复合膜工艺问题
复合膜的热压法

复合膜的热压法
复合膜的热压法是一种将两层或多层薄膜通过热压结合在一起的技术。
以下是热压法的一般步骤:
1. 薄膜准备:选择合适的薄膜材料,并确保它们的表面干净、平整,没有杂质或污染物。
2. 涂覆粘合剂:在需要粘合的薄膜表面之一上涂覆一层粘合剂。
这可以通过滚轮涂布、喷涂或其他适当的方法来完成。
3. 干燥和活化:让涂覆粘合剂的薄膜经过适当的干燥过程,以去除溶剂并激活粘合剂。
4. 热压:将两层或多层薄膜堆叠在一起,并将它们放入热压设备中。
热压设备通常提供加热和压力,以促使薄膜之间的粘合剂固化并形成牢固的结合。
5. 控制参数:在热压过程中,需要控制一些关键参数,如温度、压力、时间和加热速度。
这些参数的设置将根据所使用的薄膜材料和粘合剂类型来确定。
6. 冷却和固化:热压完成后,让复合膜在冷却阶段逐渐固化,以确保结合的牢固性。
热压法可用于制造各种复合膜产品,如包装材料、建筑膜、太阳能电池背板等。
它提供了一种高效、可靠的方法来结合不同的薄膜材料,以满足特定的应用需求。
需要注意的是,具体的热压工艺和参数可能会因材料和设备的差异而有所不同。
在实际应用中,建议根据所使用的材料和设备参考相关的技术规格和操作指南,以获得最佳的热压效果。
复合卷膜常见缺陷及处理办法

复合卷膜常见缺陷及处理办法复合卷膜是指由两种或两种以上材料,经过一次或多次复合工艺而组合在一起,从而构成一定功能特性的复合材料。
一般可以将复合材料分为印刷层、功能层和热封层。
一、复合膜外观不良1.有气泡1.1薄膜润湿不良,应提高胶的浓度和涂布量,(MST、KPT)表面不易湿润,易产生气泡,特别在冬天。
油墨上的气泡,用提高胶的用量的方法去除。
1.2油墨表面凹凸和起泡,应把复合膜的复合温度和复合压力提高。
1.3油墨表面上的胶涂布量少,应增加复合辊的压贴时间及使用光滑辊筒、薄膜预热充分、降低复合速度、选择湿润性好的胶以及正确选用油墨。
1.4薄膜中的添加剂(润滑剂、抗静电剂)被胶渗透,应选用分子量高、固化迅速的胶,提高胶浓度,提高烘箱温度充分使胶干燥,不使用超过3个月存放期的薄膜,因为电晕处理已丧失。
1.5冬天里气温低,粘结剂对薄膜和油墨转移,润湿粘附不好,操作场所保持一定温度。
1.6干燥温度太高,发生胶的起泡或表皮结皮,内里不干,应调整胶干燥温度。
1.7复合辊薄膜间夹带入空气,应提高复合辊温度,减小复合角(薄膜厚、硬时易产生气泡)。
2.复合后无气泡,经过熟化后产生了气泡2.1由于薄膜阻隔性高,胶固化时产生的CO2气体,残留在复合膜中,未印刷处也有气泡,应提高固化剂量,使胶在干燥中固化。
2.2胶中的酯酸乙酯是油墨粘结料的良好溶剂,胶溶渗了油墨,只在油墨上有气泡,避免水分渗入胶中及提高胶干燥温度,减少对油墨的溶渗。
3.复合膜上有不规则皱纹、气泡3.1薄膜厚薄不均,避免使用厚度不均膜。
3.2薄膜拉伸太大,定型不够,同热收缩,以及由于吸湿,膜发生变形,应防止薄膜吸湿变形,降低印刷卷取张力以及复合时张力不宜太高。
4.复合膜上有规则的气泡和皱纹网纹辊上的网眼有坏的,橡胶辊有损坏和凹点,复合辊上有脏东西,基材速度同网纹辊速度有偏差,薄膜厚度有偏差。
应检查网纹辊,更换或修补;检查橡胶辊是否损坏,更换或修补;清洗复合辊。
薄膜复合制袋中常见皱褶问题分析

薄膜复合制袋中常见皱褶问题分析复合薄膜的表面皱褶是复合软包装材料加工及应用过程中常见的问题。
人们通常会说:表面皱褶问题常常会有胶水不干现象相伴随,即将有表面皱褶问题的复合膜剥开时,常常会发现复合膜的胶层有不同程度的“发粘”现象。
因此,人们得出结论:复合薄膜的表面皱褶问题是由于胶水不干问题所引发的!复合薄膜的表面皱褶问题可以出现在复合薄膜的生产及应用的不同阶段:1. 复合薄膜下机时;2. 复合薄膜经过熟化处理后;3. 制袋加工完成时及放置一段时间后;4. 水煮处理完成时及放置一段时间后;5. 蒸煮处理完成时及放置一段时间后。
下图是制袋加工后的表面皱褶的案例之一。
所谓表面皱褶问题的表现是:表层的薄膜向上凸起;内层的薄膜向下凹陷。
上图的表面皱褶即属于“表层薄膜向上凸起”类的。
迄今为止,尚未发现在一张复合薄膜或一个复合膜袋上“表层的薄膜向上凸起”和“内层的薄膜向下凹陷”现象同时发生的现象。
在复合薄膜下机时所出现的表面皱褶,过去俗称为“隧道”,很多人都将其归因为胶水的“初粘力”不足。
伴随着无溶剂型干法复合加工技术的逐步普及,现在已很少有人投诉“胶水初粘力不足”了,因为大家都已清楚地知道:复合膜下机时的隧道问题的原因是放卷张力控制不良!由于放卷的张力控制(设定)不良,使得两个复合基材在复合加工过程中处于不同的延伸率状态,例如PET/CPP的复合薄膜,可能PET膜被拉长了千分之二,CPP膜被拉长了千分之四,当复合过程结束时(即复合膜下机了),由于外加的张力已去掉了,因此,PET膜就会“试图”回缩千分之二,CPP膜也会“试图”回缩千分之四。
如果此时的胶层的初粘力足够大,则两个复合基材都不能回缩到其初始的长度,所以,下机的复合膜就会呈现向CPP层方向卷曲的状态;如果此时的胶层的初粘力不够大,则PET膜就有可能完全恢复到其初始状态,CPP膜也将最大程度地恢复到接近其初始状态的状态。
此时,在两层复合膜间就出现了长度的差异,即在单位长度上,PET膜比CPP 膜长了将近千分之二!其结果就是出现了隧道问题--CPP膜平直、PET膜向上凸起的隧道!隧道问题的严重程度(单位长度上隧道的数量、隧道的长度以及隧道凸起的高度)是与两层基材膜间长度的差异成正比的!从以上的描述中不难发现:对于刚下机的复合薄膜而言,是否会产生隧道问题的原因是在无外加张力的条件下复合薄膜间是否存在长度上的差异,以及胶层的初粘力或剥离力是否足够大!由此可以推断:此种状态下所出现的隧道问题与胶层是否完全固化(即是否发粘)完全没有关系!据此,可以推而广之。
复合加工工艺一、干法复合干法复合是生产复合薄膜最常用的方法

复合加工工艺一、干法复合干法复合是生产复合薄膜最常用的方法,它是用溶剂型粘合剂将两种或数种基材复合在一起。
干法复合主要有以下特点:(l)对基材的适应性广。
可用于各种塑料薄膜、铝箔、镀铝薄膜以及纸张的复合,尤其适于同种或异种塑料薄膜的复合。
(2)生产效率高。
复合速度最高可达250m/min左右,一般为130~150m/min;加工宽度为400~1400mm。
(3)使用聚氨酯粘合剂,其粘合强度大,并有良好的耐热性和耐化学药品性,可用作耐高温蒸煮袋等。
(4)复会操作简单,只要干燥温度和张力控制适当,就可顺利生产。
干法复合的主要缺点是粘合剂用量大,能源消耗大,其生产成本较高;且聚氨酯粘合剂有一定的毒性。
目前,我国约有1/3的复合薄膜采用于法复合生产,主要用于蒸煮食品、风味食品等中高档商品的包装。
在国外,由于价格的竞争,共挤出和挤出复合薄膜占了绝大部分,而干法复合薄膜所占的比重较小,只有在需要高档包装上才使用。
如日本干法复合薄膜仅占12%;在美国和西欧等国,因聚氨酯粘合剂的毒性问题,其复合薄膜不准用于食品的包装。
近年来,我国也在注重发展共挤出和挤出复合薄膜。
1.干法复合材料及原辅料。
主要有干法复合薄膜、复合用基材、粘合剂、油墨等。
(1)干法复合薄膜。
干法复合薄膜最常见的是由2~3层基材构成,主要用于食品包装。
复合薄膜的结构,可以根据不同产品的包装要求,选择适合的基材,进行合理的设计。
如蒸煮袋要求具有较好的耐热性、阻隔性和强度等,典型的蒸煮袋结构是:PET(外)/AL(铝箔)/CPP(内),PET薄膜为蒸煮袋提供了较高的强度、印刷性和透明性;铝箔提供了刚性和阻隔性;CPP薄膜作内层材料则具有较好的热封性和化学稳定性。
常见干式复合薄膜的结构、特点及用途见表14-1。
(2)复合用基材。
干法复合可供选择的基材面广,一般基材均可用于干法复合。
从复合薄膜的结构来看,外层材料应具有较好的印刷性能和光学性能;强度高,不易划伤、磨毛;耐热性能好等特点。
干式复合的常见问题及处理方法

干式复合的常见问题及处理方法浏览次数:603 发布日期:2011-8-11 20:14:411、复合膜剥离强度不够分以下几种情况:胶水固化不完全,剥离开来的时候在胶水面还有粘性。
原因:1)粘合剂的配比错误,固化剂的比例不足导致固化不完全。
在配制粘合剂时要按粘合剂生产厂家规定的配比参数进行配制;2)溶剂的纯度不够,溶剂中含有水或醇类超标,水或醇类与胶水中的固化剂发生反应,降低的固化剂的比例导致胶水固化不完全。
用于干复的溶剂是乙酯,所以乙酯在进厂时每一批都要抽检,如发现纯度不够时不可使用;3)印刷膜中油墨的残留溶剂高引起胶水固化不够。
油墨(特别是PET油墨)的残留溶剂有一部分会与胶水中的固化剂发生反应,从而消耗了固化剂导致胶水固化不够。
对策:①薄膜印刷好后最好不要立即复合,如果时间允许的话可先放置1—2天后再进行复合;②印刷膜下机后检测残留溶剂,如残留溶剂高,在复合时可适当增加固化剂的比例;③选用快速固化的胶水。
4)复合膜熟化温度低、熟化时间不够,出现交联不充分,固化不完全。
对策:提高熟化温度或选用快速固化的胶水。
2、复合薄膜的表观问题1)小墨点。
一般复膜后马上出现的可能性较小,除非是渣浑杂质等。
复膜后一段时间的镀铝膜有可能出现这种现象,原因是因为油墨对铝的腐蚀,当油墨呈现一定的酸性或碱性,而上胶量又小,不能形成连接的一层时,就可能发生这种情况。
2)小灰点。
出现小灰点的可能性有两种,一是辊筒不均匀造成胶的斑点,二是油墨的不均匀造成的油墨没有压实的斑点。
两种可能性都和工艺有关,可以通过调整工艺解决,提高上胶量的厚度。
3)小白点。
一般表面的油墨变色的情况下容易出现。
多出现在镀铝膜的复合中。
出现原因有二:一是油墨本色的遮盖力不强或遮盖不均匀,尤其是白油墨,使铝的颜色渗透出来,没有铝颜色渗透的地方形成小白点;二是工艺原因,烘道温度(特别是一级烘道)太高或上胶量太厚,导致在一级烘道内胶层表面凝结,乙酯在二、三级烘道中冲出来的时候,挤起胶水,显出油墨本色。
硅溶胶水玻璃复合工艺易出现的问题

一、对硅溶胶水玻璃复合工艺的介绍硅溶胶水玻璃复合工艺是一种常见的玻璃加工工艺,通过将硅溶胶涂覆在玻璃表面后再进行固化处理,形成一层具有耐磨、防水、耐腐蚀等特性的材料。
这种工艺广泛应用于建筑、玻璃工艺制品、家居用品等领域。
二、硅溶胶水玻璃复合工艺易出现的问题1. 硅溶胶选择不当:硅溶胶的选择直接影响着复合后的玻璃表面性能,如果选择不当,可能导致复合膜的附着力不足、耐磨性差等问题。
2. 复合厚度不均匀:在复合过程中,如果涂覆的硅溶胶层厚度不均匀,可能导致玻璃表面出现凹凸不平的情况,降低美观度和使用寿命。
3. 固化温度不足:硅溶胶水玻璃复合后需要进行固化处理,如果固化温度不足,可能导致复合膜的硬度不足,影响其耐磨、耐腐蚀性能。
4. 固化时间不足:固化时间不足会导致硅溶胶水玻璃复合层未完全固化,使得其性能不稳定,容易出现开裂、剥离等问题。
5. 操作流程不规范:在硅溶胶水玻璃复合工艺中,如果操作人员在操作过程中存在疏忽大意、操作流程不规范等问题,可能导致复合效果不理想。
三、解决硅溶胶水玻璃复合工艺易出现的问题的建议1. 选择合适的硅溶胶:在进行硅溶胶水玻璃复合工艺时,应根据玻璃的具体用途和要求选择合适的硅溶胶,保证复合后的性能满足需求。
2. 控制涂覆厚度:在复合过程中,要严格控制涂覆厚度,确保复合膜的厚度均匀,避免出现凹凸不平的情况。
3. 严格控制固化条件:在固化过程中,要严格控制固化温度和固化时间,确保复合膜能够充分固化,保证其性能稳定。
4. 规范操作流程:在进行硅溶胶水玻璃复合工艺时,要制定规范的操作流程,严格按照操作规程进行操作,避免出现疏忽大意导致的问题。
四、结语硅溶胶水玻璃复合工艺是一种常见的玻璃加工工艺,在实际应用中容易出现一些问题。
通过选择合适的硅溶胶、严格控制涂覆厚度、固化条件和规范操作流程,可以有效解决这些问题,保证复合后的玻璃具有良好的性能和稳定的质量。
在进行硅溶胶水玻璃复合工艺时,除了上述提到的问题和解决建议外,还有一些其他容易出现的问题需要引起注意。
“局部透明”真空镀铝复合膜的研制工艺及应用问题分析
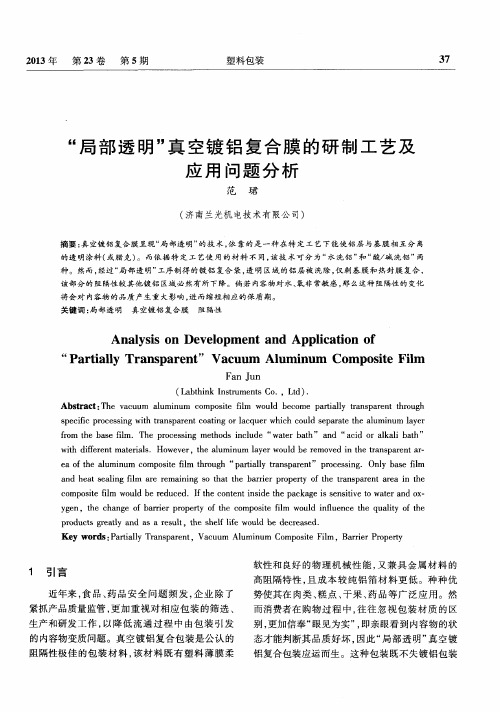
f r o m t h e b a s e i f l m .T h e p r o c e s s i n g me t h o d s i n c l u d e“ wa t e r b a t h ’ ’a n d“ a c i d o r a l k a l i b a t h”
的透 明涂 料 ( 或腊克) 。 而 依 据 特 定 工 艺使 用 的 材 料 不 同 , 该技 术 可分为 “ 水洗铝 ” 和“ 酸/ 碱 洗 铝 ”两
种 。然而, 经过“ 局部透 明” 工序制得的镀 铝复合 袋 , 透 明 区域 的 铝 层 被 洗 除 , 仅 剩基膜和 热封膜 复合 , 该 部 分 的 阻 隔性 较 其他 镀 铝 区域 必 然 有 所 下 降 。倘 若 内容 物 对 水 、 氧 非 常敏 感 , 那 么这 种 阻 隔性 的 变化 将 会 对 内容 物 的 品 质 产 生 重 大 影 响 , 进 而 缩 短相 应 的 保 质 期 。
关键词 : 局部透 明 真 空镀 铝 复合 膜 阻 隔 性
An a l y s i s o n De v e l o p me n t a n d Ap p l i c a t i o n o f “Pa r t i a l l y Tr a n s p a r e n t ” Va c u u m Al u mi n u m Co m po s i t e Fi l m
薄膜复合过程中九种问题解析!

薄膜复合过程中九种问题解析!膜复合过程中常常会产生多种问题。
粘合剂常常被认为是造成粘接问题的原因。
事实上,造成薄膜复合缺陷的原因可能是环境、基材、油墨、工艺条件等多种因素。
1斑点问题斑点问题是复合膜中经常出现的问题,斑点一般以出现在白油墨面上为主。
有时彩墨背后托白墨时也会隐约出现斑点,其实也是出现在白墨上透过彩墨反映出来。
此时版面上有空白部位时无任何缺点。
斑点的出现也有两种现象:一是复合下机时无斑,熟化后斑点出现;二是下复合机后即有斑点(以上两种现象均指不规则出现。
如有规律有规则地出现要考虑薄膜平整状态、机械平行状态、热压辊是否有污染、是否有伤痕、上胶辊系统是否有缺陷)。
现象1:下机后无斑点,熟化后出斑。
产生原因:1)白油墨太粗糙,油墨中的钛白粉颗粒度大。
2)油墨中粘接料比例小,在油墨层中造成有细孔现象。
3)粘合剂涂布量偏小。
在熟化过程中由于分子间的吸引力,毛细现象等原因粘合剂爬进了油墨的微孔中,造成界面上粘合剂的流失而形成空洞,由表面看就是白斑。
解决办法:1. 更换油墨;2. 加大粘合剂涂布量。
现象2:下机后即有斑点。
产生原因:1)粘合剂内聚力大,流动性较差,造成流平性不好,部分界面上没有胶粘剂,没有粘接。
涂布量过小,达不到流动时所需的必备条件。
解决办法:更换胶粘剂或改变涂布的工作液浓度;加大涂布量。
2)油墨界面粗糙,粘合剂流动阻力加大,造成部分界面没有粘合剂没有粘接。
解决办法:加大涂布量,适当加高使用浓度或更换油墨。
3)第一段烘干效果过高,粘合剂中的溶剂挥发过快,粘合剂层的表面张力提高过快而造成流平性差,使得部分界面没有粘合剂粘接。
解决办法:调整复合工艺,降低第一段风量温度。
4)粘合剂对乙酯的束缚力低,在第一段烘道中干燥快,使得粘合剂层的表面张力升高过快,流平性降低,造成部分界面没有粘合剂,没有粘接。
解决办法:调整复合工艺,降低第一段风量温度。
5)网线辊堵塞造成粘合剂涂布量减少,降低了流平的必须量,使得部分界面没有胶粘剂没有粘接。
- 1、下载文档前请自行甄别文档内容的完整性,平台不提供额外的编辑、内容补充、找答案等附加服务。
- 2、"仅部分预览"的文档,不可在线预览部分如存在完整性等问题,可反馈申请退款(可完整预览的文档不适用该条件!)。
- 3、如文档侵犯您的权益,请联系客服反馈,我们会尽快为您处理(人工客服工作时间:9:00-18:30)。
制备方法分为四类:
(1)层压法,首先制备很薄的致密均质膜,而后层压于微孔支撑膜上;
(2)浸涂法,把聚合物溶液浸涂于微孔膜上,然后干燥而成,也可以把活性单体或
预聚物溶液浸涂于微孔膜上,用热或辐射固化;
(3)等离子体气相沉积法,用等离子辉光使微孔支撑膜的表面产生致密的均质膜;
(4)界面聚合法,在微孔支撑膜表面上,用活性单体进行界面聚合。
复合膜主要用于反渗透、气体分离、渗透蒸发等分离过程中。
用两种不同的膜材料,分别制成具有分离功能的表面活性层(致密分离层)和起支撑作用的多孔层组成的膜。
1.干式复合法是将粘合剂通过复合机涂布在基材的表面,以加热辊压附在其它薄膜上而复合的方式。
2.湿式复合法将水溶性粘合剂(明胶、淀粉)、水分散性粘合剂(醋酸乙烯乳胶等)涂布于基材表面的湿润状态下与其它材料复合,然后用辊压附和干燥的方法。
3.挤出复合法这是复合加工中最常用的方法,用挤出机将PP、PE、EVA(乙烯―醋酸乙烯共聚物)离子型树脂等挤出薄膜状,涂粘在掺入加工剂(聚乙烯亚胺、聚氨酯系树酯等)的各种薄膜上加以复合,再经冷却、固化。
4.热熔融复合法基材树脂中掺混松香、二甲苯树脂、苯乙烯树脂等粘附剂和石蜡系等粘底降低剂的热熔剂涂布在薄膜、纸面、铝箔表面上,立刻复合在其它基材上加以冷却的方法。
5.共挤出复合法该法是由二台或三台挤出机同时成型加工可得二层以上的薄膜,有T模头法和吹塑法,能进行多种复合,可产超薄形薄膜。
3常用结构
双层复合如PT/PE、纸/铝箔、纸/PE、PET/PE、PVC/PE、NY/PVDC、PE/PVDC、PP/PVDC等。
三层复合如BOPP/PE/OPP、PET/PVDC/PE、PET/PT/PE、PT/AL/PE、蜡/纸/PE等。
四层复合如PT/PE/BOPP/PE、PVDC/PT/PVDC/PE、纸/铝箔/纸/PE等。
五层复合如PVDC/PT/PE/AL/PE等。
六层复合如PE/纸/PE/AL/PE/PE等。
4问题解决
问题原因
1.基材厚度不均匀,薄厚相差太大。
2.基材位置偏斜,导致复合膜出现褶皱,而且随着偏斜度的累积,产生褶皱的程度也会相应增大。
如果基材是容易受湿度影响的薄膜材料(如尼龙薄膜),而且发生了吸湿现象,在挤出复合过程中容易产生褶皱。
4.张力设置和控制不当,各部分张力不协调、不匹配。
5.复合压力设置不当。
6.硅橡胶压辊与冷却钢辊两者之间的轴线不平行。
7.导辊表面不干净,粘有异物,或导辊表面不平整,有凹坑、划道、碰伤等现象。
解决办法:
1.更换基材,保证基材厚度均匀。
2.调整基材的位置,在传送过程中不发生歪斜。
3.将基材进行预热干燥处理,或更换没有发生吸湿现象的基材。
4.调节放卷和收卷张力,使各部分张力相互适应和匹配。
5.根据实际情况将复合辊的压力调整至适当大小。
6.调整硅橡胶压辊与冷却钢辊之间相对的位置,使两者保持平行。
7.清洁导辊表面,更换有损伤的导辊,保证导辊表面平整、光滑、清洁。
故障原因:
1.挤出机温度设置不当,特别是模头和树脂的温度太低,造成树脂塑化不良,使熔融树脂出现鲨鱼皮现象或者类似鱼眼状的斑痕。
2.树脂中含有水分,影响树脂的塑化状况。
3.树脂中混进熔融指数或密度不同的其他树脂,使树脂塑化不好或塑化不完全。
4.更换树脂时没有将料筒彻底清洗干净,料筒中残存的其他树脂或杂质对树脂塑化状况产生不良影响。
解决办法:
1.将挤出机的挤出温度和树脂的温度调整到适当值,保证树脂塑化良好。
2.对树脂进行搅拌和烘干,去除其中所含的水分,使树脂能够充分塑化。
3.更换熔融指数和密度适当的树脂。
4.彻底清洗料筒,去除杂质等的影响。
异味故障
1.挤出机温度或树脂温度过高,造成树脂分解,产生臭味。
2.气隙太大,树脂氧化过度,表面产生有异味的各种含氧基团,使复合膜产生气味。
3.树脂本身就有异味,用其进行挤出复合后的复合膜也会有异味。
4.底涂剂中使用高沸点、不易挥发的溶剂,导致部分溶剂残留,造成复合后薄膜产生异味。
解决办法:
1.适当降低挤出温度,防止树脂发生分解。
2.调整气隙的大小到合适的值。
3.采用低臭度的树脂进行挤出复合。
4.提高烘道的干燥温度,加大吹风量,保证溶剂充分干燥。
变形故障
1.张力设置和控制不当,各部之间的张力值不适应。
2.烘道温度设置太高。
3.复合压力过大,使复合膜产生拉伸。
4.冷却钢辊表面温度太高,复合膜冷却效果差,容易枯辊产生拉伸现象。
解决办法:
1.检查并确定拉伸现象发生在设备哪一段,根据具体情况将该段的张力值调整到合适,与其他段的张力大小相匹配。
2.适当降低烘道的温度。
3.适当降低复合压力。
4.降低并控制好冷却钢辊的表面温度,使其分布均匀,有良好冷却效果。
表面故障
1.冷却钢辊表面温度太高,对熔融树脂冷却效果不佳,影响复合膜的冷却、固化及成型,导致熔融树脂粘在冷却钢辊表面。
2.复合时熔融树脂温度过高。
3.收卷张力太小,无法将复合膜从冷却钢辊表面剥离下来。
解决办法:
1.适当降低冷却水的温度和冷却钢辊的表面温度,改善冷却效果。
2.根据具体情况适当降低树脂温度,调整气隙的大小,将熔融树脂温度控制在适当范围内。
3.适当提高收卷张力,使复合膜从冷却钢辊表面剥离下来。
透明度差
1.挤出机挤出温度太低,造成树脂塑化不良,对复合膜的透明度产生一定影响。
2.冷却钢辊表面温度太高,冷却效果太差,使复合膜透明度大打折扣。
3.基材本身的透明度不好。
解决办法:
1.根据树脂性能特点及实际生产情况来设置和控制相应的挤出温度,保证树脂塑化良好,这是提高复合膜透明度的前提条件之一。
2.适当降低冷却水的温度及冷却钢辊的表面温度。
一般来说,冷却水的温度控制在20c以下,冷却钢辊的表面温度控制在60c以下。
3.更换透明性好的基材。