4挤出机3
挤出机原理介绍

挤出机原理介绍(总4页) -CAL-FENGHAI.-(YICAI)-Company One1-CAL-本页仅作为文档封面,使用请直接删除挤出机定义介绍在塑料挤出成型设备中,塑料挤出机通常称之为主机,而与其配套的后续设备塑料挤出成型机则称为辅机。
塑料挤出机经过100多年的发展,已由原来的单螺杆衍生出双螺杆、多螺杆,甚至无螺杆等多种机型。
塑料挤出机(主机)可以与管材、薄膜、捧材、单丝、扁丝、打包带、挤网、板(片)材、异型材、造粒、电缆包覆等各种塑料成型辅机匹配,组成各种塑料挤出成型生产线,生产各种塑料制品。
因此,塑料挤出成型机械无论现在或将来,都是塑料加工行业中得到广泛应用的机种之一。
塑料挤出机的工作原理螺杆挤出机是塑料成型加工最主要的设备之一,它通过外部动力传递和外部加热元件的传热进行塑料的固体输送、压实、熔融、剪切混炼挤出成型。
螺杆挤出机自诞生以来,经过近百年的发展,已由普通螺杆挤出机发展为新型螺杆挤出机。
尽管新型螺杆挤出机种类繁多,但就挤出机理而言,基本是相同的。
传统螺杆挤出机挤出过程,是靠机筒外加热、固体物料与机筒、螺杆摩擦力及熔体剪切力来实现的。
“摩擦系数”和“摩擦力”,“粘度”和“剪应力”是影响传统螺杆挤出机工作性能的主要因素,由于影响“摩擦”和“粘度”的因素十分复杂,因此,传统螺杆挤出机挤出过程是一个非稳定状态,难以控制,对某些热稳定性差、粘度高的热敏性塑料尤为突出。
自60年代以来,世界上各国学者对螺杆挤出机理进行了大量研究,也取得了明显的成就,但由于他们的研究大多局限于传统塑料挤出成型机理、机械结构形式和换能方式,因而一直未能取得重大突破。
传统螺杆挤出机所存在的如体积庞大、能耗高、噪音大、产品质量提高难等一系列缺点没有得到根本解决。
塑料挤出机特点1.模块化和专业化塑料挤出机模块化生产可以适应不同用户的特殊要求,缩短新产品的研发周期,争取更大的市场份额;而专业化生产可以将挤出成型装备的各个系统模块部件安排定点生产甚至进行全球采购,这对保证整期质量、降低成本、加速资金周转都非常有利。
4 塑料挤出机
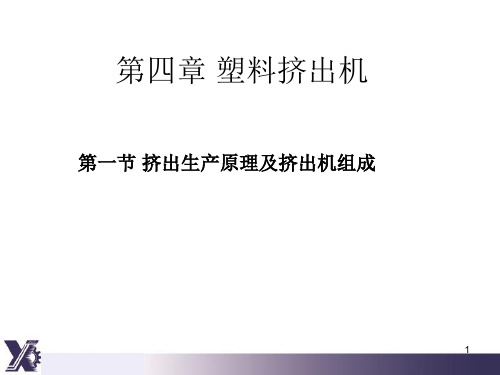
第一节 挤出生产原理及挤出机组成
1
聚合物挤出成型和注射成型是高分子材料产 品制造领域的两大加工技术, 品制造领域的两大加工技术,其中挤出成型能够 模塑成型所有的热塑性塑料和某些热固性塑料, 模塑成型所有的热塑性塑料和某些热固性塑料, 主要应用于管材 线材、板材、棒材、 管材、 主要应用于管材、线材、板材、棒材、片材和异 制品的成型。 型材制品的成型 型材制品的成型。 由于挤出成型具有效率高、投资少、制造方 由于挤出成型具有效率高、投资少、 便、连续性生产和环境清洁等优点而成为塑料制 品主要的成型方法之一, 品主要的成型方法之一,成型的塑料制品已广泛 应用于医疗、通讯、农业、建筑、石油化工、 应用于医疗、通讯、农业、建筑、石油化工、轻 工等国民经济的各个行业。据统计, 工等国民经济的各个行业。据统计,挤出制品的 产量已占整个塑料制品总产量的40%以上。 以上。 产量已占整个塑料制品总产量的 以上
成型、挤出成型、压缩成型、 成型方法:注射( 成型方法:注射(塑)成型、挤出成型、压缩成型、 压铸成型、吹塑成型等。 压铸成型、吹塑成型等。
22
随温度升高,聚合物将呈现玻璃态、高弹态、 随温度升高,聚合物将呈现玻璃态、高弹态、粘流态三 种状态。 种状态。
聚合物的物理状态与温度的关系 1-线性非结晶聚合物; -线性非结晶聚合物; 2-线形聚合物; -线形聚合物; 3-金属。 -金属。
37
2、等深变距螺杆
强度好、可增转速
少
3、变深变距螺杆
机加工难
38
39
40
(三)螺杆头部结构
常用
流动型好料
流动性差料 挤粘度大、导热 不良或有明显熔 点料
防物料滞留 挤电缆
41
(四)螺杆材料 耐高温、耐磨损、耐腐蚀、高强度,切削性能好,热处理性能 好。 45,40Cr、氮化钢、38CrMoAl等。 高强度耐磨耐腐蚀合金钢:34CrAlNi、31CrMo12等。 表面喷涂强化。 (五)新型螺杆 熔融效率低、挤出量不高、塑化混炼不均、压力波动、温度波 动、产量波动大。不适应特殊料。 1、分离型螺杆 压缩段增设副螺纹 熔融料、未熔料早 分离 2、屏障螺杆 设置屏障段 3、销钉螺杆 设销钉 4、组合螺杆 有带加料段的螺杆本体和螺杆元件组成。
40塑料挤出机 技术参数

40塑料挤出机技术参数
40塑料挤出机是一种用于制造塑料制品的设备。
它具有以下技术参数:
1. 挤出能力:40塑料挤出机的挤出能力可根据不同的生产需求进行调整。
它可以连续挤出塑料材料,使其通过模具形成所需的形状和尺寸。
2. 加热方式:该挤出机采用电加热方式,通过加热器将塑料材料加热至适宜的温度。
这样可以提高塑料的流动性,使其更容易挤出并形成所需的制品。
3. 控制系统:40塑料挤出机配备了先进的控制系统,可以精确控制挤出过程中的温度、压力和速度等参数。
这样可以确保产品的质量和生产效率。
4. 模具设计:挤出机的模具设计非常重要,它决定了最终产品的形状和尺寸。
40塑料挤出机可以根据不同的产品要求进行模具设计,并具备灵活的模具更换功能,以满足不同产品的生产需求。
5. 能耗控制:为了提高能源利用效率,40塑料挤出机配备了能耗控制系统。
它可以监测和控制设备的能耗,以减少能源浪费并降低生产成本。
40塑料挤出机是一种功能强大、技术先进的设备,适用于制造各种
塑料制品。
它的挤出能力、加热方式、控制系统、模具设计和能耗控制等技术参数都经过精心设计,以提高生产效率和产品质量。
通过使用这种挤出机,我们可以实现高效、高质量的塑料制品生产,满足市场需求。
挤出机操作规范以及安全生产注意事项范文

挤出机操作规范以及安全生产注意事项范文挤出机是一种常用的塑料加工设备,广泛应用于塑料制品制造行业。
为了保障生产操作的安全性和提高生产效率,我们需要严格遵守挤出机操作规范,并注意安全生产事项。
下面是挤出机操作规范以及安全生产注意事项的范文。
一、挤出机操作规范1. 入场前准备(1)检查挤出机设备的电气系统是否正常,无短路和漏电现象;(2)检查润滑系统是否正常工作,润滑油是否充足;(3)检查挤出机的冷却系统是否正常,冷却水是否充足;(4)检查挤出机的传动装置和运动部件是否有异常情况。
2. 开机前准备(1)检查挤出机的各个控制开关是否处于停止位置;(2)检查挤出机的温度控制器是否已设定正确的温度;(3)检查挤出机的进料系统是否正常,原料是否充足;(4)检查挤出机的挤出口是否清洁。
3. 操作过程(1)在开机前,佩戴好个人防护装备,包括安全帽、耳塞、口罩和工作服等;(2)按照操作顺序,逐步启动挤出机的各个控制开关;(3)监测挤出机的运行状态,及时发现异常情况并采取相应的措施;(4)严禁将手或其他物品伸入挤出机的工作区域,以免造成伤害;(5)定期清洁挤出机的工作区域和周围环境,保持整洁有序。
4. 关机后操作(1)关闭挤出机的所有控制开关;(2)清理挤出机的工作区域和周围环境,确保无杂物和污物;(3)对挤出机进行巡检,检查是否有损坏或需要维修的部件;(4)及时记录挤出机的运行情况和生产数据,做好相关文件的整理和归档。
二、安全生产注意事项1. 个人防护(1)佩戴好个人防护装备,包括安全帽、耳塞、口罩、工作服和防护手套等;(2)严禁穿着松散的衣服,以防被挤入挤出机的工作区域;(3)遵守相关工作规程,不擅自解除安全装置;(4)遵循操作规范,不靠近挤出机的工作区域。
2. 设备维护(1)定期检查挤出机的电气系统、传动装置和冷却系统的工作情况;(2)及时进行设备的润滑、清洁和维修,保持设备的正常运行;(3)严禁在设备运行时进行维修和调整,必要时应停机并采取相应的安全措施。
《高分子材料成型加工基础》课件——项目三-挤出成型

三.辅助设备:
• 前处理设备:预热. 干燥 • 控制生产的设备:各种控制仪表
四. 挤出机的一般操作法:
• 处理挤出物的设备:冷却定型. 牵引.切割.卷取
① 开机前准备: ② 料最好先干燥、必要时须预热 ③ 换上新的多孔板及滤网,检查并装上机头 ④ 检查电器及机械,在传动部分加足润滑油
⑤ 开电热预热:先预热机头、后机身,同时料 斗座通水冷却
● 3.螺杆: ● 挤出机的改进主要在螺杆上 ● (1)螺杆直径(D)与长径比(L/D): ● D↑:挤出机大,产量高(产量∝D2) ● L/D: L为有效长度 ● L/D↑:利于塑化, ↑产量,适应性强
(2)螺杆各段的作用:
• ①加料段: • 加料口(2~10D) • 使塑料受热前移、
压实物料
使塑料密实、排气 ● 热:外加热、 内摩擦热,物料由固体→熔体 ● 完全塑化后经机头挤出成型、冷却定型或拉、吹胀为最终制品
二.塑料在挤出成型中的受热:
● 热量来源:外加热与摩擦热 ● 加料段:
固体物料,螺槽深,温差大,外加热为主 ● 均化段:
熔体,螺槽浅,温差小,摩擦热为主 ● 压缩段:
介于以上两段之间 ● 故挤出机必须分段控温
一.挤出成型的塑料
● 几乎所有热塑性料和某些热固性料:如PVC、PE、PP、PS、PA、ABS、PC等及 PF、UF(脲醛树脂)等
二.挤出成型的制品
● 管、板、单丝、膜、电线、棒、异型材、中空制品(瓶等)等
三.挤出成型特点
生产连续化 生产效率高:挤出制品单机产
量比注塑制品大一倍以上
适应范围广 经济效益好:设备成本低、投资收效快
一.挤出成型设备(挤出生产线或挤出机组) ● ——以塑料异型材为例
挤出机原理

挤出机原理
挤出机是一种常用的塑料加工设备,其原理是利用螺杆旋转将塑料颗粒加热、
熔化,并通过一定的压力将熔融塑料挤出成型。
挤出机的工作原理可以分为三个主要步骤,加料、熔化和挤出。
首先,塑料颗粒被输送到挤出机的进料口,然后通过螺杆的旋转和推进,塑料
颗粒被逐渐推送到机筒的加热区。
在加热区,塑料颗粒受到高温加热,逐渐熔化成为熔融状态的塑料熔体。
同时,螺杆的旋转还起到了混合和均匀加热的作用,确保塑料熔体的温度和性能均匀一致。
接下来,熔化的塑料熔体被推送到机筒的压力区,通过螺杆的旋转和挤压,塑
料熔体受到一定的压力,使其在机筒内得到进一步的挤压和塑形。
在这个过程中,塑料熔体的温度和压力得到了精确的控制,以确保挤出成型的塑料制品具有良好的物理性能和外观质量。
最后,经过压力区的挤出成型后的塑料制品通过模具头,按照模具的形状和尺
寸得到所需的成型产品。
挤出成型的塑料制品可以是管材、板材、薄膜、型材等不同形状和尺寸的制品,广泛应用于塑料加工行业。
总的来说,挤出机的工作原理是通过螺杆的旋转和推进,将塑料颗粒加热、熔化,并通过一定的压力将熔融塑料挤出成型。
这种工作原理简单高效,能够满足不同形状和尺寸的塑料制品的生产需求,是塑料加工行业中不可或缺的重要设备之一。
双螺杆挤出机课件

5 工作原理
☆ 非啮合型双螺杆挤出机
拖曳流3:同时随着螺杆的旋转 ,在两螺杆的间隙处物料不断受 到搅动并被不断带走而更新(不 论两螺杆的转向如何),产生流 动3。
拖曳环流4:特别是在异向旋转过程中,物料在A处 受到阻碍,产生了流动4。
而所有这些流动形式都增加了对物料的混炼和剪切 作用。
由于这种啮合形式的双螺杆没有自清洁作用,所以
通道。
10
5 工作原理
☆ 啮合型异向双螺杆挤出机
少量物料被拉入两螺杆之间的 径向间隙,受到 螺棱和螺槽间 的研磨和滚压作用,此作用与 压 延机上物料的滚压作用相似 ,称为“压延效应”
由于压延效应,使机筒壁和轴承受力不均匀而局 部受压磨损,故异向旋转的双螺杆只能在较低的 转速下工作。
异向啮合型双螺杆混炼剪切作用较弱,故适用于 热敏料和需要受热时间短的物料的成型。
16
1、温度
☆ 热量来源 温度是双螺杆挤出过程得以进行的重要条件之
一。物料由固态变为粘流态,需要热量。挤出过 程热量的来源有两个: a.机筒外部加热器通过机筒传给物料的热量。 b.物料与物料之间、物料与螺杆、物料与机筒之间 的摩擦热和物料受剪切而生成的热量。
17
1、温度
☆ 温度的调节
加料口:为保证物料顺利加入,必须保持固体的摩 擦性质,故此段机筒不但不要加热,还需要冷却。 在加料口下游,机筒温度则需升高,以便将物料加 热,促使其熔融。
双螺杆挤出过程中机械能和加热器提供的热能不但与双螺杆 挤出机的类型有关,还与螺杆构型和不同的螺杆区段有关。
24
4、能耗
挤出过程能力沿挤压系统的变化示意
25
4、能耗
电机、加热器提供的能量与螺杆直径的关系 26
挤出机工作原理
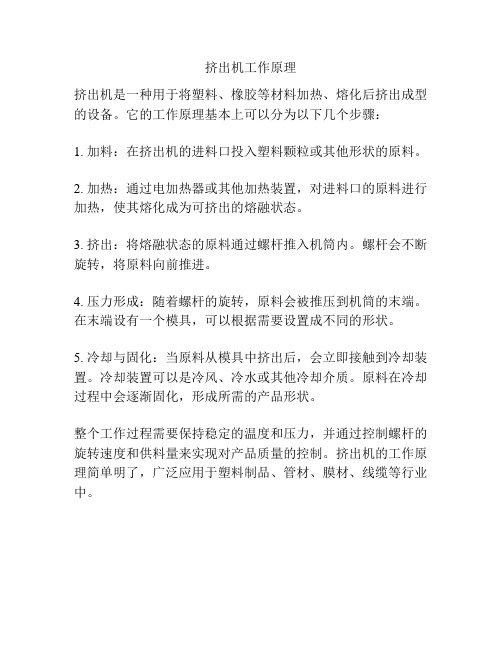
挤出机工作原理
挤出机是一种用于将塑料、橡胶等材料加热、熔化后挤出成型的设备。
它的工作原理基本上可以分为以下几个步骤:
1. 加料:在挤出机的进料口投入塑料颗粒或其他形状的原料。
2. 加热:通过电加热器或其他加热装置,对进料口的原料进行加热,使其熔化成为可挤出的熔融状态。
3. 挤出:将熔融状态的原料通过螺杆推入机筒内。
螺杆会不断旋转,将原料向前推进。
4. 压力形成:随着螺杆的旋转,原料会被推压到机筒的末端。
在末端设有一个模具,可以根据需要设置成不同的形状。
5. 冷却与固化:当原料从模具中挤出后,会立即接触到冷却装置。
冷却装置可以是冷风、冷水或其他冷却介质。
原料在冷却过程中会逐渐固化,形成所需的产品形状。
整个工作过程需要保持稳定的温度和压力,并通过控制螺杆的旋转速度和供料量来实现对产品质量的控制。
挤出机的工作原理简单明了,广泛应用于塑料制品、管材、膜材、线缆等行业中。
- 1、下载文档前请自行甄别文档内容的完整性,平台不提供额外的编辑、内容补充、找答案等附加服务。
- 2、"仅部分预览"的文档,不可在线预览部分如存在完整性等问题,可反馈申请退款(可完整预览的文档不适用该条件!)。
- 3、如文档侵犯您的权益,请联系客服反馈,我们会尽快为您处理(人工客服工作时间:9:00-18:30)。
∴ H1= A L2+ H3
(3-5)
③ 由经验公式,确定H1 实用中, 为计算方便,常直接采用经验公式来确定H1 ε 几= 0.93 H1 /H3 即: H1= ε 几H3 / 0.93 误差<0.1
(3-6)
一般讲, 由固体输送理论知:H1↑,Qs↑,故较深的H1对提高产量有利。 注意: H1确定后,必须对螺杆强度进行校核,然后再对H1作修正。
18
(六)螺纹断面及螺杆头的确定:
1) 螺纹断面:有矩形、锯齿形、梯形等,常用为:矩形和
锯齿形两种.
矩形断面的螺槽容积较大,适用于加料段。锯齿形断面的后缘有较 大的倾角α( α≤30° ),且过渡圆角R 较大,有利于物料的流动,同 时有较好的混合和均化作用,适合于压缩段和均化段。梯形断面其推进 面倾角 α=30° ,后缘面倾角β ≤45° ,可提高产量和塑化效果。 e=(0.08~ 0.12)Ds。
9
增大L/D有如下好处:
① L/D↑,螺杆总长↑,物料停留时间长,塑化更充分,故可n↑→Q↑; ② 由流率公式可知:L3 ↑,Qp↓Ql ↓故Q ↑; ③ L/D↑,对应L3↑,螺杆特性变硬,产量波动减小; ④ L3↑,易于熔体温度均化,易于实现低温挤出。
但 L/D不可无限增大。
① L↑,Q ↑,相应功率N ↑,生产成本↑ ; ② L太长,加工及装配困难(螺杆与机筒的同心度不易保证),螺机筒,使用寿命↓; ④ L/D太大,螺杆强度、刚度下降,当n↑,扭矩加大,故L/D有一个高限。 e.g. 有人作过实验:Φ 45机,(38GrMoAlA钢) HDPE n=80 L/D 限=37.5 n=100 L/D 限=32 PP n=100 L/D ≤30 否则螺杆强度不够。 因此: L/D增大尽管有益,但不可想当然盲目增加,其有一个极限。
PA
40-60%
(2-4)D
20-30%
12
2)各段深度:
ⅰ.一般首先确定H3: ① H3↓(变浅),γ ↑,剪切变强,塑化好; ② H3↓(变浅),料层薄,利于温度均化; ③ H3↓(变浅),螺杆特性变硬,产量波动减小。 H3不可太浅,因为:对热敏料,H3 ↓, γ ↑,物料易过热分解; 对低阻口模, H3 ↑,Q↑。 有实验证明: Φ 45机, H3 =3 mm , 若: H3 ↑=3.5 mm,均化质量↓流率波动 ↑ ; H3 ↓ =2 mm, Q ↓ → 30% ↓。 因此, H3 的确定应慎重,存在一个最佳值。 一般, 按经验方法: H3=k D k = 0.025-0.07 (大直径D,选k下限)
7
② 按产品规格(即制品断面尺寸)来确定螺杆直径D:
通常:螺杆直径D应与所生产的制品断面有一个合适的搭配关系。 ( 见表4-8): 表4-8
螺杆直径 硬管直径 吹模折径 挤板宽度 θ30 3~ 30 50~300
单螺杆直径与挤出制品尺寸的关系
θ 45 10~ 45 100~500 θ 65 20~ 65 400~900 400~800 θ 90 30~ 120 700~1200 700~1200 θ 120 50~ 180 ~2000 1000~1400
单位 mm
θ 150 80~300 ~3000 1200~2500 θ 200 120~400 ~ 4000 ~
大截面制品 → 大螺杆直径挤出机 小截面制品 → 小螺杆直径挤出机 由此可充分发挥设备功能,并易保证制品质量。 实践表明:以小马拉大车或大马拉小车均是不科学的。 即应:
8
㈡ 螺杆长径比(L/D):
(3 - 3)
13
上海塑料制品二厂 k 的经验数据
塑料 U-PVC R-PVC PS PE PA k 0.03-0.06 0.035-0.07 0.05-0.07 0.03-0.04 0.02-0.03
14
ⅱ.其次,确定H1:
① 根据ε几 和 H3,确定H1 :
( Ds H1 ) H1 ( S1 e1' ) 几 ' ( Ds H 3 ) H 3 ( S3 e3 )
16
(四)螺杆与机筒间隙δ 0的确定:
i. δ 0 的重要性: δ 0 是挤压系统设计中的一个重要指标, ① ∵ 根据流率公式,漏流Ql ∝ δ 0 3; ∴ δ 0 稍大一点, Ql 增大许多, Q↓ 实验表明: 当δ 0 / H3=15%时,漏流Ql太大,螺杆失效。 故: δ 0 ↓,可使Q↑。 ② δ 0 太小, 装配和加工困难,设备生产成本↑; ③ δ 0减小一点,N驱相应增加许多 ; 综上所述, δ 0 必须取得合适。 ④ 设计的δ 0 是否保得住,取决于螺杆与机筒的加工、装配精度。 ⅱ. δ 0 的确定: ① 根据被加工物料品种:PC、PVC—— δ 0 可大些(高粘料,热敏料); PE、PA —— δ 0 可小些(中、低粘料); ② 按经验公式: δ 0 =(0.003-0.005)D 螺杆直径大者,系数取小值 ; ③ 参照标准选取:教材表3-6(材料为38GrMoAlA).
17
(五)螺距S、螺旋角Φ及螺纹头数i:
1) S与Φ: 由螺距与直径和螺旋角的关系有:
S=π D tg Φ 即: Φ= tg-1 S/π D ∵ 对常规单螺杆而言,为加工方便计,取S=D, ∴ Φ= tg-1 (1/π )=17°42’
2)头数i :
对于单螺杆,实验表明: 单头(i =1)流率波动小,常用; 双头(i =2)流率波动变大,填充不匀。
3
1.3.3 常规单螺杆
1. 螺杆结构形式(有三种)
① 等距变深——加工容易、最常用。
特点:成本低;H1深进料量大;但L1 段螺杆强度有所削弱。
② 等深变距——加工较难,不常用。
特点:螺槽深度不变,螺杆强度高; 用改变螺距来形成压缩比;H3与H1 等深,均化作用较差;加工成本高。
③ 变深变距——特殊用途,加工 难,不常用。
L:为螺杆有效长度
据统计: 国内外L/D 均有加大的趋势:
年代 30-40 50-60 70-80 90-00 2000-
L/D
8~15
15~20
20~25
25~30
30~45
我国;目前常规单螺杆挤出机 L/D 一般为25-30(低于25的属老型号机) 国外;发达国家(德、日、奥、美等)目前L/D =30-35,少数大型机 D≥600,L/D可达45。
19
2)螺杆头:
作用: 使料流由螺旋运动→直线运动,平稳进入口模。 常用形式(六种):见教材图4-60
20
3. 螺杆与传动箱主轴的连接方式 :
(1)扭矩传递:
单键:—— 加工容易、装配容易、适于中、大型机,常用; 双键:—— 装配较难,适于中、大型机,但不常采用; 花键:—— 装配容易,适于小型机和螺杆结构所限无法采用平键 的时候,常用。
特点:具有以上两种螺杆的 优点,适于挤出增强塑料制品;制造 成本高。
4
(1)等距变深螺杆的基本结构
① 渐变螺杆——适于非结晶(无定形)塑料(如PVC、PC、PS等); L2 =(10-20)D , 也可用于结晶性塑料 ② 突变螺杆——适于结晶型塑料(如PE,PP,PA等); L2 =(2-5)D
5
2.常规单螺杆的几何参数
(1) 螺杆外径: D ; (2) 螺杆长径比:L/D ; (3) 螺杆分段: 常规螺杆3段: L1—加料段(或称固体输送段); L2—熔融段(或称压缩段); L3—计量段(或称均化段)。 (4) 螺槽深度: H, H1—等深; H2—渐浅; H3—等深; (5) 压缩比: ε 是确定H1和H3的依据; (6) 螺距 : S 螺棱上一点与相邻螺棱上对应点之间的距离 (常规螺杆S=D) ; T 导程:螺杆转一圈螺棱上一点上升的距离 (7) 螺纹升角: ф (亦称螺旋角); (8) 螺纹头数: i (或P),单螺杆常用单头; (9) 螺棱宽度: e (螺棱法向宽度), 轴向棱宽为e’; (10) 螺杆与机筒的配合间隙: δ 0 体现螺杆与机筒的加工精度。
10
㈢ 螺杆各段长度及深度:
I)各段长度:
ⅰ. L1 的长度要求:Qs≥ QL3 L1↑,Zb ↑, Qs ↑; L3↑, Qp ↓, Ql ↓, QL3 ↑; 通常: 比热大、熔点高、潜热高者, L1宜长;导热系数大,比热小者, L1可短。 根据实践所获经验数据:设计时可取: L1=(30-65)%L,加工结晶型塑料(如PE、PA等); L1=(10-25)%L,加工非结晶型塑料(如PVC、PC等),加工PVC粉; ⅱ. L2 的长度 通常: L2 按经验数据选取:渐变螺杆 L2 = 50~60%L 突变螺杆 L2 = (2-5)D ⅲ. L3 的长度: L3 = L-( L1 + L2 ) L3 ↑的好处: ① Q↑,∵ Qp ↓, Ql ↓; ② 螺杆特性变硬,Q波↓ ; ③ 分散混合能力↑ ; ④ 压力峰前移,压力波动↓。
聚合物成型机械
(Polymer Processing Machinery)
第三节
单螺杆挤出机
第三节 挤出机挤压系统
1.3.1挤压系统的结构
2
1.3.2 评价挤压系统优劣的标准
考核指标(评定判据): (1)挤出质量: 外观好 ——表面光滑、无斑痕、水纹、鲨鱼皮及竹节形等; 混合好 ——制品各部分力学、光学及化学性能均匀,组分分散好; 流率稳定 ——温度波动及压力波动小; 低温挤出 ——能实现较低Tf下的挤出,产品易定型,变形小。 (2)产量:考核比流率Q/n,即比较同规格螺杆在单位时间内每转一圈 的挤出量。 Q/n 的大小,在一定程度上反映了螺杆结构参数是否合理。 e.g. Φ 65挤出机,常规螺杆,通常Q/n=1(kg/r),被认为较佳。 设计追求目标: 同规格螺杆,工艺条件相同下, Q/n尽可能高。 (3)单耗: N/Q 较低,即每公斤挤出物所耗的功率小。 (4)适应性:能加工多种物料,不能片面追求。因为通常专用螺杆产量 和质量更高。 (5) 制造难易及寿命:制造难,则造价高,但若因此使产量和质量高,可图之; 螺杆寿命与螺杆选材有关,材料不好,价虽廉,但螺杆磨损快,经济性差。