甲醇制烯烃的相关工艺
甲醇制烯烃生产工艺

甲醇制烯烃生产工艺甲醇制烯烃是将甲醇转化为烯烃的一种工艺。
烯烃是一类重要的有机化工原料,广泛应用于合成塑料、橡胶、纤维等领域。
以下将介绍甲醇制烯烃的生产工艺。
首先,甲醇制烯烃的关键步骤是通过甲醇脱氢反应生成烯烃。
脱氢反应通常在催化剂存在下进行。
常用的催化剂包括氧化铜-锌(Cu-Zn-O)催化剂、模型选区氧化镁(MOx)催化剂和氧化铝(Al2O3)载体上的甲醇蒸汽重整催化剂等。
甲醇脱氢反应的条件是高温和低压。
通常反应温度在400℃~600℃之间,反应压力在0.1~1.0 MPa之间。
在这些条件下,甲醇分子发生脱氢反应,生成一氧化碳和氢气,同时还会生成一系列的烯烃产物。
接下来,脱氢反应产生的一氧化碳和氢气需要进行增氢反应才能转化为烯烃。
增氢反应通常在氧化铝载体上的催化剂存在下进行。
常用的催化剂有氧化镁(MOx)和氧化铝(Al2O3)催化剂等。
增氢反应的条件是中温和中压。
一氧化碳和氢气在催化剂上发生增氢反应,生成了一系列的烯烃产品。
这些烯烃产品可通过分离和精馏等方式得到纯度较高的产物。
甲醇制烯烃最大的难点是选择合适的催化剂和控制反应条件。
对于不同类型的催化剂,需要探索合适的反应温度、压力和甲醇的进料速率等工艺参数,以达到最佳的反应效果和产物选择性。
甲醇制烯烃的生产工艺还面临着一些挑战。
首先,催化剂具有一定的寿命,需要进行周期性的再生和更换;其次,反应过程中会生成一些副产物,如甲烷、乙烷等,需要通过后续的处理步骤进行处理。
此外,甲醇制烯烃是一个高温、高压的反应过程,对设备和安全管理提出了更高的要求。
总之,甲醇制烯烃是一种重要的有机合成工艺,可以将甲醇转化为烯烃原料。
通过选择合适的催化剂和控制反应条件,可以实现高效、高选择性的烯烃产物得到。
这种工艺的应用在化工行业具有广阔的前景。
甲醇制烯烃几种工艺比较培训

甲醇制烯烃几种工艺比较培训甲醇制烯烃是一种重要的化工过程,可以将甲醇转化为乙烯和丙烯等烯烃化合物,具有广泛的应用前景。
目前,甲醇制烯烃的工艺主要有热解法、氧化法和水蒸汽法等几种。
本文将对这几种工艺进行比较。
首先是热解法。
热解法是最早研发出来的甲醇制烯烃工艺,通过在高温条件下将甲醇分解产生烯烃。
这种方法的优点是反应温度较高,可以提高反应速率,同时产物中的乙烯和丙烯的选择性较好。
然而,热解法存在一些缺点,比如氧化剂的消耗量大,并且产生大量的副产品和废气,对环境造成污染。
其次是氧化法。
氧化法是通过加入氧化剂使甲醇发生氧化反应产生乙烯和丙烯。
这种方法的优点是反应条件相对温和,反应速率较快,可以实现大规模生产。
而且,氧化法能够实现对原料的充分利用,减少了废物的产生。
然而,氧化法的不足之处在于选择性较差,产物中会含有大量的其他氧化产物,且需要大量的氧化剂,经济性较差。
最后是水蒸汽法。
水蒸汽法是将甲醇和水蒸汽共同通过催化剂进行反应,生成乙烯和丙烯。
该工艺的优点在于反应条件温和,选择性较好,产生的副产品较少。
此外,水蒸汽法相对环保,不会产生废气污染。
然而,水蒸汽法也存在一些问题,比如催化剂的寿命较短,需要经常更换。
此外,该工艺的过程复杂,工艺设备投资较大。
综上所述,甲醇制烯烃的几种工艺各有优劣。
热解法反应速率快、选择性好,但是对环境造成严重污染;氧化法可以实现大规模生产,但是选择性较差;水蒸汽法环保,并且产物选择性好,但是催化剂寿命较短。
因此,在实际应用中,需要根据具体情况选择适合的工艺,并对其进行改进和优化,以提高生产效率和经济效益。
甲醇制烯烃是一种重要的化工过程,在石化工业中具有广泛的应用前景。
乙烯和丙烯是石化工业中最重要的两种烯烃化合物,广泛应用于塑料、合成纤维、橡胶、涂料及胶粘剂等领域。
甲醇制烯烃技术的发展,对于满足烯烃需求、降低石化行业的碳排放、提高能源利用效率具有重要的意义。
目前,甲醇制烯烃的工艺主要有热解法、氧化法和水蒸汽法等。
甲醇制烯烃技术报告(非常好)

1 甲醇制烯烃1.1 工艺技术方案的选择1.1.1 甲醇制烯烃工艺技术1.1.1.1 原料路线确定的原则和依据甲醇制乙烯、丙烯等低碳烯烃(Methanol-to-Olefin,简称MTO)是最有希望替代石脑油为原料制烯烃的工艺路线,目前工艺技术开发已趋于成熟。
该技术的工业化,开辟了由煤炭或天然气经气化生产基础有机化工原料的新工艺路线,有利于改变传统煤化工的产品格局,是实现煤化工向石油化工延伸发展的有效途径。
甲醇制烯烃的反应比较复杂,在高选择性催化剂上,MTO主要发生如下放热反应:2CH3OH CH3OCH3+H2O12CH3OH C2H4+ 2C3H6+ C4H8+12H2O6CH3OCH3C2H4+ 2C3H6+ C4H8+6H2O本项目采用煤炭气化制甲醇,甲醇制烯烃的生产路线。
1.1.1.2 国内、外工艺技术概况(1) 国外工艺技术概况二十世纪八十年代初,美国美孚(Mobil)公司在研究采用沸石催化剂利用甲醇制汽油(MTG)工艺的过程中发现并发展甲醇制烯烃(MTO)工艺。
Mobil对反应机理进行了细致的研究,优化催化剂,合成了针对MTO和MTG反应的新型沸石催化剂ZSM-5。
Mobil基于流化床的工艺示范装置自1982年底运行至1985年末,成功地证明了流化床反应系统可以应用于MTG和MTO过程。
Mobil甲醇制汽油技术的成功开发推动了甲醇制烯烃(MTO)、甲醇制丙烯(MTP)等工艺的开发。
目前,国外的工艺技术中,由※※※※/※※※※公司共同开发的MTO 工艺、由Lurgi公司开发的MTP工艺最具有产业化前景。
1986年UCC发现采用SAPO-34(磷酸硅铝分子筛)可以有效地将甲醇转化为低碳烯烃,而后UCC将相关技术转让给了※※※※公司。
1992年※※※※和Norsk※※※※合作开发了以多孔性MTO-100(主要活性组分为SAPO-34)为催化剂的※※※※/※※※※工艺,MTO-100催化剂具有更好稳定性和耐磨性。
dmto-ⅲ合成烯烃工艺

dmto-ⅲ合成烯烃工艺
DMTO(Dimethyl Ether to Olefins)是一种将甲醇转化为烯烃的工艺。
它是一种通过催化剂使甲醇分子断裂,并在特定温度和压力条件下重新组合为烯烃的方法。
DMTO工艺包括以下几个步骤:
1. 烷基化:将甲醇加入到催化剂中,催化剂通常是沸石类材料。
在高温下,催化剂将甲醇分子分解成甲基和氢分子。
2. 烯烃生成:甲基与催化剂表面上的其他甲基或烯烃中的碳氢键进行反应,形成烯烃和水。
这些烯烃可以是乙烯、丙烯等。
3. 烯烃分离:生成的混合物经过分离和纯化步骤,将烯烃单独提取出来。
DMTO工艺具有以下优点:
1. 原料广泛:DMTO工艺可以使用甲醇作为主要原料,而甲醇可以从多种来源获得,包括天然气、煤炭等。
2. 产品多样:DMTO工艺可以生产多种烯烃产品,包括乙烯、丙烯等,这些产品在化工工业中有广泛的应用。
3. 环保高效:DMTO工艺相较于传统的烯烃制备工艺,排放的污染物较少,能耗较低。
4. 市场前景广阔:随着对可替代能源和化工产品的需求日益增长,DMTO工艺的市场前景广阔。
然而,DMTO工艺也存在一些挑战,包括烯烃选择性、催化剂的稳定性和寿命等问题。
因此,进一步的研究和改进仍然需要进行,以提高工艺的效率和经济性。
甲醇制烯烃工艺技术
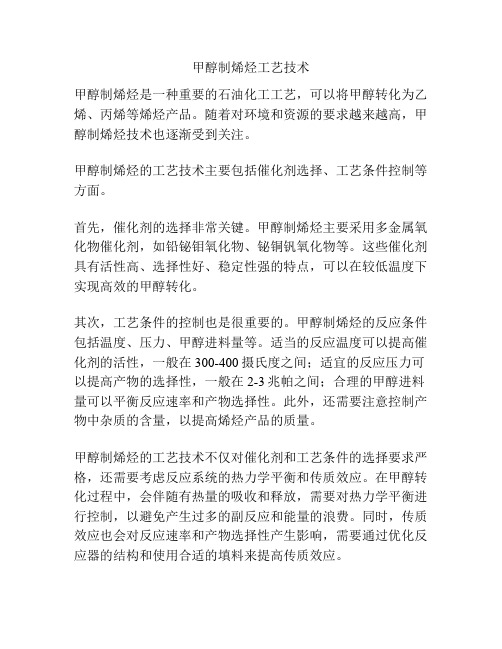
甲醇制烯烃工艺技术甲醇制烯烃是一种重要的石油化工工艺,可以将甲醇转化为乙烯、丙烯等烯烃产品。
随着对环境和资源的要求越来越高,甲醇制烯烃技术也逐渐受到关注。
甲醇制烯烃的工艺技术主要包括催化剂选择、工艺条件控制等方面。
首先,催化剂的选择非常关键。
甲醇制烯烃主要采用多金属氧化物催化剂,如铅铋钼氧化物、铋铜钒氧化物等。
这些催化剂具有活性高、选择性好、稳定性强的特点,可以在较低温度下实现高效的甲醇转化。
其次,工艺条件的控制也是很重要的。
甲醇制烯烃的反应条件包括温度、压力、甲醇进料量等。
适当的反应温度可以提高催化剂的活性,一般在300-400摄氏度之间;适宜的反应压力可以提高产物的选择性,一般在2-3兆帕之间;合理的甲醇进料量可以平衡反应速率和产物选择性。
此外,还需要注意控制产物中杂质的含量,以提高烯烃产品的质量。
甲醇制烯烃的工艺技术不仅对催化剂和工艺条件的选择要求严格,还需要考虑反应系统的热力学平衡和传质效应。
在甲醇转化过程中,会伴随有热量的吸收和释放,需要对热力学平衡进行控制,以避免产生过多的副反应和能量的浪费。
同时,传质效应也会对反应速率和产物选择性产生影响,需要通过优化反应器的结构和使用合适的填料来提高传质效应。
甲醇制烯烃工艺技术的发展离不开催化剂和反应器的创新。
目前,研究人员正在尝试开发新型的催化剂,以提高甲醇的转化率和产物的选择性。
同时,也在努力改进反应器的结构和工艺,以提高反应效率和降低能源消耗。
综上所述,甲醇制烯烃是一项有前景的石油化工工艺,其工艺技术的发展将有助于提高能源利用效率和化石能源的可持续利用。
随着科技的进步和环境保护意识的增强,相信甲醇制烯烃工艺技术将会得到更广泛的应用和发展。
甲醇制烯烃工艺流程设计与工艺优化

甲醇制烯烃工艺流程设计与工艺优化甲醇制烯烃是一种重要的工业化学反应过程,通过将甲醇转化为烯烃,可以用于合成高附加值的石化产品。
本文将探讨甲醇制烯烃的工艺流程设计和工艺优化,以提高产率和降低成本。
一、工艺流程设计甲醇制烯烃的工艺流程包括催化剂选择、反应器设计、产品分离等环节。
首先,催化剂的选择对甲醇转化效率和烯烃产率至关重要。
目前常用的催化剂有ZSM-5、SAPO-34等,选择合适的催化剂能够提高反应效果。
其次,反应器设计是工艺流程中的关键环节。
反应器的结构和尺寸需要根据反应物质的特性和反应条件进行优化。
在甲醇制烯烃反应中,温度、压力、空速等条件的控制对反应效果有直接影响。
合理设计反应器可以增加反应物料与催化剂的接触时间,提高反应转化率。
最后,产品分离是工艺流程中的最后一步,也是最关键的一步。
由于甲醇制烯烃反应产物的组分复杂性和挥发性等特点,需要选择适宜的分离技术,如精馏、吸附等。
通过优化产品分离工艺,可以提高产品的纯度和产率。
二、工艺优化工艺优化是为了改进工艺流程,提高产率、降低成本和环境污染。
在甲醇制烯烃工艺中,有几个关键方面可以进行优化。
首先,反应条件的优化是关键。
通过调节反应温度、压力和催化剂用量等参数,可以提高甲醇转化率和烯烃选择性。
此外,气体分子扩散速率、反应速率等因素也需要考虑,以达到最佳的反应条件。
其次,催化剂的改进也是工艺优化的重要方面。
通过改变催化剂的活性元素含量、物理结构等参数,可以调节催化剂对甲醇和烯烃的选择性和活性,提高反应效果。
另外,废弃物的处理也是工艺优化的重要环节。
甲醇制烯烃过程中会产生一定量的废弃物,如水、二甲醚等。
合理处理这些废弃物可以减少对环境的污染,并回收利用其中的有价值物质。
三、案例分析以ZSM-5催化剂为例,进行甲醇制烯烃工艺流程设计与工艺优化的案例分析。
在工艺流程设计方面,选择合适的反应器结构和温度、压力等参数,以最大程度提高甲醇转化率和烯烃产率。
同时,利用先进的分离技术,如吸附、晶体分离等,提高产品纯度。
甲醇制烯烃工艺技术
甲醇制烯烃工艺技术目录第一章绪论 (3)第一节概述 (3)一.烯烃、聚烯烃市场分析 (3)二.竞争力分析 (4)第二节主要产品简介 (4)一.甲醇的物理化学性质和用途 (5)二.乙烯的物理化学性质和用途 (6)三.丙烯的物理化学性质和用途 (6)四.聚乙烯的物理化学性质和用途 (7)五.聚丙烯的物理化学性质和用途 (8)第二章甲醇制烯烃工艺技术的发展概况 (11)第一节甲醇制烯烃工艺技术简介 (11)第二节甲醇制烯烃工艺技术的发展状况及趋势 (11)一.甲醇制乙烯、丙烯(MTO) (11)二.甲醇制丙烯(MTP) (13)第三章甲醇制烯烃 (16)第一节甲醇制烯烃的基本原理 (16)一.反应方程式 (16)二.反应机理 (17)三.反应热效应 (18)四.MTO反应的化学平衡 (19)五.MTO反应动力学 (19)第二节甲醇制烯烃催化剂 (20)一.分子筛催化剂的研究 (20)二.分子筛催化剂的制备 (23)三.分子筛催化剂的再生 (27)第三节甲醇制烯烃工艺条件 (27)一.反应温度 (27)二.原料空速 (28)三.反应压力 (28)四.稀释剂 (28)第四节甲醇制烯烃工艺流程及主要设备 (29)一.MTO工艺流程及主要设备 (29)二.MTP工艺流程及主要设备 (40)第四章甲醇制烯烃工艺路线的选择 (42)一、技术条件 (42)二、工业化应用现状 (42)三. 经济性对比 (43)四. 工艺技术的选择 (44)第五章聚烯烃工艺简介 (45)第一节聚乙烯工艺技术简介 (45)一、LDPE 生产工艺 (45)二、LLDPE/HDPE生产工艺 (45)三、聚乙烯工艺技术 (47)第二节聚丙烯工艺技术简介 (51)一.聚丙烯工艺技术介绍 (51)二.聚丙烯工艺技术 (52)第一章绪论第一节概述乙烯、丙烯等低碳烯烃是重要的基本化工原料,随着我国国民经济的发展,特别是现代化学工业的发展对低碳烯烃的需求日渐攀升,供需矛盾也将日益突出。
甲醇制烯烃工艺流程
甲醇制烯烃工艺流程
《甲醇制烯烃工艺流程》
甲醇制烯烃是一种重要的化工生产工艺,在化工行业有着广泛的应用。
甲醇可以通过催化转化成更高附加值的烯烃产品,这种工艺流程被广泛应用于能源化工领域。
下面将介绍甲醇制烯烃的工艺流程。
首先,甲醇和水蒸汽进入蒸汽重整器,在高温高压下通过催化剂转化成合成气(CO和H2)。
接着,合成气进入低温反应器,通过催化剂进行升压反应,生成甲醇。
然后将甲醇进一步转化成烯烃产品。
这个过程中会产生大量的余热,这些余热可以用于蒸汽重整器和低温反应器,提高能源利用率。
整个工艺流程中,催化剂的选择和工艺条件的控制非常关键。
合适的催化剂可以提高反应选择性和产物纯度,提高产物的附加值。
同时,控制好反应的温度、压力和进料物料配比,可以保证反应的高效进行。
此外,还需要考虑工艺流程中的废水处理、废气处理和废渣处理等环保问题。
合理的废水处理和废气处理系统可以保证工艺生产的环境友好性,符合国家环保政策和标准。
总的来说,《甲醇制烯烃工艺流程》是一个复杂的工艺系统,需要多个环节的协调运作,才能够高效稳定运行。
随着科技的不断进步,甲醇制烯烃工艺也在不断进行改进,从而提高产物的质量和工艺的稳定性。
甲醇制烯烃工艺流程
甲醇制烯烃工艺流程甲醇制烯烃工艺流程包括甲醇转化单元和烯烃回收单元。
甲醇转化单元通过流化床反应器将甲醇转化为烯烃,再进入烯烃回收单元中将轻烯烃回收,得到主产品乙烯、丙烯,副产品为丁烯、C5以上组分和燃料气。
其中,反应温度为400-500℃,反应压力为0.1-0.3MPa,再生温度为600-700℃,再生压力为0.1-0.3MPa。
主要工艺条件是在高选择性催化剂上,MTO发生两个主反应:2CH3OH→C2H4+2H2OH=△-11.72kJ/mol和3CH3OH→C3H6+3H2OH=△-30.98kJ/mol。
催化剂为D803C-II01。
烯烃回收单元包括进料汽化和产品急冷区、反应/再生区、蒸汽发生区、燃烧空气和废气区几部分。
其中,进料汽化和产品急冷区包括甲醇进料缓冲罐、进料闪蒸罐、洗涤水汽提塔、急冷塔、产品分离塔和产品/水汽提塔。
反应器出口物料经冷却后送入急冷塔,闪蒸罐底部少量含水物料进入氧化物汽提塔中。
一些残留的甲醇被汽提返回到进料闪蒸罐。
急冷塔用水直接冷却反应后物料,同时也除去反应产物中的杂质。
水是MTO反应的产物之一,甲醇进料中的大部分氧转化为水。
MTO反应产物中会含有极少量的醋酸,冷凝后回流到急冷塔。
为了中和这些酸,在回流中注入少量的碱(氢氧化钠)。
为了控制回流中的固体含量,由急冷塔底抽出废水,送到界区外的水处理装置。
急冷塔顶的气相送入产品分离器中。
产品分离器顶部的烯烃产品送入烯烃回收单元,进行压缩、分馏和净化。
自产品分离器底部出来的物料送入水汽提塔,残留的轻烃被汽提出来,在中间冷凝器中与新鲜进料换热后回到产品分离器。
汽提后底部的净产品水与进料甲醇换热冷却到环境温度,被送到界区外再利用或处理。
洗涤水汽提塔底主要是纯水,送到轻烯烃回收单元以回收MTO生成气中未反应的甲醇。
水和回收的甲醇返回到氧化物汽提塔,在这里甲醇和一些被吸收的轻质物被汽提,送入进料闪蒸罐。
汽提后的水返回氧化物汽提塔。
甲醇制烯烃工艺流程设计与产率提高
甲醇制烯烃工艺流程设计与产率提高甲醇制烯烃工艺是一种重要的烃化工过程,可以通过催化剂将甲醇转化为乙烯和丙烯等烯烃产品。
本文将介绍甲醇制烯烃的工艺流程设计,并探讨提高产率的方法。
一、甲醇制烯烃工艺流程设计甲醇制烯烃的工艺流程一般包括甲醇脱水制取白炭黑、白炭黑催化裂化以及烯烃分离等步骤。
1. 甲醇脱水制取白炭黑甲醇脱水是制取白炭黑的关键步骤。
常用的方法是在合适的催化剂存在下,将甲醇加热脱水生成甲烯和水。
该反应需要在适当的温度和压力条件下进行,以提高产率和选择性。
同时,对于催化剂的选择和活性的保持也是关键。
2. 白炭黑催化裂化白炭黑催化裂化是将甲醇分解为乙烯和丙烯等烯烃的重要步骤。
在催化剂的作用下,甲醇分子发生裂解并生成烯烃产品。
选择合适的催化剂对产率和选择性都至关重要。
3. 烯烃分离烯烃与其他副产物需要经过分离步骤进行有效的分离。
传统的分离方法包括蒸馏、吸附和结晶等。
针对不同的烯烃和副产物,可以采用不同的分离组合,以提高产率和纯度。
二、提高产率的方法为了提高甲醇制烯烃的产率,可以从以下几个方面进行考虑和优化。
1. 催化剂选择和改进催化剂的选择和活性对于甲醇制烯烃的产率至关重要。
通过合理选择催化剂并对其进行改进,可以提高反应的速率和选择性,从而提高产率。
此外,催化剂的稳定性和寿命也需要考虑,以保证长期稳定的生产。
2. 工艺条件优化工艺条件的选择和优化对于提高产率非常重要。
例如,适当的反应温度和压力可以提高反应速率和产率。
此外,反应过程中的流量、停留时间、催化剂的用量等参数也需要进行优化,以达到最佳的效果。
3. 副产物的深度利用甲醇制烯烃过程中会产生一些副产物,如甲烷和二甲醚等。
合理利用这些副产物可以提高整体产率。
例如,将甲烷用作燃料供应给反应器,可以提高热能利用率。
而将二甲醚转化为更有价值的烯烃产品,则可以进一步提高产率。
4. 采用新的技术和装置随着科技的进步,新的技术和装置可以帮助提高甲醇制烯烃的产率。
- 1、下载文档前请自行甄别文档内容的完整性,平台不提供额外的编辑、内容补充、找答案等附加服务。
- 2、"仅部分预览"的文档,不可在线预览部分如存在完整性等问题,可反馈申请退款(可完整预览的文档不适用该条件!)。
- 3、如文档侵犯您的权益,请联系客服反馈,我们会尽快为您处理(人工客服工作时间:9:00-18:30)。
甲醇制低碳烯烃的工艺举例以及本组最佳工艺的确定一、甲醇制低碳烯烃的工艺列举甲醇制烯烃工艺是煤基烯烃产业链中的关键步骤,其工艺流程主要为在合适的操作条件下,以甲醇为原料,选取适宜的催化剂(ZSM-5沸石催化剂、SAPO-34分子筛等),在固定床或流化床反应器中通过甲醇脱水制取低碳烯烃。
根据目的产品的不同,甲醇制烯烃工艺分为甲醇制乙烯、丙烯(methanol-to-olefin ,MTO ),甲醇制丙烯(methanol-to-propylene ,MTP )。
MTO 工艺的代表技术有环球石油公司( UOP )和海德鲁公司( Norsk Hydro )共同开发的UOP/Hydro MTO 技术,中国科学院大连化学物理研究所自主创新研发的DMTO 技术;MTP 工艺的代表技术有鲁奇公司(Lurgi )开发的Lurgi MTP 技术和我国清华大学自主研发的FMTP 技术。
1.1 UOP /I-Iydro 公司的MTO 工艺美国环球油品公司(UOP)和挪威海德鲁(Hydro)公司共同开发了UOP /Hydro MTO 工艺。
MTO 工艺对原料甲醇的适用范围较大,可以使用粗甲醇(浓度80%一82%)、燃料级甲醇(浓度95%)和AA 级甲醇(浓度>99%) 。
该工艺采用流化床反应器和再生器设计,其流程见图3。
其反应温度由回收热量的蒸汽发生系统来控制,失活的催化剂被送到流化床再生器中烧碳再生,并通过发生蒸汽将热量移除,然后返回流化床反应器继续反应。
由于流化床条件和混合均匀催化剂的共同作甲醇制取低碳烯烃 UOP/Hydro 公司的MTO 工艺 大连化学物理研究所的DMTO 工艺上海化工研究院的SMTO 工艺 鲁奇(Lurgi)公司的MTP 工艺清华大学的FMTP 工艺MTO MTP用,反应器几乎是等温的。
反应物富含烯烃,只有少量的甲烷,故流程选择前脱乙烷塔,而省去前脱甲烷塔,节省了投资和制冷能耗。
该工艺开发了基于SAPO一34的新型分子筛催化剂MTO一100,在温度350—550。
C,压力0.1 MPa-0.5 MPa下进行反应。
反应产物中乙烯和丙烯的比例可以通过改变反应强度灵活调节(摩尔比O.75—1.50),乙烷、丙烷、二烯烃和炔烃生成的数量少,生产商可根据市场需求生产适销对路产品,以获取最大的利益。
1995年,UOP与Hydro公司在挪威建成一套甲醇加工能力0.75 t/d的示范装置,连续平稳运转9O多天,甲醇转化率接近100%,乙烯和丙烯的碳基质量收率达到80%。
催化剂再生次数超过450次,其稳定性和强度得到一定的验证。
表1为UOP/Hydro MTO工艺年产500 kt乙烯装置的物料平衡表,三个主要产品乙烯、丙烯和丁烯的甲醇碳收率之和达91%,显示出该工艺的极高选择性。
2008年1月31日,新加坡Eurochem技术公司旗下的Viva公司将在尼日利亚的Lekki建设3300 kt/a甲醇装置,下游配套建设MTO装置,采用UOP/Hydro 公司的MTO技术和UOP烯烃裂解工艺技术(OCP),组成MTO—OCP加工技术方案,年产800kt烯烃,计划2012年建成投产。
1.2 大连化学物理研究所的DMTO工艺20世纪80年代,中国科学院大连化学物理研究所已开始对MTO工艺的研究,90年代大连化学物理研究所发明了以三乙胺(TEA)和二乙胺(DEA)为模板剂及用TEA 加四乙基氢氧化铵(TEAOH)为双模板剂制备SAPO分子筛的经济实用方法,采用流化床反应器进行了以小孔SAPO一34和改性SAPO 分子筛为催化剂的甲醇/二甲醚制乙烯(DMTO 法)技术研究,工艺流程如图4所示。
与传统合成气经甲醇制低碳烯烃的MTO相比较,该工艺甲醇转化率高,建设投资和操作费用节省50%一80%。
其自行研制的催化剂DO123价格低廉,具有较强的市场竞争力。
2006年2月,由中科院大连化学物理研究所与陕西新兴煤化工科技发展有限责任公司、中国石化集团洛阳石化工程公司合作在陕西华县建成的世界上第一套万吨级甲醇制取低碳烯烃规模的DMTO工业化示范装置试车成功,在规模为甲醇处理量50 t/d的工业化装置上甲醇转化率大于99.8%,乙烯、丙烯选择性大于78.16%。
乙烯和丙烯产出比例为1:1,二者之比可通过工艺参数调整,在1.5-0.8之间变换,累积平稳运行近1150 h,该装置于2006年8月通过国家级鉴定。
1.3 上海化工研究院的SMTO 工艺中石化上海化工研究院于2000年开始进行MTO技术的开发,在MTO催化剂和工艺方面已申请多项专利。
2004-2006年,SAPO一34分子筛工业放大生产成功。
2005-2006年,采用新型干燥方法的流化床催化剂制备成功,其价格低廉催化性能优异,粒度分布类似于FCC催化剂,而强度优于FCC催化剂。
为了加快自主新能源技术的开发,上海石油化工研究院与中国石化工程建设公司开展合作,开发甲醇制烯烃(SMTO)成套技术,在燕山石化建成了一套100 t/d甲醇进料的SMTO工业化示范装置。
该项目于2006年9月启动,进展顺利,2007年11月已成功投产,装置产出的乙烯和丙稀直接送燕山石化现有装置,实现连续运行。
表2对MTO工业示范装置技术进行了比较,从表中可以发现,大连化学物理研究所自主开发的甲醇制烯烃技术在主体工艺流程和催化剂方面和UOP技术基本相同,主要工艺参数优于UOP技术,实验装置规模为UOP技术的66.7倍,进一步表明国产MTO技术已达到并超过国外技术,而且进行进一步工业放大可信程度高于国外。
1.4 鲁奇(Lurgi)公司的MTP工艺德国鲁奇(Lurgi)公司在20世纪90年代开始研究甲醇制丙烯技术,鲁奇公司开发的MTP工艺,其主要产物为丙烯,同时得到市场容量巨大的副产物汽油、液化石油气(LPG)以及燃料气等,被公认为是目前从天然气通过甲醇生产丙烯费用最低的方法。
该工艺采用德国南方化学公司(Sudchmie)研究开发的改性ZSM 一5分子筛催化剂,该催化剂丙烯选择性高、结焦少、丙烷产率低,已经实现工业化生产,并且积碳量小(<0.01%的甲醇原料转化成焦炭),可进行原位间歇再生,再生温度较低(在反应温度下再生)。
鲁奇公司的MTP工艺流程如图5。
反应装置主要有3个绝热固定床反应器组成,2个反应器串联在线生产,在压力0.13 MPa-0.26 MPa和380—480。
C温度下操作,另一个反应器进行再生,这样可保证生产的连续性和催化剂的活性。
相对于甲醇制烯烃流化床工艺,甲醇制丙烯固定床工艺只用于生产丙烯,在工业放大过程中风险较小。
2002年1月鲁奇公司在挪威与TJeldbergodden甲醇联合企业合作建立了工业演示装置,设计能力为甲醇进料量360 kg/h,装置正常运转了1 1000 h,甲醇转化率大于99%,丙烯的总碳收率约为71%。
1.5 清华大学的FMTP工艺清华大学自1999年开始进行甲醇及二甲醚制烯烃方面的研究,相关研究成果已经获得国家发明专利。
清华大学以SAPO一34分子筛作催化剂,采用气固并流下行式流化床短接触反应器;催化剂与原料在气固并流下行式流化床超短接触反应器中接触、反应,物流方向为下行,催化剂及反应产物出反应器后进人设置在该反应器下部的气固快速分离器进行分离,及时中止反应的进行,有效地抑制了二次反应的发生。
分离出的催化剂进入再生器中烧炭再生,催化剂在系统中连续再生,反应循环进行。
此项专利减小了副产物烷烃的产生,降低了后续分离工艺的难度,增加了目标产物丙烯的产量,但其催化剂和反应器形式却与目前的MTO工艺的流化床类似,因此工艺记为FMTP。
2006年7月13日,清华大学与中国化学工程集团公司签订“流化床甲醇制丙烯(FMTP)I业化技术开发”项目合作协议,并与安徽淮化集团合作建立了工业试验装置。
该工业试验装置建设规模为年处理甲醇30 kt,年产丙烯近10 kt,副产液化石油气800 t,总投资约1.6亿元,2009年3月投料试车。
至2009年10月9日15时,该装置已连续、稳定、安全、环保地运行了470 h,达到了预期的效果,取得了成功。
1.6 MTO技术的新进展—MTO/OCP工艺近几年来进一步强化MTO技术的工作已取得重要进展。
在工艺方面,MTO 工艺与烯烃裂化工艺(OCP)组合(OCP是Total石化与UOP公司联合开发的)己通过工业验证试验。
用这种组合工艺,用甲醇生产乙烯+丙烯碳的选择性可以提高到85%-90%。
在这种组合工艺中,MTO装置产的C4-C6'烯烃副产品可以用作OCP装置的进料,大分子烯烃可以裂化为乙烯和丙烯,但丙烯多于乙烯。
组合工艺生产轻烯烃的灵活性很大,丙烯/乙烯产品比可以高达1.7甚至更高。
而且,可使生成的C4+副产品减少近80%,轻烯烃的收率提高20%。
MTO装置的回收部分保持不变,但其规模要适应进出OCP装置循环量增大的需要。
在催化剂方面,持续的研发工作已使MTO催化剂的性能有很大提高。
这种优化的催化剂,与原先的催化剂相比,灵活性提高,在多产丙烯时其丙烯/乙烯产出比可以提高近20%。
用这种优化的催化剂和MTO-OCP组合技术,得到的丙烯/乙烯产出比可以超过2.0,满足丙烯日益增长的需求。
二MTO与MTP技术的比较2.1 MTO与MTP技术比较2.1.1 比较的基础5000吨/天甲醇原料MTP丙烯收率是70~72%,还有乙烯、碳四、重碳氢化合物MTO与OCP组合工艺,丙烯和乙烯的综合收率是87~89%2.1.2两者的技术比较表1 MTO与MTP技术的轻烯烃收率对比MTO MTO/OCP MTP乙烯42%40%0丙烯35%50%72%碳四以上15%3%23%从上表中我们可以看出MTO技术比MTP技术的轻烯烃收率略高,如果MTO与OCP集成的工艺技术则比MTP技术在轻烯烃收率方面要高出很多。
表2 MTO与MTP技术在工艺流程方面的对比MTO+ OCP MTP并行的流程数量1个MTO流程3个烯烃裂解反应流程1个MTO流程3个烯烃裂解反应流程每个流程的反应步骤1个MTO步骤1个烯烃裂解步骤6个附加步骤1个生成二甲醚的反应步骤反应器/再生器连续操作的流化床反应器循环操作的固定床反应器最终反应器出口压力(psig)20 10反应温度℃400-500 400-550蒸汽稀释无0.5~1kg/kg甲醇最大装置能力>120万吨/年~52万吨/年表3 MTO与MTP技术在工艺操作参数方面的对比MTO+ OCP MTP反应混合进料量,kg/hr 229,600 430,500反应混合进料量, kmol/hr 7,310 15,070 相对进料体积流率 1 2.1反应有效速率,kgmol/hr 10,000 17,060甲醇制烯烃重量比例 2.63 3.21C2= 产量,吨/年317,000 0C3= 产量,吨/年317,000 519,000轻烯烃产量,吨/年634,000 519,000C4以上产量,吨/年30,000 180,000表4 MTO与MTP在技术方面的对比MTO+ OCP MTP原料甲醇(100%甲醇)208,333 208,333 甲醇原料中水10,967 10,967循环氧化物10,300 0C4+回收的碳氢化合物0 88,730 乙烯循环量0 42,250蒸汽稀释0 80,250MTO/MTP总共的原料229,600 430,530烯烃裂解混合进料比率48,000 0通过以上对比,可以看出MTO技术在很多方面还是比MTP技术具有优越性:MTO技术的乙烯和丙烯收率远高于MTP技术;MTO技术的装置生产能力也高于MTP技术。