第7章 压铸模设计概述
压铸工艺及模具设计:第7章 成型零件和模架设计
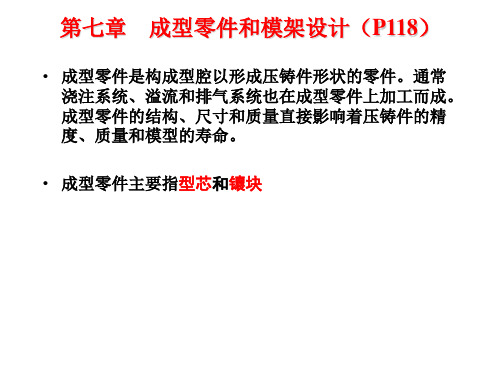
(一)主型芯的结构及固定形式 • 图7-6
(二)小型芯的结构及固定形式 • 图7-7,图7-8。
(二)小型芯的结构及固定形式
六、镶块和型芯的止转形式。
七、镶块和型芯的结构尺寸
(一)镶块壁厚尺寸
(二)整体镶块台阶尺寸
表7-8 整体镶块台阶尺寸推荐值
(三)组合式成型镶块固定部分长度
• 表7-9 组合式成型镶块固定部分长度推荐值
铸件实际尺寸的差与模具成型尺寸之比。即:
• A型-----室温下模具的成型尺寸(mm), • A实-----室温下压铸件的实际尺寸(mm)。
一、压铸件的收缩率 • (二)计算收缩率
• A’-----计算得到的模具成型零件的尺寸(mm), • A-----压铸件的公称尺寸(mm)。
常用压铸合金的计算收缩率腔尺寸(包括型腔深度尺寸) ②型芯尺寸(包括型芯高度尺寸)
③成型部分的中心距离和位置尺寸
(一)成型尺寸的分类及计算要点
成型尺寸计算的要点: • 因型腔磨损后尺寸增大,故计算型腔尺寸时应使得压
铸件外形接近于最小极限尺寸。
• 因型芯磨损后尺寸减小,故计算型腔尺寸时应使得压
铸件内形接近于最大极限尺寸。
• 1.壳体压铸件的成型尺寸分类
压铸件的①、②、③属于型腔尺寸;④、⑤、⑥属于 型芯尺寸;⑦、⑧属于中心距离、位置尺寸。另外, ②、⑤受到分型面的影响,高压、高速的金属液充填 型腔时,闭合的动、定模会出现微小的分离倾向,使 与分型面有关的尺寸略微增大。为消除这种影响,通 常将计算所得的公称尺寸减去0.05mm。
第七章 成型零件和模架设计(P118)
• 成型零件是构成型腔以形成压铸件形状的零件。通常 浇注系统、溢流和排气系统也在成型零件上加工而成。 成型零件的结构、尺寸和质量直接影响着压铸件的精 度、质量和模型的寿命。
压铸模具设计范文

压铸模具设计范文压铸模具设计是指为了生产压铸件而设计的模具,其主要任务是将液态金属注入模具中,并在模具中冷却、凝固,最终得到所需形状的金属零件。
压铸模具设计的主要工作包括设计模具的结构、选材、计算模具的合理尺寸和形状等。
一、压铸模具结构设计1.模具整体结构设计:根据压铸件的形状和尺寸,确定模具的整体结构。
一般情况下,压铸模具采用上下模结构,上模为固定模,下模为活动模。
针对复杂形状的压铸件,可能需要设计多个滑模和拉杆。
2.模腔设计:根据压铸件的形状和尺寸,确定模腔的几何形状和尺寸。
模腔的设计应保证在模具关闭时,模腔中的液态金属能够充满整个腔体,并且在冷却凝固过程中,金属能够均匀收缩,避免产生缩孔和其他缺陷。
3.浇口和导流系统设计:浇口和导流系统的设计对于压铸件的质量和生产效率有着重要的影响。
浇口的设计应尽量避免金属的湍流流动,避免气泡的产生。
导流系统的设计应考虑金属的顺序填充和排气,以及冷却和凝固过程中的温度控制。
二、压铸模具选材压铸模具的选材应根据金属的性能和压铸工艺的要求来确定。
通常情况下,模具会选用高强度和耐磨损的合金钢作为材料,以保证模具的使用寿命和精度。
同时,还需要考虑模具的热传导性能,以确保压铸件能够快速冷却、凝固。
三、压铸模具尺寸和形状计算1.模具尺寸计算:模具尺寸的计算包括模腔尺寸、模板尺寸、滑模尺寸、导流系统尺寸等。
模具尺寸的计算需要考虑压铸件的最终尺寸、缩孔和收缩率等因素。
2.模具形状计算:模具的形状计算主要是指模腔内部的曲面和棱角的设计。
对于复杂形状的压铸件,需要使用CAD软件进行三维建模和形状优化,以确保模具的制造精度和压铸件的质量。
压铸模具设计需要充分考虑压铸件的形状和尺寸、材料的性能、压铸工艺要求等因素,通过合理的结构设计、选材和计算,能够提升压铸件的质量和生产效率。
在设计过程中,还需要考虑模具的制造难度和制造成本,以确保模具的可行性和经济性。
压铸模设计及成型零件制造工艺与压铸工艺设计
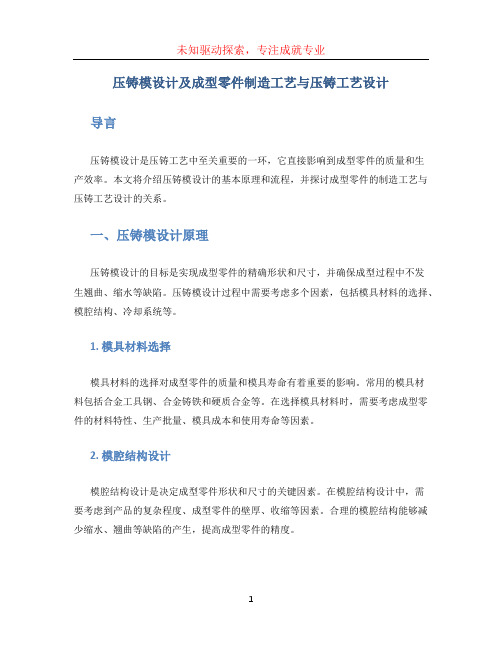
压铸模设计及成型零件制造工艺与压铸工艺设计导言压铸模设计是压铸工艺中至关重要的一环,它直接影响到成型零件的质量和生产效率。
本文将介绍压铸模设计的基本原理和流程,并探讨成型零件的制造工艺与压铸工艺设计的关系。
一、压铸模设计原理压铸模设计的目标是实现成型零件的精确形状和尺寸,并确保成型过程中不发生翘曲、缩水等缺陷。
压铸模设计过程中需要考虑多个因素,包括模具材料的选择、模腔结构、冷却系统等。
1. 模具材料选择模具材料的选择对成型零件的质量和模具寿命有着重要的影响。
常用的模具材料包括合金工具钢、合金铸铁和硬质合金等。
在选择模具材料时,需要考虑成型零件的材料特性、生产批量、模具成本和使用寿命等因素。
2. 模腔结构设计模腔结构设计是决定成型零件形状和尺寸的关键因素。
在模腔结构设计中,需要考虑到产品的复杂程度、成型零件的壁厚、收缩等因素。
合理的模腔结构能够减少缩水、翘曲等缺陷的产生,提高成型零件的精度。
3. 冷却系统设计冷却系统的设计对模具寿命和生产效率有着重要的影响。
合理的冷却系统能够快速降低模具温度,提高成型速度,减少成本。
冷却系统的设计需要考虑到模腔形状、成型零件的特性、模具材料等因素。
二、成型零件制造工艺与压铸工艺设计成型零件的制造工艺和压铸工艺设计是紧密相关的。
成型零件的制造工艺包括材料准备、熔炼、浇注、固化、清理等过程;而压铸工艺设计包括模具设计、模具制造、成型参数设置等过程。
1. 材料准备材料准备是成型零件制造工艺的第一步。
在压铸工艺中,常用的材料包括铝合金、锌合金、镁合金等。
材料的准备需要考虑到成型零件的要求和使用环境,选择合适的材料,并进行加热、熔化等处理。
2. 熔炼熔炼是将原材料加热至熔点并进行熔化的过程。
在熔炼过程中,需要控制温度、时间和熔炼速度等参数,确保材料的均匀性和纯度。
熔炼后的材料会通过浇注口注入压铸模中进行成型。
3. 浇注与固化浇注是将熔融的材料注入压铸模中的过程。
在浇注过程中,需要控制浇注速度、浇注压力和浇注位置等参数,以确保材料均匀填充模腔。
压铸模具的设计与制造

压铸模具的设计与制造摘要本文介绍了压铸模具的设计与制造的基本原理和步骤。
首先,通过分析压铸工艺的特点和要求,确定压铸模具的设计准则和选材原则。
然后,介绍了压铸模具的结构和主要部件,并详细阐述了压铸模具设计的关键要素,如模具尺寸、浇口设计、冷却系统等。
最后,介绍了压铸模具的制造过程和注意事项,包括模具加工工艺、表面处理和模具试模等。
1. 引言压铸是一种常用的金属件成型工艺,广泛应用于汽车、电器、航空航天等领域。
而压铸模具作为压铸工艺的核心部件,直接影响产品的质量和生产效率。
因此,设计和制造高质量的压铸模具对于压铸工艺的成功应用至关重要。
2. 压铸模具设计的准则和选材原则2.1 压铸模具设计准则 - 模具的结构要易于制造和装卸。
- 模具的结构要满足产品的要求,确保产品的尺寸和表面质量。
- 模具的结构要考虑生产的连续性,尽量减少生产过程中不必要的停机时间。
2.2 压铸模具选材原则 - 模具材料应具有足够的强度和耐磨性。
常用的模具材料有H13、5CrNiMo等。
- 模具材料的热稳定性要好,能够承受高温和热冷交替的工作环境。
- 模具材料的导热性要好,以便快速散热,降低模具温度。
3. 压铸模具结构和主要部件3.1 压铸模具结构 - 模具底座:承载模具的主要部件,负责固定模具和提供支撑。
- 固定板:固定模具的位置,具有高度和平面度要求。
- 移动板:用于模具的开合动作,实现铸件的脱模。
- 滑块:用于在模具开合过程中加快铸件的脱模速度。
-缩水板:用于控制铸件在冷却过程中的收缩变形。
3.2 压铸模具主要部件 - 模具腔:用于形成铸件的空腔部分,需要考虑产品的尺寸和形状。
- 浇杆系统:用于将熔融金属注入模腔中的系统,包括浇杆、浇口和溢流槽等。
- 冷却系统:用于控制模具温度的系统,可以通过冷却水或其他介质实现。
4. 压铸模具设计的关键要素4.1 模具尺寸 - 模具尺寸的确定要考虑产品的尺寸和结构要求,确保产品的尺寸和形状的准确性。
压铸模具设计方案
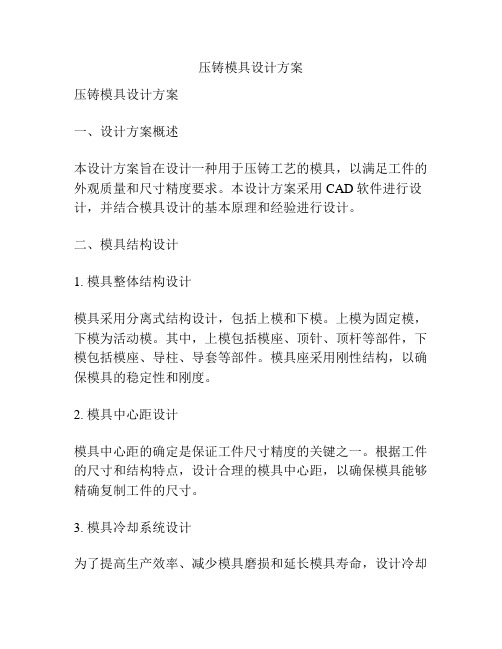
压铸模具设计方案压铸模具设计方案一、设计方案概述本设计方案旨在设计一种用于压铸工艺的模具,以满足工件的外观质量和尺寸精度要求。
本设计方案采用CAD软件进行设计,并结合模具设计的基本原理和经验进行设计。
二、模具结构设计1. 模具整体结构设计模具采用分离式结构设计,包括上模和下模。
上模为固定模,下模为活动模。
其中,上模包括模座、顶针、顶杆等部件,下模包括模座、导柱、导套等部件。
模具座采用刚性结构,以确保模具的稳定性和刚度。
2. 模具中心距设计模具中心距的确定是保证工件尺寸精度的关键之一。
根据工件的尺寸和结构特点,设计合理的模具中心距,以确保模具能够精确复制工件的尺寸。
3. 模具冷却系统设计为了提高生产效率、减少模具磨损和延长模具寿命,设计冷却系统对模具进行冷却。
冷却系统包括冷却孔和进水口,通过冷却水的流动,迅速冷却模具,以提高生产效率和模具寿命。
4. 模具材料选择模具的材料选择是保证模具寿命和使用效果的重要因素。
根据工件的材料和要求,选择适当的模具材料,保证模具具有良好的硬度和耐磨性。
三、模具生产工艺1. 加工工艺规程模具的加工工艺包括数控加工、外圆磨削等。
根据模具的具体结构和工艺要求,制定合理的加工工艺规程,以确保模具的加工质量。
2. 检测工艺模具加工完成后,进行检测以验证模具的质量。
检测工艺包括模具尺寸检测、表面质量检测等,通过合适的检测工艺,确保模具符合设计要求。
四、模具的维护、维修和更换为了保证模具的正常使用和延长其寿命,进行模具的定期维护、维修和更换。
维护工作包括清洁模具、添加润滑剂等,维修工作包括修复模具损伤、更换模具部件等,更换工作包括根据模具磨损程度,定期更换模具部件。
五、结论本设计方案是一种用于压铸工艺的模具设计方案,通过合理的结构设计、材料选择和加工工艺,可以满足工件的外观质量和尺寸精度要求。
同时,通过模具的定期维护、维修和更换,可以保证模具的正常使用和延长其寿命。
压铸模具的介绍

压铸模具的介绍压铸模具是一种用于压铸工艺的工具,它起到了定型、成型和冷却的作用。
压铸模具的设计和制造直接影响产品的质量和生产效率。
本文将介绍压铸模具的基本原理、设计要点和制造工艺。
一、压铸模具的基本原理压铸模具是一种用于将熔融金属注入到模具中并冷却凝固的工具。
它由上模、下模和导柱组成。
在压铸过程中,上模和下模会通过导柱固定,形成一个封闭的空腔。
熔融金属经过喷嘴注入到模具中,并在冷却后形成所需的产品形状。
压铸模具的设计需要考虑产品的结构、尺寸和材料特性,以及冷却系统和排气系统的设置。
二、压铸模具的设计要点1. 产品结构设计:压铸模具的设计首先要根据产品的结构特点确定上模和下模的形状和尺寸。
对于复杂的产品,需要考虑分模的设计,以方便脱模和冷却。
2. 模具材料选择:模具材料需要具有足够的硬度、强度和耐磨性,以抵御高温和高压的工作环境。
常用的模具材料包括铝合金、钢和铜合金等。
3. 冷却系统设计:在压铸过程中,模具需要快速冷却以使产品能够凝固并保持形状。
因此,冷却系统的设计非常重要。
合理的冷却系统可以提高生产效率和产品质量。
4. 排气系统设计:在压铸过程中,熔融金属会产生气体,如果不及时排出,会导致产品表面出现气孔或缺陷。
因此,排气系统的设计也是压铸模具设计的重要一环。
三、压铸模具的制造工艺压铸模具制造工艺包括模具结构设计、数控加工、装配和试模等环节。
1. 模具结构设计:根据产品的结构特点,设计模具的上模、下模和分模等零部件,并确定模具的材料和热处理工艺。
2. 数控加工:根据设计图纸,利用数控机床进行模具的精密加工,包括铣削、车削、钻孔等工序,以保证模具的尺寸和形状精度。
3. 装配:将加工好的各零部件进行装配,包括上模和下模的组装、导柱和导套的安装等。
4. 试模:在模具制造完成后,进行试模,检验模具的性能和准确性。
如果需要调整,可以进行相应的修正和改进。
总结:压铸模具在现代工业生产中起到了至关重要的作用。
压铸模具设计
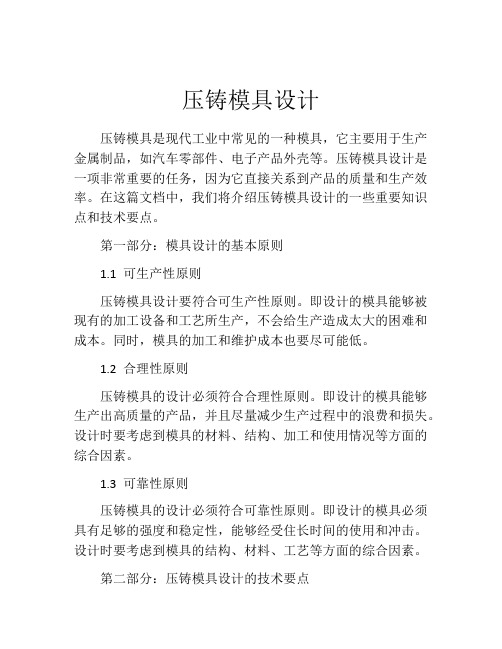
压铸模具设计压铸模具是现代工业中常见的一种模具,它主要用于生产金属制品,如汽车零部件、电子产品外壳等。
压铸模具设计是一项非常重要的任务,因为它直接关系到产品的质量和生产效率。
在这篇文档中,我们将介绍压铸模具设计的一些重要知识点和技术要点。
第一部分:模具设计的基本原则1.1 可生产性原则压铸模具设计要符合可生产性原则。
即设计的模具能够被现有的加工设备和工艺所生产,不会给生产造成太大的困难和成本。
同时,模具的加工和维护成本也要尽可能低。
1.2 合理性原则压铸模具的设计必须符合合理性原则。
即设计的模具能够生产出高质量的产品,并且尽量减少生产过程中的浪费和损失。
设计时要考虑到模具的材料、结构、加工和使用情况等方面的综合因素。
1.3 可靠性原则压铸模具的设计必须符合可靠性原则。
即设计的模具必须具有足够的强度和稳定性,能够经受住长时间的使用和冲击。
设计时要考虑到模具的结构、材料、工艺等方面的综合因素。
第二部分:压铸模具设计的技术要点2.1 模具的结构设计模具的结构设计是压铸模具设计的重要环节。
模具结构的合理性和精度直接关系到产品的质量和生产效率。
在设计时要考虑到模具的内部结构和外部结构。
内部结构包括模具的中心针、滑块、顶出杆、挡板等,这些部件直接影响产品的内部结构和尺寸精度。
外部结构包括模具的固定板、动模板、模座、导柱等,这些部件直接关系到模具的稳定性和加工精度。
2.2 材料选择与热处理压铸模具的材料选择和热处理也是设计时需要关注的问题。
常用的模具材料有铝合金、钢等。
不同的材料具有不同的强度、硬度和热膨胀系数等特性,设计时要根据具体情况选择合适的材料。
同时,进行适当的热处理也可以提高模具的强度和韧性,延长使用寿命。
2.3 模具的加工技术模具的加工技术对模具的质量和加工效率有很大的影响。
加工时需要注意以下几点:2.3.1 避免过度切削和过度磨削,以避免损坏模具表面和内部构件。
2.3.2 注意机床的油极性,避免在精密部件上留下油膜,影响加工精度。
【专业文档】压铸模具设计.doc
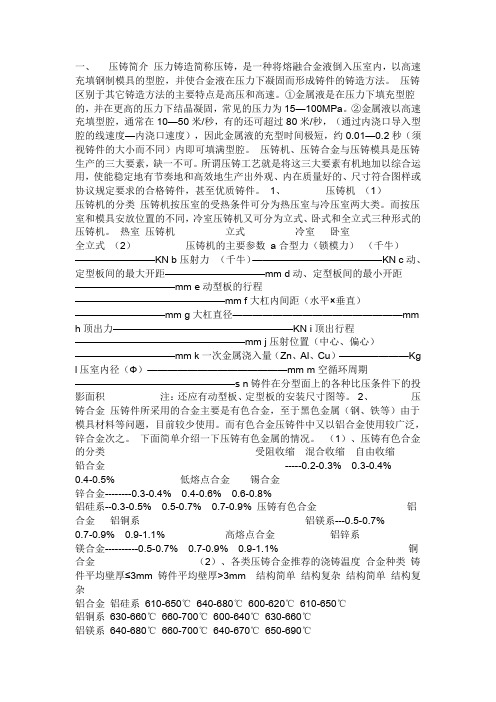
一、压铸简介压力铸造简称压铸,是一种将熔融合金液倒入压室内,以高速充填钢制模具的型腔,并使合金液在压力下凝固而形成铸件的铸造方法。
压铸区别于其它铸造方法的主要特点是高压和高速。
①金属液是在压力下填充型腔的,并在更高的压力下结晶凝固,常见的压力为15—100MPa。
②金属液以高速充填型腔,通常在10—50米/秒,有的还可超过80米/秒,(通过内浇口导入型腔的线速度—内浇口速度),因此金属液的充型时间极短,约0.01—0.2秒(须视铸件的大小而不同)内即可填满型腔。
压铸机、压铸合金与压铸模具是压铸生产的三大要素,缺一不可。
所谓压铸工艺就是将这三大要素有机地加以综合运用,使能稳定地有节奏地和高效地生产出外观、内在质量好的、尺寸符合图样或协议规定要求的合格铸件,甚至优质铸件。
1、压铸机(1)压铸机的分类压铸机按压室的受热条件可分为热压室与冷压室两大类。
而按压室和模具安放位置的不同,冷室压铸机又可分为立式、卧式和全立式三种形式的压铸机。
热室压铸机立式冷室卧室全立式(2)压铸机的主要参数a合型力(锁模力)(千牛)————————KN b压射力(千牛)—————————————KN c动、定型板间的最大开距——————————mm d动、定型板间的最小开距——————————mm e动型板的行程———————————————mm f大杠内间距(水平×垂直)—————————mm g大杠直径—————————————————mm h顶出力——————————————————KN i顶出行程—————————————————mm j压射位置(中心、偏心)——————————mm k一次金属浇入量(Zn、Al、Cu)———————Kg l压室内径(Ф)——————————————mm m空循环周期————————————————s n铸件在分型面上的各种比压条件下的投影面积注:还应有动型板、定型板的安装尺寸图等。
- 1、下载文档前请自行甄别文档内容的完整性,平台不提供额外的编辑、内容补充、找答案等附加服务。
- 2、"仅部分预览"的文档,不可在线预览部分如存在完整性等问题,可反馈申请退款(可完整预览的文档不适用该条件!)。
- 3、如文档侵犯您的权益,请联系客服反馈,我们会尽快为您处理(人工客服工作时间:9:00-18:30)。
头侧:2.6 MPa×7854×10-6 m2=20.42 kN 环形侧:1.36 MPa×4006×10-6 m2=5.45 kN 作用在压射冲头的压力为(20.42-5.45) kN=14.97 kN,这个作用力包括压射时的阻力(即摩擦力),实
15:24
7.1.2 压铸模压力-流量特性曲线和工作点
p
qv 2
2c02 An2
15:24
7.1.2 压铸模压力-流量特性曲线和工作点
15:24
7.1.2 压铸模压力-流量特性曲线和工作点
15:24
7.1.2 压铸模压力-流量特性曲线和工作点
金属液流过压铸模浇注系统时,因摩擦等原因会有能量损失,表现为金 属液的压力下降,以致测得的金属液流速小于理论流速。实测流速与理 论流速之比称为流量系数C0。C0的最大值为1(实测流速就是理论流速, 但因摩擦阻力总是存在的,故C0不可能是1),C0的最小值为0(整个流动 系统封闭且静止)。因此流量系数值C0在1~0之间。相同压射比压之下, 摩擦阻力越小,流速越大,金属液流量就越大,压铸模压力-流量特性曲 线斜度越小。而要达到同样流量时,流量系数越小需要的压射比压越大, 如图7.10所示。C0=0.4是许多压铸模浇注系统流量系数代表值,C0=0.7 则是希望值。
(4) 推出机构。推出机构是指铸件成型后动、定模分开,把铸件从模具中推出的装置。一般情况下, 推出机构由推杆、复位杆、推杆固定板、推板以及用于推出机构导向的推板导柱、推板导套等组成。如 图7.18中零件4、5、3、10、9及6、7。
(5) 抽芯机构。铸件的侧面有凹凸或孔穴时,需要用侧型芯来成型。在铸件脱模之前,必须先将侧 型芯从铸件中抽出,这个使侧型芯移动的机构称为抽芯机构或侧向抽芯机构。抽芯机构的形式很多,图 7.18所示的模具为斜导柱抽芯机构,由斜导柱18、滑块17、楔紧块16、挡块12、弹簧15、螺杆14等组 成,由斜导柱驱动侧型芯移动,完成侧向抽芯。
压铸机压力-流量特性曲线计算作图数
据来自压铸机空载测试曲线及压射机构结构
尺寸,计算作图步骤如下:
(1)
压射活塞两侧的面积分别与图
7.2(a)及图7.2(b)测试所得的压力相乘, 乘
积之差即为作用于压射冲头上的压力。
(2)
作用于压射冲头上的压力除以压射
冲头的面积,其商即为空载时的压射比压,
也就是压铸机压力-流量特性曲线与P-q2v
图中纵坐标轴的交点。
(3) 图7.2(c)中压射冲头行程除以时间,
求得压射冲头的压射速度。
15:24
7.1.1 压铸机压力-流量特性曲线
(4) 压射冲头速度乘以压室截面积,其积为空载时的压射流量,此流量的平方即为压铸 机压力-量特性曲线与P-q2v图中横坐标轴的交点。
(5) 连接以上两点,就得到该压铸机的压力-流量特性曲线。 由上所得的曲线表示该压铸机压射机构为图7.1所示尺寸时的特性,若压射冲头尺寸变化,
储能器压力变化及速度控制阀开度变化,此曲线都随之改变。 压射冲头直径不同,压铸机压力-流量特性曲线很容易修正。因为作用在压射冲头上的压力
一定时,冲头直径增大,则压射比压变小。而空载压射,冲头速度不变时,冲头面积越大, 金属液流量亦越大。所以当压射冲头直径增大时,压铸机压力-流量特性曲线的斜率减小, 如图7.4所示。
15:24
7.1.1 压铸机压力-流量特性曲线
当纵坐标是比压p、横坐标是流量的平方q2v 时,此特性曲线表现为一直线。图7.3所示为 典型压铸机压力-流量特性曲线。由图7.3可知,画该图只需两个点,即该直线与纵、横坐 标轴的两个交点。直线与纵坐标轴的交点是压铸机空载结束时的压射比压,直线与横坐标 轴的交点是压铸机空载时计算得出的金属液流量平方,这两个值都按测试曲线(见图7.2)计 算而得。
15:24
7.1.2 压铸模压力-流量特性曲线和工作点
15:24
7.1.2 压铸模压力-流量特性曲线和工作点
15:24
7.2 压铸模设计原则
压铸模设计应该遵循以下原则: (1) 压铸模所成型的压铸件应符合几何形状、尺寸精度、力学性能和表
面质量等技术要求。 (2) 模具应适应压铸生产的工艺要求。 (3) 在保证压铸件质量和安全生产的前提下,应采用先进、简单的结构。
(7) 冷却系统。为了平衡模具温度,使模具在要求的温度下工作,防止型腔温度急剧变化而影响铸 件质量,模具常设置冷却系统。冷却系统一般是在模具上开设冷却水道。
(8) 模体。模体包括定模座板、定模套板、动模座板、动模套板、支承板、垫块等。模体起装配、 定位和安装作用。如图中的零件27、19、1、32、31、8等。
际作用在内浇口处的压力小于此力。压射时的冲头速度从图7.16(c)可以算出为(129÷65) m/s=1.98 m/s。内浇口的流速vn为(1.98×1963÷70) m/s=55.5 m/s。 不考虑摩擦力,压射比压为14.97 kN÷(1963×10-6 m2)=7626 kPa≈7.6 MPa。 泵出率为1.98 m/s×l963×10-6 m2=0.00388 m3/s=3.88 L/s。
(6) 排溢系统。排溢系统是指根据金属液在型腔中的充填情况而设计的溢料槽和排气槽,其作用是 排除型腔中的气体、涂料残渣以及冷污金属液。溢料槽的设置要与浇注系统相配合,以便更好发挥作用, 一般开设在成型零件上,位于最先流入型腔的金属液流的末端;排气槽一般开设在分型面上,也可以用 通孔套板的型芯头间隙、推杆间隙等排气。
15:24
7.3 压铸模结构组成
压铸模由定模和动模两部分组成。定模固定在压铸机定模安 装板上,定模上有形成直浇道的浇口套,浇口套与压铸机的 喷嘴或压室相接;动模固定在压铸机动模安装板上,并随动 模安装板作开合模移动。合模时,动模与定模闭合构成型腔 和浇注系统,金属液在高压下充满型腔。开模时,动模与定 模分开,借助设在动模上的推出机构将压铸件推出。
分型面的表示一般是:为了分开模具,若分型面两边的模具都移动,就 用“←|→”表示;若一方不动另一方移动,则用“←|”表示,“|”表示分 型面位置,箭头指向移动方向。假如一副压铸模上有多个分型面,就按 分开的先后次序标出“A”、“B”、“C”、……或“Ⅰ”、“Ⅱ”、 “Ⅲ”、……等。
15:24
7.1.1 压铸机压力-流量特性曲线
压射速度是通过改变速度控制阀的开度来进行调整的。开度增大,压力 油通过速度控制阀的流动阻力减小,进入压射腔的压力油流量大为增加, 压射速度亦增大,因此,金属液流量随之增加。而速度控制阀开度变化, 压铸机储能器压力却不受其影响,亦即压射比压不变。故速度控制阀不 同开度的压铸机压力-流量特性曲线在纵坐标轴上交于一点,如图7.6所 示。
15:24
7.1.1 压铸机压力-流量特性曲线
经过对压铸机空载状态检测(如图7.2所示测试曲线),即可作出以压射比压为纵坐标,以金 属液流量为横坐标的直角坐标曲线,这种曲线表示了压铸机的压射特性,称压铸机的压力流.1 压铸机压力-流量特性曲线
第7章 压铸模设计概述
15:24
第7章 压铸模设计概述
压铸模是进行压铸生产的主要工艺设备。压铸生产 能否顺利进行,压铸件质量有无保证都与压铸模结 构的合理性和先进性有关。设计时必须对铸件结构 工艺性进行分析,了解所选用的压铸机的工作特性 和技术参数,掌握不同情况下金属液的充填特性以 及考虑加工制造条件和经济效果。
15:24
图7.14 储能器压力对内浇口处金属液流量的影响
7.1.2 压铸模压力-流量特性曲线和工作点
15:24
图7.15 调整压射速度控制阀对内浇口处金属液流量影响 (a)—一圈;(b)—二圈;(c)—三圈及全打开
7.1.2 压铸模压力-流量特性曲线和工作点
例:压铸机压射机构尺寸如图7.1所示,压铸铝合金压铸件,压铸件重量(包括浇注系统和溢流系统在 内为)7为0 6m.3m72,N 压70铸4时.7g测,量密的度压为铸2机.7 测g/c试m曲3,线折如合图压7.铸16件所的示总。体试积求为压2铸61机cm-压3。铸压模铸体件系的压内力浇-流口量截特面性积曲A线n 、 工作点的压射比压和泵出率、流量系数和内浇口流量。
(2) 浇注系统。浇注系统是连接模具型腔与压室,引导金属液进入型腔的通道。它是由直浇道、横 浇道、内浇口及余料组成的。图7.18中的浇口套25、浇道镶块26等构成浇注系统。
(3) 导向零件。导向零件是引导动模开合模时可靠地按一定方向进行运动并确保动定模准确定位的 零件。导向零件一般由导柱和导套组成,如图7.18中的导柱28、导套30。
15:24
7.1.1 压铸机压力-流量特性曲线
储能器压力增大或降低时,最终压射比压和金属液流量都随之增大或减少,改 变储能器内的压力,则所得的压力-流量特性曲线互相平行。因此,求出压铸机 储能器某一压力下的压力-流量特性曲线后,若储能器压力变化则可修正成该储 能器各种压力时的压力-流量特性曲线,如图7.5所示。
除上述部分之外,压铸模内还有紧固用的螺钉、圆柱销等。 15:24
7.4 分型面设计
7.4.1 分型面的形式 7.4.2 分型面选择原则
15:24
7.4 分型面设计
分型面的确定是模具设计中的第一个程序。将模具适当地分成两个或两 个以上可以分离的主要部分,可以分离部分的接触表面分开时能够取出 压铸件及浇注系统,成型时又必须紧密接触,这样的接触表面称为模具 的分型面。
15:24
第7章 压铸模设计概述
7.1 压铸机特性曲线 7.2 压铸模设计原则 7.3 压铸模结构组成 7.4 分型面设计