2.1金属切削原理及刀具
金属切削原理与刀具

金属切削原理与刀具金属切削是指通过刀具对金属材料进行加工削除的过程,是金属加工领域中常见且基础的一种加工方式。
人们在制造和加工各种金属制品的过程中,常常需要通过切削来将金属材料加工成所需的形状和尺寸。
本文将深入探讨金属切削的原理以及相关的刀具类型。
一、金属切削原理金属切削的原理是利用刀具对金属工件进行力学削除材料的过程。
主要原理可以归纳为以下几点:1. 刀具与工件的相互作用力:切削过程中,刀具施加在工件上的作用力可以分为切割力、摩擦力、压力等。
切割力使刀具沿着切削方向削除金属,摩擦力影响工件表面的质量,而压力则有助于防止振动和提高切削质量。
2. 刀具与工件的接触面积:切削过程中,刀具与工件的接触面积较小,集中在切削刃上。
通过提高切削刃的硬度和耐磨性,可以减少切削面的磨损,延长刀具的使用寿命。
3. 金属切削时的切削角度:切削角度是指刀具切削刃与工件表面法线之间的夹角。
合理选择切削角度可以使切削过程更加顺利,减少切削力和切削温度。
二、常见的刀具类型不同的金属切削需求需要选择不同类型的刀具。
以下将介绍几种常见的刀具类型及其特点:1. 钻头:用于钻孔加工的刀具,主要特点是具有较高的刚性和旋转精度。
根据孔径的大小,可以选择不同类型的钻头,如常规钻头、中心钻头和孔径加工钻头等。
2. 铣刀:用于面铣、端铣、槽铣等加工的刀具,形状像一把小锯齿,可通过旋转进行切削。
铣刀可分为平面铣刀、球头铣刀、棒铣刀等多种类型,适用于不同形状和尺寸的金属切削。
3. 刀片:用于车削加工的刀具,通常由硬质合金制成,具有较高的耐磨性。
刀片形状多样,如可直线切削的刀片、可拐弯切削的刀片等,适用于不同形状和尺寸的车削加工。
4. 锯片:用于锯切金属材料的刀具,常用于金属管、金属板的切割。
根据不同的锯片规格和齿型,可以实现不同精度和效率的锯切加工。
5. 切割刀具:包括切割刀片和切割车刀等,主要用于金属材料的切割和切断。
根据切割的需求和要求,选择合适的切割刀具可以提高加工效率和切割质量。
金属切削原理与刀具教学大纲
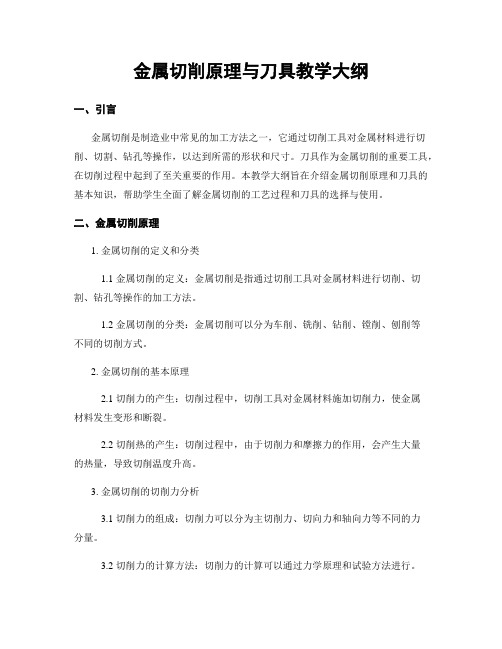
金属切削原理与刀具教学大纲一、引言金属切削是制造业中常见的加工方法之一,它通过切削工具对金属材料进行切削、切割、钻孔等操作,以达到所需的形状和尺寸。
刀具作为金属切削的重要工具,在切削过程中起到了至关重要的作用。
本教学大纲旨在介绍金属切削原理和刀具的基本知识,帮助学生全面了解金属切削的工艺过程和刀具的选择与使用。
二、金属切削原理1. 金属切削的定义和分类1.1 金属切削的定义:金属切削是指通过切削工具对金属材料进行切削、切割、钻孔等操作的加工方法。
1.2 金属切削的分类:金属切削可以分为车削、铣削、钻削、镗削、刨削等不同的切削方式。
2. 金属切削的基本原理2.1 切削力的产生:切削过程中,切削工具对金属材料施加切削力,使金属材料发生变形和断裂。
2.2 切削热的产生:切削过程中,由于切削力和摩擦力的作用,会产生大量的热量,导致切削温度升高。
3. 金属切削的切削力分析3.1 切削力的组成:切削力可以分为主切削力、切向力和轴向力等不同的力分量。
3.2 切削力的计算方法:切削力的计算可以通过力学原理和试验方法进行。
三、刀具的基本知识1. 刀具的分类和结构1.1 刀具的分类:刀具可以根据不同的切削方式和切削材料进行分类,如车刀、铣刀、钻头等。
1.2 刀具的结构:刀具由刀片和刀柄组成,刀片是切削的主要部分,刀柄用于固定刀片和传递切削力。
2. 刀具材料的选择2.1 刀具材料的要求:刀具材料需要具备一定的硬度、耐磨性、高温稳定性和切削性能等特点。
2.2 常见的刀具材料:高速钢、硬质合金、陶瓷、超硬材料等是常用的刀具材料。
3. 刀具的刀具磨损和刀具寿命3.1 刀具磨损的类型:刀具磨损可以分为刀尖磨损、刀侧磨损、刀面磨损等不同的磨损类型。
3.2 刀具寿命的影响因素:刀具寿命受到切削速度、切削深度、切削材料等因素的影响。
四、刀具的选择与使用1. 刀具的选择原则1.1 切削材料的选择:根据被切削材料的硬度、强度等特点选择合适的刀具材料。
金属切削原理与刀具教学设计

金属切削原理与刀具教学设计一、前言金属加工是实现机械零件制造的基础过程之一,而切削加工作为一种常见的制造方法,也得到了广泛的应用。
本文着重介绍金属切削原理以及刀具设计的教学内容,旨在帮助读者掌握金属切削基础知识,并带领读者深入了解刀具设计方法。
二、金属切削原理2.1 金属切削的含义金属切削是指用一定切削力破坏金属工件表面层流层,使之与切削刀具相对运动并发生剪切行为,从而将工件加工成一定形状和尺寸的过程。
切削加工是机械加工中的一种基本加工方法,包括车削、钻孔、铣削、镗削、刨削等。
2.2 金属切削的基本原理金属切削过程是由切削刀具和金属工件之间相对运动引起的,金属分子在剪切力的作用下,沿着剪切面破裂,同时与切削刀具接触面发生磨损。
具体来说,金属切削过程分为三个阶段:进给阶段、切削阶段和回退阶段。
2.3 切削力与温度在金属切削过程中,由于金属工件和刀具之间的相互作用,刀具表面会产生大量的切削热量。
同时,也会产生切削力,影响机床精度和切削质量。
因此,了解切削力和切削温度的变化规律对于金属切削加工至关重要。
三、刀具教学设计3.1 刀具材料切削加工过程中,刀具的材料需要具备耐热性、硬度高、强度高、抗磨损性能好等特点。
常用的刀具材料有高速钢、硬质合金、陶瓷和多晶刚玉等。
不同材料的刀具适用于不同类型的金属切削。
3.2 刀具设计方法刀具的设计需要根据具体加工要求确定刀具的尺寸、形状、切削部位几何形状以及平面、轴向和径向的角度尺寸等。
设计过程中需要考虑金属工件性质、机床性能、切削工况以及加工精度等因素。
同时,在刀具的设计中也需要注重刀具的刃磨和涂层工艺。
四、结论金属切削是金属加工中的一种基本加工方法,刀具的设计是金属切削加工中非常重要的环节。
在未来,随着工业自动化程度不断提高,金属切削加工技术也将不断发展。
我们需要不断学习新技术,提高自身技能水平,以适应市场的需求。
金属切削原理讲义及刀具
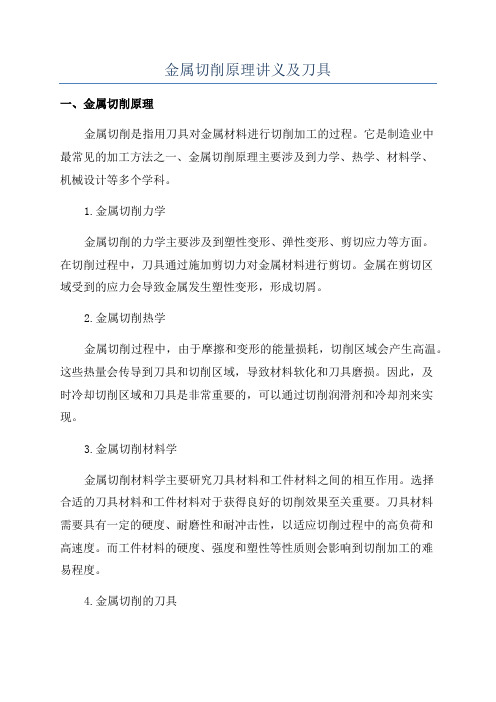
金属切削原理讲义及刀具一、金属切削原理金属切削是指用刀具对金属材料进行切削加工的过程。
它是制造业中最常见的加工方法之一、金属切削原理主要涉及到力学、热学、材料学、机械设计等多个学科。
1.金属切削力学金属切削的力学主要涉及到塑性变形、弹性变形、剪切应力等方面。
在切削过程中,刀具通过施加剪切力对金属材料进行剪切。
金属在剪切区域受到的应力会导致金属发生塑性变形,形成切屑。
2.金属切削热学金属切削过程中,由于摩擦和变形的能量损耗,切削区域会产生高温。
这些热量会传导到刀具和切削区域,导致材料软化和刀具磨损。
因此,及时冷却切削区域和刀具是非常重要的,可以通过切削润滑剂和冷却剂来实现。
3.金属切削材料学金属切削材料学主要研究刀具材料和工件材料之间的相互作用。
选择合适的刀具材料和工件材料对于获得良好的切削效果至关重要。
刀具材料需要具有一定的硬度、耐磨性和耐冲击性,以适应切削过程中的高负荷和高速度。
而工件材料的硬度、强度和塑性等性质则会影响到切削加工的难易程度。
4.金属切削的刀具刀具是金属切削过程中的重要工具,它直接与工件接触,对工件进行加工。
不同的切削操作需要使用不同类型的刀具。
常见的金属切削刀具包括刀片、铣刀、车刀和钻头等。
-刀片:刀片是金属切削中最为常用的刀具,它可用于车削、铣削、镗削等工艺。
刀片一般由高速钢制成,也有使用硬质合金和陶瓷材料制造的高级刀片。
-铣刀:铣刀是一种用于铣削操作的刀具。
它主要用于在工件上形成平面、槽口和曲面等形状。
-车刀:车刀是用于车削加工的刀具,它通过旋转刀具将工件上的旋转刀具切削掉。
-钻头:钻头是用于钻孔加工的刀具,它通过旋转切削力将工件上的孔切削掉。
以上只是金属切削原理及刀具的简要介绍,金属切削涉及的知识和技术极为广泛和复杂,需要深入学习和实践才能掌握。
通过不断的学习和实践,我们可以了解金属切削的原理和技术,并且选择合适的刀具进行加工,提高加工效率和质量。
2.王明玉,杨炯.金属材料切削原理与刀具[M].湖南大学出版社,2024.。
金属切削原理与刀具教案

金属切削原理与刀具教案
一、金属切削原理
金属切削是金属加工的主要方式,是指金属切削刀具(刀具)用力对
金属工件表面进行摩擦和削减,以获得特定尺寸和形状的过程。
1. 切削力(Cutting force)
切削力是指切削过程中,刀具和工件表面产生的有效接触力,受到许
多因素的影响,例如:切削刀具的刃型、刃口尺寸、材料硬度、切削速度、切削深度、切削温度等。
2. 切削热量 (Cutting heat)
切削热是指在切削过程中,刀具和工件表面摩擦产生的热量。
切削热
量主要来自三个方面:刀具本身的机械磨损、切削热量的摩擦损耗、以及
工件表面沿刀具刃缘的切粒引起的摩擦损耗。
3. 切削冲程(Cutting stroke)
切削冲程是指切削过程中,刀具施加在工件表面的切削力和切削冲击
力下,使工件表面在介质空气中出现的压痕或局部变形的程度。
4. 量削量 (Quantity of cut)
量削量是指切削过程中,刀具对工件表面的切削量,即刀具作用下,
从工件表面削减掉的物料量。
它受到诸多因素的影响,如切削刀具角度、
切削速度、切削深度、切削液体等。
5. 切削温度 (Cutting temperature)
切削温度是指在切削过程中,刀具和工件表面摩擦产生的温度。
金属切削原理及刀具

金属切削原理及刀具§1切削运动和切削用量刀具从毛坯上切除多余金属,从而获得在行状上、尺寸精度上和表面质量都合乎预定要求的加工,称为金属切削加工。
在切削加工过程中,刀具与工件相互接触且存在着相互运动,这种相互运动的过程称为金属切削过程。
在切削过程中,将产生各种物理现象及其变化,这些都是金属加工原理所要研究的内容。
一.切削运动1)主运动切削时直接切除工件上的金属层,使之转变为切屑的运动,称为主运动。
通常,主运动的速度最高,消耗的功率最大。
主运动可以由工件完成,也可以由刀具完成。
车削时工件的旋转运动是主运动。
一种切削加工方法其主运动只有一个。
2)进给运动不断地将多余金属投入切削,以保证切削连续进行的运动,称为进给运动。
进给运动的速度较低,消耗的功率较小。
车削的时候,车刀的纵向移动和横向移动都属于进给运动。
一种切削加工方法其进给运动不限于一个。
在切削过程中,被切金属层不断地被切削而转变为切屑,从而加工出所需要地工件表面。
在工件表面形成的过程中,工件上有三个不断变化着的表面。
(1)已加工表面切削后在工件上形成的新表面。
(2)待加工表面即将被切除的表面。
(3)加工表面切削刃正在切削着的表面。
二.切削用量切削用量是衡量切削运动和切削力大小的参数。
它包括三个要素:切削速度、进给量、切削深度。
切削用量的大小,反映单位时间内的金属切除量。
它是衡量生产率的重要参数之一。
1.切削速度即主运动的线速度,即m/s。
其中,为工件待加工表面直径,n为工件转速;由于刀刃上各点相对于工件的旋转半径不同,因而刀刃上各点的切削速度也不相同。
计算时,应以最大速度为准。
2.进给量当主运动旋转一周时,刀具(或工件)沿进给方向上的位移量。
车削时,工件旋转一周,刀具沿进给方向的位移量。
显然,进给量的大小反映着进给速度的大小关系为:3.切削深度工件上已加工表面与待加工表面之间的垂直距离。
车削时,车削深度是待加工表面直径与已加工表面直径差的一半,即,其中,为工件已加工表面直径。
第二章金属切削原理与刀具详解

2、刀具角度的参考平面(静态)
1)基面Pr:过刀刃选定点⊥ 的平面。 2)切削平面Ps:包含 并与刀刃在选定点
相切的平面。 3)正交平面Po :过刀刃选定点⊥Pr,⊥Ps
的平面。
2、刀具角度的参考平面(静态)
3、刀具的标注角度
1)主偏角κr :主刀刃在基面上投影与走 刀方向的夹角。
2)刃倾角λs:主刀刃与基面在切削平面上 的夹角。
第二章 金属切削原理 与刀具
第一节 金属切削与刀具的基本概念
金属切削过程与金属切削刀 具中有许多基本概念,熟练掌 握这些基本概念是讨论相关技 术问题的基础。
一、基本概念 1、加工表面
待加工表面:
工件上即将被切除的表面.
已加工表面:
工件上切削后新形成的表面。
加工表面(过渡表面):
工件上正在被切削的表面。
一、刀具材料应具备的性能
1)高的硬度和耐磨性 2)足够的强度和韧性 3)良好的热物理性能和耐热冲击性能 4)良好的工艺性 5)经济性
一、刀具材料应具备的性能
刀具材 料一般硬度 越高则韧性 较差;而硬度 越低则韧性 较好。
二、常用刀具材料
常用刀具材料主要有: 高速钢 硬质合金
1、高速钢
高速钢刀具一般为整体式或焊接式,热处 理后硬度一般为63~66HRC,耐热性为 500~650℃,制造工艺性好,在制造中、 低速切削刀具、形状复杂及成形刀具中高速 钢应用广泛。
第二节 刀具材料 刀具三要素: 1)刀具切削部分材料; 2)刀具切削部分几何形状; 3)刀具结构。
刀具切削部分的工作状态
刀具切削部分在工作时,受到切削力的作用和 冲击,有时会碎裂或折断。 刀具切削部分在工作时,受到工件和切屑的强 烈挤压、摩擦,会产生大量的切削热,使刀具切 削部分处于高温状态,影响刀具材料的切削性 能,在切除金属材料时,本身也会被磨损。
《金属切削原理与刀具》

《金属切削原理与刀具》金属切削原理与刀具(刀具部分)一、引言金属切削技术是现代制造业中最常用的加工方法之一、在金属切削工艺中,刀具扮演着重要的角色。
刀具的选择和使用直接影响到加工效率和加工质量。
本文将介绍金属切削原理以及常见的几种刀具类型及其使用特点。
二、金属切削原理金属切削原理是指用刀具对金属材料进行加工时,通过切削力将金属材料分离,形成所需形状和尺寸的工件。
切削过程中,刀具与金属材料之间会发生以下几个要素:切削速度、进给量、切削深度以及刀具材料。
合理控制这些要素可以达到更好的切削效果。
三、常见刀具类型及其使用特点1.铣刀铣刀是一种常用的刀具,广泛应用于金属零件的加工中。
铣刀主要用于将工件上的金属材料进行加工,切削下去,并形成所需的形状和尺寸。
铣刀通常由数个齿刃组成,其形状和数量根据加工需求而定。
铣刀的使用特点是高效、精确,适用于复杂形状的加工。
2.钻头钻头是用于孔加工的刀具,通常用于将金属材料中心钻孔,并逐渐扩大孔径。
钻头通常具有一个中心刀尖,可用于定位,并有多个切削刃,用于切削金属材料。
钻头可分为普通钻头和铺地钻头两种类型,前者主要应用于一般孔加工,后者适用于加工更大直径的孔。
3.螺纹刀螺纹刀是一种用于螺纹加工的刀具。
螺纹刀通常具有螺纹形状的刀刃,可将其螺纹形状切削到工件上,以形成所需的螺纹。
螺纹刀可分为单齿和多齿两种类型,根据加工需求选择合适的螺纹刀。
4.镗刀镗刀是一种用于加工孔的刀具,通常用于加工较精密的孔,如配合孔、镗孔等。
镗刀具有多个切削刃,能够同时加工多个切削面。
镗刀的使用特点是能够得到高精度和表面质量好的孔加工效果。
四、刀具的选用与使用注意事项在选择刀具时,需要考虑以下几个方面:工件的材料、形状和尺寸要求、切削速度以及切削负载等。
不同的刀具具有不同的切削特性,适用于不同的切削条件。
同时,在使用刀具时,要保证刀具的良好状况,及时更换磨损严重的刀片,保证加工质量。
总之,金属切削原理与刀具是现代制造业中不可或缺的一部分。
- 1、下载文档前请自行甄别文档内容的完整性,平台不提供额外的编辑、内容补充、找答案等附加服务。
- 2、"仅部分预览"的文档,不可在线预览部分如存在完整性等问题,可反馈申请退款(可完整预览的文档不适用该条件!)。
- 3、如文档侵犯您的权益,请联系客服反馈,我们会尽快为您处理(人工客服工作时间:9:00-18:30)。
2.1.1
切削运动与切削用量
基 本 定 义
在金属切削过程中,为了 要从工件上切去一部分金属, 刀具与工件之间必须完成一定 的切削运动。 如外圆车削时,工件作旋 转运动,刀具作连续的纵向直 线运动,形成了工件的外圆柱 表面。 在新的表面的形成过程中, 工件上有三个依次变化的表面:
待加工表面:即将被切去金属层的表面; 加工表面 :切削刃正在切削着的表面; 已加工表面:已经切去一部分金属形成的新表面。 这些定义也适用于其它切削。图中分别表示了车削、刨 削、钻削、铣镗削时的削的背吃刀量可用下式计算:
ap
对于钻孔 切 削 用 量 三 要 素
其中
dw dm (mm) 2
dm (mm) 2 dm——已加工表面直径 (mm); ap
dw—待加工表面直径(mm)。
2.1.2 刀具切削部分的基本定义
2.1.2.1
刀具切削部分的构造要素 金属切削刀具的切削部分的几何形状与参数都有着共性,即不论刀 具构造如何复杂,它们的切削部分总是近似地以外圆车刀的切削部分为 基本形态。
刀 具 切 削 部 分 的 构 造 要 素
国际标准化组织(ISO)在确定金属切削刀具的工作部分几何 形状的一般术语时,就是以车刀切削部分为基础的。刀具切削 部分的构造要素(图1、2)及其定义和说明如下: (1)前刀面 直接作用于被切削的金属层,并控制切屑沿其排出的刀面。 根据前刀面与主、副切削刃相毗邻的情况分为: 主前刀面: 与主切削刃毗邻的称为主前刀面; 副前刀面: 与副切削刃毗邻的称为副前刀面。 (2)后刀面 后刀面分为主后刀面与副后刀面。 主后刀面:是指与工件上加工表面相互作用和相对着的刀 面; 副后刀面:是与工件上已加工表面相互作用和相对着的刀 面。
刀具工作角度参考系: 用于定义刀具进行切削加工时几何参数的参考系。该参考 系考虑了切削运动和实际安装情况对几何参数的影响。 刀具工作角度参考系同标注角度参考系的唯一区别是:用ve 取代vc ,即用实际进给运动方向取代假定进给运动方向。
刀 具 2.1.2.4 刀具的标注角度 的 刀具标注角度:在刀具的标注角度参考系中确定的切削刃 标 注 与刀面的方位角度,称为刀具标注角度。 角 注意:由于刀具角度的参考系沿切削刃各点可能是变化的,故所定义的 度 刀具角度应指明是切削刃选定点处的角度;凡未特殊注明者,则指切削刃上 与刀尖毗邻的那一点的角度。 在切削刃是曲线或者前、后刀面是曲面的情况下,定义刀具的角度时, 应该用通过切削刃选定点的切线或切平面代替曲线刃或曲面。
切 削 用 量 三 要 素
对于刨削、插削等主运动为往复直线运动的加工,虽然 可以不规定进给速度,却需要规定间歇进给的进给量,其单 位为mm/d.st(毫米/双行程)。 对于铣刀、铰刀、拉刀、齿轮滚刀等多刃切削工具,在 它们进行工作时,还应规定每一个刀齿的进给量,即后一个 刀齿相对于前一个刀齿的进给量,单位是mm/Z(毫米/齿)。 显然 f f n f Z Z n mm/s或mm/min (3)背吃刀量 对于车削和刨削加工来说,背吃刀量ap为工件上已加工 表面和待加工表面间的垂直距离,单位是mm。
注:“静止系”本质上不是静止的,它仍然是把刀具同工件和运动联系 起来的一种特定的参考系。
刀 具 标 注 角 度 的 参 考 系
刀 具 标 注 角 度 的 参 考 系
在刀具标注角度 参考系中的刀具角度 称为标注角度。 刀具标注角度的 参考系的形成如右图 动画所示,由基面、 切削平面、主剖面等 平面构成了主剖面参 考系。
基 本 定 义
2.1 基本定义 金属切削过程 金属切削过程是工件和刀具相互作用的过程。刀具从工 件上切除多余的(或预留的)金属,并在高生产率和低成本 的前提下,使工件得到符合技术要求的形状、位臵、尺寸精 度和表面质量。 切削运动 为实现切削过程,工件与刀具之间要有相对运动,即切 削运动,它由金属切削机床来完成。 工艺系统 机床、夹具、刀具和工件,构成一个机械加工工艺系统, 切削过程的各种现象和规律都在这个系统的运动状态中去研 究。
削 运 动 与 切 削 用 量
切 削 运 动 与 切 削 用 量
1.1.1.1切削运动 金属切削机床的基本运动有直线运动和回转运动。 按切削时工件与刀具相对运动所起的作用可分为主运动和 进给运动。如图所示。 (1)主运动:切下金属所必须的最主要的运动。 特点:通常它的速度最高,消耗机床功率最多。机床的主 运动只有一个。
切 削 运 动
(3)合成运动与合成切削速度ve 主运动vc和进给运动vf可以由刀具或工件分别完成,或由 刀具单独完成。 主运动和进给运动可以 同时进行(车削、铣削等), 也可交替进行(刨削等)。 当主运动与进给运动同时 进行时,刀具切削刃上某 一点相对工件的运动称为 合成切削运动。合成速度 向量等于主运动速度与进 给运动速度的向量和: ve=vc+vf
(1)基面Pr 通过切削刃选定点,垂直于假定主运动方向的平面。 通常,基面应平行或垂直于刀具上便于制造、刃磨和测量的 某一安装定位平面或轴线。
刀 例如,图示为普通车刀或刨刀的基面,它平行于刀具底面。钻头、铣刀 具 和丝锥等旋转类刀具,其切削刃各点的旋转运动(即主运动)方向,都垂直于 标 注 通过该点并包含刀具旋转轴线的平面,故其基面Pr就是刀具的轴向剖面。 角 度 的 参 考 系
法剖面是通过切削刃选定点,垂直于切削刃的平面。 Pr-Ps-Pn组成法剖面参考系。
刀 具 标 注 角 度 的 参 考 系
右图表示由Po-Pr-Ps 组成的一个正交的主剖 面参考系,这是目前生 产中最常用的刀具标注 角度参考系。图中同时 也表示了一个由Pn-PrPs 组成的法剖面参考系。 在实际使用时一般是分 别使用某一个参考系。
确定刀具标注角度参考系的方法:
假定运动条件:首先给出刀具的假定主运动方向和假定进给 运动方向;其次假定进给速度值很小,可以用主运动向量近似 代替合成速度向量;然后再用平行和垂直于主运动方向的坐标 平面构成参考系。 假定安装条件:假定标注角度参考系的诸平面平行或垂直于 刀具上便于制造、刃磨和测量时定位与调整的平面或轴线(如车 刀底面、车刀刀杆轴线、铣刀、钻头的轴线等)。也可以说,假 定刀具的安装位臵恰好使其底面或轴线与参考系的平面平行或 垂直。
削 如:外圆车削时计算待加工表面上的速度(用dw代入公式), 用 内孔车削时计算已加工表面上的速度(用dm代入公式) , 量 钻削时计算钻头外径处的速度。 三 要 (2)进给速度、进给量和每齿进给量 进给速度是单位时间的进给量,单位是mm/s(mm/min)。 素
进给量是工件或刀具每回转一周时两者沿进给运动方向的 相对位移 (对于车削、钻削、铰削),单位是mm/r。
(2)切削平面 Ps 通过切削刃选定点,与主切削刃相切,并垂直于基面的平面。 也就是主切削刃与切削速度方向构成的平面。
基面和切削平面十分重要。这两个平面加上以下所述的任一剖面,便构 刀 成各种不同的刀具标注角度参考系。可以说,不懂得基面和切削平面就不懂 具 得刀具。 标 注 (3)主剖面Po和主剖面参考系 角 主剖面是通过切削刃选定点,同时垂直于基面和切削平面的 度 的 平面。由此可知,主剖面垂直于主切削刃在基面上的投影。 参 Pr-Ps-Po组成正交的主剖面参考系。 考 系 (4)法剖面 Pn和法剖面参考系
刀 具 标 注 角 度 的 如:普通车刀和刨刀的Pf垂直于刀杆轴 参 考 线;钻头、拉刀、端面车刀、切断刀等的 系 Pf 平行于刀具轴线;铣刀的 Pf 则垂直于 铣刀轴线。
(5)进给剖面 Pf 和背平面Pp及其组 成的进给、背平面参考系 进给剖面Pf是通过切削刃选定点, 平行于进给运动方向并垂直于基面 Pr的平面。通常,它也平行或垂直 于刀具上便于制造、刃磨和测量的 某一安装定位平面或轴线。 背平面 Pp 是通过切削刃选定点, 同时垂直于Pr和 Pf的平面。
2.1.2.2
刀具标注角度的参考系
刀 具 标 注 角 度 的 参 考 系
为了确定刀具前刀面、后刀面及切削刃在空间的位臵,首 先应建立参考系。它是一组用于定义和规定刀具角度的各基准 坐标平面。这样就可以用刀具前刀面、后刀面和切削刃相对于 各基准平面的夹角来表示它们在空间的位臵,这些夹角就是刀 具切削部分的几何角度。 工作角度:把刀具同工件和切削运动联系起来确定的刀具 角度,即刀具在使用状态下(in use)的角度。 刀具标注角度参考系:任何一把刀具,在使用之前,总可 以知道它将要安装在什么机床上,将有怎样的切削运动,因此 也可以预先给出假定的工作条件,并以此确定刀具标注角度参 考系(所谓的“静止参考系” )。
由Pr-Pf-Pp 组成一个进给、背 平面参考系,如右图所示。
2.1.2.3
刀具工作角度的参考系
前述刀具标注角度参考系,在定义基面时,都只考虑主运动,不考虑进 给运动,即在假定运动条件下确定的参考系。但刀具在实际使用时,这样的 参考系所确定的刀具角度,往往不能确切地反映切削加工的真实情形。只有 用合成切削运动方向来确定参考系,才符合切削加工的实际。 刀 下图所示三把刀具的标注角度完全相同,但由于合成切削运动方向不同, 具 切 后刀面与加工表面之间的接触和摩擦的实际情形有很大的不同: 削 部 分 的 基 本 定 义
vc 1000 m / s或m / min
式中
d——工件或刀具上某一点的回转直径(mm); n——工件或刀具的转速(r/s或r/min)。
在生产中,磨削速度单位用米/秒( m/s),其它加工的切削 速度单位习惯用米/分(m/min)。 在转速n值一定时,切削刃上各点的切削速度不同。考虑到 刀具的磨损和已加工表面质量等因素,计算时,应取最大的切 切 削速度。
内 容 提 要
教学要求: 金属切削过程就是刀具从工件上切除多余的金属,使工 件获得规定的加工精度与表面质量。因此,要进行优质、高 效与低成本的生产,必须重视金属切削过程的研究。 教学重点: 基本定义——介绍金属切削过程方面的一些基本概念, 它包括切削运动、切削用量、参考系(主剖面参考系、法剖 面参考系、进给背平面参考系)、刀具标注角度、切削层参 数等。 刀具材料——介绍刀具材料应具备的性能(硬度、耐磨性、 强度、韧性、耐热性、工艺性、经济性);两种常用的刀具材 料(高速钢、硬质合金)和其它刀具材料(涂层、陶瓷、人造金 刚石、立方氮化硼)。