PCB板制造工艺流程大纲纲要大纲.doc
PCB制造流程及说明(DOC 103)

PCB制造流程及说明一.PCB演变1.1PCB扮演的角色PCB的功能为提供完成第一层级构装的组件与其它必须的电子电路零件接合的基地,以组成一个具特定功能的模块或成品。
所以PCB在整个电子产品中,扮演了整合连结总其成所有功能的角色,也因此时常电子产品功能故障时,最先被质疑往往就是PCB。
图1.1是电子构装层级区分示意。
1.2PCB的演变1.早于1903年Mr. Albert Hanson首创利用"线路"(Circuit)观念应用于电话交换机系统。
它是用金属箔予以切割成线路导体,将之黏着于石蜡纸上,上面同样贴上一层石蜡纸,成了现今PCB的机构雏型。
见图1.22. 至1936年,Dr Paul Eisner真正发明了PCB的制作技术,也发表多项专利。
而今日之print-etch(photo image transfer)的技术,就是沿袭其发明而来的。
1.3 PCB种类及制法在材料、层次、制程上的多样化以适合不同的电子产品及其特殊需求。
以下就归纳一些通用的区别办法,来简单介绍PCB的分类以及它的制造方法。
1.3.1PCB种类A.以材质分a. 有机材质酚醛树脂、玻璃纤维/环氧树脂、Polyamide、BT/Epoxy等皆属之。
b. 无机材质铝、Copper Inver-copper、ceramic等皆属之。
主要取其散热功能B.以成品软硬区分a.硬板RigidPCBb.软板FlexiblePCB见图1.3c.软硬板Rigid-FlexPCB见图1.4C.以结构分a.单面板见图1.5b.双面板见图1.6c.多层板见图1.7D. 依用途分:通信/耗用性电子/军用/计算机/半导体/电测板…,见图1.8 B GA.另有一种射出成型的立体PCB,因使用少,不在此介绍。
1.3.2制造方法介绍A. 减除法,其流程见图1.9B. 加成法,又可分半加成与全加成法,见图1.101.11C. 尚有其它因应IC封装的变革延伸而出的一些先进制程,本光盘仅提及但不详加介绍,因有许多尚属机密也不易取得,或者成熟度尚不够。
PCB板生产工艺流程

PCB板生产工艺流程PCB板(Printed Circuit Board,印刷电路板)是在绝缘基板上印刷导电线路的一种电子组件。
它是电子元器件的重要载体,广泛应用于电子产品中。
下面是一个典型的PCB板生产工艺流程。
1.前期准备阶段:在正式开始PCB板的生产之前,需要进行一系列的准备工作。
首先,根据客户的要求和电路设计图纸进行审查,确定PCB板的制造工艺和技术要求。
然后,准备所需的原材料,包括基板、导电层、电解液、化学药液等。
最后,准备生产设备和工艺流程图。
2.基板预处理:首先,在基板表面涂覆一层光敏胶,然后将胶层曝光并显影,形成光敏图形。
接下来,在光敏图形上涂覆一层导电层,通常使用铜材质。
然后,将基板放入化学药液中进行浸蚀处理,以去除未被覆盖的铜层。
最后,用水冲洗基板,去除化学药液的残留物。
3.图形形成:使用光刻技术在基板的导电层上形成电路图形。
首先,在导电层上涂覆一层光阻胶,然后将胶层曝光并显影,形成光阻图形。
接下来,将基板放入化学药液中进行浸蚀处理,去除未被光阻保护的铜层。
最后,用水冲洗基板,去除化学药液的残留物。
4.铜层沉积:为了提高导电层的厚度和电导率,需要进行铜层沉积。
这一步骤通常采用化学镀铜的方法。
将基板放入含有铜离子的电解液中,通过电流的作用,铜离子被还原成铜层。
此时,导电层的厚度大大增加,以满足电路设计要求。
5.电镀涂层:在铜层上涂覆一层保护层,以保护铜层免受腐蚀和损坏。
通常使用有机物质(如有机锡化合物)进行涂层。
涂层之后,将基板放入烘干设备中进行固化。
6.成品检验:对生产完成的PCB板进行严格的检验。
按照客户的要求和标准,检查板面质量,包括导电层的良好连接、图形的完整性和正确性等。
此外,还需要进行各种电性能测试,以确保电路的正常工作。
7.成品包装:需要注意的是,以上的工艺流程仅仅是一个典型的PCB板生产过程,实际生产中可能还会根据具体要求和生产设备的不同而有所变化。
此外,PCB板的生产过程还需要严格控制工艺参数,以确保产品质量和稳定性。
PCB制作工艺流程简介
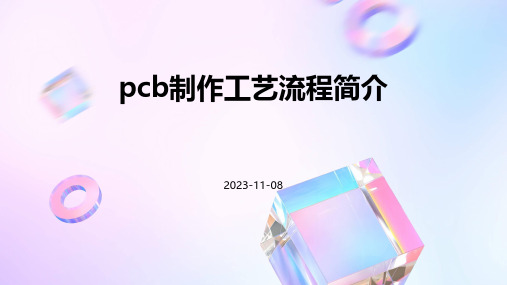
2023-11-08•pcb制作概述•pcb设计•pcb制作的前期准备•pcb制作过程•pcb制作完成后的处理目•pcb制作中的注意事项及常见问题•pcb制作的发展趋势及未来展望录01 pcb制作概述pcb基本概念Printed Circuit BoardPCB是印刷电路板,是一种用于将电子器件连接在一起的基板,通常由绝缘材料制成。
电路板组成PCB通常由导电层、绝缘层和支撑层组成,其中导电层用于传输电信号,绝缘层用于隔离导电层,支撑层则用于支撑整个电路板。
设计电路图制作裸板光绘与刻板将铜箔粘贴在绝缘材料上,形成导电层。
使用光绘机将电路图绘制在铜箔上,形成电路图形。
03pcb制作流程简介02 01根据产品需求,使用EDA设计软件绘制电路图。
通过蚀刻工艺将不需要的铜箔去除,形成所需的电路图形。
蚀刻与去膜在电路导线上沉积一层锡/金,以提高导电性能和耐腐蚀性。
沉锡/金在电路板上涂抹阻焊剂,以防止焊接时短路。
印阻焊剂对电路板进行成型和钻孔加工,以满足实际应用需求。
成型与钻孔pcb制作流程简介实现电子设备的小型化和高效化PCB是实现电子设备内部器件连接的关键部件,其制作质量直接影响到电子设备的性能和可靠性。
pcb制作的重要性保障电子设备的稳定性和安全性PCB的制作质量直接关系到电子设备的稳定性和安全性,因为一旦出现短路或信号干扰等问题,就可能导致设备故障或损坏。
提升电子设备的品质和降低成本优秀的PCB制作工艺可以提高电子设备的品质和性能,同时降低制作成本和时间成本,提高市场竞争力。
02 pcb设计03优化板型结构PCB设计应优化板型结构,提高电路板的机械强度、电气性能和散热性能。
pcb设计基本原则01确保电路功能正常PCB设计应确保电路的功能正常,满足原始电路设计的要求。
02减少信号干扰为了减少信号干扰,PCB设计应尽量选择低噪声的器件,同时避免器件之间的相互干扰。
pcb设计流程PCB检查与优化对设计好的PCB进行检查,确保没有错误和不合理的地方,并进行优化改进。
PCB板制造工艺流程

精心整理PCB 板制造工艺流程PCB 板的分类1、 按层数分:①单面板②双面板③多层板2、 按镀层工艺分:①热风整平板②化学沉金板③全板镀金板④热风整平+金手指3、 ⑤化学沉金+金手指4、 ⑥全板镀金+金手指5、 ⑦沉锡⑧沉银⑨OSP 板各种工艺多层板流程㈠热风整平多层板流程:开料——内层图像转移:(内层磨板、内层贴膜、菲林对位、曝光、显影、蚀刻、褪膜)——AOI ——棕化——层压——钻孔——沉铜——板镀——外层图像转移:(外层磨板、外层贴膜、菲林对位、曝光、显影、图镀、褪膜、蚀刻、褪锡)——丝印阻焊油墨————丝印阻——(外————(外墨——(W ——曝光、显影、蚀刻、褪膜)——AOI ——棕化——层压——钻孔——沉铜——板镀——外层图像转移:(外层磨板、外层贴膜、菲林对位、曝光、显影、图镀、褪膜、蚀刻、褪锡)——化学沉金——丝印字符——外光成像②(交货面积>1平方米)/贴蓝胶带(交货面积≤1平方米)——镀金手指——铣外形——金手指倒角——电测——终检——真空包装㈦单面板流程(热风整平为例):开料——钻孔——外层图像转移:(外层磨板、外层贴膜、菲林对位、曝光、显影、图镀、褪膜、蚀刻、褪锡)——AOI ——丝印阻焊油墨——阻焊图像转移:(菲林对位、曝光、显影)——丝印字符——热风整平——铣外形——电测——终检——真空包装(注:①因没有金属化孔,所以没有电测与沉铜板镀②外层线路菲林除全板镀金板用正片菲林外,其它都用负片)㈧双面板流程(热风整平为例):开料——钻孔——沉铜——板镀——外层图像转移:(外层磨板、外层贴膜、菲林对位、曝光、显影、图镀、褪膜、蚀刻、褪锡)——丝印阻焊油墨——阻焊图像转移:(菲林对位、曝光、显影)——丝印字符——热风整平——铣外形——电测——终检——真空包装(注:因一共两层,所以用电测代替了AOI)㈨OSP多层板流程:开料——内层图像转移:(内层磨板、内层贴膜、菲林对位、曝光、显影、蚀刻、褪膜)——AOI——棕化——层压——钻孔——沉铜——板镀——外层图像转移:(外层磨板、外层贴膜、菲林对位、曝光、显影、图镀、褪膜、蚀刻、褪锡)——丝印阻焊油墨——阻焊图像转移:(菲林对位、曝光、显影)——丝印字符——(二钻)——铣外形——OSP——终检——真空包装多层板流程的步骤、意义、作用、及注意事项,现以热风整平板+金手指为例。
PCB板制造工艺流程
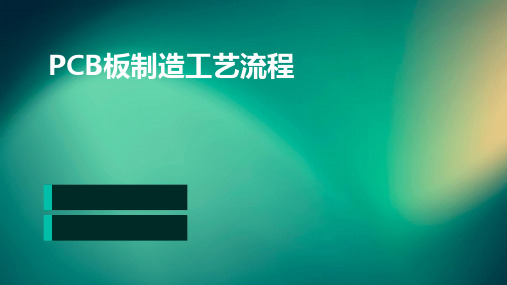
组成
主要由导电线路、绝缘基 材、电子元器件等部分组 成,通过精密的制造工艺 实现电路的布局和连接。
类型
根据不同的应用需求, PCB板有多种类型,如单 面板、双面板、多层板等。
PCB板制造的重要性
实现电路设计
PCB板是实现电子设备电 路设计的重要载体,能够 将电路设计转化为实际产 品。
保障电子设备性能
废弃物回收
建立完善的废弃物回收体系,对PCB 板生产过程中产生的废弃物进行回收 再利用,实现资源的高效利用和可持 续发展。
THANKS FOR WATCHING
感谢您的观看
基材选择
根据电路设计和实际应用需求选择 合适的绝缘基材,如FR4、CEM-1 等。
内层线路制作
在基材上制作导电线路,通过镀铜、 光刻、蚀刻等工艺实现。
外层线路制作
在已制作好的内层线路的基础上, 通过镀铜、光刻、电镀等工艺实现 外层线路的制作。
焊接
将电子元器件通过焊接工艺连接到 PCB板上,完成整个制造过程。
距和布局等要求。
确定其他特殊需求
如阻焊层、丝印层、测试点等 ,以满足生产和使用过程中的
特殊要求。
设计原理图和PCB图
根据设计需求,使用电子设计自 动化(EDA)软件设计原理图和
PCB图。
在原理图中,将电路中的元件和 连接关系进行逻辑设计和仿真。
在PCB图中,将原理图中的元件 和连接关系转换为实际的物理布
PCB板的维护保养
保持清洁
定期清洁PCB板表面,去除灰尘和污 垢,以保持其良好的电气性能。
避免受潮
保持PCB板干燥,避免长时间暴露在 潮湿环境中,以防引起电路故障。
避免机械损伤
在安装和维修过程中,应避免对PCB 板施加过大的机械应力,以防损坏其 线路和元器件。
PCB板制造工艺流程

PCB板制造工艺流程PCB板(Printed Circuit Board),即印刷电路板,是电子元器件的载体,也是电子产品的基础。
PCB板的制造工艺流程主要包括设计、布图、曝光、腐蚀、镀金、钻孔、插件等环节。
下面将详细介绍PCB板制造工艺流程。
一、设计PCB板的设计是制造工艺流程的第一步。
通过设计软件,根据产品的要求和电路原理图进行布置和路径设计,确定元件的位置和走线路径。
二、布图布图是将设计好的电路板的元件进行排列、摆放和连线,制作成实物的原型。
通常使用布图软件进行布图,将电路元件印制到膜材料上,得到电路板的样子。
三、曝光曝光是将布图得到的样子通过曝光机进行曝光,将光线照射到覆盖在样图上的感光材料上,生成一个暗纹路的半导体薄膜。
四、腐蚀腐蚀是将曝光得到的暗纹路加入化学液中,使得暗纹路能够迅速地腐蚀,形成导电的金属线路。
五、镀金镀金是在腐蚀后的PCB板上进行镀金处理,以提高电路板的导电性和防止金属氧化。
常用的镀金方式有电镀、喷涂、热沉积等,其中电镀是最常见的一种。
六、钻孔钻孔是将电路板上需要安装元件的位置钻孔,以便安装插件。
通常使用高速钻孔机进行钻孔处理。
七、插件插件是将元器件插入到钻孔好的电路板上,以完成电路的连接。
插件通常是通过自动插装机进行插入,以提高插件效率和精度。
八、焊接焊接是将插件好的元器件通过焊接方式,将插件与电路板上的金属线路连接在一起。
常用的焊接方式有手工焊接和自动焊接两种。
自动焊接通常使用波峰焊接机进行焊接,手工焊接通常使用电烙铁进行焊接。
上述就是PCB板制造工艺流程的基本步骤。
当然,实际制造过程还会包括蒸汽冲天、除残胶、涂膜、曲线固化、检查、涂脂、切割、温控、检测试验等环节,以确保电路板的质量和可靠性。
每个环节的具体步骤和要求可能会因不同的产品和制造商而有所不同,但整体流程大致如上所述。
PCB板制造工艺是电子产品制造过程中非常重要的环节,它直接影响了电子产品的性能和可靠性。
PCB制板工艺操作手册

PCB制板工艺操作手册第1章基础知识 (3)1.1 PCB概述 (3)1.2 制板工艺流程简介 (4)第2章材料准备 (5)2.1 基材选择 (5)2.2 覆铜板处理 (5)2.3 干膜制备 (6)第3章设计与布线 (6)3.1 PCB设计规范 (6)3.1.1 设计原则 (6)3.1.2 设计要求 (6)3.1.3 设计工具 (7)3.2 布线技巧 (7)3.2.1 布线规则 (7)3.2.2 层叠设计 (7)3.2.3 焊盘和过孔设计 (7)3.3 设计审查 (7)3.3.1 审查内容 (7)3.3.2 审查方法 (8)3.3.3 审查流程 (8)第4章制板前处理 (8)4.1 覆铜板切割 (8)4.1.1 材料准备 (8)4.1.2 切割操作 (8)4.1.3 质量检查 (8)4.2 钻孔与孔金属化 (8)4.2.1 钻孔 (8)4.2.2 孔金属化 (8)4.2.3 质量检查 (8)4.3 黑化处理 (8)4.3.1 材料准备 (9)4.3.2 黑化处理操作 (9)4.3.3 清洗与干燥 (9)第5章光绘与显影 (9)5.1 光绘工艺 (9)5.1.1 设备准备 (9)5.1.2 光绘参数设置 (9)5.1.3 光绘操作步骤 (9)5.1.4 注意事项 (9)5.2 显影工艺 (9)5.2.1 显影设备准备 (9)5.2.3 显影操作步骤 (10)5.2.4 注意事项 (10)5.3 质量检查 (10)5.3.1 检查方法 (10)5.3.2 检查内容 (10)5.3.3 处理措施 (10)第6章化学镀与电镀 (10)6.1 化学镀铜 (10)6.1.1 原理概述 (10)6.1.2 化学镀铜溶液组成 (10)6.1.3 操作步骤 (11)6.1.4 注意事项 (11)6.2 电镀铜 (11)6.2.1 原理概述 (11)6.2.2 电镀铜溶液组成 (11)6.2.3 操作步骤 (11)6.2.4 注意事项 (11)6.3 电镀锡铅 (11)6.3.1 原理概述 (11)6.3.2 电镀锡铅溶液组成 (12)6.3.3 操作步骤 (12)6.3.4 注意事项 (12)第7章蚀刻与去膜 (12)7.1 蚀刻工艺 (12)7.1.1 蚀刻原理 (12)7.1.2 蚀刻前准备 (12)7.1.3 蚀刻操作 (12)7.1.4 蚀刻后处理 (12)7.2 去膜工艺 (13)7.2.1 去膜原理 (13)7.2.2 去膜前准备 (13)7.2.3 去膜操作 (13)7.2.4 去膜后处理 (13)7.3 质量检查 (13)7.3.1 蚀刻质量检查 (13)7.3.2 去膜质量检查 (13)7.3.3 异常处理 (13)第8章表面处理 (13)8.1 热风整平 (13)8.1.1 工艺简介 (14)8.1.2 工艺流程 (14)8.1.3 注意事项 (14)8.2 沉金处理 (14)8.2.2 工艺流程 (14)8.2.3 注意事项 (14)8.3 阻焊油墨印刷 (15)8.3.1 工艺简介 (15)8.3.2 工艺流程 (15)8.3.3 注意事项 (15)第9章焊接与组装 (15)9.1 表面贴装技术 (15)9.1.1 表面贴装概述 (15)9.1.2 焊膏印刷 (15)9.1.3 贴片 (16)9.1.4 回流焊接 (16)9.2 通孔焊接 (16)9.2.1 通孔焊接概述 (16)9.2.2 焊料选择 (16)9.2.3 焊接过程 (16)9.3 检验与返修 (16)9.3.1 检验 (16)9.3.2 返修 (17)第10章质量控制与验收 (17)10.1 制板过程质量控制 (17)10.1.1 制程参数监控 (17)10.1.2 在线检测 (17)10.1.3 抽样检测 (17)10.1.4 工艺优化与改进 (17)10.2 成品验收标准 (17)10.2.1 外观检查 (17)10.2.2 尺寸测量 (17)10.2.3 功能性测试 (17)10.2.4 无铅焊接适应性测试 (18)10.3 故障分析与排除方法 (18)10.3.1 故障分类 (18)10.3.2 故障原因分析 (18)10.3.3 故障排除方法 (18)10.3.4 预防措施 (18)第1章基础知识1.1 PCB概述印刷电路板(Printed Circuit Board,简称PCB)是电子设备中用于支撑和连接电子元件的一种基础组件。
PCB生产工艺流程

PCB生产工艺流程PCB(Printed Circuit Board)是电子产品的重要组成部分,它通过连接电子元器件,实现电路的功能。
PCB的生产工艺流程如下:1. 设计布图:首先,需要根据电路的设计要求,制定PCB的布图。
这一过程通常由专业的电路设计师完成,他们会根据产品的需求设计出符合要求的PCB布局图。
2. 制作底板:底板是PCB的基础材料,通常由玻璃纤维材料和树脂复合而成。
制作底板的过程包括将树脂和玻璃纤维材料预先混合,然后通过压制或注塑成型。
3. 制作铜箔层:在底板上覆盖一层铜箔,然后通过化学蚀刻或机械去除部分铜箔,形成需要的电路图案。
4. 激光孔洞定位:通过激光机器进行孔洞的定位,以便后续插入元件。
5. 印刷绝缘层:在PCB上喷涂或印刷绝缘层,以保护铜箔层,同时也作为电路图案的底板。
6. 插装元件:将电子元件插入到PCB的预留孔洞中,通常通过自动插装机器完成。
7. 焊接元件:通过波峰焊接或热风烙铁对插装的元件进行焊接,确保其与PCB的连接牢固。
8. 贴装元件:将表面贴装元器件焊接到PCB表面,通常通过贴片机完成。
9. 喷涂保护层:为了保护PCB和元器件,通常需要在PCB表面喷涂一层保护层。
10. 测试验证:进行电气测试和功能验证,确保PCB电路的正常工作。
11. 包装出厂:最终将PCB进行包装,准备出厂。
通过以上的工艺流程,PCB生产便完成了。
这些工艺步骤需要特殊的设备和专业的操作技能,确保PCB的质量和稳定性。
PCB(Printed Circuit Board)是一种基于印刷技术制作电路板,它主要包括导电图形和钻孔,将PCB上的电子元件连接起来,形成一个完整的电路系统。
PCB在电子产品中被广泛应用,包括手机、平板电脑、电视机、冰箱、空调、汽车等各种电子设备。
PCB的生产工艺流程经历了多年的发展和改进,现代PCB生产工艺流程已经非常成熟,并且涉及到多个工序和精细的技术。
下面将进一步介绍PCB的生产工艺流程的相关内容。
- 1、下载文档前请自行甄别文档内容的完整性,平台不提供额外的编辑、内容补充、找答案等附加服务。
- 2、"仅部分预览"的文档,不可在线预览部分如存在完整性等问题,可反馈申请退款(可完整预览的文档不适用该条件!)。
- 3、如文档侵犯您的权益,请联系客服反馈,我们会尽快为您处理(人工客服工作时间:9:00-18:30)。
PCB 板制造工艺流程PCB板的分类1、按层数分:①单面板②双面板③多层板2、按镀层工艺分:①热风整平板②化学沉金板③全板镀金板④热风整平+金手指3、⑤化学沉金 +金手指 4、⑥全板镀金 +金手指 5、⑦沉锡⑧沉银⑨ OSP板各种工艺多层板流程㈠热风整平多层板流程:开料——内层图像转移:(内层磨板、内层贴膜、菲林对位、曝光、显影、蚀刻、褪膜)—— AOI ——棕化——层压——钻孔——沉铜——板镀——外层图像转移:(外层磨板、外层贴膜、菲林对位、曝光、显影、图镀、褪膜、蚀刻、褪锡)——丝印阻焊油墨——阻焊图像转移:(菲林对位、曝光、显影)——丝印字符——热风整平——铣外形——电测——终检——真空包装㈡热风整平 +金手指多层板流程:开料——内层图像转移:(内层磨板、内层贴膜、菲林对位、曝光、显影、蚀刻、褪膜)—— AOI ——棕化——层压——钻孔——沉铜——板镀——外层图像转移:(外层磨板、外层贴膜、菲林对位、曝光、显影、图镀、褪膜、蚀刻、褪锡)——丝印阻焊油墨——阻焊图像转移:(菲林对位、曝光、显影)——镀金手指——丝印字符——热风整平——铣外形——金手指倒角——电测——终检——真空包装㈢化学沉金多层板流程:开料——内层图像转移:(内层磨板、内层贴膜、菲林对位、曝光、显影、蚀刻、褪膜)—— AOI ——棕化——层压——钻孔——沉铜——板镀——外层图像转移:(外层磨板、外层贴膜、菲林对位、曝光、显影、图镀、褪膜、蚀刻、褪锡)——丝印阻焊油墨——阻焊图像转移:(菲林对位、曝光、显影)——化学沉金——丝印字符——铣外形——电测——终检——真空包装㈣全板镀金板多层板流程:开料——内层图像转移:(内层磨板、内层贴膜、菲林对位、曝光、显影、蚀刻、褪膜)—— AOI ——棕化——层压——钻孔——沉铜——板镀——外层图像转移:(外层磨板、外层贴膜、菲林对位、曝光、显影、图镀镍金、褪膜、蚀刻、褪锡)——丝印阻焊油墨——阻焊图像转移:(菲林对位、曝光、显影)——丝印字符——铣外形——电测——终检——真空包装(全板镀金板外层线路不补偿)㈤全板镀金 +金手指多层板流程:开料——内层图像转移:(内层磨板、内层贴膜、菲林对位、曝光、显影、蚀刻、褪膜)—— AOI ——棕化——层压——钻孔——沉铜——板镀——外光成像①(外层磨板、外层贴膜、菲林对位、曝光、显影)——图形电镀铜——镀镍金——外光成像②(W— 250干膜)——镀金手指——褪膜——蚀刻——丝印阻焊油墨——阻焊图像转移:(菲林对位、曝光、显影)——镀金手指——丝印字符——铣外形——金手指倒角——电测——终检——真空包装㈥化学沉金 +金手指多层板流程:开料——内层图像转移:(内层磨板、内层贴膜、菲林对位、曝光、显影、蚀刻、褪膜)—— AOI ——棕化——层压——钻孔——沉铜——板镀——外层图像转移:(外层磨板、外层贴膜、菲林对位、曝光、显影、图镀、褪膜、蚀刻、褪锡)——化学沉金——丝印字符——外光成像②(交货面积>1平方米) / 贴蓝胶带(交货面积≤ 1平方米)——镀金手指——铣外形——金手指倒角——电测——终检——真空包装㈦单面板流程(热风整平为例):开料——钻孔——外层图像转移:(外层磨板、外层贴膜、菲林对位、曝光、显影、图镀、褪膜、蚀刻、褪锡)—— AOI ——丝印阻焊油墨——阻焊图像转移:(菲林对位、曝光、显影)——丝印字符——热风整平——铣外形——电测——终检——真空包装(注:①因没有金属化孔,所以没有电测与沉铜板镀②外层线路菲林除全板镀金板用正片菲林外,其它都用负片)㈧双面板流程(热风整平为例):开料——钻孔——沉铜——板镀——外层图像转移:(外层磨板、外层贴膜、菲林对位、曝光、显影、图镀、褪膜、蚀刻、褪锡)——丝印阻焊油墨——阻焊图像转移:(菲林对位、曝光、显影)——丝印字符——热风整平——铣外形——电测——终检——真空包装(注:因一共两层,所以用电测代替了AOI )㈨OSP多层板流程:开料——内层图像转移:(内层磨板、内层贴膜、菲林对位、曝光、显影、蚀刻、褪膜)—— AOI ——棕化——层压——钻孔——沉铜——板镀——外层图像转移:(外层磨板、外层贴膜、菲林对位、曝光、显影、图镀、褪膜、蚀刻、褪锡)——丝印阻焊油墨——阻焊图像转移:(菲林对位、曝光、显影)——丝印字符——(二钻)——铣外形—— OSP——终检——真空包装多层板流程的步骤、意义、作用、及注意事项,现以热风整平板+金手指为例。
1、开料:对覆铜板开料。
覆铜板:就是两面覆盖铜皮的芯板。
1_覆铜板构成:基材+基铜A :基材构成:环氧树脂+玻璃纤维基材厚度≥ 0。
05MMB :基铜厚度:18 μM35μ M70μM②覆铜板的表示方法:A :小数点后一位,表示基材+基铜厚度B :小数点后两位,只表示基材的厚度C:特殊的有0.6MM 与 0.8MM 两个③覆铜板的规格:18/1835/3570/7018/3535/70单位:μM其中, 35/7018/35的称为阴阳板④覆铜板盎司 OZ的表示方法A :盎司:每平方英寸的面积上铺35μM 厚的铜的重量为1OZ 。
盎司为重量单位。
B :覆铜板盎司的表示方法:18/18=0.5/0.535/35=1/170/70=2/218/35=0.5/135/70=1/2用盎司表示规格比较方便.⑤数量:即完成一块板所需要的同板厚、同规格的内层芯板的数量。
⑥板材一般分为A: FR4板B:高频板C:无卤素板2、内层图像转移①内层磨板:分两步: A :用酸洗作用:清除板面氧化物, 2 防止夹入汽泡, 3干膜起皱。
B:用火山灰洗:使板面变的微观粗糙,增加与半固化片的结合力②内层贴膜:膜,即指干膜。
干膜分三层:顶层,聚脂薄膜;中层,光致抗蚀剂;底层,聚已烯膜。
贴膜时把底层膜去掉。
③菲林对位:通过板边马氏兰孔对位。
对位时,要用夹板条,夹板条要与放入两片蕈林之间的内层芯板等厚。
菲林一般为负片。
④曝光:用白光对菲林垂直照射⑤显影:把没有被曝光的干膜熔解掉。
(注:在曝光后、显影前去掉顶层膜,若提前去掉顶膜,则氧气会向光致抗蚀剂扩散,破坏游离基,引起感光度下降。
⑥蚀刻:把没有用的铜熔解掉。
蚀刻分为蚀刻补偿与补偿蚀刻。
A :蚀刻补偿:在正片或负片线路菲林上补偿,即加宽线宽。
补偿标准为:基铜厚内层补偿外层补偿18μm0 mil 1 mil35μm0. 4 mil1.5 mil70μm1. 0 mil3.0 mil阴阳板补偿时注意:板薄的一面多补偿,因为蚀刻时的参数时间T是以厚的基铜为准。
则有:18/35 补偿: 1.2/0.435/70 补偿: 2.4/1.0B:补偿蚀刻:是由于同板厚的板的两面蚀刻药水浓度不一样,要在时间上进行补偿,需要多进行一个△ T的时间补偿。
C:单位换算:1英尺 =12 英寸英尺:foot英寸:inch1 foot =12 inch 1 inch =1000 mil1 mm =39.37 mil ≈ 40 mil 1 inch =25.4 mm ≈ 25 mm1 mil =0.025 mm =25 μ m⑦褪膜:把被曝光的干膜熔解掉,用强碱(NAOH )3、 AOI 检测:1AOI=Automatic Optical Instrument. :自动光学检测2检测, 3 又称半检, 4 只能检查出制造问题,而 5 不6 能检查出工程问题。
7 基本过程:客户—— CAD —— CAM —— [用光绘机绘出的] 菲林——产品—— [ 用电脑 ] 扫描—— [ 在电脑中形成 ]CAM2 图形—— [ 与 CAM 进行 ] 比较。
4、棕化:使线路上生成一层棕色的氧化亚铜(CU2O )。
目的:增强与半固化片的结合力5、层压:①对铜箔开料。
铜箔厚度: 12μm 18μ m 35μm 70μ m②对半固化片开料:A :半固化片经常用的为 1080 2116,因为价格不太贵 ,含胶量比较大。
型号106 1080 3313 2116 7628 厚度( mm)0.0513 0.0773 0.1034 0.1185 0.1951 价格由大106 3313 2116 1080 7628 到小B :半固化片由:环氧树脂+玻璃纤维构成③层压:分热压和冷压。
先热压后冷压。
④层压厚度理论值公式:所有半固化片的厚度+内层芯板(不含基铜)的厚度+各层基铜的厚度×对应层的残铜率残铜率 =有用的铜 /基铜⑤层压时的叠层原则:A :优先选用厚的板材B:结构对称C:当两面基铜厚度都为 18μ m时,可以单独使用一张 1080D :层间半固化片的厚度应>2倍基铜,当为阴阳板时,则应>2倍厚的基铜E:半固化片应外薄内厚F:层间半固化片的张数应≤3张G:内层芯板应与半固化片的材料保持一致H:当板厚达不到客户要求时,可以加入光板。
6、钻孔①钻孔的步骤:A :钻定位孔(孔径为 3.2mm )B:排刀(由小到大排刀)C:钻首板D:点图对照(特殊:点图对照用点图菲林,为正片,且有边框)E:批量生产F:去批锋②钻孔要用刀,刀分为钻刀、槽刀、铣刀三种。
A钻刀范围: 0.1mm-----6.3mm ,公差: 0。
05mm当钻刀为 0。
1mm时,要求:板厚≤ 0。
6mm,层数≤ 6层当钻刀为 0。
15MM 时,要求:板厚≤1。
2mm,层数≤ 8层B 槽刀范围: 0。
6mm-------1 。
1mm当一个槽孔孔径超过这个范围可以用钻刀来代替槽刀,但槽刀钢性比钻刀好,不易断刀。
C 铣刀范围: 0.6 mm 0.8 mm 1.0 mm 1.2 mm 1.6 mm 2.4mm③ A 钻孔按性质分:金属化孔 PTH 和非金属化孔 NPTH 。
金属化孔分为:过孔、元件孔、压接孔。
B 过孔孔径范围:0。
1mm----0 。
65mm过孔特点: 1 没有字符标识 2 有电性能连接 3 排列比较零乱4 孔径相对比较小5 可以缩孔6 不插元器件过孔有四种工艺: a 过孔喷锡 b 过孔盖油 c 过孔塞孔d过孔开小窗★过孔喷锡与过孔开小窗在阻焊菲林上有图形,而过孔盖油与过孔塞孔在阻焊菲林上没有图形。
★过孔塞孔中,塞孔的范围为:0。
1mm-----0 。
65mm则在过孔塞孔过程中,盖板的对应孔径范围为0。
2mm ---0 。
75 mm★ 塞孔的方法,用开孔的铝片作为辅助板,铝片上孔的大小应比生产用板上对应孔的大大0。
1 mm,即在铝片上孔径范围为:0。
2-----0 。
75mm元件孔特点: 1 有字符标识 2 有电性能连接 3 排列比较整齐4 不可缩孔5 插元器件6 要焊接压接孔特点: 1 有字符标识 2 有电性能连接3排列比较整齐4 不可缩孔5 要插元器件6 不能焊接非金属化孔特点: 1 没有电性能连接 2 孔径相对比较大钻孔可能出现的情况:多孔、少孔、近孔、连孔、重孔、破孔、还有破盘。