涂装检验规范
涂装件外观检验通用规范
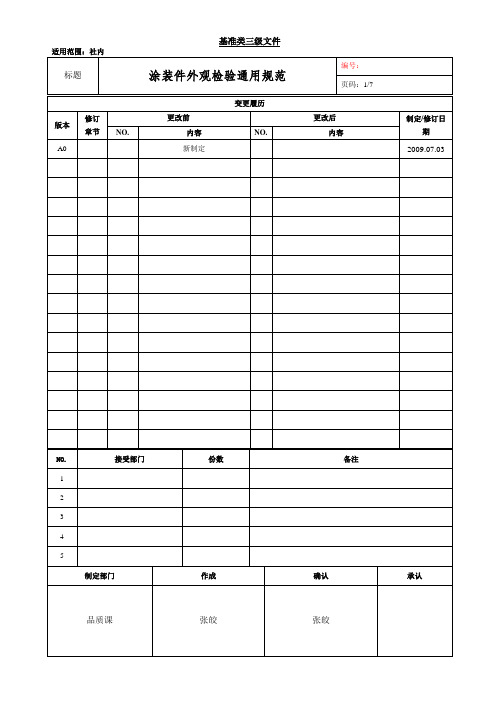
编号: 页码:2/7
1. 目的: 明确和规范公司涂装产品的表面检验标准,以确保生产和检验有章可循,确保产
品受入检验及出荷品质符合行业及客户要求。 2. 适用范围:
本标准适用于公司所有涂装品的受入检验,完成品检验,以及外协供应商。
3.职责 3.1 品质部:依本标准进行检验与测试; 3.2 物流部(仓库)依本标准进行仓存。
以上 ,允许 3 以上 ,允许 5
处以内
处以内
宽 0.20mm 以 宽 0.30mm 以
内,长度
内,长度
10mm 以内,间 20mm 以内,间距
距100mm 以上, 150 mm以上,可
可以接收3处
以接收5 处
深度≥0.20mm 深度≥0.50mm
不接受
不接受
C 级面 可接受,但不能对 产品造 成功能性影响。 具体可参照样板。
变化,或仅有少量涂层迁移到软布(或脱脂棉)上为合格(用 95%无水酒精,则来 回擦拭涂膜50 次) 7.3.5 盐雾试验: 具体操作依据盐雾试验作业指导书,具体标准按客户产品图纸要求或国家相关标准或
行业相关标准执行,一般来说按5%盐水35℃500H 不发霉氧化管控(未特别指示情 况下)。
7.3.6 耐湿性 没有特别指示的情况下:50℃湿度98%以上的恒温恒湿,240 小时无异常。 7.3.7 耐沸腾水性 没有特别指示的情况下:浸入自来水 98~100℃ 3 小时无异常。 7.3.8 耐湿水性 没有特别指示的情况下:浸入自来水 40~50℃240 小时无异常。 7.3.9 耐盐水性 没有特别指示的情况下:100%NaC1 液体中浸泡(20℃)240 小时无异常 7.3.10 耐碱性 没有特别指示的情况下:5%NaOH 液体中浸泡(20℃)48 小时无异常 7.3.11 耐酸性没有特别指示的情况下:5%醋酸液体中浸泡(20℃)24 小时无异常 7.3.12 耐油性 没有特别指示的情况下:60℃ Spindle油中浸泡60分钟无异常 附加说明:以上性能测试项目只列入描述,具体项目要求依据喷涂行业标准进行。
外墙涂料检验标准及验收规范
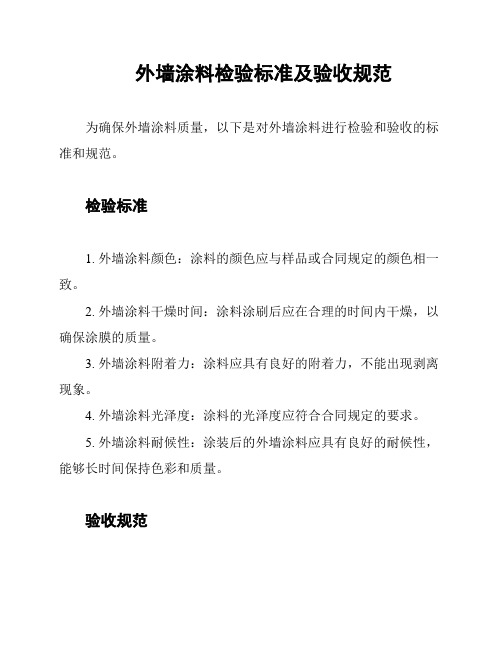
外墙涂料检验标准及验收规范
为确保外墙涂料质量,以下是对外墙涂料进行检验和验收的标准和规范。
检验标准
1. 外墙涂料颜色:涂料的颜色应与样品或合同规定的颜色相一致。
2. 外墙涂料干燥时间:涂料涂刷后应在合理的时间内干燥,以确保涂膜的质量。
3. 外墙涂料附着力:涂料应具有良好的附着力,不能出现剥离现象。
4. 外墙涂料光泽度:涂料的光泽度应符合合同规定的要求。
5. 外墙涂料耐候性:涂装后的外墙涂料应具有良好的耐候性,能够长时间保持色彩和质量。
验收规范
1. 外墙涂料样品:在施工前,涂料供应商应提供涂料样品供验收。
样品应与合同规定的涂料相一致。
2. 施工前检查:在施工前,应对基层墙体进行检查,确保其平整、无尘、干燥,以便涂料附着良好。
3. 涂刷施工:涂刷施工应符合涂料供应商的建议,并按照合同规定的涂刷层数进行施工。
4. 干燥时间:涂刷完毕后,应保证涂料能够充分干燥,避免过早接触水或其他物质。
5. 验收评定:验收时,应对涂料进行检查,确保颜色、干燥时间、附着力、光泽度和耐候性等符合检验标准。
以上是外墙涂料的检验标准和验收规范。
通过严格遵守这些标准和规范,可以保证外墙涂料的质量和使用效果。
涂装作业检验规程

1 目的为规范公司涂装检验主要流程,质量控制部门在质量管理工作中有效的履行自身职责,提高涂装施工作业的专业性,减少质量返工,有效的降低涂装作业成本,完善涂装作业流程中意外情况的处理机制,提高公司涂装作业能力。
2 术语与定义无3 适用范围3.1本规程规定了涂装作业施工中从涂料进厂,工艺的制定,涂装施工作业,质量控制等各个质量控制人员的工作职责。
3.2本规程适合公司业务涉及的铁基,非铁基以及金属热镀,冷喷,热喷等所有防腐,阴极保护作业产品。
4 职责4.1 操作人员、QSHE检验人员都要经过一定的培训,掌握基本涂装原理。
4.2 应对工作环境(杂质、温度、湿度、露点等)进行控制,以满足工艺文件的要求,必要时应加以验证。
4.3 QSHE检验员应检查涂装施工的整个过程,检查重点应放在表面处理和涂装施工的起始,以加强过程控制为主,辅以必要的多频次的工序检查,QSHE检查人员对现场操作负有监督的责任和权限。
4.4 QSHE检验人员应认真、如实、完整地填写原始记录,并按规定程序签名、处理、传递和保管,使之具有可追溯性。
4.5 涂料的进厂检验,材料收集,施工过程的质量检验和控制以及条件监督主要由QSHE检验员负责,并形成可追溯的记录,配合业主或是监理方的验收。
5 过程描述5.1 涂装流程5.1.1 涂料后进厂后由QSHE 检验员对来料包装,标识,生产日期,保质期进行审核,收集质保书,技术说明书等,合格方可入库。
5.1.2 涂装每道表面处理作业完成后都需QSHE 检验员验收合格方可进入下道程序。
表面处理后发现有上道程序遗留缺陷需运营部配合安排处理。
1)依照SSPC SP-1的标准对结构或是设备表面进行去油,脱脂处理,处理完后报QSHE检验员检测。
2)构件表面处理前QSHE 检验员需对磨料和压缩空气进行确认是否满足项目要求,必要时需进行实验确认,用以寻找正确合适的磨料配方。
3)对表面进行除锈处理以达到工艺和标准要求的状态和粗糙度。
整机涂装工艺规程及检验标准

涂装工艺、检验标准、质量要求一、工艺流程及技术要求油漆涂装工艺流程:1、铸件、结构件→抛丸室→手动抛丸→清理→人工打磨→喷底漆→自然干燥。
2、滑块部件:高性能及其变形产品系列产品,L36系列、L31系列、E36系列、E31系列等整体闭式半闭式单双点产品,JF36系列、JK36系列机床,F75G 系列、VH系列、SH系列机床-滑块、连杆(含连杆盖)在机加工完成后,转油漆工序按成品油漆标准进行涂装(不含滑块斑马线),转装配总装后不再油漆。
(使用带防护吊具,生产全过程注意油漆面防护)3、机身部件:(1)高性能等整体机身机床(不含VH系列、SH系列),机身在机加工完成后,转油漆工序,其内腔按成品油漆标准进行涂装,侧面安装电箱部位喷成机床主色;机床在完成传动部分装配(不再需翻身)后,机床立放进行成品油漆。
(使用带防护吊具,生产全过程注意油漆面防护)(2)其余分体机床的上横梁、立柱、底座及VH系列、SH系列机床机身,在机加工完成后转油漆工序,外表面及内腔均按成品油漆标准进行涂装;机床装配完成后不再油漆。
(使用带防护吊具,生产全过程注意油漆面防护)4、其他部件(导轨、工作台板除外):钣金件、走台围栏、蜗轮箱、大齿轮(刷黄漆)、管路等需油漆的机床所有的其他部件,转油漆工序完成成品油漆后进行装配。
(使用带防护吊具,生产全过程注意油漆面防护)5、导轨、工作台板、滑块斑马线:所有机床的导轨、工作台板、滑块斑马线在完成性能交验合格后进行成品油漆。
(使用帆布带吊绳、台板起吊专用工装安装工作台板)二、结构件(铸件)涂装工艺规程及检验标准1、抛丸1.1对转入抛丸工序的工件进行核实确认,并规范填写《抛丸工序记录表》,保证产品的可追溯性。
1.2操作前首先检查风机、管路输送等设备是否运转正常;喷丸服、视镜是否完好、输气管是否通畅,确认合格后方可经行抛丸工序的操作。
1.3经抛丸后的工件应达到表面无锈点、氧化皮、污垢。
要求达到瑞典分级表Sa2.5级,钢面呈均匀银白色金属光泽。
ISO9001-2015油漆喷涂质量检验规范
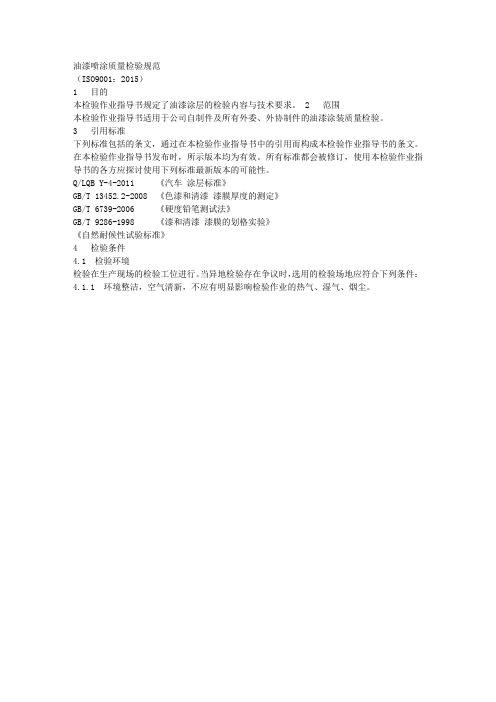
油漆喷涂质量检验规范
(ISO9001:2015)
1 目的
本检验作业指导书规定了油漆涂层的检验内容与技术要求。
2 范围
本检验作业指导书适用于公司自制件及所有外委、外协制件的油漆涂装质量检验。
3 引用标准
下列标准包括的条文,通过在本检验作业指导书中的引用而构成本检验作业指导书的条文。
在本检验作业指导书发布时,所示版本均为有效。
所有标准都会被修订,使用本检验作业指导书的各方应探讨使用下列标准最新版本的可能性。
Q/LQB Y-4-2011 《汽车涂层标准》
GB/T 13452.2-2008 《色漆和清漆漆膜厚度的测定》
GB/T 6739-2006 《硬度铅笔测试法》
GB/T 9286-1998 《漆和清漆漆膜的划格实验》
《自然耐候性试验标准》
4 检验条件
4.1 检验环境
检验在生产现场的检验工位进行。
当异地检验存在争议时,选用的检验场地应符合下列条件:4.1.1 环境整洁,空气清新,不应有明显影响检验作业的热气、湿气、烟尘。
喷漆质量检验标准(一)2024

喷漆质量检验标准(一)引言:喷漆质量检验标准是保证喷涂表面质量和涂装工艺稳定性的关键要素。
本文将介绍喷漆质量检验标准的相关内容,包括表面平整度、颜色一致性、附着力、涂层厚度和光泽度方面的检验要点。
正文:一、表面平整度检验1. 检查喷涂表面是否存在凹凸不平的现象。
2. 使用直尺或钢片检测表面是否符合正常平整度要求。
3. 检查表面是否存在鱼眼、皱纹等缺陷。
4. 利用手触摸表面检测是否存在明显的颗粒、气泡等。
二、颜色一致性检验1. 使用标准颜色卡与喷涂表面进行对比。
2. 在不同光线条件下检查颜色是否保持一致。
3. 利用专业仪器测量颜色参数,如色差、色调等。
4. 对比不同批次的喷漆,评估颜色是否一致。
三、附着力检验1. 使用划格器或者胶带进行附着力测试。
2. 进行交叉划格检验,评估涂层是否牢固。
3. 根据涂层剥离情况,确定附着力等级。
4. 检查涂层是否存在开裂、剥落等现象。
四、涂层厚度检验1. 使用合适的仪器测量涂层厚度。
2. 确保涂层厚度达到设计要求。
3. 检查涂层是否均匀,避免存在厚度梯度。
4. 对涂层厚度进行统计分析,评估涂装工艺的稳定性。
五、光泽度检验1. 使用光泽度仪测量涂层的光泽度值。
2. 对光泽度进行定量评估,确保符合标准要求。
3. 在不同角度下观察涂层反射情况,检查是否存在异物和划痕。
4. 检验光泽度是否达到设计要求,对涂装过程进行优化和改进。
总结:喷漆质量检验标准的实施对确保喷涂表面质量起着至关重要的作用。
通过对表面平整度、颜色一致性、附着力、涂层厚度和光泽度的检验,可以评估喷漆质量是否合格,从而保证涂装工艺的稳定性和产品质量的一致性。
在实施喷漆质量检验标准时,需要根据具体情况制定相应的检验方法和参数,以确保检验的准确性和可靠性。
涂装质量检验规则
涂装质量检验规则在制造和加工行业中,涂装起着非常重要的作用。
涂装能够改善产品的外观,保护产品免受腐蚀和损坏,并提供额外的耐用性。
然而,如果涂装质量不合格,可能导致产品质量下降,从而影响产品的市场竞争力和声誉。
因此,制定涂装质量检验规则对于确保产品质量和顾客满意度至关重要。
涂装质量检验规则的目的是确定涂层的质量是否符合预期标准和要求。
这些规则通常由国家或行业标准制定,涵盖了涂装的各个方面,包括涂料选择、涂布方法、涂层厚度、外观质量、附着力、耐腐蚀性能等。
以下是一些常见的涂装质量检验规则。
1. 涂料选择规则:根据不同的应用需求和环境条件,选择适合的涂料类型和配方。
例如,在室内应用中,环保型水性涂料可能是最佳选择,而在户外环境中,要求更高的耐候性的氟碳漆可能更适合。
2. 涂布方法规则:确保涂料均匀地涂布在待涂物表面上,以保证涂膜的平整度和一致性。
涂布方法可以包括刷涂、辊涂、喷涂等,具体选择取决于产品形状和要求。
3. 涂层厚度规则:涂层的厚度对于产品的性能和稳定性至关重要。
根据产品和涂装要求,测量涂层的厚度,并确保其符合规定的最小和最大要求范围。
4. 外观质量规则:涂装表面的外观直接影响产品的整体质量感和市场竞争力。
因此,在涂装过程中,需要检查和评估涂层的颜色、光泽度、平整度、表面光滑度等外观质量指标。
5. 附着力规则:涂层的附着力是衡量涂装质量的重要指标之一。
通过使用相关测试方法,检测涂层与基材之间的黏结程度和强度,以确保涂层不易剥落或剥落。
6. 耐腐蚀性能规则:特定的产品可能处于各种严峻的环境条件下,暴露于腐蚀因素。
涂装质量检验规则需要确保涂层具有足够的抗腐蚀性能,以保护产品免受腐蚀和损坏。
除了上述规则,涂装质量检验还需要在制定和实施过程中考虑以下几个关键因素。
1. 检验方法和设备:制定涂装质量检验规则时,需要确定适合该规则的检验方法和设备。
这些方法和设备可以包括颜色测量仪、涂层厚度仪、附着力测试仪等。
涂装工艺规范和检验方法
而车间底漆本身的厚度要求一般在15-20微米,所以不能直接在钢板上测量膜厚,
标准的测试方法为:
•喷砂后把光滑试板用胶带固定在钢板上,通常放置三块(如图示)
•对电子式测厚仪先进行校正。
•喷漆干燥后取下试板进行测量。
•通常按喷砂后要达到规定的干膜厚度在光滑试板上测量要高于规定值(见表)
小角落内部构件、边角和小孔的除锈。
•端型平面砂磨机Ø100 –180各种型号,可装盆形钢丝刷砂纸盘来
进行二次除锈代表性工具。
动力工具除锈处理的工艺要点
•观察打磨作业环境,做好脚手架、夜晚照明等辅助工作,准备好打磨工具、风管及接头、个人劳动保护用品。
•清理周围环境(箱体内垃圾、杂物及水)
•以上打磨工具主要对焊缝区、火工烧损区、自然锈蚀区作彻底打磨至呈现金属本色,打磨作业应先里后外,先难后易,先下后上的原则。
•用风铲将焊缝周围零星锈块和少量焊缝灰渣去除。
•清除垃圾和积灰。
表面处理的方法
•喷射除锈
(1)抛丸(前面已介绍)两种:钢板预处理流水孔和型钢处理流水孔。
(2)喷砂和喷丸(室内作为固定除锈房,室外作为移动除锈)
喷射磨料处理方式的效率高,质量好,缩短施工周期,但需要整套设备。一般原钢材的表面处理并涂上车间底漆以后,经过划线、磨料、加工、装配等阶段,最后组装成工件,在这种情况下,总有一些部分表面被焊接、切割、机械碰撞或因自然原因受到破坏,导致钢材表面重新锈蚀,所以都有一个再次进行表面处理的阶段,这就称之为二次除锈。
期涂装的施工周期(针对大型构件)。
另一阶段处理则是在钢材加工成工件后合拢成整体时,要进行涂装所
作的钢材表面处理,称之为“二次除锈”。
涂装工艺规范和检验方法
涂装工艺规范和检验方法涂装工艺规范1. 引言本涂装工艺规范是为了确保涂装工艺的统一、标准化,并提高涂装质量和效率。
本规范适合于以下涂装领域:汽车创造、家具制造、船舶涂装等。
2. 涂装前的准备工作2.1 审核涂装工艺要求:根据产品的材料、形状、颜色等要求,确定涂料的种类、厚度以及涂装步骤。
2.2 准备涂装设备:确保设备完好,操作人员熟悉设备的使用方法,进行设备的日常维护和保养工作。
2.3 准备涂料和辅助材料:选择适合的涂料品牌和种类,确保涂料的质量符合要求,准备好所需的辅助材料。
3. 涂装工艺步骤3.1 表面处理:清洁、除锈、研磨等操作,确保基材表面干净、光滑,有利于涂料附着。
3.2 底漆涂装:选择适合的底漆,并根据产品要求进行底漆涂装工作。
3.3 中涂:根据涂装要求,选择合适的中涂材料和方法进行涂装。
3.4 面漆涂装:选择适合的面漆进行涂装,保证产品表面的光泽和颜色。
3.5 烘干和固化:根据涂料厂家的要求,进行烘干和固化工作,以提高涂装效果和产品的耐久性。
4. 涂装质量检验方法4.1 外观检验:对涂装后的产品进行视觉检查,包括涂层的平整度、颜色一致性以及有无缺陷等。
4.2 涂层厚度测量:使用涂层厚度测量仪器对涂层进行厚度测量,确保涂层的厚度符合要求。
4.3 粘附力测试:使用剥离力测试仪器对涂层的粘附力进行测试,确保涂层与基材之间的粘附力良好。
4.4 耐候性测试:将涂装后的产品放置在恶劣的气候条件下,进行耐候性测试,评估涂层的耐久性。
5. 附件本所涉及附件如下:附件1:涂装工艺流程图附件2:涂料供应商信息表附件3:涂层厚度测量记录表附件4:外观检验标准表6. 法律名词及注释无---------------------------------------------------涂装工艺检验方法1. 引言涂装工艺的检验是为了确认产品的涂装质量、稳定性和耐久性。
本详细介绍了涂装工艺的各个检验项目和方法。
表面涂装通用检验规程
KX/PZ01-2015表面涂装检验通用规程1、目的规范表面油漆涂装检验标准,确保表面涂装质量满足规定要求。
2、适用范围适用于凯旋公司灭火设备产品的表面油漆涂装产品3、引用标准油漆过程确认准则GY-PY-45-00色漆清漆漆膜的划格试验GB/T92864、管理规定4.1 原辅物料验证4.1.1涂装用油漆、原子灰、稀释济的合格证、质量保证书、使用说明书、有效期等;底漆、色漆、面漆三者相容,型号符合技术规定要求;4.1.2调配好后待喷涂油漆粘度验证4.1.2.1用棒挑起测量:油漆经充分搅拌后,用棒挑起涂料进行观察。
涂料用棒挑起连接距离为30~50cm应自由降落而不断,如有中断而回缩现象,说明该涂料较稠,需用稀释剂进行稀释。
小于30cm,表明涂料粘度太小,即涂料太稀;大于50cm,表明粘度太大。
4.1.2.2用涂-4杯进行测量:环境温度在21-25℃时,油漆粘度控制在30-90S之间,低于此温度粘度偏低档,高于此温度粘度偏高档;油漆粘度控制在40-60S之间。
4.2 环境要求喷漆环境防尘、防雨、阳光直射不到,通风良好,涂装温度范围10ºC~30ºC,相对湿度在85%以下,油漆工件表面温度高于露点温度3ºC。
4.3 喷涂压力要求喷漆用进喷漆罐压力在0.4-0.8MPa之间。
4.4 喷防锈漆工件表面要求工件喷防锈漆时,表面无焊渣、颗粒、焊接药皮、焊接气孔、油、污、氧化皮、水痕等影响喷漆质量的缺陷,并用压缩空气吹净工件表面灰尘4.5喷底漆验证在底漆干透后,检查底漆的喷涂质量,表面无漏喷、流挂、拉痕、颗粒、起泡及明显桔皮等缺陷。
对油漆部位表面凹坑、划痕等缺陷,原子灰已填充处理,在原子灰干透后,再对表面用砂纸进行打磨,吹净表面灰尘,使表面外观质量满足面漆要求。
4.6 喷色漆或面漆验证在底漆(含原子灰)完全干透并确认喷漆部位无缺陷后再喷色漆或面漆,在色漆或面漆干透后,表面质量应是涂层饱满,无漏喷、流挂、颗粒、起泡、针孔、渗色、失光、桔皮等油漆缺陷。
- 1、下载文档前请自行甄别文档内容的完整性,平台不提供额外的编辑、内容补充、找答案等附加服务。
- 2、"仅部分预览"的文档,不可在线预览部分如存在完整性等问题,可反馈申请退款(可完整预览的文档不适用该条件!)。
- 3、如文档侵犯您的权益,请联系客服反馈,我们会尽快为您处理(人工客服工作时间:9:00-18:30)。
涂装质量检验规范1 目的为有效控制涂装作业的正常生产,确保产品质量,提高效益,防止因涂装不当导致结构件的防腐保护失效。
2 范围本标准规定了对涂装进行质量检验时应遵循的基本原则和控制内容。
本标准适用于涂装的质量控制,工艺纪律管理(基本要求、主要内容及考核办法)。
3 引用标准下列标准所包含的条文,通过在本标准中引用而构成为本标准的条文。
本标准出版时,所示版本均为有效。
所有标准都会被修订,使用本标准的各方应探讨使用下列标准最新版本的可能性。
GB/T 10300.5 质量管理和质量体系要素指南JB/Z 220 工序质量控制通则GB/T 19023 质量管理体系文件指南Q/XZ 200-2008 质量手册GB/T 15498 企业标准体系JB/T 5059-1991 特殊工序质量控制导则4涂装检验的基本原则4.1 涂装过程在整个工作期间易受操作者差错或有害环境的影响。
另外,要通过检查已完成的工作发现存在何种问题通常较为困难。
因此,在工作完成后再进行质量控制就不是一件容易的事。
检查人员(或任何质量控制人员)必须在工作进行过程中位于现场,并且对其进行始终如一的观察评价,才能对涂装过程作出准确判断。
4.2 操作人员、检验人员要经过技术培训和资格认证。
4.3 应对工作环境(杂质、温度、湿度、露点等)进行控制,以满足工艺文件的要求,必要时应加以验证。
4.4 检验和施工应严格遵循技术规范和质量管理等文件的要求,严格控制工艺参数及影响参数波动的各种因素,使涂装过程处于受控状态。
同时加强工艺方法的试验验证和反馈。
4.5 所用工艺材料、被加工物资应实行严格控制,必要时应进行复检。
4.6 必须使用经确认合格的模具、工装、设备和计量器具,并积极采用先进的检测技术和控制手段,对影响质量特性的主要因素进行快速、准确的检测和调整,减少质量波动。
4.7 检验员应检查涂装施工的整个过程,检查重点应放在表面处理和涂装施工的起始,以加强过程控制为主,辅以必要的多频次的工序检查,检查人员与质量保证人员对现场操作负有监督的责任和权限。
4.8 应从涂装流程分析着手,找出各环节(或分工序)影响质量特性的主要因素,研究控制方法,配备适当手段,进行工序过程的系统控制。
特别工序应遵循“点结合”的原则,在系统控制的基础上,对关键环节进行重点控制。
4.9 质保工程师对质量实施见证性审核,对工序加工中操作者是否处于自控状态,检验员是否忠于职守,图纸、工艺文件是否有效贯彻,工序加工质量是否符合规定要求等方面进行监督性检查,以确保现场质量控制的有效性。
4.10 涂装质量检验的严格程度应视产品的类型、用途、用户的要求、生产条件等情况而有所区别,允许结合本企业的具体情况,使用不同的控制方法。
4.11 检验人员应认真、如实、完整地填写原始记录,并按规定程序签名、处理、传递和保管,使之具有可追溯性。
5涂装检验的主要内容5.1 工艺规程等技术文件5.1.1 除明确工艺参数外,还应对工艺参数的控制方法、工作介质、设备和环境条件等作出具体的规定。
5.1.2 工艺规程必须经验证认可并符合有关标准。
主要工艺参数的变更,必须经过充分试验验证或专家论证合格后,方可更改文件。
5.1.3 对特殊工序,根据不同产品的技术要求和工艺特点,可在工序流程的必要环节设置控制点,进行重点控制。
控制点可按零件的质量特性、工序或设备来设置。
5.1.4 对控制点应进行工序质量分析和验证,找出主要影响因素,明确控制方法,并进行连续评价。
控制点的工艺文件应包含质量控制的内容,如对控制的项目、内容、方法、检测频次、检查方法、记录及测定人员等做出具体规定。
5.1.5 工艺部门应根据质量控制要求,编制原始记录表格并规定填表要求,包括让检验人员、质保人员对工艺参数和操作状况进行检查、监督、认定、签字的要求。
例如,可编制工艺参数核对表、检查卡、关键件的履历卡等。
主要原始记录表格应汇总归档,并规定制件加工档案的保存期限,以备查考。
5.1.6 规定并执行工艺文件的编制、评定和审批程序,以保证生产现场所使用文件的正确、完整、统一性。
5.1.7 制订并执行技术文件的保管、使用、更改和销毁制度(或标准)。
文件更改的审批程序应与原文件的审批程序相同,重要的更改应有试验验证。
5.2 人员的培训和考核5.2.1 特殊工序的操作、检验人员必须经过定期考核和培训,并持有上岗操作证。
对有特殊要求的关键岗位,必须选派经专业考核合格、有现场质量控制知识、经验丰富的人员担任。
5.2.2 明确规定特殊工序操作、检验人员应具备的专业知识和操作技能,组成技术考核委员会进行理论和实际操作的考核,各项成绩应填入考核档案,合格者发给相应的上岗操作证。
5.3 设备、仪表和工艺装备5.3.1 特殊工序使用的设备、仪器仪表和工艺装备必须符合工艺规程的要求。
5.3.2 工艺装备必须按规定进行验收、验证(或试用)合格后,方可使用。
5.3.3 新制、改进或大修后的设备和仪器仪表应按其技术条件验收,经调试、鉴定合格签证后,方可正式投入使用。
5.3.4 设备必须完整、配套,配有显示(或自动控制)工艺参数的检测、计量仪器仪表。
各种供监控用的仪表,一般应按其功能分别设置。
必要时,还应配备工艺参数自动记录仪和安全报警装置。
5.3.5 制订和执行设备、工艺装备的维修保养,仪器仪表的定期检定、校准制度。
设备主管部门应建立设备使用、点检、维修和校准的技术档案。
工装主管部门应对主要工装建立使用维修技术档案。
5.3.6 控制点的设备、工装应加以重点控制,以尽量减少设备及工装的误差引起的质量波动。
5.4 环境5.4.1 环境条件(厂房内温度和湿度,压缩空气的压力和洁净度,施工现场的风速和杂质等)应满足工艺技术文件的要求。
5.4.2 作业场所应配置有效的进、排风系统及安全技术措施,厂房空气中有害物质的最高浓度应符合有关规定。
5.4.3 应对车间一些重要的噪声源设施(如通风机、空气压缩机、抛丸机等)采取适宜的减噪或隔音措施,以控制车间的环境噪声在85dB 以下。
5.4.4 车间应有良好的自然采光或照明,操作工位应有足够的照度。
5.4.5 含有害物质的废水、废气、废渣必须进行有效的净化处理,三废排放标准应符合国家对环境保护的有关规定。
5.4.6 车间应配置必要的安全、防护设施,作业场地必须遵守防火和技术安全制度的规定。
5.5 工艺材料5.5.1 工艺材料的采购文件应明确规定物品规格、材质和技术要求,必要时,还应提出质量保证的要求。
5.5.2 重要工艺材料应严格按规定的技术要求择优定点采购。
采购部门选点时,必须经质量管理部门组织有关部门人员对供应厂进行质量考察,并经试用验证认可后才能定点。
5.5.3 进厂工艺材料必须有制造单位的合格证明文件,重要材料必须按规定复验,无合格证或复验不合格的材料禁止入库和使用。
5.5.4 超过保管期限的材料必须按规定重新复验,办理延期使用文件,经审批后方可使用。
5.5.5 应提供符合工艺材料使用要求的贮存场所和配套设施,并建立严格的保管、标志、发放、使用和回收制度。
5.5.6 使用中的各种材料必须按技术文件的要求进行定期分析,保证其成分在规定的范围内。
对不符合技术要求的材料应进行调整或更换,不合格者不准用于生产。
5.5.7 采用新牌号的重要工艺材料应进行试验及生产验证,提出试验验证报告,经主管部门组织鉴定审批后方可使用。
5.6 被加工物质的确认5.6.1 转入本工序的被加工物质必须符合技术文件的规定,并具有合格证明文件。
必要时进行抽查复验。
5.6.2 制定适用于本厂生产要求的外购物质标准,规定物质规格和技术要求,以及进厂入库的取样、检验项目和方法。
5.6.3 重要的外购物质应择优定点采购,并进行进厂复验。
必要时,应对供应厂进行质量保证能力的考察和监督,并建立合格供方的技术质量档案。
5.6.4 应建立进料验证、入库、保管、标志、发放制度,并认真执行。
5.7 工艺过程5.7.1 加工前,操作人员应熟悉工艺规程,严格按工艺规程作好各项准备工作,包括设备、材料、介质、环境条件的检查,进行各种预处理,工艺参数的试样验证等,并作好原始记录。
对特殊的关键件,工艺人员应向操作人员进行技术交底,以保证操作人员真正掌握。
5.7.2 严格按工艺规程操作。
工件的装卡、摆放,工艺参数的调整,试样的抽取、检验和保管等应根据不同物质的技术要求,按工艺规程的有关条款执行。
5.7.3 应认真、如实、完整地填写原始记录,并按规定程序签名、处理、传递和保管。
5.7.4 操作中应密切注意加工情况,如发现问题,应立即自行或通知有关部门采取有效措施予以解决,并作好原始记录。
5.7.5 每批制件必须进行首件检查,并作好标记,填写首件记录卡,并在记录上签章。
5.7.6 检验员应对生产现场进行巡回检查,对工艺的执行和原始记录的记录情况进行监督,抽检制件的加工质量,做好监督检查记录。
对巡检中发现的质量问题,应督促有关人员及时纠正。
5.7.7 关键件加工中的主要分工序,根据需要可设立“见证点”,由对质量不负直接责任的质保工程师实施见证性审核。
对工序加工中操作者是否处于自控状态,检验员是否忠于职守,图纸、工艺文件是否有效贯彻,工序加工质量是否符合规定要求等方面进行监督性检查,以确保现场质量控制的有效性。
5.7.8 制件在工序间的存放、周转与运输,应按定置管理规定及质量标准加以控制,并备有适用的工位器具和储运设备,防止损伤制件。
5.8 工艺纪律5.8.1 职能部门职责5.8.1.1 企业要有健全、统一、有效的工艺管理体系和完整、有效的工艺管理制度及各类人员岗位责任制。
5.8.1.2 技术部门必须做到工艺文件:正确、完整、统一、清晰。
5.8.1.3 生产部门对生产安排必须以工艺文件为依据,并做到均衡生产。
5.8.1.4 凡投入生产的材料、毛坯和外购件、外协件,供应部门必须保证符合设计和工艺要求。
5.8.1.5 设备部门:设备必须确保正常运转、安全、可靠,所有工艺装备应经常保持良好的技术状态。
5.8.1.6 计量器具应坚持周期检定,以保证量值正确、统一。
5.8.1.7 要有专业培训制度,做到工人初次上岗前必须经过专业培训。
做到定人、定机、定工种。
5.8.2 生产现场工艺纪律5.8.2.1 操作者要认真做好生产前的准备工作,生产中必须严格按设计图样、工艺规程和有关标准的要求进行加工、装配。
对有关时间、温度、压力、真空度、电流、电压、材料配方等工艺参数,除严格按规定执行外,还应做好记录,以便存档备查。
5.8.2.2 设备的操作者和检验人员等必须经过严格考核,合格后发给操作证,凭操作证工作。
5.8.2.3 新工艺、新技术、新材料和新装备必须经验证、鉴定合格后纳入工艺文件方可正式使用。