毕业论文外文翻译--供应链的战略成本管理(英语原文+中文翻译)
外文翻译--战略成本管理的供应链采购管理的前景(节选)

中文2969字外文翻译原文:Strategic Cost Management in the Supply Chain:A Purchasing andSupply Management PerspectiveIn the course of this study, it became clear that effective strategic cost management has both strategic and tactical aspects that must be well executed in order to deliver results. The strategic framework and tactical elements of cost management as they affect PSM are shown , which also shows the soft and hard results of effective cost management as related to PSM. The actual processes in which cross-functional teams engage to support strategic cost management include many tactical elements. In most organizations studied, the strategic cost management process occurs as an integral part of the new product development process or the strategic sourcing process. It is not a ―stand-alone activity,‖ but rather central part of supplier selection and supply base management. Some of the processes and tools that are part of the strategic cost management process are listed in Table 2, and presented in more depth in the body of the report. A cross-disciplinary team of two or more individuals, including PSM, was the norm for carrying out strategic cost management in the five core organizations studied. Often, the cost management activities were part of another, larger process, such as a strategic sourcing event, a new product development process, or part of an on- going continuous improvement effort. In exploring Figure 1 in detail, it is clear that the cross-functional team that works on strategic cost management has numerous high-level issues that it must consider. First, the price and feature needs of the ultimate customer must be heavily weighted, or the result will be a product that customers cannot afford, that does not meet their needs, or both.Organizational Support at all Levels: While PSM is held to a high level of accountability for strategic cost management and delivering bottom-line savings, PSMcannot be successful without extensive support from others throughout the organization. First and foremost, top management support is critical. It sets the tone for the attitude that everyone in the organization has toward strategic cost management. Through the business unit and functional metrics, top management determines the nature and extent of cost management focus as an organizational priority. Based on this, PSM needs the support of other functional areas cooperating teams that have a primary or second goal of managing supplier costs. The participants on cross-functional teams need to be held accountable for the identification of opportunities and delivery of results. PSM also needs specific support from cost management specialists, who are assigned to support PSM and cross- functional teams in supplier cost analysis. These individuals may be part of PSM or part of finance. The critical requirement is that they have the charter and the qualifications to effectively support supplier cost analysis and management. Supplier cost management must be viewed as one of, if not the most important aspect of their jobs. This focus is critical because supplier cost analysis is often specialized and time consuming. PSM and cross-functional teams need to know that there are internal experts upon whom they can call to support their supplier cost management efforts. Without such support, the analysis may be too complex and time consuming to be done as part of PSM’s or the cross-functional team’s regular activities.Supplier Cost Management is a Good Investment: The suggested approach for dedicating resources to supplier cost management may seem cost prohibitive. However, the organizations studied unanimously agree that they receive extremely high returns on their investments in supplier cost management efforts. The money spent on supplier should-cost analysis, supplier development, and other tools and approaches pays for itself many times over in terms of reducing costs and bottom-line prices paid to suppliers. For large Fortune 500 companies, successful strategic cost management may mean the addition of dedicated personnel to focus on supplier cost management. For smaller organizations which might not have as great an on-going need, or as great an asset base, successful strategic cost management may mean diverting resources from PSM and/or finance, and retraining one or more people tobecome internal experts on some of the cost management and analysis tools mentioned in this study.Support for Strategic Cost Management Theory: As mentioned in the brief review of the literature below, strategic cost management theory embodies understanding and managing the organization’s supply chain, the cost drivers and the customer value proposition. It is a matter of simultaneously understanding and managing these elements in relation to each other. The organizations investigated do an excellent job of understanding and managing their internal cost drivers and supplier-facing cost drivers. Two of the organizations that have a strong management focus on customer relationships also do an excellent job of managing the customer-facing cost drivers. It is not clear from the study how well these organizations understand the customers’ value proposition and translate that across internal functions and to their suppliers. Except in the case of LCP, and to some extent Deere, the translation mechanism is indirect, through one or more functions that may have direct customer contact. This represents an opportunity for potential improvement. Related to this, as mentioned in the section on supply chain perspective, most of the organizations studied do not generally have a seamless view of the supply chain from customer to supplier; the customer view and supplier view are still managed separately in different organizations, with some interface in the middle. Such coordination would be a complex undertaking, and might require a change in team structure. The organization that comes closest to embodying a true supply chain perspective is LCP, with its product supply structure. While the argument could be made that it is more important for LCP to be close to its customers because it is a consumer products firm, all types of customers are becoming more demanding (Fawcett and Magnan, 2001). LCP’s product supply structure has a Product Supply Vice President who reports into the Business Unit President. Also reporting to the VP of Product Supply are PSM, engineering, manufacturing, customer service/logistics, and finance. Deere has a similar structure, although there is a mix of direct and indirect reporting relationships.The customer information comes to the team through a secondary source, oftenfiltered through the eyes of marketing, sales, or a customer relationship manager. The corporate objectives regarding strategic cost management and cost savings goals must also be considered in terms of meeting the objectives of the team and the business unit or units that the team supports. Next, each organization utilized cost management specialists, for whom all or a major part of their jobs was to support cost analysis, help develop models, and ensure integrity in the data and the analysis results. In some cases, these individuals reported to PSM; in others, they reported to corporate or business unit finance. The key commonality across cost management specialists in these organizations was the expertise, credibility and charter to support supplier cost management. Even with the first three direct inputs, a fourth is needed: a reward an measurement system that supports cost management. The extent to which such a system exists is a function of the corporation’s cost consciou sness culture. Is everyone in the organization held accountable for cost management? Is it part of their performance reviews, annual goal setting, and overall expectations? The stronger the cost-consciousness culture, the greater the support for the team and the commitment to its results. In the center of Figure 1, the cross-functional team engages in activities designed to reduce the organization’s cost, such as identifying cost drivers and changing processes using a total cost of ownership approach, engaging in on-line reverse auctions, or working with suppliers on development. The way that the organizations studied use these processes is detailed in the body of the report. Based on the strategic cost management processes, they aim to achieve a better supply base, defined as one that has a lower cost (sometimes only a lower price), and performs as well or better than it did before the strategic cost management process. The process should also support customer satisfaction by resulting in the same or lower prices for the same or better quality and service. This should in turn lead to measurable, bottom line savings, which should translate into higher profit, higher economic value-added for the firm, and higher earnings per share. In general, when PSM thinks about achieving results, the focus is still on bottom line cost savings rather than how its performance is reflected in the overall corporation’s results.Characteristics of Companies with Effective Supply Chain Strategic CostManagement Approaches: The key characteristics that organizations with effective strategic cost management systems should display are shown in Table 3. Table 3 was developed as a composite ideal of the best characteristics of the core supply chain organizations studied. It is not representative of any one organization. There are specific attributes related to way the organization understands and manages the relationship with the customer, its supplier, and related to their own internal organization. The key organizational characteristics have been divided into cultural/organizational issues, measurement issues, and information/communication issues.Internal requirements/characteristics–Both the customer-facing and supplier-facing characteristics stem from inside the organization. The internal culture and organizational structure create the framework for effective supply chain cost management. Internally, an effective cost-management culture is characterized by top management support for cost management and a high level of cost and value consciousness throughout the company. In addition to dedicated resources to support supply chain cost management, cross-functional teams are used to identify and implement cost management approaches. Rather than an afterthought, cost management is an integral part of all key supplier processes. The right type of reward and measurement systems is also critical to reinforce the cost management culture. It is critical that the organizations measure what they want to achieve, and the metrics are aligned throughout the organization, reflecting cost goals as well as customer value and supplier performance goals. Supply chain performance metrics and results must be published and receive high visibility throughout the organization. This requires excellent information systems and communication. Part of this communication includes awareness throughout the organization of customer needs and the organization’s value proposition in serving the customer.Customer-facing knowledge– Supply chain management is all about meeting the needs of customers better than the competition does. In terms of the organization’s culture, the company needs to be customer centric, valuing its customers and working with them to meet their needs while improving the efficiency and effectiveness of thesupply chain. From a measurement standpoint, the organization needs to understand the needs of the end customer as well as market trends, and respond to these proactively. From an information and communication perspective, it is critical that the c ustomers’ needs and the organization’s plans for meeting those needs be communicated throughout the organization. This allows everyone in the organization to align his or her efforts around the customer.Supplier facing knowledge/characteristics—Effective supply chain strategic cost management relies heavily on suppliers. Culturally, this means a continuous improvement focus on working with suppliers, including early supplier involvement. It also means supporting supplier’s continuous improvement with res ources and training. From a measurement and reward standpoint, the organization must properly segment its supply base to use the appropriate types of supplier relationships and cost management techniques. It also needs to measure supplier performance, and reward the suppliers who perform well. Clearly communicating expectations and needs to suppliers is essential. The organizations studied in this research excel in the third column of Table 3: supplier-facing knowledge. The segment their supply bases, have dedicated supplier cost management resources, emphasize continuous improvement, and in many cases develop the suppliers by providing resources to support continuous improvement. They reward their top suppliers by sharing cost savings or giving them more business. They are working on improving communications and early supplier involvement. One strong recommendation is that they invest more resources in supplier training. In general, their first tier suppliers do not have as well- developed approaches to supplier cost management. Since these core organizations would prefer not to work on supplier cost management beyond their first tier suppliers, the first tier suppliers would likely be much more effective if they improved their cost management systems, and worked more closely with their suppliers.Source: Lisa M.Ellram,2002. ―Strategic Cost Management In the supply chain: Apurchasing and supply management perspective‖ .pp47-69.译文:战略成本管理的供应链:采购管理的前景在研究的过程中,战略成本管理的战略和战术方面都必须执行得好才能产生明显的效果。
外文翻译--供应链中的战略成本管理-结构性成本管理
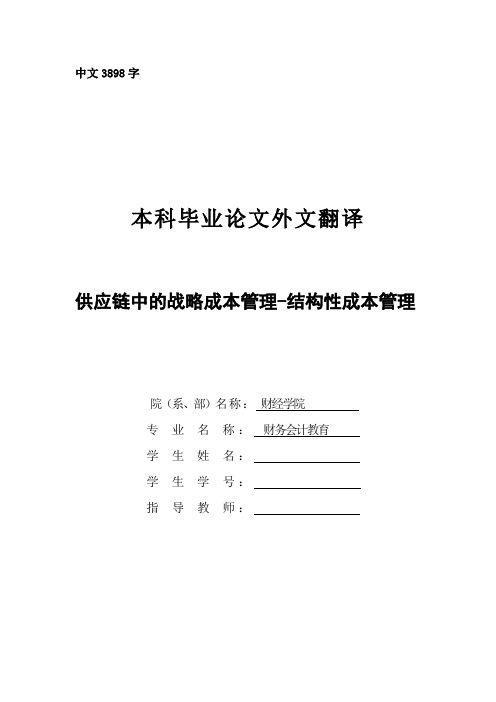
中文3898字本科毕业论文外文翻译供应链中的战略成本管理-结构性成本管理院(系、部)名称:财经学院专业名称:财务会计教育学生姓名:学生学号:指导教师:Strategic Cost Management in Supply ChainsPart 1: Structural Cost ManagementAccounting Horizons: June 2009, Vol. 23, No. 2, pp. 201-220.Shannon W. Anderson and Henri C. DekkerAbstract: Strategic cost management is the deliberate alignment of a firm’s resources and associated cost structure with long-term strategy and short-term tactics. Although managers continue to pursue efficiency and effectiveness within the firm increasingly, Improvements are obtained across the value chain: through reconfiguring firm boundaries, relocating resources, reengineering processes, and re-evaluating product and service offerings in relation to customer requirements. In this article, we review strategic cost management, especially structural cost management. Structural cost management employs tools of organizational design, product design, and process design to create a supply chain cost structure that is coherent with firm strategy.Key wards: structural cost management; su pply cha in; competitive Advantage1 INTRODUCTIONThe prevalence in the current business press about acquisitions, restructuring, outsourcing, and off shoring indicates the vigor with which firms are engaged in the modern cost management. There’s a shift from prior internal processes for efficiency and effectiveness, firms are attempt to manage costs throughout the value chain. As the value of purchased materials and services as a share of selling price has increased ,firms find themselves managing complex supply chains, that include global suppliers, contract manufacturers, service centers and so on. Firms should pay attention to the value chain, so that they can obtain the room of development.2 STRATEGIC COST MANAGEMENTCost management research has tended to fall into two related streams. The first research stream examine whether and how firms configure accounting data to support value chain analysis ; T he second research stream attempt to derive the relationship between a firm’s strategy and cost structure. The focus is on the causal relation between activity levels and the resources that are required. These research streams take as given the firm’s strate gy and structure and focus on whether accounting records are capable of reflecting or detecting the economics of the chosen strategy. In this review we take Shank’s broader perspective that much of what constitutes strategic cost management is found in choices about organizational strategy and structure. Following Anderson, we define “strategic cost management” as deliberate decision making aimed at aligning the firm’s cost structure with its strategy and with managing the enactment of the strategy.We focus on interactions across firm boundaries; Specially, the buyer/supplier interface, as a source of competitive advantage that can deliver low cost, as well as high productivity, quality, customer responsiveness, and innovation. Shank posited that two types of cost drivers are the basis for strategic cost management: structural cost drivers that reflect organizational structure, investment decisions, and the operating leverage of the firm and executive cost drivers that reflect the efficiency of executing the strategy. Stated differently,structural cost management may be conceived of as a choice among alternative production functions that use different inputs or combinations there of to meet a particular market demand. Executive cost management is concerned instead with whether, for a given production function, the firm is on the efficientfrontier. Structural and executive cost management is connected through improvement activities. For example, cost driver analysis is a catalyst for efficiency improvements of existing processes and for reengineering processes to create a different cost structure. Clearly ,cost management is only a part of long term profit maximization. This paper series will not discuss strategic revenue management; however, we acknowledge interdependencies between costs and revenues associated structural cost management and the executive cost management activities of the sustainability of the strategy. Often the greatest opportunities for strategic cost management cross firm boundaries. Shank advocated cost management across the value chain, and other accounting scholars have called for research on how accounting facilitates modern inter-organizational relationships.3 STRUCTURAL COST MANAGEMENT IN SUPPLY CHAINSShank argued that structural cost drivers associated with organizational structure, investment decisions, and the operating leverage of the firm. In supply chain management, structural cost management includes the decision to seek an external supplier, selecting one or more external suppliers, and designing the buyer/supplier relationship. These elements of supply chain management are important determinants of cost structure and are central to managing risk in supply relations. Supplier selection processes are akin to personnel controls within the firm that ensure the fitness between employee skills and job requirements. Designing the buyer/supplier relationship encompasses formal contractual management controls such as specifying authority for supply decisions, performance requirements, and rewards or sanctions for nonperformance, as well as formal and informal controls that reinforce desired cultural norms. Although we focus on structural cost management, many of the cost management decisions discussed in this section relate to balancing th e “cost of control” against risks of inter-firm transactions. We review research and contemporary practices associated with sourcing decisions, supplier selection in the sections that follow.4 SOURCING: MAKE; BUY OR ALLYA core component of structural cost management is the decision to execute activities within the firm or to outsource them to another party. The so-called “make-buy-or-ally” decision considers how and where in the value chain firms draw their organizational boundaries and which activities ar e conducted inside versus outside the firm. Although the buyer and supplier are separate firms, the supply relationship often includes collaboration in the uncertain realm of product and process design.Transaction cost economics is the most widely used framework for explaining firm boundary and organizational design choices. Production costs are defined by production technology and efficiency. A buyer and supplier’s production costs may differ if they use different technolog y, operate at different scales, or operate with different efficiency A buyer’s cost accounting records may be one basis for comparing the “make” option with prices of external suppliers. Transaction costs concerns about opportunism associated with firm’s transactions. Examples of transaction costs include costs of activities such as searching for partners, negotiating and writing contracts, monitoring and enforcing contract compliance. Transaction costs are not typically accessible and, in the case of opportunity costs, may not even be included in cost accounting records. Consequently, texts typically warn students to consider strategic factors before making a sourcing decision based only on production costs. This is one area where cost management practices, both measurement and analysis, can be improved to better support structural cost management decisions associated with sourcing.5 INTERDEPENDENCE IN SUPPLY CHAINSAlthough we discuss the sourcing decision as a logical “starting point” in supply chain management, in reality this element of structural cost management is intertwined with other elements of strategic cost management. For example, in TCE theory, sourcing decisions are posited to reflect the minimization of anticipated exchange hazards. The potential transaction partners are important predictors of exchange hazards. However, in complex supply chains in which many suppliers contribute to the completed product, product architecture is also a key determinant of sourcing decisions. The “partnership” strategies in supply chains depend critically on using criteria other than price in supplier selection. Thus, structural cost management decisions associated with sourcing are intertwined with structural cost management practices in supplier selection .6 THE SUPPLY CHAINS AS A SOURCE OF COMPETITIVE ADV ANTAGETCE, with its underlying performance risk and relational risk, focuses on potential downsides of cooperation. Another school of thought, the resource-based view RBV of the firm, focuses on the upside of cooperation. The RBV implicates inter-firm cooperation in the realization of strategic a dvantage, with firm boundaries resulting from managers’ dynamic search for opportunities to deploy valuable, scarce, inimitable resources to obtain abnormal returns. The basis for exchange in alliances can be financial, technological, physical, or managerial resources. Studies applying the RBV to explain firm boundaries emphasize the inimitable value of collaborative partnerships.While the perspectives of TCE and risk management differ from the RBV, both assume that firm choices are motivated by the goal of maximizing long-run performance. Whereas TCE focuses on minimizing transaction costs at a given time, the RBV emphasizes the illiquidity and immobility of valuable resources. This approach admits the possibility that transacting with external parties dynamically changes the resources and capabilities that will be available in future periods. Together these frameworks point to important areas for growth in management accounting, Specifically, TCE and risk management indicate the importance of measuring risk in supply relationships and formally integrating risk assessments into the make, buy, or ally decision. The RBV indicates the importance of the emerging area of accounting for human capital and other firm capabilities and intangible assets whose value changes through exchange with strategic supply partners.7 TRENDS IN SUPPLY CHAIN GROWTHRecent years have shown tremendous growth in the use of the ally mode across different industries. In manufacturing, over the past 50 years the value of purchased materials and services has grown from 20 percent to 56 percent of the selling price of finished goods. AMR Researchfind that the typical U.S. manufacturer manages over 30 contract relationships. In 2006, the worldwide market for supply chain management software, growing at an annual rate of 8.6 percent, topped $6 billion. The global IT outsourcing market was expected to grow to almost triple that size. Growth in use of collaboration is found in firms of different sizes and from different industries. for instance, report that almost 80percent of small to large Dutch firms are involved in enduring forms of interfirm cooperation,typically managing multiple partners at the same time. The largest proportion constituted outsourcing relations, a frequency that appears to follow from its potential to generate cost reductions and increased flexibility, including the opportunity to convert fixed costs into variable costs and to benefit from economies of scale and scope.In sum, sourcingdecisions are critical to structural cost management in supply chains; how-ever, there is little evidence that cost accountants have extended their expertise to include all relevant costs. Moreover, although risk management is becoming more common and supply chain risk is foremost among the risks that firms seek to control,accountants are primarily involved with controlling and mitigating risk.8 SUPPLIER SELECTIONThe search process of finding a supply partner is itself costly, entailing as it does ident ifying alternatives, evaluating supplier capabilities, and managing the final selection process. Although TCE suggests that supplier selection is a cost-minimizing choice, the RBV identifies a broader set of decision criteria. In particular, selecting suppliers with capabilities and resources that match the buyer’s needs is critical to supply chain performance and coordination. Key capabilities that have been shown to directly impact performance include inventory management, production planning and control, cash flow requirements, and product/service quality. Das and Teng defined financial resources, technological, physical, and managerial resources as the basis for alliance activity. Prior studies find that the criteria used for supplier selection typically reflect the specific resources and competencies that are desired in potential partners. Examples include competitive pricing, supplier reliability, service support, and capabilities that may have a long-term contribution to buyers’ competitive advantage. The sel ection criteria can include “hard,” quantitative measures of performance; however, frequently they are complemented with “soft” measures that capture qualitative aspects of the desired relationship with the supplier.The success of buyer/supplier relation-ships characterized as “partnerships” is related to the buyer’s use of criteria other than price in selecting suppliers. As in the decision to outsource, the recognition of risks can be essential in supplier selection processes. Relational risks, performance risks, and their associated costs are avoided when suppliers are selected based on evidence of trustworthiness and competence. Accordingly, the selection process and selection criteria should reflect both the type of supplier resources and competencies n eeded, and the anticipated risks of the relationship. These factors also link the sourcing decision and supplier.CONCLUSIONIncreasingly, business strategy focuses on reexamining the boundaries of the firm—on establishing appropriate boundaries, identifying supply chain partners with whom to co-design efficient,effective products and processes, and managing transactions with these partners to deliver profit s to all value chain participants.Article source:2009 Accounting Horizons V ol.23.供应链中的战略成本管理-结构性成本管理摘要战略成本管理是对一个公司的资源的深入的整合,它通常把企业的成本结构和企业的长期战略和短期策略联系起来,尽管管理人员不断在企业内部追求效率和效益,然而,企业效益的日益提升最终是通过价值链获得的,即通过重组企业边界(如上游供应商、下游客户),重新定位资源,再造过程和重估与顾客需求相联系的产品和服务获得的。
供应链管理外文文献及翻译

供应链管理外文文献及翻译供应链管理的实践和理论已经在全球范围内得到广泛应用和研究。
本篇文献回顾了最近的文献,旨在提供一个有关供应链管理的广泛和多样化的视角。
本文献主要关注采购、生产和物流等方面。
本文献指出了供应链管理的重要性以及不断变化的环境对供应链管理的挑战。
作者还强调了合作伙伴关系、信息共享、风险管理和绩效评估等方面的关键因素。
总的来说,对于供应链管理的研究,应该包括广泛的实践案例和深入的理论研究。
只有这样,才能理解不断变化的环境对供应链管理的影响,从而制定更好的供应链管理策略。
翻译:Supply Chain Management Foreign Literature and TranslationThe practice and theory of supply chain management have been widely applied and studied worldwide. This literature review aims toprovide a broad and diversified perspective on supply chain management, focusing mainly on procurement, production, and logistics.The literature points out the importance of supply chain management and the challenges that the constantly changing environment poses to it. The authors also emphasize critical factors such as partnership relationships, information sharing, risk management, and performance assessment.In general, research on supply chain management should include diverse practical cases and in-depth theoretical studies. Only in this way can we understand the impact of the constantly changing environmenton supply chain management and formulate better supply chain management strategies.。
供应链管理外文翻译

The Impact of Green Supply Chain Management on Transportation Cost ReductionABSTRACT: Supply chain management(SCM)has become an important competitive approach for organizations. The issue of green supply chain management is critical for the successful implementation of industrial ecosystems and industrial ecology. Organizations have a number of reasons for implementing these green supply chain policies, from reactive regulatory reasons, to proactive strategic and competitive advantage reasons. From an overall environmental and organizational perspective, it is important to understand the situation and what issues exist in this field. Many organizations worldwide have already experienced globalization and a shifting focus to competition among networks of companies in this environment. Multinational enterprises have established global networks of suppliers that take advantage of country-industry specific characteristics to build this competitive advantage. To success having this competitive advantage, logistics and supply chain managers have to balance efforts to reduce costs and innovate while maintaining good environmental performance. Therefore, today, competition is not between companies, between supply chains. This study brings us the effect of Green Supply Chain Management (GSCM) on the Transportation Cost Reduction (TCR). Keywords: Green Supply Chain; Transportation Cost; Cost Reduction1.IntroductionGlobal enterprises are permanently trying to develop new, flexible, applicable and innovative methods to enhance their success and competitiveness. Some of these organizations are enhancing their competitiveness through improvements in their environmental activities performance to comply with environmental law and regulations. The main point of complying with environmental law and regulations is customer environmental concerns and environmental impact of production and service activities. Besides, increasing of awareness of the propensity for environmental pollution within organizations’ supply network to c ost them in consumer complain, cleanup and punishment.To response the requirement of environmental law and regulations, minimum standards of environmental performance have become increasingly prevalent in the purchasing agreements of multinational corporations for their local and global suppliers. This requirement has become a new customer expectation from suppliers therefore suppliers have to reduce costs and improve quality and service to complete their responsibility for their customers.It is generally thought that green supply chain management has a great effect in increasing environmental performance, minimizing waste and achieving cost savings. Besides because of increasing synergy among business parties, green supply chain management enhances efficiency through partner and their supply networks. This synergy is expected to enhance the corporate image, competitive advantage andmarketing exposure.However, if green supply chain management practices are to be fully adopted by all organizations, a demonstrable link between such measures and cost saving, specifically transportation cost saving is very necessary. Bowen et al. state that organizations will adopt green supply chain management practices if they identify that this will result in specific financial and operational benefits.Thus, there is a clear research need to establish the potential link between structure of green supply chain and effective transportation cost saving, to provide an accelerator for enterprises to establish effective green their supply chains.Many enterprises have demonstrated significant efforts to establish green supply chain management initiatives. While there is not enough study which examine about cost reduction through Green Supply Chain Management and tested an empirical link between such efforts and Transportation Cost Reduction. Therefore, this paper presents the results of a survey of organizations to investigate the proposition that there is a significant relation between GSCM and TCR.2. Literature ReviewThis paper encompasses previous “functional” specific research on aspects of GSCM, to develop a conceptual model of GSCM and TCR. In this paper, the structure of green supply chain management encompasses environmental parameters as:(1) Purchasing and In-Bound Logistics,(2) Production or the Internal Supply Chain,(3) Distribution and Out-Bound Logistics,(4) Reverse Logistics.2.1 Purchasing and In-Bound LogisticsFrom the purchasing - the beginning point of supply chain - perspective of the supply network it is under discussion that GSCM has several benefits, ranging from cost reduction to integrating suppliers in a participative decision-making process that promotes environmental innovation). Green purchasing strategies which the largest part of inbound logistics side is adopted by the companies to response global concern of environmental stability.Green purchasing might enhance issues such as using environmental transportation, cost reduction, material substitution and waste minimization of hazardous materials. The involvement and support of suppliers is crucial to achieving such goals. Therefore, companies are increasingly managing their suppliers’ environmental performance to ensure that the materials and equipments supplied by them are environmentally-friendly in nature and are produced using environmentally friendly processes.Integration of suppliers into environmental management system could be completed in two steps. First step, Walton et al suggest that environmental issues become main part of strategic planning to response regulations and the demands of environmental accountability. In second step, organizations integrate their supplier to their supply chains to make reduction operational costs and improve customer service.2.2 Greening the Production Phase or the Internal Supply ChainThere are several notions that could be explained about green supply chain in production phase, such as cleaner production, design for environment, remanufacturing and lean production. Lean production has an importance to decrease the environmental impact of the internal supply chain. Lean production improves environmental performance by reducing general waste and minimizing hazardous wastes.Besides, production phase has an important role in keeping same quality level of organization that: having environmentally-friendly production; prevention of pollution at source; cleaner production practices are adopted; closed loop manufacturing (reverse logistics) is incorporated to the fullest extent possible, re-use and recycling of materials is maximized; material usage is reduced; the recyclable content of a product is increased; the production processes are optimized so that generation of waste, both hazardous or otherwise, is minimized; and products are redesigned (design for the environment). Also additionally design of the facility based on lean production is able to minimize vehicle movement.2.3 Greening the Outbound Function and Reverse LogisticsOn the outbound side of the green supply chain, reverse logistics, environment-friendly packaging, and environment-friendly distribution, are all initiatives that might improve the environmental performance of an organization and its supply chain. Management of wastes in the outbound function such as reverse logistics and waste exchange can lead to cost savings and enhanced competitiveness. Many of these initiatives involve compromises between various logistics functions as reverse logistics and environmental consideration in order to improve the environmental performance of an organization.In an eco-transportation system, required parameters of a transportation system such as type of transport, fuel sources, infrastructure, operational practices and organization, can be considered. These parameters and the dynamics that connect them, determine the environmental impact generated in the transportation logistics phase of the supply chain.3. Model and MethodologyAt this section, w investigate research question by using a questionnaire to collect data. After collecting, I use SPSS software to control relation between our variables by regression analysis.Model has three phases. In first phase, five dimensions are used of all GSCM dimensions which affect fuel consumption & maintenance, repairing expenditure. In second phase, the well known relation with fuel consumption & maintenance, repairing expenditure and transportation cost reduction is used to get result for this study. Transportation cost reduction side is third phase in our model. One point about methodology should be clarified in second phase.The reverse relation between fuel consumption & maintenance, repairing expenditure and transportation cost reduction. But the difficulties of finding fluctuation in transportation cost reduction in a direct way. To get result about transportation cost reduction, I use the second phase as a step phase. Through secondphase, I get effect of five dimensions into fuel consumption & maintenance, repairing expenditure, then using result and using reverse relation, I reach the point which explains the effect of five dimensions into transportation cost reduction.3.1 QuestionnaireTo validate the model given in the preceding section, regression analysis is used to determine the causal relationships between environmental transportation, suppliers by environmental criteria, helping suppliers to establish their own environmental management system, optimize internal process to minimize vehicle movement, reverse logistics and transportation cost reduction.An empirical survey-based research approach was adopted, comprising of 38 items. The questionnaire was distributed to the environmental management representative or the logistics representative of ISO 14001 certified organizations. The justification for using a five-point scale served to understand that there might have been a tendency of having most negative responses loading heavily on the median level, the center point of the scale. The research instrument was distributed to corporations using an online survey website. Company representatives enter the website and response the questions through website.That website serves data as in SPSS file and SPSS estimates a series of separate but interdependent regression equations simultaneously. We have drawn upon the theory and the research objectives to determine which independent variable will predict which dependent variable. The proposed relationships are then translated into a series of structural equations for each dependent variable. The structural model expresses these relationships among independent and dependent variables.3.2 HypothesisAt this section, there are five different hypothesis e to examine the impact of GSCM on TCR. Five different hypothesis is coming from five different dimensions of GSCM. Of course, total dimensions are not only five but as representing in the preceding section, only five of all dimensions are used to create hypothesis. Hypothesis’ are in representing as below.3.3 ResultsBased on model and hypothesis, results have been gotten by using regression analysis method. In this analysis FCMRE and TCR is dependent variables and the other five dimensions of GSCM(Using more environmental transportation, Reverse logistics, Choice of suppliers by environmental criteria, Helping suppliers to establish their own EMS, Optimize internal process to minimize vehicle movement) are independent variables.4. ConclusionThis study concludes that green supply chain management encompasses potential to make cost saving in transportation. From production firm perspective, specially, main concerns of firms are continuously tracking, controlling and thinking how to manage their all kinds of cost, especially transportation cost.As mentioned in preceding sections, there is a relation as in formula mode between fuel consumption & maintenance, repairing expenditure (FCMRE) andtransportation cost. Because of the difficulties to collect and get the transportation cost data, model has fuel consumption & maintenance, repairing expenditure as a connection variable. This study proves the existing relation between GSCM and FCMRE. After proving this relation and using the relation between FCMRE and TCR, this study explains the impact of GSCM on transportation cost. Also, these research findings suggest that green their supply chains management affect not only fuel consumption, maintenance and repairing cost, but also through these variables affect transportation cost indirectly.绿色供应链管理对降低运输成本的影响摘要:供应链管理(SCM)已成为一种重要的竞争手段。
供应链中的战略成本管理,第二部分:特殊成本管理【外文翻译】

外文翻译原文:Strategic Cost Management in Supply Chains, Part 2: ExceptionalCost ManagementINTRODUCTIONIncreasingly, purchased materials and services account for a significant share of the cost of firms’ products and services. As a result, managers are devo ting more attention to developing strategies for managing complex supply chains. Strategic cost management, the deliberate alignment of a firm’s resources with long-term strategy and short-term tactics, is critical to managing the supply chain and delivering performance for all firms in the value chain (Aberdeen Group 2005). In a recent survey, managers report that increasing complexity of products and ervices, increasing and increasingly volatile input prices (e.g., wages, fuel), and the availability of sophisticated supply chain management tools have influenced their supply chain strategies (McKinsey & Company 2008, 3–4). The overwhelming response to these influences is a renewed focus on increasing the effectiveness with which supply chains provide low-cost, high-quality products and services with speed and reliability, and on evaluating supply chain risk—all elements of what we term executioner cost management.This paper is the second in a two-part series that examines contemporary research in strategic cost management in supply chains. We employ an organizing framework from Anderson (2007)that incorporates Shank and Govindarajan’s (1992, 1994) notions of structural and executioner cost drivers as well as a value chain perspective. In the first paper in the series, (Anderson and Dekker 2009), we focus on structural cost management decisions related to sourcing, supplier selection, the design of supplier relationships, and joint activities of buyers and suppliers in product and process design. In this paper, we take up executioner cost management of buyer supplier relationships, which includes assessing transaction-level and relationship-level performance as well as assessing the sustainability of the supplypartnership in the context of the full aloe chain.We begin with a review of the organizing framework that was presented more fully in the first paper in the series. Then we turn to the two major components of executioner cost management: (1)measuring, evaluating, and improving supply chain transactions and relationships, and (2)assessing supplier health and the long-term sustainability of supply relationships. We conclude with a brief summary of the two-part series and a discussion of how recent developments in strategic cost management in supply chains presage opportunities for accounting education.STRATEGIC COST MANAGEMENTShank and Govindarajan (1992, 1994) posit that two types of cost drivers are the basis for strategic cost management: structural cost drivers that reflect organizational structure, investment decisions, and the operating leverage of the firm; and executioner cost drivers that reflect the efficacy and efficiency of executing the strategy. Stated differently, structural cost management may be conceived of as a choice among alternative production functions that use different inputs or combinations thereof to meet a particular market demand. Executioner cost management is concerned instead with whether, for a given production function, the firm is on the efficient frontier. Tomkins and Carr (1996, 276) link the two modes of cost management, positing that cost driver analysis is a catalyst for improving existing processes (i.e., executioner cost management) as well as a catalyst for reengineering processes to create a different cost structure (i.e., structural cost management).Figure 1 depicts the interplay between market and competitive analysis, strategy development and structural cost management, and executioner cost management. Taking up Porter’s (1985) emphasis on creating competitive advantage throughout the value chain, Shank and Govindarajan (1992, 1994)recognize that the greatest opportunities for cost management are often at the boundaries of the firm. Figure 1 highlights the value chain as the domain for strategic cost management. Although the focus of this series of articles is on cost management between buyers and suppliers, Figure 1 also incorporates Kaplan and Norton’s (1996_)multi-stakeholder perspective, depicting strategic cost management as influencing and being influenced by a varietyof decision makers who are involved directly (e.g., suppliers, customers) and indirectly (e.g., nongovernmental organizations, governments) in the value chain.In this paper we focus on executioner cost management applied to suppliers of direct and indirect materials and services. In this context, executioner cost management includes assessing transaction-level and relationship-level performance (bottom of Figure 1)as well as assessing the sustainability of the supply partnership (middle of Figure 1). We consider first the lower portion of Figure 1, the executioner cost management activities associated with measuring and evaluating performance, and using this information collaboratively to improve performance. We then turn to the broader question of assessing the sustainability of the collaboration strategy. Here we recognize that buyer-supplier collaborations may perform as planned; however, with changing circumstances, collaboration may not be sustainable if either party stands to gain from withdrawing from the relationship or from diminished performance. The iterative nature of strategy development and refinement that unforeseen future events and uncertainty resolution necessitates is depicted in the feedback path between executioner and structural cost management. EXECUTIONAL COST MANAGEMENT IN SUPPLY CHAINS: MEASURING, MONITORING, AND IMPROVING PERFORMANCE Executioner cost management includes the familiar management accounting elements of measuring and monitoring performance as well as the dynamic use of performance data to improve performance (bottom of Figure ). Performance measurement systems contribute to performance improvement by clarifying expectations of exchange partners through setting goals, promoting goal-directed behavior, reducing ambiguity about outcomes, and enhancing feedback and learning (Manama 2006). Although these activities can be challenging within the firm, they are even more complicated between firms. A recent survey identifies sharing knowledge between different locations (within the buying firm and with different suppliers), integrating information technology, and managing communications in a culturally diverse business setting as significant challenges to supply chain management (McKinsey & Company 2008). Clearly, even setting aside conflicting objectives andopportunistic behavior that are ameliorated by structural cost management (described in the first part of this series), we are still left with significant performance management challengesWhen two or more firms transact, significant technical uncertainties can occur in defining and measuring performance and in distinguishing each firm’s influence on interdependent outcomes. Indeed, the transaction cost economics literature identifies ambiguities in measuring performance as a central reason why many firms vertically integrate activities that are fraught with measurement difficulties. Ambiguities may arise in what defines performance, how performance is to be measured, and how blame is apportioned in the event of performance failure. As one example, Anderson et al. (2000) provide empirical evidence that product design interdependencies in automotive components influence sourcing decisions and subsequent transaction performance. Technical uncertainties, in combination with physical and temporal separation of the two parties, contribute to and are compounded by communication and coordination failures.In spite of these concerns, accounting research indicates that performance measurement is an essential component of the supply chain management control structure that is associated with performance (Dekker 2003, 2004; Dekker and Van den Abele 2009; Lang field-Smith and Smith 2003; Manama 2006; Seal et al. 2004; Schmitz and Platt’s 2004). Ding et al. (2009_)find that finance managers frequently report being responsible for facilitating buyer-supplier cooperation through results monitoring, advice, supervision, and involvement in daily operations. To achieve these aims they use frequent, detailed financial and no financial performance information about partner firms. Gunasegaram et al. (2001, 2004)argue that the role of performance measures in the success of collaborative action cannot be overstated because they affect strategic, tactical, and operational planning and control.This section reviews research and contemporary practices related to financial and no financial performance measurement and to management feedback processes that employ performance measures as a catalyst to continuous improvement.Supply Transactions: Financial Performance MeasurementTraditionally, supplier performance has had one of two meanings. For the procurement specialist charged with obtaining materials and services at low cost, good supplier performance is a purchase price that is both stable and low. For the manufacturing manager, charged with producing output, good supplier performance is defined by reliability of delivery, accuracy of inventory, and quality (free of defects) of supply. These functional perspectives often result in conflicting assessments of supplier performance, conflict that is frequently reinforced by incentive schemes that reward one function (e.g., purchasing) for taking actions that harm another function (e.g., manufacturing).1 Alternatives for reconciling these functional perspectives in large decentralized firms include modified incentives and modified decision authority (i.e., structural cost management ). As elaborated in the first paper in this series, studies such as Anderson et al. (2000), Anderson and Lane (2002), Bauman et al. (2001), Bauman and Raja (2002), Cachou and Fisher (2000), Cachou and Zipkin (1999), and Gateman (1996)provide examples of firms using product and process design, inventory ownership and stocking decisions, and unique governance structures and information sharing to align perspectives on supplier performance.In the context of executioner cost management, accounting research has focused on traditional cost accounting and performance measures as causes of the problem. Specifically, management accounting researchers note that the cost that procurement specialists minimize—the purchase price—is incomplete if it excludes “hidden” costs, such as inventory stock-outs, that trouble manufacturing managers. Carr and liter (1992)formalize this argument and provide examples of firms that modify their cost accounting systems to assign “total cost of ownership” (TCO) values to suppliers’ products. Their description of the use of TCO in Texas Instruments Corporation shows that significant costs are unrelated to purchase price and relate instead to plant-level activities associated with handling the purchased components. Sun Microsystems (Fallow et al. 1996) translates several no financial dimensions of supplier performance into a financial TCO measure of supplier-performance measure.Whereas Texas Instruments and Sun Microsystems focus on individual suppliers’ performance, other firms take a broader perspective. For example, Dekker(20030 studies a retail firm that analyzes cost data in its multi-partner value chain. Transaction partners jointly allocate costs from an activity-based costing analysis to supply chain activities that cross firm boundaries. This allows the firms to examine how interdependent decisions are associated with costs to all partners. Thus the retailer has information about the TCO alternatives offered by different suppliers that facilitates “scenario analysis” of changes to the supply chain, and suppliers have the opportunity to benchmark their performance against competitors. Over time, both the retail firm and its suppliers can monitor performance trends. This example illustrates Porter’s (1985) prescription of managing linkages between value-creating activities to improve the value chain’s efficiency and provide competitive returns to all participants. In addition to domestic and global suppliers of purchased materials and services, modern supply chain management comprises contract manufacturers, company-owned product and service centers, third-party logistics providers, and a network of transportation providers (Trebilcock 2007). A question that has received little attention in the research literature is how these collaborations interact with and are managed alongside more traditional supply relationships.A challenge of adopting the TCO approach is identifying the “hidden” costs that are associated with a particular supplier. Some firms, like the retailer studied by Dekker (2003)treat the problem as one of cost allocation. They review costs incurred in conjunction with poor supplier performance (e.g., overhead costs associated with receiving nonstandard shipments, warranty claims, returns)and assign them, along with the purchase price of the supplier’s products and services, to TCO of the supplier.A potential limitation of this approach is the foc us on “accounting costs” as compared with “economic costs.” Opportunity costs associated with stock out and delayed production are often far greater than the purchase price of materials (Calling et al. 2005) or the overhead to manage purchased materials. Indeed, in a recent survey (O’Keefe 2004), supply chain managers identify supply interruption caused by supplier failure, logistics failure, a natural disaster, or a geopolitical event as the primary risks that they seek to mitigate.Although risk mitigation is clearly at the heart of structural cost management(see Anderson and Dekker 2009), we are unaware of any research that addresses how residual risk (risk that remains after adopting management controls) is incorporated into the more routine performance evaluations that executioner cost management comprises. Firms such as Sun Microsystems address this concern, in part, by departing from a cost-allocation approach to measuring TCO. They develop an extensive list of performance criteria, each with its own goal and “weight” in the TCO calculation. “Costs” (that are not linked in any way to accounting data)are assessed based on performance-to-goal, and a measure of TCO is obtained by summing across the goals. Additional research is needed to identify approaches used by other firms. Moreover, even the Sun Microsystems case does not address whether and how the residual risk associated with a particular supplier influences evaluation of the value chain. In a linked network of suppliers, even a small amount of risk associated with a single supplier quickly propagates throughout the value chain and affects all trading partners.2 Pernot (2008), for instance, describes how in its “just-in-sequence” system, Volvo Cars Gent is concerned about operational problems at suppliers that disturb supply chain continuity, not only of Volvo’s processes, but also of its other suppliers. Volvo developed performance measures, penalty systems, and behavior controls to prevent supplier problems and to efficiently manage problems that arise.Source: Shannon W. Anderson and Henri C. Dekker. Strategic Cost Management in SupplyChains,Part2:ExecutionalCostManagement[J].AccountingHorizons.2009(9):289-305.译文:供应链中的战略成本管理,第二部分:特殊成本管理简介在越来越多公司中,购买材料和服务占了各公司的产品和服务的成本重要份额。
供应链管理毕业论文文献翻译中英文对照
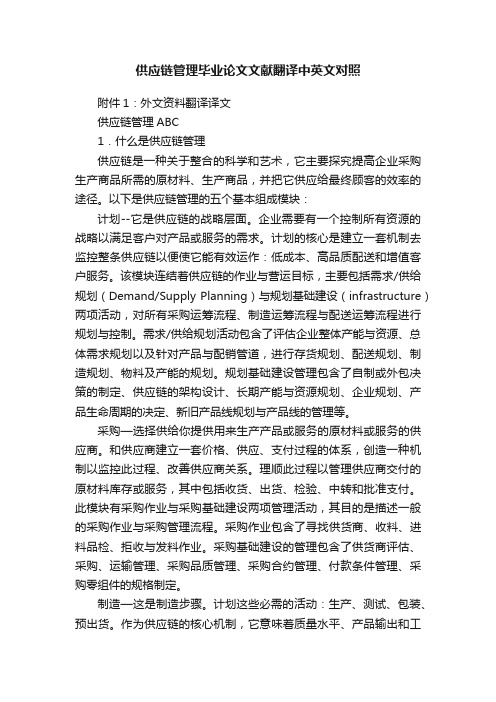
供应链管理毕业论文文献翻译中英文对照附件1:外文资料翻译译文供应链管理ABC1.什么是供应链管理供应链是一种关于整合的科学和艺术,它主要探究提高企业采购生产商品所需的原材料、生产商品,并把它供应给最终顾客的效率的途径。
以下是供应链管理的五个基本组成模块:计划--它是供应链的战略层面。
企业需要有一个控制所有资源的战略以满足客户对产品或服务的需求。
计划的核心是建立一套机制去监控整条供应链以便使它能有效运作:低成本、高品质配送和增值客户服务。
该模块连结着供应链的作业与营运目标,主要包括需求/供给规划(Demand/Supply Planning)与规划基础建设(infrastructure)两项活动,对所有采购运筹流程、制造运筹流程与配送运筹流程进行规划与控制。
需求/供给规划活动包含了评估企业整体产能与资源、总体需求规划以及针对产品与配销管道,进行存货规划、配送规划、制造规划、物料及产能的规划。
规划基础建设管理包含了自制或外包决策的制定、供应链的架构设计、长期产能与资源规划、企业规划、产品生命周期的决定、新旧产品线规划与产品线的管理等。
采购—选择供给你提供用来生产产品或服务的原材料或服务的供应商。
和供应商建立一套价格、供应、支付过程的体系,创造一种机制以监控此过程、改善供应商关系。
理顺此过程以管理供应商交付的原材料库存或服务,其中包括收货、出货、检验、中转和批准支付。
此模块有采购作业与采购基础建设两项管理活动,其目的是描述一般的采购作业与采购管理流程。
采购作业包含了寻找供货商、收料、进料品检、拒收与发料作业。
采购基础建设的管理包含了供货商评估、采购、运输管理、采购品质管理、采购合约管理、付款条件管理、采购零组件的规格制定。
制造—这是制造步骤。
计划这些必需的活动:生产、测试、包装、预出货。
作为供应链的核心机制,它意味着质量水平、产品输出和工厂产能的有效控制。
此模块具有制造执行作业与制造基础建设两项管理活动,其目的是描述制造生产作业与生产的管理流程。
供应链管理外文翻译文献
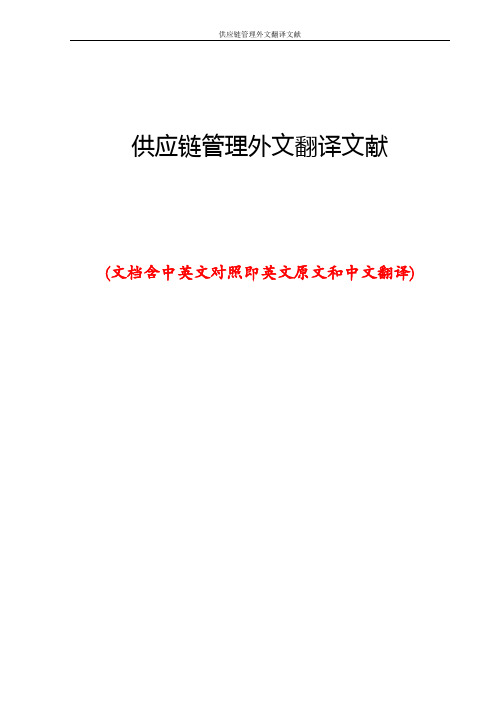
供应链管理外文翻译文献供应链管理外文翻译文献(文档含中英文对照即英文原文和中文翻译)Supply Chain ManagementThe so-called supply chain, in fact, from suppliers, manufacturers, warehouses, istribution centers and channels, and so constitute a logistics network. The same enterprise may constitute the different components of this network node, but the situation is different from a corporate network in different nodes. For example, in a supply chain, companies may not only in the same manufacturers, storage nodes, and in distribution centers, such as possession node location. In the more detailed division of labor, the higher the rofessional requirements of the supply chain, different nodes are basically composed by different enterprises. In the supply chain flows between the member units of raw materials, finished products, such as inventory and production constitutes the supply chain of goods flow.That is, to meet a certain level of customer service under the conditions, in order to make the whole supply chain to minimize costs and the suppliers, manufacturers, warehouses, distribution centers and channels, and so effectively organized together to carry out Product manufacturing, transport, distribution and sales management.From the above definition, we can be interpreted to include supply chain anagement of rich content.First of all, supply chain management products to meet customer demand in the process of the cost implications of various members of the unit are taken intoaccount, including from raw material suppliers, manufacturers to the warehouse distribution center to another channel. However, in practice in the supply chain analysis, it is necessary to consider the supplier's suppliers and customers of the customers, because their supply chain performance is also influential.Second, supply chain management is aimed at the pursuit of the whole supply chain's overall efficiency and cost effectiveness of the system as a whole, always trying to make the total system cost to a minimum. Therefore, the focus of supply chain management is not simply a supply chain so that members of the transportation costs to minimize or reduce inventory, but through the use of systems approach to coordinate the supply chain members so that the entire supply chain total cost of the minimum so that the whole supply chain System in the most fluent in the operation.Third, supply chain management is on the suppliers, manufacturers, warehouses, distribution centers and organically integrate the channel into one to start this problem, so many businesses, including its level of activities, including the strategic level, tactical and operational level Level, and so on.Although the actual logistics management, only through the organic supply chain integration, enterprises can significantly reduce costs and improve service levels, but in practice the supply chain integration is very difficult, it is because: First of all, in the supply chain There are different members of different and conflicting objectives. For example, providers generally want manufacturers to purchase large quantities of stable, and flexible delivery time can change; desire to the contrary with suppliers, although most manufacturers are willing toimplement long-term production operations, but they must take into account the needs of its customers and to make changes Positive response, which requires manufacturers choice and flexibility in procurement strategy. Therefore, suppliers and manufacturers to the goal of flexibility in the pursuit of the objectives inevitably exist between the contradictions.Secondly, the supply chain is a dynamic system, with time and constantly changing. In fact, customers not only demand and supply capacity to change over time, supply chain and the relationship between the members will change over time. For example, the increased purchasing power with customers, suppliers and manufacturers are facing greater pressure to produce more and more personalized varieties of high-quality products, then ultimately the production of customized products.Research shows that effective supply chain management can always make the supply chain of enterprises will be able to maintain stability and a lasting competitive advantage, thus increasing the overall supply chain competitiveness. Statistics show that, supply chain management will enable the effective implementation of enterprise total cost of about 20 per cent decline in the supply chain node on the enterprise-time delivery rate increased by 15 percent or more, orders to shorten the production cycle time 20 percent to 30 percent, supply chain Node on the enterprise value-added productivity increased by 15 percent or more. More and more enterprises have already recognized that the implementation of supply chain management of the great benefits, such as HP,IBM, DELL, such as supply chain management in the practice of the remarkable achievements made is proof.Supply chain management: it from a strategic level and grasp the overall perspective of the end-user demand, through effective cooperation between enterprises, access from the cost, time, efficiency, flexibility, and so the best results. From raw materials to end-users of all activities, the whole chain of process management.SCM (supply chain management) is to enable enterprises to better procurement of manufactured products and services required for raw materials, production of goods and services and their delivery to clients, the combination of art and science. Supply chain management, including the five basic elements.Plan: This is a strategic part of SCM. You need a strategy to manage all the resources to meet our customers for your products. Good plan is to build a series of methods to monitor the supply chain to enable it to effective, low-cost delivery of high quality for customers and high-value products or services.Procurement: you can choose the products and services to provide goods and services providers, and suppliers to establish a pricing, delivery and payment processes and create methods to monitor and improve the management, and the suppliers to provide goods and services Combined with management processes, including the delivery and verification of documentation, transfer of goods to your approval of the manufacturing sector and payments to suppliers and so on.Manufacturing: arrangements for the production, testing, packaged and ready for delivery, supply chain measurement is the largest part of the contents, including the level of quality, product yield and productivity of workers, such as the measurement.Delivery: a lot of "insider" as "logistics", is to adjust the user's orders receipts, the establishment of the storage network, sending and delivery service delivery personnel to the hands of customers, the establishment of commodity pricing system, receiving payments.Return: This is the supply chain problems in the handling part. Networking customers receive the refund of surplus and defective products, and customer applications to provide support for the problem.Source70 in the late 20th century, Keith Oliver adoption and Skf, Heineken, Hoechst, Cadbury-Schweppes, Philips, and other contact with customers in the process of gradually formed its own point of view. And in 1982, "Financial Times" magazine in an article on the supply chain management (SCM) of the significance, Keith Oliver was that the word will soon disappear, but "SCM" not only not disappeared, and quickly entered the public domain , The concept of the managers of procurement, logistics, operations, sales and marketing activities sense a great deal.EvolutionSupply chain has never been a universally accepted definition, supply chain management in the development process, many experts and scholars have putforth a lot of definition, reflecting the different historical backgrounds, in different stages of development of the product can be broadly defined by these For the three stages:1, the early view was that supply chain is manufacturing enterprises in an internal process2, but the supply chain concept of the attention of the links with other firms 3, the last of the supply chain concept of pay more attention around the core of the network links between enterprises, such as core business with suppliers, vendors and suppliers, and even before all the relations, and a user, after all the users and to the relationship.ApplySupply chain management involves four main areas: supply, production planning, logistics, demand. Functional areas including product engineering, product assurance, procurement, production control, inventory control, warehouse management, distribution management. Ancillary areas including customer service, manufacturing, design engineering, accounting, human resources, marketing.Supply Chain Management implementation steps: 1, analysis of market competition environment, identify market opportunities, 2, analysis of customer value, 3, identified competitive strategy, 4, the analysis of the core competitiveness of enterprises, 5, assessment, selection of partners For the supply chain partners of choice, can follow the following principles:1, partners must have available the core of their competitiveness.2, enterprises have the same values and strategic thinking3, partners must Fewer but Better.CaseAs China's largest IT distributor, Digital China in China's supply chain management fields in the first place. In the IT distribution model generally questioned the circumstances, still maintained a good momentum of development, and CISCO, SUN, AMD, NEC, IBM, and other famous international brands to maintain good relations of cooperation. e-Bridge trading system in September 2000 opening, as at the end of March 2003, and 6.4 billion yuan in transaction volume. In fact, this is the Digital China from the traditional distribution supply chain services to best reflect the changes. In the "distribution of services is a" concept, Digital China through the implementation of change channels, expansion of product and service operations, increasing its supply chain in the value of scale and specialized operations, to meet customer demand on the lower reaches of the In the course of the supply chain system can provide more value-added services, with more and more "IT services" color.供应链管理所谓供应链,其实就是由供应商、制造商、仓库、配送中心和渠道商等构成的物流网络。
供应链英语翻译(译文和原文)

Perspectives in supply chain risk managementChristopher S. TangUCLA Anderson School, 110 Westwood Plaza, UCLA, Los Angeles, CA 90095,USAReceived 3 November 2005; accepted 16 December 2005Available online 2 March 2006AbstractTo gain cost advantage and market share, many firms implemented various initiatives such as outsourced manufacturing and product variety. These initiatives are effective in a stable environment, but they could make a supply chain more vulnerable to various types of disruptions caused by uncertain economic cycles, consumer demands, and natural and manmade disasters. In this paper, we review various quantitative models for managing supply chain risks. We also relate various supply chain risk management (SCRM) strategies examined in the research literature with actual practices. The intent of this paper is three-fold. First, we develop a unified framework for classifying SCRM articles. Second, we hope this review can serve as a practical guide for some researchers to navigate through the sea of research articles in this important area. Third, by highlighting the gap between theory and practice, we hope to motivate researchers to develop new models for mitigating supply chain disruptions.Keywords:Supply chain risk management; Quantitative models; Review1. IntroductionOver the last 10 years, earthquakes, economic crises,SARS, strikes, terrorist attacks have disrupted supply chain operations repeatedly. Supply chain disruptions can have significant impact on a firm’s short-term performance. For example, Ericsson lost 400 million Euros after their supplier’s semiconductor plant caught on fire in 2000, andApple lost many customer orders during a supply shortage of DRAM chips after an earthquake hit Taiwan in 1999. Supply chain disruptions can have long-term negative effects on a firm’s financial performance as well. For instance, Hendricks and Singhal (2005) report that companies suffering from supply chain disruptions experienced 33–40% lower stock returns relative to their industry benchmarks.To mitigate supply chain disruptions associated with various types of risks (uncertain economic cycles,uncertain consumer demands, and unpredictable natural andman-made disasters), many researchers have developed different strategies/models for managing supply chain risks. In this paper, we review primarily quantitative models that deal with supply chain risks. Also, we relate various supply chain risk management (SCRM) strategies examined in the literature with actual practices. The intent of this paper is threefold. First, we develop a unified framework for classifying SCRM articles. Second, we hope this review can serve as a practical guide for some researchers to navigate through the sea of research articles in this important area. Third, by highlighting the gap between theory and practice, we hope to motivate researchers to develop new models for mitigating supply chain disruptions.2. Supply managementTo gain cost advantage, many firms outsourced certain non-core functions so as to maintain a focus on their core competence (cf., Porter (1985)). Since the 1980s, we witnessed a sea change in which firms outsourced their supply chain operations including design, production, logistics, information services, etc. Essentially, supply management deal with five inter-related issues:1. supply network design,2. supplier relationship,3. supplier selection process (criteria and supplierselection),4. supplier order allocation,5. supply contract.3.Demand managementIn Section 2, we describe how manufacturers can use different supply management strategies to mitigate various supply chain operational risks However, these supply management strategies are ineffective when the underlying supply mechanism is inflexible. For instance, in the service industry or in the fashion goods manufacturing industry, the supply mechanism is inflexible because the capacity is usually fixed. When the supply capacity is fixed, many firms have attempted to use different demand management strategies so that they can manipulate uncertain demands dynamically so that the modified demand is better matched with the fixed supply.Due to space limitation, we are unable to review the dynamic pricing or clearance pricing literature. The reader is referred to Elmaghraby and Keskinocak (2003) for an extensive review of dynamic pricing models and clearance pricing models for selling a fixed number of units over a finite horizon. Also, we do not plan to review literature that deal with coordination of pricing and ordering decisions. The reader is referred to Yano and Gilbert (2004),Petruzzi and Dada (1999), Eliashberg and Steinberg (1993) for three comprehensive reviews in this area. Instead, we shall focus on articles that emphasize on the use of demand management strategies to‘‘shape’’ uncertain demand so that a firm can use an inflexible supply to meet the modified demand.4. Product managementTo compete for market share, many manufacturers expand their product lines. As reported in Quelch and Kenny (1984), the number of stock keeping units (SKUs) in consumer packaged goods has been increasing at a rate of 16% every year between 1985 and 1992. Marketing research shows that product variety is an effective strategy to increase increasing market share because it enables a firm to serve heterogeneous market segments and to satisfy consumer’s variety seeking behavior. However, while product variety may help a firm to increase market share and revenue, product variety can increase manufacturing cost due to an increasein manufacturing complexity. Moreover, product variety can increase inventory cost due to an increase in demand uncertainty. These twoconcerns have been illustrated in an empirical study conducted by MacDuffie et al. (1996). They show that the production and inventory costs tend to increase as product variety increases. Therefore, it is critical for a firm to determine an optimal product portfolio that maximizes the firm’s profit. The reader is referred to Ramdas (2003) for a comprehensive review of literature in the area of product variety.5. Information managementAs explained in Fisher (1997), most consumer products can be classified as fashion products or functional products. Basically, fashion products usually have shorter life cycles and higher levels of demand uncertainties than the functional products. Therefore, different information management strategies would be needed to manage for different typesof products especially in the presence of supply chain risks. For this reason, we shall classify the work in this section according to the product types: fashion products and functional products.6.Robust strategies for mitigating operational and disruption risksUpon examining the underlying assumptions of the models reviewed so far, it appears most of the quantitative models are designed for managing operational risks. Even though these quantitative models often provide cost effective solutions for managing operational risks, there do not address the issue of disruption risks in an explicit manner. Before we present some potential research ideas for managing supply chain disruption risk in the next section, we shall examine how disruptions risks are managed in practice and relate these practices to the models reviewed earlier. After reviewing some qualitative analyses presented in various risk management and SCRM articles, we can summarize the key findings as follows:1.Managers’attitude towards risks:Sharpira (1986) and March and Sharpira (1987) study managers’ attitude towards risks and they conclude that:(1)Managers are quite insensitive to estimates of the probabilities of possible outcomes.(2) Managers tend to focus on critical performance targets, which affect the way they manage risk.(3) Managers make a sharp distinction between taking risks and gambling.2.Managers’ attitude towards initiatives for managing supply chaindisruption risks.7. ConclusionsIn this paper, we have reviewed various quantitative models for managing supply chain risks. We found that these quantitative models are designed for managing operational risks primarily, not disruption risks. However, we argue that some of these strategies have been adopted by practitioners because these strategies can make a supply chain become more efficient in terms of handling operational risks and more resilient in terms of managing disruption risks. Since there are few supply chain management models for managing disruption risks, we would like to present six potential ideas for future research.1.Demand and supply process:Virtually, all models reviewed in this paper are based on the assumption that the demand or the supply process is stationary. To model various types of disruptions mathematically, one may need to extend the analysis to deal with non-stationary demand or supply process. For instance, one may consider modeling the demand or the supply process as a ‘‘jump’’ process to capture the characteristics of major disruptions.2.Objective function:The performance measures of the models reviewed in this paper are primarily based on the expected cost or profit. The expected cost or profit is an appropriate measure for evaluating different strategies for managing operational risks. When dealing with disruption risks that rarely happen, one may need to consider alternative objectives besides the expected cost/profit.3.Supply management strategies:When developing supply management strategies for managing disruption risks, both academics and practitioners suggest the idea of ‘‘back-up’’ suppliers.4.Demand management strategies: Among the demand management strategies presented in Section 3, it appears that dynamic pricing/ revenue management has great potential for managing disruption risks because a firm can deploy this strategy quickly after a disruption occurs. In addition, revenue management looks promising especially after successful implementations of different revenue management systems in the airline industry for managing operational risks.5. Product management strategies: When selling products on line, e-tailers can change their product assortments dynamically according to the supply and demand of different products. This idea can be extended to brick and mortar retailers for managing disruption risks.rmation management strategies: Among the information management strategies described in Section 6, we think the CPFR strategy is promising because it fosters a tighter coordination and stronger collaboration among supply chain partners.站在供应链风险管理的角度作者:Christopher S. Tang摘要:为了获得成本优势和抢占市场份额,很多企业采取了各种措施,比如外包生产制造和产品多样化生产。
- 1、下载文档前请自行甄别文档内容的完整性,平台不提供额外的编辑、内容补充、找答案等附加服务。
- 2、"仅部分预览"的文档,不可在线预览部分如存在完整性等问题,可反馈申请退款(可完整预览的文档不适用该条件!)。
- 3、如文档侵犯您的权益,请联系客服反馈,我们会尽快为您处理(人工客服工作时间:9:00-18:30)。
本科毕业论文外文翻译供应链中的战略成本管理-结构性成本管理Strategic Cost Management in Supply ChainsPart 1: Structural Cost ManagementShannon W. Anderson and Henri C. DekkerAbstract: Strategic cost management is the deliberate alignment of a firm’s resources and associated cost structure with long-term strategy and short-term tactics. Although managers continue to pursue efficiency and effectiveness within the firm increasingly, Improvements are obtained across the value chain: through reconfiguring firm boundaries, relocating resources, reengineering processes, and re-evaluating product and service offerings in relation to customer requirements. In this article, we review strategic cost management, especially structural cost management. Structural cost management employs tools of organizational design, product design, and process design to create a supply chain cost structure that is coherent with firm strategy.Key wards: structural cost management; su pply cha in; competitive Advantage1 INTRODUCTIONThe prevalence in the current business press about acquisitions, restructuring, outsourcing, and off shoring indicates the vigor with which firms are engaged in the modern cost management. There’s a shift from prior internal processes for efficiency and effectiveness, firms are attempt to manage costs throughout the value chain. As the value of purchased materials and services as a share of selling price has increased ,firms find themselves managing complex supply chains, that include global suppliers, contract manufacturers, service centers and so on. Firms should pay attention to the value chain, so that they can obtain the room of development.2 STRATEGIC COST MANAGEMENTCost management research has tended to fall into two related streams. The first research stream examine whether and how firms configure accounting data to support value chain analysis ; T he second research stream attempt to derive the relationship between a firm’s strategy and cost structure. The focus is on the causal relation between activity levels and the resources that are required. These research streams take as given the firm’s strategy and structure and focus on whether accounting records are capable of reflecting or detecting the economics of the chosen strategy. In this review we take Shank’s broader perspect ive that much of what constitutes strategic cost management is found in choices about organizational strategy and structure. Following Anderson, we define “strategic cost management” as deliberate decision making aimed at aligning the firm’s cost structure with its strategy and with managing the enactment of the strategy.We focus on interactions across firm boundaries; Specially, the buyer/supplier interface, as a source of competitive advantage that can deliver low cost, as well as high productivity, quality, customer responsiveness, and innovation. Shank posited that two types of cost drivers are the basis for strategic cost management: structural cost drivers that reflect organizational structure, investment decisions, and the operating leverage of the firm and executive cost drivers that reflect the efficiency of executing the strategy. Stated differently,structural cost management may be conceived of as a choice among alternative production functions that use different inputs or combinations there of to meet a particular market demand. Executive cost management is concerned instead with whether, for a given production function, the firm is on the efficient frontier. Structural and executive cost management is connected through improvement activities. For example, cost driver analysis is a catalyst for efficiency improvements of existing processes and for reengineering processes to create a different cost structure. Clearly ,cost management is only a part of long term profit maximization. This paper series will not discuss strategic revenue management; however, we acknowledge interdependencies between costs and revenues associated structural cost management and the executive cost management activities of the sustainability of the strategy. Often the greatest o pportunities for strategic cost management cross firm boundaries. Shank advocated cost management across the value chain, and other accounting scholars have called for research on how accounting facilitates modern inter-organizational relationships.3 STRUCTURAL COST MANAGEMENT IN SUPPLY CHAINSShank argued that structural cost drivers associated with organizational structure, investment decisions, and the operating leverage of the firm. In supply chain management, structural cost management includes the decision to seek an external supplier, selecting one or more external suppliers, and designing the buyer/supplier relationship. These elements of supply chain management are important determinants of cost structure and are central to managing risk in supply relations. Supplier selection processes are akin to personnel controls within the firm that ensure the fitness between employee skills and job requirements. Designing the buyer/supplier relationship encompasses formal contractual management controls such as specifying authority for supply decisions, performance requirements, and rewards or sanctions for nonperformance, as well as formal and informal controls that reinforce desired cultural norms. Although we focus on structural cost management, many of the cost management decisions discussed in this section relate to balancing the “cost of control” against risks of inter-firm transactions. We review research and contemporary practices associated with sourcing decisions, supplier selection in the sections that follow.4 SOURCING: MAKE; BUY OR ALLYA core component of structural cost management is the decision to execute activities within the firm or to outsource them to another party. The so-called “make-buy-or-ally” decision considers how and where in the value chain firms draw their organizational boundaries and which activities are conducted inside versus outside the firm. Although the buyer and supplier are separate firms, the supply relationship often includes collaboration in the uncertain realm of product and process design.Transaction cost economics is the most widely used framework for explaining firm boundary and organizational design choices. Production costs are defined by production technology and efficiency. A buyer and supplier’s production costs may di ffer if they use different technology, operate at different scales, or operate with different efficiency A buyer’s cost accounting recordsmay be one basis for comparing the “make” option with prices of external suppliers. Transaction costs concerns about opportunism associated with firm’s transactions. Examples of transaction costs include costs of activities such as searching for partners, negotiating and writing contracts, monitoring and enforcing contract compliance. Transaction costs are not typically accessible and, in the case of opportunity costs, may not even be included in cost accounting records. Consequently, texts typically warn students to consider strategic factors before making a sourcing decision based only on production costs. This is one area where cost management practices, both measurement and analysis, can be improved to better support structural cost management decisions associated with sourcing.5 INTERDEPENDENCE IN SUPPLY CHAINSAlthough we discuss the sourcing decision as a logical “starting point” in supply chain management, in reality this element of structural cost management is intertwined with other elements of strategic cost management. For example, in TCE theory, sourcing decisions are posited to reflect the minimization of anti cipated exchange hazards. The potential transaction partners are important predictors of exchange hazards. However, in complex supply chains in which many suppliers contribute to the completed product, product architecture is also a key determinant of sourcing decisions. The “partnership” strategies in supply chains depend critically on using criteria other than price in supplier selection. Thus, structural cost management decisions associated with sourcing are intertwined with structural cost management practices in supplier selection .6 THE SUPPLY CHAINS AS A SOURCE OF COMPETITIVE ADV ANTAGETCE, with its underlying performance risk and relational risk, focuses on potential downsides of cooperation. Another school of thought, the resource-based view RBV of the firm, focuses on the upside of cooperation. The RBV implicates inter-firm cooperation in the realization of strategic advantage, with firm boundaries resulting from managers’ dynamic search for opportunities to deploy valuable, scarce, inimitable resources to obtain abnormal returns. The basis for exchange in alliances can be financial, technological, physical, or managerial resources. Studies applying the RBV to explain firm boundaries emphasize the inimitable value of collaborative partnerships.While the perspectives of TCE and risk management differ from the RBV, both assume that firm choices are motivated by the goal of maximizing long-run performance. Whereas TCE focuses on minimizing transaction costs at a given time, the RBV emphasizes the illiquidity and immobility of valuable resources. This approach admits the possibility that transacting with external parties dynamically changes the resources and capabilities that will be available in future periods. Together these frameworks point to important areas for growth in management accounting, Specifically, TCE and risk management indicate the importance of measuring risk in supply relationships and formally integrating risk assessments into the make, buy, or ally decision. The RBV indicates the importanc e of the emerging area of accounting for human capital and other firm capabilities and intangible assets whose value changes through exchange with strategic supply partners.7 TRENDS IN SUPPLY CHAIN GROWTHRecent years have shown tremendous growth in the use of the ally mode across different industries. In manufacturing, over the past 50 years the value of purchased materials and services has grown from 20 percent to 56 percent of the selling price of finished goods. AMR Researchfindthat the typical U.S. manufacturer manages over 30 contract relationships. In 2006, the worldwide market for supply chain management software, growing at an annual rate of 8.6 percent, topped $6 billion. The global IT outsourcing market was expected to grow to almost triple that size. Growth in use of collaboration is found in firms of different sizes and from different industries. for instance, report that almost 80percent of small to large Dutch firms are involved in enduring forms of interfirm cooperation,typically managing multiple partners at the same time. The largest proportion constituted outsourcing relations, a frequency that appears to follow from its potential to generate cost reductions and increased flexibility, including the opportunity to convert fixed costs into variable costs and to benefit from economies of scale and scope.In sum, sourcing decisions are critical to structural cost management in supply chains; how-ever, there is little evidence that cost accountants have extended their expertise to include all relevant costs. Moreover, although risk management is becoming more common and supply chain risk is foremost among the risks that firms seek to control,accountants are primarily involved with controlling and mitigating risk.8 SUPPLIER SELECTIONThe search process of finding a supply partner is itself costly, entailing as it does identifying alternatives, evaluating supplier capabilities, and managing the final selection process. Although TCE suggests that supplier selection is a cost-minimizing choice, the RBV identifies a broader set of decision criteria. In particular, selecting suppliers with capabilities and resources that match the buyer’s needs is critical to supply chain performance and coordination. Key capabilities that have been shown to directly impact performance include inventory management, production planning and control, cash flow requirements, and product/service quality. Das and Teng defined financial resources, technological, physical, and managerial resources as the basis for alliance activity. Prior s tudies find that the criteria used for supplier selection typically reflect the specific resources and competencies that are desired in potential partners. Examples include competitive pricing, supplier reliability, service support, and capabilities that may have a long-term contribution to buyers’ competitive advantage. The selection criteria can include “hard,” quantitative measures of performance; however, frequently they are complemented with “soft” measures that capture qualitative aspects of the desired relationship with the supplier.The success of buyer/supplier relation-ships characterized as “partnerships” is related to the buyer’s use of criteria other than price in selecting suppliers. As in the decision to outsource, the recognition of risks can be essential in supplier selection processes. Relational risks, performance risks, and their associated costs are avoided when suppliers are selected based on evidence of trustworthiness and competence. Accordingly, the selection process and selection criteria should reflect both the type of supplier resources and competencies needed, and the anticipated risks of the relationship. These factors also link the sourcing decision and supplier.CONCLUSIONIncreasingly, business strategy focuses on reexamining the b oundaries of the firm—on establishing appropriate boundaries, identifying supply chain partners with whom to co-design efficient,effective products and processes, and managing transactions with these partners to deliver profit s to all value chain participants.Article source:2009 Accounting Horizons V ol.23.摘要战略成本管理是对一个公司的资源的深入的整合,它通常把企业的成本结构和企业的长期战略和短期策略联系起来,尽管管理人员不断在企业内部追求效率和效益,然而,企业效益的日益提升最终是通过价值链获得的,即通过重组企业边界(如上游供应商、下游客户),重新定位资源,再造过程和重估与顾客需求相联系的产品和服务获得的。