拨叉零件机械加工工艺规程设计
“车床拨叉”零件的机械加工工艺规程整理

一、零件的分析(一)零件的作用题目所给的零件是CA6140车床的拨叉。
它位于车床变速机构中,主要起换档,使主轴回转运动按照工作者的要求工作,获得所需的速度和扭矩的作用。
零件上方的①20孔与操纵机构相连,二下方的050 半孔则是用于与所控制齿轮所在的轴接触。
通过上方的力拨动下方的齿轮变速。
两件零件铸为一体,加工时分开。
(二)零件的工艺分析零件的材料为HT200,灰铸铁生产工艺简单,铸造性能优良,但塑性较差、脆性高,不适合磨削,为此以下是拨叉需要加工的表面以及加工表面之间的位置要求:1、小头孔①20以及与此孔相通的08的锥孔、M6螺纹孔2、大头半圆孔①503、拨叉底面、小头孔端面、大头半圆孔端面,大头半圆孔两端面与小头孔中心线的垂直度误差为0.07mm小头孔上端面与其中心线的垂直度误差为0.05mm由上面分析可知,可以粗加工拨叉下端面,然后以此作为基准采用专用夹具进行加工,并且保证位置精度要求。
再根据各加工方法的经济精度及机床所能达到的位置精度,并且此拨叉零件没有复杂的加工曲面,所以根据上述技术要求采用常规的加工工艺均可保证。
二、确定毛坯1、确定毛坯种类:零件材料为HT20Q考虑零件在机床运行过程中所受冲击不大,零件结构又比较简单,生产类型为中批生产,故选择木摸手工砂型铸件毛坯。
查《机械制造工艺设计简明手册》第41页表2.2-5,选用铸件尺寸公差等级为CT-12。
2、确定铸件加工余量及形状:查《机械制造工艺设计简明手册》第41页表2.2-5,选用加工余量为MA-H级,并查表2.2-4确定各个加工面的铸件机械加工余量,铸件的分型面的选用及加工余量,如下表所示:3、绘制铸件毛坯图三、工艺规程设计(一)选择定位基准:1粗基准的选择:以零件的小头上端面为主要的定位粗基准,以两个小头孔外圆表面为辅助粗基准。
2精基准的选择:考虑要保证零件的加工精度和装夹准确方便,依据“基准重合”原则和“基准统一”原则,以粗加工后的底面为主要的定位精基准,以两个小头孔外圆柱表面为辅助的定位精基准。
课程设计:拨叉机械加工工艺规程及夹具设计

70
H
3.0 孔,降一级,单侧加工
3、画零件毛坯图(图附后)
四、 机械加工工艺过程设计
(一)选择定位基准 (1)、选择粗基准 为了方便装夹,以及依据以不加工表面为基准和毛坯表 面质量较好者为基准的原则,选底端面为粗基准。 (2)、选择精基准 依据基准重合原则,应选用统一的基准有利于保证零件 的精度。多用“一面两孔”的定位方式定位,所以选择小头孔轴线和底面为精基 准。 (二)制订工艺过程 1、根据各表面加工要求和各种加工方法所能达到的经济精度(查表 15-32、 15-33、15-34),选择加工方法: (1)、上端面 T1:粗铣(R6.3)——精铣(R3.2) (2)、上端面 T2:粗铣(R6.3)——精铣(R3.2) (3)、底端面 T3:粗铣(R6.3)——精铣(R3.2) (4)、切断面 T4:粗铣(R6.2) (5)、小端头孔 D1:扩孔(R6.3、IT10)——铰孔(R1.6、IT7)
优良,但塑性较差,脆性高,不适合磨削。 2、该零件主要加工表面及技术要求分析如下: (1)、零件上端面及孔φ50H13 的上下端面与孔φ22H7 的垂直度公差等级为
9-10 级。表面粗糙度为 Ra≤3.2um。加工时应以上端面与孔φ22H7 的内表面为基 准。又由于上端面须加工,根据“基准先行”的规则,故应先加工上端面,再加 工孔φ22H7,最后加工孔φ50H13 的上下端面。
1
表面 基本尺 加工余 加工余 代号 寸(mm) 量等级 量(mm)
说明
T1
40
H
3.5 顶面,降一级,单侧加工
T2
70
H
3.0
顶面,单侧加工
T3
70
H
3.0
底面,单侧加工
D1
课程设计-设计变速箱拨叉零件的机械加工工艺规程及工艺装备
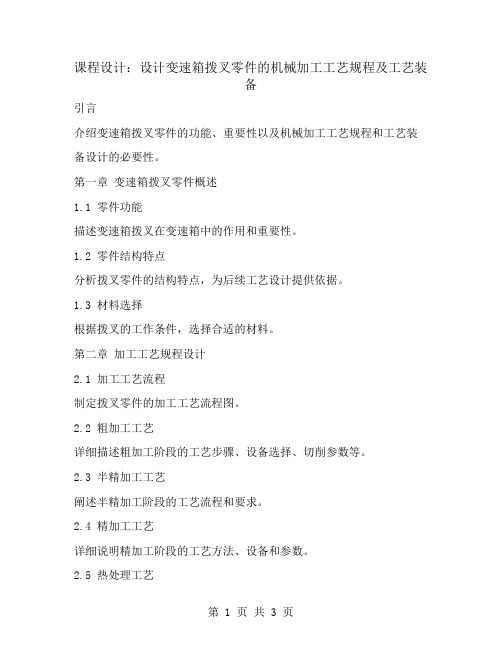
课程设计:设计变速箱拨叉零件的机械加工工艺规程及工艺装备引言介绍变速箱拨叉零件的功能、重要性以及机械加工工艺规程和工艺装备设计的必要性。
第一章变速箱拨叉零件概述1.1 零件功能描述变速箱拨叉在变速箱中的作用和重要性。
1.2 零件结构特点分析拨叉零件的结构特点,为后续工艺设计提供依据。
1.3 材料选择根据拨叉的工作条件,选择合适的材料。
第二章加工工艺规程设计2.1 加工工艺流程制定拨叉零件的加工工艺流程图。
2.2 粗加工工艺详细描述粗加工阶段的工艺步骤、设备选择、切削参数等。
2.3 半精加工工艺阐述半精加工阶段的工艺流程和要求。
2.4 精加工工艺详细说明精加工阶段的工艺方法、设备和参数。
2.5 热处理工艺如果需要,描述拨叉零件的热处理工艺。
2.6 检测与质量控制制定检测计划和质量控制标准。
第三章工艺装备设计3.1 夹具设计设计适合拨叉零件加工的夹具,并说明其工作原理。
3.2 刀具选择根据拨叉零件的材料和加工要求,选择合适的刀具。
3.3 量具与检测设备选择适合拨叉零件检测的量具和检测设备。
3.4 辅助工具与设备列出加工过程中可能需要的辅助工具和设备。
第四章工艺规程的实施4.1 工艺文件的编制说明如何编制工艺文件,包括工艺卡、作业指导书等。
4.2 工艺规程的培训对操作人员进行工艺规程的培训。
4.3 生产准备准备所需的材料、设备、工具等。
4.4 工艺规程的执行与监督确保工艺规程得到正确执行,并进行监督。
第五章经济性分析5.1 成本估算估算拨叉零件加工的成本。
5.2 效益分析分析工艺规程实施后的经济效益。
5.3 风险评估评估工艺规程实施过程中可能遇到的风险。
结语总结变速箱拨叉零件机械加工工艺规程及工艺装备设计的重要性,并对未来的改进方向提出建议。
拨叉加工工艺规程及其大孔前端面铣削夹具设计

拨叉加工工艺规程及其大孔前端面铣削夹具设计一、拨叉加工工艺规程拨叉是一种常用的机械传动件,用于改变传动方向或者传动装置的平面运动和回转运动。
在拨叉的加工工艺中,一般需要进行车削、铣削和热处理等多道工序,其中大孔前端面的铣削是非常关键的一道工序。
下面将对拨叉加工工艺规程进行详细的介绍:1.车削工序a.首先,将原材料的工件切割成合适的尺寸,并进行表面处理,去除铁锈和氧化物。
b.使用车床进行车削,将工件的外形和尺寸加工至要求的精度和表面光洁度。
2.铣削工序a.在车削好的工件上进行铣削加工,首先对孔口进行粗加工,以便后续进行铣削。
b.进行大孔前端面的铣削,保证其精度和表面光洁度满足要求。
3.热处理工序a.将经过车削和铣削后的工件进行热处理,提高其硬度和强度,以确保其在使用中具有良好的耐磨性和耐久性。
4.其他工序a.对热处理后的工件进行喷砂和抛光处理,提高其表面光洁度和美观度。
b.进行装配和质量检验,确保拨叉的各项性能指标符合要求。
以上就是拨叉加工工艺的主要规程,下面将对大孔前端面铣削夹具的设计进行介绍。
二、大孔前端面铣削夹具设计在拨叉加工工艺中,大孔前端面的铣削是一个重要的工序,需要设计一个合适的夹具来固定和夹持工件,以保证铣削的精度和稳定性。
下面是大孔前端面铣削夹具的设计要点:1.夹具结构设计a.夹具采用可调节式的固定夹具,可以根据工件的不同尺寸进行调节。
b.夹具底座采用铸铁或钢板焊接而成,具有较高的刚性和稳定性。
c.夹具上设置有多个夹持点,以确保工件能够均匀受力,避免变形和位移。
2.刀具位置设计a.在夹具上设置多个刀具安装孔,可以根据工件不同的尺寸和形状选择合适的刀具位置。
b.通过计算和试验确定刀具的最佳位置,使得铣削过程中能够保持较高的精度和表面质量。
3.夹具稳固性设计a.夹具底座上设置有安装螺栓孔,可以将夹具牢固地固定在工作台上,避免在加工过程中发生晃动和位移。
b.夹具设计合理,保证夹具自身的稳定性和刚性,以保证加工时的安全和稳定性。
拨叉机械加工工艺规程及夹具设计
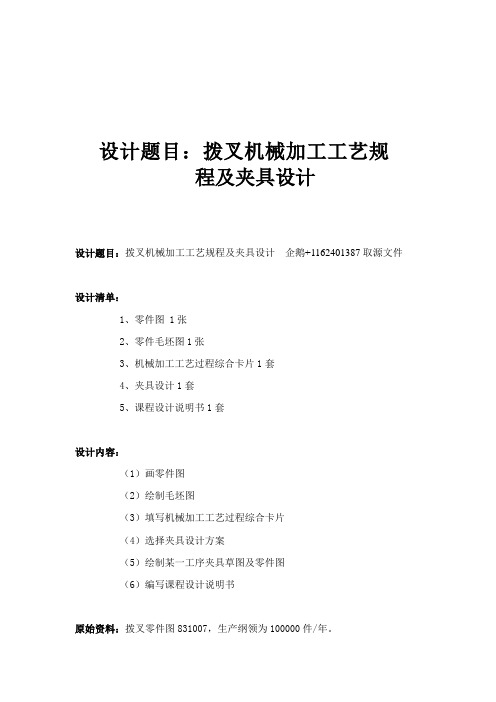
设计题目:拨叉机械加工工艺规程及夹具设计设计题目:拨叉机械加工工艺规程及夹具设计企鹅+1162401387取源文件设计清单:1、零件图 1张2、零件毛坯图1张3、机械加工工艺过程综合卡片1套4、夹具设计1套5、课程设计说明书1套设计内容:(1)画零件图(2)绘制毛坯图(3)填写机械加工工艺过程综合卡片(4)选择夹具设计方案(5)绘制某一工序夹具草图及零件图(6)编写课程设计说明书原始资料:拨叉零件图831007,生产纲领为100000件/年。
一、分析零件图(一)零件作用拨叉是传动系统中用来拨动滑移齿轮,以实现系统调速、转向的零件。
其小头通过与轴的过盈配合来传递凸轮曲线槽传来的运动;大头的内部突起处与滑移齿轮的凹槽配合。
(二)零件的工艺分析1、零件选用材料为HT200,俗称灰口铸铁。
灰铸铁生产工艺简单,铸造性能优良,但塑性较差,脆性高,不适合磨削。
2、该零件主要加工表面及技术要求分析如下:(1)、零件上端面及孔φ50H13的上下端面与孔φ22H7的垂直度公差等级为9-10级。
表面粗糙度为Ra≤3.2um。
加工时应以上端面与孔φ22H7的内表面为基准。
又由于上端面须加工,根据“基准先行”的规则,故应先加工上端面,再加工孔φ22H7,最后加工孔φ50H13的上下端面。
(2)、尺寸30、20、65、φ50、φ70都有其公差要求,加工时需要保证这些尺寸。
使其满足30-0.24+0.084、20-0.21-0.07、65-0.190φ50+0.46φ70+0.46。
(3)、φ22H7孔内表面Ra≤1.6,需要进行精铰。
φ70H13孔内表面Ra≤6.3,铣端面时就可以保证。
φ20H13内孔表面Ra≤3.2只需半精镗即可。
(4)、M8 的孔只需要钻孔与攻丝,可放在后期工序中。
(5)、φ8锥销孔只要求加工一半,故可以与M8孔同时钻出。
(6)、花键方向保持与图样一致。
两件铸在一起表面应无夹渣、气孔。
根据各加工方法的经济精度及一般机床所能达到的位置精度,该零件没有很难加工的表面尺寸,上述表面的技术要求采用常规加工工艺均可以保证。
机械工艺夹具毕业设计188设计“拨叉”零件的机械加工工艺规程及工艺装备(年产量5000件)
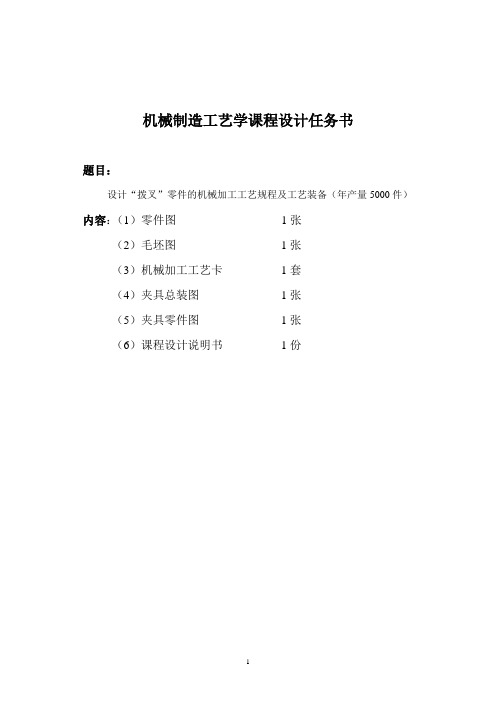
工序九 清洗去毛刺。 工序十 终检。 工序改进后,工作效率和加工精度都大大提高了。以上过程详见机械加工工 艺过程综合卡片。
(四)机械加工余量、工序尺寸及毛坯尺寸的确定
”CA6140 车床拨叉”;零件材料为 HT200,硬度 190~210HB,毛坯重量 1kg,生产件数为 5000 件,类型大批量,铸造毛坯,采用金属砂型机械造型。 据以上原始资料及加工路线,分别确定各加工表面的机械加工余量、工序尺
(三)制定工艺路线
制定工艺路线得出发点,应当是使零件的几何形状、 尺寸精度及位置精度等技术要求能得到合理的保证 ,在生产纲领已确定的情 况下,可以采用万能机床配以专用夹具,并尽量使工序集中来提高生产率。除 此之外,还应当考虑经济效果,以便使生产成本尽量下降。 1.工艺路线方案一 工序一 铣 φ 40mm 的一侧端面。 工序二 铣大槽 工序三 铣小槽外端面。
(二)基面的选择
基面选择是工艺规程设计中的重要工作之一。基面选择得正确与合理可
3
以使加工质量得到保证,生产率得以提高。否则,加工工艺过程中会问题百 出,更有甚者,还会造成零件的大批报废,是生产无法正常进行。 (1)粗基准的选择。对于一般的轴类零件而言,以外圆做为粗基准是合理 的。按照有关基准的选择原则,尽可能选择不加工表面为粗基准。而对有若 干个不加工表面的工件,则应以与加工表面要求相对位置精度较高的不加工 表面作粗基准。 根据这个基准选择原则, 现选取 φ 40mm 的不加工外轮廓表面 作为粗基准,利用一 V 形块支承这个表面,作主要定位面,限制 4 个自由度, 再以一个销钉限制 1 个自由度,再用一挡板挡住φ 40 的一侧面,限制最后一 个自由度,达到完全定位的目的,然后进行铣削。 (2)精基准的选择。主要应该考虑基准重合的问题。当设计基准与工序基 准不重合时,应该进行尺寸换算,本设计的精基准,可按照基准重合原则选 择,φ 22mm 花键孔中心线作为精基准。
拨叉零件的机械加工工艺规程及工艺装备
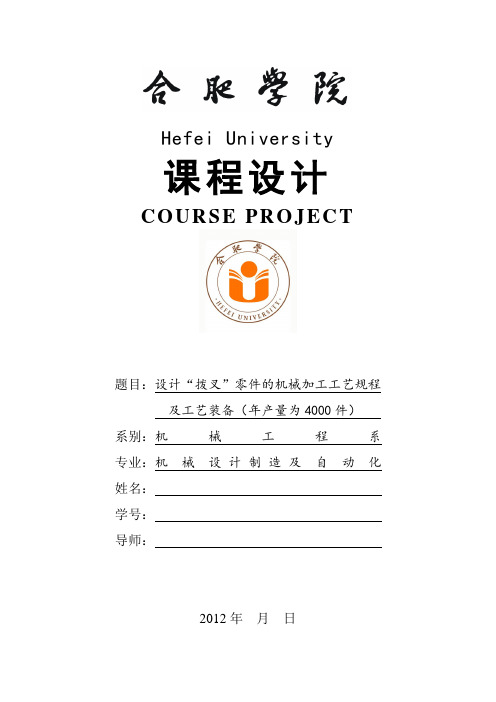
Hefei University课程设计COURSE PROJECT题目:设计“拨叉”零件的机械加工工艺规程及工艺装备(年产量为4000件)系别:机械工程系专业:机械设计制造及自动化姓名:学号:导师:2012年月日目录第1章绪论 (3)第2章拨叉的加工工艺规程设计 (4)2.1零件的分析 (4)2.1.1零件的作用 (4)2.1.2零件的工艺分析 (4)2.2确定生产类型 (5)2.3确定毛坯 (5)2.3.1确定毛坯种类 (5)2.3.2确定铸件加工余量及形状 (5)2.3.3绘制铸件零件图 (6)2.4工艺规程设计 (6)2.4.1选择定位基准 (6)2.4.2制定工艺路线 (7)2.4.3选择加工设备和工艺设备 (8)2.4.4机械加工余量、工序尺寸及公差的确定 (8)2.5确定切削用量及基本工时 (10)工序Ⅰ:粗铣Φ25H7的两端面 (11)工序Ⅱ:钻、扩、铰Φ25H7通孔 (12)工序Ⅲ:粗镗下端Φ60H12孔 (16)工序Ⅳ:半精镗下端Φ60H12孔 (16)工序Ⅴ:粗铣a、b面 (17)工序Ⅵ:钻Φ20.50孔 (19)工序Ⅶ:攻M22×1.5螺纹 (21)工序Ⅷ:粗铣16H11槽 (21)工序Ⅸ:精铣16H11槽 (22)工序Ⅹ:铣断Φ60H12孔 (23)工序ⅩⅠ:粗铣Φ60H12孔两端面 (24)工序ⅩⅡ:精铣Φ60H12孔两端面 (25)第3章专用夹具设计 ............................................................................................. - 26 -3.1镗孔夹具设计 (27)3.1.1问题的提出 (27)3.1.2夹具的设计 (27)3.2钻孔夹具设计 (28)3.2.1问题的提出 (30)3.2.2夹具的设计 (30)参考文献 (36)第一章绪论机械制造工艺学课程设计是在我们学完了大学的全部基础课、技术基础课以及大部分专业课之后进行的。
拨叉(831005型号)零件的加工工艺规程及专用夹具设计(全套图纸)
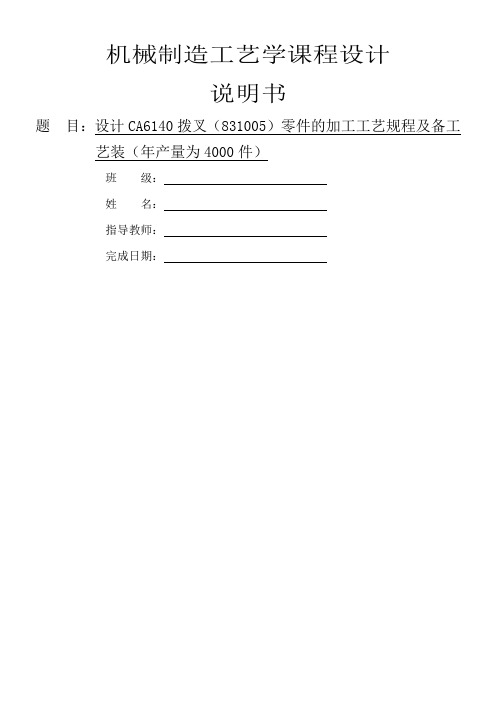
机械制造工艺学课程设计说明书题目:设计CA6140拨叉(831005)零件的加工工艺规程及备工艺装(年产量为4000件)班级:姓名:指导教师:完成日期:目录一、零件工艺性分析 (1)1.1、零件的作用 (1)1.2、零件的工艺分析 (1)二、机械加工工艺规程设计 (2)2.1、确定毛坯的制造形成 (2)2.2、基准的选择 (2)2.2.1粗基准的选择 (2)2.2.2精基准的选择 (2)2.3、制定工艺路线 (2)2.3.1工艺路线方案一 (3)2.3.2工艺路线方案二 (3)三、机械加工余量、工序尺寸及毛皮尺寸的确定 (4)3.1、毛坯余量及尺寸的确定 (4)3.2、确定工序 (4)四、夹具的设计 (12)4.1、提出问题 (12)4.2、设计思想 (13)4.3、夹具设计 (13)4.3.1定位分析 (14)4.3.2切削力、夹紧力、切屑用量和切屑速度的计算 (14)4.3.3夹具操作说明 (15)五.体会 (15)六.参考文献 (16)一、零件工艺性分析1.1、零件的作用题目给定的零件是CA6140拨叉,它位于车床变速机构中,主要起换档,使主轴回转运动按照工作者的要求进行工作。
宽度为18+0.012mm的槽尺寸精度要求很高,因为在拨叉拔动使滑移齿轮时如果槽的尺寸精度不高或间隙很大时,滑移齿轮得不到很高的位置精度。
所以,宽度为18+0.012mm的槽和滑移齿轮的配合精度要求很高。
1.2、零件的工艺分析二、机械加工工艺规程设计2.1、确定毛坯的制造形成零件材料HT200、考虑到此零件的工作过程中并有变载荷和冲击性载荷,因此选用锻件,以使金属纤维尽量不被切断,保证零件的工作可靠。
由于生产纲领为中批生产而且零件的尺寸并不很大,故可采取模锻成型。
经查《金属机械加工工艺人员手册》表5-5取等级为2级精度底面及侧面浇注确定待加工表面的加工余量为3±0.8mm。
2.2基准的选择2.2.1 粗基准的选择因为要保证花键的中心线垂直于右端面,所以以Φ40的外圆表面的粗基准。
- 1、下载文档前请自行甄别文档内容的完整性,平台不提供额外的编辑、内容补充、找答案等附加服务。
- 2、"仅部分预览"的文档,不可在线预览部分如存在完整性等问题,可反馈申请退款(可完整预览的文档不适用该条件!)。
- 3、如文档侵犯您的权益,请联系客服反馈,我们会尽快为您处理(人工客服工作时间:9:00-18:30)。
1 / 10
拨叉零件机械加工工艺规程设计
一、零件的主要技术条件分析
CA6140拨叉共有两组加工表面。
1. 以花键孔的中心线为基准的加工面
这一组面包括Ø25+0.230mm的六齿方花键孔、Ø22+0.280花键底孔两端的
2X150到角和距中心线为27mm的平面。
2. 以工件右端面为基准的8+0.030 mm的槽和18+0.120mm的槽
经上述分析可知, 对于两组加工表面,可先加工其中一组表面,然
后借助于专用夹具加工另一组表面。
二、确定毛坯及其尺寸
1、零件生产类型
中量批生产。
2、毛坯的材料及制造方法
零件材料HT200、考虑到此零件的工作过程中并有变载荷和冲击性载
荷,因此选用锻件,以使金属纤维尽量不被切断,保证零件的工作可靠。
由于生产纲领为中批生产而且零件的尺寸并不很大,故可采取模锻成型。
3、机械加工余量及毛坯尺寸
查表确定各表面机械加工总余量,确定毛坯尺寸,及偏差,填写下表
零件尺总加工余量 偏差 毛坯尺寸 根据
寸
右端面28mm 3mm _ 31mm 足够把铸铁
的硬质表面
层切除
到中心线27mm 3mm _ 30mm 足够把铸铁
的硬质表面
层切除
Ф22mm的孔 22mm Φ2228.00 mm Ф40mm_ 《机械加工
实用手册》表
5.2.1
宽为6mm的花键 6mm 606.003.0 mm _ 《机械加工
实用手册》表
5.2.1
宽为8mm的槽 8mm 803.00 mm 28mm 《机械加工
实用手册》表
5.2.1
宽为18mm的槽 18mm 18012.00 mm 34mm 《机械加工
实用手册》表
5.2.1
三、加工工艺过程设计
3 / 10
1、定位基准的选择
(1)粗基准的选择:因为要保证花键的中心线垂直于右端面,所以以Φ40的外圆表面
的粗基准。
(2)精度基准的选择:为保证定位基准和工序基准重合,以零件的A面为精基准。
2、零件表面加工方法的选择
宽为8的槽两侧面,公差等级为IT9,表面粗糙度为Ra1.6,加工方法选择为:粗
铣、半精铣、精铣;
宽为18的槽两侧面,公差等级为IT6,表面粗糙度为Ra3.2,加工方法选择为:一
次行程、二次行程、;
宽为6的花键槽两侧面,公差等级为IT9,表面粗糙度为Ra3.2,加工方法选择为:
粗铣、半精铣;
直径为25的花键圆面,公差等级为IT7,表面粗糙度为Ra1.6,加工方法选择为:
粗铣、半精铣、精铣;
直径为22的内孔面,公差等级为IT12,表面粗糙度为Ra6.3,加工方法选择为:
粗扩、一次扩孔;
到花键中心线为27mm的平面,公差等级为IT6,表面粗糙度为Ra3.2,加工方法为:
粗铣、半精铣。
3、制定工艺路线
工艺阶段的划分,如
工序Ⅰ:(详细工序内容,包括定位基准)
工序Ⅱ:
(1)以Ф40mm圆柱面为粗基准。选用C3163-1转塔式六角车床及三爪卡盘夹具。
粗、精车端面,钻、扩花键底孔、倒两端15°倒角;
(2) 拉花键。以右端面为基准;
(3) 铣削槽左端面,以花键的中心线及右端面为基准。选用X62W卧式铣床加
专用夹具,
(4) 铣削8+0.030mm的槽。以花键的中心线及右端面为基准。选用X62W卧式铣
床加专用夹具;
四、工序设计
1、选择加工机床:
①工序Ⅰ:(选择依据,零件形状、大小,经济精度,表面粗糙度要求等)
2、确定工序尺寸
(1)确定各圆柱面的工序尺寸
加工表面 工序名称 工序双边余量 工序尺寸及公差 表面粗糙度
Φ40mm圆端面 粗车 — — Ra12.5
精车 — — Ra3.2
Φ2228.00 内孔 粗扩 20.75 21.528.00
Ra25
一次扩孔 0.19 2228.00 Ra3.2
倒两端15°倒
角
粗车 — — Ra12.5
半精车 — — Ra6.3
Φ25023.00、宽为
606.003.0的花键
粗铣 高1.5、宽6 25、6 Ra3.2
精拉 高0.0115、宽0.015 25023.00、606.003.0 Ra1.6
到花键中心线
为27mm的平
面
粗铣 — — Ra12.5
半精铣 — — Ra6.3
精铣 — — Ra3.2
宽为803.00、高
为8mm的槽
粗铣 7 7 Ra12.5
半精铣 0.25 7.503.00 Ra6.3
精铣 0.015 803.00 Ra1.6
宽为18012.00、
高为23mm的
槽
粗铣 17 17 Ra12.5
半精铣 0.25 17.5012.00 Ra3.2
精铣 0.003 18012.00 Ra3.2
(2)轴向尺寸确定
根据工艺尺寸链
工艺过程的安排
五、确定切削用量
1、工序Ⅰ切削用量的确定
5 / 10
一)工序1 :车削右端面。
(1)粗铣
1).背吃刀量的确定 ap=2.5mm
2).进给量的确定:由文献【1】表5-11按铣刀直径50mm,齿数为6的条
件选取每齿进给量fz为0.4mm/z
3).由文献【1】表5-13.按高速钢立铣刀d/z=50/6的条件选取,铣削速
度v=42m/min 由文献【1】公式(5-1) n=1000×42/3.14×50=267.38 r/min
参照文献【1】表4-15选取X51型立式铣床的主轴转速,取转速n=255r/min,
再将此转速代入公式(5-1)可求出实际铣削速度v=πdn/1000=40.06 m/min
(2)2、精铣
1).背吃刀量的确定 ap=0.5mm
2).进给量的确定:由文献【1】表5-11,按铣刀直径50mm,齿数为6
的条件选取每齿进给量fz为0.25mm/z
3).铣削速度的计算:由文献【1】表5-13,按高速钢立铣刀d/z=50/6
的条件选取,铣削速度v为47 m/min。由文献【1】公式(5-1)
n=1000×47/3.14×50=299.21 r/min 。参照文献【1】表4-15选取X51立
式铣床主轴转速,取n=300 r/min,再将此转速代入文献【1】公式(5-1)
可求出该工序实际铣削速度为 v=πdn/1000=47.12 m/min。
二)工序2钻孔、扩孔、倒角。
(1)、钻孔
钻头选择:见《切削用量简明手册》表2.2