质量的影响摘要:对当前众所关注的压铸机实时压射控制系统作了较为全面的阐述和介绍。
从影响铸件质量的主要因素出发,提出实时压射控制思路的由来,进一步涉及到实时压射控制系统的实质性内容,及其时压铸优质铸件所带来的实效。
阐述了组成该系统的关键之所在,结合生产现状提出应该注意的问题,还有如何认定系统本身应具有的精度和灵敏度指标,以及引进该设备中所要求提供的测试数据等。
关键词:伺服系统实时压射工艺参数压射曲线压铸件的质量在很大程度上取决于压铸机压射性能的优劣。
现代化的压铸机在压射控制方面对冲头速度和压力曲线能够做到精确编程,但是每一次压射过程都会与事先所设定的曲线产生无法避免的偏差,在压射过程中及时去修正这些偏差,纠正压射中的相应数据,并在极为短暂的时间内将其切换成修正后的数据,回到原来所设定的最小偏差范围之内,这就是实时压射控制。
1影响压铸件质量的主要因素影响压铸件质量的因素是多方面的,其中最为主要的是充型条件,铸件中的气孔、尺寸精度及表面质量等这些均与充型条件有密切关系。
充型过程中可变因素复杂多样,从总体上可以划分为静态的、人为的和动态的3个类别。
静态方面包括:压铸机本身的性能、铸件结构、模具结构、储能器压力及增压压力。
属于人为的有:阀、定时开关、行程开关、金属液的温度及液压油的粘度等。
动态方面的可变因素众多,也是最难以控制的,压室中的金属量、冲头运行时所受的阻力、模具温度以及采用真空压铸时的负压曲线等,都会对施加于金属液上的压力和冲头的速度产生巨大的影响,而这两方面又是影响充型条件最为重要的参数。
2实时压射控制的基本原理严格的掌握压射中参数变化的规律,使其始终处于恒定状态,一直是压铸工作者努力的方向。
从当前参数变化曲线的测定和监控中,我们可以得到很多的启发。
由图1可知,理想的冲头速度,既是冲头所处位置的函数,也与冲头行程有关,在位置P,为慢速起始速度,在位置Pz为向前运行的速度,在位置Ps为充型阶段的速度以及在位置P9为瞬时实现制动到零的阶段。
浅谈压铸模结构对铸件质量及模具寿命的影响

浅谈压铸模结构对铸件质量及模具寿命的影响吴燕华;王宏霞;朱芬芳【摘要】论述了压铸模结构对铸件质量及模具寿命的影响因素,并通过实例提出了通过改善模具结构来提高铸件质量和模具寿命的方法,可为压铸模设计者提供借鉴.【期刊名称】《模具制造》【年(卷),期】2015(015)007【总页数】4页(P54-57)【关键词】压铸模结构;铸件质量;模具寿命【作者】吴燕华;王宏霞;朱芬芳【作者单位】江苏省无锡交通高等职业技术学校,江苏无锡214046;江苏省无锡交通高等职业技术学校,江苏无锡214046;江苏省无锡交通高等职业技术学校,江苏无锡214046【正文语种】中文【中图分类】TG249压力铸造生产具有效率高、材料利用率高、铸件质量稳定等优点,再结合新材料的不断开发和应用,一些体积小、质量轻、形状复杂、壁薄等特点的有色金属铸件及配件越来越广泛地采用了压力铸造的方法进行生产[1]。
在压铸生产过程中,铸件的质量和压铸模具的使用寿命是生产者最关心的问题,而铸件的质量及模具的寿命跟很多因素有关系,本文从压铸模具结构上来阐述对这两者的影响。
压铸模是压铸生产中的重要工艺装备,它对生产能否顺利进行,铸件质量的优劣起着极为重要的作用,它与压铸工艺、生产操作存在密切而又互相制约、互相影响的特殊关系[2]。
压铸模结构对铸件质量的影响主要体现在如下方面:(1)决定着铸件的形状和尺寸公差等级。
(2)其浇注系统(特别是浇口位置)决定了熔融金属的填充状况。
(3)溢流排气系统影响着熔融金属的溢渣排气条件,控制和调节压铸过程的热平衡,决定了铸件表面质量及变形程度。
(4)模具的结构会影响模具的刚度,模具的刚度限制了压射比压的最大限度,压射比压合适与否严重影响铸件的质量从而影响成品率及生产效率。
通常模具在设计时都会注重铸件的形状和尺寸精度,而浇注系统和溢流排气可以在模具试模后根据具体情况进行改进,以获得良好的表面质量和内在质量,在设计过程中,模具的强度和刚度往往是最容易被忽视的。
压铸件缺陷和改善对策
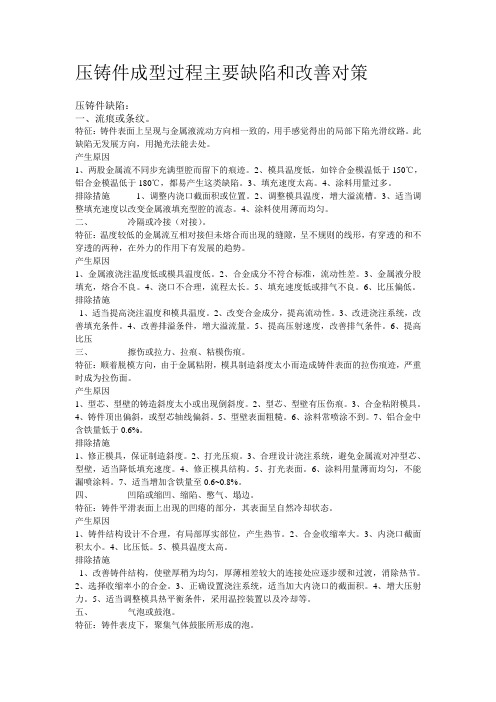
压铸件成型过程主要缺陷和改善对策压铸件缺陷:一、流痕或条纹。
特征:铸件表面上呈现与金属液流动方向相一致的,用手感觉得出的局部下陷光滑纹路。
此缺陷无发展方向,用抛光法能去处。
产生原因1、两股金属流不同步充满型腔而留下的痕迹。
2、模具温度低,如锌合金模温低于150℃,铝合金模温低于180℃,都易产生这类缺陷。
3、填充速度太高。
4、涂料用量过多。
排除措施1、调整内浇口截面积或位置。
2、调整模具温度,增大溢流槽。
3、适当调整填充速度以改变金属液填充型腔的流态。
4、涂料使用薄而均匀。
二、冷隔或冷接(对接)。
特征:温度较低的金属流互相对接但未熔合而出现的缝隙,呈不规则的线形,有穿透的和不穿透的两种,在外力的作用下有发展的趋势。
产生原因1、金属液浇注温度低或模具温度低。
2、合金成分不符合标准,流动性差。
3、金属液分股填充,熔合不良。
4、浇口不合理,流程太长。
5、填充速度低或排气不良。
6、比压偏低。
排除措施1、适当提高浇注温度和模具温度。
2、改变合金成分,提高流动性。
3、改进浇注系统,改善填充条件。
4、改善排溢条件,增大溢流量。
5、提高压射速度,改善排气条件。
6、提高比压三、擦伤或拉力、拉痕、粘模伤痕。
特征:顺着脱模方向,由于金属粘附,模具制造斜度太小而造成铸件表面的拉伤痕迹,严重时成为拉伤面。
产生原因1、型芯、型壁的铸造斜度太小或出现倒斜度。
2、型芯、型壁有压伤痕。
3、合金粘附模具。
4、铸件顶出偏斜,或型芯轴线偏斜。
5、型壁表面粗糙。
6、涂料常喷涂不到。
7、铝合金中含铁量低于0.6%。
排除措施1、修正模具,保证制造斜度。
2、打光压痕。
3、合理设计浇注系统,避免金属流对冲型芯、型壁,适当降低填充速度。
4、修正模具结构。
5、打光表面。
6、涂料用量薄而均匀,不能漏喷涂料。
7、适当增加含铁量至0.6~0.8%。
四、凹陷或缩凹、缩陷、憋气、塌边。
特征:铸件平滑表面上出现的凹瘪的部分,其表面呈自然冷却状态。
产生原因1、铸件结构设计不合理,有局部厚实部位,产生热节。
压铸件常见缺陷及解决办法手册 (完整版)
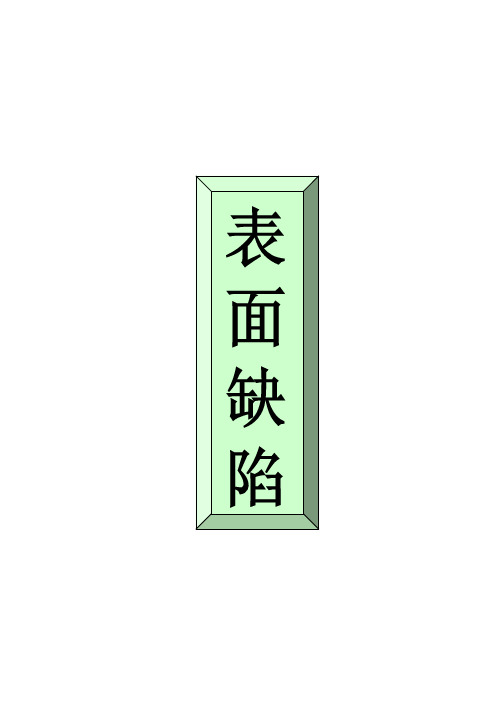
产生原因分析判断及解决办法1、金属液浇注温度低或模具温度低;2、合金成分不符合标准,流动性差;3、金属液分股填充,熔合不良;4、浇口不合理,流程太长;5、填充速度低或排气不良;6、压射比压偏低。
1、产品发黑,伴有流痕。
适当提高浇注温度和模具温度;2、改变合金成分,提高流动性;3、烫模件看铝液流向,金属液碰撞产生冷隔出现一般为涡旋状,伴有流痕。
改进浇注系统,改善内浇口的填充方向。
另外可在铸件边缘开设集渣包以改善填充条件;4、伴有远端压不实。
更改浇口位置和截面积,改善排溢条件,增大溢流量;5、产品发暗,经常伴有表面气泡。
提高压射速度,6、铸件整体压不实。
提高比压(尽量不采用)。
缺陷1 ---- 冷隔缺陷现象:温度较低的金属流互相对接但未熔合而出现的缝隙,呈不规则的线形,有穿透的和不穿透的两种,在外力的作用下有发展的趋势。
其他名称:冷接(对接)缺陷2 ---- 擦伤其他名称:拉伤、拉痕、粘模伤痕缺陷现象:顺着脱模方向,由于金属粘附,模具制造斜度太小而造成铸件表面的拉伤痕迹,严重时成为拉伤面甚至产生裂纹。
产生原因 分析判断及解决办法 1、型芯、型壁的铸造斜度太小或出现倒斜度; 2、型芯、型壁有压痕; 3、合金粘附模具;4、铸件顶出偏斜,或型芯轴线偏斜;5、型壁表面粗糙;6、涂料常喷涂不到;7、铝合金中含铁量低于0.6%; 8、合金浇注温度高或模具温度太高;9、浇注系统不正确, 直接冲击型壁或型芯 ; 10、填充速度太高;11、型腔表面未氮化。
1、产品一般拉出亮痕,不起毛。
修正模具,保证制造斜度; 2、产生拉毛甚至拉裂。
打光压痕、更换型芯或焊补型壁; 3、拉伤起毛。
抛光模具; 4、单边大面积拉伤,顶出时有异声修正模具结构; 5、拉伤为细条状,多条。
打磨抛光表面; 6、模具表面过热,均匀粘铝。
涂料用量薄而均匀,不能漏喷涂料; 7、型腔表面粘附铝合金。
适当增加含铁量至0.6~0.8%;8、型腔表面粘附铝合金,尤其是内浇口附近。
压铸件缺陷和改善对策
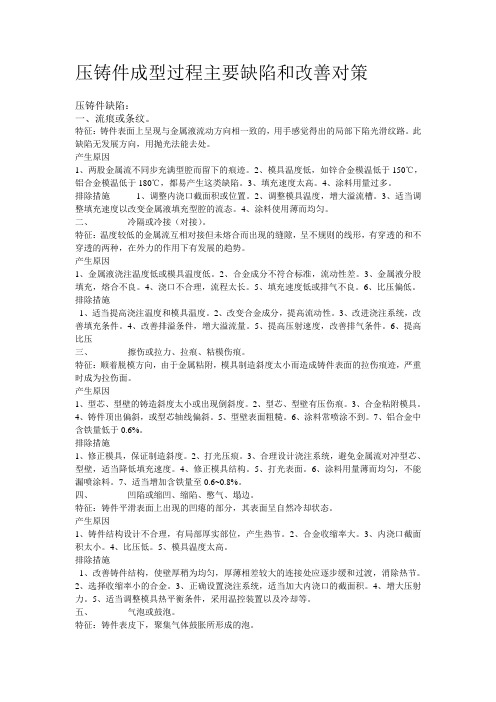
压铸件成型过程主要缺陷和改善对策压铸件缺陷:一、流痕或条纹。
特征:铸件表面上呈现与金属液流动方向相一致的,用手感觉得出的局部下陷光滑纹路。
此缺陷无发展方向,用抛光法能去处。
产生原因1、两股金属流不同步充满型腔而留下的痕迹。
2、模具温度低,如锌合金模温低于150℃,铝合金模温低于180℃,都易产生这类缺陷。
3、填充速度太高。
4、涂料用量过多。
排除措施1、调整内浇口截面积或位置。
2、调整模具温度,增大溢流槽。
3、适当调整填充速度以改变金属液填充型腔的流态。
4、涂料使用薄而均匀。
二、冷隔或冷接(对接)。
特征:温度较低的金属流互相对接但未熔合而出现的缝隙,呈不规则的线形,有穿透的和不穿透的两种,在外力的作用下有发展的趋势。
产生原因1、金属液浇注温度低或模具温度低。
2、合金成分不符合标准,流动性差。
3、金属液分股填充,熔合不良。
4、浇口不合理,流程太长。
5、填充速度低或排气不良。
6、比压偏低。
排除措施1、适当提高浇注温度和模具温度。
2、改变合金成分,提高流动性。
3、改进浇注系统,改善填充条件。
4、改善排溢条件,增大溢流量。
5、提高压射速度,改善排气条件。
6、提高比压三、擦伤或拉力、拉痕、粘模伤痕。
特征:顺着脱模方向,由于金属粘附,模具制造斜度太小而造成铸件表面的拉伤痕迹,严重时成为拉伤面。
产生原因1、型芯、型壁的铸造斜度太小或出现倒斜度。
2、型芯、型壁有压伤痕。
3、合金粘附模具。
4、铸件顶出偏斜,或型芯轴线偏斜。
5、型壁表面粗糙。
6、涂料常喷涂不到。
7、铝合金中含铁量低于0.6%。
排除措施1、修正模具,保证制造斜度。
2、打光压痕。
3、合理设计浇注系统,避免金属流对冲型芯、型壁,适当降低填充速度。
4、修正模具结构。
5、打光表面。
6、涂料用量薄而均匀,不能漏喷涂料。
7、适当增加含铁量至0.6~0.8%。
四、凹陷或缩凹、缩陷、憋气、塌边。
特征:铸件平滑表面上出现的凹瘪的部分,其表面呈自然冷却状态。
产生原因1、铸件结构设计不合理,有局部厚实部位,产生热节。
压铸产品品质改善报告范例
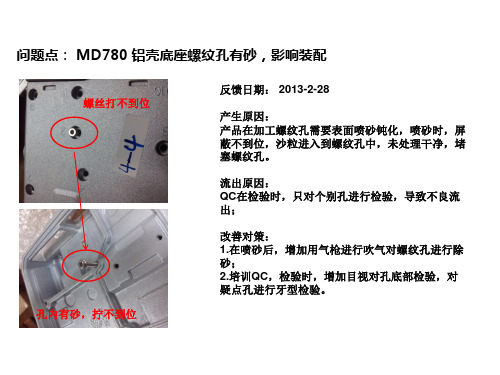
问题点: TC-780Ex螺丝孔攻穿
反馈日期: 2013-8-19
产生原因: 卡槽位滑块进入过多,卡槽边缘余量过少,钻孔后 边缘破裂;
流出原因: 此问题第一发生,未进行检验,导致不良流出。
改善对策: 1.修改模具,调整滑块长度,保证壁厚符合3D要求, 防止钻孔破裂;
改善对策: 1.生产领班在交接班时,对相关机台点检要求进行培训, 要求对刀具状态进行点检,并进行记录; 2.调机培训员,每天确认生产首件,并培训员工,进行孔 径自检; 3.对新QC进培训,由领班带领,对比SIP进行一次现场检 验培训,并对重点要求进行交接,再次提问进行考核,合 格上岗; 4.教育OQC,每次产品入库必须按抽样标准进行检验。
问题点: TC-580天线座螺孔底部多料,螺纹不贯通
反馈日期: 2013-6-7
产生原因: 模具疲劳崩缺,产品上多料,钻孔攻牙深度不够, 导致螺纹孔底部不贯通。
流出原因: 模具崩缺后,生产的产品未进行标识,分开加工, QC检验时,未拧穿检验。
改善对策: 1.维修模具,补焊缺料区域,改善多料现象; 2.调整加工深度,避免模具多料影响,改善螺纹不 贯通问题; 3.培训QC,要求在检验时对通孔检验,要求拧穿。
问题点: TC-780/795/ 780Ex卡槽边缘未倒角电池装不进
反馈日期: 2013-8-19
产生原因: 卡槽位置处于模具分模线处,压铸时,会产生披锋, 修披锋时未去除干净;
流出原因: 没有卡槽检具,无法正确判断,导致不良流出。
改善对策: 1.制作卡槽宽度检具,培训员工,要求对卡槽前端 进行倒角去披锋,并增加全检;
问题点: TC-780铝壳来料错误
浇注系统设计的优与劣

浇注系统设计的优与劣这是一个铝合金产品熔模铸造的组合方案,浇注系统设计采用阶梯式浇注系统。
大家看看,这个方案有没有问题? 姑且不论产品浇注系统设计有没有问题,单看其它设计有没有问题,是什么问题,如何修改?下面我们来分析一下这个产品设计到底有什么问题。
实际上这个产品浇注系统设计没有充分考虑脱蜡问题,这是这个浇注系统设计存在的最大问题。
我们知道,在熔模精密铸造中,浇注系统设计有三大作用:1.对金属液的导流作用,使金属液能顺利流入铸件型腔中;2.对铸件进行补缩,以形成完整、致密的铸件;3.在脱蜡时蜡的流道。
能保证脱蜡充分,不留残余。
而且保证脱蜡时能顺利脱蜡,不使模壳产生裂纹。
在这个案例中,我们可以判断,前两个作用完成应该没有多大问题,但是,后一个作用完成有一定问题。
首先,是模组在脱蜡车上的摆放问题。
由于模组明显重心不在浇道的中心线,所以模组在脱蜡车上摆放只能把截面积大的部分置于下部。
这显然与脱蜡时蜡流出方向是反方向。
脱蜡后蜡是受重力作用流动的,假如反其向流动,势必会造成脱蜡不畅进而导致模壳产生微裂纹,直至模壳报废。
一般情况下,脱蜡时模组的浇口杯处于下部,也是要利用重力使蜡料快速排出模壳。
其二,该浇注系统设计没有考虑模组在脱蜡车上的放置,在模组上不设计模组支撑,导致模组成偏重心状态,这也是这个设计存在问题的一点。
实际上对付像这类偏重心产品时,必须考虑脱蜡问题。
脱蜡时的放置以及脱蜡顺畅。
另外,脱蜡时的支撑也会成为脱蜡通道。
既能保证脱蜡顺畅,完全,而且还能保证浇注时通气排气,避免铸件产生气孔。
这样的设计何乐而不为?原则上讲,铝合金产品这么高的铸件,在采用大气浇注时应该采用蛇形浇道。
本产品浇注由于采用真空炉浇注,因而对浇注系统设计要求降低。
所以,本方案在浇注方面基本没有问题,就整个浇注方案设计如果打分,最多80分,但如果加上模组支撑,那就可以打90分以上。
当然,这仅是我个人观点,不当之处请大家评说。
压铸不良原因与措施

压铸不良原因与措施压铸是一种常见的金属加工方法,用于制造各种各样的金属零件。
然而,在压铸过程中常常会出现一些不良情况,导致产品质量下降或无法使用。
以下是一些常见的压铸不良原因及相应的措施。
1.缩孔(针眼)原因:高温熔融金属凝固时,金属液缩小所形成的孔洞。
措施:-控制材料的熔点和凝固温度,避免温度过高。
-提高注入压力和速度,确保金属充实完全。
-控制铸造工艺参数,如浇注温度、压力和速度,减少气体夹杂物。
2.气孔原因:熔融金属中混入空气或水分,冷凝成孔洞。
措施:-净化材料,确保金属液没有杂质。
-增加浇注温度,减少金属和气体冷凝。
-提高注入速度,使气体远离金属液。
3.热裂纹原因:金属在凝固过程中,由于残余应力、金属浓缩和组织缺陷等原因引起的开裂。
措施:-优化铸造工艺,减少或消除金属残余应力。
-控制金属的凝固速度,避免快速凝固造成应力集中。
-添加合适的合金元素,改善金属组织结构。
4.狭长缺陷原因:熔融金属填充模腔的过程中,金属液流动不均匀,形成局部过渡缩小的缺陷。
措施:-设计合理的铸造模具,确保金属液能够均匀填充模腔。
-调整铸造工艺参数,如入口和出口位置、浇注温度和速度,改善金属液流动状态。
-使用合适的流道和浇口设计,使金属流动更加均匀。
5.长气孔原因:金属液注入模腔的过程中,气体无法顺利排出,形成长而突出的孔。
措施:-增大出口尺寸,提高气体排出的通道。
-调整浇注顺序,避免气泡在金属液中积聚。
-使用适当的排气装置,确保顺畅排出气体。
6.表面不良原因:压铸件表面出现裂纹、气孔、疤痕等缺陷。
措施:-增加模具的冷却系统,提高金属液凝固速度。
-优化模具表面处理,减少摩擦和热传导。
-控制铸造工艺参数,如浇注温度和速度,减少金属液与模具的接触时间。
总之,压铸不良的原因和措施是多种多样的,需要根据不同情况采取相应的措施。
通过优化材料、设计模具、调整工艺参数等方法,可以有效地减少压铸不良,提高产品质量。
- 1、下载文档前请自行甄别文档内容的完整性,平台不提供额外的编辑、内容补充、找答案等附加服务。
- 2、"仅部分预览"的文档,不可在线预览部分如存在完整性等问题,可反馈申请退款(可完整预览的文档不适用该条件!)。
- 3、如文档侵犯您的权益,请联系客服反馈,我们会尽快为您处理(人工客服工作时间:9:00-18:30)。
一模多腔真空压铸浇注系统改善对产品的影响
摘要:在压铸实际生产过程中,发现很多铝合金铸件的内、外在质量与浇注系
统有密切的关系,同时有些传统的浇注系统设计思路也不利于铸件质量的提高。
随着技术革新,压铸真空系统新技术给产品带来更高质量的标准,能使产品满足后期装配要求。
在一模多腔的模具中,浇注系统的设计和真空系统良好的配合,才能生产出品质优良的产品。
关键词:真空压铸浇注系统一模多腔模具
1 前言
随着压铸技术产品不断深入到人们的日常生活,其各方面的特点越来越受到关注。
高质量、高性能才能满足科技发展以及人们日益增长的物质文化需求。
在压铸行业越来越多的产品已经开始使用真空压铸来提高产品的内在质量。
真空压铸方法是一种减少压铸件内气孔,提升压铸件力学性能的有效方法。
材料的成型方法层出不穷,铸造方法是工业生产的重要组成部分,同时也是现代机械制造工业的基础工艺之一
2.压铸工艺优缺点
2.1 压铸工艺优点
压铸的实质是在高压作用下,使液态或半固态金属以及高的速度填充进入压住模具型腔,并在压力作用下成型和冷却凝固而获得铸件的一种成形工艺。
由此可见,高压和高速充填压铸模具型腔时压铸工艺的两大特点。
与其他压铸方法相比压铸有其自身的优点:
(1)压铸件的尺寸精度高,表面粗糙度低
(2)材料利用率高
(3)可以制造形状复杂、轮廓清晰、薄壁深腔的金属零件
(4)在压铸件上可以直接嵌铸其他材料的零件,节省贵重材料和加工工时
(5)压铸件组织致密,具有较高的强度和硬度
2.2普通压铸工艺的局限性
事物往往具有两面性,虽然压铸工艺有着很多的优点,但是也不可避免地存在着许多迫待解决的问题。
这些问题即压铸工艺的局限性:
①压铸件常有气孔存在:这是由于压铸时,金属液以高速喷射状态填充型腔,型腔中的气体来不及排出而不可避免地会卷入到金属液中,从而产生气孔缺陷,降低了压铸件质量。
另外,高温时气孔内的气体膨胀会使压铸件的表面鼓泡,严重影响了压铸件外观,降低其整体的力学性能。
因此,压铸件一般不能进行热处理和焊接,也不宜在高温下工作。
②不适合小批量生产:其主要原因是压铸机和压铸模具的费用较为昂贵,加之压铸机生产效率很高,因而压铸工艺虽然可以给大批量生产带来较低的单件成本,但对小批量生产来说却不经济。
③压铸件尺寸受到限制:压铸模具的尺寸受到压铸机锁模力及其装模尺寸的限制,所以压铸工艺只适用于中小型铸件的生产,而不能应用于大型铸件。
同样,对于内凹复杂的压铸件,由于压铸模具及原理的限制,其压铸生产也较为困难。
④压铸合金种类受到限制:压铸模具受到使用温度的限制,而部分合金的熔点太高,致使其配套压铸模具寿命过低,使成本居高不下,难以应用于实际生产之中。
目前,用来进行压铸生产的合金主要是锌合金、铝合金、镁合金及铜合金等有色金属。
综观以上4钟局限性,②和④受限于经济成本,③受限于现有设备条件,迄今为止,技术上进展缓慢。
唯有①是产生于压铸工艺过程之中,可以通过一定的技术改进减少甚至完全避免气孔的产生。
事实上,也正是气孔问题的存在,不断推动着压铸工艺的改进,以满足人们对压铸件质量不断增高的要求,同时也拓展着压铸工艺的应用范围。
3 真空压铸法
真空压铸是将型腔中的气体抽出,金属液在真空状态下充填型腔,因而卷入的气体少,铸件的力学性能高,且真空压铸继承和保持了普通压铸法的优点。
为获得理想的压铸合金构件,必须尽可能的减少喷射的热金属与型腔内的空气和烟气接触;换言之,就是在压射开始至结束的全过程中尽可能地降低型腔内的空气和烟气的气体压力,将整个过程的气体含量减少到一个近于理想的状况。
真空就是要用来解决这个排气问题。
3.1真空压铸的特点
真空压铸法是通过在压铸过程中抽除压住模具型腔内的气体而消除或显著减少压铸件内的气孔和溶解气体,从而提高压铸件力学性能和表面质量的先进压铸工艺。
应用真空压铸法生产的铝镁合金压铸件已被证明可以采用焊接、热处理等加工手段,常温性能也有一定的提升。
总的来说,真空压铸法具有以下优点:
①真空压铸法可消除或减少压铸件内部的气孔,提高压铸件的机械性能和表面质量,改善镀覆性能;
②真空压铸法大大减少型腔的反压力,可使用较低的比压及铸造性能较差的合金,有可能用小机器压铸较大的铸件;
③真空压铸法改善了充填条件,可压铸较薄的铸件;
④真空阀将由合金动能关闭,压射外形的改变对真空阀的功能无影响
3.2 真空压铸的原理
在模具开设较深排气通道并与齿形集渣包相连,齿形集渣包再与带有油缸的真空阀相连,当铝水充填满排气槽后,将活塞顶回,活塞正好将与真空系统相连的通道封闭,关闭阀门。
在开模取出铸件后,活塞又返回到原来的位置。
此类真空系统,设置简单,只要求当冲头通过压室浇料口的时候,机器启动真空泵,但是,对模具制造和维护水平要求很高,特别是与真空阀相连的模具部位,相互配合的精度要求很高。
根据实际使用情况,此真空系统所达到的真空度也最高,效果最好,保证可靠。
同时真空阀要定期进行维护:在每40至45个工作小时,真空阀必须从铸模上拆卸下来以进行维护和清洗工作。
只有定期的清洗和维护才能保证真空系统的正常运用。
4.实例支架产品及其模具
4.1产品的特殊性能及装配要求
A26005支架产品用于发动机起支撑作用,其模具设计为一模六腔结构,在800T压铸设备上生产。
由于压铸本身工艺决定了产品内部不可避免有气孔缺陷,故唯有采用真空压铸才能使产品最大优质化。
A26005支架产品工序:真空压铸——切边——清理——钻孔——抛丸——检验——包装。
该产品质量要求非常高,年需求量大,在客户处需要进行旋铆加工,故对产品旋铆口部要求非常严格,要求无碰伤、裂纹、气泡等缺陷。
可是在实际的生产过程中,因为产品过程碰伤、时效后产品表面气泡等缺陷报废率高。
针对以上的缺陷,从模具结构、工艺参数、设备保证能力、过程质量控制等方面进行开展攻关改进。
4.2初始模具及其产生的问题
如图1设计模具的浇注系统,在远端设置一处渣包,这样设计的不足之处在后期进行批量压铸生产时时效工艺暴露出缺陷问题:
1)、因真空机使用及过程控制问题,未能实现完全抽真空,导致产品内部组织不良,进而实在时效工序暴露出气泡缺陷报废如图2。
2)、因为产品过程防护不当,且产品小而流转框太大,使产品摆放不受控,前期阶段碰废严重。
3)、因为采用老式保温炉,达不到A260050、A260051产品的工艺要求。
(保温温度340℃,保温时间:4小时)
4)、产品年需求量大,1模6件设计,模具结构难以全面考虑到进料速度问题。
图1 图2
在分析产生气泡缺陷时发现至少两个原因导致的:一是真空机运用失效;二是模具本身结构问题。
针对上诉两个原因,采用以下措施:
1)、购置方达瑞进口真空阀真空机,并接受其专业老师的培训。
同时,在真空系统报警后,增加程序使压铸自动停止生产,避免盲目生产。
2)、定期培训操作员工,在产品的过程摆放中,轻拿轻放,不能甩扔零件,整齐摆放在产品框中,层与层用隔板防护。
3)、新购置时效炉,与厂家技术员交流,为A260050、A260051产品的时效参数设计炉子,并设计制作专用时效隔板,保证产品在炉中充分时效。
4)、优化了模具的浇注系统和过程工艺参数,使产品成型更好。
模具结构缺陷:如图2从左到右分布的型腔号为:1-1、1-2、1-3、1-4、1-5、1-6,由于2#和3#型腔铝水先到达排溢系统,将1#腔即将跑出的铝水和气体堵在浇注系统中,造成两个远端产品的气泡缺陷严重,使产品的合格率大大降低。
通过修改模具可以改善这一状态:增加集渣包,同时将横浇道的宽度加大10mm,即19.9改为29.9,21.89改为31.89。
远端的浇道不作修改,这样在进行抽真空时,两个远端内的铝液快速填充型腔使气体可以有效的被排出。
经过这样的改进,降低了产品在后续时效工艺中气泡废品率。
图3
4.3模具浇注系统及时效控制的改善前后质量对比
在进行项目攻关前,产品因为气泡报废率高达10.68%,下表是改善前后是
通过改善模具浇注系统以及过程控制,产品质量较好,且提高了产品的合格率。
参考文献:
[1]赖华清.压铸工艺及模具,北京:机械工业出版社,2004.6
[2]杨欲国.压铸工艺与模具设计,北京:机械工艺出版社,2007.11
[3]陈丕瑾.真空技术的科学基础,北京:国防工业出版社,1987.196-210
[4]潘欢.铝合金压铸高真空技术的开发应用,2008.5.28
[5]瑞士方达瑞.真空通道设计手册[M].。