deform挤压模拟课程设计
基于DEFORM的挤压模具模块化分析系统开发
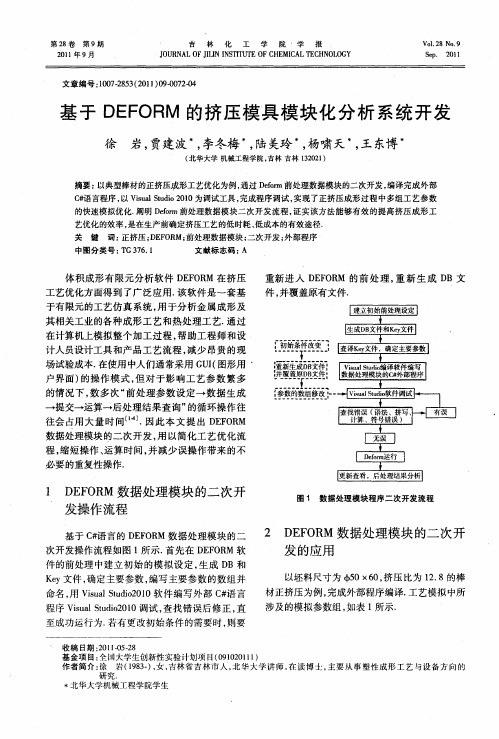
n m s= { ”et s n .D ae xr i 1 B”, x uin . uo ”et s 2 r o
DB”. xr s n . B”, xr so 4 DB”, x r — “e tu i 3 D o ”e tu in . ”e t u
s n . B ”x ui 6 D ” } i 5 D ”.et s n . B ; o r o
计人 员设计 工具 和产 品 工 艺 流程 , 少 昂贵 的现 减
重 新 进 入 D F R 的 前 处 理 , 新 生 成 D 文 EO M 重 B 件, 并覆 盖原 有文 件.
建 立初 始前 处理 没定
I 生成D 文件 ̄Ky B ' e文件1 l l
—— ——— ‘ ‘—— —— 一
第9 期
徐 岩 , 基于 D F R 等: E O M的挤压模具模块化分析系统开发
7 3
表 1 正挤压主要工艺参数表
srn a ti g n me; i ti n ;
fr( = ; o i O i< 6 i ; ++)
{
nm = a e[] a e nm si ; ga e nm si ; nm ga e[] M V T = o [] O C L m vi; F C A f [] R F C=r i ; c
ag) rs {
srn r Di t g wo k r=@ ”D: e tu in i \ xr so 2”;
srng t i
s . iLn(tn.om t”{ \ 8 D ” w Wreie s gFra( 0 B . B , t i r t
w rDr ) o i ; k ) S . i Ln ( -” ; W Wre ie ”1 ) t
deform模拟软件的实例操作与详细介绍

实验一:挤压变形过程数值模拟题目:工艺参数•锻造速度:5mm/s•摩擦系数:剪切摩擦,0.2材料:AL-5083要求•独立完成模拟过程分析,写出详细的分析报告•给出盘形件的等效应力、等效应变及流线分布图•给出载荷曲线答:(1)一、以UG软件作出锻件的三维实体图如图所示,算得其体积V=7086.4369mm3。
从而选择的毛坯为:Φ=25mm,H=15m进行锻造。
二、用CAD软件画出1/2的毛坯、上模、下模平面图,如下图所示:毛坯上模下模(2):建模过程:将单位定义为公制。
坯料的参数设计,首先定义坯料对坯料进行网格划分:(600个网格)定义材料为AL-5083:定义坯料的边界条件:上模的参数设计:上模定义为刚体下压速度为5mm/s:定义下模,刚体材料调整上模、坯料和下模的位置:定义摩擦系数为0.2:定义步长为0.0158mm/s:对模型进行检查、保存,然后进行计算:(3)后处理结果分析:锻件模拟结果如下,可以看到模腔填充完整,但产生少量飞边。
一、等效应力分析:从应力图可以看到红色区域内承受较大的应力。
二、等效应变:分析:从应变图可以看出在坯料的圆角附近区域,其应变值较大。
三、速度场矢量图:分析:从流线图可以看出,坯料向上下两凹腔和分型面出流动。
四、载荷——行程图:分析:从图中可以看出,开始时随着上模的下行载荷缓慢增加,当坯料圆柱外表面与上下模接触后,载荷随着上模的下行急剧增加,当坯料充满模腔时,载荷达到最大值。
五:流线图:分析:从图中可以看出在坯料中部流线变形很小,随着半径的增大流线越往外弓曲。
实验二:非等温问题数值模拟问题:用实验一的模型对坯料,上下模在锻后温度进行模拟。
其中坯料材料选择AlMgMn ,温度选择3000C ,模具材料选择D5-1U ,温度为1000C 。
(1)具体建模过程如实验一所示,主要区别是对模具的网格划分和坯料与模具、模具与环境、坯料与环境的热交换。
上下模网格划分都是200格,热交换定义如下图:坯料与模具热交换定义:对建立的模型进行检查、保存并计算:(2)后处理:模拟结果如下图所示:有图可以看出,锻件充型完好。
deform教程实用教案(2024)

利用deform软件自带的几何建模 工具,如线、面、体等基本元素 进行组合和编辑,构建出所需的 几何模型。
2024/1/30
导入外部模型
支持从CAD软件(如SolidWorks 、AutoCAD等)中导入已经建好 的几何模型,方便快捷。
布尔运算
通过布尔运算(并、交、差)对几 何模型进行组合和修改,以满足复 杂的建模需求。
deform教程实用教案
2024/1/30
1
目录
2024/1/30
• 课程介绍与目标 • 基础知识与操作 • 建模与网格划分 • 材料属性与边界条件设置 • 模拟计算与结果分析 • 案例实战与经验分享
2
01
课程介绍与目标
Chapter
2024/1/30
3
deform软件概述
deform软件是一款专业的有限元分析软件,广泛应用于 金属成形、热处理、焊接等领域的数值模拟。
2024/1/30
23
金属成形过程模拟案例
金属成形是制造业中常见的工艺之一,通过DEFORM 软件可以对金属成形过程进行精确的模拟,预测可能
出现的缺陷和优化工艺参数。
输入 模标拟步题骤
建立几何模型、定义材料属性、设置边界条件和加载 方式、划分网格、运行模拟并分析结果。
案例介绍
案例分析
展示模拟结果,包括成形过程中的应力、应变、温度 分布等,以及最终产品的形状、尺寸精度和表面质量
02
材料属性定义方法
在deform软件的材料库中选择合适的材料模型,输入相应的属性值;
或者通过导入外部材料数据库的方式,将材料属性导入到deform中。
03
注意事项
确保材料属性的准确性和合理性,避免对模拟结果产生不良影响。
基于DEFORM的冲压模具设计的仿真与分析

基于 DEFORM的冲压模具设计的仿真与分析摘要:本文利用DEFORM软件对车间出现不合格品较多的拉深件—碗状加强筋进行数值模拟分析,对金属塑性成形过程进行实时点跟踪描述,并演示整个成形过程,揭示金属流动规律、各种因素对变形行为的影响及成形过程中零件的应力、应变分布,从而获得金属成型过程中的速度场、应力场、应变场、负载场结果。
关键词: DEFORM,拉深件,模具设计1引言公司真空灭弧室产品中有60%的零件属于拉深件。
在生产中,一些拉深件的质量问题,如拉裂、裂纹、拉伤、起皱、椭圆、堆边等问题一直困扰着大家,碗状加强筋是构成真空灭弧室的关键零件之一,用量大,质量要求严,对它的拉深质量问题原因和解决方法都是凭经验,没有理论研究和系统的分析,使得在模具设计上存在一定的弊端,影响质量和生产。
1.碗状加强筋工艺分析碗状加强筋如图1所示,材料是06Cr19Ni10,料厚为2mm,批量生产。
为提高生产效率和节约成本,可选用普通的冲压机床(J23-80),经研究分析,确定零件的加工方法采用板料拉深完成零件成型,工艺路线:备料—落料—拉深成型—车达图—检验,入库。
图1 碗状加强筋设计图1.基于DEFORM的碗状加强筋成形仿真模拟DEFORM技术是一套基于有限元分析的仿真系统,可用来分析金属成形规律与金属工业的热处理和成形工艺。
通过计算机模拟仿真整个成形加工过程,帮助工程设计人员设计产品和工艺流程,降低现场试验成本,用以提高模具的设计速度,以此缩短产品的研发周期。
成形过程仿真系统的建立,是将刚塑性成形工艺学、弹塑性有限元理论、拟处理器和后处理三大模块组成。
有限元分析流程如图2。
图 2 DEFORM成形问题有限元分析流程3.1 模型导入与网格划分在碗状加强筋成形过程中的工作部件为凸模和凹模,故仿真模拟中只导入毛坯、凸模和凹模,模型导入见图3。
绝对网格划分方式在网格尺寸总数设定后永不会变,它会增加模拟的正确性,故采用绝对网格划分方式。
deform挤压模拟课程设计

系 别: 机械工程学院ຫໍສະໝຸດ 专业班级 : 11 级材控 1 班
指导教师 : 张 金 标
组 别:
第五组
2014 年 6 月
铜陵学院机械工程学院课程设计
第一章 课程设计内容及任务分配...............................................................................................................- 1 1.1 概述...........................................................................................................................................................- 1 1.2 设计目的...................................................................................................................................................- 1 1.3 设计内容...................................................................................................................................................- 1 1.4 设计要求...................................................................................................................................................- 1 1.5 挤压方案任务分配...................................................................................................................................- 2 第二章 工艺参数...........................................................................................................................................- 3 2.1 工艺参数的设计.......................................................................................................................................- 3 2.1.1 摩擦系数的确定.....................................................................................................................................- 3 2.1.2 挤压速度的确定.....................................................................................................................................- 3 2.1.3 工模具预热温度的确定.........................................................................................................................- 3 第三章 模具尺寸的确定...............................................................................................................................- 4 3.1 挤压工模具示意图...................................................................................................................................- 4 3.2 模具尺寸的确定.......................................................................................................................................- 4 3.2.1 挤压模结构尺寸的确定..........................................................................................................................- 4 3.2.2 挤压筒结构尺寸的确定.......................................................................................................................- 6 3.2.3 挤压垫的结构及尺寸确定.....................................................................................................................- 7 第四章 实验模拟及数据提取分析.............................................................................................................- 8 4.1 挤压工模具及工件的三维造型................................................................................................................- 8 4.2 挤压模拟...................................................................................................................................................- 8 4.3 后处理.......................................................................................................................................................- 9 4.4 分析数据....................................................................................................................................................- 9 4.5 坯料温度对挤压力的影响.....................................................................................................................- 10 4.6 坯料预热温度对破坏系数的影响.........................................................................................................- 11 个人小结.........................................................................................................................................................- 12 参考文献..........................................................................................................................................................- 21附表 《塑性成型计算机模拟》课程设计成绩评定表
DEFORM课程设计
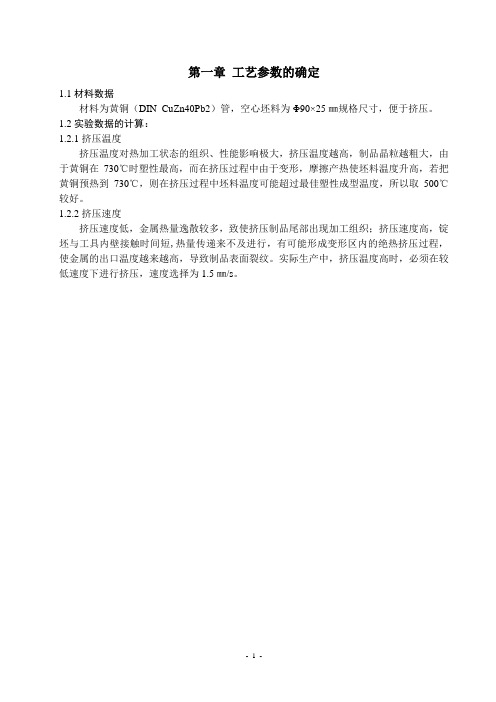
第一章工艺参数的确定1.1材料数据材料为黄铜(DIN_CuZn40Pb2)管,空心坯料为Φ90×25㎜规格尺寸,便于挤压。
1.2实验数据的计算:1.2.1挤压温度挤压温度对热加工状态的组织、性能影响极大,挤压温度越高,制品晶粒越粗大,由于黄铜在730℃时塑性最高,而在挤压过程中由于变形,摩擦产热使坯料温度升高,若把黄铜预热到730℃,则在挤压过程中坯料温度可能超过最佳塑性成型温度,所以取500℃较好。
1.2.2挤压速度挤压速度低,金属热量逸散较多,致使挤压制品尾部出现加工组织;挤压速度高,锭坯与工具内壁接触时间短,热量传递来不及进行,有可能形成变形区内的绝热挤压过程,使金属的出口温度越来越高,导致制品表面裂纹。
实际生产中,挤压温度高时,必须在较低速度下进行挤压,速度选择为1.5㎜/s。
第二章 工模具尺寸的设计2.1 模子的设计2.1.1 模角α锥模的模角在45°~60°,在此范围内的模挤压力最小。
此设计使用模角为60°。
2.1.2 工作带长度h g 和直径d g工作带又称定径带,其用以保证制品尺寸和表面质量。
挤压黄铜时工作带长度一般为8~12mm ,此设计选用工作带长度为h g =10mm 。
模子工作带直径与实际所挤压的制品直径并不相等。
挤压管材时的模孔直径为:d g =(1+k )d 0式中d 0——管材的名义直径;k ——裕量系数,对黄铜而言,裕量系数k=1%~1.2%。
则工作带直径为:d g =66×(1+1%~1.2%)mm=(66.66~67.32)mm对此设计选用工作带直径d g =67mm 。
2.1.3 出口直径D ch模子的出口直径一般应比工作带直径大5mm 左右,此设计出口直径D ch =77mm 。
2.1.4 模具直径D 和厚度H模子的外圆直径D 和厚度主要取决于其强度和标准化系列来考虑的。
根据经验,对管材,模子的外圆直径D=(1.25~1.45)D p ,故模子的外圆直径选择D=100mm 。
(完整word版)DEFORM-2D有限元模拟正反挤压
学生学号123456 实验课成绩武汉理工大学学生实验报告书实验课程名称材料成型CAE综合实验开课学院材料学院指导老师姓名学生姓名学生专业班级成型0802班2011 —2012 学年第一学期实验课程名称:材料CAE综合实验实验项目名称DEFORM-2D软件的操作与实例演练实验成绩实验者专业班级成型0802 组别同组者实验日期年月日第一部分:实验分析与设计(可加页)一、实验内容描述(问题域描述)1.了解认识DEFORM-2D软件的窗口界面。
2.了解DEFORM-2D界面中各功能键的作用。
3.掌握利用DEFORM-2D有限元建模的基本步骤。
4.学会进入前处理、后处理操作。
5.学会对DEFORM-2D模拟得出的图像进行数值分析,得出结论二、实验基本原理与设计(包括实验方案设计,实验手段的确定,试验步骤等,用硬件逻辑或者算法描述)DEFORM是一套基于有限元的工艺仿真系统,用于分析金属成形及其相关工业的各种成形工艺和热处理工艺。
通过在计算机上模拟整个加工过程,帮助工程师和设计人员:设计工具和产品工艺流程,减少昂贵的现场试验成本。
提高工模具设计效率,降低生产和材料成本。
缩短新产品的研究开发周期。
DEFORM-2D适用于各种常见的UNIX工作站平台(HP,SGI,SUN,DEC,IBM)和Windows-NT微机平台。
可以分析平面应变和轴对称等二维模型。
它包含了最新的有限元分析技术,既适用于生产设计,又方便科学研究。
三、主要仪器设备及耗材1.计算机2.DEFORM-2D软件第二部分:实验调试与结果分析(可加页)一、调试过程(包括调试方法描述、实验数据记录,实验现象记录,实验过程发现的问题等)DEFORM-2D软件操作流程:一、前处理1. 创建新的问题打开DEFORM-2D软件,单击,“New Problem”,设置好存储路径,文件名改为英文。
2.设置模拟控制单击,打开Simulation Control窗口,设置单位为SI,如图,其他默认不变。
基于DEFORM的汽车轮毂轴管热挤压过程的数值模拟
FORGING2008年第2期1前言轮毂轴管(图1)是汽车后桥上一个重要的保安件,要承受各种复杂的交变应力与疲劳载荷[1]。
因此,其工作环境的特殊性决定了其较高的质量要求和挤压工艺参数的精确化。
传统挤压工艺的制定主要是建立在经验基础上,采用试错法不断调整工艺参数和修改模具,不仅研发周期长,而且挤压件的质量难以保证。
随着数值模拟技术的发展,可以采用计算机对金属成形过程进行分析,掌握变形过程中各种场量的变化情况。
并可对变形过程中工件内部缺陷等进行预测,对挤压工艺的制定具有重要的参考价值。
本文利用有限元软件DEFORM对轴管坯料的挤压过程进行了数值模拟。
并对挤压后工件的损伤、应力场、应变场及其分布的原因进行了分析,为制定生产工艺提供了参考[2]。
2建模及模拟条件应用DEFORM软件对汽车轮毂轴管热挤压过程的数值模拟,首先需建立有限元分析模型,如图2所示。
模型初始条件为:①设定上下模为刚性模型,工件为弹性模型;TheNumericalSimulationofLargeCylinderForginginForgingProcessunderHighTemperatureXUFeixia,CUIZhenshan,CHENWen,FUQiang(Dept.ofPlasticityFormingEng.,ShanghaiJiaoTongUniv.,Shanghai200030,China)Abstract:Thistextisbasedonthetraditionalshellforgingtechnologyforlargescalecylinderathightempera-ture.Therelationshipsbetweenanvil'smovementandtherotationofthesustainingcolumninhigh-temperatureforg-ingprocessoflargecylinderforgings,anditsinfluenceonforgingsdimensionhavebeenresearchedbyfiniteelementsimulation.Besides,itraisesamoreaccuratemethodforjudgingforging'sprecisionbycomparingthesimulationre-sultswiththeforgingin3Dsoftware.Keywords:ForgingP Large-scalecylinderP NumericalsimulationP Quality!98!60+10!70!88!152!6519590380625015图1轮毂轴管零件图收稿日期:2008-01-17作者简介:温志高(1967-)男,硕士,高级工程师,从事热挤压工艺技术研究文章编号:1672-0121(2008)02-0058-03基于DEFORM的汽车轮毂轴管热挤压过程的数值模拟温志高(河南英威东风机械有限公司,河南南阳474674)摘要:本文建立了汽车轮毂轴管的有限元分析模型,利用DEFORM软件模拟了工件热挤压过程,并分析了工件的损伤、应力场及应变场的分布情况和原因。
Deform-棒材热挤压过程模拟
铜陵学院课程实验报告实验名称棒材热挤压过程模拟实验课程材料成型计算机模拟指导教师张金标. 专业班级10 材控(2)班. 姓名彭建新. 学号1010121064 .2013年05月23日实验二棒材热挤压过程模拟1实验目的与内容1.1实验目的进一步熟悉DEFORM软件前处理、后处理的操作方法,掌握热力耦合数值模拟的模拟操作。
深入理解并掌握DEFORM软件分析热挤压的塑性变形力学问题。
1.2 实验内容运用DEFORM模拟如图2所示的黄铜(DIN_CuZn40Pb2)棒挤压过程(已知:坯料φ98⨯100mm)图1 棒材挤压示意图(一)挤压条件与参数挤压工具:尺寸如图所示,材质DIN-D5-1U,COLD,温度3500。
坯料:材质DIN_CuZn40Pb2,尺寸φ98×100,温度6300。
工艺参数:挤压速度10mm/s,摩擦系数0.1。
(二)实验要求(1)运用AUTOCAD或PRO/e绘制各模具部件及棒料的三维造型,以stl格式(二)实验要求(1)运用AUTOCAD或PRO/e绘制各模具部件及棒料的三维造型,以stl 格式输出;(2)设计模拟控制参数;(3)DEFORM前处理与运算;(4)DEFORM后处理,观察圆柱体压缩变形过程,载荷曲线图,通过轴对称剖分观察圆柱体内部应力、应变及损伤值分布状态;(5)运用DEFORM后处理Flow Net(流动栅格)功能观察金属流动的不均匀性,说明原因;(6)提交分析报告(纸质和电子版)、模拟数据文件、日志文件。
2 实验过程2.1挤压工模具及工件的三维造型根据给定的几何尺寸,并从书中查得工作带长度为10mm,入口圆角半径为5mm,挤压垫外径为99mm,挤压垫厚度为9mm,运用AUTOCAD或PRO/E分别绘制坯料、挤压模、挤压垫、挤压筒的几何实体,文件名称分别为extrusion workpiece,extrusion die,extrusion dummy block,extrusion chamber。
deform3d课程设计(棒材)
目录第一章模具尺寸及工艺参数的确定 (2)1.1 模具尺寸的确定 (2)1.1.1尺寸选择 (2)1.1.2根据尺寸绘制平面图形 (2)1.1.3绘图 (3)1.2 挤压模拟工艺参数的确定 (3)1.2.1温度的确定 (3)1.2.2速度的确定 (3)第二章Deform模拟过程与模拟分析 (4)2.1 Deform模拟过程 (4)2.1.1建立新问题 (4)2.1.2添加对象 (4)2.1.3模拟控制设置 (4)2.1.4定义对象的材料模型 (4)2.1.5高速对象位置关系 (4)2.1.6网格化划分 (4)2.1.7设置对象材料属性 (4)2.1.8设置主动工具运行速度 (4)2.1.9工件体积补偿 (5)2.1.10边界条件定义 (5)2.1.11生成数据库文件 (5)2.2 Deform模拟结果分析 (5)2.2.1观察温度变化 (6)2.2.2观察应力分布 (7)2.2.3观察应变分布 (8)2.2.4观察金属破坏系数 (9)2.2.5速度分析 (10)2.2.6载荷分析 (11)2.3 分析成品棒尺寸对挤压变形的影响 (12)总结 (13)参考文献 (14)第一章 模具尺寸及工艺参数的确定1.1 模具尺寸的确定选择模具与坯料部分尺寸,并根据给定的主要尺寸,运用Auto CAD 绘出挤压过程平面图形;并设计挤压工艺参数。
1.1.1尺寸选择模角的选择:锥模的模角为30°工作带长度:挤压黄铜时,工作带一般取8~12mm ,考虑到模子的强度取g h =10mm 。
工作带直径:工作带直径与实际所挤出的制品直径并不相等。
按公式m m g d C d d 1+=计算,制品直径为m d =50mm ,裕量系数1C 取0.015,则g d =51mm 。
出口直径:模子的出口直径ch d 一般比工作带直径大3~5mm ,因过小会划伤制品表面,取ch d =56mm 。
过度圆角:工作带与出口的过渡部分:可以做成斜面或以3~5mm 的圆弧连接,以增加工作带厚度,取r=3mm 。
- 1、下载文档前请自行甄别文档内容的完整性,平台不提供额外的编辑、内容补充、找答案等附加服务。
- 2、"仅部分预览"的文档,不可在线预览部分如存在完整性等问题,可反馈申请退款(可完整预览的文档不适用该条件!)。
- 3、如文档侵犯您的权益,请联系客服反馈,我们会尽快为您处理(人工客服工作时间:9:00-18:30)。
课题: 材料成型计算机模拟系别: 机械工程学院专业班级: 11级材控1班指导教师: 张金标组别: 第五组2014年6月第一章课程设计内容及任务分配.............................................................................................................. - 1 - 1.1 概述.......................................................................................................................................................... - 1 - 1.2 设计目的.................................................................................................................................................. - 1 - 1.3 设计内容.................................................................................................................................................. - 1 - 1.4 设计要求.................................................................................................................................................. - 1 - 1.5 挤压方案任务分配.................................................................................................................................. - 2 - 第二章工艺参数.......................................................................................................................................... - 3 - 2.1 工艺参数的设计...................................................................................................................................... - 3 - 2.1.1 摩擦系数的确定.................................................................................................................................... - 3 - 2.1.2 挤压速度的确定.................................................................................................................................... - 3 - 2.1.3 工模具预热温度的确定........................................................................................................................ - 3 - 第三章模具尺寸的确定.............................................................................................................................. - 4 - 3.1 挤压工模具示意图.................................................................................................................................. - 4 - 3.2 模具尺寸的确定...................................................................................................................................... - 4 - 3.2.1挤压模结构尺寸的确定......................................................................................................................... - 4 - 3.2.2 挤压筒结构尺寸的确定...................................................................................................................... - 6 - 3.2.3 挤压垫的结构及尺寸确定.................................................................................................................... - 7 - 第四章实验模拟及数据提取分析............................................................................................................ - 8 - 4.1挤压工模具及工件的三维造型............................................................................................................... - 8 - 4.2 挤压模拟.................................................................................................................................................. - 8 - 4.3 后处理...................................................................................................................................................... - 9 - 4.4分析数据................................................................................................................................................... - 9 - 4.5 坯料温度对挤压力的影响.................................................................................................................... - 10 - 4.6 坯料预热温度对破坏系数的影响........................................................................................................ - 11 - 个人小结........................................................................................................................................................ - 12 - 参考文献........................................................................................................................................................ - 21 - 附表《塑性成型计算机模拟》课程设计成绩评定表第一章课程设计内容及任务分配1.1 概述挤压是对放在容器(挤压筒)内的金属坯料施加外力,使之从特定的模孔中流出,获得所需要断面形状和尺寸的一种塑性加工方法,有正挤压、反挤压、组合挤压、连续挤压、静液挤压等多种形式。
挤压成形能充分发挥金属塑性,获得大变形量,实现由坯料到成品的一次成型。
挤压变形能显著改善金属材料的组织,提高制品的力学性能、尺寸精度和表面质量。
因此,挤压是金属材料加工的一种应用广泛的成形方法,适用于薄壁、细长的管、线、型材的生产,特别是断面复杂的异型材的加工生产。
但是,挤压变形也存在制品组织与性能不均、工模具磨损快和设备负荷高等缺点。
挤压制品的组织性能、表面质量、尺寸及形状精度、工模具损耗以及能量消耗都与坯料、挤压工艺、工模具结构尺寸和形状等因素相关。
因此,挤压工艺与工模具的设计合理与否是挤压成形的关键。
本设计以 140mm棒材(黄铜DIN_CuZn40Pb2)挤压成形为例,研究挤压变形工艺参数、模具结构形状与尺寸对金属流动、变形力等参数的影响,通过DEFORM软件模拟分析参数的合理性。