压铸模设计说明书
压铸模具课程设计说明书
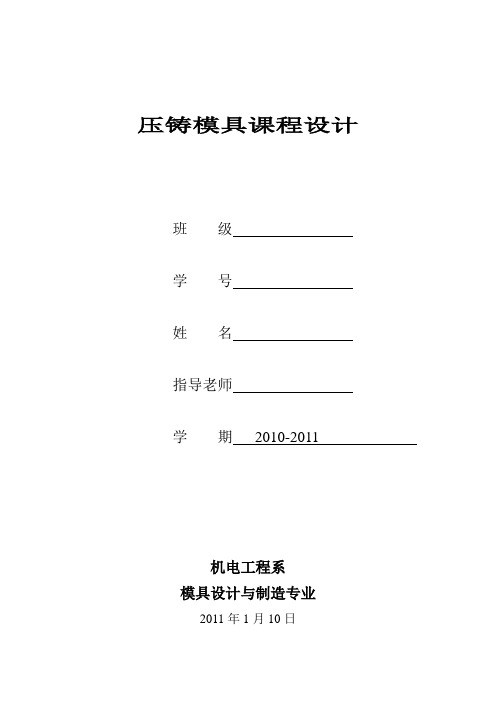
压铸模具课程设计班级学号姓名指导老师学期2010-2011机电工程系模具设计与制造专业2011年1月10日压铸模具课程设计任务书课题名称:铸件图(毛坯)铸件材料:生产批量:4万件设计要求:1、按设计指导书要求完成压铸模具装配图、零件图的绘制。
2、编写设计说明书。
3.将说明书和图样装订成册。
1、对制品成型材料的分析:本制品的材料为铝合金。
其流动性好,溢边值为0.04mm 左右,尺寸精度高,变形小,具有优异的力学综合性能。
但因为铝合金有很强的亲和力,易粘膜,应在冷室压铸机上压铸。
制品的精度为IT8。
2、压铸机的选择:由计算可知所选用的压铸机为:J116E型卧式冷室压铸机。
(1)合模力:630KN(2)动模座板尺寸:325*320mm(3)模具厚度:150~350mm(4)动模座板行程:240mm(5)顶出行程:60mm(6)压射力:90KN(7)压室直径:35~40mm(8)一次金属注入量:0.5KG(9)压实压力:57~94MPa(10)压射行程:282mm(11)机器外形尺寸:3970*1050*2100mm3、分型面的确定:分型面选在制品外型尺寸最大之处即制品的直径大端。
在此分型,一便于开模后留在动模;二能确保制品的外观质量;三是使加工、修配、更换都很方便,降低模具制造的难度,从而降低模具的制造成本。
4、成型尺寸的计算:(1)型腔径向成型尺寸计算:型腔的径向尺寸,是趋于变大的尺寸。
为了延长其寿命,应将其尺寸适当做小一点。
所以,根据经验减去制品公差(δ)的3/4计算公式:L M={L S(1+Scp)-3/4(Δ)}+(δ)(2)型腔深度成型尺寸计算:型腔的深度成型尺寸,也是趋于变大的尺寸。
为了延长其寿命,叶应将其尺寸适当做小一点。
所以,根据经验减去制品公差(δ)的2/3计算公式:H M={H S(1+Scp)-2/3(Δ)} +(δ)(3)型芯径向成型尺寸计算:型芯的径向尺寸,是趋于变小的尺寸。
模具毕业设计34电机端盖压铸模设计说明书

一、零件图如图1-1所示制件为电机端盖,材料为锌合金,属大批量生产。
图1-1一、该压铸件的材料分析和工艺性分析1. 材料分析该产品的成型材料是锌合金,该材料密度大,铸造性能好,可压铸复杂的零件,压铸时不粘模,压铸件表面易镀Cr、Ni等金属,机械切削性能好,但易老化,抗腐蚀性能不高。
2. 工艺性分析1)锌合金压铸,其锌不容易就粘在模具表面上。
2)该压铸件壁厚比较均匀,各个孔小且浅,工艺性好。
3)为了方便加工与成型及脱模,型腔、型芯均采用组合式结构。
4)该压铸件是一般精度等级。
为降低设计难度和设计周期,应采一模一腔,且需要对压铸件去除浇口废料。
二、拟定的成型工艺1.成型方法该压铸件采用冲头下压式全立式压铸机压铸。
2.各工艺参数1)经查教材(压铸成型工艺与模具设计)第32页表3.2可知压射比压为30Mpa2)经查教材第33页表3.4可知压射冲头空行程压射速度为0.3~0.5m/s 3)经查教材第34页表3.5可知充填速度为15 m/s 4)经查教材第36页表3.7可知持压时间3~4s5)经查教材第36页表3.8可知留模时间推荐值为7~12s 6)经查教材第37页表3.9可知浇注温度为410~540C 。
7)经查教材第38页表3.10可知模具预热温度130~180C 。
和工作温度180~200C 。
3. 确定型腔数目1)为降低设计难度和设计周期,应采单型腔,且需要对压铸件去除浇口废料。
2)计算压铸的体积和重量通过三维制图PRO/E 软件测量得:单件压铸件投影面积S=14257㎜2;体积V=153645㎜3查有关资料可知Al 的密度为6.8g/cm 3则压铸件重量m=1044.8g三、初选压铸机1.压铸机的锁模力模具型腔胀型力中心与压铸机压力中心重合时压铸机锁模力 S F K ≥Z N (F +F )式中 S F —压铸机锁模力,N ;Z F —作用于模具型腔且垂直与分型面方向的胀型力,N ; N F —作用于滑快楔紧块面上的法向压力,N ;K —安全系数(一般取K=1~1.3)型腔胀型力Z F =P (123A +A +A )式中 P —最终的压射比压,Pa ;1A —铸件在分型面上的投影面积,㎡;2A —浇注系统在分型面上的投影面积与压铸件投影面积不重叠部分,㎡;3A —溢流槽在分型面上的投影面积,㎡;压铸机所容许的压射比压20.785n Fp D=式中 n p —压铸机所容许的压射比压,Pa ; F —压射力,N ; D —压室直径,m 。
UG压铸模具设计说明书

UG压铸模具设计说明书UG压铸模具设计说明书一、设计背景本设计说明书旨在介绍UG压铸模具的设计过程和技术要求。
二、产品概述2.1 产品名称2.2 产品规格2.3 产品用途2.4 产品材料三、模具结构设计3.1 模具总体结构设计3.1.3 滑块设计3.2 液压系统设计3.3 水冷系统设计3.4 模芯设计3.5 模芯抽出机构设计3.6 模具定位与导向设计3.7 模具冷却设计3.8模具开合机构设计四、模具零件设计4.1 模具基座设计4.2 模具板材设计4.3 模具腔体设计4.4 模具芯杆设计4.5 模具滑块设计4.6 模具导向柱设计4.7 模具螺栓设计4.8模具冷却管道设计4.9模具其他零部件设计五、模具加工与装配5.1 模具加工工序5.2 模具加工及装配质量控制5.3 模具材料选择和处理5.4 模具零部件的精度要求5.5 模具零部件的表面处理六、模具试产与调试6.1 模具试产准备6.2 模具试产过程6.3 模具试产缺陷及解决办法6.4 模具调试注意事项七、安全与环保7.1 安全操作规程7.2 模具整体安全防护设计7.3 环保要求和措施八、引用的法律名词及注释1、模具:用于制造产品的模具,也称压铸模具。
2、滑块:模具中用于实现产品形状的可移动部分。
3、模芯:模具中用于形成产品内部结构的零件。
4、冷却系统:模具中用于降低温度并加快产量的系统。
5、开合机构:模具中用于实现模具开合动作的机构。
九、附件本文档涉及附件详见附件列表。
压铸模设计手册第一季

热流道与普通流道实物对比
Mass Saved Kilograms 40 to 80 tonnes 80 to 160 tonnes 50,000 83,000
Cost Saved Dollars $30,000 $50,000
160 to 320 tonnes
320 to 650 tonnes
190,000
原理:把镁合金颗粒投入料斗,原 料经过加热到高温的筒,螺杆的转 动对镁合金产生剪切作用,使其成 为具有触变物理性能的半固态浆料, 快速注射到模具内成形。
成形原理
射铸成形过程(1)
射铸成形过程(2)
射铸成形机
射铸成形产品图
第一讲 完
使枝晶破一流变压铸rheocasting金属锭液态制备浆料搅拌冷却半固态浆搅拌冷却半固态浆料压铸二触变压铸thixocasting金属锭液态制备浆料搅拌冷却半固态浆搅拌冷却料淬冷铸锭切割胚料重新加热触变压铸半固态浆半固态压铸工艺过程优点
第一讲 压 铸 新 工 艺
压 铸 简
压力铸造的定义:
介
熔融金属在压射冲头作用 下,高压高速充填型腔,并且在 高压下凝固形成铸件的铸造工艺。
热压室压铸机 (Hot Chamber Die Casting Machine)
热压室压铸机压铸工艺简图
冷压室压铸机 (Cold Chamber Die Casting Machine)
冷压室压铸机压铸工艺简图
压铸工艺的优点
1、可以制造形状复杂、轮廓 清晰的铸件。 2、压铸件表层组织致密,使 压铸件具有较高的硬度和强 度。
(二)触变压铸(Thixocasting) 金属锭→液态→制备浆料 (搅拌→ 冷却)→半固态浆 料→淬冷→铸锭→ 切割胚料 → 重新加热→触变压铸
压铸模具说明书

压铸模具说明书(总10页)
--本页仅作为文档封面,使用时请直接删除即可--
--内页可以根据需求调整合适字体及大小--
压铸模具说明书1307-YJ-799-A
目录
1、模具概述
2、毛坯机加工余量示意图此零件向客户提供压铸件,不做机加工
3、模穴编号示意图
此零件一出一,未刻模穴号,滑块编号如下图:
4、模具镶针编号图
镶针图档请看维响中最终的档案
5、模具备件清单
6、顶针编号表
7、顶针高度表
编号直径高度高度公差备注
A15+0
B16-8+/
B26-8+/
B36+0
B46+0
B56+0
B66+0
B76+0
B86+0
B96+0
B106+0
B1160+/
B1260+/
D18-10+/
X27+0可换刻字镶针
注:高度以分型面为基准,高出为正,低下为负。
8、模具水路图动模水路如下图:
注:点水1,2铜管高50
定模水路图如下图
9、一模多款产品对照表
此产品目前共六款,通过更换顶针X2,滑块,及滑块镶针C2/3实现,具体对照表如下:
10、装模注意事项及其他
此模具在280T上旋转吊装
此模具在350T上旋转吊装
11、喷雾示意图动定模喷雾示意图
定模喷雾示意图
11。
锌合金压铸模热处理工艺设计说明书
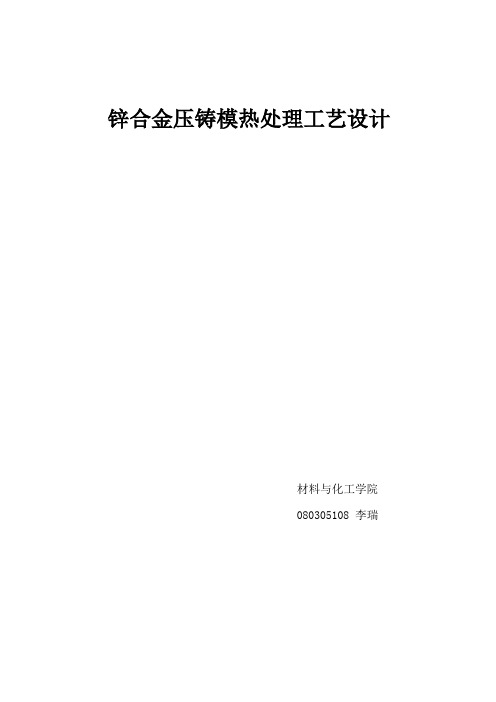
锌合金压铸模热处理工艺设计材料与化工学院 080305108 李瑞关键词:热作模具钢,H13,热处理,温度,时间。
引言:压铸模生产效率高,能压铸形状复杂、尺寸精确、轮廓清晰、表面质量及强度、硬度都较高的压铸件,故应用较广,发展较快。
目前,铝合金压铸件产量最多。
铝合金压铸模的失效形式主要是热疲劳(龟裂)、侵蚀、磨损、变形和开裂等[1]。
压铸模的工作条件较为苛刻,在生产过程中,其型腔直接与高温、高压、高速的金属液相接触,工作环境非常恶劣,不断受到金属液的冲刷、磨损、高温氧化和各种腐蚀,因而压铸模的使用寿命不高,与国外相比,也有较大差距,使用寿命仅为国外同类模具的1/5~1/3。
压铸模的制造成本占产品成本的15%~20%[2],因此,提高压铸模的使用寿命是许多企业共同关注的技术课题。
压铸模材料对其热疲劳寿命的影响极大,一般要求应具有较高的耐热疲劳、耐磨性、耐蚀性、冲击韧度、红硬性和良好的脱模性能等。
1. 锌合金压铸模的使用性能及要求压铸模寿命与压铸模的材料密切相关。
一方面受到金属液的直接冲刷磨损,高温氧化和各种腐蚀,另一方面由于生产的高效率,模具温度的升高和降低非常剧烈,并形成周期性的变化。
因此,压铸模的工作环境十分恶劣。
其使用性能的要求如下:a 具有良好的可锻性和切削性;b 高温下具有较高的红硬性,高温强度,抗回火稳定性和冲击韧度;c 具有良好的导热性和抗疲劳性;d 具有足够的高温抗氧化性;e 热膨胀系数小;f 具有高扽耐磨性和耐蚀性;g 具有良好的淬透性和较小的热处理变形率。
2. 选材(选用H13钢)我国锌合金压铸模多年来一直用3Cr2W8V钢制造,它具有良好的高温强度和热硬性,但热硬姓和热疲劳抗力较差,使这种钢在制造时过早出现热疲劳裂纹并很快扩展影响产品质量和模具使用寿命。
4Cr5MoSiV(H13)具有较高的热强性和热硬性,有相当高的韧性和耐冷热疲劳性,不易产生热疲劳裂纹,用其制作的模具使用寿命有较大提高。
压力铸造模具设计说明
压力铸造模具设计说明一、压铸简介压力铸造简称压铸,是一种将熔融合金液倒入压室内,以高速充填钢制模具的型腔,并使合金液在压力下凝固而形成铸件的铸造方法。
压铸区别于其它铸造方法的主要特点是高压和高速。
①金属液是在压力下填充型腔的,并在更高的压力下结晶凝固,常见的压力为15—100MPa。
②金属液以高速充填型腔,通常在10—50米/秒,有的还可超过80米/秒,(通过内浇口导入型腔的线速度—内浇口速度),因此金属液的充型时间极短,约0.01—0.2秒(须视铸件的大小而不同)内即可填满型腔。
压铸机、压铸合金与压铸模具是压铸生产的三大要素,缺一不可。
所谓压铸工艺就是将这三大要素有机地加以综合运用,使能稳定地有节奏地和高效地生产出外观、内在质量好的、尺寸符合图样或协议规定要求的合格铸件,甚至优质铸件。
1、压铸机(1)压铸机的分类压铸机按压室的受热条件可分为热压室与冷压室两大类。
而按压室和模具安放位置的不同,冷室压铸机又可分为立式、卧式和全立式三种形式的压铸机。
热室压铸机立式冷室卧室全立式(2)压铸机的主要参数a合型力(锁模力)(千牛)————————KN b压射力(千牛)—————————————KN c动、定型板间的最大开距——————————mm d动、定型板间的最小开距——————————mm e动型板的行程———————————————mm f大杠内间距(水平×垂直)—————————mm g大杠直径—————————————————mm h顶出力——————————————————KN i顶出行程—————————————————mm j压射位置(中心、偏心)——————————mm k一次金属浇入量(Zn、Al、Cu)———————Kg l压室内径(Ф)——————————————mm m空循环周期————————————————s n铸件在分型面上的各种比压条件下的投影面积注:还应有动型板、定型板的安装尺寸图等。
UG压铸模具设计说明书
基于UG的闭门器压铸模具设计学校:重庆工商大学专业:机械制造及其自动化班级:06模具姓名:***学号:**********指导教师:**目录1 UG压铸模具设计基础 (1)1.1 压铸模具设计基础 (1)1.1.1 压铸模具结构及其组成 (1)1.1.2 压铸模具设计原则 (2)1.1.3 压铸机的选用 (3)第2章UG压铸件建模 (5)2.1压铸件建模 (5)第3章UG压铸模具分型面设计与零部件的创建 (6)3.1 压铸模具及其零部件的设计过程 (6)3.1.1 压铸模具设计过程 (6)3.1.2 压铸模具零部件及其设计过程 (6)3.1.3 压铸模具零件功能分析 (9)3.1.4 压铸模具零件分类................................................................ 错误!未定义书签。
3.2 压铸件脱模阻力计算与动、定模的划分......................................... 错误!未定义书签。
3.2.1 压铸件的脱模工作过程........................................................ 错误!未定义书签。
3.2.2 压铸件冷却收缩所引起的脱模阻力.................................... 错误!未定义书签。
3.2.3 抽芯机构所引起的压铸件动、定模脱模阻力.................... 错误!未定义书签。
3.2.4 压铸件形状特征在模具动、定模的分布............................ 错误!未定义书签。
3.3 压铸模具成型零件设计..................................................................... 错误!未定义书签。
3.3.1 压铸模具成型零件的结构.................................................... 错误!未定义书签。
压铸模课程设计
压铸模课程设计井冈山大学压铸模课程设计说明书题目薄壁壳体压铸工艺与压铸型设计院(部):机电工程学院专业:材料成型班级:姓名:学号:指导教师:完成日期:目录摘要 (Ⅲ)1前言1.1选题背景和意义 (1)1.2 压铸相关文献综述 (1)2零件设计 (5)2.1 零件分析 (5)2.2初步确定设计方案 (5)3压铸件工艺分析 (6)3.1 压铸合金工艺分析 (6)3.2 压铸件工艺分析 (6)3.3 分型面的选择 (6)4排溢系统与浇注系统设计 (8)4.1 浇注系统的设计 (8)4.2 排溢系计统的设 (10)5 压铸模结构设计 (12)5.1 压铸机的选择 (12)5.1.1确定模具分型面上铸件的总投影面积 (12)5.1.2 确定压射比压 (13)5.2 型腔和型芯尺寸的设计 (14)5.3 镶块、型芯、模板的设计 (14)5.3.1 镶块的设计 (14)5.3.2 型芯的设计 (15)5.3.3 动、定模板的设计 (16)5.4 滑块的设计 (18)5.5斜销的设计 (19)5.6压板设计 (20)5.7垫块的设计 (21)5.8导柱、导套的设计 (22)5.9浇口套的设计 (23)5.10分流锥的设计 (24)5.11推出机构、复位机构的设计 (24)5.12模具装配图设计 (25)5.13 压铸模的技术要求 (26)6 压铸机校核 (27)6.1 压室容量的核算 (27)6.2 模具厚度核算 (27)6.3 动模行程核算 (28)7 压铸工艺流程 (30)8结论 (31)9参考文献.................... .. (32)薄壁壳体压铸工艺与压铸型设计摘要压铸是制造业的一种工艺,能够成型复杂的高精度的金属制品,多用于汽车制造,机械制造等。
本课题是对铝壳体进行模具设计并分析加工工艺。
本模具考虑到年产量、工厂的设备及铸件的精度要求,选择一型两腔结构。
以制品的最大端面为分型面,使制品顺利脱模。
压铸设计说明书
1绪论1.1模具行业发展现状[11]现代模具行业是技术、资金密集型的行业。
近年来,我国模具行业结构调整步伐加快,主要表现为大型、精密、复杂、长寿命模具和模具标准件发展速度高于行业的总体发展速度;塑料模和压铸模比例增大;面向市场的专业模具厂家数量及能力增加较快。
随着经济体制改革的不断深人,"三资"及民营企业的发展很快。
据国家统计局统计截止2006年底,中国模具制造业规模以上企业1314家,从业人员244155人;全年完成工业总产值555.61亿元。
实现销售收人和利润539.58亿元和46.7 5亿元;出口10亿美元。
进口14.7亿美元。
如果加上未统计的小型模具企业,估计我国现有的模具生产厂超过2万家,总从业人员在50万人左右。
生产压铸模的企业,一般兼作其它模具,但模具生产企业,不都生产压铸模。
由于压铸模生产的复杂性。
这些企业中只有一部分企业能生产压铸模。
全国铸造模具生产企业。
大体可以分成以下几类:第一类为铸造模具专业厂,包括合资和独资企业,这些厂设备先进,技术优良。
是铸造模具行业的主力;第二类是铸造专业厂的模具车间;第三类是近年来发展迅速的私营和民营模具厂,规模不大,数量众多,各有分工,分布在江浙、广东一带,部分厂己经具备了一定的实力;第四类是兼做铸造模具的其它一些模具厂。
总之,铸造模具生产企业里多元化,并向高水平在发展。
世界上许多国家,特别是一些发达国家都十分重视模具技术的开发,大力发展模具工业。
积极采用先进技术和设备,提高模具制造水平,己取得了显著的经济效益。
国外发达国家的模具厂一般规模都不大,但专业化强。
技术水平高,生产效率极高。
大体分为两类,一类是独立的模具厂,另一类是隶属于一些大的集团公司的模具厂。
国外模具企业人员并不是很多,一般不超过100人,多数在50人以下。
在人员结构上,设计、质量控制、营销人员要超过30%,管理人员在5%以下。
人均生产率很高。
年人均产值大多在15万-20万美元,有的达到25万-30万美元。
- 1、下载文档前请自行甄别文档内容的完整性,平台不提供额外的编辑、内容补充、找答案等附加服务。
- 2、"仅部分预览"的文档,不可在线预览部分如存在完整性等问题,可反馈申请退款(可完整预览的文档不适用该条件!)。
- 3、如文档侵犯您的权益,请联系客服反馈,我们会尽快为您处理(人工客服工作时间:9:00-18:30)。
湘潭大学毕业设计说明书题目:压铸件模具设计学院:机械工程学院专业:材料成型及控制工程学号:姓名:指导教师:完成日期: 2015.3.16目录一.设计前准备工作 (1)1.压铸工艺分析: (1)2.零件初步分析 (1)3.初步确定设计方案: (1)二.压铸件工艺分析 (2)1.压铸合金工艺分析: (2)2.压铸件工艺分析: (2)3.分型面的选择: (2)三.浇注系统和排溢系统的设计 (3)1.浇注系统的设计: (3)2.溢流排气系统的设计: (3)四.压铸机的选择 (4)1.压铸机的种类和特点 (4)2.选定压射比压 (5)3.确定型腔数目及布置形式 (5)4.确定模具分型面上铸件的总投影面积 (5)5.计算锁模力: (6)五.压铸模的结构设计 (7)1. 成型零件设计 (7)2. 结构零件设计 (9)3、各零件采用材料要求 (14)4、螺钉选用 (15)六、压铸模的整体结构 (15)1、压铸模的技术要求 (15)2、压铸模外形和安装部位的技术要求 (16)七、校核模具与压铸机的有关尺寸 (17)1、锁模力的校核 (17)2、铸件最大投影面积校核 (17)3、压室容量校核 (17)4、模具厚度的校核 (17)5、开模行程的校核 (17)八、参考文献: (18)一.设计前准备工作1.压铸工艺分析:压力铸造是将液态或半液态的金属,在高压作用下,以高的速度填充压铸模的型腔,并在压力作用下快速凝固而获得铸件的一种方法。
高压力和高速度是压铸时熔融合金充填成型过程的两大特点,也是压铸与其它铸造方法最根本的区别所在。
压铸件尺寸精度和表面粗糙度较好,铸件轮廓清晰,有致密的表层,比内层有更好的机械性能,内部存在气孔和缩孔缺陷。
2.零件初步分析零件为对称圆筒型零件,截面为工字形,中心开有一小孔。
壁厚为5mm,属于薄壁零件。
型腔深度约为97.5mm,属于深腔。
零件图如下所示:图1-1 零件图3.初步确定设计方案:1)压铸合金此铸件的材料为YZCuZn40Pb:此材料属于铅黄铜合金,具有加工性能较好,成本较低等优点,多用于化工、造船的零件和耐磨的零件。
2)铸件的精度设计为CT8级,采用压力铸造的方法能达到此精度。
3)确定压铸工艺及模具制造能力。
4)确定压铸模结构(包括分型面,型腔数目,浇注系统,成型零件的尺寸设计,结构零件的尺寸设计,以及采用型芯、型腔镶块节约贵重金属)。
二.压铸件工艺分析1.压铸合金工艺分析:1)力学性能高;2)良好的耐蚀、耐磨性能,疲劳极限和导热性高,线膨胀系数小;3)导电性能好,且具有抗磁性能;4)熔点高,模具使用寿命短。
2.压铸件工艺分析:为了从根本上防止压铸件产生缺陷,并以低成本,连续不断地生产高质量的压铸件,必须使压铸件的结构适合于压铸。
主要对铸件的壁厚、圆角、筋、出型斜度,孔,螺纹、加工余量、文字、标志、图案等进行分析。
本次铸件壁厚均匀适合压铸。
铸件的平均壁厚约为5mm,为薄壁压铸件,表面不加工,故无加工余量。
铸件本身有斜度且能减少出型时与型壁的摩擦。
铸件上无侧孔,不需设计侧抽芯结构。
该铸件内部有一个台阶,在模具设计时,拟在定模和动模各设计一个型芯。
拟采用推管推出机构。
3.分型面的选择:1)考虑到模具起模时,铸件留在动模上;2)尽量使模具整体结构简单;3)考虑铸件有一定同轴度的要求;4)同时注意使模具不至于过高。
所以铸件设计及分型面选择如下:图2-1 铸件图如图所示,选择1为分型面。
三.浇注系统和排溢系统的设计1.浇注系统的设计:经过对铸件的结构分析,铸件是对称件,对浇注系统的选择可选择侧浇口,在浇注时金属液沿分型面从型腔边缘导入,然后自下而上推向进型腔,有利于金属液的充填和排气。
采用切线浇口,避免金属液正面冲击型芯,提高模具使用寿命。
对浇注系统尺寸的设计:表3-1 浇注系统尺寸压铸件及溢流槽体积:V=206677内浇口横截面积:=473取内浇口厚度:T=3mm则内浇口宽度:L==158mm2.溢流排气系统的设计:铸件采用侧浇口切线形式,故采用分型面排气方式,无需另开设排气槽;溢流槽需在试模后确定是否开设,若需要,则开设于金属液充填最后封闭位置,以储存前端冷污金属。
溢流槽尺寸的设计如图所示:图3-1 溢流槽浇注系统及溢流排气系统的结构如下图所示:图3-2 浇注系统及溢流排气系统设计图四.压铸机的选择压铸机是压铸生产最基本的要素之一。
金属压铸模是通过压铸机的运行而实现压铸成型的。
1.压铸机的种类和特点压铸机的种类和型号很多。
一般说来,根据压铸机压室的温度状态,可分为热压室压铸机和冷压室压铸机。
冷压室压铸机又根据其结构形式分为立式压铸机,全立式压铸机和卧式压铸机。
目前,热压室压铸机通常仅适用于压铸铅、锌等低熔点合金,国外正在研究铝、镁等较高熔点合金的压铸技术。
1)立式冷压室压铸机的特点:a)适宜于压射可设置或必须设置中心浇口的压铸件。
b)金属液注入直立的压室中,操作比较方便,占地面积少。
c)在操作时,只有在浇注余量切断后,方可开模,生产效率较低。
d)金属液进入型腔时,经过90°角的转折,压力损失较大。
2)全立式冷压室压铸机的特点:a)压射冲头与直浇道方向相同,金属液进入型腔的流程短,压力损失和热量损失较小。
b)压射冲头垂直方向运行,运动平稳。
c)模具水平放置,活动型芯和嵌件安放方便、稳定、可靠。
d)占地面积少。
e)压铸件推出后需用手工取出,生产效率较低,不容易实现自动化操作。
3)卧式冷压室压铸机的特点:a)压室与压射冲头均为水平放置,金属液注入型腔时,浇道转折少,其压力损失小,有利于发挥增压机构的作用。
b)模具安装方便,卧式压铸机一般设有中心和偏心多个浇注位置,或在偏心和中心间设置可任意调节位置的扁孔。
c)便于操作,便于调整,压铸效率较高,是目前广泛应用的压铸设备。
d)压室内表面容易氧化。
e)金属液在压室内暴露在大气的表面积较大,压射时容易将空气、氧化物质及其它杂质带入型腔,引起压铸缺陷。
综合考虑铸件的形状及特点,选用卧式冷压室压铸机。
2.选定压射比压表4-1 压射比压(增压)推荐值(MPa)压铸件种类锌合金铝合金镁合金铜合金一般件13~20 30~50 30~50 40~50承载件20~30 50~80 50~80 50~80 耐气密性件或大平面薄壁件25~40 80~120 80~100 60~100 电镀件20~30选定压射比压p=70Mpa。
3.确定型腔数目及布置形式根据铸件图样及产量等要求,确定该模具的型腔数为一模一腔。
4.确定模具分型面上铸件的总投影面积ΣA=A铸+A浇+A余+A溢=6850mm2(式4.1) A铸——铸件在分型面上的投影面积;A 浇——浇道内浇口在分型面上的投影面积;A 余——余料在分型面上的投影面积;A 溢——溢流槽在分型面上的投影面积;因试模前暂时不开设溢流槽,故在计算时忽略。
5.计算锁模力:锁模力是表示压铸机最基本参数,其作用是克服压铸充填时的胀型力,使模具分型面不致张开,故设计压铸模时,首先确定胀型力的大小来选择压铸机,当压铸机的锁模力大于胀行力,则可认为该压铸机可以使用。
)+(=分主胀锁F F K KF F (式4.2)-压铸机应有的锁模力(N) -胀型力(N)-安全系数(一般取1.25)-主胀型力,与分型面上金属的投影面积有关的胀型力(N)-由侧面胀型力引起的沿锁模力方向上的分力(N),本模具不含侧型芯,故 =0F 主=Ap (式4.3)P -比压(MPa)A -压铸件、浇口和溢流槽三部分金属在分型面上的总投影面积(mm 2)计算可得,F 胀=479.5kN ,F 锁≥599.375kN;故初步选定压铸机为J116型卧式冷室压铸机,压铸机主要参数见下表表4-2 J116型卧式冷室压铸机主要参数 名称数值 名称 数值 锁模力(吨)63 压室最大容量(铝)(公斤) 0.6 开模力(吨)7 铸件最大投影面积(厘米2) 95 压射力(吨)5~9 工作循环次数(次/小时) 150~180 压射回程力(吨)2~5 管路工作压力(公斤/厘米2) 100 模板最大间距(毫米)570 电动机功率(千瓦) 11 合模行程(毫米)320 贮压罐容积(升) 100 模具尺寸(毫米) 360*450 贮压罐高度(毫米) 2430锁F 主F 分F K 胀F 分F压射偏心距(毫米) 60 压铸机外形尺寸(毫米) 3430*1200*1360 压室直径Ф(毫米) 30 40 45 压铸机重量(吨) 3压射比压(公斤/厘米2) 565~1270五.压铸模的结构设计1. 成型零件设计1)成型零件结构设计采用镶拼式结构,优点在于:a)采用整体镶块简化加工工艺,提高模具制造质量,易满足成型部位的精度要求;b)合理使用热作模具钢,降低成本;c)易损件有利于更换和修理;d)压铸件的局部结构改变时,不致使整套模具报废;e)可按铸件的几何形状在镶块上构成复杂的分型面,而在套板上仍为平直分型面;2)成型零件尺寸设计a)确定收缩率表5-1 计算收缩率由表5-1确定铸件收缩率为:受阻收缩率:0.6%;混合收缩率:0.8%;自由收缩率:1.0%。
b) 计算模具成型尺寸型腔尺寸计算公式:(式5.1)型芯尺寸计算公式: D ′、H ′—型腔尺寸或型腔深度尺寸(mm );D 、H —压铸件外形的最大极限尺寸(mm );d ′、h ′ —型芯尺寸或型芯高度尺寸(mm );d 、h —压铸件内形的最小极限尺寸(mm );φ —压铸件计算收缩率(%);△ —压铸件公称尺寸的偏差(mm);△′ —成型部分公称尺寸的制造偏差(mm ),因为CT8级精度与IT14级精度相似,故取△’=△/4;0.7△ —尺寸补偿和磨损系数计算值(mm );取受分型面影响的误差补偿值为0.05,受影响时应减去此补偿值。
表5-2 GB/T6414公差CT8级标准表: 基本尺寸(mm )公差带(mm) 公差(mm) >≤ —10 1 ±0.5 1016 1.1 ±0.55 1625 1.2 ±0.6 2540 1.3 ±0.65 4063 1.4 ±0.70 63100 1.6 ±0.80 100160 1.8 ±0.90 160250 2 ±1.0 250 400 2.2 ±1.1'''0)7.0(∆+∆∆-+ϕD D D =+''0'0)7.0(∆+∆∆-+ϕH H H =+00''')7.0(∆-∆-∆++ϕd d d =00''')7.0(∆-∆-∆++ϕh h h =(式5.2) (式5.3) (式5.4)400 630 2.6 ±1.3型芯及型腔尺寸的计算结果如下表所示表5-3 型芯尺寸 单位(mm)零件的原始尺寸 收缩率 计算尺寸及偏差 制造尺寸及偏差备注 Ф900.6% Ф Ф Ф600.6% Ф Ф 97.51.0% 受分型面影响 51.0% 受分型面影响 97.5 1.0%表5-4 型腔的尺寸单位(mm)零件的原始尺寸收缩率 型腔的尺寸 制造尺寸 备注 Ф1000.6% Ф Ф 97.51.0% 受分型面影响 102.5 0.8% 受分型面影响2. 结构零件设计1) 动、定模套板的设计采用圆形结构,因为是通孔型腔,采用公式计算,其中:h ——套板边框厚度(cm )D ——镶块外径(cm )p ——压射比压(105Pa )〔σ〕—— 套板材料抗拉强度,材料采用45号钢,〔σ〕取900*105Pa(式5.5)具体尺寸如下图所示:图5-1定模套板图5-2 动模套板2) 动模支承板的设计厚度计算公式:其中:h —动模支撑板厚度(cm );L—垫块间距(cm ); B —动模支撑板长度(cm );〔σ弯〕 — 材料抗拉强度(105Pa ),材料采用45号钢,〔σ弯〕=1000*105Pa ;F —动模支撑板所受总压力(10N )。