新型纺纱技术
精选第三章新型纺纱设备及高新技术
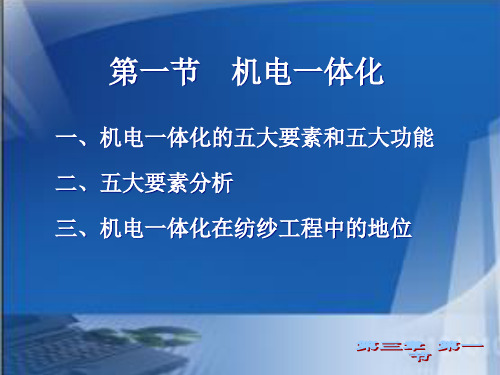
3.梳棉机
适应清梳联喂入棉层的变化,改进相应结构,方便的调整相 应工艺参数,加强电器控制,从而提高生条质量指标。
4.清梳合理分工
整个流程的连续、平稳运转,是清梳联成为一个不可分割的 统一整体的基本条件,因此各单机工艺功能应统筹考虑,合 理分工,以保证成纱质量的要求。
(三) 清梳联技术水平分析 研发生产了开松、混合、除杂,梳理度高的清梳设备。 棉条5m不匀率、开清棉机故障率和梳棉机故障率也都达到 或超过了引进清梳联的水平。
表3-3自调匀整装置对不匀率的影响% 注:以25m片段取得实验数据
项目 总不匀率U 内不匀率U 外不匀率U
有自调匀整 2.19 1.68 1.40
无自调匀整 4.27 2.03 3.76
三、清梳联技术展望 (一) 进一步提高生产效率 1.开发100kg/h左右的高产梳棉机
清梳联技术的先进性就在于高速、高产、高质量,实现 “三高”梳棉机是关键。
德国特吕茨勒:
BDT019 型抓棉机→ SP-F多功能分离器+高效凝棉 器 → MFC 双轴流开棉机→ SC155 金火探测器 →MCM 型 10 仓混棉机→CXL 型四打手清棉机→DX 型高效除尘机→ DK903 型高产梳棉机
立达的清梳联
单轴流开棉机
抓棉机
梳棉机 精细清棉机 混棉机
(三)清梳联流程的主要特点
1.实现了清棉和梳棉两个工序的连续化; 2.贯彻了“多包取用、精细抓棉、均匀混合、渐进开
松、早落少碎、以梳代打、少伤纤维”的工艺路线; 3.具有适应多品种生产功能;
4.单元机台的结构、性能走向成熟,维护保养少,安 全性、可靠性高,具有连续三班无故障运行的性能, 降低了劳动强度,提高了生产率,而且生产环境得到 很大改善,节约了用人、用地、用棉;
新型纺纱的整经浆纱技术

新型纺纱的整经浆纱技术
新型纺纱的整经浆纱技术在纺织行业中具有重要的意义。
整经浆
纱是将纱线从纱锭拉出后形成纱带,再将纱带交织并浸渍纺织浆液,
最后加热并经过一系列处理后得到的成品。
这项技术的目的是提高纺
织品的质量和效率。
整经浆纱技术的关键在于浆纱的均匀性。
传统的浆纱工艺容易出
现纱线不均匀和节点过大等问题,导致纺织品质量下降。
而新型的整
经浆纱技术通过改进纱线拉伸和浆液浸润等环节,解决了这些问题。
首先,在纱线拉伸环节,采用了先进的拉伸机械装置,能够实现
对纱线的均匀拉伸,并保持纱线的一致性。
这样可以降低纱线的断裂率,并提高纱线的强度和光泽度。
其次,在浆液浸润环节,新型的整经浆纱技术采用了纳米技术,
使纺织浆液分子更好地渗透到纱线内部,提高纱线的浆液吸附能力。
这样可以使纱线更加平滑和柔软,提高纺织品的手感和舒适度。
最后,在加热和处理环节,新型整经浆纱技术运用了先进的加热
设备和处理工艺,确保纺织品经过加热后的表面平整度和色泽均匀度。
同时,减少了处理时间和能耗,提高了生产效率和经济效益。
综上所述,新型纺纱的整经浆纱技术通过改进纱线拉伸、浆液浸
润和加热处理环节,提高了纱线的质量和整经浆纱的效率。
这项技术
将对纺织行业的发展起到积极的推动作用,并有望在未来得到更广泛
的应用。
新型纺纱技术范文

新型纺纱技术范文随着科技的不断发展,纺织行业也在不断进步和创新。
新型纺纱技术的出现,为纺织品的生产提供了更高效、更节能、更环保的方法。
下面将介绍几种新型纺纱技术。
一、无纺布纺纱技术无纺布是一种新型的纺织品制造材料,它是通过纤维材料的单根纤维或纤维的网状物重新组装制成,而不经过纺纱和织造的传统纺织工艺。
与传统纺织品相比,无纺布具有较好的透气性、柔软性、防水性和抗菌性能。
无纺布纺纱技术主要包括干法纺、湿法纺和熔喷纺。
1.干法纺:干法纺是指将纤维原料通过风力或机械力使其悬浮在空气中,再经过静电或压力作用形成网状结构,然后通过加热或涂覆等工艺使其定型。
这种纺纱技术具有操作简便、生产效率高、成本低的特点。
2.湿法纺:湿法纺是将纤维原料加入到溶剂或溶液中,经过溶解、混合和过滤等处理后,通过喷细流的方式使纤维得以凝聚成片状纺丝。
湿法纺纱技术具有纤维均匀、纺丝速度快、纱线质量稳定的特点。
3.熔喷纺:熔喷纺是将熔融的纤维原料从微细孔喷射出来,经过凝结和拉伸等过程形成纤维丝,然后通过集束、冷却和拉伸等工艺使其定型。
熔喷纺纱技术具有纺纱速度快、成本低、纤维之间的结合力强的特点。
二、空气动力纺纱技术空气动力纺纱技术是一种通过高速气流将纤维原料进行纺丝的技术。
空气动力纺纱技术具有操作简单、纺纱速度快、纤维短节短的特点,适用于生产短纤维纱线和造粒丝等纤维产品。
通过调节气流速度和纤维原料的喷射角度,可以控制纺丝过程中纤维的拉伸和取向。
三、湿旋杯纺纱技术湿旋杯纺纱技术是一种通过旋转的杯状结构将纤维原料沉积在杯底的纺纱技术。
湿旋杯纺纱技术具有纺纱速度快、纤维稳定性高的特点,适用于生产高强度和高弹性的纤维纱线。
湿旋杯纺纱技术的关键是通过旋转底部的孔洞使纤维原料被拉伸和拉断,形成纤维丝。
四、气流喷射纺纱技术气流喷射纺纱技术是一种通过高速气流将纤维原料进行纺丝的技术。
气流喷射纺纱技术具有纺纱速度快、纤维耐磨性强的特点,适用于生产耐磨性和耐拉伸性要求较高的纤维纱线。
棉纺5种实用纺纱方法

棉纺5种实用纺纱方法
1.环锭纺纱法:这种方法是目前最常用的棉纺方法之一。
将纤维放在环锭上,并在锭子周围绕着钩针上。
随着锭子的旋转,纤维就被拉伸并旋转成线。
这种方法适用于各种不同类型的棉纤维。
2. 摇杆纺纱法:这种方法是一种古老的技术,但仍然在某些地区使用。
它需要手动操作,使用一个摇杆来拉伸并旋转纤维成线。
这种方法通常用于生产特定类型的面料和纤维,如丝绸。
3. 吸气纺纱法:这种方法将纤维放在一个吸气管上,然后使用吸气力将纤维拉伸并旋转成线。
这个过程非常快,因此适用于大批量棉纺生产。
4. 水力纺纱法:这种方法使用高压水流将纤维拉伸并旋转成线。
这种方法非常快速和高效,但需要先将纤维处理成一定程度的湿润状态。
5. 气流纺纱法:这种方法使用空气流动将纤维拉伸并旋转成线。
这个过程非常快,因此适用于大批量棉纺生产。
但它需要特殊的设备来产生足够的气流。
- 1 -。
赛络紧密纺

心得体会
好的应用与创新来自丰富完备的知识积累 学会“站在巨人的肩膀上摘苹果”
34.23
34.07
10.03
10.78
8.80
8.20
1.60
1.43
3.52
3.54
3.63
3.62
7.13
7.34
自由端转杯纺纱锭数
年份 2009 中国 900 印度 386 巴基斯坦 145 印度尼西亚 美国 70 754 墨西哥 100
单位:千锭
巴西 322 土耳其 507
2010
2011 2012
赛络纺工艺流程如上页图所示: 双粗纱喂入到罗拉牵伸区,采用分离器使双粗纱分离,
以确保每一组粗纱都被单独牵伸;从牵伸系统送出的两须条
并合后加捻成单纱,即为赛络纱(Sirospun yarn) 。这种纺 纱工艺具有以下优点:在环锭纺细纱机上略加改造即可实现 生产;赛络纱的结构与股线相似;纱线的耐磨性有所改善, 同时毛羽减少。
新型纺纱技术之
赛络紧密纺
姓名:李明 学号:1314
目录
一、新型纺纱技术概述
二、一、新型纺纱技术概述
纺织纱线对于织物性能和特征具有很重要的作用, 是纺织生产加工中的重要一环。
纤维、纱线和植物的结构与性能之间的关系
分子性能和纤维结构性能
纤维性能
纱线结构
纱线性能
3.2
3.2.1
紧密纺装置
多孔滚筒式----负压式
立达公司的Com.4(Comforspin)系统: 多孔辊筒代替了原来的前下罗拉。多孔辊筒内部的吸气槽(带 槽的异形吸管)通过多孔辊筒将外部空气吸入,形成可凝聚纤 维的负压。在每个纺纱位置的上方有一个可加强纤维凝聚的气 流导向板。
新型纺纱技术

(1)自控程度高 (1)自控程度高
涡流纺整个纺纱过程受到电子系统的监控, 电子清纱器发现纱疵时即自动去除疵点,并立 即应用自动接头装置将纱接起来,因此整个纺 纱过程是全自动、连续式的。此外,每个锭子 的纱都受到自动接头器的监控,如有异常,可 实现单锭自动停止纺纱。
(2)工艺流程短 (2)工艺流程短
2、涡流纺的主要特点
涡流纺无高速回转机件采用旋转涡流加捻成纱,比 机械式加捻效率高,高速回转的涡流只作用在纤维 上,与前罗拉引出的纤维的功能一起形成对纤维的 加捻作用,高速涡流除了完成加捻任务外,并不影 响纱线支数的高低,因此可实现高速纺纱,最高纺 速实际可达380m/min,每锭的产量相当于环锭纺单 锭产量的22倍左右。由于纤维受到具有声速的喷气 涡流及卷取罗拉作用而形成真捻,因此这种特殊的 加捻作用是其它纺纱机械不能取代的,纱线高的回 旋速度下的成纱结构比环锭纱线的结构更为紧密和 稳定。
3、紧密纱线的特点
毛羽少,光洁度高。其毛羽一般比普通纱减少 70%-80%; 强度高,捻度减少。同样的纱支捻度减5%-15%, 而强力却提高约15%-25% ; 条干好。由于纤维的利用率得以提高,乌斯特条干能 够达到3%-5%; 能代替股线。由于紧密纱的强度高,其单纱可以替代 传统股线。如 16.2tex的紧密纱与8.1×2tex的传统股 线具有同等强度,在生产工艺上可以减少合股工序;
从以上紧密纱的特点可以看出它是一种与 众不同的高品质纱。由于它的优良特性给纺 纱、准备、织造、印染等一系列后道加工带 来了工艺创新,降低了后加工流程和成本, 尤其是减少了浆纱和烧毛对环境造成的工业 污染。
总之,紧密纺纱技术是目前环锭细纱机关键的重 要技术进步。纱线质量及生产费用等方面的优势,将 使紧密环锭纺纱技术不但本身具有高档产品的特征, 而且将逐步取代传统环锭纺纱技术,使纺织工业及时 装工业具有更开阔的产品开发空间,使服装设计可以 从紧密纱纺纱到最终产品进行一系列的设计,这种独 特的生产优势,一方面提高了产品档次,另一方面也 考虑了产品的经济性、生态环境特性、创新性及独特 性等。现在, 性等。现在,紧密纱在市场上的售价比传统环锭纱每公 斤高1 3.5美元,经济效益十分可观,更重要的是消费 斤高1-3.5美元,经济效益十分可观,更重要的是消费 者非常欢迎。因此,紧密纺纱技术将得到快速发展。
(完整版)主要新型纺纱的比较
主要新型纺纱的比较1、成纱原理:转杯纺依靠调整回转的纺杯,将纱尾贴紧在纺杯内壁聚槽内,而头端为引纱罗拉握持并连续输出加捻成纱。
喷气纺靠两只喷嘴喷射相反方向的回旋气流,对由牵伸装置输出的须条先加捻后解捻,表面纤维形成包缠成纱。
摩擦纺一般用两只同向回转的摩擦元件,对其楔形区的纤维施加摩擦力偶,使纤维束滚动而加捻成纱。
2、成纱截面中纤维根数不同:喷气纱中最少纤维根数略高于环锭纱,可纺中低线密度纱;摩擦纺和转杯纺中的最少纤维根数较多。
3、对纤维性能要求不同:影响转杯纱强力的主要因素是纤维的强力和线密度,摩擦纱则是纤维的摩擦因数和强力。
4、纺纱速度和成纱线密度:环锭纺的可纺线密度覆盖面最广,但产量太低,各种新型纺纱的纺纱速度都比环锭纺高,但可纺线密度有局限性5、新型特点:新型纺纱取消了锭子、筒管、钢领、钢丝圈等加捻卷绕元件,并将加捻和卷绕作用分开完成,具有产量高,细纱机的产量取决于锭子的速度,而锭速的提高,一方面受钢丝圈速度的限制,另一方面受气圈张力的限制;卷装大,环锭细纱机上增大卷装的途径是增加筒管长度和加大钢领直径,但筒管加长则气圈高度加长,钢领加大则钢丝圈线速度增大,这些都会导致断头增多,而新型纺纱方法将加捻和卷绕分开进行,可直接纺成筒子纱;工艺流程短,新型纺纱采用条子喂入,直接纺成筒子纱,省去粗纱、络筒两道工序。
转杯纺1、原理:纺杯高速旋转,纺杯内便产生离心力,离心力可使从分流腔转移到纺杯内的棉纤维产生凝聚而成为须条,须条被加捻后便成为纱条。
2、工艺过程:条子从条筒中引出送入喂给罗拉,喂给罗拉与喂给板将条子向前输送,经分梳辊分梳成单纤维,被补风口和引纱管的气流吸入纺纱杯,沿纺纱杯壁滑入凝聚槽形成凝聚须条,由于纺纱杯高速回转产生的离心力使引纱纱尾贴附于凝聚槽面而与须条连接,并被纺纱杯摩擦握持而加捻成纱。
3、转杯纱结构与性能:转杯纱由纱芯与外包缠纤维两部分组成,内层的纱芯比较紧密,外层的包缠纤维结构松散;环锭纱没有纱芯,纤维在纱中大多呈螺旋线排列。
新型环锭纺纱技术的种类
新型环锭纺纱技术的种类
新型的环锭纺纱技术主要包括环锭改革的纺纱新技术和新型纺纱。
前者是在传统的环锭纺细纱机的基础上进行革新,如赛络纺、赛络菲尔纺、缆型纺、紧密纺等,它们也可以说是环锭纺纱技术的新发展。
后者还成纱机理与环锭纺完全不同的成纱方法,如转杯纺、喷气纺、喷气涡流纺、摩擦纺、涡流纺和自捻纺等,它们按纺纱原理还可进一步分为自由端纺纱和非自由端纺纱两大类。
此外,双面纺纱技术是近年来发展起来的一种环锭纺纱技术。
传统的环锭纺纱只能在一侧纺纱,而双面纺纱技术可以在同一台机器上同时进行两面纺纱,大大提高了纺纱效率。
新型纺纱
新型纺纱当前棉纺领域中有五种实用的、倍受关注的纺纱方法,即环锭纺、转杯纺、喷气纺(包括喷气涡流纺),摩擦纺和紧密纺。
环锭纺纱方法已有100多年的历史,故又称传统纺纱,而后4种纺纱方法都是在近几十年甚至是近几年发展起来的,故统称为新型纺纱方法。
(1) 紧密纺是纺纱的新概念,新技术,主要在细纱机上作改良,牵伸系统与传统细纱机不同,在输出罗拉后多加一套令纤维会集的装置,使有效地让经过了两次牵伸的粗纱棉条,在进入加捻区前会聚,利用一股气流把条子从罗拉牵伸系统的夹持点拉出,集合在一个多孔的表面上,因吸力作用下条子被压缩,缩小钳口处粗纱宽度,大幅降低纺纱三角的高度,棉纱加捻效果增加,棉纤维抱合更加有序,更加紧密,令棉纱毛羽数量大幅下降。
(2)赛络纺又命并捻纺,中国大陆称为A,B纱,近期正式命为赛络纺。
是在细纱机上喂入两根保持一定间距的粗纱,经牵伸后,由前罗拉输出这两根单纱须条,并由于捻度的传递而使单纱须条上带有少量的捻度,拼合后被进一步加捻成类似合股的纱线,卷绕在筒管上。
赛络纺的初始设计目的是用于毛纺上,该纱存在:毛羽少,强力高,耐磨性好。
达到毛纱能单纱织造的效果,以实现毛织物的轻薄化,但尽管赛络纺在许多方面比较同类常规纱有了较大的改善,要真正达到毛纺单纱不上浆织造,尚有一定距离,其后毛纺亦多放弃此方法,反而在混纺如T/C,C.V.C等则采用此方法,因其染色后可产生并纱之麻花效果,手感好,故受欢迎,近期更因改善毛羽问题,如纺一些易产生毛羽之纤维,如人造棉,莫代尔,天丝,大豆纤维,甚至全棉都用此方法生产,赛络纱所用的原料等级可比常规环绽纺低,而其织物较常规环锭股线织物毛羽少,手感柔软,耐磨,透气性能好。
(可参考本人:SIRO YARN 工艺及注意事项一文)。
(3)赛络菲纺,与赛络纺类似,亦是在赛络纺基础上变化,不同之处是将一根粗纱改为一根细旦长丝,与另一根粗纱(毛,棉或麻,绢丝等)在环锭细纱机上加装一个长丝喂入装置,使长丝与正常牵伸的须条,保持一定距离平等喂入,并在前罗拉钳口下游汇合,交捻成纱。
纺纱概论—新型纺纱
(4)纱条引出后经电子清纱 器去除疵点后被卷绕在筒子上。
新型纺纱—喷气纺纱
喷气纺纱的成纱结构特点
• 1、喷气涡流纺(MVS)纱 的结构特点 涡流纱也是一种双重结构的纱,纱条的芯纤维是平行排列的、无
捻度,依靠旋转气流的作用使末端纤维包覆缠绕于芯纤维外部加捻成 纱。但与喷气纱不同的是,涡流纱的外层覆盖纤维比重大(约60 %),以致内部未加捻的纤维几乎被完全覆盖,表面纤维排列则更近 似于环锭纱。纱线毛羽很少,织物起球现象亦减少,染色性能及耐磨 性好。 • 2、 喷气纺(MJS)纱线结构
新型纺纱
新型纺纱概述
新型纺纱概述
1、环锭纺的特点和存在的问题 •特点: ①加捻和卷绕不分 (同时由锭子、钢领、钢丝圈完成) ②成纱结构紧密,强度较高。 ③适纺不同线密度的纱线。(细纱机牵伸范围大) •存在的问题: ①钢丝圈和纱线张力的制约 ②气圈稳定性的影响。 ③产量很难大幅度提高。
新型纺纱概述
新型纺纱---自由端纺纱
1、转杯纺原料
①天然纤维:棉、亚麻 ②再生纤维素纤维:粘胶、莫代尔、天丝 ③合成纤维(短纤维):涤纶、腈纶、 ④棉纺厂再用棉:精梳落棉、清花落棉、梳棉落棉
2、适纺纱支范围
国内:10~30英支,国际:6~40英支
3、转杯纺工艺流程
①开清棉 → 梳棉→并条 (二道)→ 转杯纺纱机
(二)非自由端纺纱 一般经过罗拉牵伸——加捻——卷绕三 个工艺过程,即纤维条自喂入端到输出端呈连续状态,加捻器 置于喂入端和输出端之间,对须条施以假捻,依靠假捻的退捻 力矩,使纱条通过并合或纤维头端包缠而获得真捻。自捻纺纱 、喷气纺纱、粘合纺纱就属于这种方法。
新型纺纱
- 1、下载文档前请自行甄别文档内容的完整性,平台不提供额外的编辑、内容补充、找答案等附加服务。
- 2、"仅部分预览"的文档,不可在线预览部分如存在完整性等问题,可反馈申请退款(可完整预览的文档不适用该条件!)。
- 3、如文档侵犯您的权益,请联系客服反馈,我们会尽快为您处理(人工客服工作时间:9:00-18:30)。
新型纺纱技术一、涡流纺纱涡流纺纱是利用高速回转的空气涡流进行纺纱的一种自由端纺纱方法,纺纱速度可比环锭纺纱提高约6-7倍。
它用一根固定的涡流管取代了高速回转的加捻器,所以是一种产量高而机构比较简单的新型纺纱方法。
祸流纺是用条子喂入,直接纺成筒子,简化了纺纱工序,可提高劳动生产率。
此外,涡流纺是在负压条件下纺纱,不产生飞花,劳动条件好。
且制成率比较高。
目前主要用以纺粗、中号的化纤纱及包芯纱等。
1、纺纱原理涡流纺基本原理是利用一只静止的纺纱器下端由真空泵抽气,二边切开线长槽孔进气,强制气流在纺纱器内形成一股强大的涡流。
被气流吸入的纤维,由于涡流的作用产生高速度回转,形成纤维环。
如用一根纱引近纺纱器顶端的纺纱头小孔处,即自动被吸入纺纱器中,同时,纱头立即与聚棉处的纤维环连接起来,因为纱头上面是握住的,所以在纺纱器内的纱尾,由于涡流的作用,产生高速度回转而进行加拈,如纤维从小孔中连续输入,纱条从纺纱器头子中连续抽出卷绕在筒子上,这就是涡流纺纱的全过程。
2、涡流纺的主要特点涡流纺无高速回转机件(如环锭纺中的锭子,钢丝圈等)采用旋转涡流加捻成纱,比机械式加捻效率高,高速回转的涡流只作用在纤维上,与前罗拉引出的纤维的功能一起形成对纤维的加捻作用,高速涡流除了完成加捻任务外,并不影响纱线支数的高低,因此可实现高速纺纱,最高纺速实际可达380m/min,每锭的产量相当于环锭纺单锭产量的22倍左右。
由于纤维受到具有声速的喷气涡流及卷取罗拉作用而形成真捻,因此这种特殊的加捻作用是其它纺纱机械不能取代的,纱线高的回旋速度下的成纱结构比环锭纱线的结构更为紧密和稳定。
(1)自控程度高涡流纺整个纺纱过程受到电子系统的监控,电子清纱器发现纱疵时即自动去除疵点,并立即应用自动接头装置将纱接起来,因此整个纺纱过程是全自动、连续式的。
此外,每个锭子的纱都受到自动接头器的监控,如有异常,可实现单锭自动停止纺纱。
(2)工艺流程短涡流纺与环锭纺相比,将粗纱、细纱、络筒和并筒等四个工序合而为一。
占用的厂房面积小、用工省(可减少250%)、能耗低(可节约30%的能源),机物料消耗与维修工作量也少,具有较低的运行费用。
(3)品种适应广涡流一般可纺10 tex以下的纯棉纱,涤/棉及化纤混纺纱,并可纺包芯纱、彩色纱、花式纱。
(4)产品有特色涡流纺其纱线是由包缠纤维和芯纤维所组成的一种双重结构纱,外观光洁,纱线的毛羽可减少3/4,3mm以上的近乎为0;具有优越的吸汗、速干、透气性,因而其产品抗起毛起球性好(可提高30%);耐磨性、染色性佳,可广泛用于机织尤其是针织产品中。
3、涡流纺工艺技术(1)试验用原料及品种原棉:原棉等级:2级;主体长度:29.4mm;短绒率:12.2%;细度:4.02熟度:1.53。
品种:JK 18tex(2)工艺流程清梳联合机→并条机→条卷机→精梳机→并条机→并条机→喷气涡流纺纱机→成件。
4、纺纱工艺要点涡流纺纱的机理是纤维条经牵伸后形成纤维束,纤维束在喷管中稳定的涡流控制下加捻及末端扩张,再经空心锭子的捻搓作用后旋转,完成外部包缠纤维和纱芯纤维的加捻作用,成纱具有独特的内外结构特征。
外部结构近似于环锭纺纱,包缠纤维呈螺旋状,与无捻纱芯一起形成捻度,相对于真捻纱,包缠纤维比较少,并有伸直缠绕的情况。
内部纱芯纤维的排列直接影响成纱强力,如纤维分布定向好,单位截面承担应力的纤维数量多,成纱强力弱环及细节出现概率少,成纱断裂强度增加。
涡流纺纱时如果喂入条纤维弯钩和棉结多,则纱芯纤维定向差,易产生强力弱环及细节,短绒含量高还将导致涡流纺纱生产中纤维散失,造成涡流纱断裂强度下降。
由此可见,喂入纤维条中的纤维整齐度、弯钩和棉结数量直接影响到涡流纺纱的成纱结构和性能,而纤维条质量主要取决于梳棉过程中对纤维的梳理和转移。
因此,涡流纺前纺工艺的侧重点和环锭纺一样,依然是提高纤维的伸直度,减少短绒的产生。
喷气涡流纺的纺速、喷嘴压力、喷针座型号、隔距等将直接影响成纱质量,(1)清花工艺采用“多梳少打,以梳代打,少落快喂”的工艺路线,尽量减少开松对纤维的损伤。
适当降低各打手速度,一般A036打手速度不高于550r/min,A076C打手速度不高于950 r/min。
同时增加风扇速度与打手速度之比,保证棉流顺利输送,减少棉结。
(2)梳棉工艺为减少纤维损伤,梳棉采用:“轻定量、低速度、大隔距、小张力”工艺原则,以使纤维得到充分梳理和良好转移。
针布的选用应考虑强化梳理、转移、减少棉结和纤维损伤,达到提高针布间的分梳、转移能力,使纤维在梳理过程中获得最佳的梳理质量。
适当提高刺辊速度,增强刺辊和开松梳理作用,同时提高刺辊纤维向锡林的转移能力,达到减少棉结和改善成纱条干的效果。
适当增加锡林与道夫间速比,实现快转移,可明显提高生条的纤维伸直度,减少纤维弯钩的产生,改善涡流纺纱质量。
(3)并条工序工艺配置一般采用“大隔距、小张力、重定量慢速度”原则,以增加纤维间的抱合力,保证足够的握持力和牵伸力。
由于生条内纤维平行伸直度较差,为了消除前弯钩,改善熟条条干,根据系统工艺学原理,头并的后牵伸倍数适当加大,一般不低于1.7倍,末道并条后牵伸一般不大于1.3,以提高条子伸直度,为成纱均匀打下良好的基础。
(4)喷气涡流纺控制质量的关键工艺参数纤维输送通道的旋转角度:影响纤维与涡流场旋转配合输送,形成自由端;引导针的定位:影响纤维准确进人纱体而加捻;涡流场:影响纤维旋转端的形成和纤维被吹散分离效果,影响加捻程度。
5、喷气涡流纺成纱质量从喷气涡流纺和环锭纺的质量对比数据来看,在同样配棉情况下,喷气涡流纺的条干与强力均较环锭纺稍逊,条干主要表现为细节多,但由于这种细节长度较短,在布面上反映不明显,涡流纺的纱线棉结少,毛羽少,加之这种纱的结构特点决定了它透气性好,这对于强力要求不太高的针织面料来说无疑是最佳选择,对于高速喷气织机,使用喷气涡流纱的织机效率也高于环锭纱。
总之,涡流纺是一种发展中的新型纺纱方法,在技术上有它的特点。
近年来,国外在自动化程度和机械制造水平上又有新的提高,如波兰PV-1A型涡流纺纱机已实现了自动接头、自动清洁和自动起纺,并大量采用压制成形的机件,便于维修保养、国内在用于起绒织物方面已取得了可喜的成果。
今后在进一步提高质量,降低消耗和提高机械制造水平的基础上,更多地扩大产品品种涡流纺必将有新的发展。
二、紧密纺紧密纺是在改进的新型环锭细纱机上进行纺纱的一种新型纺纱技术。
紧密纺纱线性能优良,不但能节约后续加工的费用,而且紧密纺纱线的优良特性为开发纺织新产品提供了有利条件。
1、紧密纺纱原理紧密纺纱系统多数采用空气动力学原理,在纺纱三角区位置,通过一组集聚元件,使牵伸后的松散纤维须条经过负压吸聚管表面时,利用空气导向作用使纤维紧密地抱合在一起,经导向胶辊输出加捻成纱,纺纱过程中加捻三角区变得很小,基本消失,大大减少浮游外露纤维(即毛羽)的数量。
还有一种紧密纺纱系统不采用吸风而采用机械-磁铁原理工作, 如罗卡斯紧密纺系统装置,其前胶辊和引纱胶辊置于前下罗拉之上, 磁性紧密器置于两个胶辊之间,共同形成紧密区。
紧密器与下罗拉之间紧密接触,没有间隙,上、下罗拉一起形成一个完全封闭的负压区,其底部的弧度与下罗拉表面完全一致,纤维束与罗拉同步移动,通过紧密器的纤维通道,被安全地输送到引纱钳口。
无论是何种紧密纺装置, 其作用是减小和消除纺纱三角区,使毛羽减少,强力提高,结构紧密,纱体光滑。
但由于国外紧密纺设备价格昂贵,目前我国只有少数企业引进或改造了紧密纺纱系统。
2、紧密纺的特点(1)由于在加捻前,纱条中单纤维充分伸直,相互平行,而且排列紧密,所以在加捻罗拉钳口处(也叫阻捻罗拉,因为其有阻止捻度传递的作用),纱条直径变得很小,所以基本消除了“加捻三角区”,由于加捻前单纤维充分伸直、平行,没有毛羽伸出纱条主体,所以成纱毛羽很少,特别是3毫米以上毛羽极少。
(2)在细纱中由于各单纤维是在伸直、平行的状态下加捻,在单纱受到拉力时,各单纤维受力基本一致,所以紧密纺强力比传统单纱高。
而且由于紧密纱中的单纤维排列紧密,相互间抱合力大,这也有助于提高纱线的强力。
(3)在紧密纺工艺中,纱条是在完成了工艺规定的牵伸之后再进行聚集,所以其条干不匀的指标没有大的改善,但在其聚集区有对纱条的整理作用,且在加捻罗拉钳口处加捻时纤维的内、外层转移没有传统工艺强烈,所以紧密纱的条干不匀,粗、细节指标比传统纱要好。
(4)由于紧密纱的上述特点,为下道工序提供了非常好的条件,紧密纱毛羽少,所以减轻了上浆、烧毛等工序的压力,在无梭织机的纬纱使用紧密纱时大大减少了引纬的阻力,提高了织机效率。
(5)由于紧密纱纤维排列紧密,和相同号数的传统纱线相比直径小,所以用相同经、纬密织成的布透气性好,布面平整、光滑,是高档纺织品的理想用纱。
3、紧密纱线的特点:(1)毛羽少,光洁度高。
其毛羽一般比普通纱减少70%-80%;(2)强度高,捻度减少。
同样的纱支捻度减5%-15%,而强力却提高约15%-25%,(3)条干好。
由于纤维的利用率得以提高,乌斯特条干能够达到3%-5% ;(4)能代替股线。
由于紧密纱的强度高,其单纱可以替代传统股线。
如16.2tex的紧密纱与8.1×2tex的传统股线具有同等强度,在生产工艺上可以减少合股工序;(5)可以减少上浆和上腊量。
由于紧密纱毛羽少,降低了纱线之间的粘缠,因此可以减少上浆量,并可以不上腊;(6)可以代替同号数的烧毛纱。
紧密纱由于毛羽少,其织物精细、光洁度好,一般可省去烧毛工序。
从以上紧密纱的特点可以看出它是一种与众不同的高品质纱。
由于它的优良特性给纺纱、准备、织造、印染等一系列后道加工带来了工艺创新,降低了后加工流程和成本,尤其是减少了浆纱和烧毛对环境造成的工业污染。
总之,紧密纺纱技术是目前环锭细纱机关键的重要技术进步。
纱线质量及生产费用等方面的优势,将使紧密环锭纺纱技术不但本身具有高档产品的特征,而且将逐步取代传统环锭纺纱技术,使纺织工业及时装工业具有更开阔的产品开发空间,使服装设计可以从紧密纱纺纱到最终产品进行一系列的设计,这种独特的生产优势,一方面提高了产品档次,另一方面也考虑了产品的经济性、生态环境特性、创新性及独特性等。
现在 ,紧密纱在市场上的售价比传统环锭纱每公斤高 1-3.5美元,经济效益十分可观,更重要的是消费者非常欢迎。
因此,紧密纺纱技术将得到快速发展。