现场5S管理制度细则(ELS)
现场5s管理制度及标准
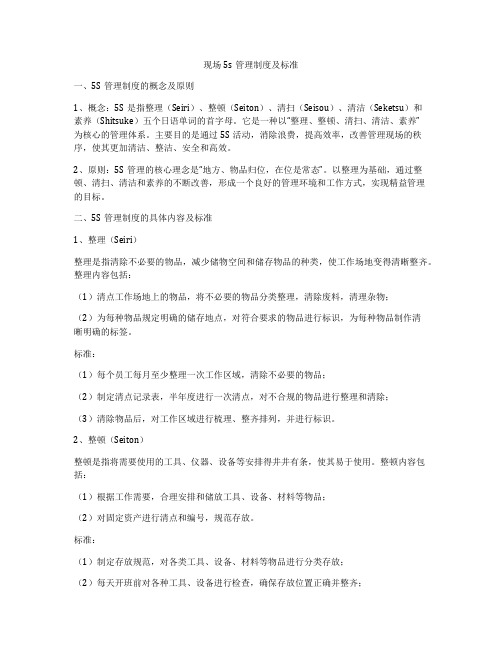
现场5s管理制度及标准一、5S管理制度的概念及原则1、概念:5S是指整理(Seiri)、整顿(Seiton)、清扫(Seisou)、清洁(Seketsu)和素养(Shitsuke)五个日语单词的首字母。
它是一种以“整理、整顿、清扫、清洁、素养”为核心的管理体系。
主要目的是通过5S活动,消除浪费,提高效率,改善管理现场的秩序,使其更加清洁、整洁、安全和高效。
2、原则:5S管理的核心理念是“地方、物品归位,在位是常态”。
以整理为基础,通过整顿、清扫、清洁和素养的不断改善,形成一个良好的管理环境和工作方式,实现精益管理的目标。
二、5S管理制度的具体内容及标准1、整理(Seiri)整理是指清除不必要的物品,减少储物空间和储存物品的种类,使工作场地变得清晰整齐。
整理内容包括:(1)清点工作场地上的物品,将不必要的物品分类整理,清除废料,清理杂物;(2)为每种物品规定明确的储存地点,对符合要求的物品进行标识,为每种物品制作清晰明确的标签。
标准:(1)每个员工每月至少整理一次工作区域,清除不必要的物品;(2)制定清点记录表,半年度进行一次清点,对不合规的物品进行整理和清除;(3)清除物品后,对工作区域进行梳理、整齐排列,并进行标识。
2、整顿(Seiton)整顿是指将需要使用的工具、仪器、设备等安排得井井有条,使其易于使用。
整顿内容包括:(1)根据工作需要,合理安排和储放工具、设备、材料等物品;(2)对固定资产进行清点和编号,规范存放。
标准:(1)制定存放规范,对各类工具、设备、材料等物品进行分类存放;(2)每天开班前对各种工具、设备进行检查,确保存放位置正确并整齐;(3)对固定资产进行清点,半年度进行一次编号清点。
3、清扫(Seisou)清扫是指对工作场所和设备进行清洁,保持清洁卫生,创造一个舒适的工作环境,避免污染和劳动事故。
清扫内容包括:(1)定期清洁工作场地、设备、机器、设施、生产线等;(2)开展周边环境的清理和整顿。
现场5S管理细则
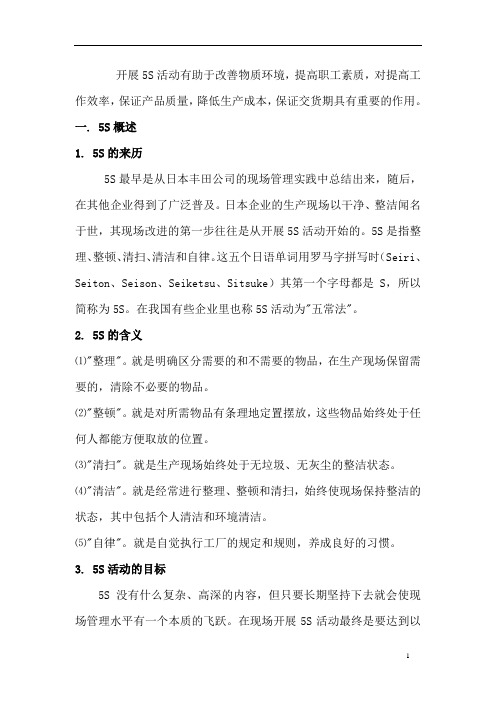
开展5S活动有助于改善物质环境,提高职工素质,对提高工作效率,保证产品质量,降低生产成本,保证交货期具有重要的作用。
一. 5S概述1. 5S的来历5S最早是从日本丰田公司的现场管理实践中总结出来,随后,在其他企业得到了广泛普及。
日本企业的生产现场以干净、整洁闻名于世,其现场改进的第一步往往是从开展5S活动开始的。
5S是指整理、整顿、清扫、清洁和自律。
这五个日语单词用罗马字拼写时(Seiri、Seiton、Seison、Seiketsu、Sitsuke)其第一个字母都是S,所以简称为5S。
在我国有些企业里也称5S活动为"五常法"。
2. 5S的含义⑴"整理"。
就是明确区分需要的和不需要的物品,在生产现场保留需要的,清除不必要的物品。
⑵"整顿"。
就是对所需物品有条理地定置摆放,这些物品始终处于任何人都能方便取放的位置。
⑶"清扫"。
就是生产现场始终处于无垃圾、无灰尘的整洁状态。
⑷"清洁"。
就是经常进行整理、整顿和清扫,始终使现场保持整洁的状态,其中包括个人清洁和环境清洁。
⑸"自律"。
就是自觉执行工厂的规定和规则,养成良好的习惯。
3. 5S活动的目标5S没有什么复杂、高深的内容,但只要长期坚持下去就会使现场管理水平有一个本质的飞跃。
在现场开展5S活动最终是要达到以下几个目标:⑴保证质量,提高工效。
⑵降低消耗,降低成本。
⑶保证机器设备的正常运转。
⑷改善工作环境,消除安全隐患,提高员工工作的满意度。
⑸提高班组长和工人现场改进能力的途径。
整理、整顿、清扫1. 整理⑴整理的目的"整理"是对物品进行区分和归类,将经常使用的物品放在使用场所附近,而将不经常使用或很少使用的物品放在高处、远处乃至仓库中去。
在具体实施中,可根据重要程度、是否经常使用、价值如何以及物品使用部门来区分。
总的说来,整理的目的是:1)腾出空间,充分利用空间。
5s管理制度细则
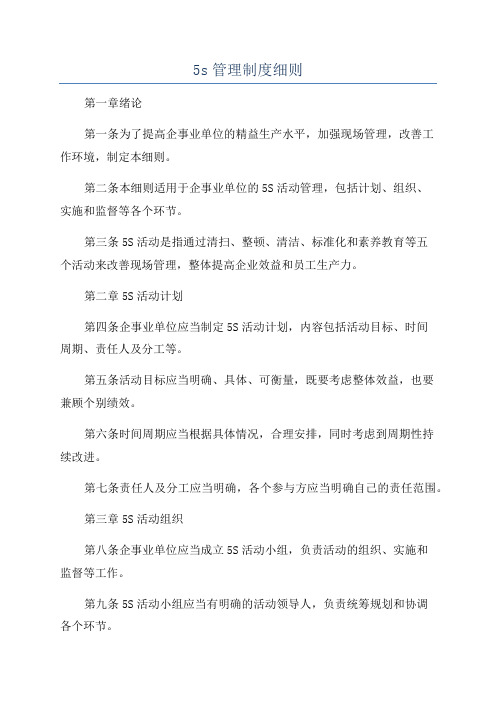
5s管理制度细则第一章绪论第一条为了提高企事业单位的精益生产水平,加强现场管理,改善工作环境,制定本细则。
第二条本细则适用于企事业单位的5S活动管理,包括计划、组织、实施和监督等各个环节。
第三条5S活动是指通过清扫、整顿、清洁、标准化和素养教育等五个活动来改善现场管理,整体提高企业效益和员工生产力。
第二章5S活动计划第四条企事业单位应当制定5S活动计划,内容包括活动目标、时间周期、责任人及分工等。
第五条活动目标应当明确、具体、可衡量,既要考虑整体效益,也要兼顾个别绩效。
第六条时间周期应当根据具体情况,合理安排,同时考虑到周期性持续改进。
第七条责任人及分工应当明确,各个参与方应当明确自己的责任范围。
第三章5S活动组织第八条企事业单位应当成立5S活动小组,负责活动的组织、实施和监督等工作。
第九条5S活动小组应当有明确的活动领导人,负责统筹规划和协调各个环节。
第十条5S活动小组应当由各个部门的代表组成,确保各个环节的有效落实。
第四章5S活动实施第十一条企事业单位应当通过培训和宣传等方式,提高员工对5S活动的认识和参与度。
第十二条企事业单位应当制定相应的工作标准和操作规程,明确各个环节的工作内容和要求。
第十三条企事业单位应当定期进行现场巡查,发现问题及时整改,确保5S活动的实施效果。
第五章5S活动监督第十四条企事业单位应当建立5S活动评估机制,定期对5S活动的实施效果进行评估,发现问题进行改进。
第十五条5S活动评估应当包括现场的实际情况、员工的参与度和整体效益等方面。
第十六条5S活动评估结果应当反馈给相关人员,追踪整改情况,确保问题得到解决。
第六章附则第十七条企事业单位应当根据实际需要,制定相应的5S活动细则,配合本制度的实施。
第十八条本细则自公布之日起生效,以后修订或者补充的,由企事业单位根据需要制定,并向相关人员进行通知。
第十九条本细则的解释权归企事业单位所有。
第二十条本细则未尽事宜,按照国家相关法律法规和企事业单位的规章制度执行。
现场“5S”管理制度
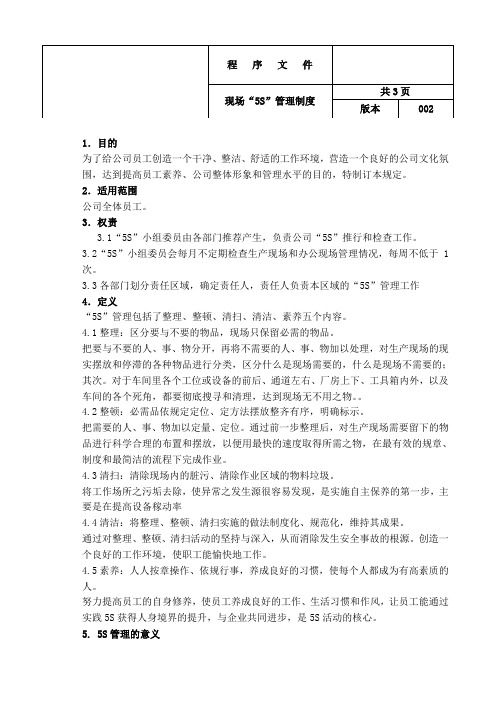
1.目的为了给公司员工创造一个干净、整洁、舒适的工作环境,营造一个良好的公司文化氛围,达到提高员工素养、公司整体形象和管理水平的目的,特制订本规定。
2.适用范围公司全体员工。
3.权责3.1“5S”小组委员由各部门推荐产生,负责公司“5S”推行和检查工作。
3.2“5S”小组委员会每月不定期检查生产现场和办公现场管理情况,每周不低于1次。
3.3各部门划分责任区域,确定责任人,责任人负责本区域的“5S”管理工作4.定义“5S”管理包括了整理、整顿、清扫、清洁、素养五个内容。
4.1整理:区分要与不要的物品,现场只保留必需的物品。
把要与不要的人、事、物分开,再将不需要的人、事、物加以处理,对生产现场的现实摆放和停滞的各种物品进行分类,区分什么是现场需要的,什么是现场不需要的;其次。
对于车间里各个工位或设备的前后、通道左右、厂房上下、工具箱内外,以及车间的各个死角,都要彻底搜寻和清理,达到现场无不用之物。
4.2整顿:必需品依规定定位、定方法摆放整齐有序,明确标示。
把需要的人、事、物加以定量、定位。
通过前一步整理后,对生产现场需要留下的物品进行科学合理的布置和摆放,以便用最快的速度取得所需之物,在最有效的规章、制度和最简洁的流程下完成作业。
4.3清扫:清除现场内的脏污、清除作业区域的物料垃圾。
将工作场所之污垢去除,使异常之发生源很容易发现,是实施自主保养的第一步,主要是在提高设备稼动率4.4清洁:将整理、整顿、清扫实施的做法制度化、规范化,维持其成果。
通过对整理、整顿、清扫活动的坚持与深入,从而消除发生安全事故的根源。
创造一个良好的工作环境,使职工能愉快地工作。
4.5素养:人人按章操作、依规行事,养成良好的习惯,使每个人都成为有高素质的人。
努力提高员工的自身修养,使员工养成良好的工作、生活习惯和作风,让员工能通过实践5S获得人身境界的提升,与企业共同进步,是5S活动的核心。
5. 5S管理的意义5.1运用“5S”的作法,彻底消除资源的浪费。
五s管理制度

“五S”管理制度是一种起源于日本的管理方法,它通过规范现场、现物,营造一目了然的工作环境,培养员工良好的工作习惯,其最终目的是提升人的品质。
以下是“五S”管理制度的具体内容:
1.整理(SEIRI):在工作现场区分要与不要的东西,只保留有用的东西,撤除不
需要的东西。
2.整顿(SEITION):把要用的东西按规定的位置摆放整齐,并做好标识进行管理。
3.清扫(SEISO):将不需要的东西彻底清扫干净。
4.清洁(SEIKETSU):使一切物品都能排列整齐,井然有序,保持美观、整洁。
5.素养(SHITSUKE):通过以上活动,使员工养成良好的工作习惯,自觉遵守各
项规章制度。
以上五点是“五S”管理制度的核心内容。
这种管理制度的目标是创造一个干净、整洁、有序、高效的工作环境,并提高工作效率和员工士气。
同时,它也有助于减少浪费、提高安全性,并提升公司的整体形象。
5s管理细则

5s管理细则在现代企业管理中,5S管理被广泛应用,以提高工作效率、减少浪费、改善工作环境等方面取得了显著成效。
本文将介绍5S管理的具体细则,帮助企业实施和推行5S管理。
第一S:整理(Seiri)整理是指通过分类、筛选,将物品分为必要和非必要的两类,保留必要的物品,淘汰或处理非必要的物品。
企业应制定相应的整理标准,让员工明确什么是必要的物品,什么是非必要的物品。
在工作现场,应配备足够的储物设施,标识清晰,方便分类储存。
第二S:整顿(Seiton)整顿是指对必要的物品进行规划和整理,使其易于取用和管理。
企业应该设计合理的储存方案,确保物品摆放有序,减少找寻时间。
对于常用的物品,要放置在使用频率较高、容易拿取的位置;对于较少使用的物品,可以储存在较远的位置,以提高工作效率。
第三S:清扫(Seiso)清扫是指对工作环境进行定期清洁和维护,保持整洁有序。
企业应制定清扫计划,明确清扫的频率和责任人。
经常清理工作现场的垃圾,保持设备的清洁和正常运行,营造一个舒适、安全的工作环境。
第四S:清洁(Seiketsu)清洁是指对整个工作环境进行标准化管理,确保5S的持续实施和改进。
企业应设立清洁检查标准,定期检查各个工作区域是否符合标准,并进行纠正和改善。
员工应接受相关培训,了解清洁的重要性,并积极参与到清洁工作中。
第五S:纪律(Shitsuke)纪律是指对5S管理制度的执行和维护,确保习惯养成。
企业应建立相关的规章制度,并进行培训和宣传,让员工明白5S管理的意义和好处。
管理层要起到表率作用,自己先遵守,鼓励员工培养良好的工作习惯。
在实施5S管理过程中,企业还需要营造良好的氛围,推行持续改进。
通过定期开展5S活动,可以激发员工的积极性和主动性,提高工作效率和质量。
同时,企业应根据实际情况,合理分配资源,为5S管理提供必要的支持和保障。
总结起来,5S管理细则包括整理、整顿、清扫、清洁和纪律五个方面。
企业在实施5S管理时,要根据实际情况和需求进行细化和适应性调整,确保5S管理的无缝衔接和持续改进,从而提高工作效率、减少浪费,并营造一个良好的工作环境。
车间现场5S管理规定(2篇)
车间现场5S管理规定整理:将车间现场内需要和不需要的东西分类,丢弃或处理不需要的东西,管理需要的东西。
目的:腾出空间,空间活用,防止误用、误送,塑造清爽的工作场所。
内容:1.车间内废品、边角料当天产生当天处理,入库或从现场清除。
2.班组产生的返修品及时返修,在班组内存放不得超过二天,避免与合格品混淆。
3.用户返回的产品应及时处理,如暂时无时间处理,应存放在临时库,不得堆放在生产现场。
4.外来产品包装物及时去除,货品堆放整齐。
工作现场不能堆放过多(带包装)外购产品。
5.合格部件、产品经检查人员确认后及时入库,不得在班组存放超过一天。
6.报废的工夹具、量具、机器设备撤离现场存放到指定的地点。
7.领料不得领取超过二天用量的部件材料,车间内不允许存放不需要的材料、部件。
8.工作垃圾(废包装盒、废包装箱、废塑料袋)及生活垃圾及时清理到卫生间。
9.窗台、设备、工作台、周转箱内个人生活用品(食品、餐饮具、包、化妆品、毛巾、卫生用品、书报、衣物、鞋)清离现场。
对整理之后留在现场的必要的物品分门别类放置,排列整齐。
物品的保管要定点、定容、定量,有效标识,以便用最快的速度取得所需之物。
目的:工作场所一目了然,消除找寻物品的时间内容:1.车间绘制现场《定置图管理图》。
2.车间对各类设备,工装,器具进行分类编号。
3.废品、废料应存放于指定废品区、废料区地点。
4.不合格品、待检品、返修品要与合格品区分开,周转箱内有清晰明显标识。
____周转箱应放在货架上或周转车上,设备上不得放置周转箱、零件。
6.操作者所加工的零部件、半成品及成品的容器内,必须有明显的标识(交检单,转序卡),注明品名,数量,操作者,生产日期。
7.搬运周转工具(吊车、拖车、升降车、周转车)应存放于指定地点,不得占用通道。
8.工具(钳子、螺丝刀、电烙铁、通路仪)、工位器具(周转箱、周转车、零件盒)、抹布、拖布、包装盒、酒精等使用后要及时放回到原位。
9.部件、材料、工装、工位器具按使用频率和重量体积安排摆放,使物品使用和存放方便,提高工作效率。
5s管理细则
5s管理细则一、引言在现代企业管理中,提高工作效率和员工满意度一直是追求的目标。
为了达到这一目标,许多企业采用了5S管理法。
本文将介绍5S管理细则,详细说明了5S管理的五个步骤,即整理(Seiri)、整顿(Seiton)、清扫(Seiso)、清洁(Seiketsu)和素养(Shitsuke),以及实施5S管理的好处。
二、整理(Seiri)整理是5S管理的第一步,它的目的是根据工作需求对工作场所进行整理和分类,去除无用物品。
具体的操作步骤如下:1. 对工作区域进行彻底的清理,移除寻找工具和材料所需的障碍物。
2. 识别并标记不再需要的物品,包括无用的文件、工具和设备。
3. 整理并妥善存放所需的物品,确保工作区域干净整洁。
三、整顿(Seiton)整顿是5S管理的第二步,其目的是确保所有物品和设备都能迅速找到并放置在正确的位置。
以下是实施整顿的关键步骤:1. 对工作区域进行重新布局,将频繁使用的物品放置在最容易访问的位置。
2. 根据物品的大小、形状和用途,为其分配合适的储存空间或容器。
3. 标记每个物品的储存位置,使用标识牌或颜色编码方便查找。
四、清扫(Seiso)清扫是5S管理的第三步,它的目的是保持工作环境的整洁和卫生。
以下是清扫步骤的详细说明:1. 制定清扫计划,确保定期的清洁工作能够进行。
2. 清理工作区域的灰尘、垃圾和杂物,并将其妥善处理。
3. 定期检查设备和工具的状况,确保其良好的维护和保养。
五、清洁(Seiketsu)清洁是5S管理的第四步,它的目的是建立持续的清洁习惯和标准。
以下是实施清洁的关键步骤:1. 建立清洁标准和程序,并对其进行培训和宣传。
2. 建立清洁检查程序,定期检查工作区域的清洁情况。
3. 持续改进清洁标准,确保其符合实际需求。
六、素养(Shitsuke)素养是5S管理的最后一步,它的目的是培养员工良好的工作习惯和积极的懂得自我管理。
以下是实施素养的关键步骤:1. 提供培训和教育,以增强员工的工作技能和意识。
5s管理细则
5s管理细则在现代企业管理中,5S管理被广泛使用,以提高工作场所的效率和安全性。
本文将介绍5S管理的细则和实施步骤,以帮助企业正确实施和应用5S管理,提升生产效率。
一、整理 (Sort)整理是指将工作场所的物品按照需要与不需要进行分类,将不需要的物品放到合适的位置或处理掉。
这样可以减少杂乱和浪费,提高工作效率。
1.分类:将工作场所的物品进行分类,如工具、文件、原材料等。
2.标识:使用标识牌或标签标识每个物品的位置和用途,方便日后使用和维护。
3.处理掉不需要的物品:将不需要的物品,如过期的文件、破损的工具等,进行清理或报废处理。
二、整顿 (Set in Order)整顿是指将整理后的物品有序地摆放在工作区域内,使工作区域变得整洁有序,提高工作效率。
1.确定合适的物品摆放位置:根据工作流程和频率来确定每个物品的最佳摆放位置。
2.标识工具:使用工具槽、钩子、标签等来摆放和标识工具,确保每个工具都有固定的归位位置。
3.使用标识牌:在工作区域内张贴标识牌,指示每个工作区域的用途和要求。
三、清扫 (Shine)清扫是指定期清洁工作场所,以保持整洁和提高工作环境的安全性。
1.制定清扫计划:制定每天、每周或每月的清扫计划,在固定的时间清洁工作区域。
2.清理垃圾和杂物:及时清理工作区域的垃圾和杂物,保持工作区域的整洁。
3.保养设备和工具:定期检查和保养设备和工具,确保其正常运行。
四、标准化 (Standardize)标准化是指制定工作标准和规范,确保工作流程的一致性和稳定性,提高工作效率和质量。
1.制定工作标准:明确每项工作的步骤、要求和质量标准,并制定操作指南。
2.培训员工:通过培训和沟通,确保员工理解和遵守工作标准。
3.定期评估和改进:定期评估工作标准的有效性,并根据实际情况进行改进和调整。
五、自律 (Sustain)自律是指持续保持5S管理的效果,形成一种良好的工作习惯和氛围,实现持续改进和提高。
1.培养责任感:提高员工的责任心和参与度,使他们主动关注和遵守5S管理的要求。
10现场5S管理细则1.doc
10现场5S管理细则1 现场5S管理规定实施日期:2014-12-10页码:第5页共5页序号作业现场监控的部位要求备注1 设备设备标识1、设备名称;2、设备周期维护日期;3、维护保养人;4、设备状态标识:每年更新、动态管理。
设备外观1.无油污、无残损部件、无采用铁线临时捆绑设备部件。
设备接线1.电线电缆无破损裸露、防护套完好;多条电线电缆捆扎成束(用线夹)。
设备开关1.脚踏开关要有防护装置,手动开关灵敏安全,自制非标设备的电器装置要符合安全管理要求:没有裸露的电线,电器开关做好防护。
设备照明1.照明灯合适亮度、机台灯具完好、照明灯高度安全合适。
机台1.生产时台面上不得堆放过多的工件妨碍操作,2.生产结束后机台不得残留散件、料片、料豆。
2 模具存放1.模具上架存放:按照供线车型、模具规格分区存放。
状态1.模具上有标识牌、模具架上有模具存放位置示意标识。
1.模具架或储存区域要有明显的状态标识:完好模具、待修模具、封存模具。
1.模具表面清洁无油污、存放区洁净无油污;有随模末件(冲压件)、末件合格签集中存放。
1.去送模具必须填写模具存、取记录(领取人签字、每月设备工装员确认)。
3 工装周转箱/器具1.漆面统一同类产品使用同一规格、无破损、防护物完好、空箱内不得有杂物。
指定位置存放1.周转箱右上角放置标识卡、器具统一位置放置标识。
现场5S管理规定实施日期:2014-12-10页码:第5页共5页4 加工作业区每个工位1、设备四周不得有非本班次加工的成品、半成品、料片;2、每个工位只允许一个待加工件周转箱或器具和放置已加工件周转箱或器具;3、各作业区不得有杂物。
5 材料暂存区钢板料条1、区域标识;2、堆高要求;3、材料标识卡;4、木方垫起规范放置在加工区或暂存区内。
物料、周转箱与通道成水平或垂直摆放。
截断钢丝1、区域标识2、材料架架摆放3、材料标识卡4、规范存放在暂存区或加工区内。
零件、小件1、标准件每个规格要有专用盛具并唯一标识;2、规格相近形状相似件的盛具要隔开摆放;3、焊接用的小件专用盛具存放。
- 1、下载文档前请自行甄别文档内容的完整性,平台不提供额外的编辑、内容补充、找答案等附加服务。
- 2、"仅部分预览"的文档,不可在线预览部分如存在完整性等问题,可反馈申请退款(可完整预览的文档不适用该条件!)。
- 3、如文档侵犯您的权益,请联系客服反馈,我们会尽快为您处理(人工客服工作时间:9:00-18:30)。
现场5S管理制度
1.目的与适应范围
加强公司的规范化管理,调动全员参与现场管理的积极性,提高产品质量,提升企业形象。
本制度适用于内蒙古泰弘生态环境发展股份有限公司·生产部
2.名词定义
“5S”定义:整理(Seiri)、整顿(Seiton)、清扫(Seisou)、清洁(Seiketsu)、素养(Shitsuke)
3.管理职责
3.1 综合办管理职责
3.1.1本制度由综合办归口管理。
综合办责编写制度;
3.1.2综合办负责统筹“5S”管理工作的组织、监督和评价制度的实施。
每月根据检查结果评出现场优秀班组和待改善班组并实施激励。
3.1.3综合办负责对现场考核进行兑现。
3.3各部门管理职责:
3.3.1负责对本部门的现场管理进行总策划、标准宣贯、自查、问题整改;
3.3.2负责配合检查和执行本制度,使生产现场及办公现场符合5S标准;
3.3.3相关部门责任人按规定参加联检并提报结果;
5.1现场管理“5S”标准
5.1.1
要的。
即区分需要与否,留下必要其它都清除;
办公区5S实施标准:
1)办公桌上的物品时时刻刻摆放整齐,下班时必须清理,保证桌面上只有电脑和相关设备。
2)。
3),同类物品不得分散放置。
4)
生产部门5S实施标准
1)原物料、成品、半成品、余料、垃圾等定时清理,区分“要”与“不要”的。
5.1.2
便取放的位置,加以标识;
办公区5S实施标准:
1)
2)
3
生产部门5S实施标准:
1)。
2)。
3)
4)。
5)不合格品、破损品及使用频度低的物品,须划出位置并作明显标示。
5.1.3生产现场始终处于无垃圾、无灰尘的整洁状态;
办公区5S实施标准:
1)。
2)屑、线头、布片。
3)。
4)。
5)。
6)窗帘、窗玻璃保持干净,悬挂整齐。
生产部门5S实施标准:
1),每个物品、区域都必须明确责任人。
2)。
3)。
4)下班前确实打扫、清理工作场所。
5.1.4
括个人清洁和环境清洁,其根本是杜绝污染源;
办公区5S实施标准:
1),时刻保持清洁。
2)
3)不得有污迹。
4)办公桌、隔断、办公椅不得有污渍。
生产部门5S实施标准:
1)。
2)维持整理、整顿、清扫的结果。
3)
5.1.5
办公区5S实施标准:
1),不穿拖鞋上班,上班准时,不迟到早退。
2)工作时间内不得无故离岗、串岗,不得闲聊、吃零食、大声喧哗,确保办公环境的安静有序。
3),语气温和,音量适中,不得大声喧哗。
4)每天的工作时间开始前和工作时间结束后做好个人工作区内的卫生保洁工作,保持物品整齐、桌面清洁。
生产部门5S实施标准
1),不迟到、不早退、不旷工。
2),上班时间不聊天、说笑、离岗、看小说、打磕睡、吃东西。
3)归位放置,不乱用别人的工具。
4)。
5)。
6检查程序与要求
6.4.1 车间班组级检查:站长和班组长每天、时时对现场进行检查,针对检查发现的问题,即时作出处理,督导员工自律,纠正员工的不良习惯;
6.4.2公司/厂级检查:
1)厂级检查每周1次,由综合办组织,检查时间周一至周六不定期检查;
6.4.3各部门联检检:
1)各部门联检每月1次,检查时间每月月底;
2)综合办准备“检查表”、确定检查组人员名单,并通知检查人员本次检查时间、集合地点;
3)检查组对受检查的部门、场所实施检查,并作好检查记录。
6.5整改管理要求。