无损检测方案
无损检测施工方案(高效)
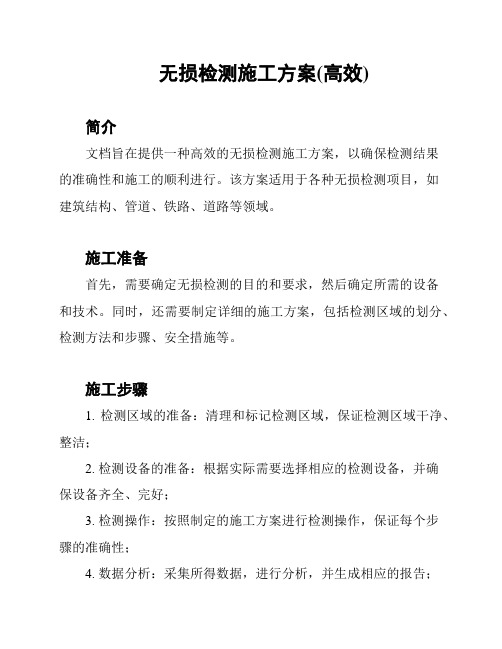
无损检测施工方案(高效)
简介
文档旨在提供一种高效的无损检测施工方案,以确保检测结果
的准确性和施工的顺利进行。
该方案适用于各种无损检测项目,如
建筑结构、管道、铁路、道路等领域。
施工准备
首先,需要确定无损检测的目的和要求,然后确定所需的设备
和技术。
同时,还需要制定详细的施工方案,包括检测区域的划分、检测方法和步骤、安全措施等。
施工步骤
1. 检测区域的准备:清理和标记检测区域,保证检测区域干净、整洁;
2. 检测设备的准备:根据实际需要选择相应的检测设备,并确
保设备齐全、完好;
3. 检测操作:按照制定的施工方案进行检测操作,保证每个步
骤的准确性;
4. 数据分析:采集所得数据,进行分析,并生成相应的报告;
5. 结果确认:针对检测结果进行确认,并在必要时进行重复检测;
6. 报告编制:根据检测结果编制详细的报告,报告中应包含检测目的、方法、结果等内容。
安全措施
在无损检测施工中,需要采取一系列安全措施,以确保施工过程中的安全性。
这些措施包括:
- 严格遵守安全操作规程;
- 设立安全防护措施,保证施工地点的安全性;
- 做好防腐、防火等工作,确保施工地点的安全性。
结论
该高效的无损检测施工方案,提供了详细的施工步骤和安全措施,以确保检测结果准确、施工过程安全。
在实际应用中,需要结合具体的项目和实际情况进行调整,以达到最佳的检测效果。
无损检测方案

无损检测方案本工程无损检测方法有RT(射线)探伤和UT(超声波)探伤。
一、无损检测委托程序二、无损检测程序管道检验按规范和图纸要求进行探伤。
管道的检测程序如下:三、无损检测方案1、作业前的准备检测时机:特种材质焊缝,必须在焊接完成经过24小时以后,方可进行检测作业。
检测前应确认材质和厚度,且经外观检查合格后才能进行操作。
2、无损检测人员要求⑴参与本工程的无损检测人员应具备国家相关部门颁发的检测资格证书。
⑴无损检测人员在实施检验前,须了解和熟悉有关监察规程、验收标准、技术文件要求,熟悉被检工件的规格、材质及其制造工艺、焊接工艺、检测工艺。
⑴I级检测资格人员只能在II级或II级以上资格人员指导和监督下从事检测操作,检测结果评定和报告签发及审核由II级或III级人员承担。
⑴检测人员应认真做好设备的维护、保养工作,执行安全防护制度。
⑴检测人员的校正视力不低于1.0,并要求评片人员距离400mm 能读出高为0.5mm,间隔0.5mm的一组印刷体字母。
⑴无损检测人员要牢固树立“质量第一”的观念,做到不漏检、不误判,准确执行检测标准。
⑴无损检测人员严格按照委托要求进行检测,做到检测比例执行率100%,扩探比例执行率100%。
3、射线检测方案⑴检测方法:采用X射线机进行双壁单影、双壁双影、单壁单影透照检测;检测设备:200/250/300KV X射线机;底片类型:JB4730-94;象质计:选用JB/T7902-99规定的R10系列线型金属丝象质计;增感屏:铅箔增感屏。
暗室处理:手工冲洗⑴检测工作流程⑴技术要求⑴底片标识底片上的显示包括工程编号、设备号或管道号、焊缝号、片位号、焊工号、规格厚度、返工标记、检验日期等。
所有标识紧密放置于工件表面与底之间,底片上的铅字影像齐全工整,并距离焊道影像5mm 以上。
如果业主或监理对焊口底片标识有进一步的要求,则应根据业主或监理要求补充标识内容和方式。
⑴象质计的放置采用单影法透照,线型象质计置于底片有效片长的1/4处,钢丝横跨焊缝并与焊缝方向垂直,每张底片都应显示象质计。
无损检测施工方案
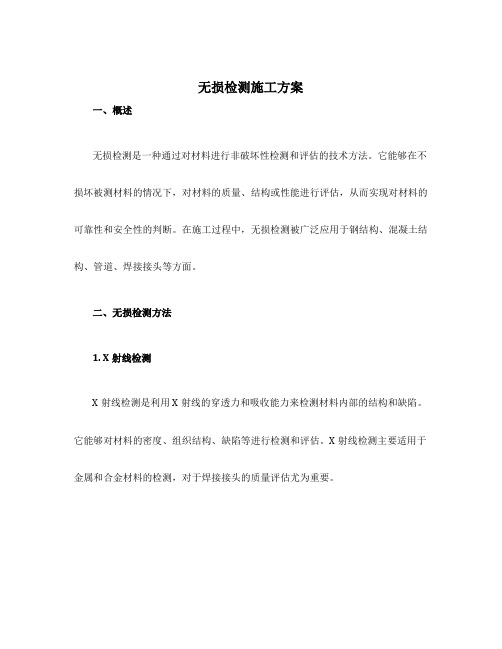
无损检测施工方案一、概述无损检测是一种通过对材料进行非破坏性检测和评估的技术方法。
它能够在不损坏被测材料的情况下,对材料的质量、结构或性能进行评估,从而实现对材料的可靠性和安全性的判断。
在施工过程中,无损检测被广泛应用于钢结构、混凝土结构、管道、焊接接头等方面。
二、无损检测方法1. X射线检测X射线检测是利用X射线的穿透力和吸收能力来检测材料内部的结构和缺陷。
它能够对材料的密度、组织结构、缺陷等进行检测和评估。
X射线检测主要适用于金属和合金材料的检测,对于焊接接头的质量评估尤为重要。
2. 超声波检测超声波检测是利用超声波在材料中的传播和反射特性来检测材料内部的结构和缺陷。
它能够对材料的厚度、波速、声阻抗等进行检测和评估,并能够定位和测量缺陷的尺寸。
超声波检测主要适用于金属和非金属材料的检测,对于混凝土结构和管道的检测具有重要意义。
3. 磁粉检测磁粉检测是利用外加磁场和磁粉的磁化作用来检测材料表面和近表层的结构和缺陷。
它能够对材料的表面裂纹、缺陷和疲劳裂纹进行检测和评估,并能够定位和测量缺陷的尺寸和形态。
磁粉检测主要适用于金属材料的表面检测,对于焊接接头和表面裂纹的检测具有重要意义。
4. 热红外检测热红外检测是利用物体的热辐射特性来检测物体的缺陷和异常情况。
它能够通过红外相机对物体的温度分布进行测量和分析,从而判断物体内部的结构和材料的性能状况。
热红外检测主要适用于建筑物、电力设备和输电线路等方面的检测,对于温度异常、能量损失等问题具有重要意义。
三、无损检测施工流程无损检测施工包括前期准备、检测方案制定、实施检测和结果分析报告等环节。
1. 前期准备在进行无损检测之前,需要对被测物体进行准备工作。
首先,要清理被测物体的表面,确保无杂质和污染物。
其次,要研究被测物体的结构和材料特性,了解其内部结构和缺陷的可能性。
2. 检测方案制定根据被测物体的特点和检测要求,制定适合的检测方案。
选择合适的无损检测方法,并确定检测仪器和设备的使用参数。
无损检测施工方案
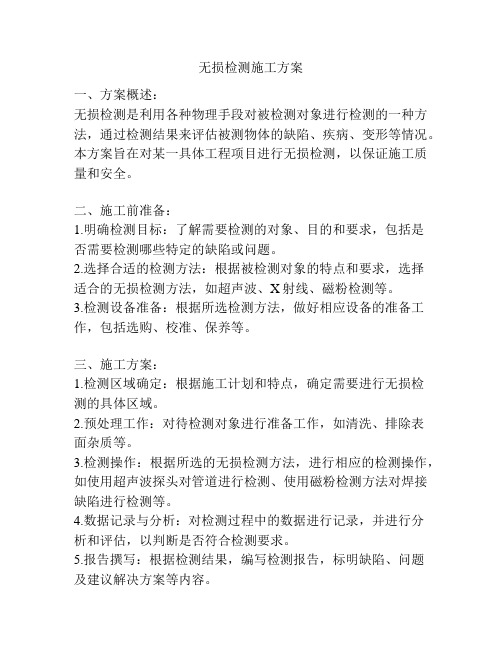
无损检测施工方案一、方案概述:无损检测是利用各种物理手段对被检测对象进行检测的一种方法,通过检测结果来评估被测物体的缺陷、疾病、变形等情况。
本方案旨在对某一具体工程项目进行无损检测,以保证施工质量和安全。
二、施工前准备:1.明确检测目标:了解需要检测的对象、目的和要求,包括是否需要检测哪些特定的缺陷或问题。
2.选择合适的检测方法:根据被检测对象的特点和要求,选择适合的无损检测方法,如超声波、X射线、磁粉检测等。
3.检测设备准备:根据所选检测方法,做好相应设备的准备工作,包括选购、校准、保养等。
三、施工方案:1.检测区域确定:根据施工计划和特点,确定需要进行无损检测的具体区域。
2.预处理工作:对待检测对象进行准备工作,如清洗、排除表面杂质等。
3.检测操作:根据所选的无损检测方法,进行相应的检测操作,如使用超声波探头对管道进行检测、使用磁粉检测方法对焊接缺陷进行检测等。
4.数据记录与分析:对检测过程中的数据进行记录,并进行分析和评估,以判断是否符合检测要求。
5.报告撰写:根据检测结果,编写检测报告,标明缺陷、问题及建议解决方案等内容。
四、施工要求:1.施工人员:由经过专业培训的无损检测人员进行,确保操作规范、准确性和安全性。
2.操作环境:提供适合的操作环境,如保持室温、降低干扰等,以确保检测过程的准确性。
3.保养维护:保养和维护无损检测设备,确保设备的正常运行。
4.安全防护:在无损检测过程中,使用符合要求的个人防护设备,确保施工人员的安全。
五、质量控制:1.制定质量控制计划:在施工前制定无损检测质量控制计划,包括检测要求、检测方法、操作标准等内容。
2.质量检查:在施工过程中进行质量检查,确保操作符合要求,并及时纠正不合格操作。
3.重要数据备份:对重要数据进行备份,以防止数据丢失造成损失。
六、施工管理:1.组织施工人员:组织好无损检测人员的工作安排和任务分配,确保施工进度和质量。
2.施工进度控制:配合工程进度安排,合理安排无损检测施工时间,确保无损检测工作的顺利进行。
无损检测管理方案
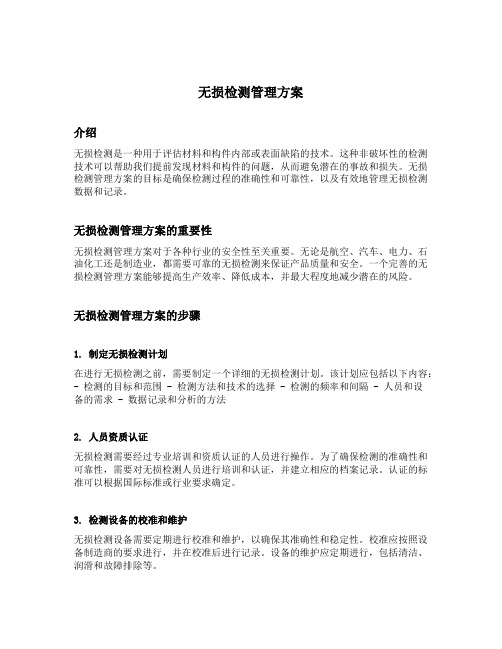
无损检测管理方案介绍无损检测是一种用于评估材料和构件内部或表面缺陷的技术。
这种非破坏性的检测技术可以帮助我们提前发现材料和构件的问题,从而避免潜在的事故和损失。
无损检测管理方案的目标是确保检测过程的准确性和可靠性,以及有效地管理无损检测数据和记录。
无损检测管理方案的重要性无损检测管理方案对于各种行业的安全性至关重要。
无论是航空、汽车、电力、石油化工还是制造业,都需要可靠的无损检测来保证产品质量和安全。
一个完善的无损检测管理方案能够提高生产效率、降低成本,并最大程度地减少潜在的风险。
无损检测管理方案的步骤1. 制定无损检测计划在进行无损检测之前,需要制定一个详细的无损检测计划。
该计划应包括以下内容:- 检测的目标和范围 - 检测方法和技术的选择 - 检测的频率和间隔 - 人员和设备的需求 - 数据记录和分析的方法2. 人员资质认证无损检测需要经过专业培训和资质认证的人员进行操作。
为了确保检测的准确性和可靠性,需要对无损检测人员进行培训和认证,并建立相应的档案记录。
认证的标准可以根据国际标准或行业要求确定。
3. 检测设备的校准和维护无损检测设备需要定期进行校准和维护,以确保其准确性和稳定性。
校准应按照设备制造商的要求进行,并在校准后进行记录。
设备的维护应定期进行,包括清洁、润滑和故障排除等。
4. 数据管理和记录无损检测生成的数据需要进行管理和记录。
应制定相应的数据管理方案,包括数据采集、存储、分析和报告等。
数据应进行备份,并按照一定的时限进行保存,以备将来可能的需求。
5. 评估和改进无损检测管理方案需要不断评估和改进。
可以通过内部审核、外部评估或科学研究等方式来评估管理方案的有效性。
根据评估结果,及时进行改进并进行相应的培训和沟通。
结论无损检测管理方案是保证无损检测准确性和可靠性的重要措施。
一个完善的管理方案能够帮助我们及早发现材料和构件的问题,降低事故风险和经济损失。
通过制定无损检测计划、人员资质认证、设备校准维护、数据管理和记录以及评估和改进等步骤,可以有效地管理无损检测过程,并及时采取措施解决问题。
无损检测方案

船舶无损检测方案一.总则例如:X-射线(RT)、超声波(UT)、磁粉(MT)、渗透(PT).无损检测数量、试验程序满足规范要求。
1.无损检测的认可标准:(1)RT:Ⅲ-Part3-CB/T 3558-94;(2)UT: Ⅲ-Part3-CB/T 3559-94;(3)MT: Ⅱ-Part3-JB/T 6061-92;(4)PT: Ⅱ-Part3-JB/T 6062-92;验收标准:CB/T3177-94二.焊缝区域等级划分1.一级焊缝在船中0.6L区, 外板横向对接缝、内底板横向对接缝;以及上甲板、纵舱壁,舭龙骨,纵桁的对接缝2.二级焊缝在船中0.6L范围外,外板横接缝;在船中0.6L范围内,外板纵接缝。
三.无损检测数量和范围1.一级焊缝(1)射线(RT)根据CCS材料与焊接规范对舯部0.6L区域内强力甲板和外板的射线拍片数量N=0.25(i+0.1Wt+0.1Wl).=0.25(644+0.1*1572+0.1*879)=222.25≈223i~~0.6L范围内纵、横向对接焊缝交叉处的总和Wt~~0.6L范围内横向对接焊缝的总长mWl~~0.6L范围内分段合拢的纵向对接焊缝的总长m具体位置见片位图纵横向对接焊缝交叉处的布片方向应平行于横向对接焊缝(2)超声波(UT)船底、舷侧和甲板纵骨的对接接头,在船中0.6L范围内每10个检查1个,0.6L范围内超声波检测位置范围见表1。
表一区域结构焊缝名称UT数量双层底纵骨HB02P/S~HB03C;HB03C~HB04C;HB04C~HB05C;HB05C~HB06C;HB06C~HB07C;HB07C~HB08C;HB08C~HB09C;HB09C~HB10C;HB10C~HB11C;HB11C~HB12C;HB12C~HB13C;HB13C~HB14C;HB14C-HB15C;4*13=52 纵桁HB02P/S~HB03C;HB03C~HB04C;HB04C~HB05C;HB05C~HB06C;HB06C~HB07C;HB07C~HB08C;HB08C~HB09C;HB09C~HB10C;HB10C~HB11C;HB11C~HB12C;HB12C~HB13C;HB13C~HB14C;HB14C-HB15C;2*13=26底边舱纵骨HS12DP/S~HB03P/S;HB03P/S~HB04P/S;HB04P/S~HB05P/S;HB05P/S~HB06P/S;HB06P/S~HB07P/S;HB07P/S~HB08P/S;HB08P/S~HB09P/S;HB09P/S~HB10P/S;HB10P/S~HB11P/S;HB11P/S~HB12P/S;HB12P/S~HB13P/S;HB13P/S~HB14P/S;HB14P/S~HB15P/S2*13*2=52 斜板HS12DP/S~HB03P/S;HB03P/S~HB04P/S;HB04P/S~HB05P/S;HB05P/S~HB06P/S;HB06P/S~HB07P/S;HB07P/S~HB08P/S;HB08P/S~HB09P/S;HB09P/S~HB10P/S;HB10P/S~HB11P/S;HB11P/S~HB12P/S;HB12P/S~HB13P/S;HB13P/S~HB14P/S;HB14P/S~HB15P/S2*13*2=52顶边舱纵骨HS12UP/S~HS13P/S;HS13P/S~HS14P/S;HS14P/S~HS15P/S;HS15P/S~HS16P/S;HS16P/S~HS17P/S;HS17P/S~HS18P/S;HS18P/S~HS19P/S;HS19P/S~HS20P/S;HS20P/S~HS21P/S;HS21P/S~HS22P/S;HS22P/S~HS23P/S;HS23P/S~HS24P/S;HS24P/S-HS25P/S2*13*2=52 斜板HS12UP/S~HS13P/S;HS13P/S~HS14P/S;HS14P/S~HS15P/S;HS15P/S~HS16P/S;HS16P/S~HS17P/S;HS17P/S~HS18P/S;HS18P/S~HS19P/S;HS19P/S~HS20P/S;HS20P/S~HS21P/S;HS21P/S~HS22P/S;HS22P/S~HS23P/S;HS23P/S~HS24P/S;HS24P/S-HS25P/S2*13*2=52UT数量总计:286舭龙骨对接焊缝100%UT.2.二级焊缝(1)射线(RT)0.6L以外的射线数量为0.6L范围呢的10%即23张,具体见片位图(2)超声波(UT)船底、舷侧和甲板纵骨的对接接头,在船中0.6L范围以外每20个检查1个.其他:1,波形壁分段焊缝10%UT,合拢焊缝10%UT2,海水箱周界100%UT3,分段内纵骨接头50%UT4,起重柱与甲板角焊缝100%UT5,顶边舱竖板与主甲板,底边舱斜板与内地板、外板100%UT6,水密与非水密肋板与舱壁内底板全焊透位置100%UT7,波形壁与底墩角焊缝100%UT,底墩侧板与底墩顶板100%UT8, 底墩侧板与底边舱斜板100%UT9, 直径大于75的一级管对接焊缝100%RT10, 直径大于100的二级管对接焊缝10%RT.11, 主基座对接接头100%用超声波(UT)检查,角接头10-20%用超声波(UT)检查12, 尾柱(铸钢件)和钢板之间的接头用超声波或者着色探伤,检测点根据CCS 验船师指定。
无损检测管理方案
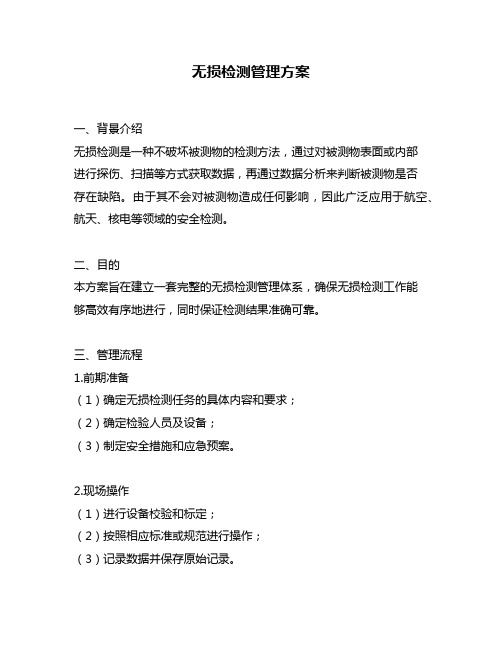
无损检测管理方案一、背景介绍无损检测是一种不破坏被测物的检测方法,通过对被测物表面或内部进行探伤、扫描等方式获取数据,再通过数据分析来判断被测物是否存在缺陷。
由于其不会对被测物造成任何影响,因此广泛应用于航空、航天、核电等领域的安全检测。
二、目的本方案旨在建立一套完整的无损检测管理体系,确保无损检测工作能够高效有序地进行,同时保证检测结果准确可靠。
三、管理流程1.前期准备(1)确定无损检测任务的具体内容和要求;(2)确定检验人员及设备;(3)制定安全措施和应急预案。
2.现场操作(1)进行设备校验和标定;(2)按照相应标准或规范进行操作;(3)记录数据并保存原始记录。
3.数据分析与评价(1)对采集到的数据进行处理和分析;(2)评价被测物是否存在缺陷,并给出相应结论。
4.报告编制与存档(1)编制无损检测报告;(2)将原始记录和报告存档。
四、管理要求1.人员要求(1)无损检测人员应具备相关专业知识和技能,并持有相应的证书;(2)检验人员应按规定进行培训和考核,确保其具备相应的能力。
2.设备要求(1)无损检测设备应符合国家标准或行业规范;(2)设备应定期进行检验和校准,确保其精度和可靠性。
3.安全要求(1)无损检测过程中必须严格遵守安全操作规程;(2)必须配备相应的安全防护措施,如防护眼镜、手套等。
4.质量控制(1)无损检测过程中必须遵守相关标准或规范;(2)必须对数据进行有效管理和存储,确保数据的可追溯性和准确性。
五、管理评估为了不断提高无损检测工作的质量和效率,需要对管理体系进行评估。
评估内容包括:(1)人员素质及培训情况;(2)设备状态及维护情况;(3)操作流程是否规范;(4)数据是否准确可靠;(5)管理体系是否完善。
六、总结无损检测是一项非常重要的工作,需要建立完善的管理体系来保证其质量和效率。
本方案提供了一套全面的无损检测管理方案,旨在为相关单位提供参考和借鉴。
同时,我们也希望相关单位能够根据自身实际情况进行相应调整和改进,不断提高无损检测工作的质量和效率。
无损检测工作计划
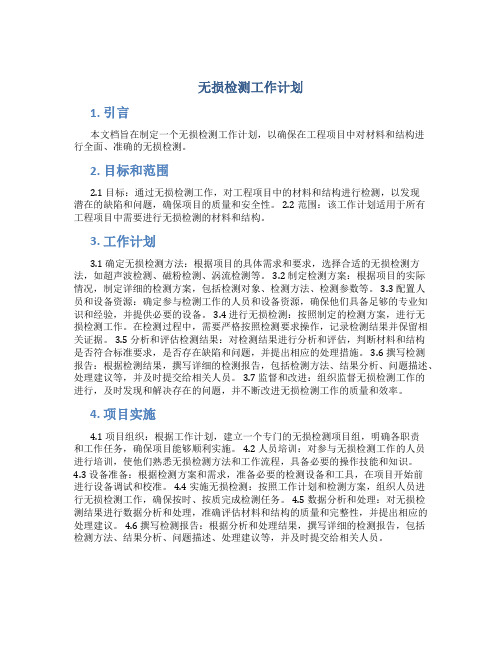
无损检测工作计划1. 引言本文档旨在制定一个无损检测工作计划,以确保在工程项目中对材料和结构进行全面、准确的无损检测。
2. 目标和范围2.1 目标:通过无损检测工作,对工程项目中的材料和结构进行检测,以发现潜在的缺陷和问题,确保项目的质量和安全性。
2.2 范围:该工作计划适用于所有工程项目中需要进行无损检测的材料和结构。
3. 工作计划3.1 确定无损检测方法:根据项目的具体需求和要求,选择合适的无损检测方法,如超声波检测、磁粉检测、涡流检测等。
3.2 制定检测方案:根据项目的实际情况,制定详细的检测方案,包括检测对象、检测方法、检测参数等。
3.3 配置人员和设备资源:确定参与检测工作的人员和设备资源,确保他们具备足够的专业知识和经验,并提供必要的设备。
3.4 进行无损检测:按照制定的检测方案,进行无损检测工作。
在检测过程中,需要严格按照检测要求操作,记录检测结果并保留相关证据。
3.5 分析和评估检测结果:对检测结果进行分析和评估,判断材料和结构是否符合标准要求,是否存在缺陷和问题,并提出相应的处理措施。
3.6 撰写检测报告:根据检测结果,撰写详细的检测报告,包括检测方法、结果分析、问题描述、处理建议等,并及时提交给相关人员。
3.7 监督和改进:组织监督无损检测工作的进行,及时发现和解决存在的问题,并不断改进无损检测工作的质量和效率。
4. 项目实施4.1 项目组织:根据工作计划,建立一个专门的无损检测项目组,明确各职责和工作任务,确保项目能够顺利实施。
4.2 人员培训:对参与无损检测工作的人员进行培训,使他们熟悉无损检测方法和工作流程,具备必要的操作技能和知识。
4.3 设备准备:根据检测方案和需求,准备必要的检测设备和工具,在项目开始前进行设备调试和校准。
4.4 实施无损检测:按照工作计划和检测方案,组织人员进行无损检测工作,确保按时、按质完成检测任务。
4.5 数据分析和处理:对无损检测结果进行数据分析和处理,准确评估材料和结构的质量和完整性,并提出相应的处理建议。
- 1、下载文档前请自行甄别文档内容的完整性,平台不提供额外的编辑、内容补充、找答案等附加服务。
- 2、"仅部分预览"的文档,不可在线预览部分如存在完整性等问题,可反馈申请退款(可完整预览的文档不适用该条件!)。
- 3、如文档侵犯您的权益,请联系客服反馈,我们会尽快为您处理(人工客服工作时间:9:00-18:30)。
1、总则中国海洋石油建淘化工有限公司60万吨/年甲醇工程属中外合资的项目,由于管道、转化炉施工工期要求紧,交叉作业多,现场安全、质量要求严格,为保证工程安全、高效、高质量中交特编制此无损检测计划。
1.1 编制依据《ASME》(美国机械工程师协会)第5章无损检测《ASME》(美国机械工程师协会)B31.1 动力管道《ASME》(美国机械工程师协会)B31.3 工艺管道《管路和部件焊接和焊缝检验》(GNA 0828E)《射线检测安全防护管理制度》(山东泰思特公司)《压力容器无损检测工艺规程》(山东泰思特公司)《压力管道无损检测工艺规范》(山东泰思特公司)《压力容器质保手册》《压力管道质保手册》(山东泰思特公司)1.2 无损检测人员要求NDT(无损探伤)人员应根据ASME B31.1,第6章或ASME B31.3,第6章的规定接受培训。
依据SNT-TC-1A的规定,检验员应拥有足够的执行无损探伤检验的技术知识。
参加生产的人员不得执行探伤检验。
取得资格证书,方能承担与资格证书的种类和技术等级相适应的无损检测工作,现场检测必须由Ⅰ级或Ⅰ级以上人员担任,无证人员不得上岗,评定试验结果和编写试验报告。
必须由Ⅱ级或Ⅱ级以上人员担任。
射线检测工作人员必须取得《射线工作人员证》方能上岗,检测作业时严禁个人单独上岗,射线检测工作人员在作业时必须穿戴防护用品和随身携带个人剂量仪。
1.3 无损检测质量控制程序无损检测质量控制程序见表1质量控制经理探伤责任工程师RT 拍片UT 调整仪器 MT 配磁悬液 PT 预清洗底片不符 合标准要 求、影响 评定或有 疑问重拍审 核 报 告甲 方 验 收表 11.4 无损检测设备射线检验采用理学2505、3005,丹东2505、3005,X 光机。
超声波检验采用汉威-600a 型超声波探伤仪,磁粉检验采用CJE -2A 型磁粉探伤仪,渗透检验采用DPT -5型渗透探伤剂,光谱检测采用NITON xlt 800系列合金分析仪。
2、无损检测工艺 2.1 渗透检测工艺暗室处理 校准灵敏度 准备工作 施渗透液 初 评 初 探 实施磁探 清 洗 复 评复 探观察分析显 象出具探伤报告观察痕迹2.1.1一般要求在执行着色渗透检验时,应遵守ASME规范第5章,第6款;和染色渗透液制造厂家说明书的规定。
应保证彻底的清洗和除脂,提供足量的着色渗透和显色时间,以及涂敷一薄层显色剂。
2.1.2渗透探伤采用溶剂去除型着色法探伤,使用溶剂去除型渗透液。
渗透剂、显象剂、清洗剂型号采用DPT-5。
对比试块为镀铬试块。
2.1.3 渗透探伤前需应对表面及附近25mm范围内进行打磨处理,不得有污垢、铁锈、锈蚀、焊渣、氧化皮、毛刺及保护层等防碍显示的杂物。
2.1.4 渗透探伤前应对受检表面进行预清洗。
2.1.5 喷洒渗透剂时喷嘴距离受检表面宜为300-400mm,渗透剂要完全润湿被检表面,在15-50℃的温度下,渗透时间不得少于10分钟,在温度低于15℃时,着色渗透时间至少应该是15分钟。
在整个着色渗透期间,应该有足够的着色渗透液复盖检验区域。
2.1.6去除多余渗透液时,应先用不脱毛的布擦掉多余渗透液,然后再用蘸有清洗剂的布向同一方向擦拭,直到把多余渗透液全部去出,但应注意不要清洗过度,同时也应防止清洗不足,清洗时不得用清洗剂直接喷洒在被检工件表面。
2.1.7施加显象剂前应充分摇动显象剂,喷洒显象剂时,喷嘴距离被检表面宜为300-400mm,喷洒方向与被检表面夹角为30-40度,显象剂喷洒应薄而均匀。
结果的观察应在被检表面光照度大于500lx的条件下进行。
观察结束后应清除剩余显象剂以防腐蚀工件。
2.1.8操作时要严禁火种和采取必要的通风措施,渗透探伤的材料应防止日晒、烘烤。
2.1.9验收标准对于“锅炉内部管道”,应依据ASME B31.1,第6章评定检验结果,对于“工艺管道”,应依据ASME B31.3,第6章,评定检验结果。
2.1.10检验标识和报告检查员应为检验对象作标识,而且应标识得在管路验收试验以前,一直能根据检验报告确定检验的焊缝;每份检验报告只能包含属于同一管子编号的焊缝。
应根据鲁齐公司资料表GFA 0424E编写检验报告。
2.2磁粉检测工艺2.2.1一般要求应依据ASME规范,第5章,第7款的规定,执行磁粉探伤。
焊缝表面和过渡区域应是清洁的,应清除焊渣和氧化皮。
必要时,受探伤的表面应打磨光滑。
2.2.2 磁悬液配制磁悬液由黑磁膏、水、分散剂配制,每挤出100mm长磁膏加入1000ml水,磁悬液浓度为10~20g/l,并加入一定数量的分散剂,若悬浮液薄层是连续并复盖试件的全部,则认为存在足够的分散剂,否则应继续加入分散剂。
2.2.3 灵敏度要求应使用A型灵敏度试片在每次探伤前及探伤结束后时进行校验,必须注意测量灵敏度时试片有槽一侧应紧贴被检表面。
2.2.4 操作采用交流电磁轭连续磁化法,探头应紧贴被检工件表面,在施加磁化电流的同时施加磁悬液,通电时间为1-3S,为保证磁化效果应反复磁化两次。
两次磁化方向应相互垂直,为保证检测结果的准确性,磁极间距应为200mm,交流电磁轭的提升力要达到44N,检测区域控制在两级连线两侧各50mm范围内,磁化区域应保证至少25mm的重叠。
结果观察应在被检工件表面的光照度不小于500lx的条件下进行,当不能判断显示的真伪时应进行重新检验或使用其它检测方法进行校验。
检测过程中若发现操作失误或灵敏度不合要求,应对原检测部位进行重新检测。
2.2.5 验收标准对于“锅炉内部管道”,应依据ASME B31.1,第6章评定检验结果,对于“工艺管道”,应依据ASME B31.3,第6章,评定检查结果。
2.2.6检验标识和报告检查员应对检验对象作标识,而且应标识得在管路验收试验以前,一直能根据检验报告确定检验的焊缝;每份检验报告只能包含属于同一管子编号的焊缝。
应利用鲁齐公司资料表GFA 0424E编写检验报告。
2.3 射线检测工艺2.3.1一般要求应依据ASME规范第5章、第2款的规定执行检验。
应满足以下附加要求:—应该使用线型射线透度计;—在焊缝平面,在一次照相胶片曝光时胶片密度应高于2.0和低于4.0;—在两次胶片曝光时,同时检查的两张胶片的胶片密度应高于3.0和低于4.0;—分段射线照相数应确定得使中心射线和端部射线之间检验厚度的增大量不超过1.10倍的壁厚;2.3.2 透照方法2.3.2.1双壁单影法X射线拍片时,在满足几何不清晰度的条件下,管径D≥200mm时采用X 射线机紧贴管壁垂直法拍片。
2.3.2.2双影双壁法D≤89mm及壁厚<8mm时,允许使用椭圆射线照相。
对于整个焊缝检验需要最少两张90 的偏移射线照像。
橢圆开口间距应控制在3-15mm之间;Φ≤76管道焊口,如果因障碍限制不能实现双壁双影透照时,可采用垂直透照,透照次数不得小于2次。
但双壁双影透照法和垂直透照法焦距必须满足几何不清晰度的要求。
2.3.3 透照次数压力管道射线检测时,各种规格的透照次数,底片的有效长度和胶片的使用长度应严格按下表的规定执行,不允许一次透照两张及两张以上片子,但中心一次曝光时例外。
管径Φ(mm)108 114 133 159 168 219 273 325 377母材厚度(mm)T≤6/6<T≤20T≤7.5/7.5<T≤20T≤12/12<T≤24T≤17/17<T≤28T≤19/19<T≤29T≤33/33<T≤37T≤10/10<T≤46T≤19/19<T≤57T≤29/29<T≤67胶片长度(mm)150 150 150 150 150 150 150 300 300 拍片张数 6 6 6 6 6 8 10 6 6 2.3.4 底片编号和象质计的摆放底片的编号按“区域号,单元号,管线号,焊缝号,片号”编排,搭接用“1 2,3,4……”标示,片号用英文字母“A,B,C,D……”标示,加扩拍片在焊缝号后加放“G”标示,中心符号用“”标示。
一次返修后在片号后加放“R1”二次返修后在片号后加放“R2”。
现场制作或组装的压力容器(如球罐、冷箱、反应器、容器、料仓、塔)射线拍片时需摆放日期标记。
底片的标记布置按下图所示。
检验公司标识管线号焊工号焊缝号片号1 2检验公司标识管线号焊工号焊缝号片号2.3.5胶片的使用甲醇工程胶片全部由用鲁齐公司提供。
2.3.6散射线屏蔽为防止散射线的影响,在胶片后面放一块1.5~2mm厚的铅板,面积应大于暗袋的面积。
为了检查背散射应在暗袋的背面粘附一个“B”的铅字(B的高度为13mm,厚度为1.6mm),若在底片上出现“B”的较淡影象,说明防护不够,应重新透照。
若出现较黑影像则不作为底片判废的依据。
2.3.7 曝光量的选择为达到标准要求,曝光量应按如下选择:X射线:曝光量应满足15mA·min,底片密度应高于2.0和低于4.0对于D≤89mm的焊口拍片采用短时间高电压。
2.3.8 暗室处理暗室处理是保证底片质量的重要工序,包括切片、装片、显影、停影、定影、水冲洗、和烘干等。
2.3.9.1 胶片的切装与保管胶片应放置在铅箱中与射线完全隔离,在阴凉干燥处存放。
胶片盒应在暗室开封,外包装纸多余量要折回盖严以防曝光。
切片时要按每次用量带衬纸取出,以防划伤。
装片时要避免胶片与其它粗物摩擦,防止静电感光。
胶片不得折叠或弯曲过度,防止折痕。
暗室操作人员接触胶片时要将手洗净,胶片处理前不得与显、定影液接触。
暗室安全红灯应距胶片0.5m以上安放,红灯不能过亮以防胶片曝光。
2.3.9.2 胶片的冲洗显影:显影液温度应控制在18-22℃,显影时间为4-8min。
显影过程中要使胶片在显影液中上下移动,以保证显影液的新鲜性。
片夹之间要有一定距离,以防止胶片接触。
停显:显影后应将胶片放入2%的冰醋酸溶液中停显1-3秒。
定影:胶片放入定影液中时,片夹之间要留有一定距离防止胶片接触。
定影时间要根据定影液的新鲜度来确定,一般时间控制在15min。
水洗:底片要在流动的水中进行冲洗,水洗时间一般为20min,不得超过30min。
底片干燥:水洗后的底片应放入有脱水剂的水中浸泡5秒钟,底片干燥应在无尘、干燥、通风处晾干。
2.3.10 返修与扩探若有超标缺陷,应填写焊缝返修通知单,通知单上应注明缺陷性质、焊缝级别和返修部位,射线探伤不合格时应按标准作补充扩探,对扩探或返修后的部位探伤应按原工艺进行。
2.3.11 底片评定2.3.11.1 底片质量底片质量要达到AB级要求,象质计和底片识别系统齐全,位置准确,应不掩盖被检焊缝影像。
底片上识别的象质指数应符合标准的规定且长度应不小于10mm。
底片有效评定区内不得有防碍底片评定的伪像。
2.3.11.2 评定对于“锅炉内部管道”应依据ASME B31.1,第6章对检验结果进行评价,对于“工艺管道”应依据ASME B31.3,第6章评定检验结果。